热处理工艺规范资料
热处理淬火工艺规范

热处理车间淬火工艺规范一、调质1.1 调质定义为了达到产品的工艺硬度要求,得到回火索氏体,得到良好的强韧性,提高使用性能和寿命,因此曲轴和连杆产品需进行调质处理。
调质,即淬火加高温回火,以获得回火索氏体组织,主要用于中碳碳素结构钢或低合金结构钢以获得良好的综合机械性能。
1.1.1 淬火的定义淬火是将钢加热到临界温度Ac3 (亚共析钢)或Ac1 (过共析钢)以上温度,保温一段时间,使之全部或部分奥氏体化,然后以大于临界冷却速度的冷速快冷到Ms以下(或Ms附近等温)进行马氏体(或贝氏体)转变的热处理工艺。
通常也将铝合金、铜合金、钛合金、钢化玻璃等材料的固溶处理或带有快速冷却过程的热处理工艺也称为淬火。
1.1.2淬火的目的淬火的目的是使过冷奥氏体进行马氏体或贝氏体转变,得到马氏体或贝氏体组织,然后配合以不同温度的回火,以大幅提高钢的刚性、硬度、耐磨性、疲劳强度以及韧性等,从而满足各种机械零件和工具的不同使用要求。
也可以通过淬火满足某些特种钢材的铁磁性、耐蚀性等特殊的物理、化学性能。
1.1.3回火的定义回火是工件淬硬后加热到Ac1 (加热时珠光体向奥氏体转变的开始温度)以下的某一温度,保温一定时间,然后冷却到室温的热处理工艺。
按回火温度范围,回火可分为低温回火、中温回火和高温回火。
4.1.1低温回火:工件在150~250C进行的回火。
目的是保持淬火工件高的硬度和耐磨性,降低淬火残留应力和脆性,回火后得到回火马氏体,指淬火马氏体低温回火时得到的组织。
应用范围:主要应用于各类高碳钢的工具、刃具、量具、模具、滚动轴承、渗碳及表面淬火的零件等。
4.1.2中温回火:工件在350〜500 C之间进行的回火。
目的是得到较高的弹性和屈服点,适当的韧性。
回火后得到回火屈氏体,指马氏体回火时形成的铁素体基体内分布着极其细小球状碳化物(或渗碳体)的复相组织。
应用范围:主要用于弹簧、发条、锻模、冲击工具等。
4.1.3高温回火:工件在500~650C以上进行的回火。
热处理通用技术规范及作业指导书
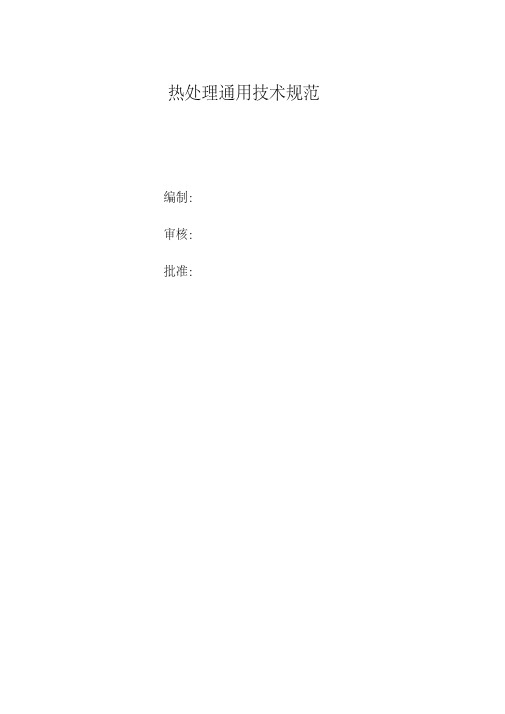
热处理通用技术规范编制:审核:批准:热处理通用技术规范1.目的为确保公司生产的产品符合产品标准技术要求,根据公司质量手册和程序文件的规定,特制定热处理通用工艺规范,用于指导热处理生产与过程控制。
2.适用范围本规范明确了热处理生产的主要工艺和质量控制方式、方法、要求,适用于石油机械API SPEC7K转盘及其配件产品的各种热处理。
属于本公司的其他产品和外协产品的热处理也可参照本规范的基本要求执行。
3.主要热处理工艺热处理是通过对工件的加热、保温和冷却,使金属或合金的组织结构发生变化,从而获得预期的性能的操作工艺。
热处理能最大限度的发挥材料潜力,改善和获得良好的机械性能、加工性能、物理性能和化学性能等。
热处理作为生产过程特殊工序,在石油机械产品生产制造中有重要作用。
可以分为:a.整体热处理与表面热处理整体热处理:如退火、正火、淬火、回火表面热处理:如感应加热表面淬火、火焰加热淬火以及化学热处理(如表面渗碳、碳氮共渗、氮化等)b.预先(或预备)热处理与最终热处理预先热处理一般是为了获得良好的加工性能而采取的热处理工艺,如时效、退火(包括去应力退火、球化退火等)、正火等,预先热处理有时也可以作为最终热处理。
一般用于焊接结构件、铸件等。
相对于最终热处理而言,某些重要、大截面钢件采用预先热处理(通常采用正火处理)是为使最终热处理产品有一个良好的组织保证。
3.1退火(Annealing)将钢件加热到Ac3+30~50度或Ac1+30~50度或Ac1以下的温度后,一般随炉温缓慢冷却。
主要是降低硬度,提高塑性,改善切削加工与压力加工性能;细化晶粒,改善力学性能,为下一工序做准备;消除冷、热加工所产生的内应力。
主要适用于合金结构钢、碳素工具钢、合金工具钢、高速钢的锻件、焊接件以及供应状态不合格的原材料,一般在毛坯状态进行退火。
按照要求目的的不同,退火可分为重结晶退火、等温退火、均匀化退火、球化退火、去除应力退火、再结晶退火以及稳定化退火等。
热处理工艺规范

➢ 本规范规定了本公司常用的金属的热处理 设备、工艺与质量检验方法
1
热处理工艺规范
目录
➢ 前言 1 规范范围 2 规范性引用文件 3 常用热处理方式定义 4 工艺分类代号 5 工件举例 6 热处理设备 7 工作要求 8 规范 9 热处理后工件的质量检验
2
热处理工艺规范
前言
本标准由技术部提出。 本标准由技术部起草。 本标准主要起草人:xx 本标准审核人:xx 本标准批准人:xx 本标准由技术部部归口并负责解释。 本标准于2019年10月首次发布,于2020年3月第一次修订。
14
热处理工艺规范
6 热处理设备 • 6.1 加热炉有效加热区实际温度偏差值(指炉罐内)
不应超过±20℃。 • 6.2 加热炉的每个加热区应配有温度测定及温度控制
自动记录装置。 • 6.3 加热炉的维护保养必须按制订的制度进行,并妥
善保管有关记录。
15
热处理工艺规范
7 工作要求 • 7.1 检查设备、仪表是否正常,并应事先将炉膛清理
干净。 • 7.2 核对材料与图样是否相符,了解零件的技术要求
和工艺规定。 • 7.3 选择好合适的工夹具,并考虑好装出炉的方法。
16
热处理工艺规范 8 规范 8.1 工艺的制定。应根据工件的特征(材料的牌号、处 理前的状态及形状、尺寸等)、热处理 目的、批量、热处理设备等具体条件来制定合理的热处 理工艺。 8.2 热处理工艺曲线见图1、图2
• 8.4 冷却时应以适当的速度,使工件各部分均匀冷 却。
• 8.5 如采用空冷,应在空气中散开冷却,不允许堆 放或置于潮湿的地上冷却。
20
热处理工艺规范 • 8.6 作为热处理后的辅助工序,清除工件的氧化皮
热处理工艺规范

材质淬火回火硬度(HRC) 备注SKD11、D2、2379、K340、XW-41、D11、DC11、DCm、QC11、K105、K110、SKD11、Cr12MoV1、SLD、GS-379 1020-1050 油冷或气淬,小件可空冷180-700 >60 回火脆性区:275-375500-525 58-60530-540 56-58540-550 54-56550-560 52-54570-580 50-5201、DF-2、SKS-3、K460、2510、9CrWMN、CrWMN 800-830油冷180-160 60-62 回火脆性区:250-330油钢180-220 58-60230-250 55-58310-350 50-55M2、SKH9、SKH51、YXM1、HSP41、S600、TS-3343、BM2、W6MO5Cr4V2 保温650(一段)950(二段)1180-1220(三段),预冷至950-1000下油或其它气体,小件可以空冷。
需要冷至40°C以下方可回火540 64-65 高速钢回火次数最好不少于4次560 62-64590 60-62610 58-60630 56-58650 54-56DC53、A88、SLD8、SLD10 1020-1050油淬或气淬、工件不厚可以风冷530-540 60-62 回火脆性区:450-510540-550 58-60550-560 55-58560-580 52-55580-600 50-521材质淬火回火硬度备注Cr12、XW-5、D3、SKD1、D6、CRD、TS-208、K107、K100、TS-2436、Cr12W 950-980油冷,回火温度要低20-30°C 180-200 59-61 回火脆性区:290-330200-280 58-60400-450 55-57500-530 52-55530-550 48-52560-590 45-46580-610 40-45PW类-767、738、638、718 870-920油冷200-250 50-54280-300 48-50320-360 46-48400-430 40-452083、440、S136 1020-1060油冷或者气淬。
热处理(调质)工艺规范

热处理工艺规范1 目的本规范适用于本厂钢制零件在周期作业加热炉中的调质、固熔工序。
2 准备工作2.1检查设备及仪表是否正常。
2.2检查零件上的材料是否符合图样要求。
2.3检查零件的尺寸是否符合图样及工艺文件的规定。
2.3.1调质件最好先经粗加工,断面大于100mm 的零件,当有内孔时,应钻孔后再调质,并且防止出现尖角。
2.3.2调质件的加工余量应大于允许的变形量。
2.4熟悉工艺要求,根据零件的毛坯重量、开头确定吊挂形式,吊挂部分可利用零件本身结构,也可在零件上另加。
2.5大型零件调质时必须检查所需的辅助冷却装置,当确认使用可靠后方可装炉。
2.6不同淬火温度的调质件,不得同炉处理,同炉处理件的有效厚度应相近。
3 工艺规范3.1 ASTM A350 LF2调质处理规范见表1。
3.1.2机械性能参数:MPa b 655485-=σ MPa 250≥s σ 22%≥δ 30%≥Φ3.1.3 LF2低温冲击韧性K A 要求:Ⅰ级 试验温度在-45.6℃ 三个试样平均值为K A ≥20J三个试样中一个试样冲击值为K A ≥16JⅡ级 试验温度在-18℃ 三个试样平均值为K A ≥27J三个试样中一个试样冲击值为K A ≥20J3.2 ASTM A182 F316、F321钢3.2.1 热处理工艺:3.2.2 机械性能参数:MPa b 515=σ MPa 205≥s σ 30%≥δ 50%≥Φ3.3 淬火冷却方法3.3.1调质件采用的淬火介质一般为水或油。
3.3.2形状简单、断面厚度不足100mm 的零件在水或油中冷却,终冷温度不予限制,以淬硬为原则。
3.3.3形状复杂、断面厚度大于100mm 的零件在淬火介质中冷至表面温度为150-200℃时取出空冷。
3.3.4采用水淬油冷的零件,水冷时间按每(3-5)mm 以1s 计算,水淬空冷的零件、水冷时间,当有效厚度小于30毫米的以S/2mm 计算,有效厚度大于30mm 的以S/1mm 计算的。
(完整)热处理工艺守则

一、热处理代号和材料标注方法(一)热处理代号1. 适用于结构钢和铸件代号:0—自然状态1—正火(或正火+回火)2—退火3—精锻+回火(如精锻或精辊叶片在精锻后只需高温回火)4—淬硬5—调质6—化学热处理(渗碳或氮化)7—除应力(包括活塞环定型处理)9—表面淬火或局部淬火2.适用铸造有色金属和奥氏体钢的代号:0—原始状态1—再结晶退火T—除应力退火T1-人工时效T4—淬火(固溶处理)T5—淬火和不完全时效T6-淬火和完全时效(固溶处理和完全时效到最高硬度)3.压力加工有色金属代号:0—原始状态M—退火C-淬火CZ—淬火和自然时效CS-淬火和人工时效(二)材料的标注方法:1.零件的材料或毛坯(包括铸锻件)如不作任何处理,也不作机械性能检查,则只标材料牌号(其热处理代号“0”在图纸上不标注)如:A3,20,35,ZQSn6—6-3。
2.零件的材料或毛坯在热处理后,不作硬度及机械性能检查者则只标注材料牌号和热处理代号:如:45-1,若有几种热处理,可用热处理代号按工艺路线顺序逐项填写:如:15CrMoA-1+7。
3.有些材料的技术条件,有几种检查组别,但强度等级只有一种或可按材料截面尺寸来决定强度等级,只注明材料牌号,热处理代号和检查组别:如:45—5(Ⅱ) 35CrMoA—5(Ⅱ)4.有些材料的技术条件,有几种组别,在同一热处理状态中有不同的强度等级,则注明材料牌号、热处理代号强度等级和检查组别,不需要规定检查组别时,检查组别可省略。
25Cr2MoVA-5 25Cr2MoVA-5如:735—Ⅲ 7355。
有些零件或者是比较重要或者是技术要求比较复杂,用上述标注方法不能说明全部要求者,则应注明标准号,在同一热处理状态中有不同的强度级别时,还应注明强度级别。
35CrMoA-5 35CrMoA-5如:Q/CCF M 3003-2003 590×Q/CCF M 3003—20036。
大锻件如叶轮、铸造轴、整体转子等的材料标注方法钢号锻件级别×标准编号7。
热处理工艺规范
ZX/JS-007江苏新中信电器设备有限公司热处理工艺规范编制:审批:二零一三年三月江苏新中信电器设备有限公司热处理工艺规范ZX/JS-0071 目的对零部件消除应力,改善材料或零件机械性能的热处理质量实施控制,以保证热处理符合技术条件的要求。
2适用范围本规范适用于本厂钢制零件在周期作业加热炉中的调质、固熔工序。
3准备工作3.1检查设备及仪表是否正常。
3.2检查零件上的材料是否符合图样要求。
3.3检查零件的尺寸是否符合图样及工艺文件的规定。
3.3.1调质件最好先经粗加工,断面大于100mm的零件,当有内孔时,应钻孔后再调质,并且防止出现尖角。
3.3.2调质件的加工余量应大于允许的变形量。
3.3.3不同淬火温度的调质件,不得同炉处理,同炉处理件的有效厚度应相近。
4 工艺规范4.1 技术部根据标准、工艺规程、材料和设计技术条件,负责编制热处理工艺规程。
4.2 热处理工艺规程至少应包括以下内容:a)热处理工件的材料牌号b)热处理设备及热处理种类(调质、固溶等)c)热处理工艺参数(升温、保温、出炉温度、回火温度及各温度段的加热时间等)和工艺曲线图。
d)冷却方法及冷却介质。
4.3 消除应力热处理后一般不得再进行焊接补焊。
否则应重新进行热处理。
4.4 ASTM A276 410或420调质处理(详见附录1)规范见表1。
表14.4.1机械性能参数:≥550MPa 。
Rm ≥690MPa ; Rp0.24.5 ASTM A276 410或420淬火处理(详见附录2)规范见表2。
表24.6 ASTM A182 F304、F316、F321钢固溶处理(详见附录3)规范见表3。
表34.6.2 机械性能参数:≥205MPa A%≥30 Z b%≥50 Rm≥515Mpa Rp0.24.7 淬火冷却方法4.7.1调质件采用的淬火介质一般为水或油。
4.7.2形状简单、断面厚度不足100mm的零件在水或油中冷却,终冷温度不予限制,以淬硬为原则。
热处理工艺规范
淬火加热 1060~1070oC
6)不同类型的零件在淬火冷却过程中应遵守下列原则:
轴、套筒、圆环类零件:应沿轴心方向垂直进入冷却剂,并在冷却剂中上下窜动。
垫圈类零件:应径向垂直进入冷却剂。 长板类零件:选择横向侧面进入冷却剂为好。
有盲孔凹面的零件:盲孔凹面向上进入冷却剂。
1060 ~1070 风冷
510~ 520
56~ 60
550~ 560
48~ 52
200~ 220
58~ 62
1020 ~1040
油
500~ 520 520~ 530 560~ 580
55~ 58 54~ 56 44~ 48
820~ 840
油
19空淬火炉淬火风冷,回 火两次。
核对温度仪表,正确执行工艺;改 变或搅拌冷却介质;严格检查原材 料,改进预先热处理; 采取保护加热。
加热温度过高;原始晶粒太大。
严格控制温度;进行预先热处理。
变形与 开裂
原材料组织不均匀, 有冶炼金属缺陷; 加热 温度过高; 冷却太快或不均; 零件的结构形状 复杂; 二次淬火前未经正火或退火处理; 未及 时回火或回火不充分。 合金工具钢锻件, 锻造 比小:材质内碳化物严重,锻打时没击碎。
第4 页 共6 页
四川华林设备有限公司
却不允许堆放或置于潮湿的地上冷却,大件或要求硬度高的零件方可在流动空气中或其它介
质中冷却。
3.加热设备:退火、正火主要采用箱式炉,必要时可选用真空炉。
4.操作方法
1)零件装炉时,必须放置在预先确定的有效加热区内,装置量、装炉方式及堆放形式的
确定应以保正零件均匀加热和冷却,且不造成有害缺陷的原则;装箱退火时,箱间距离应大
WCB铸件热处理制度及工艺规范
WCB铸件热处理制度及工艺规范(常规)根据客户要求。
对铸件(毛坯)进行退火、正火、正火+回火等热处理。
热处理工艺规范(见表)工艺名称退火正火正火+回火加热温度880-920°C940-960°C940-960°C620-680°C保温时间0.5-1h/25mm至少1h0.5-1h/25mm至少1h0.5-1h/25mm至少1h25mm/1h冷却炉冷至450°C后出炉空冷空冷空冷铸钢件焊后去应力退火加热温度600-650°C 保温1h / 25mm 空冷。
装炉温度及升温要求1、室温或者400°C以下装炉,升温至500-600°C时保温1-2h,再升温。
2、升温速率100-200°C / h,随炉冷却速率100-200°C / h。
装备(设备及设施)1、采用台车式电阻加热炉,必要时配备机械鼓风冷却。
2、温度控制采用带程序控制的PID调节器进行控温。
六、操作要求1、所有铸件在热处理前,应清砂、切冒口、清理铸件表面、对裂纹等缺陷进行补焊。
且化学成分必须检验合格、外观目视检验合格。
同时应带有同铸件冶炼炉次相同的标号的试棒。
2、铸件应放置在加热炉有效加热区内。
同炉处理的铸件壁厚相差不应太大。
在铸件加热时不至于产生变形的前提下,允许多层叠放。
试棒应和其所代表的铸件同炉进行热处理,并放置在具有代表性的位置。
3、严格执行热处理工艺规范。
加热过程中应确保温度测量、控制和记录装置的正常运行。
铸件热处理后,应按相关标准规定的检验方法检验。
浙江方文特钢有限公司2014年1月15日。
热处理工艺规范
加热炉类别
有效加热区精度℃
控温精度℃
记录仪表精度%
记录纸刻度℃/mm
Ⅰ
±3
±1
0.2
≤2
Ⅱ
±
±10
±5
0.5
≤5
Ⅳ
±15
±8
0.5
≤6
Ⅴ
±20
±10
0.5
≤8
Ⅵ
±25
±10
0.5
≤10
注:允许用修改量程的方法提高分辨力。
依据相关热处理工艺标准,具体热处理工艺对加热炉技术要求,见下表:
淬火后回火时间间隔要求与回火脆性防止:
6.3.3所有零件为了防止淬火过程中的应力造成开裂,必须在淬火后8小时内进行回火。
6.3.4淬火钢回火时,随着回火温度升高,其冲击韧性总的趋势是增大。但有一些钢在
一定温度范围回火后,冲击韧性反而比在较低温度回火后显著下降。这种在回火过程中发生的脆性现象,称为回火脆性。常见的回火脆性可分为低温回火脆性和高温回火脆性。
3、检验方式:抽检
抽检数量按每批产品的3%,但不得少于3件
4、判定准则:
同一试件不合格项目有两项或两项以上时,则直接判定该批产品出厂检验为不合格;有一项不合格项目者,则对该项加倍检验,如仍不合格,则该批产品出厂检验为不合格。
5、加热设备及仪表要求:
5.1加热设备要求:
5.1.1加热炉需按有效加热区保温精度(炉温均与性)要求分为六类,其控温精度、仪表精度和记录纸刻度等要求,见下表:
±2.5或0.75%t
备注
1、t为测量温度:℃2、允许按实际需要缩短检定周期。
6、热处理过程要求
6.1原材料要求:
原材料的冶金质量对热处理质量影响很大,如钢中非金属夹杂物、白点、带状组织、严重的碳化物偏析、发裂等,不仅在热处理时易形成畸变开裂、硬度不足、软点等,而且对使用性能及使用寿命影响也很大;在材料管理上操作不规范(未作材料标识、使用前未作火花鉴别等),造成混料、错料或非法材料代用等也是产生热处理不合格的主要原因,为此,必须做到要求如下:
- 1、下载文档前请自行甄别文档内容的完整性,平台不提供额外的编辑、内容补充、找答案等附加服务。
- 2、"仅部分预览"的文档,不可在线预览部分如存在完整性等问题,可反馈申请退款(可完整预览的文档不适用该条件!)。
- 3、如文档侵犯您的权益,请联系客服反馈,我们会尽快为您处理(人工客服工作时间:9:00-18:30)。
热处理工艺规范
一、淬火、回火工艺规范
1.淬火、回火准备工作:1)检查设备,仪表是否正常;2)正确选择夹具;3)检查零件表面是否有碰伤、裂纹、锈斑等缺陷;4)确认零件要求的淬火部位硬度、变形等的技术要求,核对零件的形状、材料的加工状态是否与图样及工艺文件相符合;5)表面不允许氧化、脱碳的零件,当在空气炉加热时,应采取防氧化脱碳剂装箱保护或采用真空炉加热;6)易开裂的部位如尖角靠边的孔,应采取预防措施,如塞石棉、耐火泥等。
2.常见材料淬火、回火工艺规范
1)加热温度
表1 常用材料的常规淬火、回火规范
注:Cr12Mo1V1 即 D2(美国)、1.2379(德国)、SLD(日立)、SKD11(日本)、K110(奥地利);
9CrWMn 即 O1(美国)、1.2510(德国)、K460(奥地利);
4Cr5MoSiV1 即 H13(美国)、1.2344(德国)、8407/8402(一胜百)、W302(奥地利);
7Cr7Mo3V2Si 即 LD1;
HS-1是高级火焰淬火,多用模具钢;
除45号钢或特别说明均采用回火两次的工艺。
2)淬火保温时间t =8~10 min+kαD
k——装炉系数(1~1.5);α——保温系数(见表2);D——零件有效厚度。
表2 淬火保温系数
3)回火保温时间
①工件有效厚度d<=50mm,保温2小时;
②工件有效厚度d>50mm,按照保温时间t=d/25(小时)计算;
③每次回火后空冷至室温,再进行下次回火。
4)去应力(入炉时效)
①高合金钢550~650℃,热透后,保温时间>3小时;
3.淬火和回火设备
1)淬火设备——真空淬火炉、中温箱式炉、高温箱式炉。
2)回火设备——真空回火炉、中温箱式炉。
3)冷却设备——水槽、油槽、风箱。
4.操作方法
1)零件应均匀摆放于炉内有效加热区,在箱式炉中一般为单层排列加热,工件间适当间隙。
小件可适当堆放,但要酌情增加保温时间。
2)细长零件加热要考虑装炉方法,以减少工件变形,如垂直吊挂,侧立放平支稳等。
3)零件同炉加热,截面尺寸不宜相差过大,厚度10~50mm同一炉,50~80mm同一炉,大截面零件应摆放在炉膛里面,以便小工件先出炉。
大小零件分别计算加热时间(仅指箱式炉)。
4)高合金钢及形状复杂的中小截面零件,应在550~650℃装炉,并经预热保温后,才能进行升温加热。
5)高温合金钢零件要经过一次或两次预热,才能加热淬火(见下图)。
淬火加热
1060~1070o C
6)不同类型的零件在淬火冷却过程中应遵守下列原则:
轴、套筒、圆环类零件:应沿轴心方向垂直进入冷却剂,并在冷却剂中上下窜动。
垫圈类零件:应径向垂直进入冷却剂。
长板类零件:选择横向侧面进入冷却剂为好。
有盲孔凹面的零件:盲孔凹面向上进入冷却剂。
截面厚薄相差较大的零件:大截面部分应先进入冷却剂。
带单面长槽的零件:应槽口向上,一端倾斜45°进入冷却剂。
7)淬火后应及时回火,一般零件淬火至回火不超过4小时,大型或复杂易裂零件应立即回火。
8)返修的零件在重淬前一般需经高温回火或正火处理;合金工具零件应退火处理。
9)有淬裂危险的零件,在淬火冷却至50~80℃即应入炉回火。
10)需多次回火的零件,每次回火均应冷至室温。
11)凸、凹模和成形零件等硬件主要进真空炉热处理,真空度<=2.66Pa。
以防氧化、脱碳。
5.常见的缺陷及解决的办法
表3 淬火缺陷原因及解决办法
缺陷特征产生原因解决方法
二、退火与正火工艺规范
1.准备工作
1)检查设备,仪表是否正常,并应事先将炉膛清理干净;
2)核对物料与图样是否相符,了解零件的技术要求与工艺规范;
3)正确选择工装夹具,确定出炉方法;
4)对不允许表氧化,脱碳的零件,应采用进行防氧化脱碳剂保护或真空炉处理。
2.工艺规范:1)加热温度
表4 常用钢退火工艺规范
表5 常用钢材的正火温度
2)保温时间:电炉加热的保温时间 = 零件有效厚度×保温系数
表6 退火、正火保温系数
3)冷却速度
碳素钢退火应以不大于100~200℃/h的冷却速度冷至500~550℃后空冷。
合金钢及高合金退火应不大于20~100℃/h的冷却速度冷至500~550℃后室冷,正火应在空气中散开冷
却不允许堆放或置于潮湿的地上冷却,大件或要求硬度高的零件方可在流动空气中或其它介质中冷却。
3.加热设备:退火、正火主要采用箱式炉,必要时可选用真空炉。
4.操作方法
1)零件装炉时,必须放置在预先确定的有效加热区内,装置量、装炉方式及堆放形式的确定应以保正零件均匀加热和冷却,且不造成有害缺陷的原则;装箱退火时,箱间距离应大于100mm。
2)装炉后需要检查零件与电热原件确无接触时,方可送电升温,在操作过程中,不得随意打开炉门。
3)零件的升温速度主要根据化学成份,几何形状等因素来确定,对于高碳,高合金钢断面较大或形状复杂的零件,以及装箱退火零件,应采用低温装炉,加热到500~550℃保温一段时间后再加热到规定的温度。
4)保温时间从炉温达到规定的温度算起,但装炉量大时,应适当延长,对于装箱退火,通常应增加2~3h。
5)对于易变形件,装炉时应注意,支平放稳。
5.常见缺陷及解决方法:
三、火焰淬火工艺
1.准备工作
1)检查乙炔,氧气瓶的压力是否符合要求;
2)检查零件是否与图样及文件及工艺文件相符,表面不得有氧化皮、毛刺等;
3)适用于火焰淬火的材料是:含碳量在0.3~0.6%碳素钢最适宜,以及碳含量为0.3~
0.5%的低合金钢。
在表面淬火前,为了获得良好的淬火质量,一般先进行正火和调质处理得到细晶粒的索氏体加铁素体或回火索氏体组织。
2.工艺规则
1)气体压力与流速:压力过低会造成淬火表面硬度过低,压力过大会引起火焰跳动,一般情况下氧气压力取0.5~0.8Mpa乙炔气的压力取0.005~0.007Mpa;
2)混合气的比例通常为氧:乙炔 =(1.1:1)~(1.57:1),这样即为中性火焰;
3)喷火器应与零件表面垂直,距冷却水的距离应为10~40mm;
4)零件加热温度一般为880~900℃,目测时呈现樱红色即可淬火;
5)对含碳量0.6%以下的碳钢用15~25℃的水冷却,碳含量大于0.6%的碳钢和含铬及锰的低合金钢用30~40℃的水与空气的联合冷却,部分高合金钢可以空冷;
6)对于易产裂纹的工件,淬火后应及时回火;
7)H S-1火焰淬火:中性焰,火焰长度10~15mm距刃口边缘4~6mm,加热带8~12mm (单喷嘴)12~20mm(双喷嘴);氧气压力49~69N/mm,乙炔压力4.9~6.9N/mm,可经火焰预热180~200℃,1~1.5小时,淬火加温900~1000℃(目测);空冷,一般模具淬火后可用火焰回火,回火后表面硬度50~60HRC,淬硬层3~4mm。
3.常见缺陷及解决办法:
四、热处理工人自检要求:
1.热处理前仔细消化图纸和工艺要求,检查工件是否和图纸符合,零件表面有无裂纹等;2.检查所用设备、仪表是否正常,能否满足工艺要求;
3.根据图纸要求和通用工艺规范确定零件的加热工艺参数(温度、时间),并随时检查仪表显示是否符合预定工艺;
4.工件在热处理工艺完成后自检内容:
1)外观:在工件表面不能有裂纹及伤痕等缺陷,按热处理工件数量100%自检;
2)表面硬度:表面硬度自检一般安排在第一次回火后进行,按热处理工件数量大小进行抽检,检测方法按《金属洛氏硬度试验法》的规定进行,未抽检的工件,用刀100%检查;
3)变形:淬火、回火工件的变形应不影响以后的机械加工和使用,允许变形量见下表:
4)变形量采用平尺、塞尺组合测量;
5)对于有特殊要求的工件应进行金相检测、探伤检测。
5.自检过程中发现不符合图纸及工艺要求,应通知现场工艺员做出处理意见,不准许流入下工序。