(R)洁净钢生产技术初探
洁净钢生产工艺调研

大量的 C : O 气体。 形成一个正压层来阻止钢液从大气 中吸氮。德 国蒂森钢公 司也提出 ,出钢时加入 白云 石 以控制空气侵入 ,加高碳锰铁 , 利用 CO 的生成 去除 [ 。高的矿石加入量和铁水 比可降低终点钢 N] 中氮含量 ,复吹工艺对降低终点钢水氮含量起着重 要作用 ,其中最重要 的是底 吹气体的性质和用于保 护喷嘴的介质种类 ,氧气中氮含量也是影响钢水终 点氮含量的重要因素 ,而吹炼末期的补吹可使钢 中 氮含量明显增高。不脱氧出钢 、控制 出钢 口形状不 散 流 以及在 钢包 内添 加含 C O 的顶 渣 可有效 防止钢 a 水 吸氮 。 精炼过程氮主要来源于与钢水接触的大气 、加 入的合金及熔剂 。钢液去氮主要靠搅拌处理 、真空 脱气或两种工艺的组合促进气体与金属 的反应来实 现。 目前真空脱气装置 中脱氮效果并不明显 ,这主
新的日 程上来 ,因此重钢要在 日趋激烈的钢材市场 竞争中立于不败之地 ,必须尽快掌握 洁净钢的生产 技术 ,及早具备规模生产洁净钢的能力 。
2 洁 净钢 的概 念
建议生产低磷钢最好使用 [ i 为 0 %的铁水 ,两 s] . 3 厂采用碱性转炉吹炼 ,用石灰石代 替白云石 ,使用 硅含量很低的铁水,并保持 良好的搅拌 ,可使 [ ] P 由铁水中( 2 ~80) 0 下降到( 0 9 ) 7 0 7 ×1 8 — 0 x1 。 0 钢中 [ ]的去除一般有三种方法 :一是铁水预 P 处理脱磷 ,这在 日本已被广泛使用 ,脱磷后铁水 中 磷含 量可 达到 10×1 ~10×1 ;二 是转 炉或 电 0 0 8 0 炉精炼脱磷 ,脱磷是与炼钢初期氧化脱碳过程 同时 进行的,吹炼终点 [ 可达到 10 P] 0 x1 左右 。 0 三是
有些厂家开始使用转炉两次脱磷工艺 ,可以使 [ ] P 含量达到 3 ×1 0 0 的水平 。新 日 铁名古屋脱 [ ] P 至 1 ×1 0 0 ,我国宝钢使用转炉两次脱磷 ,使钢中 [ P]
洁净钢生产工艺技术

洁净钢生产工艺技术1. 简介洁净钢是一种具有高纯度、低气体含量和低不纯物含量的钢材。
洁净钢的生产工艺技术在钢铁行业中起着重要的作用。
本文将介绍洁净钢的生产工艺技术、工艺流程和相关设备。
2. 洁净钢生产工艺技术的意义洁净钢的生产工艺技术可以有效降低钢材中的气体含量和不纯物含量,提高钢材的纯度和质量。
洁净钢广泛应用于汽车制造、航空航天、电子设备等高端领域,对提高产品的品质和性能具有重要意义。
3. 洁净钢生产工艺技术的主要方法洁净钢的生产工艺技术主要包括如下几种方法:3.1 精炼精炼是洁净钢生产的关键步骤之一。
通过在高温条件下对炼钢液进行溶解和脱气处理,可以将钢液中的气体含量和不纯物含量大大降低,提高钢材的纯度。
3.2 熔盐浸渍熔盐浸渍是一种将钢材浸入熔盐中,通过离子交换和溶解作用去除钢材表面的氧化物和其他杂质的方法。
这种方法可以显著降低钢材中的含氧量和含杂质量,提高钢材的纯度。
3.3 真空处理真空处理是将钢材放入真空设备中进行处理的方法。
利用真空环境可以有效去除钢材中的气体,减少钢材中的含气量和含杂质量,提高钢材的纯度。
3.4 气体透平气体透平是通过气体的透平作用去除钢材中的气体的方法。
通过将高速气体喷射到钢材中,可以将钢材中的气体冲出,降低钢材中的气体含量。
3.5 再结晶控制再结晶控制是通过控制钢材的热处理过程中的再结晶过程,来提高钢材的晶粒度和纯度的方法。
通过精确控制再结晶过程中的温度和时间,可以得到具有更好性能和纯度的洁净钢材。
4. 洁净钢生产工艺技术的工艺流程洁净钢的生产工艺技术一般包括以下几个主要步骤:1.原料准备:将适量的生铁、废钢和合金等原料按照一定比例混合。
2.熔炼:通过高炉冶炼或电炉冶炼,将原料熔化成钢水。
3.精炼:在精炼炉中对钢水进行溶解和脱气,去除其中的气体和不纯物。
4.过滤:通过过滤器将钢水中残余的杂质和固体颗粒去除。
5.熔盐浸渍:将钢材浸入熔盐中,去除表面氧化物和其他杂质。
纯净钢生产技术的分析
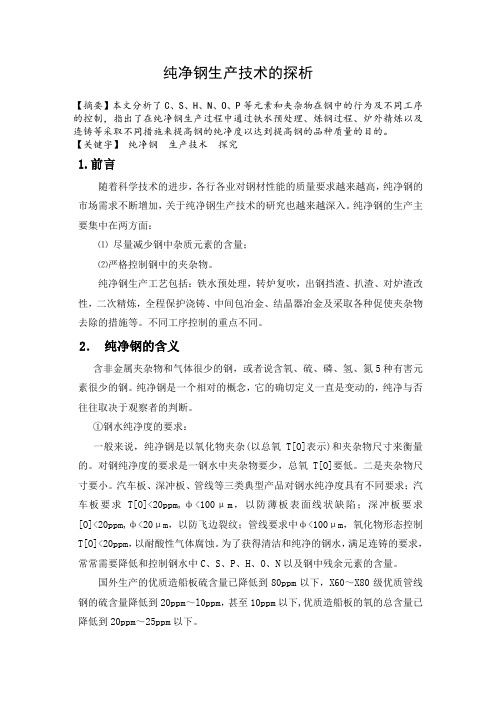
纯净钢生产技术的探析【摘要】本文分析了C、S、H、N、O、P等元素和夹杂物在钢中的行为及不同工序的控制,指出了在纯净钢生产过程中通过铁水预处理、炼钢过程、炉外精炼以及连铸等采取不同措施来提高钢的纯净度以达到提高钢的品种质量的目的。
【关键字】纯净钢生产技术探究1.前言随着科学技术的进步,各行各业对钢材性能的质量要求越来越高,纯净钢的市场需求不断增加,关于纯净钢生产技术的研究也越来越深入。
纯净钢的生产主要集中在两方面:⑴尽量减少钢中杂质元素的含量;⑵严格控制钢中的夹杂物。
纯净钢生产工艺包括:铁水预处理,转炉复吹,出钢挡渣、扒渣、对炉渣改性,二次精炼,全程保护浇铸、中间包冶金、结晶器冶金及采取各种促使夹杂物去除的措施等。
不同工序控制的重点不同。
2.纯净钢的含义含非金属夹杂物和气体很少的钢,或者说含氧、硫、磷、氢、氮5种有害元素很少的钢。
纯净钢是一个相对的概念,它的确切定义一直是变动的,纯净与否往往取决于观察者的判断。
①钢水纯净度的要求:一般来说,纯净钢是以氧化物夹杂(以总氧T[O]表示)和夹杂物尺寸来衡量的。
对钢纯净度的要求是一钢水中夹杂物要少,总氧T[O]要低。
二是夹杂物尺寸要小。
汽车板、深冲板、管线等三类典型产品对钢水纯净度具有不同要求;汽车板要求T[O]<20ppm,ф<100μm,以防薄板表面线状缺陷;深冲板要求[O]<20ppm,ф<20μm,以防飞边裂纹;管线要求中ф<100μm,氧化物形态控制T[O]<20ppm,以耐酸性气体腐蚀。
为了获得清洁和纯净的钢水,满足连铸的要求,常常需要降低和控制钢水中C、S、P、H、O、N以及钢中残余元素的含量。
国外生产的优质造船板硫含量已降低到80ppm以下,X60~X80级优质管线钢的硫含量降低到20ppm~l0ppm,甚至10ppm以下,优质造船板的氧的总含量已降低到20ppm~25ppm以下。
②纯净钢的质量控制主要集中在两方面:一是尽量减少钢中杂质元素的含量;二是严格控制钢中的夹杂物,包括夹杂物的数量尺寸、分布、形状、类型。
济钢洁净钢生产工艺实践
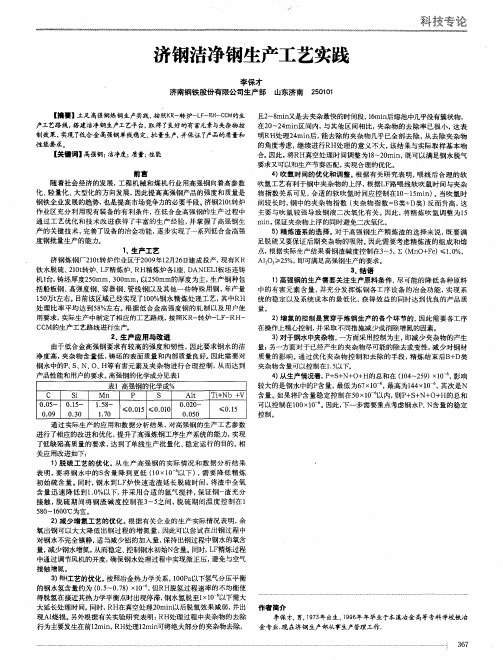
CC M的生产工艺路线 进行对于高 强钢生 产精 炼渣 的选择 来说 , 既要 满 足脱硫 又要 保证 后期夹杂 物 的吸附 。 因此需 要考虑 精炼 渣的组 成和 熔 点, 根据 实际生 产结果看 钢渣碱度 控制在3 ~ 5 , ∑( Mn O + F e ) ≤1 . 0 %,
l
表1高强钢的化学成%
C I S i l Mn I P 1 S l Al t l Ti +Nb + V
f I 1 ’ i l ≤ ㈣ s l ≤ 0 埘 o 1
l ≤ s
较大的是 钢水 中的P 含量 , 最低为 6 7 × 1 0 一, 最 高为1 4 4 × 1 0 _ 。 。 , 其次是 N 含量 。 如 果将P 含 量稳 定控制 在5 0 × 1 0 以 内, NP + S + N+ 0 + H的总和 可以控制 在1 0 0 x 1 0 ~。 因此 , 下一步需 要重 点考虑钢水P 、 N含量 的稳定
在操 作上精心控制 , 并采取 不同措施减少或 消除增氮的 因素 。 2 , 生 产应 用与 改进 3 ) 对于钢水 中夹杂物 。 一方面采用控 制为主 , 即减 少夹杂 物的产生 由于低 合金高强 钢要求 有较 高的强度 和韧 性 , 因此要求 钢水 的洁 量 ; 另一方面对于 已经产生 的夹杂 物尽可能的 除去或变性 , 减少对 钢材 净度 高, 夹杂 物含 量低 , 铸 坯的表 面质量和 内部质量 良好 因此需 要对 质量 的影响 。 通过优 化夹杂 物 控制和 去除 的手 段, 精 炼 结束后 B + D 类 钢水 中的P 、 S 、 N、 O、 H等有 害元 素及夹 杂物 进行合 理控制 , 从而 达到 夹杂物含量可 以控 制在1 . 5 以] - a 产品性能和用户的要求。 高强钢 的化学成分见表 1 4 ) 从生产情况看 , P + s + N+ 0+ H的总和在 ( 1 0 4 - 2 5 9 ) × 1 0 ~, 影响
洁净钢技术1

铸钢业界的重要课题——生产清洁钢信息类型:技术交流信息加入时间:2005年12月14日10:47 双击自动滚屏--------------------------------------------------------------------------------近十多年来,生产清洁钢一直是各国铸钢业界广泛关注的问题,为进行这方面的研究,花费了可观的时间、金钱和人力。
对于铸钢业界,生产清洁钢的含义是:加强脱氧和防止出钢和浇注过程中的二次氧化,从而减少钢中和铸件表面上的氧化物夹杂。
说起来,这是个老问题,搞铸钢的谁都知道,但实际上大多数同仁对此并无切实的认识和了解。
据国外所作的统计分析,铸钢件的直接生产成本中,表面清理费用约占20%,其中,大部分是用于清除和焊修氧化夹杂缺陷的。
美国铸钢研究学会(SFSA)自1985年起进行了大量研究工作,从各类铸钢件(包括碳钢件、低合金钢件和中高合金钢件)中取样500件以上,作研究分析,结果表明:铸钢件表面上的宏观夹杂的来源如下:l 83%是由于钢液脱氧不好和二次氧化;l 14%来自造型材料;l 2%来自炉渣;l 1%来自耐火材料。
因此,铸钢件表面上形成宏观氧化物的主要原因是钢的清洁度不够好。
从而,铸造用钢的清洁度,可用每吨铸件表面上需清除的宏观夹杂物的体积来衡量,也可以用每吨铸件修补所用的焊条量来衡量。
当然,钢中微观夹杂物的数量,形态及分布状况也与其清洁度相关,但其影响较小。
在许多铸钢厂现场所作的调查表明:不同炉次之间的铸件,每吨铸件修补所需的焊条量差别很大;同一炉次所浇注的铸件,从最先浇注的到最后浇注的,每吨铸件的焊条用量差别不大。
而且,铸件上宏观夹杂物多的炉次约占20~25%。
这说明:熔炼方面容易失控的变数较多,而浇注过程中的变数较少。
铸钢件中也会含有其他杂质,如硫化物和氮含量等,但是,钢中的氮含量可以通过脱碳沸腾可靠地加以控制,碱性炉炼钢控制含硫量也不成问题,而且钢中硫化物的情况也与脱氧有关。
(R)超洁净钢的新进展

第1卷第3期 材 料 与 冶 金 学 报 Vol11No13超洁净钢的新进展李正邦Ξ(钢铁研究总院冶金工艺研究所,北京 100081)摘 要:洁净钢已在工业规模生产.本文认为超洁净钢应针对不同钢种、不同用途,应用不同蹬精炼技术,在生产流程中各个突破、达到要求.零夹杂钢即夹杂物高度弥散分布,尺寸小于1μm的钢.本文从理论上分析其制备的可能性,展望其性能,并探讨采用冷坩埚真空感应悬浮熔炼或电子束熔炼制备零夹杂钢.关键词:超纯净钢;零夹杂钢;冷坩埚悬浮熔炼;电子束熔炼中图分类号:TF76914 文献标识码:A 文章编号:167126620(2002)0320161205N e w progress of super clean steelL I Zheng2bang(Metallurgical Technology Institute of CISRI,Beijing,100081,China)Abstract:Clean steels have been commercially produced in large scale.The“Super-Clean”is a relativeconception,which means that different steel grades have different clean requirements that meet the need ofdifferent uses.S o various unit metallurgical processes have been used to fulfil the cleanliness of specialgrades.Zero inclusion steel defined as,that the inclusions in matrix are highly dispersed and the size ofinclusion is less than1micron.The aim of this paper is to analyze the possibility of refining zero inclusionsteel theoretically,to prospect the properties of zero inclusion steel and discuss the process of refining zeroinclusion steel using cold crucible levitation melting or electron beam melting.K ey w ords:super clean steel;zero inclusion steel;cold crucible levitation melting;electron beam melting 随着科学技术的发展,对钢材性能要求日益严格,对钢材质量要求不断提高,进一步减少钢中夹杂含量,提高钢的洁净度,是本世纪发展方向.目前国内外已建立大规模生产洁净钢IF深冲汽车钢板生产体系,运作正常,钢中C、S、P、N、H、T1O质量分数之和不大于100×10-6.不少冶金学家将超洁净钢界定为S、P、N、H、T1O质量分数之和不大于40×10-6.作者认为,应用特种精炼手段,不难达到上述要求,但受经济因素制约无法大规模生产.作者认为,应在洁净钢冶炼基础上,针对不同钢种及不同用途的特殊要求,采用精炼手段,各个突破,达到性能要求.K eissling提出夹杂物“临界尺寸”的概念[1].根据断裂韧性K IC的要求,夹杂物“临界尺寸”为5~8μm.当夹杂物小于5μm时,钢材在负荷条件下,不再发生裂纹扩展.作者认为可将此界定为超洁净钢标准之一.近年来,加拿大Mitchell和新日铁Fukumoto 提出“零夹杂钢”的概念[2].所谓“零夹杂钢”,并非钢中无夹杂物,而是夹杂物尺寸小于1μm,无法用光学显微镜观察到,预示钢的抗疲劳性能将有大幅度提高.本文分析研究制备“零夹杂钢”的理论依据,提出其制备工艺技术.超洁净钢与零夹杂钢是一个问题的两个方面与两个层次,其解决可谓“异曲同工”,攻破其一,另一个必将迎刃而解.Ξ收稿日期:2001207227.作者简介:李正邦(1934—),男,中国工程院院士.1 超洁净钢111 超低硫钢11111 超低硫钢的技术要求 硫在钢中以硫化物(MnS、FeS、CaS等)形式存在,对力学性能的影响是:(1)加大各向异性,使钢材横向、厚度方向强度、塑性、冲击等性能显著低于轧制方向(纵向),特别是钢板低温冲击性能;(2)显著降低钢材抗氢致裂纹能力,因此,用于海洋工程、铁道桥梁、高层建筑、大型储氢罐的钢板,硫的质量分数已控制在50×10-6以下.硫还影响钢材抗腐蚀性能,用于输送含H2S等酸性介质油气管线钢,w[S]降至(5~10)×10-6.此外硫对钢材热加工性能、可焊性均产生不利影响.11112 生产超低硫钢的技术生产超低硫钢流程:(1)新日铁大分厂生产深冲钢板转炉流程:铁水沟脱硅—铁水喷粉深脱硫—LB/OB转炉脱碳—RH2PB循环脱气喷粉.用CaO+CaF2粉剂喷粉,脱硫率达80%,w [S]达10×10-6.技术关键在于提高转炉铁水装入比,减少铁水带入渣.真空喷粉RH2PB或V2 KIP可避免钢水翻腾、氧化与吸氮,但真空设备昂贵.(2)德国Aosta钢铁公司生产高速钢、不锈钢流程:电炉初炼—Iop2VOD脱磷—扒渣—L F升温脱硫—VD脱气。
高效低成本洁净钢生产课件

总结词:介绍了高效低成本洁净钢生产所需的设备和材料,包括熔炼炉、精炼装置、连铸机、轧机等设备和耐火材料、保护气体等辅助材料。
高效低成本洁净钢生产实践与案例分析
03
高效低成本洁净钢生产设备
介绍关键的生产设备及其工作原理,如真空脱气装置、连铸机、轧机等。
01
高效低成本洁净钢生产技术
介绍当前主流的高效低成本洁净钢生产技术,如连铸连轧技术、纯净钢冶炼技术等。
高效低成本洁净钢生产课件
目录
引言洁净钢生产技术高效低成本洁净钢生产工艺高效低成本洁净钢生产实践与案例分析结论与展望
引言
洁净钢是指钢中氧、氮、氢、硫、磷等杂质元素含量较低,且夹杂物细小弥散分布的钢种。
洁净钢的生产过程需经过冶炼、连铸和轧制等工序,通过控制各工序的工艺参数和操作条件,达到降低杂质元素含量和去除夹杂物的目的。
国内外典型案例对比
结论与展望
高效低成本洁净钢生产技术已取得显著成果,为钢铁行业的发展提供了有力支持。
高效低成本洁净钢生产技术涉及多个领域,包括冶金、材料科学、化学等,需要跨学科合作。
高效低成本洁净钢生产技术还需要在生产实践中不断优化和完善,以提高生产效率和降低成本。
钢铁行业将继续推进高效低成本洁净钢生产技术的研发和应用,以提高产品质量和降低生产成本。
02
高效低成本洁净钢生产工艺流程
详细阐述从原料选择、冶炼、连铸、轧制到产品精整的整个生产工艺流程。
分析该企业在高效低成本洁净钢生产方面的成功经验,包括技术应用、工艺优化、设备改造等方面的具体措施。
某钢铁企业高效低成本洁净钢生产实践
对比分析国内外在高效低成本洁净钢生产方面的典型案例,总结各自的优势和不足。
未来钢铁行业将更加注重环保和可持续发展,高效低成本洁净钢生产技术将发挥更加重要的作用。
浅议纯净钢的生产技术

浅议纯净钢的生产技术文章简要探讨了纯净钢的概念,分析了宣钢近几年纯净钢的冶炼工艺技术情况,为后续纯净钢产品的生产提供有益的借鉴。
标签:纯净钢;炼钢;连铸前言近二十年来,随着转炉炼钢技术的日益成熟和连铸技术、炉外处理技术的推广和发展,钢材纯净度明显提高,进而改善了钢材的加工性能和使用性能,适应了高强度、长寿命、耐腐蚀、在恶劣条件下工作的需要,就必须进行纯净钢的炼制。
文章将对纯净钢的概念进行解释,分析宣钢近几年纯净钢的冶炼工艺技术情况,为后续纯净钢产品的生产提供有借鉴。
1 纯净钢的概念纯净钢是一个相对的概念。
纯净钢对钢中的杂质元素含量要求非常严格,其中,硫、磷两种元素的含量应控制在万分之一以内,同时,对氢、氧和其它低熔点金属元素含量的要求要远远高于普通钢。
纯净钢标准下氧、硫、磷、氢、氮这五种元素含量非常低。
2 纯净钢的生产技术宣钢纯净钢冶炼技术以铁水预处理、转炉过程控制、终点控制、LF精炼以及连铸过程防止卷渣和二次氧化为主线展开。
2.1 铁水预处理上世紀八十年代以来,生产优质低磷、低硫钢必须注重铁水的预处理工艺,通过铁水预处理可以讲转炉中铁水的杂质元素含量降低至成品钢水平。
采用固体脱硫剂进行铁水脱硫,是纯净钢生产平台的重要环节。
不同温度下(1500-1600℃),脱硫能力最强的是镁,而CaO/CaC2是成本最低的,所以应用最广泛的是Mg/CaO和CaO/CaC2。
铁水预处理脱硫生产超低硫钢的工艺关键是要及时去除脱硫渣,以防止在炼钢过程中回硫。
2.2 转炉过程控制2.2.1 转炉过程双渣冶炼工艺与终点高拉碳操作采用双渣冶炼工艺去磷,在冶炼3分钟后倒前期渣,倒渣量为总渣量的1/2-3/5。
冶炼前期脱磷率为70-80%,可将铁水磷含量降到0.030%以下。
为降低转炉钢水含氧量,并同时获得良好的去磷效果,转炉终点钢水碳含量控制在0.35-0.45%。
转炉终点钢水成分见表1。
表1 宣钢转炉终点钢水化学成分2.2.2 出钢操作出钢时间不小于4分钟;由于转炉内流出的氧化性炉渣会增加氧化物夹杂,故采用挡渣锥挡渣出钢操作,钢包内渣层厚度控制在70mm以下,保证挡渣成功率在90%以上,避免出钢下渣,解决了回磷问题同时提高合金吸收水平,实现转炉出钢至成品过程中控制磷含量在0.008%以内。
- 1、下载文档前请自行甄别文档内容的完整性,平台不提供额外的编辑、内容补充、找答案等附加服务。
- 2、"仅部分预览"的文档,不可在线预览部分如存在完整性等问题,可反馈申请退款(可完整预览的文档不适用该条件!)。
- 3、如文档侵犯您的权益,请联系客服反馈,我们会尽快为您处理(人工客服工作时间:9:00-18:30)。
洁净钢生产技术初探潘秀兰 王艳红(鞍钢集团技术中心)摘要 主要论述钢的洁净度与其性能之间的关系,以及近年来国内外主要钢厂生产洁净钢控制钢中杂质元素[C、S、P、N、H、O]技术的进展,为鞍钢纯净钢的生产提供有益的借鉴。
关键词 洁净钢 炼钢 连铸E le m en tary D iscussi on on the T echno l ogy fo r C lean Steel P roducti onPan Xi ulan W ang Yanhong(A ngang T echnol ogy Center)Abstract T he paper discusses the relati on betw een the cleanness and p roperty of steel,the technical p rogress of clean steel p roducti on and that of steel i m purity ele m ents[C,S,P,N,H,O] controlling and p rovides valuable references for clean steel p roducti on in A ngang.Key W ords clean steel steel m ak ing continuous casting1 前言钢的纯净化技术是生产高性能、高质量产品的基础,代表钢铁冶金企业的技术装备水平。
20世纪80年代以来,钢的洁净度不断提高。
日本2000年批量生产的洁净钢中,有害元素[C、P、S、N、O、H]总量可达0.005%,我国宝钢可达01008%,见表1。
随着国防、交通、石油和汽车等行业对钢材质量要求的日益提高,今后钢的洁净度会进一步提高。
表1 国内外一些钢厂生产的洁净钢水平,×10-4%厂家[C][O][P][S][N][H]合计川崎 1020420 54爱知钢厂 9~12<505~10 新日铁102525315179名古屋厂<3019<30<3020~30<1.590~100迪林根厂 20~30 1030<171中钢公司<25<11 <20 66林茨钢厂2024 22 66宝钢≤20≤10152011≤180武钢20≤20501019≤2 洁净钢是一个相对概念,一般认为,洁净钢是指钢中五大杂质元素[S、P、H、N、O]含量较低,且对非金属夹杂物(主要是氧化物和硫化物)进行严格控制的钢种,主要包括:钢中总氧含量低,非金属夹杂物数量少、尺寸小、分布均匀,脆性夹杂物少以及合适的夹杂物形态。
理论和实践证明,钢的洁净度越高,其产品性能越好,使用寿命越长。
如钢中碳含量从0.004%降低到0.002%时,深冲钢的延伸率可提高7%。
提高钢的洁净度还可提高其耐磨和耐腐蚀等性能。
因此,生产洁净钢是生产高附加值产品的基础,具有明显的经济效益。
应该指出的是,不同钢种对钢的洁净度要求不同,见表2。
2 洁净钢生产技术2.1 碳的影响及脱碳钢中碳对钢的性能影响最大,碳含量高能增加钢的强度,但使塑性下降、冲压性能变坏。
因此一般优质深冲型铝镇静钢要求[C]≤0.05%,IF 钢要求[C]≤0.007%。
钢中碳的控制主要集中在炉外精炼和防止连铸过程增碳。
AN GAN G T ECHNOLO GY表2 典型洁净钢的洁净度要求产 品含量,%洁净度要求及常见缺陷汽车板[C]<0.003,[N]<0.003T[O]<0.002%,D<100Λm超深冲、非时效性、表面线状缺陷深冲罐 T[O]<0.002%,D<20Λm飞边裂纹大规模集成电路用引线枢[N]<0.005D<5Λm冲压成型裂纹显像管荫罩用钢 D<5Λm防止图像侵蚀轮胎钢芯线 非塑性夹杂D<10Λm冷拔断裂滚珠轴承钢[T i]<0.0015T[O]<0.001%,D<15Λm疲劳寿命管线钢[S]<0.001D<100Λm,氧化物形状控制酸性介质输送 T[O]<0.0015%,D<10Λm耐气体腐蚀钢轨 T[O]<0.002%,单个D<13Λm,链状D<200Λm断裂 注:D——夹杂物直径。
20世纪80年代以来,国际上应用最多的真空精炼装置是RH、VOD、VD。
其中VOD主要用于超低碳不锈钢的精炼;与VD相比,RH更适合于超低碳深冲钢、镀层钢板的生产。
为了将钢中碳脱到0.005%以下,国外发展了RH2OB、RH2KTB、RH2PTB、VOD2PB等吹氧、喷粉强制脱碳的方法。
据报道,日本住友金属工业公司采用VOD2PB喷吹氧化粉剂法,可将碳降至010003%,但其缺点是随着脱碳反应的进行,钢中氧含量会逐渐增加。
钢中碳控制的另一个重点是防止连铸过程增碳。
降低耐火材料中的碳含量,或者使钢水与含碳材料接触面最小;中间包使用不含碳或碳含量少的保温材料;结晶器使用无碳保护渣等,都有助于防止增碳。
2.2 硫的影响及脱硫硫在钢中主要以硫化物(M n、Fe)S的形式存在,除对钢材的热加工性能、焊接性能、抗腐蚀性能有较大影响外,对力学性能的影响主要表现在:①与钢材轧制方向的性能相比,非轧制方向(横向、厚度方向)的强度、延性、冲击韧性等显著降低;②显著降低钢材的抗氢致裂纹(H I C)的能力。
硫能显著降低钢板非轧制方向的性能。
用于高层建筑、重载桥梁、海洋设施等重要用途的钢板,其硫含量目前大都控制在0.008%以下,预计将来会进一步降低到0.005%以下。
用于输送含H2S等酸性介质油气的管线钢硫含量目前已降低到0.0005%~0.0001%。
脱硫的热力学条件是高温、高碱度、低氧化性,因此脱硫应注意以下三点:金属液和渣中氧含量要低、使用高硫容量的碱性渣、钢渣要混合均匀。
铁水预处理可以深脱硫,也可以部分脱磷。
目前广泛采用的铁水脱硫预处理工艺方法见表3。
表3 铁水脱硫预处理工艺的技术比较脱硫工艺方法投掷法喷吹法搅拌法(KR法)脱硫率,%60~7080~9090~95脱硫剂苏打粉M g系脱硫剂石灰脱硫剂消耗,kg t8~100.5~210~12处理后铁水最低含硫量,%0.0150.0030.002铁耗,kg t30<1015~20温降,℃ 次30~40<1020~30处理成本,元 t 1520投资成本比较低一般较高 经预处理后的铁水兑入转炉前需认真扒渣,转炉应使用低硫废钢并采用复合吹炼。
目前,国外钢厂出钢过程中对炉渣进行改性十分重视,这主要是出于降低炉渣的氧化性和进一步脱硫的综合考虑。
通常在出钢过程中添加石灰粉80%、萤石10%、铝粉10%和罐装碳化钙进行钢水脱硫,控制钢包渣中Fe O≤1.5%,可使出钢脱硫率达34%。
有的厂家还进行底吹氩搅拌,可使[S]< 01003%。
二次精炼是生产超低硫钢的必要手段,所用方法主要为喷粉、真空处理、加热造渣、喂线、吹气搅拌,实践中常常是几种手段综合采用。
所形成的精炼设备及精炼效果如表4所示。
此外,钢中的长条形(尤其是沿晶界分布的)硫化物是产生氢致裂纹的必要条件,对钢水进行钙处理可将其改变为球形,一般钙硫比( )接近2为佳。
工艺精炼方法精炼效果,%TN、K IP喷吹Ca O2CaF22A l2O3或Ca2Si[S]<0.001L F加热造还原性炉渣[S]<0.001V2K IP真空喷粉[S]<0.001VD真空造渣[S]<0.001 VOD2PB、RH2PB真空喷Ca O2CaF2粉[S]≤0.00022.3 磷的影响及脱磷磷对钢材的延性、低温韧性、调质钢的回火脆性有很大影响,优质钢对磷的要求已由过去的数钢种,例如含N i9%左右的低温储罐用钢,要求磷含量在0.003%以下。
应该指出的是,磷在低浓度时,对绝大多数钢材的延性没有明显的影响。
对于高强度热轧钢板,当[P]由0.013%降到0.002%后,钢板的冲击韧性没有明显的改善。
大多数钢种[P]降低到0101%左右即可满足钢材延性要求。
脱磷的热力学条件是低温、高碱度、高氧化性。
目前磷的去除主要在铁水预处理、转炉或电炉精炼期、二次精炼三个阶段进行,如表5所示。
表5 各工序脱磷特点比较阶段特点优点缺点铁水预处理磷分配比(P) [P]=150渣量30~50kg t温度1300~1350℃低温、渣量少、氧位高需先脱硅,有温度损失,转炉冶炼废钢比不能太高,鱼雷罐车中反应动力学条件不好转炉或电炉精炼期在炼钢初期与氧化脱碳过程同时进行,磷分配比(P) [P]=100渣量70~100kg t温度1650~1700℃搅拌条件好,钢、渣易于分离高温、渣量大、氧位稍低二次精炼磷分配比(P) [P]=150渣量10~15kg t温度1600~1650℃渣量少需进行钢液加热,脱氧前需除渣,有温度损失 铁水脱磷必须先脱硅,在高炉出铁沟及铁水包投放脱硅剂,可将铁水中的硅脱到0.2%。
川崎发明的SR P法在转炉中进行预脱磷,其脱碳炉中产生的炉渣作为脱磷剂返回脱磷炉中,采用两座转炉同时作业的目的是避免回磷。
在脱磷炉中,磷在10m in内脱到0.011%,同时可熔化7%的废钢,其后在脱碳炉中可生产出小于01010%的超低磷钢水。
此外,低温不脱氧出钢,有助于脱磷,也可防止吸氮。
2.4 氮的影响及去氮氮对钢材性能的影响有三个方面:①加快钢材的时效;②降低钢材的冷加工性能;③造成焊接热影响区脆化。
对于新一代汽车用超深冲IF钢冷轧钢板,为了保证良好的深冲性能,[N]要求低于010025%。
研究表明,为了保证厚板焊接热影响区的韧性,钢中[N]应低于0.002%。
钢中去氮比较困难,目前主要依靠转炉去氮,在浇铸过程中防止吸氮。
在最近的报道中,铁水脱氮和二次精炼脱氮已有所进展。
铁水氮含量是影响钢水终点氮含量的重要因素,低氮铁水主要靠高炉的顺行来获得。
高温、高钛、高锰、高硅均有助于减少铁水氮含量。
铁水脱硅的同时也能脱氮,COCKER I L I-SAM BR E钢厂铁水工业试验证明,在鱼雷罐车中加入40kg t 烧结矿粉,脱氮率可达50%。
转炉是有效的脱氮设备,一般可使氮含量达到0.002%~0.004%,其高低取决于铁水加入量、转炉的吹炼控制、出钢脱氧制度等。
底吹气体的性质、用于保护喷嘴的介质种类及氧气中氮含量也是影响钢水终点氮含量的重要因素,而吹炼末期的补吹可使钢水中氮含量明显增高。
不脱氧出钢、控制出钢口形状不散流以及在钢包内添加含Ca O的顶渣可有效防止钢水吸氮。
精炼过程中,氮主要来源于与钢水接触的大气、加入的合金及熔剂。
钢液去氮主要靠搅拌处理、真空脱气或两种工艺的组合。