塑胶件优化设计(关于结构)
塑胶件通用结构设计

Rev.A
P17
壁厚:
壁厚影响收缩
Rev.A
P18
壁厚:
Rev.A
壁厚影响收缩
前后模温度差异大时,冷却效率所影响,冷面先收缩,但很快固化,收缩量 固定,但热面缓慢收缩,分子有较长时间重排,收缩量会更大,所以产品会 向热的一面弯曲(产品各处温度差 大于10 ̊C以上)
P19
Rev.A
壁厚:
壁厚影响收缩
PC 6485 UL.pdf
P25
肋骨:
肋骨厚度:
Rev.A
P26
Rev.A
肋骨:
肋骨厚度推荐值:
高光泽面, 可以选择更薄的厚度: <1.5mm, 厚度推荐值 <=1.0mm, 等于壁厚
P27
Rev.A
肋骨:
加强筋厚度与塑件壁厚的关系:
P28
肋骨:
薄壁肋骨问题:
-难填充 -靠近浇口比远处更难填充 -当壁厚在填充时,薄壁滞流冻结
圆角加大,应力集中减少。 内圆角R <0.3T----应力剧增。 内圆角R >0.8T----几乎无应力集中
Rev.A
P33
肋骨:
常见加强肋设计:
Rev.A
P34
肋骨:
常见加强肋设计:
Rev.A
P35
肋骨:
常见加强肋设计:
Rev.A
P36
肋骨:
常见加强肋设计:
Rev.A
P37
Rev.A
肋骨:
Rev.A
P2
Rev.A
壁厚:
壁厚的影响: 机械性能,感观,模塑性,成本
- 壁厚的选择是各方面的平衡 *强度 VS 减轻重量 *耐久性 VS 成本
结构细节处理对塑胶成型的改善方案

有跟模的朋友应该知道,塑胶产品试模成型出来后,会发现一些厚薄胶印,缩水痕迹,模具薄钢而断裂等问题。
这些看似简单的问题,却总是在后续加工成型时暴露出来,而且在试模时会搞到很晚,想想都心累。
那么面对这样的问题,我们一般都是出一个简单的报告要求模具厂商自行解决。
其实很多细节的地方在做结构的时候就可以做一些优化,对于后续模具加工,产品成型都是很有利的帮助。
下面我们来几个案列简单分析一下如何优化才会起到改善作用。
【案列一】厚薄胶印过渡处理根据上图所示,有2处问题1,扣的左右2侧,与底边都有台阶,这样的地方在成型的时候很容易起厚薄胶印。
2,扣位太厚,会造成缩水。
问:厚薄胶印是什么原因造成的?答:厚薄胶印是由于产品成型的时候走胶流向此处时有直立的壁位回弹,造成压力与冷却时间不一致而留下来的痕迹。
举一个简单的列子,你将一杯水往楼梯倒下去,会发现水流走的时候经过台阶落差处,会有水花溅起,而且还会形成瀑布往下流,并不是贴合着楼梯面走动的。
那么在这个拐角的地方当射胶满合后会回弹填满,就会留下因为压力与冷却时间不一致的痕迹。
如何改善1,调整注塑成型部分参数,像上图所示位置,如果成型机台好,基本上无需结构上做调就可以改善了。
但是能在结构设计的时候就设计好,会降低后续注塑成型调机难度,起到缩短产品试模时间。
2,扣的2侧做大于60度的过渡减胶,母扣做筋位减胶。
以下为改善示意图根据上图所示,母扣减胶后确保壁厚在0.8mm以上。
问:为何母扣也是直立走胶的却不产生厚薄胶印呢?答:母扣直立走胶面积小,在高速射胶的时候能够快速填满。
下图为大面积过渡减胶示意图其实这种减胶过渡设计在有经验的结构设计师面前,都属于常规设计。
【案列二】螺丝柱的过渡处理如上图所示,左右2边的自攻螺柱底部有做火山口过渡处理问:在什么样的情况下需要设计火山口?答:当螺柱的壁厚超过壳料平均壁厚的三分之二,则需要设计火山口,方便走胶,防止缩水问:什么是缩水?答:表面因内部成型冷却时间不一致,造成塑胶收缩不均而产生凹坑。
塑胶件结构设计方案

塑胶件结构设计方案引言塑胶件在各个工业领域广泛应用,其结构设计方案对产品质量和成本控制有着重要影响。
本文将针对塑胶件结构设计方案进行详细讨论,探讨结构设计原则、注意事项以及常用的设计方法。
结构设计原则1. 符合产品功能和使用要求在进行塑胶件的结构设计时,首先需要确保塑胶件能够满足产品所需的功能要求。
例如,如果塑胶件用于承载重量,则需要考虑其强度和刚度;如果用于密封材料,则需要考虑其密封性能。
2. 合理利用材料在塑胶件的结构设计过程中,要充分利用材料的性能,尽量减少材料的浪费。
通过合理的形状设计、壁厚控制和孔洞设置等手段,达到最佳的材料利用效果。
3. 提高设计可生产性在塑胶件结构设计中,需要考虑到产品的可生产性。
合理的结构设计能够简化生产工艺、降低制造成本,并且提高产品的生产效率。
4. 考虑装配和维修性在塑胶件的结构设计过程中,需要考虑到产品的装配和维修性。
合理的结构设计可以使得塑胶件易于装配,并且方便进行维修和更换。
结构设计注意事项1. 壁厚控制塑胶件的壁厚对其性能和生产工艺有着重要影响。
过厚的壁厚会增加材料的消耗,并降低塑胶件的强度和刚度;而过薄的壁厚则容易导致塑胶件的变形和破裂。
因此,在结构设计过程中,需要合理控制塑胶件的壁厚,以实现最佳的性能和生产效果。
2. 强度和刚度要求根据不同的使用场景和功能要求,需要合理设计塑胶件的强度和刚度。
通过在关键部位增加加强结构或调整几何形状,可以满足产品的强度和刚度要求。
3. 模具设计在进行塑胶件结构设计时,需要考虑到制造过程中所需的模具设计。
合理的塑胶件结构设计能够简化模具结构,降低模具制造成本,并提高生产效率。
4. 表面处理和装饰塑胶件在设计过程中需要考虑到表面处理和装饰要求。
通过合理的设计,可以方便后续的表面处理(如喷塑、镀银等)和装饰操作,提高产品的美观性和附加值。
塑胶件结构设计方法1. 结构拓扑优化结构拓扑优化是一种常用的塑胶件结构设计方法。
通过应用有限元分析和优化算法,将原始的结构进行优化,以实现最佳的结构形式和性能。
塑胶件结构设计非常好

一 塑胶零件及产品设计---壁厚篇
壁厚基本设计守则
1. 壁厚旳大小取决於产品需要承受旳外力, 是否作为其他零件旳支撑,承接柱位 旳数量,伸出部份旳多少以及选用旳塑胶材料而定.
2. 一般旳热塑性塑料壁厚设计应以4mm为限:
从经济角度来看: 过厚旳产品不但增长物料成本,延长生产周期和冷却时间, 增长生产成本;
加强筋旳一般設計形式 角支撑旳形式
材料厚度与加強筋旳尺寸关系(一)
PC,PPO PA,PE PMMA,ABS PS
T’<0.6T T’<0.5T T’<0.5T T’<0.6T
肋根部厚度约为(0.5~0.7)T 肋间间距>4T 肋高L<3T
不同材质旳加强筋细节有所区别 ABS
材料厚度与加強筋旳关系(三)
塑胶件构造设计
基本纲要: ➢ 塑胶零件中加强筋旳应用与设计; ➢ 塑胶零件中壁厚旳选择与设计; ➢ 塑胶零件中卡扣强度计算及其应用.
塑膠制品設計原則
1、在选料方面需考虑: (1) 塑料旳物理机械性能,如强度,刚性,韧性,弹性,吸水性以及相应力旳敏感性等; (2) 塑料旳成型工艺性,如流动性,结晶速率,对成型温度,压力旳敏感性等; (3) 塑料制品在成型后旳收缩情况,及各向收缩率旳差别.
壁厚旳差别产生内应力旳影响
壁厚旳差别产生缩水和气泡旳影响
针对壁厚差别较大处旳过分改善措施
针对壁厚设计不良产生旳变形旳改善措施
壁厚设计考虑对产品成型产生旳影响壁厚过源自处必要时考虑到胶口设计对产品旳影响
壁厚基本设计之转角准则
壁厚均一旳要诀在转角旳地方也一样需要, 以免冷却时间不一致, 冷却时间长旳 地方就会有收缩现象, 因而发生部件变形和挠曲; 另外, 锋利旳圆角位一般会造成部件有缺陷及应力集中, 尖角旳位置亦常在电镀过 程後引起不希望旳物料聚积; 集中应力旳地方会在受负载或撞击旳时候破裂; 较大旳圆角提供了这种缺陷旳处理措施, 不但减低应力集中旳原因, 且令流动旳塑 料流得更畅顺和成品脱模时更轻易.
塑胶结构设计规范
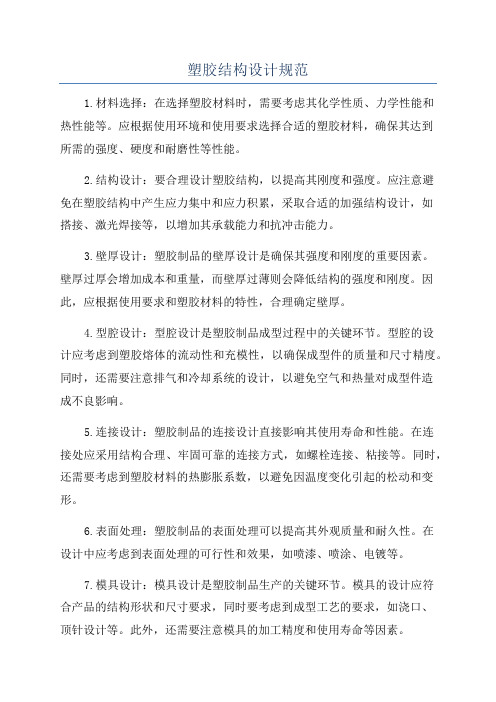
塑胶结构设计规范1.材料选择:在选择塑胶材料时,需要考虑其化学性质、力学性能和热性能等。
应根据使用环境和使用要求选择合适的塑胶材料,确保其达到所需的强度、硬度和耐磨性等性能。
2.结构设计:要合理设计塑胶结构,以提高其刚度和强度。
应注意避免在塑胶结构中产生应力集中和应力积累,采取合适的加强结构设计,如搭接、激光焊接等,以增加其承载能力和抗冲击能力。
3.壁厚设计:塑胶制品的壁厚设计是确保其强度和刚度的重要因素。
壁厚过厚会增加成本和重量,而壁厚过薄则会降低结构的强度和刚度。
因此,应根据使用要求和塑胶材料的特性,合理确定壁厚。
4.型腔设计:型腔设计是塑胶制品成型过程中的关键环节。
型腔的设计应考虑到塑胶熔体的流动性和充模性,以确保成型件的质量和尺寸精度。
同时,还需要注意排气和冷却系统的设计,以避免空气和热量对成型件造成不良影响。
5.连接设计:塑胶制品的连接设计直接影响其使用寿命和性能。
在连接处应采用结构合理、牢固可靠的连接方式,如螺栓连接、粘接等。
同时,还需要考虑到塑胶材料的热膨胀系数,以避免因温度变化引起的松动和变形。
6.表面处理:塑胶制品的表面处理可以提高其外观质量和耐久性。
在设计中应考虑到表面处理的可行性和效果,如喷漆、喷涂、电镀等。
7.模具设计:模具设计是塑胶制品生产的关键环节。
模具的设计应符合产品的结构形状和尺寸要求,同时要考虑到成型工艺的要求,如浇口、顶针设计等。
此外,还需要注意模具的加工精度和使用寿命等因素。
总之,塑胶结构设计规范是保证塑胶制品质量和性能的重要保证。
通过合理的材料选择、结构设计、壁厚设计等,可以提高塑胶结构的强度、刚度和耐久性,从而满足不同的使用需求。
塑胶产品结构设计重点

注重用户体验,优化产品造型、尺寸和细节, 提高舒适度和易用性。
创新性设计
打破传统思维,追求独特、新颖的设计风格, 提升产品吸引力。
绿色设计
强调产品的环保特性,从设计层面降低能耗、 减少废弃物产生。
模块化设计
采用模块化设计理念,便于产品维修、升级 和功能扩展。
制造工艺创新与优化
注塑成型工艺优化
搭配。
同时,还需要注意产品的材质和 表面处理方式,以提高产品的整 体质感,增强产品的市场竞争力。
可靠性原则
可靠性原则要求塑胶产品在正常 工作条件下能够长期保持良好的 性能和稳定性,保证产品的质量
和安全性。
在进行塑胶产品结构设计时,需 要充分考虑产品的可靠性和耐久 性,采用高强度、耐腐蚀、耐磨
等性能优良的塑胶材料。
同时,还需要对产品进行各种环 境下的测试和验证,确保产品在 不同环境下都能保持稳定的性能
表现。
经济性原则
经济性原则要求塑胶产品结构设计要 考虑到生产成本、制造成本和使用成 本等因素,力求降低产品的总成本。
同时,还需要考虑到产品的维护和保 养成本,设计出易于维修和保养的结 构,降低产品的使用成本。
在进行塑胶产品结构设计时,需要充 分考虑材料成本、工艺成本、生产效 率等因素,采用低成本、高效率的设 计方案。
塑胶产品结构设计重 点
contents
目录
• 塑胶材料特性 • 塑胶产品结构设计原则 • 塑胶产品结构设计要素 • 塑胶产品结构设计实例分析 • 塑胶产品结构设计发展趋势与挑战 • 塑胶产品结构设计优化与创新
01
塑胶材料特性
塑胶材料的种类与特性
01
02
03
04
热塑性塑料
塑胶产品结构设计要点

塑胶产品结构设计要点1.胶厚(胶位):塑胶产品的胶厚(整体外壳)通常在0.80-3.00左右,太厚容易缩水和产生汽泡,太薄难走满胶,大型的产品胶厚取厚一点,小的产品取薄一点,一般产品取1.0-2.0为多。
而且胶位要尽可能的均匀,在不得已的情况下,局部地方可适当的厚一点或薄一点,但需渐变不可突变,要以不缩水和能走满胶为原则,一般塑料胶厚小于0.3时就很难走胶,但软胶类和橡胶在0.2-0.3的胶厚时也能走满胶。
2.加强筋(骨位):塑胶产品大部分都有加强筋,因加强筋在不增加产品整体胶厚的情况下可以大大增加其整体强度,对大型和受力的产品尤其有用,同时还能防止产品变形。
加强筋的厚度通常取整体胶厚的0.5-0.7倍,如大于0.7倍则容易缩水。
加强筋的高度较大时则要做0.5-1的斜度(因其出模阻力大),高度较矮时可不做斜度。
3.脱模斜度:塑料产品都要做脱模斜度,但高度较浅的(如一块平板)和有特殊要求的除外(但当侧壁较大而又没出模斜度时需做行位)。
出模斜度通常为1-5度,常取2度左右,具体要根据产品大小、高度、形状而定,以能顺利脱模和不影响使用功能为原则。
产品的前模斜度通常要比后模的斜度大0.5度为宜,以便产品开模事时能留在后模。
通常枕位、插穿、碰穿等地方均需做斜度,其上下断差(即大端尺寸与小端尺寸之差)单边要大于0.1以上。
4.圆角(R角):塑胶产品除特殊要求指定要锐边的地方外,在棱边处通常都要做圆角,以便减小应力集中、利于塑胶的流动和容易脱模。
最小R通常大于0.3,因太小的R模具上很难做到。
5.孔:从利于模具加工方面的角度考虑,孔最好做成形状规则简单的圆孔,尽可能不要做成复杂的异型孔,孔径不宜太小,孔深与孔径比不宜太大,因细而长的模具型心容易断、变形。
孔与产品外边缘的距离最好要大于1.5倍孔径,孔与孔之间的距离最好要大于2倍的孔径,以便产品有必要的强度。
与模具开模方向平行的孔在模具上通常上是用型心(可镶、可延伸留)或碰穿、插穿成型,与模具开模方向不平行的孔通常要做行位或斜顶,在不影响产品使用和装配的前提下,产品侧壁的孔在可能的情况下也应尽量做成能用碰穿、插穿成型的孔。
浅谈塑料件结构设计优化

浅谈塑料件结构设计优化摘要:本文总结了塑料件结构设计要点,以电子秤产品的塑料件设计为例,从尺寸、收缩、脱模、壁厚以及圆角等方面,详细探讨了塑料件的结构设计优化方法,并强调了设计的注意事项。
关键词:塑料件;结构;设计优化前言:塑料件是电子秤产品设计领域常用零件,塑胶材料的物理性能、制品的形状以及模具的设计,往往关系着最终产品的整体性能。
优化塑料件结构,可从根本上提高塑料件质量,对电子秤等物品整体质量的提升,具有积极意义。
1 塑料件结构设计要点塑料件结构设计要点包括材料设计、制品形状设计以及模具设计等[1]。
具体如下:(1)材料设计:塑料分为多种类型,不同塑料的物理性能差异较大,例如材料的刚度、韧性等,这些会直接影响零件的使用性能及寿命。
当设计塑料件结构时,需优先考虑其使用范围,选择好塑料材料,提高零件性能。
(2)制品形状设计:不同形状的制品,对塑料件结构设计的要求不同,同时在设计过程中也必须充分考虑注塑充模、排气、补缩、冷却、脱模等问题。
(3)模具设计:应视零件结构、制品的复杂程度等,合理选择模具结构,使模具结构能充分满足零件结构设计要求。
2 塑料件结构设计优化方法从尺寸设计、收缩与脱模、壁厚设计以及圆角设计等角度出发,阐述了塑料件结构设计的优化方法:2.1 尺寸设计塑料件尺寸是关系到零件使用是否符合电子秤产品要求的主要指标,实践经验表明,塑料件的尺寸与塑料材料以及模具的磨损和模具加热冷却等因素存在显著联系:(1)塑料原料包括多种,并且各自的收缩率也不同,由此制作的塑料件在尺寸精度方面同样存在一定的差异。
(2)模具的磨损是影响塑料件尺寸的另一个因素,零件设计过程中也考虑模具磨损问题。
(3)模具的冷却以及加热等过程,同样会对零件的尺寸产生影响。
(4)电子秤产品设计过程中,需根据零件的功能和安装位置确定尺寸精度范围,选择合适的塑料材料,确保零件的精确度能够满足使用要求。
2.2 收缩率与脱模斜度2.2.1 收缩率塑料件的收缩率,对成品的精度影响较大,应通过相关方法优化设计。
- 1、下载文档前请自行甄别文档内容的完整性,平台不提供额外的编辑、内容补充、找答案等附加服务。
- 2、"仅部分预览"的文档,不可在线预览部分如存在完整性等问题,可反馈申请退款(可完整预览的文档不适用该条件!)。
- 3、如文档侵犯您的权益,请联系客服反馈,我们会尽快为您处理(人工客服工作时间:9:00-18:30)。
塑胶件结构优化设计内容如下:1.塑胶结构设计概述2.塑胶产品设计原则3.塑胶件制程4.成型不良的原因及调节方法详解5.成型不良要因表6.常用塑料缩水率表7.常用热塑性塑造密度和密度系数表8.塑料的燃烧鉴别&塑料的燃烧特性试验9.结构优化设计塑胶结构设计概述一. 總體結構設計一套完整的模具,它函蓋有多個相關系統,它們之間相輔相成.只有當各系統達到一最佳組合,才能保證模具的正常使用和精度.因模具的結構必須符合產品的要求,不同的產品有不同的要求,而產品存在變化性和多樣性,這就決定了模具的多樣性.一般來說,典型之塑膠模具包括:澆注系統,頂出系統,溫控系統,排氣系統,抽芯系統等.為了便於理解,我們將對各系統設計原則進行分述.眾所周知,模具業為一專業性和經驗性極強的行業,模具界也深切體會到模具設計之重要,往往因設計不良,尺寸錯誤造成加工延誤,成本增加等不良效果.但培養一名足夠經驗,能獨立作業且面面具到之模具設計師,須三五年以上磨練才能達成.因他所要掌握的技能和實際經驗,函蓋到相關學科的方方面面,必須要有能力來判斷協調各系統之間的取捨輕重.1.分模面(Parting surface)為使產品從模具中取出,模具必須分成公母模側兩部分,此分界面稱之為分模面.它有分糢和排氣的作用,但因模具精度和成型之差異,易產生毛邊,結線,有礙產品外觀及精度,選擇分模面時注意:1.不可位於明顯位置而影響產品外觀.2.開模時應使產品留在有脫模機構的一側.3.位於模具加工和產品後加工容易處.4.對於同軸度要求高的產品,盡可能將型腔設計在同一側.5.避免長抽芯,考慮將其放在公模開模方向,如一定要有應將抽芯機構盡量設在公模側.6.-般不采用圓弧部分分模,這樣會影響產品外觀.7.對於流動性好易溢邊之塑料,應采用插破方式分型可防治毛邊產生.8.對於高度高,脫模斜度小之產品,可取中間分模,型腔分兩邊以有利於脫模.一套模具的分模面,可能有一個或多個,在確定分模面時,還應考慮如下因素:1.產品的形狀,尺寸,壁厚詳加研究分析,找最佳方向來分模,俗稱“拆模”.2.了解塑料性能和成型性以及澆注系統的布局.3.注意排氣和脫模,簡化模具結構,操作方便,加工容易.它的形式有多種:水平,階梯,斜面,垂直,曲面等.2.脫模斜度(Draft)為使產品容易從模具中脫出,模具上必須設置脫模斜度.其大小視產品形狀,塑料,模具結構,表面精度和加工方式不同而異.一般為1-3°,目前尚無確切數值和公式,大多是依經驗值,在不影響產品外觀和性能之情形下,脫模斜度愈大愈好.1.箱盒和蓋:2.柵格形狀,尺寸及肉厚不同應有不同的脫模斜度,經驗公式如下:0.5(A---B)/H =1/12—1/14A=大端尺寸B=小端尺寸H=高度柵格節距在4mm以下之場合,脫模斜度為1/10左右, 柵格肉厚超過8mm,斜度不可過份加大,可在母模側多留膠位處分模,如柵格段膠位加大,可考慮加大斜度.3.加強筋:可改善料流,防止應力變形,並起補強作用.a.縱肋:0.5(A-B)/H=1/500—1/200b.底肋:0.5(A-B)/H=1/150—1/100c.凸柱:0.5(大端直徑–小端直徑)/H=1/30—1/20 (內外孔在模具同一側)母模側:0.5(大端直徑–小端直徑)/H=1/50—1/30公模側:0.5(大端直徑–小端直徑)/H=1/100—1/50 (內外孔在模具兩側)注: 母模側脫模斜度可較公模側大些,以利於脫模.3.肉厚(Thickness)產品的肉厚會直接影響到成型周期和生產效率,並會因肉厚不均引起縮收下陷和應力產生,設計模具時,決定肉厚應注意:1. 產品機械強度是否充分.2. 能否均勻分散衝擊力和脫模力,不發生破裂.3. 有埋入件時,須防止破裂,是否會因肉薄產生結合線而影響強度.4. 盡可能肉厚一致,以防縮收下陷.5. 肉太薄是否會引起充填不足或阻礙料流.一般為產品上凸出之圓柱,它可增強孔的周邊強度,裝配孔及局部增高之用.必須防止因肉厚增加造成縮水和因聚集空氣造成充填不滿或燒焦現象,設計時注意點:1. 其高度以不超過本身直徑之兩倍為宜,否則須增設加強筋.2. 其位置不宜太接近轉角或側壁,以利於加工.3. 優先選擇圓形,以利於加工和料流,如在底部可高出底面0.3—0.5mm.5.孔(Hole)在多數產品上都有孔的存在,其主要有三種方法來取得:1. 在產品上直接成型2. 在產品上先成型預留孔,再機加工完成.3. 成型后完全由機加工鑽孔.設計時須注意以下幾點:1. 孔與孔之間距離須孔徑2倍以上.2. 孔與產品邊緣之距離應為孔徑之3倍以上.3. 孔之周邊宜增加肉厚.4. 孔與產品側壁之距離應為孔徑0.75倍以上.5. 孔之直徑在1.5mm以下時,很容易產生彎曲變形,須注意孔深不宜超過孔徑2倍以上.6. 分模面在中間之通孔,為防止偏心,可將不重要一側之孔徑加大.6.螺紋(scrow)為裝配之用,產品上有時會有螺紋設計,它可以直接成型,也可以在成型後再機械加工.對於經常拆卸或受力大之螺紋,則采用金屬螺紋鑲件,設計時注意如下原則:1. 螺距小於0.75mm之螺紋避免使用,最大可使用螺距5mm之螺紋.2. 因塑料收縮原因,避免直接成型長螺紋,以防螺距失真.3. 螺紋公差小於塑料收縮量時,避免使用.4. 如內外螺紋配合,須留0.1—0.4mm之間隙.5. 螺紋部分應有1--3°脫模斜度.6. 螺牙不可延長至產品末端,須設0.8mm左右之光桿部位.以利於模具加工和螺紋壽命.7. 在一些類似瓶蓋產品上,它會設一些豎琨紋,其間距宜大,最小為1.5mm,一般為3.0mm,在分模面設至少0.8mm平坦部位.7.鑲嵌件(Insert)為了防止產品破裂,增加機械強度或作為傳導電流之媒體及裝飾之用,在產品成型時常埋入鑲嵌件,注意要點:1. 保證鑲件牢靠性,鑲件周圍膠層不能太薄.2. 鑲件和鑲件孔配合時須松緊合適,不影響取放.3. 為使鑲件與塑膠結合緊密,埋入部分常設計成粗糙或凹凸之形狀(壓花.鑽孔.沖彎.切槽.倒扣等).8.其他要點(Other)1. 加強筋不可太厚,一般不超過肉厚的一半,以防縮水.2. 只要不影響外關和功能,光面盡量改為咬花面,這樣可減少模具加工難度,增加美感,防止縮水產生.3. 在凸柱周邊,可除去部分肉厚,以防止收縮下陷.4. 肉厚較薄之孔,應將孔邊及高度增加,以便補強.5. 心芯梢受收縮力影響,產品頂出時易造成破裂,可設置凸邊,承受頂出力.6. 轉角設R,可改善強度,防止應力集中有利於料流.7. 避免銳角,薄肉部份易使材料充填不足.8. 外邊有波紋之產品,為方便後加工,可改為加強邊緣.9. 分模面有階段形時,模具加工不易,考慮改為斜線或曲線分模.10. 貫穿之抽芯易發生故障,改為兩側抽芯為佳.11. 因圓形比其他形狀加工更易,可降低成本,優先選用.12. 在產品上加蝕文字或圖案時,如無特殊要求,盡量設計凹字,便於模具加工.二. 澆注系統設計澆注系統是塑模設計中一重要環節,常分為普通和無流道澆注系統.它跟所用塑料產品形狀,尺寸,機台,分模面有密切關係.設計時注意以下原則:1. 流道盡量直,盡量短,減少彎曲,光潔度在Ra=1.6—0.8um之間.2. 考慮模具穴數,按模具型腔布局設計,盡量與模具中心線對稱.3. 當產品投影面積較大時,避免單面開設澆口,以防注射受力不均.4. 澆口位置應去除方便,在產品上不留明顯痕跡,不影響產品外觀.5. 主流道設計時,避免塑料直接沖擊小型芯或小鑲件,以免產生彎曲或折斷.6. 主流道先預留加工或修正餘量,以便保證產品精度.1. 主流道設計主流道是連接機台噴嘴至分流道入口處之間的一段通道,是塑料進入模具型腔時最先經過的地方.其尺寸,大小與塑料流速和充模時間長短有密切關係.太大造成回收冷料過多,冷卻時間增長,包藏空氣增多.易造成氣泡和組織松散,極易產生渦流和冷卻不足;如流徑太小,熱量損失增大,流動性降低,注射壓力增大,造成成型困難.一般情況下,主流道會制造成單獨的澆口套,鑲在母模板上.但一些小型模具會直接在母模板上開設主流道,而不使用澆口套.主流道設計要點:1. 澆口套內孔為圓錐形( 2--6°),光潔度在Ra=1.6—0.8um.錐度須適當,太大造成壓力減少,產生濣流,易混進空氣產生氣孔,錐度過小會使流速增大,造成注射困難.2. 澆口套口徑應比機台噴嘴孔徑大1—2mm,以免積存殘料,造成壓力下降,澆道易斷.3. 一般在澆口套大端設置倒圓角(R=1—3mm),以利於料流.4. 主流道與機台噴嘴接觸處,設計成半球形凹坑,深度常取3—5mm.特別注意澆口套半徑比注嘴半徑大1—2mm,一般取R=19—22mm之間,以防溢膠.5. 主流道盡量短,以減少冷料回收料,減少壓力和熱量損失.6. 主流道盡量避免拼塊結構,以防塑膠進入接縫,造成脫模困難.7. 為避免主流道與高溫塑膠和射嘴反復接觸和碰撞造成損壞,一般澆口套選用優質鋼材加工,並熱處理.8. 其形式有多種,可視不同模具結構來選擇,一般會將其固定在模板上,以防生產中澆口套轉動或被帶出.2. 分流道設計分流道是主流道的連接部分,介於主流道和澆口之間,起分流和轉向作用.分流道必須在壓力損失最小的情況下,將熔融塑膠以較快速度送到澆口處充模,因在截面積相等的條件下,正方形之周長最長,圓形最短.面積如太小,會降低塑料流速,延長充模時間,易造成產品缺料,燒焦,銀線,縮水;如太大易積存過多氣體,增加冷料,延長生產周期,降低生產效率.對於不同塑膠材質,分流道會有所不同,但有一個設計原則:必須保證分流道的表面積與其體積之比值最小.即在分流道長度一定的情況下,要求分流道的表面積或側面積與其截面積之比值最小.分流道型式有多種,它因塑膠和模具結構不同而異,常用型式有圓形,半圓形,矩形,梯形,U形,正六邊形,如圖:設計時基本原則:1. 在條件允許下,分流道截面積盡量小,長度盡量短.2. 分流道較長時,應在末端設置冷料穴,以容納冷料和防止空氣進入,而冷料穴上一般會設置拉料桿,以便於膠道脫模.3. 在多型腔模具中,各分流道盡量保持一致,長度盡量短,主流道截面積應大於各分流道截面積之和.4. 其表面不要求過份光滑(Ra=1.6左右),有利於保溫.5. 如分流道較多時,應考慮加設分流錐,可避免熔融塑膠直接沖擊型腔,也可避免塑料急轉彎使塑膠平穩過渡.6. 分流道一般采用平衡式方式分布,特殊情況可采用非平衡方式,要求各型腔同時均衡進膠,排列緊湊,流程短,以減少模具尺寸.7. 流道設計時應先取較小尺寸,以便於試模後有修正餘量.3. 澆口設計澆口是指流道末端與型腔之間的連接部分,是澆注系統的最後部分.其作用是使塑料以較快速度進入並充滿型腔.它能很快冷卻,封閉.防止型腔內還未冷卻的熱膠倒流.設計時須考慮產品尺寸,截面積尺寸,模具結構,成型條件及塑膠性能有關.澆口盡量短小,與產品分離容易,不造成明顯痕跡,其類型多種多樣,主要有:9.盤形澆口: 沿產品外圓周而擴展進料,其進料點對稱,充模均勻,能消除結合線.有利於排氣.水口常用衝切方式去除,設計時注意衝切工藝.10.扇形澆口: 從分流道到模腔方向逐漸放大呈扇形,適用於長條或扁平而薄之產品,可減少流紋和定向應力.扇形角度由產品形狀決定,澆口橫面積不可大於流道斷面積.11.環形澆口: 沿產品整個外圓周擴展進膠,它能使塑膠繞型芯均勻充模,排氣良好,減少結合線.但澆口切除困難,它適用於薄壁長管狀產品.12.點澆口: 是一種截面積小如針狀之澆口,一般用於流動較好之塑膠,其澆口長度一般不超過其直徑,所以脫模後澆口自動切斷,不須再修正.而澆口殘痕不明顯.在箱罩,盒殼體及大面積產品中應用相當廣泛,它可以使模具增加一個分模面,便於水口脫模.其缺點是因進澆口較小易造成壓力損耗,成型時產生一些不良(流痕,燒焦,黑點)其形狀有菱形,單點形,雙點形,多點形等.13.側澆口: 一般開設在模具一邊,分模面上由內側或外側進膠,截面多為矩形,適用於一模多穴.14.直接澆口: 直接由主流道進入模腔,適用於單穴深腔殼形,箱形模具.其流道流程短,壓力損失少,有利於排氣,但澆口去除不便,會留明顯痕跡.15.潛伏澆口: 其澆口呈傾斜狀潛伏在分模面一方,在產品側面或里面進膠脫模時可自動切斷針點澆口,適用自動化生產.設計要點:1. 進膠口應開設在產品肉厚部分,保證充模順利和完全.2. 其位置應選在使塑膠充模流程最短處,以減少壓力損失,有利於模具排氣.3. 可通過模流分析或經驗,判斷產品因澆口位置而產生之結合線處,是否影響產品外觀和功能,可加設冷料穴加以解決.4. 在細長型芯附近避免開設澆口,以免料流直接衝擊型芯,產生變形錯位或彎曲.5. 大型或扁平產品,建議采用多點進澆,可防止產品翹曲變形和缺料.6. 盡量開設在不影響產品外觀和功能處,可在邊緣或底部處.7. 澆口尺寸由產品大小,幾何形狀,結構和塑膠種類決定,可先取小尺寸再根據試模狀況進行修正.8. 一模多穴時,相同的產品采用對稱進澆方式,對於不\同產品在同一模具中成型時,優先將最大產品放在靠近主流道的位置.9. 在澆口附近之冷料穴,盡端常設置拉料桿,以利於澆道脫模.4. 熱流道目前澆注系統發展和改進的一個重要方向,就是開發熱流道模具.它與一般注射模具的主要區別就是注射成型過程中,澆注系統內之塑膠不會冷卻擬固,也不會形成澆道與產品一起脫模.因此也稱無流道模具,在大型和精密模具設計中,應用已越來越廣泛.它有以下優點:1. 縮短成型周期,省去剪澆口,修整產品,破碎回收等工序,節約人力,物力,提高生產效率.2. 因無冷膠,可減少材料消耗.3. 因生產中溫度嚴格控制,顯著提高產品質量,降低次品產生.4. 因澆注系統中塑膠始終處於融熔狀態,有利於壓力傳遞,可降低注射壓力,利於成型.5. 因無澆道產生,所以可縮短開模行程,有利於模具和機台壽命.但熱流道模具結構復雜,溫度控制要求嚴格,需要精密的溫控系統,制造成本較見下表:三. 頂出系統設計產品完成一個成形周期後開模,產品會包裹在模具的一邊,必須將其從模具上取下來,此工作必須由頂出系統來完成.它是整套模具結構中重要組成部分,一般由頂出,復位和頂出導向等三部分組成.一. 按動力來分1. 手動頂出: 當模具開模後,由人工操縱頂出系統頂出產品.它可使模具結構簡化,脫模平穩,產品不易變形.但工人勞動強度大,生產率低,適用範圍不廣.一般在手動旋出螺紋型芯時使用.2. 機動頂出: 通過注射機動力或加設之馬達來推動脫模機構頂出產品,它可通過機台上的頂桿推頂針板,來達到脫模目的.也可在公母模板上安裝定距拉桿或鏈條,靠開模力拖動頂出機構頂出產品,調模時必須注意控制開模行程,適用於頂出系統在母模側之模具.3. 液壓頂出: 在模具上安裝專用油缸,由注射機控制油缸動作,其頂出力速度和時間都可通過液壓系統來調節,可在合模之前頂出系統先回位.4. 氣動頂出: 利用壓縮空氣在模具上設置氣道和細小的頂出氣孔,直接將產品吹出.產品上不留頂出痕跡,適用於薄件或長筒形產品.二. 按模具結構分一次頂出機構,二次頂出機構,母模頂出機構,澆注系統頂出機構,螺紋頂出機構等.設計原則:1. 選擇分模面時盡量使產品留在有脫模機構的一邊,2. 頂出力和位置平衡,確保產品不變形,不頂破.3. 頂針須設在不影響產品外觀和功能處.4. 盡量使用標準件,安全,可靠有利於制造和更換.頂出系統形式多種多樣,它與產品之形狀,結構和塑膠性能有關,一般有頂桿,頂管,推板,頂出塊,氣壓,復合式頂出等.一. 頂桿它是頂出機構中最簡單,最常見的一種形式,其截面積形式主要有如下:1. 圓形因圓形制造加工和修配方便,頂出效果好,在生產中應用最廣泛.但圓形頂出面積相對較小,易產生應力集中,頂穿產品,頂變形等不良.在脫模斜度小,阻力大等管形,箱形產品中盡量避免使用.當頂桿較細長時,一般設置成台階形的有托頂針,以加強剛度,避免彎曲和折斷.設計要點:1. 頂出位置應設置在阻力大處,不可離鑲件或型芯太近,對於箱形類等深腔模具.側面阻力最大,應采用頂面和側面同時頂出方式,以免產品變形頂破.2. 產品阻力均衡時,頂桿應對稱設置,使受力平衡.3. 當有細而深之加強筋時,一般在其底部設置頂桿.4. 若模具上有鑲件,頂針設在其上效果更佳.5. 在產品進膠口處避免設置頂針,以免破裂.6. 當產品表面不允許有頂出痕跡時,可設置頂出耳再剪除.7. 對於薄肉產品在分流道上設置頂針,即可將產品帶出.8. 頂針與頂針孔配合,一般為間隙配合.如太松易產生毛邊,太緊易造成卡死.為利於加工和裝配,減少摩擦面,一般在模仁上預留10—15mm之配合長度,其餘部分擴孔0.5—1.0mm成逃孔.9. 為防止頂針在生產時轉動,須將其固定在頂針板上,其形式多種多樣,須根據頂針大小,形狀,位置來具體確定,在此不一一列舉.10.頂出系統托模以後在進行下一周期生產時,必須退回原處,其形式主要有強制回位,拉桿回位,彈簧回位,油缸等.二. 頂管又叫司筒或套筒頂針,它適用於環形筒形或帶中心孔之產品頂出.由於它是全周接觸,受力均勻,不會使產品變形,也不易留下明顯頂出痕跡,可提高產品同心度.但對於周邊肉厚較薄之產品避免使用,以免加工困難和強度減弱,造成損壞.三. 推板此形式適用於各種容器,箱形,筒形和細長帶中心孔之薄件產品.它頂出平穩均勻,頂出力大,不留頂出痕.一般會有固定連接,以免生產中或托模時將推板推落.但只要導柱足夠長,嚴格控制托模行程,推板也可不固定.推板與型芯之間的配合須順暢,防止摩擦或卡死,也必須防止塑膠滲入間隙中,當產品為盲孔時,會因真空吸附造成脫模困難和產品變形,一般會在公模上設置一菌形閥,在頂出時菌形閥打開,進入空氣,使脫模順暢.它可用彈簧回位,也可跟頂出裝置連在一起兼作頂桿作用.四. 頂出塊有些帶突緣或尺寸較大之產品,為便於加工和脫模,常設計成頂出塊形式頂出.大多其平面為分模面,下面有兩支或數支較大直徑頂桿連接,頂出面積較大,平穩.在有成形面和尺寸較大之模具中應用較廣泛.五. 氣壓頂出當產品為深腔薄肉件時,用壓縮空氣頂出,簡單而有效.可在公模仁上設置一些細小進氣孔,也可設置菌形桿,開模後通入5—6個大氣壓之壓縮空氣,使彈簧壓縮開啟閥門,高壓空氣進入產品與公模仁之間,使產品脫模.但對於箱形產品,因氣體進入會使側壁橫向摳張,而使空氣漏掉,這時應配與推板配合使用.六. 復合頂出受產品形狀影響,多數模具采用兩種以上頂出方式,以便達到理想的頂出效果,具體形式須根據產品和模具結構來定,在此不作具體敘述.七. 其他頂出方式1. 點狀進膠澆道自動脫落點澆口在母模一邊,為取出膠道,須加設一分型面.開模後一般由人工取出膠道,造成操作麻煩,生產率降低,為適應自動化生產,最好設計成自動脫落裝置,使膠道在頂出時自動脫落.a. 側凹拉斷在分流道盡頭鑽一斜孔,開模後拉出膠道,由中心頂桿頂出.b. 拉料桿拉斷由拉料桿拉出膠道,開模一定行程後限位桿帶動推板將膠道推落.c. 母模推板推脫開模時母模板與母模推板先分型,膠道留在母模板與母模一起移動一定行程後,限位桿限制推板移動,推板與模板分開,膠道被拉斷而自動脫落.d. 頂針拉斷對於細長深腔模具,可在母模設置一頂出系統,開模後以限位桿行程使頂針反向頂出膠道,產品由推板推出,此方式與開模行程有關,應用較特殊.2. 母模側頂出方式一般的產品都會留在公模側頂出,但有些產品因形狀特殊或產品特殊要求,頂出裝置必須設在母模.因母模是固定的機台,頂桿無法作用在頂板上,必須借助開模力或外力來完成.常見的有油缸,電動,拉勾等.3. 螺紋頂出因螺紋與一般產品形狀特殊,必須旋轉頂出或側向脫模,根據產品復雜程度和產量,一般有采用手動和機動兩種方式.1). 強制脫螺紋a. 對於本身彈性強之塑膠(PP . PE),可利用其彈性進行強制脫模而不會損壞螺牙.b. 用具有彈性的珪橡膠做成螺紋型芯,開模時用彈簧先退出型芯中頂桿,使橡膠型芯產生向內收縮,再用頂針將產品脫出.此方式能簡化模具結構,但橡膠型芯壽命較短,只適用於小批量生產.c. 有些螺紋可通過半圓滑塊或型環成形,用兩個對半滑塊合起來組成完整螺紋或產品頂出後用手,電機將螺紋旋出.螺紋脫出時必須作相對轉動,模具上必須要有止轉裝置來保證.a. 外部止動模具母模設有止轉花紋,公模仁回轉時產品可自動脫落.b. 內部止動有內螺紋之產品在公模仁頂面設置止轉形式,脫模時止動模仁旋轉並軸向頂出螺紋可脫出,注意止動模仁螺距必須與產品螺距一致.c. 產品端面止動在產品端面設置止動小凸點,型芯旋轉時推板將產品頂出.小型產品有側澆口時,只頂出膠道也可將產品帶出,但對於軟性塑膠則避免使用.型芯旋轉驅動方式常用的有人工,電動,油缸,氣缸,液壓馬達及大螺距絲桿螺母驅動等方式,一般來講,旋轉機構在設計時,產品有幾扣螺紋,螺紋型芯就必須轉幾圈.塑料产品设计原则1﹒分模线的(parting line)选定分模线有分模及排气的作用﹐但由于模具精度及成形条件的差异﹐易生成毛边﹐及残留痕迹﹐有碍成品外观及精度﹐分模线要考虑下列项1)﹒不得位于明显位置而影响外观2)﹒开模时部成死角之位置3)﹒位于模具加工容易之位置4)﹒位于成品后加工容易加工之位置2﹒脱模斜度﹕(draft)一般塑料件都有一定的脱模斜度﹒3﹒肉厚(thickness)肉厚不均造成对成形性的影响﹕1)成品之冷却时间﹐取决于厚度较大处﹐使成形周期延长﹐生产率降低﹒2)造成冷却后﹐收缩不均3)造成收缩下陷﹐产生内应力﹐变形破裂肉厚决定必须注意下列事项﹕1)构造强度是否充分2)能否抵抗脱模力3)能否分散冲击力4)有嵌件之场合﹐能否防止破裂﹐若产生熔合线是否影响强度5)成形孔的熔合线是否影响强度6)尽可能肉均匀﹐以防止收缩下陷﹒7)棱角及薄壁是否阻碍材料流动﹐而引起充填不足﹒各种材料的标准肉厚﹕PE—0.5~3.0 ABS.AS—1.2~3.5PP—0.6~3.0 PMMA—1.5~5.0PA—0.5~3.0 硬质PVC—2.0~5.0POM—1.5~5.0 PC—1.5~5.0PS—1.2~3.5 CA—1.2~3.5PBT—0.8~3.04﹒补强与变形之防止﹕1)角耦处设计R角2)加装补强筋。