B13001-弯管内热波动及其削弱机理研究
基于COMSOL软件的直角弯管声波传播特性规律研究

基于导热反问题圆管内壁腐蚀减薄及污垢增厚的识别

第49卷第1期2022年北京化工大学学报(自然科学版)Journal of Beijing University of Chemical Technology (Natural Science)Vol.49,No.12022引用格式:张经豪,熊平,郝睿智,等.基于导热反问题圆管内壁腐蚀减薄及污垢增厚的识别[J].北京化工大学学报(自然科学版),2022,49(1):98-105.ZHANG JingHao,XIONG Ping,HAO RuiZhi,et al.Identification of corrosion thinning and fouling thickening on the inner wall of a circular tube based on the inverse heat conduction problem[J].Journal of Beijing University of Chemical Technol⁃ogy (Natural Science),2022,49(1):98-105.基于导热反问题圆管内壁腐蚀减薄及污垢增厚的识别张经豪 熊 平 郝睿智 卢 涛*(北京化工大学机电工程学院,北京 100029)摘 要:以二维圆管为研究对象,基于有限元法的导热正问题(direct heat conduction problem,DHCP)以及基于列文伯格-马夸尔特(Levenberg -Marquardt,L -M)算法的优化方法来构建二维稳态导热反问题数学模型,通过关联COMSOL 与MATLAB 对圆管内壁腐蚀减薄和污垢增厚两类缺陷进行了定量识别㊂为了探究模型的有效性与精确性,分别设定了几种典型缺陷进行数值计算,并系统地分析了初值选取㊁管道外表面测温点数目及测温误差对反演精度的影响㊂数值实验结果表明该模型能够准确地识别圆管内壁面的两类缺陷,且具备良好的稳定性与抗噪性㊂关键词:导热反问题;缺陷识别;列文伯格-马夸尔特(Levenberg -Marquardt,L -M)算法中图分类号:TK38 DOI :10.13543/j.bhxbzr.2022.01.012收稿日期:2021-05-31第一作者:男,1996年生,硕士生*通信联系人E⁃mail:likesurge@引 言在工业生产中,管道广泛应用于输气㊁供水和运油等领域㊂由于管道长期处于高温高压的工作状态,在使用过程中容易造成内壁的腐蚀㊁脱落,甚至产生污垢黏连附着在内壁上导致出现内壁增厚等现象,这些缺陷的存在成为安全生产和使用的潜在隐患[1]㊂因此,对管道内壁缺陷的检测具有重要意义[2-3]㊂导热反问题(inverse heat conduction problem,IHCP)已在很多工程领域中得到广泛应用[4]㊂导热反问题常用于计算反演边界条件[5-9]㊁热物性参数[10]㊁物体内部热源[11]及初始条件等未知项,也可用于物体内部缺陷[12-15]和内壁缺陷的识别㊂Chen 等[16-17]采用共轭梯度法估计了管道外壁的未知霜层边界形状和管道内壁上的未知污垢边界形状,但只单一讨论了沿管道轴向变化的霜层或污垢分布情况;文献[18-19]对双层炉膛内壁的边界形状进行了反演,但没有探讨初始值及测点数目对反演结果精确度的影响;文献[20-24]应用共轭梯度法对管道内壁面的边界形状进行了稳态或瞬态的识别,并分别对所建反演模型的可行性进行了探究;张林等[25]在改进的一维修正算法基础上提出一维加权法,对二维圆管交界面形状进行了定量识别,提高了识别效率;Mohasseb 等[26]采用遗传算法作为非适定导热反问题的计算方法,求解了方形板的热流密度边界,但算法的稳定性与收敛速度有待提高;文献[3]㊁[27-30]均采用列文伯格-马夸尔特(Levenberg -Marquardt,L -M)算法对未知参数进行了计算,算例验证了算法的有效性和优越性㊂在众多求解导热反问题的数值计算方法中,属于梯度类算法的L -M 算法因具有稳定性好㊁构造思路简单㊁收敛快等优势而被广泛应用㊂当前的大多数研究都只对管道内壁腐蚀减薄缺陷进行单一的讨论,涉及管道内壁污垢增厚缺陷识别的相对较少,因此本文提出基于有限元法和L -M 算法构建反问题数学模型,利用COMSOL 与MAT⁃LAB 联合仿真稳定㊁快速的优势,将管道内径作为反演参数,分别对管道内壁腐蚀减薄缺陷与污垢增厚缺陷进行定量识别,并构造数值实验对反演结果的精确性和稳定性进行分析㊂1 二维圆管物理模型二维圆管物理模型如图1所示㊂管道外径a =0.3m,壁厚d =25mm㊂管道的导热系数λ1=17.60W /(m ㊃K),污垢的导热系数λ2=3.14W /(m ㊃K),外壁面对流换热系数h out =10W /(m 2㊃K),环境温度T a =25℃,内壁面对流换热系数h in =1000W /(m 2㊃K),管内流体温度T f =200℃,θ为极角,r 为出现缺陷后管道的内壁面极径㊂图1 管道两类缺陷的物理模型Fig.1 Physical model of two types of defects in pipelines2 IHCP 数学模型2.1 导热正问题(DHCP )由于所研究内容为二维圆管内壁面缺陷的稳态识别,基于此作如下合理假设:1)管道忽略轴向导热的影响;2)管道导热系数和管内外的对流换热系数均为常数㊂2.1.1 管道增厚缺陷圆管的导热偏微分方程为∂2T ∂x 2+∂2T∂y 2=0(1)假设给定内壁面和外壁面均为第三类边界条件,则边界条件为-λ(1∂T 1∂n )out =h out(T out-T a)(2)-λ(2∂T2∂n )in=h in(T in-T f)(3)污垢增厚缺陷存在着交界面Γ,在此处T 1=T 2(4)-λ(1∂T 1∂n int,)1=-λ(2∂T 2∂n int,)2(5)式中,下标1代表管壁区域Ω1,下标2代表污垢区域Ω2;下标in㊁out 分别为圆管内壁面和外壁面;n 代表法线方向;下标int 代表圆管与污垢交界面边界㊂2.1.2 管道减薄缺陷管道减薄缺陷只存在于管壁区域Ω1,将式(3)进行修改可得式(6)㊂-λ(1∂T1∂n)in=h in(T in-T f )(6)式(6)与式(1)㊁式(2)共同构成了管道减薄缺陷导热正问题的数学描写㊂2.2 导热反问题导热正问题是一个定解问题,而导热反问题则是一个最优化问题㊂2.2.1 L -M 算法L -M 算法是非线性回归中回归参数最小二乘估计的一种方法,L -M 算法将最速下降法和线性化方法相结合,从而较快地找到最优值㊂对于两类内壁面缺陷的反演,内壁面几何边界都是未知的,可由极坐标向量R (θ)描述R (θ)=[r 1,r 2, ,r n , ,r N ]T (7)式中,r 为极半径;N 为内壁面离散节点个数㊂数学偏微分方程组(式(1)~(5)以及式(1)㊁(2)㊁(6))需要获得外壁面测点温度以满足其封闭性,离散后的外壁面温度测量值记为Y =[Y 1,Y 2, ,Y m , ,Y M ]T(8)式中,M 为外壁面测点数㊂进一步构建该最优化问题的目标函数为S (R )=[Y -T (R )]T [Y -T (R )](9)式中,T (R )为根据R (θ)所求得的外壁面温度的计算值,表示为T (R )=[T 1,T 2, ,T m , ,T M ]T(10)通过式(9)对未知参量R (θ)求偏导得到目标函数梯度的最小化条件为 ΔS (R )=-2J T (R )[Y -T (R )]=0(11)式中,J (R )为敏度系数矩阵,表示为J (R )[=∂T T (R )∂]RT(12)对式(11)的T (R )进行泰勒级数展开舍去高阶项,并加入衰减参数μk LM 来调节迭代速度,得到迭代式R k +1=R k +[(J k )T J k +μk LM Ωk ]-1(J k )T [Y -T (R k )](13)式中,k 为迭代次数;Ωk 为一对角矩阵,表示为Ωk =diag[(J k )T J k ](14)迭代开始采用最速下降法以较大的μk LM 进行计㊃99㊃第1期 张经豪等:基于导热反问题圆管内壁腐蚀减薄及污垢增厚的识别算,后来降低μk LM 通过高斯牛顿法得到最终反演值㊂根据偏差原理给出收敛条件为S (R )<ε(15)式中,ε在不考虑测量误差时为一小正数㊂2.2.2 数值计算过程MATLAB 使用mphload 函数加载COMSOL 的mph 文件,通过mphinterp 函数便可读取数据,无需使用输入/输出文件㊂COMSOL 在被调用时可以自动构建几何模型㊁更新网格和求解计算,有效提高了反演效率㊂利用L -M 算法求解导热反问题的流程图如图2所示㊂图2 反演流程图Fig.2 Chart of inversion progress2.2.3 反演识别误差为验证反演结果对引入测量误差的敏感性,在由导热正问题计算得到的外壁面精确值的基础上引入随机误差,来模拟实际的测量值㊂T mea =T exact +σω(16)式中,T mea 为外壁面温度测量值;T exact 为外壁面温度精确值;σ为标准偏差;ω为区间[-2.576,2.576]内服从标准正态分布的随机数,该区间能达到99%的测量可靠度㊂当考虑实际测温误差时,收敛标准ε写成ε=∑Mm =1σ2m =Mσ2(17)为了表征反演值与精确值的偏离程度,定义平均相对误差为E RR=1N∑Nn =1r n ,exact -r n ,estr n ,exact×100%(18)式中,r n ,exact 为内径精确值;r n ,est 为内径反演值㊂3 计算结果与分析通过运行程序进行数值计算,以验证管道减薄缺陷与增厚缺陷导热反问题反演的精确性㊂首先设定内壁面缺陷形状,由导热正问题得出外壁面温度模拟的实际测量值,为导热反问题提供输入数据;所设定的内壁面缺陷形状参数作为校验数据㊂为验证程序的稳定性和抗噪性,分别探讨初值㊁测温点数目及测量误差对反演结果的影响㊂3.1 管道减薄缺陷对于管道减薄缺陷,在外壁面上均匀设置36个测点,内壁面由36个均匀分布的离散节点拟合得到㊂设定沿周向变化的内壁面几何形状为阶跃式函数㊁锲形函数和正弦函数,分别探讨这3种不同工况下的导热反问题㊂3.1.1 阶跃式函数设定内壁面边界形状按阶跃式变化,即Case 1㊂R (θ)=0.275,θ∈[0,5π/6)∪(7π/6,2π]0.2875,θ∈[5π/6,7π/6{](19)图3 不同初值下阶跃式几何边界的反演值与精确值Fig.3 Inversion and exact values for a stepped geometricalboundary with different initial values根据式(19)验证内壁面几何边界呈阶跃式规律变化下的反演结果,并探讨不同初值R 0对反演结果的影响㊂由图3可以看出,当R 0取不同值时,反演曲线与精确曲线的走向基本趋于一致,靠近阶跃边界处的识别效果相对较差,但程序仍可较好地识别出管道内壁的边界形状㊂由表1可以进一步得出,3种初始边界假设下,反演结果的平均相对误差最大仅相差0.015%,说明初始边界假设对内壁面几何边界的反演几乎没有影响;此外,3种初值下得出计算结果的平均相对误差均不超过0.1%,验证了程序反演的精确性㊂㊃001㊃北京化工大学学报(自然科学版) 2022年表1 Case1~Case3平均相对误差值Table 1 Mean relative error values of Case1to Case3Case R 0/m Mσ/℃E RR /%0.263600.06610.273600.0510.283600.0510.272400.15520.273600.0580.277200.0110.273600.00130.27360.20.9450.27360.51.3233.1.2 锲形函数设定内壁面几何边界形状以锲形函数变化,即Case 2㊂R (θ)=0.275,θ∈[0,π)∪(π,2π]0.2875,θ={π(20) 在式(20)所示的内壁边界形状以锲形函数变化的条件下,研究不同外壁面温度测点数目对识别结果的影响㊂由图4可以看出,当M =24时,程序对内壁边界的识别效果相对较差,尤其是在阶跃点附近更为明显;随着外壁面温度测点数目的增加,阶跃点处的识别效果逐渐变好,当M =72时,反演曲线与精确曲线高度吻合㊂结合表1可进一步得出,外壁面测温点数越多,识别效果就越好㊂M =36时的平均相对误差为0.058%,M =72时的平均相对误差为0.011%,均可较好地识别出内壁边界形状㊂图4 锲形几何边界不同测温点数时的反演值与精确值Fig.4 Inversion and exact values for a wedge⁃shapedgeometric boundary with different numbers of measurement points3.1.3 正弦函数设定内壁边界形状随正弦函数变化,即Case 3㊂R (θ)=0.285+0.01sin θ(21)内壁面边界形状按式(21)以正弦规律变化,引入标准偏差,分析不同偏差对反演结果的影响㊂如图5所示,可以看出当σ=0℃时,反问题得到的反演曲线与正问题得出的精确曲线几乎重合;当σ=0.2℃和σ=0.5℃时,两条反演曲线均在精确值附近上下小范围波动,且在σ=0.5℃时变化得相对更为明显㊂根据表1不难进一步得出,随着标准偏差的增大,反演误差也随之增大,但3种标准偏差下的平均相对误差均不超过1.5%,说明采用此方法反演边界形状对测量误差的变化不敏感,具有一定的抗噪性㊂图6是当边界形状为正弦函数时的迭代收敛历程图,由图可看出,迭代步长先大后小,且只需要迭代3次即可满足所设定的收敛条件㊂对比图6(c)与图6(d)可知,运用L -M 算法可在低迭代步数下准确地识别出缺陷㊂图5 正弦几何边界不同测量误差时的反演值与精确值Fig.5 Inversion and exact values of a sine geometricboundary with different measurementerrors图6 正弦函数边界缺陷反演时的收敛历程Fig.6 Convergence history of sine function boundarydefect inversion㊃101㊃第1期 张经豪等:基于导热反问题圆管内壁腐蚀减薄及污垢增厚的识别3.2 管道增厚缺陷同样地,对于管道增厚缺陷,在外边界上也均匀设置36个测点,含有污垢的内壁面亦由36个均匀分布的离散节点拟合得到,可通过反演管道内径进而得出污垢的厚度㊂设定的内壁面污垢几何形状包括均匀增厚缺陷㊁沿周向变化的三角形函数以及椭圆函数,分别探讨这3种不同工况下的导热反问题㊂3.2.1 均匀增厚设定内壁面有均匀厚度的污垢,即Case 4㊂R (θ)=0.265(22)如式(22)所示,假设周向含有均匀污垢的圆管内径为0.265m,即污垢的厚度为0.01m,分别设置不同的初值R 0,所得污垢厚度Δd 反演结果如图7所示㊂由图7可以看出,不同初值下的反演值与精确值相差甚小,且反演曲线呈小范围波动㊂由表2可得,3种初始值下反演的平均相对误差均不足0.1%,说明初值对均匀污垢反演结果的影响较小,程序对于内壁面均匀污垢有较好的识别能力㊂图7 不同初值下均匀污垢厚度的反演值与精确值Fig.7 Inversion and exact values of uniform foulingwith different initial values表2 Case4~Case6平均相对误差值Table 2 Mean relative error values of Case4to Case6Case R 0/m Mσ/℃E RR /%0.253600.01040.263600.0040.273600.0070.262400.03350.263600.0130.267200.0130.263600.00660.26360.20.3090.26360.50.7393.2.2 三角形函数设定内壁几何边界形状按三角形函数变化,即Case 5㊂R (θ)=0.005θ+0.25,θ∈[0,π)-0.005(θ-π)+(0.005π+0.25),θ∈[π,2π{](23)如图8所示,含有污垢的管道内壁面半径(即内壁污垢形状)随周向呈三角形规律变化㊂根据式(23)对反演结果进行验证,同时探讨改变外壁面测温点个数对反演结果的影响㊂由表2可知,增加外壁面测温点个数可以更加准确地识别出内壁面的污垢形状,但提高的程度有限,当测温点的个数达到一定值时,增加节点个数对识别精度的提高影响并不大㊂另外,由表2结果也可看出,当测温点个数较少时识别精度仍然较高,M =24时的平均相对误差为0.033%,表明仍能较准确地识别出内壁面的污垢形状㊂图8 不同测温点数下三角形污垢厚度的反演值与精确值Fig.8 Inversion and exact values of trianglefouling with different numbers of temperaturemeasurement points3.2.3 椭圆函数设定内壁面几何边界形状以椭圆函数变化,即Case 6㊂R (θ)=(0.27cos θ)2+(0.26sin θ)2(24)式(24)为内壁边界形状随椭圆函数变化的情况,即内壁污垢形状亦呈椭圆函数变化㊂图9为不同标准偏差下污垢尺寸的反演值与精确值㊂由图可看出,无偏差下反演值与精确值二者的曲线走向基本同步;当存在标准偏差时,反演值围绕精确值附近上下波动,且随着标准偏差的增大,波动的幅度和频率也愈为明显㊂根据表2可知,在标准偏差增大到0.5℃时,波动值仍可保持在1%以内,说明反演模㊃201㊃北京化工大学学报(自然科学版) 2022年型在识别内壁污垢时稳定性较好㊂图10为当污垢以椭圆函数变化时的管道迭代收敛历程图㊂由图可以看出,对椭圆污垢的反演与对正弦减薄缺陷的反演一样,仅是经历3次迭代就达到了最终收敛,迭代步数较少㊂图9 不同测量误差下椭圆污垢厚度的反演值与精确值Fig.9 Inversion and exact values of elliptical foulingfor different measurement errors图10 椭圆函数边界缺陷反演时的收敛历程Fig.10 Convergence history of elliptic function boundary defect inversion4 结论(1)通过设定多种工况进行数值模拟,验证了二维稳态导热反问题数学模型的有效性与精确性㊂研究结果显示,该反演模型能够实现对内壁面两类缺陷的识别,且具有较高的识别精度㊂(2)对圆管内壁腐蚀减薄及污垢增厚两类缺陷进行了反演结果稳定性的探究,计算结果表明,初值选取对反演结果无明显影响,反演精度随着外壁面测温点数目的增加而提高,但精度提高有限㊂(3)引入随机测量误差,探讨了反演结果对测量误差的敏感性㊂数值算例结果显示,本文算法具有一定的抗噪性,当存在滓=0.5℃的标准偏差时,仍能得到较为精确的结果㊂目前,本文只研究了二维圆管内壁面缺陷的稳态识别,缺少基于具体实验的验证工作㊂下一步需要结合实际工况来优化二维圆管稳态导热反演模型,并进一步开发二维圆管瞬态导热反演模型㊂参考文献:[1] ZHANG F L,YUAN Z H.The detection and evaluationfor the internal defection in industrial pipeline based on the virtual heat source temperature field[J].Journal ofThermal Analysis and Calorimetry,2019,137(3):949-964.[2] FAN C L,SUN F R,YANG L.A new computationalscheme on quantitative inner pipe boundary identification based on the estimation of effective thermal conductivity [J].Journal of Physics D:Applied Physics,2008,41(20):205501.[3] 张林,杨立,范春利.充分发展湍流管道内壁边界的红外定量识别[J].国防科技大学学报,2019,41(5):185-192.ZHANG L,YANG L,FAN C L.Infrared quantitative identification for inner boundary of fully developed turbu⁃lent pipeline [J].Journal of National University of De⁃fense Technology,2019,41(5):185-192.(in Chi⁃nese)[4] 范春利.几何形状导热反问题方法与应用[M].北京:科学出版社,2015.FAN C L.Geometric inverse heat conduction problems:methods and applications [M].Beijing:Science Press,2015.(in Chinese)[5] 熊平,陆祺,卢涛,等.基于顺序函数法的圆管内部流体温度反演[J].原子能科学技术,2020,54(9):1595-1603.XIONG P,LU Q,LU T,et al.Estimating fluid tempera⁃ture of pipe based on sequential function specification method [J ].Atomic Energy Science and Technology,2020,54(9):1595-1603.(in Chinese)[6] 韩雯雯,卢涛.基于共轭梯度法的圆管内部流体温度识别[J].工程热物理学报,2015,36(2):371-375.HAN W W,LU T.Estimating fluid temperature of pipe by using conjugate gradient method[J].Journal of Engi⁃neering Thermophysics,2015,36(2):371-375.(inChinese)㊃301㊃第1期 张经豪等:基于导热反问题圆管内壁腐蚀减薄及污垢增厚的识别[7] HUANG C H,CHEN C W.A boundary⁃element⁃basedinverse problem of estimating boundary conditions in anirregular domain with statistical analysis[J].NumericalHeat Transfer,1998,33(2):251-267. [8] 薛齐文,杨海天,胡国俊.共轭梯度法求解瞬态传热组合边界条件多宗量反问题[J].应用基础与工程科学学报,2004,12(2):113-120.XUE Q W,YANG H T,HU G J.Solving inverse heatconduction problems with multi⁃variables of boundary con⁃ditions in transient⁃state via conjugate gradient method[J].Journal of Basic Science and Engineering,2004,12(2):113-120.(in Chinese)[9] 钱炜祺,蔡金狮.顺序函数法求解二维非稳态热传导逆问题[J].空气动力学学报,2002,20(3):274-281.QIAN W Q,CAI J S.Solving two⁃dimensional transientinverse heat conduction problem with sequential functionmethod[J].Acta Aerodynamica Sinica,2002,20(3):274-281.(in Chinese)[10]KIM S K,JUNG B S,KIM H J,et al.Inverse estimationof thermophysical properties for anisotropic composite[J].Experimental Thermal and Fluid Science,2003,27(6):697-704.[11]LEE H L,CHANG W J,CHEN W L,et al.An inverseproblem of estimating the heat source in tapered optical fi⁃bers for scanning near⁃field optical microscopy[J].Ultra⁃microscopy,2007,107(8):656-662. [12]FAZELI H,MIRZAEI M.Shape identification problemson detecting of defects in a solid body using inverse heatconduction approach[J].Journal of Mechanical Scienceand Technology,2012,26(11):3681-3690. [13]FAZELI H,MIRZAEI M,FOROOGHI P.Estimation oflocation and size of defects in a solid body via inverseheat conduction problem[C]∥Proceedings of the14thInternational Heat Transfer Conference.Washington DC,2010:387-396.[14]SIAVASHI M,KOWSARY F,ABBASI⁃SHAVAZI E.Detection of flaws in a two⁃dimensional body throughmeasurement of surface temperatures and use of conjugategradient method[J].Computational Mechanics,2010,46(4):597-607.[15]KOWSARY F,SIAVASHI M.Prediction of internal flawparameters in a two⁃dimensional body using steady⁃statesurface temperature data and IHCP methods[C]∥SecondUKSIM European Symposium on Computer Modeling andSimulation.Liverpool,2008:341-346. [16]CHEN W L,YANG Y C,LEE H L,et al.Inverse esti⁃mation for unknown fouling geometry on inner wall offorced⁃convection pipe[J].Applied Mathematics andMechanics(English Edition),2011,32(1):55-68.[17]CHEN W L,YANG Y C.Inverse estimation for the un⁃known frost geometry on the external wall of a forced⁃con⁃vection pipe[J].Energy Conversion and Management,2009,50(6):1457-1464.[18]CHEN W L,YANG Y C,LEE H L,et al.Estimation forinner surface geometry of a two⁃layer⁃wall furnace with in⁃ner wall made of functionally graded materials[J].Inter⁃national Communications in Heat and Mass Transfer,2018,97:143-150.[19]WANG S H,LIN S C,YANG Y C.Geometry estimationfor the inner surface in a furnace wall made of functionallygraded materials[J].International Communications inHeat and Mass Transfer,2015,67:1-7. [20]苟小龙,张建涛,王广军.基于导热反问题的管道内部缺陷诊断[J].重庆大学学报,2010,33(2):42-46.GOU X L,ZHANG J T,WANG G J.Defects detectionin the inner surface of pipes based on inverse heat con⁃duction problem[J].Journal of Chongqing University,2010,33(2):42-46.(in Chinese) [21]范春利,孙丰瑞,杨立.基于红外测温的圆管内壁不规则边界的识别算法研究[J].热科学与技术,2006,5(2):112-117.FAN C L,SUN F R,YANG L.Algorithm study on iden⁃tification of pipeline’s irregular inner boundary for infraredthermography[J].Journal of Thermal Science and Tech⁃nology,2006,5(2):112-117.(in Chinese) [22]张林,范春利,孙丰瑞,等.基于APDL的管道内壁边界识别算法[J].红外与激光工程,2015,44(5):1477-1484.ZHANG L,FAN C L,SUN F R,et al.Identification al⁃gorithm of pipelines’inner boundary based on APDL[J].Infrared and Laser Engineering,2015,44(5):1477-1484.(in Chinese)[23]CHENG C H,CHANG M H.Shape identification by in⁃verse heat transfer method[J].Journal of Heat Transfer,2003,125(2):224-231.[24]HUANG C H,TSAI C C.A transient inverse two⁃dimen⁃sional geometry problem in estimating time⁃dependent ir⁃regular boundary configurations[J].International Journalof Heat and Mass Transfer,1998,41(12):1707-1718.[25]张林,杨立,寇蔚,等.基于一维加权法的交界面边界形状识别[J].红外技术,2018,40(6):590-597.㊃401㊃北京化工大学学报(自然科学版) 2022年ZHANG L,YANG L,KOU W,et al.Inverse identifica⁃tion of interface geometry in a multiple region domain based on one⁃dimensional weighting method[J].Infrared Technology,2018,40(6):590-597.(in Chinese)[26]MOHASSEB S,MORADI M,SOKHANSEFAT T,et al.A novel approach to solve inverse heat conduction prob⁃lems:coupling scaled boundary finite element method to a hybrid optimization algorithm [J].Engineering Analysis with Boundary Elements,2017,84:206-212.[27]LIU F B.A hybrid method for the inverse heat transfer ofestimating fluid thermal conductivity and heat capacity[J].International Journal of Thermal Sciences,2011,50(5):718-724.[28]GARCÍA E,MÉRESSE D,POMBO I,et al.Identifica⁃tion of heat partition in grinding related to process param⁃eters,using the inverse heat flux conduction model[J].Applied Thermal Engineering,2014,66(1-2):122-130.[29]XIE T,HE Y L,TONG Z X,et al.An inverse analysisto estimate the endothermic reaction parameters and phys⁃ical properties of aerogel insulating material[J].Applied Thermal Engineering,2015,87:214-224.[30]ZHANG B W,MEI J,ZHANG C Y,et al.A generalmethod for predicting the bank thickness of a smelting fur⁃nace with phase change[J].Applied Thermal Engineer⁃ing,2019,162:114219.Identification of corrosion thinning and fouling thickening on the inner wall of a circular tube based on the inverseheat conduction problemZHANG JingHao XIONG Ping HAO RuiZhi LU Tao *(College of Mechanical and Electrical Engineering,Beijing University of Chemical Technology,Beijing 100029,China)Abstract :Taking a two⁃dimensional circular tube as the research object,a mathematical model of the two⁃dimen⁃sional steady⁃state inverse heat conduction problem was constructed based on the direct heat conduction problem (DHCP)of the finite element method and an optimization method based on the Levenberg -Marquardt (L -M)al⁃gorithm.Through the combination of COMSOL and MATLAB,two types of defects corrosion thinning and fouling thickening on the inner wall of the circular tube were quantitatively identified.In order to explore the validity andaccuracy of the model,several typical defects were employed for numerical calculations.The effects of the initial value selection,the number of temperature measurement points and the temperature measurement error on the outer surface of the pipeline on the accuracy of the inversion results were systematically analyzed.Numerical experiments prove that the model can accurately identify the two types of defects on the inner wall of a circular tube,which has good stability and noise resistance.Key words :inverse heat conduction problems;defect identification;Levenberg -Marquardt(L -M)algorithm(责任编辑:吴万玲)㊃501㊃第1期 张经豪等:基于导热反问题圆管内壁腐蚀减薄及污垢增厚的识别。
螺旋椭圆扭曲管强化换热研究

12Cr1MoVG钢弯管热处理工艺对其组织性能影响_杨佳

摘 要 :某 机 组 12Cr1MoVG 钢 弯 管 后 硬 度 偏 低 ,分 析 认 为 是 弯 管 热 处 理 工 艺 不 当 所 致 ,提 出 了 加 快 正 火 冷 却 速
度、 延长回火保温时间的热处理工艺改善方法。 通过理化检验,得到材料硬度与金相组织结构、材料力学性能之间的
关系。
关键词:12Cr1MoVG 钢; 弯管; 热处理; 金相组织; 力学性能
YANG Jia1, ZHANG Yijie2, CHEN Zhongbing1, LAI Yunting1
(1. Suzhou Nuclear Power Research Institute Co., Ltd., Suzhou 215004, China; 2. Shenhua Sanhe Power Generation Co., Ltd., Sanhe 065201, China)
3 检验
3.1 金相检验 对第一批次 4 根弯管外弧侧部位进行金相组织
检验, 发现其金相组织成铁素体+少量珠光体组织 结构,形貌如图 5 所示。
检验得到的该金相组织成分, 间接证明了该批
182
《热加工工艺》 2013 年 9 月 第 42 卷 第 18 期
20 μm 图 5 第一批次弯管热处理后外弧侧金相组织 Fig.5 External arc microstructure of the first batch
20 μm 图 6 第二批次弯管热处理后外弧侧金相组织 Fig.6 External arc microstructure of the second batch
bended pipe after heat treatment
3.2 力学性能 自第一批次与第二批次弯管产品中选取试验
()螺旋扁管强化传热技术研究进展

3上海市重点学科建设项目资助(B503)收稿日期:2010-01-11杨 胜(1983- ),博士生;200237上海市徐汇区。
螺旋扁管强化传热技术研究进展3杨 胜1 张 颂2 张 莉1 徐 宏1(11华东理工大学机械与动力工程学院化学工程联合国家重点实验室,21北京迪威尔石油天然气技术开发有限公司)摘 要 介绍了新型强化传热元件螺旋扁管及其换热设备的结构特点与强化传热机理。
对无相变及相变工况下螺旋扁管传热特性的理论、实验及数值模拟研究进行了综述与讨论,介绍了螺旋扁管换热设备的应用状况。
在此基础上,指出螺旋扁管传热技术尚待开展的工作包括丰富传热介质种类、管内外流场可视化及加强相变传热特性研究。
关键词 螺旋扁管 异型管 强化传热 节能Rev i ew on enhanced hea t tran sfer technology of sp i ra l fl a t tubeYang Sheng 1 Zhang Song 2 Zhang L i 1 Xu Hong1(11East China University of Science and Technol ogy,21Beijing DW ELL Petr oleum and Gas Technol ogy Devel opment Company L td .)Abstract The structural features and enhancing heat transfer mechanis m of the tube were p resented .The theoretical,experi m ental and nu merical si m ulati on researches on the heat transfer characteristics of the tube under phase -change and no phase -change conditi ons were reviewed and discussed .The ap 2p licati on status of s p iral flat tube heat -exchange equi pments was p resented .The future works includ 2ed widening the heat transfer mediu m types,fl ow visualizati on inside and outside the tube and intensive research on the phase -change heat transfer characteristics .Keywords s p iral flat tube s pecial tube enhanced heat transfer energy conservati on 自20世纪70年代初石油危机爆发以来,以能源为中心的环境、生态和社会经济问题日益加剧。
核电奥氏体不锈钢传热弯管工艺评定及典型事件分析

( 1 )按照MC1 3 6 2 的要 求进行沸 腾Mg C 1 2 试 验 ,确 定弯管部位耐应 力 腐蚀的能 力。合格标准为试验后 无裂
纹 产 生 ;如 果 试 验 证 明有 必 要 进 行 消
应 力 热 处 理 ,则 由制 造 厂 制 定热 处 理
工 艺 条件 。
( 2 )取5 根弯管试样 对消应热 处
然而 ,经 验 表 明 ,国 内部 分 制 造厂 刘RC C—M
二、工艺评定
在进行批量生产弯管前 ,应选取预 制直管或者 成 品直管进行试验评定 ,验证所采用的弯管工艺能
够 满 足 规 定 的尺 寸 公 差要 求 ,同时 不 会 对材 料 造 成
影 响,并验证弯管段是否需要进行消应力热处理。 具体工艺评定过程如下 :
由 于 这 些 热 交 换 器 设 备 已 经 制 造 完 成 , 无 法
验证u形传热管的性能是否满足标准及技术条件要
求 ,最 终 不 得 不报 废 所 有设 备 。这次 事 件 的代 价 是 沉 重的 。 因此 ,为 了弄 清R CC—M ( 2 0 0 0 +2 0 0 2 :  ̄ b
间部 位 。 ③ 消 应 力 热 处 理 后 ,应 按 照
图 2
MC 1 3 3 0 的要求对 弯管进行金相试验检查 ( 1 0 0 倍 放大 ),合格标 准为 :与未经消应力热处理试样 的
相 同 部位 的 晶粒 相 比 ,热处 理 后 的 晶粒 尺 寸 变化 不 大 ;或者 最 大 晶粒 的 尺 寸小 于 前 者 ,晶粒 数 至少 等 于 同一 区域 的平 均值 ,这样 的 晶粒长 大 可 以接 受 。
一
点测量尺寸 ,尺寸公差须满足要求 ;弯管机必须
基于修正DEMATEL_的同桥并行管道风险评价
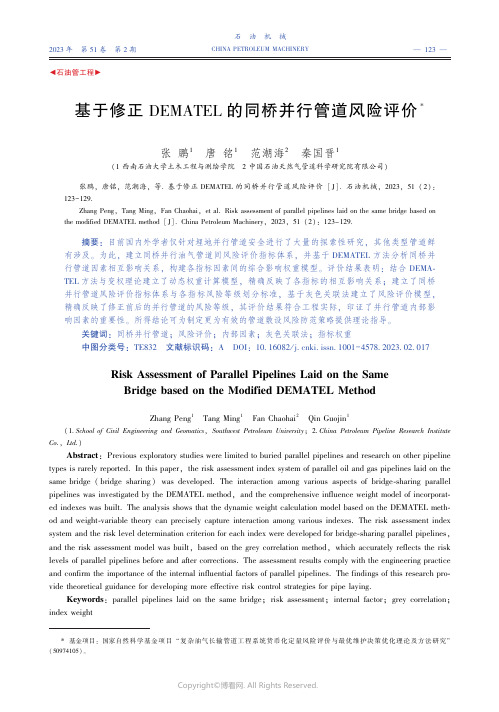
Risk Assessment of Parallel Pipelines Laid on the Same
Bridge based on the Modified DEMATEL Method
Zhang Peng 1 Tang Ming 1 Fan Chaohai 2 Qin Guojin 1
系ꎬ 导致 评 价 结 果 不 准 确ꎬ 进 而 导 致 决 策化 语 言 ( 没 有ꎬ 较 小ꎬ 一 般ꎬ 较 大ꎬ
非常大) 度量各指标之间的关系ꎬ 通过专家确定
æ a 11
ç
ç⋮
M = ç a i1
ç
ç⋮
ç
è a m1
a 1j
a ij
a mj
⋮
⋮
a 1n ö
od and weight ̄variable theory can precisely capture interaction among various indexes. The risk assessment index
system and the risk level determination criterion for each index were developed for bridge ̄sharing parallel pipelinesꎬ
间关系ꎬ 被广泛运用于复杂系统中各因素的重要性
因素的作用ꎬ 其值越大ꎬ 影响作用越强烈ꎻ 原因度
鉴于上述研究ꎬ 笔者结合资料分析、 现场调研
值越小ꎬ 被影响作用越强烈ꎮ 相关计算公式为:
Mi = di + Gi
(3)
分析 [8] ꎮ
等方式ꎬ 建立同桥并行油气管道间风险评价指标体
一起110_kV变压器套管发热缺陷分析及处理

湖 南 电 力
第 42 卷第 1 期
HUNAN ELECTRIC POWER
2022 年 02 月
doi:10 3969 / j issn 1008 ̄ 0198 2022 01 020
一起 110 kV 变压器套管发热缺陷分析及处理
庄先涛ꎬ 郝为ꎬ 种俊龙
( 国网四川省电力公司遂宁供电公司ꎬ 四川 遂宁 629000)
摘 要: 通过红外测温发现一起 110 kV 变压器套管将军帽发热故障ꎬ 介绍故障检查处
理过程ꎬ 并分析故障原因ꎮ 分析结果表明斜圈弹簧缺失是导致本次故障的直接原因ꎬ 整
改后变压器运行效果良好ꎮ 最后ꎬ 针对此类故障的分析与处理提出建议ꎮ
关键词: 变压器套管ꎻ 红外测温ꎻ 发热缺陷ꎻ 故障分析
中图分类号: TM406
( State Grid Suining Power Supply Companyꎬ Suining 629000ꎬ China)
Abstract: In this paperꎬ a heating fault of 110 kV transformer bushing is found through infrared temperature measurement. The
CO 2
1 575 91
1 603 26
616 34
C 2 H4
480 97
481 46
0 46
C 2 H6
C 2 H2
总烃
图 1 2 号主变套管红外图谱
2 试验情况
2018 年 3 月 2018 年 3 月
2017 年 11 月 2018 年 3 月
初测
复测
124 87
CH4
- 1、下载文档前请自行甄别文档内容的完整性,平台不提供额外的编辑、内容补充、找答案等附加服务。
- 2、"仅部分预览"的文档,不可在线预览部分如存在完整性等问题,可反馈申请退款(可完整预览的文档不适用该条件!)。
- 3、如文档侵犯您的权益,请联系客服反馈,我们会尽快为您处理(人工客服工作时间:9:00-18:30)。
图 2 z=0mm 处角度选取示意图和点选取示意图 Fig2 Angel selected and point selected schematic diagram at z=0mm
防涡器如图 3 所示,高 80mm,直径 44mm。防涡器嵌于分支管道的垂直管道内, 其上表面距主管道上表面 180mm。
t T
Prt x j
(9)
Ti Ti Tb T(10)其中 T TH TL , TH 表示主管道的热流体温度, TL 表示分支管道的冷流体温度, Ti 表示 T 型弯管内某一点的流体温度。 定义无量纲温差为:
Ti Tmax Tmin Tmax 为某点最高无量纲温度, Tmin 为某点最低无量纲温度。
2.2 数学模型
本文研究使用的大涡模拟(LES)控制方程包括质量方程、动量守恒方程和能量 方程。 质量守恒方程为:
ui 0 t xi
动量守恒方程为:
(1)
ui ui u j 0 T T0 g t x j xi 2 Sij ij x j
Investigations of thermal fluctuation and its weaken mechanism in an elbow pipe
LU Tao, ZHAI Hao
(College of Mechanical and Electrical Engineering, Beijing University of Chemical Technology, Beijing 100029, China) (Telephone: 13522099779, E-mail: likesurge@)
3
图 3 防涡器的物理模型 Fig3 Physical model of vortex breaker
设置流体为水,主管道热流体流速为 6m/s,热流体温度为 388.15K,分支管道冷 流体流速为 0m/s,冷流体温度为 288.15K。分别对有防涡器的 T 型弯管(算例 1)和 无防涡器的 T 型弯管(算例 2)进行模拟。
高等学校工程热物理第十九届全国学术会议
编号:B-13001
弯管内热波动及其削弱机理研究
卢涛,翟浩
(北京化工大学 机电工程学院,北京 100029) (联系电话:13522099779,E-mail:likesurge@)
摘要:运用 FLUENT 软件,对有无防涡器条件下 T 型弯管内冷热流体的温度波动过程进行了大涡模 拟,获得了弯管处无量纲温度波动曲线图。数值模拟结果表明,加入防涡器后,防涡器下方弯管处 温度波动减弱,热波动受到抑制。 关键词:弯管,热波动,削弱,大涡模拟
30 45
0
有 无 有 无 有 无
F
30 45
0
有 无 有 无 有 无
G
30 45
0
有 无 有 无 有 无
I
30 45
有 无 有 无
7
0.998 0.996 0.994 0.992 0.990 0.988 0.986 0.984 0.982 0.980 0.978 0 5 10 15 t/s 20 25 30 H F G I
Tmax Tmin
0
0.01358 0.03032 0.00642 0.02374 0.01422 0.03174 0.01278 0.0306 0.00638 0.02448 0.01516 0.03822 0.00076 0.00084 0.00046 0.00352 0.0015 0.01708 0.00004 0.00004 0.00006 0.00012 0.00008 0.0003
(a)
(b)
图 4 大涡模拟运算 30s 后 z=0mm 处温度云图:(a)有防涡器,(b)无防涡器 Fig4 Temperature distribution after computing 30s by large eddy simulation at z=0mm: (a) with vortex breaker, (b) without vortex breaker
Abstract: The temperature fluctuation of cold and hot fluids is simulated by large eddy simulation on FLUENT platform, with considers whether it contains vortex breaker, which acquires the dimensionless temperature fluctuation graph of an elbow pipe. The numerical results show that, temperature fluctuation of elbow-pipe below the vortex breaker is declined with consideration of vortex breaker, thermal fluctuation is suppressed. Key words: elbow pipe, thermal fluctuation, weaken, large eddy simulation
2
2 数学模型
2.1 物理模型
物理模型如图 1 所示,主管道长宽高为 200mm× 60mm× 20mm。分支管道内径为 44mm,整个模型壁厚为 5mm。壁面材料采用丙烯酸树脂。
图 1 T 型弯管物理模型 Fig1 Physical model of T-junction
如图 2,在 z=0mm,平面内,采集圆心角为 0° ,30° ,45° 三个位置处的数据。每 个位置处分别取 9 个点:A,B,C,D,E,F,G,H,I。其中 A 点位于管道中心处, D、H 两点距 A 点 18mm,B、F 两点距 A 点 20mm,C、G 两点距 A 点 24mm,E、 I 两点距 A 点 26mm。
(11)
5
物理模型网格数为 198 万,模拟时,先用 RSM 模型模拟至稳态收敛,然后用大 涡模拟进行非稳态模拟,进行大涡模拟时时间步长设为 5ms,模拟 30s。模拟时考虑 浮升力的影响和流固相壁面耦合。
3 模拟结果及分析
运用 FLUENT 求解器进行计算,将为算例 1 和算例 2 的模拟结果进行比较。 图 4 是算例 1 和算例 2 大涡模拟运算 30s 后 z=0mm 处温度云图。从图中可以看 出相比算例 2 算例 1 的温度分层主要发生在分支管道直管处,算例 1 中温度分层线较 算例 2 温度分层线平缓。算例 1 弯管处温度范围小于算例 2 弯管处,表明在加入防涡 器后,弯管内热波动得到了抑制。
式中,应变张量 S ij 为:
(2)
S ij
1 ui u j 2 x x j i
(3)
亚格子(SGS)雷诺应力可定义为:
ij ui u j ui u j
(4)
4
一般,SGS 模型广泛的使用涡-粘度模型:
ij
kk ij 2 t S ij
1
1 引言
T 型管道广泛应用于能源动力装置以及各种过程化工装置的管路系统中,当两种 不同温度的流体在其中混合时,便会发生热波动现象。当管壁附近的流体产生热波动 时, 管壁处会产生随机的热应力, 可导致管道穿透裂纹, 甚至造成管道的热疲劳失效, 酿成事故。近几十年来核电站由热疲劳而引发的管道失效或泄漏之类的事故,已经引 起了广泛的重视。 自从发生核电厂管道热疲劳失效事故以来,管道热疲劳问题引起了核电工作者和 研究人员的重视。国内外许多学者,通过模拟和实验的方法,对 T 型管道内的流体混 合进行了大量的研究。Simoneau 等[1]运用大涡模拟计算了核电厂 T 型管道中的湍流, 研究了 T 型管道中流体的温度波动,并从平均温度、温度波动幅度和频率与相应的实 验结果进行了对比,研究表明大涡模拟能够较准确地捕捉湍流信息。Lee 等[2]运用大 涡模拟的方法模拟了 T 型管道内的冷热流混合过程,获得了温度波动,研究发现冷热 流体温差和由于湍流混合强化了传热系数是影响 T 型管道热疲劳失效的主要因素。 王 海军等[3, 4]通过可视化实验的方法对不同射流与主流流速比下 T 型三通管中横向射流 国家自然科学基金资助(No,51276009) 的流动与传热进行了实验研究,得到了流动的基本特性以及不同流速比下局部点的温 度波动特性。郭志军等[5]对三通管内的冷热流体混合进行了大涡模拟,得出在主管下 游主管和支管交汇中心的区域内温度和速度波动情况。Hu 和 Kazimi[6]应用大涡模拟 对 T 型管道内两种不同形式的流体混合产生的热波动进行了研究, 获得的无量纲温度 波动与实验结果符合较好。 与 T 型管混合不同的是,在一端关闭的分支管道中,当分支管道充满冷流体,热 流体在主管道流动时,会产生一种叫空泡流的热流体,空泡流从主管道渗入到分支管 道,使分支管道中产生热边界层,从而对管道造成损害。本文采用防涡器来应对空泡 流,防涡器可以抑制空泡流的渗入,从而降低分支管道内的热波动。 由于大涡模拟应用广泛,捕捉的信息较为准确。因此本文拟采用大涡模拟方法, 对 T 型弯管内冷热流体传热进行数据模拟。
6
表 1 图 5―图 7 无量纲温度极值及无量纲温差 位置 有无防涡器 有 无 H 极大值 Tmax 0.9939 0.9936 0.9827 0.93968 0.97654 0.9135 0.99326 0.99394 0.98326 0.94336 0.97726 0.9167 0.99572 0.98492 0.97738 0.92212 0.96364 0.89844 0.99618 0.98478 0.977 0.919 0.96198 0.88434 极小值 Tmin 0.98032 0.96328 0.97628 0.91594 0.96232 0.88176 0.98048 0.96334 0.97688 0.91888 0.9621 0.87848 0.99496 0.98408 0.97692 0.9186 0.96214 0.88136 0.99614 0.98474 0.97694 0.91888 0.9619 0.88404 温差 T