吸塑设计及其制造
PVC板吸塑热弯成型工艺的制作流程

本技术公开了一种PVC板吸塑热弯成型工艺,涉及材料吸塑技术领域。
包括将PVC树脂、增塑剂、稳定剂、润滑剂、填充剂和色母放入混练机中均匀搅拌并升温至130℃后冷却至40℃排出得到混合料;将上述所得混合料经挤出机挤出成型,获得硬质片材;根据零部件的吸塑下料尺寸对片材进行裁切、收卷;对裁切好的片材卷料进行吸塑,根据零部件冲孔尺寸及展开尺寸对吸塑后的平面半成品进行冲切切去零部件四周多余的边料;利用加热设备对折弯部位整体进行加热,加热后进行折弯。
本技术在保证原铁质零部件的密封性、保护性功能的前提下,降低了制品整体的制造成本,以达到替代铁质材料的目的。
技术要求1.一种PVC板吸塑热弯成型工艺,其特征在于:包括:(1)、以重量百分比计将PVC树脂50-60%,增塑剂10-15%,稳定剂3-5%,润滑剂5-8%,填充剂10-20%,色母1-2%放入混练机中均匀搅拌并升温至130℃后冷却至40℃排出得到混合料;(2)、将上述所得混合料经挤出机挤出成型,获得硬质片材;(3)、根据零部件的吸塑下料尺寸对片材进行裁切、收卷;(4)、对裁切好的片材卷料进行吸塑,根据零部件冲孔尺寸及展开尺寸对吸塑后的平面半成品进行冲切切去零部件四周多余的边料;(5)、利用加热设备对折弯部位整体进行加热,加热后进行折弯。
2.根据权利要求1所述的一种PVC板吸塑热弯成型工艺,其特征在于,挤出机挤出成型过程中根据需求,通过上下压花滚轮在片材上下两表面辊扎出相应花纹纹路,花纹纹路的深度为0.01-0.05mm;在片材上形成不同深浅的纹路,增加制品的表面强度,减少表面缺陷。
3.根据权利要求2所述的一种PVC板吸塑热弯成型工艺,其特征在于,片材上表面的花纹纹路的深度较其下表面的花纹纹路的深度浅,片材上表面为零部件的内外观面,片材下表面为零部件的内部面;所述片材上表面的花纹纹路深度为0.01-0.03mm,所述片材下表面的花纹纹路深度为0.03-0.05mm。
吸塑防静电标准

吸塑防静电标准一、引言吸塑防静电是一种常见的表面处理技术,用于防止静电的产生和积累。
它在许多行业中广泛应用,如电子、航空航天、医疗器械等。
为了确保吸塑防静电的效果,制定了一系列的标准和规范,本文将介绍吸塑防静电的标准内容及其重要性。
二、吸塑防静电标准的内容1. 材料选择标准吸塑防静电材料的选择非常重要。
标准规定了材料的电阻率范围,一般在10^6~10^9 Ω之间。
材料的电阻率越低,其导电性越好,能更好地消散静电。
此外,标准还对材料的表面电阻进行了要求,一般要求在10^6~10^9 Ω/□之间。
2. 材料表面处理标准标准要求对吸塑材料进行表面处理,以提高其防静电性能。
常见的表面处理方法包括涂覆导电涂层、植入导电纤维等。
标准规定了表面处理材料的种类、厚度和施工工艺等。
3. 产品尺寸和形状标准吸塑防静电产品的尺寸和形状也受到标准的限制。
标准要求产品的尺寸和形状应符合设计要求,并保证产品的机械性能和防静电性能。
4. 防静电性能测试标准标准规定了吸塑防静电产品的防静电性能测试方法和标准。
常见的测试方法包括电阻率测试、表面电阻测试、静电放电测试等。
标准要求测试结果应符合规定的数值范围,以保证产品的稳定性和可靠性。
5. 标识要求标准还对吸塑防静电产品的标识进行了要求。
标准规定了标识的位置、内容和格式等。
标识的目的是提醒使用者产品的防静电性能和相关注意事项,以确保产品的正确使用。
三、吸塑防静电标准的重要性1. 保护电子设备吸塑防静电产品能够有效地消散静电,防止静电对电子设备的损害。
在电子制造业中,静电对电子元器件的损害是一个严重的问题。
吸塑防静电产品的广泛应用,能够保护电子设备的安全运行。
2. 提高工作环境安全性吸塑防静电产品能够防止静电的产生和积累,减少了静电火花对易燃易爆物品的引发风险。
尤其是在化工、石油等行业,吸塑防静电产品的使用对于提高工作环境的安全性至关重要。
3. 保证产品质量吸塑防静电产品的使用可以防止静电对产品的损坏。
吸塑机作业指导书
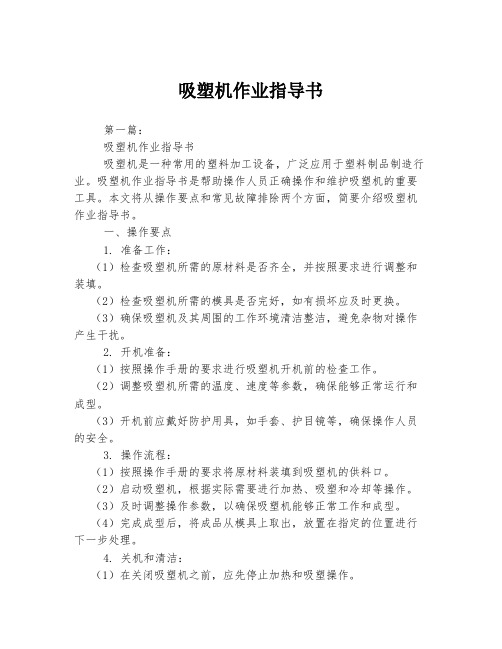
吸塑机作业指导书第一篇:吸塑机作业指导书吸塑机是一种常用的塑料加工设备,广泛应用于塑料制品制造行业。
吸塑机作业指导书是帮助操作人员正确操作和维护吸塑机的重要工具。
本文将从操作要点和常见故障排除两个方面,简要介绍吸塑机作业指导书。
一、操作要点1. 准备工作:(1)检查吸塑机所需的原材料是否齐全,并按照要求进行调整和装填。
(2)检查吸塑机所需的模具是否完好,如有损坏应及时更换。
(3)确保吸塑机及其周围的工作环境清洁整洁,避免杂物对操作产生干扰。
2. 开机准备:(1)按照操作手册的要求进行吸塑机开机前的检查工作。
(2)调整吸塑机所需的温度、速度等参数,确保能够正常运行和成型。
(3)开机前应戴好防护用具,如手套、护目镜等,确保操作人员的安全。
3. 操作流程:(1)按照操作手册的要求将原材料装填到吸塑机的供料口。
(2)启动吸塑机,根据实际需要进行加热、吸塑和冷却等操作。
(3)及时调整操作参数,以确保吸塑机能够正常工作和成型。
(4)完成成型后,将成品从模具上取出,放置在指定的位置进行下一步处理。
4. 关机和清洁:(1)在关闭吸塑机之前,应先停止加热和吸塑操作。
(2)关机后,应及时清理吸塑机及其周围的杂物,保持清洁整洁。
(3)定期对吸塑机进行维护保养工作,确保其正常运行和延长使用寿命。
二、常见故障排除1. 吸塑不良:(1)可能是温度不合适导致的,可以调整吸塑机的温度参数。
(2)可能是模具损坏导致的,可以更换模具并进行适当调整。
(3)可能是原材料问题,可以检查原材料的质量和配比。
2. 吸塑机卡料:(1)可能是原材料堆积太多导致的,可以适当减少原材料的供给量。
(2)可能是供料器出现故障,可以检查供料器的运行状况并进行维修。
3. 吸塑机异常声音:(1)可能是机器内部运转不正常,可以检查吸塑机的机械部件是否损坏。
(2)可能是供料过程中杂物进入导致的,可以清理供料口和供料器。
通过以上操作要点和常见故障排除,操作人员在使用吸塑机时能够更好地进行操作和维护,确保吸塑机的正常运行和成型效果。
吸塑知识培训资料

走访有关工艺技术人员和生产人员, 了解设备实际使用情况、操作人员技术水平、 最常出现的与模具有关的成型质量问题等, 为模具设计准备更充分的第一手资料。 2.2、制定成型工艺。
通常由成型工艺人员根据制品成型要求制定成型工艺, 并提出模具设计任务 书, 由模具设计人员进行模具设计, 但有时工厂往往会将这两项工作合并起来做, 也就是说, 模具设计人员在进行模具设计之前, 还应制定合理的成型工艺, 为后面 的模具设计打下基础。此时, 应结合节中提出的问题进行综合考虑。 2.3、熟悉成型设备技术规范:
吸塑件工艺性简介
4、拉深比的确定: 拉深比是指箱胆成型后总表面积比上参与成型的板材表面之和,通常情况
下,此值在3-3.5范围内,成型后产品厚薄差异不会太大,有利于保证产品质 量。我公司内胆深度最大620mm(吸塑机极限尺寸)。
5、胆口部设计成喇叭口状. 箱胆口部圆角不可能做得很大, 一般为R4-R6,小于R4胆口易开裂。如果
如果成型工艺控制不严, 或者模具结构不合理, 冰箱内胆容易造成制品轮廓 不清晰。为了顺利脱模, 往往需要设置抽芯机构, 使模具设计制造复杂化。另外, 为提高薄壁强度而设置的加强筋会使模具结构更复杂、成型困难。 (3) 内胆深, 成型拉伸比大.
成型拉伸比大易造成制品壁厚不均匀、内应力大, 制品的某些部位很容易 被拉破。这就要求从选材、成型工艺制定到模具设计都要充分考虑这一因素, 并采取相应措施。比如, 工艺上采取吹泡预拉伸, 模具设计上采取加大圆角半径、 合理设计抽气孔等。 四、冰箱内胆真空成型模具设计方法.
②成型体的表面粗糙度对塑料件质量和脱模有很大影响。因真空成型模具一般
吸塑机

吸塑机简介吸塑机(又叫热塑成型机)是将加热塑化的PVC、PE、PP、PET、HIPS 等热塑性塑料卷材吸制成各种形状的高级包装装璜盒、框等产品的机器。
吸塑成型机原理:吸塑成型又叫热塑成型,这种成型工艺主要是利用真空泵产生的真空吸力将加热软化后的PVC、PET、PETG、APTT、PP、PE、PS等热可塑性塑料片材经过模具吸塑成各种形状的真空罩、吸塑托盘、泡壳等。
目前市面上常见的产品有:日用品吸塑包装、小五金吸塑包装、汽车用品吸塑包装、电子产品吸塑包装、食品吸塑包装、化妆品吸塑包装、电脑周边设备吸塑包装、玩具吸塑包装、体育用品吸塑包装、文具用品吸塑包装等。
其主要构造是由给料、拉料、上下电加热炉、下闸、多功能可调尺寸、下模盘、上模、上闸、刀闸、切片、放片及配以真空装置等构成;以气动装置为主动力源,其拉片、送片采用电动、减速器,时间继电器,中间继电器,行程开关等电器组成全自动控制系统。
吸塑机对控制系统的要求是保证操作方便、机械动作和温度控制精度高、生产时间短、在同等生产条件下尽可能节约机械的耗电量。
主要应用塑料包装行业(吸塑包装、塑胶、电池、玩具、礼品、五金、家电、电子、文具、装饰);食品包装行业(快餐盒、水果托盘、饼干盒);医药行业(药丸包装、药片包装);工业上冷却塔冷却水导流板等;装饰用立体浮雕图案、塑料天花板、壁板、汽车材料、卫生器材等制造行业。
适合生产各种颜色片材:聚乙烯PS、聚氯乙烯PVC、有机玻璃、ABS、聚甲基丙烯酸甲酯;植绒片材;环保片材APET、PET、PP等;光降解材料;生物降解材料等塑料制品。
吸塑成型技术:吸塑成型技术即塑料片(板)材热成型加工技术,是塑料二次加工工业技术中的一种。
它不同于注塑,挤出等一次加工工艺,不是针对塑料树脂或颗粒进行加热模塑成型或同过口模同截面连续成型;也不是利用机床,刀具等机械进行加工手段,将一部分塑料材料切削下来,获得需要的形状,尺寸,而是针对塑料片(板)材,进行加热,利用模具,真空或压力使片(板)材变形,达到要求的形状和尺寸,辅以配套工序,实现应用目的。
塑料模具的设计与成型工艺

塑料模具的设计与成型工艺摘要:塑料成形是一种以人工合成金属树脂材料为基本合成原材料,加入其他一定量化学添加剂,在一定的工作压力、温度下,制成一定形状,并在室温下长久保持形状不变的材料。
塑料是20世纪末期发展壮大起来的一类工业新型材料,包装材料工业、日常用品制造工业,机械工业,医疗器械等工业领域。
医疗器械等领域。
塑料模具产品设计的基本技术要求之一是企业能不断生产研制出能在尺寸,精度,外观及热物理及流体力学性能等各方面条件均能充分满足实际使用性能要求的优质材料塑件。
在进行模具生产使用时,应该要力求模具生产过程效率高,自动化管理程度高,操作方便,寿命长;在应用模具结构制造工艺方面,要求模具结构设计合理,制造容易,成本低。
引言:20世纪70年代以来,石油危机持续爆发虽然使得目前我国大型塑料制品加工制造产业的主要产品原料价格上涨,其宏观经济发展趋势仍然受到很多较大一定程度的宏观经济因素抑制和被经济抑制。
所以,改善塑料的性能、推广和使用先进的模具设计制造技术,研究塑料快速成型技术显得尤为重要。
塑料模具是使塑件成型的主要工具,它可使塑件获得一定的结构形状及所需性能。
其发展受到很大程度的抑制抑制。
所以,改善塑料的性能、推广和使用先进的模具设计制造技术,研究塑料快速成型技术显得尤为重要。
塑料模具是使塑件成型的主要工具,它可使塑件获得一定的结构形状及所需性能。
用特殊模具工艺生产制造出来的的新型塑件产品具有高工艺复杂程度,高质量一致性,高操作精度、高生产率以及低材料消耗率等几大特点。
一、塑料模具简介塑料产品是用各种零件作为材料后再进行加工再成型而得以获得的一种产品。
而腔体模具就是一种利用其本身特定的腔体密闭性和腔体部件去加工成型,从而可以做成一种具有一定整体形状和大小尺寸的大型塑料金属制件的一种工具。
1、用新型机械塑料模具自动加工塑料生产工艺制造加工出来的的新型柔性塑件塑料制品。
它具有高度易操作和低精度、高性能和低一致性、高生产率和低使用材料资源消耗率等几个新的显著特点。
吸塑设计及其制造注意点复习进程

2020/5/23
Page
7
阴模成型
图5:阴模成型
2020/5/23
Page
• 真空吸塑阴模成型工艺过程如 图(图5)所示。
• 真空阴成型法生产的制品 与模腔壁贴合的一面质量较高, 结构上也比较鲜明细致,壁厚 的最大部位在模腔底部,最薄 部位在模腔侧面与底面的交界 处,而且随模腔深度的增大制 品底部转角处的壁就变得更薄。 因此真空阴模成型法不适于生 产深度很大的制品。
对于阳模制件注意如下问题
图7:阳模制件中的缺陷及其典型特征
1-冷却痕迹;2-皱褶;
3-薄部位;4-厚部位
• ① 在使用高的角式模具进行加工时,特别是当模具与夹持框 架间的距离很大时,容易产生皱褶(图7)
• ② 在角落处容易产生冷却条纹(图7); • ③ 在凸缘处壁厚不均匀(图7); • ④ 由于侧壁斜度不够而使脱模困难; • ⑤ 在成型区(夹持模框)多腔模具的嵌件和下夹持器之间会
调节好真空度,以得到符合设计要求的轮廓和尺寸一致的
产品。
2020/5/23
Page
5
三. 阳模(凸模)和阴模(凹模)成型
• 对于真空吸塑成型,受热的材料仅有一面与成型工具相接触。这样,材料与模具相接的面 就具有与成型模具完全相同表面轮廓。而成型制件的未接触面的轮廓和尺寸就只有取决于 材料的厚度。根据成型材料与成型模具的接触面的不同,成型过程可分为阳模和阴模成型。
吸塑设计及其制造注意点
吸塑设计
• 一.真空吸塑成型原理 -----------------------------------------------------03 • 二、无模成型 ----------------------------------------------------------------04 • 三. 阳模(凸模)和阴模(凹模)成型 --------------------------------06 • 四,机器基本装置 ----------------------------------------------------------12 • 五、有效成型压力 ----------------------------------------------------------18 • 六、成型面积、切入面积、夹持边缘-----------------------------------20 • 七、废料(边料)面积和废料比率 -------------------------------------21 • 八、排气面、排气孔、排气槽、槽口 ----------------------------------24 • 九、脱模斜度 ----------------------------------------------------------------25 • 十、成型比和牵引比--------------------------------------------------------26 • 十一、壁厚计算、吸塑成型制件-----------------------------------------30 • 十二、吸塑成型制件的收缩和变形--------------------------------------33 • 十三、痕迹、冷却痕迹、条纹、皱褶-----------------------------------35
吸塑模具制作流程TRAY课件
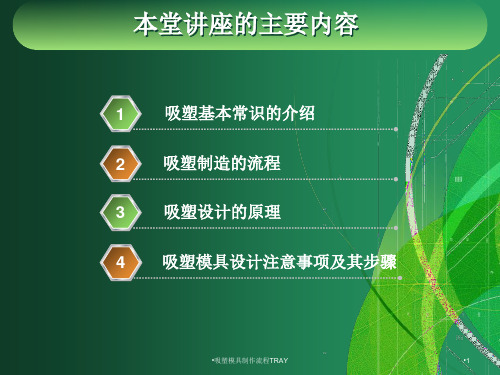
补充说明
当模具制作完成后,如需设变,需按设变原则: 1)如果穴位设变加大,在模具空间足够的情况下,可以在原模上加工. 2)如果穴位需要设变改小,原模报废,需重新开模.
二:植绒吸塑盘 是一种采用特殊材料的吸塑托盘,将普通的塑料硬片表面粘上一层绒质材料,从而使托盘表面有种绒质的手感,用来提高包装品档次。
三:抗静电吸塑盘 是一采用特殊材料的吸塑托盘,该材料表面的电阻值小于10的11次方欧姆。主要用于电子、IT产品的吸塑托盘。
吸塑盘的展示
双泡罩吸塑盒 工艺品植绒托 医疗器械包装
8
脱模斜度
脱模斜度一般为5°,零件高的为7°,要求晃动小的为3°。
9
排版
穴位形状的大小、高低、凹凸。一般情況下是根據零件的形狀來排的,這樣能保證零件在吸塑盤中的定位性,能保證共用性。
10时)。
吸塑模具设计注意事项
部分產品需要倒扣,即是上下、裏外需緊密扣牢。具體依客戶要求設計。因為有的扣是圓的,有的倒扣是方的,還有的倒扣是不規則的。
不论是铝模还是铜模,一旦模具完成,生产过程中不用担心尺寸会有变动,因为吸塑模是单模,稳定性比较好!
吸塑模具製作主要過程
設計
加工
打孔拋光
吸塑模具设计步骤
序号
步骤
要 求
1
确定材料
依客户要求、零件的大小、難易複雜程度、共用狀況、零件自身的品質要求确定用何种材料。
2
确定尺寸
依客户要求、依零件尺寸确定TRAY的外形和穴位的长、宽、高。
化妆品包装 电子类吸塑包装 手机托包装
医药托盘 纸卡塑料盒 mp3透明折边包装盒
吸塑盘的打樣流程
业务接单
- 1、下载文档前请自行甄别文档内容的完整性,平台不提供额外的编辑、内容补充、找答案等附加服务。
- 2、"仅部分预览"的文档,不可在线预览部分如存在完整性等问题,可反馈申请退款(可完整预览的文档不适用该条件!)。
- 3、如文档侵犯您的权益,请联系客服反馈,我们会尽快为您处理(人工客服工作时间:9:00-18:30)。
对于阳模制件注意如下问题
图7:阳模制件中的缺陷及其典型特征
1-冷却痕迹;2-皱褶;
3-薄部位;4-厚部位
① 在使用高的角式模具进行加工时,特别是当模 具与夹持框架间的距离很大时,容易产生皱褶(图 7)
② 在角落处容易产生冷却条纹(图7); ③ 在凸缘处壁厚不均匀(图7); ④ 由于侧壁斜度不够而使脱模困难; ⑤ 在成型区(夹持模框)多腔模具的嵌件和下夹
b 在阳模成型中由于附加的保护物的作用而使切
人面积减小;
c 在阴模成型中规定的加工切人面积
L ·B-成型区域;Ll ·B1-切人面积;f-夹持边
缘;
E-阳模成型中牵伸起始处(壁厚发生变化)
应用如下:成型材料未受热的区域(如未受热的夹持 边缘)不收缩,而成型的部分则在成型后收缩;但是 不同收缩的区域会造成模塑物的变形。
= 142353.2 mm2
废料比率 = 142353.2/(610x1200) = 0.194或19.4 %
八、排气面、排气孔、排气 槽、槽口
在真空吸塑成型加工过程中,为了除去塑料材料与模 具之间所存留的气体,模具必须是能排气的或有足够 的排气孔或排气槽;这可以使空气通过抽气装置(或 转移)快速的除去。
保持固定状态。各种类型单工位成型机上框架的下
部直接固定在成型室上。用手装型坯和成品取出的
手动和半自动成型机上,当框架尺寸很大时,都装
有在框架打开范围内的安全操作装置。对成型滑移
性较大的型坯,要求夹紧力能在比较宽的范围内调
机器基本装置(2)
2.加热设备 热塑性塑料片材和薄膜的真空吸塑成型过程,主要工
空度,以得到符合设计要求的轮廓和尺寸一致的产品。
三. 阳模(凸模)和阴模(凹模) 成型
对于真空吸塑成型,受热的材料仅有一面与成型工具相接触。这样,材料与模具相接的面 就具有与成型模具完全相同表面轮廓。而成型制件的未接触面的轮廓和尺寸就只有取决于 材料的厚度。根据成型材料与成型模具的接触面的不同,成型过程可分为阳模和阴模成型。
除了成型温度、模具温度和牵伸作用的影响外,真空吸 塑成型制件的成型精度还主要依赖于热制件与模具之间 的有效接触压力。 模具在预牵伸的过程中会产生一定的 接触压力(图9a )。而制品成型时,若在接触处抽真空 或者使用柱塞的机械压力,又就会产生一定的成型压力。 这也就是说接触处的有效压力是牵伸产生的接触压力和 由真空或柱塞的机械压力产生的成型压力之和。对于其
模腔侧面与底面的交界处,而且
随模腔深度的增大制品底部转角
处的壁就变得更薄。因此真空阴
模成型法不适于生产深度很大的
制品。
阳模和阴膜的对比
图6:a 阳模成型(简图)和b阴模成型(简图)
1-厚部位;2-薄部位;3-成品的内尺寸;4-外尺寸
对于阴模成型,制件的内尺寸是很精确的,因为它是与真空吸塑成型工具相接的一 面。相反,对于阳模成型,制品的外尺寸是很精确的,因为其外部与真空吸塑成型 模具相接触如
无模成型
图3:无模真空吸塑成型壁厚分布
真空无模成型法在成型过程中只能改变制件的拉伸程度和外
廓形状,因此不能成型外型复杂的制件。另外,成型过程中,随着
拉伸程度的增大,最大变形区(即片材中心)的厚度不断减小,因
此实际生产中拉伸比(H/D)一般应小于75%。
在运用此法进行加工时,操作员必须有熟练的技巧,调节好真
阳模成型
图4:阳模成型
真空吸塑阳模成型工艺过程如图4
所示。
本法对于制造壁厚和深度较大的制 品比较有利。
制品的主要特点是:与真空阴模成 型法一样,模腔壁贴合的一面质量较高, 结构上也比较鲜明细致。壁厚的最大部
位在阳模的顶部,而最薄部位在阳模侧
面与底面的交界区,该部位也是最后成
பைடு நூலகம்
型的部位,制品侧面常会出现牵伸和冷 却的条纹,造成条纹的原因在于片材各 部分贴合模面的时候有先后之分。先与
空表等组成,在真空成型中常采用单独机型真空泵,
此种泵的真空度应达到0.07~0.09 Mpa(520mmHg)以
上。储气罐一般是用薄钢板焊接的圆柱形箱体,底是
椭圆形的。蓄气罐的容量至少应比最大成型室的容量
大一半。真空管路上,必须装有适当的阀门,以控制 真空窄容量。
真空泵的转动功率由成型设备的大小和成型速度决定, 较大或成型速度较快的设备常用大至2~4KW的。真空中
九、脱模斜度
图13 脱模斜度
a单阳模; b 单阴模
对于阳模成型,制品会收缩而紧贴在模具上,而对于单 腔阴模成型,制品收缩后可以脱离模具表面。为了能够 脱模,模具侧面必须具有一定的倾斜度。在脱模方向上, 模具侧面的倾角被称为脱模斜度(图13)。脱模斜度应 该取得尽可能大。脱模斜度越大,脱模越快,成型周期 越短,而且在脱模的过程中制品变形的可能性小。单阳 模和单阴模的脱模斜度一般为:a=3o~5o ;对于收缩率 <0.5%的和慢速脱模a > 0.50 。
二、无模成型
图2:无模真空吸塑成型装置
真空无模成型过程如图2所示,将片材加热到所需温度后,置于夹持环 上,用压环压紧,打开真空泵阀门抽真空,通过光电管控制真空阀调 节真空度,直到片材达到所需的成型深度为止。由于自由真空成型法 中制件不接触任何模具表面,制件表面光泽度高,不带任何瑕疵。如 果塑料本自身是透明的,制件可以具有最小的光吸收率和透明性,故 可用于制造飞机部件如仪器罩和天窗等。
1.夹紧设备
塑料片材成型时,片材被固定在夹紧装置上。在真 空吸塑成型的通用型机和复合型的热成型机上多采 用便于固定各种尺寸片材的夹紧装置。有的是整个 成型机配一套夹紧框架。
夹紧装置可分为两类:一类是框架式,另一类
是分瓣式。框架式夹紧装置由上、下两个框架组成。
片材夹在两个框架之间。框架打开时,下框架一般
生产中若采用自然冷却可以获得退火制件,有利
于提高制件的耐冲击性。用水冷却虽然生产效率高,
但制件内应力较大。
机器基本装置(6)
6.脱模设备
脱模是将制品移出模外,通常无论是凹模还是凸
模,多数场合是由于制品冷却收缩而贴紧模具,所以
通过真空吸引孔或向相反方向吹风使之脱模。
尤其对于脱模斜度小的或有凹模的模具,同时使
20x2)]/{(430x950+430x200x2+950x200x2)+ [(610-
20x2)(1200-20x2)- 430x950]} = 66120/1174720 =
0.056
废料面积= 0.成0型56面x[积(610-2裁0边x2面)积(1200夹-持20边x缘2)面-积
440x960]+[610x1200-(610-20x2)(1200-20x2)]
央系统的大小视工厂具体生产和发展的要求而定。
机器基本装置(4)
4.压缩空气设备
气动系统可由成型机自身带有压缩机、储气罐、车
间主管路集、阀门等组成。成型机需要压力为
0.6~0.7MPa的压缩空气,各种真空吸塑成型机广泛采用活
塞式空气压缩机。也可以用大型的螺旋式空气压缩机整
厂供给。
压缩空气除大量应于成型外,还有当一部分用于脱模、 初制品的外冷却和操纵模具框架和运转片材等机件动作 的动力。
机器基本装置(5)
5.冷却设备
为了提高生产效率,真空吸塑成型制品脱模前常
需进行冷却。理想的情况是制件与模具接触的内表面
和外表面都冷却,而且最好采用内装冷却盘管的模具。
对于非金属模具,如木材、石膏、玻璃纤维增强塑料、
环氧树脂等模具,因无法用水冷,可改用风冷,并可
另加水雾来冷却真空吸塑成型制件的外表面。
低(图2-10)。
六、成型面积、切入面积、 夹持边缘
图11: 成型面积和切人面积
夹持框表面内部宽度大小范围区域的面积被称为成型面 积.
切人面积就是指在成型过程中发生牵伸的区域的面积。 它依赖于制件的规格,而与夹持边缘是否需要加热无关。
图11 成型面积和切人面积 :
a 对于阳模成型,成型面积等于切人面积;
吸塑设计及其制造
一.真空吸塑成型原理
图1:基本原理示意图
真空吸塑成型工艺(图1)是一种热成型加工方法。利用热 塑性塑料片材,制造开口壳体制品的一种方法。将塑料片 材裁成一定尺寸加热软化,借助片材两面的气压差或机械 压力,使其变形后覆贴在特定的模具轮廓面上,经过冷却 定型,并切边修整。 真空吸塑成型这种成型方法是依靠真 空力使片材拉伸变形。真空力容易实现、掌握与控制,因 此简单真空成型是出现最早,也是目前应用最广的一种热 成型方法
序之一就是片材加热,让片材软化成可塑性的设备。 电加热的持续时间和质量取决于加热器的结构,辐射 表面后温度传热的热惯性,片材与加热器间的距离, 辐射能吸收系数,加热器表面的特性以及材料的热物 理性能。常用的加热器有电加热器、晶体辐射器和红 外线加热器。
机器基本装置(3)
3.真空设备
真空系统由真空泵、储气罐、阀门、管路以及真
十、成型比和牵引比(1)
图14成型比 a 和b 不同几何体的成型比H :B ; c 圆形几何体的成型比
成型比(图14)是指制品的最大抽拔深度H 与成型面B 之比,或与成型面直径D 之比。成型比并不能准确反映 出牵伸比。成型比可根据图2-14 得到。
十、成型比和牵引比(2)
图15用于计算壁厚的制件 尺寸
模面接触的部分先被模具冷却,而在后
继的相关过程中,其牵伸行为较未冷却 的部位弱。这种条纹通常在接近模面顶 部的侧面处最高。
阴模成型
图5:阴模成型
真空吸塑阴模成型工艺过程如图 (图5)所示。
真空阴成型法生产的制品与
模腔壁贴合的一面质量较高,结
构上也比较鲜明细致,壁厚的最
大部位在模腔底部,最薄部位在
图12 矩形盒用料制品简图(右边为裁边后的成品图)
AB-模具底面,C-高度,L1和L2-模具延伸到片坯边