铸造铸件常见缺陷讲解
铸件常见缺陷和处理

铸件常见缺陷和处理 The pony was revised in January 2021铸件常见缺陷、修补及检验一、常见缺陷1.缺陷的分类铸件常见缺陷分为孔眼、裂纹、表面缺陷、形状及尺寸和重量不合格、成份及组织和性能不合格五大类。
(注:主要介绍铸钢件容易造成裂纹的缺陷)孔眼类缺陷孔眼类缺陷包括气孔、缩孔、缩松、渣眼、砂眼、铁豆。
1.1.1气孔:别名气眼,气泡、由气体原因造成的孔洞。
铸件气孔的特征是:一般是园形或不规则的孔眼,孔眼内表面光滑,颜色为白色或带一层旧暗色。
(如照片)气孔照片1产生的原因是:来源于气体,炉料潮湿或绣蚀、表面不干净、炉气中水蒸气等气体、炉体及浇包等修后未烘干、型腔内的气体、浇注系统不当,浇铸时卷入气体、铸型或泥芯透气性差等。
1.1.2缩孔缩孔别名缩眼,由收缩造成的孔洞。
缩孔的特征是:形状不规则,孔内粗糙不平、晶粒粗大。
产生的原因是:金属在液体及凝固期间产生收缩引起的,主要有以下几点:铸件结构设计不合理,浇铸系统不适当,冷铁的大小、数量、位置不符实际、铁水化学成份不符合要求,如含磷过高等。
浇注温度过高浇注速度过快等。
1.1.3缩松缩松别名疏松、针孔蜂窝、由收缩耐造成的小而多的孔洞。
缩松的特征是:微小而不连贯的孔,晶粒粗大、各晶粒间存在明显的网状孔眼,水压试验时渗水。
(如照片2)缩松照片2产生的原因同以上缩孔。
1.1.4渣眼渣眼别名夹渣、包渣、脏眼、铁水温度不高、浇注挡渣不当造成。
渣眼的特征是:孔眼形状不规则,不光滑、里面全部或局部充塞着渣。
(如照片3)渣眼照片3产生的原因是:铁水纯净度差、除渣不净、浇注时挡渣不好,浇注系统挡渣作用差、浇注时浇口未充满或断流。
1.1.5砂眼砂眼是夹着砂子的砂眼。
砂眼的特征是:孔眼不规则,孔眼内充塞着型砂或芯砂。
产生的原因是:合箱时型砂损坏脱落,型腔内的散砂或砂块未清除干净、型砂紧实度差、浇注时冲坏型芯、浇注系统设计不当、型芯表面涂料不好等。
铸件常见缺陷(图文并貌)
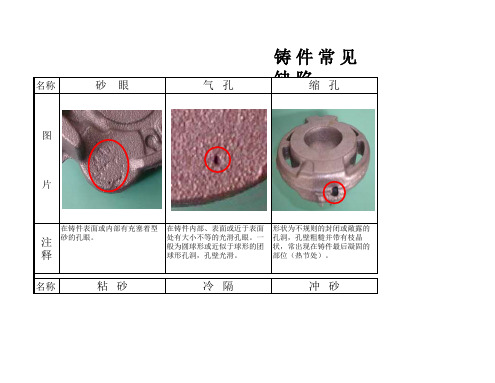
铸件常见缺陷
名称砂眼气孔缩孔披缝图
片
注释在铸件表面或内部有充塞着型
砂的孔眼。
在铸件内部、表面或近于表面
处有大小不等的光滑孔眼。
一
般为圆球形或近似于球形的团
球形孔洞,孔壁光滑。
形状为不规则的封闭或敞露的
孔洞,孔壁粗糙并带有枝晶
状,常出现在铸件最后凝固的
部位(热节处)。
披缝是铸件表面上厚薄不均匀
的片状金属突起物,常出现在
铸件分型面和芯头部位。
名称粘砂冷隔冲砂掉砂
图片
注释在铸件表面上、全部或部分覆
盖着金属与砂的混合物,或一
层烧结的型砂,致使铸件表面
粗糙。
冷隔是铸件上未完全融合的缝
隙或洼坑,其交接边缘呈圆
角,多出现在远离浇口的铸件
宽大上表面和薄壁处、金属流
股汇合处或激冷部位。
铸件表面上有粗糙不规则的金
属瘤状物,常位于浇口附近。
在铸件其它部位则往往出现砂
眼。
铸件表面的块状金属突起物,
其外形与掉落的砂块很相似。
在铸件其它部位则往往出现砂
眼或残缺。
毛 刺浇 不 足
毛刺是铸件表面上刺状金属突起物,常出现在型和芯的裂缝处,形状极不规则。
由于金属液未完全充满型腔而产生的铸件缺肉。
缺 损变 形渣 眼
在铸件清理或搬运时,损坏了铸件的完整性。
由于收缩应力或型壁变形、开
裂引起的铸件外形和尺寸与图
纸不符。
在铸件内部或表面形状不规
则的孔眼。
孔眼不光滑,里
面全部或部分充塞着渣。
铸件缺陷手册
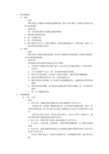
1、多肉类缺陷1)冲砂一、特征铸件表面上有粗糙不规则的金属瘤状物,常位于浇口附近。
在铸件其他部位则往往出现砂眼。
二、原因分析型、芯表面局部砂子被液态金属冲刷掉:1、型砂或芯砂强度太低。
2、型、芯舂得太松。
3、型、芯烘烤过渡。
4、浇注系统开设不当,内浇口数量少,液态金属流速过大,冲刷力强,或型、芯局部表面受冲刷时间过长。
2)掉砂一、特征铸件表面上得块状金属突起物,其外形与掉落的沙块很相似。
在铸件其他部位往往出现砂眼或残缺。
二、原因分析砂型或砂芯的局部块在机械力作用下掉落:1、分型面不平整或分型负数不适当,以及芯头不平整或间隙小,合型时将型、芯压坏。
2、下芯合型操作不小心,型、芯局部砂块被压坏挤落。
3、型芯水分过高或型、芯未烘干且通气性很差,浇注时发生沸腾现象。
4、舂砂太松或紧实度不均,型、芯局部强度不足5、模样有深而小的凹槽,由于结构不良或拔模斜度小,起模时将砂型带坏或震裂。
6、和好的砂型在紧箱、加压铁或在运输过程中受冲击碰撞,型、芯局部砂块掉落。
7、型、芯干燥温度过高。
1、空洞类缺陷1)、气孔、针孔一、特征1、析出气孔(溶解在液态金属中的气体在凝固时产生的气孔):多是细小的,呈圆形、椭圆形或针状,分布在铸件的整体或某一部分,其内壁光滑而明亮。
氢气孔比氮气孔明亮,氢氮复合气孔易产生在铸件的中心部位。
这类气孔在铝合金中,常以针孔形式存在,它的大小多在1毫米以下,通常在铸件的厚大断面或热结处较为严重。
2、侵入气孔(型和芯的气体侵入液态金属后产生的气孔):尺寸较大,孔壁光滑,表面氧化,多数呈梨形或椭圆形,位于铸件表面或内部。
3、反应气孔(液态金属的某些成分之间或液态金属与铸型在界面上发生化学反应产生的气孔):气孔位于铸件表皮下,有的呈分散的针孔,有的隐蔽在铸件上部并伴有夹渣。
二、原因分析1、液态金属中含有大量气体,且浇注温度低,析出气体来不及上浮溢出。
2、炉料潮湿、锈蚀、油污,出铁槽和浇包未烘干。
3、针孔主要是由氢、氮、一氧化碳气体造成的,硅虽可减少铸铁中氧的含量,但却增加氢的含量,故高硅铸铁易出现气孔。
常见压铸件缺陷及解决方法
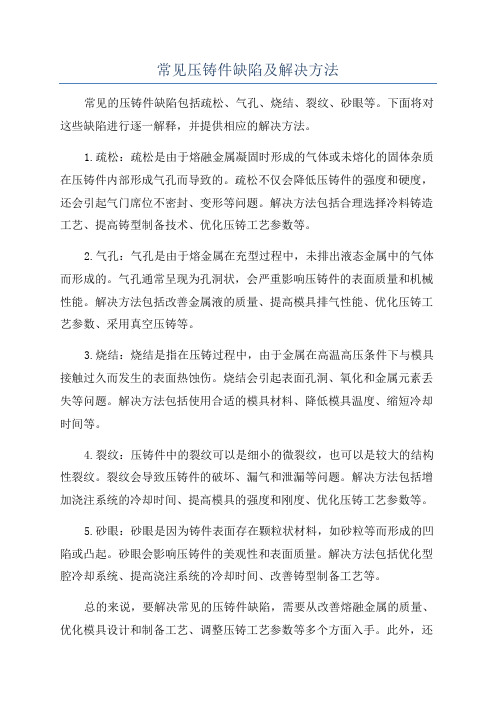
常见压铸件缺陷及解决方法常见的压铸件缺陷包括疏松、气孔、烧结、裂纹、砂眼等。
下面将对这些缺陷进行逐一解释,并提供相应的解决方法。
1.疏松:疏松是由于熔融金属凝固时形成的气体或未熔化的固体杂质在压铸件内部形成气孔而导致的。
疏松不仅会降低压铸件的强度和硬度,还会引起气门席位不密封、变形等问题。
解决方法包括合理选择冷料铸造工艺、提高铸型制备技术、优化压铸工艺参数等。
2.气孔:气孔是由于熔金属在充型过程中,未排出液态金属中的气体而形成的。
气孔通常呈现为孔洞状,会严重影响压铸件的表面质量和机械性能。
解决方法包括改善金属液的质量、提高模具排气性能、优化压铸工艺参数、采用真空压铸等。
3.烧结:烧结是指在压铸过程中,由于金属在高温高压条件下与模具接触过久而发生的表面热蚀伤。
烧结会引起表面孔洞、氧化和金属元素丢失等问题。
解决方法包括使用合适的模具材料、降低模具温度、缩短冷却时间等。
4.裂纹:压铸件中的裂纹可以是细小的微裂纹,也可以是较大的结构性裂纹。
裂纹会导致压铸件的破坏、漏气和泄漏等问题。
解决方法包括增加浇注系统的冷却时间、提高模具的强度和刚度、优化压铸工艺参数等。
5.砂眼:砂眼是因为铸件表面存在颗粒状材料,如砂粒等而形成的凹陷或凸起。
砂眼会影响压铸件的美观性和表面质量。
解决方法包括优化型腔冷却系统、提高浇注系统的冷却时间、改善铸型制备工艺等。
总的来说,要解决常见的压铸件缺陷,需要从改善熔融金属的质量、优化模具设计和制备工艺、调整压铸工艺参数等多个方面入手。
此外,还需要采用适当的检测手段,如金相分析、X射线检测、超声波检测等,对压铸件进行质量检验,及时排除可能存在的缺陷。
铸造件缺陷

铸造铸铁件常见的缺陷有:气孔、粘砂、夹砂、砂眼、胀砂、冷隔、浇不足、缩松、缩孔、缩凹、疏松、缺肉、肉瘤等。
1、气孔:气体在金属液结壳之前未及时逸出,在铸件内生成的孔洞类缺陷。
气孔的内壁光滑,明亮或带有轻微的氧化色。
铸件中产生气孔后,将会减小其有效承载面积,且在气孔周围会引起应力集中而降低铸件的抗冲击性和抗疲劳性。
气孔还会降低铸件的致密性,致使某些要求承受水压试验的铸件报废。
另外,气孔对铸件的耐腐蚀性和耐热性也有不良的影响。
此类问题可采用美嘉华技术修补铸造缺陷,简便易行,省时省工,且修复治理效果良好,并且可以针对铜、铁、钢、铝等不同材质进行修复,替代焊补工艺,避免应力损坏,为企业挽回巨大经济损失。
防止气孔的产生:降低金属液中的含气量,增大砂型的透气性,以及在型腔的最高处增设出气冒口等。
2、粘砂:铸件表面上粘附有一层难以清除的砂粒称为粘砂。
粘砂既影响铸件外观,又增加铸件清理和切削加工的工作量,甚至会影响机器的寿命。
防止粘砂:在型砂中加入煤粉,以及在铸型表面涂刷防粘砂涂料等。
3、夹砂:在铸件表面形成的沟槽和疤痕缺陷,在用湿型铸造厚大平板类铸件时极易产生。
铸件中产生夹砂的部位大多是与砂型上表面相接触的地方,型腔上表面受金属液辐射热的作用,容易拱起和翘曲,当翘起的砂层受金属液流不断冲刷时可能断裂破碎,留在原处或被带入其它部位。
铸件的上表面越大,型砂体积膨胀越大,形成夹砂的倾向性也越大。
4、砂眼:在铸件内部或表面充塞着型砂的孔洞类缺陷。
此类问题可采用美嘉华技术修补铸造缺陷,简便易行,省时省工,且修复治理效果良好,并且可以针对铜、铁、钢、铝等不同材质进行修复,替代焊补工艺,避免应力损坏,为企业挽回巨大经济损失。
5、胀砂:浇注时在金属液的压力作用下,铸型型壁移动,铸件局部胀大形成的缺陷。
为了防止胀砂,应提高砂型强度、砂箱刚度、加大合箱时的压箱力或紧固力,并适当降低浇注温度,使金属液的表面提早结壳,以降低金属液对铸型的压力。
铸件常见铸造缺陷

铸造常见缺陷特点
缺陷名称:披缝 缺陷特点:铸件表面在分模 面处的规则缩陷。 产生原因: 砂型或砂芯分模 面处的飞边未去除
铸造常见缺陷特点
缺陷名称:表面多肉 缺陷特点:铸件表面有多余 的部分。 产生原因:砂型或砂芯的相 应部分掉肉。
铸造常见缺陷特点
缺陷名称:黑皮(其二)
铸造常见缺陷特点
缺陷名称:气孔 缺陷特点:铸件内部或表面 有大小不同的孔眼,孔的内 壁光滑,多呈圆形。 产生原因:砂型太紧或型砂 透气性差;型砂太湿;砂芯 通气孔堵塞;浇注系统不正 确,气体排不出去
铸造常见缺陷特点
缺陷名称:缩孔(大而集中 的空洞 ) 缺陷特点:铸件厚、断面处 出现形状不规则的孔眼,孔 的内壁粗糙。 产生原因:冒口设置不正确 ;合金成分不合格,收缩过 大;浇注温度过高;铸件设 计不合理,无法进行补缩
铸造常见缺陷特点
缺陷名称:砂眼 缺陷特点:铸件内部或表面 有充满砂粒的孔眼,孔形不 规则 产生原因:型砂强度不够或 局部没舂紧,掉砂;型腔、 浇口内散砂未吹净;合箱时 砂型局部挤坏,掉砂;浇注 系统不合理,冲坏砂型
铸造常见缺陷特点
缺陷名称:砂眼(其二)
铸造常见缺陷特点
缺陷名称:砂眼(名称:表面多肉肉(其 二)
铸造常见缺陷特点
缺陷名称:缺肉(缺料) 缺陷特点:铸件表面有缺少 一块,可能导致报废。 产生原因:浇冒口切除时带 掉一块;
铸造常见缺陷特点
缺陷名称:表面缩凹 缺陷特点:铸件表面有缩凹。 产生原因:铸件内部收缩
铸造常见缺陷特点
缺陷名称:黑皮 缺陷特点:加工面有加工不 到的地方 产生原因:铸件加工量不足, 铸件变形,夹偏
六种铸件常见缺陷的产生原因及防止方法
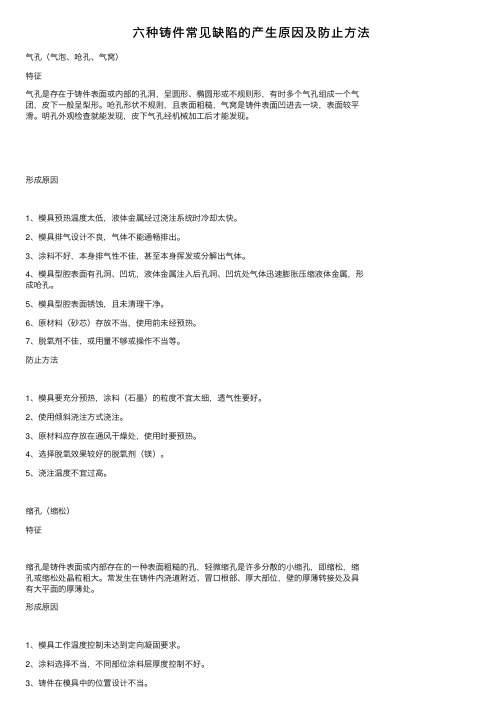
六种铸件常见缺陷的产⽣原因及防⽌⽅法⽓孔(⽓泡、呛孔、⽓窝)特征⽓孔是存在于铸件表⾯或内部的孔洞,呈圆形、椭圆形或不规则形,有时多个⽓孔组成⼀个⽓团,⽪下⼀般呈梨形。
呛孔形状不规则,且表⾯粗糙,⽓窝是铸件表⾯凹进去⼀块,表⾯较平滑。
明孔外观检查就能发现,⽪下⽓孔经机械加⼯后才能发现。
形成原因1、模具预热温度太低,液体⾦属经过浇注系统时冷却太快。
2、模具排⽓设计不良,⽓体不能通畅排出。
3、涂料不好,本⾝排⽓性不佳,甚⾄本⾝挥发或分解出⽓体。
4、模具型腔表⾯有孔洞、凹坑,液体⾦属注⼊后孔洞、凹坑处⽓体迅速膨胀压缩液体⾦属,形成呛孔。
5、模具型腔表⾯锈蚀,且未清理⼲净。
6、原材料(砂芯)存放不当,使⽤前未经预热。
7、脱氧剂不佳,或⽤量不够或操作不当等。
防⽌⽅法1、模具要充分预热,涂料(⽯墨)的粒度不宜太细,透⽓性要好。
2、使⽤倾斜浇注⽅式浇注。
3、原材料应存放在通风⼲燥处,使⽤时要预热。
4、选择脱氧效果较好的脱氧剂(镁)。
5、浇注温度不宜过⾼。
缩孔(缩松)特征缩孔是铸件表⾯或内部存在的⼀种表⾯粗糙的孔,轻微缩孔是许多分散的⼩缩孔,即缩松,缩孔或缩松处晶粒粗⼤。
常发⽣在铸件内浇道附近、冒⼝根部、厚⼤部位,壁的厚薄转接处及具有⼤平⾯的厚薄处。
形成原因1、模具⼯作温度控制未达到定向凝固要求。
2、涂料选择不当,不同部位涂料层厚度控制不好。
3、铸件在模具中的位置设计不当。
4、浇冒⼝设计未能达到起充分补缩的作⽤。
5、浇注温度过低或过⾼。
防⽌⽅法1、提⾼磨具温度。
2、调整涂料层厚度,涂料喷洒要均匀,涂料脱落⽽补涂时不可形成局部涂料堆积现象。
3、对模具进⾏局部加热或⽤绝热材料局部保温。
4、热节处镶铜块,对局部进⾏激冷。
5、模具上设计散热⽚,或通过⽔等加速局部地区冷却速度,或在模具外喷⽔,喷雾。
6、⽤可拆缷激冷块,轮流安放在型腔内,避免连续⽣产时激冷块本⾝冷却不充分。
7、模具冒⼝上设计加压装置。
8、浇注系统设计要准确,选择适宜的浇注温度。
铸造过程中常见的几种缺陷
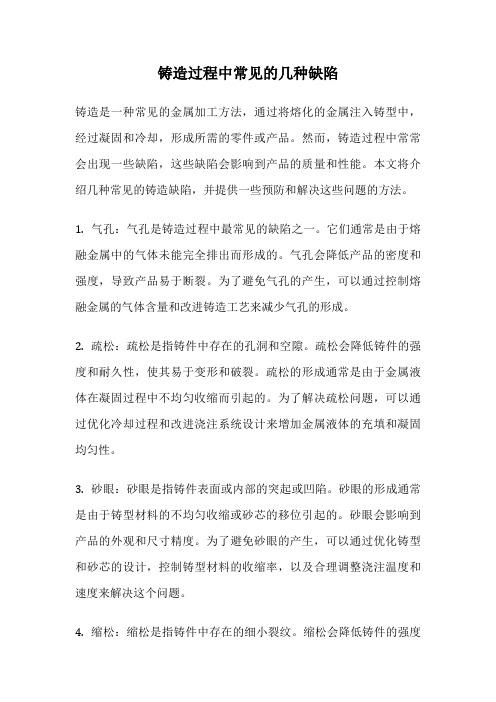
铸造过程中常见的几种缺陷铸造是一种常见的金属加工方法,通过将熔化的金属注入铸型中,经过凝固和冷却,形成所需的零件或产品。
然而,铸造过程中常常会出现一些缺陷,这些缺陷会影响到产品的质量和性能。
本文将介绍几种常见的铸造缺陷,并提供一些预防和解决这些问题的方法。
1. 气孔:气孔是铸造过程中最常见的缺陷之一。
它们通常是由于熔融金属中的气体未能完全排出而形成的。
气孔会降低产品的密度和强度,导致产品易于断裂。
为了避免气孔的产生,可以通过控制熔融金属的气体含量和改进铸造工艺来减少气孔的形成。
2. 疏松:疏松是指铸件中存在的孔洞和空隙。
疏松会降低铸件的强度和耐久性,使其易于变形和破裂。
疏松的形成通常是由于金属液体在凝固过程中不均匀收缩而引起的。
为了解决疏松问题,可以通过优化冷却过程和改进浇注系统设计来增加金属液体的充填和凝固均匀性。
3. 砂眼:砂眼是指铸件表面或内部的突起或凹陷。
砂眼的形成通常是由于铸型材料的不均匀收缩或砂芯的移位引起的。
砂眼会影响到产品的外观和尺寸精度。
为了避免砂眼的产生,可以通过优化铸型和砂芯的设计,控制铸型材料的收缩率,以及合理调整浇注温度和速度来解决这个问题。
4. 缩松:缩松是指铸件中存在的细小裂纹。
缩松会降低铸件的强度和韧性,使其易于断裂。
缩松的形成通常是由于金属液体在凝固过程中体积收缩而引起的。
为了避免缩松的产生,可以通过增加浇注温度和压力,以及优化铸型设计和浇注系统来减少金属液体的收缩。
5. 夹杂物:夹杂物是指铸件中存在的杂质和非金属物质。
夹杂物会降低铸件的强度和耐久性,导致其易于断裂。
夹杂物的形成通常是由于金属液体中的杂质和氧化物未能完全排除而引起的。
为了避免夹杂物的产生,可以通过改进金属液体的净化和过滤系统,以及优化浇注工艺和铸型设计来减少夹杂物的形成。
铸造过程中常见的缺陷包括气孔、疏松、砂眼、缩松和夹杂物。
这些缺陷会影响到铸件的质量和性能,因此在铸造过程中需要采取相应的措施来预防和解决这些问题。
- 1、下载文档前请自行甄别文档内容的完整性,平台不提供额外的编辑、内容补充、找答案等附加服务。
- 2、"仅部分预览"的文档,不可在线预览部分如存在完整性等问题,可反馈申请退款(可完整预览的文档不适用该条件!)。
- 3、如文档侵犯您的权益,请联系客服反馈,我们会尽快为您处理(人工客服工作时间:9:00-18:30)。
铸造铸件常见缺陷分析
铸造工艺过程复杂,影响铸件质量的因素很多,常见的铸件缺陷名称、特征和产生的原因,见表。
铸件质量与气孔的关系
1)合理选定铸造合金和铸件结构。
2)合理制定铸件技术要求(允许缺陷,具有规
定)。
3)模型质量检验(模型合格—铸件合格)
4)铸件质量检验(宏观,仪器)
5 铸件热处理: 消除应力,降低硬度,提高切削性,保证机械性能,退火,正火等。
1 破坏金属连续性
2 较少承载有效面积
3 气孔附近易引起应力集中,机械性能
4 弥散孔,气密性
侵入气孔,砂型材料表面聚集的气体侵入金属液体中而形成气体来源,造型材料中水分,粘结剂,各种附加物等.
气孔的特征: 多位于表面附近,尺寸较大,呈椭圆形或梨形孔的内表面被氧化。
气孔形成过程:
浇注---水汽(一部分由分型面,通气孔排出,另一部分在表面聚集呈高压中心点)—气压
升高,溶入金属---一部分从金属液中逸出—浇口,其余在铸件内部,形成气孔。
预防气孔的发生: 降低型砂(型芯砂)的发起量,增加铸型排气能力。
析出气孔: 溶于金属液中的气体在冷凝过程中,因气体溶解度下降而析出,使铸件形成气孔,原因: 金属熔化和浇注中与气体接触(H2 O2 NO CO等) 特征: 分布广,气孔尺寸甚小,影响气密性。
反应气孔: 金属液与铸型材料,型芯撑,冷铁或溶渣之间,因化学反应生成的气体而形成的气孔。
如: 冷铁有锈Fe3O4 + C –Fe +
CO 冷铁附近生成气孔防止: 冷铁型芯撑表面不得有锈蚀,油污,要干燥。
常见铸件缺陷及其预防措施。