铸件常见缺陷
铸件中常见缺陷

铸件中常见的主要缺陷有:1.气孔这是金属凝固过程中未能逸出的气体留在金属内部形成的小空洞,其内壁光滑,内含气体,对超声波具有较高的反射率,但是又因为其基本上呈球状或椭球状,亦即为点状缺陷,影响其反射波幅。
钢锭中的气孔经过锻造或轧制后被压扁成面积型缺陷而有利于被超声检测所发现,如图2.2所示。
2.缩孔与疏松铸件或钢锭冷却凝固时,体积要收缩,在最后凝固的部分因为得不到液态金属的补充而会形成空洞状的缺陷。
大而集中的空洞称为缩孔,细小而分散的空隙则称为疏松,它们一般位于钢锭或铸件中心最后凝固的部分,其内壁粗糙,周围多伴有许多杂质和细小的气孔。
由于热胀冷缩的规律,缩孔是必然存在的,只是随加工工艺处理方法不同而有不同的形态、尺寸和位置,当其延伸到铸件或钢锭本体时就成为缺陷。
钢锭在开坯锻造时如果没有把缩孔切除干净而带入锻件中就成为残余缩孔(缩孔残余、残余缩管),如图2.3、2.4、2.5所示。
如果铸件的型模设计不当、浇注工艺不当等,也会在铸件与型模接触的部位产生疏松,如图2.28所示。
断口照片中的黑色部分即为疏松部位,其呈现黑色是因为该工件已经过退火处理,使得疏松部位被氧化和渗入机油所致。
图2.28 W18钢铸件-用作铣刀齿,采用超声纵波垂直入射多次底波衰减法发现的疏松断口照片3.夹渣熔炼过程中的熔渣或熔炉炉体上的耐火材料剥落进入液态金属中,在浇注时被卷入铸件或钢锭本体内,就形成了夹渣缺陷。
夹渣通常不会单一存在,往往呈密集状态或在不同深度上分散存在,它类似体积型缺陷然而又往往有一定线度。
4.夹杂熔炼过程中的反应生成物(如氧化物、硫化物等)-非金属夹杂,如图2.1和2.6,或金属成分中某些成分的添加料未完全熔化而残留下来形成金属夹杂,如高密度、高熔点成分-钨、钼等,如图2.29,也有如图2.24所示钛合金棒材中的纯钛偏析。
(a)(b)(c)(d)(e)图2.29 BT9钛合金锻制饼坯中的钼夹杂:(a)剖面低倍照片;(b)X射线照相底片;(c)C扫描显示(图中四个白色点状显示为同一个缺陷,是使用水浸点聚焦探头以不同灵敏度检测的结果,其他分散细小的白色点状为与该缺陷无关的杂波显示);(d)B扫描显示;(e)3D显示5.偏析铸件或钢锭中的偏析主要指冶炼过程中或金属的熔化过程中因为成分分布不均而形成的成分偏析,有偏析存在的区域其力学性能有别于整个金属基体的力学性能,差异超出允许标准范围就成为缺陷,如图2.23和2.24、2.27所示。
铸件常见缺陷及防止方法
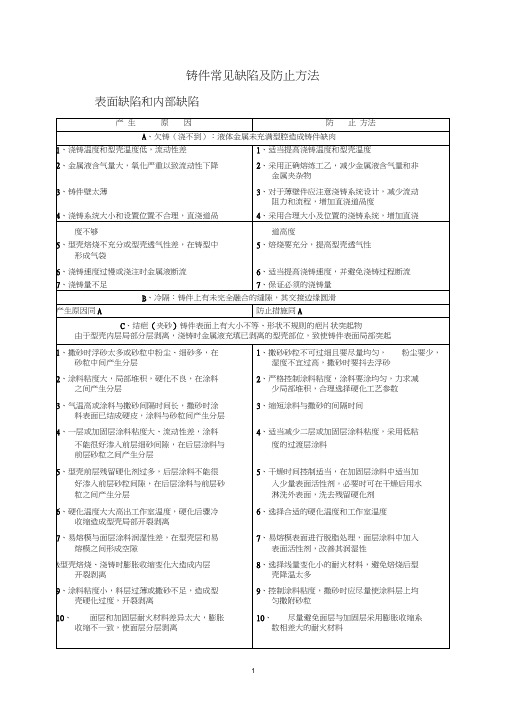
铸件常见缺陷及防止方法表面缺陷和内部缺陷
T 、跑火:钢水穿透型壳,在铸件上形成不规则的多余金属突起 尺寸和粗糙度超差
1、 拉长:铸件几何尺寸超出图样规定范围
2、 变形:铸件平面度、平行度、同轴度以及各单元的相对位置超出图样规定范围
3、 表面粗糙度差:铸件表面粗糙度超出图样规定范围
1、 2、 3铸件结构和浇铸系统设计不合理,在铸件冷
却过程中收缩受阻,产生的热应力和相变应 力超过在弹性状态的铸件材料的强度而断裂
清理过程中有残余应力铸件受外力作用断裂 钢水质量不高,杂质多 1、 2、 3改进铸件结构,减小壁厚差,增设加强肋
等。
合理设计浇铸系统,减少铸造应力
铸件生产过程中应避免受剧烈撞击 改进熔练工艺,提高钢水质量,减少杂质。
铸件常见缺陷(图文并貌)

铸件常见
缺陷
名称砂眼气孔缩孔
图
片
注释在铸件表面或内部有充塞着型
砂的孔眼。
在铸件内部、表面或近于表面
处有大小不等的光滑孔眼。
一
般为圆球形或近似于球形的团
球形孔洞,孔壁光滑。
形状为不规则的封闭或敞露的
孔洞,孔壁粗糙并带有枝晶
状,常出现在铸件最后凝固的
部位(热节处)。
名称粘砂冷隔冲砂
图片
注释在铸件表面上、全部或部分覆
盖着金属与砂的混合物,或一
层烧结的型砂,致使铸件表面
粗糙。
冷隔是铸件上未完全融合的缝
隙或洼坑,其交接边缘呈圆
角,多出现在远离浇口的铸件
宽大上表面和薄壁处、金属流
股汇合处或激冷部位。
铸件表面上有粗糙不规则的金
属瘤状物,常位于浇口附近。
在铸件其它部位则往往出现砂
眼。
披 缝毛 刺浇 不 足披缝是铸件表面上厚薄不均匀的片状金属突起物,常出现在铸件分型面和芯头部位。
毛刺是铸件表面上刺状金属突起物,常出现在型和芯的裂缝处,形状极不规则。
由于金属液未完全充满型腔而产生的铸件缺肉。
掉 砂缺 损变 形
铸件表面的块状金属突起物,其外形与掉落的砂块很相似。
在铸件其它部位则往往出现砂眼或残缺。
在铸件清理或搬运时,损坏了铸件的完整性。
由于收缩应力或型壁变形、开裂引起的铸件外形和尺寸与图纸不符。
铸造件缺陷

铸造铸铁件常见的缺陷有:气孔、粘砂、夹砂、砂眼、胀砂、冷隔、浇不足、缩松、缩孔、缩凹、疏松、缺肉、肉瘤等。
1、气孔:气体在金属液结壳之前未及时逸出,在铸件内生成的孔洞类缺陷。
气孔的内壁光滑,明亮或带有轻微的氧化色。
铸件中产生气孔后,将会减小其有效承载面积,且在气孔周围会引起应力集中而降低铸件的抗冲击性和抗疲劳性。
气孔还会降低铸件的致密性,致使某些要求承受水压试验的铸件报废。
另外,气孔对铸件的耐腐蚀性和耐热性也有不良的影响。
此类问题可采用美嘉华技术修补铸造缺陷,简便易行,省时省工,且修复治理效果良好,并且可以针对铜、铁、钢、铝等不同材质进行修复,替代焊补工艺,避免应力损坏,为企业挽回巨大经济损失。
防止气孔的产生:降低金属液中的含气量,增大砂型的透气性,以及在型腔的最高处增设出气冒口等。
2、粘砂:铸件表面上粘附有一层难以清除的砂粒称为粘砂。
粘砂既影响铸件外观,又增加铸件清理和切削加工的工作量,甚至会影响机器的寿命。
防止粘砂:在型砂中加入煤粉,以及在铸型表面涂刷防粘砂涂料等。
3、夹砂:在铸件表面形成的沟槽和疤痕缺陷,在用湿型铸造厚大平板类铸件时极易产生。
铸件中产生夹砂的部位大多是与砂型上表面相接触的地方,型腔上表面受金属液辐射热的作用,容易拱起和翘曲,当翘起的砂层受金属液流不断冲刷时可能断裂破碎,留在原处或被带入其它部位。
铸件的上表面越大,型砂体积膨胀越大,形成夹砂的倾向性也越大。
4、砂眼:在铸件内部或表面充塞着型砂的孔洞类缺陷。
此类问题可采用美嘉华技术修补铸造缺陷,简便易行,省时省工,且修复治理效果良好,并且可以针对铜、铁、钢、铝等不同材质进行修复,替代焊补工艺,避免应力损坏,为企业挽回巨大经济损失。
5、胀砂:浇注时在金属液的压力作用下,铸型型壁移动,铸件局部胀大形成的缺陷。
为了防止胀砂,应提高砂型强度、砂箱刚度、加大合箱时的压箱力或紧固力,并适当降低浇注温度,使金属液的表面提早结壳,以降低金属液对铸型的压力。
铸件缺陷有哪些
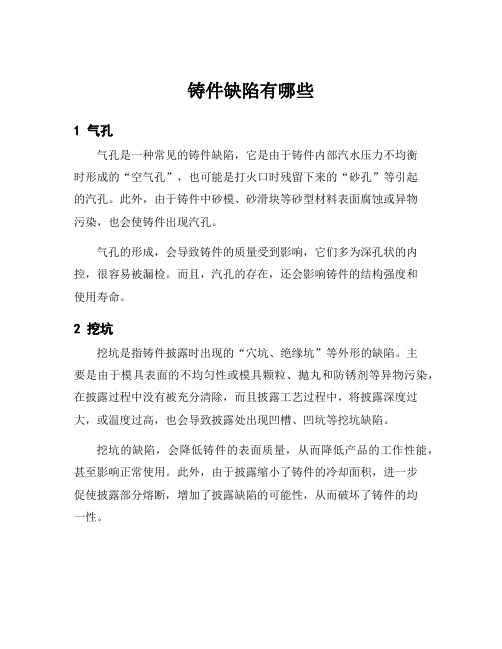
铸件缺陷有哪些1 气孔气孔是一种常见的铸件缺陷,它是由于铸件内部汽水压力不均衡时形成的“空气孔”,也可能是打火口时残留下来的“砂孔”等引起的汽孔。
此外,由于铸件中砂模、砂滑块等砂型材料表面腐蚀或异物污染,也会使铸件出现汽孔。
气孔的形成,会导致铸件的质量受到影响,它们多为深孔状的内控,很容易被漏检。
而且,汽孔的存在,还会影响铸件的结构强度和使用寿命。
2 挖坑挖坑是指铸件披露时出现的“穴坑、绝缘坑”等外形的缺陷。
主要是由于模具表面的不均匀性或模具颗粒、抛丸和防锈剂等异物污染,在披露过程中没有被充分清除,而且披露工艺过程中,将披露深度过大,或温度过高,也会导致披露处出现凹槽、凹坑等挖坑缺陷。
挖坑的缺陷,会降低铸件的表面质量,从而降低产品的工作性能,甚至影响正常使用。
此外,由于披露缩小了铸件的冷却面积,进一步促使披露部分熔断,增加了披露缺陷的可能性,从而破坏了铸件的均一性。
3 淤渣淤渣是指由于模具内铸造残留物残留在出铸件上形成的缺陷。
它多由于模具内部构形复杂、脱模系统设计不当,模具整体活动量不足,不能将模具内的余铸料和其他废料及产生的气体等以足够的速度排出,而形成的淤渣缺陷。
淤渣的存在,会影响铸件的表面,从而影响产品的外观、形状和工作性能,严重时甚至会使铸件的完整性受到影响,使其尺寸精度、强度、坚固性和耐腐蚀性受到影响,影响其材料等级。
4 熔断熔断是指铸件内部在较低温度时因内部结构发生变化产生的缺陷。
熔断可由多个因素引起,如模具润滑不佳、熔点太高或披露深度过大、冷却效果不好等,此外,对某些特定材料,如煤基铸铁,温度较低时受到高氮含量的影响,也会产生熔断缺陷。
熔断的存在,会影响铸件的结构强度和使用寿命,它们多为深孔状的内控,很难以被检测出来,未能及时发现和纠正,会导致铸件质量减退,乃至于产品失效。
铸造过程中常见的几种缺陷
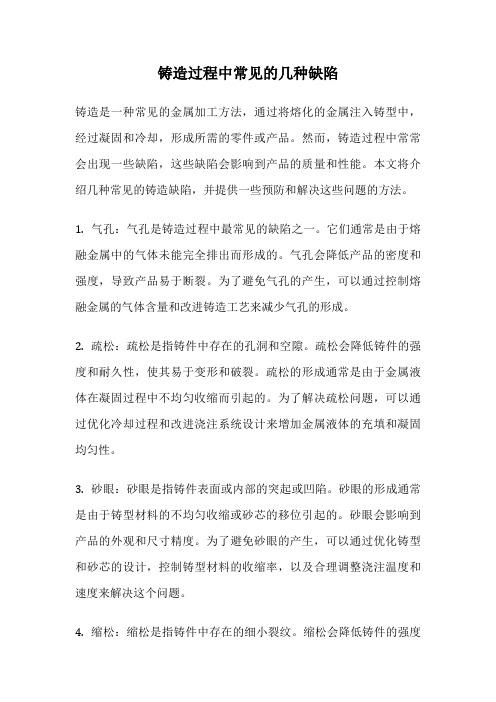
铸造过程中常见的几种缺陷铸造是一种常见的金属加工方法,通过将熔化的金属注入铸型中,经过凝固和冷却,形成所需的零件或产品。
然而,铸造过程中常常会出现一些缺陷,这些缺陷会影响到产品的质量和性能。
本文将介绍几种常见的铸造缺陷,并提供一些预防和解决这些问题的方法。
1. 气孔:气孔是铸造过程中最常见的缺陷之一。
它们通常是由于熔融金属中的气体未能完全排出而形成的。
气孔会降低产品的密度和强度,导致产品易于断裂。
为了避免气孔的产生,可以通过控制熔融金属的气体含量和改进铸造工艺来减少气孔的形成。
2. 疏松:疏松是指铸件中存在的孔洞和空隙。
疏松会降低铸件的强度和耐久性,使其易于变形和破裂。
疏松的形成通常是由于金属液体在凝固过程中不均匀收缩而引起的。
为了解决疏松问题,可以通过优化冷却过程和改进浇注系统设计来增加金属液体的充填和凝固均匀性。
3. 砂眼:砂眼是指铸件表面或内部的突起或凹陷。
砂眼的形成通常是由于铸型材料的不均匀收缩或砂芯的移位引起的。
砂眼会影响到产品的外观和尺寸精度。
为了避免砂眼的产生,可以通过优化铸型和砂芯的设计,控制铸型材料的收缩率,以及合理调整浇注温度和速度来解决这个问题。
4. 缩松:缩松是指铸件中存在的细小裂纹。
缩松会降低铸件的强度和韧性,使其易于断裂。
缩松的形成通常是由于金属液体在凝固过程中体积收缩而引起的。
为了避免缩松的产生,可以通过增加浇注温度和压力,以及优化铸型设计和浇注系统来减少金属液体的收缩。
5. 夹杂物:夹杂物是指铸件中存在的杂质和非金属物质。
夹杂物会降低铸件的强度和耐久性,导致其易于断裂。
夹杂物的形成通常是由于金属液体中的杂质和氧化物未能完全排除而引起的。
为了避免夹杂物的产生,可以通过改进金属液体的净化和过滤系统,以及优化浇注工艺和铸型设计来减少夹杂物的形成。
铸造过程中常见的缺陷包括气孔、疏松、砂眼、缩松和夹杂物。
这些缺陷会影响到铸件的质量和性能,因此在铸造过程中需要采取相应的措施来预防和解决这些问题。
铸造过程中常见的几种缺陷
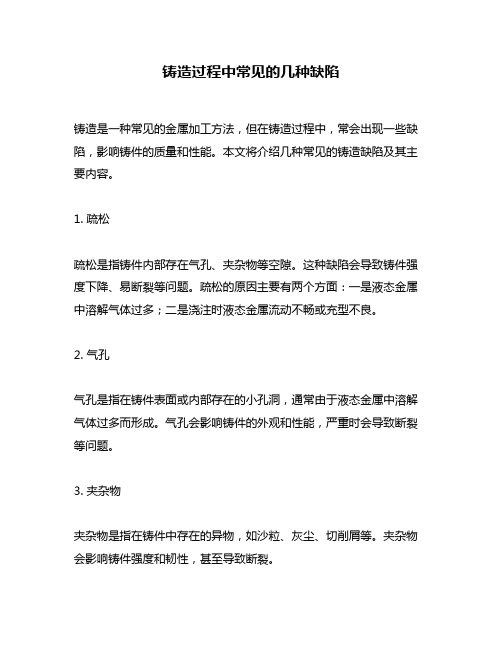
铸造过程中常见的几种缺陷
铸造是一种常见的金属加工方法,但在铸造过程中,常会出现一些缺陷,影响铸件的质量和性能。
本文将介绍几种常见的铸造缺陷及其主要内容。
1. 疏松
疏松是指铸件内部存在气孔、夹杂物等空隙。
这种缺陷会导致铸件强度下降、易断裂等问题。
疏松的原因主要有两个方面:一是液态金属中溶解气体过多;二是浇注时液态金属流动不畅或充型不良。
2. 气孔
气孔是指在铸件表面或内部存在的小孔洞,通常由于液态金属中溶解气体过多而形成。
气孔会影响铸件的外观和性能,严重时会导致断裂等问题。
3. 夹杂物
夹杂物是指在铸件中存在的异物,如沙粒、灰尘、切削屑等。
夹杂物会影响铸件强度和韧性,甚至导致断裂。
4. 热裂纹
热裂纹是指在冷却过程中,由于金属内部应力过大而导致的裂纹。
热裂纹通常发生在厚度不均匀的铸件部位,如壁厚变化处、边缘等。
5. 缩孔
缩孔是指铸件内部存在的凹陷或空洞,通常由于液态金属在凝固过程中收缩而形成。
缩孔会影响铸件的强度和密封性能。
为避免上述铸造缺陷的出现,可以采取以下措施:
1. 控制液态金属中溶解气体含量,如采用真空熔炼等方法。
2. 优化浇注系统设计,确保液态金属流动畅通。
3. 严格控制充型质量,如采用振动充型、压力充型等方法。
4. 控制冷却速度和温度梯度,避免产生应力过大的情况。
5. 优化铸件结构设计,避免壁厚变化过大、边角过于尖锐等情况。
总之,在铸造过程中要注意各个环节的质量控制和优化设计,以确保铸件质量和性能。
铸件常见缺陷和处理
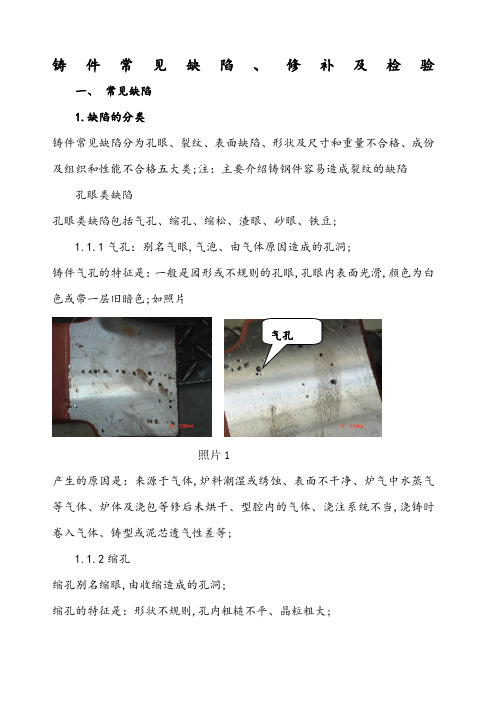
铸件常见缺陷、修补及检验一、常见缺陷1.缺陷的分类铸件常见缺陷分为孔眼、裂纹、表面缺陷、形状及尺寸和重量不合格、成份及组织和性能不合格五大类;注:主要介绍铸钢件容易造成裂纹的缺陷孔眼类缺陷孔眼类缺陷包括气孔、缩孔、缩松、渣眼、砂眼、铁豆;1.1.1气孔:别名气眼,气泡、由气体原因造成的孔洞;铸件气孔的特征是:一般是园形或不规则的孔眼,孔眼内表面光滑,颜色为白色或带一层旧暗色;如照片气孔照片1产生的原因是:来源于气体,炉料潮湿或绣蚀、表面不干净、炉气中水蒸气等气体、炉体及浇包等修后未烘干、型腔内的气体、浇注系统不当,浇铸时卷入气体、铸型或泥芯透气性差等;1.1.2缩孔缩孔别名缩眼,由收缩造成的孔洞;缩孔的特征是:形状不规则,孔内粗糙不平、晶粒粗大;产生的原因是:金属在液体及凝固期间产生收缩引起的,主要有以下几点:铸件结构设计不合理,浇铸系统不适当,冷铁的大小、数量、位置不符实际、铁水化学成份不符合要求,如含磷过高等;浇注温度过高浇注速度过快等;1.1.3缩松缩松别名疏松、针孔蜂窝、由收缩耐造成的小而多的孔洞;缩松的特征是:微小而不连贯的孔,晶粒粗大、各晶粒间存在明显的网状孔眼,水压试验时渗水;如照片2缩松照片2产生的原因同以上缩孔;1.1.4渣眼渣眼别名夹渣、包渣、脏眼、铁水温度不高、浇注挡渣不当造成;渣眼的特征是:孔眼形状不规则,不光滑、里面全部或局部充塞着渣;如照片3渣眼照片3产生的原因是:铁水纯净度差、除渣不净、浇注时挡渣不好,浇注系统挡渣作用差、浇注时浇口未充满或断流;1.1.5砂眼砂眼是夹着砂子的砂眼;砂眼的特征是:孔眼不规则,孔眼内充塞着型砂或芯砂;产生的原因是:合箱时型砂损坏脱落,型腔内的散砂或砂块未清除干净、型砂紧实度差、浇注时冲坏型芯、浇注系统设计不当、型芯表面涂料不好等;1.1.6铁豆铁豆是夹着铁珠的孔眼、别名铁珠、豆眼、铁豆砂眼等;铁豆的特征是:孔眼比较规则、孔眼内包含着金属小珠、常发生在铸铁件上;裂纹类缺陷裂纹类缺陷包括:热裂、温裂、冷裂;1.2.1热裂热裂是在较高温度下产生的,常发生在凝固温度附近;热裂的特征是:铸件上有穿透或不穿透的裂纹,呈弯曲形,开裂处表面氧化;如照片4热裂缩松照片4产生的原因是:铁中含硫量过高或杂质过多、砂型的退让性能差、浇注温度控制不当、铸件壁簿厚转接处过渡剧烈、浇口、冷铁、收缩筋、排气孔的尺寸和位置不当等;1.2.2温裂温裂又称热处理裂纹由切割、焊接或热处理不当引起;温裂的特征是:铸件上有穿透或不穿透的裂纹,开裂处金属表面氧化;1.2.3冷裂冷裂是铸件在较低温度下产生的裂纹;冷裂的特征是:铸件上有穿透或不穿透的裂纹,呈直线形,开裂处表面未氧化;产生的原因是:铸件结构不合理,厚簿不均、砂型或泥芯退让性能差、铸件各部分冷却不一致,合金自身应力倾向大;表面类缺陷表面类缺陷包括粘砂、结疤、夹砂、冷隔;我们主要针对会造成铸件裂的冷隔做一介绍:冷隔又称对火、接火等冷隔的特征是:在制件表面有不规则的明显下陷线形纹路有穿透的和不穿透的两种,形状细小而狭长,在外力作用下有发展趋势;从冷隔的特征看,它容易造成母体裂的危害;冷隔造成的裂纹,不会马上出现,它是在运用时,在承载受冲击作用下产生疲劳裂;如照片5冷隔照片5产生的原因是:多浇包多点同时浇注,使两股金属流对接,但未完全熔合而又无夹杂存在其间,两层金属结合极弱;浇注温度太低、浇注速度过慢、浇注时间太长合金性能流动性差,碳、硅太低,硫量较高;或多浇包顺序浇注,前后两包断流时间太长;铸件截面薄而长,铁水流不利,浇铸断流、砂型跑火、一次性浇注铁水不足、而补浇又不及时等;尺寸形状和重量不合格类缺陷尺寸形状和重量不合格类缺陷包括:多肉、浇不足、落砂、抬箱、偏芯、变形、错箱、损伤、形状、尺寸和重量不符等;成分组织及性能不合格类缺陷成分组织及性能不合格类缺陷包括化学成份不合格、金相不合格、偏析、过硬、物理力学性能不合格;二、缺陷的处理铸件缺陷处理较为关键,尤其在处理裂纹时,处理过程中任何一个环节不注意都会引发新的裂纹;因此我必须关注细节,严格执行工艺,确保质量;1.铸钢件缺陷修补的原则:缺陷的修补必须在不影响产品质量的前提下进行,修补依据应按相关标准有关技术规定执行;如所存在缺陷是否充许修补,及修补相关的技术要求;参照标准:TB1583-96机车车辆铸钢件补焊技术条件TB1464-91铁道机车车辆用碳钢铸件通用技术条件TB456-84车钩钩尾框技术条件TB1400-91内燃机车用铸钢轮心技术条件2.铸钢件裂纹的处理方法焊补是铸钢件的基本生产工序之一;铸钢件上的铸造缺陷几乎都可以用焊补法修复;电弧焊被广泛采用;1铸钢的焊接性:铸钢的含碳量对焊接性影响极大,合金元素的影响亦相当复杂;碳钢或低合金钢的焊接性通常用碳当量CE估计,近似计算公式颇多,大同小异;2焊补要点:为了保证焊补品质质量,应认真清理缺陷处的粘砂、氧化皮、夹杂物等;开出坡口;并根据钢的焊接性做好焊前预热和焊后热处理;打止裂孔及裂纹的消除裂纹的消除可采用电弧气刨或角型砂轮打磨、风铣刀消磨的冷消除法;建议重要件的裂纹消除尽量采用冷消除,尽可能的减少受热;浅表性裂纹可不做止裂孔,裂的深度、宽度较大必须处理前在裂纹的终端10mm以内,预制5~8 mm的止裂孔,防止裂纹的延伸;预制坡口和间隙我们在处理厂修车、构架拐壁座、轴箱拉杆座、旁承座等的裂纹时,焊缝要求焊透;一般采用60度V型坡口,预留2mm间隙;对于重要部位,裂纹较严重的T形接头或角接接头,建议对立板开30度V型坡口,这样才能保证熔合质量;焊前准备处理焊补铸钢件所用焊条应使熔敷金属的化学成份、机械性能与母材相当;处理裂纹我们建议采用碱性焊条,提高抗裂性和韧性;焊前要求对焊条预热200-250℃,使用温度不底于150℃;环境温度不低于5度;要求对坡口表面及施焊表面20mm区域内砂轮打磨;坡口表面不充许存在2mm 以上沟槽,金属表面无油污、氧化物、铁锈见金属光泽;建议在施焊前对铸钢件母体进行预热;最好采用整体预热,如不能整体预热时,可采用局部预热;局部预热的范围为焊缝两侧至少各取焊缝处截面厚三倍的宽度;各种牌号铸钢件的预热温度、焊后保温措施、焊后去除应力的热处理参照表1表1一些常用铸钢的焊接性焊接过程焊接操者须经平焊考试合格,具备焊工资质的人员操作;在施焊时应该选择合理的焊接规范;焊接引弧时,应防止电弧击伤铸件表面,禁止在非焊接区域引弧打火;施焊部位应避免人为吹风与穿堂风;对接焊缝不能一次填充过多,采用多层焊,不得少于三层;第一层焊缝采用较小直径的焊条施焊,以较小的熔合比,防止产生热裂纹;每焊完一层后,应彻底清除熔渣发现裂纹及缺陷应清除后,再焊下一层;施焊中应保持焊缝层间不低于预热温度;较长焊缝大于200mm的焊接,应采用分段法;每层的起弧和收弧位要错开不少于20mm;尽量避开死角位及终端起弧或收弧;1.铸铁件的焊补铸铁件上的气孔、砂眼、夹渣、裂纹、渗漏等缺陷,若不超过焊补的允许范围,可以进焊补修复;但是,铸铁的焊接性能差,焊后常出现气孔、变形,易断裂,难加工,因此焊补铸铁时,应非常慎重;1焊补方法:铸铁的焊补方法通常按工件的预热温度分类2焊前不预热或仅预热到250℃以下,称为冷焊;焊前预热到250~450℃,称为半热焊;焊前预热到500~700℃,称为热焊;铸铁常用焊补方法的特点及适用范围见表2.3铸铁的焊补方法及其适用范围表22焊条的选用焊补铸铁缺陷应根据母材选用适当焊条,见表3;表3根据铸铁材质选用焊条日本焊接协会注:日本JISZ3252铸铁焊条下列成分是焊缝金属成分%:表4铸铝件常用焊补方法及应用。
- 1、下载文档前请自行甄别文档内容的完整性,平台不提供额外的编辑、内容补充、找答案等附加服务。
- 2、"仅部分预览"的文档,不可在线预览部分如存在完整性等问题,可反馈申请退款(可完整预览的文档不适用该条件!)。
- 3、如文档侵犯您的权益,请联系客服反馈,我们会尽快为您处理(人工客服工作时间:9:00-18:30)。
級位
一、 外觀特征(CHARACTER):
鑄件表面出現階梯痕跡。
二、 產生原因(REASON):
1.鑲拼部位松動。
2.活動部位松動或磨損。
3.由動、定模錯位所形成。
4.由披鋒厚導致。
三、 防止方法(METHOD OF IMPROVEMENT):
1.緊固鑲塊或其它活動部位。
2.設計時消除尖角,配合間隙調整適合。
三、防止方法:
1。選用合適之壓鑄模材料及熱處理工藝。
2。有易裂傾向模具,要定期或壓鑄 2-3 萬次后退火,消除應力并打磨型腔表面。
3。盡可能使
模溫保持平衡,壓鑄前必須預熱,壓鑄時運水要通暢,切忌模溫高
一、外觀特征:
鑄體被破壞裂開,呈不規則細長線形,在外力作用下有發展
裂紋
趨向。 二、產生原因:
1.鋁合金中雜質含量過高,降低了合金的可塑性。
三、防止方法(METHOD OF IMPROVEMRNT): 1)改進內澆道,改進排氣條件,適當提高壓鑄模溫度和澆注溫度。 2) 提高壓射比壓和壓射速度。 3)注意噴水量適當且注意吹干。
冷格
一、 外觀特征: 鑄件表面有不規則的明顯下陷線形紋路,多出現在離澆口較遠區域,對各種零件產生於一定部位。 二、 產生原因: 1)流互相對接,但未完全熔合而又無夾雜其間,兩層金屬結合力弱。 2)澆口位置不正確,流路太長。 3)溢流槽位置于金屬流匯集處不吻合或容量不夠。 4)內澆口速度太低。 5)排氣槽堵塞,排氣不足。 6)料溫及模溫太低。 三、 防止方法: 1)改澆口,改善金屬流向,使兩種金屬流緊密相接。 2)在出現冷格附近增開或加大溢流槽。 3)壓鑄時先清除排氣槽上之鋁料或增大排氣槽。 4)增加壓射速度的同時適當加大澆口厚度及澆道截面積。 5)適當提高料溫及模溫。
3.優化模具設計。
4.調整好開模時間,不能太長也不能太短。
一、 外觀特征(CHARACTER):
頂針位凸出、凹入鑄件表面。
二、 產生原因(REASON):
1.頂針長短配置不合理。
2.模具局部出模困難。
頂針凸
頂針凹
3.模具局部溫度過高,頂針易卡。 三、 防止方法(METHOD OF IMPROVEMENT):
2.冷卻系統設計不合理。
開模過早。
3.澆注溫度過高。
三、防止方法
1.壁厚應均勻﹔厚薄過渡要緩和。
2.正確選擇合金液導入位置及增加內澆道截面積。
3.增加壓射壓力,延長保壓時間。
4.適當降低澆注溫度及壓鑄模溫度﹔對局部高溫要局部冷卻。
5.改善排溢
條件。排气槽批缝及时清理。
5 燒模
一、外觀特征: 壓鑄合金輿型壁粘連而產生拉傷痕跡甚至撕破。 二、產生原因: 1.離模劑噴射不足或不均勻。 2.澆注系統不正確,使合金正面沖擊型壁和型芯。 3.充填速度太高。 4.料溫,模溫太高。 5.模具材料不當,熱處理工藝不正確,硬度不足使模具近內澆口 6.鋁合金含鐵(Fe)量<0.6%或有偏析。 三、防止方法: 1.改變噴離模劑方法,過熱部位多噴離模劑。 2.修改澆注系統,避免合金正面沖擊型芯和型壁。 3.改善內澆口,降低充填速度。 4.降低料溫,適當調整模溫。 5.提高型芯硬度(氮化)。 6.校核合金含鐵量,消除偏析。
3.在保証填充良好的情況下,盡可能增大內澆口截面積。
4.排氣槽部
位要設置合理并有足夠的排氣能力。排气槽要及时清理。
5.喷涂离模
剂要适量。
氣泡
3
一、 外觀特征: 鑄件接近表面有氣體集聚,有時看到鑄件表面鼓泡。 二、 產生原因: 1)由卷入氣體引起。型腔氣體沒有排出,被包在鑄件中﹔ 2)由合金氣體引起。合金內吸有較多氣體,凝固時 3)析出留在鑄件內。 局部模溫過高,料溫過高。 三、 防止方法: 1)改善內澆道、溢流槽排氣道的大小和位置﹔改善填充時間和內澆道處流速﹔ 2)清除合金液中的氣體和氧化物﹔爐料要管理好,避免被塵土油類污染。 3)局部模溫過高處多噴水,控制好料溫。
二、產生原因: 1)模溫過低﹔料溫過低。 2)澆道設計不良,內澆口位置不良﹔澆注系統不合理。 3)填充速度低,填充時間短。 4)排氣不良﹔噴霧不合理。 三、防止方法: 1)調整內澆道截面積或位置。 2)提高模溫,料溫。 3)調整內澆道速度及壓力。 4)適當的選用塗料及調整用量。
一、 外觀特征:
氣孔具有光滑的表面,形狀呈圓形或橢圓形。
2)
在拉傷部位相應的模具上多噴水。
3)
調整頂針,使頂出受力平衡。
一、 外觀特征(CHARACTER):
夾層
在鑄件局部有金屬的明顯層次。
二、 產生原因(REASON):
1)模具剛性不夠在金屬液填充過程中,模板產生抖動。
2)在壓射過程中沖頭出現爬行現象。
3)澆道系統設計不當。
三 防止方法(METHOD OF IMPROVEMENT):
模裂紋
一、外觀特征: 鑄件表面有網狀發絲一樣凸起或凹陷的痕跡隨壓鑄次數增
加而不斷擴大延伸。
二、產生原因:
1.壓鑄模腔龜裂。
2.模肉材料品質欠佳和熱處理不當。
3.冷卻系統調節不當。
4.鑄件壁厚超越 4mm 以上,因而模溫過高。
5.模溫差冷熱聚變,噴涂不當,對模肉激冷過劇。
6.內澆口附近經受沖蝕最易產生熱裂。
成型不良
一、外觀特征(CHARACTER) : 金屬液充滿型腔,鑄件表面有不規則的孔洞、凹陷或棱角不齊,表面形狀呈自然液流或輿液面相似。 二、 生原因(REASON): 1)內澆道寬度不夠或壓鑄模排氣不良。 2)合金流動性差。 3)澆注溫度低或壓鑄模溫度低,壓射速度低。 4)壓射比壓不足。 5)壓鑄型腔邊角尺寸不合理、不易填充。 6)噴水太多或沒吹干。
6)料溫太高。
三、防止方法:
1)檢查合模力及增壓情況。 2)調整增壓機構使壓射增壓峰值降低。
3)檢查壓鑄模強度和閉鎖元件。 4)檢查壓鑄模損壞情況并修理。 5)清理分型面防止有雜物。
2
6)增大鎖模力。 7)控制好料溫。
流紋
一、外觀特征: 鑄件表面上有與金屬液流動方向一致的條紋,有明顯可見的與金屬基本體顏色不一樣無方向性的紋路, 無發展趨勢。
3.改善鑄件結構使壓鑄模消除穿插的鑲嵌形式,改進壓鑄模結構。
培訓資料
外 觀 檢 查 圖 片
8
2.模具溫度太低。
3.鑄件壁厚過薄或壁厚有劇烈變化之處。
4.因鑄體形狀結構造成收縮時產生應力而撕裂。
5.留模時間過長。
6.頂出時受力不均。
7.脫模斜度不夠。
8.填充不良,鑄體凝固未熔合,強度不夠。
三、防止方法:
6
1.正確控制合金成份。
2.提高模具溫度。
3.改變鑄件結構,避免出現壁厚厚薄劇變,拐角、凹凸槽、柱位等根部加大 R 角,并打磨光滑倒扣。
1.選擇合適的材料。
2.將鑲針進行氮化,提高硬度。
3.合理設計產品內澆口位及鑲針長度的確定。
4.注意易斷鑲針的噴水。
5.定期更
換鑲針。
縮陷
一、外觀特征:
在壓鑄件厚大部分的表面上有平滑的凹痕(狀如盤碟)。
二、產生原因
1.由收縮引起。
鑄件設計不當壁厚差太大﹔澆道位置不當﹔壓射比壓低,保壓時間短﹔壓鑄模局部溫度過高。
4
斷 針
一、 外觀特征(CHARACTER):
孔深變淺,且孔底不平整
二、 產生原因(REASON):
1.鑲針選材不合適,熱疲勞性差。
2.鑲針硬度不夠。
3.鑲針太長,容易变形,在外力作用下断裂。
4.澆道位置設計不合理,易受铝液冲击。
5.鑲針老化。
三、 防止方法(METHOD OF IMPROVEMENT):
氣孔
二、 產生原因:
1.壓射速度調整不合理,在料槽內卷氣。
2.橫澆道設計不合理,內澆口位置不合理,分型面選擇不
當。
3.排氣不良。
4.鋁液含氣量高,雜質含量高。
5.模溫、料溫過高,冷確系統設計不合理。
三、 防止方法:
1.使用干燥而干淨的添加劑,不使合金過熱并很好排氣,改善金屬導入方向。
2.調整壓射速度,防止在料槽內卷氣。
1
扣模
一、 外觀特征:
鑄件表面順著出模方向留有擦傷的痕跡。
二、 產生原因:
1)設計和制造不正確。如型芯或成型部份無出模斜度或有反斜度。
2)成形表面光潔度不夠或加工紋向不對,脫模方向上平整度較差。
3)成形表面有碰傷。
4)噴水太少。
5)金屬流撞擊壁過劇。
6)鑄件頂出有偏斜。
三、 防止方法:
1)固定部位拉傷時,要檢修模具,修正斜度,打光滑倒扣。
變形
一、 外觀特征(CHARACTER): 鑄件歪(彎)曲,超出圖紙公差。
二、 產生原因(REASON): 1.鑄件結構不合理,各部收縮不均勻。 2.開模時間太短。 3.頂出過程鑄件偏斜,受力不均。 4.鑄件剛性不夠。 5.堆放不合理或去除澆口不當。 三、防止方法(METHOD OF IMPROVEMENT): 1.改進鑄件結構,使鑄件壁厚均勻。 2.不要堆疊存放,特別是大而薄的鑄件。 3.加強剛性。注意开模时间以及顶出时间和顶出速度的调整。 4.必要時可以進行整(校)形。
4.在公差范圍內加大脫模斜度。
5.適當增加頂針。
6.檢查抽芯部份有否偏斜并進行調整。
7.修改內
澆口改善填充情況。
粘模
一、外觀特征:
鑄件表面缺肉且表面無金屬光澤。
二、產生原因:
1.模具局部溫度過高。
2.模具表面粗糙。
3.模具拔模斜度太小。
4.開模時間不恰當。
三、防止方法:
1.注意噴水,保持模溫平衡。
2.模具省光。
1.頂針長短要配置合理。
2.模具局部溫度偏高需多噴水,降低模溫。
3.修省出模難處。