催化裂化技术
催化裂化工艺介绍

1。
0催化裂化催化裂化是原料油在酸性催化剂存在下,在500℃左右、1×105~3×105Pa 下发生裂解,生成轻质油、气体和焦炭的过程.催化裂化是现代化炼油厂用来改质重质瓦斯油和渣油的核心技术,是炼厂获取经济效益的重要手段。
催化裂化的石油炼制工艺目的:1)提高原油加工深度,得到更多数量的轻质油产品;2)增加品种,提高产品质量。
催化裂化是炼油工业中最重要的一种二次加工工艺,是重油轻质化和改质的重要手段之一,已成为当今石油炼制的核心工艺之一。
1。
1催化裂化的发展概况催化裂化的发展经历了四个阶段:固定床、移动床、流化床和提升管。
见下图:固定床移动床流化床提升管(并列式)在全世界催化裂化装置的总加工能力中,提升管催化裂化已占绝大多数。
1。
2催化裂化的原料和产品1。
2。
0原料催化裂化的原料范围广泛,可分为馏分油和渣油两大类。
馏分油主要是直馏减压馏分油(VGO),馏程350—500℃,也包括少量的二次加工重馏分油如焦化蜡油等,以此种原料进行催化裂化称为馏分油催化裂化。
渣油主要是减压渣油、脱沥青的减压渣油、加氢处理重油等。
渣油都是以一定的比例掺入到减压馏分油中进行加工,其掺入的比例主要受制于原料的金属含量和残炭值.对于一些金属含量低的石蜡基原有也可以直接用常压重油为原料。
当减压馏分油中掺入渣油使通称为RFCC。
以此种原料进行催化裂化称为重油催化裂化。
1。
2.1产品催化裂化的产品包括气体、液体和焦炭。
1、气体在一般工业条件下,气体产率约为10%-20%,其中含干气和液化气。
2、液体产物1)汽油,汽油产率约为30%-60%;这类汽油安定性较好。
2)柴油,柴油产率约为0—40%;因含较多芳烃,所有十六烷值较低,由重油催化裂化得到的柴油的十六烷值更低,这类柴油需经加氢处理。
3)重柴油(回炼油),可以返回到反应器内,已提高轻质油收率,不回炼时就以重柴油产品出装置,也可作为商品燃料油的调和组分。
4)油浆,油浆产率约为5%—10%,从催化裂化分馏塔底得到的渣油,含少量催化剂细粉,可以送回反应器回炼以回收催化剂。
催化裂化工艺

nm,比表面积可达500—700m2/g。 ➢硅酸铝的催化活性来源于其表面的酸性。
第31页/共84页
分子筛催化剂特点
➢分子筛催化剂在催化裂化中的应用是催化裂化 技术的重大发展。分子筛催化剂是60年代发展 起来的一种新型的高活性催化剂。它的出现, 使流化催化裂化工艺发生了很大变化,装置处 理能力显著提高,产品产率及质量都得到改善。
显微镜下的催化裂解催化剂
第36页/共84页
分子筛催化剂的组成
➢ 活性组元分子筛:ZSM-5和Y. ZSM-5作添加剂,占 15~50%; ➢ 基质或者称之为载体:一般为高岭土或合成基质,占20~70%; ➢ 粘结剂:铝溶胶、硅溶胶或硅铝溶胶; ➢ 添加物或助剂成分:抗Ni、V、N等。
0.50 0.75
1.00
金属在催化剂上的含量,(W)%
第24页/共84页
金属污染对产氢量的影响
氢,Nm3/ m3
800-
Ni
600-
400-
200-
镍
的
脱
氢
功
能
V
高
于
钒
01000 2000 3000 4000 5000 6000
催化剂上的金属含量,ppm
第25页/共84页
金属污染对焦炭产率的影响
➢1965年五朵金花之一的流化催化裂化在抚顺石油二厂建 成投产。五朵金花:催化裂化、催化重整、延迟焦化、尿 素脱蜡、微球催化剂与添加剂。
➢1974年我国建成投产了第一套提升管催化裂化工业装置 。
➢随着催化剂和催化工艺的发展,其加工的原料逐步重质化、 劣质化。
第5页/共84页
催化裂化技术.

①.散式流化态: 颗粒均匀地分布在整个流化床内且随着 流速的增加床层均匀膨胀,床内孔隙率均匀 增加,床层上界面平稳,压降稳定、波动很 小。因此,散式流化态是较理想的流化状态。 一般流-固两相密度差较小的体系呈现散式流 态化特征,如液-固流化床。 ②.聚式流化态: 颗粒在床层的分布不均匀,床层呈现两 相结构:一相是颗粒浓度与空隙率分布较为 均匀且接近初始流态化状态的连续相,称为 乳化相;另一相则是以气泡形式夹带少量颗 粒穿过床层向上运动的不连续的气泡相,因 此又称为鼓泡流态化。
四、催化裂化的方法 1、固定床: 反应和再生过程是在同一设备中交替进行, 属于间歇式操作。为了使整个装置能连续生产, 就要用几个反应器轮流的进行反应和再生。因 此这种装置的设备结构复杂,生产能力小,钢 材耗量大,操作麻烦,工业上早已被淘汰。 2、移动床: 移动床催化裂化,使用直径约3mm的小 球催化剂,起初是用机械提升的方法在两器间 运送催化剂,后来改为空气提升,生产能力较 固定床大为提高,产品质量也得到改善。由于 催化剂在反应器和再生器内靠重力向下移动, 速度缓慢,所以对设备磨损较小,不过移动床 的设备结构仍比较复杂,钢材耗量比较大。
催化裂化技术
第一章 概述
一、催化裂化技术 二、催化裂化技术发展状况 三、催化裂化反应类型 四、催化裂化的方法 五、催化裂化的目的及意义
第二章 工艺叙述
一、反应-再生系统 二、分馏系统
三、吸收—稳定系统
四、余热锅炉系统 五、反应系统主要设备
第一章
概述
一、催化裂化技术 催化裂化(Fluid Catalytic Cracking)是石油炼制 过程之一,是在热和催化剂的作用下使重质油发生裂 化反应,转变为裂化气、汽油和柴油等的过程。催化 裂化原料是原油通过原油蒸馏(或其他石油炼制过程) 分馏所得的重质馏分油;或在重质馏分油中掺入少量渣 油,或经溶剂脱沥青后的脱沥青渣油;或全部用常压渣 油或减压渣油。在反应过程中由于不挥发的类碳物质 沉积在催化剂上,缩合为焦炭,使催化剂活性下降, 需要用空气烧去(见催化剂再生),以恢复催化活性, 并提供裂化反应所需热量。催化裂化是石油炼厂从重 质油生产汽油的主要过程之一。所产汽油辛烷值高 (马达法80左右),裂化气(一种炼厂气)含丙烯、 丁烯、异构烃多。
先进炼油化工技术催化裂解技术(DCC)
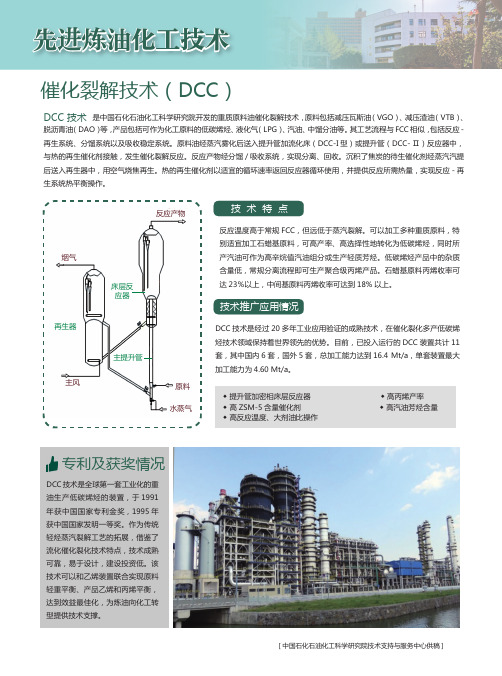
催化裂解技术(DCC)
DCC 技术 是中国石化石油化工科学研究院开发的重质原料油催化裂解技术,原料包括减压瓦斯油(VGO)、减压渣油(VTB)、脱沥青油(DAO)等,产品包括可作为化工原料的低碳烯烃、液化气(LPG)、汽油、中馏分油等。
其工艺流程与FCC 相似,包括反应-再生系统、分馏系统以及吸收稳定系统。
原料油经蒸汽雾化后送入提升管加流化床(DCC-I 型)或提升管(DCC-Ⅱ)反应器中,与热的再生催化剂接触,发生催化裂解反应。
反应产物经分馏/吸收系统,实现分离、回收。
沉积了焦炭的待生催化剂经蒸汽汽提后送入再生器中,用空气烧焦再生。
热的再生催化剂以适宜的循环速率返回反应器循环使用,并提供反应所需热量,实现反应-再生系统热平衡操作。
DCC 油生产低碳烯烃的装置,于[中国石化石油化工科学研究院技术支持与服务中心供稿]反应产物烟气原料
水蒸气主风再生器床层反应器主提升管
先进炼油化工技术。
催化催化裂化技术

催化催化裂化技术催化裂化技术是一种重要的炼油工艺,可以将重质石油馏分转化为高附加值的轻质产品。
本文将从催化裂化技术的原理、应用和发展前景等方面进行探讨,以期为读者提供对该技术的全面了解。
一、催化裂化技术的原理催化裂化技术是通过催化剂的作用将重质石油馏分分解为较轻的产品。
其主要原理是在高温和高压的条件下,将原料油与催化剂接触,使其发生裂化反应。
这种反应可以将长链烃分子裂解成短链烃分子,从而提高汽油和燃料油的产率。
催化裂化反应主要分为两个阶段:热裂化和催化裂化。
在热裂化阶段,原料油在高温下分解成烃气和液体烃。
然后,在催化剂的作用下,烃气和液体烃进一步反应,生成较轻的产品,如汽油、液化气和柴油等。
二、催化裂化技术的应用催化裂化技术在炼油行业中具有广泛的应用。
首先,它可以提高汽油的产率。
由于汽车的普及,对汽油的需求量不断增加。
催化裂化技术可以将重质石油馏分转化为轻质的汽油,从而满足市场需求。
催化裂化技术可以生产出高质量的柴油。
在催化裂化过程中,石油馏分中的硫、氮和金属等杂质可以得到有效去除,从而提高柴油的质量。
这对于减少柴油排放的污染物具有重要意义。
催化裂化技术还可以生产出液化气、石脑油和石化原料等产品。
这些产品在化工、冶金和化肥等行业中具有广泛的应用。
三、催化裂化技术的发展前景随着能源需求的增加和石油资源的日益枯竭,催化裂化技术在未来的发展前景十分广阔。
一方面,随着汽车工业的高速发展,对汽油的需求将持续增加,催化裂化技术将成为满足市场需求的重要手段。
另一方面,随着环境保护意识的提高,对燃料油质量的要求也越来越高。
催化裂化技术可以提高燃料油的质量,减少对环境的污染,因此在未来的发展中具有重要的作用。
随着科技的不断进步,催化剂的研发和改进也将推动催化裂化技术的发展。
新型的催化剂可以提高反应的选择性和活性,从而提高产品的产率和质量。
催化裂化技术作为一种重要的炼油工艺,在提高石油产品产率和质量方面具有重要的作用。
石油化工重油催化裂化工艺技术

石油化工重油催化裂化工艺技术石油化工重油催化裂化工艺技术是一种将重油转化为轻质油和化学品的过程。
该过程主要利用催化剂的作用,在高温高压条件下,使重油的大分子裂解成小分子,同时发生异构化、芳构化和氢转移等反应,以获得更多的轻质油和化学品。
催化剂的选择:催化剂是该技术的核心,其选择对产品的质量和产量有着至关重要的影响。
目前,常用的催化剂包括酸性催化剂、金属催化剂和金属氧化物催化剂等。
工艺条件的控制:工艺条件包括反应温度、压力、空速等,这些因素对产品的质量和产量都有着极大的影响。
因此,精确控制这些工艺条件是重油催化裂化工艺技术成功应用的关键。
产品的质量和性能:重油催化裂化工艺技术生产的产品具有高辛烷值、低硫含量等特点,被广泛应用于汽油、柴油、航空煤油等领域。
在应用方面,石油化工重油催化裂化工艺技术适用于不同类型重油,如减压渣油、催化裂化残渣油、脱沥青油等。
对于不同工业应用,可根据实际需求选择合适的工艺技术。
例如,对于生产高质量汽油和柴油的需求,可以选择更为精细的催化剂和严格的工艺条件;对于生产高附加值化学品的需求,则可以通过调整工艺流程和催化剂类型来增加化学品产量。
虽然石油化工重油催化裂化工艺技术在提高石油利用率、生产高质量石油化工产品方面具有重要作用,但也面临着一些挑战。
催化剂的活性、选择性和稳定性是该技术的关键,而目前催化剂的研究与开发尚存在诸多困难。
重油催化裂化过程中产生的固体废物和废气等对环境造成了严重影响,亟需解决。
由于重油资源的有限性,需要进一步探索和研发更为高效、环保的石油化工技术,以适应未来可持续发展的需要。
石油化工重油催化裂化工艺技术在石油化工产业中具有重要地位。
随着经济的发展和科技的进步,该技术将不断完善和优化,提高石油利用率和生产效率,同时注重环保和可持续发展。
未来,需要加强催化剂的研发与优化,减少环境污染,提高技术的绿色性和可持续性。
应积极探索新的石油化工技术,以应对全球能源危机和环境问题的挑战。
催化裂化技术的现状及发展趋势
催化裂化技术的现状及发展趋势
催化裂化技术是最近几年来人们极力推进研究的一个技术,它对于提高生物柴油的性能以及破坏有毒有机物质有显著的改善。
目前,催化裂化技术已经发展迅猛,并在未来的发展中有发挥出巨大的潜力,其中包括其在碳氢化合物低温裂化领域的巨量发展。
首先,催化裂化技术在开发绿色燃料、降低有毒物质的排放方面发挥着重要作用。
它为油脂,烃类,污染物,有毒有机物,废弃物,碳氢化合物等制备生物柴油等清洁能源提供了可能。
其中,碳氢化合物的低温裂烃技术可以提高生物柴油的收率,降低有毒有机物的排放,提高燃料的燃烧能效,为构建低碳的绿色社会奠定基础。
其次,催化裂化技术近年来发展迅猛,包括催化剂的合成,催化裂化反应机理,催化剂和反应条件等。
例如,今年在日本开发出用于催化裂化柴油的新型钴催化剂。
此外,也合成了用于催化裂化石油、烃类和有机废料等材料的新型催化剂,例如以钯和钼为分子基础的纳米微粒等。
另外,催化裂化技术也受到国内外科学家的研究关注,已经取得了显著的进展。
国外的研究主要集中在改进催化加氢裂化反应最前沿的技术和装置技术以及提高反应温度和在碳氢化合物低温裂化方面取得巨大进展。
至于国内,主要工作集中在改进催化剂和催化反应机理以及提高催化裂化反应效率的方面,如金属催化剂和非金属催化剂的研究以及反应温度的改进等,以期在技术发展上取得突破性进展。
总的来说,催化裂化技术的发展取得了显著的成绩,在未来的研究中,将会继续完善并发展其本身的技术,并继续在低温碳氢化合物催化裂烃方面展示出巨大的潜力。
催化裂化装置技术手册
催化裂化装置技术手册催化裂化装置是炼油行业中重要的加工设备,其技术手册的编写对于保证装置正常运行和提高生产效率至关重要。
本文将从催化裂化装置的原理、操作指南和维护保养等方面进行详细介绍。
一、催化裂化装置原理催化裂化装置通过将高分子量的石蜡、石油渣和重油等原料在催化剂的作用下进行热裂解,从而得到低分子量的石油产品。
该装置主要由裂化炉、催化剂循环系统、裂化反应器和产品分离装置等组成。
具体操作过程如下:1. 原料进料原料(如石蜡、石油渣和重油)通过进料系统进入裂化炉。
2. 热解反应原料在高温条件下与催化剂接触,发生热裂解反应,生成裂化油气。
3. 分离装置裂化产物通过分离装置进行分离,分离出裂化汽油、裂化液化气和裂化轻石蜡等产品。
4. 催化剂循环裂化后的催化剂通过循环系统回到裂化炉,起到持续催化裂化反应的作用。
二、催化裂化装置操作指南1. 温度控制裂化炉温度是影响裂化反应效果的关键参数。
在操作中,应根据不同原料的特性和所需产品质量,合理控制催化裂化温度,避免温度过高导致催化剂失活或温度过低影响反应速率。
2. 原料选择不同原料的性质对裂化反应的影响有所差异。
应根据目标产品质量和市场需求,合理选择原料,并进行合适的预处理,如脱蜡、脱硫等,以提高裂化效果和产品品质。
3. 催化剂活性管理催化剂是催化裂化装置中最关键的组成部分。
为保证装置的正常运行,应定期检测催化剂的活性,并进行必要的处理,如焙烧、再生等,以延长催化剂的使用寿命。
4. 安全操作在操作催化裂化装置时,应严格遵守操作规程,保证操作人员的人身安全和设备的正常运行。
同时,应加强对催化裂化装置的检测和维护,及时发现和处理潜在的安全隐患。
三、催化裂化装置维护保养1. 清洗与清理定期对催化裂化装置进行清洗和清理,去除附着物、沉积物和焦炭,以保证装置的畅通和正常运行。
2. 检修和更换定期进行设备的检修和更换,如检修泵、阀门等关键设备,更换老化和磨损的零部件,以确保催化裂化装置的长期稳定运行。
催化裂化工艺流程介绍
催化裂化工艺流程介绍
《催化裂化工艺流程介绍》
催化裂化是一种重要的石油加工工艺,用于将原油转化为高附加值的石油产品,如汽油、柴油和润滑油基础油。
催化裂化工艺通过将长链烃分子裂解为较短的链烃分子,从而提高产品的烃值和增加汽油产量。
催化裂化工艺的流程包括以下几个关键步骤:
1. 原料预处理:原油首先经过脱盐、脱硫等预处理工序,去除杂质和硫化物,净化原料。
2. 加热:经过预处理的原油被加热至裂化温度,通常在450-500摄氏度。
3. 进料分级:加热后的原油通过分级器进行分级,分离出不同碳数的馏分。
4. 裂化反应:分级后的原油进入裂化反应器,通过加入催化剂进行裂解,长链烃分子裂解成较短链烃分子。
5. 产品分离:裂化反应后,得到混合产品,通过分馏塔将产品进行分离,得到汽油、柴油等各种石油产品。
6. 催化剂再生:用过的催化剂需通过再生系统进行再生,以恢复其活性。
催化裂化工艺是炼油厂中一项复杂而重要的工艺,通过裂解原油,提高产品附加值,提高炼油厂的经济效益。
同时,催化裂化工艺也面临着环保和安全等方面的挑战,需要技术和设备的不断改进与升级。
我国催化裂化工艺技术进展
我国催化裂化工艺技术进展催化裂化工艺技术是一种将重质烃类裂解为轻质烃类和汽油等燃料的重要手段。
在我国,随着石油化工行业的快速发展,催化裂化工艺技术也取得了显著的进步。
本文将简要回顾我国催化裂化工艺技术的发展历程,介绍技术创新与应用情况,并展望未来的发展前景。
自20世纪50年代以来,我国催化裂化工艺技术经历了从引进到自主研发的过程。
早期,我国从国外引进了一批先进的催化裂化装置和技术,在消化吸收的基础上,逐渐开始自主创新。
到20世纪80年代,我国已成功开发出具有自主知识产权的催化裂化工艺技术,并在大型工业装置上得到应用。
进入21世纪,我国催化裂化工艺技术水平进一步提升,已成为世界催化裂化工艺技术的重要研发和应用大国。
近年来,我国催化裂化工艺技术在技术创新和应用方面取得了许多重要成果。
在催化剂的种类和性能方面,通过优化制备工艺和组分设计,成功开发出多种高效、环保型催化剂。
这些催化剂在提高产品收率、降低能源消耗、减少污染物排放等方面具有显著优势。
在反应器设计方面,我国已成功开发出多套具有自主知识产权的反应器设计。
这些反应器在提高原料适应性、优化产品分布、降低能源消耗等方面表现出色。
例如,某新型反应器采用独特的结构设计,有效提高了催化剂的利用率和产品的分离效果,降低了装置的运行成本。
展望未来,我国催化裂化工艺技术将继续深入研究和技术创新。
随着环保要求的日益严格,开发高效、环保型催化裂化工艺技术将成为重要方向。
通过优化催化剂和反应器设计,降低污染物排放,提高资源利用率,实现绿色生产。
市场对燃料油和化工产品的需求将持续增长,因此催化裂化工艺技术的研究和应用将更加注重产品结构的优化和多样性的拓展。
例如,通过引入新的反应条件和原料,开发生产高附加值化学品的技术,提高企业的经济效益。
随着智能化和自动化的快速发展,催化裂化工艺技术将更加注重信息技术和自动化技术的应用。
通过建立自动化控制系统和实时监测分析系统,提高装置的运行效率和安全性,实现生产过程的智能化和信息化。
- 1、下载文档前请自行甄别文档内容的完整性,平台不提供额外的编辑、内容补充、找答案等附加服务。
- 2、"仅部分预览"的文档,不可在线预览部分如存在完整性等问题,可反馈申请退款(可完整预览的文档不适用该条件!)。
- 3、如文档侵犯您的权益,请联系客服反馈,我们会尽快为您处理(人工客服工作时间:9:00-18:30)。
催化裂化原料 催化裂化原料分为馏分油和渣油两大类。
1、Distillate Oil(馏分油)
(1)直馏重馏分油(350~500℃)
大多数直馏重馏分含芳烃较少,容易裂化,轻油收率较高, 是理想的催化裂化原料。
(2)热加工产物:焦化蜡油、减粘裂化馏出油等。
其中烯烃、芳烃含量较多,转化率低、生焦率高。不单独
• 5.正碳离子将H+ 还给催化剂,本身变成烯烃,反应中止。
催化裂化催化剂
一、催化裂化剂的种类、组成和结构
工业上使用的裂化催化剂归纳起来有三大类:
1、天然白土催化剂
催化裂化装置最初使用的经处理的天然白土,其主要活性 组分是硅酸铝。
2、无定型硅酸铝催化剂
天然白土被人工合成硅酸铝所取代。
• 无定型硅酸铝催化剂 • 硅酸铝的主要成分是氧化硅和氧化铝,合成硅酸铝依铝含量的不同又分 为低铝(含Al2O310%~13%)和高铝(含Al2O3约25%)二种。其催化剂 按颗粒大小又分为小球状(直径在3~6mm)和微球状(直径在40~80)。 • Al2O3、SiO2及少量水分是必要的活性组分,而其它组分是在催化剂的制 备过程中残留下来的极少量的杂质。合成硅酸铝是由Na2SiO3和Al2(SO4)3 溶液按一定的比例配合而成凝胶,再经水洗、过滤、成型、干燥、活化 而制成的。硅酸铝催化剂的表面具有酸性,并形成许多酸性中心,催化 剂的活性就来源于这些酸性中心,即催化剂的活性中心。
在全世界催化裂化装置的总加工能力中,提升管催化
裂化已占绝大多数。
流程图画面
催化裂化化学反应原理
• 一、单体烃催化裂化的化学反应 • (一)烷烃 • 烷烃主要发生分解反应,分解成较小分子的烷烃和烯烃, 烷烃分解时多从中间的C—C键处断裂,分子越大越容易 断裂
• (二)烯烃
• 烯烃的主要反应也是分解反应,但还有一些其它重要反应, 主要反应有: • (1)分解反应:分解为两个较小分子的烯烃,烯烃的分解 速度比烷烃高得多,且大分子烯烃分解反应速度比小分子 快,异构烯烃的分解速度比正构烯烃快。
• (四)抗重金属污染性能 • 重金属对催化剂的污染程度用污染指数表示: • 污染指数=0.1(Fe + Cu + 14Ni + 4V) • 式中:Fe 、 Cu 、 Ni 、 V 分别为催化剂上铁、铜、镍、钒的含量, 以表示。 • (五)流化性能和抗磨性能
• 为保证催化剂在流化床中有良好的流化状态,要求催化剂有适宜的粒 径或筛分组成。工业用微球催化剂颗粒直径一般在20~80之间。
CH2 CH2 CH CH CH3 CH3 CH3 +3H2
CH3 CH2
• (三)环烷烃 • 环烷烃的环可断裂生成烯烃,烯烃再继续进行上述各项反应;环烷烃 带有长侧链,则侧链本身会发生断裂生成环烷烃和烯烃;环烷烃可以 通过氢转移反应转化为芳烃;带侧链的五员环烷烃可以异构化成六员 环烷烃,并进一步脱氢生成芳烃。
油进行深度加工。
衡量原料性质的指标
馏分组成
化学组成
残炭 含氮含硫化合物 重金属 催化裂化产品特点 1、产品分布
气体:10~20%; 汽油:40~60%; 柴油:20~40%; 焦炭:5~10%。
2、产品特点
(1)气体产品 大量的是C3、C4,约占90%(重),液化气主要成分, 烯烃比烷烃多,为石油化工的宝贵原料。
无定形硅酸铝 低 长 差(焦炭产率高) 较差 较低(约600℃) 较低 较弱 可在0.5%左右
二、催化剂的使用性能
• (一)活性 • 活性是指催化剂促进化学反应进行的能力。对无定形硅酸铝催化剂,采 用D+L法,它是以待定催化剂和标准原料在标准裂化条件下进行化学反 应,以反应所得干点小于204℃的汽油加上蒸馏损失占原料油的重量百分 数,即(D+L)%来表示。工业上经常采用更为简便的间接测定方法—— KOH指数法。 • (二)选择性 表示催化剂增加目的产品.(汽油、柴油)和减少副产品(气体和焦炭)的选择 反应能力。 高活性的催化剂选择性不一定好,所以选择催化剂时必须考虑它的选择 性。 催化裂化反应通常用“汽油产率/焦炭产率”或“汽油产率/转化率”. 来表示催化剂的选择性好坏。 • (三)稳定性 • 催化剂在使用过程中保持其活性和选择性的性能称为稳定性。 • 常情况下,分子筛催化剂的稳定性比无定型硅酸铝催化剂好,无定型硅 酸铝催化剂中高铝的稳定性比低铝好,分子筛催化剂中Y型比X型的稳定 性好。
使用,与直馏馏分油掺合作为混合进料。
(3)润滑油溶剂精制的抽出油
含大量难以裂化的芳烃,尤其是稠环化合物,极易生焦。
(4)加氢裂化尾油
含饱和烃多,含杂质少,是催化裂化的理想原料。
2、Residue(渣油)
易于裂解的是高沸点烃类,最难裂解的是稠环芳烃、胶质 和沥青质。
为充分利用石油资源和↗原油加工的经济效益,必须对原
3、分子筛催化剂 分子筛催化剂 的应用是催化裂化技术的重大发展。
(1)特点
与无定型硅酸铝相比具有的特点:
选择性、活性和稳定性更高,比表面600~800m2/g;
稳定、均一的微孔结构。其大小为分子大小数量级; (2)结构 是由人工合成、具有微孔型立方晶格的硅铝酸盐。
依据其晶体内部孔穴大小而吸附或排斥不同物质的分子, 故又称为“分子筛”。 目前,应用于催化裂化的主要Y型分子筛,由AlO4和SiO4四 面体组成。主要有四种Y型分子筛:
REY:稀土-Y型分子筛 HY:HY型分子筛,以氢离子置换Na+ RE-HY:兼用氢离子和稀土金属离子置换Na+。 超稳Y型:HY型分子筛经脱铝得到的更高Si/Al。
一般催化裂化催化剂含分子筛为10~35%。
分子筛催化剂与无定形硅酸铝催化剂的性能比较
分子筛催化剂 性能 催化剂 裂解和异构活性高 短(约1~4秒) 好(焦炭产率低) 好 高(约700℃) 很高 较强 不大于0.2% 活性 所需反应时间 选择性 对热稳定性 再生温度 氢转移反应活性 抗重金属稳定性 对再生催化剂含炭 量的要求
• (三)剂油比(C/O)
• 剂油比是单位时间内进入反应器的催化剂Hale Waihona Puke (即催化剂循环量)与 总进料量之比。
• 提高剂油比,则催化剂上积炭少,催化剂活性下降小,转化率增加。 但催化剂循环量过高将降低再生效果。
(2)液体产品
汽油的辛烷值较高 含有较多烯烃(一般50%以上)、异构烷烃和芳烃,故辛
烷值较高,一般为90左右(RON)。
柴油的十六烷值低
含有较多的芳烃约为40~50%,故十六烷值较直馏柴
油低很多,只有20~30。 需要与直馏柴油等调合后才能使用。
(3) Coke(焦炭) 焦炭沉积在Cat.上,不能作产品。 由此可见:
催化裂化是重油轻质化过程;
主要目的:生产高辛烷值汽油,同时↗柴油产率。
概述
一、催化裂化在炼油过程中的地位 催化裂化是现代化炼油厂用来改质重质馏分和渣油的 核心技术。
我国车用汽油70--80%是
产量, Mt/a
800 700 600 500 400 300 200 100 0 1991 1993 1995 1997 1999 2001 时间,年份
• (2)异构化反应:该反应包括二种,其一是分子骨架异
构,另一种双键异构(分子中双键向中间位置转移)。
CH3 CH2 CH2 CH2 CH CH2
CH3 CH2 CH CH2
CH3 CH2 CH CH CH2 CH3
CH3 C CH3 CH2
• (3)氢转移反应:二个烯烃分子之间发生氢转移反应, 一个获得氢变成烷烃,另一个失去氢转化为多烯烃及芳烃 或缩合程度更高的分子,直到缩合至焦炭。氢转移反应是 烯烃的重要反应,是催化裂化汽油饱和度较高的主要原因, 但反应速度较慢,需要较高活性催化剂。 • (4)芳构化反应:烯烃环化并脱氢生成芳香烃。
催化裂化工艺主要操作条件
• 一、催化裂化反应操作的影响因素
• (一)反应温度 • 一方面,反应温度高则反应速度增大。当反应温度升高时,热裂化 反应的速度提高比较快,当温度高于500℃时,热裂化趋于重要,产 品中出现热裂化产品的特征(气体中C1、C2多,产品的不饱和度上 升)。但是,即使这样高的温度,催化裂化的反应仍占主导地位。 另一方面,反应温度可以通过对各类反应速率大小来影响产品的分 布和质量。温度升高汽油的辛烷值上升,但汽油产率下降,气体产 率上升,产品的产量和质量对温度的要求产生矛盾,必须适当选取温 度。 • 在我国要求多产柴油时,可采用较低的反应温度(460~470℃),在 低转化率下进行大回炼操作;当要求多产汽油时,可采用较高的反应 温度(500~510℃),在高转化率下进行小回炼操作或单程操作;多 产气体时,反应温度则更高。
催化裂化 Catalytic Cracking
概述
原油一次加工
常减压蒸馏:只可得10~40%的汽油、煤油、柴油等 轻质油品,其余为重质馏分和渣油。
原油二次加工
催化裂化:在催化剂作用下,在一定温度压力下,大
分子烃类裂化为较小分子的烃类的过程, 重质油轻质化的过程 催化重整:生产高辛烷值汽油及轻芳烃。 催化加氢:石油馏分在氢气存在下催化加工的过程。 产品精制:提高产品质量,满足产品规格要求。
• 我国用磨损指数来评价微球催化剂的机械强度
三、催化裂化催化剂失活与再生 1、催化剂的失活 催化剂的失活:在反应-再生过程中,催化剂的活性和
选择性不断下降的现象。
催化裂化催化剂失活性的原因 ①水热失活 在高温和水蒸气作用下,裂化催化剂的比表面积↙、 孔容↙,分子筛晶体结构破坏。
②结焦失活 焦炭沉积在催化剂的表面上,覆盖在催化剂的活性中
CH2 CH2 CH3
CH3 CH2 CH2 CH2 CH CH CH2 CH2 CH3