机械加工确定加工余量的方法有哪些
机械加工工艺规程的制定 机械制作技术基础复习与测试题

第五章机械加工工艺规程的制定1.生产过程与工艺过程的含义是什么?两者的主要组成部分有哪些?[解]机械的生产过程是指机械从原材料开始直到制成机械产品之间的各个相互联系的劳动过程的总和。
它包括毛坯制造—零件的加工及热处理—机械的装配及检验—油漆及包装过程等直接生产过程.还包括原材料的运输和保管以及设计、工艺装备(刀,夹,量具等)的制造、维修等生产技术准备工作。
工艺过程是生产过程的重要组成部分,包括直接改变工件的形状(铸造,锻造等)、尺寸(机械加工)、位置(装配)和材料性质(热处理)使其成为预期产品的过程。
机械加工的工艺过程一般由工序、安装或工位、工步、走刀等组成。
2.生产纲领的含义是什么?划分生产类型的主要依据有哪些因素?[解]生产纲领即指年产量,它应计入备品和废品的数量。
可按下式计算:N零=N×n×(1+α)(1十β)。
生产类型的划分主要考虑年产量,产品本身的大小和结构的复杂性。
3.经济精度的含义是什么?它在工艺规程设计中起什么作用?[解]经济精度是指在正常的机床、刀具、工人等工作条件下,以合适的工时消耗所能达到的加工精度。
因此,在经济精度的范围内,加工精度和加工成本是互相适应的。
有关资料表格中列出各种加工方法所能达到的经济精度及表面租糙度是拟定零件工艺路线的基础,用以从中选择最合适的加工方法和加工设备。
4.何谓结构工艺性?对机械零件结构工艺性有哪些要求?[解]结构工艺性是指机器和零件的结构是否便于加工,装配和维修。
衡量工艺性的主要依据是能够可靠保证产品质量,且加工劳动量小、生产成本低,材料消耗少。
5.试分析下列加工情况的定位基准:(1)拉齿坯内孔时;(2)珩磨连杆大头孔时;(3)无心磨削活塞销外圆时;(4)磨削床身导轨面时;(5)用浮动镗刀块精镗内孔时;(6)超精加工主轴轴颈时;(7)箱体零件攻螺纹时;(8)用与主轴浮动连接的铰刀铰孔时。
[解]以上都是自为基准的加工例子,即以加工面本身作为定位基准。
加工余量的确定.

图3
由图可看出: 公称加工余量 = 前工序尺寸 - 本工序尺寸 最小加工余量=前工序尺寸的最小值 - 本工序尺寸的最大值 最大加工余量=前工序尺寸的最大值 - 本工序尺寸的最小值 工序加工余量的变动范围(最大加工余量与最小加工余量之差)= 前工序工序尺寸公差+ 本工序的工序尺寸公差
(二)总加工余量:总加工余量是指零件从毛坯变为成品的整个加工过 程中从某一表面所切除金属层的总厚度,也即零件毛坯尺寸与零件图 上设计尺寸之差。总加工余量等于各工序加工余量之和,即
z
zi
总
= zi
i =1
n
式中 n–––某一表面的工序(或工步)数目。
--第i道工序加工余量
图4
二、影响加工余量的因素
(一)前工序的工序尺寸公差(Ta)。
(二)前工序形成的表面粗糙度和表面缺陷层深度(Ra+Da)。
(三)前工序形成的形状误差和位置误差(△x、△w)。
(四)本工序的装夹误差(εb)。
三、确定加工余量的方法
(一)查表修正法 (目前应用最广)
(二)经验估计法 (只适用于单件、小批生产)
(三)分析计算法 (目前应用较少)
余量为单边余量
图1
2、旋转表面:
对于轴:Z=da-db 对于孔:Z=db-da
余量为双边余量
图2
• 工序余量和工序尺寸及其公差的 计算公式: (轴) • Z=Zmin+Ta • Zmax=Z+Tb= Zmin+Ta +Tb • 式中 Zmin——最小工序余量 Zmax——最大工序余量 Ta——上工序尺寸的公差 Tb——本工序尺寸的公差
加工的概念
加工余量:在机械加工过程中,从加工表面切去的金属层厚度。
机械制造工艺学习题及答案填空选择

《机械制造工艺学》习题及答案一填充题1 机械制造工艺学的研究对象主要是机械加工中的三大问题即,,。
2 机械加工工艺系统包括,,,等四个方面。
3 工艺过程划分加工阶段的原因是:,,,。
4 在机械制造中,通常将生产方式划分为、、三种类型。
5 确定毛坯加工余量的方法有三种即、、。
大批量生产用。
6 根据作用的不同,基准通常可分为和两大类,定位基准属于。
7 为了保证加工质量,安排机加工顺序的原则是、、、。
8 选择定位粗基准要考虑(1)使各加工面都有一定的和比较均匀的;(2)保证加工面与非加工面的。
9 零件的加工精度包括三方面的内容即、、。
10 零件表层的机械物理性质包括、、。
11 刀具磨损属于误差,可以通过计算后输入来补偿。
12 零件的表面质量包括、、、。
13 工艺系统的振动分为两大类即与,其中振幅随切削用量而变的是。
14 切削加工后,引起表面残余应力的主要原因有、、。
15 精密机床加工精度零件为了减少热变形,加工前应具备两条:、。
15 弯曲的轴进行冷校直后,原来凸出处会产生应力,原来凹下处产生应力。
16 磨削长薄片状工件时若在长度方向两端顶住,在热影响下工件发生的变形,冷后具有的形状误差。
17 解释自激振动的原理主要有两条、。
18 在普通车床上用两顶尖装夹长轴外圆,若机床刚度较低,则工件产生的形状误差;若工件刚度较低,则工件产生的误差。
19 普通车床上对加工精度影响较大的导轨误差是及。
20 切削加工中,若同时用几把刀具加工零件的几个表面则称这种工步为,若一把刀具同时加工几个表面则称这种刀具为。
21 十大原始误差中、、、属于动误差。
22 主轴轴承外环滚道有形状误差则对类机床的加工精度影响较大;内环滚道有形状误差则对类机床的加工精度影响较大。
25 机械加工过程所产生的加工误差,根据性质可分为两大类与。
机床的制造误差属于,刀具尺寸磨损属于,工件材料硬度变化导致的误差为。
26 车床主轴轴向窜动使被加工零件端面产误差,加工螺纹时将造成工件误差。
机械制造工艺学复习题
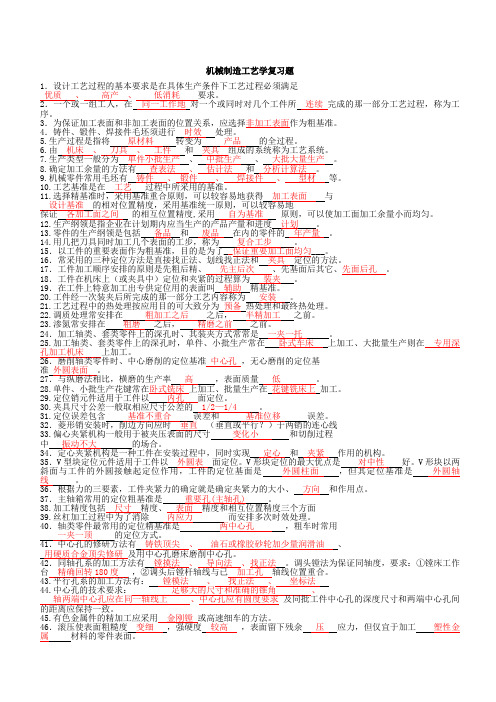
机械制造工艺学复习题1.设计工艺过程的基本要求是在具体生产条件下工艺过程必须满足优质、高产、低消耗要求。
2.一个或一组工人,在同一工作地对一个或同时对几个工件所连续完成的那一部分工艺过程,称为工序。
3.为保证加工表面和非加工表面的位置关系,应选择非加工表面作为粗基准。
4.铸件、锻件、焊接件毛坯须进行时效处理。
5.生产过程是指将原材料转变为产品的全过程。
6.由机床、刀具、工件和夹具组成的系统称为工艺系统。
7.生产类型一般分为单件小批生产、中批生产、大批大量生产。
8.确定加工余量的方法有查表法、估计法和分析计算法。
9.机械零件常用毛坯有铸件、锻件、焊接件、型材等。
10.工艺基准是在工艺过程中所采用的基准。
11.选择精基准时,采用基准重合原则,可以较容易地获得加工表面与设计基准的相对位置精度,采用基准统一原则,可以较容易地保证各加工面之间的相互位置精度,采用自为基准原则,可以使加工面加工余量小而均匀。
12.生产纲领是指企业在计划期内应当生产的产品产量和进度计划。
13.零件的生产纲领是包括备品和废品在内的零件的年产量。
14.用几把刀具同时加工几个表面的工步,称为复合工步。
15.以工件的重要表面作为粗基准,目的是为了__保证重要加工面均匀___。
16.常采用的三种定位方法是直接找正法、划线找正法和夹具定位的方法。
17.工件加工顺序安排的原则是先粗后精、先主后次、先基面后其它、先面后孔。
18.工件在机床上(或夹具中)定位和夹紧的过程算为装夹。
19.在工件上特意加工出专供定位用的表面叫辅助精基准。
20.工件经一次装夹后所完成的那一部分工艺内容称为安装。
21.工艺过程中的热处理按应用目的可大致分为预备热处理和最终热处理。
22.调质处理常安排在粗加工之后之后,半精加工之前。
23.渗氮常安排在粗磨之后,精磨之前之前。
24.加工轴类、套类零件上的深孔时、其装夹方式常常是一夹一托。
25.加工轴类、套类零件上的深孔时,单件、小批生产常在卧式车床上加工、大批量生产则在专用深孔加工机床上加工。
机械加工余量

机械加工余量机械加工余量,通常指零件在加工过程中留下的一定尺寸或形状偏差,它是为了确保零件在加工完成后符合设计要求,以便进行后续的装配、检测,防止零件因加工尺寸不足或过大而无法使用。
机械加工余量是一个重要的概念,对于机械加工工艺的控制和零部件设计起着十分关键的作用。
具体而言,机械加工余量有以下几个方面:1.设计时的余量在机械设计时,就要为加工余量留出一定的设计空间。
这主要包括对零件的几何形状、加工工艺、加工设备等进行考虑。
通常情况下,对于普通的零件,其形状偏差应控制在0.1mm以内,对于精密零件则要在0.01mm以内。
2.加工技术中的余量加工技术中的余量主要指在机床上进行切削或磨削过程中,由于刀具磨损、机床刚度等因素的影响,所导致的零件加工尺寸与设计尺寸的偏差。
在实际操作中,加工技术中的余量可以通过调整刀具切削角度或者加工速度等措施来进行控制。
3.热变形对加工余量的影响在加工加热敏感的金属材料时,由于加热时材料发生热膨胀,会导致加工余量发生偏差。
这时,加工人员可以通过调整加工参数、减少加热时间、加强冷却等方法来调整加工余量。
机械加工余量的控制非常重要,一定程度上,它也是衡量机械加工技术水平的重要标准。
而在实际应用过程中,如何掌握机械加工余量的大小和控制方法,影响着机械零件的质量和生产效率。
以下是一些有关机械加工余量控制的方法:1.合理选择切削工艺参数在进行机械加工时,加工人员应该合理选择切削工艺参数,包括切削速度、进给量、切削深度等方面,以达到减少加工余量的目的。
2.优化刀具设计优化刀具设计也是减小机械加工余量的重要方面。
合理的切削角度可以减少切削力和变形,从而控制加工余量。
此外,刀具的刃磨加工精度也需要达到精度级别,从而减小加工余量。
3.控制机床几何精度机床几何精度是影响加工余量的重要因素之一。
因为机床精度的影响,加工出来的零件在尺寸、直线度、平行度、垂直度等方面都会受到不同程度的影响,进而导致加工余量的产生。
机械加工工序间余量

3.2机械加工工序间余量本章规定的常见工序间加工留量作为本公司编制机械加工工序及有关单位确定加工余量的依据,如有特殊情况可由工艺部门另作规定。
3.2.1切料头时留芯部安全尺寸如图3.2-1所示,当工件材料σs=400~450MPa时,切料头留芯部安全尺寸d按表3.2-1选取。
表3.2-1 中数据用公式d3≈5Q l/σs计算,式中的σs材料屈服极限。
如为其它材料时,应根据其σs大小将安全尺寸d应乘上修正系数K,K值按表3.2-2选取。
表3.2-1 mm注:①、切料头安全尺寸d应按h13级精度加工。
②、切料头当接近安全尺寸时严禁啃刀。
③、切料头前床面上必须垫适当数量的枕木,在架中心架或托辊切断时,直径可以适当缩小。
表3.2-23.2.2 各类锯片及铣刀切口宽度及切割规格各类锯片及铣刀宽度及切割规格见表3.2-3。
表3.2-3 mm注:圆锯能切割方料的最大尺寸为圆料的70%。
3.2.3 车床切断刀及插床切口刀的切口宽度及切割深度车床切断刀及插床切口刀的切口宽度及切割深度见表3.2-4。
表3.2-4 mm注:车床、插床的刀具宽度可以适当磨小。
如果设计专用切断刀时宽度可以适当减少。
3.2.4箱体、架体零件粗加工后人工时效余量箱体、架体零件粗加工后人工时效余量见表3.2-5 。
表3.2-5 mm注:①、适用于铸铁件粗加工后人工时效及粗精加工分开如床身、立柱、工作台、箱体等,不适用于容易变形的薄板。
②、自然时效余量为表中数值的0.5~0.6倍。
③、铸钢件可按表中数值增加1~2mm。
3.2.5 平键修配余量平键修配余量见表3.2-6。
表3.2-6 mm注:①、间隙配合的导向键及切向键不留修配余量。
②、斜健的两侧不留修配余量,斜面上一般情况设计时已留有0.3~0.5mm的修配量,如图纸上未留量时,工艺上应留量。
3.2.6 孔的钻、扩、铰余量孔的钻、扩、铰余量见表3.2-7.表3.2-7 mm注:①、大于Φ30mm的孔,可在二次走刀中钻出,先用较小钻头预钻孔。
机械加工余量选择方法

机械加工余量选择方法1.基本余量法基本余量法是机械加工中最常用的一种方法。
根据经验和相关的机械加工标准,确定不同材料或零件类型应有的基本余量值。
例如,在车削加工中,对外圆进行车削时,可选择的基本余量为0.5-1.5mm;而对内圆进行车削时,可选择的基本余量为0.1-0.3mm。
根据实际情况,合理选择基本余量值,以确保零件尺寸的精度和质量。
2.递减余量法递减余量法是根据机械加工过程中的实际情况,逐步减小加工余量的方法。
根据零件尺寸的精度要求和加工工艺的特点,通过试验和实践,逐渐调整和减小加工余量,以满足零件的尺寸要求。
这种方法在一些对尺寸精度要求较高的零件加工中比较常用,可以尽量减小加工余量,提高加工精度。
3.检测修正法检测修正法是一种基于实际测量结果的余量选择方法。
在零件加工结束后,通过测量零件的尺寸,与设计尺寸进行比较。
根据实际测量结果,修正设计尺寸和加工余量,以满足零件尺寸要求。
这种方法相对较为灵活,可以根据实际情况进行调整和修正,适用于对尺寸要求较为严格的零件加工。
4.确定余量法确定余量法是通过实验和计算,根据工艺参数和材料性质,确定加工余量的具体数值。
根据材料的热膨胀系数、强度和硬度等特性,结合机械加工过程中材料的变形和切削刃的磨损等因素,采用数学模型和计算方法,确定合适的加工余量。
这种方法相对较为精细和科学,适用于复杂零件和高精度加工。
在实际机械加工中,选择合适的机械加工余量方法,对于确保零件尺寸的精度和质量至关重要。
工程师和技术人员应根据具体的加工要求、材料特性和加工工艺,合理选择和调整机械加工余量,以获得满足要求的加工结果。
同时,还需要结合实际情况,不断总结和改进机械加工余量的选择方法,提高加工效率和质量。
加工余量与工序尺寸的确定和基准--2011
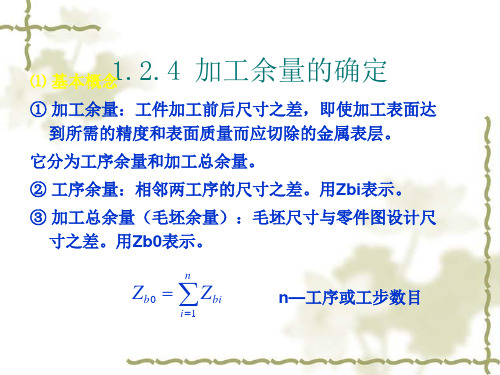
③ 尺寸链的分类 a) 按应用场合来分 工艺尺寸链:全部组成环为同一零件的设 计尺寸所形成的尺寸链,如图2。 特点:所有尺寸都在一个零件上 装配尺寸链:全部组成环为不同零件的工 艺尺寸所形成的尺寸链,如图1。 特点:每一个尺寸都分布在不同的零件上
b) 按各环所处的空间位置来分 直线尺寸链:尺寸链中各环位于同一平面内 且相互平行,最为常规最基本的尺寸链。 平面尺寸链:尺寸链中各环位于同一平面或 几个相互平行平面内,但某些组成环不平行 于封闭环的尺寸链。 空间尺寸链:尺寸链中各环不在同一平面且 互不平行。
极限尺寸的计算:
A0max Az max Aj min
A0min Az min Aj max
⑵ 工序尺寸及其公差的确定 ① 工序基准与设计基准重合,即对同一表面进行多
次加工
这种工序尺寸计算较简单,只需根据各工序的加 工余量就可以算出各工序的基本尺寸。其计算顺 序是由最后一道工序开始逐步向前推算。 例:加工某一个钢制零件上的一个孔,其设计尺 0 寸为 72.50.03 mm,表面粗糙度为Ra0.4。现经过 粗镗、半精镗、精镗、粗磨和精磨五次加工,计 算各次加工的工序尺寸及其公差。
尺寸链中在装配过程或加工过程最后形成 的一环。
c) 组成环:加工或装配时直接影响封闭环 精度的各原始尺寸。
尺寸链中对封闭环有影响的全部环。
增环:尺寸链中的组成环,由于该环的变 动引起封闭环同向变动。 减环:尺寸链中的组成环,由于该环的变 动引起封闭环反向变动。
d) 尺寸链的两个主要功能 公差分配(反计算):已知封闭环基本尺寸 及公差,组成环基本尺寸,求解组成环的公 差。 公差控制(正计算):已知组成环基本尺寸 及公差,核算封闭环尺寸及公差。
- 1、下载文档前请自行甄别文档内容的完整性,平台不提供额外的编辑、内容补充、找答案等附加服务。
- 2、"仅部分预览"的文档,不可在线预览部分如存在完整性等问题,可反馈申请退款(可完整预览的文档不适用该条件!)。
- 3、如文档侵犯您的权益,请联系客服反馈,我们会尽快为您处理(人工客服工作时间:9:00-18:30)。
精密零件加工确定加工余量的方法有哪些
精密零件加工在实际工作中,确定加工余量的方法有哪些?下面小编来为您讲解:
1、经验估计法。
根据工艺人员本身积累的经验确定加工余量。
一般为了防止余量过小而产生废品,所估计的余量总是偏大。
常用于单件、小批量生产。
2、查表法。
根据有关手册提供的加工余量数据,再结合本厂生产实际情况加以修正后确定加工余量。
这是各工厂广泛的,采用的方法。
3、分析计算法。
根据理论公式和一定的试验资料,对影响零件加工余量的各因素进行分析、计算来确定加工余量。
这种方法较合理,但需要全面可靠的试验资料,计算也较复杂。
一般只在材料十分贵重或少数大批、大量生产的工厂中采用。