宏程序车蜗杆的方法
宏程序车削蜗杆的应用

取槽宽为进刀宽度!利用两个循环语句!第一个循环沿斜线径 向单边以 "0# 77的吃刀深度进行循环切削!第二个循环切削 蜗杆槽宽度的部分! 4P方向以 "0! 77进给量进行循环切削0 这种方案最大的特点就是切削力非常小!不会出现扎刀'打刀 情况$
图 2&方法一&蜗杆螺纹粗车刀图
"#
创新与实践
!"#$%&'&() *%+ ,*-."! -./0!%!1.0%!!"#$
&引言 蜗杆在各类大型机械的减速机构上都有广泛应用!但蜗杆
的加工!特别是大模数的蜗杆的加工是比较棘手的问题!在普 车上车削要求工人要有比较熟练的操作技巧!其加工的精度和 生产效率受人为因素和操作技术水平影响比较大$ 虽然数控 车床具有较高的精度和稳定的加工性能!为蜗杆齿形的车削提 供了良好的加工基础!但是其程序的编制与操作控制均有较高 的难度$
技术与市场 !"#$ 年第!蜗 杆和大导程螺 纹零件 的齿形$ ) 用这个方法时!在数控车床能承受的范围内!可尽可能选择较 高的切削速度!比如(在车削模数 7Ub' 时!选用 2%" ;S789$ &蜗杆数控车削走刀方式设计
方法一(走刀路线如图 ! ) C* 所示$ 采用刀头宽小于齿形 槽宽的车刀如图 2 所示!采用 !0' 77的刀头宽加工 !03$$ 77 槽宽的蜗杆螺纹!巧妙地结合普通车床车削蜗杆时应用的左右 赶刀工艺技巧!采用左右分层车削斜面的方法取代成形刀法来
!+`!"`共六种!而蜗杆螺纹的齿形角度为 '"`!由于现在的数控 车床多数有 宏 变 量 编 程! 可 采 用 宏 变 量 控 制 走 刀 方 式! 结 合 R2! 或 R$! 螺纹指令完成蜗杆的加工$ &刀具的选择
一种蜗杆通用数控旋风铣削的R参数程序

内赋 值 , 整 数 值 时 可 去 除 小 数 点 , 号 可 以省 去 。 如 取 正 果 使 用 指 数 表 示 法 可 以 在 - 1 ~1 更 大 范 围 - / 0。 0” 内 赋 值 , 在 NC 程 序 中 可 以 写 成 如 RO= 1 8 E ( . 5 X8 即
制 电 机 转 速 。 动 力 头 刀 盘 上 安 装 有 一 把 或 多 把 成 形 刀
含 义 蜗 杆 头 数 蜗 杆 中 径 铣 削 层 数 向 铣 刀 安 全距 离
蜗 杆底 径 蜗 杆导 程
一i 左 旋 ;+1右 旋 : :
R3 蜗 杆 轴 向模 数 R 0 5 :全 部 铣 削 ;l~R 1铣 削 对 应 头 号 R 7
内 部 计 算 。 对 于 此 台专 用 机 床 来 说 , 统 提 供 的 标 准 而 系 加 工 循 环 程 序 用 户 根 本 用 不 到 ,所 以 可 自由使 用 这 些
R参数 。 1 t参 数 可 在 ±0 0 0 0 0 l~9 9 9 . 0 0 9 9 9 9 9数 值 范 围
1 蜗 杆 数 控 旋 风 铣床
目前 许 多 生 产 蜗 轮 蜗 杆 减 速 器 的 企 业 将 车 床 或 铲 齿 车 床 进 行 数 控 化 改 造 , 满 足 蜗 杆 的 毛 坯 加 工 。 过 以 通 对 原 有 大 拖 板 的 纵 向 移 动 、中 拖 板 的 横 向 移 动 以 及 主 轴 的 旋 转 进 行 改 造 , 别 用 3个 交 流 伺 服 电 机 控 制 , 分 系 统 中 定 义 为 Z 轴 、 轴 和 C 轴 。X 轴 控 制 进 刀 深 度 , X z 轴 和 C 轴 插 补 运 动 形 成 蜗 杆 的 螺 旋 线 。将 原 有 刀 架 拆 除 , 成 旋 风 铣 削 动 力 头 ( 旋 风 或 外 旋 风 ) 动 力 头 电 换 内 , 机 由 变 频 器 控 制 , 数 控 系 统 输 出 0~ I V 模 拟 电 压 控 O
数控车床蜗杆加工的计算

数控车床蜗杆加工的计算
螺距=模数乘以3.141(精确到三位),导程是螺距乘以头数,阿基米德蜗杆用的较多,刀尖角度是40度(半角20度),刀尖宽度等于模数乘以0.697,牙高一般图纸上会标出来,编程小牙距用G76复合循环,大螺距用宏程序。
模数螺纹 (蜗杆)牙型角为40度,模数用m表示
螺距=π*m (π就是圆周率3.14159265)
蜗杆导程=π×模数×头数
齿深=2.2*m(单面切削深度)
牙顶间隙=0.2*m
牙顶宽度=0.843*m
牙底宽度=0.697*m
双线蜗杆的数控车加工技艺

双线蜗杆的数控车加工技艺摘要:文章主要论述采用数控车床利用宏程序车削,进刀方法使用车槽法和左右车削法相结合的车削蜗杆方法,车削时刀具是单刃切削,使刀具每次车削都保持小的、均匀的加工量,切削平稳。
能保证加工顺利进行,提高工件加工质量,预防扎刀。
文章以实例编写了加工程序加以论述双线蜗杆的数控车加工技术。
关键词:双线蜗杆;进刀方法;宏程序1 双线蜗杆零件特点蜗杆的齿形面与梯形螺纹很相似,其轴向剖面为梯形,但是蜗杆的齿形较深、导程较大、切削面积大,车削时比一般梯形螺纹难得多。
车蜗杆时,首先要合理选择车刀的几何参数,其次要采用合理的进刀方法,才能顺利完成蜗杆的车削。
2 车削加工中的难题车削蜗杆一般在普通车床加工,在加工大模数蜗杆时由于导程大,刀具运动速度快,车削时容易出现碰撞现象,技术性要求较高,由于是手动操作,加工质量难以保证,有时受到车床进给箱和挂轮的限制,如果名牌上没有相应的模数,蜗杆是无法加工的。
图1 零件图如果在数控车床上加工就能解决这一问题。
但是蜗杆在数控车床上加工时会遇到一些实际问题:因为蜗杆的齿槽比较深,如采用G92单循环指令车削蜗杆为直进法,加工时刀具三刃车削,刀具受力大,易产生振动,刀具很容易折断,刀具与工件摩擦强烈、排屑困难,齿面表面质量也很差。
如采用G76复合循环指令车蜗杆,刀具为斜进法,加工时刀具是两刃车削,刚开始车削时是比较平稳的,但随着切削深度的加深,刀具与工件接触面积越来越来越大,刀具受力逐渐增大,特别在最后几刀,刀具很容易折断,而且加工后的蜗杆齿面一侧光滑、一侧粗糙度较大,特别是大模数的蜗杆根本无法加工。
3 解决方案3.1 进刀方法的选择根据上述分析和自己多年的实践,进刀法无论采用直进法或斜进法车削模数(mx≥2)的蜗杆,其加工过程无法顺利进行,极易产生刀具折断,工件顶弯等现象,加工质量无法保证。
要想顺利加工,就要在车削时减小刀具与工件的接触面积,以达到减小切削抗力的目的。
圆弧面蜗杆数控车削加工的宏程序
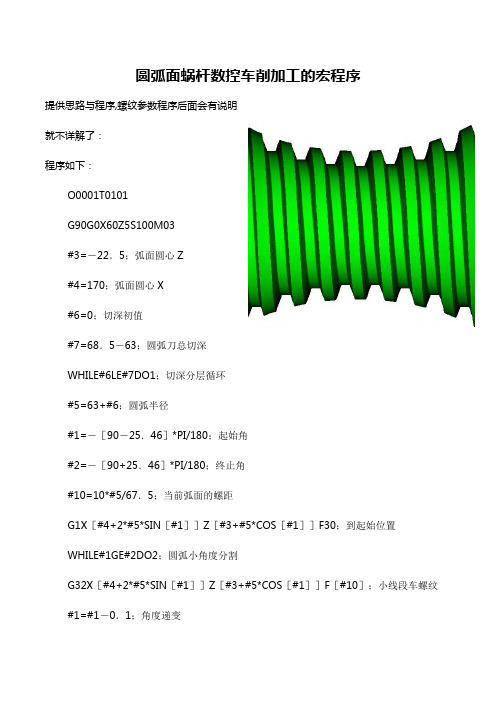
圆弧面蜗杆数控车削加工的宏程序
提供思路与程序,螺纹参数程序后面会有说明
就不详解了:
程序如下:
O0001T0101
G90G0X60Z5S100M03
#3=-22.5;弧面圆心Z
#4=170;弧面圆心X
#6=0;切深初值
#7=68.5-63;圆弧刀总切深
WHILE#6LE#7DO1;切深分层循环
#5=63+#6;圆弧半径
#1=-[90-25.46]*PI/180;起始角
#2=-[90+25.46]*PI/180;终止角
#10=10*#5/67.5;当前弧面的螺距
G1X[#4+2*#5*SIN[#1]]Z[#3+#5*COS[#1]]F30;到起始位置
WHILE#1GE#2DO2;圆弧小角度分割
G32X[#4+2*#5*SIN[#1]]Z[#3+#5*COS[#1]]F[#10];小线段车螺纹#1=#1-0.1;角度递变
ENDW2
G0X60F50G0Z5
#6=#6+0.08;切深递变
ENDW1
G0X100.Z100.
M05
M30
加工时,圆弧车刀以圆弧中心为刀位点对刀,其最终切深按两侧齿廓线以刀尖圆弧半径倒圆后的圆心位置来确定,圆弧段螺纹车制的起始和终止角度可按超出有效毛坯外的第一个齿槽位置求算。
采用圆弧车刀预切结束的同时也完成了齿底的加工,仅剩两侧齿廓留余量。
由于刀具采用直进直出的运动,弧面蜗杆有效齿廓线的两侧不允许有倒卷,否则会产生刀具干涉,即弧面蜗杆的弧面半径和有效区段的弧心角应受到一定的限制。
蜗杆加工方法

在数控车床上快速车削蜗杆的方法摘要:在数控车床上车削较大导程的蜗杆、梯形螺纹和锯齿螺纹,由于工件的齿形深,需要切除的毛坯余量多,一般是选择较低的切削速度和高速钢成形刀,使用G32和G76等指令车削,加工精度特别是表面粗糙度很难达到图纸要求,加工难度较大。
针对出现的加工精度低、生产效率低等特点,说明如何有效地发挥数控车床的高精度,高速度、定位精度高、生产效率高的优势。
我们以沈阳CAK3675v 华中数控系统的车床来论述快速车削蜗杆的方法。
如图1关键词:蜗杆数控车床成形刀硬质合金宏程序蜗杆和大导程螺纹车削的进刀方法有多种,如直进法、左右切削法、斜进法和切槽法等。
以前车削蜗杆等大导程零件的方法是:选用较低主轴转速(数控车床最低速为100转/分时转动无力)和高速钢成形车刀,车削蜗杆时的生产效率低。
为解决上述问题,我认为应从刀具材料、几何形状及角度和车削方法来谈谈快速车削蜗杆和大导程螺纹的方法。
一、突破传统选择刀具的习惯,合理选择车削蜗杆的刀具角度,使刀具的刀尖角小于齿形角车削蜗杆刀具的刀尖角如果等于蜗杆的齿形角。
这种刀具在车削时两侧刀刃与工件侧面容易发生摩擦,甚至三个刀刃同时参加切削,易产生较大的切削力而损坏刀具。
如果选择车刀的刀尖角35小于蜗杆的齿形角40,(如图2)这种车刀在车削时,可防止三个刀刃同时参加切削,减少了摩擦、切削力,能很好地避免“闷车”、“扎刀”和打刀的情况发生。
二、在数控车床上使用硬质合金车刀高转速车削蜗杆成为现实以前,车削加工蜗杆和大导程螺纹,只能用高速钢车刀低速车削加工,生产效率非常低。
如果将车刀的刀尖角磨小,使车刀的刀尖角35小于蜗杆的齿形角40,可避免三个刀刃同时参加切削,切削刀显剧下降,这时可使用较高的切削速度和硬质合金车刀对蜗杆进行车削。
当工件直径、导程越大时,可获得的线速度越高,加工出的工件表面质量越好,而且生产效率明显提高。
彻底解决在数控车床不能用硬质合金刀具车削蜗杆和大导程螺纹零件。
运用宏程序在数控车床上实现环面蜗杆的车削

·94·
在实际加工中, 我们不需时时控制刀具刀位点的位置, 主要只要控制每次螺旋线切削时的起点位置, 之后的刀具位 置有机床螺纹切削的同步功能自动实现 。ψ 的变化范围通常 在 70° ~ 110° 之间, 在螺纹加工起始点可取 ψ = 70° , 螺旋线结 束点处取 ψ = 110° 即可。
两种, 全修型在普通设备上更难以实现 。 合修型” 采用数控车床加工直廓环面蜗杆后, 使得“全修型 ” 和 “综合修型” “全修型” , 都能方便的实现。对于 其修型原理是 当蜗杆毛坯匀速转动时, 带动刀具转动的工作台要作变速运 这种变速在普通机床上是非常难以实现的, 但在数控车 动, 床上, 只要使不同 ψ 位置处的螺距 F 作适当变化就可以了, “综合修型 ” , 这在宏程序中是可以实现的 。对于 其修型原理 并在加工 是将蜗杆传动中的中心距和传动比都作相应改变, 时要求蜗杆作一定的轴向偏移, 这在普通加工中也较难实 z0 等就可实 现, 但在数控车削中, 只需适当改变编程参数 a0 、 现了。 三、编程 ( 一) 程序流程图。根据在数控车床上加工直廓环面蜗 首先编制了如图 4 的流程图, 在此流程图中 杆的动作要求, 没有反应粗精加工, 在实际编程中可另行加入 。 ( 二) 部 分 程 序。 根 据 以 上 分 析 与 设 01. MPF G71G90G95G64 M3S200 M08 T4D1 G0X150Z - 40 R1 = 70 ; 环面蜗杆切削起始角度 R2 = 110 ; 环面蜗杆切削终止角度 R4 = 4 ; 刀具宽度 R14 = - 4. 4 ; 径向切削起始深度 R18 = 4. 8 ; 径向切削终止深度 R15 = - 99 ; 蜗杆喉部中心在 Z 方向上的坐标 MA1 : R14 = R14 + 0. 1 IF R14 > 0 GOTOF MA3 R11 = R1 R12 = R2 R10 = R14 + 0. 3 G9G0X = 2* R13 - 2* ( R16 + R10 ) * SIN( R11 ) Z = R15
蜗杆加工工艺流程
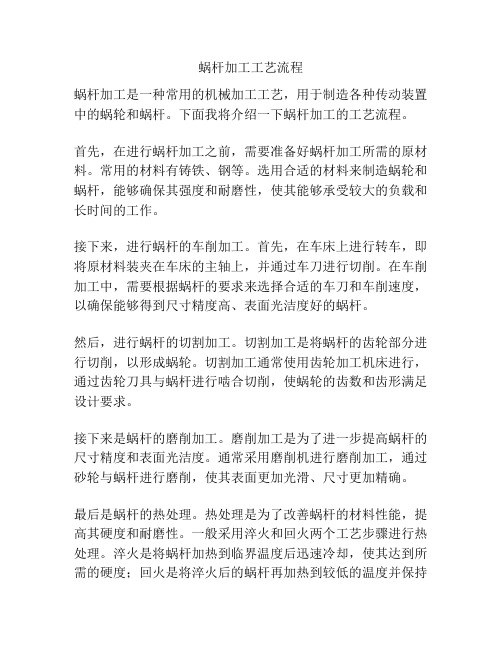
蜗杆加工工艺流程蜗杆加工是一种常用的机械加工工艺,用于制造各种传动装置中的蜗轮和蜗杆。
下面我将介绍一下蜗杆加工的工艺流程。
首先,在进行蜗杆加工之前,需要准备好蜗杆加工所需的原材料。
常用的材料有铸铁、钢等。
选用合适的材料来制造蜗轮和蜗杆,能够确保其强度和耐磨性,使其能够承受较大的负载和长时间的工作。
接下来,进行蜗杆的车削加工。
首先,在车床上进行转车,即将原材料装夹在车床的主轴上,并通过车刀进行切削。
在车削加工中,需要根据蜗杆的要求来选择合适的车刀和车削速度,以确保能够得到尺寸精度高、表面光洁度好的蜗杆。
然后,进行蜗杆的切割加工。
切割加工是将蜗杆的齿轮部分进行切削,以形成蜗轮。
切割加工通常使用齿轮加工机床进行,通过齿轮刀具与蜗杆进行啮合切削,使蜗轮的齿数和齿形满足设计要求。
接下来是蜗杆的磨削加工。
磨削加工是为了进一步提高蜗杆的尺寸精度和表面光洁度。
通常采用磨削机进行磨削加工,通过砂轮与蜗杆进行磨削,使其表面更加光滑、尺寸更加精确。
最后是蜗杆的热处理。
热处理是为了改善蜗杆的材料性能,提高其硬度和耐磨性。
一般采用淬火和回火两个工艺步骤进行热处理。
淬火是将蜗杆加热到临界温度后迅速冷却,使其达到所需的硬度;回火是将淬火后的蜗杆再加热到较低的温度并保持一定时间后冷却,以减轻淬火带来的脆性和应力。
综上所述,蜗杆加工工艺流程包括原材料准备、车削加工、切割加工、磨削加工和热处理。
每个工艺步骤都需要合理选择加工设备和工艺参数,才能够得到质量满足要求的蜗轮和蜗杆。
蜗杆加工工艺流程的优化和改进,能够提高蜗杆的加工效率和质量,满足各种传动装置的使用要求。