预防过程错混料管理规定
预防混料管理办法

预防混料管理办法一、目的规范我司原物料,半成品,成品的管理,防止公司错混料的发生。
二、适应范围车间范围内所有与原材料,半成品,成品所接触到的部门,以及我司供应商。
三、定义错混料:原料物,半成品,成品中用错料或混料的现象统称为错混料。
四、职责4.1业务负责接到订单后将客户订单转化为内部订单责任确认单,并将信息传递至下单员录入系统。
4.2 技术部负责产品BOM的组成和材料性能确认选择。
4.3生产管理部负责下达排产任务单,原材料需求采购和监督任务执行。
4.4供应部依据计划提出的采购需求,进行保障到货。
4.5仓库负责原材料与成品的储存及管理(包括收发及5S管理)。
4.6质量部负责物料,半成品与成品的检验管理。
4.7生产部负责对生产中所有原材料,半成品与成品的管理和组织人员生产保证订单按期完成。
五、内容5.1.工艺文件错混料管理5.1.1技术部根据客户新产品、图纸、技术指标或工艺要求,注意图纸版本及产品技术指标细节,转换成我司的技术文件和现场工艺文件,进行受控和发行。
5.1.2专职人员统一管理技术文件,注意图纸编号,图纸版本,技术文件编号,技术文件版本,发行日期,发行换版编号,同时做好回收作废工作,放置图纸错误造成混料。
5.2业务接单/下单错混料管理5.2.1业务接收客户订单时候,经过评审后,将客户相关要求进行记录,按照唯一编号进行比对识别。
5.2.2业务下单时,将相关要求在销售订单责任确认单上进行注明,特别产品包装要求和生产注意事项,对于产品类型相似及包装方式相同的产品重点说明。
5.2.3.特殊产品:系统下单进行唯一编码进行识别,确保下单和系统录入;常规产品:正常系统下单,根据规格进行识别进行。
5.3模具错混料管理5.3.1模具仓库设有专人员管理,并做有专门记录,记录有模具类别,尺寸,领用机台,数量,做好明细登记和标识,同一机台最多两台。
5.3.2相关产品按照规定模具进行配模生产,管控规定。
5.4样品新生产时错混料管理5.4.1业务部接新产品(以从前未生产过)或客户产品变更消息时及时转交技术部,技术部根据业务提供的相关资料做成BOM,同时对材料选型确认指标规定做好规定和要求,供应部依据BOM进行厂家选择,材料选择,物料回来经质量部验收合格后进行入库。
车间预防错混料管理规定

15.两个班交接必须按照第1条、第2条和第3条进行现场查看,当面确认无误后方可让上个 班的人员下班。
3.物料必须作好标识,标识清楚是否生产、是什么类型、颜色、数量、规格等。 4.物料员领取物料必须弄清楚是什么类型,物料领取到车间后必须第一时间告之并交接给 拉上的管段时间则必须按第1条和第3条执行。
6.拉上管理人员安排物料员领取物料必须详细告诉物料员具体的领料信息(领什么料?什 么颜色?多少数量?)。
10.如非PMC计划安排,拉上严禁同时生产多种类型的物料,如有生产则拉长必须指定一个 助拉专门跟进预防混料和防止人为错失的发生。
11.如拉上在同时生产多种类型的物料,则拉长必须安排助拉或指定专人进行物料周转,非 指定人员严禁进行物料周转。
12.如拉上在同时生产多种类型的物料,则拉长在生产前必须告之操作员具体的注意事项, 每个人必须清楚生产类型、生产数量。
16、产品检验工序人员在检验产品时,第一检验工序为是否漏工序,然后才是按标准检查 其它管控项目。
17.物料如长时间不能流转到下道工序车间则必须按第1条和第2条执行,且用保鲜膜包缠好 。 18、在流水线上,上一工段与下一工段之间必须设置挡板,以防止产品漏工序而流通。同 时禁止产品逆流。
19.未按以上执行者第一次扣拉长助拉绩效5分,第二次10分,第三次取消当月绩效考核。
7.生产过程中同一物料架、同一机台严禁存放两种类型的物料,必须生产完结一种类型的 物料后才可以生产另一种类型的物料。 8.生产过程中,已生产的物料与未生产的物料,必须按照具体的标识存放于物料架上指定 的隔层,严禁已生产的物料隔层存放未生产的物料和未生产的物料隔层存放已生产的物料 。 9.生产过程中生产完的产品放进吸塑盘或物料框内时,产品必须朝统一放置。
预防混料管理办法
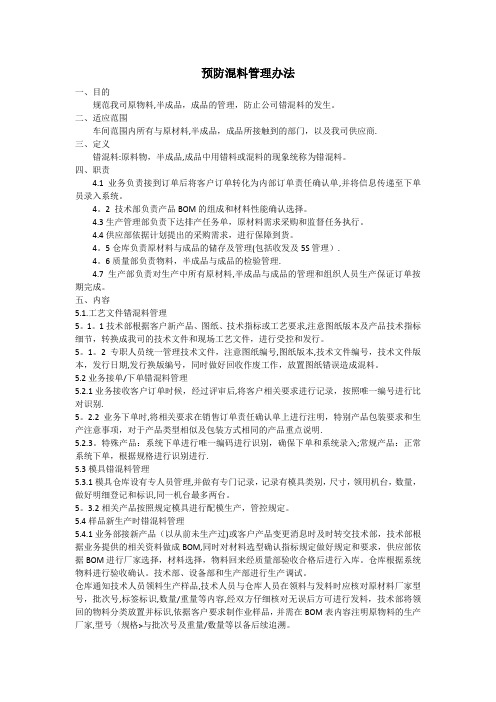
预防混料管理办法一、目的规范我司原物料,半成品,成品的管理,防止公司错混料的发生。
二、适应范围车间范围内所有与原材料,半成品,成品所接触到的部门,以及我司供应商.三、定义错混料:原料物,半成品,成品中用错料或混料的现象统称为错混料。
四、职责4.1业务负责接到订单后将客户订单转化为内部订单责任确认单,并将信息传递至下单员录入系统。
4。
2 技术部负责产品BOM的组成和材料性能确认选择。
4.3生产管理部负责下达排产任务单,原材料需求采购和监督任务执行。
4.4供应部依据计划提出的采购需求,进行保障到货。
4。
5仓库负责原材料与成品的储存及管理(包括收发及5S管理).4。
6质量部负责物料,半成品与成品的检验管理.4.7生产部负责对生产中所有原材料,半成品与成品的管理和组织人员生产保证订单按期完成。
五、内容5.1.工艺文件错混料管理5。
1。
1技术部根据客户新产品、图纸、技术指标或工艺要求,注意图纸版本及产品技术指标细节,转换成我司的技术文件和现场工艺文件,进行受控和发行。
5。
1。
2专职人员统一管理技术文件,注意图纸编号,图纸版本,技术文件编号,技术文件版本,发行日期,发行换版编号,同时做好回收作废工作,放置图纸错误造成混料。
5.2业务接单/下单错混料管理5.2.1业务接收客户订单时候,经过评审后,将客户相关要求进行记录,按照唯一编号进行比对识别.5。
2.2业务下单时,将相关要求在销售订单责任确认单上进行注明,特别产品包装要求和生产注意事项,对于产品类型相似及包装方式相同的产品重点说明.5.2.3。
特殊产品:系统下单进行唯一编码进行识别,确保下单和系统录入;常规产品:正常系统下单,根据规格进行识别进行.5.3模具错混料管理5.3.1模具仓库设有专人员管理,并做有专门记录,记录有模具类别,尺寸,领用机台,数量,做好明细登记和标识,同一机台最多两台。
5。
3.2相关产品按照规定模具进行配模生产,管控规定。
5.4样品新生产时错混料管理5.4.1业务部接新产品(以从前未生产过)或客户产品变更消息时及时转交技术部,技术部根据业务提供的相关资料做成BOM,同时对材料选型确认指标规定做好规定和要求,供应部依据BOM进行厂家选择,材料选择,物料回来经质量部验收合格后进行入库。
预防混料管理办法
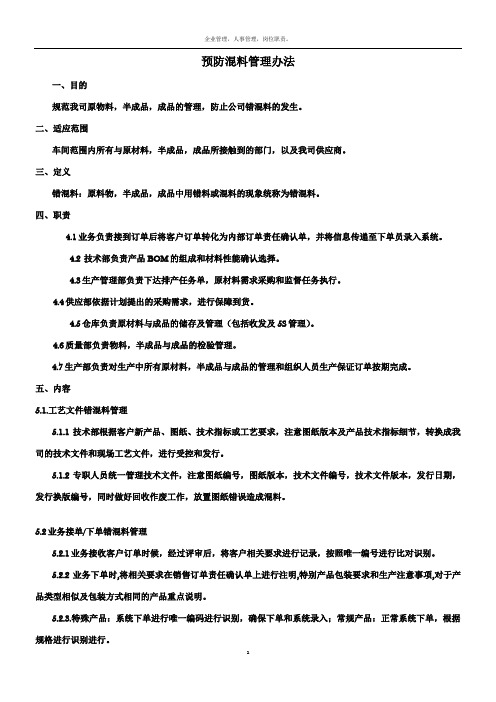
预防混料管理办法一、目的规范我司原物料,半成品,成品的管理,防止公司错混料的发生。
二、适应范围车间范围内所有与原材料,半成品,成品所接触到的部门,以及我司供应商。
三、定义错混料:原料物,半成品,成品中用错料或混料的现象统称为错混料。
四、职责4.1业务负责接到订单后将客户订单转化为内部订单责任确认单,并将信息传递至下单员录入系统。
4.2 技术部负责产品BOM的组成和材料性能确认选择。
4.3生产管理部负责下达排产任务单,原材料需求采购和监督任务执行。
4.4供应部依据计划提出的采购需求,进行保障到货。
4.5仓库负责原材料与成品的储存及管理(包括收发及5S管理)。
4.6质量部负责物料,半成品与成品的检验管理。
4.7生产部负责对生产中所有原材料,半成品与成品的管理和组织人员生产保证订单按期完成。
五、内容5.1.工艺文件错混料管理5.1.1技术部根据客户新产品、图纸、技术指标或工艺要求,注意图纸版本及产品技术指标细节,转换成我司的技术文件和现场工艺文件,进行受控和发行。
5.1.2专职人员统一管理技术文件,注意图纸编号,图纸版本,技术文件编号,技术文件版本,发行日期,发行换版编号,同时做好回收作废工作,放置图纸错误造成混料。
5.2业务接单/下单错混料管理5.2.1业务接收客户订单时候,经过评审后,将客户相关要求进行记录,按照唯一编号进行比对识别。
5.2.2业务下单时,将相关要求在销售订单责任确认单上进行注明,特别产品包装要求和生产注意事项,对于产品类型相似及包装方式相同的产品重点说明。
5.2.3.特殊产品:系统下单进行唯一编码进行识别,确保下单和系统录入;常规产品:正常系统下单,根据规格进行识别进行。
5.3模具错混料管理5.3.1模具仓库设有专人员管理,并做有专门记录,记录有模具类别,尺寸,领用机台,数量,做好明细登记和标识,同一机台最多两台。
5.3.2相关产品按照规定模具进行配模生产,管控规定。
5.4样品新生产时错混料管理5.4.1业务部接新产品(以从前未生产过)或客户产品变更消息时及时转交技术部,技术部根据业务提供的相关资料做成BOM,同时对材料选型确认指标规定做好规定和要求,供应部依据BOM进行厂家选择,材料选择,物料回来经质量部验收合格后进行入库。
生产过程预防错混料SOP

7.1.6在生产过程中如有非品质部门人员从生产线中拿走物料的,作业员必须禁止其行为;必须报告组长,经组长同意之後才能从生产线中拿走物料;如拿走物料部门要将物料归还给生产部门,必须归还物料交组长,禁止任何非品质部门人员擅自从生产线拿走物料,及擅自将物料放在生产线上的行为,如生产部门发现有该行为,开立处罚单处罚当事人10 元人民币。
7.1.7下班前,组长必须进行清线作业(将流水线上的产品全部完工作业,然後将多余物料放置好),禁止停线下班了,生产线物料没有清理的行为。
7.1.8清线过程中要将不良和良品有效的区别开来:不良品用红色盒子装,幷统一拿到返修区由返工人员进行返修作业;待下工序的良品必须标注下工序的物料流动卡,,以提示下工序的流向。
7.1.9如果是停线超过48 小时的,必须用上下盖将物料盒里面的物料盖住,幷标注下工序的物料流动卡,以提示下工序的流向。
7.1.10生产及换线依生产现场6S 管理规定执行,生产尾数需分开标示区分,生产线上人员需落实自检动作,核对流程卡所示品名规格、数量需与实物一致,避免因换线产品清理不彻底导致混料,核对无误之产品由作业人员填写物料标签标示于产品外包装上。
7.2生产包装过程的预防作业方式:7.2.1包装员必须培训上岗,熟悉各产品的包装方式,所有封箱包装作业必须在包装区域完成。
7.2.2包装台面上禁止放置两种或以上类似产品同时包装作业,必须分开区域、分开作业。
7.2.3包装员的封箱作业前,必须核对内外箱标签;组长在拿标签给包装员时必须自我核对幷交代清楚,及提示注意事项。
7.2.4包装过程如出现标签过多情况或不清晰情况,包装员要立即上报组长重新更换,及交上级清查多数标签的原因,排除少贴、错贴因素之後,才将多於标签销毁处理。
7.2.5如包装因工单数量需要包装尾数箱时,必须在外箱上注明“尾数箱”标识,幷提示品保检验人员特别抽检该箱的标识、数量核对等。
7.2.6所有包装箱在入库前必须用电子称进行称重确认。
防跑料、串料管理规定
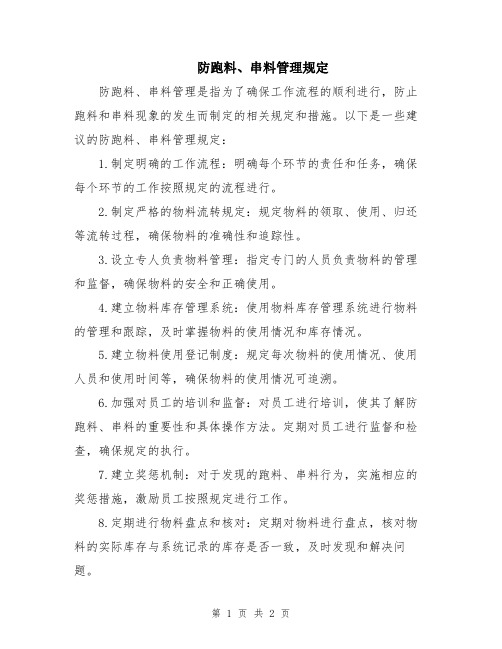
防跑料、串料管理规定
防跑料、串料管理是指为了确保工作流程的顺利进行,防止跑料和串料现象的发生而制定的相关规定和措施。
以下是一些建议的防跑料、串料管理规定:
1.制定明确的工作流程:明确每个环节的责任和任务,确保每个环节的工作按照规定的流程进行。
2.制定严格的物料流转规定:规定物料的领取、使用、归还等流转过程,确保物料的准确性和追踪性。
3.设立专人负责物料管理:指定专门的人员负责物料的管理和监督,确保物料的安全和正确使用。
4.建立物料库存管理系统:使用物料库存管理系统进行物料的管理和跟踪,及时掌握物料的使用情况和库存情况。
5.建立物料使用登记制度:规定每次物料的使用情况、使用人员和使用时间等,确保物料的使用情况可追溯。
6.加强对员工的培训和监督:对员工进行培训,使其了解防跑料、串料的重要性和具体操作方法。
定期对员工进行监督和检查,确保规定的执行。
7.建立奖惩机制:对于发现的跑料、串料行为,实施相应的奖惩措施,激励员工按照规定进行工作。
8.定期进行物料盘点和核对:定期对物料进行盘点,核对物料的实际库存与系统记录的库存是否一致,及时发现和解决问题。
9.不定期进行物料清理和整理:定期对物料进行清理和整理,淘汰过期物料,整理杂乱的物料存放区域,确保物料的整齐和清晰可见。
10.建立监督反馈机制:建立可以接受员工举报和投诉的渠道,对于涉及跑料、串料行为的举报和投诉进行调查和处理。
以上是一些常用的防跑料、串料管理规定,具体可以根据企业实际情况进行定制和调整。
同时,要求员工自觉遵守相关规定,积极维护工作秩序和规范。
防错混料管理指导书
5.3品质部
5.3.1 首件时使用BOM表核对原物料编码,按照图纸或样品进行“六面”外观对比并保留记录
5.3.2 QC需确认生产部门对应是否按照SOP生产、点检表是否点检、线体是否符合规定、清线是否清完全、尾料标签是否及时粘贴等。
5.5.5 相似机种分区域放置并有明显警示标示
5.5.6库房严禁私自开箱作业,需开箱由品质对接生产领入产线作业;外仓严格禁止在仓库私自开箱作业,除客户同意外,仓库单独设立合并箱区域或房间,有摄像头全程监控,经过生产单位、仓库、SC三方共同作业并记录,摄像内容需要保留6个月以上。
5.5.7 第三方SortingT平台或者第三方特殊作业出货对BOX标签与客户标签比对,传递预防错混料管理要求。
5.5.8 纸箱或客户标签破损等原因需要更换纸箱或标签是能由品质人员确认更换(外长由各限地CS更换)
5.6业务部
5.6.1 运输过程中不可对产品进行除运输外的任何操作,并签署错混料相关处罚协议
六、参考文件及使用表单
6.1《首件管控程序》
6.2《相似机种一览表》
6.3《产品BOM(原材开料规格)表、样品》
5.2.1.4相似机种若共用模具且接连生产,产品必须更换LOT号进行区分切冲压领班由品质签署首件后且确认所有尾料清理完成后方可生产;
5.2.1.5 相似品生产时现场放入相似品专属区域,每托粘贴产品标识卡,由品质QC确认OK粘贴ACC标签。
5.2.1.6 品质贴附ACC标签后产品任何部门不可擅自移动或拿取产品,只允许整托运输。QC检验合格封箱之后不允许进行任何操作,包括粘贴标签、合并箱等一切改变状态的行为
预防混料管理办法
预防混料管理办法一、目的规范我司原物料,半成品,成品的管理,防止公司错混料的发生。
二、适应范围车间范围内所有与原材料,半成品,成品所接触到的部门,以及我司供应商。
三、定义错混料:原料物,半成品,成品中用错料或混料的现象统称为错混料。
四、职责4.1 业务负责接到订单后将客户订单转化为内部订单责任确认单,并将信息传递至下单员录入系统。
4.2技术部负责产品 BOM 的组成和材料性能确认选择。
4.3生产管理部负责下达排产任务单,原材料需求采购和监督任务执行。
4.4供应部依据计划提出的采购需求,进行保障到货。
4.5仓库负责原材料与成品的储存及管理(包括收发及5S 管理)。
4.6质量部负责物料,半成品与成品的检验管理。
4.7 生产部负责对生产中所有原材料,半成品与成品的管理和组织人员生产保证订单按期完成。
五、内容5.1.工艺文件错混料管理5.1.1 技术部根据客户新产品、图纸、技术指标或工艺要求,注意图纸版本及产品技术指标细节,转换成我司的技术文件和现场工艺文件,进行受控和发行。
5.1.2 专职人员统一管理技术文件,注意图纸编号,图纸版本,技术文件编号,技术文件版本,发行日期,发行换版编号,同时做好回收作废工作,放置图纸错误造成混料。
5.2 业务接单 / 下单错混料管理5.2.1 业务接收客户订单时候,经过评审后,将客户相关要求进行记录,按照唯一编号进行比对识别。
,特别产品包装要求和生产5.2.2 业务下单时 ,将相关要求在销售订单责任确认单上进行注明注意事项 ,对于产品类型相似及包装方式相同的产品重点说明。
5.2.3.特殊产品:系统下单进行唯一编码进行识别,确保下单和系统录入;常规产品:正常系统下单,根据规格进行识别进行。
5.3 模具错混料管理5.3.1 模具仓库设有专人员管理,并做有专门记录,记录有模具类别,尺寸,领用机台,数量,做好明细登记和标识,同一机台最多两台。
5.3.2 相关产品按照规定模具进行配模生产,管控规定。
生产过程防止污染、交叉污染、混淆和差错的管理规程
生产过程防止污染、交叉污染、混淆和差错的管理规程目的:建立防止污染、交叉污染、混淆和差错管理规程,规定了在药品生产活动过程中防止污染、交叉污染、混淆和差错管理内容和要求适用范围:适用于药品生产活动过程中防止污染、交叉污染、混淆和差错的管理职责:生产技术部、质保部、车间对实施本规程负责内容:1.定义1.1污染:在生产、取样、包装或重新包装、贮存或运输等操作过程中,原辅料、中间产品、待包装产品、成品受到具有化学或微生物特性的杂质或异物的不利影响。
1。
2 交叉污染:不同原料、辅料及产品之间发生的相互污染。
1.3混淆:在生产或包装的过程中,误将一种或一批物料当成了另一种或另一批物料进行使用、操作。
1.4 差错:在生产过程中,因为计量器具未调试到位、或计量方式不正确、或计数不准确而造成的错误2. 产生污染、交叉污染、混淆和差错的原因2。
1 人员:操作人员患有传染病、皮肤病等,或未接受卫生方面的培训,未按要求穿戴工作服,行为不规范、人员带来外部污染,生产人员未按工艺规程和SOP要求操作,工作责任心不强,工作量过大,操作中随意性大等。
2。
2 设备:表面不光洁、平整,材质不稳定,不易清洁,设备选型不合理,维修、保养不及时,没有定期验证或没有保持验证状态。
生产中使用的设备、容器无状态标志,清场不彻底等造成混淆.2.3 物料:购进的原辅料本身质量不好,或在运输、贮存、检验取样、配料过程中造成污染。
原辅料微生物指标超限。
原辅料、包装材料、半成品、中间体等无明显标志,放置混乱,散装或放在易破损的包装中,印刷性包装材料管理不善等。
2.4 文件:文件管理制度不健全,或执行不力,无复核、监控,发现问题未及时查找原因等,特别是配料、包装等重要部门管理不严格。
2。
5 环境:厂房设计不合理,生产环境如空气中粒子过多,车间地面、墙壁、天花板等不平整、易脱落、长霉、消毒不严格等造成污染.2。
6 清洁:清洁效果不能保证微生物除去水平及残留限度,清洁剂残留、消毒剂效果不能保证;生产结束后不及时清洁清场等造成污染.2。
预防混料管理办法
预防混料管理办法要求进行BOM的组成和材料性能确认选择,确保新产品的生产材料正确无误。
5.4.2生产过程中,对于样品新生产的产品,必须进行严格的检验管理,确保产品符合要求。
5.5原材料采购错混料管理5.5.1采购部门依据生产计划,对原材料进行采购,采购人员必须对采购的原材料进行严格的检查,确保原材料的品质符合要求。
5.5.2采购部门负责将采购的原材料送至仓库,仓库人员必须进行收货检验,确保原材料的品质符合要求,并对原材料进行妥善的储存和管理。
5.6生产过程中错混料管理5.6.1生产过程中,必须对原材料、半成品和成品进行严格的管理,确保不发生错混料的情况。
5.6.2生产管理部门负责下达排产任务单,并对生产过程进行监督和管理,确保生产任务按期完成。
5.7成品出库错混料管理5.7.1仓库人员在进行成品出库前,必须进行严格的检查,确保出库的产品符合要求。
5.7.2出库单上必须注明产品的规格、型号、数量和出库日期等信息,确保产品的唯一性和可追溯性。
以上是预防混料管理办法,通过严格的管理和监督,确保公司的产品质量和客户满意度。
在业务提供的相关资料中,应制作BOM清单,并对材料选型确认指标规定做好规定和要求。
供应部根据BOM进行厂家选择和材料选择,经质量部验收合格后进行入库。
仓库根据系统物料进行验收确认。
技术部、设备部和生产部进行生产调试。
仓库通知技术人员领料生产样品,技术人员与仓库人员在领料与发料时应核对原材料厂家型号、批次号、标签标识、数量/重量等内容,经双方仔细核对无误后方可进行发料。
技术部将领回的物料分类放置并标识,依据客户要求制作业样品,并在BOM表中注明原物料的生产厂家、型号(规格)与批次号及重量/数量等以备后续追溯。
生产部依据计划下达任务单进行领料,生产人员与仓库人员在领料与发料时应核对原材料厂家型号、批次号、标签标识、数量/重量等内容,经双方仔细核对无误后方可发料。
生产再次核对生产厂家、物料型号(规格)与批次号和数量/重量等信息,以防错混料现象的发生。
- 1、下载文档前请自行甄别文档内容的完整性,平台不提供额外的编辑、内容补充、找答案等附加服务。
- 2、"仅部分预览"的文档,不可在线预览部分如存在完整性等问题,可反馈申请退款(可完整预览的文档不适用该条件!)。
- 3、如文档侵犯您的权益,请联系客服反馈,我们会尽快为您处理(人工客服工作时间:9:00-18:30)。
3.7 标准规范引用:
3.7.1《来料检验作业流程》;
3.7.2《调模(机)品管理办法》
3.7.3 《不良品处理作业流程》
3.7.4 《出货检验作业流程》
编号
变更内容
核准
审核
制定
3.2.2.生产员工按计划批次先后顺序作业;
3.2.3调(修)模品:由调模人员对机台周边调模品进行清理,具体见《调模(机)品管理办法》
3.2.4首件管理:首件确认好后,悬挂机台固定位置,本工序生产完后,由生产组长收集交由品管工序留样;
3.2.5 机台切换管理:生产前,作业员确认机台周边(包括不良胶框内)及模具内无其它产品;
3.4.7.4 内包装袋标识需在线贴附,外箱标识由封箱人员封好箱后立即贴附;
3.4.7.5客户特殊要求:新品、尾数箱需追加贴附“新品”及“零”尾标签;
3.4.7.6成品包装完,由包装组长确认好尾数箱标签(料号、数量),拉至成品待检验区,通知品管入库抽检;
3.5外协过程:
依来料品质控制要求对实物(规格、数量)与标签相符合性进行确认,具体见《来料检验作业流程》.
3.2.7.3报废品由工程、品质确认,确认NG品放置报废品区,由生产组长再统一申请废弃;
3.2.8区域管理:在线暂放区产品、半成品放置区产品必须有明显料号、工序、状态标示且在放置区内;
3.2.9 转序管理(待清洗包装):无标识(料号、工序、状态)部品不可转序.
3.3清洗过程:
3.3.1待清洗的产品必须摆放整齐放置专用清洗铁框内,清洗前作业员确认清洗槽内无其它遗留产品;
3.3.2 清洗后部品放置专用胶框内,并做好物料标识(料号、工序、状态);
3.4 包装过程:
3.4.1 包装前,包装组长确认包装平台及划定的平台固定范围内没有其它部品(包括遗留首件、限度样品等);
3.4.2 类似品不允许同一时间相邻包装台包装;
3.4.3 同一时间内只允许一种物料进入固定包装平台区域;
3.4.4 同一栈板上(包装平台或工位)只允许放置一种物料;
3.4.5 装完箱后立即封箱;
3.4.6选别的不良品放置专用胶框,包装完后必须隔离到指定的区域待品管最终确认;
3.4.பைடு நூலகம் 标签管理:
3.4.7.1标签打印必须专人负责;
3.4.7.2标签打印数量不能够多打,依赖实际包装数,打印数量需登记;
3.4.7.3 标签领取、更换、补曾、报废由专人负责,各数量明细需登记;
3.2.6工序物料增补或切换:禁止工位作业人员私自拉放物料,物料增补或切换必须经过物料人员,无标示物料禁止切换;
3.2.7制程不良品管理:具体见《不良品处理作业流程》;
3.2.7.1制程不良品由品管进行追溯确认,生产组长进行标示隔离;
3.2.7.2返修后物料由生产组长提报品管确认,确认好的产品由专人返回下工程;
1.目的:
对各厂内各过程作相关规定,预防产品错混料,造成客户投诉。
2.范围:
适用于所有部品作业过程
3.步骤:
3.1 接单、下发单:
依据固化的客户编码、图纸或已转换为内部固定的型号核实单据料号、材质、规格、环保要求一致性;
3.2冲压(油压)、二次加工(二次硫化)过程:
3.2.1生产安排严格按计划先后顺序安排生产;
3.6 仓储、送货过程:
3.6.1 库房需进行分区货位管理,不同物料(产品)需分开放置/存放;
3.6.2 更换纸箱/标签后的物料需经过检验员对实物、内箱标签、外箱标签一致性进行再确认;
3.6.3 更换纸箱/标签后的物料及品管检验后的物料需及时封箱;
3.6.4 同一时间只能有一种物料进行分箱作业;
3.6.5 出货时品管需对标签与实物相符性再确认,具体见《出货检验作业流程》;