机械制造课程设计说明书《连杆盖》
课程设计---连杆盖夹具设计说明书

课程设计院别:机电学院专业:机械设计制造及其自动化姓名:学号:指导教师:日期:2011年5月目录机床夹具设计课程设计任务书 (1)序言 (4)一、零件的分析 (3)1、零件的生产类型 (3)2、零件的工艺分析 (5)二、工艺规程设计 (5)1、毛坯的选择及毛坯的余量确定 (6)2、基准的选择 (6)3、制定工艺路线 (7)4、工序内容设计 (8)三、铣床夹具设计 (9)1、设计任务 (13)2、夹具方案分析 (13)2.1工件的定位方案分析 (13)2.2加紧方案分析 (13)2.3夹具体设计 (13)四、设计小结 (14)参考文献 (17)机床夹具设计课程设计任务书一.设计题目:设计连杆盖铣下地面(连杆盖与连杆体的剖分面)专用夹具设计(生产纲领:大批量)二.设计要求:(上交电子文件和纸资文件)零件图 1张工序图 1张专用夹具装配图 1张夹具体零件图 1张课程设计说明书 1份三、时间:二周(2010~2011学年度第二学期的第十四、十五周)四、设计步骤及要求:第一部分检验、分析1.检验、分极零件图绘制零件图,分析视图是否完整,是否有不合理之处2.零件技术经济分析哪些面是重要表面,哪些面的技术要求较高,哪些面有位置精度要求第二部分制定工艺路线1.毛坯的选择及毛坯余量确定2、基准的选择3.制定工艺路线,填写工艺过程卡第三部分.夹具的设计1.确定加工部位,分析技术要求2.确定定位方案1).选择定位元件,包括尺寸和公差2).分析定位的合理性,判断有无欠定位和过定位3.确定夹紧方案,选择夹紧元件和夹紧结构第四部分.夹具结构设计1. 夹具体及其它零件设计,确定夹具详细结构。
2. 定位误差计算第五部分.夹具体绘制总装图绘制,零件图绘制序言本课程设计是在学完了机械制造技术基础和大部分专业课的基础上进行的。
本设计是根据学生的实际能力以及结合现代技术的发展趋势综合考虑而做的,主要培养学生综合运用学过的知识,独立地分析和拟定一个零件的合理工艺路线,初步具备设计一个中等复杂程度零件的工艺规程的能力,能根据被加工零件的技术要求,运用夹具设计的基本原理和方法。
连杆盖工艺课程设计说明书G
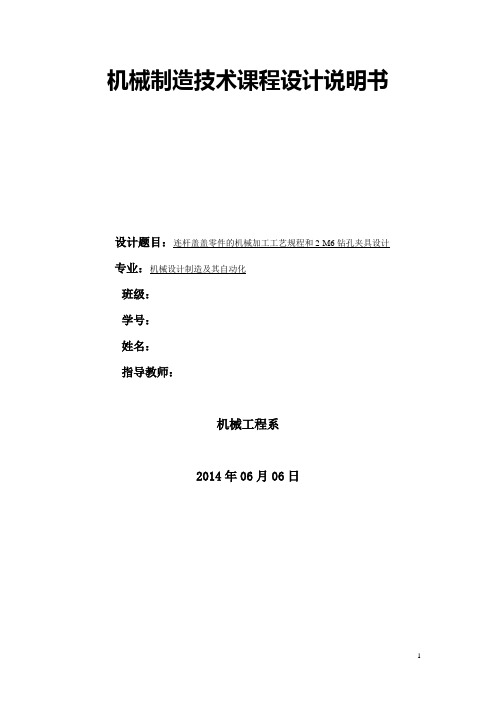
机械制造技术课程设计说明书设计题目:连杆盖盖零件的机械加工工艺规程和2-M6钻孔夹具设计专业:机械设计制造及其自动化班级:学号:姓名:指导教师:机械工程系2014年06月06日目录序言 (3)一、课程设计任务书 (3)二、零件的工艺分析 (3)1、零件的作用和结构特点: (3)2、零件的加工表面和技术要求分析: (4)三、工艺设计 (5)1、生产纲领、确定生产类型 (5)2、毛坯的选择与毛坯图说明 (6)3、工艺路线的确定 (6)3.1粗基准的选择 (6)3.2精基准的选择 (7)3.3各表面加工方法的确定 (7)3.4 工序的顺序安排 (8)3.5集中与分散 (9)3.6设备与工艺装备的选择 (9)3.7方案的分析比较 (9)4、加工余量、切削用量的确定 (12)4.1加工余量 (12)4.2削用量 (16)4.3加工 (22)4.4加工 (25)4.5孔加工 (28)4.6孔加工 (29)5工艺过程卡工艺卡如下 (31)四、钻床专用夹具设计 (50)1钻两端面2-M6底孔夹具设计 (50)2具定位方案的确定 (50)3夹具的夹紧机构的确定 (50)4具钻模板翻转装置确定 (51)4.1 切削力及夹紧力的计算 (51)4.2定位误差分析 (52)5具设计及操作的简要说明 (52)五、设计心得体会 (53)六、参考文献 (54)序言机械制造业是制造具有一定形状位置和尺寸的零件和产品,并把它们装备成机械装备的行业。
机械制造业的产品既可以直接供人们使用,也可以为其它行业的生产提供装备,社会上有着各种各样的机械或机械制造业的产品。
我们的生活离不开制造业,因此制造业是国民经济发展的重要行业,是一个国家或地区发展的重要基础及有力支柱。
从某中意义上讲,机械制造水平的高低是衡量一个国家国民经济综合实力和科学技术水平的重要指标。
我希望通过这次课程设计对自己未来将从事的工作进行一次适应性的训练,从中锻炼自己分析问题,解决问题的能力,为今后参加祖国的现代化建设做出一些贡献。
连杆盖_课程设计
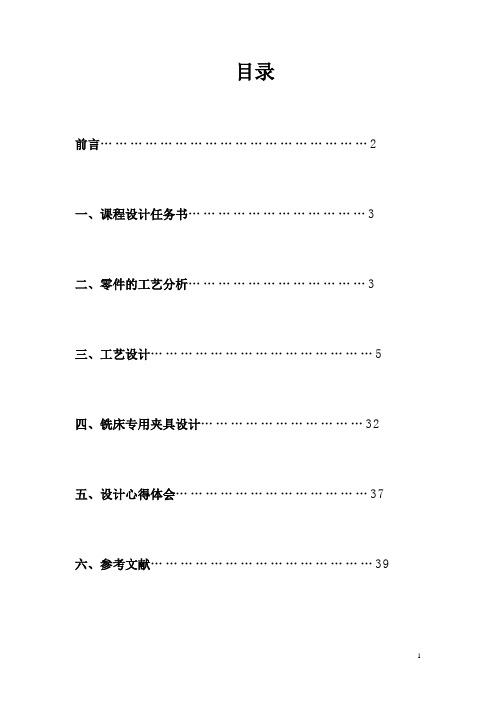
目录前言 (2)一、课程设计任务书 (3)二、零件的工艺分析 (3)三、工艺设计 (5)四、铣床专用夹具设计 (32)五、设计心得体会 (37)六、参考文献 (39)前言机械制造技术课程设计是在我们学完了大学的全部基础课,以及大部分专业课之后进行的。
这是我们在进行课程设计对所学各课程的一次深入的综合性的总复习,也是一次理论联系实际的训练,因此,它在我们四年大学生活中占有重要的地位,本次课程设计旨在培养学生设计机械加工工艺规程的工程实践能力,通过这次设计锻炼了我们综合运用过去所学全部课程进行机械制造工艺及结构设计的基本能力,为学生搞好毕业设计,走上工作岗位打下坚实的基础。
本课程设计的目的在于:(1)培养学生运用机械制造工程学及相关课程(工程材料与热处理、机械设计、公差与技术测量等)的知识,结合生产实习中学到的实践知识,独立地分析和解决零件机械加工工艺问题,初步具备设计一个中等复杂程度零件的工艺规程的能力。
(2)能根据被加工零件的技术要求,运用机床夹具设计的基本原理和方法,学会拟订机床夹具设计方案,完成夹具结构设计,提高结构设计能力。
(3)培养学生熟悉并运用有关手册、规范、图表等技术资料的能力。
(4)进一步培养学生识图、制图、运算和编写技术文件等基本技能。
此次课程设计对给定的零件图分析并进行工艺规程设计,其中考察了定位基准的选择,零件便面加工方法的选择,加工工艺路线的拟定及工序加工余量,工序尺寸,公差等相关知识,历时三个星期的设计加深了对所学知识的理解,有助于今后能够熟练地运用于工作中。
设计过程中遇到一些疑问经过老师的悉心指导都得以解决,在此对老师表示衷心的感谢。
适应性训练,从中锻炼自己分析问题,解决问题的能力,为今后工作打下一个良好的基础。
由于能力有限,设计尚有许多不足之处,恳请老师给与指教。
一、课程设计任务书1、绘制零件图(按1︰1的比例)1张2、绘制毛坯图(按1︰1的比例)1张3、填写零件机械加工工艺规程卡片1套(包括:机械加工工艺过程卡片1套,机械加工工序卡片1套)4、机床夹具总体方案图1张5、夹具零件图2张6、编写零件课程设计说明书1份原始资料:零件图样1张;零件生产纲领为10000件/年;每日1班。
连杆盖说明书
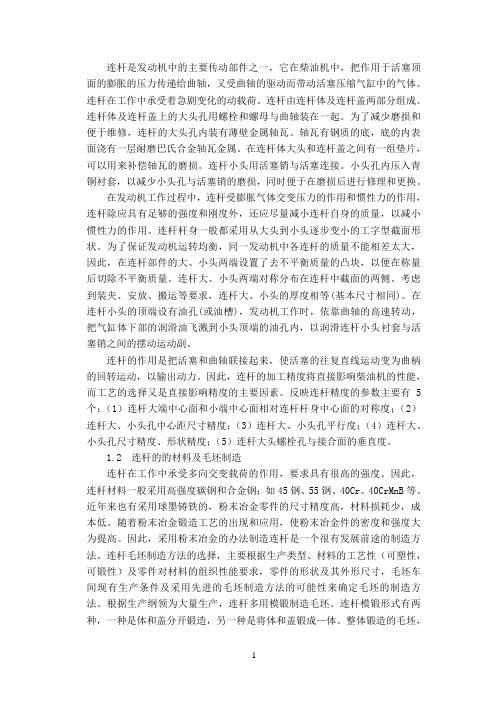
连杆是发动机中的主要传动部件之一,它在柴油机中,把作用于活塞顶面的膨胀的压力传递给曲轴,又受曲轴的驱动而带动活塞压缩气缸中的气体。
连杆在工作中承受着急剧变化的动载荷。
连杆由连杆体及连杆盖两部分组成。
连杆体及连杆盖上的大头孔用螺栓和螺母与曲轴装在一起。
为了减少磨损和便于维修,连杆的大头孔内装有薄壁金属轴瓦。
轴瓦有钢质的底,底的内表面浇有一层耐磨巴氏合金轴瓦金属。
在连杆体大头和连杆盖之间有一组垫片,可以用来补偿轴瓦的磨损。
连杆小头用活塞销与活塞连接。
小头孔内压入青铜衬套,以减少小头孔与活塞销的磨损,同时便于在磨损后进行修理和更换。
在发动机工作过程中,连杆受膨胀气体交变压力的作用和惯性力的作用,连杆除应具有足够的强度和刚度外,还应尽量减小连杆自身的质量,以减小惯性力的作用。
连杆杆身一般都采用从大头到小头逐步变小的工字型截面形状。
为了保证发动机运转均衡,同一发动机中各连杆的质量不能相差太大,因此,在连杆部件的大、小头两端设置了去不平衡质量的凸块,以便在称量后切除不平衡质量。
连杆大、小头两端对称分布在连杆中截面的两侧。
考虑到装夹、安放、搬运等要求,连杆大、小头的厚度相等(基本尺寸相同)。
在连杆小头的顶端设有油孔(或油槽),发动机工作时,依靠曲轴的高速转动,把气缸体下部的润滑油飞溅到小头顶端的油孔内,以润滑连杆小头衬套与活塞销之间的摆动运动副。
连杆的作用是把活塞和曲轴联接起来,使活塞的往复直线运动变为曲柄的回转运动,以输出动力。
因此,连杆的加工精度将直接影响柴油机的性能,而工艺的选择又是直接影响精度的主要因素。
反映连杆精度的参数主要有5个:(1)连杆大端中心面和小端中心面相对连杆杆身中心面的对称度;(2)连杆大、小头孔中心距尺寸精度;(3)连杆大、小头孔平行度;(4)连杆大、小头孔尺寸精度、形状精度;(5)连杆大头螺栓孔与接合面的垂直度。
1.2 连杆的的材料及毛坯制造连杆在工作中承受多向交变载荷的作用,要求具有很高的强度。
连杆盖设计说明书及钻2m12孔夹具设计课程设计 _大学论文
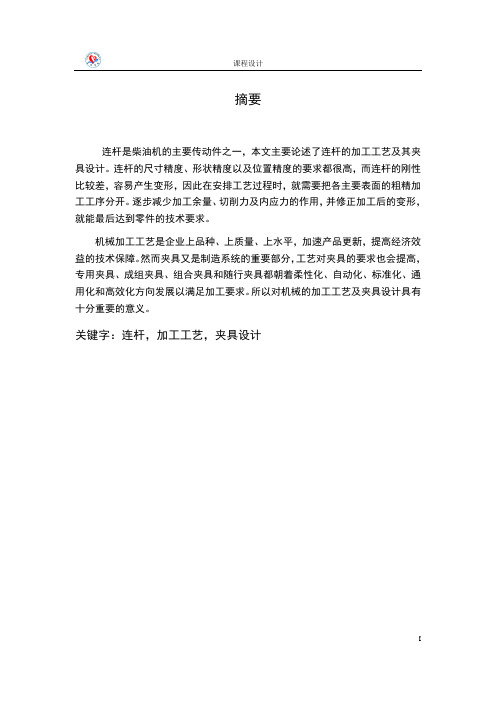
摘要连杆是柴油机的主要传动件之一,本文主要论述了连杆的加工工艺及其夹具设计。
连杆的尺寸精度、形状精度以及位置精度的要求都很高,而连杆的刚性比较差,容易产生变形,因此在安排工艺过程时,就需要把各主要表面的粗精加工工序分开。
逐步减少加工余量、切削力及内应力的作用,并修正加工后的变形,就能最后达到零件的技术要求。
机械加工工艺是企业上品种、上质量、上水平,加速产品更新,提高经济效益的技术保障。
然而夹具又是制造系统的重要部分,工艺对夹具的要求也会提高,专用夹具、成组夹具、组合夹具和随行夹具都朝着柔性化、自动化、标准化、通用化和高效化方向发展以满足加工要求。
所以对机械的加工工艺及夹具设计具有十分重要的意义。
关键字:连杆,加工工艺,夹具设计目录摘要 (I)第1章零件的工艺分析 (1)1.1零件的功用、结构及特点 (1)1.2 零件的工艺分析 (2)第2章毛坯的选择 (3)2.1 确定毛坯的类型、制造方法和尺寸及其公差 (3)2.2 定毛坯的技术要求 (3)2.3 绘制毛坯图 (3)2.4 确定机械加工余量、工序尺寸及公差 (4)第3章基准的选择 (5)第4章拟订机械加工工艺路线 (6)4.1 确定各表面的加工方法 (6)4.2 拟订加工工艺路线 (6)4.2.1工艺路线方案1 (6)4.2.2工艺路线方案2 (7)4.3工艺方案的比较与分析 (7)第5章确立切削用量及基本工时 (8)5.1工序2切削用量及其基本时间的确定 (8)5.1.1 确定每齿进给量fz (8)5.1.2 选择铣刀磨钝标准和耐用度 (8)5.1.3确定切削速度和工作台每分钟进给量 (8)5.1.4基本时间 (9)5.2工序4切削用量及其基本时间的确定 (9)5.2.1 确定进给量f (9)5.2.2 确定切削速度V (9)5.2.3 确定切削速度V (9)5.2.4 基本时间的确定 (10)5.3工序9切削用量及其基本时间的确定 (10)5.3.1 确定每齿进给量f (10)z5.3.2 选择铣刀磨钝标准和耐用度 (10)5.3.3 确定切削速度和工作台每分钟进给量 (10)5.3.4基本时间 (11)5.4工序10切削用量及其基本时间的确定 (11) (11)5.4.1 确定每齿进给量fz5.4.2 选择铣刀磨钝标准和耐用度 (11)5.4.3 确定切削速度和工作台每分钟进给量 (12)5.4.4基本时间 (12)第6章夹具体方案设计 (13)6.1确定定位基准 (13)6.2 确定夹具整体方案 (13)6.2.1 方案的选择 (14)6.3夹具定位误差分析 (14)6.4夹紧力的计算 (14)6.5切屑参数的设定 (15)6.5.1钻孔切削用量 (15)6.5.2确定进给量f (15)6.5.3 确定切削速度v (15)6.6、钻孔基本时间的确定 (16)6.7、定位误差分析 (16)6.8 夹具精度分析 (16)6.9 夹具总体设计 (17)第7章夹具结构设计 (20)7.1钻套 (20)7.2夹具体设计 (20)7.3压板 (21)7.4夹紧机构 (22)7.5刀具的选择 (23)7.6夹具的设计及操作的简要说明 (24)7.7结构特点 (24)设计心得 (24)参考文献 (25)附录 (26)第1章零件的工艺分析1.1零件的功用、结构及特点图1.1为连杆盖零件,材料为QT450-10铸件,生产纲领为6000 件/年。
连杆盖制造说明书
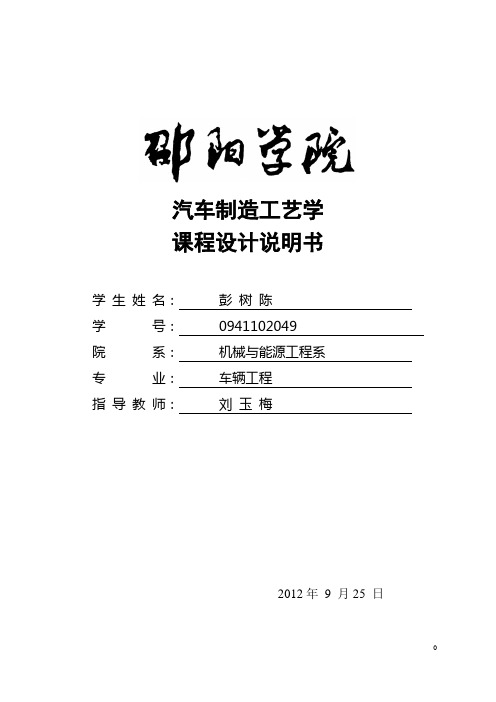
汽车制造工艺学课程设计说明书***名:***学号:**********院系:机械与能源工程系专业:车辆工程***师:***2012年9 月25 日目录一、序言 (2)二、设计任务书 (3)三.连杆盖加工工艺及分析 (5)3.1连杆盖的用途及其特点 (5)3.2连杆盖的的材料及毛坯制造 (6)3.3连杆盖的加工工艺过程和工艺分析 (6)3.4工序的设计 (9)3.5工艺过程卡和工序卡 (10)四、连杆盖钻孔夹具设计 (16)4.1、对专用夹具的基本要求 (16)4.2、专用夹具设计步骤 (17)4.2、工件的加工工艺分析 (18)4.4、确定夹具的结构方案 (18)4.5、夹紧装置的设计 (19)4.6、钻套钻模版的设计 (20)4.7、绘制总图及确定主要尺寸和技术要求 (22)五、设计小结 (22)六参考文献 (23)一、序言机械制造技术课程设计是在我们学完了大学的全部基础课、以及大部分专业课之后进行的。
这是我们在进行课程设计对所学各课程的一次深入的综合性的总复习,也是一次理论联系实际的训练,因此,它在我们四年大学生活中占有重要的地位,本次课程设计旨在培养学生设计机械加工工艺规程的工程实践能力,通过这次设计我将使我们获得综合运用过去所学全部课程进行机械制造工艺及结构设计的基本能力,为学生搞好毕业设计、走上工作岗位打下坚实基础。
本次课程设计的目的在于:1.培养学生解决机械加工工艺问题的能力。
通过课程设计,熟练运用机械制造技术基础课程中的基本理论以及在生产实习中学到的实践知识,正确地解决一个零件在加工中的定位、夹紧以及工艺路线安排、工艺尺寸的确定等问题,保证零件的加工质量,初步具备设计一个中等复杂程度零件的工艺规程的能力。
2.提高结构设计能力。
学生通过训练,能根据被加工零件的加工要求,选择高效、省力、经济合理而能保证加工质量的夹具,提高结构设计能力。
3.培养学生熟悉并运用有关手册、规范、图表等技术资料的能力。
连杆盖夹具课程设计
摘要两周的时间一转眼就过去了,这个两周我们进行了机械制造加工工艺设计及夹具设计。
我们这组设计的设计题目是连杆盖。
我所设计是铣上端15mm凹槽。
本次我设计的夹具是,在设计上别出心裁,有以下优点:1. 安装方便,将工件放如2个定位销内便可以定位,再用压扳压紧,即可对工件加工;2. 便于拆卸,在普通压板上改进,使用梯形设计,可以很快拆卸和安装。
提高了生产效率;3. 夹具结构简单,夹紧可靠。
本文主要论述了连杆的加工工艺及其夹具设计。
连杆的尺寸精度、形状精度以及位置精度的要求都很高,而连杆的刚性比较差,容易产生变形,因此在安排工艺过程时,就需要把各主要表面的粗精加工工序分开。
逐步减少加工余量、切削力及内应力的作用,并修正加工后的变形,就能最后达到零件的技术要求。
本次设计阐述了专业夹具结构设计及工作过程。
本夹具性能可靠,运行平稳,提高生产效率,降低劳动强度和生产成本。
关键字:连杆盖 ,夹具设计,现代加工工艺I目录摘要 (I)第1章零件的工艺分析 (1)1.1零件的功用、结构及特点 (1)1.2 零件的工艺分析 (2)第2章毛坯的选择 (3)2.1 确定毛坯的类型、制造方法和尺寸及其公差 (3)2.2 定毛坯的技术要求 (3)2.3 绘制毛坯图 (3)2.4 确定机械加工余量、工序尺寸及公差 (4)第3章基准的选择 (5)第4章拟订机械加工工艺路线 (6)4.1 确定各表面的加工方法 (6)4.2 拟订加工工艺路线 (6)4.2.1工艺路线方案1 (6)4.2.1工艺路线方案2 (7)4.3工艺方案的比较与分析 (7)第5章确立切削用量及基本工时 (8)5.1工序2切削用量及其基本时间的确定 (8)5.1.1 确定每齿进给量fz (8)5.1.2 选择铣刀磨钝标准和耐用度 (8)5.1.3确定切削速度和工作台每分钟进给量 (8)5.1.4基本时间 (9)5.2工序4切削用量及其基本时间的确定 (9)5.2.1 确定进给f (9)5.2.2 确定切削速度V (9)5.2.3 确定切削速V (10)5.2.4 基本时间的确定 (10)5.3工序9切削用量及其基本时间的确定 (10)5.3.1 确定每齿进给量 (10)5.3.2 选择铣刀磨钝标准和耐用度 (10)5.3.3 确定切削速度和工作台每分钟进给量 (10)5.3.4基本时间 (11)5.4工序10切削用量及其基本时间的确定 (11)II5.4.1 确定每齿进给量 (11)5.4.2 选择铣刀磨钝标准和耐用度 (11)5.4.3 确定切削速度和工作台每分钟进给量 (12)5.4.4基本时间 (12)第6章夹具体的总体设计 (13)6.1确定定位基准 (13)6.2 确定夹具整体方案 (14)6.3定位误差的分析 (15)6.4夹紧力的计算 (15)6.5夹具精度分析 (16)6.6位误差分析 (16)6.7 夹具总体设计 (16)6.8夹具的设计及操作的简要说明 (18)6.9结构特点 (18)总结 (19)参考文献 (20)附录 (21)III1第1章 零件的工艺分析1.1零件的功用、结构及特点图1.1为连杆盖零件,材料为QT450-10铸件,生产纲领为6000 件/年。
连杆盖机械加工工艺规程课程设计说明书
连杆盖机械加工工艺规程设计说明书课程名称:机械制造技术课程设计院别:机电学院专业:机械电子工程班级:10机电本姓名:学号:指导教师:张平教务处制二00八年十二月二十日序言 (2)一、零件的分析 (3)(一)产品零件图分析 (3)(二)零件的结构工艺性分析 (4)(三)零件的生产类型 (4)二、毛坯的确定 (4)(一)确定毛坯类型 (4)(二)确定毛坯制造方法 (5)(三)查有关手册确定毛坯表面加工余量及公差 (5)(四)绘制毛坯图 (5)三、工艺规程设计 (6)(一)选择定位基准 (6)(二)各表面加工方法 (6)(三)拟定工艺路线 (7)(四)选择加工设备及刀、夹、量具 (7)(1)选择机床根据不同的工序选择机床 (7)(2)选择刀具 (8)(五)加工余量及工序尺寸与公差的确定 (8)(六)切削用量及其基本时间的确定 (9)(1)工序10切削用量及其基本时间的确定 (9)(2)工序20、30切削用量及其基本时间的确定 (11)(3)工序40切削用量及其基本时间的确定 (12)1、铣轴瓦锁止口,保证止口加工深度尺寸为2.5mm (12)2、切削工时 (13)(4)工序50切削用量及其基本时间的确定 (13)1、钻孔切削用量 (13)2、钻孔基本时间的确定 (13)3、扩孔切削用量 (13)(5)工序60切削用量及其基本时间的确定 (14)1、工序和刀具 (14)2、确定进给量和切削速度 (14)课程设计总结 (15)参考文献 (15)序言机械制造工艺学课程设计是我们学习完大学阶段的机械类基础和技术基础课以及专业课程之后的一个综合课程,它是将设计和制造知识有机的结合,并融合现阶段机械制造业的实际生产情况和较先进成熟的制造技术的应用,而进行的一次理论联系实际的训练,通过本课程的训练,将有助于我们对所学知识的理解;是在学完了机械制造工艺学的理论课程之后,并进行了生产实习的基础上进行的又一个实践性教学环节。
连杆加工工艺规程课程设计说明书
大学《汽车制造工艺学》课程设计说明书设计题目:编制连杆工艺规程及铣连杆大头平面夹具班级:设计者:指导教师:评定成绩:设计日期:年月目录序言课程设计任务书一、生产纲领及零件说明二、连杆的材料和毛坯三、连杆的技术要求四、连杆的机械加工工艺过程五、切削用量的选择原则六、工时定额的计算七、专用夹具设计课程设计总结参考文献汽车制造工艺学课程设计任务书一.原始资料:1. 连杆零件图2. 生产纲领:3000—10000件3. 生产类型:批量生产4. 质量标准:严格执行零件设计图提出的要求5. 车间:机加工机床(X62铣床)二.工艺规程步骤:1. 画连杆零件图,体、盖各一张2. 编制连杆工艺规程(1).分析零件图,对零件进行工艺分析(2).拟定工艺路线,其主要工作是:A. 选择定位基准B. 确定各表面的加工方法C. 安排加工顺序D. 安排检验等辅助工序(3).确定各工序的加工余量,计算工序尺寸及公差(4).确定工艺所使用的设备及刀、夹、量具和辅助工具(5).确定切削用量及时间定额(6).确定各工序的技术要求及检验方法(7).填写工艺卡片A. 机械加工工艺过程卡片B. 机械加工工序卡片三.夹具设计步骤:1. 设计的准备(在进行夹具设计之前,应该收集和掌握下列必要的的资料)(1).生产纲领(2).零件图与工序图(3).工序内容(夹具所在工序的内容)2. 方案设计(1).定位基准的分析(分析限制工件的自由度)(2).定位方案的确定(计算定位误差)(3).夹紧方案的确定(进行夹紧力的计算)3. 审核4. 总体设计5. 尺寸和夹具技术要求的标注(在夹具总图上标注必要的尺寸和夹具技术)6. 夹具零件图的绘制四.具体要求:1. 产品零件图各一张2. 机械加工工艺过程卡片一套3. 机械加工工序卡片一套4. 夹具总装配图2#图纸一张5. 夹具主要零件图(3#)一张6. 课程设计说明书(4000—6000字)一份(1).封面(2).目录(3).设计任务书(4).课程设计说明书正文(包括工艺规程设计和夹具设计的全部内容)五.参考资料1. 《切削用量简明手册》2. 《机械加工工艺手册》3. 《机械零件设计手册》4. 《机械制造工艺与机床夹具课程设计指导》汽车工程系2012年6月序言《汽车制造工艺学课程设计》是我们学习完大学阶段的汽车类基础和技术基础课以及专业课程之后的一个综合的课程设计,它是将设计和制造知识有机的结合,并融合现阶段汽车制造业的实际生产情况和较先进成熟的制造技术的应用,而进行的一次理论联系实际的训练,通过本课程的训练,将有助于我们对所学知识的理解,并为后续的课程学习以及今后的工作打下一定的基础。
连杆盖课程设计说明书(机械制造)
连杆盖课程设计说明书(机械制造)目录一、零件的分析 (3)二、工艺规程设计 (4)三、铣床夹具设计 (9)四、设计小结 (12)五、参考文献 (13)一、零件的分析1、零件的生产类型根据所给要求,以确定,本两件加工属大批量生产。
2、零件的工艺分析此零件为连杆合件之一——连杆盖,连杆盖的视图完整,尺寸、公差及技术要求齐全。
此零件形状结构较为简单,零件各表面的加工并不困难,但是基准孔Ø81+0.021 0mm以及小头孔要求表面粗糙度Ra1.6µm偏高。
基本思路为先加工大头孔再以其为基准来加工小头孔。
在小头孔中间的大的沟槽需要用R67mm刀具去加工,同样在加工大头孔内表面的沟槽时也要用特殊的R25mm的刀具去加工。
此外还应该注意:1.该连杆盖为整体铸造成型,其外形可不再加工,根据GB/T 6414-1999的规定,铸件尺寸公差代号为CT公差等级分为16级,由于零件的轮廓尺寸不大,形状不是很复杂,为大批量生产,从减少加工难度来说,经查机制工艺手册,毛坯采用铸造成型。
2.连杆小头孔对A基准的平行度公差为0.01mm。
3.大头孔两端的台阶面对B基准的对称度公差为0.3mm。
4.小头孔中间的沟槽,对基准B的对称度为0.2mm。
5.铸件毛坯需要经过人工时效处理。
6.材料QT450-10 。
7.连杆大小头孔平行度的检验,可采用穿入专用心轴,在平台上用等高的V型块支撑连杆大头孔心轴,测量大头孔心轴在最高位置时两端的差值,其差值一半即为平行度误差。
二、工艺规程设计1、毛坯的选择及毛坯余量确定在各类机械中,连杆盖为为传动件,由于其在工作时处于运动中,经常受冲击和高压载荷,要求具有一定的强度和韧性。
该零件的材料选择QT450-10,零件的轮廓尺寸不大,形状不是很复杂,为成批量生产模型,从减少加工难度来说,经查机制工艺手册,毛坯采用铸造成型。
因为零件形状并不复杂,但为减小加工时的切削用量和提高生产效率,节约毛坯材料,毛坯形状可以与零件形状接近。
- 1、下载文档前请自行甄别文档内容的完整性,平台不提供额外的编辑、内容补充、找答案等附加服务。
- 2、"仅部分预览"的文档,不可在线预览部分如存在完整性等问题,可反馈申请退款(可完整预览的文档不适用该条件!)。
- 3、如文档侵犯您的权益,请联系客服反馈,我们会尽快为您处理(人工客服工作时间:9:00-18:30)。
1、零件的工艺分析
此零件为连杆盖合件之二-连杆盖,连杆盖的视图完整,尺寸、公差及技术要求齐全。
此零件形状结构较为简单,零件各表面的加工并不困难,但是基准孔Ø81+0.021 0mm以及小头孔要求表面粗糙度Ra1.6µm偏高。
基本思路为先加工大头孔再以其为基准来加工小头孔。
在小头孔中间的大的沟槽需要用R67mm具去加工,同样在加工大头孔内表面的沟槽时也要用特殊的R25mm的刀具去加工。
此外还应该注意:
1.该连杆盖为整体铸造成型,其外形可不在加工。
铸件尺寸公差,铸件尺寸公差分为16级,由于是中批量生产,毛坯制造方法采用金属模铸造,由机械加工工艺简明手册查得,铸件尺寸公差等级为13级。
2.连杆大头孔对A基准的平行度公差为0.01mm。
3.大头孔两端的台阶面对B基准的对称度公差为0.3mm。
4.小头孔中间的沟槽,对基准B的对称度为0.2mm。
5.铸件毛坯需要经过人工时效处理。
6.材料 QT450-10 。
7. 工序(12)采用2mm的锯片铣刀加工,也可以改为线切割加工,该道工序使的连杆大孔为一个不完整的半圆。
若采用线切割可减小加工缺陷,但是采用铣刀可以节约加工时间。
由于加工为中批量生产所以采用铣刀加工。
8.连杆大小头孔平行度的检验,可采用穿入专用心轴,在平台上用等高的V型块支撑连杆大头孔心轴,测量大头孔心轴在最高位置时两端的差值,其差值一半即为平行度误差。
2选择毛坯、绘制毛坯简图
在各类机械中,连杆盖为为传动件,由于其在工作时处于运动中,经常受冲击和高压载荷,要求具有一定的强度和韧性。
该零件的材料选择QT450-10,零件的轮廓尺寸不大,形状不是很复杂,为成批量生产模型,从减少加工难度来说,经查机制工艺手册,毛坯采用铸造成型。
因为零件形状并不复杂,但为减小加工时的切削用量和提高生产效率,节约毛坯材料,毛坯形状可以与零件形状接近。
即外形做成台阶形,内部孔铸造出。
确定机械加工余量,及毛坯尺寸。
1)确定机械加工余量
(1)铸件质量:零件表面无明显的裂纹等缺陷。
(2)加工精度:零件除孔以外的各表面为一般加工精度。
(3) 机械加工余量。
根据铸件质量、形状,以及各个加工部位的要求毛坯尺寸和余量如下。
加工表面
基本尺寸
mm
毛坯尺寸
mm
单边总加工余量mm
小头孔直径Ø 20Ø 10 5
大头孔直径Ø 81Ø 70 5.5
零件厚度 43 45 1
大头孔两端
深度
3.5 0 1.75
铸造圆角R3-R5
表:毛坯尺寸和余量
3、工艺规程设计
1.定位基准的选择
该零件是带孔的盘状零件,孔是其设计基准,为避免由于基准不重合而产生误差,应-选孔为定位基准,即选Ø81+0.021 0mm孔及一端面为加工精基准。
由连杆盖有孔、沟槽等都需加工,而孔作为精基准应先加工,因此选外圆及一端面为粗基准。
2.表面加工方法的确定
该零件的加工面有内孔、端面、小孔及槽等,材料为QT450-10。
参考有关资料,其加工方法的选择如下
毛坯的两端面应该互为基准加工,表面粗糙度为Ra3.2µm,需粗铣-半精铣。
大头孔Ø81+0.021 0mm:内表面粗糙度为Ra1.6µm,需进行粗镗-精镗。
小头孔Ø20+0.023 0:内表面粗糙度为Ra1.6µm,需进行扩-半精铰。
大头孔内沟槽:表面粗糙度为Ra6.3µm,一次成型磨即可。
切割面:表面粗糙度为Ra1.6µm,需精铣。
两台阶面;底面为Ra6.3µm,侧面为Ra1.6µm,故采用粗铣台阶面后,对则面进行精铣并保证距离尺寸94 0 -0.023mm,以及对称度0.3mm A。
两个螺纹孔的加工:钻-铰孔。
小头孔的大沟槽采用R67mm的成型铣刀去加工。
大头孔内表面的沟槽采用R25的砂轮磨削。
小头孔里面的够槽用精细的镗刀加工。
在将连杆盖毛坯从大头孔中间切开的时候采用2mm的锯片铣刀。
3.确定工艺路线
连杆的加工工艺路线一般是先进行外形的加工,再进行孔、槽等加工。
连杆的加工包括各侧面和端面的加工。
按照先加工基准面及先粗后精的原则,连杆盖加工可按下面工艺路线进行。
又因为此零件要求小批量生产,所以工序安排要求较集中。
工序10:铸造毛坯。
工序20:无损探伤,查是否有夹渣,气孔,疏松等缺陷。
工序30:清理毛刺、飞边,涂漆。
工序40:人工时效处理。
工序50:划杆身中心线,以及大小头孔的中心线。
工序60:按线加工,精铣连杆大小头两平面,互为基准(加工中多翻转几次)至尺寸43-0.20 -0.36mm。
工序70:重划大小头孔中心线,并选择一个面为基面。
工序80:以基面定位,按线找正,粗镗大小头孔,分别为Ø78±0.05mm,
Ø17±0.05mm.
工序90:以基面定位,按线找正,精镗大头孔到Ø81+0.021 0mm。
并定其轴线为基准A。
工序100:以大头孔、基面定位,借助侧面装夹工件,精镗小头孔至
Ø20+0.023 0mm。
并保证中心距为85+0.1 0mm,以及对基准A的平行度为0.01mm。
工序110:磨大头孔内表面的沟槽砂轮R25mm,磨削深度2.5mm。
车倒角1*45度。
工序120:以基面、侧面和小头孔定位装夹工件,按照大头孔的中心线用锯片铣刀将连杆
切开,并对连杆做好标记。
工序130:以基面、连杆体侧面和分割面装夹工件,铣削两个台阶面,保证台阶面的距离为94 0 -0.023mm,深度3.5+0.05 0mm,以及对基准A的对称度为0.3mm。
钻两边的底孔Ø10mm,保证中心距为110±0.15。
工序140:由钳工铰孔2-M12-6H。
工序150:以连杆分割面、基面定位装夹,铣削沟槽宽15+0.15 +0.05mm,R67mm的盘形铣刀。
对基准A的对称度为0.01mm。
工序160:用微型铣刀铣内沟槽直径Ø21+0.28 0mm,宽1.1+0.12 0 mm,两沟槽距离37+0.15 0mm。
工序170:车倒角0.5*45度。
工序180:检查各个部分的尺寸和精度。
工序190:组装入库。
4.工序设计
1) 选择加工设备与工艺装备。
(1) 选择机床。
a.工序11、17、是车倒角。
该零件外廓尺寸不大,选用CA6140卧式车床即可。
b.工序06、13为粗铣铣、精铣。
由于加工的零件轮廓尺寸不大,,故宜在普通铣床就可以。
选用立式铣床X52K型铣床。
c.工序08、09、10为粗镗、精镗。
从加工要求及尺寸大小考虑,选用卧式镗床T611。
d.工序11是用Ø50mm的砂轮去磨,需要组合夹具,用内圆磨床考虑到孔的大小用M2120内圆磨床。
e.工序12因为要将连杆锯断,工件尺寸不是很大,用卧式铣床X63W。
f.工序13 钻孔考虑孔的尺寸等技术要求,采用立时钻床Z518。
g.工序15考虑到加工位置和技术要求需要用卧式铣床X63W。
h.工序16加工内沟槽,用微型镗刀加工,由于是回转体采用车床CA6140。
(2) 夹具。
组合夹具和普通的三抓、四爪卡盘就可以。
(3) 选择刀具。
在工序11需用到R25mm的砂轮。
工序16需要刃口小于1.1mm的细小镗刀。
(4) 选择量具。
本零件属于小批量生产,一般采用通用量具。
选择量具的方法有两种:一是按计量器具的精确度选择;二是按计量器具的测量方法极限误差选择。
a.各工序的量具见下表
b.选择加工槽所用量具。
均可选用分度值0.02mm,测量范围0~150mm游标卡尺进行测量。
2)确定工序尺寸
(1)确定圆柱面的工序尺寸。
查表可以得出该零件圆柱表面的工序加工余量、工序尺寸及公差、表面粗糙度见下表
1
1
1
g.确定铣小头沟槽的工序尺寸。
精铣可达到要求,则该工序尺寸:槽宽15+0.15 +0.05mm,槽深R67。
粗铣时,为半精铣留有加工余量:槽宽双边余量为2mm,槽深余量为2mm。
则粗铣的工序尺
寸:槽宽为13mm,槽深为R65mm的圆。
将以上结果填入机械加工工序卡内。