轮胎各部件结构设计
轮胎各部件结构设计课件

学习交流PPT
1
2、外胎技术设计
1) 、外胎断面轮廓曲线的设计; 2) 、 胎面花纹形状的设计;
3) 、外胎材料分布图的绘制.
学习交流PPT
2
L h
b b'
外 胎
技 术 设 计
D
d
H
H1
Hr
R1
B R2
R3 R4
R5
W
学习交流PPT C
Rn
R
3
1、外胎断面轮廓曲线的设计
⑴着合宽度C的确定:
R2=〔1/4×(326-252-2×24.5)2 +(150.5-46)2〕/(326-2522×24.5) =443.06mm.
取R2=353mm.
学习交流PPT
D
d
H
H1
B R2
3.3 C
15
⑿下胎侧弧度半径R3 的确定:
根据R2和轮辋曲线, 结合其它方法途径搜集 的数据,综合权衡确定 R3的数据。 以12.00R20 S811 18P.R 为例 取R3=90mm.
R3
取R4=21.5mm(轮辋23mm).
180mm. b'
R
H L h
Rn
R1
学习交流PPT
14
⑾下胎侧圆弧半径R2的确定:
R2=〔1/4×(B-C-2a)2
+(H1-Hc)2〕/(B-C-2a)
式中a为轮辋曲线宽的2/3.Hc为 轮辋曲线高.
一般情况下,R2 弧的延长线与 着合位置线的交点距离着合宽 度端点大约0~5mm.
以12.00R20 S811 18P.R为例
3.2
2
5°
Φ508
8.50"X20"Ⅰ型平底轮辋
工程机械轮胎的冠带层结构设计

钢 丝补强 的轮胎胎 面更 容 易产 生崩 花和 掉块 。
为 1%, 0 收缩 率 为 1 以下 。 O 在 图 示 的 实 施 例 中 , 用 了 韧 性 为 3c 采 7 N/
面和 或/ 胎侧 的抗 切 割层 。 经 验证 明采用 钢 丝补 强 的工 程 机 械轮 胎 的 耐
本发 明 提供 的抗 崩花掉 块 性 能好 的工程 机 械 轮胎具 有 胎 圈 、 卷 胎 圈 的胎 体 帘 布层 、 置 于轮 包 配 胎 冠 部 的胎 体 帘 布层 上 方 的胎 面 、 置 于 胎 面 与 配
或有机 纤维 编 织 成 的钢 丝 / 机 纤 维 复 合 结 构 作 有
为 轮胎 补强 织 物 ; 国第 1 2 6 0号 专利 提 出 将 美 28 5
强层 使用 , 这种 橡胶 具有 更 大 的弹性 。 则
美 国第 5 4 9 5号 专 利 提 出 , 尼 龙 单 丝 作 73 7 用 为 中型载 重子 午线 轮胎 的最 外 层 带束 层 帘 线 可 以 最大 限度 地 提 高 胎 面 耐 切 割性 , 提 高 中 型载 重 可
1 以下。 O
关 键 词 : 程 机 械 轮 胎 ; 带 层 ; 带 层挂 胶 ; 花 掉 块性 能 工 冠 冠 抗
1 背 景 技 术
补 强材 料 间 的 隔离 层 , 可 以通 过 将 作 用 于胎 面 则 的力 更均 匀 地 向轮胎更 宽 的部 分 分 散 而起 到 防止 崩花 掉块 的 作用 。如果 向 橡 胶 追 加 补 强 材 料 , 则 可 以进 一步 提 高分散 这种 力 的能力 。 如果 用 低硫 橡胶 与尼龙 补 强 材 料组 合 作 为补
轮胎设计与工艺学 10 第三章 普通轮胎结构设计

成型机头宽度计算
1.主要技术参数的确定
2.成型机头宽度Bs的计算
1.主要技术参数的确定 主要技术参数的确定 (1)第一帘布筒直径d0 (2)帘线的假定伸张值δ1 (3)胎冠角度βk (4)成型机头的帘线角度αc 计算
(1)第一帘布筒直径d0 一般半芯轮式成型机头常用套筒法成 型,帘布提前制成帘布筒备用,第一帘布 筒直径小于成型机头直径,便于操作,第一 帘布筒至机头直径的伸张为5~15%,即 Dc/d0=1.05~1.15。
第四节、成型机头宽度计算
成型机头宽度:BS是指机头两端最宽点间的距离,即等 于机头中部平筒宽度加上两端机头肩部宽度。 机头宽度合理的确定,能使胎体帘线均匀伸张, 充分发挥帘线的作用,保证轮胎质量。 计算成型机头所需用的主要参数:为第一帘布筒 直径d0,帘线的假定伸张值δ1,胎冠角度βk和机头 上的帘线角度αc等。
DC
式中
DK
Dc—成型机头直径,mm; Dk—胎里直径,mm; δ—成型胎坯冠部伸张值。
通常半鼓式成型机头的δ值取1.30~1.65;半芯轮式成型机头 的δ值取1.30~1.55。
成型机头直径越小,越能保证外胎的成型质量,提高生产 效率,但是,成型机头过小,胎冠部伸张值增大,则导致胎体 强度降低。
半芯轮式的δ在1.3~1.5。
断面大而胎圈直径小的轮胎,成型机头 直径与其胎圈直径比值Dc /d超过1.5时,成型 后机头自动折叠也难以将胎圈卸下,此时, 只能采用卸除鼓肩后再折叠的卸胎方法。 因此,确定成型机头直径,应在不影响 胎体强度和便利操作的前提下,Dc尽可能取 小值。 各种规格成型机头直径见表2-13所列。
Ⅰ线相切,交于IV-Ⅳ线上,R1圆心位臵至
Ⅲ-Ⅲ线的距离为机头肩部宽度C。
第四章子午线轮胎结构设计
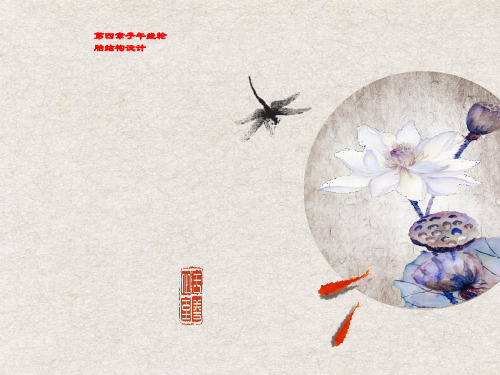
二、子午线轮胎与斜交轮胎结构特征比较。
(1)斜交轮胎胎体中的帘线按一定角度排列,各层 间帘线相互交叉,胎体帘线层数为偶数,胎体承 受内压引起的初始应力的80~90%。
(2)子午线轮胎胎体各帘面层间的帘线,系相互平 行地由一胎圈至另一胎圈呈了午线方向的排列 (与胎胎冠中心线夹角为90度)。胎冠有大角度 基本不伸张的刚性带束层箍紧,这种结构使:
W 双 =0.88×9.485=8.437KN
三、 轮廓设计主要结构参数的选取
1、模型外直径D和断面宽B的确定
到目前为止,还没有科学的方法来确定轮胎 硫化模型尺寸与充气压后轮胎尺寸之间的关系, 因此子午胎的设计也只能根据经验考虑不同的胎 体帘线的伸长性能、轮胎断面轮廓形状、带束层 角度和长度等的影响来选择充气轮胎与硫化模型 之间断面宽和外直径的膨胀比。下表列出载重和 轻卡子午线轮胎充气断面宽(B΄)和模型断面宽(B) 对不同胎体帘线的断面膨胀比的取值范围。
轿车子午线轮胎,高宽比为0.7~0.8时 (人造丝胎体钢丝带束层结构)充气后外径一 般膨胀0~2mm,断面宽膨胀0~2%。根据经 验,子午线轮胎D′/D值大约在1.000~1.003 之间,B′/B值为1.00~1.02左右。
几种轿车子午线轮胎断面膨胀率如表4-1 所示。
表4-1 几种轿车子午胎断面膨胀率
SS1180 0s1i4 n .13(W 11/S1)
Sd S0.63d7
d0.9 6S0.7H
S0.7S118 O 0 1 si3 .6 1 n (W 51/S1)
先计算 S 0 .7
S 0 .7 1.5 8 1 8 s1 0 i1 ( .n 1 3 6 .0 4 5 /1.5 ) 8 1.8 7 (c 5)m
钢丝帘线主要用于子午线轮胎的胎体及 带束层,其主要特点是耐热性极好,强度 高,同时伸长率极小,对保持轮胎尺寸稳 定性极为有利。
子午线轮胎结构设计与制造技术

子午线轮胎结构设计与制造技术
子午线轮胎是一种高性能轮胎,由于其特殊的结构设计和制造技术而得到广泛应用。
其主要特点是采用平行于中心线的钢丝束作为骨架材料,能够提供优秀的耐磨性和抗拉强度,使轮胎能承受高强度、高速度和长时间运行的要求。
子午线轮胎的结构设计和制造技术包括以下几个方面:
1.骨架结构设计:子午线轮胎采用钢丝束作为骨架材料,一般包含两到三层。
骨架材料的种类、材质和层数均影响了轮胎的性能。
通过优化骨架结构设计,可以提高轮胎的抗拉强度和耐磨性。
2.胎面花纹设计:胎面花纹是轮胎与路面之间的唯一接触面。
子午线轮胎的花纹设计对于轮胎的性能有着重要的影响。
通过优化花纹设计,可以提高轮胎的防滑性和抓地力。
3.胎侧加强结构设计:轮胎的胎侧加强结构对于轮胎的耐磨性和抗撞击性具有重要意义。
子午线轮胎一般采用加强胎侧结构,以提高轮胎耐用性和安全性。
4.制造工艺技术:子午线轮胎的制造工艺技术包括轮胎胎体的成型、钢丝束的辊压、轮胎胎面花纹切割、轮胎成型和贴合等工序。
制造工艺技术的精度和质量直接影响轮胎的性能。
综上所述,子午线轮胎的结构设计和制造技术是决定轮胎性能和品质的重要因素。
如今,随着科技的不断发展和制造工艺的不断升级,子午线轮胎的性能和质量有了大幅提升。
轮胎设计与工艺学 9 第三章 普通轮胎结构设计
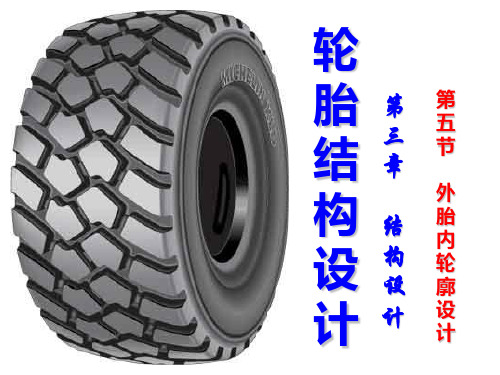
★
2.旦(Denier)-定长制 单位长度(9000米)的纤维或纱线所具有的重量 (以克计)称“旦”。(即纤维的相对密度为一定时 旦数越大,则纤维越粗)
G 9000 D L / 9000 Nm
式中:D—旦数; G—纤维或纱线的重量,g; L—纤维或纱线的长度,m
★
3.特(tex)或分特(dtex)-定长制
安全倍数为:
S 22 k 11.1 N 1.969
计算结果符合要求。
② 挂胶帘布厚度
作用:帘布层和缓冲层均由数层挂胶帘布组成, 挂胶帘布层上覆上一定厚度的胶层,使布层 间与帘线间增加粘合力,提高帘线的疲劳强 度和弹性。
厚度:依据胶层帘线种类、帘线粗度、轮胎类型和规格、胶料
性能及工艺条件等因素确定,帘布层之间胶层厚度不宜过厚
30 cos 30 6.0 5.16(根 / cm) 47.9 cos 50.92
ik 3
将93Odtex/2的帘线密度换算为相当于1400dtex/2规格
的帘线密度,再进行帘线密度总和的计算。
因93Odtex/2的S=14.5N/根,5.16根/cm(93Odtex/2)相
当于5.16×14.5/22=3.4根/cm(1400dtex/丝帘线
1938年美国轮胎工业开始采用人造丝代替棉帘 线,大大提高了轮胎的质量 40、50年代的小轿车和卡车的轮胎大多采用人 造丝帘线为骨架材料 到六十年代初当时的联邦德国使用人造丝的比 例高达93%,而且整个欧洲都广泛应用。
采用人造丝帘线的特点:
人造丝的高温强力降低少,在120℃时强力仅
单位长度(1000米)的纤维或纱线所具有的重量(以 克计)称“特”。若重量以分克计(1/10g),则称“分 特”。
轮辋设计
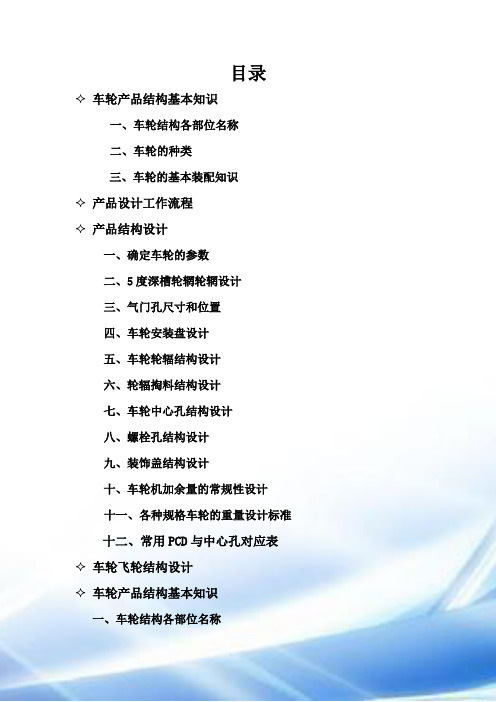
目录✧车轮产品结构基本知识一、车轮结构各部位名称二、车轮的种类三、车轮的基本装配知识✧产品设计工作流程✧产品结构设计一、确定车轮的参数二、5度深槽轮辋轮辋设计三、气门孔尺寸和位置四、车轮安装盘设计五、车轮轮辐结构设计六、轮辐掏料结构设计七、车轮中心孔结构设计八、螺栓孔结构设计九、装饰盖结构设计十、车轮机加余量的常规性设计十一、各种规格车轮的重量设计标准十二、常用PCD与中心孔对应表✧车轮飞轮结构设计✧车轮产品结构基本知识一、车轮结构各部位名称1、轮辋:与轮胎装配配合,支撑轮胎的车轮部分。
2、轮辐:与车轴轮毂实施安装连接,支撑轮辋的车轮部分。
3、偏距:轮辋中心面到轮辐安装面间的距离。
有正偏距、零偏距、负偏距之分。
4、轮缘:保持并支撑轮胎方向的轮辋部分。
5、胎圈座:与轮胎圈接触,支撑维持轮胎半径方向的轮辋部分。
6、槽底:为方便轮胎装拆,在轮辋上留有一定深度和宽度的凹坑。
7、气门孔:安装轮胎气门嘴的孔。
1 轮辋宽度10 螺栓孔节圆直径2 轮辋名义直径11 螺栓孔直径3 轮缘12 轮辐安装面4 胎圈座13 安装面直径5 凸峰14 后距6 槽底15 轮辐7 气门孔16 轮辋8 偏距17 轮辋中心线9 中心孔18二、车轮的种类按轮辋和轮辐结合形式的不同,车轮可分为如下结构,其代表型结构用图例来表示:1、整体式:轮辐和轮辋是由一个整体组成的。
2、组合式:由2个以上的零件组合而成的车轮,其组成的零件可以分开,按其组合形式可分为三类:(1)、两片式车轮:由轮辋和轮辐结合起来的结构;(2)、三片式车轮:由两个轮辋零件和一个轮辐结合起来的结构。
(3)、辐条式车轮:轮辋与中央轮盘部件,通过很多辐条实现连结的车轮结构。
三、车轮的基本装配知识车轮的有关装配主要有以下的几种装配情况:1 车轮轮辋与轮胎之间的装配2 车轮与装饰钉之间的装配3 车轮与刹车钳之间的装配4 车轮安装面与车轴之间的装配5 车轮螺栓孔与螺母之间的装配6 车轮螺栓孔与车轴之间的装配7 车轮与装饰盖之间的装配8 车轮中心孔与车轴之间的装配9 车轮气门孔与气门嘴之间的装配10 车轮与平衡块之间的装配✧产品设计工作流程✧产品结构设计车轮的结构设计的基本步骤:(1)、根据车轮的装车情况对设计的车轮进行归类,并初定出车轮的各种装配参数。
车轮机构设计中的结构优化与分析

车轮机构设计中的结构优化与分析近年来,汽车行业的不断发展让我们深刻认识到了车辆性能的重要性。
其中,车轮机构设计作为汽车行业中至关重要的一环,直接影响着汽车的性能表现。
在车轮机构设计中,结构优化与分析一直是研究者们关注的热点问题。
本文旨在介绍车轮机构设计中的结构优化与分析。
一、车轮机构结构分析车轮机构是汽车行业的核心部件之一,其结构复杂,如何进行合理分析是关乎车辆性能的重要问题。
车轮机构主要是由轮毂、轮辋、轮胎、制动器和悬挂系统组成。
因此,车轮机构的结构分析是从轮毂、轮辋、轮胎、制动器及悬挂系统等方面来进行的。
1、轮毂结构分析轮毂是汽车车轮机构中最重要的组成部分之一,其结构对整个车轮的性能影响十分重要。
轮毂通常由轮毂盘和轮毂孔组成,其中轮毂盘是直接与轮胎接触的部分。
轮毂盘的材料、结构和表面处理技术可直接影响轮毂的质量和车轮的性能。
2、轮辋结构分析轮辋是连接车轮主体和车辆悬挂系统的重要结构部件。
轮辋分为外辋和内辋,其主要的设计考虑点有轮辋的尺寸、形状、材料等。
不同的材料与工艺对轮辋的性能和强度产生直接影响。
3、轮胎结构分析轮胎是车轮机构中与地面直接接触的部分,它的质量和性能对整个车轮的安全性、舒适性以及经济性都具有重要影响。
轮胎的材料种类、花纹结构、压力等因素均会影响其性能。
制动器是车轮机构的重要部分之一,它决定了制动舒适性、制动效果以及制动稳定性等因素。
轮毂面的轮盘制动以及轮毂内的制动器均会影响到整个汽车的行驶性能。
因此,制动器在车轮机构的结构设计中要得到合理的考虑。
5、悬挂系统结构分析悬挂系统是车轮机构中最重要的组成部分之一,其重要性在于它决定了车轮的行驶稳定性、悬挂舒适性以及车辆的安全性能等方面。
悬挂系统的结构设计要考虑多种因素,如悬挂形式、弹簧刚度、悬架几何参数等。
二、车轮机构结构优化在进行车轮机构结构优化的过程中,需要考虑车轮的安全性、可靠性、经济性和舒适性等多方面因素。
以下是常见的结构优化手段:1、轮毂结构优化轮毂的材料与表面处理技术对车轮性能影响非常大。
- 1、下载文档前请自行甄别文档内容的完整性,平台不提供额外的编辑、内容补充、找答案等附加服务。
- 2、"仅部分预览"的文档,不可在线预览部分如存在完整性等问题,可反馈申请退款(可完整预览的文档不适用该条件!)。
- 3、如文档侵犯您的权益,请联系客服反馈,我们会尽快为您处理(人工客服工作时间:9:00-18:30)。
b'
的数据,综合权衡确定
R
R1的数据为165mm.
H L h
Rn
R1
a
13
⑽肩下反弧R的确定 对于全钢载重子午胎,肩下一般不采用切线,而采 用一反弧,反弧R过肩部端点和R1相切,一般b较 大,R较小, b较小,R较大。
以12.00R20 S811 18P.R为例 结合其它方法途径搜集的数据,综合权衡确定R为
DJ DF
DC
a
25
以12.00R20 S811 18P.R为例 冠部总厚=16.5+5.5+7.5+2+2.5=34mm
2.5 7.5 16.5 2 5.522 34
a
26
肩部总厚DJ的确定,一般DJ/DT ≤1.25
DI DT
DJ DF
B4 B1 B3
B2
DC
a
27
以12.00R20 S811 18P.R为例 肩部总厚=42mm,42/34=1.2353
HS HF HB1 Ф HZ HB2
DN DW
DL
a
W
34
以12.00R20 S811 18P.R为例 胎体反包点高度
=65mm 子口包布外端点高度
=50mm 胎体反包点到下胎侧 轮廓线的距离=10mm 胎体反包点到胎体帘 线的距离=13mm 填充胶的高度=140mm 140/150.5=0.9302
条形花纹 以条形为主 以横沟为主 越野花纹 混合花纹 混合花a 纹
M+S花纹
19
⑵花纹形状及尺寸的确定: 根据已确定的花纹类型,来确定其形状及尺寸。 花纹沟走向与带束层钢丝走向至少差5°. 以12.00R20 S811 18P.R为例 轮胎主要用于较好或一般路面
a
20
⑶花纹沟深度的确定:
根据新设计轮胎的使用条件,花纹类型,参照国内 外情况和全面权衡综合性能,来确定花纹沟深度。
180mm.
b'
R
H L h
Rn
R1
a
14
⑾下胎侧圆弧半径R2的确定:
R2=〔1/4×(B-C-2a)2
+(H1-Hc)2〕/(B-C-2a)
式中a为轮辋曲线宽的2/3.Hc为 轮辋曲线高.
一般情况下,R2 弧的延长线与 着合位置线的交点距离着合宽 度端点大约0~5mm.
以12.00R20 S811 18P.R为例
DN
子口宽度W根据做图和
DW
材料分布确定.
DL
HS HF HB1 Ф HZ HB2
a
W
36
以12.00R20 S811 18P.R为例
子口包布内端点高度
=40mm,轮辋高度=46/44.5mm
子口耐磨胶内端点高度
=30mm 钢丝圈内径
=511+(2+1.5+4.25) ×2=526.5mm
Ф526.5 30 40
条形花纹花纹深度较浅,混合花纹花纹深度较深, 越野花纹一般是加深型,M+S花纹超加深型。花纹 沟倾斜角度尽可能大些10~15°。
以12.00R20 S811 18P.R为例 花纹深度确定为 16.5mm.
15°
15°
16.5
a
全圆弧
21
⑷花纹沟占地面积的计算: 不同的花纹类型,花纹沟占地面积是不同的, 条形花纹一般19~25%, 混合花纹一般24~35%, 越野花纹和M+S花纹30%以上 以12.00R20 S811 18P.R为例 经计算花纹沟占地面积为29%
R3
取R4=21.5mm(轮辋23mm). 取R5=9mm(轮辋≤8mm).
R4
取Hr=21.5mm(轮辋23mm).
β
β =2.5° (轮辋5 °).
W =35mm.
a
W 17
⒁经实际绘图,确定12.00R20 S811 18P.R 轮胎断面轮廓图如下:
226 120.2803
R180
86.5 7.7
a
22
DI DT
DJ DF
3、外胎材料分布图 的绘制
DC
B4 B1 B3
B2
HS HF HB1 Ф HZ HB2
DN DW
DL
a
W
23
DI DT
⑴ 绘制材料分布图前,对胎体、带束层和胎圈所承受 的力进行计算,来确定胎体、带束层和胎圈采用何种 钢丝材料;
⑵ 平衡轴上边几个主要尺寸的确定:
冠部总厚
DJ DF
子口轮辋点处厚度
32
=32mm
子口宽度=35mm
35
a
37
以12.00R20 S811 18P.R为例,材料分布尺寸确 定如图:
22 34
16.5
7.5 42
21
B’= 315±3.5%mm,考虑充气膨胀比率,取
B=312+14.44=326.44mm≈326mm
a
5
⑶外直径D的确定:
根据整体设计的需要,一般B取值较小,D 就要取值较大。结合其它方法途径搜集的 数据,综合权衡确定D的数据。
以12.00R20 S811 18P.R为例
D’= 1125±1%mm,考虑充气膨胀比 率, 取 D=1121mm
a
6
⑷着合直径d的确定: 根据轮胎装配的轮辋尺寸来确定着合直径 d 以12.00R20 S811 18P.R为例,d=511mm
R≥2.5 R≥1
46 Φ513.46
R≤8
≥24.5 ≤2°
R23
216(8.5") (36)
3.2
8.50"X20"Ⅰ型平底轮辋
a
44.5
Φ508
≥27 ≤2°
14 R27
216(8.5") 32
R≤8
2 5°
8.50V"X20"Ⅱ型平底轮辋
7
H1' (110.24) H' (234.02)
⑸断面水平轴位置 的确定:
断面高H=1/2(D -d)
H1由轮辋点到平 衡轴距离H1’和由 轮辋点到胎体冠 中心点距离H’的比 值来确定,一般 H1’/H’=0.3~0.5
a
8
以12.00R20 S811 18P.R为例
Ca
4
⑵断面宽B的确定:
根据一般规律,英制系列轮胎,轮辋每增大0.5 ”,断面 宽增大0.2 ” ,公制系列轮胎,轮辋每增大0.5 “ ,断 面宽增大5mm。结合其它方法途径搜集的数据,综 合权衡确定B的数据。
以12.00R20 S811 18P.R为例
断面宽B增加宽度应为 (9.9213−8.50)/0.5×0.2=0.5685“=14.44mm
22 34
16.5
42
2.5
a
28
带束层宽度的确定,一般2#带束层宽B2/行驶面宽
b≥ 0.8,根据实际需要来确定,如果对带束层强度要 求较高,就可以取宽些,但端点离肩下胶面要 ≥10mm,B1、B3与B2相临端点的差级≥10mm, B4最窄,端点尽量避开花纹沟底;
DI DT
DJ DF
B4 B1 B3
块分型处厚度;
B4 B1 B3 B2
DI DT
DJ DF
DC
a
31
7.5 42
21
以12.00R20 S811 18P.R为例 胎侧总厚度 =5+2+2.5 =9.5mm; 侧板和活络块 分型处厚度 =21mm.
9.5 5
a
32
⑶平衡轴下边几个主要尺寸的确定:
胎体反包点高度HF,参考轮辋高度和实际使用情况 来确定,一般到第三条防水线的高度;子口包布外 端点高度HB1,
R2=〔1/4×(326-252-2×24.5)2 +(150.5-46)2〕/(326-2522×24.5) =443.06mm.
取R2=353mm.
a
D
d
H
H1
R2
3.3
15
⑿下胎侧弧度半径R3 的确定:
根据R2和轮辋曲线, 结合其它方法途径搜 集的数据,综合权衡 确定R3的数据。
H
以12.00R20 S811 18P.R为例
h=7.7mm
b
h
a
10
Hale Waihona Puke ⑺胎冠弧度半径Rn的确定:一般情况下,胎冠弧度半径Rn=1.75~2B,具体数 值根据需要来确定,b值较小、h值较小,Rn值较 大, b值较大、h值较大,Rn值较小;对于较小规 格轮胎,胎冠一般采用一段弧设计,对于较大规格, 胎冠一般采用中间一段弧、两端为切线设计。
以12.00R20 S811 18P.R为例
DT=花纹沟深度+
基部胶厚度+ 四层带束层厚度+
胎体厚度+ 内衬层厚度DI
B4 B1 B3
B2
DC
a
24
基部胶厚度根据花纹深度和实际使用情况来确定,
一般≤5.5mm;带束层和胎体厚度根据所用材料
和半成品压延厚度
来确定;内衬层厚度
DI ≥2.5mm,气密
层厚度≥ 1.2mm;
B4 B1 B3 B2
DI DT
与HF至少保证
10mm的差级;
胎体反包点到下
胎侧轮廓线的距
离DW,根据不
DN
同的规格和胎体 反包点的走式,
DW DL
一般6~12mm;
HS HF HB1 Ф HZ HB2
a
W
33
胎体反包点到胎体帘线的距离DN,根据不同的规格 和胎体的走式(下胎侧胎体帘线一般较直),一般 8~14mm;填充胶的高度HS,一般参考平衡轴的高 度H1和实际应用来确定,HS/H1=0.85~1;