上引法无氧铜杆工艺
上引法生产线工艺流程说明
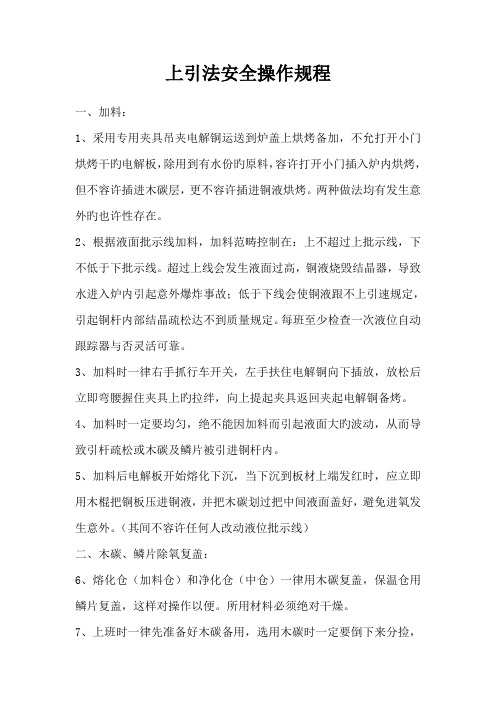
上引法安全操作规程一、加料:1、采用专用夹具吊夹电解铜运送到炉盖上烘烤备加,不允打开小门烘烤干旳电解板,除用到有水份旳原料,容许打开小门插入炉内烘烤,但不容许插进木碳层,更不容许插进铜液烘烤。
两种做法均有发生意外旳也许性存在。
2、根据液面批示线加料,加料范畴控制在:上不超过上批示线,下不低于下批示线。
超过上线会发生液面过高,铜液烧毁结晶器,导致水进入炉内引起意外爆炸事故;低于下线会使铜液跟不上引速规定,引起铜杆内部结晶疏松达不到质量规定。
每班至少检查一次液位自动跟踪器与否灵活可靠。
3、加料时一律右手抓行车开关,左手扶住电解铜向下插放,放松后立即弯腰握住夹具上旳拉绊,向上提起夹具返回夹起电解铜备烤。
4、加料时一定要均匀,绝不能因加料而引起液面大旳波动,从而导致引杆疏松或木碳及鳞片被引进铜杆内。
5、加料后电解板开始熔化下沉,当下沉到板材上端发红时,应立即用木棍把铜板压进铜液,并把木碳划过把中间液面盖好,避免进氧发生意外。
(其间不容许任何人改动液位批示线)二、木碳、鳞片除氧复盖:6、熔化仓(加料仓)和净化仓(中仓)一律用木碳复盖,保温仓用鳞片复盖,这样对操作以便。
所用材料必须绝对干燥。
7、上班时一律先准备好木碳备用,选用木碳时一定要倒下来分捡,捡去木碳中碳屑部分和铁钉,挑块子木碳装袋运上炉台备用。
8、干木碳容许直接投炉,但必须加在红木碳上面,待烧五分钟以上方可翻动木碳,以防冷木碳直接接触铜液引起铜液溅出伤人。
湿木碳一律装桶烧烤清除水份后方可进炉使用。
严禁湿木碳和湿度高旳树棍进炉使用,杜绝氢脆病旳缺陷发生。
9、净化仓木碳每两小时翻一次,每班至少加一次木碳,出一次灰;熔化仓要做到勤翻木碳,每班加两次木碳,出两次灰(具体状况根据木碳质量来定)。
同步一定要出完灰加好木碳才可交班。
班中和交接班时熔化仓和净化仓绝不容许有死灰存在。
炉中木碳厚度一般控制在八——十二公分之间。
启动炉门时人一定要偏开站立,用钩子拉开小炉门,避免一氧化碳忽然引爆伤人。
无氧铜生产工艺流程.
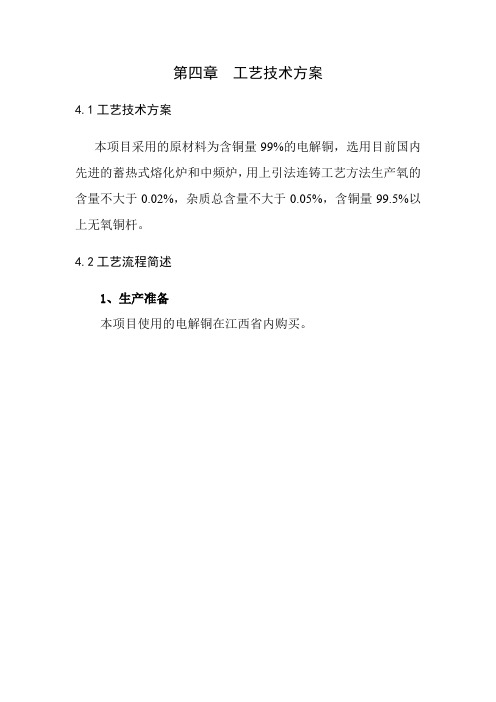
第四章工艺技术方案4.1工艺技术方案本项目采用的原材料为含铜量99%的电解铜,选用目前国内先进的蓄热式熔化炉和中频炉,用上引法连铸工艺方法生产氧的含量不大于0.02%,杂质总含量不大于0.05%,含铜量99.5%以上无氧铜杆。
4.2工艺流程简述1、生产准备本项目使用的电解铜在江西省内购买。
图4-1 项目生产工艺流程图2、上引法连铸工艺流程本项目采用上引法连铸工艺生产无氧铜杆。
上引法连铸铜杆的基本特点是“无氧”,即氧含量在10ppm以下。
上引法与连铸连轧和浸涂法相比,其特点是:1)由于拉扎工艺和铸造工艺不是连续的,拉扎是在常温下进行的,不需要气体保护,钢材也不会被氧化。
因此设备投资小,厂房布置也灵活。
2)单机产量变化范围大,年产量可以从几百吨到几万吨,可供不同规模的厂家选用不同型号的上引机组。
此外,由于连铸机是多头的,可以很容易的通过改变铸造规格(铸杆直径),来改变单位时间的产量,因此其产量可视原材料的供应情况和产品的需求情况来确定,便于组织生产、节约能源。
3)只需更换结晶器和改变石墨模的形状,即可生产铜管、铜排等异型铜材,并可在同一机器上上产不同规格、品种的铜材,灵活机动,这是上引法的中最大特点。
上引法连铸工艺流程:原料通过加料机加入融化炉进行熔化、氧化、扒渣处理后,熔融的铜液经过一段时间的静置还原脱氧并达到一定的温度后,通过有CO气体保护的流槽经过渡腔(铜液在此进一步还原脱氧、清除渣质),进而平稳的流入中频炉保温静置,铜液的温度由热电偶测量,温度值由仪表显示,温度控制在1150℃±10℃。
连铸机固定于中频保温炉的上方,连铸机铜液在结晶器中快速结晶连续不断地生产出铜杆,最后经双头挠杆机等辅助设备装盘成产品。
⑴加料:原料一般用加料机加入,炉头多加、炉尾少加。
加冷料时要使铜料距炉顶及烟道口有一定距离,以保证燃料燃烧和炉气流动的顺畅。
加料时要保证炉膛有足够高的温度,一般应达到1300℃以上,炉内应保证零压或微负压。
上引规程
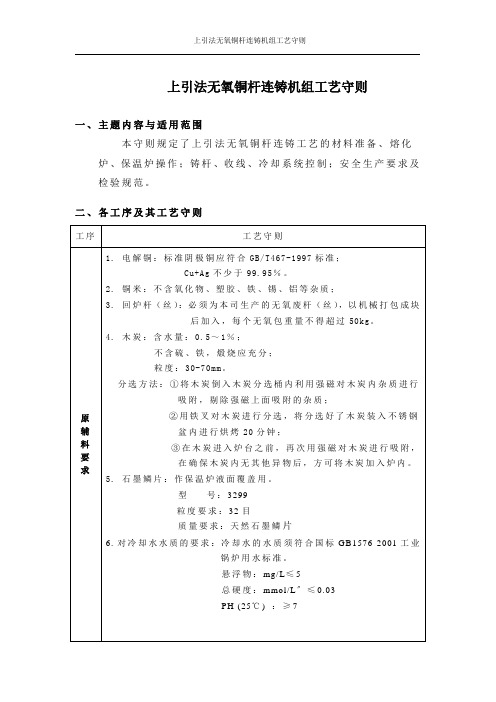
上引法无氧铜杆连铸机组工艺守则一、主题内容与适用范围本守则规定了上引法无氧铜杆连铸工艺的材料准备、熔化炉、保温炉操作;铸杆、收线、冷却系统控制;安全生产要求及检验规范。
二、各工序及其工艺守则工序工艺守则原辅料要求1. 电解铜:标准阴极铜应符合GB/T467-1997标准;Cu+Ag不少于99.95%。
2. 铜米:不含氧化物、塑胶、铁、锡、铝等杂质;3. 回炉杆(丝):必须为本司生产的无氧废杆(丝),以机械打包成块后加入,每个无氧包重量不得超过50kg。
4. 木炭:含水量:0.5~1%;不含硫、铁,煅烧应充分;粒度:30-70mm。
分选方法:①将木炭倒入木炭分选桶内利用强磁对木炭内杂质进行吸附,剔除强磁上面吸附的杂质;②用铁叉对木炭进行分选,将分选好了木炭装入不锈钢盆内进行烘烤20分钟;③在木炭进入炉台之前,再次用强磁对木炭进行吸附,在确保木炭内无其他异物后,方可将木炭加入炉内。
5.石墨鳞片:作保温炉液面覆盖用。
型号:3299粒度要求:32目质量要求:天然石墨鳞片6.对冷却水水质的要求:冷却水的水质须符合国标GB1576-2001工业锅炉用水标准。
悬浮物:mg/L≤5总硬度:mmol/L〞≤0.03PH (25℃) :≥7加料1.在加料前,须将合格的电解铜或回炉料在炉盖上预热10分钟左右,以除去原料表面的水分,电解铜表面铜绿应用砂纸清除,铜豆应予以切除;2.加料时,检查是否存在未熔尽的铜块,如有用木棒轻轻拨动,使之熔尽,然后用加料机构上的电动葫芦把整块电解铜板轻轻放入铜液内,并密切注意铜液温度、液位变化;3.加料频率以确保铜液液面高度为准,加料时间间隔一致。
少加、勤加减少铜液温度的变化。
以加料控制温度,以牵引速度控制液位高度,使加料量与出杆量保持平衡;4. 按生产要求,适当加入铜米和回炉料,若用回炉料或铜米需在每次加入电解铜后,待炉温升高后加入回炉料或铜米,加入量是此次加入电解铜量的5%~40%(具体以生产任务单为依据),在铜杆质量稳定合格前提下,回炉料、铜米可适当增加,但必须及时检测。
上引法操作工艺守则
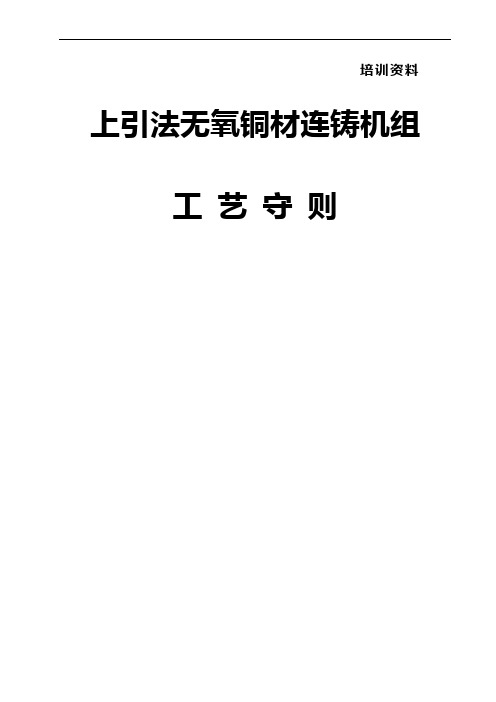
上引法无氧铜材连铸机组
工艺守则
一、主题内容与适用范围
本守则规定了上引法无氧铜材连铸工艺的材料准备、熔化炉(腔)、中间炉(腔)、保温炉(腔)操作;铸杆、收线、水系统、气源系统控制;安全生产要求及检验规范。
二、原材料、辅助材料技术要求
1.对原材料的技术要求:
1)对标准阴极铜技术要求:
由于上引法设备只进行熔化和铸造,因而不能对铜进行精炼,为了保证光亮无氧铜杆的质量,标准阴极铜应符合GB/T467-1997标准。
四、铸杆
1.结晶器准备
1)对新的和使用期超过半个月的结晶器,应进行检查,内管是否变形,密封圈是否已老化,污垢是否已清除,合格后进行水压试验,水压为1Mpa保持20分钟不漏水。1.8~2MPa保持10分钟,允许有轻微渗水。
2)准备装配石墨模时,应把结晶器内螺纹用标准丝锥,对丝牙回一遍,清除垃圾,把检验合格的石墨模,旋入结晶器,端面到位。
7)清灰工具必须涂上涂料,并烘干后使用,以防粘铜或铜液增铁。严禁将潮湿未烘干的工具浸入铜液,以免铜液爆炸,造成事故。
(1)涂料配方
石墨粉:25%~30%
水玻璃:5%
水:适量
(2)涂刷方法
当选用工具预热到150~200℃时将涂料涂刷或喷涂于用工具上,然后放于炉口烘干。
2.保温炉的操作
1)保温炉引杆腔铜液温度控制在:
若铜杆规格稍有改动,引速应作适当调整。
2)经常检查铜杆表面质量,观察结晶器、水套、线圈的进出水温度,及结晶器插入深度,液位跟踪系统工作状况,如遇异常情况,及时排除。
3)浮子要经常检查,随时调整。
五、收线
1.收线时将引锭头头部切除,将铜杆通过限位装置,穿过并夹紧收线导轮,引入收线盘内。
2.铜杆进入收线盘后,由于各铜杆之间有温度差异会产生弯曲,为保持排线整齐,可用木板轻轻拍齐。
无氧铜生产工艺流程
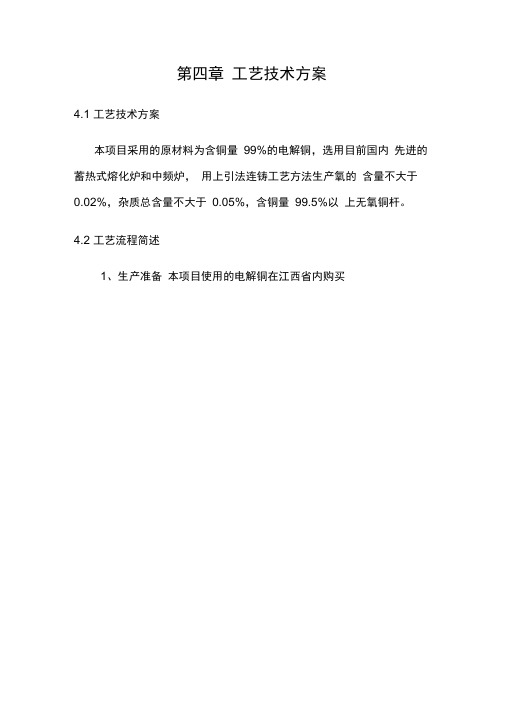
第四章工艺技术方案4.1 工艺技术方案本项目采用的原材料为含铜量99%的电解铜,选用目前国内先进的蓄热式熔化炉和中频炉,用上引法连铸工艺方法生产氧的含量不大于0.02%,杂质总含量不大于0.05%,含铜量99.5%以上无氧铜杆。
4.2 工艺流程简述1、生产准备本项目使用的电解铜在江西省内购买2、上引法连铸工艺流程本项目采用上引法连铸工艺生产无氧铜杆。
上引法连铸铜杆的基氧气烟囱图4-1 项目生产工艺流程图电解铜原料准备合格原料重油烟 1气-喷雾冷却-布袋收尘烟 尘中频炉烟气大气熔剂(副产还原脱氧、保温熔化炉结晶出杆 装盘无氧铜杆(外本特点是“无氧”,即氧含量在10pp m以下。
上引法与连铸连轧和浸涂法相比,其特点是:1)由于拉扎工艺和铸造工艺不是连续的,拉扎是在常温下进行的,不需要气体保护,钢材也不会被氧化。
因此设备投资小,厂房布置也灵活。
2)单机产量变化范围大,年产量可以从几百吨到几万吨,可供不同规模的厂家选用不同型号的上引机组。
此外,由于连铸机是多头的,可以很容易的通过改变铸造规格(铸杆直径),来改变单位时间的产量,因此其产量可视原材料的供应情况和产品的需求情况来确定,便于组织生产、节约能源。
3)只需更换结晶器和改变石墨模的形状,即可生产铜管、铜排等异型铜材,并可在同一机器上上产不同规格、品种的铜材,灵活机动,这是上引法的中最大特点。
上引法连铸工艺流程:原料通过加料机加入融化炉进行熔化、氧化、扒渣处理后,熔融的铜液经过一段时间的静置还原脱氧并达到一定的温度后,通过有CO气体保护的流槽经过渡腔(铜液在此进一步还原脱氧、清除渣质),进而平稳的流入中频炉保温静置,铜液的温度由热电偶测量,温度值由仪表显示,温度控制在1150C 土10C。
连铸机固定于中频保温炉的上方,连铸机铜液在结晶器中快速结晶连续不断地生产出铜杆,最后经双头挠杆机等辅助设备装盘成产品。
⑴加料:原料一般用加料机加入,炉头多加、炉尾少加。
上引法操作工艺守则
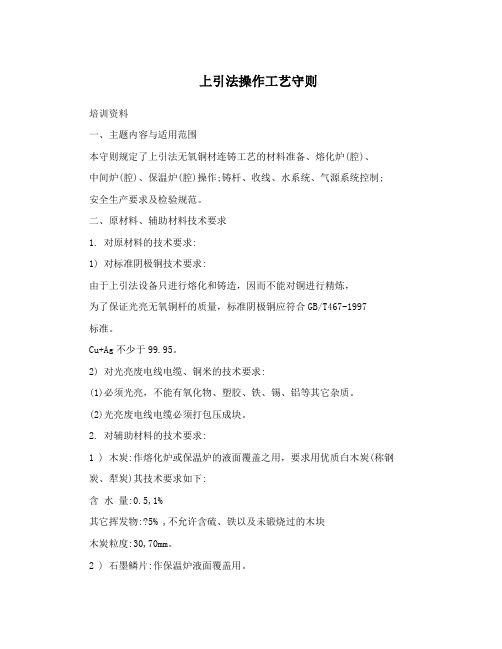
上引法操作工艺守则培训资料一、主题内容与适用范围本守则规定了上引法无氧铜材连铸工艺的材料准备、熔化炉(腔)、中间炉(腔)、保温炉(腔)操作;铸杆、收线、水系统、气源系统控制; 安全生产要求及检验规范。
二、原材料、辅助材料技术要求1. 对原材料的技术要求:1) 对标准阴极铜技术要求:由于上引法设备只进行熔化和铸造,因而不能对铜进行精炼,为了保证光亮无氧铜杆的质量,标准阴极铜应符合GB/T467-1997标准。
Cu+Ag不少于99.95。
2) 对光亮废电线电缆、铜米的技术要求:(1)必须光亮,不能有氧化物、塑胶、铁、锡、铝等其它杂质。
(2)光亮废电线电缆必须打包压成块。
2. 对辅助材料的技术要求:1 ) 木炭:作熔化炉或保温炉的液面覆盖之用,要求用优质白木炭(称钢炭、犁炭)其技术要求如下:含水量:0.5,1%其它挥发物:?5% ,不允许含硫、铁以及未锻烧过的木块木炭粒度:30,70mm。
2 ) 石墨鳞片:作保温炉液面覆盖用。
型号:3299粒度要求:32目?1?质量要求:天然石墨鳞片3. 对冷却水水质的要求:冷却水的水质须符合中国国标GB1576-2001工业锅炉用水标准。
悬浮物:mg/L?5总硬度:mmol/L〞?0.03PH (25?) :?7三、连体炉、组合炉的操作1. 熔化炉的操作1) 炉料为合格电解铜及干净、无油腻的本机组生产的回炉铜杆(丝)。
(回炉铜杆、丝须经机械打包压块,块重30kg左右) 2) 将合格的电解铜及回炉铜杆(丝)置炉盖上预热10分钟左右,以去除表面水份,电解铜表面绿色附着物应用铁刷清除。
3) 加料时,打开炉盖检查是否存在未熔尽的铜块,如有用木棒轻轻拨动,使之熔尽,然后用加料机构上的电动葫芦把整块电解铜板轻轻放入铜液内,完全熔化后关闭炉盖,并密切注意大屏幕显示器上的铜液温度变化。
4) 加入电解铜,若用回炉料需在每次加入电解铜后,待炉温升高后加入回炉料,加入量是此次加入电解铜量的10%,30%,在铜杆质量稳定合格前提下,回炉料可适当增加,但必须及时检测。
无氧铜生产工艺流程图

第四章工艺技术方案4.1工艺技术方案本项目采用的原材料为含铜量99%的电解铜,选用目前国内先进的蓄热式熔化炉和中频炉,用上引法连铸工艺方法生产氧的含量不大于0.02%,杂质总含量不大于0.05%,含铜量99.5%以上无氧铜杆。
4.2工艺流程简述1、生产准备本项目使用的电解铜在江西省内购买。
图4-1 项目生产工艺流程图2、上引法连铸工艺流程本项目采用上引法连铸工艺生产无氧铜杆。
上引法连铸铜杆的基本特点是“无氧”,即氧含量在10ppm以下。
上引法与连铸连轧和浸涂法相比,其特点是:1)由于拉扎工艺和铸造工艺不是连续的,拉扎是在常温下进行的,不需要气体保护,钢材也不会被氧化。
因此设备投资小,厂房布置也灵活。
2)单机产量变化范围大,年产量可以从几百吨到几万吨,可供不同规模的厂家选用不同型号的上引机组。
此外,由于连铸机是多头的,可以很容易的通过改变铸造规格(铸杆直径),来改变单位时间的产量,因此其产量可视原材料的供应情况和产品的需求情况来确定,便于组织生产、节约能源。
3)只需更换结晶器和改变石墨模的形状,即可生产铜管、铜排等异型铜材,并可在同一机器上上产不同规格、品种的铜材,灵活机动,这是上引法的中最大特点。
上引法连铸工艺流程:原料通过加料机加入融化炉进行熔化、氧化、扒渣处理后,熔融的铜液经过一段时间的静置还原脱氧并达到一定的温度后,通过有CO气体保护的流槽经过渡腔(铜液在此进一步还原脱氧、清除渣质),进而平稳的流入中频炉保温静置,铜液的温度由热电偶测量,温度值由仪表显示,温度控制在1150℃±10℃。
连铸机固定于中频保温炉的上方,连铸机铜液在结晶器中快速结晶连续不断地生产出铜杆,最后经双头挠杆机等辅助设备装盘成产品。
⑴加料:原料一般用加料机加入,炉头多加、炉尾少加。
加冷料时要使铜料距炉顶及烟道口有一定距离,以保证燃料燃烧和炉气流动的顺畅。
加料时要保证炉膛有足够高的温度,一般应达到1300℃以上,炉内应保证零压或微负压。
无氧铜杆的生产方法
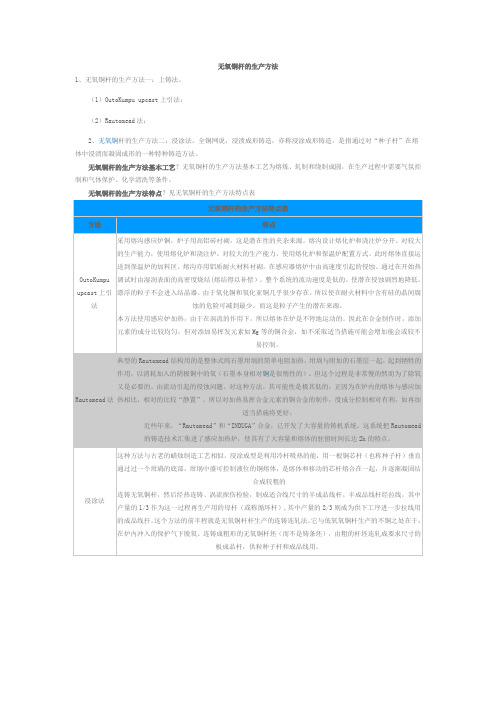
无氧铜杆的生产方法1、无氧铜杆的生产方法一:上铸法。
(1)OutoKumpu upcast上引法:(2)Rautomead法:2、无氧铜杆的生产方法二:浸涂法。
全铜网说,浸渍成形铸造,亦称浸涂成形铸造,是指通过对“种子杆”在熔体中浸渍而凝固成形的一种特种铸造方法。
无氧铜杆的生产方法基本工艺?无氧铜杆的生产方法基本工艺为熔炼、轧制和绕制成圆,在生产过程中需要气氛控制和气体保护、化学清洗等条件。
无氧铜杆的生产方法特点?见无氧铜杆的生产方法特点表Rautomead铸机截面图无氧铜杆的生产方法优势?性能优良,工艺先进,生产效率高并节约能源,不需酸洗。
此外,能减少加工工序,而且铜的损耗率低。
无氧铜杆的生产方法之冶金化学反应?1、阴极铜予处理阶段,阴极铜加入熔化炉前,如在预热炉热(700*c左右)。
此时铜板表面存在的胆矾和碱碳酸铜及水分发生离解和蒸发,其反应式如下CuSO4·5H2O→CuO+SO2↑+H2O↑CuCO3·Cu(OH)2250~270℃→CuCO3+CuO+H2O↑CuCO3560~600℃→CuO+CO2↑H2O(液)→H2O(汽)↑2、阴极铜加入炉内熔化,对浸涂法,铜板加入工频感应熔化炉内,熔体在电磁感应作用下不断运动,铜液中杂质元素间及碳层和保护氨气中的氢元素之间(一般木炭覆盖层厚100~150mm;炉内充入含有2%氢的氮气会发生一系列化学反应,如下4CuO1025℃→2Cu2O+O2↑4Cu+O2≡2Cu2OCu2O+Me←→MeO(造渣)+2Cu(Me—金属杂质)2Cu2O+Cu2S≡6Cu+SO2↑Cu2O+H2≡2Cu+HO2↑Cu2S+H2←→2Cu+H2S↑2Cu2O+C≡4Cu+CO2↑SO2+C≡S+CO2↑2Me+C≡2Me+CO2↑无氧铜杆无氧铜杆的生产方法之生产线参数?下面说的是浸涂法的生产线参数。
1、表格化:现场工艺控制。
现代化生产线的有效管理方法之一,是采取表格化的形式,实行现场工艺控制。
- 1、下载文档前请自行甄别文档内容的完整性,平台不提供额外的编辑、内容补充、找答案等附加服务。
- 2、"仅部分预览"的文档,不可在线预览部分如存在完整性等问题,可反馈申请退款(可完整预览的文档不适用该条件!)。
- 3、如文档侵犯您的权益,请联系客服反馈,我们会尽快为您处理(人工客服工作时间:9:00-18:30)。
上引法无氧铜杆工艺
随着工业的发展,铜杆作为一种重要的电气导体材料,应用范围越来越广泛。
在电力、通讯、航空航天等领域,铜杆都扮演着不可或缺的角色。
而在铜杆的生产过程中,无氧铜杆的生产工艺尤为重要。
无氧铜杆是指不含氧化铜的铜杆,其电导率、延展性和强度等性能都比普通铜杆优异。
无氧铜杆的生产工艺主要有两种,一种是连铸法,另一种是上引法。
本文将介绍上引法无氧铜杆的生产工艺。
上引法无氧铜杆工艺是在真空或惰性气氛下进行的一种铜杆生
产工艺。
其特点是熔化铜材后通过铜杆上引的方式进行成杆。
这种工艺可以避免铜杆表面氧化,保证铜杆的纯度和性能。
工艺流程如下:
1.原材料准备:选择高纯度的电解铜作为原材料,并进行化验检测,确保其化学成分符合要求。
2.熔炼:将原材料放入熔炉中进行熔炼。
熔炉采用电炉或气炉,熔化温度一般在1100℃左右。
在熔炼过程中,要注意控制熔炉内部的气氛,避免铜材表面氧化。
3.上引成杆:将熔化的铜液通过铜杆上引的方式进行成杆。
上引成杆一般采用真空或惰性气氛,以保证铜杆表面不受氧化影响。
在上引成杆的过程中,要注意控制成杆速度和杆径,以保证铜杆的质量和性能。
4.拉拔:将成杆的铜杆进行拉拔,以达到所需的直径和长度。
拉拔过程中,要注意控制拉拔速度和拉拔力度,以保证铜杆的延展性和
强度。
5.清洗和包装:将拉拔好的铜杆进行清洗和包装,以保证铜杆表面干净无污染,并防止铜杆在运输和储存过程中受到损坏。
上引法无氧铜杆工艺具有以下优点:
1.生产出的铜杆纯度高,性能优异。
2.工艺流程简单,易于控制。
3.生产效率高,能够满足大规模生产的需求。
4.铜杆表面干净无污染,不会对后续加工和使用产生影响。
总之,上引法无氧铜杆工艺是一种优异的铜杆生产工艺。
它可以生产出高纯度、高性能的无氧铜杆,广泛应用于电力、通讯、航空航天等领域。
在实际生产中,要注意控制工艺参数和操作技术,以保证铜杆的质量和性能。