PCB板焊接工艺通用标准
PCB电路板焊接工艺及要求

6)元器件在PCB板上的插装应分布均匀,排列整齐美观,不允许斜排、立体交叉和重叠排列,不允许一边高,一边低,也不允许引脚一边长,一边短。
7)做好防静电措施,手工焊接电烙铁一定要接地。
8)部分特殊原件பைடு நூலகம்接要求,如下表:
a:晶振XT1:焊接时需要加绝缘垫片,外壳要接地用焊锡把晶振外壳和旁边的焊盘短接。
2)用喷涂的方法涂覆三防漆时,喷涂面积应比器件所占面积大,以保证全部覆盖器件和焊盘;
3)原则上喷涂三防漆一次,喷涂厚度为0.1—0.3mm之间。喷涂时线路板尽量平放,电路板的顶层和底层均应喷涂,喷涂后不应有滴露,也不能有裸露的部分。
4)电路板做喷涂三防漆前,对电路板标号J1,J2,J3,J4端子做相应防护;底层标号AD_L,AD_R,AD_M,VDD,VCC,GND做相应防护;红外对管D1,D2接收、发送的表面做相应防护。
b:红外对管D1,D2:焊接时整体高度要求8.8mm±0.2mm。如下图:
注:晶振、红外对管在电路板清洗后焊接。
器件
项目
SMD贴片器件
DIP直插器件
焊接时烙铁头温度
320±10℃
330±5℃
焊接时间
每个焊点1—3秒
2—3秒
拆除时烙铁头温度
310—350℃
330±5℃
备注
波峰焊,浸焊最高温度260℃。
波峰焊,浸焊时间≤5S。
当焊接大功率或焊点与大铜箔相连,上述温度无法焊接时,烙铁温度可升高至360℃。当焊接敏感怕热零件(LED、传感器、晶振)温度控制在200—300℃,使用免清洗焊锡丝焊接。
PCB板
1)焊点的机械强度要足够
2)焊接可靠,保证导电性能
PCB工艺制造常用标准

PCB工艺制造常用标准1) IPC-AC-62A:焊接后水成清洗手册。
描述制造残留物、水成清洁剂的类型和性质、水成清洁的过程、设备和工艺、质量控制、环境控制及员工安全以及清洁度的测定和测定的费用。
2) IPC-SA-61 A:焊接后半水成清洗手册。
包括半水成清洗的各个方面,包括化学的、生产的残留物、设备、工艺、过程控制以及环境和安全方面的考虑3) IPC-ESD-2020:静电放电控制程序开发的联合标准。
包括静电放电控制程序所必须的设计、建立、实现和维护。
根据某些军事组织和商业组织的历史经验,为静电放电敏感时期进行处理和保护提供指导。
4) IPC-DRM -4 0E:通孔焊接点评估桌面参考手册。
按照标准要求对元器件、孔壁以及焊接面的覆盖等详细的描述,除此之外还包括计算机生成的3D 图形。
涵盖了填锡、接触角、沾锡、垂直填充、焊垫覆盖以及为数众多的焊接点缺陷情况。
5) IPC-TA-722:焊接技术评估手册。
包括关于焊接技术各个方面的45 篇文章,内容涉及普通焊接、焊接材料、手工焊接、批量焊接、波峰焊接、回流焊接、气相焊接和红外焊接。
6) IPC-7525:模板设计指南。
为焊锡膏和表面贴装粘结剂涂敷模板的设计和制造提供指导方针i 还讨论了应用表面贴装技术的模板设计,并介绍了带有通孔或倒装晶片元器件的?昆合技术,包括套印、双印和阶段式模板设计。
7) IPC/EIA J-STD-004:助焊剂的规格需求一包括附录I 。
包含松香、树脂等的技术指标和分类,根据助焊剂中卤化物的含量和活化程度分类的有机和无机助焊剂;还包括助焊剂的使用、含有助焊剂的物质以及免清洗工艺中使用的低残留助焊剂。
8)IPC/EIA J-STD -005:焊锡膏的规格需求一包括附录I 。
列出了焊锡膏的特征和技术指标需求,也包括测试方法和金属含量的标准,以及粘滞度、塌散、焊锡球、粘性和焊锡膏的沾锡性能。
9) IPC/EIA J-STD -0 06A:电子等级焊锡合金、助焊剂和非助焊剂固体焊锡的规格需求。
电路板焊接工艺模板

资料内容仅供您学习参考,如有不当或者侵权,请联系改正或者删除。
PCB板焊接工艺1.PCB板焊接的工艺流程1.1PCB板焊接工艺流程介绍PCB板焊接过程中需手工插件、手工焊接、修理和检验。
1.2PCB板焊接的工艺流程按清单归类元器件—插件—焊接—剪脚—检查—修整。
2.PCB板焊接的工艺要求2.1元器件加工处理的工艺要求2.1.1元器件在插装之前, 必须对元器件的可焊接性进行处理, 若可焊性差的要先对元器件引脚镀锡。
2.1.2元器件引脚整形后, 其引脚间距要求与PCB板对应的焊盘孔间距一致。
2.1.3元器件引脚加工的形状应有利于元器件焊接时的散热和焊接后的机械强度。
2.2元器件在PCB板插装的工艺要求2.2.1元器件在PCB板插装的顺序是先低后高, 先小后大, 先轻后重, 先易后难, 先一般元器件后特殊元器件, 且上道工序安装后不能影响下道工序的安装。
2.2.2元器件插装后, 其标志应向着易于认读的方向, 并尽可能从左到右的顺序读出。
2.2.3有极性的元器件极性应严格按照图纸上的要求安装, 不能错装。
2.2.4元器件在PCB板上的插装应分布均匀, 排列整齐美观, 不允许斜排、立体交叉和重叠排列; 不允许一边高, 一边低; 也不允许引脚一边长, 一边短。
2.3PCB板焊点的工艺要求2.3.1焊点的机械强度要足够2.3.2焊接可靠, 保证导电性能2.3.3焊点表面要光滑、清洁3.PCB板焊接过程的静电防护3.1静电防护原理3.1.1对可能产生静电的地方要防止静电积累, 采取措施使之控制在安全范围内。
3.1.2对已经存在的静电积累应迅速消除掉, 即时释放。
3.2静电防护方法3.2.1泄漏与接地。
对可能产生或已经产生静电的部位进行接地, 提供静电释放通道。
采用埋地线的方法建立”独立”地线。
3.2.2非导体带静电的消除: 用离子风机产生正、负离子, 能够中和静电源的静电。
常使用的防静电器材4.电子元器件的插装电子元器件插装要求做到整齐、美观、稳固。
电路板板焊接工艺和流程
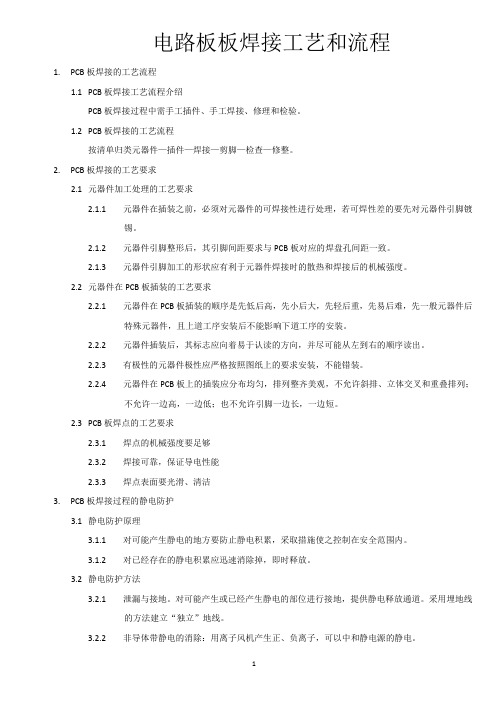
电路板板焊接工艺和流程1.PCB板焊接的工艺流程1.1PCB板焊接工艺流程介绍PCB板焊接过程中需手工插件、手工焊接、修理和检验。
1.2PCB板焊接的工艺流程按清单归类元器件—插件—焊接—剪脚—检查—修整。
2.PCB板焊接的工艺要求2.1元器件加工处理的工艺要求2.1.1元器件在插装之前,必须对元器件的可焊接性进行处理,若可焊性差的要先对元器件引脚镀锡。
2.1.2元器件引脚整形后,其引脚间距要求与PCB板对应的焊盘孔间距一致。
2.1.3元器件引脚加工的形状应有利于元器件焊接时的散热和焊接后的机械强度。
2.2元器件在PCB板插装的工艺要求2.2.1元器件在PCB板插装的顺序是先低后高,先小后大,先轻后重,先易后难,先一般元器件后特殊元器件,且上道工序安装后不能影响下道工序的安装。
2.2.2元器件插装后,其标志应向着易于认读的方向,并尽可能从左到右的顺序读出。
2.2.3有极性的元器件极性应严格按照图纸上的要求安装,不能错装。
2.2.4元器件在PCB板上的插装应分布均匀,排列整齐美观,不允许斜排、立体交叉和重叠排列;不允许一边高,一边低;也不允许引脚一边长,一边短。
2.3PCB板焊点的工艺要求2.3.1焊点的机械强度要足够2.3.2焊接可靠,保证导电性能2.3.3焊点表面要光滑、清洁3.PCB板焊接过程的静电防护3.1静电防护原理3.1.1对可能产生静电的地方要防止静电积累,采取措施使之控制在安全范围内。
3.1.2对已经存在的静电积累应迅速消除掉,即时释放。
3.2静电防护方法3.2.1泄漏与接地。
对可能产生或已经产生静电的部位进行接地,提供静电释放通道。
采用埋地线的方法建立“独立”地线。
3.2.2非导体带静电的消除:用离子风机产生正、负离子,可以中和静电源的静电。
常使用的防静电器材4.电子元器件的插装电子元器件插装要求做到整齐、美观、稳固。
同时应方便焊接和有利于元器件焊接时的散热。
4.1元器件分类按电路图或清单将电阻、电容、二极管、三极管,变压器,插排线、座,导线,紧固件等归类。
PCB设计工艺标准系列 焊接工艺标准
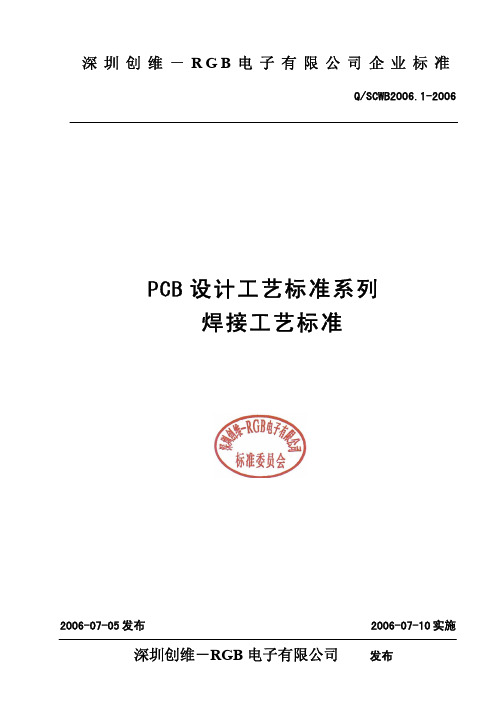
深圳创维-R G B电子有限公司企业标准 Q/SCWB2006.1-2006PCB设计工艺标准系列焊接工艺标准2006-07-05发布 2006-07-10实施 深圳创维-RGB电子有限公司 发布Q/SCWB2006.1-2006目 次前言 (II)1.范围 (1)2.PCB尺寸 (1)3.PCB板边 (1)4.IC及多位插座排版方向 (2)5.PCB设置支撑标识 (2)6.PCB标识过波峰方向 (2)7.装焊的元件焊盘要开阻焊槽 (3)8.白油线阻焊 (3)9.偷锡焊盘 (4)10.接地螺钉孔焊盘 (4)前 言本标准是为了规范、统一深圳创维-RGB电子有限公司所有电子产品的PCB设计工艺标准中有关的焊接工艺,使PCB的设计满足波峰焊接的工艺性,从而提高焊接质量。
本标准是深圳创维-RGB电子有限公司标准委员会制定的内部产品技术标准,适用于深圳创维-RGB电子有限公司内所有电子产品的PCB设计工艺。
本标准由深圳创维-RGB电子有限公司标准委员会提出并归口。
本标准起草单位:深圳创维-RGB电子有限公司制造总部工程部。
本标准主要起草人:陈立志、朱凯坤、邱立波、姚林、霍勇、杨军治。
本标准批准人:吴慧云本标准首次发布日期:2006年7月5日PCB 设计工艺标准体系焊接工艺标准1 范围本标准规定了深圳创维-RGB 电子有限公司内进行PCB 板设计的焊接工艺要求。
本标准适用于公司内所有电子产品的PCB 设计工艺,以及PCB 工艺性的评审。
2 PCB 尺寸2.1 采用机插、波峰焊接工艺的单面PCB 板的最大面积为:508×330mm;最小面积(包括拼板后的面积) 为:90×60mm。
(现波峰焊机的最大宽度为330mm,故PCB 板宽不能超过330mm)2.2 采用机贴、回流焊接工艺的多层PCB 板的最大面积为:460×350mm;最小面积(包括拼板后的面积) 为:50×50mm。
PCBA焊锡作业标准及通用检验标准
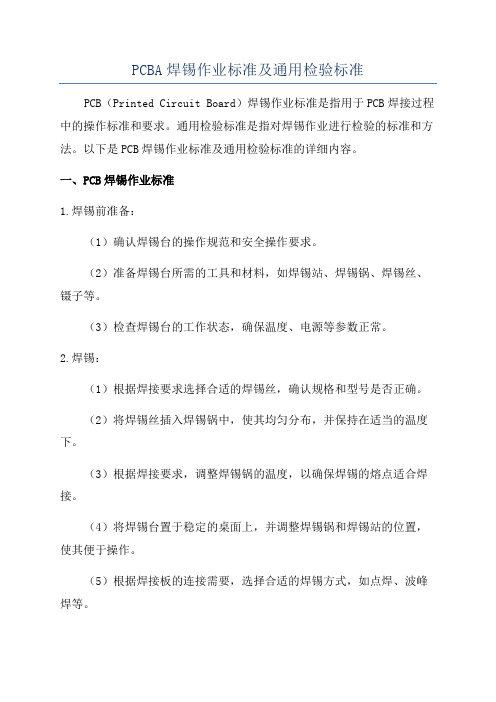
PCBA焊锡作业标准及通用检验标准PCB(Printed Circuit Board)焊锡作业标准是指用于PCB焊接过程中的操作标准和要求。
通用检验标准是指对焊锡作业进行检验的标准和方法。
以下是PCB焊锡作业标准及通用检验标准的详细内容。
一、PCB焊锡作业标准1.焊锡前准备:(1)确认焊锡台的操作规范和安全操作要求。
(2)准备焊锡台所需的工具和材料,如焊锡站、焊锡锅、焊锡丝、镊子等。
(3)检查焊锡台的工作状态,确保温度、电源等参数正常。
2.焊锡:(1)根据焊接要求选择合适的焊锡丝,确认规格和型号是否正确。
(2)将焊锡丝插入焊锡锅中,使其均匀分布,并保持在适当的温度下。
(3)根据焊接要求,调整焊锡锅的温度,以确保焊锡的熔点适合焊接。
(4)将焊锡台置于稳定的桌面上,并调整焊锡锅和焊锡站的位置,使其便于操作。
(5)根据焊接板的连接需要,选择合适的焊锡方式,如点焊、波峰焊等。
(6)将焊锡台插入电源,开启电源,待焊锡锅温度达到预设温度时,即可进行焊锡作业。
3.焊锡操作:(1)根据焊接板的要求,将焊锡丝加热熔化,使其变为液态。
(2)将焊锡丝沿着焊接板的焊盘或焊脚上涂抹,确保焊锡覆盖完整且与焊盘或焊脚接触紧密。
(3)焊锡过程中,保持焊锡锅温度适宜,避免焊锡过热或过冷,影响焊接效果。
(4)焊锡完毕后,用镊子将焊锡丝修剪整齐,确保焊接部位平整、美观。
4.清洁和保养:(1)焊锡作业完成后,及时清洁焊锡台和焊锡锅,以防止焊锡残渣附着和污染。
(2)定期检查焊锡台和焊锡锅的工作状态,维护和保养设备,确保其正常运行。
1.外观检查:(1)检查焊接部位的焊锡覆盖是否均匀,焊接点和焊脚是否有无焊、短路等情况。
(2)检查焊接部位是否有焊渣、焊尖等残留物,以及焊接面是否平整、光滑。
2.尺寸检查:(1)测量焊接部位的焊盘或焊脚的尺寸是否符合设计要求。
(2)检查焊接部位的间距是否一致,焊点与焊点之间是否存在短路现象。
3.电性能检查:(1)使用万用表或特定仪器测量焊接点的电阻值,确认焊接是否牢固,导通性良好。
电路板的焊接工艺标准

电路板的焊接工艺标准The Circuit Board Soldering ProcessSoldering is an essential process in ___ results。
___.1.Necessary ns for Soldering1.1 Clean Metal SurfaceIf the metal surface to be soldered has an oxide film or any dirt。
it will create obstacles during soldering。
making ___。
it is necessary to remove them。
The oxide film can be removed with rosin。
while dirt like grease requires solvents.1.2 Appropriate ___If the temperature of the heated metal is lower than the melting point of the solder。
the solder will not melt properly and will not adhere to the metal surface。
Therefore。
it is essential to heat it within the appropriate temperature range。
If the heating temperature is too low。
the n and n properties will rate。
___.1.3 Appropriate Amount of SolderIf the amount of solder supplied cannot match the size of the soldering area。
PCBA焊接规范

PCB焊接操作规范1、PCB焊接工艺过程1.1 PCB焊接工艺流程PCB焊接过程需手工插件、手工焊接、修理和检验1.2PCB焊接的工艺过程按清单归类元器件—插件—焊接—剪脚—检查—修整2、PCB焊接的工艺要求2.1元器件加工处理的工艺要求2.1.1 元器件在插装前,检查插接件的外观、引脚间隙与焊盘孔间隙一致2.1.2 元器件引脚加工的形状必须有利于元器件的焊接和焊接后的强度并且符合设计图纸要求2.2、元器件在PCB的插装的工艺要求2.2.1元器件PCB的插装顺序是先低后高,先小后大,先轻后重,先易后难,先一般元器件后特殊元器件,且上道工序后不能影响下到工序2.2.2元器件插装后,其标准应向着易于认读的方向,并尽可能从左到右的顺序排列2.2.3有极性的元器件必须要按照图纸要求进行安装,不能装错2.2.4 元器件在PCB焊接后必须插针高度一致,整齐美观,不允许歪斜,一高一矮,引脚一边长一边短2.2.5电烙铁移动方向下面不能有电子元器件、PCB板等待焊接物料以及已经焊接完整的PCB板2.3、PCB的焊点工艺要求2.3.1焊点的机械结构强2.3.2焊点可靠,保证通断2.3.3焊点表面光滑、漂亮、清洁3、PCB的焊接过程的静电防护3.1静电防护3.1.1对可能产生静电的地方要防止静电积累,采取措施使之控制在安全范围内3.1.2对已经存在静电积累的应迅速释放,避免静电击穿3.2静电防护方法3.2.1对可能产生或已经产生静电的部位进行接地,提供静电释放通道(佩戴防静电手带)3.3.2非导体的带静电消除:用离子风扇,产生正、负离子进行中和静电3.3.3作业时车间需佩戴防静电手带、橡胶手指套或防静电手套、身穿静电服、脚穿静电鞋4、电子元器件4.1电子元器件的分类按电子清单将接插件、PCB、电阻、电容、继电器、导线,紧固件等进行归类,桌面整齐、不干净,每日开班前后对桌面进行整理、整顿不允许混料,乱放,标识不清,桌面不干净4.2元器件的整形基本要求所有元器件引脚不准从根部进行弯曲,最小尺寸为1.5mm4.3元器件的引脚变形手工加工的元器件整形,弯引脚允许使用镊子、小螺丝刀等工具对引脚进行整形4.4插装插接件插装时不准用手碰触导电盘、焊盘等线路板金属部件,员工操作时必须佩戴橡胶手指套,防静电手带5、手工焊接主要工具5.1手工焊接是每个电子焊接工必须要掌握的技术,正确选用焊接材料,根据实际选用焊接工具是保证焊接质量的必要条件5.2常用焊接材料:焊锡丝、松香、助焊剂、酒精、洗板水5.3常用焊接工具:恒温电烙铁、热风枪、吸锡枪、烙铁头、漏网(当焊盘较小时采用尖嘴烙铁头、当使用IC类采用刀型烙铁头、一般使用3C烙铁头、烙铁架下面必须存放漏网)6、手工焊的流程和方法6.1手工焊的条件被焊件必须具备可焊性、被焊件金属表面清洁、使用合理的助焊剂、具有合适的焊接温度、具有适合的焊接时间6.2手工焊的方法6.2.1电烙铁和焊锡丝的握法手工焊3种焊接方法反握、正握、握笔试下图是2种送锡拿法6.2.2手工焊的操作步骤①准备焊接清洁桌面上的尘埃,上次焊接后的多余PCB、插件总成等物料②进行焊接将沾有焊锡的烙铁头碰触到需要焊接的位置,时间需要控制在4s内,温度设置为有铅焊锡丝:350±30℃,无铅焊锡丝:400±30℃,引线发光管:370±30℃(适应于无铅焊锡丝,有铅焊锡丝温度:350±30℃)③检查焊接目测焊点光滑圆润,光亮,牢固,是否与其它元器件有连焊现象7.焊接不现象8、焊接拆卸拆卸工具:电烙铁、吸锡器、镊子①普通插件元器件拆卸方法:一手拿着电烙铁对着拆卸的元器件上,另外一手拿镊子夹着元器件,待焊点融化时,用镊子轻轻往外拉元器件②IC类元器件拆卸方法:使用热风枪进行拆卸,温度控制在350±30℃,风量控制3-4格,对引脚来回、均匀的进行吹热风,用镊子夹取IC类元器件9、焊接工装批量生产前允许使用高温胶粘贴待焊接PCBA的导电盘后进行手工焊接,试生产后必须使用焊接工装进行手工焊接(如没有焊接工装,需要出临时文件以及规定时间内完成焊接工装)(条件允许的情况下可使用自动焊接或者波峰焊进行焊接)①焊接工装不允许与待焊接PCBA和插接件有干涉、让位不足等影响产品质量的问题②焊接工装需要增加待焊接PCBA导电盘的和发光管的防护板③易于手工焊接电烙铁的放置和焊锡丝的抽取,优先级<①、②。
- 1、下载文档前请自行甄别文档内容的完整性,平台不提供额外的编辑、内容补充、找答案等附加服务。
- 2、"仅部分预览"的文档,不可在线预览部分如存在完整性等问题,可反馈申请退款(可完整预览的文档不适用该条件!)。
- 3、如文档侵犯您的权益,请联系客服反馈,我们会尽快为您处理(人工客服工作时间:9:00-18:30)。
P C B板焊接工艺通用标准集团标准化工作小组 #Q8QGGQT-GX8G08Q8-GNQGJ8-MHHGN#PCB板焊接工艺(通用标准)1.P CB板焊接的工艺流程1.1PCB板焊接工艺流程介绍PCB板焊接过程中需手工插件、手工焊接、修理和检验。
1.2PCB板焊接的工艺流程按清单归类元器件—插件—焊接—剪脚—检查—修整。
2.P CB板焊接的工艺要求2.1元器件加工处理的工艺要求2.1.1元器件在插装之前,必须对元器件的可焊接性进行处理,若可焊性差的要先对元器件引脚镀锡。
2.1.2元器件引脚整形后,其引脚间距要求与PCB板对应的焊盘孔间距一致。
2.1.3元器件引脚加工的形状应有利于元器件焊接时的散热和焊接后的机械强度。
2.2元器件在PCB板插装的工艺要求2.2.1元器件在PCB板插装的顺序是先低后高,先小后大,先轻后重,先易后难,先一般元器件后特殊元器件,且上道工序安装后不能影响下道工序的安装。
2.2.2元器件插装后,其标志应向着易于认读的方向,并尽可能从左到右的顺序读出。
2.2.3有极性的元器件极性应严格按照图纸上的要求安装,不能错装。
2.2.4元器件在PCB板上的插装应分布均匀,排列整齐美观,不允许斜排、立体交叉和重叠排列;不允许一边高,一边低;也不允许引脚一边长,一边短。
2.3PCB板焊点的工艺要求2.3.1焊点的机械强度要足够2.3.2焊接可靠,保证导电性能2.3.3焊点表面要光滑、清洁3.P CB板焊接过程的静电防护3.1静电防护原理3.1.1对可能产生静电的地方要防止静电积累,采取措施使之控制在安全范围内。
3.1.2对已经存在的静电积累应迅速消除掉,即时释放。
3.2静电防护方法3.2.1泄漏与接地。
对可能产生或已经产生静电的部位进行接地,提供静电释放通道。
采用埋地线的方法建立“独立”地线。
3.2.2非导体带静电的消除:用离子风机产生正、负离子,可以中和静电源的静电。
4.电子元器件的插装电子元器件插装要求做到整齐、美观、稳固。
同时应方便焊接和有利于元器件焊接时的散热。
4.1元器件分类按电路图或清单将电阻、电容、二极管、三极管,变压器,插排线、座,导线,紧固件等归类。
4.2元器件引脚成形4.2.1元器件整形的基本要求●所有元器件引脚均不得从根部弯曲,一般应留1.5mm以上。
●要尽量将有字符的元器件面置于容易观察的位置。
4.2.2元器件的引脚成形手工加工的元器件整形,弯引脚可以借助镊子或小螺丝刀对引脚整形。
4.3插件顺序手工插装元器件,应该满足工艺要求。
插装时不要用手直接碰元器件引脚和印制板上铜箔。
4.4元器件插装的方式二极管、电容器、电阻器等元器件均是俯卧式安装在印刷PCB板上的。
5.焊接主要工具手工焊接是每一个电子装配工必须掌握的技术,正确选用焊料和焊剂,根据实际情况选择焊接工具,是保证焊接质量的必备条件。
5.1焊料与焊剂5.1.1焊料能熔合两种或两种以上的金属,使之成为一个整体的易熔金属或合金都叫焊料。
常用的锡铅焊料中,锡占%,铅占%。
这种配比的焊锡熔点和凝固点都是183℃,可以由液态直接冷却为固态,不经过半液态,焊点可迅速凝固,缩短焊接时间,减少虚焊,该点温度称为共晶点,该成分配比的焊锡称为共晶焊锡。
共晶焊锡具有低熔点,熔点与凝固点一致,流动性好,表面张力小,润湿性好,机械强度高,焊点能承受较大的拉力和剪力,导电性能好的特点。
5.1.2助焊剂助焊剂是一种焊接辅助材料,其作用如下:●去除氧化膜。
●防止氧化。
●减小表面张力。
●使焊点美观。
常用的助焊剂有松香、松香酒精助焊剂、焊膏、氯化锌助焊剂、氯化铵助焊剂等。
焊接中常采用中心夹有松香助焊剂、含锡量为61%的39 锡铅焊锡丝,也称为松香焊锡丝5.2焊接工具的选用5.2.1普通电烙铁普通电烙铁只适合焊接要求不高的场合使用。
如焊接导线、连接线等。
恒温电烙铁的重要特点是有一个恒温控制装置,使得焊接温度稳定,用来焊接较精细的PCB板。
5.2.2吸锡器吸锡器实际是一个小型手动空气泵,压下吸锡器的压杆,就排出了吸锡器腔内的空气;释放吸锡器压杆的锁钮,弹簧推动压杆迅速回到原位,在吸锡器腔内形成空气的负压力,就能够把熔融的焊料吸走。
5.2.3热风枪热风枪又称贴片电子元器件拆焊台。
它专门用于表面贴片安装电子元器件(特别是多引脚的SMD集成电路)的焊接和拆卸。
5.2.4烙铁头当焊接焊盘较大的可选用截面式烙铁头。
如图中—1:当焊接焊盘较小的可选用尖嘴式烙铁头。
如图中—2:当焊接多脚贴片IC时可以选用刀型烙铁头。
如图中—3:当焊接元器件高低变化较大的电路时,可以使用弯型电烙铁头。
6.手工焊接的流程和方法6.1手工焊接的条件●被焊件必须具备可焊性。
●被焊金属表面应保持清洁。
●使用合适的助焊剂。
●具有适当的焊接温度。
●具有合适的焊接时间6.2手工焊接的方法6.2.1电烙铁与焊锡丝的握法手工焊接握电烙铁的方法有反握、正握及握笔式三种下图是两种焊锡丝的拿法6.2.2手工焊接的步骤●准备焊接。
清洁焊接部位的积尘及污渍、元器件的插装、导线与接线端钩连,为焊接做好前期的预备工作。
●加热焊接。
将沾有少许焊锡的电烙铁头接触被焊元器件约几秒钟。
若是要拆下PCB板上的元器件,则待烙铁头加热后,用手或镊子轻轻拉动元器件,看是否可以取下。
●清理焊接面。
若所焊部位焊锡过多,可将烙铁头上的焊锡甩掉(注意不要烫伤皮肤,也不要甩到PCB板上),然后用烙铁头“沾”些焊锡出来。
若焊点焊锡过少、不圆滑时,可以用电烙铁头“蘸”些焊锡对焊点进行补焊。
●检查焊点。
看焊点是否圆润、光亮、牢固,是否有与周围元器件连焊的现象。
6.2.3手工焊接的方法●加热焊件。
恒温烙铁温度一般控制在280至360℃之间,焊接时间控制在4秒以内。
部分原件的特殊焊接要求:焊接时烙铁头与PCB板成45°角,电烙铁头顶住焊盘和元器件引脚然后给元器件引脚和焊盘均匀预热。
●移入焊锡丝。
焊锡丝从元器件脚和烙铁接触面处引入,焊锡丝应靠在元器件脚与烙铁头之间。
加热焊件移入焊锡●移开焊锡。
当焊锡丝熔化(要掌握进锡速度)焊锡散满整个焊盘时,即可以450角方向拿开焊锡丝。
●移开电烙铁。
焊锡丝拿开后,烙铁继续放在焊盘上持续1~2秒,当焊锡只有轻微烟雾冒出时,即可拿开烙铁,拿开烙铁时,不要过于迅速或用力往上挑,以免溅落锡珠、锡点、或使焊锡点拉尖等,同时要保证被焊元器件在焊锡凝固之前不要移动或受到震动,否则极易造成焊点结构疏松、虚焊等现象。
移开焊锡移开电烙铁6.3导线和接线端子的焊接6.3.1常用连接导线●单股导线。
●多股导线。
●屏蔽线。
6.3.2导线焊前处理●剥绝缘层导线焊接前要除去末端绝缘层。
拨出绝缘层可用普通工具或专用工具。
用剥线钳或普通偏口钳剥线时要注意对单股线不应伤及导线,多股线及屏蔽线不断线,否则将影响接头质量。
对多股线剥除绝缘层时注意将线芯拧成螺旋状,一般采用边拽边拧的方式。
●预焊预焊是导线焊接的关键步骤。
导线的预焊又称为挂锡,但注意导线挂锡时要边上锡边旋转,旋转方向与拧合方向一致,多股导线挂锡要注意“烛心效应”,即焊锡浸入绝缘层内,造成软线变硬,容易导致接头故障。
6.3.3导线和接线端子的焊接●绕焊绕焊把经过上锡的导线端头在接线端子上缠一圈,用钳子拉紧缠牢后进行焊接,绝缘层不要接触端子,导线一定要留1~3mm为宜。
●钩焊钩焊是将导线端子弯成钩形,钩在接线端子上并用钳子夹紧后施焊。
●搭焊搭焊把经过镀锡的导线搭到接线端子上施焊。
绕焊钩焊搭焊7.P CB板上的焊接7.1PCB板焊接的注意事项7.1.1电烙铁一般应选内热式20~35W或调温式,烙铁的温度不超过400℃的为宜。
烙铁头形状应根据PCB板焊盘大小采用截面式或尖嘴式,目前PCB板发展趋势是小型密集化,因此一般常用小型尖嘴式烙铁头。
7.1.2加热时应尽量使烙铁头同时接触印制板上铜箔和元器件引脚,对较大的焊盘(直径大于5mm)焊接时可移动烙铁,即烙铁绕焊盘转动,以免长时间停留一点导致局部过热。
7.1.3金属化孔的焊接。
焊接时不仅要让焊料润湿焊盘,而且孔内也要润湿填充。
因此金属化孔加热时间应长于单面板,7.1.4焊接时不要用烙铁头摩擦焊盘的方法增强焊料润湿性能,而要靠表面清理和预焊。
7.2PCB板的焊接工艺7.2.1焊前准备按照元器件清单检查元器件型号、规格及数量是否符合要求。
焊接人员带防静电手腕,确认恒温烙铁接地。
7.2.2装焊顺序元器件的装焊顺序依次是电阻器、电容器、二极管、三极管、集成电路、大功率管,其它元器件是先小后大。
7.2.3对元器件焊接的要求●电阻器的焊接。
按元器件清单将电阻器准确地装入规定位置,并要求标记向上,字向一致。
装完一种规格再装另一种规格,尽量使电阻器的高低一致。
焊接后将露在PCB板表面上多余的引脚齐根剪去。
●电容器的焊接。
将电容器按元器件清单装入规定位置,并注意有极性的电容器其“+”与“-”极不能接错。
电容器上的标记方向要易看得见。
先装玻璃釉电容器、金属膜电容器、瓷介电容器,最后装电解电容器。
●二极管的焊接。
正确辨认正负极后按要求装入规定位置,型号及标记要易看得见。
焊接立式二极管时,对最短的引脚焊接时,时间不要超过2秒钟。
●三极管的焊接。
按要求将e、b、c三根引脚装入规定位置。
焊接时间应尽可能的短些,焊接时用镊子夹住引脚,以帮助散热。
焊接大功率三极管时,若需要加装散热片,应将接触面平整、光滑后再紧固。
●集成电路的焊接。
将集成电路插装在线路板上,按元器件清单要求,检查集成电路的型号、引脚位置是否符合要求。
焊接时先焊集成电路边沿的二只引脚,以使其定位,然后再从左到右或从上至下进行逐个焊接。
焊接时,烙铁一次沾取锡量为焊接2~3只引脚的量,烙铁头先接触印制电路的铜箔,待焊锡进入集成电路引脚底部时,烙铁头再接触引脚,接触时间以不超过3秒钟为宜,而且要使焊锡均匀包住引脚。
焊接完毕后要查一下,是否有漏焊、碰焊、虚焊之处,并清理焊点处的焊料。
7.3焊接质量的分析及拆焊7.3.1焊接的质量分析构成焊点虚焊主要有下列几种原因:●被焊件引脚受氧化;●被焊件引脚表面有污垢;●焊锡的质量差;●焊接质量不过关,焊接时焊锡用量太少;●电烙铁温度太低或太高,焊接时间过长或太短;●焊接时焊锡未凝固前焊件抖动。
7.3.2手工焊接质量分析手工焊接常见的不良现象7.3.3拆焊工具在拆卸过程中,主要用的工具有:电烙铁、吸锡器、镊子等。
7.3.4拆卸方法●引脚较少的元器件拆法:一手拿着电烙铁加热待拆元器件引脚焊点,一手用镊子夹着元器件,待焊点焊锡熔化时,用夹子将元器件轻轻往外拉。
●多焊点元器件且引脚较硬的元器件拆法:采用吸锡器逐个将引脚焊锡吸干净后,再用夹子取出元器件。
●双列或四列IC的拆卸用热风枪拆焊,温度控制在3500C,风量控制在3~4格,对着引脚垂直、均匀的来回吹热风,同时用镊子的尖端靠在集成电路的一个角上,待所有引脚焊锡熔化时,用镊子尖轻轻将IC挑起。