数控车床的程序编制
数控车床编程实例详解(30个例子)

数控车床编程实例详解(30个例子)车床编程实例一半径编程图 3.1.1 半径编程%3110 (主程序程序名)N1 G92 X16 Z1 (设立坐标系,定义对刀点的位置)N2 G37 G00 Z0 M03 (移到子程序起点处、主轴正转)N3 M98 P0003 L6 (调用子程序,并循环6 次)N4 G00 X16 Z1 (返回对刀点)N5 G36 (取消半径编程)N6 M05 (主轴停)N7 M30 (主程序结束并复位)%0003 (子程序名)N1 G01 U-12 F100 (进刀到切削起点处,注意留下后面切削的余量)N2 G03 U7.385 W-4.923 R8(加工R8 园弧段)N3U3.215 W-39.877 R60 (加工R60 园弧段)N4 G02 U1.4 W-28.636 R40(加工切R40 园弧段)N5 G00 U4 (离开已加工表面)N6 W73.436 (回到循环起点Z 轴处)N7 G01 U-4.8 F100 (调整每次循环的切削量)N8 M99 (子程序结束,并回到主程序)车床编程实例二直线插补指令编程%3305N1 G92 X100 Z10 (设立坐标系,定义对刀点的位置)N2 G00 X16 Z2 M03 (移到倒角延长线,Z 轴2mm 处)N3 G01 U10 W-5 F300 (倒3×45°角)N4 Z-48 (加工Φ26 外圆)N5 U34 W-10 (切第一段锥)N6 U20 Z-73 (切第二段锥)N7 X90 (退刀)N8 G00 X100 Z10 (回对刀点)N9 M05 (主轴停)N10 M30 (主程序结束并复位)图 3.3.5 G01 编程实例车床编程实例三圆弧插补指令编程%3308N1 G92 X40 Z5 (设立坐标系,定义对刀点的位置)N2 M03 S400 (主轴以400r/min 旋转)N3 G00 X0 (到达工件中心)N4 G01 Z0 F60 (工进接触工件毛坯)N5 G03 U24 W-24 R15 (加工R15 圆弧段)N6 G02 X26 Z-31 R5 (加工R5 圆弧段)N7 G01 Z-40 (加工Φ26 外圆)N8 X40 Z5 (回对刀点)N9 M30 (主轴停、主程序结束并复位图 3.3.8 G02/G03 编程实例车床编程实例四倒角指令编程图 3.3.10.1 倒角编程实例%3310N10 G92 X70 Z10 (设立坐标系,定义对刀点的位置)N20 G00 U-70 W-10 (从编程规划起点,移到工件前端面中心处)N30 G01 U26 C3 F100 (倒3×45°直角)N40 W-22 R3 (倒R3 圆角)N50 U39 W-14 C3 (倒边长为3 等腰直角)N60 W-34 (加工Φ65 外圆)N70 G00 U5 W80 (回到编程规划起点)N80 M30 (主轴停、主程序结束并复位)车床编程实例五倒角指令编程%3310N10 G92 X70 Z10 (设立坐标系,定义对刀点的位置)N20 G00 X0 Z4 (到工件中心)N30 G01 W-4 F100 (工进接触工件)N40 X26 C3 (倒3×45°的直角)N50 Z-21 (加工Φ26 外圆)N60 G02 U30 W-15 R15 RL=3(加工R15 圆弧,并倒边长为 4 的直角)N70 G01 Z-70 (加工Φ56 外圆)N80 G00 U10 (退刀,离开工件)N90 X70 Z10 (返回程序起点位置)M30 (主轴停、主程序结束并复位)图 3.3.10.2 倒角编程实例车床编程实例六圆柱螺纹编程螺纹导程为 1.5mm,δ=1.5mm,δ '=1mm ,每次吃刀量(直径值)分别为0.8mm、0.6 mm 、0.4mm、0.16mm图 3.3.12 螺纹编程实例%3312N1 G92 X50 Z120 (设立坐标系,定义对刀点的位置)N2 M03 S300 (主轴以300r/min 旋转)N3 G00 X29.2 Z101.5 (到螺纹起点,升速段1.5mm,吃刀深0.8mm)N4 G32 Z19 F1.5 (切削螺纹到螺纹切削终点,降速段1mm)N5 G00 X40 (X 轴方向快退)N6 Z101.5 (Z 轴方向快退到螺纹起点处)N7 X28.6 (X轴方向快进到螺纹起点处,吃刀深0.6mm)N8 G32 Z19 F1.5 (切削螺纹到螺纹切削终点)N9 G00 X40 (X 轴方向快退)N10 Z101.5 (Z 轴方向快退到螺纹起点处)N11 X28.2 (X轴方向快进到螺纹起点处,吃刀深0.4mm)N12 G32 Z19 F1.5 (切削螺纹到螺纹切削终点)N13 G00 X40 (X轴方向快退)N14 Z101.5 (Z 轴方向快退到螺纹起点处)N15 U-11.96 (X轴方向快进到螺纹起点处,吃刀深0.16mm)N16 G32 W-82.5 F1.5 (切削螺纹到螺纹切削终点)N17 G00 X40 (X轴方向快退)N18 X50 Z120 (回对刀点)N19 M05 (主轴停)N20 M30 (主程序结束并复位)车床编程实例七恒线速度功能编程%3314N1 G92 X40 Z5 N2 M03 S400 N3 G96 S80 N4 G00 X0 N5 G01 Z0 F60N6 G03 U24 W-24 R15 N7 G02 X26 Z-31 R5 N8 G01 Z-40 N9 X40 Z5 N10 G97 S300N11 M30图 3.3.14 恒线速度编程实例(设立坐标系,定义对刀点的位置)(主轴以400r/min 旋转)(恒线速度有效,线速度为80m/min)(刀到中心,转速升高,直到主轴到最大限速)(工进接触工件)(加工R15 圆弧段)(加工R5 圆弧段)(加工Φ26 外圆)(回对刀点)(取消恒线速度功能,设定主轴按300r/min 旋转)(主轴停、主程序结束并复位)车床编程实例八%3317 M03 S400 (主轴以400r/min 旋转)G91 G80 X-10 Z-33 I-5.5 F100(加工第一次循环,吃刀深3mm)X-13 Z-33 I-5.5(加工第二次循环,吃刀深3mm)X-16 Z-33 I-5.5(加工第三次循环,吃刀深3mm)M30 (主轴停、主程序结束并复位)图 3.3.17 G80 切削循环编程实例车床编程实例九G81 指令编程(点画线代表毛坯)图 3.3.20 G81 切削循环编程实例%3320 N1 G54 G90 G00 X60 Z45 M03 (选定坐标系,主轴正转,到循环起点)N2 G81 X25 Z31.5 K-3.5 F100 (加工第一次循环,吃刀深2mm)N3 X25 Z29.5 K-3.5 (每次吃刀均为2mm,)N4 X25 Z27.5 K-3.5 (每次切削起点位,距工件外圆面5mm,故K 值为-3.5)N5 X25 Z25.5 K-3.5 (加工第四次循环,吃刀深2mm)N6 M05 (主轴停)N7 M30 (主程序结束并复位车床编程实例十G82 指令编程(毛坯外形已加工完成)%3323N1 G55 G00 X35 Z104(选定坐标系G55,到循环起点)N2 M03 S300 (主轴以300r/min 正转)N3 G82 X29.2 Z18.5 C2 P180 F3(第一次循环切螺纹,切深0.8mm)N4 X28.6 Z18.5 C2 P180 F3(第二次循环切螺纹,切深0.4mm)N5 X28.2 Z18.5 C2 P180 F3(第三次循环切螺纹,切深0.4mm)N6 X28.04 Z18.5 C2 P180 F3(第四次循环切螺纹,切深0.16mm)N7 M30 (主轴停、主程序结束并复位)图 3.3.23 G82 切削循环编程实例车床编程实例十一外径粗加工复合循环编制图 3.3.27 所示零件的加工程序:要求循环起始点在A(46,3),切削深度为 1.5mm(半径量)。
数控车床编程实例详解(30个例子)

车床编程实例一半径编程图3.1.1 半径编程%3110 (主程序程序名)N1 G92 X16 Z1 (设立坐标系,定义对刀点的位置)N2 G37 G00 Z0 M03 (移到子程序起点处、主轴正转)N3 M98 P0003 L6 (调用子程序,并循环6 次)N4 G00 X16 Z1 (返回对刀点)N5 G36 (取消半径编程)N6 M05 (主轴停)N7 M30 (主程序结束并复位)%0003 (子程序名)N1 G01 U-12 F100 (进刀到切削起点处,注意留下后面切削的余量)N2 G03 U7.385 W-4.923 R8(加工R8 园弧段)N3U3.215 W-39.877 R60 (加工R60 园弧段)N4 G02 U1.4 W-28.636 R40(加工切R40 园弧段)N5 G00 U4 (离开已加工表面)N6 W73.436 (回到循环起点Z 轴处)N7 G01 U-4.8 F100 (调整每次循环的切削量)N8 M99 (子程序结束,并回到主程序)1直线插补指令编程%3305车床编程实例二图3.3.5 G01 编程实例N1 G92 X100 Z10 (设立坐标系,定义对刀点的位置)N2 G00 X16 Z2 M03 (移到倒角延长线,Z 轴2mm 处)N3 G01 U10 W-5 F300 (倒3×45°角)N4 Z-48 (加工Φ26 外圆)N5 U34 W-10 (切第一段锥)N6 U20 Z-73 (切第二段锥)N7 X90 (退刀)N8 G00 X100 Z10 (回对刀点)N9 M05 (主轴停)N10 M30 (主程序结束并复位)圆弧插补指令编程车床编程实例三%3308N1 G92 X40 Z5 (设立坐标系,定义对刀点的位置)N2 M03 S400 (主轴以400r/min 旋转)N3 G00 X0 (到达工件中心)N4 G01 Z0 F60 (工进接触工件毛坯)N5 G03 U24 W-24 R15 (加工R15 圆弧段)N6 G02 X26 Z-31 R5 (加工R5 圆弧段)N7 G01 Z-40 (加工Φ26 外圆)N8 X40 Z5 (回对刀点)N9 M30 (主轴停、主程序结束并复位图3.3.8 G02/G03 编程实例2倒角指令编程%3310车床编程实例四图3.3.10.1 倒角编程实例N10 G92 X70 Z10 (设立坐标系,定义对刀点的位置)N20 G00 U-70 W-10 (从编程规划起点,移到工件前端面中心处)N30 G01 U26 C3 F100 (倒3×45°直角)N40 W-22 R3 (倒R3 圆角)N50 U39 W-14 C3 (倒边长为3 等腰直角)N60 W-34 (加工Φ65 外圆)N70 G00 U5 W80 (回到编程规划起点)N80 M30 (主轴停、主程序结束并复位)倒角指令编程%3310车床编程实例五N10 G92 X70 Z10 (设立坐标系,定义对刀点的位置)N20 G00 X0 Z4 (到工件中心)N30 G01 W-4 F100 (工进接触工件)N40 X26 C3 (倒3×45°的直角)N50 Z-21 (加工Φ26 外圆)N60 G02 U30 W-15 R15 RL=3(加工R15 圆弧,并倒边长为4 的直角)N70 G01 Z-70 (加工Φ56 外圆)N80 G00 U10 (退刀,离开工件)N90 X70 Z10 (返回程序起点位置)M30 (主轴停、主程序结束并复位)图3.3.10.2 倒角编程实例3车床编程实例六圆柱螺纹编程螺纹导程为1.5mm,δ=1.5mm,δ'=1mm ,每次吃刀量(直径值)分别为0.8mm、0.6 mm 、0.4mm、0.16mm图3.3.12 螺纹编程实例%3312N1 G92 X50 Z120 (设立坐标系,定义对刀点的位置)N2 M03 S300 (主轴以300r/min 旋转)N3 G00 X29.2 Z101.5 (到螺纹起点,升速段1.5mm,吃刀深0.8mm)N4 G32 Z19 F1.5 (切削螺纹到螺纹切削终点,降速段1mm)N5 G00 X40 (X 轴方向快退)N6 Z101.5 (Z 轴方向快退到螺纹起点处)N7 X28.6 (X 轴方向快进到螺纹起点处,吃刀深0.6mm)N8 G32 Z19 F1.5 (切削螺纹到螺纹切削终点)N9 G00 X40 (X 轴方向快退)N10 Z101.5 (Z 轴方向快退到螺纹起点处)N11 X28.2 (X 轴方向快进到螺纹起点处,吃刀深0.4mm)N12 G32 Z19 F1.5 (切削螺纹到螺纹切削终点)N13 G00 X40 (X 轴方向快退)N14 Z101.5 (Z 轴方向快退到螺纹起点处)N15 U-11.96 (X 轴方向快进到螺纹起点处,吃刀深0.16mm)N16 G32 W-82.5 F1.5 (切削螺纹到螺纹切削终点)N17 G00 X40 (X 轴方向快退)N18 X50 Z120 (回对刀点)N19 M05 (主轴停)N20 M30 (主程序结束并复位)4恒线速度功能编程%3314车床编程实例七图3.3.14 恒线速度编程实例N1 G92 X40 Z5 (设立坐标系,定义对刀点的位置)N2 M03 S400 (主轴以400r/min 旋转)N3 G96 S80 (恒线速度有效,线速度为80m/min)N4 G00 X0 (刀到中心,转速升高,直到主轴到最大限速)N5 G01 Z0 F60 (工进接触工件)N6 G03 U24 W-24 R15 (加工R15 圆弧段)N7 G02 X26 Z-31 R5 (加工R5 圆弧段)N8 G01 Z-40 (加工Φ26 外圆)N9 X40 Z5 (回对刀点)N10 G97 S300 (取消恒线速度功能,设定主轴按300r/min 旋转)N11 M30 (主轴停、主程序结束并复位)车床编程实例八%3317M03 S400 (主轴以400r/min 旋转)G91 G80 X-10 Z-33 I-5.5 F100(加工第一次循环,吃刀深3mm)X-13 Z-33 I-5.5(加工第二次循环,吃刀深3mm)X-16 Z-33 I-5.5(加工第三次循环,吃刀深3mm)M30 (主轴停、主程序结束并复位)图3.3.17 G80 切削循环编程实例5车床编程实例九G81 指令编程(点画线代表毛坯)图3.3.20 G81 切削循环编程实例%3320N1 G54 G90 G00 X60 Z45 M03 (选定坐标系,主轴正转,到循环起点)N2 G81 X25 Z31.5 K-3.5 F100 (加工第一次循环,吃刀深2mm)N3 X25 Z29.5 K-3.5 (每次吃刀均为2mm,)N4 X25 Z27.5 K-3.5 (每次切削起点位,距工件外圆面5mm,故K 值为-3.5)N5 X25 Z25.5 K-3.5 (加工第四次循环,吃刀深2mm)N6 M05 (主轴停)N7 M30 (主程序结束并复位车床编程实例十G82 指令编程(毛坯外形已加工完成)%3323N1 G55 G00 X35 Z104(选定坐标系G55,到循环起点)N2 M03 S300 (主轴以300r/min 正转)N3 G82 X29.2 Z18.5 C2 P180 F3(第一次循环切螺纹,切深0.8mm)N4 X28.6 Z18.5 C2 P180 F3(第二次循环切螺纹,切深0.4mm)N5 X28.2 Z18.5 C2 P180 F3(第三次循环切螺纹,切深0.4mm)N6 X28.04 Z18.5 C2 P180 F3(第四次循环切螺纹,切深0.16mm)N7 M30 (主轴停、主程序结束并复位)图3.3.23 G82 切削循环编程实例6车床编程实例十一外径粗加工复合循环编制图3.3.27 所示零件的加工程序:要求循环起始点在A(46,3),切削深度为1.5mm(半径量)。
数车编程数控车床的程序编制高级教学

每转进给量
内容展示
10
主轴转速功能(S)指令
主轴转速功能(S)指令用于控制主轴转速。 特殊形式: 恒线速控制 编程格式 G96 S_ m/min
如图中所示的零件,为保持A、B、C各点的线速度在150 m/min, 则各点在加工时的主轴转速分别为多少?
最高转速限制 编程格式 G50 S_ r/min
内容展示
42
• 程序延时
G04 P/X ❖ 子程序
程序中固定顺序或重复出现的程序单独抽出来,编 成一个程序,供主程序调用,这类程序叫做子程序。
M98 P__ __ M99
内容展示
43
内容展示
44
典型零件的程序编制 (1)
内容展示
45
内容展示
46
(2) 加工如图所示的零件,退刀槽槽深为2㎜(直径方向),槽宽3mm, 已知毛坯尺寸为φ30棒料,对零件图进行工艺分析,
确定装夹方案、加工顺序,制定数控加工刀具卡及加工工序卡, 编制加工程序.
图 加工实例
内容展示
47
内容展示
48
数控加工刀具卡
产品名称及代 号 序号 刀具号
1 T01
刀具规格名称 35°硬质合金外圆偏刀
零件 名称
轴
数量 加工表面
粗精车外 1 圆表面及
端面
零件 图号
KS-01
刀尖半 径(mm
)
备注
20X20
内容展示
37
简单螺纹切削循环指令G92
简单螺纹切削循环指令G92可以用来加工圆柱螺纹和圆锥螺纹。该指令 的循环路线与前述的G90指令基本相同,只是F后面的进给量改为螺纹螺距即 可。格式:G92 X(U)_Z(W)_I/R_F_;
数控车床的程序编制

数控车床的程序编制数控车床是目前使用最广泛的数控机床之一。
数控车床要紧用于加工轴类、盘类等回转体零件。
通过数控加工程序的运行,可自动完成内外圆柱面、圆锥面、成形表面、螺纹和端面等工序的切削加工,并能进行车槽、钻孔、扩孔、铰孔等工作。
车削中心可在一次装夹中完成更多的加工工序,提高加工精度和生产效率,专门适合于复杂形状回转类零件的加工。
3.1 数控车床程序编制的基础针对回转体零件加工的数控车床,在车削加工工艺、车削工艺装备、编程指令应用等方面都有鲜亮的特色。
为充分发挥数控车床的效益,下面将结合HM-077数控车床的使用,分析数控车床加工程序编制的基础,第一讨论以下三个问题:数控车床的工艺装备;对刀方法;数控车床的编程特点。
3.1.1数控车床的工艺装备由于数控车床的加工对象多为回转体,一样使用通用三爪卡盘夹具,因而在工艺装备中,我们将以WALTER系列车削刀具为例,重点讨论车削刀具的选用及使用问题。
1、数控车床可转位刀具特点数控车床所采纳的可转位车刀,与通用车床相比一样无本质的区别,其差不多结构、功能特点是相同的。
但数控车床的加工工序是自动完成的,因此对可转位车刀的要求又有别于通用车床所使用的刀具,具体要求和特点如表3.1所示。
表3.1可转位车刀特点2、数控车床刀具的选刀过程数控车床刀具的选刀过程,如图3.1所示。
从对被加工零件图样的分析开始,到选定刀具,共需通过十个差不多步骤,以图3.1中的10个图标来表示。
选刀工作过程从第1图标〝零件图样〞开始,经箭头所示的两条路径,共同到达最后一个图标〝选定刀具〞,以完成选刀工作。
其中,第一条路线为:零件图样、机床阻碍因素、选择刀杆、刀片夹紧系统、选择刀片形状,要紧考虑机床和刀具的情形;第二条路线为:工件阻碍因素、选择工件材料代码、确定刀片的断屑槽型代码或ISO断屑范畴代码、选择加工条件脸谱,这条路线要紧考虑工件的情形。
综合这两条路线的结果,才能确定所选用的刀具。
数控机床的程序编写
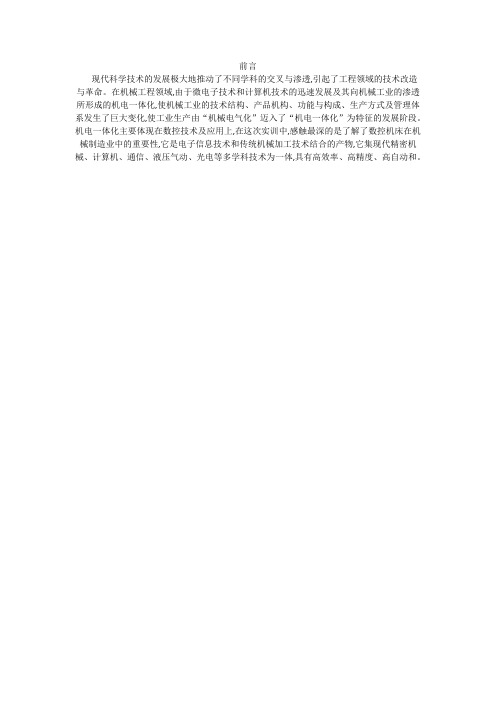
前言现代科学技术的发展极大地推动了不同学科的交叉与渗透,引起了工程领域的技术改造与革命。
在机械工程领域,由于微电子技术和计算机技术的迅速发展及其向机械工业的渗透所形成的机电一体化,使机械工业的技术结构、产品机构、功能与构成、生产方式及管理体系发生了巨大变化,使工业生产由“机械电气化”迈入了“机电一体化”为特征的发展阶段。
机电一体化主要体现在数控技术及应用上,在这次实训中,感触最深的是了解了数控机床在机械制造业中的重要性,它是电子信息技术和传统机械加工技术结合的产物,它集现代精密机械、计算机、通信、液压气动、光电等多学科技术为一体,具有高效率、高精度、高自动和。
摘要数控技术是机械加工自动化的基础,是数控机床的核心技术,其水平高低关系到国家战略地位和体现国家综合国力的水平,近年来,PLC在工业自动控制领域应用愈来愈广,它在控制性能、组机周期和硬件成本等方面所表现出的综合优势是其它工控产品难以比拟的。
随着PLC技术的发展, 它在位置控制、过程控制、数据处理等方面的应用也越来越多。
在机床的实际设计和生产过程中,为了提高数控机床加工的精度,对其定位控制装置的选择就显得尤为重要。
FBs系列PLC的NC定位功能较其它PLC更精准,且程序的设计和调试相当方便。
本文提出的是如何应用PLC的NC定位控制实现机床数控系统控制功能的方法来满足控制要求,在实际运行中是切实可行的。
整机控制系统具有程序设计思路清晰、硬件电路简单实用、可靠性高、抗干扰能力强,具有良好的性能价格比等显著优点,其软硬件的设计思路可供工矿企业的相关数控机床设计改造借鉴。
目录第一章:概述1.1、数控机床的发展趋势 (1)1.2、数控机床的发展历史 (2)第二章:数控加工的特点与刀具2.1、数控机床的特点 (3)2.1.1、数控车床的5大特点 (4)2.2、数控机床的常用种类 (4)2.3、数控机床的刀具选择与应用 (5)第三章:数控机床的程序编写3.1、数控机床的编程 (6)3.1.1、数控机床的自动编程内容与步骤 (6)3.1.2、数控机床编程的基本概览 (9)3.2、数控机床常用术语 (9)第四章:数控车床程序编程 (11)第一章概述1.1、数控机传递个发展趋势数控机床数字控制机床是用数字代码形式的信息(程序指令),控制刀具按给定的工作程序、运动速度和轨迹进行自动加工的机床,简称数控机床。
数控车床程序编制的基本方法
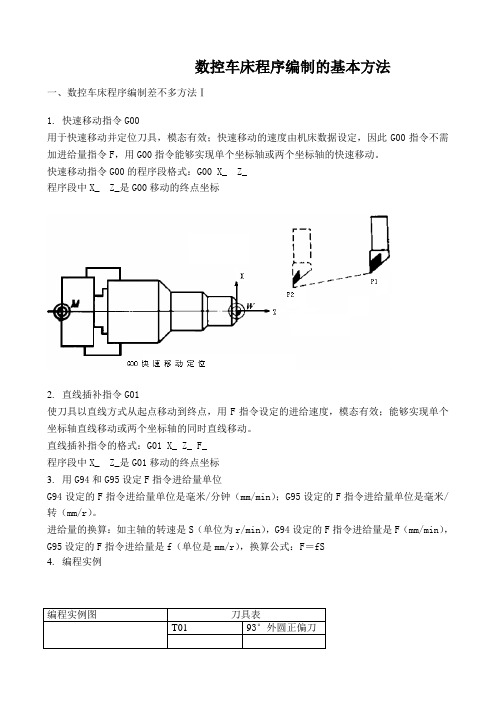
数控车床程序编制的基本方法一、数控车床程序编制差不多方法Ⅰ1.快速移动指令G00用于快速移动并定位刀具,模态有效;快速移动的速度由机床数据设定,因此G00指令不需加进给量指令F,用G00指令能够实现单个坐标轴或两个坐标轴的快速移动。
快速移动指令G00的程序段格式:G00 X_ Z_程序段中X_ Z_是G00移动的终点坐标2.直线插补指令G01使刀具以直线方式从起点移动到终点,用F指令设定的进给速度,模态有效;能够实现单个坐标轴直线移动或两个坐标轴的同时直线移动。
直线插补指令的格式:G01 X_ Z_ F_程序段中X_ Z_是G01移动的终点坐标3.用G94和G95设定F指令进给量单位G94设定的F指令进给量单位是毫米/分钟(mm/min);G95设定的F指令进给量单位是毫米/转(mm/r)。
进给量的换算:如主轴的转速是S(单位为r/min),G94设定的F指令进给量是F(mm/min),G95设定的F指令进给量是f(单位是mm/r),换算公式:F=fS4.编程实例编程实例图刀具表T01 93°外圆正偏刀切削用量主轴速度S 500r/min进给量F 0.2mm/r切削深度a p小于4mm 加工程序程序注释SK01.MPF 主程序名N10 G90 G54 G95 G23 S500 M03 T01 设定工件坐标系,主轴转速为500 r/min,选择1号刀,用G95设定进给量F单位(N10 G90G54G94G23S500 M03 T01)或用G94设定进给量F单位N20 G00 X18 Z2 快速移动点定位N30 G01 X18 Z-15 F0.2 车ø18外圆,进给量F=0.2mm/r(N30 G01 Z-15 F100) 车ø18外圆,进给量F=100mm/minN40 X24 车台阶面N50 Z-30 车ø24外圆长30mm(比零件总长加割刀宽度略长)N60 X26 车出毛坯外圆N70 G00 X50 Z200 快速移动点定位至换刀点N80 M05 主轴停止N90 M02 程序终止二、数控车床程序编制差不多方法Ⅱ1.绝对尺寸G90和增量尺寸G91分别代表绝对尺寸数据输入和增量尺寸数据输入,模态有效。
数控车床的程序编制

数控车床的程序编制数控车床是一种高精度、高效率的现代化机械设备,广泛应用于各种制造行业中。
作为一种数控设备,它需要通过编写程序来实现对零件的加工。
因此,程序编制是数控车床加工过程中不可或缺的一部分。
下面,我们将详细介绍数控车床的程序编制。
一、基本概念数控车床的程序编制其实就是将机床轴的位置、刀具路径、加工参数等信息输入到计算机中,使计算机能够自动控制车床进行加工。
其中,程序包括几何程序和加工参数程序。
几何程序是指需要加工零件的图形和轮廓,也就是加工轨迹;而加工参数则包括切削速度、切削深度、进给速度等。
在程序编制过程中,需要使用数控编程软件。
常见的数控编程软件有EdgeCAM、MasterCAM、PowerMill 等。
这些软件种类繁多,但它们的作用都是一样的。
用户通过这些软件可以编制出符合机床条件的加工程序,并输出G代码到数控机床中,即可自动进行加工操作。
二、程序编制步骤数控车床的程序编制主要包括以下步骤:1. 绘制零件图形:首先需要将需要加工的零件进行绘图,用计算机辅助设计(CAD)软件绘制出准确的零件图形。
在绘制的过程中,需要按照一定的标准进行绘制,包括设计尺寸、精度等方面。
2. 确定坐标系:将零件图形中的坐标系与机床坐标系进行对应,确定数控机床中的X、Y、Z三个坐标轴与设计图中的坐标轴的对应关系。
在编程过程中,需要明确这些坐标的位置、初始值、相对数值等参数。
3. 编写几何程序:将零件图形转化为机床轴的运动轨迹,编写出G代码。
这个过程中需要考虑机床加工的工艺,包括加工方式、刀具方向、切削方式、刀具规格等。
4. 编写加工参数程序:根据要加工的材料,确定加工参数,包括进给速度、切削速度、切削深度、冷却液的使用等参数,并将这些参数编写成M代码。
5. 存储程序:将编写好的几何程序和加工参数程序存储到机床中,可以直接使用或在需要时进行修改。
三、常见的几个注意点1. 选取合适的加工路径:加工路径的选取需要考虑到机床刀具和工件的特性,比如刀具材质、切削方向,工件的形状、材料。
数控车床编程实例详解(30个例子)
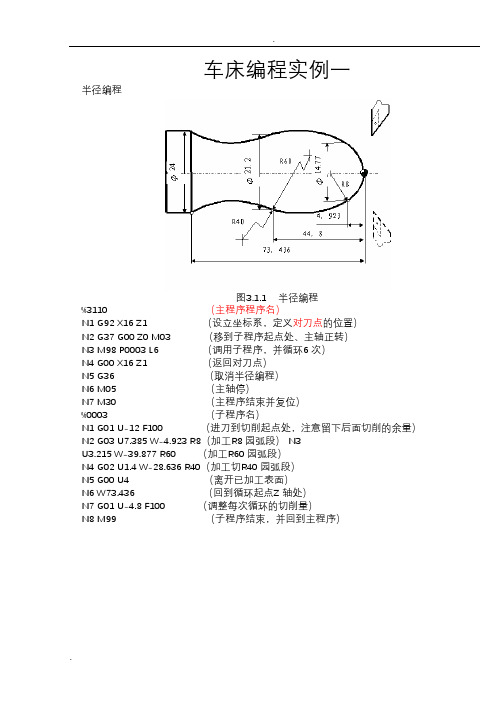
车床编程实例一半径编程图3.1.1 半径编程%3110 (主程序程序名)N1 G92 X16 Z1 (设立坐标系,定义对刀点的位置)N2 G37 G00 Z0 M03 (移到子程序起点处、主轴正转)N3 M98 P0003 L6 (调用子程序,并循环6次)N4 G00 X16 Z1 (返回对刀点)N5 G36 (取消半径编程)N6 M05 (主轴停)N7 M30 (主程序结束并复位)%0003 (子程序名)N1 G01 U-12 F100 (进刀到切削起点处,注意留下后面切削的余量)N2 G03 U7.385 W-4.923 R8(加工R8 园弧段)N3 U3.215 W-39.877 R60 (加工R60 园弧段)N4 G02 U1.4 W-28.636 R40(加工切R40 园弧段) N5 G00 U4 (离开已加工表面)N6 W73.436 (回到循环起点Z轴处)N7 G01 U-4.8 F100 (调整每次循环的切削量)N8 M99 (子程序结束,并回到主程序)1直线插补指令编程 %3305 车床编程实例二图 3.3.5 G01 编程实例 N1 G92 X100 Z10 (设立坐标系,定义对刀点的位置) N2 G00 X16 Z2 M03 (移到倒角延长线,Z 轴 2mm 处) N3 G01 U10 W-5 F300 (倒 3×45°角) N4 Z-48 (加工Φ26 外圆) N5 U34 W-10 (切第一段锥) N6 U20 Z-73 (切第二段锥) N7 X90 (退刀) N8 G00 X100 Z10 (回对刀点) N9 M05 (主轴停) N10 M30 (主程序结束并复位) 圆弧插补指令编程车床编程实例三%3308N1 G92 X40 Z5 (设立坐标系,定义对刀点的位置)N2 M03 S400 (主轴以 400r/min 旋转)N3 G00 X0 (到达工件中心)N4 G01 Z0 F60 (工进接触工件毛坯)N5 G03 U24 W-24 R15 (加工 R 15 圆弧段)N6 G02 X26 Z-31 R5 (加工 R 5 圆弧段)N7 G01 Z-40 (加工Φ26 外圆)N8 X40 Z5 (回对刀点)N9 M30 (主轴停、主程序结束并复位图3.3.8 G02/G03 编程实例2倒角指令编程 %3310 车床编程实例四图 3.3.10.1 倒角编程实例 N10 G92 X70 Z10 (设立坐标系,定义对刀点的位置) N20 G00 U-70 W-10 (从编程规划起点,移到工件前端面中心处) N30 G01 U26 C3 F100 (倒 3×45°直角) N40 W-22 R3 (倒 R 3 圆角) N50 U39 W-14 C3 (倒边长为 3 等腰直角) N60 W-34 (加工Φ65 外圆) N70 G00 U5 W80 (回到编程规划起点) N80 M30 (主轴停、主程序结束并复位) 倒角指令编程%3310车床编程实例五N10 G92 X70 Z10(设立坐标系,定义对刀点的位置) N20 G00 X0 Z4(到工件中心) N30 G01 W-4 F100(工进接触工件) N40 X26 C3(倒 3×45°的直角) N50 Z-21 (加工Φ26 外圆)N60 G02 U30 W-15 R15 RL=3(加工 R 15 圆弧,并倒边长为 4 的直角)N70 G01 Z-70 (加工Φ56 外圆)N80 G00 U10 (退刀,离开工件) N90 X70 Z10 (返回程序起点位置) M30 (主轴停、主程序结束并复位)图3.3.10.2 倒角编程实例3车床编程实例六圆柱螺纹编程螺纹导程为 1.5mm , δ=1.5mm , δ '=1mm ,每次吃刀量(直径值)分别为 0.8mm 、0.6 mm 、0.4mm 、0.16mm图 3.3.12 螺纹编程实例 %3312 N1 G92 X50 Z120 (设立坐标系,定义对刀点的位置) N2 M03 S300 (主轴以 300r/min 旋转) N3 G00 X29.2 Z101.5 (到螺纹起点,升速段 1.5mm ,吃刀深 0.8mm ) N4 G32 Z19 F1.5 (切削螺纹到螺纹切削终点,降速段 1mm ) N5 G00 X40 (X 轴方向快退) N6 Z101.5 (Z 轴方向快退到螺纹起点处) N7 X28.6 (X 轴方向快进到螺纹起点处,吃刀深 0.6mm ) N8 G32 Z19 F1.5 (切削螺纹到螺纹切削终点) N9 G00 X40 (X 轴方向快退) N10 Z101.5 (Z 轴方向快退到螺纹起点处) N11 X28.2 (X 轴方向快进到螺纹起点处,吃刀深 0.4mm ) N12 G32 Z19 F1.5 (切削螺纹到螺纹切削终点) N13 G00 X40 (X 轴方向快退) N14 Z101.5 (Z 轴方向快退到螺纹起点处) N15 U-11.96 (X 轴方向快进到螺纹起点处,吃刀深 0.16mm ) N16 G32 W-82.5 F1.5 (切削螺纹到螺纹切削终点) N17 G00 X40 (X 轴方向快退) N18 X50 Z120 (回对刀点) N19 M05 (主轴停) N20 M30 (主程序结束并复位)4恒线速度功能编程 %3314车床编程实例七 图 3.3.14 恒线速度编程实例 N1 G92 X40 Z5(设立坐标系,定义对刀点的位置) N2 M03 S400(主轴以 400r/min 旋转) N3 G96 S80(恒线速度有效,线速度为 80m/min ) N4 G00 X0(刀到中心,转速升高,直到主轴到最大限速) N5 G01 Z0 F60(工进接触工件) N6 G03 U24 W-24 R15(加工 R 15 圆弧段) N7 G02 X26 Z-31 R5(加工 R 5 圆弧段) N8 G01 Z-40(加工Φ26 外圆) N9 X40 Z5(回对刀点) N10 G97 S300(取消恒线速度功能,设定主轴按 300r/min 旋转) N11 M30 (主轴停、主程序结束并复位)车床编程实例八%3317M03 S400 (主轴以 400r/min 旋转) G91 G80 X-10 Z-33 I-5.5 F100(加工第一次循环,吃刀深 3mm ) X-13 Z-33 I-5.5(加工第二次循环,吃刀深 3mm ) X-16 Z-33 I-5.5 (加工第三次循环,吃刀深 3mm ) M30 (主轴停、主程序结束并复位)图3.3.17 G80 切削循环编程实例5车床编程实例九G81 指令编程(点画线代表毛坯)图 3.3.20 G81 切削循环编程实例 %3320 N1 G54 G90 G00 X60 Z45 M03 (选定坐标系,主轴正转,到循环起点)N2 G81 X25 Z31.5 K-3.5 F100 (加工第一次循环,吃刀深 2mm )N3 X25 Z29.5 K-3.5 (每次吃刀均为 2mm ,)N4 X25 Z27.5 K-3.5 (每次切削起点位,距工件外圆面 5mm ,故 K 值为-3.5) N5 X25 Z25.5 K-3.5 (加工第四次循环,吃刀深 2mm )N6 M05 (主轴停)N7 M30 (主程序结束并复位车床编程实例十G82 指令编程(毛坯外形已加工完成)%3323N1 G55 G00 X35 Z104(选定坐标系 G 55,到循环起点)N2 M03 S300 (主轴以 300r/min 正转)N3 G82 X29.2 Z18.5 C2 P180 F3(第一次循环切螺纹,切深 0.8mm )N4 X28.6 Z18.5 C2 P180 F3(第二次循环切螺纹,切深 0.4mm )N5 X28.2 Z18.5 C2 P180 F3(第三次循环切螺纹,切深 0.4mm )N6 X28.04 Z18.5 C2 P180 F3(第四次循环切螺纹,切深0.16mm)N7 M30 (主轴停、主程序结束并复位)图3.3.23 G82 切削循环编程实例6车床编程实例十一外径粗加工复合循环编制图 3.3.27 所示零件的加工程序:要求循环起始点在 A(46,3),切削深度为1.5mm(半径量)。