制造质量1
一锻造过程质量控制
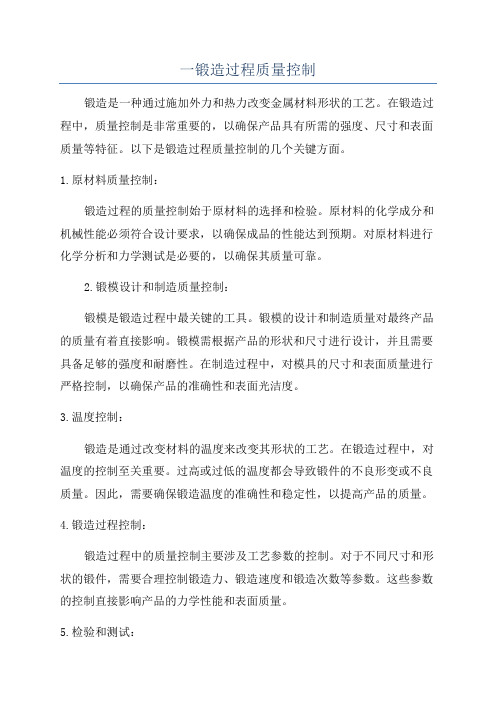
一锻造过程质量控制锻造是一种通过施加外力和热力改变金属材料形状的工艺。
在锻造过程中,质量控制是非常重要的,以确保产品具有所需的强度、尺寸和表面质量等特征。
以下是锻造过程质量控制的几个关键方面。
1.原材料质量控制:锻造过程的质量控制始于原材料的选择和检验。
原材料的化学成分和机械性能必须符合设计要求,以确保成品的性能达到预期。
对原材料进行化学分析和力学测试是必要的,以确保其质量可靠。
2.锻模设计和制造质量控制:锻模是锻造过程中最关键的工具。
锻模的设计和制造质量对最终产品的质量有着直接影响。
锻模需根据产品的形状和尺寸进行设计,并且需要具备足够的强度和耐磨性。
在制造过程中,对模具的尺寸和表面质量进行严格控制,以确保产品的准确性和表面光洁度。
3.温度控制:锻造是通过改变材料的温度来改变其形状的工艺。
在锻造过程中,对温度的控制至关重要。
过高或过低的温度都会导致锻件的不良形变或不良质量。
因此,需要确保锻造温度的准确性和稳定性,以提高产品的质量。
4.锻造过程控制:锻造过程中的质量控制主要涉及工艺参数的控制。
对于不同尺寸和形状的锻件,需要合理控制锻造力、锻造速度和锻造次数等参数。
这些参数的控制直接影响产品的力学性能和表面质量。
5.检验和测试:在锻造过程中,对产品进行检验和测试是保证质量的重要手段。
通常使用的检验方法包括尺寸测量、化学分析、力学性能测试和金相分析等。
这些检验和测试手段需要根据产品的特点和要求进行选择,以确保产品符合设计要求和标准。
6.质量记录和追溯:在完成锻造工艺后,需要对产品的质量进行记录和追溯,以便后期的质量检验和追溯。
质量记录包括各道工序的操作记录、检验记录和测试数据等。
追溯体系可以确保产品的质量问题可以溯源,并及时采取纠正措施。
在锻造过程中,质量控制是一个全过程的工作。
通过严格控制原材料质量、锻模设计和制造质量、温度控制、锻造过程控制、检验和测试,以及质量记录和追溯等措施,可以有效提高锻造产品的质量和稳定性。
5机械制造质量分析与控制1
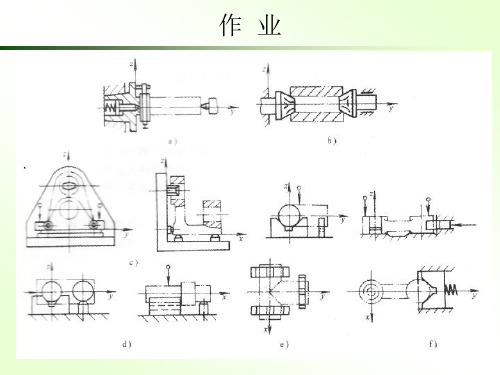
5.工艺系统刚度对加工精度的影响
(1)工艺系统刚度变化引起的误差
y系统
yx
y刀架
Fy
1 k刀架
1 (l k 头座
x )2 l
k
1(
尾座
x l
)2
k系统
Fy y系统
1
1 1 (l x)2
1 ( x)2
k刀架 k头座 l
k尾座 l
5.工艺系统刚度对加工精度的影响
(2)切削力变化引起的误差
➢ 通常要求定位误差和夹具 制造误差不大于工件相应 公差的1/3。
31
三、 调整误差
试切法(图 a)
➢ 测量误差。 ➢ 试切时与正式切削时切削厚度
不同造成的误差。 ➢ 机床进给机构的位移误差。
调整法(图 b)
➢定程机构误差。 ➢样件或样板误差。 ➢测量有限试件造成的误差。
a)
b)
试切法与调整法
32
通常将机械制造质量分成加工精度和 表面质量两个方面来研究。
第一节 机械加工精度
一、基本概念
1.加工精度与加工误差
加工精度指零件加工后的实际几何参数( 尺寸、形状和位置)与理想几何参数的符合程 度。
零件加工后的实际几何参数对理想几何参 数的偏离程度,称为加工误差。
提高加工精度意义重大。对于特定产品只 要求满足规定的公差要求即可。
作业
第五章 机械制造质量分析与控制
产品质量
指用户对产品的满意程度。
• 产品质量包括范围
产品的设计质量; 产品的制造质量; 产品售后服务质量。
第五章 机械制造质量分析与控制
机械制造质量组成
1 零件几何精度
零件几何误差,包括尺寸误差、几何形 状误差和位置误差。
船舶制造质量检验[1]
![船舶制造质量检验[1]](https://img.taocdn.com/s3/m/0bc8213b87c24028915fc34a.png)
船舶建造质量检验内容简介本书系统地阐述了船舶建造质量检验的原理和方法。
内容包括:质量检验概论,以及船用材料、船体、船装、机装、电装、涂装、内装和试验等方面的检验方法和接受准则。
全书共由十一章组成:第一章概论,第二章船用金属材料检验,第三章船体建造检验,第四章船体舾装检验,第五章管系制造和安装检验,第六章轴系及螺旋桨制造和安装检验,第七章柴油机和辅机安装检验,第八章电气系统安装检验,第九章涂装和内装检验,第十章系泊试验,第十一章航行试验。
本书可供船舶质量检验人员,设计和工艺师、验船师、监理人员,工程管理人员使用,也可供专业人员作为培训教材和工作参考书。
第一章概论第一节质量检验的概念和历史一.质量检验的历史二.船舶的入级、法定和监督检测三、质量检验方面的术语第二节质量检验过程一.质量检验活动和职能二.质量检验的实施三.不合格品的控制和纠正措施四、质量问题的处理第三节质量检验组织一.质量检验部门的设置二.质量检验人员的配置第二章船用金属材料检验第一节概述一、材料检验的基本要求二、材料复检的程序和内容第二节钢材检验一、钢板和型钢检验二、钢管检验第三节焊接材料检验一、概述二、焊接材料的检验程序三、电弧焊条检验四、埋弧自动焊焊丝和焊剂检验五、电焊条保管第四节铸钢件和锻钢件检验一、铸钢件检验二、锻钢件检验第三章船体建造检验第一节放样和号料检验一、放样检验二、号料检验第二节零件和部件检验一、零件检验二、部件检验第三节分段制造检验一、胎架检验二、划线检验三、平面和曲面分段检验四、立体分段检验五、分段完工检验第四节船台装配检验一、分段预修整检验二、船台基准线检验三、分段安装检验第五节焊接质量检验一、焊缝的焊前检验二、焊缝的焊接规格和表面质量检验三、焊缝内部质量检验第六节船体密性试验一、船体密性试验要求二、船体密性试验方法和标准三、船体密性试验条件和程序第七节船体完工检验一、船体主尺度和外形检验二、船舶载重线标志与吃水标志检验三、船体下水前的完整性检验第八节船体建造精度标准和偏差许可一、船体建造精度标准类别与说明二、船体建造偏差许可和修复工艺第四章船体舾装检验第一节舵系制造和安装检验一、舵叶制造检验二、舵系零部件机械加工和装配检验三、舵系安装检验第二节锚泊及系泊设备安装检验一、锚、锚链和锚机安装检验二、系泊设备安装检验第三节舱口盖、桅和门窗及其它舾装件检验一、钢质水密货舱口盖检验二、桅、起重柱和吊货杆检验三、门、窗、盖及其它舾装件检验第五章管系制造和安装检验第一节概述一、管子的分类和等级二、管子材料第二节管子制造检验一、弯管检验二、校管和焊缝检验三、管子及附件液压试验第三节管子表面处理检验一、管子酸洗检验二、管子支架、垫床和色标检验三、管子安装检验和密性试验第六章轴系及螺旋桨制造和安装检验第一节螺旋桨、轴和尾轴管加工检验一、螺旋桨锥孔加工检验二、轴加工检验三、轴系拉线检验四、轴系中心线的定位检验五、尾轴管镗孔检验六、尾轴管前后轴承加工检验第二节轴系安装检验一、尾轴管前后轴承安装检验二、螺旋桨轴安装检验三、螺旋桨安装检验四、尾轴管理管封装置安装检验五、轴系安装检验六、轴系连接螺栓安装检验第三节侧推装置安装检验一、概述二、侧推装置安装检验程序第七章柴油主机和辅机的安装检验第一节柴油主机安装检验一、主机基座加工检验二、主机机座安装检验三、曲轴安装检验四、机架、气缸体和扫气箱安装检验五、贯穿螺栓安装检验六、活塞组、十字头和连杆等部件安装检验七、气缸盖(头)安装检验八、时规齿轮或链条安装检验九、柴油主机安装完工检验十、柴油主机整机安装检验第二节柴油发电机组和辅机安装检验一、柴油发电机组安装检验二、辅机安装检验三、通海阀和舷旁阀安装检验第八章电气系统安装检验第一节电气舾装件安装检验一、支承舾装件安装检验二、电缆贯通件安装检验第二节电缆敷设检验一、电缆敷设完工检验二、电缆贯通件密封性检验第三节电气接线和设备安装检验一、电缆接线检验二、电缆管和屏蔽罩等构件接地检验三、电气设备安装检验第九章涂装和内装检验第一节涂装检验一、钢材预处理检验二、二次除锈检验三、涂层检验第二节内装检验一、绝缘敷设检验二、甲板敷料敷设检验三、舱室内壁和顶板安装检验四、舱室完整性检验第十章系泊试验第一节主机和轴系系泊试验一、投油清洗检验二、动力系统泵的试验三、主机保护装置试验四、主机报警装置试验五、集控台主机报警点试验六、主机起动及换向试验七、主机和轴系系泊运转试验第二节柴油发电机组和配电板试验一、发电机组和配电板绝缘电阻测量二、柴油发电机组起动试验三、安全报警装置试验四、主配电板保护装置试验五、柴油发电机组负荷试验六、柴油发电机特性试验七、柴油发电机并联运行试验八、配电板联锁试验第三节甲板机械及各类辅机试验一、锚机系泊试验二、舵机系泊试验三、救生设备试验四、起得设备试验五、水密门、窗和风雨密小舱口盖密性试验六、舷梯、引航员舷梯及机械升降机试验七、空气压缩机及系统试验八、燃油锅炉试验九、燃油和滑油分油机试验十、制淡装置试验十一、焚烧炉试验十二、舱底油水分离器试验十三、生活污水处理装置试验十四、系缆及拖曳设备试验十五、机舱行车试验十六、集装箱堆装试验十七、传令设备试验第四节船舶系统试验一、泵及系统的效用试验二、灭火系统和消防设备试验三、冷藏装置试验四、空调装置试验五、通风系统试验第五节电气设备试验一、试验的一般过程二、充放电板与蓄电池检验三、应急切断系统试验四、照明设备及专用灯具试验五、船内通讯和信号装置试验六、雾笛、刮水器及扫雪器试验七、无线电设备试验八、助航设备试验第六节倾斜试验一、试验条件的检查二、试验的实施第十一章航行试验第一节航行试验的条件一、概述二、航行试验的准备工作第二节船舶性能试验一、航速测定二、停船试验三、回转试验和初始回转试验四、Z型操纵试验五、威廉逊(Willamson)溺水救生试验六、航向稳定性试验七、侧向推进器试验八、船体振动试验九、机械设备振动试验十、轴系振动试验十一、船舶噪声试验第三节主机、轴系和其它装置试验一、主机和轴系试验二、废气锅炉试验三、海水淡化装置试验四、操舵试验五、抛锚试验第四节航海和通讯设备试验一、航海设备试验二、无线电通讯设备试验第五节船舶自动化系统试验一、机舱集控台检测报警试验二、自动电站试验三、泵的自动转换试验四、主机遥控试验五、机舱自动化试验第一章概论第一节质量检验的概念和历史一、质量检验的历史质量检验,包括船舶检验,作为一项管理手段,它是随着生产力和科学技术水平的提高而产生、发展起来的。
压力容器制造质量方针和质量目标
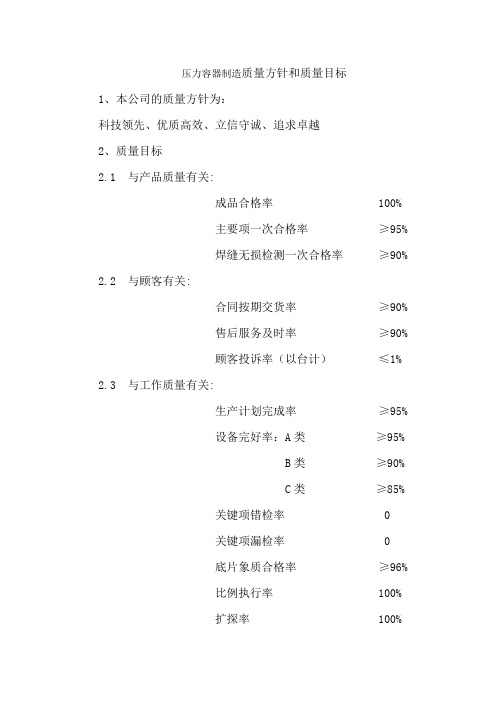
压力容器制造质量方针和质量目标1、本公司的质量方针为:科技领先、优质高效、立信守诚、追求卓越2、质量目标2.1 与产品质量有关:成品合格率 100%主要项一次合格率≥95%焊缝无损检测一次合格率≥90% 2.2 与顾客有关:合同按期交货率≥90%售后服务及时率≥90%顾客投诉率(以台计)≤1% 2.3 与工作质量有关:生产计划完成率≥95%设备完好率:A类≥95%B类≥90%C类≥85%关键项错检率 0关键项漏检率 0底片象质合格率≥96%比例执行率 100%扩探率 100%底片评定准确率≥95%工艺纪律执行率≥98%2.4 与改进有关:每年进行一次质量管理评审和改进并有效实施。
产品工艺方法每年寻找1-2个改进点并有效实施。
3、目标分解3.1 营销部3.1.1 合同按期交货率≥90%(按季统计)。
3.1.2 售后服务及时率90%。
3.1.3 顾客满意度问卷调查回收率大于60%。
3.2 生产部3.2.1 生产计划完成率(按月)≥95%。
3.2.2 成品一次合格率为100%、主要项一次合格率≥95%、焊缝无损检测一次合格率≥90%。
3.3 技术部3.3.1 工艺方法每年寻找1-2个改进点。
3.4 质检部3.4.1 关键项错漏检率为0。
3.4.2 底片象质合格率≥96%,X射线检测比例执行率100%,X 射线探测扩探率100%,底片评定准确率≥95%。
3.4.3 顾客现场质量问题及时服务率90%。
3.5 设备计量科3.5.1设备完好率:A类≥95%,B类≥90%,C类≥85%。
3.6 质管办3.6.1 协助质保工程师组织有关人员对质量管理体系每年进行一次质量管理评审。
3.6.2 每年各层次人员培训面应大于90%。
3.6.3 工艺纪律执行率≥98%。
一台钢琴的寿命

一台钢琴的寿命
一架钢琴的寿命与多种因素有关,例如制造质量、使用频率、环境条件和维护状况等。
一般来说,一架高质量的钢琴在正确的使用和维护下,可以持续使用超过100年。
以下列举一些影响钢琴寿命的一些因素:
1.制造质量:一架优质的钢琴制作精良、材质优良,其零件和配件
也都非常耐用,可以保证钢琴的长期使用。
2.使用频率:频繁使用钢琴也会加速钢琴的磨损和老化。
如果钢琴
每天都被弹奏多个小时,其寿命可能会比使用较少的钢琴短。
3.环境条件:钢琴需要放置在通风、湿度合适、温度稳定的环境中。
如果钢琴长时间暴露在高温、高湿、阳光直射等不好的环境中,它的寿命可能会受到影响。
4.维护状况:定期进行钢琴维护和保养可以延长钢琴的使用寿命。
保持钢琴的清洁,定期检查保养、更换易损耗件,定期调律,保持琴体和键盘的稳定,都能减缓钢琴老化的速度。
总的来说,正确的使用和保养可以延长钢琴的使用寿命。
一架高质量、正确使用和维护的钢琴,可以持续使用超过100年,而一些历史悠久的钢琴已经经过多次修复和维护,仍然可以发挥出非常好的音质。
一-、锻造过程质量控制

一、锻造过程质量控制锻造是制造行业中重要的成型工艺之一,主要应用于金属制品的生产。
正确的质量控制可以提高锻造的成功率,减少不合格品率,降低生产成本,提高生产效率。
本文将介绍锻造过程中的质量控制方法和技巧。
1. 原材料控制1.1. 原材料材质和尺寸的选择不同的材质和尺寸的原材料会对后续锻造工艺的成功与否产生重大影响。
选择正确的原材料是保证锻造成功的重要因素。
原材料应符合国家标准和行业规范,并经过严格的质量检测和审核。
1.2. 原材料储存原材料的储存应该在防潮、防震、防污染的情况下进行,确保原材料的质量不会受到影响。
在储存过程中要注意分类、标识、清点,并对储存环境定期进行检查。
2. 模具的质量控制2.1. 模具的制造模具的制造质量直接影响到成品的质量。
模具的制造过程应该符合相关技术规范和标准,以确保模具具备耐用性、精度和稳定性等特性。
2.2. 模具的维护模具使用过程中需要进行适当的维护,如要及时清理、润滑,做好防锈工作等。
维护模具可延长其使用寿命,节约生产成本,保证成品的质量。
3. 锻造的工艺控制3.1. 锻造温度和时间的控制锻造温度是影响锻造质量的重要因素,打开锻模前应根据锻造材料确定合适的合金锻造温度。
锻造过程中应根据材料性能来调控温度和工序。
打制物件、加工装备、锻造工艺的不同都会影响锻造时间的选择。
3.2. 锻造的过程控制锻造过程中需要严格控制上、下件之间的高度和位置,防止成品的形状变形或出现缺陷。
在锻造过程中要避免热裂和表面缺陷、孔洞的出现。
在锻造的过程中要根据锻造材料的物性,将锻造力度控制在合理的范围内,以确保成品质量。
4. 成品的质量控制4.1. 成品尺寸控制成品的尺寸控制是保证产品质量的关键。
需使用量具对产品进行尺寸测量,并根据测量的数据进行修正。
成品严重尺寸超标将直接影响产品的质量和外观。
4.2. 成品外观和表面处理成品外观质量是保证产品销售的关键因素之一。
成品表面的处理需要做到光滑、美观、符合质量要求。
n-1的概念
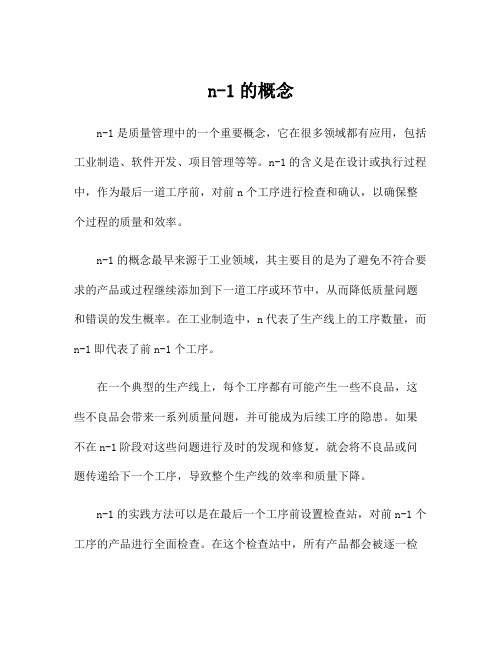
n-1的概念n-1是质量管理中的一个重要概念,它在很多领域都有应用,包括工业制造、软件开发、项目管理等等。
n-1的含义是在设计或执行过程中,作为最后一道工序前,对前n个工序进行检查和确认,以确保整个过程的质量和效率。
n-1的概念最早来源于工业领域,其主要目的是为了避免不符合要求的产品或过程继续添加到下一道工序或环节中,从而降低质量问题和错误的发生概率。
在工业制造中,n代表了生产线上的工序数量,而n-1即代表了前n-1个工序。
在一个典型的生产线上,每个工序都有可能产生一些不良品,这些不良品会带来一系列质量问题,并可能成为后续工序的隐患。
如果不在n-1阶段对这些问题进行及时的发现和修复,就会将不良品或问题传递给下一个工序,导致整个生产线的效率和质量下降。
n-1的实践方法可以是在最后一个工序前设置检查站,对前n-1个工序的产品进行全面检查。
在这个检查站中,所有产品都会被逐一检查,以确保其符合质量标准。
如果发现不良品或质量问题,需要及时修复或返工,而不将其传递到下一个工序。
在n-1的实践中,还需要建立一套科学、全面的质量检查体系,包括检查标准、检查方法和检查流程等。
只有通过科学可行的方式,才能确保对n-1工序的检查结果准确可靠。
此外,还需要做好记录和追溯工作,将检查结果及时反馈给前n-1个工序的负责人,并对问题进行分析和跟踪。
n-1的概念不仅仅适用于工业制造领域,对于软件开发和项目管理也有较大的价值。
在软件开发中,n-1可以指代代码自动化测试中的前n-1个测试用例,通过对这些用例进行全面检查,可以及时发现代码中的潜在问题。
在项目管理中,n-1可以指代项目执行过程中的前n-1个阶段,通过对这些阶段的绩效和产出进行评估,可以及时发现并修正项目的问题和偏差。
总之,n-1作为质量管理中的一个重要概念,可以帮助我们有效地提高产品和过程的质量。
通过在最后一个工序前对前n-1个工序进行全面检查,可以减少质量问题的发生,提前发现和修复潜在问题,保证产品和过程的质量达到预期目标。
制造全面质量管理方案模板
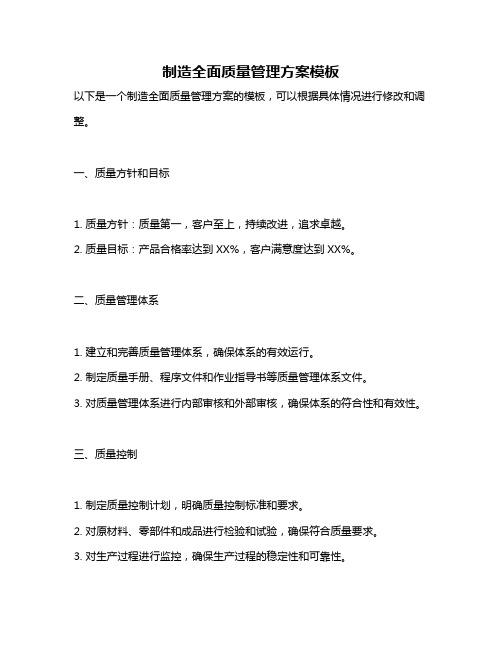
制造全面质量管理方案模板以下是一个制造全面质量管理方案的模板,可以根据具体情况进行修改和调整。
一、质量方针和目标1. 质量方针:质量第一,客户至上,持续改进,追求卓越。
2. 质量目标:产品合格率达到XX%,客户满意度达到XX%。
二、质量管理体系1. 建立和完善质量管理体系,确保体系的有效运行。
2. 制定质量手册、程序文件和作业指导书等质量管理体系文件。
3. 对质量管理体系进行内部审核和外部审核,确保体系的符合性和有效性。
三、质量控制1. 制定质量控制计划,明确质量控制标准和要求。
2. 对原材料、零部件和成品进行检验和试验,确保符合质量要求。
3. 对生产过程进行监控,确保生产过程的稳定性和可靠性。
4. 对不合格品进行处理,防止不合格品的流出。
四、质量改进1. 建立质量改进机制,鼓励员工提出质量改进建议。
2. 对质量改进项目进行立项、实施和验收,确保改进的有效性。
3. 定期对质量管理体系、质量控制和生产过程进行评审和优化,提高质量管理水平。
五、培训和意识提升1. 定期开展质量管理培训和意识提升活动,提高员工的质量意识和技能水平。
2. 鼓励员工参加质量管理相关的培训和认证,提升个人素质和能力。
3. 建立质量管理人才库,为质量管理提供人才保障。
六、持续改进1. 建立持续改进机制,鼓励员工关注生产过程中的细节和问题,提出改进建议。
2. 对改进项目进行跟踪和评估,确保改进成果的落地和持续优化。
3. 定期对质量管理体系、质量控制、生产过程等进行审计和评估,发现问题并及时整改。
同时,根据市场变化、技术更新等情况及时调整质量管理方案,保持方案的时效性和有效性。
通过持续改进,不断提高产品质量和客户满意度,提升企业核心竞争力。
- 1、下载文档前请自行甄别文档内容的完整性,平台不提供额外的编辑、内容补充、找答案等附加服务。
- 2、"仅部分预览"的文档,不可在线预览部分如存在完整性等问题,可反馈申请退款(可完整预览的文档不适用该条件!)。
- 3、如文档侵犯您的权益,请联系客服反馈,我们会尽快为您处理(人工客服工作时间:9:00-18:30)。
总装车间制造中质量和跟踪流程 G/A SHOP BUILT-IN-AULITY AND FOLLOW UP PROCESS
•遵守标准化作业 Follow SOS/JIS •清楚质量要求 Know all specifications •严格FPS Work to FPS •正确使用质量暗灯 Use Andon
Request Of Blue Card 何时需要兰卡
Interrogating the process to determine 评审流程的判定 • Sequence 工序 • Tools 工具 • Material 物件 • Parts Quality 零件质量 be correct prior to assigning the problem to the engineering for resolution 在把问题提交到工程更改的解决问题之前都是正确的
TRACKING 跟踪
CIP For Built-In-Quality 制造质量的不断改进 Error Proofing Automation
防出错和自动停 ---use of simple devices or controls enables the problem to be detected and stops the operation so corrections can be made. 使用简单的装置或控制方法使得问题被发 现,停止运行以便纠正问题.
避免和发现缺陷. • Countermeasure implemented & prevent recurrence. 实行对策及避免重复发生.
Purpose: 目的: To ensure that defects are not passed to the customer. 保证不让缺陷留给顾客.
People Response for Advanced Andon 各级人员在高级暗灯中的职责 T/M--Intelligent use of Andon to call T/L.
组员--活用暗灯来叫组长. T/L--Be observant always.Predict problems & prevent from happening. 组长--永远关注现场,指出并避免问题的发生.
• Standardized operations 标准化操作 • Standardized inspection process 标准化检验程序
Standardized Operation 标准化工作
• Standardized Operation Sheets(SOS) 标准作业单 • Job Instruction Sheets (JIS) 岗位指导书
质量检查部门 QUALITY GATES
•领导工段解决问题 Lead P. S. Activities of group •每周操作检查 Weekly operation checks •支持工段长 Support G/Ls •每天质量汇报 Daily quality report
Built-in-Quality 制造质量 (GA篇)
Definition:The methods by which quality is built into the manufacturing process,so that: 定义:制造质量是一种方法.此方法旨在将质量熔入到制造 过程中,即 prevented & detected. • Defects
Tool We Use For Problem Solving
• Blue cards 蓝卡 • Problem communication reports(PCR) 问题交流报告
Blue Card 兰卡
To determining of some part of our regular manufacturing process has failed to meet the quality standard demanded by our customers 同时测定那些正常的生产流程已经不能达 到顾客要求的质量标准时.
•检查质量门 Check QG 2x/shift(MIN) •快速反应质量门暗灯/代码 1 Respond to QG Andon/Code
班组长 Team Leader
•在线检查 Check line* •操作检查 Check operation(SOS,tool,parts…)* •确定短期措施 Establish S.T.C/M* •开展班组解决问题 P.S. At team level* •实施长期纠正措施 Make L.T. Corrections*
Quality Control Operations Sheet (QCOS) 质量控制操作表
Focus on:Quality 重点:质量
Cost成本 Man人 Material 料 Quality 质量 Sop 正式生产 Time 时间 Machine 机 T/M 生产成员 Mgr.. 管理成员 Method 方法 100% Quality 质量 80% Quality,20% volume 质量 产量 Volume 产量
划痕
松弛
颗粒
凹陷
Cause & Efficient Diagram(Fish Bone Diagram) 原因效果图(鱼刺图)
I.E. In PCR 如 在PCR中
Control Chart 控制图
90 80 70 60 50 40 30 20 10 0
I.E. Q-Cos Control 如 Q-Cos控制
Purpose of Andon 暗灯的作用
• Communicate 交流 • Response 快速反应 • Collect data 收集信息
Communication:When something is wrong---First step of Andon use 交流:有地方不对劲时,首先用暗灯 Communicate with signal between 在下列成员之间通过信号交流
• Quick response to Andon in your team & other teams if required, before line stops. 对自己班组及需要时包括其他班组的暗 灯快速反应,避免停线. • Take decisive action to minimize the line stop,zero line stop is better if possible. 尽可能减少停线最好不停线.
日期 Date:Jan 12,2000 操作组员 Team Member
•检查班组质量 Check teams outgoing quality •迅速反应暗灯Respond to Andon
在线操作 ONLINE OPERATION
•参与解决问题 Participate In P.S. activity
Advanced Andon高级的暗灯
• Built-in-quality 制造质量 • Quick response to Andon 对暗灯的快速反应 • Solve problems quickly 快速解决问题 • Effective communication and decision making 有效交流和快速决定
Tools Supporting Built-in-quality 用于支持制造质量的工具
• Andon for quality 质量暗灯 • Error proofing,Autonomation 防出错,自动停止 • Quality checks 质量检查
Andon 暗灯 WHEN?
• Poor quality from previous processes 较差的质量从前道工序流过来时 • Material shortage or wrong parts 物料短缺或零件送错时 • Malfunctioning equipment 设备功能异常时 • Missing manifest,kanban card,etc 无装车单,看板卡等.
G/L--Give clear targets for improvement to your teams & follow up & support. 工段长---对自己的班组下达明确的 改进目标,并跟踪及提供支持. • Support overtime for CIP ACTIVITY 对需加班进行的不断改进活动提供支持 • Push support departments 推动相应的支持部门 • Make priorities for your teams CIP 对班组的不断改进确定先后次序 • Quick decision to progress/resolve line stop 快速决定单改进或解决停线 • Communicate to S/L & relevant department if big problem happens 如果有较大问题发生,与值班长及横向部门进行交流.
Quality is the key to customer satisfaction. 质量是顾客满意的关键.
Built-in-quality means: 制造质量意味着:
Accept 接受 Build 制造 Ship 传递
Defect 缺陷
Main Supporting Elements of Built-in-Quality 支持制造质量的主要因素 Standardized work 标准化工作
S/L---Co-ordinate support department,improve activities值班长---协调支持部门改进工作
• Clear targets for improve your groups & follow up & support 对自己的工段给出明确的目标,跟踪及提供支持. • Go & see major bottle neck processes/issues & take actions to improve 亲临现场对瓶颈工艺或工位进行观察,作出改进的决 定. • Ensure achievement of all production targets 保证各项生产指标的完成.