铸件缺陷修补方法
铸件常见缺陷和处理
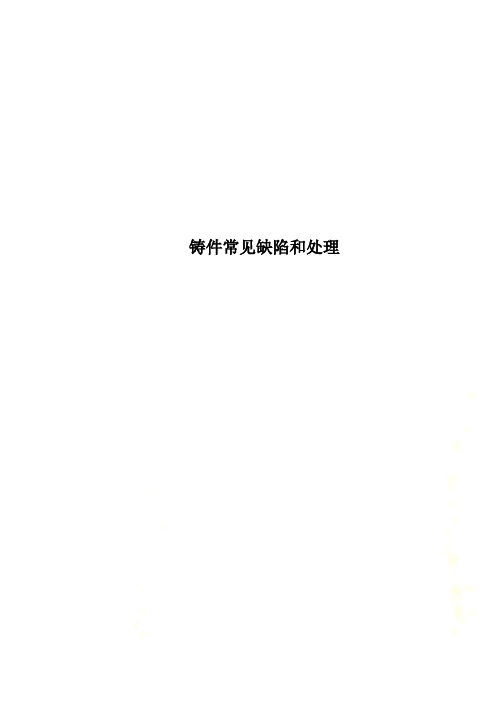
铸件常见缺陷和处理铸件常见缺陷、修补及检验一、常见缺陷1.缺陷的分类铸件常见缺陷分为孔眼、裂纹、表面缺陷、形状及尺寸和重量不合格、成份及组织和性能不合格五大类。
(注:主要介绍铸钢件容易造成裂纹的缺陷)1.1孔眼类缺陷孔眼类缺陷包括气孔、缩孔、缩松、渣眼、砂眼、铁豆。
1.1.1气孔:别名气眼,气泡、由气体原因造成的孔洞。
铸件气孔的特征是:一般是园形或不规则的孔眼,孔眼内表面光滑,颜色为白色或带一层旧暗色。
(如照片)气孔照片1产生的原因是:来源于气体,炉料潮湿或绣蚀、表面不干净、炉气中水蒸气等气体、炉体及浇包等修后未烘干、型腔内的气体、浇注系统不当,浇铸时卷入气体、铸型或泥芯透气性差等。
1.1.2缩孔缩孔别名缩眼,由收缩造成的孔洞。
缩孔的特征是:形状不规则,孔内粗糙不平、晶粒粗大。
产生的原因是:金属在液体及凝固期间产生收缩引起的,主要有以下几点:铸件结构设计不合理,浇铸系统不适当,冷铁的大小、数量、位置不符实际、铁水化学成份不符合要求,如含磷过高等。
浇注温度过高浇注速度过快等。
1.1.3缩松缩松别名疏松、针孔蜂窝、由收缩耐造成的小而多的孔洞。
缩松的特征是:微小而不连贯的孔,晶粒粗大、各晶粒间存在明显的网状孔眼,水压试验时渗水。
(如照片2)缩松照片2产生的原因同以上缩孔。
1.1.4渣眼渣眼别名夹渣、包渣、脏眼、铁水温度不高、浇注挡渣不当造成。
渣眼的特征是:孔眼形状不规则,不光滑、里面全部或局部充塞着渣。
(如照片3)渣眼照片3产生的原因是:铁水纯净度差、除渣不净、浇注时挡渣不好,浇注系统挡渣作用差、浇注时浇口未充满或断流。
1.1.5砂眼砂眼是夹着砂子的砂眼。
砂眼的特征是:孔眼不规则,孔眼内充塞着型砂或芯砂。
产生的原因是:合箱时型砂损坏脱落,型腔内的散砂或砂块未清除干净、型砂紧实度差、浇注时冲坏型芯、浇注系统设计不当、型芯表面涂料不好等。
1.1.6铁豆铁豆是夹着铁珠的孔眼、别名铁珠、豆眼、铁豆砂眼等。
铁豆的特征是:孔眼比较规则、孔眼内包含着金属小珠、常发生在铸铁件上。
常见压铸件缺陷解决方法
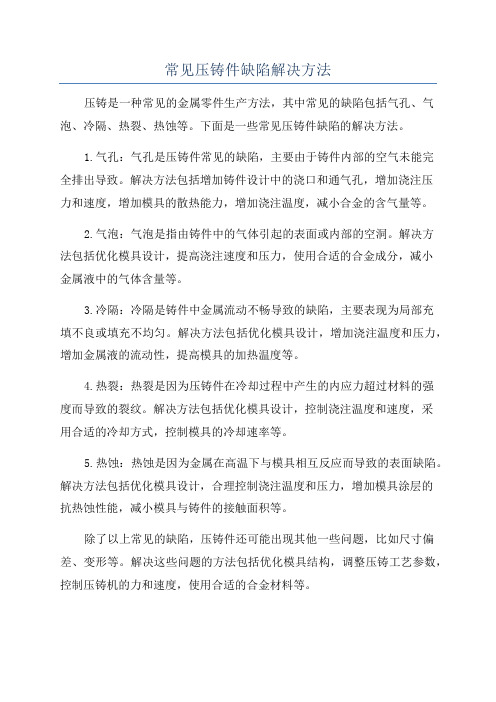
常见压铸件缺陷解决方法
压铸是一种常见的金属零件生产方法,其中常见的缺陷包括气孔、气泡、冷隔、热裂、热蚀等。
下面是一些常见压铸件缺陷的解决方法。
1.气孔:气孔是压铸件常见的缺陷,主要由于铸件内部的空气未能完
全排出导致。
解决方法包括增加铸件设计中的浇口和通气孔,增加浇注压
力和速度,增加模具的散热能力,增加浇注温度,减小合金的含气量等。
2.气泡:气泡是指由铸件中的气体引起的表面或内部的空洞。
解决方
法包括优化模具设计,提高浇注速度和压力,使用合适的合金成分,减小
金属液中的气体含量等。
3.冷隔:冷隔是铸件中金属流动不畅导致的缺陷,主要表现为局部充
填不良或填充不均匀。
解决方法包括优化模具设计,增加浇注温度和压力,增加金属液的流动性,提高模具的加热温度等。
4.热裂:热裂是因为压铸件在冷却过程中产生的内应力超过材料的强
度而导致的裂纹。
解决方法包括优化模具设计,控制浇注温度和速度,采
用合适的冷却方式,控制模具的冷却速率等。
5.热蚀:热蚀是因为金属在高温下与模具相互反应而导致的表面缺陷。
解决方法包括优化模具设计,合理控制浇注温度和压力,增加模具涂层的
抗热蚀性能,减小模具与铸件的接触面积等。
除了以上常见的缺陷,压铸件还可能出现其他一些问题,比如尺寸偏差、变形等。
解决这些问题的方法包括优化模具结构,调整压铸工艺参数,控制压铸机的力和速度,使用合适的合金材料等。
总的来说,解决压铸件缺陷的方法需要综合考虑材料、模具设计、工艺参数等多个因素,通过不断的实验和改进来提高铸件的质量。
压铸件常见缺陷及解决办法

压铸件常见缺陷及解决办法
1、尖角缺陷:表现为在压铸件的边缘和表面出现尖利的角,其
原因是模具的固定不牢,模具合模前没有铂精加光等操作,模具和表
面间的空隙较大,导致铸件连续流和溅射的金属物料的冷凝无法完全
填充到模具内。
解决办法是在压铸件的模具制作中要注意模具的固定,还要在合模前进行铂精加光,使模具缝隙尽量控制在最小。
2、翘曲缺陷:表现为铸件胚体过大或模具设计不当,导致部分
孔表面被填充的金属物料过度凝固后发生变形。
解决办法是提高铸件
的成型质量,在模具设计时应注意做到模具中高低正常,同时要增加
相应的引流装置,降低铸件表面在压铸过程中的温度,减少物料凝固
时间。
3、凹槽缺陷:表现为压铸件内壁或内孔出现浅深不均、粗糙凹槽,一般出现在内壁与模穴孔面间,其原因是模具合模时并未完全排
除空气,另外铸件内孔口位、形喉与内壁模穴间距过大,空气中的熔
融物料的细沙子难以充分清除也会导致此缺陷的产生。
解决办法是采
取真空压铸成型,即采用真空室和真空阀将空气真空,以消除空气;
另外应改变合模方式和模具设计,减少内孔口位与形喉与内壁模穴间距。
常见压铸件缺陷及解决方法
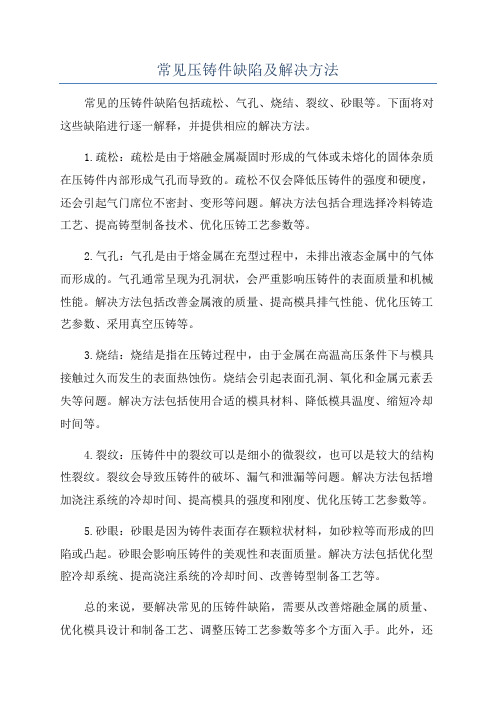
常见压铸件缺陷及解决方法常见的压铸件缺陷包括疏松、气孔、烧结、裂纹、砂眼等。
下面将对这些缺陷进行逐一解释,并提供相应的解决方法。
1.疏松:疏松是由于熔融金属凝固时形成的气体或未熔化的固体杂质在压铸件内部形成气孔而导致的。
疏松不仅会降低压铸件的强度和硬度,还会引起气门席位不密封、变形等问题。
解决方法包括合理选择冷料铸造工艺、提高铸型制备技术、优化压铸工艺参数等。
2.气孔:气孔是由于熔金属在充型过程中,未排出液态金属中的气体而形成的。
气孔通常呈现为孔洞状,会严重影响压铸件的表面质量和机械性能。
解决方法包括改善金属液的质量、提高模具排气性能、优化压铸工艺参数、采用真空压铸等。
3.烧结:烧结是指在压铸过程中,由于金属在高温高压条件下与模具接触过久而发生的表面热蚀伤。
烧结会引起表面孔洞、氧化和金属元素丢失等问题。
解决方法包括使用合适的模具材料、降低模具温度、缩短冷却时间等。
4.裂纹:压铸件中的裂纹可以是细小的微裂纹,也可以是较大的结构性裂纹。
裂纹会导致压铸件的破坏、漏气和泄漏等问题。
解决方法包括增加浇注系统的冷却时间、提高模具的强度和刚度、优化压铸工艺参数等。
5.砂眼:砂眼是因为铸件表面存在颗粒状材料,如砂粒等而形成的凹陷或凸起。
砂眼会影响压铸件的美观性和表面质量。
解决方法包括优化型腔冷却系统、提高浇注系统的冷却时间、改善铸型制备工艺等。
总的来说,要解决常见的压铸件缺陷,需要从改善熔融金属的质量、优化模具设计和制备工艺、调整压铸工艺参数等多个方面入手。
此外,还需要采用适当的检测手段,如金相分析、X射线检测、超声波检测等,对压铸件进行质量检验,及时排除可能存在的缺陷。
几种常见铸钢件缺陷的补焊方法和经验
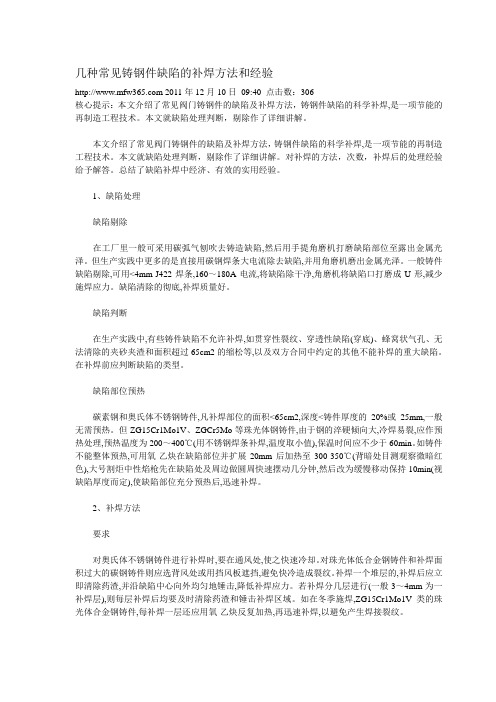
对于阀门铸件的“重缺陷”和“重要补焊”,ASTMA217A217M-2007标准中规定,如铸件生产符合S4(磁粉检查)补充要求的规定,补焊要采用检查铸件同一质量标准的磁粉检验来检查。如铸件生产符合S5(射线照相检查)补充要求的规定,对于水压试验渗漏的铸件、或准备补焊的任何凹坑深度超过壁厚的20%或1in1(25mm)的铸件以及准备补焊的任何凹坑面积约大于10in2(65cm2)的铸件的补焊,都要采用检查铸件同一标准的射线检验进行检查。JB/T5263-2005标准中规定,重缺陷补焊后应进行射线或超声检测。即对于重缺陷和重要补焊,必须要进行有效的无损检查,证明合格后方能使用。
1、缺陷处理
缺陷剔除
在工厂里一般可采用碳弧气刨吹去铸造缺陷,然后用手提角磨机打磨缺陷部位至露出金属光泽。但生产实践中更多的是直接用碳钢焊条大电流除去缺陷,并用角磨机磨出金属光泽。一般铸件缺陷剔除,可用<4mm-J422焊条,160~180A电流,将缺陷除干净,角磨机将缺陷口打磨成U形,减少施焊应力。缺陷清除的彻底,补焊质量好。
消除应力
精加工后发现的缺陷补焊后,已无法做整体消除应力回火处理,一般可采用缺陷部位氧-乙炔火焰局部加热回火方法。采用大号割炬中性火焰来回缓慢摆动,将铸件加热到表面出现目视可见暗红色(约740℃),保温(2min/mm,但不少于30min)。消除应力处理后应立即在缺陷处盖上石棉板。珠光体钢阀门通径上的缺陷,补焊时还应在通径内腔填塞石棉板,使之缓冷。此种操作,既简便又经济,但要求焊工有一定实践经验。
焊条处理
补焊前,应首先检查焊条是否预热,一般焊条应经150~250℃烘干1h。预热后的焊条应置保温箱中,做到随用随取。焊条反复预热3次,若焊条表面药皮有脱落、开裂和生锈,应不予使用。
铸造中常见缺陷及其处理方法
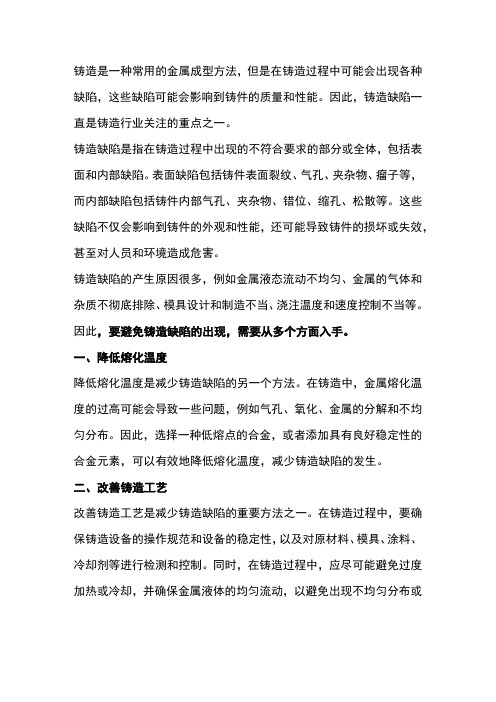
铸造是一种常用的金属成型方法,但是在铸造过程中可能会出现各种缺陷,这些缺陷可能会影响到铸件的质量和性能。
因此,铸造缺陷一直是铸造行业关注的重点之一。
铸造缺陷是指在铸造过程中出现的不符合要求的部分或全体,包括表面和内部缺陷。
表面缺陷包括铸件表面裂纹、气孔、夹杂物、瘤子等,而内部缺陷包括铸件内部气孔、夹杂物、错位、缩孔、松散等。
这些缺陷不仅会影响到铸件的外观和性能,还可能导致铸件的损坏或失效,甚至对人员和环境造成危害。
铸造缺陷的产生原因很多,例如金属液态流动不均匀、金属的气体和杂质不彻底排除、模具设计和制造不当、浇注温度和速度控制不当等。
因此,要避免铸造缺陷的出现,需要从多个方面入手。
一、降低熔化温度降低熔化温度是减少铸造缺陷的另一个方法。
在铸造中,金属熔化温度的过高可能会导致一些问题,例如气孔、氧化、金属的分解和不均匀分布。
因此,选择一种低熔点的合金,或者添加具有良好稳定性的合金元素,可以有效地降低熔化温度,减少铸造缺陷的发生。
二、改善铸造工艺改善铸造工艺是减少铸造缺陷的重要方法之一。
在铸造过程中,要确保铸造设备的操作规范和设备的稳定性,以及对原材料、模具、涂料、冷却剂等进行检测和控制。
同时,在铸造过程中,应尽可能避免过度加热或冷却,并确保金属液体的均匀流动,以避免出现不均匀分布或过热的情况,从而减少铸造缺陷的发生。
三、质量检测和控制质量检测和控制是减少铸造缺陷的关键步骤之一。
在铸造完成后,应对铸件进行全面的检测和控制包括X射线检测、超声波检测、金相分析、硬度测试等。
通过这些检测和控制方法,可以及时发现铸造缺陷,及时采取措施进行修复或重新铸造,从而保证铸件的质量和稳定性。
四、培养专业人才铸造行业的专业人才对于减少铸造缺陷的重要性不言而喻。
铸造行业需要拥有一批专业的技术人员和工人,他们能够理解和掌握铸造技术的各个方面,并能够在实践中灵活应对各种情况。
因此,铸造企业应该加强人才培养和引进工作,提高行业整体素质,从而减少铸造缺陷的发生。
常见压铸件缺陷解决方法

常见压铸件缺陷解决方法压铸件是一种常用的金属制造工艺,常见的缺陷包括炸漏、气孔、缩松、错型、夹杂物等。
针对这些常见的压铸件缺陷,可以采取以下解决方法。
首先,针对炸漏问题,可以从以下几个方面解决。
首先,可以对铸件结构进行优化设计,通过增加或调整料斗口以及压铸型腔等措施,避免或减少高温金属液体和气体的直接接触,从而减少炸漏的发生。
其次,可以通过提高压铸参数,如提高注射速度、提高注射压力等,增强金属流动性,减少气体残留。
此外,还可以采用适当的工艺措施,如喷水降温、选用耐火材料等,减少温度梯度造成的热应力,减少炸漏的发生。
其次,针对气孔问题,可以从以下几个方面解决。
首先,可以通过优化喷嘴造型和增加压铸过程中的温度控制来改善金属的流动性,从而减少气体的残留。
其次,可以通过改变浇注方式和提高压铸参数来改变金属的流动路径,减少气孔的形成。
另外,要注意压铸型腔的排气问题,通过合理设置和调整排气装置来排除气孔。
再次,针对缩松问题,可以从以下几个方面解决。
首先,可以通过优化铸件结构设计,减少厚度梯度,避免出现过薄或过厚的部位,从而减少缩松的产生。
其次,可以通过增加冷却时间和降低冷却速度,使金属更充分地凝固和压实,减少缩松的发生。
此外,还可以通过合理控制铸造温度和压铸参数,调整金属流动性,减少缩松的形成。
此外,针对错型问题,可以从以下几个方面解决。
首先,可以通过优化压铸工艺参数,如增加注射速度、增加压力等,使金属流动性更好,减少错型的发生。
其次,可以通过改变喷嘴和模具的设计,减少或避免金属漏流,避免错型的产生。
另外,还可以通过改善铸型材料和涂料的性能,提高涂覆性能和附着力,减少错型的发生。
最后,针对夹杂物问题,可以从以下几个方面解决。
首先,可以通过加强金属的净化处理,如增加过滤装置、净化金属液、控制铸件质量等,减少夹杂物的产生。
其次,可以通过加强压铸模具的清洁和维护,防止杂质进入,减少夹杂物的形成。
另外,还可以通过优化施工工艺,增加金属流动路径,减少流动阻力,减少夹杂物的带入。
压铸件常见缺陷及改善对策(1)

压铸件常见缺陷及改善对策(1)压铸件常见缺陷及改善对策压铸件是汽车、电器、机械等行业生产的重要部件,具有成本低、成型形状复杂、尺寸精度高等优点,但在生产过程中,常出现一些缺陷,影响产品的质量和性能。
本文将介绍压铸件常见缺陷及改善对策。
一、缺陷分类(一)表面缺陷1.气孔:表面或内部存在大小不一的圆形或椭圆形小孔。
2.夹渣:表面或内部存在小颗粒或纤维杂质。
3.闪亮:表面出现暗角或光亮,且材料表面的形状失真。
(二)内部缺陷1.开裂:铸件内部存在一定大小、方向和数量的开裂,导致铸件强度下降。
2.气孔:铸件内部存在大小不一、分布不均匀的空隙,导致铸件强度下降。
3.缩松:铸件灌注过程中未完全充实、冷却时出现局部收缩,导致铸件强度下降。
二、改善对策(一)工厂加工环境1.密闭铸造室:确保铸造工艺的真空、氩气气氛、风机循环扇等工作环境的洁净度和稳定性。
2.温度控制:在铸件铸造、冷却、急冷和退火等多个环节,控制温度变化。
3.砂芯制作环境和温度:砂芯质量直接影响铸件内部缺陷情况,制作时要确保环境稳定、温度协调。
(二)工艺改善1.铸造压力:适当增加铸造压力可降低铸造缺陷的比例。
2.浇注速度:适当调整铸造流速,避免在铸造过程中产生气泡。
3.铸造温度:根据铸造材料的特性,调整铸造温度。
4.铸模制作:铸模是决定铸件质量的关键,铸模制作过程需加强工艺控制和质量监管。
结论压铸件是一种重要的制造工艺,其质量直接影响到产品的性能和寿命。
本文简要介绍了压铸件常见缺陷分类及改善对策,提供一定的参考与借鉴。
工厂要加强工艺改进,在生产过程中增加检测措施,提高生产过程中的整体质量控制水平。
- 1、下载文档前请自行甄别文档内容的完整性,平台不提供额外的编辑、内容补充、找答案等附加服务。
- 2、"仅部分预览"的文档,不可在线预览部分如存在完整性等问题,可反馈申请退款(可完整预览的文档不适用该条件!)。
- 3、如文档侵犯您的权益,请联系客服反馈,我们会尽快为您处理(人工客服工作时间:9:00-18:30)。
发动机砂眼、气孔缺陷修补方法
适用范围:本方法仅针对已装上整机的机体、油底壳,缸盖等零件,适用于发动机检修或维修服务人员使用,对新装车零件未经许可
编制: 审核: 批准:
1、多肉类缺陷:飞翅和毛刺、抬型、胀砂、冲砂、掉砂、外渗物;
2、孔洞类缺陷:气孔、针孔、缩孔、缩松、疏松;
3、裂纹、冷隔类缺陷:冷裂、热裂、白点、冷隔、热处理裂纹;
4、表面缺陷:鼠尾、沟槽、夹砂结疤、粘砂和表面粗糙、皱皮、缩陷
5、残缺类缺陷:浇不到、未浇满、跑火、型漏、损伤;
6、形状及重量差错类缺陷:尺寸和重量差错、变形、错型、偏芯、舂移;
7、夹杂类缺陷:外来金属夹杂物、冷豆、内渗物、夹渣、砂眼;
8、性能、成分、组织不合格:物理性能、力学性能和化学成分不合格、石墨漂浮、石墨集结、组织粗大、偏析、硬点、白口、反白口、球化不良和球化衰退。