环氧自流平施工工艺
环氧自流平施工工艺
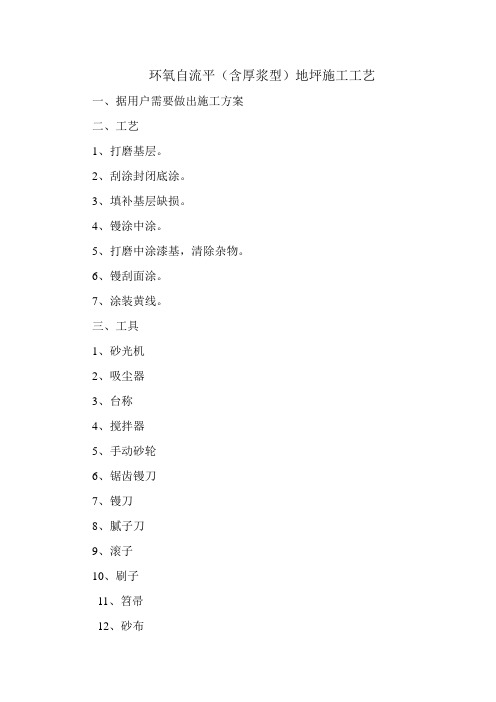
环氧自流平(含厚浆型)地坪施工工艺一、据用户需要做出施工方案二、工艺1、打磨基层。
2、刮涂封闭底涂。
3、填补基层缺损。
4、镘涂中涂。
5、打磨中涂漆基,清除杂物。
6、镘刮面涂。
7、涂装黄线。
三、工具1、砂光机2、吸尘器3、台称4、搅拌器5、手动砂轮6、锯齿镘刀7、镘刀8、腻子刀9、滚子10、刷子11、笤帚12、砂布13、电缆线14、插座15、钢钉16、施工线17、开桶器18、纸胶带19、卷尺20、消泡滚筒21、洒精喷灯四、基层检查及处理水泥基层要求整体机械拍浆,至少5cm以上,坚硬平整。
中性,含水量低于8%。
含水量超标环境湿度大于80%不能施工。
含水率测定方法很多,可用简单易行的塑料薄膜法、氯化钙增重法等测定。
施工前应对基础进行机械打磨,粗糙度达到30—70。
清除油污,风化层及突出物,用吸尘器吸除砂粒灰尘,平整度要求达到2mm/m²。
五、涂装1、底漆涂布根据施工方案,开始涂布封闭底漆,可采用刮涂或滚涂,尽量做到薄而匀,但要确保封闭混凝土。
封闭底漆涂布量为0.13kg/m²。
2、中涂涂装中涂涂装方法有两种:一为批刮溶剂型中涂需要间隔时间长,若溶剂未完全挥发掉,会造成中间层产生气泡,严重的会造成面层开裂;二为自流平中涂采用锯齿镘刀批刮,可以避免溶剂型中涂为面层带来的诸多禁忌,并能保证面层的平整光滑减少使用量。
中涂施工时,按比例将甲乙组份称量,加入粉、砂等骨料(骨料加入量可视设计要求),搅拌均匀,静置10分钟后开始涂装,将配合好的敷料一次性倒在地面上,以锯齿镘刀抹平。
施工时注意用力均匀,以免砂、粉等填充骨料在涂层中分布不匀,同时注意涂层的厚度均匀。
3、面涂涂装采用无溶剂中涂,中涂层施工24小时后,需进行涂层清理、打磨、消除瑕疵,即可进行面涂施工。
采用溶剂型中涂,则应确保涂层中溶剂完全挥发,才能进行面涂施工,施工前需进行整体打磨,施工间隔大于48小时。
面涂施工时,将配合好的涂料,静置10分钟后倒在地面上,以锯齿镘刀刮平,注意用力均匀。
环氧自流平的施工方法
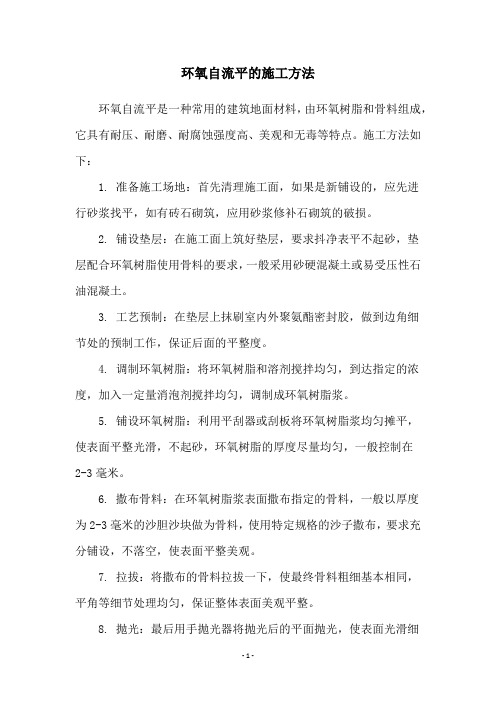
环氧自流平的施工方法
环氧自流平是一种常用的建筑地面材料,由环氧树脂和骨料组成,它具有耐压、耐磨、耐腐蚀强度高、美观和无毒等特点。
施工方法如下:
1. 准备施工场地:首先清理施工面,如果是新铺设的,应先进
行砂浆找平,如有砖石砌筑,应用砂浆修补石砌筑的破损。
2. 铺设垫层:在施工面上筑好垫层,要求抖净表平不起砂,垫
层配合环氧树脂使用骨料的要求,一般采用砂硬混凝土或易受压性石油混凝土。
3. 工艺预制:在垫层上抹刷室内外聚氨酯密封胶,做到边角细
节处的预制工作,保证后面的平整度。
4. 调制环氧树脂:将环氧树脂和溶剂搅拌均匀,到达指定的浓度,加入一定量消泡剂搅拌均匀,调制成环氧树脂浆。
5. 铺设环氧树脂:利用平刮器或刮板将环氧树脂浆均匀摊平,
使表面平整光滑,不起砂,环氧树脂的厚度尽量均匀,一般控制在
2-3毫米。
6. 撒布骨料:在环氧树脂浆表面撒布指定的骨料,一般以厚度
为2-3毫米的沙胆沙块做为骨料,使用特定规格的沙子撒布,要求充分铺设,不落空,使表面平整美观。
7. 拉拔:将撒布的骨料拉拔一下,使最终骨料粗细基本相同,
平角等细节处理均匀,保证整体表面美观平整。
8. 抛光:最后用手抛光器将抛光后的平面抛光,使表面光滑细
腻,使整个施工工程完成。
环氧自流平施工工艺
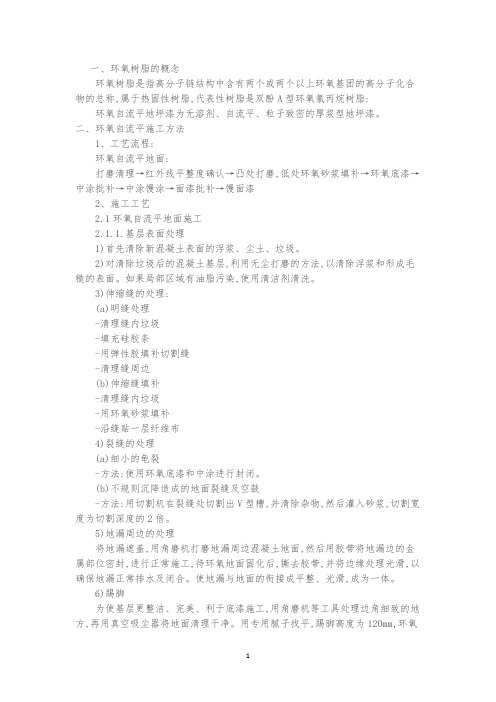
一、环氧树脂的概念环氧树脂是指高分子链结构中含有两个或两个以上环氧基团的高分子化合物的总称,属于热固性树脂,代表性树脂是双酚A型环氧氯丙烷树脂: 环氧自流平地坪漆为无溶剂、自流平、粒子致密的厚浆型地坪漆。
二、环氧自流平施工方法1、工艺流程:环氧自流平地面:打磨清理→红外线平整度确认→凸处打磨,低处环氧砂浆填补→环氧底漆→中涂批补→中涂馒涂→面漆批补→馒面漆2、施工工艺2.1环氧自流平地面施工2.1.1.基层表面处理1)首先清除新混凝土表面的浮浆、尘土、垃圾。
2)对清除垃圾后的混凝土基层,利用无尘打磨的方法,以清除浮浆和形成毛糙的表面。
如果局部区域有油脂污染,使用清洁剂清洗。
3)伸缩缝的处理:(a)明缝处理-清理缝内垃圾-填充硅胶条-用弹性胶填补切割缝-清理缝周边(b)伸缩缝填补-清理缝内垃圾-用环氧砂浆填补-沿缝贴一层纤维布4)裂缝的处理(a)细小的龟裂-方法:使用环氧底漆和中涂进行封闭。
(b)不规则沉降造成的地面裂缝及空鼓-方法:用切割机在裂缝处切割出V型槽,并清除杂物,然后灌入砂浆,切割宽度为切割深度的2倍。
5)地漏周边的处理将地漏遮盖,用角磨机打磨地漏周边混凝土地面,然后用胶带将地漏边的金属部位密封,进行正常施工,待环氧地面固化后,撕去胶带,并将边缘处理光滑,以确保地漏正常排水及闭合。
使地漏与地面的衔接成平整、光滑,成为一体。
6)踢脚为使基层更整洁、完美、利于底漆施工,用角磨机等工具处理边角细致的地方,再用真空吸尘器将地面清理干净。
用专用腻子找平,踢脚高度为120mm,环氧涂刷厚度为2mm。
2.1.2.环氧底漆施工按比例(1:1)将主剂、固化剂混合,充分搅拌均匀,在可使用时间内滚涂(30分钟之内),滚涂时要做到薄而匀,涂布后有光泽,无光泽之处(粗糙之水泥地面)在适当时候进行补涂。
12小时之后可进行下道工序。
2.1.3.中间层施工1)环氧中涂批补施工先将中涂漆主剂充分搅拌均匀,然后按比例(3:1)将主剂、固化剂混合,充分搅拌均匀。
环氧树脂自流平地面施工工艺
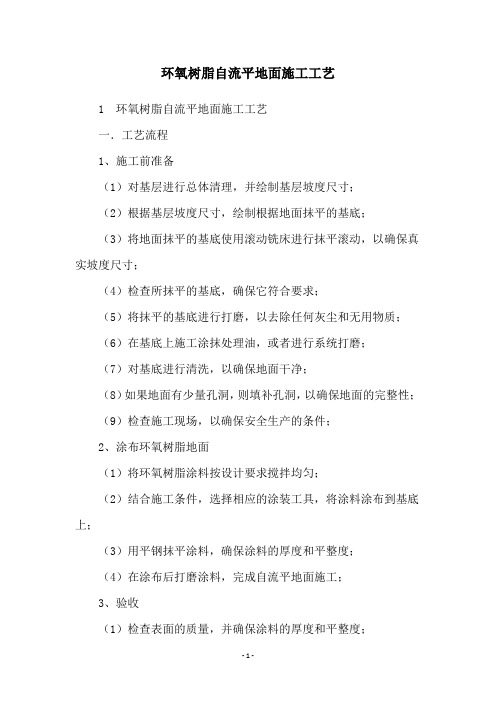
环氧树脂自流平地面施工工艺
1 环氧树脂自流平地面施工工艺
一.工艺流程
1、施工前准备
(1)对基层进行总体清理,并绘制基层坡度尺寸;
(2)根据基层坡度尺寸,绘制根据地面抹平的基底;
(3)将地面抹平的基底使用滚动铣床进行抹平滚动,以确保真实坡度尺寸;
(4)检查所抹平的基底,确保它符合要求;
(5)将抹平的基底进行打磨,以去除任何灰尘和无用物质;
(6)在基底上施工涂抹处理油,或者进行系统打磨;
(7)对基底进行清洗,以确保地面干净;
(8)如果地面有少量孔洞,则填补孔洞,以确保地面的完整性;
(9)检查施工现场,以确保安全生产的条件;
2、涂布环氧树脂地面
(1)将环氧树脂涂料按设计要求搅拌均匀;
(2)结合施工条件,选择相应的涂装工具,将涂料涂布到基底上;
(3)用平钢抹平涂料,确保涂料的厚度和平整度;
(4)在涂布后打磨涂料,完成自流平地面施工;
3、验收
(1)检查表面的质量,并确保涂料的厚度和平整度;
(2)检查施工后的效果,如果满足设计要求,则可以验收通过;
二、施工注意事项
1、在施工前请确保基层的清理工作已完成,且基层表面清洁、干燥;
2、在施工涂布环氧树脂涂料时,应充分考虑涂料的厚度和整体的施工效果;
3、在施工完成后,请及时进行清洁工作,以保护施工现场和施工后的地面;
4、自流平地面施工时,请及时进行施工质量检查,以保证施工质量。
环氧树脂自流平的施工工艺
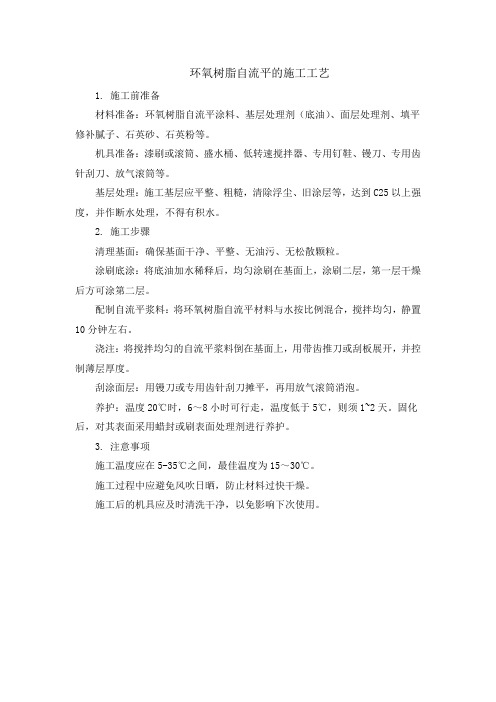
环氧树脂自流平的施工工艺
1. 施工前准备
材料准备:环氧树脂自流平涂料、基层处理剂(底油)、面层处理剂、填平修补腻子、石英砂、石英粉等。
机具准备:漆刷或滚筒、盛水桶、低转速搅拌器、专用钉鞋、镘刀、专用齿针刮刀、放气滚筒等。
基层处理:施工基层应平整、粗糙,清除浮尘、旧涂层等,达到C25以上强度,并作断水处理,不得有积水。
2. 施工步骤
清理基面:确保基面干净、平整、无油污、无松散颗粒。
涂刷底涂:将底油加水稀释后,均匀涂刷在基面上,涂刷二层,第一层干燥后方可涂第二层。
配制自流平浆料:将环氧树脂自流平材料与水按比例混合,搅拌均匀,静置10分钟左右。
浇注:将搅拌均匀的自流平浆料倒在基面上,用带齿推刀或刮板展开,并控制薄层厚度。
刮涂面层:用镘刀或专用齿针刮刀摊平,再用放气滚筒消泡。
养护:温度20℃时,6~8小时可行走,温度低于5℃,则须1~2天。
固化后,对其表面采用蜡封或刷表面处理剂进行养护。
3. 注意事项
施工温度应在5-35℃之间,最佳温度为15~30℃。
施工过程中应避免风吹日晒,防止材料过快干燥。
施工后的机具应及时清洗干净,以免影响下次使用。
环氧自流平施工工艺
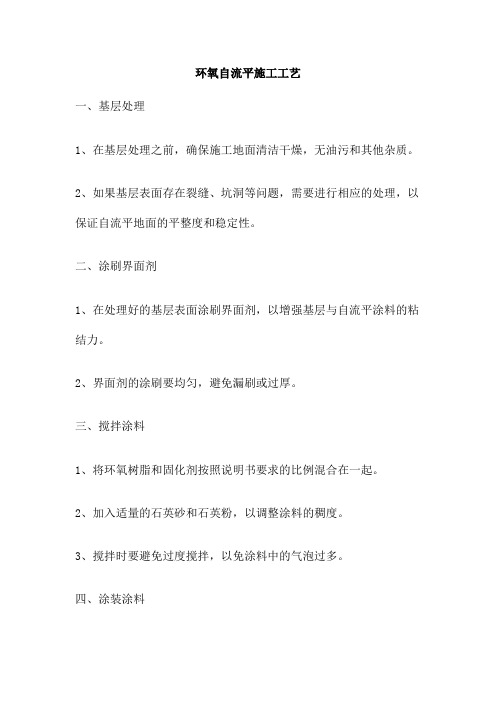
环氧自流平施工工艺一、基层处理1、在基层处理之前,确保施工地面清洁干燥,无油污和其他杂质。
2、如果基层表面存在裂缝、坑洞等问题,需要进行相应的处理,以保证自流平地面的平整度和稳定性。
二、涂刷界面剂1、在处理好的基层表面涂刷界面剂,以增强基层与自流平涂料的粘结力。
2、界面剂的涂刷要均匀,避免漏刷或过厚。
三、搅拌涂料1、将环氧树脂和固化剂按照说明书要求的比例混合在一起。
2、加入适量的石英砂和石英粉,以调整涂料的稠度。
3、搅拌时要避免过度搅拌,以免涂料中的气泡过多。
四、涂装涂料1、将搅拌好的涂料均匀地涂刷在地面上,可以从一端开始,逐渐向前推进。
2、涂装时要掌握好涂料的厚度,一般控制在0.5-1mm之间。
3、在涂装过程中,要避免涂料堆积或漏涂。
五、消泡处理1、在涂装完成后,等待一段时间让涂料充分流平。
2、使用消泡滚筒在表面滚动,以去除涂料中的气泡。
3、如果消泡不彻底,可以在消泡滚筒上加一些水,以增强消泡效果。
六、养护处理1、在消泡处理完成后,等待一段时间让涂料充分固化。
2、使用养护剂进行养护处理,以增强地面的耐磨性和光泽度。
3、养护处理的时间一般控制在24-48小时之间。
水泥自流平施工工艺一、施工前的准备1、施工前应测量施工区域的温度和湿度,以确保自流平水泥的施工质量。
2、施工前应清洁地面,除去杂质,确保地面干燥、平整,以避免出现气泡、裂缝等问题。
3、施工前应准备好施工工具,如搅拌器、刮板、吸尘器等。
4、施工前应选择适当的水泥品种,考虑到地面因素及施工厚度等因素。
二、施工工艺1、搅拌水泥:将适量的水加入到水泥中,用搅拌器搅拌,搅拌时间不少于2分钟,以保证水泥充分混合。
2、铺设水泥:将搅拌好的水泥倒在地面上,用刮板将水泥刮平,使水泥在地面上分布均匀。
3等待凝固:让水泥在室温下自然凝固,一般需要等待6-8小时。
4、打磨地面:在水泥完全凝固后,用打磨机对地面进行打磨,使地面光滑平整。
5、收尾工作:将打磨后的地面清洁干净,可以在地面上涂上一层保护剂,以保护地面不受损坏。
环氧树脂自流平施工工艺

环氧树脂自流平施工工艺1. 简介环氧树脂自流平施工工艺是一种常用于地面涂装的技术,适用于各种场所,如工业厂房、商业建筑、医院、学校等。
这种工艺能够提供耐磨、防滑、易清洁等优异的性能,同时具有美观的外观效果。
本文将深入介绍环氧树脂自流平施工工艺的步骤和注意事项。
2. 工艺步骤2.1 地面准备在进行环氧树脂自流平施工之前,首先需要对地面进行准备。
具体步骤如下:1.清理地面:清除地面上的尘土、油污等杂物,确保表面干净。
2.防尘处理:使用专门的防尘剂对地面进行处理,以增强涂层与地面的粘结力。
3.研磨处理:使用研磨机对地面进行研磨处理,以去除表面的旧涂层或不平整。
4.补平处理:对地面进行补平处理,修复裂缝、凹坑等问题,确保地面平整。
2.2 环氧树脂底涂施工环氧树脂底涂是为了增强地面涂层的附着力和耐磨性。
具体步骤如下:1.搅拌:按照产品说明书的要求,将环氧树脂底涂材料进行充分搅拌,确保材料均匀。
2.涂刷:使用刷子或辊筒将环氧树脂底涂均匀地涂刷在地面上,注意避免漏涂或堆积。
3.平整处理:使用专门的工具对涂刷后的地面进行平整处理,确保表面平滑。
4.干燥时间:根据产品说明书的要求,等待环氧树脂底涂干燥至适当程度。
2.3 环氧树脂自流平施工环氧树脂自流平施工是通过将自流平材料倒在地面上,并利用其自身流动性实现地面平整。
具体步骤如下:1.搅拌:按照产品说明书的要求,将环氧树脂自流平材料进行充分搅拌,确保材料均匀。
2.倒涂:将搅拌好的环氧树脂自流平材料倒在地面上,注意避免漏涂或堆积。
3.平整处理:使用专门的工具对自流平材料进行平整处理,确保地面表面平滑。
4.除气处理:使用专门的工具对自流平材料表面进行除气处理,以去除可能产生的气泡。
5.干燥时间:根据产品说明书的要求,等待环氧树脂自流平施工完成后的干燥时间。
2.4 环氧树脂面涂施工环氧树脂面涂是为了增加地面涂层的耐磨性和美观性。
具体步骤如下:1.搅拌:按照产品说明书的要求,将环氧树脂面涂材料进行充分搅拌,确保材料均匀。
环氧自流平施工工艺
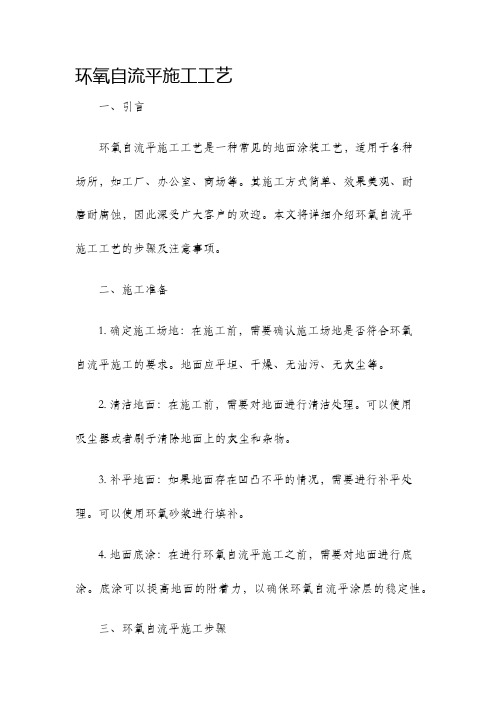
环氧自流平施工工艺一、引言环氧自流平施工工艺是一种常见的地面涂装工艺,适用于各种场所,如工厂、办公室、商场等。
其施工方式简单、效果美观、耐磨耐腐蚀,因此深受广大客户的欢迎。
本文将详细介绍环氧自流平施工工艺的步骤及注意事项。
二、施工准备1. 确定施工场地:在施工前,需要确认施工场地是否符合环氧自流平施工的要求。
地面应平坦、干燥、无油污、无灰尘等。
2. 清洁地面:在施工前,需要对地面进行清洁处理。
可以使用吸尘器或者刷子清除地面上的灰尘和杂物。
3. 补平地面:如果地面存在凹凸不平的情况,需要进行补平处理。
可以使用环氧砂浆进行填补。
4. 地面底涂:在进行环氧自流平施工之前,需要对地面进行底涂。
底涂可以提高地面的附着力,以确保环氧自流平涂层的稳定性。
三、环氧自流平施工步骤1. 搅拌材料:在施工前,需要将环氧自流平材料进行充分的搅拌,以确保材料的均匀性。
搅拌时应注意不要产生气泡。
2. 浇注材料:将搅拌好的环氧自流平材料均匀地浇注在地面上,可以使用滚筒或者刮刀将材料均匀地涂抹开。
3. 环刮材料:用环刮工具对浇注的环氧自流平材料进行刮平操作,以确保地面表面平整。
刮平时要注意力度的均匀,并及时清理刮刀上的材料。
4. 染色材料(可选):如果需要给地面染色,可以在环氧自流平涂层干燥之前,将染色剂均匀地喷洒在地面上。
然后再进行环刮工作。
5. 养护材料:环氧自流平施工完毕后,需要对其进行养护。
通常情况下,需要等待24-48小时,让环氧自流平涂层完全干燥。
四、注意事项1. 环氧自流平材料的搅拌应充分均匀,避免气泡的生成。
2. 施工温度应在15℃-25℃之间,并保持相对湿度在85%以下。
3. 施工过程中要注意安全,戴好口罩、手套等防护用品。
- 1、下载文档前请自行甄别文档内容的完整性,平台不提供额外的编辑、内容补充、找答案等附加服务。
- 2、"仅部分预览"的文档,不可在线预览部分如存在完整性等问题,可反馈申请退款(可完整预览的文档不适用该条件!)。
- 3、如文档侵犯您的权益,请联系客服反馈,我们会尽快为您处理(人工客服工作时间:9:00-18:30)。
一、环氧树脂的概念环氧树脂是指高分子链结构中含有两个或两个以上环氧基团的高分子化合物的总称,属于热固性树脂,代表性树脂是双酚A型环氧氯丙烷树脂: 环氧自流平地坪漆为无溶剂、自流平、粒子致密的厚浆型地坪漆。
二、环氧自流平施工方法1、工艺流程:环氧自流平地面:打磨清理→红外线平整度确认→凸处打磨,低处环氧砂浆填补→环氧底漆→中涂批补→中涂馒涂→面漆批补→馒面漆2、施工工艺2。
1环氧自流平地面施工2.1。
1。
基层表面处理1)首先清除新混凝土表面的浮浆、尘土、垃圾。
2)对清除垃圾后的混凝土基层,利用无尘打磨的方法,以清除浮浆和形成毛糙的表面。
如果局部区域有油脂污染,使用清洁剂清洗。
3)伸缩缝的处理:(a)明缝处理—清理缝内垃圾—填充硅胶条—用弹性胶填补切割缝-清理缝周边(b)伸缩缝填补—清理缝内垃圾—用环氧砂浆填补-沿缝贴一层纤维布4)裂缝的处理(a)细小的龟裂-方法:使用环氧底漆和中涂进行封闭.(b)不规则沉降造成的地面裂缝及空鼓-方法:用切割机在裂缝处切割出V型槽,并清除杂物,然后灌入砂浆,切割宽度为切割深度的2倍。
5)地漏周边的处理将地漏遮盖,用角磨机打磨地漏周边混凝土地面,然后用胶带将地漏边的金属部位密封,进行正常施工,待环氧地面固化后,撕去胶带,并将边缘处理光滑,以确保地漏正常排水及闭合。
使地漏与地面的衔接成平整、光滑,成为一体。
6)踢脚为使基层更整洁、完美、利于底漆施工,用角磨机等工具处理边角细致的地方,再用真空吸尘器将地面清理干净。
用专用腻子找平,踢脚高度为120mm,环氧涂刷厚度为2mm。
2.1。
2.环氧底漆施工按比例(1:1)将主剂、固化剂混合,充分搅拌均匀,在可使用时间内滚涂(30分钟之内),滚涂时要做到薄而匀,涂布后有光泽,无光泽之处(粗糙之水泥地面)在适当时候进行补涂。
12小时之后可进行下道工序。
2。
1。
3。
中间层施工1)环氧中涂批补施工先将中涂漆主剂充分搅拌均匀,然后按比例(3:1)将主剂、固化剂混合,充分搅拌均匀。
混合时应将固化剂向有主剂的桶中央倒入,避免材料混合不匀。
搅拌后加入适量细石英砂(粉),充分搅拌均匀,倒在地面上,以镘刀全面做一层披覆填平砂孔,使表面平整。
施工时,以齿尖除去大泡,并挑去粗粒杂质。
若批补不平整,或者过于光滑,间隔时间长(如:3天以上),则须硬化干燥后全面砂磨,以吸尘器吸干净.搅拌桶内涂料若呈硬化状态时,则必须停止使用并随时更换搅拌桶。
24小时之后可进行下道工序。
2)环氧中涂树脂砂浆施工先将中涂主剂充分搅拌均匀,然后将固化剂向有主剂的桶中央倒入,避免材料混合不匀。
充分搅拌均匀后,加入适量适当规格的石英砂,充分搅拌均匀,倒在地面上,用有齿镘刀依规格镘涂.搅拌桶内涂料若呈硬化状态时,则必须停止使用并更换搅拌桶。
24小时之后可进行下道工序。
2.1。
4.面漆施工1)环氧面漆批补施工先将面漆主剂充分搅拌均匀,然后按比例(24:5。
4)将主剂、固化剂混合,充分搅拌均匀.混合时应将固化剂向有主剂的桶中央倒入,避免材料混合不匀。
若批补不平整,或者过于光滑,间隔时间长(如:3天以上),则须硬化干燥后全面砂磨,以吸尘器吸干净。
搅拌桶内涂料若呈硬化状态时,则须停止使用并更换搅拌桶。
24小时之后可进行下道工序。
2)环氧面漆施工先将主剂充分搅拌均匀,然后将固化剂向盛有主剂的桶中央倒入,以免材料混合不匀。
充分搅拌均匀后,倒在地上用2mm镘刀一次成型,环氧平涂则用滚筒进行滚涂2次,施工时发现有气泡用齿尖除去,搅拌桶涂料若呈硬化状态时,则必须停止使用并随时更换搅拌桶。
72小时之后可轻踩上人.三、质量标准1、主控项目:1。
1.施工所用材料的品种、型号和性能符合设计要求和施工及验收规范的规定.检验方法:观察检查和检查材质合格证明文件及检测报告。
1。
2。
环氧地面的颜色、光泽、图案符合设计要求。
1.3。
环氧地面涂饰均匀、粘结牢固、不漏涂、透底、起皮和反锈。
1.4.地面的基层处理符合规范要求,检验方法:用小锤轻击检查,防静电表面和泄漏指标为106—108欧姆。
2、一般项目:2.1.面层表面应颜色均匀一致、光泽均匀一致,即光滑、无交接痕迹,无皱皮、无分色、表面无流淌,不起皱。
检验方法:观察检查。
2。
2.环氧地面与地漏结合处严密平顺。
检验方法:观察检查.2。
3。
其中涂层与其他材料的设备相接处应吻合,方向清晰,踢脚线平直,地面分色顺直清晰。
四、注意事项1、施工注意事项1.1。
雨期施工:如空气湿度超出施工条件时,应增加人工排风设施(排风扇等)控制湿度。
遇大雨、高湿度等天时应停止施工。
1。
2.树脂整体面层施工时,环境温度不得过低、过高,湿度不得过大,防止树脂砂浆产生假固化。
1.3.施工场所应注意通风良好。
1。
4。
施工中涂料避免接触皮肤,最好双手能有保护手套。
1.5.施工中玷污处要清洗干净,施工后顺将场地、垃圾清除完毕。
1。
6。
地面灰尘须彻底清除,以确保底漆之接着效果.1。
7。
地面潮湿时须使之干燥,含水率8%以下,或者选用特殊底漆.1.8。
环氧树脂的各层涂料若出超出有效接着地间,须将材料表面打粗并处理干净,涂上一层底漆(依间隔时间长短),再进行上层涂料施工.1.9。
底漆须待完全挥发后方可进行施工,以免起泡现象。
1。
10.材料调配时,须以底布(或纸板)垫底半避免任何一种材料单独滴于素地上,造成不干,若已滴于素地上时须立即擦去。
1。
11.搅拌后的材料应在可使用时间内涂布完毕,避免表面接近硬化无法流平.1.12.涂布发现砂粒或其它杂质时,立即清除。
1.13.环氧树脂防尘耐磨地坪施工时应注意其混合比例,混合搅拌均匀才可使用。
地坪表面的处理1、新竣工的工业地坪必须经过一定的养护后方可施工,约28天.2、清除表面的水泥浮浆、旧漆以及粘附的垃圾杂物。
3、彻底清除表面的油污,用克油王清洗剂处理。
4、清除积水,并使潮处彻底干燥。
5、表面的清洁需用无尘清扫机及大型吸尘器来完成.6、平整的表面允许空隙为2~2.5mm,含水量在6%以下,PH值6~8.7、地坪表面的打毛,需用无尘打磨机来完成,并用吸尘器彻底清洁。
8、对地坪表面的洞孔和明显凹陷处应用腻子来填补批刮,实干后,打磨吸尘。
二、涂饰封闭涂料1、在处理清洁、平整的砼表面,采用高压无气喷涂或辊涂,环氧封闭底涂料一道。
2、环氧封闭漆有很强的渗透性,在涂刷底漆时应加入一定量的稀释剂,使稀释后的底漆能渗入基层内部,增强涂层和基层的附着力,其涂布必须连续,不得间断,涂布量以表面刚好饱和为准。
3、局部漏涂可用刷子补涂,表面多余的底漆必须在下道工序施工前打磨处理好。
三、批刮批刮料1、在实干(25℃,约4小时)以后的底漆表面采用两道批刮腻子的方法,以确保地坪的耐磨损、耐压性、碰撞、水、矿物油、酸碱溶液等性能,并调整地面平整度。
2、用100~200目的石英砂和环氧批刮料,作为第1道腻子,要充分搅拌均匀、刮平,此道主要用于增强地面的耐磨及抗压性能。
3、用砂袋式无尘滚动磨砂机打磨第1道腻子,并吸尘清洁。
4、用200—270目的石英砂和环氧批刮料,作为第2道腻子,要充分搅拌均匀、刮平,此道主要用于增强地面的耐磨及平整度。
5、用砂袋式无尘滚动磨砂机打磨第2道腻子,并吸尘清洁。
6、两道腻子实干以后,如有麻面、裂缝处应先进行修补,然后用平板砂光机进行打磨,使其平整,并吸尘清洁。
7、石英砂使用目数由现场工程师根据地面具体情况确定。
四、涂饰地坪中间层1、在打磨、清洁后的腻子表面上(20℃,24小时)用环氧地坪涂料涂饰中间层,涂饰方法可用刷涂、批刮、高压无空气喷涂,大面积施工以高压无空气喷涂为最佳,喷涂压力为20~25Mpa。
2、此遍可使地面更趋于平整,更便于发现地面仍存在的缺陷,以便下一面层施工找平。
3、此遍还方便甲方对设备安装等的安排。
五、涂饰地坪面层1、在中间层实干后,进行环氧地坪层涂装,涂装方法用批刮和高压无空气喷涂,但以高压无空气喷涂为宜。
2、涂装前应对于中间层用砂袋式无尘滚动磨砂机进行打磨、吸尘.3、如甲方在中间层实干后,先进行了设备的安装调试,造成地面形成新的缺陷,应用批刮料找平、打磨,并吸尘、清洁后喷涂面层。
六、施工注意事项1、施工现场的环境温度应高于5℃,相对湿度小于85%时方能施工。
2、施工者应做好施工部位、时间、温度、相对湿度、地坪表面处理、材料等实际记录,以备查考。
3、涂料施工后,应立即清洗有关设备和工具。
七、安全技术要求1、施工场地四周应拉好警戒带和挂好警告牌。
2、施工场地四周10米内严禁明火作业,严禁吸烟。
3、使用高压无气喷涂泵应结妥地线。
4、涂料和稀释剂应放在通风良好的库房内。
5、工作时注意做好个人防护。
6、电动工具的使用须有专人负责,做完离场前需切断电源.。