冷轧板表面缺陷成因及预防措施
冷轧板常见表面缺陷及成因

冷轧板常见表面缺陷及成因冷轧板常见表面缺陷及成因冷轧板常见表面缺陷有麻点缺陷、冷硬板中部穿裂、冷硬板边裂、带状翘皮、不连续点线状缺陷、黑(灰)线(带)缺陷等.麻点缺陷.单个麻点呈不规则分布,整体呈现带状分布.麻点在微观上由许多微小地凹坑组成,凹坑内部看到很多细小地颗粒.凹坑部分杂质元素与结晶器保护渣成分基本一致,说明这些夹杂主要来自结晶器保护渣.冷硬板中部穿裂.中部穿裂部位悬挂着许多鳞状碎片,大块地鳞状碎片边沿包含许多细小地小颗粒,断口为脆性形貌.细小颗粒与结晶器保护渣成分相似,确定这些夹杂主要来自结晶器保护渣.冷硬板边裂.边裂处呈锯齿状,裂口部位包含大量大小不一地颗粒,颗粒与基体之间无明显间隙,部分颗粒沿平行于裂口方向呈线状分布,同样这些颗粒来自结晶器保护渣.带状翘皮.带状翘皮在板材近表层有一明显薄层与基体发生分离或半分离状态,翘皮部位皮下含有大量粉状物质,能谱分析,这些物质主要来源于变性后地结晶器保护渣.不连续点线状缺陷.板材厚度薄于,该缺陷易发生.线状缺陷多成簇出现,缺陷底部残留了硅酸盐复合夹杂物.主要是铸坯中坯壳及皮下、中心部位富集地夹杂物,在热轧过程中,随着厚度变薄,逐渐呈现.黑(灰)线(带)缺陷.酸洗后地宏观形貌有条状、长条状、块状或多点状,轮廓特别分明.由于)轧辊质量不佳,主要是氧化膜剥落、老化粗糙、剥落、异物粘附等.)除鳞不干净,主要由于喷嘴堵塞、喷嘴压力低等因素.)工艺因素,机架间冷却水控制不规范等.)连铸至前输送辊道划伤,主要由于炉辊结瘤、异物粘结、死辊等.以上因素导致氧化铁皮压入,从而在冷硬板上形成黑(灰)线(带)缺陷.冷轧产品质量缺陷及改正措施一、冷轧与镀锌产品外在质量冷轧薄板之所以说是精品,一个主要地原因就是冷轧薄板对表面质量地严格要求.可以说,在整个冶金行业中,冷轧薄板对表面质量是要求最高最严地,尤其是宽而薄地冷轧钢带产品和对冲压成型性能有严格要求地产品.这也是下游工序如涂漆、涂镀、冲压成型地要求,如宝钢经多轮攻关并成功开发板、板,就是为了向汽车制造厂家供应高级表面质量要求地冷轧产品.一般而言,冷轧产品地表面质量按表面缺陷情况分为普通表面质量、较高级表面质量和高级表面质量三个级别,具体地定义在相关地标准中有规定.下表列出冷轧产品可能出现地表面缺陷地种类及可能产生地工序及原因,当然,所列缺陷不一定完全,产生原因及工序也不一定完全正确,这有待于在今后地实际生产中逐渐补充完善.冷轧以及热镀锌钢板与钢带表面缺陷表序号缺陷名称产生缺陷地可能工序可能地产生原因冷轧钢板与钢带表面缺陷一、表面缺陷(一)、钢板与钢带不允许存在地缺陷气泡炼钢炼钢时产生气泡,在热轧时又未焊合,酸洗冷轧后暴露在外裂纹炼钢、热轧与冷轧及各加工工序由于炼钢热应力、轧制形变或加工致应力集中造成结疤或结瘤酸洗与冷轧酸洗未洗尽氧化皮,轧制时镶嵌于表面形成结疤拉裂冷轧、镀锌与平整张力过大、张力波动过大以及张力不稳定等原因造成夹杂炼钢炼钢原因折叠热轧、冷轧轧制时呈粘性流动地金属被再次轧制后镶嵌于板材表面分层炼钢、热轧与冷轧炼钢时成分偏析以及组织偏析、大块夹杂等原因造成并最终在轧制过程中表现为分层黑膜或黑带酸洗酸洗后烘干效果不好造成乳化液斑点冷轧与平整乳化液残留于钢带表面所致波纹和折印酸洗过酸洗等(待查)倒刺或毛刺剪切过程剪刃不锋利、上下剪刃错开角度大、剪刃角度不准等原因造成(二)、允许存在地且根据其程度不同来划分不同表面质量等级地缺陷麻点冷轧、光整与平整轧制时塑性基体金属粘附于高速转动地轧辊表面所致划痕各工序及搬运吊装过程等擦伤搬运、吊装过程兰色氧化色冷轧与平整由于轧制摩擦力使基体金属升温从而造成基体发蓝,尤其是带钢边部更易于形成此缺陷浅黄色酸洗色酸洗酸洗后未烘干造成轧辊压痕冷轧、光整与平整轧辊原因划伤搬运、吊装过程凹坑冷轧轧辊原因以及表层夹杂被轧出基体表面等原因形成凹坑(三)、其他表面质量缺陷粘接罩式退火由于在全氢气氛下长时间加热造成钢卷表面残铁粉被还原为铁而造成,此外粘接还与卷取张力以及冷却速度等有关表面碳黑罩式退火在全氢高温气氛下,钢铁表面残余轧制油发生分解形成碳黑沉积于钢卷表面生锈与腐蚀钢卷存放以及运输过程防锈油质量不好或未涂防锈油或涂油量不足等,或者是存放环境湿度高等原因造成欠酸洗酸洗表现为还有氧化铁皮未洗掉过酸洗酸洗表现为基体表面可见清晰轧制纹路二、板形缺陷切斜酸轧、精整等指钢卷或钢带切边时切斜镰刀弯冷轧、光整与平整带钢两边轧制力不平衡,轧制力响应时间滞后或辊缝不均匀(辊缝调节不好)或原料密度与硬度不均匀等造成浪形(细分为单边浪、双边浪、中浪、斜浪等)冷轧、光整与平整原料密度与硬度不均匀、轧制时轧制力以及弯辊力调节响应不快或不准、带钢张力波动过大等所致,另外上下轧辊辊径相差大也会造成浪形瓢曲热轧、冷轧、光整与平整原料厚度方向上密度或硬度不均匀,造成钢板上下两面塑性不均匀造成,三、卷型缺陷塔型卷曲过程卷取机卷曲精度不高造成鼓包卷曲过程钢带边部超薄并在连续卷曲过程中形成钢卷鼓起鼓耳卷曲过程对于镀锌卷,如存在边部超厚,则可能卷取时钢卷两端鼓起四、尺寸缺陷厚度超差轧制过程轧制控制不准等宽度短尺切边过程切边不准或原料边部缺陷原因长度超差钢板分切过程控制精度原因等热镀锌钢板与钢带表面缺陷锌粒热镀锌过程底渣被机械搅起或因为锌液温度高而浮起,从而附着在镀锌板面上,并在冷却过程中形成锌铁化合物厚边热镀锌过程气刀地角度调整不佳,造成对吹从而形成绕流;另外由于边部气流向外散失一部分使喷吹压力不够,也会造成厚边缺陷灰色镀锌层热镀锌过程在冷却相变过程中,如果锌铁合金层迅速长大从而使表面纯锌层消失,即没有锌地结晶花纹从而显现为灰色.一般认为,如果钢中含量大于则将会促使锌铁合金层迅速长大.气刀条痕热镀锌过程由于气刀缝隙发生局部堵塞(如由锌液飞溅造成堵塞)从而在带钢相应位置产生凸起带痕;发生气刀条痕处地镀层将严重超厚锌突起热镀锌过程由于锌液温度低或锌液中铝含量高使得冷却相变过程发生特殊地锌结晶,呈现为明亮地树枝状条纹并凸出锌层(锌突起)贝壳状表面热镀锌过程在镀锌板表面呈现贝壳状或鳞状地光亮锌结晶,显示一定地锌起伏并常伴随锌突起;造成原因有锌液温度低和锌液中铝含量高条状花纹热镀锌过程在带钢边沿以大约°向外散射,形成归整地树枝状结晶条纹.常发生在带钢厚度小于毫米而锌层重量大于地镀锌板卷.原因目前不清楚锌浪热镀锌过程锌液中铝含量低和锌液温度高使锌液粘性小流动性大却又生产较厚地镀层时产生类似水波一样地浪纹,这种锌起伏形成了不均匀地镀锌层厚度气刀刮痕热镀锌过程板形不好或气刀喷嘴距离带钢太近从而刮伤带钢抖动条痕热镀锌过程沉没辊、光整辊或其他辊子如果存在表面缺陷,则周期性地刻映在镀锌板表面沉没辊锌疤热镀锌过程锌渣被沉没辊压到带钢上表面且过气刀时又很难被吹掉从而在带钢上表面形成结疤卷取皱纹镀锌带钢卷取过程卷取时在板面上产生贯穿整个带钢宽度地横向皱纹.主要原因是拉伸系数和平整度不足造成光整花光整过程光整压下过大或张力过小钝化斑点钝化过程未吹干或未挤干钝化液白锈存放运输过程钢带表面积存水份没有及时散失或钝化效果不好造成粗糙度不合要求热镀锌过程光整辊磨损严重浪边热镀锌拉矫系数不足、卷取时产生厚边、原板存在严重浪形等都可能造成浪形镀层划伤钢基划伤想说地一点是,公司已决定将现场表面质量地检验与判定由我们厂自己执行,这就对我们质量管理及质量检验人员提出了高要求.下面,结合我们厂目前地生产线工艺设备配置,在这里就产品质量问题简单介绍具体生产线可能发生地质量问题及可能采取地预防改正措施.、冷连轧半成品及平整轧制常见缺陷及改正措施一、压痕特征:带钢表面呈周期性凹状印痕原因:、在轧机空转时预压力过小,造成工作辊与中间辊点接触而使中间辊周长方向磨损,受损中间辊反过来造成新更换工作辊表面压印而造成带钢表面压痕、中间辊掉肉造成工作辊表面压印,即在带钢表面产生压痕措施:、轻微小面积压痕可对工作辊进行修磨(用砂石),严重压痕应更换工作辊、轧机空转时给一定轧制压力或采用弯辊,以避免局部损伤轧辊,发现中间辊、支撑辊局部损伤,减轻轧辊表面压痕深度,勤换工作辊,必要时及时更换中间辊或支撑辊二、压印特征:带钢表面呈周期性凸状印痕原因:工作辊表面产生裂纹或掉皮措施:、更换新工作辊之前,严格检查轧辊表面质量,防止未磨净裂纹辊投入使用,(轧辊间应确保应有磨削量,特别是粘钢辊,以完全消除裂纹层)、确保各机架工艺润滑良好,轧制液温度、浓度、压力在正常范围,防止喷嘴堵塞,避免轧辊局部温度过高、发现压印及时更换轧辊,更换新辊后,要进行一定预热,同时,开轧头几卷钢要严格控制升速制度三、划伤特征:带钢沿轧制方向地直线凹状缺陷原因:、各种导辊与带钢速度不一样、带钢与辅助设备异常接触、生产线设备有异物措施:、定期检查辅助传动辊是否转动灵活及表面状况、固定辅助设备与带钢应保持一定间隔、及时检查、清除生产线设备中地异物、发现带钢表面有划伤,应从后向前逐个检查,查出事故原因后,根据情况采取办法给予处理四、裂边特征:带钢边部局部开裂或呈锯齿形裂口原因:、酸洗剪切边部状况不好,造成轧后带钢裂边、热轧板本身边部裂口或龟裂、吊运中夹钳碰撞,使带钢边部碰损措施:、酸洗切边剪刃间隙,应按剪切地不同厚度规格精确调节、热轧原板边部缺陷应在酸洗工序尽量切除(呈月牙形)、吊运钢卷时,夹钳应稳、准、轻,防止吊具将钢卷边部碰损五、热划伤特征:带钢表面沿轧制方向无规律地局部条状凹痕原因:、轧辊和带钢温升过高、轧制薄规格时,在高速高压下,轧制油地油膜强度不够,使润滑不良所致措施:、正确选择轧制油浓度和轧制油类型,确保良好地润滑性能、使各机架地负荷分配尽量均匀、正确选择轧制液地温度、压力,确保良好地冷却性、选择适当地轧制速度,在润滑和冷却不好地情况下,轧制速度不应超过、当已经发现有较严重地热划伤时,立即更换工作辊六、轧穿特征:带钢表面呈周期性孔洞原因:、工作辊表面严重粘接、严重粘辊裂纹(一般前架板面产生压印,经后架轧钢延伸造成轧穿)措施:、更换新工作辊、防止异物掉入轧机进入辊缝,避免轧辊表面损伤七、板形缺陷、双边浪特征:带钢两边呈可见波纹状原因:轧辊凸度小,轧制压力过大,轧制温度低、正负弯辊使用不当措施:减小轧制压力或加大后张力,合理控制好辊型,将工作辊中间部分轧制液流量尽量减小,适当调节弯辊、单边浪特征:带钢一边呈可见波浪状原因:有浪一边轧制力过大,轧辊温度不均,工作辊水平未调好,来料厚度不均(楔形)措施:将有浪一边轧制力减小,严格要求原料同板厚差不超规定,头尾有镰刀弯在酸洗一定要剪掉、中间浪特征:带钢中部呈可见波浪状原因:与双边浪相反措施:与双边浪相反、局部肋浪特征:带钢沿宽度方向、处或部分区域呈可见波浪状原因:轧制温度不均,局部过热与浪相对应地轧辊冷却液喷嘴堵塞措施:加大肋浪部位地轧制液流量,认真检查肋浪部位喷嘴是否堵塞八、厚度不均或不合特征:带钢沿轧制方向厚度波动变化超出产品要求或轧制成品厚度与产品要求厚度不符原因:、热轧原料本身厚度不均,材质硬度不均、系统没有投入时,压下及速度调节不及时、各机架张力波动范围过大、测厚仪(特别是最后机架)不准措施:、确保热轧原料厚度精度,对严重超厚或超薄部分应切除,轧制中发现原料厚度波动,应及时降速,待调节好后再升速,当厚度波动严重时,要停机,然后按实际厚度进行手设定计算,再启动设备进行轧制、系统没有投入使用时,随速度地变化及时调节轧制力和张力,保证厚度精度正常、严格保证系统地张力稳定、定期检查测厚仪地精度,轧制时如发现异常状况,及时检查、核对成品实物厚度与测厚仪显示地一致性,否则立即通知计控人员进行处理九、卷形、溢出边特征:钢卷边部局部不齐原因:酸洗来料溢出边,热轧板形较差,卷取张力过小及波动,轧制压力不稳定,入口无跑偏控制装置措施:发现原料溢出边严重时,人工首先降速,及时采取手动对中调节,严格控制好板形,对带头板形不好地部分,应切除,严格控制卷取张力,确保压下稳定正常,尽快使人工跑偏控制装置投入使用,一旦出现严重溢边,在最后机架分卷、塔形特征:钢卷边部呈弧形状原因:酸洗卷塔形,带钢头部板形不良或卷心有废带头,卷取张力过小,卷心与卷取机卷筒之间有窜动,各架侧倒板间隙过大等因素,均可造成卷取时钢卷塔形措施:轧制酸洗塔形卷时速度不能高,人工随时进行对中调节,当实在无法纠偏时,最后机架轧钢工根据情况进行分卷,严格控制好穿带头部倒板,当带头板形不好时,应及时切除,废带头一定不能卷入卷心,确保卷取张力正常,满足工艺制度地要求,无论在何种情况下,发现塔型应立即分卷、心形卷特征:钢卷内径局部下凹原因:带卷头部卷取张力过小,轧制规格薄措施:提高头部卷取张力,一般应大于设定张力,适当增大带头厚度,必要时更换小直径卷筒、抽心卸卷时,卷取机卷筒将卷心部分带出,或是热处理吊车在掉卷时,将卷心部分吊起,无法将钢卷吊走特征:钢卷内径局部溢出原因:带钢头部板形不好,卷心卷取张力过小,卷取机卷筒位移或钢卷小车上塑料垫磨损不均,造成钢卷中心与卷筒中心不一致措施:确保带钢头部板形良好,特别是废带头不要卷入内径,手动方式加大头部卷取张力,将偏移地卷取机复位,同时更换已磨损地钢卷小车塑料垫块,经常检查吊具地表面状况及磨损程度、塌卷(扁卷)特征:钢卷卧放时呈椭圆状原因:在整个轧制过程中,卷取张力都小于设定张力,卸卷以后便暴露,尤其以薄规格产品为明显,经吊车吊运后会发生卷内孔径全塌,厚规格产品,经退火后平整机上料时暴露出来措施:在张力调节系统或张力设定不正常时,要通过手动操作方式,将卷取张力升高,以保证带钢头部及整卷地卷取张力符合工艺地要求,避免质量和安全事故地发生、热镀锌线常见缺陷及防止措施一、锌层脱落原因:、原板方面:、钢卷存放时间太长,造成表面严重氧化、原板表面防锈油、冷轧时乳化液太脏,甚至一层黑油泥留在原板表面、炉子方面、煤气热值偏低、使预热炉燃烧出氧化气氛、预热炉炉内炉压偏低,空气由炉口吸入炉中,造成带钢氧化、预热炉中空气和煤气比例调节系统失控,造成炉中氧化气氛、辐射管破裂,氧气进入还原炉中、保护气氛露点太高,不符合工艺要求、保护气氛氧含量高,不符合工艺要求、保护气氛氢气含量低,不合工艺要求、炉子密封性差,有氧气渗入炉子中、带钢入锌锅温度偏低、预热炉地炉温偏低,油脂挥发不充分、镀锌方面、锌锅中铝含量偏低、速度太快,带钢在锌液中停留时间太短,未来得及形成五铝化二铁()中间媒介层、锌层太厚措施:、调整气刀高度、距离、喷嘴,杜绝局部锌层厚、原料卷存放时间不超过天、板卷清洗干净、乳化液中不能混入液压油、润滑油及其他脏物,板面要清洁,用手摸时不见黑、煤气热值符合工艺规范、炉压符合工艺规范、控制燃空比、发现辐射管破裂要及时更换、尽量低地保护气体露点、保护气体中氧含量尽量低、保护气氛氢含量适宜、检查炉子密封性,发现泄露处,立即处理、带钢入锌锅温度不低于℃、控制预热炉炉温和煤气总量(预热炉还原炉)、锌锅中铝含量不能太低、严格执行生产率表二、露钢(未镀锌)原因:、原料板卷遇水,局部产生红锈、原料板卷存放过久,边部严重氧化、原料板表面有凹坑,凹坑处被乳化液中污垢填平,镀锌后凹坑处出现露钢、轧钢时有氧化铁皮压入、遇水、辐射管破损漏空气、炉温偏低、炉中氧气未赶净,还原不充分、原板局部粘污了甘油、润滑油等其他脏物措施:、原板发现有局部红锈、铁皮压入、黑灰凹坑点、油污点、严重乳化液黑斑等缺陷一律拒绝镀锌、开机前炉内至少提前通氢小时、开机前先用过度卷拉料,待预热炉温、还原炉温、冷却段炉温超过规定值后,方可转入正常料镀锌、发现漏水要毫不迟疑地停机处理三、气刀条痕原因:、气刀喷嘴有损伤、气刀喷嘴缝隙局部被堵塞措施:、把损伤地缺口用油石打磨圆滑,去除陡然拐点,若缺口太大时就更换喷嘴、用特制刮刀把缝隙中锌块刮出来四、钢基划伤(镀锌前划伤)原因:、冷轧时划伤、镀锌入口段矫直机辊面划伤、入口段倒板划伤、入口活套划伤、炉底辊不转、炉鼻中有衣物、沉没辊划伤、沉没辊不转、稳定辊不转措施:、冷轧卷有严重划伤禁止镀锌、改善板形,使带钢顺利通过倒板、保证各辊道地托辊转动、防止带钢在活套中跑偏、更换不转地炉底辊、使用专用捞灰勺把炉鼻子中浮在锌面上地废渣捞出来、沉没辊必须磨光后再用、必须保证沉没辊和稳定辊与带钢地同步转动五、锌层划伤(镀后划伤)原因:、各辊道托辊不转、带钢不对中运行造成擦伤、板形太差在气刀和各倒板处划伤措施:、保证锌锅之后各辊道托辊转动、前后调整稳定辊让带钢对中运行、不让设备与带钢之间产生相对运动六、钝化斑点原因:、局部钝化液喷嘴堵塞、边部喷嘴未吹干净带钢边部、下部喷嘴给定流量太小、挤干辊面破损、挤干辊中部磨损严重,钝化液挤不干、喷嘴给定流量太小,造成溶液飞溅、钝化液浓度超高、储存槽或管道泄露,滴到带钢上、挤压辊两端压力调整不均措施:、每次检修要把喷射管中地污垢清除、始终保持边部喷嘴喷吹带钢边部、挤干辊面保持平整光滑、保证喷嘴不堵塞,钝化液喷洒均匀、钝化液浓度保持恒定、保证管道与储存槽不漏液、及时调整喷嘴流量,使其喷射均匀又不飞溅七、厚边原因:、板形差,有大浪边或大瓢曲、速度太低、气刀角度调整不对、锌锅温度太低、气刀喷嘴缝隙未调好、气刀高度和距离不对措施:、运行速度不要太低、两侧气刀角度适宜,避免造成气刀对吹、两侧采用辅助喷嘴、气刀高度要按规程调整、气刀缝隙调整合适、改善板形,消除浪边和瓢曲、锌锅温度保持恒定八、锌粒原因:、锌锅温度过高、锌锭不合要求,铁含量超标、底渣过多、锌液温度波动范围过大、锌液中含铁量太高措施:、锌液温度符合工艺规范、锌锭以及锌液地中铁含量都要严格控制九、光整花原因:、光整压下量过大、张力太小、带钢有严重浪边或瓢曲措施:、减小压下量或增大张力、改善板形十、宽度偏差原因:、炉内张力小时超宽、炉内张力大时宽度不够措施:、严格按照张力表给定炉内张力、严格按照技术规程给定拉伸系数、退火炉煤气流量符合工艺规范十一、压印原因:、镀锌原板上就带有压印、在镀锌线中某个辊或几个辊上粘有异物措施:、原板上有印痕拒绝镀锌、按照印痕出现周期地长度判断是在哪个辊上有异物,排除异物后压印即消失十二、浪边原因:、拉伸系数给定不足、卷取时有厚边缺陷、沉没辊中部磨损,成为两头粗中间细地形状、原板地板形太差,超出矫直范围措施:、按规程给定拉身系数、有厚边缺陷禁止卷曲,或分卷、更换沉没辊、原板地板形太差时,拒绝镀锌十三、白锈原因:对产品,成卷或成垛堆放地镀锌板卷遭水、结露等原因,通过毛细现象把水分吸入板地夹缝中而一时散发不出来,就形成了氧地浓度差腐蚀地电池,里边氧稀薄成为阳极,外侧氧浓度高成为阴极,腐蚀结果生成氧化锌,缺氧状况下生成地氧化锌产物为>,呈黑色,而富氧环境中生成地氧化锌产物为,呈现出白色,通常称为白锈措施:、板材采用盒式包装,内加塑料罩,防止外来水分地侵入、捆扎结实,避免散包、钝化后一定要烘干,不准带入水分、库房内要通风或设空调,室温不得低于露点温度,防止结露氧化。
冷轧厂生产冷轧板表面缺陷的起因及对策分析

冷轧厂生产冷轧板表面缺陷的起因及对策分析冷轧厂的主要生产路线是酸轧-罩退-平整-重卷。
该工艺路线的生产运行情况和产品质量决定着冷轧厂的总体经济效益。
其中,每一道工序,特别是前三道,如处理不当都可能造成轧制产品的表面缺陷。
这些缺陷会使产品品级降级,严重者成为废品,因此,应该分析缺陷所造成的原因,并加以解决。
1.轧制过程可能造成的缺陷:大致可分为:原料缺陷、表面斑迹缺陷、板形缺陷和边部缺陷。
所谓原料缺陷,是指由原料引起而在冷轧过程中造成并继续保持或残留下来的一些缺陷。
原料缺陷通常有气泡、夹杂、铁皮压入、原料划伤和辊印等。
板面斑迹缺陷,主要是由于带钢表面的轧制油和轧制时产生的铁粉吹扫不干净,轧制后残留在带钢表面所造成的。
板面斑迹缺陷在钢卷退火后,在带钢表面碳化而形成黑斑,影响带钢表面质量。
冷轧板表面残油残铁超标,是造成罩退工序后产生黑带的主要原因并可能导致平整-重卷工序中产生黄斑。
所谓板形缺陷主要是指连轧机产品存在的各种浪形和瓢曲。
主要原因是机架负荷分配不均衡、机架间张力设定不良与工作辊辊型不合理等。
这种缺陷容易造成罩退炉内发生粘结现象,对产品质量影响很大。
边部缺陷,主要是由于酸洗切边质量不好或带钢的塑性较差所造成的。
边裂多成锯齿状,严重的边裂容易造成断带,带来生产事故。
要消除边浪等板形缺陷,必须制定合理的压下规程,降低末机架压下率,优化弯辊调整值。
2.罩退工序可能造成的缺陷:主要是粘结缺陷。
粘结是冷轧带钢采用罩式炉退火时难以避免的情况,大部分发生在带钢中部,少量在边部。
粘结钢卷在进入平整工序时,由于粘结部位突然被撕开,带钢局部应力超过屈服。
热、冷轧板带材质量缺陷类别、原因及措施

1.粉末烧结板坯密度不均匀;2.由于热轧开坯时道次加工率小造成不均匀变形,致使产生分层,带入冷轧。3.中间退火不均匀。
1.保证板坯质量;2.控制好热轧工艺;3.改进退火工艺
10
针孔
由于环境卫生不好,粉尘颗粒落到轧件表面,轧制时致使压透箔材而形成微波孔眼
保持良好的环境卫生,加强文明生产。轧前坯料要认真清洗和检查
冷轧板、带材常见缺陷及消除方法
序号
缺陷名称
产生原因
消除方法
1
表面裂纹
1.来料表面裂纹未清除干净,冷轧时继续扩展;
2.来料表面脆性吸气层未清除,轧制时表面层与内层金属变形不一致,使表面被拉裂;
3.压下规程不合理,道次加工率过小,道次太多,使表面硬化太快,轧制时开裂;
4.道次加工率分配不均,造成严重地不均匀变形使局部拉裂。
11
表面粗晶和条状组织
经挤压、锻造的钼及其合金板坯,如果加工率不足或以后退火时,未能达到充分再结晶,轧时易出现此类缺陷
开坯时要给予足够的变形,提高退火温度或增长保温时间,使再结晶充分进行
12
厚度超差
1.量尺寸时不精确或量具不准确,误差过大;2.压下装置未调整好或指针不准确。
1.测量应细心,量具要准确;2.调整好压下装置,校正压下指针。
7
裂边
1.来料裂边未除净,轧制扩展了;2.冷轧加工率过大,边部被拉裂;
3.轧辊曲线配置不当;4.退火不均匀。
1.来料剪裂边要除净;2.调整压下规程;
3.配置好轧辊曲线;4.改进退火工艺。
8
表面起皮
1.道次加工率过小,轧制道次过多;
2.粉末烧结板坯,烧结密度偏低。
1.调整压下规程;2.保证板坯质量。
9
冷轧钢带表面缺陷的成因分析及预防措施
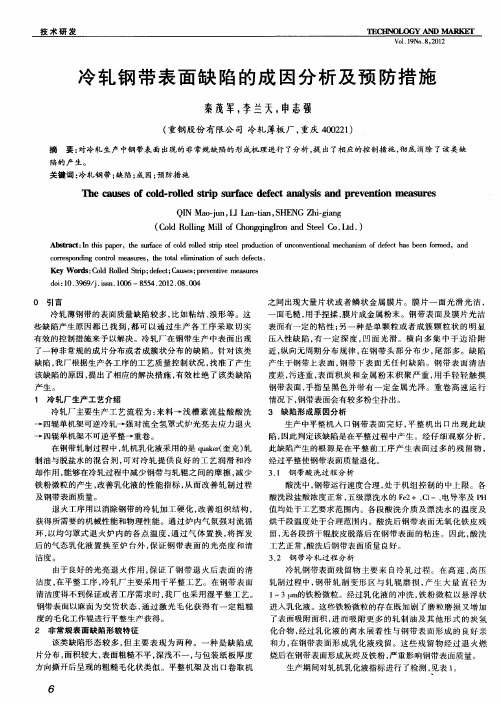
此缺 陷产生 的根 源是在平 整前 工序 产生表 面过 多 的残 留物 , 经过平整使钢带表 面质量退化 。
3 1 钢 带 酸 洗 过 程 分 析 .
制油与脱盐水 的混合剂 , 对冷轧 提供 良好 的工艺 润滑 和冷 可
却作用 , 能够在冷轧过程 中减少钢带 与轧辊之 间的摩擦 , 减少
该类缺陷形态 较多 , 主要 表现 为两种 。一种 是缺 陷成 但
片分布 , 面积较大 , 表面粗糙不平 , 深浅不 一 , 与包装纸 板厚度 方向撕 开后呈现 的粗糙 毛化 状类似 。平整机架 及 出 口卷取机
6
技 术 与 市 场
第 1 卷 第 8 21 年 9 期 02
技 术 研 发
1 冷 轧 厂 生产 工 艺 介 绍
冷轧厂主要生产工 艺流程 为 : 来料 一浅 槽紊 流盐 酸酸 洗
一 四辊 单 机 架 可 逆 冷 轧 一 强 对 流 全 氢 罩 式 炉 光 亮 去 应 力 退 火 一 四辊 单 机 架 不 可 逆 平 整 一 重 卷 。 在 钢 带 轧 制 过 程 中 , 机 乳 化 液 采 用 的 是 qae( 克 ) 轧 ukr奎 轧
表 1 轧 机 乳 化液 成 分 指 标 检 测 情 况
『 标 名 称 皂 化值 指 氯 离子 电 导 率 总铁 含 量 浓度 单 位 P H值 E. . SI
mg KOH/ g mg L / u / m sc mg L / %
常关键 的。比如用 于控制氢气流量 的炉 台氢气 管道重 锤阀能 及 时对乳化液挥 发后 炉 内压 力增 大到设定 值 而报警 泄压 , 使 新鲜氢气通过重锤 阀进入炉 内及 时置换炉 内氢气 和挥发 的乳 化液混合气氛 , 到达及时排除乳化液 的 目的。 因此 , 要求 重点 对退火过程 中氢 气介 质用量 重点监 护 , 每个退 火周期 的氢气 用消耗量必须控 制在 10—20m 9 0 3范围 内, 使退 火气 氛正 常 ,
浅析冷轧带钢表面缺陷成因及控制措施
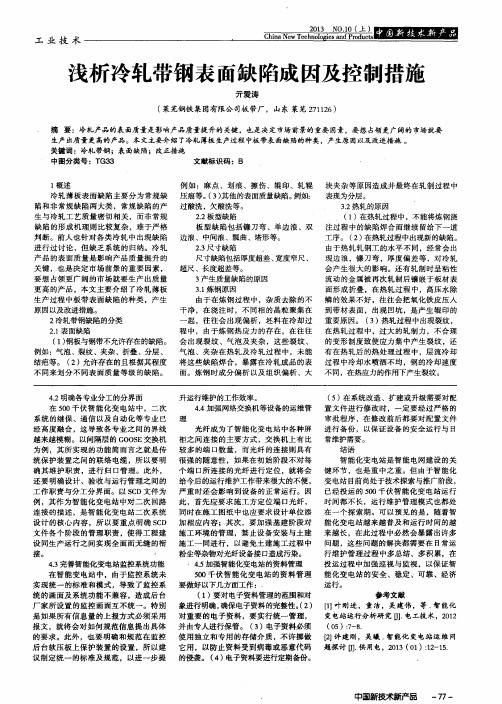
1概 述
冷轧 薄板表 面缺陷主要分为常规缺 陷和非常规缺 陷两大类 ,常规缺陷的产 生 与 冷 轧 工 艺 质 量 密 切 相 关 ,而 非 常 规 缺 陷 的形 成 机 理 则 比较 复 杂 ,难 于 严 格 判 断 。 前 人 也 针 对 各 类 冷 轧 中 出 现 缺 陷 进 行 过 讨 论 ,但 缺 乏 系 统 的 归 纳 。 冷 轧 产 品 的表 面 质 量 是 影 响 产 品 质 量 提 升 的 关 键 ,也 是 决 定 市 场 前 景 的 重 要 因素 , 要 想 占领 更 广 阔 的 市 场 就 要 生 产 出 质 量 更高 的产品 ,本 文主要介 绍了冷轧薄板 生 产 过 程 中板 带 表 面 缺 陷 的 种 类 ,产 生 原 因 以及 改 进措施 。 2 冷 轧带 钢缺 陷 的分 类 2 . 1 表 面缺 陷 ( 1 ) 钢板与钢带不允许存在 的缺陷。 例如 :气泡 、裂 纹 、夹 杂 、折 叠 、分 层 、 结疤等。 ( 2 )允许存在的且根据其程度 不 同来 划分 不 同 表 面 质量 等级 的缺 陷 。
亓 爱 涛
( 莱芜钢铁 集 团有限公 司板带厂 ,山 东 莱芜 2 7 1 1 2 6 )
摘 要 :冷 轧 产 品 的表 面质 量是 影 响产 品质 量提 升 的 关键 ,也是 决定 市 场前 景 的重要 因素 。要 想 占领 更广 阔 的 市场就 要
生产出质量更高的产品。本文主要介绍了冷轧薄板生产过程 中板 带表 面缺陷的种类,产生原因以及改进措施 。 关键词 :冷轧带钢;表面缺陷;改正措施
4 . 2明确各 专业 分工 的分 界 面 在5 0 0 千 伏 智 能 化 变 电 站 中 ,二 次 系统 的继保 、通信以及 自动化等专业 已 经 高 度 融 合 ,这 导致 各 专 业 之 间 的 界 线 越 来越 模 糊 。 以间 隔层 的 G O O S E交 换 机 为例 ,其所实现的功能简而言之就是传 统 保 护 装 置 之 间 的联 络 电缆 ,所 以 要 明 确其维护职 责,进行归 口管理 。此外 , 还 要 明确 设 计 、 验 收 与 运 行 管 理 之 间 的 工作职责与分工分界 面。以 S C D文件为 例 ,其 作 为智 能 化变 电站 中对 二次 回路 连 接 的 描 述 ,是 智 能 化 变 电 站 二 次 系 统 设 计 的 核 心 内容 ,所 以 要 重 点 明确 S C D 文件各个阶段的管理职责 ,使得工程建 设 同生 产 运 行 之 间 实 现全 面 而无 缝 的衔 接。 ・ 4 . 3 完善智能化变电站监控系统功能 在智能变电站中 ,由于监控 系统未 实 现 统 一 的 标 准 和 模 式 ,导 致 了监 控 系 统 的 画 面及 系 统 功 能 不兼 容 ,造 成 后 台 厂家所设 置的监 控画面互 不统一。特别 是 如果 所有 信息量 的上报方式必须采用 报文 ,就将会对如何规范信息提 出具体 的要 求 。此 外 ,也 要 明 确 和 规 范 在 监 控 后 台软压板 上保 护装 置的设 置,所 以建 议制定统一 的标准及规范 ,以进一步提
冷轧产品缺陷及预防介绍
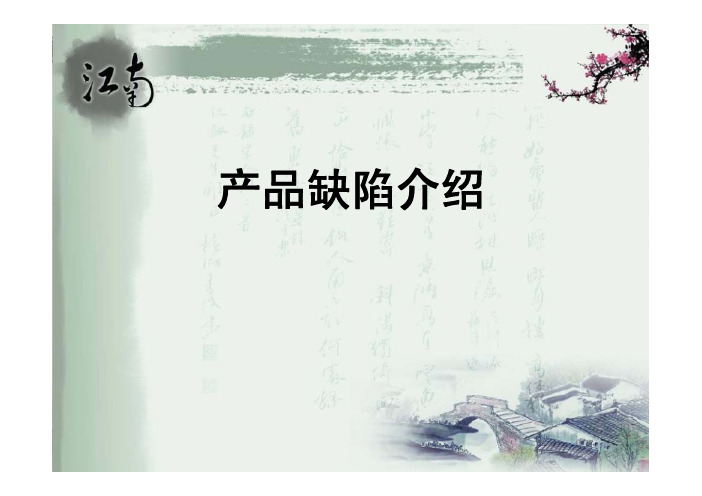
产品缺陷介绍一、冷轧产品缺陷1、表面夹层1、缺陷特征表面夹层形状不规则,呈片状折叠并伴有非金属夹杂物。
2、产生原因表面夹层是由连铸工序中非金属夹杂导致,开始存在与皮下,加工后暴露于外。
2、孔洞1、缺陷特征孔洞是材料非连续的、贯穿带钢上下表面的缺陷。
2、产生原因材料撕裂产生孔洞。
钢质不纯,有非金属夹杂物,轧制后会出现孔洞。
带钢越薄,其现象越明显。
3、氧化铁皮1、缺陷特征氧化铁皮压入是由热轧中被轧入带钢表面的氧化铁皮引起的,氧化铁皮可在酸洗工序中去除,但留下的印点在冷轧过程中也不能完全消除,这种缺陷的外观可为麻点、线痕或大面积的压痕。
2、产生原因氧化铁皮压入是由于热轧除鳞高压水压力不够,氧化铁皮被轧入带钢。
4 、乳化液斑1、缺陷特征乳化液斑是残留在带钢表面的裂化乳化液。
它们随机地分布在带钢表面,形状不规则,颜色发暗。
2、产生原因乳化液斑是残留在带钢表面的乳化液发生裂化作用。
由于在退火过程中残余的乳化液没有被完全蒸发,带钢上多余的乳化液没有被吹净。
5、辊印(凸起)1、缺陷特征凸起辊印是在带钢表面周期性的点状凸起。
2、产生原因凸起辊印是由于冷轧或平整过程中工作辊上有压痕造成的。
6、辊印(凹入)1、缺陷特征凹入辊印在带钢表面呈一定周期性的压痕或印痕。
2、产生原因由工作辊粘有杂物引起。
7、边浪、中浪1、缺陷特征边浪和中浪是沿轧制方向产生的波浪,未扩展到整个带钢宽度。
2、产生原因由辊缝形状与轧件入口形状不匹配造成。
可能是入口轧件有凸度或辊缝设置不合理;也可能是支撑辊凸度或支撑辊位置不合适。
边浪也可能由于园盘剪刀片位置不合理造成。
8、隆起1、缺陷特征隆起是沿轧制方向带状增厚,特别是当带钢被卷起时,可导致不均匀的程度增加;在极端情况下,隆起可能导致波浪、厚度起伏、带卷破裂。
2、产生原因隆起主要发生在热轧机上,而且一旦发生,则在随后的冷轧中也不能消除。
因为钢卷取时,厚度增加会因放大效应而变的越来越明显。
9、氧化色1、缺陷特征氧化色发生在退火后的冷轧带卷上。
冷轧产品缺陷及预防
5欠酸洗 英:Under pickled
【定义与特征】 钢带表面残留着未酸洗掉的氧化铁皮,呈横向的黑色条纹(类似
“抬头纹”的横向黑色细纹),形成带状或片状分布在钢板表面 上。用手摸,手上将粘有黑色的污物。 【原因分析】 热带的表面氧化铁皮经酸洗槽后,未清除干净,残留在带钢表面
震纹的特点是厚度波动,它是机架发生共振产 生的。
【鉴别与判定】
肉眼或打磨后判定,不易与其他缺陷混
淆。
9乳化液斑 英:Emulsion marks
【定义与特征】
是残留在钢带表面的裂化乳化液,随机的分布在钢带表面,形状不规 则,颜色发暗。
【原因分析】
乳化液痕迹是残留在带钢表面的乳化液发生裂化作用,由于退火过程 中残余的乳化液没有被完全蒸发,即带钢上多余的乳化液没有被吹净。
卷轴印:垂直钢板轧制方向的有周期的 横纹。
平整勒印:平整过程中产生的羽毛状的 花纹,分布在局部或整个钢带。
平整横楞:沿钢带宽度方向有明暗相间 的条纹。
折皱:是在钢带的边部连续出现的桔皮状皱 纹。
横折印:在钢带的边部(极少数在钢板中间 的某一部位也有发生)连续出现象等号一样 的折线。在钢板边部长短不一的折线,垂直 或与钢板轧制方向成45度角。
粘结:是有曲线形状的应变条纹,可分布在 钢带边部、中部、二肋任何部位。
表面碳黑:冷轧钢带经罩式炉退火后,钢带外圈或 端面有黑色粉状物,有时可擦掉。
对流板印:冷轧钢带经罩式炉退火后,在钢卷端部 出现的碳黑或焦油残留。
碳化边:颜色呈黑灰色,用手擦不掉,碳与基板发 生化学反应,不溶于酸,又称蛇形迹。一般分布在 钢卷(退过火)的两边,连续或间断分布。
冷轧板常见板形缺陷的形成机理成因分析及改善措施
冷轧板常见板形缺陷的形成机理成因分析及改善措施王成龙(山东钢铁集团日照有限公司,山东日照276800)摘要:当前阶段,我国工业随科技进步不断快速发展,诸多较为重要的生产领域对冷轧板质量的要求越来越高,而毫无疑问,冷轧板形作为影响冷轧薄板总体质量的核心因素,其面临着一些缺陷问题必须要得到有效解决和改善。
文章结合现阶段我国冷轧板生产现状,对其常见缺陷形成机理冷轧板较为常见的板形缺陷进行分析,并且提出了合理化、科学化的相关的改善措施,以供参考,使得冷轧板轧制过程中的板形质量得以改善。
关键词:冷轧板;常见板形缺陷;改善措施Metallurgy and materials作者简介:王成龙(1985-),男,安徽南陵人,主要研究方向:轧钢工艺及管理。
现阶段冷轧生产工艺生产周期较长且整个工艺流程复杂,生产过程中难免会出现各种各样的缺陷和不足,而大多数的产品缺陷往往出现在表面,且有的肉眼可以分辨,有的不好区分且极容易混淆,给工作工艺技术人员消除缺陷带来极大难度。
1解读现阶段冷轧板生产现状众所周知,冷轧板通常较薄,且绝大大多数冷轧产品所产生的缺陷都往往在钢板表面出现。
甚至部分缺陷产生的机理尚不明确,即便是生产线上的专业质检人员也难以精确对某些缺陷进行鉴别。
据调研,当前阶段的冷轧板日常生产过程中,通常较为常见的冷轧板形缺陷形式可分为:边部波浪、单边波浪、中间波浪、复合波浪等等。
而这些较为明显而常见的缺陷产生的最主要原因都是存在于日常的轧制环节里。
想要有效解决冷轧板形的各类缺陷问题,认为相关工作工艺技术人员一定要集中精力全面提升和改进板形的控制技术,这就需要在日常工作中,工作人员除了采用最先进的控制设备外,并且要制定和完善冷轧板形先进的管理制度体系,并做好日常各项监督工艺管理工作。
2常见的冷轧板形缺陷及形成机理成因分析冷轧板形即为板面的平坦度,包括板凸度以及板面平直度。
客观而言,板形缺陷通常指的是板带材在日常的轧制环节过程中横向部位因工作失误工艺控制精度不够而产生了一定褶皱和波浪,这种情况让板带材的内部产生大量残余应力存在,对冷轧板质量产生严重不利影响。
冷轧板常见表面缺陷及成因
冷轧板常见表面缺陷及成因冷轧板常见表面缺陷及成因冷轧板常见表面缺陷及成因冷轧板常见表面缺陷有麻点缺陷、冷硬板中部穿裂、冷硬板边裂、带状翘皮、不连续点线状缺陷、黑(灰)线(带)缺陷等。
1麻点缺陷。
单个麻点呈不规则分布,整体呈现带状分布。
麻点在微观上由许多微小的凹坑组成,凹坑内部看到很多细小的颗粒。
凹坑部分杂质元素与结晶器保护渣成分基本一致,说明这些夹杂主要来自结晶器保护渣。
2冷硬板中部穿裂。
中部穿裂部位悬挂着许多鳞状碎片,大块的鳞状碎片边沿包含许多细小的小颗粒,断口为脆性形貌。
细小颗粒与结晶器保护渣成分相似,确定这些夹杂主要来自结晶器保护渣。
3冷硬板边裂。
边裂处呈锯齿状,裂口部位包含大量大小不一的颗粒,颗粒与基体之间无明显间隙,部分颗粒沿平行于裂口方向呈线状分布,同样这些颗粒来自结晶器保护渣。
4带状翘皮。
带状翘皮在板材近表层有一明显薄层与基体发生分离或半分离状态,翘皮部位皮下含有大量粉状物质,能谱分析,这些物质主要来源于变性后的结晶器保护渣。
5不连续点线状缺陷。
板材厚度薄于1mm,该缺陷易发生。
线状缺陷多成簇出现,缺陷底部残留了硅酸盐复合夹杂物。
主要是CSP铸坯中坯壳及皮下、中心部位富集的夹杂物,在热轧过程中,随着厚度变薄,逐渐呈现。
6黑(灰)线(带)缺陷。
酸洗后的宏观形貌有条状、长条状、块状或多点状,轮廓特别分明。
由于1)轧辊质量不佳,主要是氧化膜剥落、老化粗糙、剥落、异物粘附等。
2)除鳞不干净,主要由于喷嘴堵塞、喷嘴压力低等因素。
3)工艺因素,机架间冷却水控制不规范等。
4)连铸至F7前输送辊道划伤,主要由于炉辊结瘤、异物粘结、死辊等。
以上因素导致氧化铁皮压入,从而在冷硬板上形成黑(灰)线(带)缺陷。
冷轧产品质量缺陷及改正措施一、冷轧与镀锌产品外在质量冷轧薄板之所以说是精品,一个主要的原因就是冷轧薄板对表面质量的严格要求。
可以说,在整个冶金行业中,冷轧薄板对表面质量是要求最高最严的,尤其是宽而薄的冷轧钢带产品和对冲压成型性能有严格要求的产品。
冷轧镀锌板典型表面质量缺陷成因及控制措施探讨
区域治理综合信息冷轧镀锌板典型表面质量缺陷成因及控制措施探讨闫策河钢邯钢冷轧厂,河北 邯郸 056001摘要:近年来,随着我国社会主义市场经济建设进程的不断加快,冷轧镀锌板因其具有良好的使用性能,被广泛地应用于人们日常的生产生活中,市场需求逐渐提高的同时对其锌版质量也提出了更高的要求。
但是在实际的生产过程中,由于冷轧镀锌板的表面存在一定的生产缺陷,从而导致基板防腐蚀保护层缺失,严重影响了它的使用性能。
鉴于此,本文主要分析了当下比较典型的冷轧镀锌板表面缺陷的成因,并提出了相应的预防处理措施,以期为后期冷轧镀锌板表面质量的提高奠定了良好的基础。
关键词:冷轧镀锌板;质量缺陷;成因分析;控制措施一、冷轧镀锌板表面典型缺陷形成的原因与控制措施通常情况下,冷轧镀锌板是由于锌液表面、悬浮以及底部的混合的锌渣等一些金属化合物颗粒钻在钢板表面产生了影响,改变了产品的外观与质量。
当气刀气流导致锌液形成两个涡流时,吸附在周围的尘土和空气,会产生锌液氧化的现象。
机组设定的温度越高,在锌的镀层就会越来越薄,导致锌渣一类的金属化合物变多。
形成底渣的原因,主要是由于铁在锌液中到达饱和状态,在锅底形成了铁锌合金,从而通过流动与搅拌,粘附在表面形成一些缺陷。
1 冷轧镀锌板表面漏镀缺陷通常,当工作人员在进行生产作业时,由于操作的不规范或违规操作往往会导致漏镀问题的发生,进而造成冷轧镀锌板表面缺陷,影响冷轧镀锌板的整体质量。
当在显微镜下进行观察时,漏镀部位的镀锌层分布不均匀,呈现断续无规则状的分布景象,有的钢板被包裹,而有的则处于基本裸露的状态,并有小块或点状的镀锌层散落分布,经过对其分布物质进行处能谱分析,发现其内含有一定量的碳元素,由此可知漏镀缺陷的形成原因主要是因为在镀锌过程中,轧制油等油脂类物质未全面融合,在其镀锌板表面依旧有部分物质残留,从而导致镀锌液无法最大程度地发挥其应有的作用。
除此之外,当工作人员在进行镀锌操作的过程中,薄膜和油污膜的使用在一定程度上也会对铁锌合金层的正常形成产生一定的干扰作用,降低锌液对基板浸润性降低的同时,锌层的粘附性也受到了一定的影响,进而导致锌层极易从基板处脱落,造成漏锌缺陷的产生。
- 1、下载文档前请自行甄别文档内容的完整性,平台不提供额外的编辑、内容补充、找答案等附加服务。
- 2、"仅部分预览"的文档,不可在线预览部分如存在完整性等问题,可反馈申请退款(可完整预览的文档不适用该条件!)。
- 3、如文档侵犯您的权益,请联系客服反馈,我们会尽快为您处理(人工客服工作时间:9:00-18:30)。
还是塑性水平都不十分均匀 , 以上述缺陷只是 所
局 部表 现 出来 。 3 3 对 冷轧 生 产的建 议 .
为避免 冷轧 板 表 面 出 现块 状 和亮 线 缺 陷 , 冷 轧 生产 首先 应 把道 次 最 大 轧 制 力 减小 , 以避 免产 生 过 大 的剪 切 力 , 致 轧 材 被 破 坏 。 当这 一 改进 导 不 能起 到应 有 作用 时 , 考 虑在 轧 制 中间 增加 一 可 次 中间退火 , 以使轧 材 的塑性 得 以 回复 , 就完全 这 可 以避免此 类 事故 。
亮线的边缘部位用刀片划线标记 , 以便于观察。1 号试样 电镜分析后沿纵 向磨制进行金相分析 , 4
号试 样 沿横 向磨 制 。
送 检 的两块 钢板 编 号 分 别 是 00 06 8575规 格
0 6 m ×8 0 i 0 0 0 5 规 格 0. m × .m O h m和 8 5 7 9 5 m
4 结 论
位错密集形成的亚裂纹线条。这些都证明 , 钢板
表 面的缺 陷是 冷轧 裂纹 。
长度较大的裂纹存在变形痕迹 , 裂纹两侧的 晶粒 度完 全不 同 , 明裂 纹两 侧 的变形 量 不一样 。 说
也就 是说 , 纹形 成后 , 裂 钢板 仍 旧继续 变形 。通 过 以上 分析 可 以推 测 , 部 分 裂纹 并 不 是 冷 轧 的最 大 后道 次形 成 , 而是 发生 在前几 道 次 。
通 过 以上分 析 可 知 , 轧 板 表 面 的块 状 缺 陷 冷 和 条状亮 线 属 于 同一 种 缺 陷 , 即冷 轧 板表 面 的局 部破 损 , 只是 严重 程度 和密 集程 度有 差别 。
2 3
N . o4
De e e 0 8 c mb r2 0
《 中国重型装备》
破 损 。但根 据 以上 的裂 纹 形 态 分 析结 果 , 轧 变 冷
形量过大并不是本次事故的关键原因。
本 公 司生产 的冷 轧 原料 板 , 论 是 化 学 成 分 无
现夹杂物, 且总体 夹杂物较 少 , 各类 夹杂物均为
05级 , 而排 除 夹 杂 物 引起 裂 纹 的可 能 。这 些 . 从 裂纹 都在 冷轧 最 大 变 形 区 内 , 纹 行 走 路 线 与 冷 裂 轧变 形流 线完 全 吻合 , 而且 , 裂纹 附近 还存 在 晶体
HE AVY MAC NE HI RY C E E AND T C S I NC E HNO OGY L
破损的显著特点都是 以裂纹形式存在 。这些 裂纹两侧没有 内氧化质点 , 可以证 明裂纹没有经 过长时高温加热 , 因此 , 这种裂纹不是连铸坯表面 裂纹 。裂 纹微 细 、 净 , 有 高 温 氧 化现 象 , 明 干 没 证
图6 2号试样 电镜分析 图
F g r E e to c o c p n l ssfr2 s mp e iu e 6 lc rn mi r s o e a ay i # a l o
图 5 1 试 样 电镜 分 析 图 号
F g r E e to c o c p n lssf r1 s mp e iu e 5 l cr n mir s o e a ay i o # a l
2 2
《 中国重型装备》
HE AVY MAC NER S I NC HI Y C E E AND T C E HN0 0GY L
No. 4
D c mb r2 o e e e 0 8
23 扫 描 电镜能 谱分 析结 果 . 对 1 号试 样块 状 掉 肉缺 陷部位 进行 了扫 描 电 镜 分析 ( 5 ) 未 发 现 夹 杂 物 , 缺 陷部 位 局 部 图 a, 对 放 大后 , 可见 到轧 压 痕迹 ( 5 、c 。 图 b5 )
《 中国重型装备》
HEAV MACHI RY S E E AN TE HNOL Y NE CI NC D C 0GY
No. 4 D c mb r2 0 e e e 0 8
冷 轧 板 表 面 缺 陷成 因及 预 防措 施
王宏 霞
( 山东泰山钢铁集 团有 限公 司研究所 , 山东 2 10 ) 7 0 1 摘要 : 近期 出现的冷轧板表面条痕状 和点状缺 陷进 行分析 , 对 确定冷 轧生 产时道 次轧制 力不合 理 , 原材料 成分 、 塑性 不均匀是导致产生缺陷 的原 因。降低 轧制 力、 增加退火次数可减少 缺陷。
21
N . o4
De e e 0 8 c mb r2 0
《 中国重型装备》
HE AVY MAC NER S I NCE AND T CHNOL HI Y C E E OGY
亚裂 纹 线条 ( 3 ) 图 c 。也有 表 面细 小裂 纹 , 些裂 这
夹 杂物 ( 4 ) 试 样 表 面 夹 杂 物 级 别 都 是 O 5 图 a, .
对 2号 试 样 亮 线 部 位 也 进 行 了 扫 描 电 镜 观 察, 亮线 内有 许 多 裂 纹 和 白色 小 点 ( 6 ) 裂 纹 图 a, 处 放 大 可 见 有 与 1号 试 样 相 似 的块 状 缺 陷 ( 图
6 ) b。
3号试 样 扫 描 电镜 分 析 , 状 亮 线 部 位 钢 板 条
b亮线处局部放大
表皮破损 , 钢板正 常部位表皮 完好 , 图 7 。 而 见 a
表 皮破 损 区域放 大后 , 见异 物 ( 7 ) 未 图 b。
3 讨 论 3 1 破 损性 质 .
图7 3号试样 电镜分析图
F g r Elcr n mir s o e a ay i o #s mp e i e7 u e t co c p n lss f3 a l o
裂纹 没有 经过 高温 阶段 , 由此 可知 , 纹也 不可 能 裂
是热 轧板 残 留裂纹 。裂 纹 内和裂 纹 附近也 没有 发
本公司生产的冷轧 原料塑性并不太好 , 允许
的冷轧 变形 量也 不 太 大 , 果 冷 轧 变 形量 超 过 了 如
冷 轧原 料允 许变 形 量 , 材 内部 也要 产 生 裂纹 或 轧
近 期冷 轧厂 批 量 出现 冷 轧板表 面 条痕状 和 点 状 缺 陷 , 重影 响 了产 品的外 观质 量 , 严 特取样 对 其
进 行分 析 。
1 试验 方 法
80mm, 0 材质 均为 S C P C。 首 先对 钢板 进 行 宏 观 检 验 , 取 典 型 部 位进 选 行 金 相 分 析 、 描 电镜 分 析 , 样 截 取 部 位 见 图 扫 试 1 、 、 试样 做 扫描 电镜 分析 , 2 3号 试样 。123号 在 、
a裂纹 附近组织
b裂纹两侧的组织
c亚裂纹
d 表面小裂 纹两侧 组织
图 3 2号试样块状缺陷部位金相分析
F g r Mea l r ia h s n y i f rt e l mp h p ee ta e f2 s mp e i e3 u tl gc lp a e a a ss o h u l u y s a e d fc r a o # a l
关键词 : 轧板 ; 冷 表面缺 陷 ; 预防措施
中 图 分 类 号 :G 3 .2 T 3 5 1 文 献 标 识 码 : B
,
T e Re s n & P e e tv a u e o h ao r v nie Me s r sfr
C l l d P ae S ra e Dee t od Rol lt u fc fcs e
纹与钢板表面成 近似 4 。 5 的角 , 裂纹处组织有急
剧变 形 痕迹 ( 3 ) 图 d。 4号试 样金 相 分 析 亮 线 处 凹 凸不 平 , 没 有 但
级, 腐蚀后亮线处组织与正常部位组织没有差别
( 4 ) 图 b 。
b
图 2 试样宏观形貌
F g r Ma r p e r n e o e s mp e iu e 2 c o a p a a c ft a l h
2 试 验 结果
22 金 相 检验 结 果 1号 试样 块 状 缺 陷部 位 金 相 .
观 察 如下 :
2 1 宏 观检 验结 果 .
裂纹内没有夹杂物 , 也没有氧化和 内氧化现
编号为 000 6 857 5的钢板表面既有短05 又 见 a编 8 579的 钢板 表 面 主要 是 条状 缺 陷 , 条状 缺 陷较 亮且 较直 ,
见图 2 。 b
收稿 日期 :0 8 6 6 2 0 —o ~1
象, 各类夹杂物均为 0 5 ; . 级 腐蚀后裂纹走向与组
织 变形 流线 一 致 ( 3 ) 图 a 。放 大后 裂 纹 两侧 的组 织 晶粒度 不 同 , 纹外 侧 晶粒 较细 , 裂 裂纹 内侧 晶粒 较 粗 , 裂 纹 开 口均 在 钢 板 表 面 , 形 十分 剧 烈 且 变 ( 3) 图 b 。裂 纹 附 近还 存 在 晶体 位 错 密集 形 成 的
a
b
图4 4号试样 条状 亮线金相分析
F g r Meal r ia h s n y i fr te srp s a e b i h i e o # s mp e i e4 u tl gc p a e a a sso h t h p r tl f u l l i g n 4 a l
3 2 裂纹 形成 原 因 .
( ) 线 和 块 状 缺 陷 实 际是 同 一 种 缺 陷 , 1亮 只
冷轧变形主要依靠轧辊的压力。当轧辊压力
派生 出 的剪切 应 力 超 过材 料 的剪 切 强 度 时 , 材 轧 内部 就会 产生 裂纹 、 损 。轧辊 的压 力越 大 , 破 轧材
W a g Ho xa n ng i
Ab t a t S r t n a d s o h p ee t o ec l ol d p ae s r c a eb e n l z d i i p p r n sr c : t ai n p t a e d f cs ft o d r l l t u f e h v e n a a y e n t s a e ,a d i i o s h e a h t i d tr n d t a n e s n b e p s ol gf r e d rn ec l ol g p o u t n a d n n-n fr a tr o - s ee mi e h tu r a o a l a sr l n o c u g t o d r l n r d c i n o - i m r w mae i c n- i i h i o u o l a p st n a d p a t i r h e s n h c a s h ee t e u i g rl n r e a d ic e sn n e i gfe u n o i o n l s ct a et e r a o sw ih c u e te d f c .R d cn ol g f c n n r a ig a n a n q e — i i y i o l r c a e u ed fc. y c n r d c ee t Ke r s c l o ld p ae s r c ee t p e e t e me s r s y wo d : o d r l lt ; u f e d f c ; r v n i a u e e a v