CrMo钢冶炼工艺操作要点
钢铁行业冶炼工艺技术手册
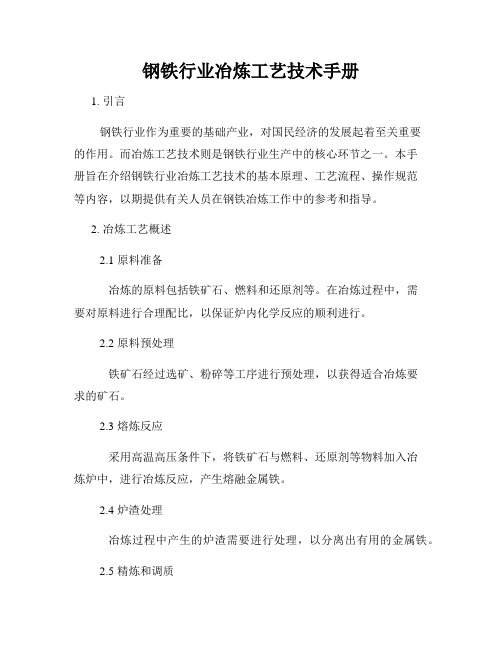
钢铁行业冶炼工艺技术手册1. 引言钢铁行业作为重要的基础产业,对国民经济的发展起着至关重要的作用。
而冶炼工艺技术则是钢铁行业生产中的核心环节之一。
本手册旨在介绍钢铁行业冶炼工艺技术的基本原理、工艺流程、操作规范等内容,以期提供有关人员在钢铁冶炼工作中的参考和指导。
2. 冶炼工艺概述2.1 原料准备冶炼的原料包括铁矿石、燃料和还原剂等。
在冶炼过程中,需要对原料进行合理配比,以保证炉内化学反应的顺利进行。
2.2 原料预处理铁矿石经过选矿、粉碎等工序进行预处理,以获得适合冶炼要求的矿石。
2.3 熔炼反应采用高温高压条件下,将铁矿石与燃料、还原剂等物料加入冶炼炉中,进行冶炼反应,产生熔融金属铁。
2.4 炉渣处理冶炼过程中产生的炉渣需要进行处理,以分离出有用的金属铁。
2.5 精炼和调质对熔融的金属铁进行精炼和调质处理,以获得所需的钢铁产品。
2.6 后处理对冶炼出的钢铁产品进行表面处理、降温、检验和包装等工序,最终得到成品钢铁。
3. 冶炼工艺技术的基本原理3.1 还原反应原理冶炼过程中,通过加入还原剂实现金属铁从矿石中的还原,还原反应是冶炼工艺的关键环节。
3.2 熔融反应原理在高温条件下,铁矿石与燃料、还原剂等物料的熔融反应,使金属铁和炉渣分离。
3.3 精炼和调质原理通过加入适量的合金元素、控制温度和冷却速率等手段,实现对金属铁成分和性能的调控和改善。
4. 冶炼工艺技术的工艺流程4.1 原料准备4.1.1 确定原料类型和比例4.1.2 对原料进行粉碎和混合4.2 熔炼反应4.2.1 确定熔炼炉型和操作参数4.2.2 加入矿石、燃料和还原剂4.3 炉渣处理4.3.1 确定炉渣处理方法和设备4.3.2 对炉渣进行分离、处理和回收 4.4 精炼和调质4.4.1 确定精炼方法和设备4.4.2 控制合金元素的加入和温度 4.5 后处理4.5.1 对钢铁表面进行处理4.5.2 进行冷却、检验和包装5. 冶炼工艺技术操作规范5.1 安全操作5.1.1 遵守安全操作规程5.1.2 使用个人防护装备5.2 设备操作5.2.1 准确操作冶炼设备5.2.2 定期保养和维护设备5.3 原料配料5.3.1 严格按照配比要求进行原料配料5.3.2 预防原料混乱和误配5.4 控制参数5.4.1 监测和调节冶炼过程中的温度、压力等参数5.4.2 根据需要进行及时的参数调整6. 结论钢铁行业冶炼工艺技术手册详细介绍了钢铁冶炼过程中的基本原理、工艺流程和操作规范。
钢铁行业冶炼工艺安全操作规程
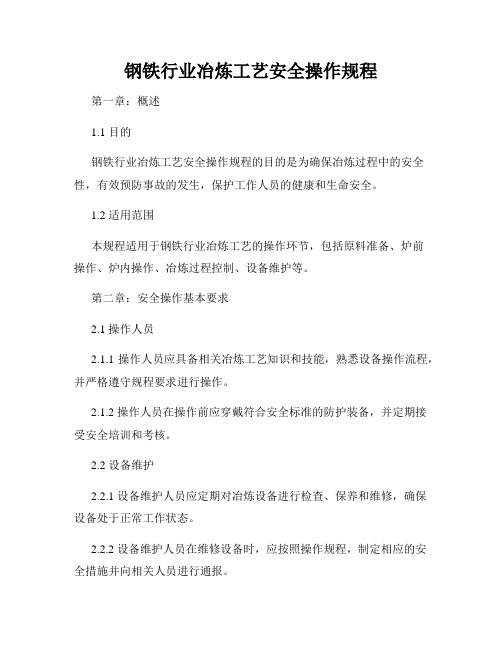
钢铁行业冶炼工艺安全操作规程第一章:概述1.1 目的钢铁行业冶炼工艺安全操作规程的目的是为确保冶炼过程中的安全性,有效预防事故的发生,保护工作人员的健康和生命安全。
1.2 适用范围本规程适用于钢铁行业冶炼工艺的操作环节,包括原料准备、炉前操作、炉内操作、冶炼过程控制、设备维护等。
第二章:安全操作基本要求2.1 操作人员2.1.1 操作人员应具备相关冶炼工艺知识和技能,熟悉设备操作流程,并严格遵守规程要求进行操作。
2.1.2 操作人员在操作前应穿戴符合安全标准的防护装备,并定期接受安全培训和考核。
2.2 设备维护2.2.1 设备维护人员应定期对冶炼设备进行检查、保养和维修,确保设备处于正常工作状态。
2.2.2 设备维护人员在维修设备时,应按照操作规程,制定相应的安全措施并向相关人员进行通报。
2.3 原料准备2.3.1 原料准备人员应按照冶炼工艺要求,正确选择、加工和存储原料,确保原料质量符合标准。
2.3.2 原料准备人员在操作过程中应注意防火防爆安全,使用防火装置和工具,防止事故的发生。
第三章:冶炼过程安全操作3.1 炉前操作3.1.1 炉前操作人员应在冶炼炉前设置明确的安全警示标志,并按照规程要求使用相应的操作工具。
3.1.2 炉前操作人员应定期对冶炼炉前进行清理和检查,确保炉前环境整洁以及设备的正常运行。
3.2 炉内操作3.2.1 炉内操作人员应在安全通道内进行操作,严禁越过限定区域,确保人身安全。
3.2.2 炉内操作人员应严格遵守操作规程,掌握炉内温度、压力、流量等关键参数,并按照要求进行监控和调整。
3.3 冶炼过程控制3.3.1 冶炼过程控制人员应熟悉冶炼工艺流程,合理控制炉温、炉压等参数,确保冶炼过程的稳定性和安全性。
3.3.2 冶炼过程控制人员应随时关注冶炼设备的运行状况,及时发现并处理异常情况,确保冶炼过程的安全运行。
第四章:事故应急处理4.1 事故预防4.1.1 冶炼过程中的事故预防工作是保障冶炼安全的重要环节,操作人员应严格按照规程要求执行操作,并随时注意事故的可能风险。
炼钢工艺控制点

炼钢主要工艺控制点一、转炉炉后工艺控制点1、脱氧合金化要求:(1)合金加入顺序必须遵循先弱后强的原则。
即硅锰——硅铁——脱氧剂;为了保证合金的有效收得率,在过氧化钢水的处理上可以先加部分硅铁或脱氧剂进行预脱氧,但为了避免钢水翻包,预脱氧剂不能加到包底。
(2)合金加入时间必须遵循在出钢到四分之一开始加入,在钢水出到四分之三时必须加完。
出钢时间必须大于三分钟。
(3)为避免钢水成分不均匀,严禁在出完钢后补加合金。
(4)有条件的钢车可以在加入合金后来回晃动,增加合金的融化速度和均匀性。
(5)合金加入点必须对准钢流加入。
2、出钢挡渣要求:(1)任何钢种必须进行双挡渣操作。
即出钢之前必须检查挡渣塞是否堵好。
(2)出钢到五分之四时必须加入挡渣锥或挡渣球。
(3)出完钢后检查出钢口情况,必须把残渣或堵塞物清理干净,然后堵上挡渣塞。
3、精炼要求:(1)出完钢后必须进行吹氩气(或氮气)操作,有条件的必须在出钢过程中进行。
(2)吹气时间必须大于五分钟,吹气效果以钢水表面微翻波动为准则,为避免钢水二次氧化不允许钢水大翻。
吹气压力0.4-.0.6Mp.(3)吹气前和吹完气后必须进行钢水测温,其温度制度根据不同的钢种和上连铸包次要求执行工艺制度。
(4)同时在吹完气后必须进行取样观察和检验,如果钢水成分和含氧量不合乎要求,必须经行喂丝操作,具体数量根据成分和含氧量而定。
(5)完毕后必须加入钢包覆盖剂,具体数量已覆盖钢包表面为原则。
二、钢包工艺控制点1、必须热包出钢,钢包烘烤温度大于800℃要求。
2、钢包出钢前必须清理干净,不允许有残渣或残钢,特别是水口和透气砖部分。
3、出钢前必须对底吹透气砖进行确认检查是否透气。
4、出钢前必须对引流砂确认检查,要求覆盖碗口且成堆积状。
三、连铸浇注平台工艺控制点1、中间包浇注前工艺检查要求(1)中间包浇注前必须烘烤,烘烤温度必须大于800℃。
(2)中间包浇注前必须检查是否清理干净,特别是水口部位。
钢铁冶炼操作规程

钢铁冶炼操作规程一、引言钢铁冶炼是一项重要的工业生产过程,它涉及到多个环节和操作步骤。
为了确保冶炼工艺的顺利进行,提高冶炼效率和产品质量,制定一套科学合理的操作规程势在必行。
本文将详细介绍钢铁冶炼操作规程的内容和要求。
二、操作规程的目的和基本原则1. 目的钢铁冶炼操作规程的目的是规范冶炼工艺,确保生产过程的安全可靠、高效稳定。
2. 基本原则(1)安全第一:确保员工和设备的安全,防止事故的发生。
(2)科学合理:根据冶炼工艺的特点和要求,设计合理的操作流程。
(3)高效节能:优化操作流程,提高生产效率,降低能源消耗。
(4)产品质量可控:通过严格操作规程的执行,确保产品质量的稳定可靠。
三、冶炼操作规程的具体内容1. 原料准备(1)确保原料质量:对于待冶炼的原料,必须进行质量检验,保证其符合冶炼要求。
(2)合理配比:根据原料特性和要求,确定合理的配比比例,以确保冶炼过程的顺利进行。
2. 熔炼操作(1)预热炉料:在炉料进入冶炼设备之前,需要进行预热,以提高熔化效率。
(2)控制冶炼温度:根据冶炼工艺要求,精确控制冶炼温度,保持在适宜的范围内。
(3)添加熔剂:根据冶炼需要,适量添加熔剂,提高炉渣的流动性。
(4)冶炼时间:根据不同的炉型和工艺要求,确定冶炼时间,以确保冶炼的充分完成。
3. 钢水处理(1)温度控制:确保钢水温度在规定范围内,以满足下一步的工艺要求。
(2)添加合金元素:根据产品质量要求,适量添加合金元素,调整钢水成分。
(3)去除杂质:通过真空处理、脱气等工艺,去除钢水中的气体和杂质。
(4)定温保温:在钢水处理过程中,要进行定温保温,确保钢水质量的稳定。
4. 出钢操作(1)铸钢模具准备:准备好适用的铸钢模具,确保模具干净无损。
(2)浇注方式:根据产品要求选择合适的浇注方式,确保钢水顺利注入模具。
(3)冷却保护:在钢水浇注后,及时进行冷却保护,防止钢水过早冷却引起问题。
(4)钢坯处理:对于冷却后的钢坯进行必要的处理,以满足后续加工工艺要求。
铬铁冶炼生产操作规程
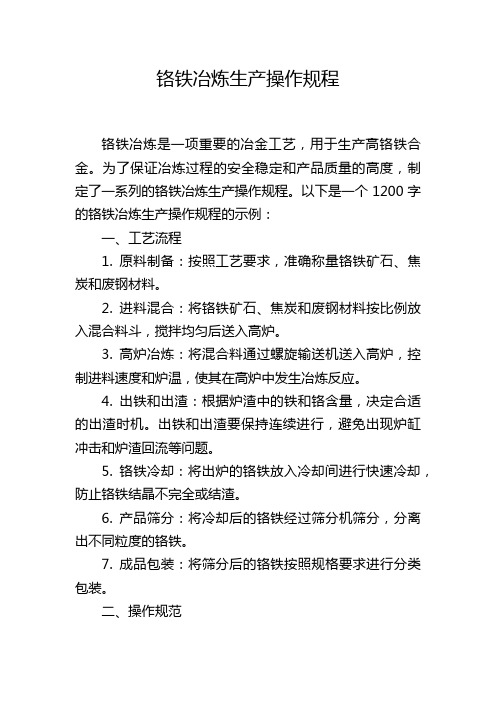
铬铁冶炼生产操作规程铬铁冶炼是一项重要的冶金工艺,用于生产高铬铁合金。
为了保证冶炼过程的安全稳定和产品质量的高度,制定了一系列的铬铁冶炼生产操作规程。
以下是一个1200字的铬铁冶炼生产操作规程的示例:一、工艺流程1. 原料制备:按照工艺要求,准确称量铬铁矿石、焦炭和废钢材料。
2. 进料混合:将铬铁矿石、焦炭和废钢材料按比例放入混合料斗,搅拌均匀后送入高炉。
3. 高炉冶炼:将混合料通过螺旋输送机送入高炉,控制进料速度和炉温,使其在高炉中发生冶炼反应。
4. 出铁和出渣:根据炉渣中的铁和铬含量,决定合适的出渣时机。
出铁和出渣要保持连续进行,避免出现炉缸冲击和炉渣回流等问题。
5. 铬铁冷却:将出炉的铬铁放入冷却间进行快速冷却,防止铬铁结晶不完全或结渣。
6. 产品筛分:将冷却后的铬铁经过筛分机筛分,分离出不同粒度的铬铁。
7. 成品包装:将筛分后的铬铁按照规格要求进行分类包装。
二、操作规范1. 操作人员要经过专业培训并持证上岗,了解铬铁冶炼工艺流程和安全操作规程。
2. 在进行原料制备和进料混合时,操作人员要戴好防护手套、口罩和护目镜,避免直接接触有害物质。
3. 高炉冶炼过程中,要定期对高炉炉温、进料速度和炉内压力进行监控和调整,确保冶炼反应能够顺利进行。
4. 出铁和出渣过程中,操作人员要保持警惕,定期检查出铁口和出渣口是否堵塞,及时处理堵塞问题。
5. 铬铁冷却时,要确保冷却间的通风良好,防止温度过高造成火灾事故。
6. 产品筛分过程中,操作人员应注意筛分机的运行状态,定期清理堵塞物。
7. 成品包装时,要将铬铁包装密封,标注产品规格、批次和生产日期,在包装上加盖“合格”标识。
三、安全措施1. 严格遵守安全操作规程,操作人员必须穿戴好个人防护装备,做好个人防护。
2. 对危险化学品进行合理存放,防止与其它物质混存或接触。
3. 定期检查和维护设备,确保其正常运行,及时处理设备故障和隐患。
4. 加强火灾防范和灭火设备的配置,在生产场所设立灭火器材,并进行定期检测和维护。
12cr1mov加工工艺

12cr1mov加工工艺
12Cr1MoV是一种低合金高强度钢,主要用于高温高压设备和管道,其加工工艺可以包括以下步骤:
1. 材料准备:获取经过质量检验合格的12Cr1MoV钢材,并进行标记和记录。
2. 切割:根据设计要求,使用锯床、剪切机或其他合适的设备对钢材进行切割,得到符合尺寸要求的工件。
3. 热处理:对工件进行热处理,包括退火、正火、淬火等工艺,以改善材料的力学性能和组织结构。
4. 成型加工:根据工程设计要求,使用冲压、锻造、旋压、铣削、钻孔等方法对工件进行成型加工,获得所需的形状和尺寸。
5. 焊接:对需要进行焊接的接头或组件,采用合适的焊接方法(如电弧焊、气焊、电阻焊等)进行焊接连接。
6. 精加工:使用切削工具(如车床、铣床、磨床等)
对工件进行精细加工,以获得更高的尺寸精度和表面光洁度。
7. 表面处理:进行必要的表面处理,包括打磨、抛光、喷涂等,以提高工件的表面质量和防护性能。
8. 检测和质量控制:使用可靠的检测方法,如超声波检测、硬度测试、尺寸测量等,对加工的工件进行质量检查,确保符合设计要求和相关标准。
需要注意的是,12Cr1MoV钢材的加工工艺应遵循相关的国家和行业标准,以确保产品的质量和可靠性。
对于具体的加工要求和工艺参数,建议咨询专业的加工工程师、材料专家或参考相关的标准和技术文件。
钢铁冶炼生产操作指南
钢铁冶炼生产操作指南钢铁冶炼是一个复杂而关键的工艺过程,在现代工业中扮演着重要的角色。
本文旨在给予钢铁冶炼操作人员一个操作指南,以确保生产过程的顺利进行和产品质量的提高。
一、准备工作在开始钢铁冶炼之前,操作人员需要做好充分的准备工作。
首先,检查和准备冶炼炉设备,确保其正常运作并具备良好的工作状态。
其次,检查原料,包括铁矿石、废钢料等,确保其质量符合要求,并妥善储存和处理。
二、原料处理将准备好的原料送入炼钢炉中进行处理。
在处理过程中,操作人员需要掌握适当的加热、冶炼时间和温度控制等参数,以确保原料完全熔化和反应的完成。
此外,还应注意添加适当的辅助材料,如石灰石、焦炭等,以调整炉内化学反应的平衡。
三、炼钢过程炼钢过程是钢铁冶炼中的关键环节,操作人员需要密切关注炉内的温度、压力、气氛等参数,并及时做出调整。
同时,应掌握炼钢渣的控制技术,确保钢液中的杂质得以去除,从而提高产品的质量。
此外,还应注意炼钢过程中可能出现的其他问题,如气体泄漏、设备故障等,并及时采取应对措施,确保生产的连续进行。
四、铸造和调质完成炼钢过程后,钢液需要进行铸造和调质处理。
操作人员需要掌握适当的铸造技术,确保钢水顺利流入模具中,并形成所需的铸件。
同时,还应注意铸件的冷却和收缩过程,以防止出现裂纹和缺陷。
在调质处理中,操作人员需要根据产品的要求,控制加热和冷却速率,以达到所需的材料性能。
五、质量控制钢铁冶炼生产操作中,质量控制是一个至关重要的环节。
操作人员需要频繁进行化验和检测,以确保产品符合要求。
同时,还需要密切关注各种指标的变化趋势,及时调整操作参数,以提高产品的质量稳定性。
此外,还应妥善处理可能出现的质量问题,如杂质含量超标、机械性能不达标等,以减少损失并确保客户满意度。
六、安全环保在钢铁冶炼生产过程中,操作人员需要时刻关注安全和环保要求。
确保个人安全装备的佩戴和使用,严格执行安全操作规程,并参与相应的安全培训。
此外,还需关注环境保护,合理处理废气、废水和固体废弃物,确保对环境的最小影响。
X12CrMo5钢板冶炼方法和熔炼分析
X12CrMo5交货状态:X12CrMo5钢板正火(N)回火(T) 调质(QT)。
X12CrMo5执行标准:欧标EN10028X12CrMo5冶炼方法:采用电炉+炉外精炼+真空脱气方式冶炼,细晶粒镇静钢X12CrMo5钢板尺寸、外形、重量及允许偏差X12CrMo5钢板的尺寸、外形、重量及允许偏差应符合EN10029的规定,厚度允许偏差按EN10029的等级B类偏差。
X12CrMo5用途:X12CrMo5钢板属于欧洲压力容器用钢板,用于制造反应器、换热器、分离器、球罐、油气罐、液化气罐、核能反应堆压力壳、液化石油汽瓶、水轮机蜗壳等。
X12CrMo5化学成分:X12CrMo5化学成分%C Si Mn Cr Ni Mo NbV P S0.10~0.1 5 ≤0.500.30~0.64.00~6.0≤0.30.45~0.65~ ~≤0.020≤0.005X12CrMo5部分现货:耐磨板:WNM360E.WNM400E.WNM450A.WNM500A.WRZ360.WRZ400A. 耐磨钢:WSM718R.WSMP20R..调质高强钢板:WQ690D.S960Q.WH100QD.WQ960E.S960Q.WQ890D.A514GrQ/A517Gr Q/E690/EQ70.A514GrF.TMCP高强钢板:E500.Q500E.S500M.调质钢板:EQ47/E460.EQ63/E620. A/SA533B.EQ51/E500.1E0653.1E0682.1E1839.WNM255A核电钢板:16MnD5/18MnD5/20MnD5.15MnNi.20控Gr.军工钢板:603(30CrMnMoRE)GY4(28Cr2Mo).GY5(26SiMnMo).675(30CrNi3MoV)电渣钢板:Q345E类.Q390类.Q420D-Q460D类.Q235D类.容器板:Q245R(HIC)、Q345R(HIC)、SA516Gr70、15CrMoR、Q420R、09MnNiDR、SA387Gr11、SA387Gr22、13MnNiMoR、14Cr1MoR、12Cr1MoVR A48CPR、16Mo3、P355GH、12Cr2Mo1R、P91合金钢:35CrMo、42CrMo、40Cr、10CrMoAL、22SiMn2、30CrMnSiA。
冶金行业炼钢工艺规程
冶金行业炼钢工艺规程钢材作为现代工业的重要材料之一,在各个领域中都扮演着重要的角色。
而炼钢工艺是钢材生产的核心环节之一,对于确保钢材质量、降低成本和提高效率具有重要的意义。
本文将围绕冶金行业炼钢工艺规程展开论述,旨在提升炼钢工艺的标准化和规范化水平,以推动钢材产业的可持续发展。
1. 前处理工艺在炼钢过程中,前处理工艺起着至关重要的作用,它可以对原料进行筛选、破碎和预处理,以确保后续工艺环节的进行顺利。
前处理工艺规程应包括原料的选择标准、破碎设备的运行参数、预处理工艺流程等内容,并且应根据不同种类的原料和生产需求进行调整和优化。
2. 炼钢工艺炼钢工艺是将原料转化为高品质钢材的关键步骤,其规范化和优化可以提高钢材质量、减少生产成本。
炼钢工艺规程应包括炉型选择和设计、炉料比例、炼钢温度和时间控制、冶炼剂的使用方法等内容,以确保钢材的化学成分和物理性能达到预期要求。
3. 精炼工艺精炼工艺是在炼钢工艺之后进行的一个重要环节,它可以进一步提升钢材的质量和纯度。
精炼工艺规程应包括精炼设备的选型和运行参数、精炼剂的使用方法、工艺流程等内容,以确保钢材中的杂质和非金属夹杂物得到有效去除,从而获得高纯度的钢材。
4. 连铸工艺连铸工艺是将炼钢后的钢水铸造成坯料的重要环节,它直接关系到钢材的成品率和质量。
连铸工艺规程应包括连铸机的选型和运行参数、结晶器的设计和使用、冷却水的供应等内容,并应根据不同的钢种和规格进行适当调整,以确保钢材的凝固过程稳定,获得理想的坯料。
5. 熔炼废料处理工艺在冶金行业中,产生了大量的熔炼废料,如果不进行有效处理,将对环境和资源造成巨大的影响。
熔炼废料处理工艺规程应包括废料的分类和分拣、处理方式的选择和优化、废料处理设备的选型和运行参数等内容,并应遵循环保和资源综合利用的原则,以减少对环境的污染和资源的浪费。
6. 能源管理和安全生产在炼钢工艺中,能源消耗和生产安全是两个非常重要的方面。
能源管理方面,规程应包括能源的使用和消耗监控、能源利用效率的提升、能源节约措施等内容。
冶金炼钢操作规范
冶金炼钢操作规范在冶金行业,炼钢是一个至关重要的工序,其操作规范对钢铁生产质量和安全运行具有重要意义。
本文将从炼钢操作的准备工作、炉料配料、炉膛控制、渣铁处理以及产品质量控制等几个方面探讨冶金炼钢操作规范。
1. 准备工作准备工作是冶金炼钢操作的第一步,它包括铁水准备、炉前装料和检查设备运行等。
首先,确保铁水质量符合标准,避免铁水中含有过量的硫、氧化铁等有害元素。
其次,进行炉前装料时,应按照炼钢配方要求精确称取原料,确保每个炉次的配料准确无误。
最后,检查各项设备是否正常运行,如传感器、仪表等是否灵敏准确,确保可以实时掌握工艺参数。
2. 炉料配料炼钢的炉料配料是影响炼钢工艺和产品质量的重要环节。
在进行炉料配料时,需要根据炉型和炼钢工艺要求,准确计算原料的配比,确保各种原料能够充分反应。
同时,应注意避免炉料中过多的杂质和有害元素,以免对产品质量造成不良影响。
此外,还应合理控制炉料的水分含量,避免过高或过低影响炉内反应进程。
3. 炉膛控制炉膛控制是冶金炼钢操作中的核心环节,对炼钢过程中的温度、氧气强度、气氛等进行精确控制,以保证炼钢工艺的顺利进行。
在炉膛控制中,应根据炼钢工艺要求,合理设置下料速度、吹气量、燃料供应等,确保炉内温度和气氛稳定。
此外,还应进行温度和成分的实时监测,及时调整控制参数,确保炉内反应达到最佳状态。
4. 渣铁处理渣铁处理是炼钢操作中的重要环节,它直接关系到炼钢工艺的顺利进行和钢铁质量的提高。
在进行渣铁处理时,首先要对渣铁进行分类,将不同类型的渣铁适当配比加入炉内。
其次,在渣铁投料过程中,应注意投料均匀,避免炉内渣铁分布不均,影响炉内反应。
最后,渣铁处理后要及时清理和修复炉膛,确保下一炉次的操作不受影响。
5. 产品质量控制产品质量控制是冶金炼钢操作中不可或缺的一环。
为了保证钢铁产品的质量,应对产品进行严格的质量控制。
首先,及时采集样品,进行成分和物理性能的测试,并按照标准规范进行评估。
- 1、下载文档前请自行甄别文档内容的完整性,平台不提供额外的编辑、内容补充、找答案等附加服务。
- 2、"仅部分预览"的文档,不可在线预览部分如存在完整性等问题,可反馈申请退款(可完整预览的文档不适用该条件!)。
- 3、如文档侵犯您的权益,请联系客服反馈,我们会尽快为您处理(人工客服工作时间:9:00-18:30)。
CrMo钢冶炼工艺操作要点
1 技术条件
1.1 技术标准GB/T3077-1999、YB/T054-1994、YB/T5221-1993及JNTG/J等相关技术协议。
1.2 化学成分:钢中化学元素的含量应符合表1、表2和表3的规定。
表1 钢中主要元素的含量范围
注:1、JNTG/J01、JNTG/J34的20CrMoA,JNTG/J16的20CrMoA、35CrMoA ,JNTG/J15
的全部同YB/T054。
2、JNTG/J20、JNTG/J21的20CrMo、35CrMo、42CrMo同GB/T3077。
3、JNTG/J30的20CrMo,JNTG/J34的30CrMoA同GB/T3077。
4、JNTG/J23、JNTG/J2
5、JNTG/J27、JNTG/J29的35CrMo同GB/T3077。
5、JNTG/J24同JNTG/J02。
6、YB/T5221同GB/T3077
1.3控制规格
1.3.1 下列JNTG/J技术条件的CrMo钢协议要求控制的化学成份范围
表2 JNTG/J技术条件CrMo 钢协议要求控制成份范围
表3 钢中残余元素的控制范围
注:B7成品P≤0.015%、[Al]0.015~0.025%、50CrMo4 成品S≤0.015%1.3.2我公司CrMo钢内控规格
1.3.
2.1表2中各技术协议条件的CrMo钢,公司要求内控化学成份范围:
C:42CrMo(B7)0.39~0.41%、其它按表2要求。
Cr:表2中为0.95~1.10%的按1.00~1.05%控制
表2中为0.90~1.10%的按0.95~1.00%控制
Mn、42CrMo(B7)按表2要求控制。
Mo、42CrMo(B7)按0.18%,其它按表2要求的下限+0.01%控制。
1.3.
2.2表1所列各技术条件CrMo钢,公司要求内控化学成份范围
表1中除表2所列JNTG/J技术条件有控制规格的元素按1.3.2.1规定控制外,其它表2未列的技术条件和没有控制规格的化学元素,一律按下述原则控制:
C、规格下限+0.01%~规格上限-0.02%。
Mn、Cr、规格中限-0.05%~规格中限。
Mo、抽油杆、管坯按规格下限+0.01~+0.03%,其它用途的按规格下限+0.02~+0.03%。
Si、0.22~0.26%。
2 工艺操作要点
2.1电炉
2.1.1电炉出钢条件
2.1.1.1 出钢化学成份:
C: 12CrMo、15CrMo C≤0.010%、其它钢种0.10%≤C≤规格下限-合金増碳量。
P:有A、P≤0.012%;无A 、P≤0.015%。
2.1.1.2 出钢温度1640~1660℃。
2.1.2 钢的化学成分调整:
C、12CrMo、15CrMo出钢不调,其它按规格下限-合金増碳量调整。
Mn、Cr按下限调整、Si不计损失按0.25%调整。
钢芯铝、硅钙钡铝的用量按下表规定执行。
表4 电炉出钢予脱氧钢芯铝、硅钙钡铝的用量
钢芯铝和硅钙钡铝在出钢10~15t后,随钢流加入钢包,硅锰、高锰、铬铁随渣料加入钢包。
为防止12CrMo、15CrMo在LF精练时増碳,应增加渣量.渣料组成:CaO10~12kg/t、
预熔渣3.5~4.5kg/t。
其它钢种为CaO8~10kg/t、预熔渣3.0~4.0kg/t。
2.2 LF炉
2.2.1 钢包到LF工位后送电加热。
12~15CrMo采用加1~2批Al粉(0.3~0.5kg/t)和碳化硅扩散脱氧造白渣、其它钢种采用加1~2批电石和碳化硅扩散脱氧造白渣,渣白后,分批加少量SiC脱氧以保持白渣和炉内还原性气氛。
2.2.2 第一批脱氧剂后,钢渣形成良好,按1m/t喂Al线。
2.2.3 第二个样结果回来后,按控制规格和前述原则调整化学成分:
C按规格或控制规格下限+0.01%;
Si 0.20~0.23%;
Mn、Cr控制规格调整;
Mo42CrMo(B7)按0.18%,按规格+0.02~0.03%或控制规格下限+0.01%控制;
[Al]s按0.010-0.015%、B7按0.015~0.025%、不足补喂Al线。
2.2.4 出钢温度
表5 出钢温度
50CrMo4走VD按130×130方坯规程执行。
-[ Al]s喂CaSi线1~2m/t
2.2.5 喂CaSi线:按△[Al]=[Al]
T
2.2.6 出钢后加覆盖剂,要全部、均匀覆盖渣面。
2.3 连铸
2.3.1 LF出钢后,在连铸平台测温吹Ar,吹Ar强度以不裸露钢水面为准。
吹氩时间≥8~15min。
2.3.2 中包仍采用现低碳低碱度覆盖剂,要及时补加覆盖剂,不得裸露和变红。
2.3.3 液相线温度
表6 液相线温度
2.3.4 大包上台温度
浇次第一炉 T=TL+85±5℃
连浇炉次 T=TL+75±5℃
2.3.5 拉速控制见分钢种拉速表。
2.3.6 配水按表7、表8控制
表7 配水参数Kn
表8 配水参数m
2.3.7电磁搅拌按表9控制
表9 电磁搅拌参数
2.3.8 保护渣
表10 保护渣使用表
2.3.9 铸坯定尺长度按生产计划要求执行。
2.4其它未尽事宜按基本工艺操作规程执行。