ZnCl2/TMAC离子液体中电镀锌的研究
溶剂萃取法从镀锌酸洗废液中分离锌_铁的研究

¹
基金项目: 广州市环境保护局资助项目 ( II 99- 05) 收稿日期: 2003 -04 -07 第一作者 男 副教授
48
矿 冶
工
程
第 23 卷
分离铁、 锌的效果较好, 笔者在前期的工作中比较了三 烷基胺 N235 ( R3N) 与季胺盐 N263 ( R3 CH 3NCl) 对锌的萃 取效果 , 发现在低 pH 值的条件下 , N235 对锌的萃取效 果并不理想, 而 N263 对锌的萃取率较高
[ 5]
N263 在磺化煤油中的溶解度不大 , 需加入部分 TBP 作助溶剂以促 进溶解。根据实验经验 , N263 与 TBP 的 配比为 4B1 时 ( 体积比 ) 时即可保证 N263 全部溶解, 但 当磺化煤油中 N263 的浓度超过 40% 以后 , 有机相即不 稳定, 当其与水相接触一段时间 , N 263 从磺化煤油中析 出, 并在油水两中之间形成新的相。因此, 实验中萃取 剂浓度最高取为 30% ( 体积比) 。 实验结果表明: 当萃 取剂浓度为 23% ~ 24% 时, 铁锌分离系数达到最高点 , 在此之后分离系 数下降。 这是因为萃取剂浓度增加到一定程度后 , 过剩的萃取 容量势必将部分铁也萃取进入有机相, 导致分离系数 下降。经检测, 进入有机相的总铁中以三价铁离子居 多, 表明在实验条件下 , 溶液中三价铁离子过多 , 会影 响锌铁的分离效率。 3. 2 Cl- 离子对锌、 铁分离的影响 笔者前期的研究结果表明: 在低 pH 值的条件下, 加入一定的 Cl- , 有 助于锌萃 取率的提 高, 这 是因为 Zn2+ 与 Cl- 形成的络阴离子 ZnCl4 2- , 更容易被 N263 萃 取, 考虑到此因素, 在实验中考察了 Cl- 对锌铁分离的 影响。 Cl 加入量按与水溶液中金属离子的摩尔比 4B1 加入 , 在有 Cl- 参与的情况下, 锌铁的分离系数随萃取 剂浓度的改变而发生较大幅度的变化。在萃取剂浓度 低于 13% 时 , 分离系数的变化比较平缓 ; 而当萃取剂 浓度在 13% ~ 19% 时 , 锌铁分离系数随萃取剂浓度的 增大而急剧增大 ; 当萃取剂浓度超过 21% 以后, 锌铁 分离系数急剧下降。对于上述现象 , 笔者认为BCl- 对
快速电镀锌的方法

快速电镀锌的方法 (2008-09-13 16:40:07)标签:镀件电镀锌电镀液溶液分类:问题讨论常用的镀锌电镀液为弱酸性,与溶液中的[Zn2+]相比,[H+]仍然较大,在镀件表面存在着氢与锌的共析现象。
氢气的生成妨碍锌原子的紧密排列,影响着锌的电沉积速度,因此镀层易成为蓬松的海绵状。
另外,课堂演示要等待15分钟方可见到结果,不利于组织教学。
笔者曾多次试改镀液的配方,效果好的是以Na2ZnO2为主的碱性电镀液,用4.5V的电池组,不附加电阻,镀件单侧面不小于5cm2,以控制电流密度。
通电10秒钟,镀件上出现明显的银白色镀层;30秒时取出镀件,表面为浅灰色,用软布擦拭,即成为光亮的银白色。
溶液稳定,反应迅速,现象明显,重复性好,这些特点能满足课上演示实验和学生实验的要求。
镀液的配制在大烧杯中放入浓的ZnCl2溶液(潮解形成的亦可)20m1,在不断搅拌的情况下缓慢加入浓度为15%的NaoH溶液。
当大量的白色沉淀Zn(OH)2生成以后,继续缓慢(最后改为滴加)加入浓碱液,不断搅拌,使沉淀物大部分溶解,生成Na2ZnO2。
当所剩沉淀不多时,停止加入碱液,以沉淀物的存在显示碱不过量,这是配液的关键,因为在强碱溶液中锌不能稳定存在。
待烧杯中的溶液静置以后,倾取上层清液,即为镀锌电镀液,测其pH值为13;槽镀、刷镀均可,用毕装瓶,胶塞封存,隔年可再用。
因[H+]降到很小,排除了氢的共析因素,锌原子在镀件表面的排列快而不乱。
硫锌-30硫酸盐镀锌光亮剂以硫锌-30为光亮剂的新型线材电镀工艺,保留了原有工艺中主盐成份基本不变,舍去了“阿拉伯胶、桃胶、硫脲”等成份,改善提高了溶液的阴极极化能力分散能力,提高了镀层的致密度,镀液稳定,工作范围宽,提高了线材的光亮度。
一、推荐配方硫酸锌: 250 ~ 400 克/升硼酸:30 ~ 40 克/升硫锌-30: 14 ~ 18 毫升/升P H值: 3 ~ 5.5电流密度: 4 ~ 10 安培/分米 2温度:10 ~ 70 ℃阴极电流效率大于95%二、注意事项1、配槽时硼酸一定要用沸水溶解,其它盐用50℃温水溶解后混合、冷却,去除沉渣后,再加入计量的光量剂,新配槽以上限为宜。
低共熔溶剂在电沉积金属及其合金方面的研究进展
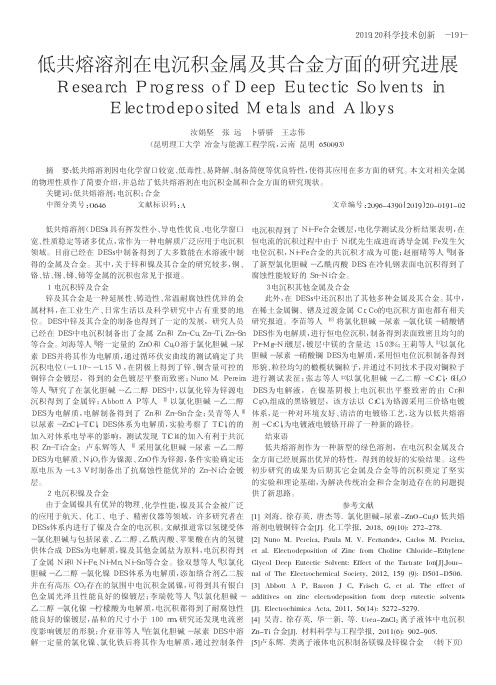
2019.20科学技术创新低共熔溶剂在电沉积金属及其合金方面的研究进展ResearchProgressofDeepEutecticSolventsinElectrodepositedMetalsandAlloys汝娟坚张远卜骄骄王志伟(昆明理工大学冶金与能源工程学院,云南昆明650093)低共熔溶剂(DESs)具有挥发性小、导电性优良、电化学窗口宽、性质稳定等诸多优点,常作为一种电解质广泛应用于电沉积领域。
目前已经在DESs中制备得到了大多数能在水溶液中制得的金属及合金。
其中,关于锌和镍及其合金的研究较多,铜、铬、钴、锡、锑、铈等金属的沉积也常见于报道。
1电沉积锌及合金锌及其合金是一种延展性、铸造性、常温耐腐蚀性优异的金属材料,在工业生产、日常生活以及科学研究中占有重要的地位。
DES中锌及其合金的制备也得到了一定的发展,研究人员已经在DES中电沉积制备出了金属Zn和Zn-Cu、Zn-Ti、Zn-Sn等合金。
刘海等人[1]将一定量的ZnO和Cu2O溶于氯化胆碱-尿素DES并将其作为电解质,通过循环伏安曲线的测试确定了共沉积电位(-1.10~-1.15V),在阴极上得到了锌、铜含量可控的铜锌合金镀层,得到的金色镀层平整而致密;NunoM.Pereira等人[2]研究了在氯化胆碱-乙二醇DES中,以氯化锌为锌源电沉积得到了金属锌;AbbottAP等人[3]以氯化胆碱-乙二醇DES为电解质,电解制备得到了Zn和Zn-Sn合金;吴青等人[4]以尿素-ZnCl2-TiCl4DES体系为电解质,实验考察了TiCl4的的加入对体系电导率的影响,测试发现TiCl4的加入有利于共沉积Zn-Ti合金;卢东辉等人[5]采用氯化胆碱-尿素-乙二醇DES为电解质、Ni2O3作为镍源、ZnO作为锌源,条件实验确定还原电压为-1.3V时制备出了抗腐蚀性能优异的Zn-Ni合金镀层。
2电沉积镍及合金由于金属镍具有优异的物理、化学性能,镍及其合金被广泛的应用于航天、化工、电子、精密仪器等领域,许多研究者在DESs体系内进行了镍及合金的电沉积。
ZnCl2-EMIC离子液体中电沉积锌

ZnCl2-EMIC离子液体中电沉积锌马军德;李冰;颜灵光;陈彦【期刊名称】《中国有色金属学报》【年(卷),期】2008(018)006【摘要】采用ZnCl2-EMIC离子液体,用电化学方法对体系在镍电极和钨电极上的反应阴极过程进行研究,分析锌沉积机制,并用直流和脉冲电源进行电沉积实验,研究电流密度、温度和脉冲参数等因素对镀层的影响.结果表明:阴极反应为准可逆反应,锌离子在镍电极和钨电极上形核是三维瞬时形核半球形扩散长大过程,直流电流密度为4mA/cm2,温度为80 ℃时,镀层质量最好;脉冲电沉积得到的镀层要优于直流电沉积得到的镀层,尤其在脉冲宽度为2ms,脉冲间隔为8ms,电流密度为8mA/cm2时,得到的镀层光滑而均匀,颗粒大小接近0.3μm .【总页数】8页(P1135-1142)【作者】马军德;李冰;颜灵光;陈彦【作者单位】华东理工大学,资源与环境工程学院,上海,200237;华东理工大学,资源与环境工程学院,上海,200237;华东理工大学,资源与环境工程学院,上海,200237;华东理工大学,资源与环境工程学院,上海,200237【正文语种】中文【中图分类】TQ153【相关文献】1.ZnCl2/TMAC离子液体中电沉积锌的研究 [J], 翟秀静; 符岩; 张跃宏; 李斌川2.1,3-二甲基-2-咪唑啉酮−ZnCl2溶剂化离子液体的物化性质及在锌电沉积中的应用 [J], 刘爱民;郭梦霞;石忠宁;刘玉宝;刘风国;胡宪伟;杨酉坚;陶文举;王兆文3.1,3-二甲基-2-咪唑啉酮−ZnCl_(2)溶剂化离子液体的物化性质及在锌电沉积中的应用 [J], 刘爱民;郭梦霞;石忠宁;刘玉宝;刘风国;胡宪伟;杨酉坚;陶文举;王兆文4.现场表面增强红外光谱法研究离子液体中锌电沉积过程:水的影响 [J], 于奥秋;周尉5.离子液体[Bmim]BF_4中锌的电沉积研究 [J], 黄红艳;李宁;成旦红;印仁和;周尉因版权原因,仅展示原文概要,查看原文内容请购买。
钕铁硼磁钢离子液体电镀锌的研究试验

钕铁硼磁钢离子液体电镀锌的研究试验摘要:钕铁硼磁体化学活性较高且表面疏松多孔,在日常环境中极易受氧化和腐蚀,在水溶液中进行电镀时容易发生镀层起泡、分层现象。
本文采用尿素-NaBr-KBr-甲酰胺-ZnCl2离子液体作为溶剂在钕铁硼表面电镀锌,包括基体前处理工艺和镀后处理工艺,考察了添加剂、供电方式等对镀层形貌和耐腐蚀性的影响,通过中性盐雾试验、SEM、XRD等对镀层进行测试表征。
结果表明:在适量添加剂存在下采用脉冲电镀电源实施电镀,得到的镀层光亮致密均匀,耐腐性能好。
关键词:钕铁硼、离子液体、电镀锌、添加剂、脉冲电镀1引言钕铁硼磁体因其优异的磁性能被称为“磁中之王”,自80年代问世以来受到人们的广泛关注,应用于通讯、计算机、军事、医疗等领域[1]。
但是由于钕铁硼磁体内活泼钕的存在,导致其耐蚀性较差[2],极大的限制了该磁体的应用。
因此,提高钕铁硼磁体的表面防护技术成为关键问题。
我国钕铁硼磁体的表面防护主要采用电镀锌、电镀镍或活学镀镍[3],传统电镀锌工艺存在镀件易产生氢脆、电流效率低、环境污染严重等问题[4]。
因此如何在获得高质量锌镀层的同时减少对环境的污染成为绿色化学的当务之需。
近年来,离子液体由于其熔点低、溶解性能好、导电率好、电化学窗口宽、性质稳定等优点,逐渐地被广泛应用于电化学的各个方面[5~8]。
离子液体中电镀锌在常温无水情况下进行,可避免析氢而产生的氢脆现象且可使用有机添加剂来提高镀层的质量,是一种应用前景十分广泛的表面防护新技术。
目前,国内外关于离子液体中电镀锌或锌合金的报道已有一些,马军德等[9]研究了ZnCl2-EMIC离子液体中在镍电极和钨电极上锌的电沉积行为;Andrew P. Abbott等[10]报道了在尿素-氯化胆碱离子液体中的电沉积锌锡合金的研究。
综合国内外关于离子液体中电镀锌方面的报道,主要研究的离子液体体系有ZnCl2/EMIC、ZnCl2/TMAC、尿素-氯化胆碱等[9~14],采用的阴极材料主要以惰性电极为主,鲜有关于阴极材料为钕铁硼磁体的报道,所合成离子液体大都成本较高或对空气较敏感,且对添加剂的研究不够完善,得到的镀层效果仍有待提高。
溶液中锌与铁沉积电位的比较
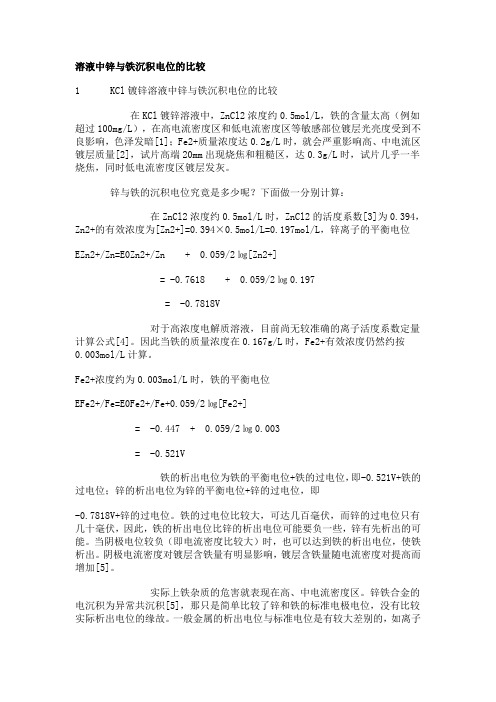
溶液中锌与铁沉积电位的比较1 KCl镀锌溶液中锌与铁沉积电位的比较在KCl镀锌溶液中,ZnCl2浓度约0.5mol/L,铁的含量太高(例如超过100mg/L),在高电流密度区和低电流密度区等敏感部位镀层光亮度受到不良影响,色泽发暗[1];Fe2+质量浓度达0.2g/L时,就会严重影响高、中电流区镀层质量[2],试片高端20mm出现烧焦和粗糙区,达0.3g/L时,试片几乎一半烧焦,同时低电流密度区镀层发灰。
锌与铁的沉积电位究竟是多少呢?下面做一分别计算:在ZnCl2浓度约0.5mol/L时,ZnCl2的活度系数[3]为0.394,Zn2+的有效浓度为[Zn2+]=0.394×0.5mol/L=0.197mol/L,锌离子的平衡电位EZn2+/Zn=E0Zn2+/Zn + 0.059/2㏒[Zn2+]= -0.7618 + 0.059/2㏒0.197= -0.7818V对于高浓度电解质溶液,目前尚无较准确的离子活度系数定量计算公式[4]。
因此当铁的质量浓度在0.167g/L时,Fe2+有效浓度仍然约按0.003mol/L 计算。
Fe2+浓度约为0.003mol/L时,铁的平衡电位EFe2+/Fe=E0Fe2+/Fe+0.059/2㏒[Fe2+]= -0.447 + 0.059/2㏒0.003= -0.521V铁的析出电位为铁的平衡电位+铁的过电位,即-0.521V+铁的过电位;锌的析出电位为锌的平衡电位+锌的过电位,即-0.7818V+锌的过电位。
铁的过电位比较大,可达几百毫伏,而锌的过电位只有几十毫伏,因此,铁的析出电位比锌的析出电位可能要负一些,锌有先析出的可能。
当阴极电位较负(即电流密度比较大)时,也可以达到铁的析出电位,使铁析出。
阴极电流密度对镀层含铁量有明显影响,镀层含铁量随电流密度对提高而增加[5]。
实际上铁杂质的危害就表现在高、中电流密度区。
锌铁合金的电沉积为异常共沉积[5],那只是简单比较了锌和铁的标准电极电位,没有比较实际析出电位的缘故。
二元配合物中电镀锌镍合金的结构与抗腐蚀性

二元配合物中电镀锌镍合金的结构与抗腐蚀性张秀;龙晋明;裴和中;由劲博;黄攀【摘要】为深入了解碱性锌酸盐体系的工艺参数对锌镍合金镀层结构和耐蚀性的影响,在以四乙烯五胺( TEPA)为镍离子主络合剂、三乙醇胺( TEA)为辅助络合剂的碱性镀液中电沉积制备了锌镍合金镀层,利用电子能谱、X射线衍射、极化曲线和电化学阻抗谱等方法表征镀层的组成结构和在氯化钠溶液中的耐腐蚀性.结果表明:镀层含镍原子数分数11.54%~20.12%,为γ-Ni2 Zn11+纯Zn两相结构(低含镍原子数分数时)或单一γ相结构(较高含镍原子数分数时),γ相晶粒在(600)方向上具有不同程度的择优取向性;随着镀液中镍原子数分数的提高,镀层的腐蚀电位正移,阻抗增加,耐蚀性提高;当电流密度为2 A/dm2时,镀层的腐蚀电位和电荷传递电阻最高,耐蚀性最好.%To know how the technological parameters affect the structure and anti⁃corrosion propertyof Zinc⁃nickel alloy plating in alkaline zincate system, the synthesis of the zinc⁃nickel alloy plating is made by the electrochemical deposition method. The alkaline solution is a mixture of Tetraethylenepentamine ( TEPA) and Triethanolamine ( TEA ) , and the prior part is the main complexing agent for nickel ions. The energy dispersive spectrometer ( EDS ) , X⁃ray diffraction ( XRD ) associated with polarization curves and electrochemical impedance spectroscopy ( EIS ) were used to characterize the structure and anti⁃corrosion property respectively. The result shows that the particlesinγ⁃phase preferred (600) orientation with respect to the atom percentage of nickel varies between 11.54% and 20.12%, 11.54% corresponds toaγ⁃Ni2 Zn11 and Zn two⁃phase area and 20.12% corresponds to a singleγ⁃phase. With an increasing atom percentage of nickel in the bath, the corrosion potential of plating becomes more positive, which results in an increasing impedance and a better anti⁃corrosion property. At last, the plating displays its highest corrosion resistance when the current density reaches 2 A/dm2 .【期刊名称】《材料科学与工艺》【年(卷),期】2015(000)001【总页数】6页(P83-88)【关键词】碱性电沉积;锌镍合金;二元络合;结构;腐蚀【作者】张秀;龙晋明;裴和中;由劲博;黄攀【作者单位】昆明理工大学材料科学与工程学院,昆明650093;昆明理工大学材料科学与工程学院,昆明650093;昆明理工大学材料科学与工程学院,昆明650093;昆明理工大学材料科学与工程学院,昆明650093;昆明理工大学材料科学与工程学院,昆明650093【正文语种】中文【中图分类】TG174.441锌镍合金镀层一般指含镍质量分数20%以下的合金镀层.含镍质量分数在10%~15%的锌镍合金镀层的耐蚀性和耐磨性是纯锌镀层的3~6倍,钝化后的合金镀层的耐蚀性是锌镀层钝化后的3~5倍,和镉镀层的性能相近,甚至更好[1-3].碱性电镀锌镍合金的氢脆小,在宽的电流密度下含镍量均匀,镀液对设备的腐蚀小,镀液成本低且废液易处理,而且镀层的机械性能和加工性能(上漆性,焊接性能等)优良[4-5].电镀锌镍合金工艺由 Schoch和Cocks在20世纪初提出,经过数十年的发展,已经发展出酸性、碱性多种电镀体系,镀层的性能也有了很大的提高[6-8].此技术近年来已开始应用于汽车、航空、电子等工业中,用来提高产品的抗腐蚀能力[9].作为一种较新的钢铁和镁合金等材料的表面防护性镀层,锌镍合金镀层受到国内外研究者的关注.虽然在酸性和弱酸性镀液体系中所得锌镍合金镀层的组成结构及性能已有较多研究报道[2,10-12],但对于碱性锌酸盐体系中电镀锌镍合金的研究还不够充分,尤其是该体系中络合剂或配位剂的选择及其影响的研究较少.已有的研究表明,碱性镀液中只有在合适的锌镍比范围内才能得到γ单相锌镍合金.杨房祖等[13]在不同锌镍比的锌酸盐镀液中,以三乙醇胺为络合剂电沉积得到不同结构的锌镍合金;Mülle等[14]选择三乙烯四胺、四乙烯五胺、二乙基三胺等物质作为配位剂,对锌酸盐体系电镀锌镍合金作了初步研究.本文针对碱性锌酸盐镀液体系,采用四乙烯五胺和三乙醇胺(TEA)两种物质组成不同的二元配合物,研究不同电镀条件参数对镀层的组成结构和抗腐蚀性能的影响,以期为工艺优化及应用提供参考.1 实验1.1 电镀工艺实验室用1 cm×1 cm×1 mm的低碳钢片作基体材料,电镀使用高纯镍板作阳极材料,使用试剂均为分析纯试剂,试验用水为去离子水,在室温下电镀.电镀液的主要成分如下:NaOH,质量浓度120 g/L;ZnO,质量浓度12 g/L;NiSO4·7H2O,质量浓度4.61~17.77 g/L(Ni2+/Ni2++Zn2+原子数分数x=10%~30%);镀锌光亮剂(FK-303,福州八达表面工程技术研究所),体积分数3.2 mL/L;糖精钠,质量浓度0.6 g/L;1,4-丁炔二醇,质量浓度0.4 g/L;十二烷基苯磺酸钠,质量浓度0.1g/L;四乙烯五胺,质量浓度15.45 g/L;三乙醇胺,质量浓度4~20 g/L(TEA/Ni2+原子个数比=2).电镀阴阳极的面积比为1∶2,电流密度为1~5 A/dm2,电镀时间40 min.电镀完毕后用水清洗试样并烘干.1.2 腐蚀电化学测试用质量分数3.5%的NaCl水溶液作为腐蚀介质(模拟海水条件),通过测试镀层的极化曲线和交流阻抗谱来考察其耐腐蚀特性.使用CS350型电化学工作站(武汉科思特仪器有限公司)和标准三电极体系进行电化学测试,温度为室温(20±5)℃.以铂电极为辅助电极,饱和甘汞电极(SCE)为参比电极,镀层试片为工作电极.极化曲线测试的电位范围为稳态下开路电位±300 mV,扫描速度0.5 mV/s;交流阻抗测试时,工作电极的电位设定于开路电位,交流信号频率100 000~0.01 Hz,振幅±10 mV.本文所提到的电位均相对于SCE.1.3 镀层分析采用能谱仪(PHOENIX型,美国 EDAX公司)对镀层进行表面成分分析.使用多晶转靶X-射线衍射仪(Model D/max-2200,日本Rigaku公司)测定镀层的相组成和织构,实验条件:Cu靶0.154 2 nm,30 mA,36 kV,扫描速率10(°)/min.镀层的择优取向用(hkl)晶面择优取向密度Jhkl(也称为织构系数)表征,根据 Harris 法[15]可由式(1)计算Jhkl:式中:Ihkl为实测镀层(hkl)晶面的衍射线相对强度;I0hkl为标准图谱中(hkl)的衍射线相对强度;n为计算时所取图谱中的衍射线条数目.若各晶面的择优取向度Jhkl均为1,则表示镀层中的晶粒呈现无序取向;若各晶面的Jhkl不等于1,说明镀层晶粒存在择优取向或织构.当干涉面的Jhkl大于1,表明大多数晶粒的(hkl)晶面与镀面平行,此时该晶面称为择优取向面;若某干涉面的Jhkl等于n时(其余晶面的Jhkl等于0),则表示其为唯一的择优取向面[16].2 结果与讨论2.1 镀液中镍离子含量对镀层的影响2.1.1 耐腐蚀性许多文献指出,改变镀液中金属主盐含量会使镀层的结构组成以及电化学性能发生变化[2,11-13].图1为电沉积电流密度 2 A/dm2、镀液的TEA/Ni2+原子个数比保持为2的条件下,不同镍原子数分数x(Ni2+/Ni2++Zn2+)=10%~30%的镀液中所制备的锌镍合金镀层的极化曲线.由图1可以看到:当镀液中镍离子含量较低(原子数分数x=10%)时,镀层在质量分数3.5%的NaCl水溶液中的腐蚀电位很低,为-1.020 3 V,而腐蚀电流密度较高,阳极活性溶解的电位范围较宽;随着镍离子含量的提高,镀层的腐蚀电位正移,腐蚀电流密度减小,阳极活性溶解的电位范围变窄;当镍离子原子数分数增加到25%时,镀层的腐蚀电位达到最高,腐蚀电流密度最小,阳极活性溶解的电位范围最窄,表明此时镀层的耐蚀性最好.图1 不同镍离子原子数分数镀液制备的锌镍合金镀层在3.5%NaCl溶液中的极化曲线图2为镀层在质量分数3.5%的NaCl溶液中的交流阻抗谱图.采用Zsimpwin阻抗分析软件对阻抗谱进行拟合,得到对应的等效电路见图3,其中Rs为溶液电阻,常相位元件CEPdl为双电层电容,Rt为电荷传递电阻.图2 不同镍离子原子数分数镀液制备的锌镍合金镀层在质量分数3.5%NaCl溶液中的交流阻抗谱图3 锌镍合金镀层在质量分数3.5%NaCl溶液中的交流阻抗谱的等效电路由图2可以看到,随着镀液中镍含量的增加,镀层在腐蚀介质中的容抗弧的直径增加,电荷传递电阻变大.根据镀层在质量分数3.5%NaCl溶液中的极化曲线和交流阻抗谱,得到腐蚀电化学参数,列于表1中.由表1数据可见:当镍离子原子数分数为25%时,镀层在质量分数3.5%NaCl溶液中腐蚀反应的电荷传递电阻最大,为1 683 Ω·cm2,相应的腐蚀电流密度最小,为2.6 μA/cm2;而镍离子原子数分数低于或高于25%时,得到的镀层耐蚀性要稍低一些,但差别并不十分明显,表明对于本实验的锌镍合金镀液体系,其允许的镍离子原子数分数范围较宽,x(Ni2+/Ni2++Zn2+)=15%~30%.在实际电镀生产中,当镀液在较宽的镍离子浓度范围内变化时,对于得到抗腐蚀性能较好的锌镍合金镀层是有利的.表1 不同镍离子原子数分数镀液制备的锌镍合金镀层在3.5%NaCl溶液中的腐蚀电化学参数x(Ni2+/Ni2++Zn2+)/%icorr/(μA·cm-2)Ecorr/V Rt/(Ω·cm2)腐蚀速率/(mm·a-1)10 9.555 8 -1.020 3 219 0.112 4 15 2.878 2 -0.790 6 1 630 0.033 9 20 4.666 9 -0.772 2 1 338 0.054 9 25 2.612 1 -0.702 6 1 683 0.030 7 30 5.882 1 -0.746 3 1 376 0.042 72.1.2 镀层镍含量、相结构与择优取向EDS和XRD分析发现,镀液中镍离子的相对含量对镀层的镍的原子数分数、相结构与择优取向有显著影响.图4为锌镍合金镀层中的镍原子数分数与镀液中的镍离子原子数分数间的关系曲线,其中CRL线表示镀液对应的镍含量.图4 电流密度2 A/dm2时锌镍合金镀层中含镍量与镀液中的镍离子含量间的关系曲线由图4可看出,在x(Ni2+/Ni2++Zn2+)=10%~30%内,随着镀液中镍离子浓度的提高,镀层的含镍量也相应增加;当镍离子原子数分数超过20%后,镀层的镍含量开始显著低于镀液中的镍含量,并且两者的差值随溶液中镍离子浓度的提高而进一步增大,即表明此时锌镍合金异常共沉积的倾向加剧.图5为锌镍合金镀层的XRD谱图,由式(1)计算出的镀层择优取向度列于表2中.对于在x(Ni2+/Ni2++Zn2+)=10%的镀液中得到的镀层,镍原子数分数为11.5%(图4).根据XRD物相分析可知,其由γ-Ni2Zn11和纯Zn两相组成,镀层的择优取向性不明显.图5 在不同镍离子原子数分数镀液中电沉积(ic=2 A/dm2)制备的锌镍合金镀层的X射线衍射谱图表2 在不同镍离子含量镀液中电沉积(ic=2 A/dm2)制备的锌镍合金镀层的择优取向度x(Ni2+/Ni2++Zn2+)/%(330)择优取向度(600)择优取向度(721)择优取向度10 0.182 52 0.236 84 0.164 78 15 0.076 68 9.757 65 0.196 27 20 0.063 9411.104 7 0.144 61 25 0.018 12 10.945 3 0.068 12 30 0.020 62 9.784 65 0.066 82当镀液中镍原子数分数超过15%后,镀层中的纯Zn相已经不存在,成为单相(γ-Ni2Zn11)结构,这种γ相结构的镀层表现出明显的(600)晶面择优取向性(见表2).结合图5和表2可以看出,随着锌镍合金镀层含镍量的变化,镀层的相结构也有所变化.在x(Ni2+/Ni2++Zn2+)=10%的镀液中得到的镀层含有纯锌相,所以镀层的腐蚀电位接近锌在质量分数3.5%的NaCl溶液中的腐蚀电位(约为-1 100 mV),而且γ相在(600)方向上的生长受到强烈地抑制;随着镀层中镍含量的增加,γ相的生长方式也发生了变化:(222)方向上基本上没有生长,(330)和(721)方向的生长受到进一步抑制,衍射峰的强度减弱.尤其是当镍原子数分数达到20%后,γ相沿(721)方向的生长变得非常弱,导致该衍射峰消失.在x(Ni2+/Ni2++Zn2+)=15%~30%的镀液中得到的镀层均具有γ单相(γ-Ni2Zn11)结构,且其结晶晶粒均呈现(600)面择优生长.金属电沉积一般需要经过基体外延生长、无序取向、择优取向3个状态[16].由于镀液中金属离子的浓度、络合物的稳定性以及电沉积电流密度等工艺条件的影响,不同晶面的生长速度不同,使电结晶形成的多晶体镀层出现择优取向.通过对照锌镍二元合金相图[17]可知,在镍原子数分数为16.81%~19.40%时,锌镍合金的平衡相组成应为单一的γ相(镍含量可在一定范围内变化),而此处(镀液x(Ni2+/Ni2++Zn2+)=15%~30%)所得的同样含镍量范围的锌镍合金镀层,也具有γ单相结构,因此可认为本实验条件下得到的锌镍合金镀层的相组成,与相图反映的热力学相平衡状态基本上是接近的.通过上述分析可知,镀液中镍含量的变化将引起镀层中镍含量、相组成结构和结晶生长方式发生变化,从而导致合金镀层在腐蚀介质中的抗腐蚀性能发生变化.2.2 电沉积电流密度对镀层的影响2.2.1 耐腐蚀性图6和图7分别为镍原子数分数x(Ni2+/Ni2++Zn2+)=15%的镀液中,以不同电沉积电流密度制备的锌镍合金镀层的极化曲线和电化学阻抗谱,主要的腐蚀电化学参数列于表3中.图6 以不同电沉积电流密度制备的锌镍合金镀层在3.5%NaCl溶液中的极化曲线图7 以不同电沉积电流密度制备的锌镍合金镀层在3.5%NaCl溶液中的交流阻抗谱由图6可以看到:除电流密度为1 A/dm2外,其他试样的极化曲线在阴极极化区都出现电流平台,表明反应过程受到扩散控制[18];在阳极极化区的末端出现钝化现象,且随着电流增大钝化区的维钝电流增加.由图7可以看到,电流密度为1 A/dm2时得到镀层的阻抗最小(496 Ω·cm2),而当电流密度提高到2 A/dm2时镀层的阻抗最大(1 630 Ω·cm2).值得注意的是,当进一步增大电流密度时,镀层的阻抗反而减小.观察发现,在电镀过程中提高电流密度会加剧氢气的析出,同时使镀层镍含量增加[19],结晶择优取向改变.显然,镀层耐腐蚀性的变化与此有密切联系.在电流密度为2 A/dm2时,得到的镀层相对其他电流密度下得到的镀层具有更强的抗腐蚀性能,这与其具有最大的(600)择优取向度有关(见2.2.2节讨论).表3 以不同电沉积电流密度(ic)制备的锌镍合金镀层的腐蚀电化学参数ic/(A·dm-2)icorr/(μA·cm-2)Ecorr/V Rt/(Ω·cm2)腐蚀速率/(mm·a-1)1 10.604 0 -1.001 5496 0.124 7 2 2.878 2 -0.790 6 1 630 0.033 9 3 1.014 8 -0.817 3 1 094 0.094 7 4 6.969 6 -0.838 6 1 231 0.082 0 5 9.010 3 -0.869 9 914 0.106 02.2.2 镀层镍含量、相结构与择优取向在合金电镀中,电沉积电流密度对合金成分的影响非常明显,电流密度提高使得阴极极化过电位增大,这有利于合金中电位较负金属的含量增加[20].图8为镀液中 x(Ni2+/Ni2++Zn2+)=15%时锌镍合金镀层中的镍原子数分数与电沉积电流密度间的关系曲线,其中CRL线表示镀液对应的镍原子数分数.由图8可以看到,随着电流密度的增加,镀层中镍的原子数分数由15.23%增加到16.93%,超过镀液中x(Ni2+/Ni2++Zn2+),这说明增加电沉积电流密度可以促进被络合剂(TEPA、TEA)络合、电位变负的镍离子的沉积,抑制锌镍金属离子异常共沉积.图8 镀液中x(Ni2+/Ni2++Zn2+)=15%时锌镍合金镀层中的镍含量与电沉积电流密度间的关系曲线在图9和表4中可以看到:增加电沉积电流密度会使组成镀层相的生长方式发生改变,出现不同的择优取向;当电流密度由1 A/dm2增大到2 A/dm2时,(600)衍射峰强度变得最大,即具有最显著的(600)择优取向;当电流密度大于2 A/dm2后,镀层的(600)峰强度开始急剧下降,(600)择优取向度变小,说明当电流密度超过一定值(2 A/dm2)时,晶粒在(600)方向上的生长开始受到强烈地抑制;同样,增加电流密度使合金γ相在(721)方向上生长有一定择优取向,择优取向度随电流密度的增加而变大,衍射峰的强度有一定的增强.图9 镀液中x(Ni2+/Ni2++Zn2+)=15%时不同电沉积电流密度下制备的锌镍合金镀层的X射线衍射谱图表4 镀液中x(Ni2+/Ni2++Zn2+)=15%时不同电沉积电流密度下制备的锌镍合金镀层的择优取向度电流密度/(A·dm-2)(330)择优取向度(600)择优取向度(721)择优取向度1 0.059 32 5.007 18 0.110 97 2 0.075 53 9.611 33 0.191 80 3 0.07853 2.771 78 0.148 25 4 0.213 83 0.824 59 0.204 71 5 0.258 55 0.495 650.244 66比较表3和表4中数据可发现:(600)晶面的择优取向对镀层的抗腐蚀性能有很大的影响;在2 A/dm2时(600)晶面择优取向度最大(9.611 33),镀层的抗腐蚀性能相应也最强;随着电流密度的增加,镀层(600)晶面的择优取向度减小,镀层的抗腐蚀性能也相应降低.3 结论1)在以四乙烯五胺(TEPA)和三乙醇胺(TEA)为络合剂的碱性镀液中,镍离子的相对浓度和电沉积电流密度对锌镍合金镀层的成分、相结构、结晶取向和耐腐蚀性具有显著影响.2)在电流密度为2 A/dm2时,随着镀液中镍离子含量的增加,镀层中镍含量相应增加.当镍离子原子数分数超过10%后,镀层的相组成由γ+Zn两相变为γ单相.γ相晶粒在(330)、(721)方向上的生长受到抑制,在(600)方向的生长得到促进,使得其在氯化钠溶液中的抗腐蚀能力增强.3)镀液中镍原子数分数为15%时,随着电沉积电流密度的增加,镀层中镍含量增加,镀层在(330)、(721)方向的择优取向度增加.电流密度由1 A/dm2提高到2 A/dm2时,镀层γ相具有最大的(600)择优取向度,同时显示出最优的耐腐蚀性能.4)锌镍合金镀层的耐腐蚀性除了与镍含量有关外,在很大程度上还与镀层γ相晶粒的择优取向度有关.参考文献:[1] HAMMAMI O,DHOUIBI L,TRIKI E.Influence of Zn-Ni alloy electrodeposition techniques on the coating corrosion behaviour in chloride solution[J].Surface and Coatings Technology,2009,203(19):2863-2870.[2] BYK T V,GAEVSKAYA T V,TSYBULSKAYA L S.Effect of electrodeposition conditions on the composition,microstructure,and corrosion resistance of Zn-Ni alloy coatings[J].Surface and Coatings Technology,2008,202(24):5817-5823.[3] WYKPIS K,POPCZYK M,BUDNIOK A.Electrolytic deposition and corrosion resistance of Zn-Ni coatings obtained from sulphate-chloride bath[J].Bulletin of Materials Science,2011,34(4):997-1001.[4]曹浪,左正忠,田志斌,等.电镀锌镍合金的研究现状与展望[J].材料保护,2010,43(4):33-37.CAO Lang,ZUO Zhengzhong,TIAN Zhibin,et al.Research status and prospect of Zn-Ni alloy electroplating[J].Materials Protection,2010,43(4):33-37.[5]黄攀,裴和中,张国亮,等.碱性锌镍合金电镀的研究现状及展望[J].热加工工艺,2012,41(2):161-164.HUANG Pan,PEI Hezhong,ZHANG Guoliang,et al.Study on reality and prospect of alkaline zinc nickel alloy electroplating [J].Hot Working Technology,2012,41(2):161-164. [6] MOSAVAT S H,SHARIAT M H,BAHROLOLOOM M E.Study of corrosion performance of electrodeposited nanocrystalline Zn-Ni alloy coatings[J].Corrosion Science,2012,59:81-87.[7] WYKPIS K,POPCZYK M,NIEDBAŁA J,et al.Influence ofthermaltreatmenton the corrosion resistance of electrolytic Zn-Ni coatings[J].Materials Science-Poland,2011,29(3):177-183.[8] YOGESHA S,HEGDE A C.Optimization of bright zinc-nickel alloy bath for better corrosion resistance[J].Transactions of the IndianInstitute of Metals,2010,63(6):841-846.[9]田伟,吴向清,谢发勤.Zn-Ni合金电镀的研究进展[J].材料保护,2004,37(4):26-29.TIAN Wei,WU Xiangqing,XIE Faqin.Research and development of zinc-nickel alloy electroplating [J].Materials Protection,2004,37(4):26-29.[10] QIAO Xiaoping,LI Helin,ZHAO Wenzhen,et al.Effects of deposition temperature on electrodeposition of zinc-nickel alloy coatings [J].Electrochimica Acta,2013,89:771-777.[11] RAVINDRAN V,MURALIDHARAN V S.Characterization of zinc-nickel alloy electrodeposits obtained from sulphamate bath containing substituted aldehydes[J].Bulletin of Materials Science,2006,29(3):293-301.[12] De OLIVEIRA E M,CARLOS I A.Study of the effect of mannitol on ZnNi alloy electrodeposition from acid baths and on the morphology,composition,and structure of the deposit[J].Journal of Applied Electrochemistry,2009,39(10):1849-1856.[13]杨房祖,许书楷,周绍民.锌镍合金镀层的组成与相结构的关系[J].厦门大学学报:自然科学版,1994,33(1):63-67.YANG Fangzu,XU Shukai,ZHOU Shaomin.Relationship between the composition and phase structure of the Zn-Ni alloy deposits[J].Journal of Xiamen University(Natural Science),1994,33(1):63-67.[14]MÜLLE C,SARRET plexing agents for a Zn-Ni alkaline bath [J].Journal of Electroanalytical Chemistry,2002,519(1/2):85-92.[15]王英华.X光衍射技术基础[M].北京:原子能出版社,1993:230-262.[16]周绍民.金属电沉积——原理与研究方法[M].上海:上海科学技术出版社,1987,437.[17]长崎诚三,平林真,刘安生.二元合金状态图集[M].北京:冶金工业出版社,2004:240.[18] DESLOUIS C,TRIBOLLER B,MENGOLI G.Electrochemical behaviorof copper in mentral aerated chloride solutionⅠ:steady-state investigation [J].Journal of Applied Electrochemistry,1988,18(3):374-383.[19]鹿文珊,徐天凤,陈宇,等.碱性电镀锌镍合金的研究[J].中国腐蚀与防护学报,2012,32(6):443-448.LU Wenshan,XU Tianfeng,CHEN Yu,et al.Zincnickel alloy electroplating in an alkaline bath [J].Journal of Chinese Society for Corrosion and Protection,2012,32(6):443-448. [20]屠振密.电镀合金原理与工艺[M].北京:国防工业出版社,1993:207-213.。
氯化钾镀锌溶液的分析

氯化钾镀锌溶液的分析规程一、氯化锌的测定1、仪器:1ml移液管2只,250锥形瓶3只,10ml量筒1个,酸式滴定管1支(附台、夹)。
2、原理:在pH=10的溶液中,锌与EDTA形成稳定的络和物,以铬黑T作指示剂。
Zn2++H2Y2-=ZnY2-+2H+HZn2-+Zn2+=ZnIn2-+2H+3、试剂:①pH=10的缓冲溶液;②铬黑T指示剂;③0.05M EDTA标准溶液。
4、分析方法:用移液管吸取镀液1ml于250ml锥形瓶中,加水50ml,pH=10的缓冲溶液10ml,铬黑T少许(绿豆粒大小),用0.05M EDTA标准溶液滴定至溶液由紫红色变为淡兰色为终点。
平行测定三次。
5、计算:ZnCl2(g/L)=C×V×136.3式中,C——标准EDTA溶液的当量浓度;V——消耗标准EDTA的毫升数。
二、氯化钾的测定:1、仪器:1ml移液管2只,250锥形瓶3只,10ml量筒1个,酸式滴定管1支(附台、夹)。
2、原理:AgNO3与氯离子定量的生成白色氯化银沉淀,以铬酸钾指示剂,在中性溶液中过量的Ag+与CrO42-生成砖红色沉淀以示终点。
Cl-+Ag+=AgCl↓(白色)2Ag++CrO42-=Ag2CrO4↓(砖红色)3、试剂:①20%K2CrO4溶液;②0.1N的AgNO3标准溶液。
4、分析方法:用移液管吸取镀液1ml于250ml锥形瓶中,加水50ml,20% K2CrO4溶液3~4滴,用0.1N的AgNO3滴定至溶液由黄色浑浊略红色为终点。
平行测定三次。
5、计算:KCl(g/L)=(C×V-W/68)×74.6式中,C——AgNO3标准溶液的当量浓度;V——耗用标准AgNO3溶液的毫升数;W——ZnCl2的含量(g/L)。
三、硼酸的测定:1、仪器:1ml移液管2只,250锥形瓶3只,100量筒1个,酸式滴定管1支(附台、夹)。
2、原理:硼酸虽是多元酸,但酸性极弱,不能直接用碱滴定。
- 1、下载文档前请自行甄别文档内容的完整性,平台不提供额外的编辑、内容补充、找答案等附加服务。
- 2、"仅部分预览"的文档,不可在线预览部分如存在完整性等问题,可反馈申请退款(可完整预览的文档不适用该条件!)。
- 3、如文档侵犯您的权益,请联系客服反馈,我们会尽快为您处理(人工客服工作时间:9:00-18:30)。
电镀锌 是一 个 量 大 面广 的镀 种 , 占总镀 种 的 它 6 以上口 。 目前主 要 采用 酸性 体 系镀 锌 , O ] 此技 术 存在 部件产 生氢 脆 、 电流 效率 低 、 水 处 理 、 作 温 废 工
溶剂 , 研究 了锌 在铜 电极上 的沉 积过程 , 考察 电解 液
浓 度 、 度 对 镀 层 的影 响 。 温
・ 2・ 1
有色金 属 ( 冶炼 部分 ) 2 1 0 0年 4期
Z C 2TMAC离 子液 体 中 电镀锌 的研 究 n1 /
张跃 宏 , 秀静 , 亚 琼 , 翟 李 冯乃 祥
( 北大 学材料 与冶金 学 院 , 阳 1 0 0 ) 东 沈 1 0 4
摘 要 : 究 了 Z C。 T 研 n I MAC离 子 液 体 体 系 在 铜 电极 上 的 阴极 沉积 过程 , 量 了体 系 的 电 导 率 , 察 了 电 / 测 考 解 质 浓 度 、 度 等 工艺 条 件对 镀 层 的影 响 。结 果 表 明 , 极 过 程 为 准 可 逆 过 程 ; 系 电 导 率 随 温 度 升 高 温 阴 体 而 升 高 #5 电 压 2 O 电 沉 积 时 间 3 i, 得 到 致 密 镀 层 , 粒 大 小 接 近 3/ 电 流 效 率 达 3 8K, .4V, 0r n 可 a 颗 z m,
离 子液体用 于 电沉积 金属及 合金 方 面已有很 多
研 究[ , 5 ] 目前 用 于 电镀 锌 主 要 采 用 Z C E C n t MI /
水氯 化锌 。电解 液 配 置 在氩 气 气 氛 手套 箱 内进 行 , Z C。 TMAC 的 摩 尔 比为 7:3 溶 剂 P 分 析 n 1与 , C(
度高 等问题 [ 。如何在 获得高 质量 镀层 的同 时消 除 2 ] 电解 液对环 境 的危害 已成 为绿色 电化学 和环 保工业
亟待解 决 的问题 , 离子 液 体 使 之成 为 可 能 。离 子液 体具有 : 电化 学窗 口宽 、 电性 好 、 导 黏度 比较大 、 扩散 速率慢 等特点I 。 s 叫]
ZHANG eh n ZHAIXi-ig, — i FENG i in Yu - o g, uj n LIYa qu, Na— a g x
( h o fM ae il Sc o lo tras& M ealr y,No t a tr ie st tl g u rhe sen Un v riy,S e y n 1 0 4,Chn ) h n ag1 0 0 ia
Ab ta t Th lcr d 0 iin o icwa n e t a e n Te rm eh lmmo im h o ie ( sr c ; eee to 印 st fzn si v si td i ta t ya o g nu c lrd TM AC)c n o—
t i e t n 2 Tt m n h a t r u h a h o c n a n d wi Z CI. h e e e t ia n u t t f e ee t o y es s e a d t e f c o ss c s t e c n e — c v t
9 %。 0
关 键 词 : 子 液 体 ; 镀 ; ; 环 伏 安 离 电 锌 循
中 圈 分 类 号 : Q13 1 T 5. 5 文 献标 识 码 : A 文 章 编 号 :0 7 74 (0 0 0 — 0 1 一O 10 — 5 52 1 )4 O 2 4
R sa c n E e to lt go icfo Z C 2 T e e r h o lcr p ai fZ n r m n I/ MAC I ncL q i n o i iud
1 实验
由 于无水 氯 化 锌具 有 很 强 的吸水 性 , 空气 中 在
极 易水 解 , 市售 分 析纯 无 水 氯 化 锌大 多 是 Z C z n l 和
Z( n OH) I C 的混 合 物 。本 实 验 采 用 干燥 氯 化 锌 于 4 3K 脱水 , 在 10 3K 升 华 得 到 了 高纯 度 的 无 2 再 7
p r t r f 3 8 K ,t ec a i g wa o a t n h u r n f iin y wa 0 d p stn o 0 r i . Th e au eo 5 h o t sc mp c d t ec r e te f e c s9 n a c e o ii g f r 3 n a e
W ih t e t het mpe a ur nc e sn r t ei r a i g,t o uc i t nc e s d W h n t e lv la e wa . 4 V tt e t m— hec nd tviy i r a e . e he c l o t g s 2 0 a h e
ta in o lcr lt n e p r t r r t de . Th e u t n p o e s o ic wa u s r v ri l. r t fee to y ea d tm e au e we e su id o e r d ci r c s fzn s q a i e e sb e o —
s eo r sa sn a l “ i fc y t lwa e ry 3 m. z
Ke wo d : o i i u d; l c rcp a i g Z n ; ci o t mm e r y r s I n c l i E e t i l t ; i c Cy l v la q n c ty