无氧铜杆生产工艺流程
上引法无氧铜杆工艺
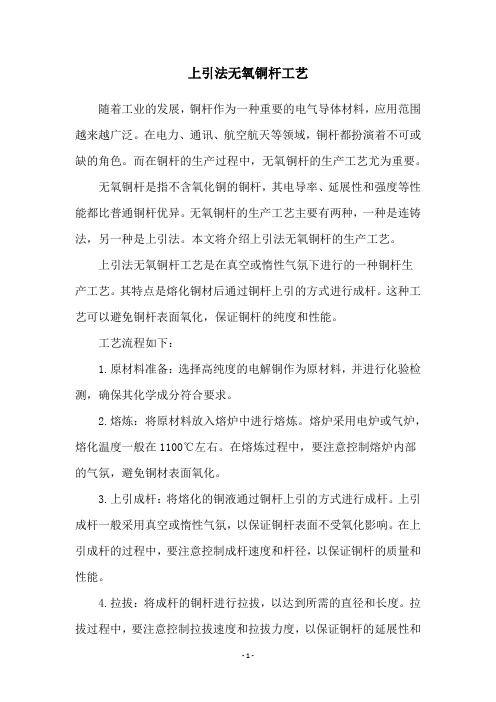
上引法无氧铜杆工艺随着工业的发展,铜杆作为一种重要的电气导体材料,应用范围越来越广泛。
在电力、通讯、航空航天等领域,铜杆都扮演着不可或缺的角色。
而在铜杆的生产过程中,无氧铜杆的生产工艺尤为重要。
无氧铜杆是指不含氧化铜的铜杆,其电导率、延展性和强度等性能都比普通铜杆优异。
无氧铜杆的生产工艺主要有两种,一种是连铸法,另一种是上引法。
本文将介绍上引法无氧铜杆的生产工艺。
上引法无氧铜杆工艺是在真空或惰性气氛下进行的一种铜杆生产工艺。
其特点是熔化铜材后通过铜杆上引的方式进行成杆。
这种工艺可以避免铜杆表面氧化,保证铜杆的纯度和性能。
工艺流程如下:1.原材料准备:选择高纯度的电解铜作为原材料,并进行化验检测,确保其化学成分符合要求。
2.熔炼:将原材料放入熔炉中进行熔炼。
熔炉采用电炉或气炉,熔化温度一般在1100℃左右。
在熔炼过程中,要注意控制熔炉内部的气氛,避免铜材表面氧化。
3.上引成杆:将熔化的铜液通过铜杆上引的方式进行成杆。
上引成杆一般采用真空或惰性气氛,以保证铜杆表面不受氧化影响。
在上引成杆的过程中,要注意控制成杆速度和杆径,以保证铜杆的质量和性能。
4.拉拔:将成杆的铜杆进行拉拔,以达到所需的直径和长度。
拉拔过程中,要注意控制拉拔速度和拉拔力度,以保证铜杆的延展性和强度。
5.清洗和包装:将拉拔好的铜杆进行清洗和包装,以保证铜杆表面干净无污染,并防止铜杆在运输和储存过程中受到损坏。
上引法无氧铜杆工艺具有以下优点:1.生产出的铜杆纯度高,性能优异。
2.工艺流程简单,易于控制。
3.生产效率高,能够满足大规模生产的需求。
4.铜杆表面干净无污染,不会对后续加工和使用产生影响。
总之,上引法无氧铜杆工艺是一种优异的铜杆生产工艺。
它可以生产出高纯度、高性能的无氧铜杆,广泛应用于电力、通讯、航空航天等领域。
在实际生产中,要注意控制工艺参数和操作技术,以保证铜杆的质量和性能。
无氧铜生产工艺流程.
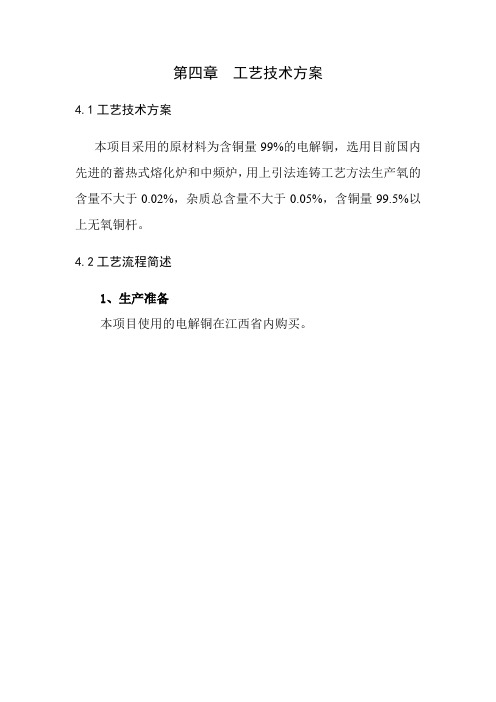
第四章工艺技术方案4.1工艺技术方案本项目采用的原材料为含铜量99%的电解铜,选用目前国内先进的蓄热式熔化炉和中频炉,用上引法连铸工艺方法生产氧的含量不大于0.02%,杂质总含量不大于0.05%,含铜量99.5%以上无氧铜杆。
4.2工艺流程简述1、生产准备本项目使用的电解铜在江西省内购买。
图4-1 项目生产工艺流程图2、上引法连铸工艺流程本项目采用上引法连铸工艺生产无氧铜杆。
上引法连铸铜杆的基本特点是“无氧”,即氧含量在10ppm以下。
上引法与连铸连轧和浸涂法相比,其特点是:1)由于拉扎工艺和铸造工艺不是连续的,拉扎是在常温下进行的,不需要气体保护,钢材也不会被氧化。
因此设备投资小,厂房布置也灵活。
2)单机产量变化范围大,年产量可以从几百吨到几万吨,可供不同规模的厂家选用不同型号的上引机组。
此外,由于连铸机是多头的,可以很容易的通过改变铸造规格(铸杆直径),来改变单位时间的产量,因此其产量可视原材料的供应情况和产品的需求情况来确定,便于组织生产、节约能源。
3)只需更换结晶器和改变石墨模的形状,即可生产铜管、铜排等异型铜材,并可在同一机器上上产不同规格、品种的铜材,灵活机动,这是上引法的中最大特点。
上引法连铸工艺流程:原料通过加料机加入融化炉进行熔化、氧化、扒渣处理后,熔融的铜液经过一段时间的静置还原脱氧并达到一定的温度后,通过有CO气体保护的流槽经过渡腔(铜液在此进一步还原脱氧、清除渣质),进而平稳的流入中频炉保温静置,铜液的温度由热电偶测量,温度值由仪表显示,温度控制在1150℃±10℃。
连铸机固定于中频保温炉的上方,连铸机铜液在结晶器中快速结晶连续不断地生产出铜杆,最后经双头挠杆机等辅助设备装盘成产品。
⑴加料:原料一般用加料机加入,炉头多加、炉尾少加。
加冷料时要使铜料距炉顶及烟道口有一定距离,以保证燃料燃烧和炉气流动的顺畅。
加料时要保证炉膛有足够高的温度,一般应达到1300℃以上,炉内应保证零压或微负压。
无氧铜铜杆工艺流程
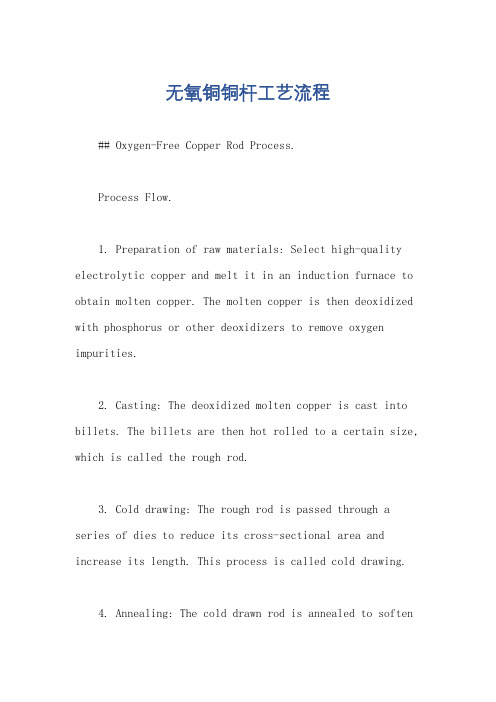
无氧铜铜杆工艺流程## Oxygen-Free Copper Rod Process.Process Flow.1. Preparation of raw materials: Select high-quality electrolytic copper and melt it in an induction furnace to obtain molten copper. The molten copper is then deoxidized with phosphorus or other deoxidizers to remove oxygen impurities.2. Casting: The deoxidized molten copper is cast into billets. The billets are then hot rolled to a certain size, which is called the rough rod.3. Cold drawing: The rough rod is passed through a series of dies to reduce its cross-sectional area and increase its length. This process is called cold drawing.4. Annealing: The cold drawn rod is annealed to softenit and remove internal stresses. Annealing is done by heating the rod to a certain temperature and then cooling it slowly.5. Pickling: The annealed rod is pickled in an acid solution to remove any oxide layer or other impurities on the surface.6. Drawing to the finished size: The pickled rod is drawn to the desired finished size. This process is done by passing the rod through a series of dies.7. Inspection: The finished rod is inspected to ensure that it meets the required specifications.8. Packing and storage: The finished rod is packed and stored in a clean and dry environment.## 无氧铜铜杆工艺流程。
无氧铜生产工艺流程
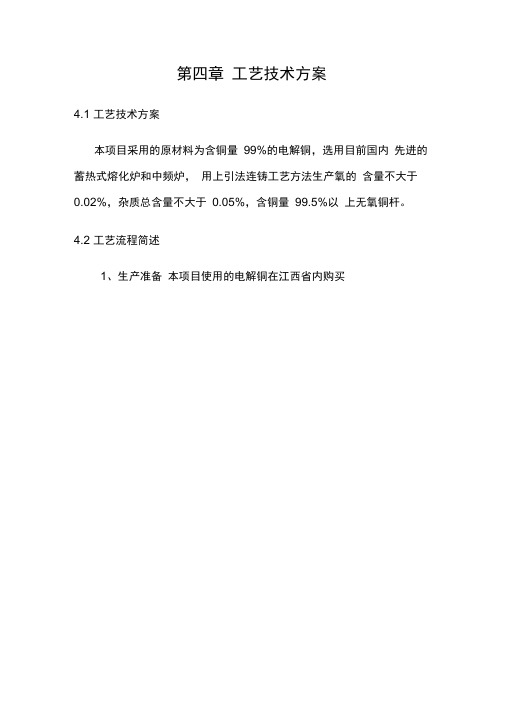
第四章工艺技术方案4.1 工艺技术方案本项目采用的原材料为含铜量99%的电解铜,选用目前国内先进的蓄热式熔化炉和中频炉,用上引法连铸工艺方法生产氧的含量不大于0.02%,杂质总含量不大于0.05%,含铜量99.5%以上无氧铜杆。
4.2 工艺流程简述1、生产准备本项目使用的电解铜在江西省内购买2、上引法连铸工艺流程本项目采用上引法连铸工艺生产无氧铜杆。
上引法连铸铜杆的基氧气烟囱图4-1 项目生产工艺流程图电解铜原料准备合格原料重油烟 1气-喷雾冷却-布袋收尘烟 尘中频炉烟气大气熔剂(副产还原脱氧、保温熔化炉结晶出杆 装盘无氧铜杆(外本特点是“无氧”,即氧含量在10pp m以下。
上引法与连铸连轧和浸涂法相比,其特点是:1)由于拉扎工艺和铸造工艺不是连续的,拉扎是在常温下进行的,不需要气体保护,钢材也不会被氧化。
因此设备投资小,厂房布置也灵活。
2)单机产量变化范围大,年产量可以从几百吨到几万吨,可供不同规模的厂家选用不同型号的上引机组。
此外,由于连铸机是多头的,可以很容易的通过改变铸造规格(铸杆直径),来改变单位时间的产量,因此其产量可视原材料的供应情况和产品的需求情况来确定,便于组织生产、节约能源。
3)只需更换结晶器和改变石墨模的形状,即可生产铜管、铜排等异型铜材,并可在同一机器上上产不同规格、品种的铜材,灵活机动,这是上引法的中最大特点。
上引法连铸工艺流程:原料通过加料机加入融化炉进行熔化、氧化、扒渣处理后,熔融的铜液经过一段时间的静置还原脱氧并达到一定的温度后,通过有CO气体保护的流槽经过渡腔(铜液在此进一步还原脱氧、清除渣质),进而平稳的流入中频炉保温静置,铜液的温度由热电偶测量,温度值由仪表显示,温度控制在1150C 土10C。
连铸机固定于中频保温炉的上方,连铸机铜液在结晶器中快速结晶连续不断地生产出铜杆,最后经双头挠杆机等辅助设备装盘成产品。
⑴加料:原料一般用加料机加入,炉头多加、炉尾少加。
无氧铜杆连铸连轧生产线
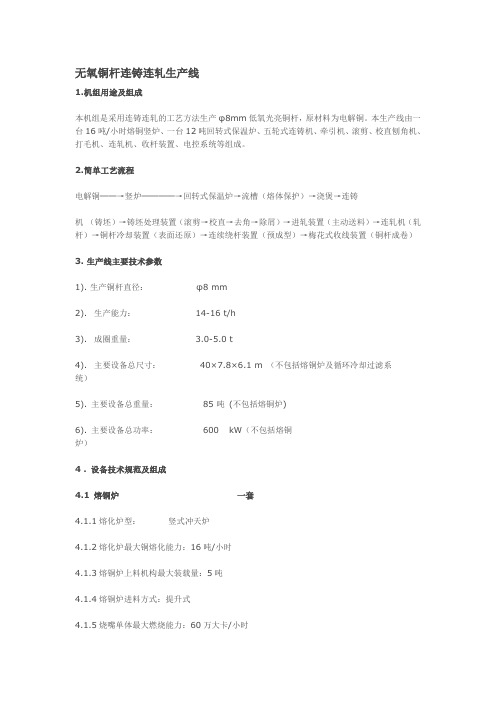
无氧铜杆连铸连轧生产线1.机组用途及组成本机组是采用连铸连轧的工艺方法生产φ8mm低氧光亮铜杆,原材料为电解铜。
本生产线由一台16吨/小时熔铜竖炉、一台12吨回转式保温炉、五轮式连铸机、牵引机、滚剪、校直刨角机、打毛机、连轧机、收杆装置、电控系统等组成。
2.简单工艺流程电解铜──→竖炉────→回转式保温炉→流槽(熔体保护)→浇煲→连铸机(铸坯)→铸坯处理装置(滚剪→校直→去角→除屑)→进轧装置(主动送料)→连轧机(轧杆)→铜杆冷却装置(表面还原)→连续绕杆装置(预成型)→梅花式收线装置(铜杆成卷)3. 生产线主要技术参数1). 生产铜杆直径:φ8 mm2). 生产能力:14-16 t/h3). 成圈重量: 3.0-5.0 t4). 主要设备总尺寸: 40×7.8×6.1 m (不包括熔铜炉及循环冷却过滤系统)5). 主要设备总重量: 85 吨(不包括熔铜炉)6). 主要设备总功率: 600 kW(不包括熔铜炉)4 .设备技术规范及组成4.1熔铜炉一套4.1.1熔化炉型:竖式冲天炉4.1.2熔化炉最大铜熔化能力:16吨/小时4.1.3熔铜炉上料机构最大装载量:5吨4.1.4熔铜炉进料方式:提升式4.1.5烧嘴单体最大燃烧能力:60万大卡/小时4.1.6熔铜炉烧嘴数量:15只4.1.7烧嘴冷却方式:水冷4.1.8烧嘴点火方式:自动4.1.9使用燃料:天然气、液化气、城市煤气4.1.10保温炉炉型:液压回转式4.1.11保温炉有效容量:12吨4.1.12保温炉最高倾力角度:>70º4.1.13烧嘴单体最大燃烧能力:60万大卡/小时4.1.14保温炉烧嘴数量:1只4.1.15燃烧控制方式:比例燃烧,具有保护装置4.1.16燃气阀检漏方式:手动/自动熔铜炉包括冲天式铜熔化炉、回转式保温炉、上下流槽、燃烧控制系统等四大部分。
具有熔化速度快、铜水含氧量低、流量连续可调、铜水温度独立可控、单位铜水燃气消耗量低等特点。
无氧铜杆连铸连轧生产线
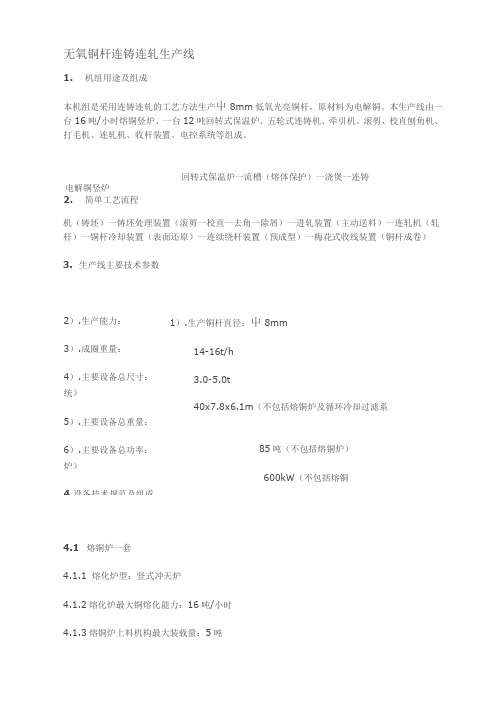
电解铜竖炉回转式保温炉一流槽(熔体保护)一浇煲一连铸2).生产能力:3).成圈重量:4).主要设备总尺寸:统) 5).主要设备总重量:6).主要设备总功率:炉)4.设备技术规范及组成 无氧铜杆连铸连轧生产线1. 机组用途及组成本机组是采用连铸连轧的工艺方法生产屮8mm 低氧光亮铜杆,原材料为电解铜。
本生产线由一台16吨/小时熔铜竖炉、一台12吨回转式保温炉、五轮式连铸机、牵引机、滚剪、校直刨角机、打毛机、连轧机、收杆装置、电控系统等组成。
2. 简单工艺流程机(铸坯)一铸坯处理装置(滚剪一校直一去角一除屑)一进轧装置(主动送料)一连轧机(轧杆)一铜杆冷却装置(表面还原)一连续绕杆装置(预成型)一梅花式收线装置(铜杆成卷)3. 生产线主要技术参数1).生产铜杆直径:屮8mm 14-16t/h 3.0-5.0t40x7.8x6.1m (不包括熔铜炉及循环冷却过滤系85吨(不包括熔铜炉)600kW (不包括熔铜4.1 熔铜炉一套4.1.1 熔化炉型:竖式冲天炉4.1.2熔化炉最大铜熔化能力:16吨/小时4.1.3熔铜炉上料机构最大装载量:5吨4.1.4熔铜炉进料方式:提升式4.1.5烧嘴单体最大燃烧能力:60万大卡/小时4.1.6熔铜炉烧嘴数量:15只4.1.7烧嘴冷却方式:水冷4.1.8烧嘴点火方式:自动4.1.9使用燃料:天然气、液化气、城市煤气4.1.10保温炉炉型:液压回转式4.1.11保温炉有效容量:12吨4.1.12保温炉最高倾力角度:>70。
4.1.13烧嘴单体最大燃烧能力:60万大卡/小时4.1.14保温炉烧嘴数量:1只4.1.15燃烧控制方式:比例燃烧,具有保护装置4.1.16燃气阀检漏方式:手动/自动熔铜炉包括冲天式铜熔化炉、回转式保温炉、上下流槽、燃烧控制系统等四大部分。
具有熔化速度快、铜水含氧量低、流量连续可调、铜水温度独立可控、单位铜水燃气消耗量低等特点。
①冲天式铜熔化炉(竖炉)熔化炉简称竖炉,由炉底、炉身、碰撞保护块、加料口、上料机构、烟囱、炉衬和冷却风机等部分组成。
无氧铜杆的生产方法
无氧铜杆的生产方法1、无氧铜杆的生产方法一:上铸法。
(1)OutoKumpu upcast上引法:(2)Rautomead法:2、无氧铜杆的生产方法二:浸涂法。
全铜网说,浸渍成形铸造,亦称浸涂成形铸造,是指通过对“种子杆”在熔体中浸渍而凝固成形的一种特种铸造方法。
无氧铜杆的生产方法基本工艺?无氧铜杆的生产方法基本工艺为熔炼、轧制和绕制成圆,在生产过程中需要气氛控制和气体保护、化学清洗等条件。
无氧铜杆的生产方法特点?见无氧铜杆的生产方法特点表Rautomead铸机截面图无氧铜杆的生产方法优势?性能优良,工艺先进,生产效率高并节约能源,不需酸洗。
此外,能减少加工工序,而且铜的损耗率低。
无氧铜杆的生产方法之冶金化学反应?1、阴极铜予处理阶段,阴极铜加入熔化炉前,如在预热炉热(700*c左右)。
此时铜板表面存在的胆矾和碱碳酸铜及水分发生离解和蒸发,其反应式如下CuSO4·5H2O→CuO+SO2↑+H2O↑CuCO3·Cu(OH)2250~270℃→CuCO3+CuO+H2O↑CuCO3560~600℃→CuO+CO2↑H2O(液)→H2O(汽)↑2、阴极铜加入炉内熔化,对浸涂法,铜板加入工频感应熔化炉内,熔体在电磁感应作用下不断运动,铜液中杂质元素间及碳层和保护氨气中的氢元素之间(一般木炭覆盖层厚100~150mm;炉内充入含有2%氢的氮气会发生一系列化学反应,如下4CuO1025℃→2Cu2O+O2↑4Cu+O2≡2Cu2OCu2O+Me←→MeO(造渣)+2Cu(Me—金属杂质)2Cu2O+Cu2S≡6Cu+SO2↑Cu2O+H2≡2Cu+HO2↑Cu2S+H2←→2Cu+H2S↑2Cu2O+C≡4Cu+CO2↑SO2+C≡S+CO2↑2Me+C≡2Me+CO2↑无氧铜杆无氧铜杆的生产方法之生产线参数?下面说的是浸涂法的生产线参数。
1、表格化:现场工艺控制。
现代化生产线的有效管理方法之一,是采取表格化的形式,实行现场工艺控制。
无氧铜杆生产工艺流程
无氧铜杆生产工艺流程
无氧铜杆生产工艺流程包括铜原料准备、冶炼、连铸、轧制、拉拔和包装等几个主要步骤。
下面将详细介绍这些步骤。
首先,铜原料准备。
在无氧铜杆的生产中,一般采用高纯度电解铜作为原料。
原料铜应具备高纯度、低氧含量、低杂质含量等特点。
其次,冶炼。
将原料铜放入熔炉中,通过加热和熔融的方式将其变为液态铜。
熔炼过程中需要控制合金成分和温度,以确保得到所需的纯净铜。
接下来是连铸。
将液态铜注入连铸机,通过金属流动的方式将液态铜冷却并凝固成连续的铜坯。
连铸机的运行速度、喷淋水温度和冷却时间等因素都会影响铜坯的质量。
然后是轧制。
将铜坯放入轧机中进行轧制加工,将其变成所需的铜杆。
轧制是通过连续的冷加工过程,逐渐降低铜坯的截面积并增加其长度。
轧制过程中需要控制轧制力、轧制速度和轧制温度等参数,以确保铜杆的均匀性和质量。
接下来是拉拔。
将轧制成的铜杆放入拉拔机中进行拉拔加工。
拉拔是通过连续的冷加工过程,逐渐减小铜杆的截面积并增加其长度。
拉拔过程中需要控制拉拔力、拉拔速度和拉拔温度等参数,以确保铜杆的尺寸精度和表面质量。
最后是包装。
经过拉拔加工后的铜杆需要进行定尺切割和包装。
根据需求将铜杆切割成所需的长度,并进行包装,以便运输和储存。
以上就是无氧铜杆的生产工艺流程的简要介绍。
当然,实际的生产流程可能会因为设备和工艺的不同而有所差异,但总体上都是基于原料准备、冶炼、连铸、轧制、拉拔和包装这几个主要步骤完成的。
无氧铜杆生产工艺
无氧铜杆生产工艺
无氧铜杆是一种高纯度的铜制品,广泛应用于电工、机械、船舶等行业。
下面将介绍无氧铜杆的生产工艺。
无氧铜杆的生产主要分为两个步骤:电解精炼和连铸。
首先是电解精炼。
原料铜经过清洗后,放入电解槽中,作为阴极。
阳极则是高纯度铜块,两者之间有隔离膜隔开。
通过电流的作用,阳极的铜以离子形式溶解到电解液中,并沉积在阴极上。
这个过程称为电解精炼。
在电解精炼的过程中,通过控制电流密度、温度和电解液的成分等参数,可以使铜的纯度达到99.99%以上。
经过电解精炼后,得到高纯度的铜块。
然后将高纯度的铜块放入连铸机中进行连铸。
连铸是指将液态金属铜注入到铸模中,通过冷却后,形成固态铜杆。
在连铸过程中,需要控制铜液的温度、注入速度和冷却方式等参数,以确保铜杆的质量。
连铸过程中,连铸机将铜液注入到连续链式铸坯机中,在连铸机内,旋转模具,使液态铜在模具中形成圆形截面的连续铜杆。
然后通过冷却水冷却,使铜液逐渐凝固,并拉出固态铜杆。
通过连续链式铸坯机,可以快速、连续地生产高质量的无氧铜杆。
最后,根据客户的需求,可以对无氧铜杆进行进一步的加工。
常见的加工方法有拉伸、切割、热处理等。
以上就是无氧铜杆的生产工艺。
通过电解精炼和连铸,可以生产出高纯度的无氧铜杆,广泛应用于各个行业。
同时,在生产过程中,需要严格控制各个参数,以确保产品的质量。
无氧铜生产工艺流程
第四章工艺技术方案4.1工艺技术方案本项目采用的原材料为含铜量99%的电解铜,选用目前国内先进的蓄热式熔化炉和中频炉,用上引法连铸工艺方法生产氧的含量不大于0.02%,杂质总含量不大于0.05%,含铜量99.5%以上无氧铜杆。
4.2工艺流程简述1、生产准备本项目使用的电解铜在江西省内购买。
图4-1 项目生产工艺流程图2、上引法连铸工艺流程本项目采用上引法连铸工艺生产无氧铜杆。
上引法连铸铜杆的基本特点是“无氧”,即氧含量在10ppm以下。
上引法与连铸连轧和浸涂法相比,其特点是:1)由于拉扎工艺和铸造工艺不是连续的,拉扎是在常温下进行的,不需要气体保护,钢材也不会被氧化。
因此设备投资小,厂房布置也灵活。
2)单机产量变化范围大,年产量可以从几百吨到几万吨,可供不同规模的厂家选用不同型号的上引机组。
此外,由于连铸机是多头的,可以很容易的通过改变铸造规格(铸杆直径),来改变单位时间的产量,因此其产量可视原材料的供应情况和产品的需求情况来确定,便于组织生产、节约能源。
3)只需更换结晶器和改变石墨模的形状,即可生产铜管、铜排等异型铜材,并可在同一机器上上产不同规格、品种的铜材,灵活机动,这是上引法的中最大特点。
上引法连铸工艺流程:原料通过加料机加入融化炉进行熔化、氧化、扒渣处理后,熔融的铜液经过一段时间的静置还原脱氧并达到一定的温度后,通过有CO气体保护的流槽经过渡腔(铜液在此进一步还原脱氧、清除渣质),进而平稳的流入中频炉保温静置,铜液的温度由热电偶测量,温度值由仪表显示,温度控制在1150℃±10℃。
连铸机固定于中频保温炉的上方,连铸机铜液在结晶器中快速结晶连续不断地生产出铜杆,最后经双头挠杆机等辅助设备装盘成产品。
⑴加料:原料一般用加料机加入,炉头多加、炉尾少加。
加冷料时要使铜料距炉顶及烟道口有一定距离,以保证燃料燃烧和炉气流动的顺畅。
加料时要保证炉膛有足够高的温度,一般应达到1300℃以上,炉内应保证零压或微负压。
- 1、下载文档前请自行甄别文档内容的完整性,平台不提供额外的编辑、内容补充、找答案等附加服务。
- 2、"仅部分预览"的文档,不可在线预览部分如存在完整性等问题,可反馈申请退款(可完整预览的文档不适用该条件!)。
- 3、如文档侵犯您的权益,请联系客服反馈,我们会尽快为您处理(人工客服工作时间:9:00-18:30)。
无氧铜杆生产工艺流程
无氧铜杆是一种高纯度铜杆,广泛用于电力、电子、电工等领域。
下面介绍一下无氧铜杆的生产工艺流程。
1. 铜坯制备:选用高纯度电解铜作为原料,将其熔化后浇铸在铜坯模具中制成铜坯。
此过程需要严格控制温度和纯度,以确保铜坯的质量。
2. 铜坯预拉伸:将铜坯加热至一定温度后,通过预拉伸机械设备进行拉伸,使铜坯变形成型,分散其中的氧化物和杂质。
3. 热挤压:将预拉伸的铜坯放入热挤压机中,经过高温高压下的挤压,使铜坯形成无氧铜杆。
此过程能够有效提高铜杆的致密度和机械性能。
4. 热处理:经过挤压成型的无氧铜杆需要进行热处理,以消除内部应力和组织不均匀性。
将铜杆置于高温炉中进行加热,然后再进行冷却处理,使铜杆具有更好的力学性能和导电性能。
5. 焊接:根据需要,将多根无氧铜杆进行焊接,连接成所需长度和直径的铜杆。
焊接时需要控制温度和焊接参数,以确保焊接质量。
6. 表面处理:将焊接好的铜杆进行表面处理,包括除油、清洗和抛光等工艺。
这些步骤旨在提高铜杆的表面光洁度和质量。
7. 检测:对生产出的无氧铜杆进行质量检测,包括外观质量、
力学性能和化学成分等方面的检测。
确保无氧铜杆符合相关标准要求。
8. 包装和储存:将合格的无氧铜杆进行包装,并进行标记和记录。
然后将其存放在干燥、通风、防潮的仓库中,待需求时进行发货。
以上就是无氧铜杆的生产工艺流程。
通过严格控制每个环节的工艺参数和质量要求,可以生产出高质量的无氧铜杆,满足各个领域的需求。