沉镍金制作流程(精)
浅谈沉镍金工艺
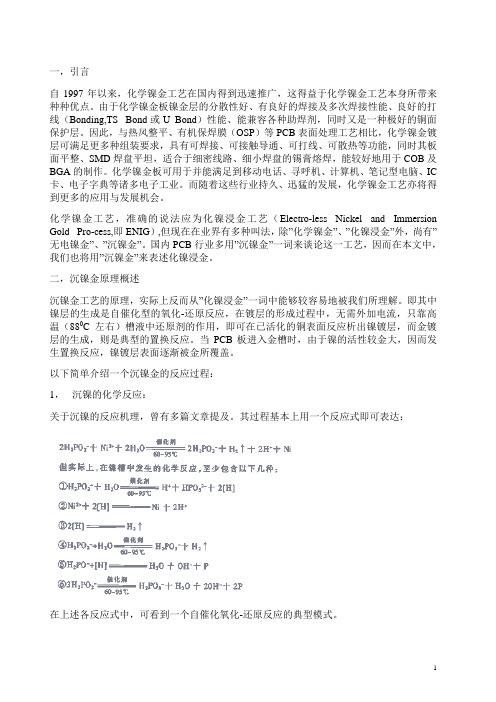
一,引言自1997年以来,化学镍金工艺在国内得到迅速推广,这得益于化学镍金工艺本身所带来种种优点。
由于化学镍金板镍金层的分散性好、有良好的焊接及多次焊接性能、良好的打线(Bonding,TS Bond或U Bond)性能、能兼容各种助焊剂,同时又是一种极好的铜面保护层。
因此,与热风整平、有机保焊膜(OSP)等PCB表面处理工艺相比,化学镍金镀层可满足更多种组装要求,具有可焊接、可接触导通、可打线、可散热等功能,同时其板面平整、SMD焊盘平坦,适合于细密线路、细小焊盘的锡膏熔焊,能较好地用于COB及BGA的制作。
化学镍金板可用于并能满足到移动电话、寻呼机、计算机、笔记型电脑、IC 卡、电子字典等诸多电子工业。
而随着这些行业持久、迅猛的发展,化学镍金工艺亦将得到更多的应用与发展机会。
化学镍金工艺,准确的说法应为化镍浸金工艺(Electro-less Nickel and Immersion Gold Pro-cess,即ENIG),但现在在业界有多种叫法,除”化学镍金”、”化镍浸金”外,尚有”无电镍金”、”沉镍金”。
国内PCB行业多用”沉镍金”一词来谈论这一工艺,因而在本文中,我们也将用”沉镍金”来表述化镍浸金。
二,沉镍金原理概述沉镍金工艺的原理,实际上反而从”化镍浸金”一词中能够较容易地被我们所理解。
即其中镍层的生成是自催化型的氧化-还原反应,在镀层的形成过程中,无需外加电流,只靠高温(880C左右)槽液中还原剂的作用,即可在已活化的铜表面反应析出镍镀层,而金镀层的生成,则是典型的置换反应。
当PCB板进入金槽时,由于镍的活性较金大,因而发生置换反应,镍镀层表面逐渐被金所覆盖。
以下简单介绍一个沉镍金的反应过程:1,沉镍的化学反应:关于沉镍的反应机理,曾有多篇文章提及。
其过程基本上用一个反应式即可表达:在上述各反应式中,可看到一个自催化氧化-还原反应的典型模式。
而在上述各反应中,需要注意的是反应⑤⑥,从中我们可看到有单体磷的生成,在沉镍过程中,此单体磷亦会一并沉于镍层中,因而,事实上的沉镍层,是磷镍构成。
PCB沉金工艺介绍
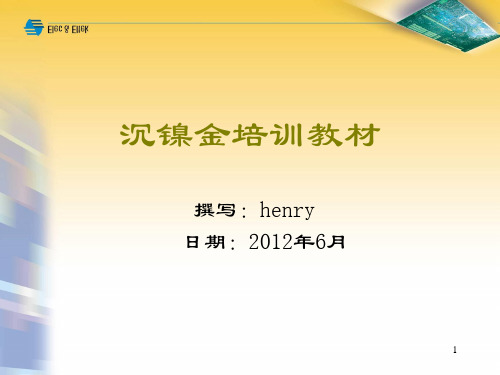
化学镍药水的分类:
按操作温度分可将镀液分成高温镀液(85950C)、中温镀液(65-750C)、低温 镀液(500C)以下
按其使用的还原剂又可大致分为次磷酸盐 型、硼氢化物型、肼型、胺基硼烷型4种。
26
按pH值分又可将其分为酸性镀液和碱性镀 液; 最常用的是次磷酸盐为还原剂的酸性高温 化学镀镍液,常称为普通化学镀镍液。
1.5 ±0.5min
搅拌:摆动及药液循环搅拌或空气打气
槽材质:PVC或PP
加热器:石英或铁弗龙加热器
15
铜浓度控制:
由于Cu2+对微蚀速率影响较大,通 常须将Cu2+的浓度控制在5-25g/l, 以保证微蚀速率处于0.5-1.5μm之间。 生产过程中,换缸时往往保留1/5-1/3 缸母液(旧液),以保持一定的Cu2+浓 度。
通常情况,不采用调节药水浓度或 升高温度来弥补因时间不足而引起的镍 厚不足,一定要根据客户镍层要求来设 置适当的镀镍时间。否则,可能引起活 性不稳定,会造成许多不良后果。
44
C、浓度: 不同供应商之不同系列药水,
其浓度控制范围各不相同。由于化 学镀镍的本身特点,其动态平衡的 控制难度远远大于化学镀铜,其控 制范围很窄则可说明这一点。因此, 尽可能使用自动补料器来控制药水 浓度,手动补料是很难保证每一个 制板的良品率。
• B、随着NaH2PO2和NiSO4浓度的增加, 沉积速度逐渐提高,而后趋于稳定或稍 有降低。但此时溶液的稳定性下降;
40
•C、化学镀镍层的厚度一般控制4~5μm, 最少要大于2.5μm厚的镍磷层才能起到 有效的阻挡层作用,防止铜的迁移,以免渗 出金面,氧化后导致导电性不良;
•D、镀覆PCB的装载量(裸铜面)应适 中,以0.1~0.5dm2/L为宜。负载太大会导 致镍缸活性逐渐升高,甚至导致反应失 控,造成严重后果;负载太低会导致镍 缸活性逐渐降低,造成漏镀等问题。
化镍沉金作业办法
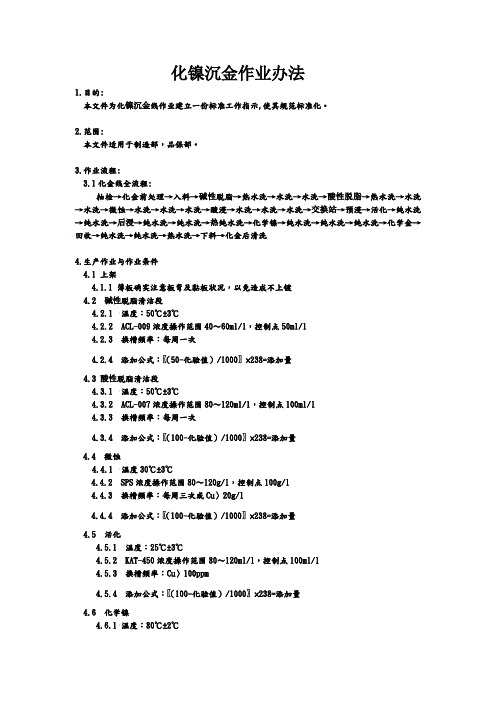
化镍沉金作业办法1.目的:本文件为化镍沉金线作业建立一份标准工作指示,使其规范标准化。
2.范围:本文件适用于制造部,品保部。
3.作业流程:3.1化金线全流程:抽检→化金前处理→入料→碱性脱脂→热水洗→水洗→水洗→酸性脱脂→热水洗→水洗→水洗→微蚀→水洗→水洗→水洗→酸浸→水洗→水洗→水洗→交换站→预浸→活化→纯水洗→纯水洗→后浸→纯水洗→纯水洗→热纯水洗→化学镍→纯水洗→纯水洗→纯水洗→化学金→回收→纯水洗→纯水洗→热水洗→下料→化金后清洗4.生产作业与作业条件4.1 上架4.1.1 薄板确实注意板弯及黏板状况,以免造成不上镀4.2 碱性脱脂清洁段4.2.1 温度:50℃±3℃4.2.2 ACL-009浓度操作范围40~60ml/l,控制点50ml/l4.2.3 换槽频率:每周一次4.2.4 添加公式:〖(50-化验值)/1000〗×238=添加量4.3 酸性脱脂清洁段4.3.1 温度:50℃±3℃4.3.2 ACL-007浓度操作范围80~120ml/l,控制点100ml/l4.3.3 换槽频率:每周一次4.3.4 添加公式:〖(100-化验值)/1000〗×238=添加量4.4 微蚀4.4.1 温度30℃±3℃4.4.2 SPS浓度操作范围80~120g/l,控制点100g/l4.4.3 换槽频率:每周三次或Cu〉20g/l4.4.4 添加公式:〖(100-化验值)/1000〗×238=添加量4.5 活化4.5.1 温度:25℃±3℃4.5.2 KAT-450浓度操作范围80~120ml/l,控制点100ml/l4.5.3 换槽频率:Cu〉100ppm4.5.4 添加公式:〖(100-化验值)/1000〗×238=添加量4.6 化学镍4.6.1 温度:80℃±2℃4.6.2 添加方式为自动添加4.6.3 浓度操作范围依MTO上升范围4.3~5.0g/l4.6.3.1 镍含量每上升0.5个MTO 镍标准值上升0.1g/l4.6.3.2 PH操作点4.6 操作范围4.4~4.84.6.3.3 SHP: Ni含量每上升1个MTO SHP上升1g/l4.6.3.4 添加公式:NPR-4A的添加量为:(4.5-化验值)X 682/100=添加量(L)其它主份的添加量按照如下比例添加:NPR-4A:NPR-4B:NPR-4C:NPR-4D=1:1:1:0.5 .当分析值与标准值偏差太大时或NPR-4A一次性的添加量大于4L时,则添加按照如下方式进行:NPR-4A:NPR-4M:NPR-4D=45:150:0.54.6.4 换槽频率:4.6.4.1 手动添加MTO值高于3.5以上,低于4.0以下时4.6.4.2 整流器定电压0.9V,电流值大于1.0以上时4.6.4.3 NPR-4D药水连续添加三次(每次500ml,亦即一小时内添加1500ml),镍层厚度依旧无法高于110μ时4.6.5 当班不生产必须将加热器切至OFF,以防止A,B,C,D,M剂挥发,造成镍槽A,B,C,D,M剂比例不对4.7.1 金槽4.7.1.1 温度:85℃±3℃4.7.1.2 TCL-61浓度操作范围160~240ml/l控制点200ml/l4.7.1.3 Au浓度操作范围1.0~3.0g/l操作点2.04.7.1.4 换槽频率:Ni含量超过900ppm或Cu含量超过8ppm即可换槽4.7.1.5 TCL-61-M5添加公式:〖(200-化验值)/1000〗×520=添加量4.7.1.6 Au添加公式:〖(2.0-化验值)/0.683〗×520=添加量4.7.1.7 PH调整方式:每调升0.1,添加氨水150ml;每调降0.1,添加柠檬酸150g4.7.2 槽液浓度调整:4.7.2.1 生产1000SF则各槽药水添加量如下:脱脂槽ACL-007=1.5L,微蚀槽SPS=3.0kg,活化槽KAT-450=3.5L(Cu含量〈19ppm〉、4.0L(Cu含量20~49ppm)、4.5L(Cu含量50~79ppm)金槽TCL-61=2.5L,Au=94g4.7.2.2 依照化验数据作适当德调整补充,控制点为其操作范围之中心值。
ENIG培训资料(沉镍浸金)
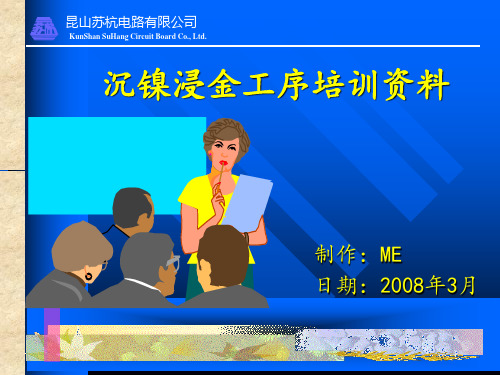
如果遇特殊情况停电时,活化槽以后的板要走 完全流程,活化前的板取出水洗即可。
如果停线不生产,需要将镍槽温度降低到65度, 并且将自动添加系统关闭。
精品文档
23
昆山苏杭电路板有限公司
未重新开缸时: 挂5块(18“×24”)铜板或相当尺寸磨板后的 拖缸板,其后接着挂生产板,进入正常生产阶 段。 停产24小时以上重新开线时要延时 15min~ 30min,才能进入正常生产阶段。
精品文档
22
昆山苏杭电路板有限公司
KunShan SuHang Circuit Board Co., Ltd.
30
昆山苏杭电路板有限公司
KunShan SuHang Circuit Board Co., Ltd.
问题描述
原因
常见问题处理 解决方法
2、镍厚不足
1、PH太低
1、调高pH值
2、温度太低
2、提高温度
3、拖缸板不足够 3、拖缸
4、镍缸超过4MTO 4、更换镍缸
精品文档
31
昆山苏杭电路板有限公司
KunShan SuHang Circuit Board Co., Ltd.
常温
精品文档
15
昆山苏杭电路板有限公司
KunShan SuHang Circuit Board Co., Ltd.
4、预浸
工艺流程介绍
预浸作用: 1、保持铜面新鲜状态,无氧化物存在。 2、维持活化槽中的酸度. 参数控制:
主要项目 H2SO4 时间
工艺范围 10 – 30 ml/l
30“
沉镍金
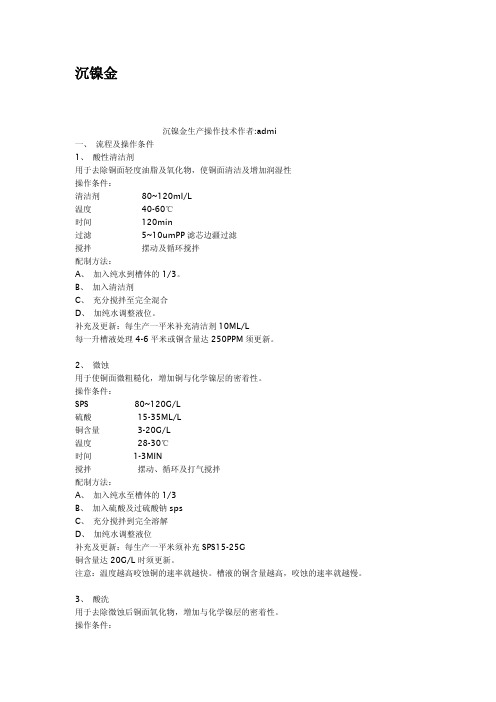
B、 启动循环泵循环 2 小时以上或直到槽壁灰黑色沉积物完全去除为止(如有需要可加热至
40-50 度)
C、 排出硝酸液,并加水循环 10-20 分钟后,排放,至少更换两次以上。
D、 加纯水循环 10-20 分钟,并用 PH 试纸确认 PH 值在 4.5 以上,排放。如 PH 值未达到 4.5
以上则需要重复清洗
3、 酸洗 用于去除微蚀后铜面氧化物,增加与化学镍层的密着性。 操作条件:
硫酸(98%)
40-80ML/L
温度
室温
时间
1-3MIN
搅拌
摆动及循环搅拌
配制方法:
A、 加入纯水至槽体的 1/3
B、 加入硫酸
C、 充分搅拌到完全混合
D、 加纯水调整至液位
补充及更新:每一平米补充硫酸 2-5ML
每 1L 槽液处理 4-6 平米或铜含量达 2000PPM 时须换槽
2、 NAOH 溶液浸泡后洗净——3~5%NAOH 溶液加热至 50℃,4-6 小时循环后洗净 3、 加水至操作液位及升温——启动循环泵,管路试漏 4、 硝酸纯化——68%浓硝酸加水稀释 1 倍后,循环 2-3 小时,室温 12 小时以上浸渍 5、 水洗及中和——水洗 2 次以上,使用 PH 试纸确认 PH 为 4.5 以上 6、 最终杂质去除及纯水洗——干净吸水布料或无尘纸擦试过滤筒内洗净 7、 建浴 B、 挂架的洗净——用 3%硫酸浸渍 2 小时后洗净。 C、 金槽及各药液槽 1、 杂质去除及水洗 2、 3%NAOH 浸渍 4-8 小时后洗净 3、 加水后循环,管路试漏 4、 升温测试 5、 杂质去除,水洗 6、 3%硫酸循环 2 小时后,用纯水洗(金槽使用 20%柠檬酸) 7、 建浴
铜含量达 5PPM 或镍含量达 900PPM 时须更新
沉镍金流程

3
一、什么是化学镀
化学镀是在金属的催化作用 下,通过可控制的氧化还原 反应产生金属沉积的过程。
4
化学镀应具备的条件:
1、氧化还原电位应显著低于金属 还原电位; 2、溶液不产生自发分解,催化时 才发生金属沉积; 3、PH值、温度可以调节镀覆速度; 4、具有自催化作用; 5、溶液有足够寿命。
5
镀液成分:
9
第二部分
沉镍金原理及工艺流程
10
一、沉镍金原理 催化 化学镀镍 浸金
(一)、催化(活化) • 作用:为化学镍提供催化晶体 • 反应式:Pd2++Cu Pd+Cu2+
11
(二)、化学镍 • 作用:在钯的催化作用下,Ni2+在NaH2PO2的还
原条件下沉积在裸铜表面。当镍沉积覆盖钯催 化晶体时,自催化反应将继续进行,直至达到 所需之镍层厚度。
21
3、铜浓度控制:
由于Cu2+ 对微蚀速率影响较大, 通常须将Cu2+的浓度控制在5-25g/l, 以保证微蚀速率处于0.5-1.5μm之间。 生产过程中,换缸时往往保留1/5-1/3 缸母液(旧液),以保持一定的Cu2+ 浓 度。
22
4、逆流水洗:
由于带出的微蚀残液,会导致铜 面在水洗过程中迅速氧化,所以微蚀 后水质和流量以及浸泡时间都须特别 考 虑 。否 则 ,预 浸 缸会 产 生太 多 的 Cu2+ ,继而影响钯缸寿命。所以,在 条件允许的情况下(有足够的排缸), 微蚀后二级逆流水洗,之后再加入5% 左右的硫酸浸洗,经二级逆流水洗后 进入预浸缸。
1、微蚀药剂组成:
过硫酸钠Na2S2O8 硫酸H2SO4 H 作用: 酸性过硫酸钠微蚀液用于使铜面微 粗糙化,增加铜与化学镍层的密着性。 沉镍金生产也有使用硫酸双氧水或酸性 过硫酸钾微蚀液来进行的。
PCB沉金工艺介绍

镀液中镍离子浓度不宜过高,镀液中镍离子 过多会降低镀液的稳定性,容易形成粗糙的 镀层,甚至可能诱发镀液瞬时分解,继而析 出海绵状镍。镍离子与次磷酸盐浓度的最佳 摩尔比应在0.4左右 B、还原剂 化学镀镍的主要成分,它能提供还原镍离 子所需要的电子。 在一定范围内镍沉积的反应速度与次磷酸 盐的浓度成正比,因而次磷酸盐的浓度直 接影响着反应的沉积速率,
锌、铅、镉、锑及某些有机或无机含硫化合物 如硫脲以及三氯化钼都是化学镀镍的催化剂毒 物,如含量很少时,对镀液有一定的稳定作用, 但若含量过高会使镀液失效导致镍不能沉积出 来。
31
镍沉积速度影响因素
A B 温度 PH值
CDΒιβλιοθήκη 缸老化度(正常生产时老化度以MTO来衡量)
主盐(NiSO4)浓度
E
F
•
还原剂(NaH2PO2) 浓度
41
•E、镀液应连续过滤,以除去溶液中的 固体杂质。镀液加热时,必须要有空气 搅拌或连续循环系统,使被加热的镀液 迅速扩散开。当槽内壁镀有镍层时,应 及时用硝酸(1:3)褪除,适当时可考虑加 热,但不可超过50OC, 以免污染空气。 •F、镀液寿命一般控制在4MTO(即Ni离 子添补量累积达到4倍开缸量),超过此 限主要问题是镍厚不足。
其含义是:
在裸铜面进行化学镀镍,然后化学浸金。
5
四、沉镍金工艺的目的
• 沉镍金工艺既能满足日益复杂的PCB装配、 焊接的要求,又比电镀镍金的成本低,同 时还能对导线的侧边进行有效的保护,防 止在使用过程中产生不良现象。 AU Ni CU
6
五、沉镍金工艺的用途
化学镍金镀层集可焊接、可接触导通,可打线、 可散热等功能于一身,是 PCB 板面单一处理却具 有多用途的湿制程。 化学镍的厚度一般控制在 4-5μm,其不但对铜面进行有效保护,防止铜的 迁移,而且具备一定硬度和耐磨性能,同时拥有 良好的平整度。浸金的厚度一般控制在 0.050.1μm,其对镍面具有良好的保护作用,而且具 备很好的接触导通性能。
(完整版)沉镍金流程

达到所需之镍层厚度。
• 化学反应: Ni2+ +2H2PO2- +2H2O
Ni
+2HPO32-+4H++H2
• 副反应: 4H2PO2+2P+2H2O+H2
2HPO32-
12
反应机理
• H2PO2- +H2O HPO32-+H++2H • Ni2++2H Ni+2H+ • H2PO2-+H OH-+P+H2O • H2PO2- + H2O HPO32-+H++H2
20
2、操作条件:
Na2S2O8: H2SO4: Cu2+ :
100±20g/l 20 ±10g/l 5~25g/l
温度:
30 ±2OC
时间:
1.5 ±0.5min
搅拌:摆动及药液循环搅拌或空气打气
槽材质:PVC或PP
加热器:石英或铁弗龙加热器
21
3、铜浓度控制:
由于Cu2+对微蚀速率影响较大,通 常 须 将 Cu2+ 的 浓 度 控 制 在 5-25g/l , 以保证微蚀速率处于0.5-1.5μm之间。 生产过程中,换缸时往往保留1/5-1/3 缸母液(旧液),以保持一定的Cu2+浓 度。
22
4、逆流水洗:
由于带出的微蚀残液,会导致铜 面在水洗过程中迅速氧化,所以微蚀 后水质和流量以及浸泡时间都须特别 考虑。否则,预浸缸会产生太多的 Cu2+,继而影响钯缸寿命。所以,在 条件允许的情况下(有足够的排缸), 微蚀后二级逆流水洗,之后再加入5% 左右的硫酸浸洗,经二级逆流水洗后 进入预浸缸。
- 1、下载文档前请自行甄别文档内容的完整性,平台不提供额外的编辑、内容补充、找答案等附加服务。
- 2、"仅部分预览"的文档,不可在线预览部分如存在完整性等问题,可反馈申请退款(可完整预览的文档不适用该条件!)。
- 3、如文档侵犯您的权益,请联系客服反馈,我们会尽快为您处理(人工客服工作时间:9:00-18:30)。
沉镍金制作流程
一、简介:
通过化学反应在铜表面沉积较薄一层镍金、金层具有稳定的化学和电器特性,镀层具有优良的可焊性,耐蚀性等特点。
二、流程及作用:
(1沉金前处理:
①微蚀:除去烘烤绿油造成的铜面过度氧化物。
② 1200#磨刷幼磨:除去铜面杂物,清洁板面。
(2沉镍金流程:
上板→除油→Ⅱ级水洗→微蚀→→Ⅱ级水洗→酸洗→Ⅱ级水洗→预浸→活化→Ⅱ级水洗→后浸酸→Ⅰ级水洗→沉镍→Ⅱ级水洗→沉金→金回收→水洗→热水洗→下板
①除油:除去铜表面之轻度油脂及氧化物,使表面活化及清洁。
②微蚀:除去铜面氧化物及污染物,适度粗化铜面,增加镀层密着性、结
合力。
③预浸:保护活化药液。
④活化:使用离子钯溶液使表面铜活化,可以只在铜面上沉积而基材的
Pd化合物极易清洗,提供化学沉镍的启镀剂。
⑤化学镀镍:利用电子转移使溶液中的Ni2+还原在待镀铜面上而沉积出镍
金属:但同时会有P析出,Ni层实际为Ni/P合金,Ni层厚度一般为
100-200u〃。
⑥通过置换反应在新鲜镍面置换一层薄金,作为防止基体金属氧化和作为自身活化型镀金的底层,镍基体上覆盖一层金后金沉积就停止,所以厚
度有一定了限制,Au层厚度一般为1-3 u〃。
(3沉金后处理:
①草酸洗:除去金面氧化异物,,对金层疏孔处的镍底层作酸封孔处理,
增加其耐蚀性。
②抗氧化清洗:防止镀层氧化,使焊锡维持更长的寿命。
三、流程控制注意事项:
(1控制微蚀速率在0.6-0.8um,速率太低,镀层发亮,太高出现色差即
金色不良。
(2活化缸Cu2+浓度≤200PPM需更换,且后期易出现渗金。
(3Ni缸温度不可太高,药水高温对绿油攻击较大,易出现甩S/M问题,
槽液使用4.0MTD后需换槽。
(4金缸需控制Ni2+含量≤800PPM,Ni2+太高易出现金色不良及不上金问题。
四、常见问题介绍及处理方法:
(1漏镀:①活化浓度温度过低,浴老化或活化后水洗过久。
②镍缸浓度、温度、PH值太低,或有不以纯物混入,成份失调。
③绿油冲板不净,有残渣附着铜面,需煲板返印。
④退锡不净,或退锡前放置太久,前处理不能除去。
⑤绿油塞孔导致电势差,W/F工艺改为不塞孔。
(2渗金:①防止活化时间太长,药水老化(Cu2+≤200PPM
②加强活化后打气量,适当提高后浸酸浓度。
③降低Ni缸活性,对于部分较细线路板可安排于Ni缸前期生产。
④蚀刻沙滩太重,造成线隙过小。
⑤蚀板后孔处理效果不好,返做孔处理。
(3金色不良:
①防止W/F局板铜面氧化过度,加强微蚀磨板前处理。
②药水清洗不净,及时更换老化槽液,用H2SO4浸泡各级水洗缸。
③微蚀过度,调低微蚀速率。
④Au缸后期,Ni2+含量太高,及时更换金缸。
⑤大关位板铜面条件差,可用W/F前粗磨改善铜面。
(4金面氧化:
① Au受Cu2+污染,控制在5PPM以下;并加强药液循环过滤,防止不溶性杂物混入。
② Au层太薄,控制1u〃以上。
③ Au缸后回收水洗有机物污染严重,更换并用H2SO4浸泡。
④加强沉金洗板机酸洗、抗氧化、水洗、烘干效果。
控制洗板后存放环境温湿度、室温、湿度50%左右。
(5甩绿油:
①加强绿油局板效果:防止前处理磨板过重。
②独立线位油薄,易甩油,增加油厚。
③Ni缸温度太高成为保证Ni厚沉镍时间太长,调节Ni缸温度,且不可为保证Ni厚沉镍时间太长。
调节Ni缸湿度,且不可为保证Ni厚延时过久。
特殊要求板可作改流程处理。
④Ni缸药水本身对绿油攻击较大,或所用绿油本身耐攻击力小不适用于沉金板生产
五、返工返修流程:
(1停电或机械故障板返工时未过活化板取出过幼磨再正常沉金,活化后板先过孔处理,再幼磨、沉金。
(2漏镀轻微板作拖金处理,整板漏镀较大面积板过1200#幼磨,再酸洗、活化、沉镍10-15min,沉金、修理的色差较小,可UAI行板。
(3轻微渗金板用刀介修理,严重报废。
(4甩S/M板轻微VAI行板,严重需煲板、返印、返沉金。
六、特殊流程板:
(1BGA位塞孔板沉金易漏镀,改W/F工BGA位Via孔加挡油PAD做
通孔再正常沉金。
(2单面纸基板沉金易孔黑,沉金前需先过孔处理。
(3沉金加厚金手指板因Ni原要求都170u〃以上,需Ni缸延时两缸时间。