轧 辊 使 用 制 度
轧辊的在钢厂应用原理

轧辊的在钢厂应用原理1. 轧辊的定义与作用轧辊是钢厂生产线中的重要设备,用于对钢材进行加工和变形。
它是一种圆柱形辊子,通常由高强度合金钢制成,并通过专业的热处理工艺进行强化。
轧辊通过轧制的方式将初始钢坯经过一系列辊道变形并获得所需形状和尺寸的钢材。
它在钢厂生产过程中起到关键的作用,影响着钢材的成品质量和生产效率。
2. 轧辊的工作原理轧辊的工作原理是通过对钢坯施加压力和变形来实现形状和尺寸的改变。
钢坯在被送入轧机后,通过不同的辊道进行多次轧制。
每段轧制都会对钢坯造成一定的压力,使钢坯发生塑性变形,逐渐获得需要的形状和尺寸。
在轧辊的工作过程中,主要涉及以下几个方面的原理:2.1 压力原理轧辊通过对钢坯施加压力来使钢材发生塑性变形。
压力的大小和施加时间取决于钢材的性质和所需的变形程度。
轧辊能够产生足够的压力来使钢材塑性变形,使得钢材的形状和尺寸得以改变。
2.2 变形原理轧辊通过不同的辊道和形状来实现对钢材的变形。
不同形状的轧辊可以对钢材施加不同方向和大小的变形力,从而实现对钢材的塑性变形和形状调整。
2.3 冷却原理轧辊在工作过程中会产生大量的热量,为了防止轧辊过热而损坏,需要采取冷却措施。
冷却水通过内部的通道流过轧辊,吸收热量并降低轧辊的温度,以保持轧辊的正常工作温度。
3. 轧辊的分类根据不同的轧制方式和用途,轧辊可以分为多种类型。
以下是几种常见的轧辊分类:3.1 热轧辊热轧辊是用于对高温下的钢坯进行轧制的辊子。
它通常由合金钢制成,能够承受高温和高压的工作环境。
热轧辊主要用于热轧钢材的生产过程。
3.2 冷轧辊冷轧辊是用于对室温下的钢坯进行轧制的辊子。
冷轧辊一般采用硬质合金材料制成,具有较高的耐磨性和寿命。
冷轧辊主要用于冷轧钢材的生产过程。
3.3 支撑辊支撑辊是一种用于支撑和导向钢材运动的辊子。
它主要位于轧机的两侧,起到支撑和稳定钢材的作用。
支撑辊一般由高强度合金钢制成,能够承受较大的压力和冲击。
3.4 模具辊模具辊是一种特殊的轧辊,它具有特定的轮廓和凹槽,用于生产特殊形状和尺寸的钢材。
辊轧成型(roll forming)工艺

辊轧成型(roll forming)是一种通过辊轧机将金属板材或带钢等长条材料连续弯曲成所需横截面形状的成型工艺。
这种工艺通常用于大批量生产金属制品,如建筑材料、车辆零部件、家具和电器等。
辊轧成型的工艺过程一般包括以下几个步骤:
1.设计模具:首先需要根据最终产品的要求设计好成型模具。
模具的设计需要考虑到产品
的尺寸、横截面形状以及材料性能等因素。
2.预处理:在进行辊轧成型之前,通常需要对原材料进行预处理,包括清洁、切割和对边
等工序,以确保材料的质量和尺寸符合要求。
3.辊轧成型:将经过预处理的金属板材或带钢送入辊轧机中,通过一系列辊轧的作用,使
材料连续地进行弯曲和塑性变形,最终得到所需的横截面形状。
4.切割和整形:在完成辊轧成型后,需要根据产品的长度要求对其进行切割,同时可能还
需要进行整形和修整,以确保产品的尺寸和外观符合要求。
5.其它加工:根据产品要求,还可能需要进行其它加工工序,如冲孔、打孔、焊接等,最
终得到成品。
辊轧成型工艺具有高效、自动化程度高、生产周期短等优点,适合于大规模生产相对简单形状的金属制品。
随着工艺技术的不断进步,辊轧成型在各个领域得到了广泛的应用。
轧 辊 使 用 制 度

轧辊使用制度轧辊是轧机的主要组成部件。
轧辊的尺寸结构、材质、使用、维护在相当程度上决定了轧机的技术水平。
轧辊既是轧机设计的重要内容,也是组织生产的主要管理对象,因此,建立合理的轧辊使用制度对提高轧机的使用寿命尤为重要。
一、轧辊材质的选择轧机选用轧辊最主要的出发点是保证成品的表面质量,而保证成品的表面质量最主要的是槽孔的形状和粗糙度,轧辊的耐磨性和辊身的径向硬度的均匀性是选择轧辊的主要指标。
热轧带钢轧辊精轧机精轧工作辊在轧制过程中与高温钢板接触,热疲劳导致轧辊表面出现龟裂,为避免因热疲劳龟纹控制不当造成轧辊出现大面积剥落,建立科学的使用维护及磨削制度相当重要。
在使用中要求:1 、冷却水要连续、足量的对轧辊进行冷却。
在正常工作轧制时工作辊表面温度应严格控制,如辊温过高, 需即刻更换轧辊, 预防使用轧辊过早出现热疲劳裂纹; 轧辊冷却水量最低应维持在400 -600m 3 /h ;2 、每次轧辊上机前必须将轧辊表面的缺陷(主要是龟裂纹)去除掉。
即使无龟裂纹,也要将辊面疲劳层去除,热轧带钢精轧工作辊常规正常磨削一般为0.15~ 0.30mm / 次;中板精轧工作辊常规正常磨削一般为0.25~ 0.50mm / 次( 有的厂家为减少换辊次数, 常常长周期换辊, 这样轧辊磨损大, 一次磨削也大, 约1.0-3.0mm , 不利于合理使用轧辊) 。
3 、轧辊在使用中极易出现龟裂纹,这对轧辊正常使用危害是最大的。
由于轧辊龟裂纹在轧制初期形成较为缓慢,对轧辊不会产生太严重的危害。
但当裂纹形成到一定程度,再继续使用,龟纹将迅速向深度和长度方向扩展。
一是造成磨削量增大,减少轧辊的轧材量;二是如果再严重将造成轧辊剥落的发生,甚至出现大掉肉。
因此,合理使用轧辊,建议每次轧辊上机服役轧材量1800~2400 吨为宜。
热轧工作辊建议按轧制公里标定,每轧制40~60 公里换辊一次;中板轧辊,建议最多2-3 个作业班次换一次辊。
过量轧制,将导致轧辊过度磨损和微裂纹加深,增大二次磨削量,轧辊消耗增高。
第二章 轧 辊

式中:F1 、 F2——辊身与辊颈断面积。
f2
P
GD2
[a
-
b 2
2c
D d
2
1)]
辊身中间总弯曲挠度为:
f
f1
f2
P 18.8ED4
[8a3
- 4ab2
b2
64c(3
D 4 d
1)]
P
GD2
[a -
b 2
2c
D 2 d
[12ab2
7b3 ]
Pb
2GD2
作业3
推导轧辊辊身中间和辊身边部挠度差值计算
f1
P 384EI
1
[12ab
2
7b 3 ]
切力引起的挠度差值f2′ :
Qx
dMx dx
P 2
R Px , b
Qx 1 R
f
2
1 GF1
b 2 0
P 2
Px b
dx
P GF1
b 8
Pb
2GD2
辊身中间和钢板边部挠度差值为
f1
P 18.8ED4
MD=P/2(L/4-b/8) =1950/2 × (0.83/4-0.5/8)=282.8KNm
支撑辊辊身最大弯曲应力: σD=282.8/0.1×0.43=44.20MPa工作 辊颈危险断面应力: σd=(1950/2×0.165)/0.1×0.223
=15100MPa τd=(23/2)/0.2×0.223=510MPa
轧辊种类的划分

轧辊种类的划分轧辊是金属加工中常用的一种工具,广泛应用于轧钢、轧铝、轧铜等行业。
根据不同的使用场景和工艺要求,轧辊可以分为多种类型。
下面将对轧辊的几种常见分类进行介绍。
一、工作辊和支撑辊根据轧机的结构和作用方式,轧辊可以分为工作辊和支撑辊两种类型。
工作辊是直接参与金属材料压制和塑性变形的辊子,其表面通常需要具备一定的硬度和耐磨性。
而支撑辊则是用来支撑工作辊和金属材料的辊子,其主要作用是为工作辊提供支撑和稳定。
二、冷轧辊和热轧辊根据轧制过程中的温度条件,轧辊可以分为冷轧辊和热轧辊两种类型。
冷轧辊主要用于对室温下的金属材料进行轧制,如冷轧钢板、冷轧铝板等。
由于冷轧过程中金属材料硬度较高,所以冷轧辊的表面需要具备较高的硬度和耐磨性。
而热轧辊则主要用于对高温下的金属材料进行塑性变形,如热轧钢坯、热轧铝坯等。
热轧辊的表面要求相对较低,主要是为了保证辊面的光洁度和平整度。
三、工作辊和支撑辊的结构形式根据轧辊的结构形式,轧辊可以分为整体式轧辊和组合式轧辊两种类型。
整体式轧辊是指轧辊的辊身和辊颈为一体的结构,适用于较小的轧机。
组合式轧辊是指轧辊的辊身和辊颈分开制造后再进行组合的结构,适用于大型轧机和冷轧机组。
四、硬质合金轧辊和高铬铸铁轧辊根据轧辊的材质,轧辊可以分为硬质合金轧辊和高铬铸铁轧辊两种类型。
硬质合金轧辊的辊面通常采用硬质合金材料制造,具有较高的硬度和耐磨性,适用于高强度金属材料的轧制。
高铬铸铁轧辊的辊面则采用高铬铸铁材料制造,具有较好的耐磨性和耐腐蚀性,适用于一般金属材料的轧制。
五、镀铬轧辊和镀硬铬轧辊根据轧辊的表面处理方式,轧辊可以分为镀铬轧辊和镀硬铬轧辊两种类型。
镀铬轧辊是将铬层镀在轧辊表面,提高轧辊的耐磨性和耐腐蚀性。
镀硬铬轧辊则是在镀铬的基础上,再进行热处理,使轧辊表面形成一层硬度更高的硬铬层,提高轧辊的耐磨性和使用寿命。
轧辊根据不同的分类标准可以分为工作辊和支撑辊、冷轧辊和热轧辊、整体式轧辊和组合式轧辊、硬质合金轧辊和高铬铸铁轧辊、镀铬轧辊和镀硬铬轧辊等多种类型。
轧辊强度-轧制力调整对比方法

(3)参数:D-辊身直径
L-辊身长度
(4)对轧辊辊身的要求:
①有很高的强度;②有足够的刚度;
③有较高的表面硬度和耐磨性;
④有良好的组织稳定性,以抵抗轧件的高温 影响。
2、辊颈
(1) 定义:是轧辊的支承部分。轧辊依 靠辊身两侧的辊颈支承在轧辊轴承上。
(2)轧辊的辊颈有圆柱形辊颈和圆锥形辊颈 。(图2-1)
(2)复合铸造轧辊技术 具有使辊面和辊芯采用不用材质,轧辊内外
层具有不同要求的良好性能。
外层:用合金成分较高的铸钢或铸铁制成的 ;
内层:高韧性的普通铸铁、普通铸钢或低 合金钢铸成。
3、轧辊的制造新工艺
淬火工艺
淬火的目的在于提高轧辊表层硬度,获得足 够深的淬硬层,延长轧辊的使用寿命。
§2.3. 2 轧辊的材料的选择及辊面硬度
(3)参数:d1-辊头直径 l1-辊头长度 当轧辊不传动(工作辊驱动条件下的支
承辊)或只有单侧传动时,轧辊可以不做专 门的辊头,仅在辊颈外留有可供换辊的起吊 部分。
§2.1.2 轧辊的分类 1、按构造分类
①光面轧辊:应用于轧制板带材。
②有槽轧辊:应用于轧制型钢、线材和钢 坯。
2、按用途分类 ① 工作辊:一般是驱动辊,辊颈小,并
4、轧辊的重车率
在轧制过程中,轧辊辊面因工作磨损 ,需不止一次地重车或重磨。轧辊工作 表面的每次重车量为0.5~5 mm; 重磨量为 0.01~0.5 mm 。轧辊直径减小到一定程 度后,即不能再使用。轧辊从开始使用 直到报废,其全部重车量与轧辊名义直 径的百分比称为重车率。
初轧机轧辊的重车率受咬入能力和辊 面硬度的限制;板带钢轧机轧辊的重车 率只受表面硬度的限制。
R--支反力,取max {R1,R2}中较大值,即R= max {R1,R2} 辊颈与辊身相接处的弯曲应力为:
轧辊型号分类

轧辊型号分类轧辊型号及其分类•按材质分类–铁质轧辊:由铸铁、合金钢等铁质材料制成的轧辊。
具有较高的硬度和强度,适用于对硬材料进行轧制。
–合金轧辊:由钢材与其他合金元素(如钴、铬等)合金化制成的轧辊。
具有耐磨性、耐蚀性等优点,适用于对高硬度材料进行轧制。
–陶瓷轧辊:由陶瓷材料制成的轧辊。
具有耐高温、耐磨性好等特点,适用于对高温、脆性材料进行轧制。
•按结构分类–平辊轧辊:由平面辊筒组成的轧辊。
平辊轧辊适用于对宽度较大的材料进行轧制,轧制效果均匀。
–斜辊轧辊:由斜辊筒组成的轧辊。
斜辊轧辊适用于轧制较薄的材料,可实现较好的轧制效果。
–异型辊轧辊:由具有特定形状的辊筒组成的轧辊。
异型辊轧辊通常用于对特殊形状的材料进行轧制,可以定制不同的辊筒形状以满足轧制需求。
•按用途分类–冷轧辊:用于对冷态材料进行轧制的轧辊。
冷轧辊可实现材料的塑性变形和表面质量的提升。
–热轧辊:用于对热态材料进行轧制的轧辊。
热轧辊主要用于大型轧机,能够实现高速、高温下的轧制。
–中间辊:位于轧机两辊之间,起支撑、传递轧制力等作用。
中间辊一般采用合金材料制成,具有较高的硬度和耐磨性。
–支承辊:位于轧机两辊之外,起支撑作用,使轧机稳定运行。
支承辊通常采用铁质材料制成,具有良好的强度和稳定性。
–导入辊:用于将材料导入轧机的轧辊。
导入辊通常采用平辊结构,以保证材料的均匀进入轧机。
–导出辊:位于轧机出料端,用于将轧制后的材料导出。
导出辊的结构通常根据轧制需求进行设计。
以上是对轧辊型号的常见分类及相关说明。
不同的轧辊型号适用于不同的材料和轧制工艺,能够满足不同的生产需求。
如需具体了解某一型号的轧辊,请联系相关专业人员或生产商。
轧辊
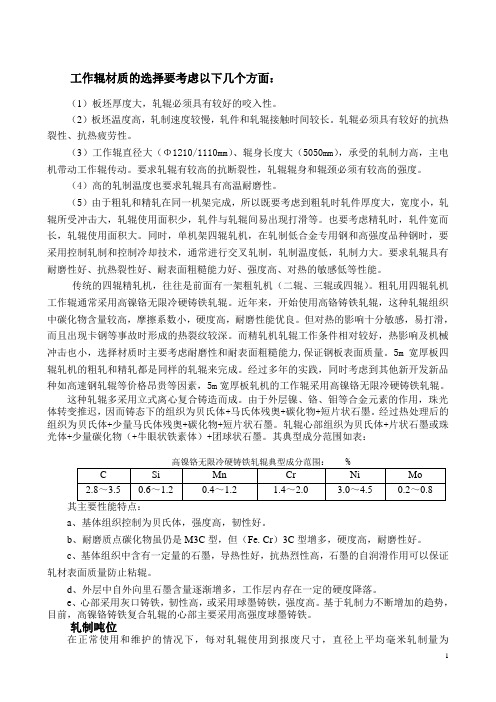
工作辊材质的选择要考虑以下几个方面:(1)板坯厚度大,轧辊必须具有较好的咬入性。
(2)板坯温度高,轧制速度较慢,轧件和轧辊接触时间较长。
轧辊必须具有较好的抗热裂性、抗热疲劳性。
(3)工作辊直径大(Φ1210/1110mm)、辊身长度大(5050mm),承受的轧制力高,主电机带动工作辊传动。
要求轧辊有较高的抗断裂性,轧辊辊身和辊颈必须有较高的强度。
(4)高的轧制温度也要求轧辊具有高温耐磨性。
(5)由于粗轧和精轧在同一机架完成,所以既要考虑到粗轧时轧件厚度大,宽度小,轧辊所受冲击大,轧辊使用面积少,轧件与轧辊间易出现打滑等。
也要考虑精轧时,轧件宽而长,轧辊使用面积大。
同时,单机架四辊轧机,在轧制低合金专用钢和高强度品种钢时,要采用控制轧制和控制冷却技术,通常进行交叉轧制,轧制温度低,轧制力大。
要求轧辊具有耐磨性好、抗热裂性好、耐表面粗糙能力好、强度高、对热的敏感低等性能。
传统的四辊精轧机,往往是前面有一架粗轧机(二辊、三辊或四辊)。
粗轧用四辊轧机工作辊通常采用高镍铬无限冷硬铸铁轧辊。
近年来,开始使用高铬铸铁轧辊,这种轧辊组织中碳化物含量较高,摩擦系数小,硬度高,耐磨性能优良。
但对热的影响十分敏感,易打滑,而且出现卡钢等事故时形成的热裂纹较深。
而精轧机轧辊工作条件相对较好,热影响及机械冲击也小,选择材质时主要考虑耐磨性和耐表面粗糙能力,保证钢板表面质量。
5m宽厚板四辊轧机的粗轧和精轧都是同样的轧辊来完成。
经过多年的实践,同时考虑到其他新开发新品种如高速钢轧辊等价格昂贵等因素,5m宽厚板轧机的工作辊采用高镍铬无限冷硬铸铁轧辊。
这种轧辊多采用立式离心复合铸造而成。
由于外层镍、铬、钼等合金元素的作用,珠光体转变推迟,因而铸态下的组织为贝氏体+马氏体残奥+碳化物+短片状石墨。
经过热处理后的组织为贝氏体+少量马氏体残奥+碳化物+短片状石墨。
轧辊心部组织为贝氏体+片状石墨或珠光体+少量碳化物(+牛眼状铁素体)+团球状石墨。
- 1、下载文档前请自行甄别文档内容的完整性,平台不提供额外的编辑、内容补充、找答案等附加服务。
- 2、"仅部分预览"的文档,不可在线预览部分如存在完整性等问题,可反馈申请退款(可完整预览的文档不适用该条件!)。
- 3、如文档侵犯您的权益,请联系客服反馈,我们会尽快为您处理(人工客服工作时间:9:00-18:30)。
軋輥使用制度軋輥是軋機的主要組成部件。
軋輥的尺寸結構、材質、使用、維護在相當程度上決定了軋機的技術水準。
軋輥既是軋機設計的重要內容,也是組織生產的主要管理物件,因此,建立合理的軋輥使用制度對提高軋機的使用壽命尤為重要。
一、軋輥材質的選擇軋機選用軋輥最主要的出發點是保證成品的表面品質,而保證成品的表面品質最主要的是槽孔的形狀和粗糙度,軋輥的耐磨性和輥身的徑向硬度的均勻性是選擇軋輥的主要指標。
熱軋帶鋼軋輥精軋機精軋工作輥在軋製過程中與高溫鋼板接觸,熱疲勞導致軋輥表面出現龜裂,為避免因熱疲勞龜紋控制不當造成軋輥出現大面積剝落,建立科學的使用維護及磨削制度相當重要。
在使用中要求:1 、冷卻水要連續、足量的對軋輥進行冷卻。
在正常工作軋製時工作輥表面溫度應嚴格控制,如輥溫過高, 需即刻更換軋輥, 預防使用軋輥過早出現熱疲勞裂紋; 軋輥冷卻水量最低應維持在400 -600m 3 /h;2 、每次軋輥上機前必須將軋輥表面的缺陷(主要是龜裂紋)去除掉。
即使無龜裂紋,也要將輥面疲勞層去除,熱軋帶鋼精軋工作輥常規正常磨削一般為0.15~ 0.30mm / 次;中板精軋工作輥常規正常磨削一般為0.25~ 0.50mm / 次( 有的廠家為減少換輥次數, 常常長週期換輥, 這樣軋輥磨損大, 一次磨削也大, 約1.0-3.0mm ,不利於合理使用軋輥) 。
3 、軋輥在使用中極易出現龜裂紋,這對軋輥正常使用危害是最大的。
由於軋輥龜裂紋在軋製初期形成較為緩慢,對軋輥不會產生太嚴重的危害。
但當裂紋形成到一定程度,再繼續使用,龜紋將迅速向深度和長度方向擴展。
一是造成磨削量增大,減少軋輥的軋材量;二是如果再嚴重將造成軋輥剝落的發生,甚至出現大掉肉。
因此,合理使用軋輥,建議每次軋輥上機服役軋材量1800~2400 噸為宜。
熱軋工作輥建議按軋製公里標定,每軋製40~60 公里換輥一次;中板軋輥,建議最多2-3 個作業班次換一次輥。
過量軋製,將導致軋輥過度磨損和微裂紋加深,增大二次磨削量,軋輥消耗增高。
板材品質(粗糙度、平整度、尺寸精度、厚度偏差)也將嚴重下降。
4 、當軋製過程中冷卻水系統發生故障或出現軋製事故時,對軋輥的損傷是在所難免的。
為避免形成深的龜裂紋的損壞,當發生軋製事故後,應儘快打開軋機,減少水流。
軋輥要下機檢查,將龜裂紋徹底磨削掉。
否則再次上機軋製,殘餘裂紋會迅速擴展,造成大的剝落產生。
5 、軋輥在軋製服役當中,一旦發生燒傷,必須對下機對軋輥進行冷卻、磨削修復,將燒傷層去除以後方可上機使用。
即使無龜裂紋,也需這樣做。
6 、熱軋帶鋼軋機配輥,需遵循大直徑軋輥在上,小直徑軋輥在下配輥使用,上下軋輥直徑偏差在0.05~ 0.15mm為佳。
軋機配輥在這種狀態下軋製服役,能夠很好地克服與降低軋件入軋機進口對軋輥暫態衝擊力過大問題,保護輥面不因軋件對軋輥衝擊力過大產生受損。
中板軋機配輥,需遵循大輥在下,小輥在上原則,對輥直徑差3 -8mm 。
軋輥上機使用,輥面為曲線形狀,中間凸,兩邊凹。
曲線凸度(+5 )—(-10 )變化過度,且輥身邊部30 — 50mm 寬導棱-0.2 — -0.3mm 。
7 、軋輥嚴禁激冷激熱。
下軋機軋輥應首先存放在緩冷坑(或冷卻裝置)慢慢冷卻, 待軋輥徹底冷卻至常溫後再進行磨削,否則磨削出的軋輥曲線不真實。
軋輥上機前,最好先預熱,預熱溫度25~ 40 ℃,預熱時間2~4 小時。
嚴寒天氣,作業現場保溫不好,這點尤為重要。
8 、常規軋輥配輥,為確保軋輥正常周轉,熱軋帶鋼軋輥建議按「一配七」;中板軋輥建議按「一配四」,目的提高軋輥抗事故風險性(事故軋輥掉隊、下機軋輥冷卻與磨削準備)。
9 、精軋機架新軋輥初期使用,建議對通配機架軋輥優先安排在軋機前架使用一階段後,移至末架使用,最後依次往前架使用。
新輥初期使用一階段後,軋輥綜合性能最優(所謂磨合),這樣做,軋輥在成品架使用,軋材品質最穩定。
10 、無論軋輥在入廠使用前還是在使用一個階段,定期對軋輥進行探傷檢查跟蹤是必須的,可有效預防缺陷軋輥上機使用時出現軋製故障。
11 、軋機試軋與軋製工藝調整試驗,建議選用低硬度值軋輥進行試軋,可提高軋輥抗事故能力。
12 、應建立完整的軋輥品質卡,記錄軋輥輥號、配輥部位、上下機磨損、磨削技術資料、軋材量、軋輥表面等使用資訊,並將原始記錄歸檔,一定階段對軋輥使用資訊統計分析,能夠有效綜合評價軋輥品質好與壞。
軋機在軋製生產過程中,軋輥處於複雜的應力狀態。
熱軋機軋輥的工作環境更為惡劣:軋輥與軋件接觸加熱、軋輥水冷引起的週期性熱應力,軋製負荷引起的接觸應力、剪切應力以及殘餘應力等。
如軋輥的選材、設計、製作工藝等不合理,或軋製時卡鋼等造成局部發熱引起熱衝擊等,都易使軋輥失效。
軋輥失效主要有剝落、斷裂、裂紋等形式。
任何一種失效形式都會直接導致軋輥使用壽命縮短。
因此有必要結合軋輥的失效形式,探究其產生的原因,找出延長軋輥使用壽命的有效途徑。
1、軋輥剝落軋輥剝落為首要的損壞形式,現場調查亦表明,剝落是軋輥損壞,甚至早期報廢的主要原因。
軋製中局部超載和升溫,使帶鋼焊合在軋輥表面,產生于次表層的裂紋沿徑向擴展進入硬化層並多方向分枝擴展,該裂紋在逆向軋製條件下即造成剝落。
1.1 支撐輥輥面剝落支撐輥剝落大多位於軋輥兩端,沿圓周方向擴展,在寬度上呈塊狀或大塊片狀剝落,剝落坑表面較平整。
支撐輥和工作輥接觸可看作兩平行圓柱體的接觸,在純滾動情況下,接觸處的接觸應力為三向壓應力。
在離接觸表面深度為0.786b 處( b 為接觸面寬度之半) 剪切應力最大,隨著表層摩擦力的增大而移向表層。
疲勞裂紋並不是發生在剪應力最大處,而是更接近于表面,即在Z為0.5b的交變剪應力層處。
該處剪應力平行于軋輥表面,據剪應力互等定理,與表面垂直的方向同樣存在大小相等的剪應力。
此力隨軋輥的轉動而發生大小和方向的改變,是造成接觸疲勞的根源。
週期交變的剪切應力是軋輥損壞最常見的致因。
在交變剪切應力作用下,反復變形使材料局部弱化,達到疲勞極限時,出現裂紋。
另外,軋輥製造工藝造成的材質不均勻和微型缺陷的存在,亦有助於裂紋的產生。
若表面冷硬層厚度不均,芯部強度過低,過渡區組織性能變化太大,在接觸應力的作用下,疲勞裂紋就可能在硬化過渡層起源並沿表面向平行方向擴展,而形成表層壓碎剝落。
支撐輥剝落只是位於輥身邊部兩端,而非沿輥身全長,這是由支撐輥的磨損型式決定的。
由於服役週期較長,支撐輥中間磨損量大、兩端磨損量小而呈U 型,使得輥身兩端產生了局部的接觸壓力尖峰、兩端交變剪應力的增大,加快了疲勞破壞。
輥身中部的交變剪應力點,在軋輥磨損的推動作用下,逐漸往輥身內部移動至少0.5mm ,不易形成疲勞裂紋;而軋輥邊部磨損較少,最大交變剪應力點基本不動。
在其反復作用下,局部材料弱化,出現裂紋。
軋製過程中,輥面下由接觸疲勞引起的裂紋源,由於尖端存在應力集中現象,從而自尖端以與輥面垂直方向向輥面擴展,或與輥面成小角度以致呈平行的方向擴展。
兩者相互作用,隨著裂紋擴展,最終造成剝落。
支撐輥剝落主要出現在上游機架,為小塊剝落,在軋輥表面產生麻坑或橢球狀凹坑,分佈于與軋件接觸的輥身範圍內。
有時,在卡鋼等情況下,則出現沿輥身中部軸向長達數百毫米的大塊剝落。
1.2 工作輥輥面剝落工作輥剝落同樣存在裂紋產生和發展的過程,生產中出現的工作輥剝落,多數為輥面裂紋所致。
工作輥與支撐輥接觸,同樣產生接觸壓應力及相應的交變剪應力。
由於工作輥只服役幾個小時即下機進行磨削,故不易產生交變剪應力疲勞裂紋。
軋製中,支撐輥與工作輥接觸寬度不到20mm ,工作輥表面週期性的加熱和冷卻導致了變化的溫度場,從而產生顯著的週期應力。
輥面表層受熱疲勞應力的作用,當熱應力超過材料的疲勞極限時,軋輥表面便產生細小的網狀熱裂紋,即通稱的龜裂。
軋製中發生卡鋼等事故,造成軋輥局部溫度升高而產生熱應力和組織應力。
軋件的冷頭、冷尾及冷邊引起的顯著溫差,同樣產生熱應力。
當軋輥應力值超過材料強度極限時產生熱衝擊裂紋。
在軋製過程中,帶鋼出現甩尾、疊軋時,軋件劃傷軋輥,亦可形成新的裂紋源。
另外,更換下來的軋輥,尤其上游機架軋輥,多數輥面上存在裂紋,應在軋輥磨削時全部消除。
如軋輥磨削量不夠,裂紋殘留下來,在下一次使用時這些裂紋將成為疲勞核心。
軋輥表面的龜裂等表層裂紋,在工作應力、殘餘應力和冷卻引起的氧化等作用下,裂紋尖端的應力急劇增加並超過材料的允許應力而朝軋輥內部擴展。
當裂紋發展成與輥面成一定的角度甚至向與輥面平行的方向擴展,則最終造成剝落。
軋輥剝落問題, 大多數剝落與六類軋機操作和軋輥使用不當有關:如軋製量過高、換輥週期過長、軋輥修磨量不足、衝擊載荷、軋輥工作面壓力分佈不均、軋製時停機造成軋輥內部溫度分佈不均、熱衝擊等。
前四種情況常與軋輥亞表層赫茲應力有關,應力作用產生的裂紋向內或向外擴展產生剪切破壞,導致剝落。
後兩種情況, 易造成內部裂紋按螺旋方式擴展成表面裂紋,導致大塊剝落。
改善軋輥抗剝落性的措施有:提高軋輥的顯微組織及硬度均勻性;保證適當的淬透性;提高軋輥的剪切強度和塑性,降低軋輥殘餘應力。
對中厚板軋機,在輥身邊部時常會遇有掉肩(爛肩)剝落現象發生,避免軋輥邊部剝落措施是支撐輥帶倒角。
帶倒角支撐輥是將支撐輥輥身兩端250mm 寬倒一棱角約-1mm 。
倒角( 曲線) 量採用模擬計算,其依據是軋製最大板寬時不至發生過大的反凸度,從而避免軋輥邊部產生應力集中和剝落。
2、軋輥斷裂軋輥在工作過程中還常常發生突然斷輥事故,其斷裂部位主要為工作輥的輥身、輥頸處、輥脖與輥頸交界處。
因軋製鋼種、品種與生產工藝條件差異,各斷裂部位所占比例不同。
斷輥可以是一次性的瞬斷,也可以是由於疲勞裂紋發展而致。
根據柯垂爾脆斷條件:( τD/2 + K) K≥4Gγ時,才發生脆斷。
其中τ——應力;D——晶粒直徑;K——係數;G——材料的彈性模量;γ——有效表面能。
也就是說,當τ和D較大時,易發生脆性斷裂,脆性斷裂的斷面總體平齊。
對高鉻複合鑄鐵軋輥,如果軋輥熱處理回火不充分, 外層組織中會含有大量馬氏體、殘餘奧氏體, 導致軋輥鑄態應力較高,亦即τ值增大;τ與D的增大, 是軋輥斷裂的內因。
軋製機械應力、熱應力的疊加是造成輥斷裂的外因。
鍛造工藝不當也會導致軋輥脆性斷裂。
如終鍛溫度過低,易形成位於軋輥心部附近其形貌具有「人」字形特徵的裂紋。
若加上在終鍛時控制不當,很容易造成穿晶型裂紋。
在鍛造變形時,熱加工壓力過小,變形不合理造成心部未鍛透,僅鋼材表面產生塑性變形而內部產生拉應力,當此拉應力超過該區的金屬強度時,即可引起內部橫裂。
脆性斷裂總是以軋輥內部存在的裂紋作為裂紋源。
如果軋輥內部存在大量裂紋,在服役過程中,裂紋尖端產生應力集中而快速擴展連接,形成一個較大的裂紋,這種裂紋在交變應力作用下,由內向外逐漸擴大,當裂紋大到一定程度時就發生疲勞斷裂。