复合模实例
落料冲孔复合模设计实例

落料冲孔复合模设计实例在此实例中,我们需要设计一个落料冲孔复合模,用于冲压一块厚度为2mm的方形薄板。
薄板的尺寸为100mm × 100mm。
冲孔部分需要在薄板的四个角上冲孔,冲孔直径为10mm。
同时,需要在薄板的一边进行切割,切割长度为80mm。
首先,我们需要确定冲孔的位置和数量。
考虑到薄板的尺寸和形状,我们决定在薄板的四个角上进行冲孔。
冲孔直径为10mm。
为了保证冲孔的准确性和稳定性,我们需要设计一个冲孔模具,包括冲孔钢模和冲孔衬套。
冲孔钢模的尺寸为20mm × 20mm × 10mm。
冲孔衬套的尺寸与冲孔钢模相匹配。
冲孔钢模通过安装在冲床上,固定在冲床的上模座上。
冲孔衬套则通过螺纹固定在冲孔钢模上。
薄板在冲孔时会被钢模和衬套夹住,冲孔钢模通过冲击力将薄板冲孔。
接下来,我们需要设计切割部分的模具。
根据需求,切割长度为80mm。
我们选择使用切割刀具来完成切割操作。
切割刀具的尺寸为80mm × 10mm,其材料为高速钢。
切割刀具通过安装在切割模架上,固定在冲床的下模座上。
切割模架通过滑动导轨与下模座连接,可以准确地控制切割位置和长度。
为了提高生产效率,我们可以选择一次冲孔和切割多个薄板。
这就需要在冲床上设计合适的夹持装置,以固定多个薄板。
夹持装置可以同时夹持多个薄板,使冲孔和切割的连续进行,提高生产效率。
在设计完成后,我们需要进行模具制造和组装。
首先,我们制造冲孔钢模和冲孔衬套,确保其尺寸和形状的准确性。
接着,制造切割刀具和切割模架,保证其切割性能和精度。
最后,将冲孔钢模、冲孔衬套、切割刀具和切割模架组装在冲床上。
当我们需要进行冲孔和切割时,将薄板放入夹持装置中,通过冲床的运动,冲孔钢模将薄板冲孔,切割刀具将薄板切割。
这样,我们就完成了落料冲孔复合模的设计和制造。
总结起来,落料冲孔复合模的设计需要考虑冲孔和切割的几何形状、材料厚度和生产效率等因素。
在此设计实例中,我们根据需求设计了冲孔模具和切割模具,并制造和组装了这些模具。
设计实例(落料拉深复合模)部分
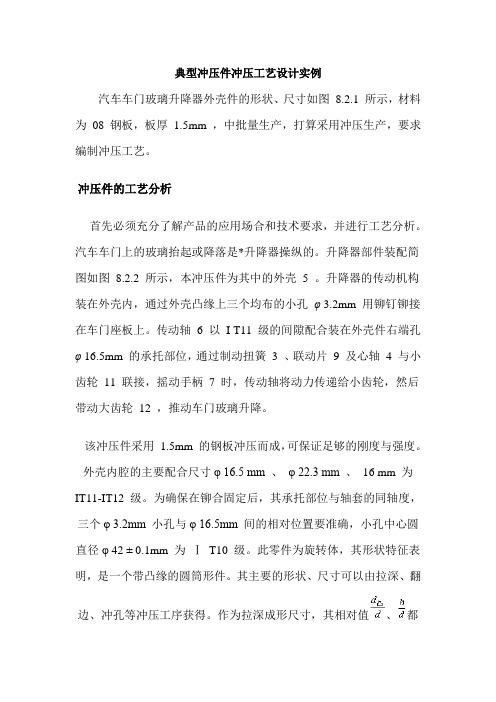
典型冲压件冲压工艺设计实例汽车车门玻璃升降器外壳件的形状、尺寸如图8.2.1 所示,材料为08 钢板,板厚1.5mm ,中批量生产,打算采用冲压生产,要求编制冲压工艺。
冲压件的工艺分析首先必须充分了解产品的应用场合和技术要求,并进行工艺分析。
汽车车门上的玻璃抬起或降落是*升降器操纵的。
升降器部件装配简图如图8.2.2 所示,本冲压件为其中的外壳 5 。
升降器的传动机构装在外壳内,通过外壳凸缘上三个均布的小孔φ 3.2mm 用铆钉铆接在车门座板上。
传动轴6 以I T11 级的间隙配合装在外壳件右端孔φ 16.5mm 的承托部位,通过制动扭簧3 、联动片9 及心轴4 与小齿轮11 联接,摇动手柄7 时,传动轴将动力传递给小齿轮,然后带动大齿轮12 ,推动车门玻璃升降。
该冲压件采用1.5mm 的钢板冲压而成,可保证足够的刚度与强度。
外壳内腔的主要配合尺寸φ 16.5 mm 、φ 22.3 mm 、16 mm 为IT11-IT12 级。
为确保在铆合固定后,其承托部位与轴套的同轴度,三个φ 3.2mm 小孔与φ 16.5mm 间的相对位置要准确,小孔中心圆直径φ 42 ± 0.1mm 为ⅠT10 级。
此零件为旋转体,其形状特征表明,是一个带凸缘的圆筒形件。
其主要的形状、尺寸可以由拉深、翻边、冲孔等冲压工序获得。
作为拉深成形尺寸,其相对值、都比较合适,拉深工艺性较好。
φ 22.3 mm 、16 mm 的公差要求偏高,拉深件底部及口部的圆角半径R1.5 mm 也偏小,故应在拉深之后,另加整形工序,并用制造精度较高、间隙较小的模具来达到。
三个小孔φ 3.2 mm 的中心圆直径42 ± 0.1mm 的精度要求较高,按冲裁件工艺性分析,应以φ 22.3 mm 的内径定位,用高精度(IT7 级以上)冲模在一道工序中同时冲出。
图8.2.1 玻璃升降器外壳图8.2.2 玻璃升降器外壳的装配简图冲压件冲压工艺过程的确定一.工艺方案的分析比较外壳的形状表明,它为拉深件,所以拉深为基本工序。
复合模实例
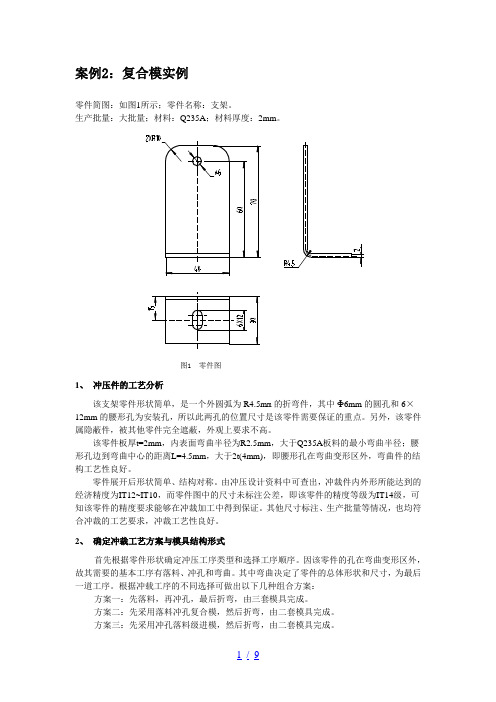
案例2:复合模实例零件简图:如图1所示;零件名称:支架。
生产批量:大批量;材料:Q235A;材料厚度:2mm。
图1 零件图1、冲压件的工艺分析该支架零件形状简单,是一个外圆弧为R4.5m m的折弯件,其中Ф6mm的圆孔和6×12mm的腰形孔为安装孔,所以此两孔的位置尺寸是该零件需要保证的重点。
另外,该零件属隐蔽件,被其他零件完全遮蔽,外观上要求不高。
该零件板厚t=2mm,内表面弯曲半径为R2.5mm,大于Q235A板料的最小弯曲半径;腰形孔边到弯曲中心的距离L=4.5mm,大于2t(4mm),即腰形孔在弯曲变形区外,弯曲件的结构工艺性良好。
零件展开后形状简单、结构对称。
由冲压设计资料中可查出,冲裁件内外形所能达到的经济精度为IT12~IT10,而零件图中的尺寸未标注公差,即该零件的精度等级为IT14级,可知该零件的精度要求能够在冲裁加工中得到保证。
其他尺寸标注、生产批量等情况,也均符合冲裁的工艺要求,冲裁工艺性良好。
2、确定冲裁工艺方案与模具结构形式首先根据零件形状确定冲压工序类型和选择工序顺序。
因该零件的孔在弯曲变形区外,故其需要的基本工序有落料、冲孔和弯曲。
其中弯曲决定了零件的总体形状和尺寸,为最后一道工序。
根据冲载工序的不同选择可做出以下几种组合方案:方案一:先落料,再冲孔,最后折弯,由三套模具完成。
方案二:先采用落料冲孔复合模,然后折弯,由二套模具完成。
方案三:先采用冲孔落料级进模,然后折弯,由二套模具完成。
比较上述各方案可以看出,方案一的优点是:模具结构简单、寿命长、制造周期短、投产快。
缺点是:工序分散,需用模具、压力机和操作人员较多,劳动生产率低。
方案二落料冲孔在一道工序内完成,内、外形的位置尺寸精度高,工件的平整性好;方案三由于是先冲孔后落料,内、外形的位置尺寸精度不如方案二高,工件易弯曲,平整性不如方案二好,但操作安全、方便。
方案二和方案三与方案一相比,工序集中,劳动生产率高,但模具结构复杂,制造周期长。
落料冲孔复合模研发设计实例
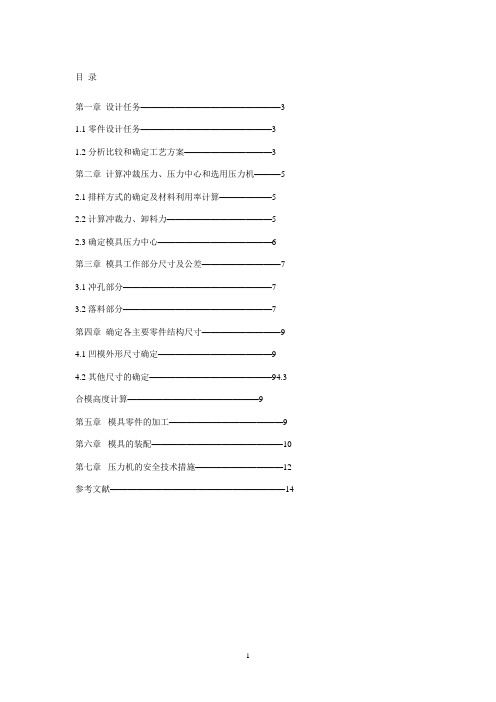
目录第一章设计任务————————————————3 1.1零件设计任务———————————————31.2分析比较和确定工艺方案——————————3第二章计算冲裁压力、压力中心和选用压力机———5 2.1排样方式的确定及材料利用率计算——————52.2计算冲裁力、卸料力————————————52.3确定模具压力中心—————————————6第三章模具工作部分尺寸及公差—————————7 3.1冲孔部分—————————————————73.2落料部分—————————————————7第四章确定各主要零件结构尺寸—————————9 4.1凹模外形尺寸确定—————————————94.2其他尺寸的确定——————————————94.3 合模高度计算———————————————9第五章模具零件的加工—————————————9 第六章模具的装配———————————————10 第七章压力机的安全技术措施——————————12 参考文献————————————————————14落料冲孔复合模设计实例(一)零件工艺性分析工件为图1所示的落料冲孔件,材料为Q235钢,材料厚度2mm ,生产批量为大批量。
工艺性分析内容如下:1.材料分析Q235为普通碳素结构钢,具有较好的冲裁成形性能。
2. 结构分析零件结构简单对称,无尖角,对冲裁加工较为有利。
零件中部有一异形孔,孔的最小尺寸为6mm ,满足冲裁最小孔径min d ≥mm 20.1=t 的要求。
另外,经计算异形孔距零件外形之间的最小孔边距为5.5mm ,满足冲裁件最小孔边距min l ≥mm 35.1=t 的要求。
所以,该零件的结构满足冲裁的要求。
3. 精度分析:零件上有4个尺寸标注了公差要求,由公差表查得其公差要求都属IT13,所以普通冲裁可以达到零件的精度要求。
对于未注公差尺寸按IT14精度等级查补。
由以上分析可知,该零件可以用普通冲裁的加工方法制得。
落料冲孔复合模设计实例

落料冲孔复合模设计实例(一)零件工艺性分析工件为图1所示的落料冲孔件,材料为Q235钢,材料厚度2mm,生产批量为大批量。
工艺性分析内容如下:图1 工件图1.材料分析Q235为普通碳素结构钢,具有较好的冲裁成形性能。
2. 结构分析零件结构简单对称,无尖角,对冲裁加工较为有利。
零件中部有一异形孔,孔的最小尺寸为6mm,满足冲裁最小孔径≥的要求。
另外,经计算异形孔距零件外形之间的最小孔边距为5.5mm,满足冲裁件最小孔边距≥的要求。
所以,该零件的结构满足冲裁的要求。
3. 精度分析:零件上有4个尺寸标注了公差要求,由公差表查得其公差要求都属IT13,所以普通冲裁可以达到零件的精度要求。
对于未注公差尺寸按IT14精度等级查补。
由以上分析可知,该零件可以用普通冲裁的加工方法制得。
(二)冲裁工艺方案的确定零件为一落料冲孔件,可提出的加工方案如下:方案一:先落料,后冲孔。
采用两套单工序模生产。
方案二:落料—冲孔复合冲压,采用复合模生产。
方案三:冲孔—落料连续冲压,采用级进模生产。
方案一模具结构简单,但需两道工序、两副模具,生产效率低,零件精度较差,在生产批量较大的情况下不适用。
方案二只需一副模具,冲压件的形位精度和尺寸精度易保证,且生产效率高。
尽管模具结构较方案一复杂,但由于零件的几何形状较简单,模具制造并不困难。
方案三也只需一副模具,生产效率也很高,但与方案二比生产的零件精度稍差。
欲保证冲压件的形位精度,需在模具上设置导正销导正,模具制造、装配较复合模略复杂。
所以,比较三个方案欲采用方案二生产。
现对复合模中凸凹模壁厚进行校核,当材料厚度为2mm时,可查得凸凹模最小壁厚为4.9mm,现零件上的最小孔边距为5.5mm,所以可以采用复合模生产,即采用方案二。
(三)零件工艺计算1.刃口尺寸计算根据零件形状特点,刃口尺寸计算采用分开制造法。
(1)落料件尺寸的基本计算公式为尺寸,可查得凸、凹模最小间隙Zmin=0.246mm,最大间隙Zmax=0.360mm,凸模制造公差,凹模制造公差。
第二章第6节 冲压模具设计——复合模和连续模
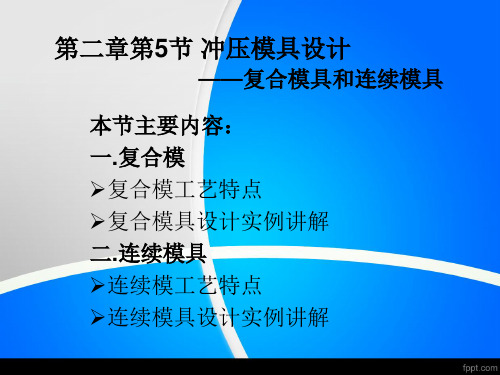
(1)工序排样的内容
①在冲切刃口设计的基础上,将各工序内容进行优化组合 形成一系列工序组,对工序排序,确定工位数和每一工位 的加工工序。 ②确定载体形式与坯料定位方式。 ③设计导正孔直径,确定导正销数量。 ④绘制工序排样图(图7-21)。 (2)工序排样类型
①落料型工序排样; ②切边型工序排样; ③混合型工序排样
4.正装和倒装复合模的比较:
结构的比较:凸凹模位置不同,废料和冲 件取出方式不同。 生产率的比较:倒装模比正装模生产率高; 安全性的比较:倒装模比正装模安全可靠。 在倒装复合模中,如果在上模内采用弹性装置, 也可保证冲件有较高的平直度。所以,倒装模比正 装模应用更广泛。
5.复合模与其它模的比较:
3.2搭边值的确定
3.3条料宽度的确定
3.4材料利用率
3.5计算冲压力
3.6计算模具压力中心
由于该零件完全对称于相互垂直的两条多层 次线,所以模具的压力中心在几何图形的中 模具的形式 复合模又可分为正装式和倒装式。
经分析,此工件无较高的平直度要求,工 件精度要求也较低,所以从操作方便、模具制 造简单等方面考虑,决定采用倒装式复合模。
工艺设计时必须得到试制或小批量生产的技术数据或工 序样件,必要时还可以使用简易模具或手工进行工艺验证, 以获得较为准确的零件展开形状及尺寸、工序性质、工序数 量、工序顺序以及工序件(半成品)尺寸等。而这些都是多工 位冲压条料排样设计的重要依据,而连续模排样设计是连续 模结构设计的关键。排样之后便可进行凸模、凹模、凸模固 定板、垫板、卸料装置,导料、定距等零部件的结构设计。 最后绘制模具总装配图和零件图,并提出使用维护的说明。
一、工艺方案分析
1.垫片冲压工艺分析 2.产品尺寸精度、粗糙度、断面质量分析
倒装复合模-模具设计模板-大学课程设计

落料冲孔复合模具设计一、零件工艺性分析零件为落料冲孔件,材料为H62,厚度为0.5mm 。
生产纲领为100万件/年,为大批量生产。
零件图如下所示:图1 接线片1.1 材料分析H62为普通黄铜,抗拉强度为385Mpa ,延伸率为15%,有良好的力学性能,冷态下塑性不错,切削性能好,适合冲裁加工。
1.2 结构分析零件外形几何结构简单,易于冲裁加工。
零件中部有一圆形孔,孔的尺寸为6mm ,满足冲裁最小孔径min d =6mm mm 5.0mm 5.010.1=⨯=≥t 的要求。
另外,经计算孔距零件外形之间的最小孔边距为1.5mm ,满足冲裁件最小孔边距的要求。
且工件的边缘不会产生膨胀或歪扭变形,零件的加工工艺性能好。
所以,该零件的结构满足冲裁的要求。
1.3 精度分析零件上尺寸标注了公差要求,由公差表查得其公差要求都属IT10到IT11之间,所以普通冲裁可以达到零件的精度要求。
综上所述,该零件具有良好的冲裁工艺性,适合冲裁加工。
二、冲裁工艺方案的确定零件为一落料冲孔件,可提出的加工方案如下:方案一:先落料,后冲孔。
采用两套单工序模生产。
方案二:落料—冲孔复合冲压,采用复合模生产。
方案三:冲孔—落料连续冲压,采用级进模生产。
方案一模具结构简单,但需两道工序、两副模具,生产效率低,零件精度较差,在生产批量较大的情况下不适用。
方案二只需一副模具,冲压件的形位精度和尺寸精度易保证,且生产效率高。
尽管模具结构较方案一复杂,但由于零件的几何形状较简单,模具制造并不困难。
方案三也只需一副模具,生产效率也很高,但与方案二比生产的零件精度稍差。
欲保证冲压件的形位精度,需在模具上设置导正销导正,模具制造、装配较复合模略复杂。
所以,比较三个方案欲采用方案二生产。
现对复合模中凸凹模壁厚进行校核,当材料厚度为0.5mm时,可查得凸凹模最小壁厚为0.75mm,现零件上的最小孔边距为1.5mm,所以可以采用复合模生产,即采用方案二。
复合模结构

图一:复合模的结构图空板上垫板上夹板母模下托板下垫脚下夹板 下模座外脱板打板内脱板公模123564911101287上模座13复合模其加工工件的工艺是多重的(如下料、冲孔、打凸、拉伸)故称为复合模;因为其导柱倒装所以也称为倒装模;而有时因其只是在冲压过后工序件为产品的外形(不冲孔、打凸等),也称为下料模;有时也称冲孔,下料模、剪口模。
复合模的主要功用是下料即冲裁后工序件是产品的展开外形,另会在此工序中加入如,冲孔、打凸、拉伸、抽牙等。
一般为第一工序。
1上模座的功用:保持冲模精度,固定上下模,易于架模。
其一般材质用A3铁料;或是用S50C 料而不用上垫板以节约成本。
2空板的功用:放置弹簧箱或优力胶,增加弹簧行程。
空板的形式是A3料在中间火割一个方孔,废料一般客户都会带回。
空板较厚,有时也可用上垫块(脚)替换。
3打板的功用:打板也有叫上承板的。
其主要是承接压力和垫板的功用差不多。
一般用45#,有时也会热处理至45º。
4上垫板的功用:防止冲头对模座侵入。
这时做为垫板的CR12料,热处理后的HRC为42º~45º而45#钢本身的特性所以此时垫板热处理也只是在45º左右。
5上夹板的功用:固定冲头、弹簧及上模座。
上夹板因是起固定做用,不承受力所以用45#的铁料,有的公司也会用C45。
夹板是不用热处理的,而且用软料易在后续的如修模、设变、改模中加工。
6母模板的功用:与公模作用,冲裁出产品的展开外形。
母模的材质一般用CR12MOV、SKD11,DC537公模板的功用:与母模板作用,冲裁出产品的展开外形及与冲头作用冲孔、拉伸、打凸等。
在通常情况下,公母模会做锥共用出。
直身的高度会根据所冲剪的材料和板材的厚度来确定,但一般不会低于3.0mm。
公母模同出时,母模割产品外形不放间隙即单+0.0割;公模放冲剪间隙即单-5﹪t。
公模的材质一般用CR12MOV、SKD11,DC53 8内外脱板的功用:脱料、压料保护冲头。
- 1、下载文档前请自行甄别文档内容的完整性,平台不提供额外的编辑、内容补充、找答案等附加服务。
- 2、"仅部分预览"的文档,不可在线预览部分如存在完整性等问题,可反馈申请退款(可完整预览的文档不适用该条件!)。
- 3、如文档侵犯您的权益,请联系客服反馈,我们会尽快为您处理(人工客服工作时间:9:00-18:30)。
案例2:复合模实例零件简图:如图1所示;零件名称:支架。
生产批量:大批量;材料:Q235A;材料厚度:2mm。
图1 零件图1、冲压件的工艺分析该支架零件形状简单,是一个外圆弧为R4.5m m的折弯件,其中Ф6mm的圆孔和6×12mm的腰形孔为安装孔,所以此两孔的位置尺寸是该零件需要保证的重点。
另外,该零件属隐蔽件,被其他零件完全遮蔽,外观上要求不高。
该零件板厚t=2mm,内表面弯曲半径为R2.5mm,大于Q235A板料的最小弯曲半径;腰形孔边到弯曲中心的距离L=4.5mm,大于2t(4mm),即腰形孔在弯曲变形区外,弯曲件的结构工艺性良好。
零件展开后形状简单、结构对称。
由冲压设计资料中可查出,冲裁件内外形所能达到的经济精度为IT12~IT10,而零件图中的尺寸未标注公差,即该零件的精度等级为IT14级,可知该零件的精度要求能够在冲裁加工中得到保证。
其他尺寸标注、生产批量等情况,也均符合冲裁的工艺要求,冲裁工艺性良好。
2、确定冲裁工艺方案与模具结构形式首先根据零件形状确定冲压工序类型和选择工序顺序。
因该零件的孔在弯曲变形区外,故其需要的基本工序有落料、冲孔和弯曲。
其中弯曲决定了零件的总体形状和尺寸,为最后一道工序。
根据冲载工序的不同选择可做出以下几种组合方案:方案一:先落料,再冲孔,最后折弯,由三套模具完成。
方案二:先采用落料冲孔复合模,然后折弯,由二套模具完成。
方案三:先采用冲孔落料级进模,然后折弯,由二套模具完成。
比较上述各方案可以看出,方案一的优点是:模具结构简单、寿命长、制造周期短、投产快。
缺点是:工序分散,需用模具、压力机和操作人员较多,劳动生产率低。
方案二落料冲孔在一道工序内完成,内、外形的位置尺寸精度高,工件的平整性好;方案三由于是先冲孔后落料,内、外形的位置尺寸精度不如方案二高,工件易弯曲,平整性不如方案二好,但操作安全、方便。
方案二和方案三与方案一相比,工序集中,劳动生产率高,但模具结构复杂,制造周期长。
综上所述,虽然该零件外观要求不高,但要求平整,两孔的安装位置尺寸要求得到保证,且为大批量生产,生产率要高,故采用方案二。
复合模有正装复合模和倒装复合模,该零件材料为Q235A ,板厚为2mm ,不属软、薄材料,且倒装复合模的废料可直接从压力机台面漏下,冲裁件由推件装置从上模推下,比较容易取出,操作安全方便,生产效率高,故采用倒装复合模,并采用后侧导柱导套导向,弹性卸料。
3、 主要工艺参数计算(1) 毛坯展开尺寸L=L 1+L 2+L 3其中 L 1=70-4.5=65.5(mm )20()180L r xt πϕ=+ r=2.5mm, t=2mm, 则r/t=2.5/2=1.3,查表得x=0.342090()(2.50.342)5()180180L r xt mm πϕπ=+=+⨯=L 3=30-4.5=25.5(mm)则 L=L 1+L 2+L 3=65.5+5+25.5=96(mm) 零件展开图(复合模的工序图)如图2所示(2) ① 用单排方案 (见图3)。
查表得a min =2.2mm ,a 1min =2mm ,板料剪裁时的下偏差Δ=0.9mm ,取a=3mm ,a 1=2.5mm 。
② 计算材料利用率条料宽度:B=96+2×3=102(mm) 送料步距:A=40+2.5=42.5(mm) 一个步距内零件的实际面积:S 1=(96-10)×40+(40-10×2)×10+(π×102)/2-2×π×32-(12-6)×6=3704.53(mm 2)一个步距内所需的毛坯面积:S0=A×B=42.5×102=4335(mm2)一个步距的材料利用率为:13704.53100%100%85.46%4335SSη=⨯=⨯=图3 排样图③计算冲压力和选择冲压设备查表得Q235A材料的抗剪强度:τ=310~380MPa,取τ=350 MPa落料力F1=KL1tτ=1.3×(40+86×2+40-10×2+π×10) ×2×350=1.3×263.416×2×350=239708.56(N)=239.7(KN)冲孔力F2=KL2tτ=1.3×(6×2+2×π×6) ×2×350=1.3×49.7×2×350=45227(N)=45.23(KN)查表得K卸=0.04 K推=0.055卸料力F卸= K卸×F1=0.04×239708.56=9588.34(N) =9.59(KN)推件力F推=n×K推×F2n为梗塞在凸凹模内的冲件数,取凸凹模刃口高度h=6mm,则n=2×h/t=2×6/2=6 F推=n×K推×F2=6×0.055×45227=14924.91(N)=14.92(KN) 总冲裁力F= F1+ F2+ F卸+ F推=239708.56+45227+9588.34+14924.91=309448.81(N)=309.45(KN) 根据所计算冲裁力,初选压力机型号为JA21-35(开式双柱固定台压力机),其公称压力为350KN,满足该冲裁件所需冲裁力的要求。
JA21-35的主要技术参数滑块形程:130mm最大闭合高度:280mm闭合高度调节量:60mm工作台尺寸:前后:380mm 左右:610mm工作台孔尺寸:前后:200mm 左右:290mm 直径:260mm垫板尺寸:厚度:60mm 直径:22.5mm模柄尺寸:直径:50mm 深度:70mm滑块底面尺寸:前后:210mm 左右:270mm④计算压力中心按比例画出零件形状,选定坐标系xoy,如图4 所示。
该零件上下对称,即y0=0,故只需计算x0即可。
将工件冲裁周边分成L1、L2、L3、L4、L5、L6、L7基本线段,求出各段长度及各段的重心位置:L4=20mm x4=96mm L5=86mm x5=43mmL6=2×(6+π×3)=30.85mm x6=15mm L7=π×6=18.85 mm x7=86mm112277012745.7l x l x l x x mm l l l +++==+++零件近似几何中心坐标48x mm =,与压力中心相差2.3mm ,为方便模具制造,取零件几何中心坐标48x mm =,y=0为模具制造中心。
⑤ 计算凸、凹模刃口尺寸查表得Z min =0.25mm, Z max =0.36mm零件图上未注公差的尺寸,属自由尺寸,可按IT14级确定工件尺寸的公差。
查公差表可得各尺寸公差为:零件外形:00.6240- mm 、00.8796- mm 、00.3610R - mm 零件内形:Ф0.3006+ mm 、0.300.4300612++⨯ mm 孔心距:710.37± mm 、31.033± mm 采用单配加工法加工模具的工作零件。
落料部分以落料凹模为基准计算,落料凸模按间隙值配制;冲孔部分以冲孔凸模为基准计算,冲孔凹模按间隙值配制。
即以落料凹模、冲孔凸模为基准,凸凹模按间隙值配制。
落料凹模的尺寸:查表得:尺寸00.6240-、00.8796-、00.3610R -的磨损系数x 均为0.5 (冲件精度为IT14级:x =0.5)0.620.1640040(400.50.62)39.69++=-⨯=凹(mm) 0.870.22496(960.50.87)95.57++=-⨯=凹(mm)0.360.09410(100.50.36)9.82R ++=-⨯=凹(mm) ● 落料凸模的尺寸:尺寸40凸、96凸按相应凹模尺寸配作,保证双面间隙在0.25~0.36mm 之间,尺寸10R 凸按相应凹模尺寸配作,保证单面间隙在0.13~0.18mm 之间。
● 冲孔凸模的尺寸:查表得:尺寸0.3006+、0.300.4300612++⨯、的磨损系数x 均为0.5 000.30.0846(60.50.3) 6.15φ--=+⨯=凸(mm)000.30.0846(60.50.3) 6.15--=+⨯=凸(mm)000.430.11412(120.50.43)12.22--=+⨯=凸(mm)● 冲孔凹模的尺寸:尺寸6φ凹、612⨯凹凹按相应凸模尺寸配作,保证双面间隙在0.25~0.36mm 之间。
(mm)● 孔心距:09.0718237.07171±=⨯±=L (mm) 08.0338231.03333±=⨯±=L (mm)4、 模具主要零部件的结构与尺寸设计① 工作零件的结构与尺寸设计 ● 落料凹模:凹模厚度:H=Kb( ≥15mm)查表得K=0.28 则H=Kb=0.28×96=27(mm)凹模壁厚:C=(1.5~2)H=(1.5~2) ×24=40~54 (mm) 实取H=28mm ,C=42mm凹模边长:L=b+2c=96+2×42=180(mm)凹模宽度:B=40+2×42=124,实取B=125mm 凹模尺寸为:180×125×28(mm) 零件简图如图5所示:图5凹模冲孔凸模:Ф6mm冲头:冲头长度:L=h1+h2=25+25=50(mm)其中:h1——凸模固定板厚h2——凹模板厚冲头的固定形式:采用台阶式固定零件简图如图6所示:图6 Ф6mm冲头6×12mm腰形冲头:冲头长度:计算同Ф6mm冲头为50mm。
冲头的固定形式:采用圆柱销固定零件简图如图7所示:图7 6×12mm腰形冲头凸凹模:凸凹模长度:L= h1+h2+h =20+20+20=60(mm)其中:h1——凸凹模固定板厚h2——弹性卸料板厚h——增加长度(包括凸模进入凹模深度,弹性元件安装高度等)凸凹模内外刃口间壁厚校核:该零件板厚2 mm,查表得凸凹模允许最小壁厚4.9mm,根据该冲裁件结构实际内外刃口间最小壁厚为7 mm,故该凸凹模侧壁强度足够。
零件简图如图8所示图8凸凹模其他模具零件的结构尺寸(略)5、冲压设备的校核初选压力机型号为JA21-35,该压力机最大装模高度H max为220mm(不装垫板的最大装模高度),该模具闭合高度为236mm,所选压力机的装模高度不符合要求,改选用型号为J23-40的压力机,其主要工艺参数如下:公称压力:400KN滑块行程:100mm最大闭合高度:330mm连杆调节长度:65mm垫板厚度:65mm工作台尺寸(前后×左右):460mm×700mm经校核,该压力机的公称压力、安装尺寸及装模空间均符合要求。