201406FDA warning letter(天津)
FDA检查表中文

私人公司或合资公司供应商评估清单私人公司或合资公司供应商评估清单审计日期(县) _______________________________审核日期由被审核者一般信息:基本信息公司(公司名称)_____________________________________________________________________地址(地址)_______________________________________________________________________工厂地址:(生产厂地址)这是确切地址在哪里制造的产品是否是这确切的地址产品是制作的地方如果没有,什么是地址如果没有,什么是地址____________________________________________________________________________________________________________________________________________________ __________________________________________________________________________主要联系人_____________________________Title_____________________________电话__________________传真_____________________电子邮件:____________________主要联系人_____________________________标题____________________________电话_________________传真_____________________电子邮件:____________________是工厂设施登记的美国食品和药物管理局( FDA )否是登记号:_______________有过工厂视察美国食品和药物管理局否是日期______________483是美国FDA发出否是如果有,请审查林业局483形式和该公司的回应美国食品和药物管理局483 。
美国FDA给予药企的警告信(含中文翻译)
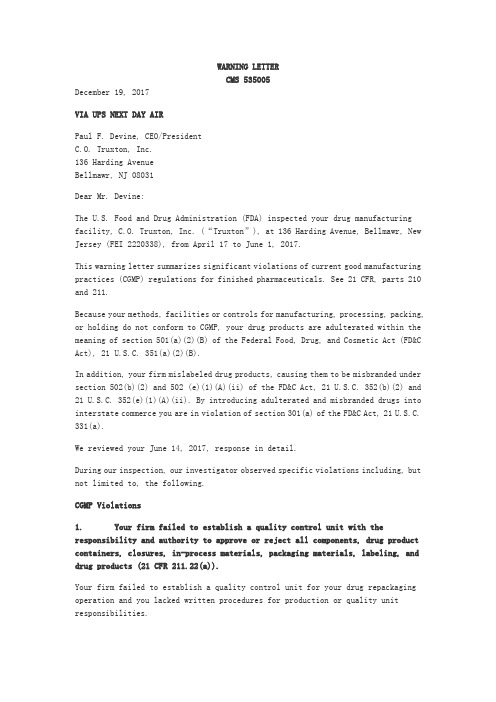
WARNING LETTERCMS 535005December 19, 2017VIA UPS NEXT DAY AIRPaul F. Devine, CEO/PresidentC.O. Truxton, Inc.136 Harding AvenueBellmawr, NJ 08031Dear Mr. Devine:The U.S. Food and Drug Administration (FDA) inspected your drug manufacturing facility, C.O. Truxton, Inc. (“Truxton”), at 136 Harding Avenue, Bellmawr, New Jersey (FEI 2220338), from April 17 to June 1, 2017.This warning letter summarizes significant violations of current good manufacturing practices (CGMP) regulations for finished pharmaceuticals. See 21 CFR, parts 210 and 211.Because your methods, facilities or controls for manufacturing, processing, packing, or holding do not conform to CGMP, your drug products are adulterated within the meaning of section 501(a)(2)(B) of the Federal Food, Drug, and Cosmetic Act (FD&C Act), 21 U.S.C. 351(a)(2)(B).In addition, your firm mislabeled drug products, causing them to be misbranded under section 502(b)(2) and 502 (e)(1)(A)(ii) of the FD&C Act, 21 U.S.C. 352(b)(2) and 21 U.S.C. 352(e)(1)(A)(ii). By introducing adulterated and misbranded drugs into interstate commerce you are in violation of section 301(a) of the FD&C Act, 21 U.S.C. 331(a).We reviewed your June 14, 2017, response in detail.During our inspection, our investigator observed specific violations including, but not limited to, the following.CGMP Violations1. Your firm failed to establish a quality control unit with the responsibility and authority to approve or reject all components, drug product containers, closures, in-process materials, packaging materials, labeling, and drug products (21 CFR 211.22(a)).Your firm failed to establish a quality control unit for your drug repackaging operation and you lacked written procedures for production or quality unit responsibilities.You did not address this observation in your response. You stated that “some items were not addressed, as they should not have been done and will not be done by C.O. Truxton Inc., in the future.” We are unclear as to what specific items you referred to in your response.In your response to this letter, provide your procedure detailing the responsibilities of the quality control unit, and outline your repackaging operations with their corresponding procedures. In addition, specify which operations your firm has ceased to perform and the dates on which such operations were halted.2. Your firm failed to establish and follow written procedures to assure that correct labels and packaging materials are used for drug products (21 CFR 211.130).Your firm performs repackaging and labeling operations but did not have written procedures governing the application of packaging and labeling materials to your drug products. You incorrectly labeled a container filled with Phenobarbital tablets 30 mg as Phenobarbital tablets, USP 15 mg (schedule IV) lot 70952A. In the affidavit collected during the inspection, you stated, “I have no records to show the repackaging operation.”You did not address this observation in your response. In your response to this letter, provide your plan, including written procedures, to ensure compliance with CGMP for all drug repackaging activities in which you engage.3. Your firm failed to establish and follow adequate written procedures describing the handling of all written and oral complaints regarding a drug product (21 CFR 211.198(a).Your firm lacked an adequate procedure for handling complaints. You received a complaint regarding a bottle labeled as Phenobarbital Tablets USP (15 mg, 1000 count), lot 70952A. The product received was actually Phenobarbital Tablets USP (30 mg, 1000 count.) You sold this drug product to both human and animal clinics. Your firm did not maintain a record of the complaint or investigate it to determine the cause of the labeling mix-up.In response to our inspection, you drafted and submitted a complaint handling procedure. However, this procedure is inadequate because it lacks adequate provisions to investigate the complaints you receive.In your response to this letter, provide your complaint handling procedure, including cataloguing, tracking, and investigating complaints.4. Your firm failed to establish a written distribution procedure to includea system by which each lot of drug product can be readily determined to facilitate its recall if necessary (21 CFR 211.150(b)).Your firm lacked any procedures describing your drug distribution system. Your distribution system was deficient in that it could not differentiate between the lot number your firm assigns and the lot number assigned by the manufacturer, and therefore there is no product traceability if a recall is required. Our investigator observed that neither your receiving or shipping records included the lot numbers of products you received and shipped.In your response, you stated that, moving forward, only Phendimetrazine manufactured and packaged by (b)(4)will bear the Truxton label. Your response was inadequate because you did not address your firm’s lack of traceability for your repackaged drug products.In your response to this letter, provide your drug distribution and tracking procedures for your repackaged drug products.5. Your firm failed to establish and follow a written testing program designed to assess the stability characteristics of drug products and to use results of such stability testing to determine appropriate storage conditions and expiration dates (21 CFR 211.166(a)).You had no data to support the expiration date of Phenobarbital tablets, USP 15 mg (schedule IV) lot 70952A repackaged from original container-closure system(500-count bottle size) to a new container- closure system (1000-count bottle size). You had not performed stability testing of the drug product in the newcontainer-closure system and you did not have any supporting stability data to support the use of the new container-closure system. In addition, you were unable to provide documentation to show that the container-closure system used to repackage drug products was identical or equivalent to their original container-closure systems.You did not address this observation in your response. In your response to this letter, provide your evaluation of any other drug products that may have been repackaged into a different container-closure system, and the procedures and controls you have in place to assess stability of the drug products in their new container-closure systems. Include your corrective action plan if you find drug products that are unstable in the new container-closure system.Misbranding ViolationsYour phenobarbital tablets were labeled as containing 15 mg of Phenobarbital but in fact the tablets contained 30 mg of Phenobarbital. Further, as labeled, the Phenobarbital 15 mg tablets are misbranded drugs within the meaning of section 502(b)(2) of the FD&C Act, 21 U.S.C. 352(b)(2), in that the labels for these packaged drug products did not bear an accurate statement of the quantity or the contents in terms of weight, measure, or numerical count. Also, your Phenobarbital 15 mg tablets are misbranded within the meaning of section 502(e)(1)(A)(ii) of the FD&C Act, 21 U.S.C. 352(e)(1)(A)(ii), in that the drug product is labeled as Phenobarbital15 mg, and the proportion of the active ingredient in each phenobarbital tablet is 30 mg of Phenobarbital (as identified by tablet markings)In addition to the CGMP violations, your firm repackaged mislabeled drugs in violation of the FD&C Act at your facility. Based on the information collected during the inspection, you mislabeled the following prescription drug, including, but not limited to: Phenobarbital Tablets 30 mg mislabeled as Phenobarbital Tablets 15 mg.As labeled, the Phenobarbital Tablets are misbranded drugs within the meaning of section 502(a) of the FD&C Act, 21 U.S.C. 352(a), in that the labels are false.ConclusionViolations cited in this letter are not intended as an all-inclusive list. You are responsible for investigating these violations, for determining the causes, for preventing their recurrence, and for preventing other violations.If you are considering an action that is likely to lead to a disruption in the supply of drugs produced at your facility, FDA requests that you contact CDER’s Drug Shortages Staff immediately, at*********************.gov,so that FDA can work with you on the most effective way to bring your operations into compliance with the law. Contacting the Drug Shortages Staff also allows you to meet any obligations you may have to report discontinuances or interruptions in your drug manufacture under 21 U.S.C. 356C(b) and allows FDA to consider, as soon as possible, what actions, if any, may be needed to avoid shortages and protect the health of patients who depend on your products.Correct the violations cited in this letter promptly. Failure to promptly correct these violations may result in legal action without further notice, including, without limitation, seizure and injunction.Unresolved violations in this warning letter may also prevent other federal agencies from awarding contracts.Until these violations are corrected, we may withhold approval of pending drug applications listing your facility, or remove your current misbranded drugs listing information from public databases such as the online NDC Directory. We may re-inspect to verify that you have completed your corrective actions.We may also refuse your requests for export certificates.After you receive this letter, respond to this office in writing within 15 working days. Specify what you have done since our inspection to correct your violations and to prevent their recurrence. If you cannot complete corrective actions within 15 working days, state your reasons for delay and your schedule for completion.Send your firm’s response to the U.S. Food and Drug Administration, 10 Waterview Boulevard, 3rdFloor, Parsippany, New Jersey 07054. Refer to CMS case 535005 whenreplying. If you have any questions about this letter, please contact CDR Liatte Krueger, Compliance Officer, at (973) 331-4933.Sincerely,/S/Diana Amador-ToroDivision Director/OPQ Division 1New Jersey District Office警告信CMS 5350052017年12月19日首席执行官兼总裁Paul F. DevineC.O. 如织,Inc.136 哈丁大道贝尔玛尔,NJ 08031尊敬的Devine先生:美国食品和药物管理局(FDA)于2017年4月17日至6月1日在新泽西贝尔玛尔市哈丁大街136号(FEI 2220338)检查了你的药物生产设施C.O. Truxton,Inc.。
Warning Letters _ Hospira Spa 3_31_15

U.S. Food and Drug AdministrationProtecting and Promoting Your HealthHospira Spa 3/31/15Department of Health and Human ServicesPublic Health ServiceFood and Drug AdministrationSilver Spring, MD 20993Warning LetterCERTIFIED MAILRETURN RECEIPT REQUESTEDWL: 320-15-08 March 31, 2015Mr. Michael BallChief Executive OfficerHospira S.p.A.275 N. Field DriveLake Forest, IL 60045USADear Mr. Ball:During our May 5-9 and 12-13, 2014 inspection of your pharmaceutical manufacturing facility, Hospira S.p.A., located at Via Fosse Ardeatine 2, Liscate, Italy, investigators from the U.S. Food and Drug Administration (FDA) identified significant violations of current good manufacturing practice (CGMP) regulations for finished pharmaceuticals, Title 21, Code of Federal Regulations, Parts 210 and 211. These violations cause your drug products to be adulterated within the meaning of Section 501(a)(2)(B) of the Federal Food, Drug, and Cosmetic Act (the Act), 21 U.S.C. 351(a) (2)(B), in that the methods used in, or the facilities or controls used for, their manufacture, processing, packing, or holding do not conform to, or are not operated or administered inconformity with, CGMP.We have conducted a detailed review of your firm’s response dated June 4, 2014 and note that it lacks sufficient corrective actions. We acknowledge receipt of your firm’s correspondence dated August 4, 2014, October 2, 2014, December 4, 2014, and February 9, 2015Our investigators observed specific violations during the inspection, including, but not limited to, the following:1. Your firm failed to establish and follow appropriate written procedures that are designed to prevent microbiological contamination of drug products purporting to be sterile, and that include validation of all aseptic and sterilization processes (21 CFR 211.113(b)).Your firm did not evaluate all critical operations during dynamic airflow studies to determine risk to product sterility.a) Your firm did not evaluate significant aseptic interventions during dynamic airflow studies (smoke studies) to determine how the movement of air and personnel during aseptic operations could pose risks to product sterility. For example,i. Your smoke studies did not evaluate the impact of operators pushing (b)(4) vials down achute while simultaneously removing a (b)(4) located (b)(4) the chute to load vials in thedesignated (b)(4). The inspection documented that (b)(4) from the vials during this (b)(4) vial transfer operation, potentially exposing the product in the vials to contaminants frompersonnel or the surrounding environment. In addition, during our inspection, the investigator observed operators reaching over the (b)(4) vials during this operation, an action which could compromise product sterility by introducing microbiological contaminants.Your investigation on February 18, 2013, documented that you were aware of problemscaused by the (b)(4) vial loading operation. Exception report record, PR ID 119409, noted that the (b)(4) vial loading operation frequently results in rough aseptic transitions. However, our investigator observed operators continuing this practice over a year after you closed PR ID119409. It did not appear that you had acted on your findings to correct this problem orprevent its recurrence, and the sterility of your products may have been compromised in the meantime.ii. You did not perform smoke studies to demonstrate unidirectional airflow for set-upactivities of the aseptic fill line or for the (b)(4) transfer of (b)(4) vials from the vial holding area to the (b)(4). Your smoke studies also did not show unidirectional airflow above the un-stoppered vials that pass (b)(4) the stopper loading chute. Without smoke study data todemonstrate that air flows unidirectionally over these critical operations and processingsteps, you cannot show that your processes are designed to prevent microbiologicalcontamination of your products or provide adequate assurance of product sterility.iii. We also note that your stopper (b)(4) creates air turbulence in the area around thestopper loading chute, which could lead to additional opportunities for microbiologicalcontamination.The examples listed above show how disruptions to the unidirectional flow of air could lead to the contamination of product in exposed vials. We acknowledge your response that you have performed smoke studies, and made limited modifications to the operation in an effort to reduce risks posed by the design deficiencies identified in our inspection. For example, we note that you made some minor changes to reduce rocking of the (b)(4) during the (b)(4) vial transfer operation described above in 1. a) 1. However, your response is inadequate because you have not committed to provide a thorough design assessment. You also failed to provide a video of the new smoke studies you indicated that you performed.In response to this letter, please describe further design modifications you will make to mitigate the contamination hazards in your operation, including, but not limited to, the examples discussed above in examples 1. a)1-3. Also, provide a copy of the video/DVD depicting smoke studies you performed to demonstrate unidirectional airflow during the manufacturing operations described above.b) Your firm rejected possible integral units (i.e., units with intact container/closure systems) from media fills without a written justification or explanation. For example, during media fill batch (b)(4) (June 2012), you rejected 5 vials as “tilted” and you also rejected 250 vials during the (b)(4) process without explanation or justification. Similarly, during media fill batch (b)(4) (December 2013), you rejected 21 vials as “tilted” and you also rejected 30 vials during the (b)(4) process without explanation or justification. During the inspection, your management told the investigator that the vials you rejected as “tilted” would likely be fully stoppered and integral. Your media fill batch records did not include any further rationale for rejecting these vials, although many of them were likely integral.When you perform a final product inspection of units immediately following a media fill run, all integral units should proceed to incubation. Units found to have defects not related to integrity (e.g., cosmetic defects) should be incubated; units that lack integrity should be rejected. Erroneously rejected units should be returned promptly for incubation with the media fill lot. After incubation is underway, any unit found to be damaged should be included in the data for the media fill run because the units might be representative of drug product released to the market. Any decision to exclude non-integral units from the final run tally should be fully justified and you should fully explain the deviation in your media fill report. If a correlation emerges between difficult to detect damageand microbial contamination, you should conduct a thorough investigation to determine its cause.We acknowledge that you completed a media fill performance qualification. However, your protocol, Shut Dow n Media Fill Qualification Protocol KC4103-PQ, is inadequate because it does not provide criteria that adequately defines when vials are to be rejected. In your response to this letter, provide your categorization criteria and justification for rejection of vials from a media fill.These violations are similar to those found during the October 2012 inspection of your Irugattukottai, Sriperumburdur, India manufacturing site. Dynamic airflow study and media fill deficiencies were noted in Warning Letter (WL: 320-13-18), issued May 28, 2013. Your response to that warning letter stated that you implemented your Global Quality Strategy and Global Quality Plan in February 2013for your manufacturing facilities. Provide evidence of the effectiveness of your implemented global corrective actions and preventive actions.2. Your firm failed to thoroughly investigate any unexplained discrepancy or failure of a batch or any of its components to meet any of its specifications, whether or not the batch has already been distributed (21 CFR 211.192).For example, your firm failed to conduct a thorough investigation for 103 complaints for (b)(4) injection related to discoloration of (b)(4) or (b)(4) solution between November 1, 2011 and October 31, 2013, and a more recent complaint on April 3, 2014. Many customer complaints have stated that the product changed to a (b)(4) color, rather than the normal “(b)(4)” appearance. You concluded that the root cause for the discoloration was the (b)(4) of the product. Your investigation is inadequate because you failed to evaluate the impact that (b)(4) may have on the quality of the product and to correlate the level of (b)(4) degradant with the amount of discoloration observed. Your investigation also failed to consider that the discoloration might have been caused by the failure to perform a step in the manufacturing process in an (b)(4) environment. Specifically, you mention that some vials may have (b)(4) as a result of them (b)(4) shelf during the stoppering manufacturing phase. You state that the unloading of the vials from the (b)(4) to (b)(4) is not performed (b)(4) and that there is a potential for (b)(4) ingress.We acknowledge your commitment to continue the investigation of (b)(4) levels in (b)(4) vials per protocol KC3601-ENG. However, your response does not adequately address the impact of the effect of (b)(4) in that your medical assessment lacks an evaluation of whether the degradant poses a risk to patients.In addition, your firm has not adequately addressed vulnerabilities in your manufacturing process that can be addressed to prevent the potential ingress of (b)(4).Please provide a protocol and timeline for the assessment of your manufacturing process to controlthe level of (b)(4) in the vial (b)(4). Also, include your scientific rationale that the level of the (b)(4) degradant has no meaningful impact on product quality.Please also explain whether your firm will be identifying and quantifying the (b)(4) degradant, and any other major degradants, and if you have determined that appropriate specification limits should be established.In your response, you indicate that your appearance specification ((b)(4)) is subjective. Please explain how you intend to qualify the appearance specification for the (b)(4) finished product.3. Your firm failed to exercise appropriate controls over computer or related systems to assure that only authorized personnel institute changes in master production and control records, or other records (21 CFR 211.68(b)).Specifically, your high performance liquid chromatography (HPLC) and gas chromatography (GC) data acquisition software, TotalChrom®, did not have sufficient controls to prevent the deletion or alteration of raw data files. During the inspection, the investigator observed that the server that maintains electronic raw data for HPLC and GC analyses (the J drive) contains a folder named “Test,” and that chromatographic methods, sequences, and injection data saved into this folder can be deleted by analysts. The investigator also found that data files initially created and stored in the “Test” folder had been deleted, and that back-up files are overwritten (b)(4).In addition, because no audit trail function was enabled for the “Test” folder, your firm was unable to verify what types of injections were made, who made them, or the date or time of deletion. The use of audit trails for computerized analytical instrumentation is essential to ensure the integrity and reliability of the electronic data generated.Your response indicates that you have added computer controls to prevent the deletion of folders and files in the J drive for electronic raw data. However, you provide no evidence demonstrating how your firm will prevent deletion of newly created folders and files in each of your computer systems. We acknowledge your commitment to hire a third party consultant to address the inadequacies of your data systems. However, your response is inadequate as it fails to address how you will enable and review audit trail functions for all of your analytical computer systems.In response to this letter, provide specific details about the comprehensive controls in place to ensure the integrity of electronic raw data generated by all computer systems used to support the manufacture and testing of drug products. Your response should demonstrate an understanding of your processes and the appropriate controls needed for each stage of manufacture that generates electronic raw data, as well as for your laboratories.We identified a similar inspectional finding during the December 2013 inspection of yourIrugattukottai, Sriperumburdur, India, manufacturing facility and noted this finding in an Untitled Letter, issued April 16, 2014. Explain how your firm will implement global corrective actions and preventive actions concerning computer controls and provide a timeline for implementation.4. Your firm failed to ensure that laboratory records included complete data derived from all tests necessary to assure compliance with established specifications and standards (21CFR211.194(a)).a) Our investigators identified your practice of performing trial sample injections for HPLC analyses. For example, trial injections of (b)(4) stability samples (lot (b)(4) and (b)(4)) were acquired in the “Test” folder prior to official testing. Immediately after the trial injections were completed, the official samples were analyzed. The trial injection raw data, captured in the back-up files, were deleted from the test folder.b) You retested analytical samples without reporting original results in laboratoryrecords. Because of this practice, you are unable to assure that all raw data generated is included and evaluated when you review analytical test results to determine whether your products conform with their established specifications and standards.For example, (b)(4) lot #(b)(4) failed the content uniformity test, where sample #8 of (b)(4) resulted with a value (b)(4)%. Your firm proceeded to retest the sample on a different instrument without initiating an out-of-specification (OOS) investigation, as required by your chemistry laboratory investigation standard operating procedure, SOP QAG-097. These injections were not reported as part of the original data or included in your laboratory investigation report. Subsequently, the electronic raw data files were deleted. Moreover, there is no procedure describing the use of re-injections for standards or samples on a different system to verify an original result.Your response indicates that the “Test” folders were used to equilibrate the analytical columns and to determine when the system was ready for analysis. It is your responsibility to follow validated methods that include specific procedures to assess the suitability of your instruments. Neither the ICH document Q2R, "Validation of Analytical Procedure: Text and Methodology," nor the United States Pharmacopoeia (USP), General Chapter <1058>, "Analytical Instrument Qualification," provides for use of “trial” injections as part of a validated method. Your rationale that you retested failing samples on different analytical instrumentation to evaluate system suitability is inadequate. See USP General Chapter <621>, “Chromatography,” which discusses system suitability tests and the use of replicate injections of a standard preparation or other standards to determine if the requirements for precision are satisfied.These are serious CGMP violations that demonstrate that your quality system does not adequately ensure the accuracy and integrity of the data you generate to support the safety, effectiveness, and quality of the drug products you manufacture. We acknowledge your commitment to work with athird party consultant to conduct a comprehensive assessment of your firm’s manufacturing, laboratory, and quality operations. However, it is your responsibility to ensure that the third party audit includes a full evaluation of sophisticated electronic systems and the potential for manipulation of such systems. In response to this letter, provide the following to the Agency:1. A comprehensive evaluation of the extent of the inaccuracy of the reported data. As part of your comprehensive evaluation, provide a detailed action plan to investigate the extent of the deficient documentation practices noted above;2. A risk assessment regarding the potential effect on the quality of drug products. As part of your risk assessment, determine the effects of your deficient documentation practices on the quality of the drug product released for distribution; and3. A management strategy for your firm that includes the details of your global corrective action and preventive action plan.a) As part of your corrective action and preventive action plan, describe the actions youhave taken or will take, such as contacting your customers, recalling product, conductingadditional testing and/or adding lots to your stability programs to assure stability, monitoring of complaints, or other steps to assure the quality of the product manufactured under theviolative conditions discussed above.b) In addition, as part of your corrective action and preventive action plan, describe theactions you have taken or will take, such as revising procedures, implementing new controls, training or re-training personnel, or other steps to prevent the recurrence of CGMP violations, including breaches of data integrity.The violations cited in this letter are not intended to be an all-inclusive list of violations that exist at your facility. You are responsible for investigating and determining the causes of the violations identified above and for preventing their recurrence and the occurrence of other violations.If, as a result of receiving this warning letter or for other reasons, you are considering a decision that could reduce the number of finished drug products produced by your manufacturing facility, FDA requests that you contact CDER's Drug Shortages Program immediately, as you begin your internal discussions, at drugshortages@ so that we can work with you on the most effective way to bring your operations into compliance with the law. Contacting the Drug Shortages Program also allows you to meet any obligations you may have to report discontinuances in the manufacture of your drug under 21 U.S.C. 356C(a)(1), and allows FDA to consider, as soon as possible, what actions, if any, may be needed to avoid shortages and protect the health of patients who depend on your products. In appropriate cases, you may be able to take corrective action without interrupting supply, or to shorten any interruption, thereby avoiding or limiting drugshortages.Until all corrections have been completed and FDA has confirmed corrections of the violations and your firm’s compliance with CGMP, FDA may withhold approval of any new applications or supplements listing your firm as a drug product manufacturer. In addition, your failure to correct these violations may result in FDA refusing admission of articles manufactured at Hospira S.p.A located at Via Fosse Ardeatine 2, Liscate, Italy into the United States under Section 801(a)(3) of the Act, 21 U.S.C. 381(a)(3). The articles may be subject to refusal of admission pursuant to Section 801(a)(3) of the Act, 21 U.S.C. 381(a)(3), in that the methods and controls used in their manufacture do not appear to conform to CGMP within the meaning of Section 501(a)(2)(B) of the Act, 21 U.S.C. 351(a)(2)(B).Within fifteen working days of receipt of this letter, please notify this office in writing of the specific steps that you have taken to correct and prevent the recurrence of violations, and provide copies of supporting documentation. If you cannot complete corrective actions within fifteen working days, state the reason for the delay and the date by which you will have completed thecorrections. Additionally, if you no longer manufacture or distribute the drug products at issue, provide the date(s) and reason(s) you ceased production. Please identify your response with FEI # 3004640070.Please send your reply to:Christina Alemu-CruickshankCompliance OfficerU.S. Food and Drug AdministrationCenter for Drug Evaluation and ResearchOffice of Manufacturing QualityDivision of Drug Quality IWhite Oak, Building 51 room 423310903 New Hampshire Ave.Silver Spring, MD 20993Sincerely,/S/Thomas Cosgrove, J.D.DirectorOffice of Manufacturing QualityOffice of ComplianceCenter for Drug Evaluation and ResearchMore in Compliance Actions and ActivitiesMore in Compliance Actions and Activities(/ICECI/EnforcementActions/default.htm)Warning Letters (/ICECI/EnforcementActions/WarningLetters/default.htm) 2015 (/ICECI/EnforcementActions/WarningLetters/2015/default.htm)2014 (/ICECI/EnforcementActions/WarningLetters/2014/default.htm)2013 (/ICECI/EnforcementActions/WarningLetters/2013/default.htm)2012 (/ICECI/EnforcementActions/WarningLetters/2012/default.htm)2011 (/ICECI/EnforcementActions/WarningLetters/2011/default.htm)2010 (/ICECI/EnforcementActions/WarningLetters/2010/default.htm)2009 (/ICECI/EnforcementActions/WarningLetters/2009/default.htm)2008 (/ICECI/EnforcementActions/WarningLetters/2008/default.htm)2007 (/ICECI/EnforcementActions/WarningLetters/2007/default.htm)2006 (/ICECI/EnforcementActions/WarningLetters/2006/default.htm)2005 (/ICECI/EnforcementActions/WarningLetters/2005/default.htm) Tobacco Retailer Warning Letters(/ICECI/EnforcementActions/WarningLetters/Tobacco/default.htm)。
最新FDA警告信:包装问题,数据完整性问题,投诉处理问题

最新FDA警告信:包装问题,数据完整性问题,投诉处理问题Warning letter due to insufficient container-/closure integrity由于包装密闭完整性不充分引发的警告信A site of the company Hospira in Italy received a comprehensive FDA Warning Letter at the end of March which criticises among others defects concerning the closure of vials and the related possible microbiological contaminations. Main problem for the FDA is that operators carried out operations over the vials that pose a microbiological risk for the product. Furthermore, the company did not perform smoke studies to demonstrate unidirectional airflow as protection for the product. This is aggravated by the fact that the FDA has criticised this already in 2013 and nothing has changed. According to the FDA this means that the sterility of the products produced since then is questioned. The FDA is clearly missing a video demonstrating the airflow and thus the protection of the product as well as a detailed assessment of the filling equipment design. HOSPIRA公司的一个意大利工厂在3月底收到FDA警告信,其中批评了关于西林瓶的密闭问题,以及疑似微生物污染问题。
FDA警告信案例分析

引言:本文将对FDA警告信案例进行分析,探讨其背后的原因及其对相关方面的影响。
FDA警告信是美国食品药品监督管理局(FDA)发出的一种警告通知,用于指导企业改正违规行为并确保产品的质量和安全性。
通过对一系列案例的详细研究,我们可以了解到FDA警告信的种类、常见的违规行为以及企业如何应对。
概述:FDA是美国联邦政府机构,负责监督和确保食品、药品、医疗器械等产品的质量和安全性。
FDA警告信是该机构在检查中发现企业存在违规行为时发出的一种警告通知。
这些警告信要求企业迅速采取行动,纠正违规行为,并确保产品符合规定。
警告信的内容通常包括违规事项的描述、必须采取的行动以及违规行为对公众健康和企业声誉的潜在影响。
正文内容:1.案例一:违规生产1.1.产品质量问题1.2.生产过程违规行为1.3.企业应对措施1.4.影响及教训2.案例二:虚假宣传2.1.不实的广告宣传2.2.虚假的临床试验结果2.3.企业应对措施2.4.影响及教训3.案例三:产品安全问题3.1.不当使用材料3.2.产品设计缺陷3.3.企业应对措施3.4.影响及教训4.案例四:违规销售4.1.未经批准销售4.2.超出销售范围4.3.企业应对措施4.4.影响及教训5.案例五:违规操作5.1.不符合生产标准5.2.未经批准的更改5.3.企业应对措施5.4.影响及教训总结:通过对FDA警告信案例的分析,我们可以看到违规行为的多样性以及其对企业和公众的潜在影响。
而企业应对违规行为的措施和行动则是决定其未来发展的关键。
从这些案例中我们可以得出结论,企业需要高度重视对产品质量和安全的管理,遵循相关的法规和规定,并确保企业内部的管理和操作符合标准。
及时、透明地回应FDA警告信,并采取具体措施改进存在的问题,对于维护企业声誉和建立公众信任至关重要。
总体而言,FDA警告信案例分析提供了宝贵的经验教训,帮助企业了解FDA的监管标准,规避违规行为,保障产品质量和安全性,提升企业竞争力和可持续发展。
浅谈美国医用食品(Medical Foods)的监管法规与市场准入

42 食品安全导刊 2019年1~2月
浅谈美国医用食品(Medical Foods)的监管法规与市场准入
□ 陶鑫 霍金路伟律师事务所华盛顿办公室
特殊医学用途配方食品(简称“特医食品”)是指为满足进食受限、消化吸收障碍、代谢紊乱或特定疾病状态人群对营
养或膳食的特殊需求,专门加工配制而成的配方食品。
2016年《特殊医学用途配方食品注册管理办法》的实施标志着我国特殊医学用途配方食品市场正式开放;2017年4月,原国家食品药品监督管理总局成立了特殊食品注册管理司;截至2018年10月,累计共有18款特医食品获得国家市场监督管理总局的相关批文。
在美国,特殊医学用途配方食品又被称为“医用食品”(Medical Foods),并于1988年修订的《孤儿药法案》(Orphan
Drug Act,也称“罕见病药物法案”)中首次被明确定义。
经过多年的发展,医用食品市场在美国已十分成熟。
本文浅谈美国医用食品的监管与市场准入的相关法规,以期对国内特医食品厂商的前瞻性布局有所启示。
法律视角
Jan~Feb 2019 CHINA FOOD SAFETY
43。
FDA检查常见三种文件

FDA检查常见三种文件Form 483 #483表格This form with the eponymous number 483 is used by the executing Inspector (FDA Investigator) to document the deficiencies he found. It is issued at the end of the inspection and should be answered officially. This response is expected within 15 working days after its issuance. Only then it is guaranteed that the statement will be taken into account in a possible Warning Letter (see below). Sometime, in the case of reasonable compliance, no 483 is issued.483表格用于执行检查的检查员(FDA调查员)记录其所发现的缺陷。
在检查结束时检查员要签发该表格,受检企业则需要对其中缺陷进行正式回复。
对该表格中缺陷的回复需要在其签署后的15个工作日内提交。
只有在收到回复后,才会可能做出决定是否签发警告信(见下)。
有时,在达到合理符合的情况下,没有483表格签出来。
EIR: Establishment Investigation Report 工厂调查报告The EIR is also created by the Inspector in addition to the form 483. This should be done within 30 working days. The EIR is then examined by the responsible Center or District Office of the FDA, issuing the following statuses:除了483表以外,检查员还要制作EIR。
fda警告信回顾与案例解读

FDA警告信回顾与案例解读:FDA(美国食品药品监督管理局)在保护公众健康方面起着至关重要的作用,通过发出警告信来确保公众安全使用药品、医疗器械、食品和其他产品。
这些警告信是对企业违规行为的严肃提醒,并可能对企业造成严重的财务和声誉影响。
本文将对一些FDA警告信的回顾与案例解读,旨在提供一些有用的信息和建议。
一、FDA警告信回顾1. 涉及不合规行为的警告信FDA发出警告信的主要原因是发现企业的产品或行为不符合相关法规要求。
这些不合规行为可能涉及药品、医疗器械、食品等多个领域,例如:未通过审批擅自上市、生产过程存在缺陷、产品存在安全隐患等。
在发出警告信之前,FDA通常会进行现场检查和产品抽检,以确保企业遵守相关法规。
2. 警告信对企业的影响FDA发出的警告信对企业的影响非常大。
首先,警告信可能导致企业面临财务损失,因为需要花费大量资金来整改和符合法规要求。
此外,警告信还会对企业的声誉造成影响,可能使企业失去客户的信任和支持。
如果企业未能在规定时间内完成整改,FDA可能会采取更严厉的措施,例如:撤销产品的批准文号或禁止企业从事相关业务。
二、案例解读1. 案例一:未通过审批擅自上市某制药企业未经FDA批准就擅自上市了一款新药。
在FDA进行现场检查时,发现了这一违规行为。
FDA发出了警告信,要求企业立即停止销售该药品,并进行了罚款。
这一案例提醒企业必须遵守相关法规,确保产品符合审批要求。
2. 案例二:生产过程存在缺陷某医疗器械生产企业由于生产过程中存在缺陷,导致产品不合格。
FDA在抽检时发现了这一问题,发出了警告信。
企业需要花费大量资金对生产线进行整改,并重新申请审批。
这一案例提醒企业必须重视生产过程中的质量控制,确保产品符合标准。
3. 案例三:产品存在安全隐患某食品生产企业生产的食品被发现存在安全隐患,可能对消费者健康造成影响。
FDA发出了警告信,要求企业立即召回问题产品,并进行了罚款。
这一案例提醒企业必须对产品进行严格的安全性评估,确保产品安全可靠。
- 1、下载文档前请自行甄别文档内容的完整性,平台不提供额外的编辑、内容补充、找答案等附加服务。
- 2、"仅部分预览"的文档,不可在线预览部分如存在完整性等问题,可反馈申请退款(可完整预览的文档不适用该条件!)。
- 3、如文档侵犯您的权益,请联系客服反馈,我们会尽快为您处理(人工客服工作时间:9:00-18:30)。
【GMP缺陷】g011 201406 FDA警告信(天津某药厂) Warning LetterCERTIFIED MAIL WL: 320-14-09RETURN RECEIPT REQUESTEDJune 10, 2014Mr. Li ZhengenGeneral ManagerTianjin Zhongan Pharmaceutical Co. Ltd.No. 188 Fukang RoadXiqing DistrictTianjin 300384ChinaDear Mr. Li Zhengen:During our September 23-27, 2013 inspection of your pharmaceutical manufacturing facility, Tianjin Zhongan Pharmaceutical Co. Ltd., located at No. 188 Fukang Road, Xiqing District, Tianjin, China, an investigator from the U.S. Food and Drug Administration (FDA) identified significant deviations of current good manufacturing practice (CGMP) for the manufacture of active pharmaceutical ingredients (APIs). These deviations cause your APIs to be adulterated within the meaning of Section 501(a)(2)(B) of the Federal Food, Drug, and Cosmetic Act (the Act), 21 U.S.C. 351(a)(2)(B), in that the methods used in, or the facilities or controls used for, their manufacture, processing, packing, or holding do not conform to, or are not operated or administered in conformity with, CGMP.We have conducted a detailed review of your firm’s response and note that it lacks sufficient corrective actions.Our investigator observed specific deviations during the inspection, including, but not limited to, the following:检查中所发现的缺陷包括,但不仅限于以下1. Failure to adequately complete and follow written procedures for cleaning equipment and its release for use in API manufacture, and to maintain adequate records of major equipment usage.未能完全遵守书面的设备清洁程序,将其放行用于原料药生产,主要设备使用记录不充分。
Your firm failed to ensure that employees adequately cleaned (b)(4) after use. Your (b)(4) equipment cleaning standard operating procedures (SOP-HE 063-02 - instruction 4.2.2.1, SOP-HE 064-02 –instruction 4.3.4.3, and SOP-HE 055-02 –instruction 4.2.1.1), require that employees visually inspect equipment after the cleaning process. Our inspection found (b)(4) in the manufacturing workshop for (b)(4) with various levels of contamination and foreign objects inside, including what looked like the remains of a pen in one of the (b)(4). Your employees had labeled this equipment as clean. These (b)(4) are used for the manufacture of multiple APIs.你公司未能保证员工对使用后的设备进行充分的清洁。
XX设备清洁SOP中,要求员工在清洁完成后目视检查。
我们检查中发现YY产品生产车间XX设备有不同程度的污染,设备里面发现异物,一台XX设备中的异物貌似一支笔,而你们的员工已将该设备标识为已清洁。
这些XX设备用于多个原料药生产。
In addition, your firm’s production system did not maintain equipment logs or other documents that adequately record manufacturing operations performed on individual pieces of equipment.另外,你公司的生产系统没有保持各设备的使用日志或其它文件,以充分记录各设备生产操作。
We note that your production operation supervisors and Quality Unit (QU) failed to detect and correct these deficient cleaning practices.我们注意到你们的生产操作主管和质量部门未能察觉和纠正这些有缺陷的清洁操作。
Your response is inadequate because it does not address the extent of these deficient practices throughout your facility, or the impact on the quality of your active ingredients. Additionally, you do not commit to maintain equipment logs or other documents that record all of the manufacturingoperations performed on individual pieces of equipment.你们的回复不够充分,因为回复中并没有说明这些缺陷操作在整个工厂普遍程度,以及对你们的活性成份质量的影响。
另外,你们没有承诺保持设备日志,或其它文件记录各设备上所进行的生产操作。
In response to this letter, you should prepare and implement a corrective action plan sufficient to address and prevent the recurrence of these deficiencies. The corrective action plan should detail the systemic improvements to be made, including, but not limited to, improved management oversight of cleaning operations, commitment to maintain individual equipment records (e.g., equipment logs), and training all relevant personnel in cleaning procedures. You should also demonstrate the sufficiency and effectiveness of this corrective action plan.在回复本警告信时,你们应该制订并实施一份纠正措施计划,对这些缺陷进行说明并防止其再次发生。
该纠正措施计划应详细说明要进行的系统性提高,包括但不仅限于,提高管理层对清洁操作的监督,承诺维持各设备的记录(例如设备日志),对所有相关人员进行清洁程序培训。
你还应该证明这些纠正措施计划的充分性和有效性。
2. Failure to conduct adequate change control to evaluate all changes that could affect the production and control of intermediates or APIs.未能对所有可能影响中间体或原料药生产和控制的变更进行充分的变更控制,评估其影响。
a. Your firm failed to identify, document, evaluate, and approve several changes in production. Specifically, the equipment referenced in the flow chart in Drug Master File (DMF) (b)(4) for the manufacture of (b)(4) API differed from the equipment actually used. The DMF (b)(4) flow chart contains a step for (b)(4) that follows the (b)(4) step. Firm officials stated that your firm no longer conducted the (b)(4) during the manufacture of this API. You did not evaluate whether this change was appropriate based on its impact on product quality, or validate the effectiveness of change implementation. In addition, you failed to conduct a change control investigation or document the significant changes in your manufacturing process as required by your change control SOP SMP-QA 009-08.你公司未能对生产中的几个变更进行识别、记录、评估和批准。