钢板表面缺陷
钢板表面气泡缺陷

钢板表面气泡缺陷
钢板表面出现气泡缺陷可能是由以下原因导致的:
1. 炼钢过程中的问题:在炼钢过程中,钢水中可能混入了气体,如氢气、氮气等。
这些气体在凝固过程中无法及时逸出,形成了气泡缺陷。
2. 连铸过程中的问题:在连铸过程中,钢水在凝固时可能会产生气泡。
这可能是由于钢水的脱氧不充分、浇铸速度过快或结晶器设计不合理等原因导致的。
3. 轧制过程中的问题:在轧制过程中,钢板表面的气泡可能会被压扁并拉长,形成长条状的缺陷。
这可能是由于轧制温度过高、轧制速度过快或轧辊表面状况不佳等原因导致的。
4. 钢板表面的污染:钢板表面的油污、锈蚀或其他污染物可能会阻碍气体的逸出,从而导致气泡缺陷的形成。
为了减少钢板表面气泡缺陷的出现,可以采取以下措施:
1. 优化炼钢工艺,确保钢水的脱氧充分。
2. 改进连铸工艺,控制浇铸速度和结晶器设计。
3. 优化轧制工艺,控制轧制温度和速度,保证轧辊表面状况良好。
4. 加强钢板表面的清洁和处理,避免表面污染。
如果气泡缺陷已经出现,可以通过打磨、修补或切除等方法进行处理。
对于严重的气泡缺陷,可能需要报废该部分钢板。
以上内容仅提供了一些可能的原因和措施,具体情况可能因生产工艺和设备的不同而有所差异。
钢在轧制中常见的缺陷总结
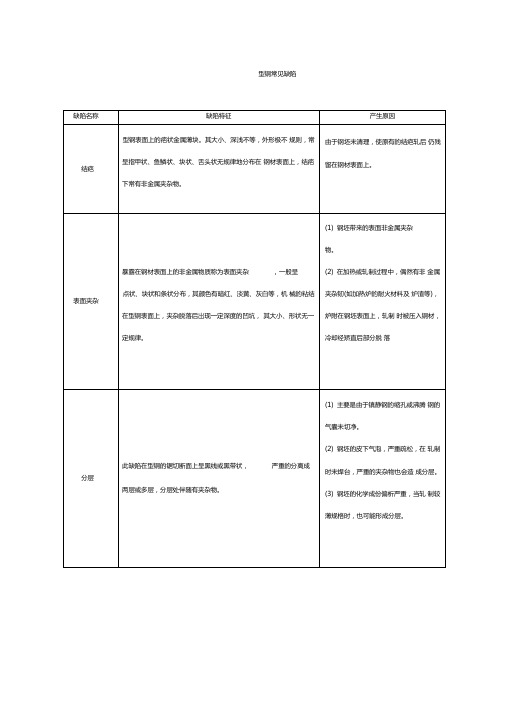
型钢常见缺陷型钢表面呈现的一种无规律分布的园形凸起称为凸包, 凸起部分的外缘比较园滑,凸包破裂后成鸡爪形裂口或舌形结钢坯有皮下气泡,轧制时未焊合。
疤,叫气泡。
多产生于型钢的角部及腿尖。
(1) 钢坯有裂缝或皮下气泡、非金属 夹杂物,经轧制破裂暴露。
(2) 加热温度不均匀,温度过低,轧 件在轧制时各部延伸与宽展不一顺轧制方向岀现在型钢表面上的线形开裂,一般呈直线形, 致。
有时呈“Y'形,多为通长出现,有时局部出现。
(3) 加热速度过快、炉尾温度过高或 轧制后冷却不当,易形成裂纹,此种 情况多发生在高碳钢和低合金钢 上。
尺寸超差是指型钢截面几何尺寸不符标准规定要求的统称。
尺寸超差(尺这类缺陷名目繁多,大部以产生部位以及其超差程度加以命 寸不合、规格名。
例工、槽、角钢的腿长、腿短、腰厚、腰薄及一腿长, 不合) 一腿短。
气泡(凸包)裂纹(1) 对工字钢成品孔腿长往往表现在 开口腿上,主要由于腰部压下量不 够,角钢和槽钢成品孔压下量的大 小,直接影响腿长和腿短。
(2) 切深孔切人太深,造成腿长无法 消除。
(3) 轧辊不水平或有轴向串动,以及 800咬入不正,成品孔夹板上偏等都 会造成一腿长,一腿短等。
(4) 腰的厚、薄主要是成品孔及成品 前孔压下量不合理所造成。
一般呈直线或弧形的沟槽,其深度不等,通长可见沟底,长划伤(刮伤、度自几毫米到几米,连续或断续地分布于钢材的局部或全擦伤、划痕) 长,多为单条,有时岀现多条。
型钢其一侧面沿轧制方向全长或周期性的缺少金属称缺肉, 缺肉缺陷处没有成品孔轧槽的热轧印迹,色暗、表面较粗糙。
耳子(1)导卫板安装不当,对轧件压力过大,将轧件表面划伤。
(2)导卫板加工不良,口边不圆滑,或磨损严重,粘有氧化铁皮,将轧件表面划伤。
(3)孔型侧壁磨损严重,当轧件接触时产生弧形划伤。
(4)钢材在运输过程中与表面粗糙的辊道、盖板、移钢机、活动挡板等接触划伤。
(1)孔型设计不良,轧辊车削不正确及轧机调整不当,使轧件进入成品孔时由于金属量不足,造成孔型充填不满。
钢板表面缺陷检测技术的研究与应用

钢板表面缺陷检测技术的研究与应用一、引言随着工业化进程的不断推进,钢材作为基本的建筑材料,在建筑、桥梁、交通运输等领域得到了广泛的应用。
钢材品质的好坏直接影响到工程质量和安全性,因此钢板表面缺陷的检测变得尤为重要。
本文将从钢板表面缺陷检测技术的研究与应用的角度出发,分析目前常见的钢板表面缺陷检测技术及其应用。
二、钢板表面缺陷检测技术1.目视检测法目视检测法是一种最简单、最常用的缺陷检测方法,通过肉眼观察钢板表面缺陷的方式来进行识别。
这种检测方法的优点是成本低,操作简单,但是存在识别不准确、实时性差等缺陷。
2.磁粉检测法磁粉检测法是通过涂覆磁粉或将磁粉喷涂到钢板表面,并产生磁场,利用磁粉在缺陷附近产生聚集并形成缺陷轮廓线来检测缺陷。
这种方法能够检测到较小的缺陷,但是需要对钢板进行磁化处理,同时也会对环境造成一定的污染。
3.超声波检测法超声波检测法是一种通过超声波对钢板进行检测的方法。
利用超声波在材料中的传播规律,来检测钢板表面的缺陷。
这种方法具有检测速度快、操作简单、准确性高等优点,但是对于不同类型的缺陷,需要针对性的选择超声波探头。
4.电磁感应检测法电磁感应检测法是一种利用钢材表面的电磁感应来检测缺陷的技术。
该技术不需要对钢板进行磁化处理,并且对环境无污染,但是需要针对不同的缺陷类型选择不同类型的探头。
5.激光检测法激光检测法利用激光束对钢板进行激发,通过反射光信号来检测表面缺陷。
这种方法具有高速、高精度、无需接触样品以及无需待机的优点,但是价格昂贵,操作复杂。
三、钢板表面缺陷检测技术的应用1.建筑领域在建筑领域,需要对钢板进行缺陷检测,主要是因为缺陷可能导致安全问题。
钢板在建筑领域的主要应用包括建筑物外立面、建筑辅助结构以及建筑桥梁。
基于不同的要求,通常选择不同的检测技术。
2.交通运输领域在交通运输领域,需要对钢板进行局部的缺陷检测,主要是因为缺陷可能对车辆或船只产生破坏。
主要包括汽车的轮胎和汽车底盘板的检测、火车铁轨以及船舶的钢板表面检测。
钢铁产品常见缺陷

型钢常见缺陷缺陷名称缺陷特征产生原因结疤型钢表面上的疤状金属薄块。
其大小、深浅不等,外形极不规则,常呈指甲状、鱼鳞状、块状、舌头状无规律地分布在钢材表面上,结疤下常有非金属夹杂物。
由于钢坯未清理,使原有的结疤轧后仍残留在钢材表面上。
表面夹杂暴露在钢材表面上的非金属物质称为表面夹杂,一? 般呈点状、块状和条状分布,其颜色有暗红、淡黄、灰白等,机械的粘结在型钢表面上,夹杂脱落后出现一定深度的凹坑,其大小、形状无一定规律。
???(1)钢坯带来的表面非金属夹杂物。
(2)在加热或轧制过程中,偶然有非金属夹杂韧(如加热炉的耐火材料及炉渣等),炉附在钢坯表面上,轧制时被压入钢材,冷却经矫直后部分脱落分层此缺陷在型钢的锯切断面上呈黑线或黑带状,严重的分离成两层或多层,分层处伴随有夹杂物。
?(1)主要是由于镇静钢的缩孔或沸腾钢的气囊未切净。
(2)钢坯的皮下气泡,严重疏松,在轧制时未焊台,严重的夹杂物也会造成分层。
(3)钢坯的化学成份偏析严重,当轧制较薄规格时,也可能形成分层。
气泡(凸包)型钢表面呈现的一种无规律分布的园形凸起称为凸包,凸起部分的外缘比较园滑,凸包破裂后成鸡爪形裂口或舌形结疤,叫气泡。
多产生于型钢的角部及腿尖。
钢坯有皮下气泡,轧制时未焊合。
裂纹顺轧制方向出现在型钢表面上的线形开裂,一般呈直线形,有时呈“Y”形,多为通长出现,有时局部出现。
(1)钢坯有裂缝或皮下气泡、非金属夹杂物,经轧制破裂暴露。
(2)加热温度不均匀,温度过低,轧件在轧制时各部延伸与宽展不一致。
(3)加热速度过快、炉尾温度过高或轧制后冷却不当,易形成裂纹,此种情况多发生在高碳钢和低合金钢上。
尺寸超差(尺寸不合、规格不合)尺寸超差是指型钢截面几何尺寸不符标准规定要求的统称。
这类缺陷名目繁多,大部以产生部位以及其超差程度加以命名。
例工、槽、角钢的腿长、腿短、腰厚、腰薄及一腿长,一腿短。
(1)对工字钢成品孔腿长往往表现在开口腿上,主要由于腰部压下量不够,角钢和槽钢成品孔压下量的大小,直接影响腿长和腿短。
en10163-3钢板表面缺陷标准
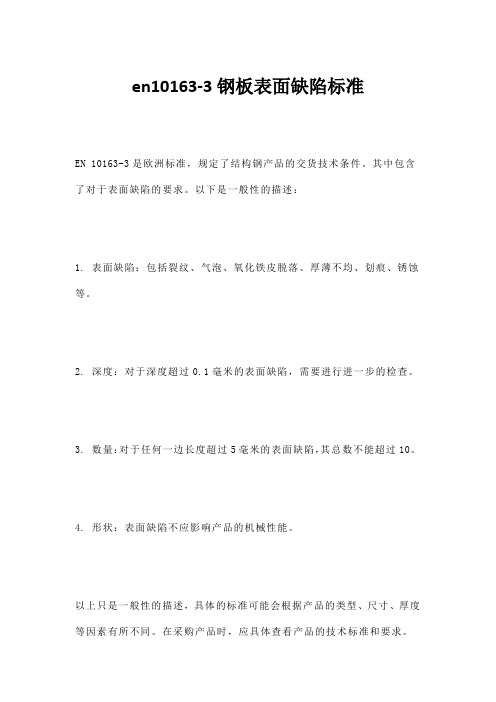
en10163-3钢板表面缺陷标准
EN 10163-3是欧洲标准,规定了结构钢产品的交货技术条件。
其中包含了对于表面缺陷的要求。
以下是一般性的描述:
1. 表面缺陷:包括裂纹、气泡、氧化铁皮脱落、厚薄不均、划痕、锈蚀等。
2. 深度:对于深度超过0.1毫米的表面缺陷,需要进行进一步的检查。
3. 数量:对于任何一边长度超过5毫米的表面缺陷,其总数不能超过10。
4. 形状:表面缺陷不应影响产品的机械性能。
以上只是一般性的描述,具体的标准可能会根据产品的类型、尺寸、厚度等因素有所不同。
在采购产品时,应具体查看产品的技术标准和要求。
不锈钢表面常见缺陷类型汇总
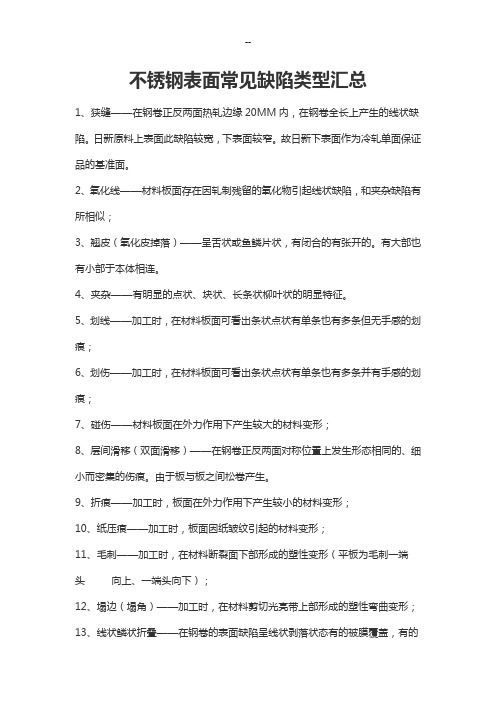
不锈钢表面常见缺陷类型汇总1、狭缝——在钢卷正反两面热轧边缘20MM内,在钢卷全长上产生的线状缺陷。
日新原料上表面此缺陷较宽,下表面较窄。
故日新下表面作为冷轧单面保证品的基准面。
2、氧化线——材料板面存在因轧制残留的氧化物引起线状缺陷,和夹杂缺陷有所相似;3、翘皮(氧化皮掉落)——呈舌状或鱼鳞片状,有闭合的有张开的。
有大部也有小部于本体相连。
4、夹杂——有明显的点状、块状、长条状柳叶状的明显特征。
5、划线——加工时,在材料板面可看出条状点状有单条也有多条但无手感的划痕;6、划伤——加工时,在材料板面可看出条状点状有单条也有多条并有手感的划痕;7、碰伤——材料板面在外力作用下产生较大的材料变形;8、层间滑移(双面滑移)——在钢卷正反两面对称位置上发生形态相同的、细小而密集的伤痕。
由于板与板之间松卷产生。
9、折痕——加工时,板面在外力作用下产生较小的材料变形;10、纸压痕——加工时,板面因纸皱纹引起的材料变形;11、毛刺——加工时,在材料断裂面下部形成的塑性变形(平板为毛刺一端头向上、一端头向下);12、塌边(塌角)——加工时,在材料剪切光亮带上部形成的塑性弯曲变形;13、线状鳞状折叠——在钢卷的表面缺陷呈线状剥落状态有的被膜覆盖,有的未被覆盖。
14、边部鳞状折叠——在钢卷边部轧制边缘50MM以内发生的线状或山状的鳞状剥落,与轧制方向平行,连续或断续发生。
15、山形鳞状折叠——钢卷表面为山形剥落缺陷,发生的位置无特征,山形方向与轧制方向平行。
16、热轧头部滑移——在热轧卷头部大约5米两面有滑移伤痕。
17、氧化皮缺陷——在热轧的下表面头尾发生较多,呈长椭圆形的较多里面的材料呈凹下状。
18、停辊印——在钢带表面发生与轧制方向垂直的一条凹痕。
19、平整辊印——在钢板轧制方向上,以SPM工作辊周长为间距产生的凹凸形伤痕。
20、辊印——在钢板长度方向上,以CRM工作辊周长为间距而出现的凹凸形伤痕;中间辊印、支撑辊印:在长度方向无周期、是直线发生的凹凸伤痕21、边波——钢卷单边或者两边出现的波浪形形变22、凹坑——在热轧时常发生的不定形的杂物咬入而引起的,发生的位置不固定23、高温计冷却水斑点——带钢表面上有白色斑点,中间空的部位颜色和带钢一样。
所有钢材常见缺陷及原因
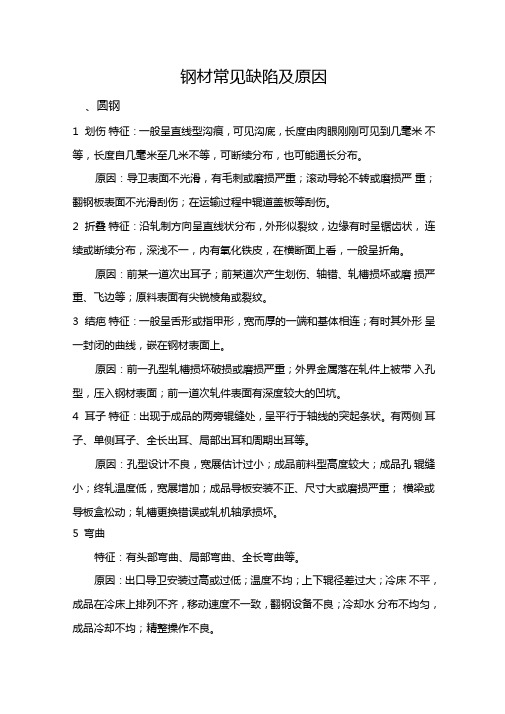
钢材常见缺陷及原因、圆钢1划伤特征:一般呈直线型沟痕,可见沟底,长度由肉眼刚刚可见到几毫米不等,长度自几毫米至几米不等,可断续分布,也可能通长分布。
原因:导卫表面不光滑,有毛刺或磨损严重;滚动导轮不转或磨损严重;翻钢板表面不光滑刮伤;在运输过程中辊道盖板等刮伤。
2折叠特征:沿轧制方向呈直线状分布,外形似裂纹,边缘有时呈锯齿状,连续或断续分布,深浅不一,内有氧化铁皮,在横断面上看,一般呈折角。
原因:前某一道次出耳子;前某道次产生划伤、轴错、轧槽损坏或磨损严重、飞边等;原料表面有尖锐棱角或裂纹。
3结疤特征:一般呈舌形或指甲形,宽而厚的一端和基体相连;有时其外形呈一封闭的曲线,嵌在钢材表面上。
原因:前一孔型轧槽损坏破损或磨损严重;外界金属落在轧件上被带入孔型,压入钢材表面;前一道次轧件表面有深度较大的凹坑。
4耳子特征:出现于成品的两旁辊缝处,呈平行于轴线的突起条状。
有两侧耳子、单侧耳子、全长出耳、局部出耳和周期出耳等。
原因:孔型设计不良,宽展估计过小;成品前料型高度较大;成品孔辊缝小;终轧温度低,宽展增加;成品导板安装不正、尺寸大或磨损严重;横梁或导板盒松动;轧槽更换错误或轧机轴承损坏。
5弯曲特征:有头部弯曲、局部弯曲、全长弯曲等。
原因:出口导卫安装过高或过低;温度不均;上下辊径差过大;冷床不平,成品在冷床上排列不齐,移动速度不一致,翻钢设备不良;冷却水分布不均匀,成品冷却不均;精整操作不良。
6翘皮特征:呈鱼鳞状或分层翘起的薄皮,大部分是生根的,也有不生根的。
原因:导卫装置加工或安装不良,围盘有尖锐棱角,刮伤了轧件表面,再轧后,引起翘皮;输送辊道表面粗糙,刮起伤了轧件表面,再轧后造成翘皮;轧件带有薄耳子;轧槽磨损严重,轧件在孔型内打滑;连铸坯内部有较大的皮下气泡,轧后破裂形成翘皮。
7表面夹杂特征:一般呈点状、条状或块状分布,其颜色有暗红、暗黄、灰白等,机械地粘结在成品表面上,不易剥落,且有一定的深度。
钢板常见质量缺陷

钢材销售业务中经常会碰到客户的质量投诉,业务员需要对其进行仔细的了解、分析、判断,并给予正确的反馈,本人根据工作中的经验,对常用的板材会出现的一些质量问题进行了归纳,供有关人员作参考,如有错误的地方请予指正:冷轧钢板1表面夹杂:表面呈现点状、块状或线条状的非金属夹杂物,沿轧制方向间断或连续分布,其颜色为好棕色、深灰色或白色。
严重时,钢板出现孔洞、破裂、断带。
原因:1)炼钢时造渣不良,钢水粘度大,流动性差,渣子不能上浮,钢中非金属夹杂物多;2)铸温低,沸腾不良,夹杂物未上浮;3)连铸时,保护渣带入钢中;4)钢水罐、钢锭模或注管内的非金属材料未清扫干净。
2介在物:缺陷呈点状,一般色泽与钢带不同,多呈白色、灰白色。
长度不是很长,多存在于钢带的头、屋部,程度严重时即形成剥片、孔洞。
分为闭口状和开口状。
原因是由于炼钢时钢水中有夹杂物,或热轧时钢带表面存在刮痕、凿痕等缺陷,经过冷轧时,在钢带表面即形成点状之痕迹。
3轧入污物:缺陷呈块状,一般呈白色,易集中发生在钢带某段长度。
原因是由于外来物(如衬纸、胶粒)被轧入钢带表面,而形成大面积、块状之缺陷。
4气孔和夹层:切断面上呈上下两层裂纹,但无分离。
原因是由于炼钢、热轧时钢带表面残留有气泡。
5结疤:表面出现不规则的“舌状”、“鱼鳞状”或条状翘起的金属起层,有的与钢板本体相连接,有的与钢板本体不相连,前面叫开口结疤,后者叫闭口结疤,闭口结疤在轧制时易脱落,使板面成为凹坑。
原因:1)炼钢方面:锭模内壁清理不净,横壁掉肉,上注时,钢液飞溅,粘于横壁,发生氧化,铸温低,有时中断注流,继续注钢时,形成翻皮;下注时,保护渣加入不当,造成钢液飞溅;2)轧钢方面:板坯表面残留结疤未清除干净,经轧制后留在钢板上。
6氧化铁皮:缺陷呈点状、条状或鱼鳞状的黑色斑点,分布面积大小不等,压入的深浅不一。
这类铁皮在酸洗工序难于洗尽,当铁皮脱落时形成凹坑。
原因:1)板坯加热温度过高,时间过长;炉内呈强氧化气氛,炉生氧化铁皮轧制时压入;2)高压水压力不足,连轧前氧化铁皮未清除干净;3)高压水喷咀堵塞,局部氧化铁皮未清除;4)集鳞管道打开组数不够,除鳞不干净。
- 1、下载文档前请自行甄别文档内容的完整性,平台不提供额外的编辑、内容补充、找答案等附加服务。
- 2、"仅部分预览"的文档,不可在线预览部分如存在完整性等问题,可反馈申请退款(可完整预览的文档不适用该条件!)。
- 3、如文档侵犯您的权益,请联系客服反馈,我们会尽快为您处理(人工客服工作时间:9:00-18:30)。
钢板表面缺陷
不同的钢板其表面缺陷有不同的表状:
序号|缺陷名称|产生缺陷的可能工序|可能的产生原因
冷轧钢板与钢带表面缺陷
一、表面缺陷
(一)、钢板与钢带不允许存在的缺陷
1气泡| 炼钢| 炼钢时产生气泡,在热轧时又未焊合,酸洗冷轧后暴露在外
2裂纹| 炼钢、热轧与冷轧及各加工工序| 由于炼钢热应力、轧制形变或加工致应力集中造成
3结疤或结瘤| 酸洗与冷轧| 酸洗未洗尽氧化皮,轧制时镶嵌于表面形成结疤4拉裂| 冷轧、镀锌与平整| 张力过大、张力波动过大以及张力不稳定等原因造成
5 夹杂| 炼钢| 炼钢原因
6 折叠| 热轧、冷轧| 轧制时呈粘性流动的金属被再次轧制后镶嵌于板材表面
7 分层| 炼钢、热轧与冷轧| 炼钢时成分偏析以及组织偏析、大块夹杂等原因造成并最终在轧制过程中表现为分层
8 黑膜或黑带| 酸洗| 酸洗后烘干效果不好造成
9 乳化液斑点| 冷轧与平整| 乳化液残留于钢带表面所致
10 波纹和折印| 酸洗| 过酸洗等(待查)
11 倒刺或毛刺| 剪切过程| 剪刃不锋利、上下剪刃错开角度大、剪刃角度不准等原因造成
(二)、允许存在的且根据其程度不同来划分不同表面质量等级的缺陷
1 麻点| 冷轧、光整与平整| 轧制时塑性基体金属粘附于高速转动的轧辊表面所致
2 划痕| 各工序及搬运吊装过程等
3 擦伤| 搬运、吊装过程
4 兰色氧化色| 冷轧与平整| 由于轧制摩擦力使基体金属升温从而造成基体发蓝,尤其是带钢边部更易于形成此缺陷
5 浅黄色酸洗色| 酸洗| 酸洗后未烘干造成
6 轧辊压痕| 冷轧、光整与平整| 轧辊原因
7 划伤| 搬运、吊装过程
8 凹坑| 冷轧| 轧辊原因以及表层夹杂被轧出基体表面等原因形成凹坑(三)、其他表面质量缺陷
1 粘接| 罩式退火| 由于在全氢气氛下长时间加热造成钢卷表面残铁粉被还原为铁而造成,此外粘接还与卷取张力以及冷却速度等有关
2 表面碳黑| 罩式退火| 在全氢高温气氛下,钢铁表面残余轧制油发生分解形成碳黑沉积于钢卷表面
3 生锈与腐蚀| 钢卷存放以及运输过程| 防锈油质量不好或未涂防锈油或涂油量不足等,或者是存放环境湿度高等原因造成
4 欠酸洗| 酸洗| 表现为还有氧化铁皮未洗掉
5 过酸洗| 酸洗| 表现为基体表面可见清晰轧制纹路
二、板形缺陷
1 切斜| 酸轧、精整等| 指钢卷或钢带切边时切斜
2 镰刀弯| 冷轧、光整与平整| 带钢两边轧制力不平衡,轧制力响应时间滞后或辊缝不均匀(辊缝调节不好)或原料密度与硬度不均匀等造成
3 浪形(细分为单边浪、双边浪、中浪、斜浪等)| 冷轧、光整与平整| 原料密度与硬度不均匀、轧制时轧制力以及弯辊力调节响应不快或不准、带钢张力波动过大等所致,另外上下轧辊辊径相差大也会造成浪形
4 瓢曲| 热轧、冷轧、光整与平整| 原料厚度方向上密度或硬度不均匀,造成钢板上下两面塑性不均匀造成,三、卷型缺陷
1 塔型| 卷曲过程| 卷取机卷曲精度不高造成
2 鼓包| 卷曲过程| 钢带边部超薄并在连续卷曲过程中形成钢卷鼓起
3 鼓耳| 卷曲过程| 对于镀锌卷,如存在边部超厚,则可能卷取时钢卷两端鼓起
四、尺寸缺陷
1 厚度超差| 轧制过程| 轧制控制不准等
2 宽度短尺| 切边过程| 切边不准或原料边部缺陷原因
3 长度超差| 钢板分切过程| 控制精度原因等
热镀锌钢板与钢带表面缺陷
1 锌粒| 热镀锌过程| 底渣被机械搅起或因为锌液温度高而浮起,从而附着在镀锌板面上,并在冷却过程中形成锌铁化合物FeZn10
2 厚边| 热镀锌过程| 气刀的角度调整不佳,造成对吹从而形成绕流;另外由于边部气流向外散失一部分使喷吹压力不够,也会造成厚边缺陷
3 灰色镀锌层| 热镀锌过程| 在冷却相变过程中,如果锌铁合金层迅速长大从而使表面纯锌层消失,即没有锌的结晶花纹从而显现为灰色。
一般认为,如果钢中Si含量大于0.1%则将会促使锌铁合金层迅速长大。
4 气刀条痕| 热镀锌过程| 由于气刀缝隙发生局部堵塞(如由锌液飞溅造成堵塞)从而在带钢相应位置产生凸起带痕;发生气刀条痕处的镀层将严重超厚
5 锌突起| 热镀锌过程| 由于锌液温度低或锌液中铝含量高使得冷却相变过程发生特殊的锌结晶,呈现为明亮的树枝状条纹并凸出锌层(锌突起)
6 贝壳状表面| 热镀锌过程| 在镀锌板表面呈现贝壳状或鳞状的光亮锌结晶,显示一定的锌起伏并常伴随锌突起;造成原因有锌液温度低和锌液中铝含量高
7 条状花纹| 热镀锌过程| 在带钢边沿以大约45°向外散射,形成归整的树枝状结晶条纹。
常发生在带钢厚度小于1毫米而锌层重量大于275g/m2的镀锌板卷。
原因目前不清楚
8 锌浪| 热镀锌过程| 锌液中铝含量低和锌液温度高使锌液粘性小流动性大却又生产较厚的镀层时产生类似水波一样的浪纹,这种锌起伏形成了不均匀的镀锌层厚度
9 气刀刮痕| 热镀锌过程| 板形不好或气刀喷嘴距离带钢太近从而刮伤带钢
10 抖动条痕| 热镀锌过程 |沉没辊、光整辊或其他辊子如果存在表面缺陷,则周期性地刻映在镀锌板表面
11 沉没辊锌疤| 热镀锌过程| 锌渣被沉没辊压到带钢上表面且过气刀时又很难被吹掉从而在带钢上表面形成结疤
12 卷取皱纹| 镀锌带钢卷取过程| 卷取时在板面上产生贯穿整个带钢宽度的横向皱纹。
主要原因是拉伸系数和平整度不足造成
13 光整花| 光整过程| 光整压下过大或张力过小
14 钝化斑点| 钝化过程| 未吹干或未挤干钝化液
15 白锈| 存放运输过程| 钢带表面积存水份没有及时散失或钝化效果不好造成
16 粗糙度不合要求| 热镀锌过程| 光整辊磨损严重
17 浪边| 热镀锌| 拉矫系数不足、卷取时产生厚边、原板存在严重浪形等都可能造成浪形。