冷轧薄板断带控制
冷轧热镀锌机组自动控制系统

热镀 锌钢 板作 为 防腐 涂层 产品 , 在 我国建 筑 、 家 电、 汽 车等领 域 , 应用 的广
度和 深度不 断扩大 , 是 国民经济建 设 中常用的 、 基础 的 、 节 能环保 的循环 经济用 材。 ? 我厂 热镀锌机 组于2 0 0 5 年顺 利实现 热负荷 试车一 次成功 , 目前正处 于生产 过程 中 , 其 自动控 制系统 采用 了西 门子 自动化 产品 , 本 文就其 系统 配置 和特 点 及 张力控 制作 一 阐述 。 1 . 工 艺简 介 二镀锌 生产 线 由法 国克 莱西姆 公司 负责总 体设 计 , 关键设 备从 法 国、 美 国 引进 , 最 高工艺速度 可达 到 1 2 0 米/ S Y t : 0, 设计 年产 热轧镀锌 钢板5 o 7 z 吨, 产 品规 格 为0 . 8 ~5 . O m m ×8 2 0 -1 6 5 0 am; r 主 要设 备有2 台开 卷机 、 1 台 窄搭接 焊机 、 入 口活套 、 布 里克 蒙卧式退 火炉 、 锌锅 及气 刀 、 冷 却段 、 光整 机 、 拉 矫机 、 钝化 系统 、 出 口活 套 、 涂 油机 、 飞剪、 2 台卷取 机 。
[ 摘 要] 介绍了冷轧薄板) -2 #连续热镀锌生产线带钢的 自动控制系统, 其 自动控制系统采用了西门子 自动化产品, 本文就其系统配置和特点以及张力控
制作一 阐述 。 [ 关键 词] 热镀 自动 控 制 西 门子
中图分 类号 : T P 2 7 3 . 5
文 献标 识码 : A
文章编 号 : 1 0 0 9 — 9 1 4 X( 2 0 1 4 ) 0 7 — 0 3 1 6 一 O l 操 作指 令及 设定值 的选 择和 下达 ; 辅 助传 动控 制命令 的产 生 ; 穿带 、 甩尾、 定位 等自动顺序控制 ; 传动的接通、 关断控制及状态监视; 成组及单独点动操作 ; 带
冷轧薄板生产线卷取机控制要点
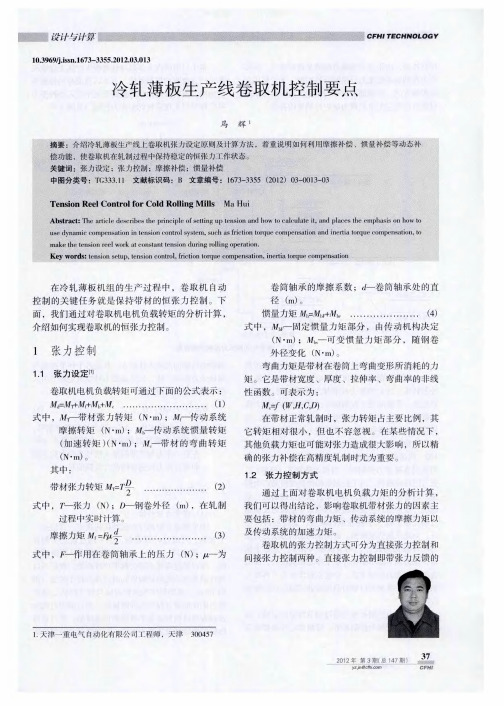
用 中 ,一般 我们 测取 十个 特征 点 (见 图 3a)。
(3) 带材 弯 曲力矩补偿
带材弯曲力矩的计算公式是非常复杂 的非线性
函数 。函数 中带材 的厚 度 、宽度 、拉伸率 在 同一道
次 轧制 时变化 很小 ,可 以看 成是 常量 。因此这 里 只
速度 实 值
际 值
【a)
(b)
D _最 小 卷 径 值 (m);D 一最
大卷径值 (m); 一按最大卷径值
和 最 大 加 速 度 下 标 定 的可 变 惯 量
极 速力矩 系数 。
需要注意 的是 ,通过计算获得 的惯
量 转 矩 值 ,都 统 一 按 电机 额 定 转 矩 进 行
标定 。
(2) 摩擦 力 矩补偿
理论上讲 ,卷取机摩擦力矩可以通过摩擦力矩
2012年 第 3期(总 147期)
yz.is@cfhLcom
蕊◇0设计s计算
交 流 电 流 检 测
图 2 卷 取 机 直接 张 力控 制 系统 框 图
要 根据 卷径 变化 实时计 算 。
数
式 中 ,
11诅 x
…
…
…
可变惯量加速力矩
(6)
…
(N·m);
D 广 实 际 卷 径 计 算 值 (m);
一 曩 技 了lc
设待s计算 l
闭环 控制 ,由张力 传感器 直接 测量 带材 张力 。问接 张力控 制 为不带 张 力反馈 的开 环控 制 。无 论采 用何 种控 制方 式 ,为保 证带 材张力 恒定 ,需 要对 影响带 材 张 力的其它 电机 负载 力矩进 行精 确 的补偿 。
鉴 于 目前 国内大多 数冷轧 薄板 生产 线上卷 取机 都 采用 直流驱 动控 制系 统 。下 面 以直 流驱 动控制 系 统为例,说明如何在张力控制系统 中引入各种张力 补偿 环节 以实现带 材 的恒张力 控制 (见 图 1)[21。
浅析本钢连退机组退火炉快冷段断带
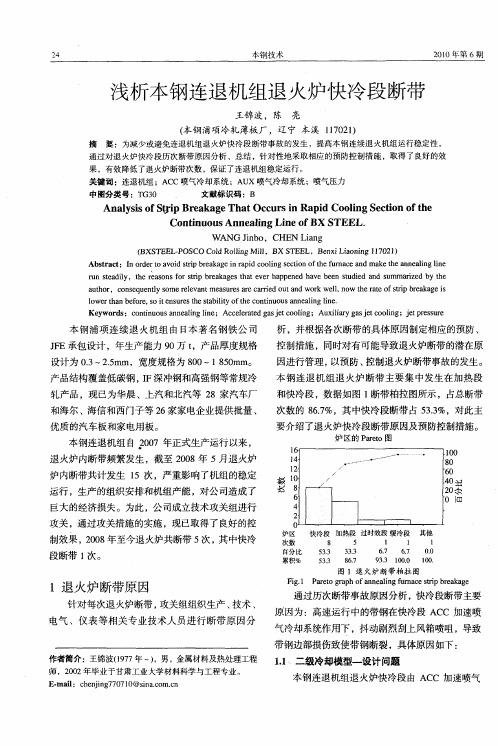
Ke w rs ot uu na n n ;A cl a dg secoig y od :cni o s n el gl e ce rt a t o l ;Auiay a to l g jt rsue n a i i e e j n xl sec oi ; e pesr i g j n r
2 4
本钢 技 术
2 1 第 6期 0 0年
浅析本钢连退机组退火炉快冷段断带
王锦 波 .陈 亮
( 本钢浦项冷轧薄板厂 ,辽宁 本溪 I 0 1 J 2) 7
摘 要 :为减少或避免连退机组退火炉快冷段断带事故 的发生 ,提高本钢连续退火机组运行稳定性 , 通过对退火炉快冷段历次断带原 因分析 、总结 ,针对性地采取相应的预防控制措 施 ,取得 了良好的效
本 钢浦 项 连 续 退 火 机 组 由 日本著 名钢 铁 公 司 JE承包设 计 ,年生产 能力 9 F 0万 t 品厚度规 格 ,产
析 ,并根据各次断带 的具体原因制定相应的预防、
控制措施 ,同时对 有可能导 致退火 炉断带 的潜 在原 因进行 管理 , 以预 防 、 控制 退火炉 断带事故 的发生 。 本 钢 连 退机 组 退 火 炉 断带 主 要 集 中发 生 在加 热段
果 ,有效降低 了退火炉断带次数 ,保证 了连退机组稳定运行。 关键词 :连退机组 ;A C喷气冷却系统 ;A X喷气冷却 系统 ;喷气 压力 C U
中圈分 类号 :T 3 G0 文献标识码 :B
An lss f ti e k g a c r p dCo l gS c ino e ay i j p Bra a eTh t o S' Oc u si Ra i oi e t f h n n o t
通过历次断带事故原因分析 , 快冷段断带主要 原因为:高速运行中的带钢在快冷段 A C 加速喷 C 气冷却系统作用下 , 抖动剧烈刮上风箱喷咀 , 导致
冷轧薄板 L2 HMI 操作手册

冷轧薄板L2 HMI 操作手册从开始菜单程序中启动二级自动化控制系统(版本号),或者从桌面快捷方式双击启动程序。
程序启动后,需要输入登录信息,其中用户名:自动默认为产线名称,产线名称可以在选项界面进行配置(详见选项界面)密码:自动默认为产线名称。
班别:操作工根据自己所在班别进行选择(以程序为准)班次:自动根据当前时间进行选择,一般不需要操作工手工选择(以程序为准)登陆后,进入二级自动化控制系统的主界面1450_1:产线名称乙班:当前生产班别白班:当前生产班次与L1通讯正常(不正常):显示与L1通讯状态待轧钢卷(列表):显示等待轧制的钢卷列表下一卷(列表):显示即将上线轧制的钢卷列表当前在线钢卷(列表):显示当前正在轧制的钢卷列表自动排程:自动(或手动)将待轧钢卷状态修改为下一卷沿用策略:沿用(或不沿用)上一个钢卷的轧制策略下一卷:手动将待轧钢卷修改为下一卷待轧:手动将下一卷状态修改为待轧自动上线:自动(或不自动)将下一卷状态修改为当前在线钢卷上线:手动将下一卷状态修改为在线钢卷下一卷:手动将在线钢卷修改为下一卷待轧钢卷数量:统计数据库中所有待轧状态的钢卷数量与重量轧成钢卷数量:统计数据库中所有轧成状态的钢卷数量与重量断带钢卷数量:统计数据库中所有断带状态的钢卷数量与重量钢卷号:显示所选钢卷的钢卷号来料厚度:显示所选钢卷的来料厚度钢种牌号:显示所选钢卷的钢种牌号目标厚度:显示所选钢卷的目标厚度来料卷重:显示所选钢卷的来料卷重来料宽度:显示所选钢卷的来料宽度PDI:进入PDI管理界面PDO:进入PDO管理界面设定计算:进入设定计算界面报表:进入报表管理界面用户:进入用户管理界面轧制表:进入轧制表管理界面通讯:进入通讯管理界面选项:进入选项界面退出:退出程序PDI管理界面搜索:输入部分或全部钢卷号搜索,显示跟所输入的字符相关的钢卷号的钢卷创建:创建新的PDI修改:修改所选择的PDI删除:删除所选择的PDI全部:显示全部的PDIPDI的当前状态显示PDI的数据:钢种牌号原料卷重原料宽度原料厚度目标厚度是否切边修改:可以修改PDI的数据值创建PDI:用户可以在此界面输入PDI数据,点击确定按钮,保存到数据库中或者也可以从其他PDI复制,只要选择要复制的PDI就可以钢卷号一般会自动生成。
八钢冷轧轧机断带的分析与对策
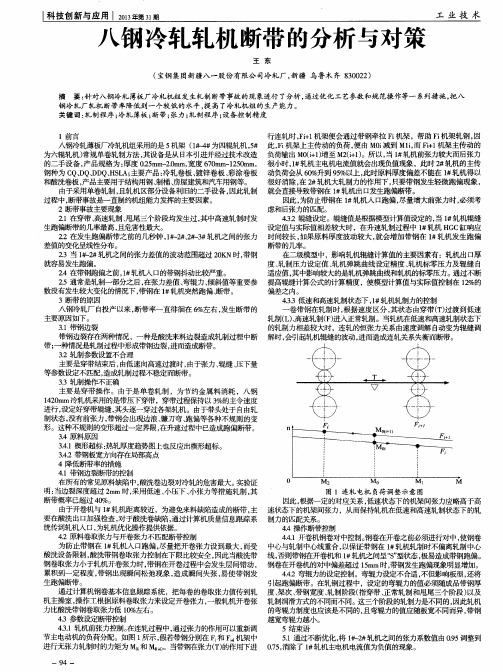
工 业 技 术
八钢冷轧轧机 断带 的分析与对策
王 东 Biblioteka ( 宝铜集 团新疆八 一股份有 限公 司冷轧厂 , 新疆 乌鲁木齐 8 3 0 0 2 2 ) 摘 要: 针对八钢冷轧薄板厂冷轧机组发生轧制断带事故 的现 象进行了分析, 通过优化 工艺参数和规 范操作等一 系列措施 , 把八 钢冷轧厂轧机断带率降低到一个较低的水平 , 提高了冷轧机组的生产能力。 关键词: 轧制程序 ; 冷轧薄板 ; 断带 ; 张力; 轧制程序 ; 设备控制精度
1 前 言 八钢冷轧 薄板厂冷轧 机组采用 的是 5 机架 ( 1 } 为四辊轧机 , 5 # 为六辊 轧机 ) 常规 单卷轧制方 法 , 其设 备是从 1 3 本引进并 经过技 术改造 的二手 设备 , 产 品规格 为 : 厚度 0 . 2 5 m m - 2 . 0 m m, 宽度 6 7 0 m m ~ 1 2 5 0 m m, 钢种 为 C Q、 D Q 、 D D Q、 H S L A; 主要产 品 : 冷 轧卷 板 、 镀锌 卷板 、 彩涂 卷板 和酸洗卷 板 , 产 品主要用 于结 构用钢 、 制桶 、 房屋建 筑和汽车用 钢等 。 由于采用 单卷轧 制 , 且轧机 区部分 设备利 旧的二手 设备 , 因此轧制 过程 中 , 断带 事故是一直 制约机组能力 发挥的主要 因素。 2断带事故主要 现象 2 1在穿带 、 高 速轧制 、 甩尾 三个 阶段均发生过 , 其中高 速轧制时发 生跑偏 断带的几率最 高 , 且危害 陛最 大。 2 . 2在发 生跑偏 断带之 前的几 秒钟 , 1 # - 2 # 、 2 # - 3 # 轧 机之 间的张力 差值 的变 化呈线性分布 。
行连轧时, F i + l 机架便会通过带钢牵拉 F i 机架,帮助 F i 机架轧钢 , 因 此, F i 机架上主传动的负荷 , 便 由M0 i 减到 Ml i , 而F i + l 机架主传动的 负荷 输出 M0 ( i + 1 ) 增至 M2 ( i + 1 ) 。所 以 , 当1 # 轧机前张力 较大而后张力 很小时, 1 #轧机主电机电流值就会出现负值现象 , 此时 2 # 轧机的主传 动负荷会从 6 %Y 0 - I - N 9 5 %以上 , 此时原料厚度偏差不能在 1 } } 轧机得 以 很好 消 除 , 在2 } } 轧机大 轧制力 的作用下 , 只要 带钢发 生轻微 跑偏 现象 , 就会直接导致带钢在 1 # 轧机出口发生跑偏断带。 因此 , 为防止带 钢在 1 #轧机入 口跑偏 , 尽量 增大前 张力 时 , 必 须考
冷轧板夹杂类表面缺陷成因分析及控制
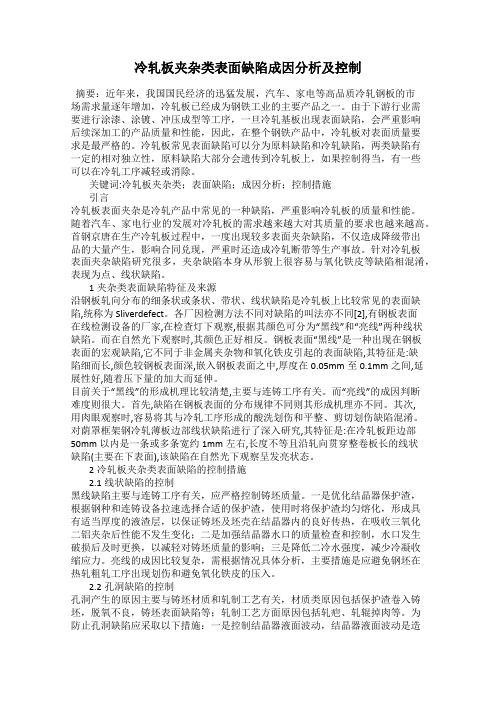
冷轧板夹杂类表面缺陷成因分析及控制摘要:近年来,我国国民经济的迅猛发展,汽车、家电等高品质冷轧钢板的市场需求量逐年增加,冷轧板已经成为钢铁工业的主要产品之一。
由于下游行业需要进行涂漆、涂镀、冲压成型等工序,一旦冷轧基板出现表面缺陷,会严重影响后续深加工的产品质量和性能,因此,在整个钢铁产品中,冷轧板对表面质量要求是最严格的。
冷轧板常见表面缺陷可以分为原料缺陷和冷轧缺陷,两类缺陷有一定的相对独立性,原料缺陷大部分会遗传到冷轧板上,如果控制得当,有一些可以在冷轧工序减轻或消除。
关键词:冷轧板夹杂类;表面缺陷;成因分析;控制措施引言冷轧板表面夹杂是冷轧产品中常见的一种缺陷,严重影响冷轧板的质量和性能。
随着汽车、家电行业的发展对冷轧板的需求越来越大对其质量的要求也越来越高。
首钢京唐在生产冷轧板过程中,一度出现较多表面夹杂缺陷,不仅造成降级带出品的大量产生,影响合同兑现,严重时还造成冷轧断带等生产事故。
针对冷轧板表面夹杂缺陷研究很多,夹杂缺陷本身从形貌上很容易与氧化铁皮等缺陷相混淆,表现为点、线状缺陷。
1夹杂类表面缺陷特征及来源沿钢板轧向分布的细条状或条状、带状、线状缺陷是冷轧板上比较常见的表面缺陷,统称为Sliverdefect。
各厂因检测方法不同对缺陷的叫法亦不同[2],有钢板表面在线检测设备的厂家,在检查灯下观察,根据其颜色可分为“黑线”和“亮线”两种线状缺陷。
而在自然光下观察时,其颜色正好相反。
钢板表面“黑线”是一种出现在钢板表面的宏观缺陷,它不同于非金属夹杂物和氧化铁皮引起的表面缺陷,其特征是:缺陷细而长,颜色较钢板表面深,嵌入钢板表面之中,厚度在0.05mm至0.1mm之间,延展性好,随着压下量的加大而延伸。
目前关于“黑线”的形成机理比较清楚,主要与连铸工序有关。
而“亮线”的成因判断难度则很大。
首先,缺陷在钢板表面的分布规律不同则其形成机理亦不同。
其次,用肉眼观察时,容易将其与冷轧工序形成的酸洗划伤和平整、剪切划伤缺陷混淆。
冷轧自动化的过程控制

冷轧自动化的过程控制2身份证号码:6227271986****0137新疆乌鲁木齐市830022摘要:现阶段计算机技术、传感器技术以及网络技术等的迅速发展,为自动控制领域的进步发展营造了极其良好的条件,当下工业生产自动化技术越来越成熟,应用效果越来越稳定。
因此在当下冷轧生产过程中,为了提高生产的效率和生产的质量,要积极做好对自动化控制系統的应用和研究。
基于此,文章对当下冷轧自动化的过程控制进行了分析和研究,并提出了相关建议,以供借鉴。
关键词:冷轧自动化;过程控制;研究引言冷轧过程一般在室温下进行操作,对钢材进行轧制的一个制造加工流程,原材料一般是4mm以下的热轧薄板,经过自动化加工轧制成为所需厚度的钢板,属于生产制造行业中的高端材料,目前对轧制成品的要求越来越高,因此,冷轧自动化工艺的要求越来越高,冷轧工艺成为关键问题,它是冶金制造业的重要加工技术。
现阶段,冷轧生产线的精度、效率、操作稳定性等诸多要求使得相应的计算机控制技术需要进一步提升。
1.冷轧自动化控制系统冷轧自动化控制系统指的是在冷轧生产过程中的自动化进程,在具体生产中通过应用相应的数学控制模型、自动控制装置、计算机程序等来实现对整个冷轧过程参数变化的有效管控,使其可以保持在一个既定的阈值范围内,从而实现对整个冷轧生产的自动化操作和自动化控制。
在当下市场中对于冷轧板的要求越来越高,所以在当下冷轧生产中,通过自动化控制系统来提高生产质量,已经成为冷轧生产中最为重要的一个部分。
二级计算机系统在整个冷轧自动控制中有着非常重要的作用,具体作用如下:材料跟踪,以便于实现对大规模生产的有效控制;通过系统模型来进行相关参数值的设置和计算,再反馈到轧钢生产现场,从而为现场控制设备的操作提供帮助,降低操作压力,促进生产质量的提高;通过神经网络控制来实现对相关产品生产过程的优化,降低能耗,提高生产效率;预留日志,以此为基础工程师就可以更好地实现对相关技术参数的掌握和控制。
冷轧板常见表面缺陷及成因

冷轧板常见表面缺陷及成因冷轧板常见表面缺陷及成因冷轧板常见表面缺陷有麻点缺陷、冷硬板中部穿裂、冷硬板边裂、带状翘皮、不连续点线状缺陷、黑(灰)线(带)缺陷等。
1麻点缺陷。
单个麻点呈不规则分布,整体呈现带状分布。
麻点在微观上由许多微小的凹坑组成,凹坑内部看到很多细小的颗粒。
凹坑部分杂质元素与结晶器保护渣成分基本一致,说明这些夹杂主要来自结晶器保护渣。
2冷硬板中部穿裂。
中部穿裂部位悬挂着许多鳞状碎片,大块的鳞状碎片边沿包含许多细小的小颗粒,断口为脆性形貌。
细小颗粒与结晶器保护渣成分相似,确定这些夹杂主要来自结晶器保护渣。
3冷硬板边裂。
边裂处呈锯齿状,裂口部位包含大量大小不一的颗粒,颗粒与基体之间无明显间隙,部分颗粒沿平行于裂口方向呈线状分布,同样这些颗粒来自结晶器保护渣。
4带状翘皮。
带状翘皮在板材近表层有一明显薄层与基体发生分离或半分离状态,翘皮部位皮下含有大量粉状物质,能谱分析,这些物质主要来源于变性后的结晶器保护渣。
5不连续点线状缺陷。
板材厚度薄于1mm,该缺陷易发生。
线状缺陷多成簇出现,缺陷底部残留了硅酸盐复合夹杂物。
主要是CSP铸坯中坯壳及皮下、中心部位富集的夹杂物,在热轧过程中,随着厚度变薄,逐渐呈现。
6黑(灰)线(带)缺陷。
酸洗后的宏观形貌有条状、长条状、块状或多点状,轮廓特别分明。
由于1)轧辊质量不佳,主要是氧化膜剥落、老化粗糙、剥落、异物粘附等。
2)除鳞不干净,主要由于喷嘴堵塞、喷嘴压力低等因素。
3)工艺因素,机架间冷却水控制不规范等。
4)连铸至F7前输送辊道划伤,主要由于炉辊结瘤、异物粘结、死辊等。
以上因素导致氧化铁皮压入,从而在冷硬板上形成黑(灰)线(带)缺陷。
冷轧产品质量缺陷及改正措施一、冷轧与镀锌产品外在质量冷轧薄板之所以说是精品,一个主要的原因就是冷轧薄板对表面质量的严格要求。
可以说,在整个冶金行业中,冷轧薄板对表面质量是要求最高最严的,尤其是宽而薄的冷轧钢带产品和对冲压成型性能有严格要求的产品。
- 1、下载文档前请自行甄别文档内容的完整性,平台不提供额外的编辑、内容补充、找答案等附加服务。
- 2、"仅部分预览"的文档,不可在线预览部分如存在完整性等问题,可反馈申请退款(可完整预览的文档不适用该条件!)。
- 3、如文档侵犯您的权益,请联系客服反馈,我们会尽快为您处理(人工客服工作时间:9:00-18:30)。
1500HC双机可逆轧机断带的控制朱兆顺1夏新禾2罗军31.武钢集团鄂钢公司技术中心,湖北鄂州 4360022.武钢集团鄂钢公司公司办,湖北鄂州 4360023.武钢集团鄂钢公司冷轧薄板厂,湖北鄂州 436002摘要:争对断带现象,从设备、电器、原料、工艺、操作等方面进行了分析,提出了相应的改进措施,控制了断带现象。
关键词:原料工艺断带1500HC two-plane break with the controlof reversing millZhu Zhaoshun 1 Xia Xinhe 2 Luo Jun 31. Wuhan Iron and Steel Group E Steel Co., Ltd. Technical Center, Hubei Ezhou 436,0022. Wuhan Iron and Steel Company Group, Hubei Office, Hubei Ezhou 436,0023. Hubei Wuhan Iron and Steel Group, Cold Rolling Mill Steel Co., Ltd., Hubei Ezhou 436,002Abstract: The contention of the thrust belt phenomena, from the equipment, electrical equipment, raw materials, technology, operations and other aspects of the analysis, put forward the corresponding improvement measures to control the phenomenon of the broken belt.Key words: raw materials technology belt1.前言鄂钢1500mmUCM双机架六辊可逆轧机于2007年4月调试。
该机型采用小直径工作辊, 工作辊正、负弯辊,中间辊正弯辊,中间辊横移三种板形控制方式,可有效提高压下率并改善板形质量。
双机架可逆轧机国内目前只有4套,都是2004年以后筹建项目,没有成熟经验,调试难度大。
轧机调试期间,截止10月份发生100多起断带故障(如表1)。
断带的碎片使工作辊、中间辊粘结,有时废带与支撑辊发生严重粘结。
粘结的废带堵在轧机内,使中间辊、工作辊抽出相当困难。
且因双机架轧机结构布置紧凑,废带清理时间长、残留碎片多。
表1 轧机调试断带情况经统计分类,造成断带的主要类别有:电控故障;来料缺陷;轧件跑偏;轧制规范不合理等;次要原因有:轧机振动、操作不当、液压系统故障等。
所占的比例如表2。
表2 断带频率2.原因分析2.1来料缺陷2.1.1热轧过程中带钢原料厚度不均,原料板型有严重的边浪或中间浪。
冷轧时浪型处易形成折叠,折叠处剧烈变形造成断带。
2.1.2热轧时氧化铁皮未除干净,压人带钢表面,酸洗不掉,冷轧时氧化铁皮黑点便扩展延伸呈黑色状,带钢表面形成凹坑,凹坑部位在轧制过程中受拉应力。
当拉应力及附加延伸超过轧件的强度及延伸率时,造成带钢。
2.1.3在酸洗过程中存在严重的欠酸洗、过酸洗。
欠酸洗有氧化铁皮压入形成凹坑,过酸洗使带钢表面产生小孔,使带钢的塑性降低。
在冷轧过程中,塑性低的部位被拉断造成断带。
2.1.4酸洗来料最主要的缺陷是带钢边部有锯齿边(也叫啃边),产生原因有:园盘剪剪刃使用时间较长、剪刃间隙太大、剪刃磨损不均、剪刃上有缺口造成等。
有此缺陷的带钢会产生应力集中,在冷轧过程中随着厚度逐渐减薄,加工硬化,变形抗力增加,钢材的塑性和韧性下降。
在大张力的作用下,带钢有裂边的地方应力瞬间增大,撕裂带钢。
2.2轧件跑偏初期调试过程中,轧机在20m/min速度起动慢速轧制,带钢经常向传动侧跑偏使带钢边部折皱进人轧机。
轻微时发生轧辊划伤,严重时刮破带钢边部,在张力作用下,撕断带钢。
经分析主要原因有:2.2.1 来料厚薄不均;2.2.2 在第一道次开卷张力太小,上道工序酸洗卷取张边过小,使带钢轧制时产生偏移;2.2.3轧制过程中带钢不在轧制中心线上轧制,与卷取机中心不线对中,作用在带钢两边轧制压力不均衡,促使带钢朝一边倾斜。
2.2.3 卷取机与轧辊轴线不平行,带钢不能均衡卷取。
2.3轧制规范不合理造成断带冷轧工艺中压下量的分配应考虑电机功率允许范闱。
还应考虑设备能力和设定速度、轧辊强度、原料和成品尺寸等;由于初道次带钢塑性较好压下率尽量大一些,单位张力取得较小。
随累计压下率增加,加工硬化加剧,压下量分配较小,单位张力取得较大一些。
但是在初期轧机调试时,对轧制规程的计算和张力计算、分配不合理,引起在最后一道次变形量不大但轧制力反而偏大,造成板型不良,以致断带。
2.4电气控制系统故障2.4.1为了保证轧制正常和设备运转正常,电气设备控制系统有许多联锁条件和保护设备位,电机的极限值控制。
如果突然某个联锁条件不满足、轧机就会自动停车,在停车前几秒钟造成张力波动或张力消失发生断带。
如工作辊换辊辊道下降限位信号丢失,三个测张辊掉电致使带钢断带。
2.4.2测厚仪故障:在轧制时测厚仪所得值波动较大,轧机调整液压压上缸的伺服阀根据测厚仪测出结果反馈,到计算机进行闭环控制调整,误差较大时,造成压上缸向上压断带钢而发生断带。
2.4.3测速仪故障:在反穿带时乳化液薄膜阀关不严液体喷到镜头上,测不到速度,张力无法计算,导致失张断带。
2.4.4电机电流和轧机的轧制力超过一定的极限值造成主传动跳闸造成断带。
2.5操作失误不当2.5.1由于操作人员在轧制过程中调整板型需要调整轧制力使厚度达到目标要求;要根据视在板型来调节钢板的板型,应调节中间辊、工作辊弯辊量。
轧制时板型出现中间浪和边浪在加减弯辊时,忙中出错,操作失误到轧制压力柄上压断带钢产生断带。
2.5.2主操作工在轧制力生效时,设定轧制力过高,在轧机启动一瞬间压断带钢发生断带。
2.5.3来料有溢出边,在高速轧制时,或开卷机CPC对中反映不灵敏时应降速,但操作工未降速。
2.5.4前道次由于事故停车再启动时,钢卷某处厚度波动较大,后道次轧制时未计算圈数或抬压下造成断带等。
2.6轧机振动轧机振动一般发生在高速轧制薄带钢时,由于轧机振动,带钢厚度产生波动,局部张力失控,当波动超过一定极限时,造成断带。
轧机振动的原因有:2.6.1穿带时钢板进入钳口未卷平,致使轧件抖动较大;2.6.2轧制速度较高,成品厚度薄;2.6.3成品道次的轧制力较低,带钢前张力较大;2.6.4润滑情况太好或太坏,工作辊使用时间较长,粗糙度不够,支撑辊有损伤,轧辊轴承和轴承座之间的间隙较大等。
2.7液压和机械系统故障在轧制过程中液压系统泄漏和伺服阀的堵塞造成AGC系统的工作压力不正常,使厚度波动较大发生断带;张力辊和卷取机工作不正常自动停车,也造成瞬间张力丢失和变大,拉断带钢。
3.解决方法和防范措施3.1来料缺陷预防措施:3.1.1检查热轧卷外形质量,带钢不能有较大边浪和中间浪,否则挑出。
3.1.2检查热轧卷外形尺寸和表面质量,发现问题及时处置。
3.1.3酸洗机组加强酸液浓度检查,保证酸洗生产正常,防止过酸洗、欠酸洗。
3.1.4酸洗圆盘剪工序要按剪切厚度控制剪刃间隙、重迭量,发现问题及时调整。
3.1.5酸洗机组针对来料质量缺陷做好记录,反馈到轧机以便于轧机在轧制时酌情处理。
3.2轧制时轧件跑偏的解决方法:3.2.1保证来料厚度尺寸精度在公差范围内。
3.2.2上道工序应与下道工序的张力匹配,即酸洗机组的酸洗卷取张力在设备允许的情况下尽量大些,而轧机的开卷张力应小于或等于酸洗卷取张力。
开卷张力设定在恒定状态,轧制时应控制波动范围。
3.2.3轧制过程中操作工在起步开始时要认真观察钢板的位置,根据钢板偏移方向来适当调整轧机的倾斜值(双摆),使其钢板在轧制中心线上轧制,用外力控制其钢板跑偏。
轧制时如发现严重跑偏应及时停车,抬起轧辊辊缝,将带钢拉正、拉直后再重新启动轧制。
3.3轧制不合理断带解决方法针对轧制规范不合理,随着调试轧制过程、多种规格的调试轧制,应对相同规格轧制规范、轧制力计算、分配和张力计算、分配数据,应保存下来对比,通过下道工序(镀锌和平整机组)的质量信息反馈来优化轧制规范、压下规程,稳定板型,防止断带。
3.4电气控制系统故障造成断带解决方法3.4.1对造成停车的工作辊换辊轨道、三个测张辊、转向夹送辊等极限信号应加强紧固,防止松动。
3.4.2轧制时应对测厚仪(测速仪)的运行情况进行检查,按操作规程每8小时校正一次测厚仪。
3.4.3轧制时应注意主传动的各电机的电流值,以防超过保护极限值跳闸停车。
发现有异常现象应及时通知电气控制系统的负责人,尽量把隐患消灭在萌芽状态。
3.5操作失误造成断带解决方法3.5.1操作工之间应互相学习,提高操作技术水平,特别是对本岗位的按钮和按钮位置做到心中有数;出现紧急情况时,应做到忙而不乱,操作时应确认到位,了解本岗位操作按钮、设备的性能和调整范围,养成良好的操作习惯,针对不同的问题制定出不同的解决方法。
3.5.2主操工应对轧制规格的每一道次轧制力设定做到心中有数,设置轧制力时不能过大。
3.5.3在轧制来料有缺陷带钢和CPC对中反映不灵敏时,应降速轧制。
3.5.4轧制中途停车的带钢对当时卷径作好记录,下一道次到此卷径时应降速轧制。
3.6轧机振动造成断带解决方法轧制薄带时避免高速;穿带操作时尽量将进入钳口带钢卷平;尽量将成品道次轧制力和变形量分配合理;对张力分配按情况而定;机械润滑应有专人负责检查,严格执行换辊制度;换辊组应对轧辊轴承和轴承座勤检查,勤清洗,尽量消除轧机振动,保证轧机的正常运行。
3.7液压和机械系统故障造成断带解决方法轧制时轧钢工应配合轧机液压工密切注意传动系统、AGC系统压力变化和液压伺服阀的工作情况,发现异常情况及时向液压工反映处理,以免发生事故。
时刻注意张力辊和卷取机运转情况,发现异响和不正常情况及时停车,向点检工反映及时处理。
4.取得效果采取上述措施后,有效地控制了轧制中的断带。
断带的处理效率也大大提高。
断带明显减少,每月小于1次。
5.结束语通过对断带的分析,找出了断带原因,制定了相应的解决方法和防范措施。
这些方法和措施加速了冷轧调试进度,为冷轧薄板顺利投产、达产发挥了有效的作用。
参考文献[1]傅作宝.冷轧薄钢板生产. 北京:[M]冶金工业出版社,2005.[2]曲克.轧钢工艺学. 北京:[M]冶金工业出版社,2004.[3]赵家骏,魏立群.冷轧带钢生产问答.北京:[M]冶金工业出版社,2004.朱兆顺1962-3,男,汉,湖北省武汉市,高工,科长,本科,轧钢工艺管理。