车间预防错混料管理规定
员工的混料预防措施

员工的混料预防措施
防混料措施
1、岗位工接到主控室堆料指令后,必须确认料种及货位。
2、皮带开启后,注意观察大皮带有无杂料,发现有杂料时,应把悬臂打向一边堆出。
3、岗位供应熟记料场货位分布,以免堆错料或上错料。
4、堆料时,随时查看来料是否与货位相符,以免混料。
5、堆料过程中,发现来料混有其他物料或颜色不对时,及时停机汇报主控,等待确认后方可开机(并在记录本上详细记录)。
6、岗位工必须熟记车间通知混堆的料种,在不确定的情况下不得开机。
7、堆料换料堆时,应特别清理堆料漏斗(特别是堆完块矿)。
8、堆完料后应观察皮带及漏斗有无未带完的料,若有及时联系主控室带料。
9、发现来料杂质较多时(如石块等)汇报主控并通知值班长(并记录清楚)。
10、在堆块矿或精粉时应保持2-3米的间距,以防混料。
11、料堆之间控制在2-3米的间距,料堆与排水沟挡墙控制在2米的间距,一次料场各跨北侧留路3米,块矿料场B跨南侧留路3米。
12、接到主控取料指令后,应首先查看取料漏斗及溜槽是否清理干净。
13、接到取料指令后,岗位工应对主控重复所取料种以免出现错误信息。
14、取完块矿换取精粉时,岗位工必须空转斗轮几圈,然后把漏斗清理干净,方可取精粉。
15、取完精粉或块矿后沿线各漏斗必须及时清理漏斗以免漏斗内所占物料混入。
注塑预防错混料管理规范[模板]
![注塑预防错混料管理规范[模板]](https://img.taocdn.com/s3/m/908139cc5901020206409c35.png)
1. 目的为了预防产品错、混料现象发生,制订规范2. 概述本规范描述了排产、区域划分、转产(清线)、包装、标签、尾数、运输搬运等管理要求。
3. 术语4. 内容4.1权责:4.1.1、作业员:严格按照SOP包装工艺要求对产品进行点数包装作业。
4.1.2、生产组长:负责对作业员点数包装作业的监督、作业指导及落实相关规定。
4.1.3、品检员:对打包的产品进行数量、包装、现品票的核对。
4.1.4、领班:严格按排产计划对转产(清线)、尾数按相关规定落实、并监督执行。
4.1.5、物料组长:按要求对物料区域划分并标识。
4.2转产(清线)管理4.2.1、排产前计划要确认相似产品不能安排在相邻两台机生产,避免产品混淆。
4.2.2、按排产计划提前准备好模具、物料等相关物品。
4.2.3、生产前确认所领物料产品型号、版本是否与生产计划一致。
4.2.4、机台转产时必须将上一个型号产品、首件、不良品、全部清理入库,相关的资料存档。
4.2.5、转产机型做首件时领班必须确认机型、版本是否与生产计划一致。
4.2.6、作业员必须对产品型号、版本了解,经过培训后作业员方可上岗作业。
4.2.7、生产或加工时不可堆积产品。
4.3包装管理4.3.1、点数时一定确认产品数量,不可少放多放,实物必须与SOP要求一致。
4.3.2、吸塑盒及外包箱严格按SOP要求执行,脏、损坏、不符合要求的包材不可以使用。
4.3.3、吸塑盒叠放时必须按要求错位叠放,避免压伤产品。
4.3.4、如打包时发现混料、混版现象,立即对之前生产的产品全部重新全检,并通知检验员注意。
4.3.5、回收包材必须清理完外箱标签、有损坏的不可进入车间。
在使用回收包材前作业员要仔细确认好外箱标签有无撕掉。
4.3.6、对产品型号、版本、数量确认OK后及时装箱并封箱再贴现品票。
4.3.7、尾数箱需贴尾数标签。
4.3.8、同一时间只能允许同一种物料(产品)在包装区作业。
4.4标签管理4.4.1、AB班各组长负责打印现品票(由公司K3系统导出,具体格式要求按不同的客户指定格式、客户格式较特殊时,由专案QE与我司网管协商制作);4.4.2、按每日计划单上的制令单号由K3系统导出现品票,按计划数量打印现品票张数(不可多打)。
生产车间物料管理规定模版

生产车间物料管理规定模版一、目的及背景为了加强生产车间物料管理工作,确保生产过程中物料的准确、全面、高效的供应和使用,提高生产效率和产品质量,制定本物料管理规定。
二、适用范围本规定适用于生产车间的物料管理工作。
三、管理职责1. 生产主管负责对生产车间物料的计划、采购、接收、储存、发放、使用等环节进行统筹管理,并确保物料的充分供应和及时调配。
2. 物料管理员负责对生产车间物料的入库、出库、库存管理等工作进行具体操作,并保证物料的安全和准确性。
3. 生产班组长负责对生产车间物料的领取、使用、归还等工作进行监督和管理,并确保物料的合理使用和节约。
四、物料采购1. 生产主管根据生产计划和需求,编制物料采购计划,并提交给采购部门进行采购。
2. 采购部门根据物料采购计划进行采购,确保物料的品质、数量和交期满足生产需求。
3. 采购部门收到物料后,通过验收流程进行验收,确保物料的质量和数量无误。
4. 物料管理员负责对采购的物料进行入库,并及时更新库存记录。
五、物料储存1. 物料管理员应根据物料的性质和特点,合理规划储存空间,并对不同类型的物料进行分类储存。
2. 物料储存区域应保持整洁、干燥、通风,并设有明显的标识和防火措施。
3. 入库的物料应按照标识进行摆放,避免混淆和交叉污染。
4. 物料管理员应定期检查物料的储存情况,并及时处理过期、损坏和不合格的物料。
六、物料发放和使用1. 生产班组长应根据生产计划和操作要求,及时向物料管理员提出物料领取申请。
2. 物料管理员对领取申请进行审批,并按照领取单上的数量进行发放。
3. 生产班组长应根据物料的实际需求进行合理使用,并做好物料的清点和记录。
4. 物料的使用过程中如有余料或剩余,应及时归还给物料管理员进行合理储存。
七、物料盘点与报废1. 物料管理员应定期对库存物料进行盘点,确保库存记录与实际库存一致。
2. 盘点时应对物料进行检查,发现不合格或过期的物料应及时报废,并做好相应记录。
混料预防措施

.
2 系列产品生产流程图
原材料领料
注塑(冲压)零件生产 托外加工(电镀/喷漆) 托外加工(电镀/喷漆)
组装车间领料生产
QC全检
QA抽检
包装入库/出货
.
3 原材料、零件生产混料预防措施
原材料仓库保管员在原材料出库时必须严格按照原材料 使用清单发料,注塑、冲压车间领料人员进行详细核对后签 字确认,杜绝原材料领错可能引起的材料使用错误情况发生。
.
4 托外加工(电镀/喷漆)混料预防措施
托外加工时,仓库保管员一定要再次核对产品标示卡与 实物是否对应,针对有特殊标示的产品不能同一时间安排 (变更前后物料,客户有特殊要求的物料)托外加工。
仓管员还必须遵守相似产品不能安排在相近时间托外加 工的原则,杜绝电镀厂在加工时可能将相似物料混料的可能 性。
.
IQC 电镀检验员在每批进料时除了常规检验项目外,必 须加大抽检数量针对混料不良进行重点检查,杜绝该不良情 形流入仓库。
.
5
组装车间混料预防措施
生产计划员在排单时必须将相似的产品尽量分车间生产;
针对特殊情况下相似产品确实不能分车间生产时,车间主任排线也 必须将相似产品安排在相隔较远的生产线生产,待一种产品生产完毕 作业员彻底清理生产线后再排另外种产品生产。
.
6 QC/QA/包装混料预防措施
QC组长在安排全检时相似的产品不能安排在相邻的两个工位全检, 且 在每个相邻的工位放置一个隔板,防止工位之间产品混料。
QC检验员在开始检验产品前必须依据成品检验作业指导书核对产品随工 单与产品实物是否一致,确认一致后方可进行全检作业
检验完一组产品后必须将工作台面不良品盒清理干净,将全检OK的产品 放置在待定区域后方可进行下一组产品的检验,该工作由QC组长负责监督。
生物公司防跑料、串料管理规定模版
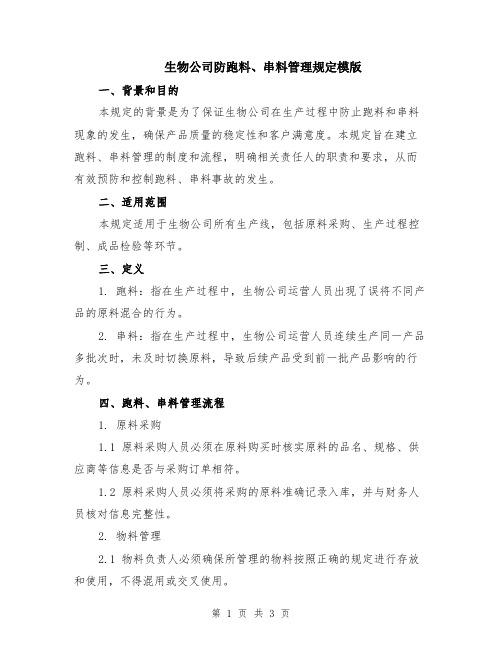
生物公司防跑料、串料管理规定模版一、背景和目的本规定的背景是为了保证生物公司在生产过程中防止跑料和串料现象的发生,确保产品质量的稳定性和客户满意度。
本规定旨在建立跑料、串料管理的制度和流程,明确相关责任人的职责和要求,从而有效预防和控制跑料、串料事故的发生。
二、适用范围本规定适用于生物公司所有生产线,包括原料采购、生产过程控制、成品检验等环节。
三、定义1. 跑料:指在生产过程中,生物公司运营人员出现了误将不同产品的原料混合的行为。
2. 串料:指在生产过程中,生物公司运营人员连续生产同一产品多批次时,未及时切换原料,导致后续产品受到前一批产品影响的行为。
四、跑料、串料管理流程1. 原料采购1.1 原料采购人员必须在原料购买时核实原料的品名、规格、供应商等信息是否与采购订单相符。
1.2 原料采购人员必须将采购的原料准确记录入库,并与财务人员核对信息完整性。
2. 物料管理2.1 物料负责人必须确保所管理的物料按照正确的规定进行存放和使用,不得混用或交叉使用。
2.2 物料负责人必须定期检查存放的物料,确保原料存放的整齐和标识的清晰可辨。
2.3 物料负责人必须制定严格的物料投放计划和标准,确保在生产过程中准确投料。
3. 生产过程控制3.1 操作人员必须确保在操作过程中按照正确的生产指令进行操作,不得随意更换或跳过工序。
3.2 操作人员必须严格遵守产品生产批次的切换规定,确保原料的切换和清洗工作有效完成,避免跑料、串料现象的产生。
3.3 操作人员必须及时记录生产信息和操作记录,确保生产过程的可追溯性。
4. 成品检验4.1 成品检验人员必须在每批次成品交付前对产品进行检验,确保产品质量的合格率。
4.2 成品检验人员必须制定严格的检验标准和程序,确保跑料、串料等问题的及时发现和处理。
五、责任人及职责1. 原料采购人员:负责核实原料信息并准确记录入库。
2. 物料负责人:负责物料管理和存放,确保物料的整齐和标识的清晰可辨。
车间物料摆放的六条原则

车间物料摆放的六条原则1.引言1.1 概述车间物料摆放是车间管理的重要内容之一,良好的物料摆放可以提高车间的工作效率和工作品质。
本文介绍了车间物料摆放的六条原则,旨在帮助车间管理者和工人们更好地组织和管理车间物料。
通过遵循这些原则,可以有效地减少物料损耗、避免交叉污染、提高工作效率和安全性等方面的问题。
首先,第一条原则是按照物品的使用频率进行摆放。
即将使用频率高的物料放置在离工作区域较近且便于取用的位置,而使用频率较低的物料可以放置在离工作区域较远或不易取用的位置。
这样做的好处是能够节约工人的时间和精力,提高工作效率。
其次,第二条原则是按照物料的属性进行分类摆放。
不同类型的物料应该被分开存放,避免发生交叉污染或者误用的情况。
例如,化学品应该与易燃物品分开存放,以防止发生意外事故。
分类摆放还能够帮助工人们更快地找到所需的物料,提高工作效率。
第三条原则是合理利用仓储空间。
车间通常会有限的仓储空间,因此需要合理规划和利用。
常用的物料应该放在离工作区域较近且易于取得的位置,而使用频率较低的物料可以放在离工作区域较远或不易取用的位置。
在摆放物料时,还可以考虑使用垂直空间,如利用货架等物品进行层层叠放,提高空间的利用率。
第四条原则是保持摆放的整洁有序。
车间物料摆放的整洁度和有序性直接影响工作效率和工作品质。
工人们应该定期对摆放的物料进行整理和清理,确保物品摆放的规范和合理。
此外,可以使用标识牌或者标签对物料进行标识,便于辨认和取用。
第五条原则是合理使用容器和包装。
物料摆放时,可以考虑使用合适的容器和包装进行包装和封装。
合适的容器和包装可以保护物料免受外界环境的影响,延长物料的使用寿命。
而且,使用容器和包装还可以对物料进行整理和分类,提高摆放的整洁度和有序性。
最后,第六条原则是定期检查和调整物料摆放。
随着车间工作的进行,物料的使用情况会发生变化,因此,车间管理者和工人们应该定期对物料的摆放进行检查和调整。
有需要时,可以重新评估摆放的效果,并进行必要的调整,以保持物料摆放的合理性和有效性。
预防混料管理办法
预防混料管理办法一、目的规范我司原物料,半成品,成品的管理,防止公司错混料的发生。
二、适应范围车间范围内所有与原材料,半成品,成品所接触到的部门,以及我司供应商。
三、定义错混料:原料物,半成品,成品中用错料或混料的现象统称为错混料。
四、职责4.1业务负责接到订单后将客户订单转化为内部订单责任确认单,并将信息传递至下单员录入系统。
4.2 技术部负责产品BOM的组成和材料性能确认选择。
4.3生产管理部负责下达排产任务单,原材料需求采购和监督任务执行。
4.4供应部依据计划提出的采购需求,进行保障到货。
4.5仓库负责原材料与成品的储存及管理(包括收发及5S管理)。
4.6质量部负责物料,半成品与成品的检验管理。
4.7生产部负责对生产中所有原材料,半成品与成品的管理和组织人员生产保证订单按期完成。
五、内容5.1.工艺文件错混料管理5.1.1技术部根据客户新产品、图纸、技术指标或工艺要求,注意图纸版本及产品技术指标细节,转换成我司的技术文件和现场工艺文件,进行受控和发行。
5.1.2专职人员统一管理技术文件,注意图纸编号,图纸版本,技术文件编号,技术文件版本,发行日期,发行换版编号,同时做好回收作废工作,放置图纸错误造成混料。
5.2业务接单/下单错混料管理5.2.1业务接收客户订单时候,经过评审后,将客户相关要求进行记录,按照唯一编号进行比对识别。
5.2.2业务下单时,将相关要求在销售订单责任确认单上进行注明,特别产品包装要求和生产注意事项,对于产品类型相似及包装方式相同的产品重点说明。
5.2.3.特殊产品:系统下单进行唯一编码进行识别,确保下单和系统录入;常规产品:正常系统下单,根据规格进行识别进行。
5.3模具错混料管理5.3.1模具仓库设有专人员管理,并做有专门记录,记录有模具类别,尺寸,领用机台,数量,做好明细登记和标识,同一机台最多两台。
5.3.2相关产品按照规定模具进行配模生产,管控规定。
5.4样品新生产时错混料管理5.4.1业务部接新产品(以从前未生产过)或客户产品变更消息时及时转交技术部,技术部根据业务提供的相关资料做成BOM,同时对材料选型确认指标规定做好规定和要求,供应部依据BOM进行厂家选择,材料选择,物料回来经质量部验收合格后进行入库。
生产部DIP车间物料防错防混管理规范
4.1.3各拉在物料交接及转拉过程中,各拉须安排助拉(物料员)进行操作,在周转时,物料的最小包装须标有物料编号,并要确认物料编号与BOM(或投料单)一致,同时所转接的物料按工单放置在周转箱中,并在周转箱贴上标识(标识产品名称、工单号、工单量)。
1、目的:
为防止生产部(DIP)车间制程过程中出现物料混料、用错物料,特制定此规范。
2、范围:
适用于生产部DIP车间。
3、定义:
3.1错料:生产过程中使用的物料与BOM单\SOP不符合出现的不良现象。
3.2混料:生产过程中同一物料盒内出现2种物料产产生产不良现象。
4、职责:
物料组长:负责物料员的电子元件的识别培训及领料过程中不出现领错料、周转过中的不出现混料。
4.1.8 IE在排工位时,体积、颜色、形状相似的物料不能排在一个工位作业,防止混料,要分开二个人作业,产线在作业时发现此类问题及时反应给IE,由IE修改SOP。
4.1.9下拉过时中如出现掉料的情况,非此位置的作业的人员不得进行补料,应及时向插件助拉或是拉长报告,助拉或是拉长将掉下的物料收集在不良品盒内,重新拿良品物料进行补料,补料时要对照SOP确认无误后补料。
4.2.3后焊段制程出现的少料及不良材料的更换按“修理作业规范”进行。
5、流程图:
无ቤተ መጻሕፍቲ ባይዱ
6、相关文件:
物料损耗控制管理规定PMWI-A-016
修理作业规范PEWI-A-007
制程检验作业规范QAWI-A-003
7、相关记录:
产品补(换)料记录表PRQR007
维修日报表PEQR017
4.1.4转线前由生产线助拉(或拉长)制作首件送检,首件经IPQC和工程PE确认合格后方可进行转线,如在确认中发现生产线送检的有用问题的现象,参照《制程检验作业规范》执行。
防错混料管理办法
1目的:为减少错料,混料产生,预防错料,混料外流而造成公司不必要损失,特制定此管制办法。
2范围:全厂生产各课、品质,仓库适用之。
3权责:3.1现场IPQC: 由IPQC组长监督执行。
3.2FQA: 由FQA组长监督执行。
3.3生产、仓库严格配合管理要求之工作, 由各单位组长级以上人员监督管理.4定义: 无5作业内容:5.1PMC课5.1.1安排生产计划时对易错混产品安排在不同拉生产。
5.1.2PMC课及时结单,对易混错物料及成品以客户订单号结单。
5.1.3PMC课依未来订单情形及物料结余数量拟定采购计划。
5.2技术部5.2.1设计易混错物料的识别标记并传达清楚。
5.2.2对易混错物料及成品的呆料做处置决定。
5.2.3解决易混错物料生产时的品质异常。
5.3品质部5.3.1进料IQC5.3.1.1查看物料规格、RoHS、卤素标示是否与材料本身规格相符。
5.3.1.2入库时品管监督,要求仓库按不同规格产品指定不同区域摆放.发料时,不清晰或不明确事项须经品管确认后执行。
5.3.2压铸,冲压,高光,CNC,批锋,镭雕,包装IPQC:5.3.2.1各生产单位到仓库领取原材料到车间, 须经IPQC确认品名,外观,尺寸OK方可进行生产。
5.3.2.2IPQC做首件检查或查机台时,对机台料架上产品也要进行巡查,对首件进行确认,避免员工因拿错料造成混料。
5.3.2.3批检时, 拿产品范围不可超出胶箱范围, 避免落入相邻箱内,造成混料。
5.3.2.4检验完毕后,认真填写好标示卡,并确认产品与标示卡一一对。
5.3.2.5批检时增加标示,每天由品管下班前30分钟内将机台号及品番写于标示卡上,以避免员工倒错箱造成混料。
5.3.2.6机台上,料架上或批检区抽到之少量不良品,须放置于红色不良品盒内。
下班时及时清理记录重量进行报废处理。
5.3.2.7当天生产相似产品,须用醒目标示卡,入库合箱时需对搬运人员进行监督,避免搬运人员入库时倒错箱。
车间预防混料及漏工序措施
16.物料如长时间不能流转到下道工序车间则必须按第1条和第2条执行,且用保鲜膜包缠好。
17.未按以上执行者第一次扣拉长助拉绩效5分,第二次10分,第三次取消当月绩效考核。
18.以上规定从8月28日起生效。
9.生产过程中生产完的产品放进吸塑盘时,打SPEAK孔的产品统一朝外以方便检查。
10.如拉上在同时生产多种类型的物料,则拉长必须指定一个助拉专门跟进预防混料和防止人为错失的发生。
11.如拉上在同时生产多种类型的物料,则拉长必须安排助拉或指定专人进行物料周转,非指定人员严禁进行物料周转。 12.如拉上在同时生产多种类型的物料,则拉长在生产前必须告之操作员具体的注意事项,每个人必须清楚生产类型、生产数 量。 13.生产过程中员工积极加强自检,凡是员工自检后的产品被发现有漏工序或者其它品质缺陷逃逸的发现一个产品扣当事人20 元,如在后道工序车间发现的,每发现一个扣专门负责漏工序预防的助拉20元及全检员20元。 14.生产完后必须按第3条及时标识相关信息并交接给下道工序,如要在车间存放由必须按第1序措施
1.未生产的物料与已经生产的物料严禁存放于同一卡板和同一放置区域,必须存放于不同的区域和不同的卡板。
2.生产过程中不管颜色是否相同,未生产和已经生产的物料都严禁存放于同一吸塑盘。
3.物料必须作好标识,标识清楚是否生产、是什么类型(DOE\EVT\LINE QUAL\量产等)、颜色、数量、规格等。
4.物料员领取物料必须弄清楚是什么类型,物料领取到车间后必须第一时间告之并交接给拉上的管理人员。
5.如不是第一时间生产而要存放一段时间则必须按第1条和第3条执行。
6.拉上管理人员安排物料员领取物料必须详细告诉物料员具体的领料信息(领什么料?什么颜色?多少数量?)。 7.生产过程中同一物料架、同一机台严禁存放两种类型的物料,必须生产完结一种类型的物料后才可以生产另一种类型的物料 。 8.生产过程中,已生产的物料与未生产的物料,必须按照具体的标识存放于物料架上指定的隔层,严禁已生产的物料隔层存放 未生产的物料和未生产的物料隔层存放已生产的物料。
- 1、下载文档前请自行甄别文档内容的完整性,平台不提供额外的编辑、内容补充、找答案等附加服务。
- 2、"仅部分预览"的文档,不可在线预览部分如存在完整性等问题,可反馈申请退款(可完整预览的文档不适用该条件!)。
- 3、如文档侵犯您的权益,请联系客服反馈,我们会尽快为您处理(人工客服工作时间:9:00-18:30)。
15.两个班交接必须按照第1条、第2条和第3条进行现场查看,当面确认无误后方可让上个 班的人员下班。
3.物料必须作好标识,标识清楚是否生产、是什么类型、颜色、数量、规格等。 4.物料员领取物料必须弄清楚是什么类型,物料领取到车间后必须第一时间告之并交接给 拉上的管段时间则必须按第1条和第3条执行。
6.拉上管理人员安排物料员领取物料必须详细告诉物料员具体的领料信息(领什么料?什 么颜色?多少数量?)。
10.如非PMC计划安排,拉上严禁同时生产多种类型的物料,如有生产则拉长必须指定一个 助拉专门跟进预防混料和防止人为错失的发生。
11.如拉上在同时生产多种类型的物料,则拉长必须安排助拉或指定专人进行物料周转,非 指定人员严禁进行物料周转。
12.如拉上在同时生产多种类型的物料,则拉长在生产前必须告之操作员具体的注意事项, 每个人必须清楚生产类型、生产数量。
16、产品检验工序人员在检验产品时,第一检验工序为是否漏工序,然后才是按标准检查 其它管控项目。
17.物料如长时间不能流转到下道工序车间则必须按第1条和第2条执行,且用保鲜膜包缠好 。 18、在流水线上,上一工段与下一工段之间必须设置挡板,以防止产品漏工序而流通。同 时禁止产品逆流。
19.未按以上执行者第一次扣拉长助拉绩效5分,第二次10分,第三次取消当月绩效考核。
7.生产过程中同一物料架、同一机台严禁存放两种类型的物料,必须生产完结一种类型的 物料后才可以生产另一种类型的物料。 8.生产过程中,已生产的物料与未生产的物料,必须按照具体的标识存放于物料架上指定 的隔层,严禁已生产的物料隔层存放未生产的物料和未生产的物料隔层存放已生产的物料 。 9.生产过程中生产完的产品放进吸塑盘或物料框内时,产品必须朝统一放置。
车间预防错、混、漏工序管理规定
文件名称
车间预防错混料管 理规定
文件编号 发行部门
生产部
页码 版本
2/2 A
一.目的: 1 预防物料、产品在转运过程中产生混料、错料
2 预防物料、产品在生产中产生混料或用错料的情况;
二操作说明: 1.未生产的物料与已经生产的物料严禁存放于同一卡板和同一放置区域,必须存放于不同 的区域和不同的卡板。 2.生产过程中不管颜色是否相同,未生产和已经生产的物料都严禁存放于同一吸塑盘。
20.以上规定从7月1日起生效。
三、相 关记录 表单:
1 物料标识卡
2 ERP单据
核准 日期
审核
制 作
日期
日 期