45钢淬火后出现表面裂纹原因分析及对策
45钢淬火开裂解决方案

45钢淬火开裂解决方案1. 引言钢材是广泛应用于机械制造和工业领域的材料之一,而淬火是对钢材进行热处理的一种常用方法。
然而,淬火过程中可能会出现开裂问题,这给钢材的性能和可靠性带来了威胁。
因此,针对淬火开裂问题,需要制定解决方案,以确保钢材质量和使用寿命。
2. 开裂原因分析钢材淬火开裂的原因很多,主要包括以下几个方面:2.1 内应力过大在淬火过程中,钢材的表面和内部会迅速冷却,造成急剧的温度和应力变化。
当冷却速度过快或不均匀时,钢材产生内部应力过大,容易导致开裂。
2.2 压缩应力不足淬火后,钢材表面会形成一层脆性的马氏体,而内部保留了一定的奥氏体组织。
如果钢材内部奥氏体的体积增大,而表面的马氏体受到压缩不足,也容易导致开裂。
2.3 杂质和夹杂物钢材中的杂质和夹杂物也是导致开裂的重要原因之一。
杂质会降低钢材的韧性和延展性,夹杂物则成为开裂的起始点。
2.4 硬度不均匀淬火后,钢材的硬度分布不均匀也会导致开裂。
硬度过高或过低的区域容易发生应力集中,从而引发开裂。
3. 解决方案针对淬火开裂问题,我们提出以下解决方案:3.1 优化淬火工艺参数通过优化淬火工艺参数,可以控制钢材的冷却速度和温度梯度,从而减小内应力和压缩不足的问题。
合理选择淬火介质和温度,以避免过快或不均匀的冷却。
3.2 降低表面应力在淬火过程中,采取一些措施来降低钢材表面应力。
例如,可对钢材进行预处理,如表面机械处理、脱碳退火等,以减少开裂的风险。
3.3 优化钢材的化学成分合理控制钢材的化学成分,降低杂质和夹杂物的含量。
采用纯净的原材料和改进冶炼工艺,可以有效减少开裂的概率。
3.4 加强表面处理在淬火前对钢材进行表面处理,如酸洗、喷丸、抛光等,可以去除一些表面缺陷和杂质,减少开裂的可能性。
同时,还可以增加表面硬度分布的均匀性。
3.5 适当回火处理淬火后,适当进行回火处理,有助于减轻内应力,改善钢材的韧性。
选择合适的回火温度和时间,以平衡硬度和韧性的要求,避免开裂的发生。
45_圆钢表面裂纹原因浅析_吴晖
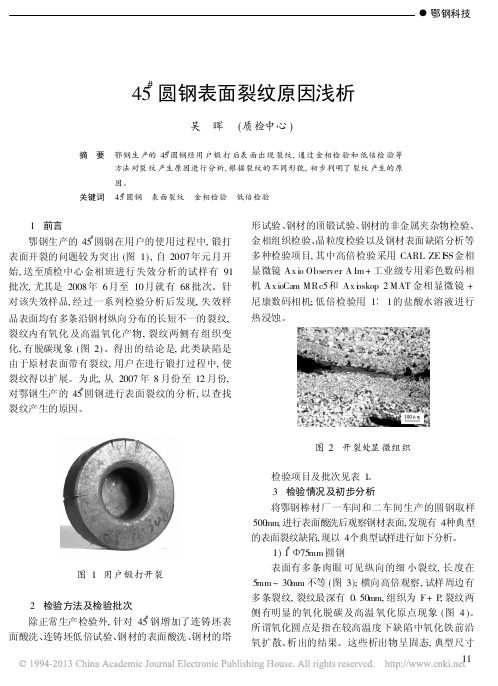
5 改进措施及建议 综上所述, 产生圆钢表面裂纹的原因不仅与炼钢 有关, 也与轧钢有关, 针对这一问题, 可采取一系列的 措施来减轻或消除。 1)炼钢主要是减少钢中气体和夹杂物的含量, 消 除表面气孔, 皮下气泡及非金属夹杂物, 即消除发
图 9 5 28mm 圆钢表面裂纹
4 裂纹原因分析 从上述可知, 1# 、2# 试样是铸坯上有缺陷, 在轧制 后形成裂纹; 3#、4#试样是在轧制过程中形成裂纹。 4. 1 连铸坯表面质量缺陷对裂纹的影响 在检验连铸坯低倍质量中发现, 连铸坯表面有针 孔状的缺陷、皮下气泡、表面裂纹等, 针孔和皮下气泡 分布在连铸坯的外表面及皮下, 分布面广, 数量多, 其 直径在 015~ 2mm 之间; 表面裂纹缺陷是在钢坯的表 面有纵向裂纹, 深 3~ 5mm 之间 (图 11) 。 连铸坯缺陷在轧钢加热炉中的高温下, 暴露于空气 中会被氧化, 在随后的轧制过程中缺陷延伸在钢材表面 形成细小的裂纹, 此类裂纹在显微镜下观察裂纹内和裂 纹尾部有高温氧化产物, 裂纹两侧有明显的脱碳。 4. 2 连铸坯外来夹杂产生的裂纹 连铸坯中外来夹杂物 ( 图 12) 的产生途径有: 耐 火材料剥落进入钢水中; 保护渣卷入钢水中。该外来 夹杂破坏了钢的基体连续性, 引起应力集中, 导致裂 纹的形成, 当连铸坯中大量 的外来夹杂物附 集在皮 下, 在轧钢加热炉中未暴露于空气, 在随后的轧制过 程中夹杂物轧出钢材表面形成裂纹, 此类裂纹在显微 镜下观察裂 纹内填充有外来夹杂 物, 裂纹两 侧无脱 碳, 裂纹附近有大量的外来夹杂物。 4. 3 轧制过程中产生的裂纹 折叠 (图 13) 是轧件表面的纵向突起或凹痕在继 续轧制过程中被轧平引起的表面缺陷, 在横断面上缺 陷的端部不分枝, 充满氧化铁, 裂纹两侧脱碳深度不 等。轧件在孔型轧制过程中, 产生了纵向突起, 如轧 件过充满 (耳子 ) 、错位等, 翻转 90b继续轧制时, 这些 纵向突起被压倒、轧平形成折叠。
45钢轴套零件裂纹原因分析及改进措施

31HRC,宏观硬度值趋向于技术要求的中上限,轴套零件 硬度基本符合要求,判定为合格。
(3)金相分析 观察金相组织,轴套零件裂纹形态,裂纹较粗大,裂 纹两边及附近未见氧化、脱碳层,也未见明显的非金属夹 杂物。裂纹始于表面,由表及里由粗变细,沿原奥氏体晶 界呈曲折锯齿状向内伸展,愈向内裂纹尾部愈尖细。淬火 回火后组织回火索氏体,按照GB6394-2017标准,实际奥 氏体晶粒度为5-6级,无过热现象。轴套零件的原始组织 为铁素体基体上分布着细粒状珠光体,略呈轧向分布,单 面脱碳层为0.02mm,符合45材料要求。
4.改进措施 (1)优化零件的结构尺寸 在该轴套零件两端面的外圆、内孔处增加倒角 45°×1.5mm;不考虑成本可将零件壁厚放大到11mm, 即将内孔Φ32mm修改为Φ26mm,避开淬裂敏感尺寸区。 优化后零件结构如图2所示。
(2)热处理参数调整 轴套零件原热处理淬火温度符合45钢调质参数,轴套 零件壁厚仍按原8mm,在能够保证零件调质硬度的前提 下,并结合该零件成品使用环境为室温条件,可以通过适 当降低淬火温度,降低了奥氏体中的固溶含碳量,从而减 少了形成马氏体时的晶格歪扭,减小了组织应力减小,另 外随着温度的降低,热应力也相应减小。 经过试验轴套零件将热处理淬火参数中的淬火温度调 整为790~810℃在保护气氛炉中加热防止零件氧化脱碳, 保温时间:12mm/min,水冷。虽然淬火硬度有所降低, 可适当调整即降低轴套回火温度20℃~40℃,保证轴套零 件调质硬度的要求,这样轴套零件裂纹率有较大降低。 (3)热处理淬火冷却方法改变 轴套零件壁厚仍按原8mm,轴套零件采用双液淬火 (水淬油冷)的方法,将轴套零件用铁丝捆绑6件/每串, 这种冷却方法关键在于准确控制水冷时间,正确掌握轴套 零件出水温度,经验证明,轴套淬火在水中控制停留时 间为2~3秒然后迅速转入油中冷却,保证零件出水温度 450~350℃,即能获得马氏体组织,也使淬火应力限制在 最低水平,从而大大减小了轴套零件淬火开裂。
解决45钢淬火开裂问题的实用措施

解决45钢淬火开裂问题的实用措施解决45 钢淬火开裂问题的实用措施45钢是工业生产中最常用的材料,热处理量很大,但这种材料淬火开裂与畸变也是热处理生产中经常发生的问题。
特别是当 45 钢含碳、含锰量在规定范围上限,或含铬、含铜、含钼总量超过一定数值(>0.2 %),或含有微量元素钨、硼;或者工件形状复杂,在常规淬火冷却时(水冷)很容易开裂、畸变,造成报废。
为此,安徽合力公司施家山等人根据他们的生产经验,提出了一些措施,取得了一定的效果。
一、将水冷改为油冷,能有效地防止淬火开裂、減少畸变。
45 钢调质所采用的冷淬方法通常是水冷,水冷后综合力学性能比较好。
但水冷容易开裂,畸变又大。
有些产品力学性能要求不是很高,在此情况下,在硬度能达到技术要求的前提下,可以改用油冷,能有效避免淬火开裂,且所得材料硬度比较均匀。
例如,对一种硬度要求达到235~260HB的套筒,原淬火工艺是820℃ 加热,自来水冷却至室温,淬火后硬度50~55HRC,550℃回火后硬度240~260 HB。
结果发现10%~15%产品在内径处有裂纹,纵向出现长度10~20 mm、深度0.30~0.50 mm的龟裂。
分析其原因是水冷时内外径冷却不均匀,导致裂纹产生。
现淬火工艺改为840℃加热,20#机油冷却,油温60~80℃,并且用空压机鼓气搅拌。
淬火后硬度为45~50HRC,530℃回火后硬度240~255HB,全部合格。
所生产的产品,由于改进了淬火介质,既能避免开裂,又能满足技术要求。
用户使用4年多来,没有出现质量问题,使用效果良好,经济效益明显。
二、采用渗碳淬火+油冷工艺。
对于一些形状复杂、厚薄不均,又有孔、凹槽、缺口的模具,如用水冷,不仅容易开裂,而且畸变大;硬度又不均匀,报废率很高,造成很大的经济损失。
但如改用机油冷却,硬度又达不到要求。
对于这一类材料,可以采用渗碳淬火工艺,不仅可以消除淬火开裂、减少畸变,而且还提高了使用寿命。
例如,对于一种硬度要求为55~60HRC成型模,其缺口涨大要求小于0.20mm。
45钢制零件淬火开裂分析

失效分析45钢制零件淬火开裂分析王 荣(上海材料研究所,上海200437)摘 要:某45钢零件按常规热处理工艺进行淬火时,多次发生淬裂现象。
随炉试样力学性能测试结果表明,屈服强度较高,伸长率偏低,无法满足该零件技术要求。
从原材料着手,通过金相组织、晶粒度和夹杂物分析,对零件在热处理时淬火开裂的原因和热处理后力学性能异常进行了探讨,认为该零件原材料存在过热造成的组织缺陷和脆性夹杂物超标是导致材料热处理后失效的主要原因。
关键词:热处理;奥氏体晶粒度;非金属夹杂物中图分类号:TG 142.31 文献标识码:A 文章编号:100124012(2004)1120576202FA IL U RE ANAL YSIS OF HEA 2TREA TM EN T FOR 45STEEL COMPON EN TWANG Rong(Shanghai Research Institute of Materials ,Shanghai 200437,China )Abstract :S ome parts made from 45steel which cracked frenquently during conventional quenching process.Themechanical property testing showed that the yield strength is too high and the elongation rate is less than the technical requirements.This paper presents the main causes through analyzing the microstructure ,grain size and the non 2metallic inclusions of the test pieces.The presentations are as follows :analyzing the cracking causes of the steel in quench and the improper mechanical properties after heat treatment.And so ,many actual problems are solved in production.K eyw ords :Heat treatment ;Austenitic grain size ;Non 2metallic inclusion1 引言某单位生产的45钢制零件(规格:<280mm ×30mm ,L =1200mm )在热处理时常发生淬裂现象,淬裂率达90%以上,裂纹随机分布,多呈月牙状。
45_钢热处理淬火裂纹控制_边晋荣

0引言 45#钢 是 机 械 制 造 行 业 中 最 常 用 的 传 统 材 料 之 一 ,
为获得良好的索氏体组织, 其需淬火和高温回火热处 理。45#钢传统淬火热处理规范是淬火温度为 810℃, 冷
却介质为水或 10%盐水, 水温为室温, 但 45#钢淬火热
处理极易产生不同程度的淬火裂纹, 废品损失较大, 在 生产中淬火裂纹不易控制[1][2][3]。近年来, 我们经过大量
在本设计中, 中断系统的周期是 0.1 ms。所以在任 务 1 中, 接收到一个中断脉冲就将被处理一次; 在任务 2 中, 接收到 10 个中断脉冲时被处理一次; 在任务 3 中当接收到 500 个中断脉冲时才被处理一次。在任务 2 的执行中, 如果 0.1 ms 的中断信号被接收的话, 即跳 跃执行任务 1, 执行后才继续执行任务 2。同样, 在任务 3 的执行中, 如果 1 ms 的中断信号被接收的话, 即 跳 跃执行任务 2, 执行后才继续执行任务 3。 3 多车床数控系统的单个车床操作面板[2]
45钢零件在冷却前期受到较大的热应力作用产生大量的塑性变形而大量的塑性变形使奥氏体在ms点以上发生马氏体转变这部分硬而脆的马氏体不仅数量少而且分布在应力集中的缺陷和晶界上在以后的塑性变形及应力转换过程中极易与组织应力叠加易使材料发生裂纹
第 4 期(总第 97 期) No.4 (SUM No.97 )
图 2 几种淬火介质冷却特性图
热处理淬火开裂及预防
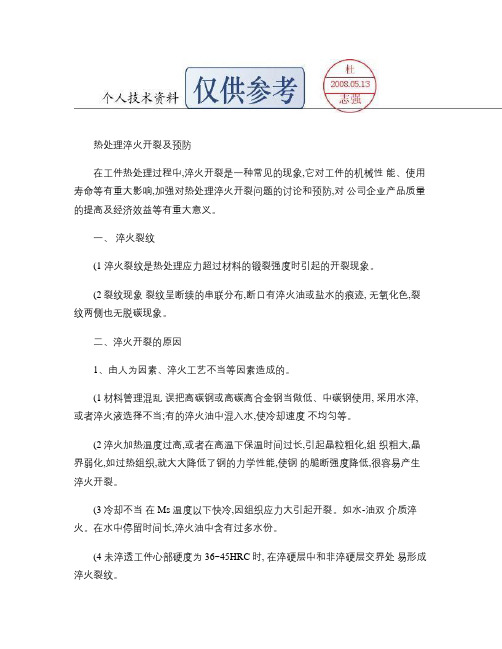
(4正确预先热处理,避免正火、退火组织缺陷(魏氏组织等。
(5正确选择加热参数。减少因加热温度过高、加热速度过快等原因引起的开裂。
(6正确的选择淬火介质和淬火工艺(方法。
(7合理的安排热处理工艺,尽量减少截面突变等容易引起冷却速度不均匀,应力增大的开裂现象。
(8对工件容易开裂的部位,如尖角、薄壁、孔等进行局部包扎。1、(9
3、
力较大,易在内孔壁上形成纵向分布的裂纹,从端面看呈放射状。
4、
时间差很大,形成很大的组织应力,以至产生裂纹。例如小件头部毛坯裂纹。5、应力集中引起裂纹钢件上有尖角、缺口等存在的情况下,易在淬火时造成Байду номын сангаас力集中而产生裂纹,尤其在应力集中和截面急剧变化的共同作用下淬裂危险更大。
6、网状裂纹这种裂纹具有任意方向性而与工件形状无关,网状裂纹的深度一般在0.01~0.15范围内,是一种表现裂纹,高碳工具钢和合金工具钢表面脱碳后淬火医形成网状裂纹。
(3冷却不当在Ms温度以下快冷,因组织应力大引起开裂。如水-油双介质淬火。在水中停留时间长,淬火油中含有过多水份。
(4未淬透工件心部硬度为36~45HRC时,在淬硬层中和非淬硬层交界处易形成淬火裂纹。
(5重复淬火前未经中间退火,过热倾向大,前项淬火的应力未能完全消
除,以及多次加热引起表面脱碳,都会促使淬火开裂。
(3具有最危险淬火尺寸的工件易形成淬火裂纹。工件的全部淬透时有一最危险的的淬火尺寸,其直径(或厚度是:水淬时约8~15㎜;油淬时约25~40㎜。尺寸小于最危险的尺寸时,心部与表面温差小,淬火应力小,不易开裂。工件尺寸大于最危险尺寸时,淬火应力虽然大,但拉应力峰值远离表面,淬火倾向反而减小。只有中间某一尺寸(最危险尺寸的工件,拉应力峰靠近表面,且数值也较大对淬裂最敏感。4、典型裂纹现象
45钢淬火开裂解决方案(一)

45钢淬火开裂解决方案(一)
解决方案:45钢淬火开裂
问题概述
•问题描述:淬火后的45钢存在开裂现象
•问题影响:影响生产正常进行,降低产品质量
原因分析
•原因1:钢材性质不符合生产要求
•原因2:淬火工艺参数设置不合理
解决方案
•方案1:购买符合生产要求的钢材
–优点:保证钢材的质量,稳妥有效
–缺点:成本较高,需增加采购成本
•方案2:调整淬火工艺参数
–优点:成本较低,能够有效解决问题
–缺点:需要大量实验验证,存在不确定性
选取方案
选择方案2,调整淬火工艺参数。
考虑到成本和效果的平衡,该方案最为适宜。
具体方案
•步骤1:分析淬火工艺参数,找出不合理之处
•步骤2:针对不合理的地方进行优化调整
•步骤3:制定实验方案,进行测试验证
•步骤4:根据实验结果,不断优化调整,最终确定合理的淬火工艺参数
实施效果
经过实验验证,成功解决45钢淬火开裂问题。
生产正常进行,产品质量得到有效提升。
实施要点
•根据实际情况,分析并找出淬火工艺参数不合理之处。
•优化调整方案时,需综合考虑多个因素。
•制定实验方案时,应尽可能模拟实际生产情况。
•在实验过程中,要严格按照实验方案执行,控制各项参数。
•根据实验结果及时调整优化,直至确定合理淬火工艺参数。
结论
通过调整淬火工艺参数,成功解决45钢淬火开裂问题,提升了产品质量和生产效率。
预计实施该方案后,能够降低生产成本和提高利润。
- 1、下载文档前请自行甄别文档内容的完整性,平台不提供额外的编辑、内容补充、找答案等附加服务。
- 2、"仅部分预览"的文档,不可在线预览部分如存在完整性等问题,可反馈申请退款(可完整预览的文档不适用该条件!)。
- 3、如文档侵犯您的权益,请联系客服反馈,我们会尽快为您处理(人工客服工作时间:9:00-18:30)。
45钢淬火后出现表面裂纹原因分析及对策
毛喆;李亚龙;刘建悟;王洲
【摘要】针对公司45钢淬火后出现表面裂纹的现象,通过金相组织和热处理后的应力分析,确定制件表面存在脱碳层是导致淬火开裂的主要原因.从产生脱碳的环节进行查找,通过热处理前机加工余量去除的控制,结合热处理加热方式和防氧化的措施,成功解决了这一问题.
【期刊名称】《热处理技术与装备》
【年(卷),期】2018(039)002
【总页数】3页(P58-60)
【关键词】表面裂纹;热处理应力;脱碳
【作者】毛喆;李亚龙;刘建悟;王洲
【作者单位】保定向阳航空精密机械有限公司热表厂,河北保定 071000;保定向阳航空精密机械有限公司热表厂,河北保定 071000;保定向阳航空精密机械有限公司热表厂,河北保定 071000;保定向阳航空机械有限公司理化计量中心,河北保定071000
【正文语种】中文
【中图分类】TG174.44
我公司的45钢制件在淬火后经常出现表面肉眼可见的裂纹,经磁粉探伤后,裂纹显现裂纹深度一度在0.5 mm左右,个别达到1 mm,超出了制件后期的加工余
量,导致制件报废。
这类问题主要出现在板材制件上,并且板材厚度在5~15
mm范围内都存在。
因此,分析裂纹产生原因及制定相应措施成为了我们思考的
问题。
1 制件加工流程简介
加工流程为:供料→正火→铣加工板材上下两面→淬火、回火→后续加工。
工序说明:1)材料为热轧退火状态;2)公司没有盐浴炉,正火和淬火均采用箱式电阻炉。
供应板材单边的余量比最终制件的尺寸大1.5 mm左右;3)正火是为了细化晶粒,防止后期淬火产生贯穿性裂纹。
同时提高制件硬度,便于铣加工;4)铣加工要求正火后板材的上下表面各去除1 mm;5)热处理淬火前,制件单面余量有0.5 mm;
6)正火和淬火温度都为840±10 ℃,保温时间也相同,正火采用空冷,淬火采用
水-油分级淬火。
2 金相组织分析
原材料投入生产前,均按GB/T 10561—2005《钢中非金属夹杂物含量的测定》
进行了夹杂物分析,均符合要求。
对淬火、回火后的板材裂纹处进行金相分析,经4%硝酸酒精腐蚀后,在200倍目镜下观察,显微组织为回火索氏体。
裂纹开裂于零件表面,零件表面铁素体基体上弥散分布的细粒状渗碳体明显少于心部组织,在显微镜下表现为颜色稍浅,其深度约为0.1 mm(如图1)。
图1 制件表层显微组织Fig.1 Surface microstructure of part
观察裂纹状况,裂纹由表面向内部扩展深度约为1 mm,裂纹开口大,内部小,
呈撕裂状,如图2。
扩展裂纹两侧无脱碳情况。
由此可见,表层脱碳层处是裂纹的起始点。
图2 裂纹的显微状况×200Fig.2 Microscopic state of crack ×200
3 开裂原因分析
热处理后制件开裂主要出现在淬火工序,造成开裂的原因是热处理淬火时产生的应
力大于材料的断裂强度,造成开裂。
热处理应力主要分组织应力和热应力两大类。
45钢热处理所产生的组织应力来源有两个方面:一方面,45钢加热时为奥氏体,淬火冷却后组织为马氏体,马氏体比奥氏体体积大,会产生体积膨胀,产生组织应力;另一方面,马氏体转变的不同时性。
在淬火冷却过程中,制件表层和心部的马氏体相变不同时进行,45钢加热到奥氏体,在冷却过程中,过冷奥氏体在Ms点
发生马氏体相变,表层先发生,此时制件心部仍为过冷奥氏体,表面为压应力,心部为拉应力。
待心部降温到Ms点以下后,发生马氏体转变,产生体积膨胀,受制件表层已转变为高强度的马氏体的阻碍,这样在制件心部产生压应力,表层产生拉应力。
热应力是由于表层和心部温差引起金属零件的体积收缩不均匀而产生的内应力。
在不考虑相变的情况下,制件表面先冷却,产生体积收缩,心部还没冷却,此时表面表现为拉应力,心部为压应力。
制件冷却后期,表面已冷却,心部要继续降温和体积收缩,而表层则阻碍心部收缩,这样心部产生拉应力,表层产生压应力。
由于制件热应力从淬火冷却开始就产生,而组织应力则是在制件冷至Ms点时发生马氏体相变后才产生。
热应力和组织应力在淬火金属截面内处于相同部位,但作用力相反,两者相互作用后,应力降低或消失。
组织应力的切向应力明显大于轴向应力,而热应力则相反,即轴向应力大于切向应力。
可见两者同时作用有致裂和抑制裂纹形成的双重性。
组织应力和热应力是在热处理淬火冷却中形成,应力的形成是产生和传递的过程,上述分析也表明在整个冷却过程中,两种应力所产生的拉应力和压应力也是不同转换的,最终所表现的应力分布只是残余应力,而导致开裂的主要因素是瞬时应力过大。
无论何种裂纹,都是在拉应力作用下产生的[1]。
而出现
开裂必定存在应力梯度,即应力集中[2]。
因此,瞬时拉应力过大,造成应力集中,超过材料自身的断裂强度σb,是裂纹的产生根本原因。
制件表面存在的脱碳层使制件表面碳浓度比心部低,在冷却转变的Ms点比正常
45钢的Ms点高,也就是说冷却时表层先发生马氏体转变,而脱碳层下还没冷却
到马氏体转变温度,此时表层受热应力所产生的拉应力,在组织应力下为压应力。
脱碳层一般较浅,在0.2 mm以内,当进一步冷却达到45钢正常Ms点温度(330 ℃)时,脱碳层下的组织发生马氏体转变,马氏体是无扩散转变,体积膨胀会形成较大的瞬时应力,对已发生转变的脱碳层表现为拉应力。
而此时制件心部还继续降温,故此时热应力仍使制件表面表现为拉应力。
由此可见,此时脱碳层所受的瞬时应力全部表现为拉应力。
同时,材料的淬硬性主要决定于自身的含碳量,制件表面碳含量低,淬火后自身的强度也比正常的45钢的低,在瞬时拉应力的作用下,出现开裂现象。
表面裂纹一般深度为0.01~1.5 mm[3],深度的深浅决定瞬时拉应力的大小,瞬时拉应力大
会使裂纹沿晶界发生撕裂,向制件内部延伸,导致裂纹深度增加。
45钢属于中碳钢,淬火时形成的马氏体比容较大,产生的应力也大,容易使表面裂纹向内部撕裂。
若在Ms点以下的冷速快,这点表现的更为明显。
4 脱碳产生的原因
1)制件本身存在脱碳层。
钢件有热轧和冷轧的,冷轧脱碳层浅,热轧则有一定深度的脱碳层,在这方面板材表现得更为明显。
2)热处理前机加未均匀去除余量。
对于热轧制件,表面有一层较厚的氧化皮,氧化皮下有一定深度的脱碳层,热处理前机加进行去除。
对于轴类制件,是回转体加工,能够保证制件整体去除均匀。
而板材制件,机加采取铣削的加工方式,需两面分别加工,有时操作者则一面见光,另一面加工到工艺规定尺寸,造成制件有一面脱碳层没能完全去除。
3)热处理加热方式。
热处理加热保温过程中也会产生氧化、脱碳现象。
由于公司热处理淬火时,使用箱式电阻炉。
加热时45钢表层的铁与空气中的氧发生反应生成氧化膜。
氧化膜由Fe2O3、Fe3O4、FeO三种组成。
随着加热温度的升高,不仅
氧化程度增加,而且氧化膜厚度也增加,达到一定厚度就形成氧化皮,它与钢的膨胀系数不同,会使氧化皮产生机械剥离,进一步加速钢件的氧化。
高温下,溶解在奥氏体中的碳和碳化物中的化合碳被空气中的氧烧损,造成脱碳。
反应方程式如下:
C(γ-Fe)+O2=CO2
(1)
Fe3C+O2=3Fe+CO2
(2)
45钢是在600 ℃以上氧化比较明显,在氧化的过程中也伴随着脱碳,在加热到800 ℃以上时,制件的脱碳现象更为明显。
氧化脱碳的现象不仅跟温度有关,和加热时间也有很大关系,温度高、时间长都会使氧化脱碳加剧。
5 解决措施
1)热处理前均匀去除余量。
对于板材制件,尤其是热轧板材,应保证热处理前脱碳层去除彻底。
一方面要在选材时在厚度上应考虑脱碳层厚度,另一方面,机加工艺应明确对板材制件均匀去除余量,并结合检验控制保证。
2)加热。
工艺规程只标明了45钢淬火加热温度和保温时间,对加热方式并没有进行严格规定。
HB/Z136—2000《航空结构钢热处理工艺》中“6.4.2热处理时,制件一般是到温后装炉”。
在日常生产中,操作者有时是到温装炉,有时是随炉升温。
为防止在加热升温过程中的氧化脱碳,采取到温装炉的方式。
即将电阻炉升温至840 ℃后,打开炉门装入制件,等炉温回升至840 ℃后再开始计算保温时间。
3)防氧化。
为减少45钢制件在淬火保温过程中的氧化脱碳,在装入制件的同时,放入一定量的木炭。
木炭和电阻炉中的空气进行反应,生成还原性气氛CO。
CO 可进一步与氧气反应,消耗空气中的氧气,可减少45钢制件的氧化脱碳。
6 结论
通过上述前期加工均匀去除余量,结合对加热方式的明确和采用加热过程用木炭防氧化保护措施,在后续生产中,45钢淬火后没有再出现表面裂纹的现象。
参考文献
[1] 钢的热处理裂纹和变形编写组. 钢的热处理裂纹和变形[M].北京:机械工业出版社,1978:56
[2] 陈锐,罗新民. 钢件的热处理淬火变形与控制[J].热处理技术与装备,2006,27(1):18-22.
[3] 钟群鹏,周煜,张峥. 裂纹学[M].北京:高等教育出版社,2014:271。