铸件缺陷分类及解决方法
铸造缺陷及其对策

尺寸、重量与
铸件图样或技 术条件一部份在分型面处相互错位;
不符
错芯
由于砂芯在分型面处错位,使铸件内腔沿分型面 错开,一侧多肉,另一侧缺肉;
孔偏(偏 砂芯在金属液热作用、充型压力及浮力作用下, 芯、漂芯) 发生上抬、位移、漂浮甚至断裂,使铸件内孔位
置发生偏错,形状和尺寸不符合图面要求;
凹陷
铸件厚断面或断面交接处上平面塌陷;
4、残缺类缺陷
定义
缺陷名 称
特征
浇不到
铸件残缺,轮廓不完整,或轮廓虽完整,但边、 棱、角圆钝;
铸件由于各种
原因造成的外
形缺损缺陷的 总称
未浇满 跑水
铸件上部残缺,残缺部份边角呈圆形,浇注糸 统未充满;
铸件分型面以上部份残缺,残缺表面凹陷;
型漏(漏箱) 存在于铸件内的严重的空壳状残缺;
1、铸件内部缩孔可采用超声波探伤(UT)、射线探 伤(RT)或加工后用染色探伤法(PT)进行检验; 2、铸件表面的缩孔用肉眼可观察到。
3、形成原因:
1、合金的液态收缩和凝固收缩大于固态收缩,凝 固时间过长; 2、浇注温度不当,过高易产生缩孔,过低易产生 缩松和疏松; 3、浇注系统、冒口、冷铁设置不合理,铸件凝固 时得不到有效补缩; 4、铸件结构不合理; 5、砂箱、芯骨钢度差,型、芯紧实度和强度低而 不均,铸件易产生胀型、缩孔、缩松; 6、原材料的遗传性。
理后铁液停留、浇注、凝固时间过长而引起的铸铁石墨 球化率低或不球化缺陷;
三、案例
1.缩孔
缩孔
1、定义和特征:
1、铸件在凝固过程中因补缩不良而在热节或最 后凝固部位形成的宏观孔洞;
2、缩孔形状不规则,孔壁粗糙,常伴有粗大树枝 晶夹杂物、气孔、裂纹、偏析等缺陷;
铸造工艺流程中的铸件缺陷分析与改进策略

铸造工艺流程中的铸件缺陷分析与改进策略铸造工艺是一种重要的金属加工方法,用于制造各种形状的金属件。
然而,在铸造过程中,铸件缺陷是一个常见的问题,它会影响到铸件的质量和性能。
因此,对于铸造工艺流程中的铸件缺陷进行深入分析,并提出改进策略,对于提高铸件质量和工艺效率具有重要意义。
一、铸件缺陷的分类与原因分析在铸造工艺中,铸件缺陷可以分为表面缺陷和内部缺陷两类。
常见的表面缺陷包括气孔、砂眼、砂洞等;内部缺陷主要有夹杂物、孔洞、收缩系数不均匀等。
1.1 气孔气孔是铸造工艺中最常见的表面缺陷之一。
其形成的原因通常有两个方面,一是液态金属中溶解气体含量过高,二是在金属凝固过程中,气体生成而未能有效排除。
造成气孔的常见因素包括砂芯质量不佳、浇注温度过高、浇注速度过快等。
1.2 砂眼和砂洞砂眼是指铸件表面局部凹陷的缺陷,而砂洞是指铸件内部或边缘凹陷的缺陷。
主要原因包括模具缺陷、浇注系统设计不合理、浇注金属温度过低等。
1.3 夹杂物夹杂物是指铸件中存在的杂质,如炉渣、油污等。
其主要原因包括铁水净化不彻底、砂芯质量不佳等。
1.4 孔洞孔洞是指铸件内部存在的封闭空腔。
常见的孔洞形式包括气孔和收缩孔。
造成孔洞的原因主要有铁水中含气量高、铸型泥浆含水量高等。
1.5 收缩系数不均匀收缩系数不均匀是指铸件不同部位的收缩量不一致。
这可能会引起铸件的内部应力集中,从而导致开裂和变形。
收缩系数不均匀的原因包括铸造合金的特性、浇注温度的控制等。
二、改进策略为了减少铸件缺陷,提高铸件质量和工艺效率,以下是一些改进策略的具体措施:2.1 优化模具设计模具设计是影响铸件质量的关键因素之一。
通过优化模具结构、提高模具材料质量和表面光洁度,可以减少砂眼、砂洞等表面缺陷的产生。
2.2 控制浇注温度和速度浇注温度和速度对铸件质量有着直接的影响。
合理控制浇注温度和速度,可以降低气孔和夹杂物等缺陷的产生。
2.3 改进铸型材料和工艺选择合适的铸型材料,对铸件质量和工艺效率的提高至关重要。
常见压铸件缺陷解决方法
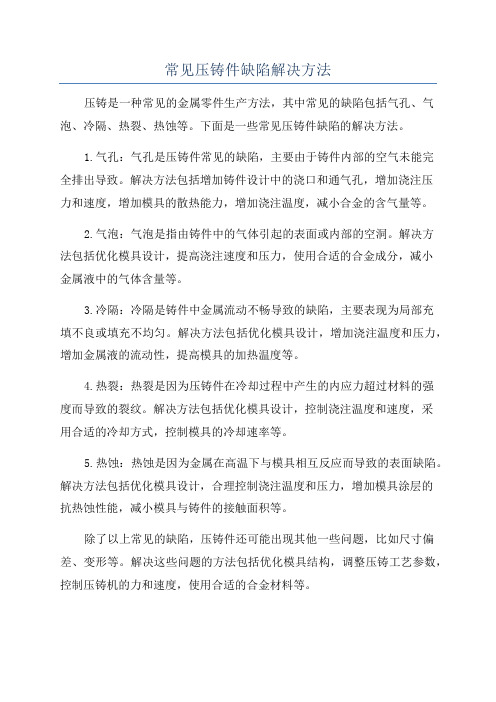
常见压铸件缺陷解决方法
压铸是一种常见的金属零件生产方法,其中常见的缺陷包括气孔、气泡、冷隔、热裂、热蚀等。
下面是一些常见压铸件缺陷的解决方法。
1.气孔:气孔是压铸件常见的缺陷,主要由于铸件内部的空气未能完
全排出导致。
解决方法包括增加铸件设计中的浇口和通气孔,增加浇注压
力和速度,增加模具的散热能力,增加浇注温度,减小合金的含气量等。
2.气泡:气泡是指由铸件中的气体引起的表面或内部的空洞。
解决方
法包括优化模具设计,提高浇注速度和压力,使用合适的合金成分,减小
金属液中的气体含量等。
3.冷隔:冷隔是铸件中金属流动不畅导致的缺陷,主要表现为局部充
填不良或填充不均匀。
解决方法包括优化模具设计,增加浇注温度和压力,增加金属液的流动性,提高模具的加热温度等。
4.热裂:热裂是因为压铸件在冷却过程中产生的内应力超过材料的强
度而导致的裂纹。
解决方法包括优化模具设计,控制浇注温度和速度,采
用合适的冷却方式,控制模具的冷却速率等。
5.热蚀:热蚀是因为金属在高温下与模具相互反应而导致的表面缺陷。
解决方法包括优化模具设计,合理控制浇注温度和压力,增加模具涂层的
抗热蚀性能,减小模具与铸件的接触面积等。
除了以上常见的缺陷,压铸件还可能出现其他一些问题,比如尺寸偏差、变形等。
解决这些问题的方法包括优化模具结构,调整压铸工艺参数,控制压铸机的力和速度,使用合适的合金材料等。
总的来说,解决压铸件缺陷的方法需要综合考虑材料、模具设计、工艺参数等多个因素,通过不断的实验和改进来提高铸件的质量。
常见压铸件缺陷及解决方法

常见压铸件缺陷及解决方法(总10页)--本页仅作为文档封面,使用时请直接删除即可----内页可以根据需求调整合适字体及大小--常见压铸件缺陷及解决方法一、流痕其他名称:条纹。
特征:铸件表面上呈现与金属液流动方向相一致的,用手感觉得出的局部下陷光滑纹路。
此缺陷无发展方向,用抛光法能去处。
产生原因:1、两股金属流不同步充满型腔而留下的痕迹。
2、模具温度低,如锌合金模温低于150℃,铝合金模温低于180℃,都易产生这类缺陷。
3、填充速度太高。
4、涂料用量过多。
排除措施:1、调整内浇口截面积或位置。
2、调整模具温度,增大溢流槽。
3、适当调整填充速度以改变金属液填充型腔的流态。
4、涂料使用薄而均匀。
二、冷隔,水纹其他名称:冷接(对接),水纹。
特征:温度较低的金属流互相对接但未熔合而出现的缝隙,呈不规则的线形,有穿透的和不穿透的两种,在外力的作用下有发展的趋势。
产生原因:1、金属液浇注温度低或模具温度低。
2、合金成分不符合标准,流动性差。
3、金属液分股填充,熔合不良。
4、浇口不合理,流程太长。
5、填充速度低或排气不良。
6、比压偏低。
排除措施:1、适当提高浇注温度和模具温度。
2、改变合金成分,提高流动性。
3、改进浇注系统,加大内浇口速度,改善填充条件。
4、改善排溢条件,增大溢流量。
5、提高压射速度,改善排气条件。
6、提高比压三、擦伤其他名称:拉力、拉痕、粘模伤痕。
特征:顺着脱模方向,由于金属粘附,模具制造斜度太小而造成铸件表面的拉伤痕迹,严重时成为拉伤面。
产生原因:1、型芯、型壁的铸造斜度太小或出现倒斜度。
2、型芯、型壁有压伤痕。
3、合金粘附模具。
4、铸件顶出偏斜,或型芯轴线偏斜。
5、型壁表面粗糙。
6、涂料常喷涂不到。
7、铝合金中含铁量低于%。
排除措施:1、修正模具,保证制造斜度。
2、打光压痕。
3、合理设计浇注系统,避免金属流对冲型芯、型壁,适当降低填充速度。
4、修正模具结构。
5、打光表面。
6、涂料用量薄而均匀,不能漏喷涂料。
压铸件常见缺陷及解决办法

压铸件常见缺陷及解决办法
1、尖角缺陷:表现为在压铸件的边缘和表面出现尖利的角,其
原因是模具的固定不牢,模具合模前没有铂精加光等操作,模具和表
面间的空隙较大,导致铸件连续流和溅射的金属物料的冷凝无法完全
填充到模具内。
解决办法是在压铸件的模具制作中要注意模具的固定,还要在合模前进行铂精加光,使模具缝隙尽量控制在最小。
2、翘曲缺陷:表现为铸件胚体过大或模具设计不当,导致部分
孔表面被填充的金属物料过度凝固后发生变形。
解决办法是提高铸件
的成型质量,在模具设计时应注意做到模具中高低正常,同时要增加
相应的引流装置,降低铸件表面在压铸过程中的温度,减少物料凝固
时间。
3、凹槽缺陷:表现为压铸件内壁或内孔出现浅深不均、粗糙凹槽,一般出现在内壁与模穴孔面间,其原因是模具合模时并未完全排
除空气,另外铸件内孔口位、形喉与内壁模穴间距过大,空气中的熔
融物料的细沙子难以充分清除也会导致此缺陷的产生。
解决办法是采
取真空压铸成型,即采用真空室和真空阀将空气真空,以消除空气;
另外应改变合模方式和模具设计,减少内孔口位与形喉与内壁模穴间距。
常见压铸件缺陷及解决方法
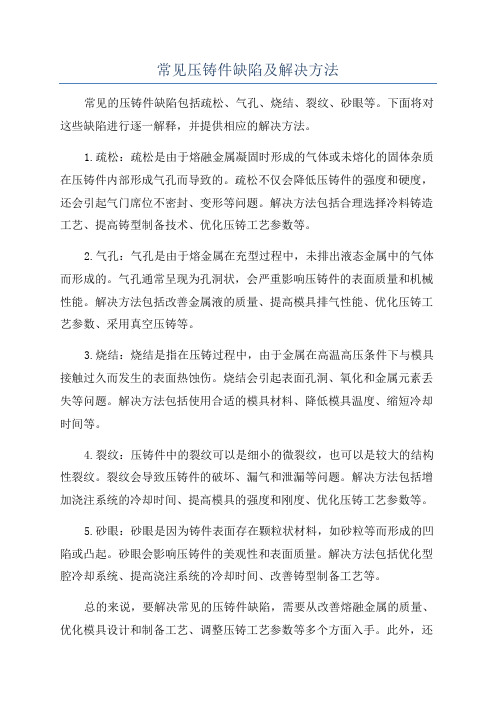
常见压铸件缺陷及解决方法常见的压铸件缺陷包括疏松、气孔、烧结、裂纹、砂眼等。
下面将对这些缺陷进行逐一解释,并提供相应的解决方法。
1.疏松:疏松是由于熔融金属凝固时形成的气体或未熔化的固体杂质在压铸件内部形成气孔而导致的。
疏松不仅会降低压铸件的强度和硬度,还会引起气门席位不密封、变形等问题。
解决方法包括合理选择冷料铸造工艺、提高铸型制备技术、优化压铸工艺参数等。
2.气孔:气孔是由于熔金属在充型过程中,未排出液态金属中的气体而形成的。
气孔通常呈现为孔洞状,会严重影响压铸件的表面质量和机械性能。
解决方法包括改善金属液的质量、提高模具排气性能、优化压铸工艺参数、采用真空压铸等。
3.烧结:烧结是指在压铸过程中,由于金属在高温高压条件下与模具接触过久而发生的表面热蚀伤。
烧结会引起表面孔洞、氧化和金属元素丢失等问题。
解决方法包括使用合适的模具材料、降低模具温度、缩短冷却时间等。
4.裂纹:压铸件中的裂纹可以是细小的微裂纹,也可以是较大的结构性裂纹。
裂纹会导致压铸件的破坏、漏气和泄漏等问题。
解决方法包括增加浇注系统的冷却时间、提高模具的强度和刚度、优化压铸工艺参数等。
5.砂眼:砂眼是因为铸件表面存在颗粒状材料,如砂粒等而形成的凹陷或凸起。
砂眼会影响压铸件的美观性和表面质量。
解决方法包括优化型腔冷却系统、提高浇注系统的冷却时间、改善铸型制备工艺等。
总的来说,要解决常见的压铸件缺陷,需要从改善熔融金属的质量、优化模具设计和制备工艺、调整压铸工艺参数等多个方面入手。
此外,还需要采用适当的检测手段,如金相分析、X射线检测、超声波检测等,对压铸件进行质量检验,及时排除可能存在的缺陷。
铝铸件常见缺陷及整改办法

铝铸件常见缺陷及整改办法铝铸件常见缺陷及整改办法1、欠铸(浇不足、轮廓不清、边角残缺):形成原因:(1)铝液流动性不强,液中含气量高,氧化皮较多。
(2)浇铸系统不良原因。
内浇口截面太小。
(3)排气条件不良原因。
排气不畅,涂料过多,模温过高导致型腔内气压高使气体不易排出。
防止办法:(1)提高铝液流动性,尤其是精炼和扒渣。
适当提高浇温和模温。
提高浇铸速度。
改进铸件结构,调整厚度余量,设辅助筋通道等。
(2)增大内浇口截面积。
(3)改善排气条件,增设液流槽和排气线,深凹型腔处开设排气塞。
使涂料薄而均匀,并待干燥后再合模。
2、裂纹:特征:毛坯被破坏或断开,形成细长裂缝,呈不规则线状,有穿透和不穿透二种,在外力作用下呈发展趋势。
冷、热裂的区别:冷裂缝处金属未被氧化,热裂缝处被氧化。
形成原因:(1)铸件结构欠合理,收缩受阻铸造圆角太小。
(2)顶出装置发生偏斜,受力不匀。
-(3)模温过低或过高,严重拉伤而开裂。
(4)合金中有害元素超标,伸长率下降。
防止方法:(1)改进铸件结构,减小壁厚差,增大圆角和圆弧R,设置工艺筋使截面变化平缓。
(2)修正模具。
(3)调整模温到工作温度,去除倒斜度和不平整现象,避免拉裂。
(4)控制好铝涂成份,成其是有害元素成份。
3、冷隔:特征:液流对接或搭接处有痕迹,其交接边缘圆滑,在外力作用下有继续发展趋势。
形成原因:(1)液流流动性差。
(2)液流分股填充融合不良或流程太长。
(3)填充温充太低或排气不良。
(4)充型压力不足。
防止方法:(1)适当提高铝液温度和模具温度,检查调整合金成份。
(2)使充填充分,合理布置溢流槽。
(3)提高浇铸速度,改善排气。
(4)增大充型压力。
4、凹陷:特征:在平滑表面上出现的凹陷部分。
形成原因:(1)铸件结构不合理,在局部厚实部位产生热节。
(2)合金收缩率大。
(3)浇口截面积太小。
(4)模温太高。
防止方法:(1)改进铸件结构,壁厚尽量均匀,多用过渡性连接,厚实部位可用镶件消除热节。
铸造工艺缺陷及解决措施
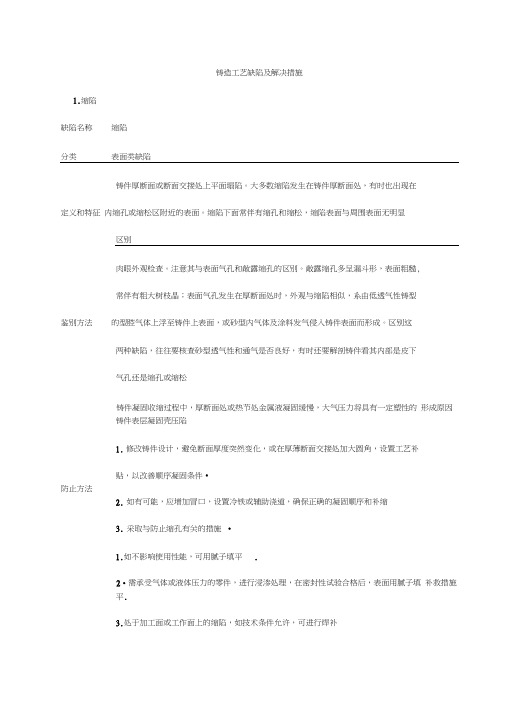
脉纹
分类
多肉类缺陷
定义和特征
鉴别方法
砂芯烘干时,若型砂剧烈收缩,易导致砂型表面开裂•
形成原因
避免加热时升温过快,控制烘干温度在250C左右,保证烘干加热均匀.
补救措施
概率因子
0.4
缺陷名称
脉纹
分类
鉴别方法
多肉类缺陷
定义和特征
型芯捣得过硬则膨胀产生的热应力大,易产生脉纹•
形成原因
造型,制芯时注意控制型砂的紧实度,在型砂中加入2%的氧化铁粉.
并加强孕育处理,降低铁液粘度,改善铁液流动性;采用挡渣效果好的浇包,浇注前铁
1 1
1
液在浇包中停留足够时间,使熔渣和夹杂物充分上浮,
2.采用保护性气氛熔炼和浇注镁合金,防止金属液氧化;浇注位置和浇注系统设置应保 证金属液迅速平稳充满型腔,缩短或中性气氛中浇注.
补救措施
概率因子
0.4
3.合金钢中的易氧化元素在浇注和充型过程中氧化
4.一般皱皮是由于液态金属粘度大,浇注温度低或浇注速度过慢,浇注过程中金属氧化, 金属液与型壁反应产生气体及金属型型温过低等原因所引起
1
1.用优质炉料熔炼球墨铸铁,降低原铁液含硫量及气体、夹杂物含量;在保证球化前提
1
防止方法
1
下减少加镁量以降低球墨铸铁残留镁量;调整铁液含碳量和碳当量,适当提高球化温度
铁件和镁合金铸件特有的缺陷,根据合金种类易与一般皱皮相区别
1
1.镁球墨铸铁在加镁处理时形成的化合物(氧化物、硫化物、硅酸盐等),通常以薄膜形
1
式分散在金属液中,在浇包中上浮缓慢,浇注时随金属液进入铸型,并上浮至铸件上表
形成原因
面,离心铸造时则聚集在铸件内壁,
- 1、下载文档前请自行甄别文档内容的完整性,平台不提供额外的编辑、内容补充、找答案等附加服务。
- 2、"仅部分预览"的文档,不可在线预览部分如存在完整性等问题,可反馈申请退款(可完整预览的文档不适用该条件!)。
- 3、如文档侵犯您的权益,请联系客服反馈,我们会尽快为您处理(人工客服工作时间:9:00-18:30)。
铸件缺陷分类及解决方法
4.1铸件缺陷分类
分为多肉类,孔洞类,裂纹,冷隔类,表面缺陷,残缺类,形状及重量差错类,夹杂类,性能,成分,组织不合格等八类缺陷.
4.2铸件缺陷分析
4.2.1多肉类缺陷
多肉类缺陷主要有飞翅(飞边,披峰),毛刺,抬型(抬箱)等.
飞翅与毛刺区别:飞翅主要产生的分型面等活动块结合处,通常垂直于铸件表面.又称飞边或披峰.毛刺指铸件表面形状不规则刺状突起.常出现在型,芯开裂处. 飞翅与毛刺的形成原因:飞翅形成主要是压射前机器的锁模力调整不佳导致分型面等活动块的配合不严;模具及滑块损坏,闭锁组件失效.毛刺形成主要是紧实度不均匀,浇注温度过高等致使开裂产生.
飞翅与毛刺的防止方法:飞翅是检查合模力或增压情况,调整压射增压机构,使压射增压峰值降低;检查模具滑块损坏程度并修整.毛刺的防止方法是浇注温度不宜过高,加大起模斜度等.
飞翅与毛刺的补救措施:轻微的用滚筒或喷丸清理,较厚的用铲,磨,冲切等方法去除.
抬型与飞翅区别:抬型是铸件在分型面部位高度增大,并伴有厚大飞翅;单纯飞翅厚度较薄,铸件分型面部位高度不增加.
4.2.2孔洞类缺陷
孔洞类缺陷主要有:气孔,针孔,缩孔,缩松和疏松.
针孔属于气孔的一种.气孔主要是指出现在铸件内部或表层,截面呈圆形,椭圆形,腰圆形,梨形或针头状,孤立存在或成群分布的孔洞.
气孔形成原因:炉料潮湿,锈蚀,油污,气候潮湿;浇注系统不合理;压室充满度不够;排气不畅;模具型腔位置太深;涂料成分不当或过多;金属液除渣不良等.
气孔的防止方法:坩锅等要充分预热和烘干;直浇道的喷嘴截面积应尽可能比内浇口截面积大;提高压室充满度;深腔处开设排气塞;重熔料的加入比例要适当;加强除渣,除气;充型速度不宜过高,浇注位置与浇注系统的设置应保证金属液平稳在充满型腔;适当提高浇注温度和铸型温度,合理设置排气塞和溢流槽等.
气孔的补救措施:超出验收标准时报废;单独大气孔焊补;成群小气孔可用浸渗处理方法填补,质量要求高的可采用热等静压处理法消除气孔.
缩松属于缩孔的一种,指细小的分散缩孔.
缩孔与气孔及缩松,疏松的区别:缩孔形状不规则,表面粗糙,产生在铸件热节和最后凝固部位,常伴有粗大树枝晶;气孔形状规则,表面光滑,分布在铸件表面或遍布整个铸件或某个局部,断口不呈海绵状;缩松与疏松断口呈海绵状,常产生在铸件厚大部位,不遍布整个铸件,缩松与疏松无严格分界,只是程度差别.
缩孔,缩松,疏松产生的原因:凝固时间过长;浇注温度不当,过高易产生缩孔,过低易产生缩松和疏松;凝固温度间隔过宽,易产生缩松和疏松;合金杂质过多;浇注系统设置不当;铸件结构不合理,壁厚变化突然;内浇道问题;合金杂质过多;模温问题.
缩孔,缩松,疏松的防止方法:改进铸型工艺设计;改进铸件结构设计;加强合金精炼;降低浇注温度和浇注速度,延长浇注时间.
缩孔,缩松,疏松的补救措施:焊补;浸渗;重要零件可进行热等静压处理.
4.2.3裂纹,冷隔类缺陷
裂纹,冷隔类缺陷主要有:冷裂,热裂,白点(发裂),冷隔等.
冷裂,热裂及白点的定义:冷裂指铸件凝固后冷却到弹性状态时,因铸件局部的铸造应力大于合金的极限强度而引起的裂纹.热裂是铸件在凝固末期或终凝后不久,铸件尚处于强度和塑性很低状态下,因铸件固态收缩受阻而引起的裂纹.白点是淬透性高的合金钢铸件在快速冷却时,因析出氢及产生较高的组织应力和热应力而引起的微细裂纹.
冷裂,热裂及白点(发裂)的区别:冷裂为穿晶裂纹,呈平直折线,常贯穿整个铸件截面;热裂为沿晶裂纹,呈较宽,粗细不均的不规则曲线,多发生在铸件壁厚突变和最后凝固部位;白点仅发生在超级合金及高淬透性钢中,裂纹微细,呈毛发状沿晶断裂,无方向性.在断口特征方面,冷裂一般有金属光泽;热裂氧化严重,无金属光泽;白点为银白色圆斑或椭圆斑,呈冰糖花样.
冷裂,热裂及白点的防止方法:改进铸件结构设计,壁厚力求均匀,平滑过渡,铸件内腔圆角够大,工艺设计合理,尽量减少铸件收缩阻力;适当降低浇注温度;提高模温;缩短开模及抽芯时间;严格控制有害杂质,锌合金降低铅,锡,镉,铁的含量,
铝合金降低锌,铜,铁的含量.
冷裂,热裂及白点的补救措施:冷裂允许焊补的铸件,焊后应进行消除应力处理;热裂铸件一般应报废,若允许焊补则应在彻底挖除缺陷区的金属后进行焊补,焊后应进行消除应力处理;白点致裂铸件应报废.
冷隔定义:冷隔是铸件上穿透或不穿透的缝隙,边缘呈圆角状,由充型金属流股汇合时熔合不良造成.
冷隔与裂纹类及未浇满的区别:冷隔铸件整体上是浇满的,与未浇满区别;冷隔边缘呈圆角状,可与裂纹类区别.
冷隔防止方法:减少金属液中的气体和氧化夹渣,提高金属液的流动性;提高浇注温度和浇注速度;提高充型速度;改变浇注位置和浇注系统;适当增加铸件薄壁部位的厚度;加强铸件排气.
4.2.4表面缺陷
表面缺陷主要有拉模,流痕,皱皮,缩陷,填充不良,气泡等.
拉模原因:型芯,型壁的铸造斜度太小或出现倒斜度;型芯,型壁有压伤痕;合金粘附模具;铸件顶出偏斜,或型芯轴线偏斜;型壁表面粗糙;涂料常涂喷不到;铝合金中含铁量低于0.6%.
拉模的改善措施:修正模具,保证制造斜度;打光型芯,型壁的压痕;修正模具结构(如顶出偏斜等);合理设计浇注系统避免金属流对冲型芯型壁,适当降低填充速度;打光型壁表面粗糙处;涂料用量薄而均匀;适当增加含铁量至0.6-0.8%.
流痕特征:铸件表面呈现与金属液流动方向相一致的,用物感觉得出的局部下陷光滑纹路.
流痕产生原因:两股金属流不同步充满型腔而留下的痕迹;模温低;填充速度太高;涂料用量过多.
流痕改善措施:调整内浇口截面积或位置;调整模温,增大溢流槽;调整填充整度以改变金属液填充型腔的流态;涂料使用薄面喷匀.
皱皮特征:铸件表面不规则的粗粒状或皱褶状疤痕,一般带有较深的网状沟槽. 缩陷指铸件厚断面或断面交接处上平面塌陷.缩陷下面常伴有缩孔和缩松.
缩陷产生原因:铸件结构设计不合理,有局部厚实部位,产生热节;合金收缩率大;内浇口截面积太小;比压低;模具温度太高.
缩陷防止方法:修改铸件设计,避免断面厚度突然变化,或在厚薄断面交接处加大圆角;选择收缩率小的合金;正确设置浇注系统,加大内浇口的截面积;增大压射力;调整模具热平衡条件,采用温控装置及冷却等.
填充不良的改善措施:改善合金的流动性(采用正确的熔炼工艺,排除气体及非金属夹杂物;适当提高浇注温度和模具温度;提高压射速度;补充氮气,提高有效压力;采用定量浇注;改进铸件结构,适当调整壁厚);改善浇注系统(正确选择浇口位置和导流方式;增大内浇口截面积和提高压射速度);改善排气条件(增设溢流槽和排气道,深凹型腔处可开设通气塞;涂料使用薄而均匀,吹干燃尽后合模;降低模温).
气泡产生原因:模具或汤料温度太高;填充速度太高,金属卷入气体过多;涂料发气量大,用量过多;排气不畅;开模过早.
气泡改善措施:冷却模具或汤料至适当温度;降低压射速度,避免涡流包气;选用发气量小的涂料,用量薄而均匀;清理和增设溢流槽和排气道;调整留模时间. 4.2.5残缺类缺陷
残缺类缺陷主要有浇不到,未浇满,损伤等.
浇不到与未浇满的区别:浇不到铸件的浇注系统是充满的,未浇满的浇注系统是未充满的.
损伤的形成原因:铸件结构不良;铸件在搬运,装卸过程中受撞击而损坏;铸件在机械加工时夹紧力和切削力过大;浇道,冒口,出气冒口截面积过大,与铸件本体连接处无缩颈或缩颈尺寸太大;圆角过小;敲除冒口方法不当;铸件强度和韧性差;铸件内部有较大残留应力或已有裂纹.
损伤的防止方法:改进铸件结构,避免薄弱结构,避免壁厚悬殊过大和尖角过渡;小心清理,存放,运输铸件;正确设计冒口;敲除冒口的方向和方法要正确;提高合金力学性能.
4.2.6形状及重量差错类缺陷
形状及重量差错类缺陷是指铸件的形状,尺寸,重量与铸件图样或技术条件的规定不符.主要有尺寸和重量差错,变形,错型(错箱),错芯,偏芯(漂芯),舂移等. 变形的改善措施:改进铸件结构,使壁厚均匀;确定最佳开模时间,加强铸件刚性;放大铸造斜度;小心取放铸件;合理堆放及去除浇口;合理布置推杆位置.
错型与错芯和舂移的区别:错型是铸件外形在分型面处错位,一侧多肉,另一侧缺肉;错芯是铸件内腔沿分芯面错位,一侧多肉,一侧缺肉;舂移是铸件外形在分型面附近局部突起,形成多肉,通常是单侧多肉,另一侧不缺肉.
错型的改善措施:合理设置内浇口;调整镶块加以紧固;更换导柱导套;进行修整,消除误差.
4.2.7夹杂类缺陷
夹杂类缺陷是铸件中各种金属和非金属夹杂物的总称,是最常见的缺陷之一.主要分为金属夹杂物和非金属夹杂物.常见的非金属夹杂物主要有夹渣和砂眼. 4.2.8性能,成分,组织不合格缺陷
常见的性能,成分,组织不合格缺陷分为两类,一类是物理性能,力学性能和化学成分不合格;另一类是组织异常.。