风力机叶片的设计
1011第十-十一讲 叶片设计理论

N max
1 2
C
p
sv13
34
而
1 2
sv1正是风速为
v1
的风能,故
Nmax CpT
Cp =0.593说明风吹在叶片上,叶片所能获得的最
大功率为风吹过叶片扫掠面积风能的59.3%.贝茨
理论说明,理想的风能对风轮叶片做功的最高效率
是59.3%。
35
通常风力机风轮叶片接受风能的效率达不到59.3%, 一般设计时根据叶片的数量、叶片翼型、功率等 情况,取0.25~0.45。
' 1 z
2
42
因为, 可得:
a' (Z ) /
Z (a'1)
气流对叶轮的角速度
' 1 (1 a' )
2
(2)
43
三、动量理论
图9 动量理论简图
44
在叶轮上r--r+dr的环域内应用动量定理(如图 9),则风作用在该环域上的轴向推力为
26
s
v1
s1
v
s2 v2
图7 贝茨(Betz)理论计算简图
vv12
s
—叶片前的风速;
v
—风经过叶片后的速度; —风经过叶片时的面积;
ss12
—风经过叶片时的速度; —叶片前风速的面积; —风经过叶片后的面积
27
分析一个放置在移动的空气中的“理想风轮”叶 片上所有受到的力及移动空气对风轮叶片所做的 功。
22
当空气经过风轮圆盘时显然有静压降存在,以至 于空气离开风轮时其压力会小于大气压力。空气 流就会以减小的速度和静压向下游前进——这个 气流域被称为尾流。
风力机预弯叶片多目标优化设计

风力机预弯叶片多目标优化设计风力机是一种利用风能发电的设备,在近几年中逐渐成为可再生能源领域中的热点讨论对象。
其中,风力机叶片作为其核心部件之一,对于整个系统的能量转换效率起着至关重要的作用。
因此,对于风力机预弯叶片的多目标优化设计研究显得尤为重要。
一、风力机预弯叶片的概念与优化设计的背景风力机预弯叶片是指在风力机叶片生产过程中预先制造一定大小的前截面弯曲度,从而达到旋转时的更优状态。
优化设计的目的是在保证面积、角度和形状等基本要素不变的前提下,提高叶片风能转化效率和产生的电能。
预弯叶片可以减小发电机和齿轮机的工作负荷,降低风力机停机时间,提高系统的稳定性,减少斜风时的振动,进而增加风电场的电能产出。
因此,研究如何通过对风力机预弯叶片进行多目标优化设计,提高其风能转化效率和电能产出,对于推进风电发电技术、提高风电经济性和可行性具有重要的意义。
二、风力机预弯叶片多目标优化设计的研究现状风力机预弯叶片的优化设计研究起源于20世纪90年代初期。
此后,越来越多的研究者开始关注风力机预弯叶片的性能优化设计,针对其旋转过程中的力学性能参数进行优化设计和仿真模拟分析。
目前,主要的优化设计研究包括传统的单目标优化设计和多目标优化设计两大类。
1、单目标优化设计单目标优化设计是指将叶片参数的优化设计转化为寻找特定性能指标的最优值。
例如,有研究者通过有限元分析法对预弯叶片形状、厚度分布、拉伸强度等因素进行了分析,结果显示应该选择具有减小机械应力和扰动流阻、增加发电量等特点的叶片工作状态。
2、多目标优化设计多目标优化设计是指将叶片的多项性能指标同时考虑,使得因素之间相互衔接的经济性、效率性、安全性等达到一个良好的平衡。
例如,在风力机叶片的多目标优化设计中,不仅需要考虑叶片的弯曲程度,还需要考虑其在旋转时的气动性能、静力学参数、疲劳性能等方面的指标。
目前,常用的研究方法包括传统的多目标优化方法(如功率法、权衡优化法等)以及近些年发展的多目标进化算法。
风力发电机组叶片设计与性能分析

风力发电机组叶片设计与性能分析叶片作为风力发电机组的核心部件之一,其设计和性能分析对于提高风力发电机的发电效率和性能至关重要。
本文将围绕风力发电机组叶片的设计和性能进行详细讨论,包括叶片的设计原理、材料选择、结构设计以及性能分析与优化等方面。
1. 叶片设计原理风力发电机组叶片的设计原理主要包括气动力学原理和结构力学原理。
气动力学原理研究风力对叶片的作用力,包括气动力的大小、方向和分布等;结构力学原理研究叶片的强度、刚度和振动等特性。
在进行叶片设计时,需要将这两个原理进行综合考虑,以满足风力发电机组的性能要求。
2. 材料选择叶片的材料选择直接影响到叶片的强度、刚度和重量等性能指标。
常用的叶片材料有纤维复合材料(如碳纤维、玻璃纤维)、铝合金和钢材等。
纤维复合材料具有优良的强度和刚度,同时具备较低的重量和惰性,因此在风力发电机组叶片设计中被广泛应用。
3. 结构设计风力发电机组叶片的结构设计主要包括叶片的长度、形状和剖面等几何参数的确定。
通常情况下,叶片的长度应根据风力发电机组的机组容量和环境条件进行确定,以实现最佳的发电效率。
叶片的形状和剖面则直接影响到叶片的气动特性,如风阻、升力和推力等。
为了充分利用风能,叶片的气动特性应该尽可能优化,逐步增大风阻和升力,减小风阻系数和剪力等。
4. 性能分析与优化风力发电机组叶片的性能分析与优化通常采用计算流体动力学(CFD)模拟和试验验证相结合的方法。
通过CFD模拟,可以对叶片在不同工况下的流动场进行数值计算,获得叶片的气动特性,如风阻、升力系数、剪力等。
同时还可以对叶片进行结构力学分析,评估其强度和刚度等。
通过与试验数据的对比,可以验证CFD模拟的准确性,并对叶片的设计进行优化。
在进行风力发电机组叶片设计与性能分析时,还需要考虑以下几个关键因素:A. 多工况性能分析:叶片在不同风速下的气动特性会发生变化,因此需要对叶片在多个工况下进行性能分析,并针对不同风速进行优化设计。
风力机叶片设计及翼型气动性能分析

风力机叶片设计及翼型气动性能分析风力机叶片是风力发电机的核心部件之一,其设计和翼型选择对风力机的发电效率、噪音和寿命等都有着非常重要的影响。
本文将介绍风力机叶片的设计及翼型气动性能分析。
一、叶片设计原理风力机叶片的设计目的是将大气中的风能转换成旋转能,并将其通过转轴传递给发电机,从而产生电能。
因此,叶片的设计主要围绕以下几点展开:1. 创造足够的扭矩:风力机的转子需要达到一定的转速才能发电,而叶片的弯曲和扭矩对于旋转速度的影响至关重要。
设计中需要选择合适的曲线形状和长度来实现理想的扭矩和转速。
2. 保证叶片的强度和稳定性:因叶片在高速旋转状态下会受到巨大的惯性力和风力力矩的作用,因此其材料和结构要足够坚固和稳定,以避免可能的断裂等事故。
3. 提高叶片的气动效率:叶片的气动效率是指其转化风能的能力,通常可以通过优化翼型、减小阻力、降低风阻等方法来提高。
二、叶片设计步骤1. 选定叶片长度:叶片长度通常是根据风力机的规格和性能要求来确定的,也可以根据标准长度来选择。
2. 选择翼型:翼型是叶片的重要组成部分,其形状和性能决定了叶片的阻力和气动效率。
目前,常用的翼型有NACA0012、NACA4415等,根据实际需求来选择。
3. 确定叶片曲线:叶片的曲线是决定扭矩和转速的关键因素,可以通过实验或模拟方法得到合适的曲线形状。
4. 优化叶片的结构:结构设计主要涉及到叶片的强度和稳定性,通常需要进行材料选择、计算等工作以保证叶片的安全性和寿命。
5. 模拟叶片气动特性:叶片的气动特性可以通过流场模拟、试验等方式来获取,可以根据实际需求来对叶片进行调整以达到理想的效果。
三、翼型气动性能分析翼型气动性能是指翼型在气流中运动时产生的力和力矩,其中,升力和阻力是翼型气动力的主要组成部分。
通过分析翼型气动性能,可以选择最优化的翼型来设计叶片。
1. 升力和阻力翼型的升力和阻力是由翼型形状、气流速度、攻角等因素共同决定的。
实际上,翼型的气动性能曲线通常都是非线性的,其升力和阻力特性会随着攻角的变化而不断变化。
风力发电机组的叶片设计与优化
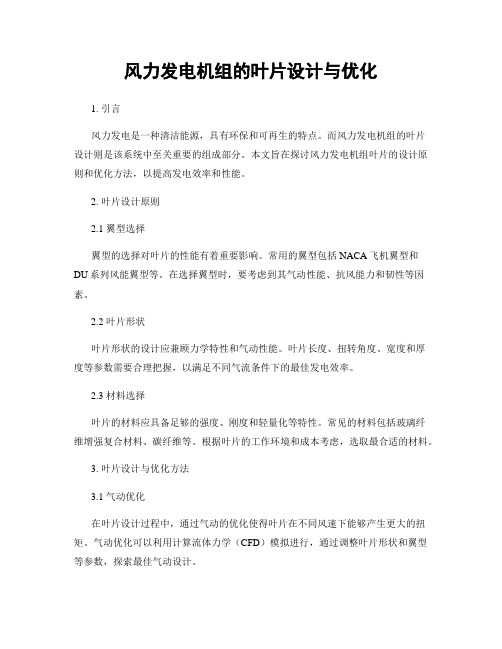
风力发电机组的叶片设计与优化1. 引言风力发电是一种清洁能源,具有环保和可再生的特点。
而风力发电机组的叶片设计则是该系统中至关重要的组成部分。
本文旨在探讨风力发电机组叶片的设计原则和优化方法,以提高发电效率和性能。
2. 叶片设计原则2.1 翼型选择翼型的选择对叶片的性能有着重要影响。
常用的翼型包括NACA飞机翼型和DU系列风能翼型等。
在选择翼型时,要考虑到其气动性能、抗风能力和韧性等因素。
2.2 叶片形状叶片形状的设计应兼顾力学特性和气动性能。
叶片长度、扭转角度、宽度和厚度等参数需要合理把握,以满足不同气流条件下的最佳发电效率。
2.3 材料选择叶片的材料应具备足够的强度、刚度和轻量化等特性。
常见的材料包括玻璃纤维增强复合材料、碳纤维等。
根据叶片的工作环境和成本考虑,选取最合适的材料。
3. 叶片设计与优化方法3.1 气动优化在叶片设计过程中,通过气动的优化使得叶片在不同风速下能够产生更大的扭矩。
气动优化可以利用计算流体力学(CFD)模拟进行,通过调整叶片形状和翼型等参数,探索最佳气动设计。
3.2 结构优化叶片在运行过程中承受着风力和离心力等巨大压力。
为了保证叶片的强度和刚度,可以利用有限元分析方法对叶片的结构进行优化,确保其能够承受更大的载荷。
3.3 声音优化风力发电机组在工作时会产生一定的噪音,为了降低环境噪音污染,叶片设计中需要考虑减小噪音的方法。
可以通过改变叶片的形状、增加吸音材料等方式来达到声音的降噪效果。
4. 叶片优化示例4.1 Aerodyn公司的叶片优化Aerodyn公司通过使用CFD模拟和结构优化方法,设计出了一款低噪音、高效率的风力发电机组叶片。
优化后的叶片在各个风速下都能够提供更高的发电能力,同时降低了噪音水平。
4.2 叶片材料优化研究人员针对叶片材料进行了优化研究,提出了一种新型复合材料。
该材料在保持足够强度的同时,具备更好的轻量化性能,能够最大程度地提高叶片的转速和发电效率。
风力发电课程设计 风力机叶片设计

展望:未来叶片设计将更加 注重提高风能利用效率和可 靠性
技术进步:叶片设计将采用 更先进的材料和制造工艺, 提高叶片的强度和耐用性
优化设计:通过优化叶片形 状和结构,提高风能利用效 率和可靠性
智能控制:通过智能控制技 术,提高叶片的运行效率和 可靠性
环保要求:叶片设计需要满 足环保要求,降低对环境的 影响
叶片长度:60米
叶片重量:10吨
叶片设计特点:低风 速性能好,抗风能力
高
叶片制造工艺:真空 灌注成型
叶片测试结果:风能 转换效率高,运行稳
定可靠
案例二:新型风力机叶片设计研究
设计目标:提高风力机叶片的效率和稳定性 设计方法:采用CFD仿真技术进行叶片优化设计 设计结果:叶片效率提高10%,稳定性提高20% 应用前景:广泛应用于风力发电领域,提高发电效率和稳定性
风力发电机:将风能转化为 电能的核心设备
输电线路:将风力发电机产 生的电能输送到电网中
变电站:将风力发电机产生 的电能转换为适合电网的电
压等级
储能设备:储存风力发电机 产生的电能,保证电力系统
的稳定运行
风力发电的优势与局限性
优势:清洁能源,无污染,可再生,可持续 优势:成本低,维护费用低,运行稳定 局限性:受自然条件限制,如风速、风向等 局限性:占地面积大,对环境有一定影响
降低成本和促进大规模应用
降低材料成本:采 用新型材料,如碳 纤维、玻璃纤维等, 降低叶片制造成本
提高生产效率:采 用自动化生产线, 提高叶片生产效率, 降低生产成本
优化设计:通过优 化叶片设计,提高 叶片性能,降低制 造成本
促进大规模应用: 通过降低成本,提 高风力发电的经济 性,促进风力发电 的大规模应用
风力发电机叶片设计

风力发电机叶片设计风力发电机叶片设计是指设计和制造适合风力发电机使用的叶片,以最大程度地从风能中获取能量,并将其转换为电能。
叶片设计的主要目标是提高发电机的效率、降低维护成本和延长叶片使用寿命。
下面将从叶片设计原理、材料选择、几何形状和结构设计等方面详细介绍风力发电机叶片设计。
叶片设计的原理是基于空气动力学原理,即通过叶片与风之间的相互作用来获得动力。
在设备运行过程中,叶片受到来自风的力和阻力的作用。
为了提高风能的捕获效率,叶片需要具备良好的气动性能,使风能充分地传递到发电机上。
材料选择是叶片设计的重要环节。
叶片需要具备良好的强度和刚度来承受风压力和旋转力。
常用的材料包括玻璃纤维增强塑料(GRP)、碳纤维增强塑料(CFRP)和木材等。
其中,GRP是最常用的材料之一,因为它相对便宜且易于加工。
CFRP 具有较高的强度和刚度,但成本较高。
木材具有较好的弹性和耐久性,但需要进行防腐处理。
叶片的几何形状是影响风能捕获效率和运行稳定性的重要因素。
几何形状包括叶片长度、弦长、扭转角和平均弯曲半径等。
一般来说,叶片长度越长,捕获风能的面积越大,但受到的风力也越大。
叶片的弦长和扭转角决定了叶片的气动特性,对叶片的刚性和强度要求也有一定影响。
平均弯曲半径则影响了叶片的载荷分布和结构强度。
叶片的几何形状需要通过数值模拟和实验验证来确定最佳设计。
叶片的结构设计是确保叶片可以顺利运行并承受外部环境力量的关键。
结构设计包括叶片的内部结构、连接方式和防护措施等。
叶片常常采用空心结构,以降低自重和提高强度。
连接方式通常采用螺栓连接或胶粘剂连接。
叶片的内部结构可以通过加入加筋肋、填充泡沫等方式来增加刚度。
为了防止叶片受到外部环境的侵蚀,叶片表面通常采用防腐涂层或防风腐蚀材料。
除了以上设计原则,叶片的制造工艺和质量控制同样重要。
制造工艺包括叶片模具设计、复合材料制备、成型和固化等。
质量控制需要对叶片的尺寸、质量和结构进行严格控制,以确保叶片的一致性和可靠性。
风力机叶片的设计
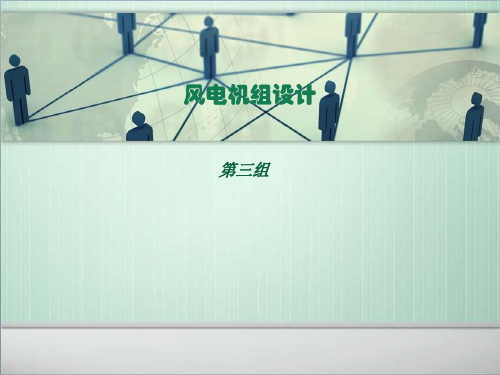
240 3.14 1.4 = 30 7.8 =4,51
(4)计算各截面的周速比
r 80 =0.26 0 = r × 0 =4.51× R 1400 r 170 0.55 1 = r × 1 = 4.51 R 1400 r 260 2 = r 2 4.51 0.84 R 1400 r 350 3 = r 3 4.51 1.13 R 1400 r 440 4 r 4 4.51 1.42 R 1400 r 530 5 r 5 4.51 1.71 R 1400 r 620 6 r 6 4.51 2.00 R 1400 r 710 7 r 7 4.51 2.29 R 1400
对每个叶素来说,其速度可以分解为垂直于风轮旋转平面的分量 Vy 0 和平行风轮旋转平面的分量 Vy 0 ,速度三角形和空气动力分量 如图 2-3 所示。图中:Φ 角为入流角, 为迎角, 为叶片在叶素处的几何扭角。
合成气流速度 V0 引起的作用在长度为 dr 叶素上的空气动力 dFa 可以 分解为法向力 dFn 和切向力 dFt , dFa 和 dFt 可分别表示为
(5) 、确定各个截面的安装角和弦长。
1)、确定翼型的设计升力系数和最佳攻角
2)、应用Glauert方法设计
1)、确定翼型的设计升力系数和最佳攻 根据Profili软件输入翼型型号 NACA23012,可得到表3-1和图3-1、图3-2、图3-3及图3-4如下所示 角
Alfa -8 -7.5 -7 -6.5 -6 -5.5 -5 -4.5 -4 -3.5 -3 -2.5 -2 -1.5 -1 0 0.5 1 1.5 2 2.5 3 3.5 4 4.5 5 5.5 6 6.5 7 7.5 8 8.5 Cl -0.7451 -0.7144 -0.679 -0.6395 -0.5674 -0.492 -0.4268 -0.355 -0.2778 -0.223 -0.1688 -0.1176 -0.0773 -0.0315 0.017 0.1182 0.1677 0.2293 0.2927 0.3685 0.438 0.5114 0.5873 0.6512 0.6972 0.7421 0.7887 0.8339 0.8779 0.9256 0.9716 1.0162 1.065 Cd 0.0241 0.021 0.0194 0.0179 0.0167 0.0154 0.0131 0.0121 0.0115 0.0103 0.0099 0.0093 0.0074 0.0067 0.0065 0.0066 0.007 0.0074 0.0079 0.0084 0.0089 0.0093 0.0097 0.01 0.0103 0.0107 0.011 0.0114 0.012 0.0123 0.0127 0.0134 0.0137 Cl/Cd -30.917 -34.019 -35 -35.7263 -33.976 -31.9481 -32.5802 -29.3388 -24.1565 -21.6505 -17.0505 -12.6452 -10.4459 -4.7015 2.6154 17.9091 23.9571 30.9865 37.0506 43.869 49.2135 54.9892 60.5464 65.12 67.6893 69.3551 71.7 73.1491 73.1583 75.252 76.5039 75.8358 77.7372 Cm -0.0119 -0.0078 -0.0043 -0.0014 -0.0049 -0.009 -0.0111 -0.0145 -0.0188 -0.018 -0.017 -0.0154 -0.0128 -0.0104 -0.0081 -0.0043 -0.0019 -0.0026 -0.004 -0.0083 -0.0113 -0.0154 -0.0199 -0.0219 -0.0203 -0.0183 -0.0166 -0.0147 -0.0125 -0.011 -0.0093 -0.0075 -0.0063
- 1、下载文档前请自行甄别文档内容的完整性,平台不提供额外的编辑、内容补充、找答案等附加服务。
- 2、"仅部分预览"的文档,不可在线预览部分如存在完整性等问题,可反馈申请退款(可完整预览的文档不适用该条件!)。
- 3、如文档侵犯您的权益,请联系客服反馈,我们会尽快为您处理(人工客服工作时间:9:00-18:30)。
(4)计算各截面的周速比
0
=
r
×r0 R
=4.51× 80 1400
=0.26
1 =
r
× r1 R
=
4.51 170 1400
0.55
2
=r
r2 R
4.51
260 1400
0.84
3
=r
r3 R
4.51
350 1400
-0.009 -0.0111 -0.0145 -0.0188
-0.018 -0.017 -0.0154 -0.0128 -0.0104 -0.0081 -0.0043 -0.0019 -0.0026 -0.004 -0.0083 -0.0113 -0.0154 -0.0199 -0.0219 -0.0203 -0.0183 -0.0166 -0.0147 -0.0125 -0.011 -0.0093 -0.0075 -0.0063
3.16
11
r
r11 R
4.51 1070 1400
3.45
12
r
r12 R
4.51 1160 1400
3.74
13
r
r13 R
4.51 1250 1400
4.03
14
r
r14 R
4.51 1340 1400
4.32
15
r
r5 R
4.51
1400 1400
4.51
(5)、确定各个截面的安装角和弦长。
0.007 0.0074 0.0079 0.0084 0.0089 0.0093 0.0097
0.01 0.0103 0.0107
0.011 0.0114
0.012 0.0123 0.0127 0.0134 0.0137
Cl/Cd -30.917 -34.019
-35 -35.7263
-33.976 -31.9481 -32.5802 -29.3388 -24.1565 -21.6505 -17.0505 -12.6452 -10.4459
(2-1)
dFn
1 2
cV0
2
Cn
dr
1
2
dFt 2 cV0 Ct dr
其中 ——空气密度;c——叶素剖面弦长;;e、q——分别表示
法向力系数和切向力系数,即
(2-2)
Cn Cl cos Cd sin
Ct Clsin Cd cos
这时,作用在风轮平面 dr 圆环上的轴向力可表示为
dT
-4.7015 2.6154 17.9091 23.9571 30.9865 37.0506 43.869 49.2135 54.9892 60.5464
65.12 67.6893 69.3551
71.7 73.1491 73.1583
75.252 76.5039 75.8358 77.7372
Cm -0.0119 -0.0078 -0.0043 -0.0014 -0.0049
1 2
Bcv02Cn dr
(2-3)
式中 B--叶片数。
作用在风轮平面 dr 圆环上的转矩为
(2-4)
dM
1 2
02Ct rdr
(二)相关参数确定
•
(三)叶片的设计过程 (1)计算风轮直径。利用公式
D= 8Pu / CpU1312
=
8 500
1.2253.147.83 0.40.72
=2.8m 则风轮半径 R=1.4mm。
1)、确定翼型的设计升力系数和最佳攻角 2)、应用Glauert方法设计
1)、确定翼型的设计升力系数和最佳攻 角 根据Profili软件输入翼型型号NACA23012,可得到表3-1和图3-1、图3-2、图3-3及图3-4如下所示
Alfa -8
-7.5 -7
-6.5 -6
-5.5 -5
-4.5 -4
-3.5 -3
-2.5 -2
-1.5 -1 0
0.5 1
1.5 2
2.5 3
3.5 4
4.5 5
5.5 6
6.5 7
7.5 8
8.5
Cl -0.7451 -0.7144
-0.679 -0.6395 -0.5674
-0.492 -0.4268
-0.355 -0.2778
-0.223 -0.1688 -0.1176 -0.0773 -0.0315
(2)计算叶片长度。假设轮毂半径为 80mm,那么叶片长度 Lb 为
Lb =R- rhub =1400-80=1320mm
(3)等分叶片。把它分成 15 等份,则每等份为 88mm,取成整数后可以把前 14 个 截面段分为 90mm,这样,最后一个截面段为 60mm。
计算各截面周速比。首先计算出额定叶尖速比r
1.13
4
r
r4 R
4.51
440 1400
1.42
5
r
r5 R
4.51
530 1400
1.71
6
r
r6 R
4.51
620 1400
2.00
7
r
r7 R
4.51
710 1400
2.29
8
r
r8 R
4.51
800 1400
2.58
9
r
r9 R
4.51
890 1400
2.87
10
r
r10 R
4.51 980 1400
由表格可知 该翼型的最 佳攻角为9.5, 设计升力系 数为1.1583, 阻力系数为 0.0149,最大 升阻比为
0.017 0.1182 0.1677 0.2293 0.2927 0.3685
0.438 0.5114 0.5873 0.6512 0.6972 0.7421 0.7887 0.8339 0.8779 0.9256 0.9716 1.0162
1.065
Cd 0.0241
0.021 0.0194 0.0179 0.0167 0.0154 0.0131 0.0121 0.0115 0.0103 0.0099 0.0093 0.0074 0.0067 0.0065 0.0066
对每个叶素来说,其速度可以分解为垂直于风轮旋转平面的分量Vy0 和平行风轮旋转平面的分量Vy0 ,速度三角形和空气动力分量
如图 2-3 所示。图中:Φ角为入流角, 为迎角, 为叶片在叶素处的几何扭角。
合成气流速度 V0 引起的作用在长度为 dr 叶素上的空气动力 dFa 可以
分解为法向力 dFn 和切向力 dFt , dFa 和 dFt 可分别表示为
风电机组设计
第三组
(一) 设计理论 (二) 相关参数确定 (三) 叶片的设计过程 (四) 总结 (五) 主要参考文献
(一)设计理论
叶素理论
叶素理论的基本出发点是将风轮叶片沿展向分成许多微段,称这些微段为叶素。假设在每个叶素上的流动相互之间没有干 扰,即叶素可以看成是二维翼型,这时,将作用在每个叶素的力和力矩沿展向积分,就可以求得作用在风轮上的力和力矩。