铝合金焊接接头产生裂纹特征及产生机理
浅议铝合金焊接接头裂纹产生及防治

I剖 酱 辘 | 庶 苷 ) 詹 瞬弃 , 问 鼓7
() 4 必要 时, 实施切割导轨 工程; 以释放导轨 内部积聚 的应 力; 提高安全性及乘搭舒适感 。 () 5 导轨切割主要步骤: ① 拆 除 导 轨 底 部 固定 支 架 。 ⑦ 设 定 切 割 高度 。 切割 高度= 力释放距离 (0 3mm + 应 2 ~ 0 ) 导轨底座 高度 ( 约为 5mm + 0 ) 预留距 离 ( 约为 8mm 0 ) ③按设定高度切割导轨 。
萌 生和 发 展 有 密 切 联 系 的冶 金 因素 。 力 学 因素 方 面 看 , 接 热 从 焊
最 靛 裙 况
f 连 度变 ,导 f # 高 麦 , 井 高 靶 轨 , 遣 度 化 辩 )
支 位 , 点 轨 截 压 再造 路 进 泉 移 遣 蓐 轻 路轨 , 成 轨
图 1
。 \
一/
f
—
L- =一
c =
/ 匕=
匕 =
/
_
_
④割短低端导轨后 , 瞬问释放 了一部分 内应 力。( 图 1步 如 :
骤 4 )
面保持一定间隙。
⑤对于没有支架 的, 加装导轨底支架 。 需在 日常保养 时,经 常确 认导轨底部和 调整螺栓 项面保持
一
产生重大影响,而本研究试验 中却发现焊缝拉伸试样中同时存 在着 由夹杂和气 孔诱发微裂纹 的现象 。气孔诱发微裂纹的现象 是否只是一种居次要地位 的伴生现象 ,还是引起焊缝拉伸强度 大幅度下 降的主要因素之一 , 亦还有待进一步的研究。
2 热裂纹产 生的过程
通常人们将脆性温度 区间的大小及在此温度 区间内具有 的 延性值称为产生焊接热裂纹 的冶金 因素 ,而把脆性温度区 内金 属的变形率大小称为力学因素 。焊接过程是一系列不平衡 的工 艺过程 的综合,这种特征从本质上与焊接接头金属断裂的冶金 因素和力学因素发生重要 的联系 ,如焊接工艺过程与冶金过程 的产物 即物理的 、 化学的与组织上 的不均匀性 、 熔渣 与夹杂物 、 气 体元 素 与 处 于 过饱 和 浓 度 的空 位 等 。 所有 这 些 , 都是 与裂 纹 的
7A10铝合金焊接裂纹的成因及预防对策探讨

7A10 铝合金焊接裂纹的成因及预中国中车长春轨道客车股份公司,吉林 长春 130062)
摘 要 :伴随我国制造业的发展,铝合金被广泛应用于许多领域中,如零部件加工、轨道车辆制造、汽车制造等。值得注意的是,
铝合金材料应用下存在的问题较多,以 7A10 铝合金为例,焊接中极易出现裂纹,极大程度上影响铝合金综合性能。对此情况,
尽管铝合金在各方面性能上有较多优势,但实际做焊接处理 中,可能出现的问题较多,具体表现为 :第一,裂纹形成。裂纹 问题在铝合金焊接中发生可能性较高如凝固状态下,体积收缩, 焊接变形可能性较高,加之焊接中近缝区内焊接金属影响,有热 裂纹或液化裂纹情况,若易熔共晶体较多,也将导致凝固裂纹出 现。第二,易氧化。铝合金焊接中,与空气接触后可能有氧化情 况,氧化后的铝在熔点上较高,一旦出现氧化情况,将有较多缺 陷出现,如未熔合、未焊透或夹渣生成,一旦铝表面有过多水分 附着,或出现氧化膜,将导致焊缝有气孔出现。第三,焊接过程 中产生气泡。由于高温下的的铝合金在向由固态向液态转化的过 程中易产生氢气,而由于铝合金物态中幻化的这一过程发生的时 间较快,分解出来的氢气在铝合金固化时不能及时的排放就被凝 固在固体中,因此在焊接过程中就极易产生因氢气而形成的气泡 孔。此外,焊接头抗腐蚀性降低,焊接过程中,由于各种外界因 素的干扰以及实际操作过程中的消耗,会导致焊接头的抗腐蚀性 低于原材料。产生这种情况的原因首先归因于焊接过程中的消耗 和磨损,打乱了焊接头部的物质分布,因此会出现电位的不稳定 现象。或因焊接头的纯度不高,其中含有大颗粒的杂质,出现腐 蚀问题。这些问题的存在,均可能导致氯化金综合性能降低 [2]。
2 7A10铝合金焊接裂纹产生原因分析 2.1 7A10 铝合金焊接裂纹类型与原因
铝合金部件焊接接头裂纹分析
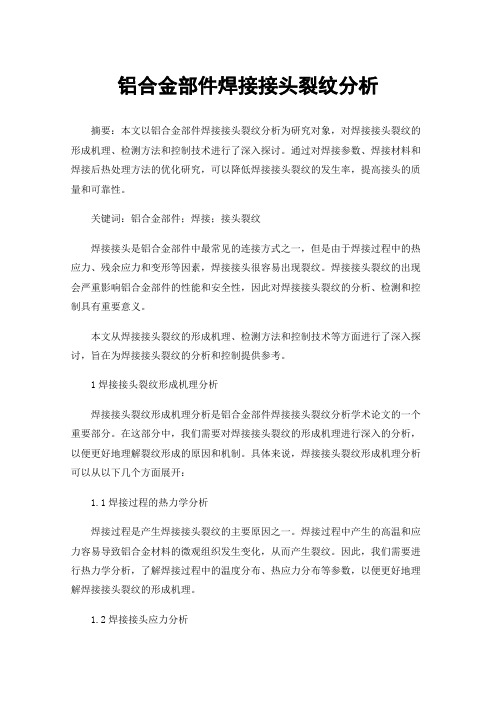
铝合金部件焊接接头裂纹分析摘要:本文以铝合金部件焊接接头裂纹分析为研究对象,对焊接接头裂纹的形成机理、检测方法和控制技术进行了深入探讨。
通过对焊接参数、焊接材料和焊接后热处理方法的优化研究,可以降低焊接接头裂纹的发生率,提高接头的质量和可靠性。
关键词:铝合金部件;焊接;接头裂纹焊接接头是铝合金部件中最常见的连接方式之一,但是由于焊接过程中的热应力、残余应力和变形等因素,焊接接头很容易出现裂纹。
焊接接头裂纹的出现会严重影响铝合金部件的性能和安全性,因此对焊接接头裂纹的分析、检测和控制具有重要意义。
本文从焊接接头裂纹的形成机理、检测方法和控制技术等方面进行了深入探讨,旨在为焊接接头裂纹的分析和控制提供参考。
1焊接接头裂纹形成机理分析焊接接头裂纹形成机理分析是铝合金部件焊接接头裂纹分析学术论文的一个重要部分。
在这部分中,我们需要对焊接接头裂纹的形成机理进行深入的分析,以便更好地理解裂纹形成的原因和机制。
具体来说,焊接接头裂纹形成机理分析可以从以下几个方面展开:1.1焊接过程的热力学分析焊接过程是产生焊接接头裂纹的主要原因之一。
焊接过程中产生的高温和应力容易导致铝合金材料的微观组织发生变化,从而产生裂纹。
因此,我们需要进行热力学分析,了解焊接过程中的温度分布、热应力分布等参数,以便更好地理解焊接接头裂纹的形成机理。
1.2焊接接头应力分析焊接接头的应力是产生焊接接头裂纹的另一个主要原因。
焊接接头在焊接后会受到内部应力的影响,这些应力会导致接头的变形和裂纹。
因此,我们需要进行应力分析,了解焊接接头中各个部位的应力情况,以便更好地预测焊接接头裂纹的形成位置和形态。
1.3焊接接头金相组织分析铝合金部件的微观组织是决定其力学性能和耐腐蚀性能的重要因素。
焊接接头的金相组织分析可以帮助我们了解焊接接头中的晶粒结构、相组成、缺陷分布等信息,从而更好地理解焊接接头裂纹的形成机理。
综上所述,焊接接头裂纹形成机理分析是铝合金部件焊接接头裂纹分析学术论文的重要内容之一。
5A06铝合金焊接接头裂纹失效分析

2 7
5 A0 6铝 合 金 焊 接 接 头裂 纹 失效 分 析
Fa i l u r e An a l y s i s o f 5 A0 6 Al u mi n u m Al l o y We l d i n g J o i n t Cr a c k
Mi c r o — f r a c t ur e a n d ma c r o f r a c t u r e a r e a n a l y z e d by SEM a nd f o un d t ha t t h e r e a r e s e c o nd a r y c r a c ks i n t he f r a c t u r e ,a n d t he f r a c t u r e wa s b r i t t l e f r a c t u r e .
近 年来 , 铝、 镁 等 轻 质 合 金 由 于其 节 约 能 源 、 减 少 废气 排 放 等特 点 , 在 海事 用 途 ( 如船 舶 ) 、 汽 车、 飞
摘 要 :针 对 5 A 0 6 铝 合 金 焊 缝 附 近 出 现 的 裂 纹 进 行 了分 析 。5 A 0 6铝 合 金 母 材 、 焊缝及 热影响区组织分析结果 表明 , 材 料
成 型 后 的组 织 不 均 匀 , 并且存在夹杂物 , 晶 内 和 晶 界 有 析 出相 出 现 。采 用 光 学 显 微 镜 对 裂 纹 的 扩 展 特 征 进 行 分 析 , 结 果
d o i :1 0 . 3 9 6 9 / j . i s s n . 1 0 0 1 — 4 3 8 1 . 2 0 1 3 . 0 3 . 0 0 6 中图 分 类 号 : TG1 4 6 . 2 1 文献 标 识 码 : A 文 章 编 号 :1 0 0 1 — 4 3 8 1 ( 2 0 1 3 ) 0 3 — 0 0 2 7 - 0 5
铝合金焊接开裂原因

铝合金焊接开裂原因铝合金是一种常见的工程材料,因其具有良好的强度和轻质特性而被广泛应用于各种工业领域。
然而,铝合金在焊接过程中容易出现开裂问题,这给焊接工艺和焊接质量带来了一定的挑战。
本文将探讨铝合金焊接开裂的原因,并提出相应的解决方法。
铝合金焊接开裂的原因可以归结为以下几个方面。
一、热裂纹铝合金焊接过程中,由于热应力的作用,易发生热裂纹。
热裂纹主要是由于焊接过程中产生的局部高温引起的。
铝合金的热导率较高,容易导致焊缝局部温度升高,当焊接过程中产生的热应力超过了铝合金的塑性极限时,就会发生热裂纹。
二、固溶体析出铝合金焊接后,焊缝区域会发生固溶体析出现象。
固溶体析出是指在焊接过程中,由于铝合金的化学成分和热处理条件的改变,使得合金中的某些元素从固溶体中析出出来。
这种析出现象会导致焊缝区域的组织结构不均匀,从而引发开裂问题。
三、应力集中焊接过程中,由于热应力和残余应力的作用,焊缝区域容易出现应力集中现象。
应力集中会导致焊缝区域的应力超过材料的强度极限,从而引起开裂。
应力集中现象通常发生在焊缝的两端或焊缝与基材的交界处。
四、气孔铝合金焊接过程中,气孔是另一个常见的开裂原因。
气孔是指焊接过程中由于气体无法完全排出而形成的孔洞。
气孔会导致焊缝区域的强度降低,从而引发开裂。
针对上述问题,我们可以采取一些措施来预防铝合金焊接开裂。
一、合理控制焊接温度通过合理控制焊接温度,可以减少焊缝区域的热应力,从而降低热裂纹的风险。
可以采用预热和后热处理的方法,使焊接温度均匀分布,避免局部温度过高。
二、选择适当的焊接材料和焊接工艺选择适当的焊接材料和焊接工艺,可以减少固溶体析出和应力集中的问题。
合理选择焊接材料的成分和焊接工艺的参数,确保焊缝区域的组织结构均匀,避免应力集中。
三、控制焊接过程中的气体通过控制焊接过程中的气体,可以减少气孔的形成。
可以采用惰性气体保护和适当的焊接速度,避免气体进入焊接区域,减少气孔的发生。
铝合金焊接开裂是由多种因素共同作用导致的。
关于铝合金焊接裂纹产生的原因和预防的探讨

关于铝合金焊接裂纹产生的原因和预防的探讨摘要:铝合金材料作为一种具有较强的物理特性和力学性能的材料,常应用于工业制造和生产生活,在工业经济发展中起到了重要的作用。
随着轨道列车行业对铝合金焊接件的需求日益增加,使铝合金的焊接性研究也逐步深入。
由于铝合金的导热系数以及冷却速度等特性,使得铝合金焊接过程中容易出现裂纹。
本文分析铝合金焊接裂纹产生的原因和预防措施,通过分析、提出解决的措施有效的降低铝合金的焊接裂纹情况的出现。
关键词:铝合金;焊接;裂纹;原因;预防措施一、铝合金焊接裂纹产生的原因分析1.1金属结构的因素由于铝合金材料在焊接的过程中,容易出现裂纹的现象,因此首先要考虑的是改变金属材料的结构,通过改变金属结构的材料成分,都能够起到积极的影响。
由于金属结构的影响,会导致铝合金焊接中出现的热裂纹,需要进行材料金属特性的改变。
1.2焊接工艺参数的影响焊接工艺参数也会对铝合金的金属生产制造产生影响,尤其是当前铝合金金属制造中各种自动化焊接设备需要大量人工参与,这样就会导致焊接工艺的参数的不稳定,在生产过程中还会受到温度、湿度及粉尘等外部因素的影响,都会对焊接工艺参数造成干扰。
1.3焊接速度的影响焊接速度同样会影响铝合金的焊接,由于焊接速度会影响到铝合金的焊接的膨胀量,对于在制造过程中,焊接速度的不稳定,就会对铝合金的焊接接头成型造成影响,同时焊接速度形成的不同的焊接电流,都会成为铝合金的焊接裂纹产生的因素之一[1]。
当前焊接的速度控制分为人工操作和机械操作以及人机共同操控三种形式,人工操作的形式多见于对于加工精度要求高以及中小企业的操作中,机械操作适合大规模的量化生产,当前的人机共同操作的模式也是十分常见,这种模式集合了人工操作和机械操作的优点,同时能够方便操作者实施控制工艺的进程,选择不同的形式,都会对焊接速度造成影响。
1.4 材料的清洁度因素由于在运输、仓储以及加工的过程中,铝合金的焊接材料都会受到不同程度的污染,会对材料的表面受到影响,这样就影响到了材料的清洁度。
7020铝合金焊接件开裂分析

Abstract:7020aluminum alloyweldmentcrackedinservice.Torevealcauseoftheweldmentcracking,the
specimenswerecutfrom theweldandsubjectedtomacrocheck,metallographictest,andchemicalcomposition
坦,裂面由黑斑边缘起向下(外表)扩展,条状台阶 一,未见明显异常,但可见焊接孔洞,且裂纹起始与
《热处理》 2019年第 34卷 第 1期
·43·
焊接孔洞 有 关。该 处 开 裂 起 始 区 孔 洞 直 径 约 为 0.25mm,距焊缝表面约 2.65mm。
进一步观察,焊缝内局部可见与原裂面近似垂 直的细微裂纹,长短不一,最长约 200μm,最短约 50μm,如图 8所示。
analysis.Theresultsshowedthatthecrackinghappenedintheweld,andwasattributedtogasholespresentinit.
Keywords:7020aluminum alloy;welding;cracking;gashole
0 引言
图 6 裂面扩展区的疲劳辉纹形貌 Fig.6 Fatiguestriationsinthefractureextendingarea
1.2 扫描电镜分析
1.3 显微组织观察金相分析[2],裂纹附近的
图 4所示。图 4上侧为黑斑区,呈条状,表面比较平 组织如图 7所示。裂纹呈断续曲折状分布,宽窄不
拟与焊接枝晶有关。裂面上分布有大量孔洞,内壁 光滑,表明为气孔,未见由气孔扩展引起的开裂。在 较高倍率下可见黑斑区表面呈自由表面状态,并有 流变形态,表明为焊缝内原始焊接缺陷。相邻裂面 上可见解理花样,如图 5所示。
铝合金焊接接头产生裂纹特征及产生机理分析
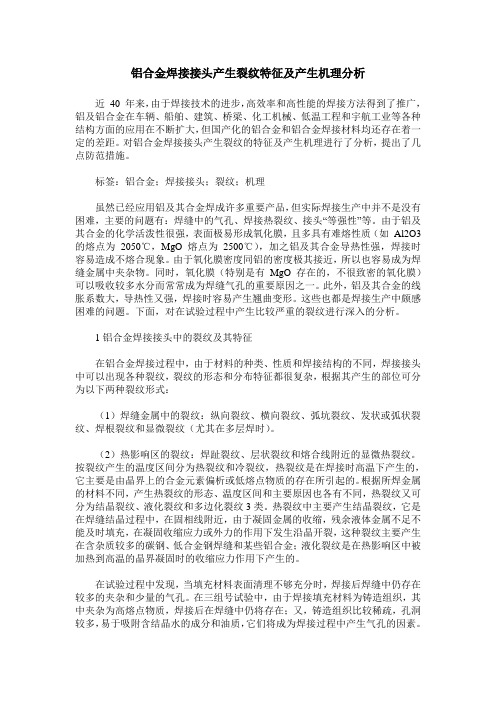
铝合金焊接接头产生裂纹特征及产生机理分析近40 年来,由于焊接技术的进步,高效率和高性能的焊接方法得到了推广,铝及铝合金在车辆、船舶、建筑、桥梁、化工机械、低温工程和宇航工业等各种结构方面的应用在不断扩大,但国产化的铝合金和铝合金焊接材料均还存在着一定的差距。
对铝合金焊接接头产生裂纹的特征及产生机理进行了分析,提出了几点防范措施。
标签:铝合金;焊接接头;裂纹;机理虽然已经应用铝及其合金焊成许多重要产品,但实际焊接生产中并不是没有困难,主要的问题有:焊缝中的气孔、焊接热裂纹、接头“等强性”等。
由于铝及其合金的化学活泼性很强,表面极易形成氧化膜,且多具有难熔性质(如Al2O3的熔点为2050℃,MgO 熔点为2500℃),加之铝及其合金导热性强,焊接时容易造成不熔合现象。
由于氧化膜密度同铝的密度极其接近,所以也容易成为焊缝金属中夹杂物。
同时,氧化膜(特别是有MgO 存在的,不很致密的氧化膜)可以吸收较多水分而常常成为焊缝气孔的重要原因之一。
此外,铝及其合金的线胀系数大,导热性又强,焊接时容易产生翘曲变形。
这些也都是焊接生产中颇感困难的问题。
下面,对在试验过程中产生比较严重的裂纹进行深入的分析。
1铝合金焊接接头中的裂纹及其特征在铝合金焊接过程中,由于材料的种类、性质和焊接结构的不同,焊接接头中可以出现各种裂纹,裂纹的形态和分布特征都很复杂,根据其产生的部位可分为以下两种裂纹形式:(1)焊缝金属中的裂纹:纵向裂纹、横向裂纹、弧坑裂纹、发状或弧状裂纹、焊根裂纹和显微裂纹(尤其在多层焊时)。
(2)热影响区的裂纹:焊趾裂纹、层状裂纹和熔合线附近的显微热裂纹。
按裂纹产生的温度区间分为热裂纹和冷裂纹,热裂纹是在焊接时高温下产生的,它主要是由晶界上的合金元素偏析或低熔点物质的存在所引起的。
根据所焊金属的材料不同,产生热裂纹的形态、温度区间和主要原因也各有不同,热裂纹又可分为结晶裂纹、液化裂纹和多边化裂纹3类。
热裂纹中主要产生结晶裂纹,它是在焊缝结晶过程中,在固相线附近,由于凝固金属的收缩,残余液体金属不足不能及时填充,在凝固收缩应力或外力的作用下发生沿晶开裂,这种裂纹主要产生在含杂质较多的碳钢、低合金钢焊缝和某些铝合金;液化裂纹是在热影响区中被加热到高温的晶界凝固时的收缩应力作用下产生的。
- 1、下载文档前请自行甄别文档内容的完整性,平台不提供额外的编辑、内容补充、找答案等附加服务。
- 2、"仅部分预览"的文档,不可在线预览部分如存在完整性等问题,可反馈申请退款(可完整预览的文档不适用该条件!)。
- 3、如文档侵犯您的权益,请联系客服反馈,我们会尽快为您处理(人工客服工作时间:9:00-18:30)。
(8)焊接接头的耐腐蚀性能低于母材
热处理强化铝合金(如硬铝)接头的耐腐蚀性的降低很明显,接头组织越不均匀,耐蚀性越易降低。焊缝金属的纯度或致密性也影响接头耐蚀性能。杂质较多、晶粒粗大以及脆性相析出等,耐蚀性就会明显下降,不仅产生局部表面腐蚀而且经常出现晶间腐蚀,此外对于铝合金,焊接应力的存在也是影响耐蚀性的一个重要因素。 为了提高焊接接头的耐蚀性,主要采取以下几个措施[5]:1、改善接头组织成分的不均匀性。主要是通过焊接材料使焊缝合金化,细化晶粒并防止缺陷;同时调整焊接工艺以减小热影响区,并防止过热,焊后热处理。2、消除焊接应力,如局部表面拉应力可以采用局部锤击办法来消除。3、采取保护措施,如采取阳极氧化处理或涂层等。
(6)合金元素蒸发ห้องสมุดไป่ตู้烧损
某些铝合金含有低沸点的合金元素,这些元素在高温下容易蒸发烧损,从而改变了焊缝金属的化学成分,降低了焊接接头的性能。为了弥补这些烧损,在调整工艺的同时,常常采用含有这些沸点元素含量比母材高的焊丝或其他焊接材料。
(7)铝在高温时的强度和塑性低
铝在370℃时强度仅为10Mpa,焊接时会因为不能支撑住液体金属而使焊缝成形不良,甚至形成塌陷或烧穿,为了解决这个问题,焊接铝及铝合金时常常要采用垫板。
(2)铝的热导率和比热大,导热快
尽管铝及铝合金的熔点远比钢低,但是铝及铝合金的导热系数、比热容都很大,比钢大一倍多,在焊接过程中大量的热能被迅速传导到基体金属内部,为了获得高质量的焊接接头,必须采用能量集中、功率大的热源,有时需采用预热等工艺措施,才能实现熔焊过程。
(3)线膨胀系数大
铝及铝合金的线膨胀系数约为钢的2倍,凝固时体积收缩率达6.5%-6.6%,因此易产生焊接变形。防止变形的有效措施是除了选择合理的工艺参数和焊接顺序外,采用适宜的焊接工装也是非常重要的,焊接薄板时尤其如此。另外,某些铝及铝合金焊接时,在焊缝金属中形成结晶裂纹的倾向性和在热影响区形成液化裂纹的倾向性均较大,往往由于过大的内应力而在脆性温度区间内产生热裂纹。这是铝合金,尤其是高强铝合金焊接时最常见的严重缺陷之一。在实际焊接现场中防止这类裂纹的措施主要是改进接头设计,选择合理的焊接工艺参数和焊接顺序,采用适应母材特点的
(9)无色泽变化,给焊接操作带来困难
铝及铝合金焊接时由固态转变为液态时,没有明显的颜色变化,因此在焊接过程中给操作者带来不少困难。因此,要求焊工掌握好焊接时的加热温度,尽量采用平焊,在引(熄)弧板上引(熄)弧等[1]。
1.4铝合金焊接方法
几乎各种焊接方法都可以用于焊接铝及铝合金,但是铝及铝合金对各种焊接方法的适应性不同,各种焊接方法有其各自的应用场合。气焊和焊条电弧焊方法,设备简单、操作方便[8]。气焊可用于对焊接质量要求不高的铝薄板及铸件的补焊。焊条电弧焊可用于铝合金铸件的补焊。惰性气体保护焊(TIG或MIG)方法是应用最广泛的铝及铝合金焊接方法[10]。铝及铝合金薄板可采用钨极交流氩弧焊或钨极脉冲氩弧焊。铝及铝合金厚板可采用钨极氦弧焊、氩氦混合钨极气体保护焊、熔化极气体保护焊、脉冲熔化极气体保护焊。熔化极气体保护焊、脉冲熔化极气体保护焊应用越来越广泛(氩气或氩/氦混合气)[3]。
(5)焊接接头容易软化
焊接可热处理强化的铝合金时,由于焊接热的影响,焊接接头中热影响区会出现软化,即强度降低,使基体金属近缝区部位的一些力学性能变坏。对于冷作硬化的合金也是如此,使接头性能弱化,并且焊接线能量越大,性能降低的程序也愈严重。针对此类问题,采取的措施主要是制定符合特定材料焊接的工艺,如限制焊接条件,采取适当的焊接顺序,控制预热温度和层间温度,焊后热处理等。对于焊后软化不能恢复的铝合金,最好采用退火或在固溶状态下焊接,焊后再进行热处理,若不允许进行焊后热处理,则应采用能量集中的焊接方法和小线能量焊接,以减小接头强度降低。
1.3铝合金的焊接特点
(1)强的氧化能力
铝与氧的亲和力很强,在空气中极易与氧结合生成致密而结实的AL2O3薄膜,厚度约为0.1μm,熔点高达2050℃,远远超过铝及铝合金的熔点,而且密度很大,约为铝的1.4倍。在焊接过程中,氧化铝薄膜会阻碍金属之间的良好结合,并易造成夹渣。氧化膜还会吸附水分,焊接时会促使焊缝生成气孔。这些缺陷,都会降低焊接接头的性能。为了保证焊接质量,焊前必须严格清理焊件表面的氧化物,并防止在焊接过程中再氧化,对熔化金属和处于高温下的金属进行有效的保护,这是铝及铝合金焊接的一个重要特点。具体的保护措施是[4]:1、焊前用机械或化学方法清除工件坡口及周围部分和焊丝表面的氧化物;2、焊接过程中要采用合格的保护气体进行保护;3、在气焊时,采用熔剂,在焊接过程中不断用焊丝挑破熔池表面的氧化膜。
焊接填充材料等。
(4)容易形成气孔
焊接接头中的气孔是铝及铝合金焊接时极易产生的缺陷,尤其是纯铝和防锈铝的焊接。氢是铝及铝合金焊接时产生气孔的主要原因,这已为实践所证明。氢的来源,主要是弧柱气氛中的水分、焊接材料及母材所吸附的水分,其中焊丝及母材表面氧化膜的吸附水分,以焊缝气孔的产生,常常占有突出的地位。铝及铝合金的液体熔池很容易吸收气体,在高温下溶入的大量气体,在由液态凝固时,溶解度急剧下降,在焊后冷却凝固过程中来不及析出,而聚集在焊缝中形成气孔。为了防止气孔的产生,以获得良好的焊接接头,对氢的来源要加以严格控制,焊前必须严格限制所使用焊接材料(包括焊丝、焊条、熔剂、保护气体)的含水量,使用前要进行干燥处理。清理后的母材及焊丝最好在2-3小时内焊接完毕,最多不超过24小时。TIG焊时,选用大的焊接电流配合较高的焊接速度。MIG焊时,选用大的焊接电流慢的焊接速度,以提高熔池的存在时间。Al-Li合金焊接时,加强正、背面保护,配合坡口刮削,清除概况氧化膜,可有效地防止气孔。
1.2铝合金的概述
铝合金是以铝为基的合金总称。主要合金元素有铜、硅、镁、锌、锰,次要合金元素有镍、铁、钛、铬、锂等。是工业中应用最广泛的一类有色金属结构材料,在航空、航天、汽车、机械制造、船舶及化学工业中已大量应用。随着近年来科学技术以及工业经济的飞速发展,对铝合金焊接结构件的需求日益增多,使铝合金的焊接性研究也随之深入。铝合金的广泛应用促进了铝合金焊接技术的发展,同时焊接技术的发展又拓展了铝合金的应用领域,因此铝合金的焊接技术正成为研究的热点之一。
摘要
近几十年来,随着科学技术的不断进步,焊接技术也在不断进步,许多高效率和高性能的焊接方法得到了推广。铝及铝合金材料密度低,强度高,热电导率高,耐腐蚀能力强,无磁性,成形性好及低温性能好,具有良好的物理特性和力学性能,因而广泛应用于工业产品的焊接结构上。但国产化的铝合金和铝合金焊接材料均与国外还存在着一定的差距。虽然已经应用铝及其合金焊成许多重要产品,但铝及铝合金由于具有独特的理化性能,因此在焊接过程中会产生一系列的困难,主要的问题有:焊缝中的气孔、焊接热裂纹、接头“等强性”等。本文对铝合金焊接接头产生裂纹的特征及产生机理进行了分析,提出了几点防范措施。
KeyWords:aluminum alloy; Welding joint; Crack; Mechanism; measures
1绪论
1.1引言
铝及铝合金材料密度低,强度高,热电导率高,耐腐蚀能力强,具有良好的物理特性和力学性能,因而广泛应用于工业产品的焊接结构上。随着焊接技术的广泛应用,目前已经应用铝及其合金焊成许多重要产品,但实际焊接生产中并不是没有困难,主要的问题有:焊缝中的气孔、焊接热裂纹、接头“等强性”等。由于铝及其合金的化学活泼性很强,表面极易形成氧化膜,且多具有难熔性质(如 Al2O3的熔点为 2050℃,MgO 熔点为 2500℃),加之铝及其合金导热性强,焊接时容易造成不熔合现象。由于氧化膜密度同铝的密度极其接近,所以也容易成为焊缝金属中夹杂物。同时,氧化膜(特别是有 MgO 存在的,不很致密的氧化膜)可以吸收较多水分而常常成为焊缝气孔的重要原因之一[1]。此外,铝及其合金的线胀系数大,导热性又强,焊接时容易产生翘曲变形。这些也都是焊接生产中颇感困难的问题。
关键词:铝合金;焊接接头;裂纹;机理;措施
Abstract
In recent decades, with the improvement of science and technology, the welding technology also continued to make progress, many high efficiency and high performance welding method for promotion. Aluminum and aluminum alloy material low density, high strength, and thermal conductivity high, corrosion resistance, and a strong ability without magnetic, forming the gender is good and low temperature performance is good, have good physical properties and mechanical properties, and widely used in industrial products of welding structure. But the aluminum alloy and aluminum alloy localization of welding materials are abroad and a big gap between the still exist. Although has been used aluminum alloys welding into many important products, but aluminum and aluminum alloy with their unique physical and chemical properties, so the welding process of will produce a series of difficulties, the main problem: the porosity, welding seam hot cracking, joint "aggressive", etc. In this paper, the aluminum alloy welding joint crack characteristics and produce mechanism are analyzed, and puts forward some preventive measures.