第4章 飞机钣金零件制造
飞机超薄铝合金钣金零件成形技术
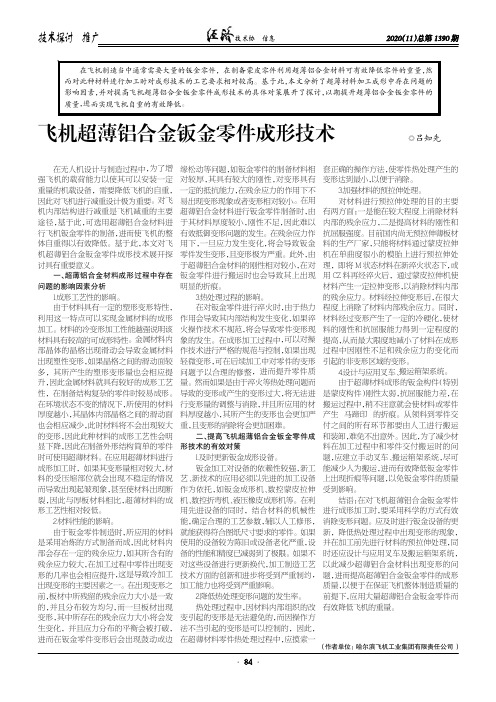
成形加工时,如果其变形量相对较大,材
钣金加工对设备的依赖性较强,新工 能减少人为搬运,进而有效降低钣金零件
料的受压缩部位就会出现不稳定的情况 艺、新技术的应用必须以先进的加工设备 上出现折痕等问题,以免钣金零件的质量
而导致出现起皱现象,甚至使材料出现断 作为依托,如钣金成形机、数控蒙皮拉伸 受到影响。
在环境状态不变的情况下,所使用的材料 行变形量的调整与消除,并且所应用的材 搬运过程中,稍不注意就会使材料或零件
厚度越小,其晶体内部晶格之间的滑动面 料厚度越小,其所产生的变形也会更加严 产生 " 马蹄印 " 的折痕。从领料到零件交
也会相应减少,此时材料将不会出现较大 重,且变形的消除将会更加困难。
材料具有较高的可成形特性。金属材料内 象的发生。在成形加工过程中,可以对操 提高,从而最大限度地减小了材料在成形
部晶体的晶格出现滑动会导致金属材料 作技术进行严格的规范与控制,如果出现 过程中因刚性不足和残余应力的变化而
出现塑性变形,如果晶格之间的滑动面较 轻微变形,可在后续加工中对零件的变形 引起的非变形区域的变形。
形的几率也会相应提升,这是导致冷加工 技术方面的创新和进步将受到严重制约, 题,进而提高超薄铝合金钣金零件的成形
出现变形的主要因素之一。在出现变形之 加工能力也将受到严重影响。
质量,以便于在保证飞机整体制造质量的
前,板材中所残留的残余应力大小是一致
2.降低热处理变形问题的发生率。 前提下,应用大量超薄铝合金钣金零件而
(作者单位:哈尔滨飞机工业集团有限责任公司 )
是采用冶炼的方式制备而成,因此材料内 使用的设备较为陈旧或设备老化严重,设 并在加工前先进行材料的预拉伸处理,同
部会存在一定的残余应力,如其所含有的 备的性能和精度已减弱到了极限。如果不 时还应设计与应用叉车及搬运箱架系统,
(完整版)飞机制造工艺基础3
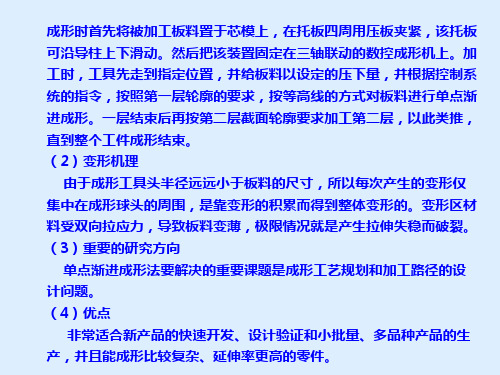
一.整体壁板毛坯 主要为铝合金,另有钛合金、镁合金。整体壁板毛坯的主要制造方法: 热摸锻、挤压、自由锻板坯、热轧平板毛坯和特种铸造。
1.大吨位液压机和锻模生产壁板毛坯 优点:生产率高、锻件纤维组织连续,晶粒致密,强度高,可制造复杂 形状筋肋和对接接头。
热模锻毛坯接近于成品尺寸,厚度和桁 条间距误差小于0.6mm,锻造斜度小锻需要吨位极大的机床,铝合金壁 板每平方米投影面积约需3万吨压力, 精锻时要5~6万吨。且锻模制造困难、 周期长、劳动量大。如某飞机整体壁板 的锻模重量达50~60吨。 这些问题限制了热模锻方法的广泛应用。
Most authors used in their experimental study on incremental forming regular 3 axis milling machine. Figure 7 presents the incremental forming process.
characteristics of the incremental forming process are pointed out:
- the sheet is formed according to a given locus - the deformation of the sheet is point-by-point - the deformation of every step is small.
Figure 8 The control system of Dieless NC Forming machine.
Figure 9 Equipment for Dieless NC Forming process
The blank sheet is attached to a blank holder. The blank holder moves in vertical direction according to descending of Ztool and along X- and Y-planes.
西北工业大学飞机钣金零件成形弯曲课件
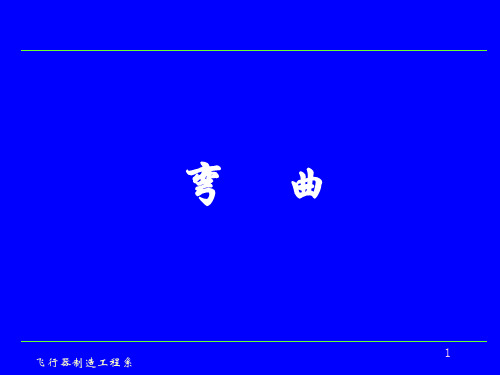
弯曲力
自由弯曲力 校正弯曲力
摩擦 板厚偏差
摩擦在大多数情况下可以增大弯曲变形区的拉应力,可 使零件形状接近于模具的形状。 如果毛坯的厚度偏差大时,对于一定的模具来说,其实 际间隙是忽大忽小的,因而回弹值也是波动的。
飞行器制造工程系
37
弯曲
六、弯曲回弹与补偿措施
3.
减小回弹的措施
在工件设计上采取措施 在工艺上采取措施 在模具结构上采取措施
1.
板料弯曲过程
飞行器制造工程系
11
弯曲
二、板料弯曲的基本原理
1.
板料弯曲过程
立体纯塑性弯曲阶段
1)应变中性层位置从板料中间逐 步向内层移动,变形量愈大, 内移量也愈大。
α tlb = π (R − r ) b 2π
2 2
l = αρ 0
R = r + ξt
1 r ξ ρ 0 = + ξt = r + ξt ξ 2 t 2
y y ε θ = ln ≈ ρ 1 + ρ y σ θ = Eε θ = E
飞行器制造工程系 ρ
σ max ≤ σ s
E ≤σs 2r 1+ t
r 1 E ≥ − 1 t 2 σ 10 s
弯曲
二、板料弯曲的基本原理
弹—塑性弯曲阶段和线性纯塑性弯曲阶段
材料的机械性能
r 相对弯曲半径 t
2.
影响弯曲回弹的主要因素
弯曲角度 弯曲方式和模具结构 弯曲力 摩擦 板厚偏差
飞行器制造工程系
33
弯曲
六、弯曲回弹与补偿措施
σ S / E 越小,回弹越小。
【飞机制造】第四章 锻造

二、锤上模锻
锤上模锻是上、下模块分别紧固 在锤头与砧座上,将加热透的金 属坯料放入下模膛中,利用上模 向下的冲击作用,迫使金属在锻 模摸膛内塑性流动,而获得与模 膛形状一致的锻件。
1、锤上模锻特点 锤上模锻的工艺特点有: (1)可实现多种工步。锤头的行程、打击速度都可调节,能实现轻重缓急
胎模锻是在自由锻设备上使用比较简单的可移动的模具生产锻件的方法,胎 模不固定在锤头或砧座上。
(1)与自由锻相比,胎模锻件的尺寸精度高,表面粗糙度小,敷料少,加工 余量小;有较合理的组织结构;生产率较高。
(2)与模锻相比,胎模制造简单,不需要专门的锻造设备,成本低,操作工 艺灵活等。但胎模锻的锻件的尺寸精度、生产率和模具寿命较模锻低,且 操作人员的劳动强度大。
一、自由锻锻件的结构工艺性
锻件公差
锻造余块或敷料
自由锻
2、计算坯料的质量 和尺寸 (1)坯料质量的计算
(2)坯料尺寸的确定:
当第一道工序采用镦粗法时: 当第一道工序采用拔长时:
3、确定锻造工序
模锻指金属坯料在具有与锻件形状一致的锻模模膛内受冲
击力或压力而变形,获得所需锻件的加工方法。按照所
使用的设备不同,模锻可分为锤上模锻、胎模锻、压力 机和液压机、上模锻等,并 有其各自的工艺特点。
(2)确定模锻工步
根据锻件形状、尺寸,确定模锻工步。为便于拟定工艺规程,合理地设计 锻件及锻模,按照锻件外形和模锻时的轴线方向,把模锻件分成圆饼类、 长轴类、顶镦类和复合类。
(3)修整工序 修整工序包括切边、冲连皮、表面清理、热处理、校正、 精压及检验。
①切边和冲连皮
②热处理
③表面清理 表面清理的目的是去除锻件表面的氧化皮、 局部表面缺陷(如裂纹、折叠、划伤等)、残余毛刺、 油污等,检查、发现表面缺陷,以防止表面缺陷扩大, 提高表面质量。常用的清理方法有滚筒、振动、喷砂 (丸)清理和酸洗等。
飞行器制造复习

钛板热成形;
拉深工艺中的常见缺陷是什么? 根据相应的示意图,指出钣金的成形工艺?
第五章
飞机装配过程? 设计分离面和工艺分离面 定义?
分散装配原则和集中装配原则 ?
飞机整体结构件的外形多数与飞机外形有关,有复杂的装配 协调关系,精度要求较高。 多数整体结构件尺寸大,形状复杂,加工技术难度大。其 中梁类整体件还有纵向刚性较差的特点
整体结构件的材料大部分采用航空用的铝合金,高强度合金 钢、钛合金和复合材料。
化学铣切的工艺流程? 数控加工刀轨规划方法? 喷丸的作用?
3 作为其它定位方法 的辅助定位
1 有配合关系的、 尺寸或形状相一致的 零件之间的装配
2 与其它定位方法 混合使用
1 单曲度,平滑双曲度 壁板中蒙皮、长桁、框的 装配
2 内部加强件的定位 3 平面组合件非外形零 件的定位 4 组合件与组合件之间 的定位
应用广泛的定位方法, 能保证各类结构件的 装配准确度要求
2 用专用样板划线 3 用明胶模线晒相 的方法
特点
1 简便易行 2 装配准确度低 3 工作效率低 4 节省工装费用
以产品结构件上的某 些点、线、面确定待 装件的位置
1 简便易行、节省工 装、装配开畅、协调性 好
2 基准件必须具有较 好的刚性和位置准确度
在相互连接的零件 (组合件)上,按一 定的协调路线分别制 出孔,装配时零件以 对应的孔定位来确定 零件(组合件)的相 互位置 利用型架定位确定结 构件的装配位置或加 工位置(如精加工台)
飞机装配中准确度的要求一般包括哪些?
飞机钣金零件成型工艺及设计李杰
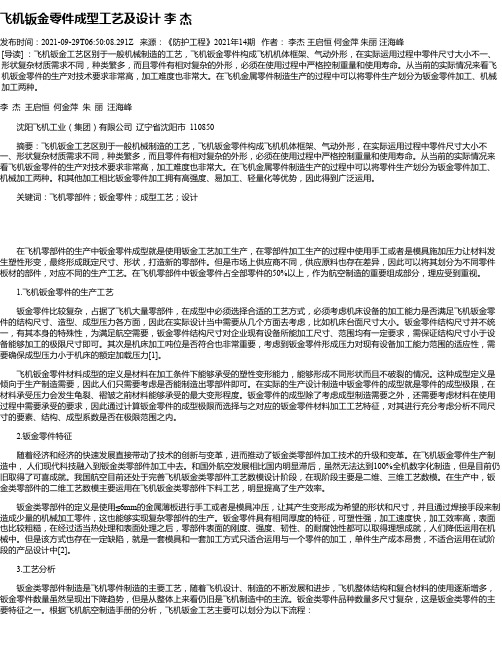
飞机钣金零件成型工艺及设计李杰发布时间:2021-09-29T06:50:08.291Z 来源:《防护工程》2021年14期作者:李杰王启恒何金萍朱丽汪海峰[导读] :飞机钣金工艺区别于一般机械制造的工艺,飞机钣金零件构成飞机机体框架、气动外形,在实际运用过程中零件尺寸大小不一、形状复杂材质需求不同,种类繁多,而且零件有相对复杂的外形,必须在使用过程中严格控制重量和使用寿命。
从当前的实际情况来看飞机钣金零件的生产对技术要求非常高,加工难度也非常大。
在飞机金属零件制造生产的过程中可以将零件生产划分为钣金零件加工、机械加工两种。
李杰王启恒何金萍朱丽汪海峰沈阳飞机工业(集团)有限公司辽宁省沈阳市 110850摘要:飞机钣金工艺区别于一般机械制造的工艺,飞机钣金零件构成飞机机体框架、气动外形,在实际运用过程中零件尺寸大小不一、形状复杂材质需求不同,种类繁多,而且零件有相对复杂的外形,必须在使用过程中严格控制重量和使用寿命。
从当前的实际情况来看飞机钣金零件的生产对技术要求非常高,加工难度也非常大。
在飞机金属零件制造生产的过程中可以将零件生产划分为钣金零件加工、机械加工两种。
和其他加工相比钣金零件加工拥有高强度、易加工、轻量化等优势,因此得到广泛运用。
关键词:飞机零部件;钣金零件;成型工艺;设计在飞机零部件的生产中钣金零件成型就是使用钣金工艺加工生产,在零部件加工生产的过程中使用手工或者是模具施加压力让材料发生塑性形变,最终形成既定尺寸、形状,打造新的零部件。
但是市场上供应商不同,供应原料也存在差异,因此可以将其划分为不同零件板材的部件,对应不同的生产工艺。
在飞机零部件中钣金零件占全部零件的50%以上,作为航空制造的重要组成部分,理应受到重视。
1.飞机钣金零件的生产工艺钣金零件比较复杂,占据了飞机大量零部件,在成型中必须选择合适的工艺方式,必须考虑机床设备的加工能力是否满足飞机钣金零件的结构尺寸、造型、成型压力各方面,因此在实际设计当中需要从几个方面去考虑,比如机床台面尺寸大小。
飞机钣金零件的冲压加工工艺设计

飞机钣金零件的冲压加工工艺设计作者:孔羡夫来源:《名城绘》2020年第11期摘要:冷冲压指的是冲压的过程是处于常温下,钣金件是通过钣金工艺加工出来的产品,与人们的生产生活有着密切的联系。
钣金是一种针对金属薄板的综合冷加工工艺,主要包括剪、冲、切、复合、折、焊接、铆接、拼接、成型等环节,最显著的特征就是同一个零件在厚度方面要保持一致,该文介绍了冷冲压成形钣金件的简易模具制作工艺,分析了航空领域钣金件生产过程中容易出现的问题,并针对这些问题给出了相应的建议。
关键词:冷冲压成形;简易模具;钣金件制作工艺对于飞机零件而言,数量最多的就是钣金零件,这类零件的制造普遍采用冲压加工方法,因此冲压加工就成为了飞机钣金零件的主要加工方法。
对飞机钣金零件的加工要求是尺寸精度适中,但表面质量好。
冲压加工能达到的精度等级在IT9级到IT6级之间,能够满足飞机钣金零件的尺寸精度要求。
冲压加工所用模具凸凹模的工作部分表面质量很高,可以保证制件的表面质量。
因此,本文通过分析某型飞机托架的冲压加工工艺性,并进行必要的工艺计算,从而制定最终工艺方案,为最终实现该零件的冲压加工提供理论基础。
一、钣金零件的设计要求分析1.1设计过程中的材料要求。
在设计之前,要对应用材料的性能加以分析,并对其设计特性进行合理考量。
在飞机钣金零件制造中,铝合金材料的应用最为广泛,耐蚀钢的应用居于第二,有时也会应用低合金钢,此外,钛合金钢的应用率较高。
在材料选择时,要确保所选材料制成的钣金零件可以满足飞机的使用需求,还要对其制备成本进行有效控制。
具体应依据如下因素进行材料选择:1.1.1根据制造工艺及制造费用而进行材料选择。
1.1.2根据加工硬化速度选择适合的材料。
1.1.3选择符合钣金零件使用强度需求的材料进行制备,并确保其具有良好的可成型特性。
1.1.4强度值越高的材料其成型难度也越高,应合理进行二者的协调与选择。
1.1.5确保所选材料符合航空部门的标准。
飞机钣金管子加工课件
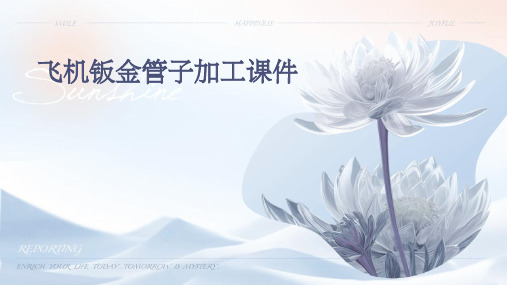
对成型后的管子进行矫直、修整 等后处理,以提高管子的质量和 外观。
质量检测技术
尺寸检测
采用测量工具对管子的尺寸进 行检测,确保管子的尺寸精度
符合要求。
外观检测
通过目视、触摸等方式对管子 的外观质量进行检测,确保管
子的表面质量符合要求。
性能检测
根据管子的材质和用途,进行 相应的性能检测,如拉伸、弯 曲、冲击等,以确保管子的机
飞机钣金管子加工课件
目录 CONTENT
• 飞机钣金管子加工概述 • 飞机钣金管子加工流程 • 飞机钣金管子加工技术 • 飞机钣金管子加工案例分析
01
飞机钣金管子加工概述
飞机钣金管子加工的定义与特点
定义
飞机钣金管子加工是指通过一系列的 机械和热加工工艺,将金属板材和管 材加工成飞机上所需的钣金零件和管 件的过程。
运输与存储
合理安排运输方式和存储地点,确保 管子在运输和存储过程中不受损伤。
03
飞机钣金管子加工技术
模具设计技术
模具设计原则
根据管子的形状、尺寸和材料特性,设计合 理的模具结构,确保加工过程的稳定性和准 确性。
模具材料选择
根据管子的材质和加工要求,选择合适的模具材料 ,以保证模具的耐用性和加工精度。
割、等离子切割等。
弯曲
通过弯曲机或其他设备,将材 料弯曲成所需的形状和角度。
拼接与焊接
将多个零件拼接或焊接在一起 ,形成完整的钣金管子。
去毛刺与打磨
去除管子表面的毛刺和焊缝, 并进行打磨,提高表面质量。
质量检测与控制
尺寸检测
使用测量工具对管子的尺寸进行测量,确保 符合设计要求。
强度检测
对管子进行拉伸、压缩等试验,检测其力学 性能是否达标。