PCB沉金工艺介绍
化学沉镍金工艺控制概述-刘兴武

化学沉镍金工艺控制概述生益电子:刘兴武摘要:本文简单介绍了化学沉镍金工艺的优缺点、原理、流程参数控制;并总结了常见问题的原因、改善措施以及检测方法等。
一、前言随着电子工业的飞速发展,IC组装对印制板(PCB)的要求也越来越高,无铅化表面处理(Lead-free Surface Finishes)已成主流。
化学沉镍金(Electroless Nickel Immersion Gold简称ENIG)、沉银(Immersion Silver简称ImAg)、沉锡(Immersion Tin 简称ImSn)、有机助焊保护膜(Organic Solderability Presevatives简称OSP)是替代传统锡铅涂覆的有效工艺方法,又因化学沉镍金的众多优点,其更受客户的青睐,已成为锡铅涂覆替代工艺的核心。
化学沉镍金又叫无电镍浸金或化镍浸金,它是通过钯的催化作用,在酸性条件下使裸铜面上沉积一层镍,然后通过置换反应再沉积上一层薄金的表面涂覆工艺,其金层提供良好的电气连接性,镍层作为阻挡层以阻止铜的扩散,从而避免在焊接和返工操作过程中焊料对铜层的污染。
二、化学沉镍金的优缺点1、优点(1)、高可靠性,适用复杂的电路设计。
(2)、高可焊性,适用多种及多重焊接(熔焊/Solder Fusing、波峰焊/Wave Solder、回流焊/Re-flow Solder、线焊/Wire Bonding)。
(3)、高平整、共面性,适用各种精密元器件的复杂组装。
(4)、良好的外观,不褪色,耐腐蚀、储存寿命长。
(5)、电气接触导通性、散热性好、具EMI(电磁干扰)屏蔽作用。
2、缺点(1)、焊点不良(工艺控制不当时发生)(2)、工艺复杂、操作温度较高(3)、成本高、价格昂贵三、主要化学反应原理1、活化Cu + Pd2++ 2NH4Cl Cu(NH3)2Cl2+ Pd+ 2H+2、化学沉镍催化剂[H2PO2]-+ H2O [H2PO3]-+ 2H(催化剂)Ni2++ 2H(催化剂)Ni ↓+ 2H+[H2PO2]-+ H(催化剂)H2O+ OH-+ P3Ni + P Ni3P (会产生金属间化合物)2H(催化剂)H2 ↑(会产生气泡)3、化学浸金Ni + 2[Au(CN)2]-Ni2+ + 2Au + 4CN-四、所需之设备物料1、目前,安美特、麦德美、优美科、罗门哈斯、上村药水在市场上较为流行,本公司所用安美特的Aurotech系列药水。
沉金和镀金区别及差异
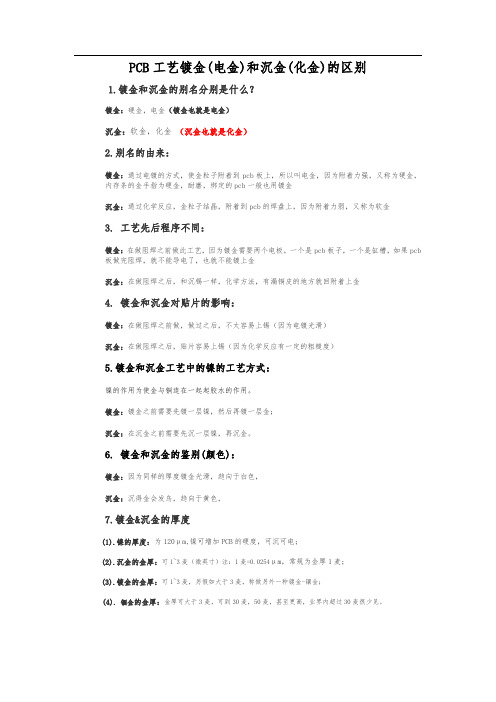
PCB工艺镀金(电金)和沉金(化金)的区别
1.镀金和沉金的别名分别是什么?
镀金:硬金,电金(镀金也就是电金)
沉金:软金,化金(沉金也就是化金)
2.别名的由来:
镀金:通过电镀的方式,使金粒子附着到pcb板上,所以叫电金,因为附着力强,又称为硬金,内存条的金手指为硬金,耐磨,绑定的pcb一般也用镀金
沉金:通过化学反应,金粒子结晶,附着到pcb的焊盘上,因为附着力弱,又称为软金
3. 工艺先后程序不同:
镀金:在做阻焊之前做此工艺,因为镀金需要两个电极,一个是pcb板子,一个是缸槽,如果pcb 板做完阻焊,就不能导电了,也就不能镀上金
沉金:在做阻焊之后,和沉锡一样,化学方法,有漏铜皮的地方就回附着上金
4. 镀金和沉金对贴片的影响:
镀金:在做阻焊之前做,做过之后,不太容易上锡(因为电镀光滑)
沉金:在做阻焊之后,贴片容易上锡(因为化学反应有一定的粗糙度)
5.镀金和沉金工艺中的镍的工艺方式:
镍的作用为使金与铜连在一起起胶水的作用。
镀金:镀金之前需要先镀一层镍,然后再镀一层金;
沉金:在沉金之前需要先沉一层镍,再沉金。
6. 镀金和沉金的鉴别(颜色):
镀金:因为同样的厚度镀金光滑,趋向于白色,
沉金:沉得金会发乌,趋向于黄色,
7.镀金&沉金的厚度
(1).镍的厚度:为120μm,镍可增加PCB的硬度,可沉可电;
(2).沉金的金厚:可1~3麦(微英寸)注:1麦=0.0254μm,常规为金厚1麦;
(3).镀金的金厚:可1~3麦,另假如大于3麦,称做另外一种镀金-锢金;
(4).锢金的金厚:金厚可大于3麦,可到30麦,50麦,甚至更高,业界内超过30麦很少见。
沉金和镀金的工艺区别
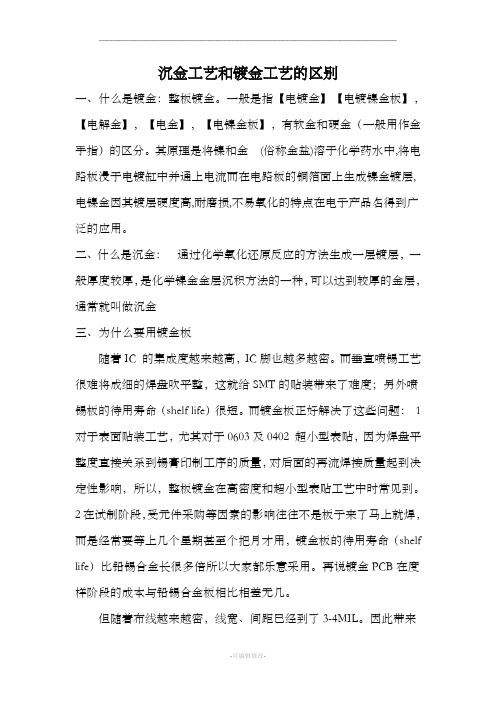
沉金工艺和镀金工艺的区别一、什么是镀金:整板镀金。
一般是指【电镀金】【电镀镍金板】,【电解金】,【电金】,【电镍金板】,有软金和硬金(一般用作金手指)的区分。
其原理是将镍和金(俗称金盐)溶于化学药水中,将电路板浸于电镀缸中并通上电流而在电路板的铜箔面上生成镍金镀层,电镍金因其镀层硬度高,耐磨损,不易氧化的特点在电子产品名得到广泛的应用。
二、什么是沉金:通过化学氧化还原反应的方法生成一层镀层,一般厚度较厚,是化学镍金金层沉积方法的一种,可以达到较厚的金层,通常就叫做沉金三、为什么要用镀金板随着IC 的集成度越来越高,IC脚也越多越密。
而垂直喷锡工艺很难将成细的焊盘吹平整,这就给SMT的贴装带来了难度;另外喷锡板的待用寿命(shelf life)很短。
而镀金板正好解决了这些问题:1对于表面贴装工艺,尤其对于0603及0402 超小型表贴,因为焊盘平整度直接关系到锡膏印制工序的质量,对后面的再流焊接质量起到决定性影响,所以,整板镀金在高密度和超小型表贴工艺中时常见到。
2在试制阶段,受元件采购等因素的影响往往不是板子来了马上就焊,而是经常要等上几个星期甚至个把月才用,镀金板的待用寿命(shelf life)比铅锡合金长很多倍所以大家都乐意采用。
再说镀金PCB在度样阶段的成本与铅锡合金板相比相差无几。
但随着布线越来越密,线宽、间距已经到了3-4MIL。
因此带来了金丝短路的问题:随着信号的频率越来越高,因趋肤效应造成信号在多镀层中传输的情况对信号质量的影响越明显:趋肤效应是指:高频的交流电,电流将趋向集中在导线的表面流动。
根据计算,趋肤深度与频率有关:四、为什么要用沉金板为解决镀金板的以上问题,采用沉金板的PCB主要有以下特点:1、因沉金与镀金所形成的晶体结构不一样,沉金会呈金黄色较镀金来说更黄,客户更满意。
2、因沉金与镀金所形成的晶体结构不一样,沉金较镀金来说更容易焊接,不会造成焊接不良,引起客户投诉。
3、因沉金板只有焊盘上有镍金,趋肤效应中信号的传输是在铜层不会对信号有影响。
电路板沉金工艺
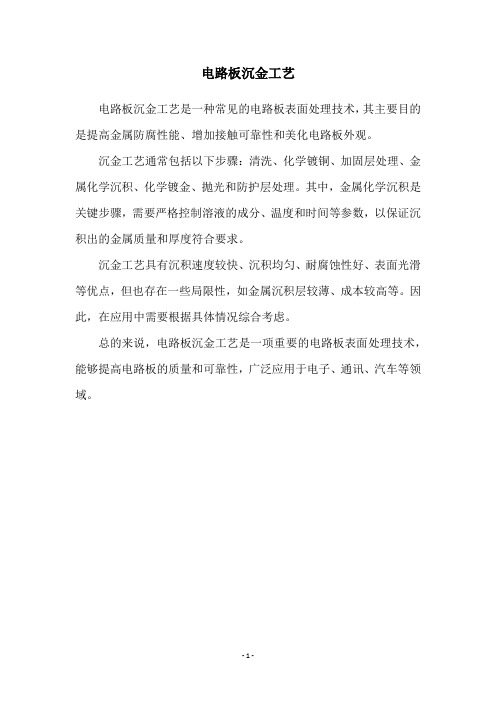
电路板沉金工艺
电路板沉金工艺是一种常见的电路板表面处理技术,其主要目的是提高金属防腐性能、增加接触可靠性和美化电路板外观。
沉金工艺通常包括以下步骤:清洗、化学镀铜、加固层处理、金属化学沉积、化学镀金、抛光和防护层处理。
其中,金属化学沉积是关键步骤,需要严格控制溶液的成分、温度和时间等参数,以保证沉积出的金属质量和厚度符合要求。
沉金工艺具有沉积速度较快、沉积均匀、耐腐蚀性好、表面光滑等优点,但也存在一些局限性,如金属沉积层较薄、成本较高等。
因此,在应用中需要根据具体情况综合考虑。
总的来说,电路板沉金工艺是一项重要的电路板表面处理技术,能够提高电路板的质量和可靠性,广泛应用于电子、通讯、汽车等领域。
- 1 -。
PCB工艺介绍
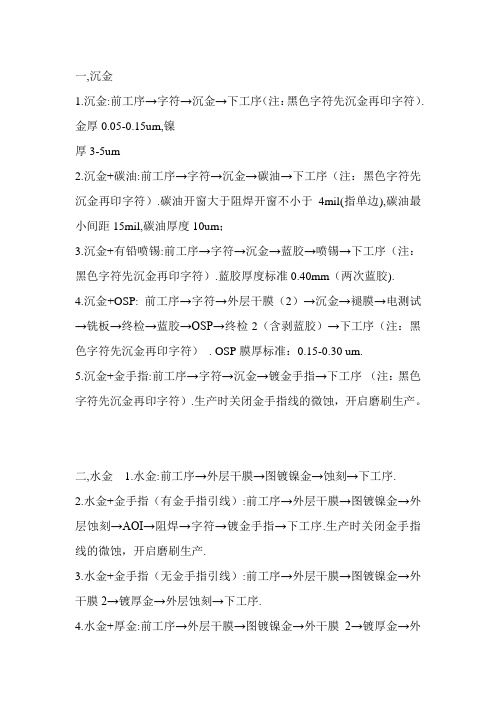
一,沉金1.沉金:前工序→字符→沉金→下工序(注:黑色字符先沉金再印字符).金厚0.05-0.15um,镍厚3-5um2.沉金+碳油:前工序→字符→沉金→碳油→下工序(注:黑色字符先沉金再印字符).碳油开窗大于阻焊开窗不小于4mil(指单边),碳油最小间距15mil,碳油厚度10um;3.沉金+有铅喷锡:前工序→字符→沉金→蓝胶→喷锡→下工序(注:黑色字符先沉金再印字符).蓝胶厚度标准0.40mm(两次蓝胶).4.沉金+OSP: 前工序→字符→外层干膜(2)→沉金→褪膜→电测试→铣板→终检→蓝胶→OSP→终检2(含剥蓝胶)→下工序(注:黑色字符先沉金再印字符). OSP膜厚标准:0.15-0.30 um.5.沉金+金手指:前工序→字符→沉金→镀金手指→下工序(注:黑色字符先沉金再印字符).生产时关闭金手指线的微蚀,开启磨刷生产。
二,水金 1.水金:前工序→外层干膜→图镀镍金→蚀刻→下工序.2.水金+金手指(有金手指引线):前工序→外层干膜→图镀镍金→外层蚀刻→AOI→阻焊→字符→镀金手指→下工序.生产时关闭金手指线的微蚀,开启磨刷生产.3.水金+金手指(无金手指引线):前工序→外层干膜→图镀镍金→外干膜2→镀厚金→外层蚀刻→下工序.4.水金+厚金:前工序→外层干膜→图镀镍金→外干膜2→镀厚金→外层蚀刻→下工序.水金标准:金厚0.25-0.75um,镍厚3-5um .增加干膜2厚金菲林.5.水金+有铅喷锡:前工序→图镀镍金→外层蚀刻→外层AOI→阻焊→字符→印兰胶→喷锡→下工序.增加印蓝胶的菲林,蓝胶制作相邻位置连片制作,以便于后续剥蓝胶.蓝胶厚度标准0.40mm(两次蓝胶).三,沉锡. 1.沉锡:锡厚度标准:0.8-1.2um.1)成品尺寸≥50X100mm (长边必须≥100mm,短边必须≥50mm): 前工序→字符→外形→电测→ 沉锡→电测试2→终检(2)成品尺寸<50X100mm(长边<100mm 或短边<50mm):前工序→字符→电测→ 沉锡→外形→电测试2→终检.2.沉锡+碳油:碳油厚度10um.前工序→字符→碳油→电测→印兰胶→沉锡→电测试(2)→终检.增加印碳油的菲林;印炭油前需在火山灰磨板线清洗板面,关闭磨刷.四,沉银. 1.沉银:银厚度标准:0.10-0.30um;前工序→字符→外形→电测→半检→ 沉银→半检→电测试2→终检.2.沉银+碳油:碳油厚度10um.前工序→字符→碳油→电测→印兰胶→半检→沉银→半检→电测试2→终检.增加印碳油的菲林.印炭油前需在火山灰磨板线清洗板面,关闭磨刷.3.沉银+金手指:金手指标准:镍厚:3-5um;常规金厚0.25-0.75um;厚金0.8~1.5um .前工序→字符→镀金手指→外形→电测→(贴红胶带)→半检→ 沉银→半检→电测试(2)→终检.(所有沉银板必须先字符再沉银.)五.OSP 1.OSP:OSP膜厚标准:0.15-0.30um.前工序→铣板→终检→OSP→终检2→后工序.2.OSP+碳油:碳油厚度10um.前工序→字符→ 碳油→电测试→铣板→终检→OSP →终检2→ 后工序.增加印碳油的菲林.印炭油前需在火山灰磨板线清洗板面,关闭磨刷.3.OSP+镀金手指:金手指标准:镍厚:3-5um,常规金厚0.25-0.75um;厚金0.8~1.5um .前工序→字符→镀金手指→铣板→电测试→终检→OSP→终检2→后工序.生产时关闭金手指线的微蚀,开启磨刷生产.六,喷锡 1.喷锡(有铅):锡厚标准:2-40um.前工序→字符→喷锡→下工序.2.喷锡(无铅):前工序→字符→喷锡→下工序.3.喷锡(有铅)+金手指:金手指标准:镍厚:3-5um,金厚0.25-0.75um前工序→字符→镀金手指→喷锡→下工序.4.喷锡(无铅)+金手指:前工序→字符→镀金手指→喷锡→下工序.5.碳油+喷锡(有铅):碳油厚度10um.阻焊→字符→碳油→喷锡→下工序.增加印碳油的菲林.印炭油前需在火山灰磨板线清洗板面,关闭磨刷;6.碳油+喷锡(无铅):(同上).七,全板镀厚金:硬金厚度标准:镍厚控制3-5um;常规厚金0.25-0.75um;超厚金0.8~2.0um.钻孔→沉铜→板镀→外光成像→图镀镍金(Cu/Ni/Au)→镀厚金→外层蚀刻→下工序.优缺点:.沉金:A.沉积层平整,有较强的硬度,表层不易擦花.2.有很好的导电性和多次焊接性能3.储存期长(1年以上).1.生产成本高;2.流程控制比较困难;3.有潜在的黑垫缺陷;4.修理及返工困难;B.沉银:1.沉积层平整;2.有很好的导电性和焊接性;3.流程控制简单;4.返工和修理简单;1.储存期短(6~12个月);2.不能多次焊接;3.银面易变黄;4.对储存环境和运输要求很高;C.OSP:1.生产成本低;2.流程控制简单;3.返工简单;1.储存期短;2.不能多次焊接;膜太薄,耐热冲击能力差.D.喷锡:1.生产成本低;2.有很好的导电性和焊接性;3.可多次焊接;4.储存期长(1年以上)1.喷锡表面平整性差;2.细间距加工困难;3.高温处理板易变形;4.含铅,严重污染环境;E.沉锡:1.流程控制简单;2.沉积层平整;3.有很好的导电性及焊接性;4.可多次焊接;5.储存期为一年;1.易擦花;2.有潜在的锡须生产的可能;。
沉金和镀金的工艺区别

沉金工艺和镀金工艺的区别一、什么是镀金:整板镀金。
一般是指【电镀金】【电镀镍金板】,【电解金】,【电金】,【电镍金板】,有软金和硬金(一般用作金手指)的区分。
其原理是将镍和金(俗称金盐)溶于化学药水中,将电路板浸于电镀缸中并通上电流而在电路板的铜箔面上生成镍金镀层,电镍金因其镀层硬度高,耐磨损,不易氧化的特点在电子产品名得到广泛的应用。
二、什么是沉金:通过化学氧化还原反应的方法生成一层镀层,一般厚度较厚,是化学镍金金层沉积方法的一种,可以达到较厚的金层,通常就叫做沉金三、为什么要用镀金板?随着IC 的集成度越来越高,IC脚也越多越密。
而垂直喷锡工艺很难将成细的焊盘吹平整,这就给SMT的贴装带来了难度;另外喷锡板的待用寿命(shelf life)很短。
而镀金板正好解决了这些问题: 1对于表面贴装工艺,尤其对于0603及0402 超小型表贴,因为焊盘平整度直接关系到锡膏印制工序的质量,对后面的再流焊接质量起到决定性影响,所以,整板镀金在高密度和超小型表贴工艺中时常见到。
2在试制阶段,受元件采购等因素的影响往往不是板子来了马上就焊,而是经常要等上几个星期甚至个把月才用,镀金板的待用寿命(shelf life)比铅锡合金长很多倍所以大家都乐意采用。
再说镀金PCB在度样阶段的成本与铅锡合金板相比相差无几。
?但随着布线越来越密,线宽、间距已经到了3-4MIL。
因此带来了金丝短路的问题:?随着信号的频率越来越高,因趋肤效应造成信号在多镀层中传输的情况对信号质量的影响越明显:?趋肤效应是指:高频的交流电,电流将趋向集中在导线的表面流动。
?根据计算,趋肤深度与频率有关:四、为什么要用沉金板为解决镀金板的以上问题,采用沉金板的PCB主要有以下特点:1、因沉金与镀金所形成的晶体结构不一样,沉金会呈金黄色较镀金来说更黄,客户更满意。
2、因沉金与镀金所形成的晶体结构不一样,沉金较镀金来说更容易焊接,不会造成焊接不良,引起客户投诉。
PCB电路板为什么要沉金和镀金?有什么区别?
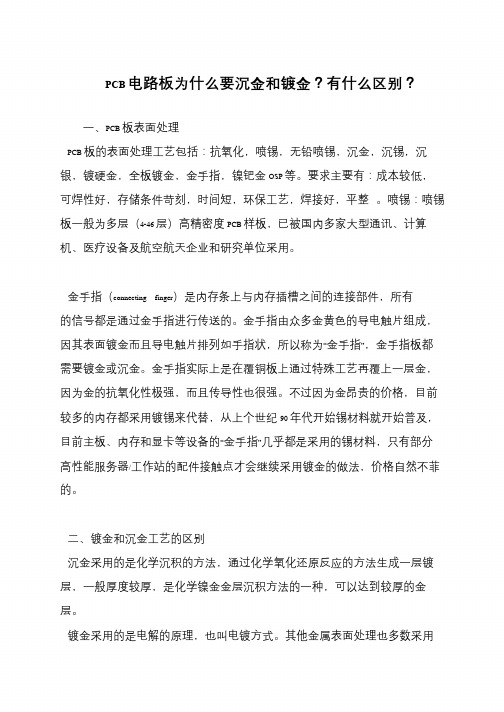
PCB 电路板为什么要沉金和镀金?有什么区别?
一、PCB 板表面处理
PCB 板的表面处理工艺包括:抗氧化,喷锡,无铅喷锡,沉金,沉锡,沉银,镀硬金,全板镀金,金手指,镍钯金OSP 等。
要求主要有:成本较低,可焊性好,存储条件苛刻,时间短,环保工艺,焊接好,平整。
喷锡:喷锡板一般为多层(4-46 层)高精密度PCB 样板,已被国内多家大型通讯、计算机、医疗设备及航空航天企业和研究单位采用。
金手指(connecting finger)是内存条上与内存插槽之间的连接部件,所有的信号都是通过金手指进行传送的。
金手指由众多金黄色的导电触片组成,
因其表面镀金而且导电触片排列如手指状,所以称为“金手指”,金手指板都
需要镀金或沉金。
金手指实际上是在覆铜板上通过特殊工艺再覆上一层金,
因为金的抗氧化性极强,而且传导性也很强。
不过因为金昂贵的价格,目前
较多的内存都采用镀锡来代替,从上个世纪90 年代开始锡材料就开始普及,目前主板、内存和显卡等设备的“金手指”几乎都是采用的锡材料,只有部分
高性能服务器/工作站的配件接触点才会继续采用镀金的做法,价格自然不菲的。
二、镀金和沉金工艺的区别
沉金采用的是化学沉积的方法,通过化学氧化还原反应的方法生成一层镀层,一般厚度较厚,是化学镍金金层沉积方法的一种,可以达到较厚的金
层。
镀金采用的是电解的原理,也叫电镀方式。
其他金属表面处理也多数采用。
多层印制线路板沉金工艺控制简述
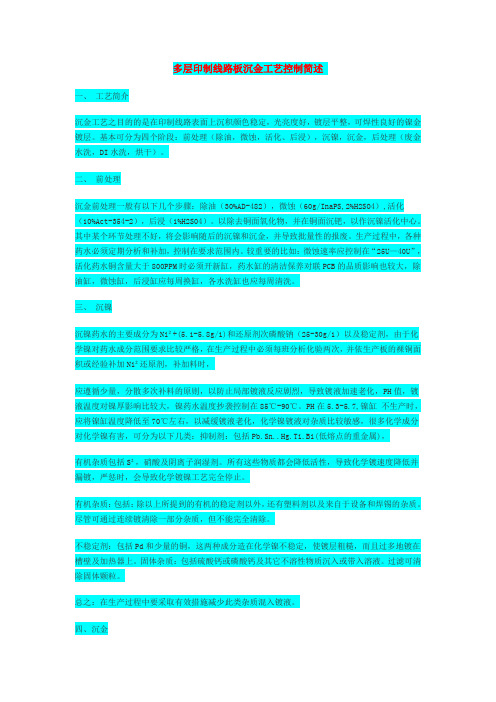
多层印制线路板沉金工艺控制简述一、工艺简介沉金工艺之目的的是在印制线路表面上沉积颜色稳定,光亮度好,镀层平整,可焊性良好的镍金镀层。
基本可分为四个阶段:前处理(除油,微蚀,活化、后浸),沉镍,沉金,后处理(废金水洗,DI水洗,烘干)。
二、前处理沉金前处理一般有以下几个步骤:除油(30%AD-482),微蚀(60g/InaPS,2%H2SO4),活化(10%Act-354-2),后浸(1%H2S04)。
以除去铜面氧化物,并在铜面沉钯,以作沉镍活化中心。
其中某个环节处理不好,将会影响随后的沉镍和沉金,并导致批量性的报废。
生产过程中,各种药水必须定期分析和补加,控制在要求范围内。
较重要的比如:微蚀速率应控制在“25U—40U”,活化药水铜含量大于800PPM时必须开新缸,药水缸的清洁保养对联PCB的品质影响也较大,除油缸,微蚀缸,后浸缸应每周换缸,各水洗缸也应每周清洗。
三、沉镍沉镍药水的主要成分为Ni²+(5.1-5.8g/1)和还原剂次磷酸钠(25-30g/1)以及稳定剂,由于化学镍对药水成分范围要求比较严格,在生产过程中必须每班分析化验两次,并依生产板的裸铜面积或经验补加Ni²还原剂,补加料时,应遵循少量,分散多次补料的原则,以防止局部镀液反应剧烈,导致镀液加速老化,PH值,镀液温度对镍厚影响比较大,镍药水温度抄袭控制在85℃-90℃。
PH在5.3-5.7,镍缸不生产时,应将镍缸温度降低至70℃左右,以减缓镀液老化,化学镍镀液对杂质比较敏感,很多化学成分对化学镍有害,可分为以下几类:抑制剂:包括Pb.Sn..Hg.Ti.Bi(低熔点的重金属),有机杂质包括S²,硝酸及阴离子润湿剂。
所有这些物质都会降低活性,导致化学镀速度降低并漏镀,严惩时,会导致化学镀镍工艺完全停止。
有机杂质:包括:除以上所提到的有机的稳定剂以外,还有塑料剂以及来自于设备和焊锡的杂质。
尽管可通过连续镀清除一部分杂质,但不能完全清除。
- 1、下载文档前请自行甄别文档内容的完整性,平台不提供额外的编辑、内容补充、找答案等附加服务。
- 2、"仅部分预览"的文档,不可在线预览部分如存在完整性等问题,可反馈申请退款(可完整预览的文档不适用该条件!)。
- 3、如文档侵犯您的权益,请联系客服反馈,我们会尽快为您处理(人工客服工作时间:9:00-18:30)。
化学镍药水的分类:
按操作温度分可将镀液分成高温镀液(85950C)、中温镀液(65-750C)、低温 镀液(500C)以下
按其使用的还原剂又可大致分为次磷酸盐 型、硼氢化物型、肼型、胺基硼烷型4种。
26
按pH值分又可将其分为酸性镀液和碱性镀 液; 最常用的是次磷酸盐为还原剂的酸性高温 化学镀镍液,常称为普通化学镀镍液。
1.5 ±0.5min
搅拌:摆动及药液循环搅拌或空气打气
槽材质:PVC或PP
加热器:石英或铁弗龙加热器
15
铜浓度控制:
由于Cu2+对微蚀速率影响较大,通 常须将Cu2+的浓度控制在5-25g/l, 以保证微蚀速率处于0.5-1.5μm之间。 生产过程中,换缸时往往保留1/5-1/3 缸母液(旧液),以保持一定的Cu2+浓 度。
通常情况,不采用调节药水浓度或 升高温度来弥补因时间不足而引起的镍 厚不足,一定要根据客户镍层要求来设 置适当的镀镍时间。否则,可能引起活 性不稳定,会造成许多不良后果。
44
C、浓度: 不同供应商之不同系列药水,
其浓度控制范围各不相同。由于化 学镀镍的本身特点,其动态平衡的 控制难度远远大于化学镀铜,其控 制范围很窄则可说明这一点。因此, 尽可能使用自动补料器来控制药水 浓度,手动补料是很难保证每一个 制板的良品率。
• B、随着NaH2PO2和NiSO4浓度的增加, 沉积速度逐渐提高,而后趋于稳定或稍 有降低。但此时溶液的稳定性下降;
40
•C、化学镀镍层的厚度一般控制4~5μm, 最少要大于2.5μm厚的镍磷层才能起到 有效的阻挡层作用,防止铜的迁移,以免渗 出金面,氧化后导致导电性不良;
•D、镀覆PCB的装载量(裸铜面)应适 中,以0.1~0.5dm2/L为宜。负载太大会导 致镍缸活性逐渐升高,甚至导致反应失 控,造成严重后果;负载太低会导致镍 缸活性逐渐降低,造成漏镀等问题。
老化度与析出速度试验结果
25 20 15 10 5 0
012345
溶液老化度(MTO)
6
35
析出速度(μm/hr)
析出速度与镍浓度关系
25 24 23 22 21 20 19
4.8
5.2 5.9 6.4
镍浓度(g/L)
6.7
36
析出速度(μm/hr)
还原剂浓度与析出速度关系
25
20
15
10
5
0
18
6
五、沉镍金工艺的用途
化学镍金镀层集可焊接、可接触导通,可打线、 可散热等功能于一身,是PCB板面单一处理却具 有多用途的湿制程。 化学镍的厚度一般控制在 4-5μm,其不但对铜面进行有效保护,防止铜 的迁移,而且具备一定硬度和耐磨性能,同时拥 有良好的平整度。浸金的厚度一般控制在0.050.1μm,其对镍面具有良好的保护作用,而且具 备很好的接触导通性能。
铜面清洁及增加润湿性。
特性要求:
A: 一般为酸性除油剂 B:不损伤solder mask C:低泡型,容易水洗
11
操作条件:
温度:50±10oC 时间:6 ±2min 过滤:5μmPP滤芯连续过滤 搅拌:摆动及药液循环搅拌 槽材质:PP或SUS 加热器:石英或铁弗龙加热器
12
逆流水洗:
除油缸之后通常为二级市水洗,如 果水压及流量不稳定或经常变化,则将 逆流水洗设计为三级市水洗更佳。
21
逆流水洗:
水洗缸中少量的Pd带入镍缸,并不 会对镍缸造成太大的影响,所以不必 太在意活化后水洗时间太短,一般情 况下,二级水洗总时间控制在1-3min 为佳。尤其重要的是,活化后水洗不 宜使用超声波装置,否则,不但导致 大面积漏镀,而且渗镀问题依然存在。
22
6、沉镍
• 作用:在钯的活化作用下,Ni2+在NaH2PO2
沉镍金培训教材
撰写:henry 日期:2012年6月
1
第一部分 沉镍金基本概念
2
一、什么是化学镀
化学镀是在金属的催化作用 下,通过可控制的氧化还原 反应产生金属沉积的过程。
3
二、化学镀应具备的条件:
1、氧化还原电位应显著低于金属 还原电位; 2、溶液不产生自发分解,催化时 才发生金属沉积; 3、PH值、温度可以调节镀覆速度; 4、具有自催化作用; 5、溶液有足够寿命。
13
3、微蚀缸
作用: 酸性过硫酸钠微蚀液用于使铜面微
粗化,增加铜与化学镍层的密着性。沉 镍金生产也有使用硫酸双氧水或酸性过 硫酸钾微蚀液来进行的。
14
操作条件(NPS系列):
Na2S2O8: H2SO4: Cu2+ :
100±20g/l 20 ±10g/l 5~25g/l
温度:
30 ±2OC
时间:
铅、镉、锑及某些有机或无机含硫化合物如硫 脲以及三氯化钼都是化学镀镍的催化剂毒物, 如含量很少时,对镀液有一定的稳定作用,但 若含量过高会使镀液失效导致镍不能沉积出来。
31
镍沉积速度影响因素
A 温度 B PH值 C 缸老化度(正常生产时老化度以MTO来衡量
) D 主盐(NiSO4)浓度 E 还原剂(NaH2PO2) 浓度 F 溶液的过滤与搅拌
2.镍离子在活化钯面上迅速还原镀出镍 金属。 Ni2++2H Ni+2H+
24
3.小部分次磷酸根在催化氢的刺激下,产生 磷原子并沉积在镍层中。
H2PO2-+H OH-+P+H2O 4.部分次磷酸根在催化环境下,自己也会氧 化并生成氢气从镍面上向外冒出。
H2PO2- + H2O HPO32-+H++H2
29
一般均使用NaH2PO2,其控制浓度一般为 20-40g/l。在镀液中,主反应将Ni2+还原 成为金属Ni,副反应为其本身的歧化反应 生成单质P,主反应及副反应过程中均伴随 CH、2逸缓冲出剂。、络合剂
缓冲剂主要用处是维持镀液的pH值防止化学镀镍 时由于大量析氢所引起的pH值下降 络合剂作用主要是与镍离子进行络合降低游离镍离 子的浓度,提高镀液的稳定性。
在化学镀镍溶液中通常选用有机酸及其盐作 为缓冲剂、络合剂。
30
柠檬酸、羟基乙酸、琥珀酸、苹果 酸、乳 酸及其盐、氯化铵、焦磷酸盐、乙二胺、 三乙醇胺等均为结合剂,其中某些药品还 起缓冲剂作用;
D、稳定剂 其主要用处是防止化学镀镍溶 液在受到污染及存在有催化活性的固体 颗粒、负载量过大或过小、pH值过高等 异常情况下,自发分解 。重金属离子锡、锌、
27
溶液的组成及作用:
A、金属盐 次磷酸镍是镍离子最为理想的来源。
如能解决其在制备过程中遇到的问题,使 用这种镍盐将极大地改善镀液的性能
目前 最常用的镍盐有硫酸镍和氯化镍 两种。由于硫酸镍的价格低廉,且容易制 成纯度较高的产品,被认为是镍盐的最佳 选择。由于氯离子的活性高,化学镀镍时 一般不使用氯化镍
作用:
维持活化缸的酸度及使铜面在新鲜状 态(无氧化物)的情况下,进入活化缸。
操作条件:
温度:
室温
时间:
1±0.5min
搅拌:
摆动及药液循环搅拌
槽材质:
PVC或PP
18பைடு நூலகம்
5、活化
作用:
在电化序中,铜位于镍的后面,所以必须 将铜面活化,才能进行化学镀镍。PCB行 业大多是采用先在铜面上生成一层置换钯 层的方式使其活化。
• 注:MTO 即 Metal Turn Over ,缸内金属离子的加入量
32
析出速度(μm/hr)
浴温变化试验结果
25 20 15 10
5 0
75
80
85
浴温(℃)
90
33
析出速度(μm/hr)
PH变化试验结果
30 25 20 15 10
4.4 4.5 4.6 4.7 4.8 PH
5
34
析出速度(μm/hr)
45
•D、循环过滤 循 时循环环量:抽5液~量~1所0 占tu开rn缸ov体e积r p的er倍h数ou)r(。每小 过滤:优先考虑布袋式过滤,棉芯过滤需监 控流量(发现堵塞及时更换)。 E、摇摆:
41
•E、镀液应连续过滤,以除去溶液中的 固体杂质。镀液加热时,必须要有空气 搅拌或连续循环系统,使被加热的镀液 迅速扩散开。当槽内壁镀有镍层时,应 及时用硝酸(1:3)褪除,适当时可考虑加 热,但不可超过50OC, 以免污染空气。
•F、镀液寿命一般控制在4MTO(即Ni 离子添补量累积达到4倍开缸量),超过 此限主要问题是镍厚不足。
搅拌:摆动及药液循环搅拌
20
工艺维护
• 影响钯缸稳定性的主要因素除了药水系 列不同之外,钯缸控制温度和Pd2+浓度则 是首要考虑的问题。温度越低、Pd2+浓度 越低,越有利于钯缸的控制。但不能太 低,否则会影响活化效果引起漏镀发生。
• 通常情况下,钯缸温度设定在20300C,其控制范围应在±10C,而Pd2+浓 度则控制在20-40ppm,至于活化效果, 则按需要选取适当的时间。
7
第二部分
沉镍金原理及工艺介绍
8
一、基本工艺流程
整孔 水洗 水洗
除油 活化 沉金
水洗 水洗 水洗
微蚀 沉镍 烘干
9
二、各流程简介
1、整孔
A、目的:使非导通孔孔内残留的钯失 去活性,以防止其沉上镍金。 B、通常在蚀刻后褪锡前以水平线处理, 使用的药水一般为:硫脲和盐酸
10
2、除油
作作用:用于除去铜面之轻度油脂及氧化物,
4
三、什么是沉镍金?
也叫无电镍金或沉镍浸金(Electroless Nickel Immersion Gold),是指在PCB 裸铜表面涂覆可焊性涂层的一种工艺。