主轴驱动系统和主轴电机发展趋势
数控系统发展趋势
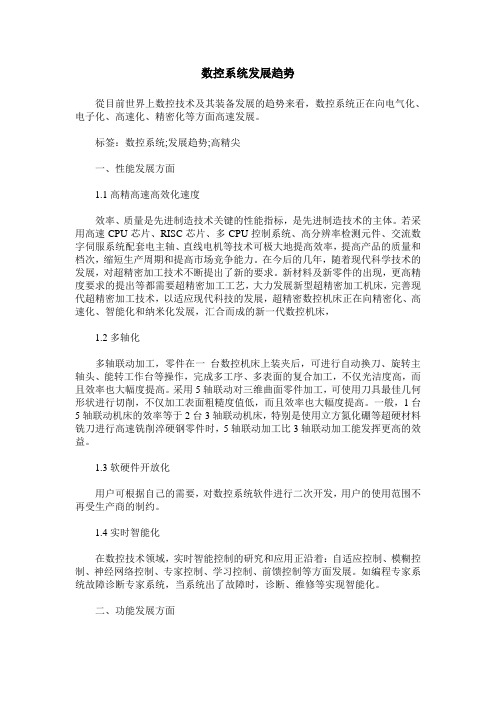
数控系统发展趋势從目前世界上数控技术及其装备发展的趋势来看,数控系统正在向电气化、电子化、高速化、精密化等方面高速发展。
标签:数控系统;发展趋势;高精尖一、性能发展方面1.1高精高速高效化速度效率、质量是先进制造技术关键的性能指标,是先进制造技术的主体。
若采用高速CPU芯片、RISC芯片、多CPU控制系统、高分辨率检测元件、交流数字伺服系统配套电主轴、直线电机等技术可极大地提高效率,提高产品的质量和档次,缩短生产周期和提高市场竞争能力。
在今后的几年,随着现代科学技术的发展,对超精密加工技术不断提出了新的要求。
新材料及新零件的出现,更高精度要求的提出等都需要超精密加工工艺,大力发展新型超精密加工机床,完善现代超精密加工技术,以适应现代科技的发展,超精密数控机床正在向精密化、高速化、智能化和纳米化发展,汇合而成的新一代数控机床,1.2多轴化多轴联动加工,零件在一台数控机床上装夹后,可进行自动换刀、旋转主轴头、能转工作台等操作,完成多工序、多表面的复合加工,不仅光洁度高,而且效率也大幅度提高。
采用5轴联动对三维曲面零件加工,可使用刀具最佳几何形状进行切削,不仅加工表面粗糙度值低,而且效率也大幅度提高。
一般,1台5轴联动机床的效率等于2台3轴联动机床,特别是使用立方氮化硼等超硬材料铣刀进行高速铣削淬硬钢零件时,5轴联动加工比3轴联动加工能发挥更高的效益。
1.3软硬件开放化用户可根据自己的需要,对数控系统软件进行二次开发,用户的使用范围不再受生产商的制约。
1.4实时智能化在数控技术领域,实时智能控制的研究和应用正沿着:自适应控制、模糊控制、神经网络控制、专家控制、学习控制、前馈控制等方面发展。
如编程专家系统故障诊断专家系统,当系统出了故障时,诊断、维修等实现智能化。
二、功能发展方面2.1图形化界面功能和水平进一步提高高档数控系统发展对图形化界面的功能和水平要求进一步提高,用户希望看到更丰富、更形象、更直观的界面,以此减少用户编程难度,提高编程和加工效率。
什么是电主轴?电主轴和机械主轴优缺点对比
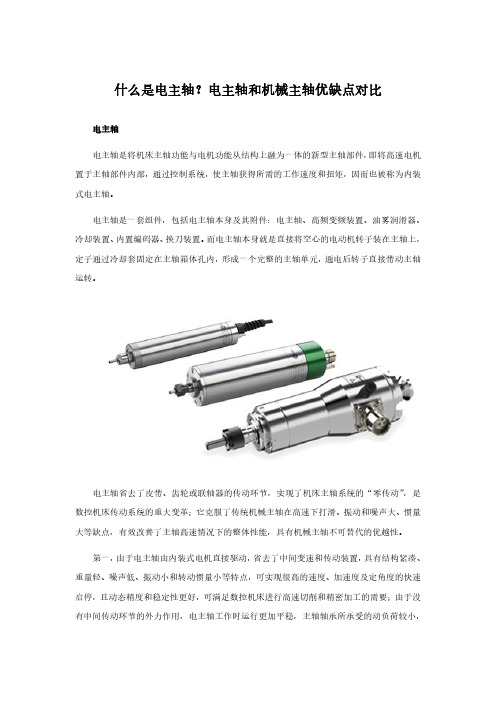
什么是电主轴?电主轴和机械主轴优缺点对比电主轴电主轴是将机床主轴功能与电机功能从结构上融为一体的新型主轴部件,即将高速电机置于主轴部件内部,通过控制系统,使主轴获得所需的工作速度和扭矩,因而也被称为内装式电主轴。
电主轴是一套组件,包括电主轴本身及其附件:电主轴、高频变频装置、油雾润滑器、冷却装置、内置编码器、换刀装置。
而电主轴本身就是直接将空心的电动机转子装在主轴上,定子通过冷却套固定在主轴箱体孔内,形成一个完整的主轴单元,通电后转子直接带动主轴运转。
电主轴省去了皮带、齿轮或联轴器的传动环节,实现了机床主轴系统的“零传动”,是数控机床传动系统的重大变革;它克服了传统机械主轴在高速下打滑、振动和噪声大、惯量大等缺点,有效改善了主轴高速情况下的整体性能,具有机械主轴不可替代的优越性。
第一,由于电主轴由内装式电机直接驱动,省去了中间变速和传动装置,具有结构紧凑、重量轻、噪声低、振动小和转动惯量小等特点,可实现很高的速度、加速度及定角度的快速启停,且动态精度和稳定性更好,可满足数控机床进行高速切削和精密加工的需要;由于没有中间传动环节的外力作用,电主轴工作时运行更加平稳,主轴轴承所承受的动负荷较小,延长了其精度寿命;利用交流变频和矢量控制技术,电主轴可在额定转速范围内实现无极变速,以适应机床工作时各种工况和负载变化的需要。
第二,电主轴的电机内藏式结构使其从机床的传动系统和整体结构中相对独立出来,形成一个功能相对完整的“主轴单元”,从而促进了机床结构的模块化。
电主轴厂商根据机床的用途、结构、性能参数等特征形成标准化、系列化的产品,供机床制造商选用,改变了传统机床厂商“大而全”的生产模式,缩短了机床的研发和生产周期,更加适应快速多变的市场环境。
此外,标准化、系列化的电主轴产品易于形成专业化、规模化的生产能力,从而促进制造成本的降低。
第三,某些高档数控机床,如并联运动机床、五面体加工中心、小孔和微孔加工机床等,由于加工工艺和加工对象的特殊性,其对主轴的转速、精度以及机床的结构都有特殊要求。
电主轴

• •
• • •
5、我国数控机床用电主轴技术与国 际先进国家之间的差距
• • • • • (1)在电主轴的低速大扭矩方面,国外产品低速段的输出扭矩最大可以达到300Nm以 上,而我国目前紧限于100Nm以内。 (2)在高速方面,国外用于加工中心等数控机床用主轴的转速已经达到了75000r/min, 而我国则多在15000r/min以下。 (3)在电主轴的轴承润滑方面,国外已普遍采用油气润滑方法,而我国现在仍然普遍 采用油脂润滑。 (4)在其它与电主轴相关的配套技术方面,如主轴电机矢量控制和交流伺服控制技术、 精确定向(准停)技术、快速起动与停止技术、HSC刀柄制造与应用技术等,仍然不 够成熟,或不能满足实际需要。 (5)在产品品种、数量及制造规模方面,尽管已经有洛阳轴承研究所等数家专业研究、 制造电主轴的企业,但仍然以磨用电主轴为主,在数控机床用电主轴发面,则处于小 量开发试制阶段,还没有形成系列化、专业化和规模化生产,远远不能满足国内市场 日益增长的需要,还不具备与国外产品相抗衡的能力。 数控机床用高速精密电主轴是高速数控设备的首选功能部件,但目前仍处于研制与推 广应用阶段,成为影响数控机床向高性能、高水平、高速度、高精度方向发展的主要 制约因素,需要有关方面的共同努力及国家相关产业政策的有力支持,只有在各功能 部件高水平发展的基础上,我国数控机床的整体水平才能得以提高,才能在加入WTO 之后,我国的机床行业具备与国外相抗衡的能力。
•
2、电主轴的优点
• 传统机床主轴是由电机通过中间的传动、变速装置(如皮带、齿轮、 联轴节等)带动主轴旋转而进行工作的,这样的主轴称为分离式主轴, 与此相比,电主轴具有如下优点: • 1)主轴由内装式电机直接驱动,省去了皮带、齿轮、联轴节等中间 传动、变速机构或连接零件,具利用交流变频技术,电主轴可以在额定转速范围内实现无级变速, 以适应机床各种工况和负载变化的需要。 • 3)利用电机矢量控制、伺服控制等技术,不仅可以满足机床强力切 削时低速大扭矩的要求,还可以实现准确的C轴定位及传动的功能, 适应对C轴功能有较高要求的车削、镗铣等加工中心及其它数控机床 的需要。 • 4)与其它形式的主轴相比,电主轴更易于实现高速化,其动态精度 和动态稳定性更好。 • 5)由于没有中间传动环节的外力作用,主轴运行更加平衡,没有冲 击,使得主轴轴承的寿命相应得到了延长。
论文:数控机床的发展趋势及国内发展现状

数控机床的发展趋势及国内发展现状摘要:本文简要分析了数控机床高速化、高精度化、复合化、智能化、开放化、网络化、多轴化、绿色化等发展趋势,并提出了我国数控机床发展中存在的一些问题。
关键词:数控机床趋势问题1.引言从20世纪中叶数控技术出现以来,数控机床给机械制造业带来了革命性的变化。
数控加工具有如下特点:加工柔性好,加工精度高,生产率高,减轻操作者劳动强度、改善劳动条件,有利于生产管理的现代化以及经济效益的提高。
数控机床是一种高度机电一体化的产品,适用于加工多品种小批量零件、结构较复杂、精度要求较高的零件、需要频繁改型的零件、价格昂贵不允许报废的关键零件、要求精密复制的零件、需要缩短生产周期的急需零件以及要求100%检验的零件。
数控机床的特点及其应用范围使其成为国民经济和国防建设发展的重要装备。
进入21世纪,我国经济与国际全面接轨,进入了一个蓬勃发展的新时期。
机床制造业既面临着机械制造业需求水平提升而引发的制造装备发展的良机,也遭遇到加入世界贸易组织后激烈的国际市场竞争的压力,加速推进数控机床的发展是解决机床制造业持续发展的一个关键。
随着制造业对数控机床的大量需求以及计算机技术和现代设计技术的飞速进步,数控机床的应用范围还在不断扩大,并且不断发展以更适应生产加工的需要。
本文简要分析了数控机床高速化、高精度化、复合化、智能化、开放化、网络化、多轴化、绿色化等发展趋势,并提出了我国数控机床发展中存在的一些问题。
2.数控机床的发展趋势2.1 高速化随着汽车、国防、航空、航天等工业的高速发展以及铝合金等新材料的应用,对数控机床加工的高速化要求越来越高。
(1)主轴转速:机床采用电主轴(内装式主轴电机),主轴最高转速达200000r/min;(2)进给率:在分辨率为0.01μm时,最大进给率达到240m/min 且可获得复杂型面的精确加工;(3)运算速度:微处理器的迅速发展为数控系统向高速、高精度方向发展提供了保障,开发出CPU已发展到32位以及64位的数控系统,频率提高到几百兆赫、上千兆赫。
数控技术的发展趋势
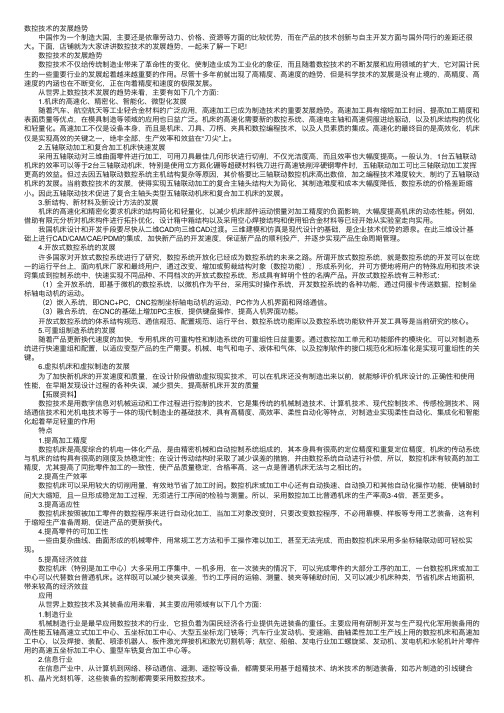
数控技术的发展趋势 中国作为⼀个制造⼤国,主要还是依靠劳动⼒、价格、资源等⽅⾯的⽐较优势,⽽在产品的技术创新与⾃主开发⽅⾯与国外同⾏的差距还很⼤。
下⾯,店铺就为⼤家讲讲数控技术的发展趋势,⼀起来了解⼀下吧! 数控技术的发展趋势 数控技术不仅给传统制造业带来了⾰命性的变化,使制造业成为⼯业化的象征,⽽且随着数控技术的不断发展和应⽤领域的扩⼤,它对国计民⽣的⼀些重要⾏业的发展起着越来越重要的作⽤。
尽管⼗多年前就出现了⾼精度、⾼速度的趋势,但是科学技术的发展是没有⽌境的,⾼精度、⾼速度的内涵也在不断变化,正在向着精度和速度的极限发展。
从世界上数控技术发展的趋势来看,主要有如下⼏个⽅⾯: 1.机床的⾼速化、精密化、智能化、微型化发展 随着汽车、航空航天等⼯业轻合⾦材料的⼴泛应⽤,⾼速加⼯已成为制造技术的重要发展趋势。
⾼速加⼯具有缩短加⼯时间、提⾼加⼯精度和表⾯质量等优点,在模具制造等领域的应⽤也⽇益⼴泛。
机床的⾼速化需要新的数控系统、⾼速电主轴和⾼速伺服进给驱动,以及机床结构的优化和轻量化。
⾼速加⼯不仅是设备本⾝,⽽且是机床、⼑具、⼑柄、夹具和数控编程技术,以及⼈员素质的集成。
⾼速化的最终⽬的是⾼效化,机床仅是实现⾼效的关键之⼀,绝⾮全部,⽣产效率和效益在“⼑尖”上。
2.五轴联动加⼯和复合加⼯机床快速发展 采⽤五轴联动对三维曲⾯零件进⾏加⼯,可⽤⼑具最佳⼏何形状进⾏切削,不仅光洁度⾼,⽽且效率也⼤幅度提⾼。
⼀般认为,1台五轴联动机床的效率可以等于2台三轴联动机床,特别是使⽤⽴⽅氮化硼等超硬材料铣⼑进⾏⾼速铣削淬硬钢零件时,五轴联动加⼯可⽐三轴联动加⼯发挥更⾼的效益。
但过去因五轴联动数控系统主机结构复杂等原因,其价格要⽐三轴联动数控机床⾼出数倍,加之编程技术难度较⼤,制约了五轴联动机床的发展。
当前数控技术的发展,使得实现五轴联动加⼯的复合主轴头结构⼤为简化,其制造难度和成本⼤幅度降低,数控系统的价格差距缩⼩。
数控进给伺服系统与驱动电机的发展及趋势
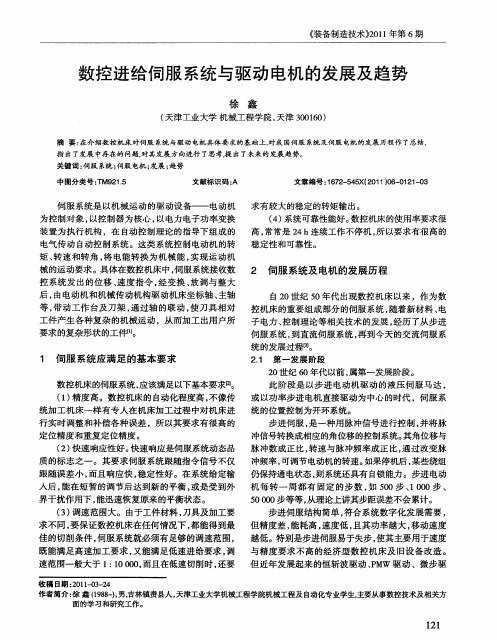
盛发展 的时代 ,由于直流电动机具有优 良的调速性 能, 很多高性能驱动装置采用了直流 电动机 , 伺服 系 统 的位置 控制 , 由开环 系统 发 展为 闭环 系统 。 也 直 流伺 服 的工作 原 理 ,是 建立 在 电磁力 定 律 基 础 上 。与 电磁 转矩 相 关 的 , 互 相独 立 的两个 变 量 主 是 磁通与 电枢电流 ,它们 分别控制励磁 电流与电枢 电 流, 可方便地进行转矩与转速控制。另一方面从控制 角度看 , 直流伺服的控制 , 是一个单输入单输出的单 变量控制系统 , 经典控制理论完全适用于这种系统。 因此 , 直流伺服 系统控制简单 , 调速性能优异 , 在数 控机床的进给驱动中, 曾占据着主导地位 。 然而 , 从实际运行考虑 , 直流伺 服电动机引入了 机械换向装置。 其成本高 , 障多 , 故 维护 困难 , 经常因 碳刷产生的火花而影响生产 ,并对其他设备产 生电 磁 干 扰 。同时机 械换 向器 的换 向能 力 , 限制 了 电动机 的容量和速度。电动机的电枢在转子上 , 使得电动机 效 率 低 , 热 差 。为 了改 善 换 向能力 , 小 电枢 的漏 散 减 感 , 子 变得 短 粗 , 响 了系统 的动 态性 能 。 转 影 23 第 三 个发 展 阶段 . 2 世纪 8 年代至今 , 0 0 属第三发展阶段 。 这一阶段是 以机电一体化时代为背景的 ,由于 伺服 电动机结构及其永磁材料和控制技术 的突破性 进展 , 出现 了无刷直流伺服 电动机 ( 方波驱动 )交流 , 伺 服 电动机 ( 弦波 驱 动 ) 正 等种 种新 型 的 电动机 。 针对直流 电动机 的缺陷 , 如果将其做 “ 翻外 ” 里 的处理 , 即把 电 驱 绕组 装 在 定 子 、 子 为永 磁 部 分 , 转 由转子轴上的编码器测 出磁极位置 ,就构成了永磁 无刷 电动机 , 同时随着矢量控制方法 的实用化 , 使交 流伺服系统具有 良好的伺服特性。其宽调速范围、 高 稳速精度 、快速动态响应及四象限运行等 良好的技
电机控制技术发展前景

电机控制技术发展前景(一)伺服电机控制技术的发展推动加工技术的高速高精化。
80年代以来,数控系统逐渐应用伺服电机作为驱动器件。
交流伺服电机内是无刷结构,几乎不需维修,体积相对较小,有利于转速和功率的提高。
目前交流伺服系统已在很大范围内取代了直流伺服系统。
在当代数控系统中,交流伺服取代直流伺服、软件控制取代硬件控制成为了伺服技术的发展趋势。
由此产生了应用在数控机床的伺服进给和主轴装置上的交流数字驱动系统。
随着微处理器和全数字化交流 伺服系统的发展,数控系统的计算速度大大提高,采样时间大大减少。
硬件伺服控制变为软件伺服控制后,大大地提高了伺服系统的性能。
例如OSP-U10/U100网络式数控系统的伺服控制环就是一种高性能的伺服控制网,它对进行自律控制的各个伺服装置和部件实现了分散配置,网络连接,进一步发挥了它对机床的控制能力和通信速度。
这些技术的发展,使伺服系统性能改善、可靠性提高、调试方便、柔性增强,大大推动了高精高速加工技术的发展。
另外,先进传感器检测技术的发展也极大地提高了交流电动机调速系统的动态响应性能和定位精度。
交流伺服电机调速系统一般选用无刷旋转变压器、混合型的光电编码器和绝对值编码器作为位置、速度传感器,其传感器具有小于1μs的响应时间。
伺服电动机本身也在向高速方向发展,与上述高速编码器配合实现了60m/min甚至100m/min的快速进给和1g的加速度。
为保证高速时电动机旋转更加平滑,改进了电动机的磁路设计,并配合高速数字伺服软件,可保证电动机即使在小于1μm转动时也显得平滑而无爬行。
(二)交流直线伺服电机直接驱动进给技术已趋成熟。
数控机床的进给驱动有“旋转伺服电机+精密高速滚珠丝杠”和“直线电机直接驱动” 两种类型。
传统的滚珠丝杠工艺成熟加工精度较高,实现高速化的成本相对较低,所以目前应用广泛。
使用滚,珠丝杠驱动的高速加工机床最大移动速度90m/min,加速度1.5g。
但滚珠丝杠是机械传动,机械元件间存在弹性变形、摩擦和反向间隙,相应会造成运动滞后和非线性误差,所以再进一步提高滚珠丝杠副移动速度和加速度比较难了。
数控机床主轴驱动系统的选用研究
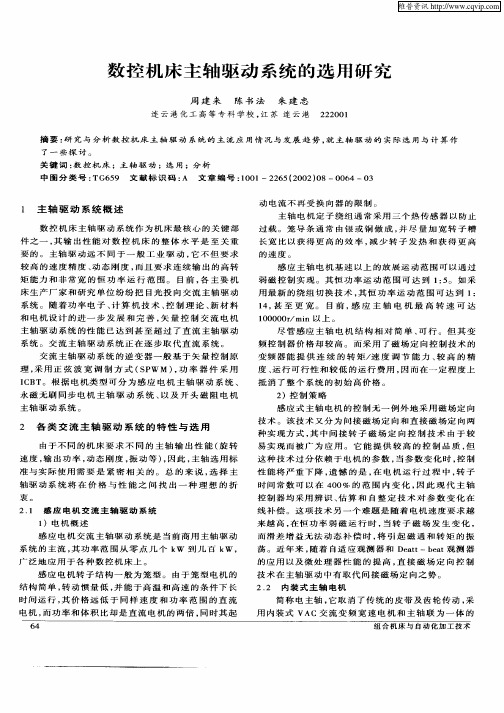
主轴驱动 系统 。
抵 消 了整 个 系 统 的初 始 高 价 格 。 2 )控 制 策 略
感 应 式 主 轴 电 机 的 控 制 无 一 例 外 地 采 用 磁 场 定 向
技 术 。 该 技 术 又 分 为 间 接 磁 场 定 向 和 直 接 磁 场 定 向 两
主轴 电 机 定 子 绕 组 通 常 采用 三 个 热 传 感 器 以 防止
过 载 。笼 导 条 通 常 由银 或 铜 做 成 , 尽 量 加 宽 转 子 糟 并 长 宽 比 以获 得 更 高 的 效 率 , 少 转 子 发 热 和 获 得 更 高 减
的速度 。
感 应 主 轴 电 机 基 速 以 上 的放 展 运 动 范 围 可 以 通 过 弱 磁 控 制 实 现 。 其 恒 功 率 运 动 范 围 可 达 到 1 5 如 采 :。 用 最 新 的 绕 组 切 换 技 术 , 恒 功 率 运 动 范 围 可 达 到 1 其 : 1 甚 至 更 宽 。 目 前 , 应 主 轴 电 机 最 高 转 速 可 达 4, 感
维普资讯
数 控 机 床 主 轴 驱 动 系 统 的 选 用 研 究
周 建 来 陈 书 法 朱 建 忠
连 云 港 化 工 高 等 专 科 学 校 , 苏 连 云 港 2 2 0 江 20 1
摘 要 : 究与 分析 数 控 机 床 主 轴 驱 动 系 统 的 主 流 应 用 情 况 与 发 展 趋 势 , 主 轴驱 动 的 实 际 选 用 与 计 算 作 研 就
感 应 电机 交 流 主 轴 驱 动 系 统 是 当 前 商 用 主 轴动 系 统 的 特 性 与 选 用
- 1、下载文档前请自行甄别文档内容的完整性,平台不提供额外的编辑、内容补充、找答案等附加服务。
- 2、"仅部分预览"的文档,不可在线预览部分如存在完整性等问题,可反馈申请退款(可完整预览的文档不适用该条件!)。
- 3、如文档侵犯您的权益,请联系客服反馈,我们会尽快为您处理(人工客服工作时间:9:00-18:30)。
( 7 ) 高频变频装置: 要实现电主轴每分钟几万甚至十几万 转的转速, 必须用高频变频装置来驱动电主轴的内置高速电 机, 变频器的输出频率甚至需要达到几千 Hz。
2 现代机床主轴发展趋势
现代机床主轴发展趋势是逐渐由传统机床主轴向电主轴 过渡。
传统机床主轴是通过传动装置带动主轴旋转而工作的, 电 主轴的主要特点是将电机置于主轴内部, 通过驱动电源直接驱 动主轴进行工作, 实现了电机、主轴的一体化功能。
与传统机床主轴相比, 电主轴具有十分明显的优势。由于 主轴由内装式电机直接驱动, 省去了皮带、齿轮、联轴节等中间 变 速 和 传 动 装 置 , 具 有 结 构 简 单 紧 凑 、效 率 高 、噪 声 低 、振 动 小 和精度高等特点。而且利用交流变频技术, 电主轴可以在额定 转速范围内实现无级变速, 以适应机床工作时各种工况和负载 变化的需要。
电主轴是将机床主轴与主轴电机融为一体的高新技术产 品。电主轴实际是指电主轴系统, 由电主轴、驱动控制器、编码 器 、润 滑 装 置 、冷 却 装 置 等 组 成 。电 主 轴 系 统 是 数 控 机 床 三 大 高 新技术之一( 高速电主轴、数控系统、送给驱动) 。随着数控技术 及切削刀具的飞跃发展, 越来越多的机械制造装备都在不断向 高 速 、高 精 、高 效 、高 智 能 化 发 展 , 电 主 轴 已 成 为 最 能 适 应 上 述 高性能工况的数控机床核心功能部件之一, 尤其是在多轴联 动 、多 面 体 加 工 、并 联 机 床 、复 合 加 工 机 床 等 诸 多 先 进 产 品 中 , 电主轴的优异特点是机械主轴单元不能替代的。
场定向控制技术在主轴驱动中有取代间接磁场定向之势。 1.2 永磁交流主轴驱动系统
永磁交流 主 轴 电 机 分 为 正 弦 波 驱 动(PMSM)主 轴 电 机 和 方 波驱动无刷直流(BDCM)主轴电机。此 类 主 轴 电 机 以 转 子 无 铜 耗、高效率和高功率/ 转矩密度著称。其低速运行时可获得更 大的功率和转矩, 因此在同步攻丝时的伺服锁定运行和快速定 向方面有较大的优势。一般永磁主轴电机功率在 l0kW 以下, 速 度 低 于 8000r/ min。 但 目 前 转 速 在 20000—30000r/ min 之间, 功率超过 l0kW 的主轴电机已在制造。永磁主轴电机在 转子上不存在发热元件, 显著提高了电机效率, 同时高性能钕 铁硼材料的应用, 使得永磁主轴电机在所有形式的交流主轴电 机中具有最高 的 效 率 和 最 小 的 体 积 。PMSM 和 BDCM 电 机 均 可运行于高速范围。但弱磁范围受到一定限制, 使速度不能很 高。在控制策略方面, PMSM 电机的定子绕组经特殊绕制后将 产生正弦反电势, 当绕组通入正弦电流后, 便可获得恒定的转 矩 。但 是 磁 场 定 向 必 须 借 助 于 绝 对 转 子 位 置 编 码 器 来 实 现 。近 年提出的无 传 感 器 控 制 为 PMSM 主 轴 电 机 高 速 运 行 提 供 了 另 一种选择。BDCM 电机定子绕组则使电机产生梯形波反电势, 但 同 样 也 需 要 转 于 位 置 传 感 器 来 实 现 定 子 电 流 换 向 。无 传 感 器 运行对 BDCM 也可实现。永磁交 流 主 轴 电 机 的 控 制 难 点 主 要 在于如何拓展弱磁运行范围。PMSM 主轴电机通常采用内装式 结构, 而在控制上通常以满足最大转矩弱磁为准则。BDCM 主 轴 电 机 通 常 采 用 最 优 电 流 和 最 优 PWM 控 制 方 式 以 抑 制 脉 动 转矩, 提高电机效率。 1.3 开关磁阻型主轴驱动系统
开 关 磁 阻 电 机 (SR M)以 其 简 单 、坚 固 的 机 械 构 造 、高 速 运 行 能力和体积小、重量轻、效率高等特性 , 近年来在工业界引起了 广泛的兴趣, 尤其是其优秀的高速度运行能力和价格优势, 使 其 在 10kW 以 下 , 调 速 范 围 至 100000r/ min 的 数 控 机 床 主 轴 驱动应用中, 大有与感应式主轴电机一争高低之势。开关磁阻 电机定子极上绕有集中绕组, 转子则既无绕组也无永磁体。 SRM 电机定转子的极数不 同 , 广 泛 采 用 三 相 6/ 4 结 构 。 为 获 得最优平均转矩, 气隙需要精确控制并使极弧与气隙之比在 25—30 之问。SRM 主轴电机的结构通常与控制策略和功率变 换器同时考虑, 其三者的牵制作用要比感应电机和永磁电机 强。通过适当的角度位置控制, SRM 可容易地获得 1: 3 的恒功 率运行范围。在控制策略方面, 当电机低于基速以下运行时, 常 采用电流斩波控制方式, 以避免过大的电流和磁链值, 取得恒
主 轴 电 机 另 一 个 发 展 趋 势 主 要 是 向 高 效 、大 功 率 主 轴 电 动 机发展。
为 提 高 机 床 主 轴 电 动 机 的 切 削 速 度 、快 速 响 应 能 力 和 控 制 精度 , 大多数 CNC 机床都选择 集 成 式 主 轴 AC 感 应 主 轴 电 动 机代替以往的由皮带或齿轮减速的分离式主轴电动机, 而最近 随着技术的进步, 新开发出一种含稀有材料的永久磁铁集成式 主轴电动机, 由于它能更高效、大功率地传递扭矩, 所以大有取 代感应式集成主轴电动机的趋势据。据介绍, 这种含铌的永久 磁铁集成式主轴电动机与通用的感应式集成主轴电动机相 比. 具有以三个优点:
对电主轴的外壁通以循环冷却剂, 冷却装置的作用是保持冷却 剂的温度。
( 5 ) 内置脉冲编码器: 为了实现பைடு நூலகம்动换刀以及刚性攻丝, 电 主轴内置一脉冲编码器, 以实现准确的相位控制以及与进给的配 合。
( 6 ) 自动换刀装置: 为了适用于加工中心, 电主轴配备了 能进行自动换刀的装置, 包括碟形簧、拉刀油缸。
流主轴驱动系统正在逐步取代直流系统, 电主轴逐渐取代传统机床主轴。
【关 键 词】 主轴驱动系统; 主轴电机; 电主轴
【中 图 分 类 号】 TG659 【文 献 标 识 码】 A
【文 章 编 号】 1003- 2673(2008)03- 37- 02
数控机床主轴驱动系统作为机床的最核心的关键部件之 一, 其输出性能对数控机床的整体水平是至关重要的。主轴驱 动 远 不 同 于 一 般 工 业 驱 动 , 它 不 但 要 求 较 高 的 速 度 精 度 、动 态 刚度, 而且要求连续输出的高转矩能力和非常宽的恒功率运行 范围。目前, 各主要机床生产厂家和研究单位纷纷把目光投向 交 流 主 轴 驱 动 系 统 。 随 着 功 率 电 子 、计 算 机 技 术 、控 制 理 论 、新 材料和电机设计的进一步发展和完善, 矢量控制交流电机主轴 驱 动 系 统 的 性 能 已 达 到 甚 至 超 过 了 直 流 主 轴 驱 动 系 统 。交 流 主 轴驱动系统正在逐步取代直流系统。
1 交流主轴驱动系统发展趋势
交流主轴驱动系统的逆变器一般基于矢量控制原理, 采用 正弦波宽调制方式(SPWM), 功率器件 采 用 ICBT。 根 据 电 机 类 型 可 分 为 感 应 电 机 主 轴 驱 动 系 统 、永 磁 无 刷 同 步 电 机 主 轴 驱 动 系 统 、开 头 磁 阻 电 机 主 轴 驱 动 系 统 。 1.1 感应电机交流主轴驱动系统
( 1 ) 传 递 扭 矩 大 用 两 种 功 率 为 N=7.46kW, 转 速 n=600Or/min 的电动机所作的比较性试验表明, 通用的感应式 集成主轴电 动 机 传 递 的 转 矩 为 95N·m。 而 含 稀 有 材 料 的 永 久 磁铁型集成式主轴电动机则能传递 160N·m 的转矩。
感应电机交流主轴驱动系统是当前商用主轴驱动系统的 主流, 其功率范围从零点几个 kW 到几百 kW, 广泛地应用于各 种数控机床上。
感应主轴电机基速以上的放展运动范围可以通过弱磁控 制实现。其恒功率运动范围可达到 1: 5。如采用最新的绕组切 换技术, 其恒功率运动范围可达到 1: 14, 甚至更宽。目前, 感应 主轴电机最高转速可达 100000r/ min 以上。尽管感应主轴电 机 结 构 相 对 简 单 、但 其 变 频 控 制 器 价 格 却 较 高 。 而 采 用 了 磁 场 定向控制技术的变频器能提供连续的转矩/ 速度调节能力、较 高 的 精 度 、运 行 可 行 性 和 较 低 的 运 行 费 用 , 因 而 在 一 定 程 度 上 抵消了整个系统的初始高价格。
2008 年 3 月 第 3 期( 总第 111 期)
广西轻工业
GUANGXI JOURNAL OF LIGHT INDUSTRY
主轴驱动系统和主轴电机发展趋势
机械与电气
杨玥
( 天津工业大学机械工程及自动化系, 天津 3001 60)
【摘 要】 文章主要介绍了主轴驱动系统和主轴电机发展的趋势, 并介绍了几种交流主轴驱动系统和电主轴系统 , 指 出 交
电主轴是最近几年在数控机床领域出现的将机床主轴与 主 轴 电 机 融 为 一 体 的 新 技 术 , 它 与 直 线 电 机 技 术 、高 速 刀 具 技 术一起, 将会把高速加工推向一个新时代。
电主轴是一套组件, 它包括电主轴本身及其附件: 电主轴、高 频变频装置、油雾润滑器、冷却装置、内置编码器、换刀装置等。
【作 者 简 介】杨玥, 女 , 天津人, 天津工业大学机械工程及自动化系 2004 级本科生。研究方向: 机械工程及自动化。
37
转矩机械特性。同时为获得最佳效率和减少转矩谐波, SRM 主 轴 驱 动 系 统 通 常 采 用 自 适 应 控 制 、最 优 控 制 和 预 测 控 制 技 术 来 控制开头模式。而在基速以上的弱磁运行范围, SRM 常采用角 度位置控制方式, 通过导通角口的调节, 调节电机的转矩实现 调速目的。SRM 的主要不足在于 低 速 时 的 高 谐 波 转 矩 和 高 噪 声。而 SRM 主轴电机主要运行于高速恒功率区域, 因此影响并 不明显。