机械切削力的数学建模与仿真分析
机械自动化系统的建模与仿真分析
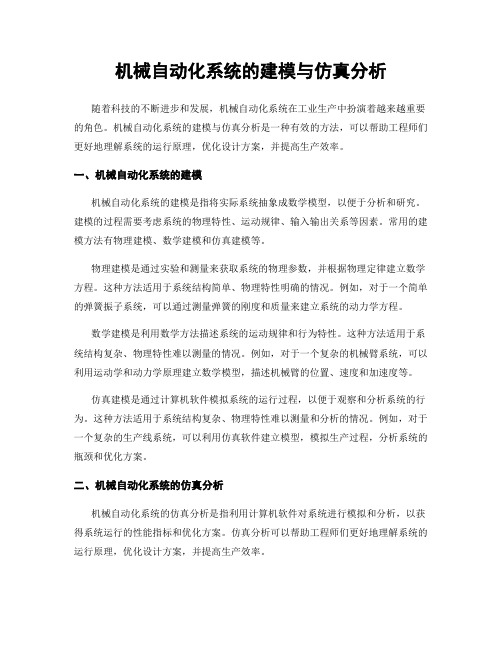
机械自动化系统的建模与仿真分析随着科技的不断进步和发展,机械自动化系统在工业生产中扮演着越来越重要的角色。
机械自动化系统的建模与仿真分析是一种有效的方法,可以帮助工程师们更好地理解系统的运行原理,优化设计方案,并提高生产效率。
一、机械自动化系统的建模机械自动化系统的建模是指将实际系统抽象成数学模型,以便于分析和研究。
建模的过程需要考虑系统的物理特性、运动规律、输入输出关系等因素。
常用的建模方法有物理建模、数学建模和仿真建模等。
物理建模是通过实验和测量来获取系统的物理参数,并根据物理定律建立数学方程。
这种方法适用于系统结构简单、物理特性明确的情况。
例如,对于一个简单的弹簧振子系统,可以通过测量弹簧的刚度和质量来建立系统的动力学方程。
数学建模是利用数学方法描述系统的运动规律和行为特性。
这种方法适用于系统结构复杂、物理特性难以测量的情况。
例如,对于一个复杂的机械臂系统,可以利用运动学和动力学原理建立数学模型,描述机械臂的位置、速度和加速度等。
仿真建模是通过计算机软件模拟系统的运行过程,以便于观察和分析系统的行为。
这种方法适用于系统结构复杂、物理特性难以测量和分析的情况。
例如,对于一个复杂的生产线系统,可以利用仿真软件建立模型,模拟生产过程,分析系统的瓶颈和优化方案。
二、机械自动化系统的仿真分析机械自动化系统的仿真分析是指利用计算机软件对系统进行模拟和分析,以获得系统运行的性能指标和优化方案。
仿真分析可以帮助工程师们更好地理解系统的运行原理,优化设计方案,并提高生产效率。
在进行仿真分析时,首先需要确定系统的输入输出关系和性能指标。
例如,对于一个生产线系统,输入可以是原材料的供应速度,输出可以是产品的产量和质量。
然后,通过建立数学模型和仿真软件,模拟系统的运行过程,观察和分析系统的行为。
仿真分析可以帮助工程师们评估不同设计方案的性能差异。
通过对比不同方案的仿真结果,可以选择最优的设计方案,并进行进一步的优化。
机械系统的动力学建模与仿真分析

机械系统的动力学建模与仿真分析一、引言机械系统是由多个相互作用的部件组成的复杂系统,其动力学行为是研究的核心问题之一。
动力学建模与仿真分析可以帮助工程师深入理解机械系统的运动规律,预测系统的性能,并优化设计。
本文将介绍机械系统的动力学建模方法以及仿真分析技术。
二、动力学建模1. 基本原理机械系统的动力学建模是基于牛顿力学的基本原理进行的。
通过分析受力、受力矩以及质量、惯性等因素,可以建立机械系统的运动方程。
在建立方程时,需要考虑系统的自由度、刚体或者弹性体的运动特性以及约束条件等因素。
2. 运动学建模运动学建模是机械系统动力学建模的前提。
通过研究机械系统的几何结构和运动规律,可以得到系统的等效长度、转动角度等信息。
基于运动学建模,可以计算系统的速度、加速度以及运动的轨迹等。
3. 动力学建模动力学建模是机械系统分析的核心部分。
基于受力和受力矩的平衡条件,可以建立机械系统的运动方程。
通常采用牛顿第二定律和力矩平衡条件,可以得到刚体的平动和旋转方程。
对于复杂的非线性系统,也可以采用拉格朗日方程或者哈密顿原理进行建模。
三、仿真分析1. 数值解算方法为了求解机械系统的运动方程,需要采用适当的数值解算方法。
常见的方法包括欧拉法、龙格-库塔法、变步长积分法等。
这些方法可以将微分方程离散化,然后通过迭代计算求解系统的状态变量。
2. 动力学仿真动力学仿真是建立在动力学模型的基础上。
通过将模型转化成计算机程序,可以在计算机上模拟机械系统的运动行为。
通过仿真分析,可以研究系统的稳定性、动态响应以及力学性能等。
3. 优化设计动力学仿真还可以应用于优化设计。
通过改变系统参数、构型和控制策略等,可以研究不同设计方案的性能差异,并选择最佳方案。
通过仿真分析,可以避免实际试验的成本和时间消耗。
四、案例分析以汽车悬挂系统为例,进行动力学建模与仿真分析。
汽车悬挂系统是一个典型的机械系统,包含减震器、弹簧、悬挂臂等部件。
首先进行运动学建模,分析车轮的运动状态和轨迹。
切削仿真研究报告总结
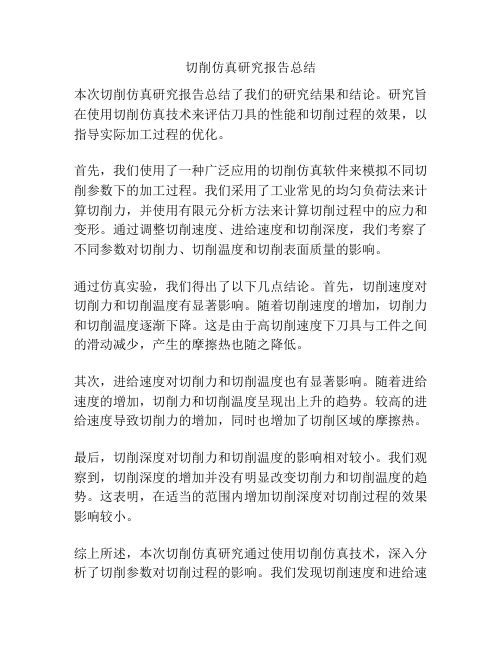
切削仿真研究报告总结
本次切削仿真研究报告总结了我们的研究结果和结论。
研究旨在使用切削仿真技术来评估刀具的性能和切削过程的效果,以指导实际加工过程的优化。
首先,我们使用了一种广泛应用的切削仿真软件来模拟不同切削参数下的加工过程。
我们采用了工业常见的均匀负荷法来计算切削力,并使用有限元分析方法来计算切削过程中的应力和变形。
通过调整切削速度、进给速度和切削深度,我们考察了不同参数对切削力、切削温度和切削表面质量的影响。
通过仿真实验,我们得出了以下几点结论。
首先,切削速度对切削力和切削温度有显著影响。
随着切削速度的增加,切削力和切削温度逐渐下降。
这是由于高切削速度下刀具与工件之间的滑动减少,产生的摩擦热也随之降低。
其次,进给速度对切削力和切削温度也有显著影响。
随着进给速度的增加,切削力和切削温度呈现出上升的趋势。
较高的进给速度导致切削力的增加,同时也增加了切削区域的摩擦热。
最后,切削深度对切削力和切削温度的影响相对较小。
我们观察到,切削深度的增加并没有明显改变切削力和切削温度的趋势。
这表明,在适当的范围内增加切削深度对切削过程的效果影响较小。
综上所述,本次切削仿真研究通过使用切削仿真技术,深入分析了切削参数对切削过程的影响。
我们发现切削速度和进给速
度对切削力和切削温度具有显著影响,而切削深度的影响相对较小。
这些结论为优化切削参数提供了指导,能够帮助提高切削效率和加工质量。
在实际应用中,我们可以根据具体工件材料和切削条件,通过合理调整切削参数来优化加工过程,并达到更好的加工效果。
数控机床铣削切削力的模拟与实测方法

数控机床铣削切削力的模拟与实测方法摘要:数控机床在现代制造业中发挥着重要作用,铣削切削力的模拟与实测是数控机床加工研究的关键问题之一。
本文将介绍数控机床铣削切削力的模拟与实测方法,包括力学模型的建立、数值仿真和实验测试等方面的内容,以期为相关研究提供参考。
一、引言数控机床作为现代制造业的重要工具,其高精度、高效率的特点受到广泛关注。
而铣削切削力在数控铣床加工过程中起着决定性作用,对加工质量和机床性能具有重要影响。
因此,模拟和实测数控机床铣削切削力成为加工研究的重要内容之一。
二、模拟方法1. 力学模型的建立铣削切削力的模拟首先要建立合适的力学模型。
常用的力学模型包括切削力系数模型和有限元模型两种。
切削力系数模型是通过实验获得相关参数后,根据经验公式计算切削力。
有限元模型则是将加工过程建模为一系列有限元素,通过数值分析计算切削力的分布和大小。
2. 数值仿真数值仿真是利用计算机软件模拟数控机床加工过程和切削力的计算。
常用的仿真软件有Deform、ABAQUS等。
数值仿真可以通过调整刀具几何参数、切削条件和材料性质等因素,预测不同情况下的切削力大小和分布情况,为工艺优化提供指导。
三、实测方法1. 切削力测量设备实测切削力是了解加工过程中切削力的真实情况的重要手段。
常用的切削力测量设备包括力传感器、力加载装置和数据采集系统。
力传感器可以精确测量切削力大小,力加载装置则提供切削力测量所需的切削环境。
数据采集系统可以记录和分析切削力的变化规律。
2. 实验测试方法实验测试是通过具体的切削加工试验获取切削力的实际数值。
实验测试中需要准确控制切削条件,包括切削速度、进给速度和切削深度等。
通过实验测试可以获得不同切削条件下的切削力数值,用于验证模拟结果的准确性。
四、研究进展与展望随着数控机床技术的不断发展,数控机床铣削切削力的模拟与实测方法也在不断改进和完善。
当前的研究重点主要集中在提高模拟精度和实验测试的准确性,并进一步优化数控机床的切削性能。
基于数值模型的数控加工中切削力与稳定域仿真

第1期(总第230期)2022年2月机械工程与自动化MECHANICAL ENGINEERING & AUTOMATIONNo. 1 Feb.文章编号:1672-6413(2022)01-0088-03基于数值模型的数控加工中切削力与稳定域仿真罗汉兵1,王海霞2(1.珠海格力电器股份有限公司,广东 珠海519070; 2.珠海精实测控技术有限公司,广东 珠海519070)摘要:针对数控铳削加工工艺参数选择存在的问题,以球头铳刀高速铳削过程为研究对象,建立了考虑机床-刀具-工件系统振动的非线性动力学模型,分析了铳削力中的动态分量对切削颤振的影响,在考虑再生颤 振的基础上建立非线性动力学模型。
基于动态铳削力建模和颤振稳定域分析计算,提出了机床切削系统稳定 性极限预测方法,并对其进行仿真分析,为铳削加工参数的确定提供理论支持。
比较试验数据与仿真结果,证明了模型的准确性和仿真算法的有效性。
关键词:切削力;稳定域;仿真;数控加工;数值模型中图分类号:TP391. 9 : TG54 文献标识码:A0引言颤振是指切削加工过程中刀具、工件间产生的强 烈自激振动口②,会影响加工系统的稳定性,且对加工 环境造成污染。
对数控加工过程中的刀具动态位移、 动态切削力以及颤振稳定域进行仿真分析,选择稳定 区内的参数进行切削是避免颤振最有效的手段。
Sridhar 等⑶考虑了时变切削力系数,对铳削过程中的 颤振进行了系统的理论研究,并建立了直齿铳削通用 数学模型。
Tlusty 等⑷提出了铳削颤振的非线性力学模型,通过数值仿真分析了其加工稳定性。
Budak 等皈提出了针对铳削稳定域的分析预测法。
Abrari 等⑹考虑刀具的振动、工件表面波纹引起的切削厚度 变化以及后刀面和已加工表面间的摩擦建立了球头铳 削动力学模型。
张雪薇等⑺建立了薄壁零件铳削动力学模型,运用全离散解析方法对颤振稳定叶瓣图进行 了模拟仿真试验验证。
孟玉培⑻以加工中心 (KMC500S U)铳削系统为研究对象,建立了铳削再生 型颤振模型,进行铳削稳定性分析,研究结果为切削参 数的选择提供参考依据。
机械系统的建模与仿真研究

机械系统的建模与仿真研究在现代工程领域中,机械系统的建模与仿真研究作为一种重要的方法论,被广泛应用于各个领域,包括机械工程、自动化、航空航天等。
机械系统的建模与仿真研究通过建立系统的数学模型,利用计算机技术进行仿真分析,可以辅助工程师们了解和预测系统的动力学行为,优化设计方案,提高系统性能,并降低实验成本。
本文将围绕机械系统的建模方法和仿真研究的应用领域进行论述。
一、建模方法机械系统的建模是模拟、描述和预测机械系统运行行为的过程。
建模的关键在于准确地描述系统的结构和动力学特性。
常用的建模方法包括质点法、刚体法、有限元法等。
质点法是一种简化的建模方法,将机械系统中的实际物体当作质点处理,忽略其尺寸和形状,仅考虑质量和位置信息。
这种方法适用于分析质点受力和运动的场景,例如弹簧振子和重力摆等。
刚体法是一种更为复杂的建模方法,将机械系统中的实际物体当作刚体处理,考虑其形状和尺寸,但忽略其变形。
刚体的运动可以用欧拉角或四元数等方式描述。
刚体法适用于分析刚性连接和运动的场景,例如机械臂和机械车等。
有限元法是一种广泛应用于工程领域的建模方法,它将实际物体离散成多个小单元,利用微分方程或矩阵方程描述每个小单元的运动,并通过组装这些方程求解整个系统的运动。
有限元法可以用于分析复杂结构的应力、振动和热传导等问题,例如汽车车身和建筑物的结构强度优化。
二、仿真研究的应用领域机械系统的仿真研究在许多领域都有广泛的应用。
以下将介绍几个典型的应用领域,包括机械工程、自动化和航空航天等。
在机械工程领域,仿真研究可以用于优化机械设备的设计和制造。
例如,在汽车制造中,可以使用仿真软件对零部件的运动学和动力学进行模拟,以评估其性能和可靠性。
在船舶工程中,可以通过仿真研究系统的稳定性和航行性能。
这些仿真研究可以帮助工程师们设计更高效、更安全的机械系统。
在自动化领域,仿真研究可以用于控制系统的设计和优化。
例如,在工业机器人领域,可以利用仿真软件对机器人的运动轨迹和物料搬运进行仿真分析,以提高生产效率和质量。
CNC机床加工中的加工力学建模与仿真

CNC机床加工中的加工力学建模与仿真随着制造业的发展,CNC机床在加工过程中发挥着重要的作用。
然而,在CNC机床的加工过程中,加工力学是一个关键问题。
加工力学建模与仿真是解决这一问题的一种有效方法。
本文将通过对CNC机床加工中的加工力学建模与仿真的研究,探讨其在提高加工效率和质量方面的潜力。
1. 引言CNC机床(Computer Numerical Control)是一种数字化控制的机床,通过预先编程的控制系统指令,使机床能够自动完成各种加工操作。
在CNC机床的加工过程中,加工力学是一个关键问题。
加工力学的研究可以帮助我们理解材料在切削过程中的变形和损伤机制,从而提高加工效率和质量。
2. 加工力学的基本原理在CNC机床的加工过程中,加工力学的基本原理包括切削力的产生和传递、切削区域的变形和材料的损伤机制等。
切削力的产生和传递受到刀具和工件的材料性能、机床刚度和切削参数等因素的影响。
切削区域的变形包括刀具在材料上的滑动、切削过程中的变形以及材料的回弹等。
材料的损伤机制主要包括切削时的切割、剪切和摩擦等。
3. 加工力学建模方法为了更好地理解CNC机床加工中的加工力学行为,需要建立相应的力学模型。
加工力学建模方法可以分为经验模型和物理模型两种。
经验模型是根据经验总结得出的,主要基于实验数据进行分析和推导。
物理模型则是通过对材料力学和切削理论的研究,建立起来的一种理论模型。
3.1 经验模型经验模型是在实际切削过程中得出的一种经验总结,通常基于实验数据进行分析和推导。
根据经验模型可以计算出切削力、切削温度和切削区域的变形等参数。
然而,经验模型通常只能适用于特定材料和切削条件,对于新材料和复杂切削条件的预测能力较差。
3.2 物理模型物理模型则是通过对材料力学和切削理论的研究,建立起来的一种理论模型。
物理模型可以更好地理解切削过程中的力学行为。
通过建立合理的数学模型和使用数值仿真方法,可以计算出切削力、切削温度和切削区域的变形等参数。
机械工程中的建模与仿真技术研究
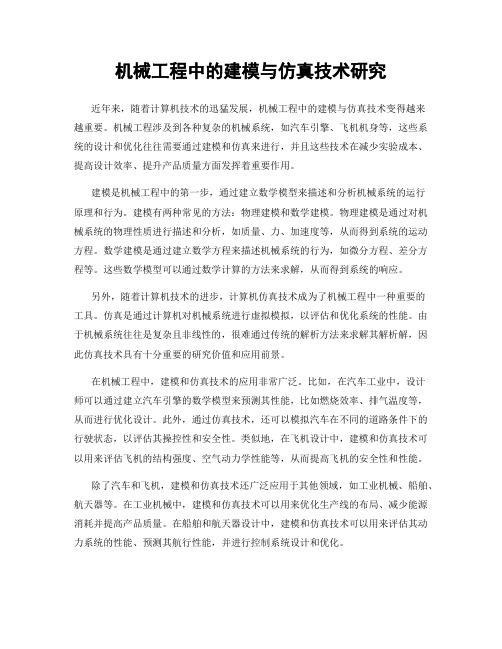
机械工程中的建模与仿真技术研究近年来,随着计算机技术的迅猛发展,机械工程中的建模与仿真技术变得越来越重要。
机械工程涉及到各种复杂的机械系统,如汽车引擎、飞机机身等,这些系统的设计和优化往往需要通过建模和仿真来进行,并且这些技术在减少实验成本、提高设计效率、提升产品质量方面发挥着重要作用。
建模是机械工程中的第一步,通过建立数学模型来描述和分析机械系统的运行原理和行为。
建模有两种常见的方法:物理建模和数学建模。
物理建模是通过对机械系统的物理性质进行描述和分析,如质量、力、加速度等,从而得到系统的运动方程。
数学建模是通过建立数学方程来描述机械系统的行为,如微分方程、差分方程等。
这些数学模型可以通过数学计算的方法来求解,从而得到系统的响应。
另外,随着计算机技术的进步,计算机仿真技术成为了机械工程中一种重要的工具。
仿真是通过计算机对机械系统进行虚拟模拟,以评估和优化系统的性能。
由于机械系统往往是复杂且非线性的,很难通过传统的解析方法来求解其解析解,因此仿真技术具有十分重要的研究价值和应用前景。
在机械工程中,建模和仿真技术的应用非常广泛。
比如,在汽车工业中,设计师可以通过建立汽车引擎的数学模型来预测其性能,比如燃烧效率、排气温度等,从而进行优化设计。
此外,通过仿真技术,还可以模拟汽车在不同的道路条件下的行驶状态,以评估其操控性和安全性。
类似地,在飞机设计中,建模和仿真技术可以用来评估飞机的结构强度、空气动力学性能等,从而提高飞机的安全性和性能。
除了汽车和飞机,建模和仿真技术还广泛应用于其他领域,如工业机械、船舶、航天器等。
在工业机械中,建模和仿真技术可以用来优化生产线的布局、减少能源消耗并提高产品质量。
在船舶和航天器设计中,建模和仿真技术可以用来评估其动力系统的性能、预测其航行性能,并进行控制系统设计和优化。
总结而言,机械工程中的建模与仿真技术是一门十分重要的技术,它可以帮助工程师们更好地理解和分析机械系统的行为,从而进行优化设计和提高系统性能。
- 1、下载文档前请自行甄别文档内容的完整性,平台不提供额外的编辑、内容补充、找答案等附加服务。
- 2、"仅部分预览"的文档,不可在线预览部分如存在完整性等问题,可反馈申请退款(可完整预览的文档不适用该条件!)。
- 3、如文档侵犯您的权益,请联系客服反馈,我们会尽快为您处理(人工客服工作时间:9:00-18:30)。
机械切削力的数学建模与仿真分析
机械切削力是指在机械加工过程中,切削工具对工件施加的力。
准确预测和控制切削力对于提高加工效率和产品质量至关重要。
因此,研究机械切削力的数学建模和仿真分析具有重要的实际意义。
机械切削力的数学建模是通过建立数学模型来描述切削过程中的力学现象。
切削力的大小与切削参数、切削工具和工件材料性质等因素有关。
在数学建模时,我们需要考虑这些因素,并建立相应的数学关系和方程式。
首先,我们可以通过经验公式来描述机械切削力。
经验公式是基于实验数据和经验总结得出的,可以较为准确地估计切削力。
这种方法简便实用,适用于一些常见的切削操作。
然而,经验公式是基于经验总结,对于特殊情况可能不够准确。
为了更精确地描述机械切削力,我们可以采用力学原理进行数学建模。
例如,在铣削过程中,工件受到切削力和切削刀齿力的作用。
我们可以将切削力分解为切向力和径向力,并分别描述切向力和径向力之间的关系。
在数学建模过程中,我们可以应用物理学中的切削力模型。
切削力模型使用切削力系数、切削深度和进给量等参数,可以较好地描述切削力的大小和变化规律。
其中,切削力系数是由切削工具和工件材料的力学性质决定的。
除了数学建模,仿真分析是研究机械切削力的重要手段。
仿真分析可以通过计算机模拟切削过程,得到切削力的数值结果。
通过仿真分析,我们可以研究不同切削参数和切削工况下的切削力变化情况,进一步优化切削工艺。
在进行切削力的数学建模和仿真分析时,我们还需要考虑各种实际工况对切削力的影响。
例如,工件材料的不均匀性、切削润滑和冷却等因素都会对切削力产生影响。
因此,在数学建模和仿真分析中,我们应该综合考虑这些因素,并做相应的修正和改进。
总之,机械切削力的数学建模和仿真分析对于工业生产具有重要的意义。
通过建立准确的数学模型,我们可以预测和控制切削力,提高切削效率和产品质量。
未来,随着数学建模和仿真技术的不断发展,我们可以实现更精确、更可靠的切削力分析,推动机械加工技术的进一步发展。