QSB学习资料
GM+质量体系基础QSB培训教材

针对质量事件的标准化快速反应流程:
FR&PS NCM VS LPA EPV WPO SWI (SOS)
QSB WORKSHOP REV. 012307
2
OI (JES) SOT(JIT)
Risk Reduct
Contam
SCM
General Motors Corporation. All rights reserved.
黄色或红色的项目状态 ,应标出目标完成时间
要评估的要点: 责任人
退出标准
整体状态
FR&PS NCM VS LPA EPV WPO SWI (SOS)
QSB WORKSHOP REV. 012307
8
OI (JES) SOT(JIT)
Risk Reduct
Contam
SCM
General Motors Corporation. All rights reserved.
QSB WORKSHOP REV. 012307
11
OI (JES) SOT(JIT)
Risk Reduct
Contam
SCM
General Motors Corporation. All rights reserved.
问题解决
问题是持续改善的种子! 问题是积极的机会! 没有任何问题则意味着有些错 误已经发生!
Contam inated
333933
McGrath 4/29/2005 G
G
G
G
G
G
Y
G
Y
Open
G
2
Burrs
2/15/2005 98002222 Adam s CLOSED G G G G G G G G G 4/23/05
通用QSB+培训内容

QSB 13项内容,目的是让顾客满意QSB+ 15项内容,以TS16949为基础,平衡成本、效益,以达到世界级质量水平(无重大质量事故、零缺陷、零抱怨)维护:1. 维护管理流程2. L1级维护3. 备件管理4. 客户工装管理制造与材料流管理1. 订单接收/评审2. 主生产计划管理3. 生产排程管理4. 包装管理5. 库存管理6. 内部物流管理7. 快速换型(模)管理– 4步法8. 制约因素管理– 6步法外部物流1. 收料过程管理2. 发货过程管理3. 物流供方管理4. 快速反应维护部分:1. 维护对象:设备、工装(模具、夹具、刀具、检具)、周转器具(液压车、料箱、叉车、料架、航车)、通讯工具(信息网络、ERP、EDI)2.维护主体:(1)谁使用谁维护,(2)专业团队维护(车间--设备维护小组、基建–厂房)3. TPM(1)total 全员、全时,强调全面;productive生产性;machine设备(2)TPM:注重异常征兆,积极主动理解设备中断的隐藏原因,在设备失效前发现并纠正那些(可能会导致设备失效的)缺陷。
(3)分类汇总:故障设备类别和故障模式类别4. TPM维护分类:(1)预防性维护-- 预测/事先定义的频次如:定量/定时更换刀具、定期更换部件等。
其中,预测性维护是一种特殊的预防性维护。
(2)条件维护-- 基于设备关键参数的测量如:旋转设备的震动分析、流体分析、自动报警等(3)故障维护–故障后实施的维护,目的是让设备尽可能快的重新启动,尽管可能会采取了降级措施。
5. 维护管理核心流程:(1)编制维护计划/任务-- 针对每一台设备、每一个工装都要有维护作业指导书,要具体到每个设备的每个地方、每个项目(2)编制维护作业指导书并培训-- (JES格式)(3)按计划实施维护并记录(4)月度统计分析-- 针对关键(重点)设备做全面的总结分析,不能太笼统,要具体到某个车间的具体生产线6. 备件管理流程(维护管理支持流程1):(1)编制备件清单-- 找出关键备件(生产瓶颈设备、复杂的设备、昂贵的设备)(2)建立备件库存-- 安全库存、最高库存、最低库存(3)备件领用/更换–废旧零件是否遗留在现场,影响5S(4)盘库存,检查(每月一次,检查数量和质量)(5)统计分析、改进(关注异常的领用、消耗数量,盘存备件是否超差库存)(6)更新备件清单–根据每一类备件的实际使用情况,要关注因配件导致的生产工时损失7. 客户工装管理流程(维护管理支持流程2):(1)验收、标识并目视化-- 不同顾客不同标识;验收记录(1.按照工装图纸的验收记录2.生产验证的验收记录);在验收合格后标识(铭牌优先)(2)客户批准(3)建立客户工装台账(工装易损件的安全库存)(4)储存与库存管理(储存偏重环境库存偏重数量)(5)领用、使用和维护(6)分供方管理(7)替换与再认可(8)处置(报废、封存、改制)8.客户工装分类(1)所有权是客户的工装如:工装夹具、检具、模具、料筐等(2)某个客户产品的专用工装加工单一产品、专用产品9. L1维护(一级维护,即使用者维护)(1)内容:(最终目标:一级维护的内容要占到维护内容的80%以上)建立和维护目视管理和岗位5S清洁和检查执行每日维护(点检、润滑等)质量检查和调试诊断设备原因的缺陷更换工装重置设备出错修改和小调试填写实施记录(2)维护途径:改进维护方法预防污染(3)目视化-- 不同状态标识不同颜色,只看颜色就能立即发现偏差(4)要编制一级维护作业指导书并培训10. 维护的关键绩效指标(1)OEE (单个设备而非整体设备、重点:关键设备、瓶颈设备)(2)TEEP总体有效设备性能(3)MTBF/MTTR 平均运行周期/平均维修周期(单台设备的数据)(4)纠正/预防维护比率(5)设备故障率(6)备件平均库存周转率(7)维护计划达成率(8)设备点检合格率11.目前我司弱项:(1)目视化程度低(2)没有维护作业指导书(3)备件管理不细致(4)没有客户工装标识生产和物料流管理部分:(培训内容与题纲内容有出入)1.流程OP10. 全部客户要求–客户订单初评(客户订单数是否和实际需求数量一致)OP20. 长期战略规划-- (设备、厂房、人员招聘)OP30. 年度销售运行计划(AOP)OP40. 月销售计划(SOP)注意计划与实际的差异,(当期)T+6个月的滚动计划OP50. 主生产计划(MPS)流程的主导和关键步骤主计划每月评审一次,每周要有系统的回顾,并且主计划要沟通到所以部门更改计划、追加变更也要通知到各个部门;需要以下4个方面的支持:1.发运记录2.工装3.原材料采购(外购、外协)4.人员招聘OP60. 生产排程计划/生产任务书2.SOP评审五步法(支持流程)(1)快速换模(SMED)(2)制约因素管理(3)包装与搬运管理(4)储存与库存管理(5)内部支付管理3.快速换模(SMED)最后一个合格零件A结束到生产出第一个合格零件B为止所花费的实际快速换模的优点:减小生产批量、降低库存、提高生产计划响应能力SMED四步法:识别隔离转换(将内部操作转化为外部操作)减少最满意的结果:快速换模时间在30分钟以内4.从全局性、系统性来评审生产计划,要考虑的因素有:(1)产能利用率(2)交付周期(3)原材料周期(4)加工周期(5)装配周期(6)运输周期5.优先订单管理(快反会议,第一时间进行沟通,信息要及时传递到各个部门)(1)客户追加的订单(2)客户不再需求的订单6.瓶颈管理工序产能小于客户需求即为瓶颈最糟糕的瓶颈即为制约因素制约因素管理6步法:(1)明确产品和生产过程(2)识别具体产能瓶颈工位(3)决定如何破解瓶颈(4)重新评估其他瓶颈工位(5)系统瓶颈整体改善(6)瓶颈改善后,PDCA循环,回到第一步7.包装和标签管理对象(现场所有的物料都包含在内,如:胶水、防锈液等)(1)需要验证和认可的成品包装和规范(2)半成品/在制品(3)中转品(4)外协件(5)特殊物料(6)不合格品(变质、混料均为不合格品)(7)样件、调试件8.包装和标签管理内容(目的:把顾客抱怨减少到0)(1)包装标准/规范(原材料、成品、半成品、特殊物料)(2)包装区域管理和目视化(3)空箱、半箱、满箱管理(4)标签防错(成品标签、物流标签、特殊要求标签)-- 重点审核(5)包装维护(清洁)与质量检查以便于循环使用(6)材料处理和存储管理材料处理:打毛刺、方法工具、清洗等存储管理:先进先出、可追溯批次、5S、防异物、防混料、安全库存、帐卡物一致、防潮、防火、防盗等(7)库存品质(质量控制检查)进行周期性检查,要注意标称的保质期和实际保质期的差别9.包装方法/包装规范:1.包装区域规划2.5S 3.空箱管理(什么地方、有多少)10.周转器具管理:满箱、空箱、半箱(零头)管理—长宽高、满载重量、满载体积、质量11.KPI指标相关库存周转率、盘盈盘亏、产量达成率、换型/调机周期、库存差异率、周转箱运转周期、生产线缺料次数、库存水平、交付率、品种完成率等。
GM+质量体系基础QSB培训教材

• 每个问题都必须有一个问题解决报告( Practical Problem Solving Report PPSR)或类似的报告。这个表格会在会议中被回 顾,以汇报问题的整体结构状况,并保持既定的会议时间安排不被 打乱。 ― 希望供应商在早期遏制阶段和针对根本原因采取纠正措施时, 采用问题解决报告PPSR或类似格式进行汇报和更新。
FR&PS NCM VS LPA EPV WPO SWI (SOS)
QSB WORKSHOP REV. 012307
6
OI (JES) SOT(JIT)
Risk Reduct
Contam
SCM
General Motors Corporation. All rights reserved.
快速反应
• 负责人汇报必须包括问题解决报告PPSR中的更新:
14
OI (JES) SOT(JIT)
Risk Reduct
Contam
SCM
General Motors Corporation. All rights reserved.
8D 问题解决流程图
(例)
D1 选择团队
D2 定义问题
D3 遏制问题
D4
识别根本原因
D5
实施长期措施
D6 验证措施的有效性
D7
月份
1月
每日质量状态图
年度
2004
31
29
28
30
(例)
22
24
26
21
23
25
27
13
15
17
19
12
14
QSB质量系统基础概述

负责人
生产部门 1
过程 是 否正确?
是
生产部门 2
工具/刀具 是否正确
是
生产部门 3
相关的开发工程 师/供应商质量/供 应商
4
零件 是否正确
是
零件 质量?
否
是否需要开发支持? 负责人
车辆组装工 艺
5
设计开发 6
工艺更改 是 否解决问题?
否
产品更改 是否需要?
不确定
统计工程 7
极端复杂问题
SDE Module 2011.04
差
最高管理者牵头
0
SDE Module 2011.04
SGM Confidential
5%
New BusinessExcellent
新业务
优
4
Quality Systems Basics
质量系统基础
QSB
引领至世界级质量
Lead to world class quality
• 快速响应 Fast Response • 不合格产品的控制 Control of Non-Conforming Product • 验证岗位 Verification Station • 标准化操作 Standardized Operations • 标准化的操作工培训 Standardized Operator Training • 防错验证 Error Proofing Verification • 分层审核 Layered Process Audits • 风险降低 RPN Risk Reduction • 异物控制 Contamination Control • 供应链管理 Supply Chain Management • 变更管理 Managing Change
QSB(质量体系基础)介绍
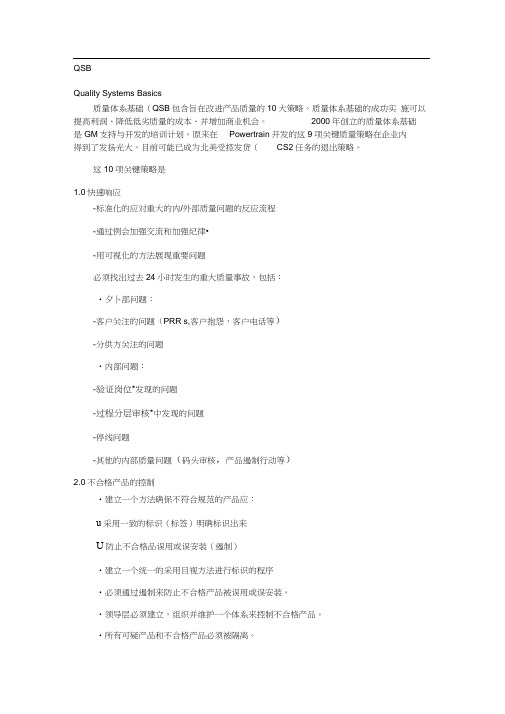
QSBQuality Systems Basics质量体系基础(QSB包含旨在改进产品质量的10大策略。
质量体系基础的成功实施可以提高利润、降低低劣质量的成本、并增加商业机会。
2000年创立的质量体系基础是GM支持与开发的培训计划。
原来在Powertrain开发的这9项关键质量策略在企业内得到了发扬光大,目前可能已成为北美受控发货(CS2任务的退出策略。
这10项关键策略是1.0快速响应-标准化的应对重大的内/外部质量问题的反应流程-通过例会加强交流和加强纪律•-用可视化的方法展现重要问题必须找出过去24小时发生的重大质量事故,包括:•夕卜部问题:-客户关注的问题(PRR s,客户抱怨,客户电话等)-分供方关注的问题•内部问题:-验证岗位*发现的问题-过程分层审核*中发现的问题-停线问题-其他的内部质量问题(码头审核,产品遏制行动等)2.0不合格产品的控制•建立一个方法确保不符合规范的产品应:u采用一致的标识(标签)明确标识出来U防止不合格品误用或误安装(遏制)•建立一个统一的采用目视方法进行标识的程序•必须通过遏制来防止不合格产品被误用或误安装。
•领导层必须建立,组织并维护一个体系来控制不合格产品。
•所有可疑产品和不合格产品必须被隔离。
3.0验证岗位验证岗位就是检查过程是否提供你所要的产品验证岗位也对频发的,低严重度不合格品提醒注意。
验证岗位最终减少缺陷零件数量,改善厂内一次合格率(FTQFirst time quality),直通率(Direct Run),从而在为顾客提供更好产品的同时也降低了成本。
•提供一个系统的方法减少过程变差。
•改善一次合格率(FTQ和提高过程能力:-迅速识别特殊原因变差。
-以数据做决定。
-系统地减少普通原因变差。
•警示操作员过程有变化。
•存在以下状况的任何过程或作业点:-高风险-PRR (顾客抱怨)-高RPN-低过程能力(Ppk, Cpk, FTQ) 任何Cpk或Ppk低于1.33的工序必须100% 检验。
质量系统基础QSB

频率
• 高风险项目应该至少每班检查一 次
• 分层审核频率是基于产量和过程 风险级别,还有相关的程序
目标和要求
• 分层审核应该检验相关的质量文件 • 分层审核结果应被记录下来并在适当的时候加入到经
验教训数据库 • 不合格项应该立即得到处理 • 针对分层审核过程中所检测到的不合格项的应对计划
预生产会议
经验
Life of Part
GM APQP
先 期 产 品 质 量 策 划 (APQP)
选点决定 潜在供应商评审
PSA,TA,TR,风险评估
APQP Kick off
Gate1 review 组建项目小组;建立跟踪墙;时 间进度表;产能分析
核数查模技,样S术件t输a] r入t [oSOf RP,r图o纸du,标c准tio, n
GP9流程的关键概念
GP9流程的结果
• Pass:实际结果满足QTC和LCR要求 • Stage:在项目初期,供应商已经提交了逐
步满足SGM生产要求的产能提升计划(分 阶段LCR),SGM和供应商达成了产能提高 的约定,在GP9验证时符合当时约定的产 量要求 • Fail:运行结果不满足QTC和LCR • 顾客原因失败:因LCR超出合同产能导致的 失败
Nov
Dec
40
50
38
7.9
7.82 8.53 8.19
9
7.81 7.83 6.81
7.6
11.2
8.6
9.45 5.09 7.19 12.54 6.97
SPILL
TOTAL DOWN TIME
2.5
18
2
1.5
1
o
QSB+培训资料
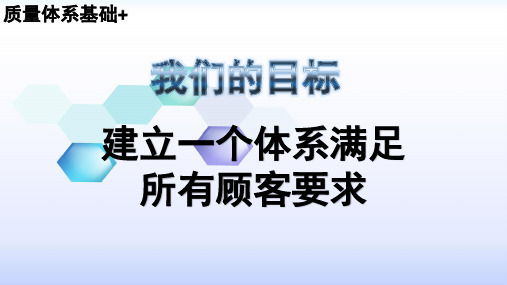
√ 在准备快速反应会议,每天会问题:----客户关注的问题(客户报怨、售后问题、客户电话等)----供应商关注的问题(如需要,可通知供应商到会)2.内部问题:----验证岗位发生的问题----过程分层审核发现的问题----停线问题----其他内部质量问题(如码头审核、产品遏制行动等)----防错装置失效
组织必须√ 指定生产部门负责并执行过程分层审核(质管建立清单)。√ 识别出需要在审核过程中进行验证的高风险项目检查表。√ 如适用,须执行验证特殊工艺审核。√ 建立逐级审核计划和频次。√ 跟踪并评估过程分层审核。√ 将过程分层审核中的问题添加到快速反应、用户认可检查&评估及经验教训数据库。
快 速 响 应 步骤描述
质量体系基础+
G--点检表/数据表 H--工艺点检表(设备) I--极限样件(语言无法描述、主观因素起决定作用、不容易损坏变质) J--培训记录4.执行经验教训
质量体系基础+
选择工位
分层审核流程说明
执行审核
给出反馈记录结果
跟踪
基于过程分层审核计划,选择待审工位(覆盖所有的班次/工位,每月一次)
按照分层审核检查表
立即将审核结果通知所有的组员
在检查表上记录所有的不符合项,并完成相应的对策措施表
指定负责人和完成日期
尽快执行对策措施
跟踪未关闭的项目,确保在目标完成日期前关闭
快 速 响 应
通过目视化的管理,越快、越早地在上游解决问题。帮助问题负责人进行及时的纠正行动
质量体系基础+
快 速 响 应 关键步骤
质量体系基础+
1.收集当天重要的质量问题
2.召开快速响应会议
4.状态跟踪
3.解决问题
QSB+培训资料

质量体系基础+
快速响应
步骤描述
Step4-实施纠正措施 1.头脑风暴,想出可能的解决方案并选择最有效的 2.确认是否需要试生产(或试验)来确认解决方案是否有效 3.确认实施和时间安排 4.识别断点,与所有利益相关方沟通 Step5-验证行动有效性 1.利用分层审核验证预定行动如我们期望的那样工作 2.通过测量和数据,验证有效性 3.建立验证周期 4.确定谁跟进 5.建立标准化的流程和方;
****实业有限公司
快速响应
通过目视化的管理,越快、越早地在上游解决问题。 帮助问题负责人进行及时的纠正行动
质量体系基础+
快速响应
1.收集当天重要的质量问题
关键步骤
****实业有限公司
2.召开快速响应会议
4.状态跟踪
3.解决问题
5.经验教训
质量体系基础+
快速响应
****实业有限公司 三部分之二
质量体系基础+
过程分层审核
第三部分(生产系统) *是否完成安全训导和巡视 *是否符合过程控制计划 *是否符合工厂布局标准 *是否正确使用逐级上报流程 *是否有效的解决问题和实施对策
****实业有限公司 三部分之三
质量体系基础+
过程分层审核
****实业有限公司 总结,必须
5)对于支持职能和特殊工艺审核实施分层审核(LPA),(例如:工艺/产品特殊审核,CQI审核等)
质量体系基础+
过程分层审核
****实业有限公司 我们在寻找什么?
LPA2:涵盖整个操作活动的LPA是由生产部门执行的
1)按计划频次对每个工位都进行审核,应确保: - 覆盖所有的班次 - 每个工位至少每月审核一次 - LPA覆盖遏制行动(例如:挑选,发运全检,GP12等) 2)所有层级都有分层审核计划:明确所有层级人员及其频次(从班组长到高层),覆盖所有制造领域。 3)生产部门跟踪LPA计划
- 1、下载文档前请自行甄别文档内容的完整性,平台不提供额外的编辑、内容补充、找答案等附加服务。
- 2、"仅部分预览"的文档,不可在线预览部分如存在完整性等问题,可反馈申请退款(可完整预览的文档不适用该条件!)。
- 3、如文档侵犯您的权益,请联系客服反馈,我们会尽快为您处理(人工客服工作时间:9:00-18:30)。
1
2
3
4
5
6
7
8
9
10
11
12
13
14
15
16
17
18
19
领导层参与快反会议,督促问题的及时跟进和解决
已关闭问题及时举一反三,防止问题的再发生。
Lesson learned in time
培养问题解决队伍,关键在于找到根本原因通过分层审核及时验证措施的有效落实
Verify action plan based on L.P.A. in time
20
21
22
23
24
25
26
27
28
通过遏制工作表加以遏制(全过程筛选)
在取出点或之前重新回到过程流中(防止漏加工)
Reintroduced into the process stream at or prior to the point of removal 放行时,应按规定程序进行并有授权(独立执行)领导层必须对产品遏制问题进行审核(领导重视)Product containment issues shall be reviewed by Leadership
29
30
31
32
33
34
35
设定报警界限SET ALARM LIMITS 设定报警界限SET ALARM LIMITS 逐级上报流程ESCALATION PROCESSES 逐级上报流程ESCALATION PROCESSES
立即行动响应IMMEDIATE ACTION RESPONSE 立即行动响应IMMEDIATE ACTION RESPONSE 质量反馈/质量汇报QUALITY FEEDBACK / FEEDFORWARD
质量反馈/质量汇报QUALITY FEEDBACK / FEEDFORWARD
36
到达报警界线时,立即采取行动(问题上升)根据验证岗位信息,实施整改(问题解决)Implement corrective actions based on VS data
管理层定期到验证岗位进行巡视/并召开会议(领导重视)3. 验证岗位
Verification Stations 将根本原因/整改行动增加到过程分层审核中(执行确认)Add the Root Cause/Corrective Action to the Layered Process Audit
37
38
39
40
41
42
43
44
45
标准化操作指导书应具有可操作性,采纳工人的意见(全员参与)所有的操作工位均应张贴标准化操作指导书(目视化)
Post Standardized Work Instructions at all operations
当过程/产品更改时,通过分层审核确认更新的操作指导书(及时确认)
发生重大质量或安全事故的工位应张贴警示(风险警示)Station where happen major quality/safe issues post “Quality/ Safe alert ”
46
47
48
49
50。