硫化碱生产工艺流程
硫化碱脱硫、膜吸收脱硫、微生物脱硫技术及工艺与优缺点图文并茂详解
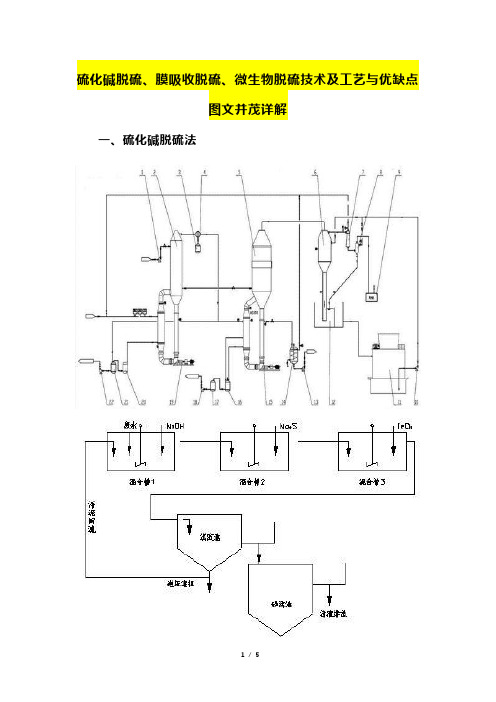
硫化碱脱硫、膜吸收脱硫、微生物脱硫技术及工艺与优缺点图文并茂详解一、硫化碱脱硫法硫化碱脱硫法主要利用工业级硫化纳作为原料来吸收SO2工业烟气,产品以生成硫磺为目的。
反应过程相当复杂,有Na2SO4、Na2SO3、Na2S203、S、Na2Sx等物质生成,由生成物可以看出过程耗能较高,而且副产品价值低,过程中的各种硫的化合物含量随反应条件的改变而改变,将溶液pH值控制在5.5—6.5之间,加入少量起氧化作用的添加剂TFS,则产品主要生成Na2S203,过滤、蒸发可得到附加值高的5H 0·Na2S203,而且脱硫率高达97%,反应过程为:SO2 Na2S=Na2S203 S。
二、膜吸收脱硫法以有机高分子膜为代表的膜分离技术是一种气体分离新技术,已得到广泛的应用,尤其在水的净化和处理方面。
利用膜来吸收脱出SO2气体,效果比较显著,脱硫率达90%。
过程是:他们利用聚丙烯中空纤维膜吸收器,以NaOH溶液为吸收液,脱除SO2气体,其特点是利用多孔膜将气体SO2气体和NaOH吸收液分开,SO2气体通过多孔膜中的孔道到达气液相界面处,SO2与NaOH迅速反应,达到脱硫的目的。
此法是膜分离技术与吸收技术相结合的一种新技术,能耗低,操作简单,投资少。
三、微生物脱硫技术根据微生物参与硫循环的各个过程,并获得能量这一特点,利用微生物进行烟气脱硫。
机理为:在有氧条件下,通过脱硫细菌的间接氧化作用,将烟气中的SO2氧化成硫酸,细菌从中获取能量。
生物法脱硫与传统的化学和物理脱硫相比,基本没有高温、高压、催化剂等外在条件,均为常温常压下操作,而且工艺流程简单,无二次污染。
以地热发电站每天脱除5t量的H:S为基础;计算微生物脱硫的总费用是常规湿法50%。
无论对于有机硫还是无机硫,一经燃烧均可生成被微生物间接利用的无机硫SO2,微生物烟气脱硫技术在实验室条件下,选用氧化亚铁杆菌进行脱硫,在较低的液气比下,脱硫率达98%。
精制硫化碱可行性研究报告

精制硫化碱可行性研究报告本报告旨在探讨精制硫化碱的可行性,通过对现有技术的调研和分析,提出一种新型的硫化碱生产工艺,并评估其经济性和环保性。
具体内容如下:一、硫化碱生产现状及存在的问题1. 硫化碱的应用领域及市场需求硫化碱作为一种重要的硫化物,在橡胶、化工和冶金等产业中有着广泛的应用。
根据市场研究数据显示,硫化碱的市场需求量逐年增长,且价格稳定。
2. 硫化碱生产的传统工艺及问题目前硫化碱的生产主要采用硫磺工艺,即硫磺与氢氧化钠反应生成硫化碱。
这种工艺存在着硫磺资源消耗大、废气废水污染严重、生产成本高等问题。
二、精制硫化碱生产工艺研究1. 新型硫化碱生产工艺介绍通过对目前硫化碱生产工艺的缺陷进行分析,提出了一种基于氨硫化法的新型硫化碱生产工艺。
该工艺利用氢硫气体与氨水反应生成硫化氢,再与氢氧化钠反应生成硫化碱。
该工艺具有原料易得、废料少、生产成本低等优点。
2. 工艺流程设计根据新型硫化碱生产工艺的特点,设计了相应的工艺流程。
主要包括氨硫化反应器、硫化碱生成反应器、反应产物处理装置等组成。
三、精制硫化碱生产工艺可行性评估1. 经济性分析通过对新型硫化碱生产工艺的设备投资、原料成本、能耗费用等进行分析,得出了生产一吨硫化碱的成本。
同时根据市场需求量和价格,评估了该工艺的经济效益。
2. 环保性评估新型硫化碱生产工艺采用氨硫化法替代硫磺工艺,能够减少硫磺资源消耗,降低废气废水排放量,减少环境污染。
因此,该工艺具有明显的环保优势。
四、结论与展望通过对精制硫化碱的可行性研究,我们得出了以下结论:1. 新型硫化碱生产工艺具有较高的经济性和环保性,能够满足市场需求。
2. 未来可以进一步完善该工艺,提高生产效率和产品质量。
3. 鼓励企业在生产中采用新型硫化碱工艺,实现经济效益和环保效益的双赢。
综上所述,精制硫化碱的生产工艺具有明显的可行性,有望成为硫化碱生产的新趋势。
希望本报告能够为相关行业提供参考,推动新型硫化碱工艺的推广应用。
硫氢化钠
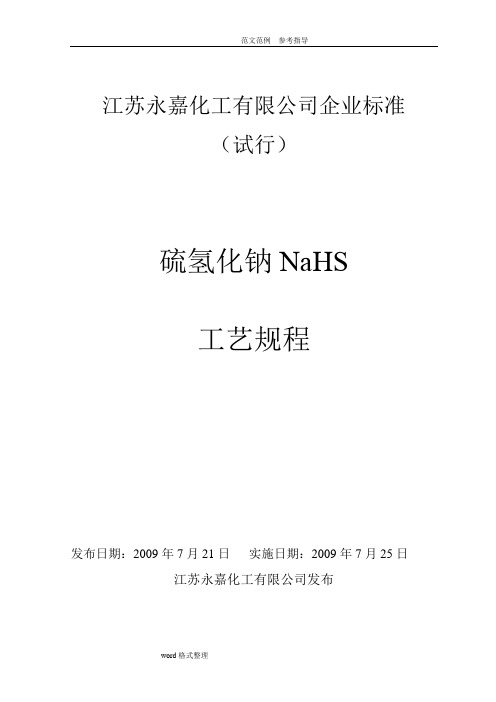
江苏永嘉化工有限公司企业标准(试行)硫氢化钠NaHS工艺规程发布日期:2009年7月21日实施日期:2009年7月25日江苏永嘉化工有限公司发布前言本标准的主要起草人为何炳良本标准于2009年7月进行第一次修订修订:日期:批准:日期:1、主题内容与适用范围本标准规定了硫氢化钠NaHS产品说明,原材料规程,生产基本原理及化学反应方程式,工艺流程叙述,生产控制一览表,可能发生的不正常现象处理方法,消耗定额,安全生产的基本原则。
原材料及成品的检验,设备一览表,工艺规程的修改与补充。
2、产品说明2.1名称:硫氢化钠分子量:76分子式:NaHS2.2产品性质水溶液呈强碱性。
遇酸反应生成硫化氢。
工业品一般呈橙色或黄色溶液,味苦。
2.3产品规格2.3.1液体硫氢化钠的质量指标:2.3.2固体硫氢化钠质量指标a.总还原力质量分数(以NaHS计):≥30.0%b.溶剂萃取色泽:合格(内控)c.外观呈橙色或黄色溶液2.4产品用途染料工业用于合成有机中间体和制备硫化染料的助剂,工业用于生皮的脱毛及鞣革等。
化肥工业用于脱去活性炭去中的单体硫,采矿工业大量用于铜矿选矿,人造纤维生产中用于亚硫酸染色等,是制造硫化铵及农药正硫醇半成品的原料,还用于废水处理等。
3.原材料规格4、生产基本原理及化学反应方程式基本原理:本反应是硫化氢与碱液的酸碱反应,它分二步完成,生成产品硫氢化钠:反应方程式:a. H2S + 2NaOH →Na2S + 2H2Ob. Na2S + H2S →2 NaHS总方程式:H2S + NaH →NaHS + H2O5、工艺流程概述5.1配方(还原力30%的NaHS)5.2配料5.2.1还原力30%的NaHS的配料在2#吸收罐内加液碱2542kg,加2328 kg,打循环10分钟,在取样品取样测稀碱的比重,确保比重在1.162-1.63之间5.2.2用于切片生产的NaHS的配料在2#吸收罐内加32%的液碱4870kg。
硫化钠.——精选推荐

5
3 碳还原芒硝法生产流程简述
将含 Na2SO4 85%的无水芒硝与含固定碳 60%的原料煤按 100/22.5(质量比) 配比混料,用自动上料机打入料斗,送入喷烧 200#重油的回转炉内进行反应。 反应温度为 1100K,其反应如下: Na2SO4+2C=Na2S+2CO2 当炉内有黄色烛火出现即为反应终点。反应好的含硫化钠 70%左右的黑灰熔 体出料、稍经冷却、后粉碎在化碱器内,用 6 Be 碱液化成混浊的浓碱液。目前, 转炉卸出的熔体大多用热浸法, 即熔体从回转炉中放出不经冷却和凝固立即在热 浸取,搅拌 24 小时左右,浸取分为 4 级浸取,以提高硫化钠的回收率,最终所 制得含 28-32%硫化钠的溶液。用离心机或真空吸滤机分离滤渣。滤渣主要是未 反应的煤,灰分,重金属硫化物等。浓碱液送去蒸发,蒸发浓缩至 60%的碱液, 注入铁皮桶中自然冷却,整块凝固即得块状硫化钠产品。
K=
年产量 纯度 工作时间 摩尔质量 0.857
20000 60% 1000 300 24 0.857 78.04 =24.920kmol/h
1
1 设计任务 1.1 课程设计题目
年产 20000t 60%的硫化钠的工业设计
1.2 设计要求 1、生产能力:20000t/a 60%的硫化钠 2、生产原料:含 85%Na2SO4 的芒硝;含 60%固定碳的原料煤;200#重油为燃 料油; 3、其他参数自己选择;
1.3 设计图要求 1、用 A4 图纸绘制装置图一张:一主视图,一俯视图,一剖视图,两个局部 放大图。设备技术要求、主要参数、接管表、部件明细表、标题栏。 2、用 A4 图纸绘制设备流程图一张。 3、用 A4 图纸绘制车间布局图一张。
8
硫化钠

硫化钠一概述1基本情况俗称:臭碱化学式:Na2S分子量:78.042 理化性质纯硫化钠为无色结晶粉末。
吸潮性强,易溶于水。
水溶液呈强碱性反应。
触及皮肤和毛发时会造成灼伤。
故硫化钠俗称硫化碱。
硫化钠水溶液在空气中会缓慢地氧化成硫代硫酸钠、亚硫酸钠、硫酸钠和多硫化钠。
由于硫代硫酸钠的生成速度较快,所以氧化的主要产物是硫代硫酸钠。
硫化钠在空气中潮解,并碳酸化而变质,不断释出硫化氢气体。
工业硫化钠因含有杂质其色泽呈粉红色、棕红色、土黄色。
比重、熔点、沸点,也因杂质影响而异。
当把硫化钠暴露于潮湿的空气的时候,NaS和它的水合物喷出氢硫化物。
23用途硫化钠的用途广泛,是染料工业中用作制造硫化染料的主要原料,在印染工业中,用于溶解硫化染料的助染剂。
在制革工业中,由它所生成的HS- 离子使皮革脱毛,在人造纤维中用于硝化物的还原。
在化学试剂工业中,用于制备硫化氢硫氢化钠、硫代硫酸钠等产品的原料。
二生产工艺1 生产工艺硫化钠的工业生产方法主要有4种:煤粉还原芒硝法,气体还原法,硫酸钡副产硫化钠法。
硫化氢法,根据生产原料限定条件,后 2种方法是不合适的。
第2种方法因生产工艺复杂,生产成本高使用受到限制。
煤粉还原芒硝法,工艺设备简单,易操作控制,对原辅材料要求较低,生产成本低,到目前仍为多数国家所采用,在国内,该法的产量约占总产量的95%以上。
因此,工艺路线采用煤粉还原芒硝工艺硫化钠。
工艺流程:(1)煅烧工序煅烧工序工艺流程如图1所示将含固定碳质量分数在68%以上的原料煤破碎至3 mm以下,经计量,含硫酸钠质量分数85%的芒硝按照纯煤与纯硝质量比为19%-25%的比例配料,混合均匀,用自动上料机送人转炉内,燃料煤经球磨机磨细到80目左右。
由提升机和气流输送装置送人转炉炉膛内燃烧加热,在30-40min内将炉内物料加热到900--950℃,此时,煤部分燃烧而硫酸钠部分熔融,继续提高温度到l050一l150℃.由于反应物中产生的气泡而体积增大,气泡逸出时物料强烈“沸腾”,约15min后,物料体积减小,凝固并粘于炉子内壁上,继续加热,物料变成糊状粗碱体(含Na2S质量分数65%一70% )即可卸出炉外,直接送到浸取工序。
硫化钠生产工艺及在浮选中的应用

硫化钠的生产工艺一种颗粒状硫化钠生产工艺,包括原料-煅烧-热熔-澄清洗泥-化学除杂-沉淀-蒸发浓缩等工序,将浓缩后的硫化钠溶液储存在反应器或搅拌器内,硫化钠含量≥60%,由泵泵出,经过滤器将杂质过滤,进入造粒机的硫化钠溶液温度为130-150℃,输送压力0.3-0.5MPa,经机头喷嘴喷出,在钢带冷却器上冷却成型,固化后的颗粒卸料进入下料器内,真空包装或塑料袋密封包装,即得成品。
硫化钠生产工艺一种颗粒状硫化钠生产工艺,包括原料-煅烧-热熔-澄清洗泥-化学除杂-沉淀-蒸发浓缩等工序,将浓缩后的硫化钠溶液储存在反应器或搅拌器内,硫化钠含量≥60%,由泵泵出,经过滤器将杂质过滤,进入造粒机的硫化钠溶液温度为130-150℃,输送压力0.3-0.5MPa,经机头喷嘴喷出,在钢带冷却器上冷却成型,固化后的颗粒卸料进入下料器内,真空包装或塑料袋密封包装,即得成品。
上述颗粒状硫化钠生产工艺,设计合理,技术先进,依据硫化钠浓缩液独特的物理特性,提供造粒工艺条件、造粒设备,使硫化钠产品实现了颗粒化,真空包装技术得以应用,有效地防止了硫化钠产品的潮解、氧化,从而延长了库存时间。
颗粒化产品可采用自动包装系统,减轻劳动强度,改善工作环境,降低包装成本。
主权项1、一种颗粒状硫化钠生产工艺,包括原料工序——煅烧工序——热熔工序——澄清洗泥工序——化学除杂工序——沉淀工序——蒸发浓缩工序,其特征在于经蒸发浓缩后的硫化钠溶液,硫化钠含量≥60%,由泵泵出,经过滤器将杂质过滤,进入造粒机机头的硫化钠溶液温度为130-150℃,输送压力0.3 -0.5Mpa,经机头喷嘴喷出,在钢带冷却器上冷却成型,固化后的颗粒卸料进入下料器内,真空包装或塑料袋密封包装,即得成品。
一种制备无水、高纯度硫化钠的方法[CN25049-0013-0001][摘要] 本发明涉及一种制备无水、高纯度硫化钠的方法,通过干燥含水的硫化钠使Na2S的含量至少为98wt.%,所用的方法是将含水硫化钠和与水不混溶的有机溶剂一起加热到低于含水硫化钠熔点10-20℃处;然后采用梯级式加热,每级升温1-10℃,并保持5-15分钟,直到高于含水硫化钠熔点10-20℃处;继续加热至水-溶剂混合物的沸点,在真空或压力下共沸蒸馏,蒸馏除去结晶水。
精制硫化碱生产工艺探讨
搅拌 1m n看它的总体积 , 0i 烘到烘箱里 ( 烘箱温
度 8 ̄ 0C)烘 的时 间不能 低于 4 。 h
表 1 实 验 数 据 比较
法和锌 法,并且对 该生产 工艺进行 实验 ,为投 入 工业生产提供 可靠 的实验 依据 和数据 ,保 证 工业生产 的可行性 ,还 确保 了废弃物排放 量的最 小化 和企业利 润的最 大化 。
关键 词 :生产工 艺;可行性 ;最 小化 ;最 大化
l 前 言
随着科 技 的发展 , 人们生 活品质 的不 断提高 , 精 制硫化 碱被广泛 用于制造 高级纸 张 、 高档 颜料 、
碳酸钠 含量降低 到 2 %以下。 () 色上达到黄 色或者浅 黄色 。 3颜 3 硫化钡 溶液 的制 备 . 2
21 0 第 4期 0年
() 把硫 化钡 的黑 灰含 量化验 出来 。 1 先
新疆 降后 的碱水 ,先 看 它 的总体 积 、 2取
色。 34 实验数 据 比较 ( . 见表 1 )
() 碱水 ,测碱水 的 比重 ,温度 ,化 验 它的 1 取 硫 化钠 ( 2 NaS)浓 度 、碳 酸钠 ( 2 O ) 度 、 NaC 3 浓
铁 ( e) 度 。 F 浓 然后 把碱 水温 度升 到 8 " 加 1 0 C再 ~
同液 比 、化 验它 的硫 化钠 ( 2 NaS)浓 度 、碳 酸钠
() 10 2称 0 g硫化 钡 的黑灰 置于 5 0 烧 杯 中 , 0 ml 5 0 清水 温度 升到 8 ℃加 到黑灰 上 ,在 8 ℃下 0 ml 0 0 烘 到烘 箱里 5~4 h并 观察它 的变化 。 0
33 实 验步骤 -
3 的硫 酸锌 ( n O ) 拌 5 i,后加 硫化 钡 g Z S 4 ,搅 a rn ( a 溶液 ( 碱 水 中碳 酸钠 含量 的 5 % ~8 % ) B S) 按 0 0
全棉织物硫化染料染色的原理及工艺流程
Related46网印工业Screen Printing Industry2021.04相关行业染色的原理全棉纺织品应用硫化染料染色的确很经济,而且色牢度也不错,但常会产生红斑、红条,需要返工,影响了产量和成本。
要解决这个问题,必须注意以下几点:用好硫化碱(Na 2S)硫化碱是硫化染料染色不可缺少的主要助剂。
硫化染料染色一定要按具体产品配上不同比例的硫化碱(50%),一般与染料(折成100%)是1:1,像硫化蓝也可配成1:1.5。
它的作用主要是促进染料的溶解与还原。
有时使用的硫化碱不是红棕色,而成灰白色粉末,也一起加入了染浴。
其实,硫化碱呈灰白色粉末状已经被风化,加在染浴中不仅不起溶解、还原染料的作用,相反会使染料过早氧化成为色淀,如水洗不净,就必然产生红斑、红条等染色疵病。
控制好染色工艺条件实践证明,硫化染料的浸染不能按理论上的所谓80~85℃染色,尤其是硫化蓝、硫化黑。
应该在加完染料和硫化碱以后,逐步升温至98℃,保温染色15~20min,然后停止加热;边染色边让缸内的温度降至80~85℃,继续染色20min左右,再边排液边进冷水清洗氧全棉织物硫化染料染色的原理及工艺流程化。
无论排除残液(热)和加入冷水,速度宜缓慢,不宜过快。
这种先热后温的染色方法,既有利匀染,又有利染料的充分溶解和还原,能克服染色疵病。
染物要缓慢清洗上面已经提到,染色后的织物不能一下子放在冷水浴中进行清洗。
尤其像硫化蓝,染好后应从染浴中过渡到温和,甚至在含有一定还原剂的水中进行清洗,术语叫“脚缸”。
这样做不仅有利于织物上的碱剂和还原剂充分净洗,而且有利于织物上染料的充分发色(氧化)。
当然,对于一些难氧化的染料,如硫化蓝CV/3G、红棕GN、深棕等,在第2~3缸水洗浴中还应加入1~2g/L的过硼酸钠和双氧水促使染料充分氧化发色。
注意染浴稳定,在出缸前解决问题硫化染料是一种含硫量较多的染料,尤其如黑色,应用时不稳定的因素很多。
硫化钠的化学式及制备方法
硫化钠的化学式及制备方法
吸收法,用380~420 g/L氢氧化钠溶液吸收含H2S>85%硫化氢废气,所得产物经蒸发浓缩,制得硫化钠成品。
化学反应方程式:H2S+2NaOH→Na2S+2H2O
扩展资料
煤粉还原法:
将芒硝与煤粉按100:(21~22.5)(重量比)配比混合于800~1100℃高温下煅烧还原,生成物经冷却后用稀碱液热溶成液体,静置澄清后,把上部浓碱液进行浓缩,即得固体硫化钠。
经中转槽、制片(或造粒)制得片(或粒)状硫化钠产品
化学反应方程式:Na2SO4+2C→Na2S+2CO2
硫化钡法:
用硫酸钠与硫化钡进行复分解反应制沉淀硫酸钡时可以副产得到硫化钠。
其化学反应方程式:BaS+Na2SO4→Na2S+BaSO4↓
气体还原法:
在有铁催化剂存在下,将氢气(或一氧化碳、发生炉煤气、甲烷气)在沸腾炉中与硫酸钠进行反应,可制得优质无水颗粒状硫化钠(含Na2S 95%~97%)。
化学反应方程式:Na2SO4+4CO→Na2S+4CO2Na2SO4+4H2→Na2S+4H2O 生产方法,精制法以生产沉淀硫酸钡过程中副产的浓度为4%左右的硫化钠溶液为原料,用泵打入双效蒸发器蒸浓至23%后,进人搅拌罐脱铁、除碳处理后,用泵打入蒸发器(用纯镍材制造)蒸发碱液达到浓度,送到滚筒水内冷却式制片机制成后,经筛选、包装而得成品。
- 1、下载文档前请自行甄别文档内容的完整性,平台不提供额外的编辑、内容补充、找答案等附加服务。
- 2、"仅部分预览"的文档,不可在线预览部分如存在完整性等问题,可反馈申请退款(可完整预览的文档不适用该条件!)。
- 3、如文档侵犯您的权益,请联系客服反馈,我们会尽快为您处理(人工客服工作时间:9:00-18:30)。
4.2.1.2 工艺流程说明 本项目对原装置部分使用价值较高的设备进行搬迁,生产工艺流程仍按照搬迁前的进行设计,以焦炭粉为还原剂,采用含铬芒硝和脱水芒硝为原料生产工业低铁硫化碱。生产工序主要包括备料上料工序、煅烧工序、化坯洗渣工序、沉淀洗泥工序、低铁硫化碱制液工序、蒸发工序、制片包装工序。 工艺流程如下: (1) 备料上料工序 由于十水芒硝不能满足硫化碱生产原料的要求,首先要对十水芒硝进行脱水处理。十水芒硝先进入化硝罐,加入热水进行溶解,溶解液体进入蒸发器进行蒸发,蒸发热源采用蒸发工序二次蒸汽,蒸发液送入结晶罐进行冷却结晶,然后再通过皮带输送机送至离心机进行离心分离,分离后的固体为无水芒硝,送至仓库备用,离心母液再返回至蒸发器中进行循环。 原料含铬芒硝和脱水芒硝分别存入专门的储仓,经过破碎后保证进入工艺系统的芒硝粒径不超过50mm,芒硝、焦炭粉分别通过斗式提升机、皮带计量机送至混料机,按一定比例混合,再通过混料皮带输送机送入储料仓,然后经送料螺旋机送入煅烧工序。 (2) 煅烧工序 物料在长转炉(Φ2500×45000)内进行还原反应所需的热量由燃料煤燃烧提供。燃料煤由煤库经皮带输送机送至雷蒙机研磨后,再用斗式提升机送到煤粉仓,由皮带输送机送到炉头煤粉斗,再经下端送料螺旋机送入送风管道内,由罗茨鼓风机吹入长转炉内燃烧。 来自储料仓的芒硝与焦炭粉先进入预热器,然后进入长转炉尾部,燃料煤粉从转炉头部进入,与原料成逆向流动,当炉内温度为1050-1150℃时,芒硝与焦炭粉发生如下化学反应: Na2SO4+2C+→Na2S+2CO2 生成硫化碱; Cr6++C→Cr3+ 毒性较大的Cr6+变为无毒稳定的Cr6+; 同时,在有水蒸汽存在条件下,发生副反应 Na2S+CO2+H2O→Na2CO3+H2S 生成碳酸钠和硫化氢。 物料在转炉内经预热、熔化、沸腾、成熟制得熔体黑灰,从炉头送入热熔罐中,进入化坯洗渣工序,进行热溶。 每台转炉配套一台特制预热器,高温转炉烟气先经过预热器对生料进行预热,然后经降尘室降尘,再用麻石水膜除尘器进行除尘,除尘后进入脱硫塔进行脱硫,达标后排空。回收粉尘经过酸洗后外运至园区指定地点,可用作制砖。 (3)化坯洗渣工序 由煅烧工序来的熔融态黑灰由炉头直接进入热溶罐进行热溶,在搅拌机的作用下,用沉淀洗泥工序的洗渣水(稀卤水)直接制取浓卤碱水,当溶液中Na2S浓度达到23%左右时,用浓卤液下泵将其打至沉淀罐,沉淀罐上层清液送至沉淀洗泥工序浓卤储槽。 沉淀泥渣经过一号铰刀输送至一洗罐,在一洗罐中进一步浸取泥渣中含有的Na2S,一洗罐洗净的渣泥经二号绞刀送至二洗罐,当渣泥中碱含量小于1%时,将渣泥进行酸洗后外运至园区指定地点。洗渣用水为沉淀洗泥工序送来的洗泥水(稀卤水),洗渣水送至热熔罐循环使用。 化坯过程中,Na2S与H2O反应产生少量的H2S气体,故热溶罐为封闭装置,热溶过程中产生的碱雾及H2S气体经喷淋塔洗涤后,由高度为15m的排气筒排空,洗涤液循环使用,浓度增加至一定值时送至热溶罐;喷淋塔污泥定期排至热溶罐,供化坯用。 (4)沉淀洗泥工序 由化坯工序来的浓度为23%的浓卤碱水进入浓卤储槽,通过浓卤泵送入低铁澄清罐中,通入蒸汽,加热浓卤水碱水至70-80℃后恒温静置16小时以上,然后经过浓卤泵送至箱式压滤机进行压滤,压滤后合格的23%的清液送至浓卤清液中转槽中,然后用清液泵送至低铁反应罐进行制备低铁硫化碱。滤渣卸至洗泥地罐,热水洗涤,当洗涤液中碱含量小于1%时,将渣泥送至酸洗罐进行酸洗后外运至园区指定地点,用于制砖。洗泥水送至化坯洗渣工序化坯用。 (5)低铁硫化碱制液工序 制备原理:硫化碱浓卤中的铁是以FeS的胶团微粒形式存在,并处于亚稳定状态。由于浓卤中含有较多的Na2CO3 、Na2SO4、 Na2S2O3 、Na2SO3等可溶性杂质,会影响产品的质量和颜色,本工艺选择加入硫化钡溶液和氧化锌,硫化钡溶液可与这些杂质生成沉淀而除去,硫酸锌和硫化钠生成硫化锌沉淀,沉淀的生成破坏了溶液中FeS胶粒的稳定性,同时生成的沉淀将FeS微粒包裹、吸附、共沉淀,从而达到除铁目的。 工艺流程: 1)硫化钡的制备 焦炭粉和重晶石分别通过斗式提升机、下料管预热器。然后送入原小长转炉(Φ2000×32000)内进行高温煅烧,煅烧热源同煅烧芒硝相同,燃料煤粉由罗茨鼓风机吹入长转炉内燃烧,与重晶石成逆向流动,当炉内温度为1100℃左右时,重晶石与焦炭粉发生如下化学反应: BaSO4+2C+→BaS+2CO2 生成硫化钡。 转炉烟气先经过预热器回收余热,加热生料重晶石,然后再用麻石水膜除尘器进行除尘,除尘后进入脱硫塔进行脱硫,达标后排空。回收粉尘与渣泥一同经过酸洗外运至园区指定地点,用于制砖。 2)硫化钡溶液的制备 煅烧来的熔融态黑灰由炉头直接进入硫化钡浸取槽进行热溶,在电机搅拌的作用下,用新鲜水直接制取硫化钡溶液,洗涤至一定浓度后,将硫化钡溶液送至硫化钡溶液储罐备用。 硫化钡溶液制取工艺流程简图 3)低铁硫化碱制液 浓卤清液进入低铁反应罐后,将配制好的硫化钡溶液及氧化锌加入到低铁反应罐内搅拌20min左右,使溶液中的Na2CO3 、Na2SO4、FeS等杂质充分与除铁剂反应,静置16-24h后,将沉淀下的不溶物通过溜槽排放到低铁地下泥槽,然后将泥渣送至沉淀洗泥工序洗泥地罐进行洗泥;除杂后的澄清液用低铁清液泵送至低铁清液储槽中以备蒸发。 (6)蒸发工序 将低铁清液送入列管蒸发器,通入蒸汽进行加热真空浓缩,当碱液浓缩至34-38%时,调整碱液温度到100℃,直接浓缩至60%后,通过成品液泵打入成品罐。蒸发产生的二次蒸汽送至备料上料工序,用作制备无水芒硝,蒸汽冷凝生成的冷凝水送回锅炉装置。 (7)制片包装工序 由成品罐来的60%浓卤液经泵缓慢送至制片机,经冷却后得到低铁硫化碱,通过皮带输送机输送到自动包装机料斗,包装后送库房储存待售。低铁硫化碱工艺流程简图4.2.2 物料平衡说明 物料平衡图见附图3。
4.2.3 工艺消耗定额 原材料及动力消耗定额
项目 单位 消耗量 (以t产品计) 年耗量
原材料消耗 芒硝 t 34000 焦炭粉 t 8000 重晶石 t 2000 氧化锌 kg 1500 稀盐酸 t 900 石灰 t 1000 包装袋 条 40 800000
公用工程消耗 燃料煤 t 8300 生产用水 m3 36720 工艺生产用电 kW ?h 6103800 蒸汽 t 24624 循环水 t 864
主要设备选择 本项目属于搬迁项目,为了减少投资,只淘汰部分落后及废旧设备,其余设备仍用以前硫化碱生产设备,本项目主要设备选择如下: 一、搬迁设备 (1)雷蒙机:燃料煤每小时消耗量为,原厂5R4018摆式磨煤机1台,磨煤量为2~5t/h,可满足本项目使用要求。 (2)长转炉:煅烧芒硝,炉长度45米,炉体直径2.5m,共2台;煅烧重晶石,炉长度32米,炉体直径2m,共1台,转炉内砌筑高铝耐火砖,另外附属设备有转炉减速机、托辊、托带、挡轮、密封装置等,可满足本项目使用要求。 (3)沉淀罐:沉淀浓卤碱液中的较大颗粒渣体,入口设有隔板,外设保温层,设备直径3米。 (4)蒸发器:按照进液浓度和蒸发使用蒸汽的温度进行计算,仍用以前换热面积为43m2和120m2的强制外循环蒸发器各1台,换热面积为90m2的强制外循环蒸发器2台,能够保证生产正常运行。 (5)制片机:浓度为60%的片碱产量为h,因此设计中选择5台生产能力为1 t/h的制片机。 二、新增更换设备 (1)热化罐:设备附件有搅拌装置和布料盘,考虑到物料的冲刷腐蚀等因素,设备壁厚应选δ=20 mm;考虑劳保卫生条件,化灰槽上方设置集气罩。 (2)钡卤浸取箱:钢板厚度δ=20mm;内设搅拌桨,设备尺寸为长5米,宽1.6米,高1米。 (3)低铁反应罐:钢板厚度δ=20mm;内设搅拌桨,设备尺寸为直径3米,高2米。 (4)洗泥地罐:回收沉淀洗泥工序中残留的硫化钠,钢板厚度δ=20mm,内设搅拌桨。 主要设备一览表 新增更换设备 序号 名称 规格型号 单位 数量 备注 一 工艺装置
1 结晶罐 Φ2000×1800 台 1 2 化硝罐 Φ3000×4000 台 2 3 离心机 Q=800m3/h,N=45kW 台 1
4 斗式提升机 N=3kW 台 3 5 皮带计量机 B=500,L=3000,N= 台 3 6 混料机 B=650,L=5500,N= 台 1 7 储料仓 2000×2000×1200 个 1 需防渗防风防雨 8 送料螺旋机 Φ400,L=3000,N= 台 3 9 皮带输送机 B=650,L=5500,N= 台 5 10 预热器 台 3 11 除尘设备 套 3 12 脱硫塔 套 3 13 烟囱 H=30米 套 3
14 热化罐 Φ3000×1800 个 3 2520 附:搅拌电机 N=20kW
15 浓卤储槽 Φ5000×4000 个 9 附:搅拌电机 N=15kW 16 浓卤清液中转罐 Φ3000×2000 个 7 17 清液泵 Q=10m3/h,H=21.5m,N= 个 7 18 低铁总卤罐 Φ3000×2000 个 6
19 低铁反应罐 Φ3000×2000 个 6 附:搅拌电机 N=
20 洗泥地罐 Φ2000×1800 个 1 附:搅拌电机 N=
21 低铁地下泥槽 Φ3000×2000 个 1 附:搅拌电机 N=
22 钡卤浸取箱 5000×1600×1000 个 3 23 钡卤输送泵 Q=15m3/h,H=30m,N= 个 3
24 硫化钡溶液储槽 Φ3000×2000 个 2 附:搅拌电机 N=
25 低铁清液泵 Q=15m3/h,H=30m,N= 台 6
26 溜槽 B=500,L=2500 个 2 二 空压制氮站 1 空气压缩机 排 气 量Q=min 套 2 备一 排气压力P=,N=15kW
2 微热再生干燥器 处理气量Q=min,N=3 kW 台 2 备一 3 工艺空气储罐 V=2m3 台 1 16MnR 搬迁设备 1 颚式破碎机 PE250×400,N= 台 1