催化裂化工艺介绍
催化裂化工艺介绍

1。
0催化裂化催化裂化是原料油在酸性催化剂存在下,在500℃左右、1×105~3×105Pa 下发生裂解,生成轻质油、气体和焦炭的过程.催化裂化是现代化炼油厂用来改质重质瓦斯油和渣油的核心技术,是炼厂获取经济效益的重要手段。
催化裂化的石油炼制工艺目的:1)提高原油加工深度,得到更多数量的轻质油产品;2)增加品种,提高产品质量。
催化裂化是炼油工业中最重要的一种二次加工工艺,是重油轻质化和改质的重要手段之一,已成为当今石油炼制的核心工艺之一。
1。
1催化裂化的发展概况催化裂化的发展经历了四个阶段:固定床、移动床、流化床和提升管。
见下图:固定床移动床流化床提升管(并列式)在全世界催化裂化装置的总加工能力中,提升管催化裂化已占绝大多数。
1。
2催化裂化的原料和产品1。
2。
0原料催化裂化的原料范围广泛,可分为馏分油和渣油两大类。
馏分油主要是直馏减压馏分油(VGO),馏程350—500℃,也包括少量的二次加工重馏分油如焦化蜡油等,以此种原料进行催化裂化称为馏分油催化裂化。
渣油主要是减压渣油、脱沥青的减压渣油、加氢处理重油等。
渣油都是以一定的比例掺入到减压馏分油中进行加工,其掺入的比例主要受制于原料的金属含量和残炭值.对于一些金属含量低的石蜡基原有也可以直接用常压重油为原料。
当减压馏分油中掺入渣油使通称为RFCC。
以此种原料进行催化裂化称为重油催化裂化。
1。
2.1产品催化裂化的产品包括气体、液体和焦炭。
1、气体在一般工业条件下,气体产率约为10%-20%,其中含干气和液化气。
2、液体产物1)汽油,汽油产率约为30%-60%;这类汽油安定性较好。
2)柴油,柴油产率约为0—40%;因含较多芳烃,所有十六烷值较低,由重油催化裂化得到的柴油的十六烷值更低,这类柴油需经加氢处理。
3)重柴油(回炼油),可以返回到反应器内,已提高轻质油收率,不回炼时就以重柴油产品出装置,也可作为商品燃料油的调和组分。
4)油浆,油浆产率约为5%—10%,从催化裂化分馏塔底得到的渣油,含少量催化剂细粉,可以送回反应器回炼以回收催化剂。
催化裂化工艺
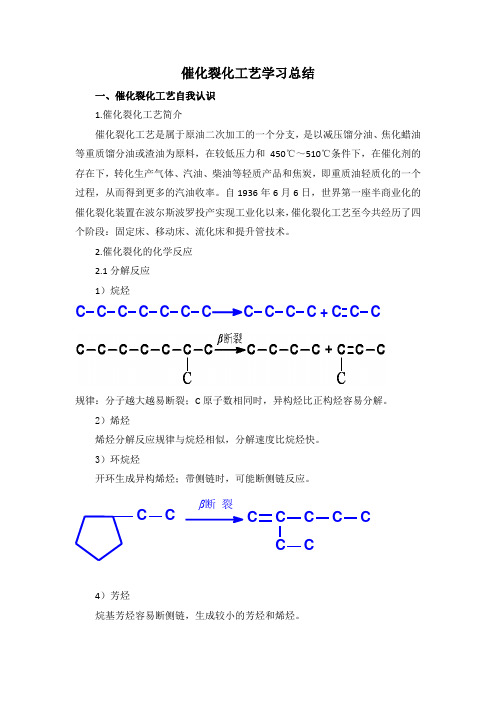
催化裂化工艺学习总结一、催化裂化工艺自我认识1.催化裂化工艺简介催化裂化工艺是属于原油二次加工的一个分支,是以减压馏分油、焦化蜡油等重质馏分油或渣油为原料,在较低压力和450℃~510℃条件下,在催化剂的存在下,转化生产气体、汽油、柴油等轻质产品和焦炭,即重质油轻质化的一个过程,从而得到更多的汽油收率。
自1936年6月6日,世界第一座半商业化的催化裂化装置在波尔斯波罗投产实现工业化以来,催化裂化工艺至今共经历了四个阶段:固定床、移动床、流化床和提升管技术。
2.催化裂化的化学反应2.1分解反应1)烷烃C C C C C C C C C C C + C C C规律:分子越大越易断裂;C原子数相同时,异构烃比正构烃容易分解。
2)烯烃烯烃分解反应规律与烷烃相似,分解速度比烷烃快。
3)环烷烃开环生成异构烯烃;带侧链时,可能断侧链反应。
β断裂C C C C C C CC C4)芳烃烷基芳烃容易断侧链,生成较小的芳烃和烯烃。
C C CC+ C C C C规律:至少3个C 的侧链才易脱落,脱乙基较困难;侧链越长、异构程度越大,越容易脱落。
2.2异构化反应分子量不变只改变分子结构的反应。
2.3氢转移反应某烃分子上的氢脱下来加到另一烯烃分子上使之饱和的反应。
氢转移是催化裂化特有的反应。
其中二烯烃最易接受氢转化为单烯烃,故产品中二烯烃很少。
2.4芳构化反应所有能生成芳烃的反应。
也是催化裂化的主要反应。
2.5叠合反应烯烃与烯烃合成大分子烯烃的反应。
随叠合深度不断加深,最终将生成焦炭。
与叠合相反的分解反应占优势,故催化裂化过程叠合反应不显著。
2.6烷基化反应烯烃与芳烃或烷烃的加合反应。
3.催化裂化工艺流程催化裂化装置一般由3个部分组成:1)反应-再生系统 由提升管反应器和再生器构成:反应器内发生催化裂化反应;再生器内进行催化剂再生。
反应沉降器在反应器的上部,反应器出来的反应油气进入反应沉降器进行催化剂和油气的自由沉降分离,没有沉降下来的催化剂进入设在沉降器顶部的旋风分离器进行继续进行分离。
催化裂化工艺

nm,比表面积可达500—700m2/g。 ➢硅酸铝的催化活性来源于其表面的酸性。
第31页/共84页
分子筛催化剂特点
➢分子筛催化剂在催化裂化中的应用是催化裂化 技术的重大发展。分子筛催化剂是60年代发展 起来的一种新型的高活性催化剂。它的出现, 使流化催化裂化工艺发生了很大变化,装置处 理能力显著提高,产品产率及质量都得到改善。
显微镜下的催化裂解催化剂
第36页/共84页
分子筛催化剂的组成
➢ 活性组元分子筛:ZSM-5和Y. ZSM-5作添加剂,占 15~50%; ➢ 基质或者称之为载体:一般为高岭土或合成基质,占20~70%; ➢ 粘结剂:铝溶胶、硅溶胶或硅铝溶胶; ➢ 添加物或助剂成分:抗Ni、V、N等。
0.50 0.75
1.00
金属在催化剂上的含量,(W)%
第24页/共84页
金属污染对产氢量的影响
氢,Nm3/ m3
800-
Ni
600-
400-
200-
镍
的
脱
氢
功
能
V
高
于
钒
01000 2000 3000 4000 5000 6000
催化剂上的金属含量,ppm
第25页/共84页
金属污染对焦炭产率的影响
➢1965年五朵金花之一的流化催化裂化在抚顺石油二厂建 成投产。五朵金花:催化裂化、催化重整、延迟焦化、尿 素脱蜡、微球催化剂与添加剂。
➢1974年我国建成投产了第一套提升管催化裂化工业装置 。
➢随着催化剂和催化工艺的发展,其加工的原料逐步重质化、 劣质化。
第5页/共84页
催化裂化工艺流程
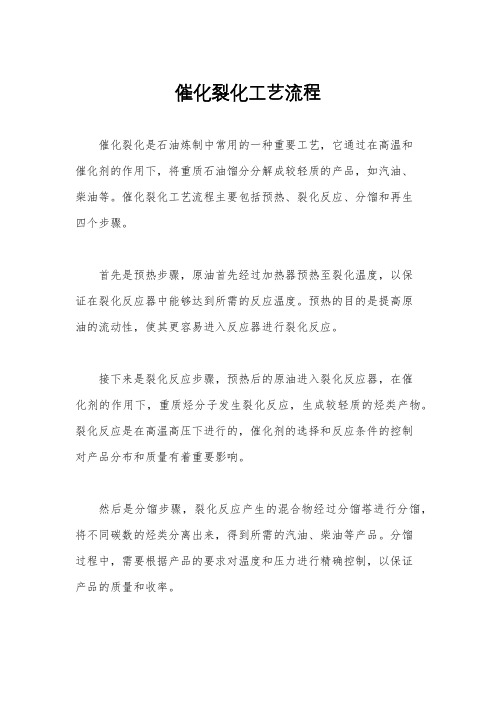
催化裂化工艺流程
催化裂化是石油炼制中常用的一种重要工艺,它通过在高温和
催化剂的作用下,将重质石油馏分分解成较轻质的产品,如汽油、
柴油等。
催化裂化工艺流程主要包括预热、裂化反应、分馏和再生
四个步骤。
首先是预热步骤,原油首先经过加热器预热至裂化温度,以保
证在裂化反应器中能够达到所需的反应温度。
预热的目的是提高原
油的流动性,使其更容易进入反应器进行裂化反应。
接下来是裂化反应步骤,预热后的原油进入裂化反应器,在催
化剂的作用下,重质烃分子发生裂化反应,生成较轻质的烃类产物。
裂化反应是在高温高压下进行的,催化剂的选择和反应条件的控制
对产品分布和质量有着重要影响。
然后是分馏步骤,裂化反应产生的混合物经过分馏塔进行分馏,将不同碳数的烃类分离出来,得到所需的汽油、柴油等产品。
分馏
过程中,需要根据产品的要求对温度和压力进行精确控制,以保证
产品的质量和收率。
最后是再生步骤,裂化反应产生的催化剂在经过一段时间的使
用后会失活,需要进行再生。
再生过程包括焙烧和再生氢化两个步骤,通过高温气体的通入和催化剂的洗涤,使催化剂重新获得活性,可以继续用于裂化反应。
总的来说,催化裂化工艺流程是一个复杂的过程,需要对原油
的性质、催化剂的选择、反应条件的控制等方面进行精确的把握。
只有在各个步骤都能够得到合理的设计和操作,才能够得到高质量
的裂化产品。
同时,随着石油资源的日益枯竭和环保要求的提高,
对催化裂化工艺的研究和改进也变得日益重要,希望在未来能够有
更多的突破和创新,为炼油行业的发展做出更大的贡献。
催化裂化rtc工艺技术

催化裂化rtc工艺技术催化裂化是一种重要的炼油工艺,用于将原油中的重质烃类分解为较轻质的产品。
催化裂化工艺技术(RTC)是催化裂化的一种改进技术,能够提高裂化效率和产品质量。
催化裂化RTC工艺技术主要包括三个方面的改进:催化剂的优化、反应器的改进和生产过程的改进。
首先,催化剂的优化是提高催化裂化效率的关键。
采用高活性和高选择性的催化剂,能够促进裂化反应的进行,同时减少副反应的发生。
通过选择合适的催化剂组分和处理方法,能够提高催化剂的稳定性和寿命,延长其使用寿命。
其次,反应器的改进是提高裂化效率和产品质量的重要手段。
通过优化反应器的结构设计和工艺参数的控制,能够提高裂化反应的效率和产量。
例如,采用多级反应器系统,可以充分利用热量和物料的传递,提高产物的收率和产品质量。
此外,采用先进的控制技术和自动化设备,能够实现反应器系统的精确控制,提高产品的稳定性和一致性。
最后,生产过程的改进是提高催化裂化RTC工艺技术的关键。
通过优化原油的预处理和催化裂化的操作条件,可以提高裂化反应的效率和选择性。
例如,采用适当的预处理方法,如加氢处理和脱盐处理,能够去除原油中的杂质和重金属,减少催化剂中毒和磨损。
此外,通过优化操作参数,如温度、压力和进料比等,能够更好地控制反应的进行,提高产品的质量和产量。
催化裂化RTC工艺技术具有以下优势:一是能够提高炼油厂的利润和竞争力。
采用RTC技术,能够提高裂化产物的收率和产品质量,同时减少能耗和废水废气的排放,降低生产成本。
二是能够提高产品的附加值和市场竞争力。
通过优化裂化产物的组分和品质,能够提高产品的附加值,满足市场需求。
三是对环境保护具有积极作用。
采用RTC技术,能够减少能源消耗和废物排放,降低对环境的污染。
总之,催化裂化RTC工艺技术是一种重要的炼油工艺技术,能够提高裂化效率和产品质量。
通过催化剂的优化、反应器的改进和生产过程的改进,能够实现催化裂化过程的精确控制,提高产品的收率和附加值,同时降低能耗和环境污染。
催化裂化的工艺特点及基本原理

催化裂化的工艺特点及基本原理催化裂化是一种重要的石油加工工艺,其开发和应用对于提高石油产业发展水平具有重要的意义。
催化裂化工艺的特点和基本原理如下:一、工艺特点:1.高选择性:催化裂化工艺可以将石油馏分中的大分子烃化合物按照其碳数分解为较低碳数的烃化合物,其中可选择的烃化合物主要是汽油和液化气。
因此,催化裂化可以提高汽油和液化气产率,达到更好的操作经济效益。
2.产物分布广:催化裂化反应不仅可以生成汽油和液化气,还可以生成较低碳数的烃化合物,如乙烯、丙烯等。
因此,催化裂化反应可以提供多种不同碳数的烃化合物,满足不同需求。
3.增塔体积积极:催化裂化工艺采用固定床反应器,反应器内填充了催化剂颗粒,因此反应器体积较大。
大体积的反应器可以增加催化裂化反应的容量,提高石油裂解速率,并且还可以增加反应过程的稳定性和可控性。
4.废气利用:催化裂化反应产生的废气中含有非常丰富的烃化合物和能量,可以通过适当的处理和回收利用,从而得到更好的经济效益,并减少对环境的污染。
二、基本原理:催化裂化反应是通过催化剂的作用来进行的,其基本原理如下:1.裂解反应:石油中的长链烃化合物在催化剂的作用下发生热裂解反应,将大分子烷烃分解成较小分子的烃化合物。
这种反应是一个链状反应过程,会生成一系列的短链烃化合物和碳氢烃中间体。
2.重排反应:短链烃化合物和碳氢烃中间体在催化剂的作用下发生重排反应,重新组合成不同碳数的烃化合物。
3.芳构化反应:在催化裂化过程中,由于催化剂特殊的性质,烃化合物还会发生芳构化反应,生成芳烃类化合物,如苯、甲苯等。
4.积碳反应:由于裂化过程产生的碳元素会在催化剂表面析出,形成碳黑,导致催化剂失活。
因此,催化裂化还需要定期对催化剂进行再生,以保持其活性。
综上所述,催化裂化工艺具有高选择性、广泛的产物分布、增塔体积积极和废气利用等特点。
其基本原理包括裂解反应、重排反应、芳构化反应和积碳反应。
催化裂化工艺的开发和应用有助于提高石油产业的经济效益和环境可持续性。
简述催化裂化工艺原理
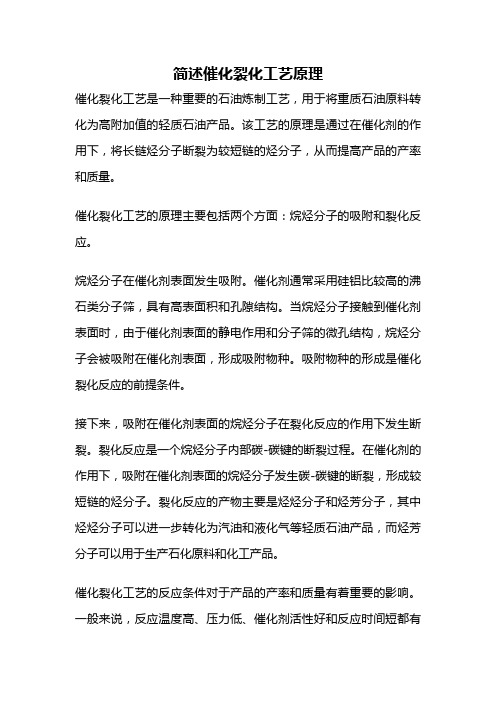
简述催化裂化工艺原理催化裂化工艺是一种重要的石油炼制工艺,用于将重质石油原料转化为高附加值的轻质石油产品。
该工艺的原理是通过在催化剂的作用下,将长链烃分子断裂为较短链的烃分子,从而提高产品的产率和质量。
催化裂化工艺的原理主要包括两个方面:烷烃分子的吸附和裂化反应。
烷烃分子在催化剂表面发生吸附。
催化剂通常采用硅铝比较高的沸石类分子筛,具有高表面积和孔隙结构。
当烷烃分子接触到催化剂表面时,由于催化剂表面的静电作用和分子筛的微孔结构,烷烃分子会被吸附在催化剂表面,形成吸附物种。
吸附物种的形成是催化裂化反应的前提条件。
接下来,吸附在催化剂表面的烷烃分子在裂化反应的作用下发生断裂。
裂化反应是一个烷烃分子内部碳-碳键的断裂过程。
在催化剂的作用下,吸附在催化剂表面的烷烃分子发生碳-碳键的断裂,形成较短链的烃分子。
裂化反应的产物主要是烃烃分子和烃芳分子,其中烃烃分子可以进一步转化为汽油和液化气等轻质石油产品,而烃芳分子可以用于生产石化原料和化工产品。
催化裂化工艺的反应条件对于产品的产率和质量有着重要的影响。
一般来说,反应温度高、压力低、催化剂活性好和反应时间短都有利于提高产品的产率。
此外,催化裂化工艺还需要添加适量的催化剂再生剂,以保证催化剂的活性和稳定性。
催化裂化工艺在石油炼制中具有广泛的应用。
通过该工艺可以将重质石油原料转化为高附加值的轻质石油产品,如汽油、柴油和液化气等。
同时,催化裂化工艺还可以提高石油产品的产率和质量,减少燃料的消耗和环境污染。
催化裂化工艺是一种重要的石油炼制工艺,通过在催化剂的作用下将重质石油原料转化为轻质石油产品。
该工艺的原理是在催化剂表面发生烷烃分子的吸附和裂化反应,从而提高产品的产率和质量。
催化裂化工艺在石油炼制中具有广泛的应用,为能源行业的发展做出了重要的贡献。
简述催化裂化工艺原理
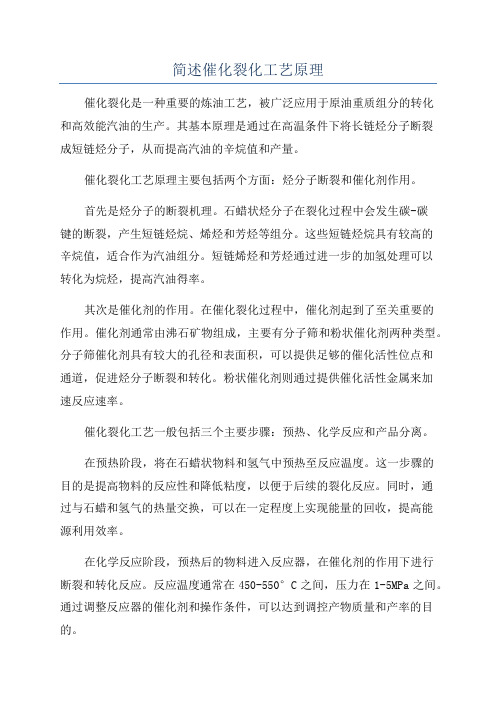
简述催化裂化工艺原理催化裂化是一种重要的炼油工艺,被广泛应用于原油重质组分的转化和高效能汽油的生产。
其基本原理是通过在高温条件下将长链烃分子断裂成短链烃分子,从而提高汽油的辛烷值和产量。
催化裂化工艺原理主要包括两个方面:烃分子断裂和催化剂作用。
首先是烃分子的断裂机理。
石蜡状烃分子在裂化过程中会发生碳-碳键的断裂,产生短链烃烷、烯烃和芳烃等组分。
这些短链烃烷具有较高的辛烷值,适合作为汽油组分。
短链烯烃和芳烃通过进一步的加氢处理可以转化为烷烃,提高汽油得率。
其次是催化剂的作用。
在催化裂化过程中,催化剂起到了至关重要的作用。
催化剂通常由沸石矿物组成,主要有分子筛和粉状催化剂两种类型。
分子筛催化剂具有较大的孔径和表面积,可以提供足够的催化活性位点和通道,促进烃分子断裂和转化。
粉状催化剂则通过提供催化活性金属来加速反应速率。
催化裂化工艺一般包括三个主要步骤:预热、化学反应和产品分离。
在预热阶段,将在石蜡状物料和氢气中预热至反应温度。
这一步骤的目的是提高物料的反应性和降低粘度,以便于后续的裂化反应。
同时,通过与石蜡和氢气的热量交换,可以在一定程度上实现能量的回收,提高能源利用效率。
在化学反应阶段,预热后的物料进入反应器,在催化剂的作用下进行断裂和转化反应。
反应温度通常在450-550°C之间,压力在1-5MPa之间。
通过调整反应器的催化剂和操作条件,可以达到调控产物质量和产率的目的。
最后,在产品分离阶段,通过一系列的分离操作,将裂化产物中的不同组分分离出来。
主要的分离方式包括蒸馏、吸附和萃取等。
其中,蒸馏是最主要的分离手段,可以将产物按烃碳数分为不同的馏分,进一步提纯和精制。
催化裂化工艺具有许多优点。
首先,可以将重质石油产品转化为高辛烷值的汽油,提高产品附加值和经济效益。
其次,可以通过调整催化剂和操作条件,实现灵活生产不同品质和组分的汽油。
再者,催化裂化可以与其他炼油工艺相结合,如加氢裂化、重整和烷基化等,进行综合重整和分子设计,进一步提高汽油产率和质量。
- 1、下载文档前请自行甄别文档内容的完整性,平台不提供额外的编辑、内容补充、找答案等附加服务。
- 2、"仅部分预览"的文档,不可在线预览部分如存在完整性等问题,可反馈申请退款(可完整预览的文档不适用该条件!)。
- 3、如文档侵犯您的权益,请联系客服反馈,我们会尽快为您处理(人工客服工作时间:9:00-18:30)。
1.0催化裂化催化裂化是原料油在酸性催化剂存在下,在500℃左右、1×105~3×105Pa 下发生裂解,生成轻质油、气体和焦炭的过程。
催化裂化是现代化炼油厂用来改质重质瓦斯油和渣油的核心技术,是炼厂获取经济效益的重要手段。
催化裂化的石油炼制工艺目的:1)提高原油加工深度,得到更多数量的轻质油产品;2)增加品种,提高产品质量。
催化裂化是炼油工业中最重要的一种二次加工工艺,是重油轻质化和改质的重要手段之一,已成为当今石油炼制的核心工艺之一。
1.1催化裂化的发展概况催化裂化的发展经历了四个阶段:固定床、移动床、流化床和提升管。
见下图:固定床移动床流化床提升管(并列式)在全世界催化裂化装置的总加工能力中,提升管催化裂化已占绝大多数。
1.2催化裂化的原料和产品1.2.0原料催化裂化的原料范围广泛,可分为馏分油和渣油两大类。
馏分油主要是直馏减压馏分油(VGO),馏程350-500℃,也包括少量的二次加工重馏分油如焦化蜡油等,以此种原料进行催化裂化称为馏分油催化裂化。
渣油主要是减压渣油、脱沥青的减压渣油、加氢处理重油等。
渣油都是以一定的比例掺入到减压馏分油中进行加工,其掺入的比例主要受制于原料的金属含量和残炭值。
对于一些金属含量低的石蜡基原有也可以直接用常压重油为原料。
当减压馏分油中掺入渣油使通称为RFCC。
以此种原料进行催化裂化称为重油催化裂化。
1.2.1产品催化裂化的产品包括气体、液体和焦炭。
1、气体在一般工业条件下,气体产率约为10%-20%,其中含干气和液化气。
2、液体产物1)汽油,汽油产率约为30%-60%;这类汽油安定性较好。
2)柴油,柴油产率约为0-40%;因含较多芳烃,所有十六烷值较低,由重油催化裂化得到的柴油的十六烷值更低,这类柴油需经加氢处理。
3)重柴油(回炼油),可以返回到反应器内,已提高轻质油收率,不回炼时就以重柴油产品出装置,也可作为商品燃料油的调和组分。
4)油浆,油浆产率约为5%-10%,从催化裂化分馏塔底得到的渣油,含少量催化剂细粉,可以送回反应器回炼以回收催化剂。
油浆经沉降出去催化剂粉末后称为澄清油,因多环芳烃的含量较大,所以是制造针焦的好原料,或作为商品燃料油的调和组分,也可作加氢裂化的原料。
3、焦炭焦炭产率约为5%-7%,重油催化裂化的焦炭产率可达8%-10%。
焦炭是缩合产物,它沉积在催化剂的表面上,使催化剂丧失活性,所以用空气将其烧去使催化剂恢复活性,因而焦炭不能作为产品分离出来。
1.3催化裂化工业装置的组成部分催化裂化生产装置主要由四个系统组成,即:反应-再生系统、分馏系统、吸收稳定系统和能量回收系统,其关系如图:(针对RFCC装置进行阐述)1、反应-再生系统反应-再生系统是本装置的重要组成部分。
预先经过加热的原料油通过提升管反应器变成反应产物,即各种产品的混合气体,再送到分馏系统处理,反应过程中生产的焦炭沉积到催化剂上不断地被送入两个再生器进行催化剂再生,在再生器中采用强制通风将沉积在催化剂上碳烧掉,烧焦放出的热量使催化剂及通入的风的温度均大大提高,催化剂带出的热量提供了反应所需的热量,高温空气则送去能量回收系统。
反应系统还包括催化剂的加料和卸料系统以及原料油的进行最后预热所用的加热炉。
2、分馏系统分馏系统地任务是把反应器送来的产物,油气混合物进行冷却并分成各种产品,使产品的主要性质合乎规定的质量标准,主要设备是分馏塔。
分馏塔顶分出粗汽油和最轻的气体部分(叫做富气),都送到吸收稳定系统进一步处理,而其中部和底部分别出轻柴油及油浆产品。
分馏系统还包括产品的热量回收系统(即换热系统),把各个产品带出的热量先通过换热器以预热原料油,然后才经冷却器至较低温度送出装置。
3、吸收稳定系统吸收稳定的任务是进行富气的分离和使汽油质量最后合乎要求,它包括富气压缩机、解吸塔、一、二级吸收塔、稳定塔及含氰污水水解塔几个部分。
富气首先经过压缩机升高压力后送到吸收塔并在塔顶分出干气,其余去稳定塔分出液化气和稳定汽油,粗汽油先进吸收塔作吸收油用,后在稳定塔分出,称为稳定汽油、达到蒸汽压指标合格。
在生产操作中这三个系统是紧密相联的整体。
反应再生系统是龙头,部分操作的变化会很快地反映和影响到分馏和吸收稳定系统,而后两个系统地操作变化也会反过来影响反应再生系统,不过分馏操作变化时影响面较大,而吸收稳定操作变化时对前两个系统地影响较小。
4、能量回收系统能量回收系统地任务是回收烧焦所用空气带出的高温热能及动力能,它主要由两部分组成,旋风和烟气机机组。
由两个再生器出来的烟气混合后入三级旋风分离器,进一步降低烟气中催化剂粉尘的浓度,由三旋出来后的烟入能量回收设备——烟气透平,进行能量回收。
烟气机机组由四部分组成:烟气透平、轴流式风机、蒸气透平、电动/发电机。
此四部分安装在同一轴上,正常运行时,在衡定转速下,由烟机及蒸气透平驱动,轴流式风机向两个再生器内供风,电动/发电机在发电状态进行发电。
1.4我国催化裂化类型1.5催化裂化工艺技术1.5.1催化裂化增产轻质油技术1、TSRFCC(两段提升管催化裂化)石油大学开发的两段管提升管催化裂化技术,强化和改善了催化反应过程,有效提高了反应深度、轻质油收率和液体产率,改善了产品质量,显著降低了催化汽油中的烯烃含量,增加了催化汽油中的异构烃和芳烃的含量,提高了汽油的辛烷值。
石油大学开发的两段提升管技术2、SCT——short contact time(短时接触)SCT是Exxon公司开发的。
主要通过FCC装置改造:1)新型进料喷嘴——Exxon公司的专利技术:改善了原料的雾化效果和剂油的接触状况,减少返混2)新型反应器出口系统:采用封闭式耦合旋分器,催化剂与裂化产物快速分离3)新型汽提体统:先进的分段汽提装置,更好地去除催化剂上携带的烃类,减少生焦。
3、MSCC——millisecond catalytic cracking(毫秒催化裂化)MSCC是UOP公司开发的,在MSCC过程中,催化剂向下流动形成催化剂帘,原料油水平注入与催化剂垂直接触,实现毫秒催化反应。
反应产物和待生催化剂水平移动,依靠重力作用实现油气与催化剂的快速分离。
主要通过FCC装置改造实现:1)催化剂下落,原料油水平喷入2)采用外置旋风分离器MSCC的特点:油剂接触时间极短;有效降低二次反应和热裂化反应;提高汽油和烯烃产率;降低焦炭产率。
2、催化裂化生产清洁汽油技术1)催化裂化汽油辅助反应器改质降烯烃技术石油大学(北京)催化汽油辅助反应器改质降烯烃技术,将重油提升管反应器得到的催化粗汽油打入辅助反应器进行改质降烯烃并多产丙烯。
装置主要生产高辛烷值、低烯烃汽油及富含丙烯的液化石油气和柴油。
原料经原料油雾化喷嘴进入主提升反应器;从分馏来的回炼油和回炼油浆混合后分两路经回炼油雾化喷嘴进入主提升管反应器,与690℃高温催化剂接触进行原料的升温、气化及反应,然后进入主沉降器。
主提升管反应器的出口温度为530℃。
反应后的油气与待生催化剂在提升管出口经粗旋风分离器(CSC)迅速分离后经升气管进入沉降器四组单级旋风分离器,再进一步除去携带的催化剂细粉后离开沉降器,进入分馏塔。
重油催化裂化的粗汽油由主分馏塔顶油气分离器出来,自粗汽油泵加压后,一部分去辅助提升反应器,其余进吸收塔。
回炼汽油经喷嘴进入辅助反应器的提升管下部,与其中的高温再生催化剂进行接触、气化、混合和反应,然后反应油气和催化剂进入辅助沉降器,再通过设在顶部的旋分系统将催化剂和反应油气分开,催化剂进入辅助反应器的汽提段,与汽提蒸汽进行逆流接触,汽提出催化剂夹带的油气。
汽提后的催化剂由待生斜管进入再生器。
改质后的油气经过油气管线进入辅助分馏塔。
2)MIP——Maximum iso-paraffinsMIP的设计思想是既保留提升管反应器具有高反应强度的特点,同时又能够进行某些二次反应以多产异构烷烃和芳烃。
为此设计了一种新型提升管反应器。
该反应器具一下特征:新型提升管反应器是在现有的提升管反应器基础上将反应器分成两个反应区(如图所示)第一反应区类似现有的提升管反应器,油气和催化剂混合后,在该反应区以一次裂解反应为主,采用较高的反应强度,即较高的反应温度和剂油比,生成较多的烯烃和处理较重的原料油,经较短的停留时间后进入扩径的第二反应区下部,该反应区与传统的提升管反应器的不同之处在于降低油气和催化剂的流速,可以注入急冷介质和采用其它措施,降低该区反应温度,以抑制二次裂化反应,增加异构化和氢转移反应,从而使汽油中的异构烷烃和芳烃含量增加;物流在该反应区停留时间较长,然后进入径向收缩的出口区,该区也类似传统的提升管反应器顶部出口部分,物流在该区停留时间较短,也是为了抑制过裂化反应和增加流体线速;然后物流进入分离系统进行气固分离,分离出的气相由旋风分离器出口引出,催化剂颗粒经汽提后进入再生器。
3)CGP4)FDFCC(灵活多效催化裂化工艺)灵活多效催化裂化工艺FDFCC采用一套设有两根提升管反应器的催化裂化装置,通过双提升管实现工艺操作的可选择性,为汽油理想二次反应提供独立改质空间和充分的反应时间,从而实现降低催化裂化汽油的烯烃含量和硫含量,改善柴汽比,提高催化汽油的辛烷值,同时增产液化气和丙烯的目的。
FDFCC特点是:原料适应性强;产品方案调节灵活,装置操作弹性大;催化剂适应能力强。
3、催化裂化多产低碳烯烃技术1)DCC(催化裂解工艺)催化裂解工艺是一项重油制取低碳烯烃技术。
该工艺是由中国石化石油化工科学研究院开发的,以重质油为原料,适用固体酸择形分子筛催化剂,在较缓和的反应条件下进行裂解反应。
DCC工艺具有两种操作方式——DCC-Ⅰ和DCC-Ⅱ。
DCC-Ⅰ选用较为苛刻的操作条件,在提升管加密相流化床反应器内进行反应,最大量生产以丙烯为主的气体烯烃;DCC-Ⅱ选用较缓和的操作条件,在提升管反应器内进行反应,最大量地生产丙烯、异丁烯和异戊烯等小分子烯烃,并同时兼产高辛烷值优质汽油。
2)MIO多产异构烯烃(MIO)工艺技术是石油化工科学研究院开发的最大量地生产异构烯烃的新工艺技术。
该工艺技术以掺炼部分渣油的重质馏分油为原料,使用RFC催化剂,在特定的工艺条件下,采用特定的反应工艺条件,以达到大量生产异构烯烃(异丁烯、异戊烯)和高辛烷值汽油的目的。
MIO工艺技术的催化剂为石油化工科学研究院开发的RFC专利催化剂。
它选用了新型催化材料和专利分子筛,具有良好的异构烯烃选择性和抑制氢转移反应的能力,可减少中间裂化产物烯烃进行氢转移反应的程度;它增加了反应物分子,特别是重油大分子对酸性中心的可接近性,加强了一次裂化深度;同时它优化了孔尺寸分布,较好地抑制了二次反应深度,改变了产物中碳三、碳四、碳五烯烃的比例。