产品制程工艺
smt制程基本工艺流程

smt制程基本工艺流程《SMT制程基本工艺流程》SMT(Surface Mount Technology)是一种表面贴装技术,用于电子元器件的表面装配。
它不仅提高了电子产品的集成度和可靠性,还大大提高了生产效率。
SMT制程基本工艺流程包括以下几个关键步骤。
1. 设计与制造:在SMT制程中,首先需要进行PCB(Printed Circuit Board)设计和制造。
PCB是电子元器件的载体,设计良好的PCB可以提高电子产品的性能和可靠性。
2. 印刷焊膏:印刷焊膏是SMT制程中的第一步,用于在PCB表面涂覆一层薄膜焊膏。
这一步骤需要高精度的设备和操作,以确保焊膏均匀涂覆在PCB表面上。
3. 贴装:贴装是SMT制程中的关键步骤,它包括将电子元器件(如贴片元件、IC芯片等)粘贴在覆有焊膏的PCB上。
这一步骤需要自动贴片机或其他设备来实现高速、高精度的贴装过程。
4. 固化焊接:固化焊接是SMT制程中的重要步骤,它通过加热将焊膏固化,使电子元器件与PCB表面牢固地焊接在一起。
这一步骤需要控制加热温度和时间,以确保焊接质量和稳定性。
5. 检测与修正:在SMT制程中,还需要进行元器件的检测与修正。
通过视觉检测、X射线检测等手段,对焊接质量进行检查,并对可能存在的问题进行修正,以确保产品质量和可靠性。
总的来说,SMT制程基本工艺流程是一个多步骤、多环节的复杂过程。
通过精密的设备和严格的工艺控制,可以实现高效、高质量的电子产品生产。
随着电子技术的不断发展和进步,SMT制程也在不断完善和提升,以满足不断变化的市场需求。
smt制程基本工艺流程

smt制程基本工艺流程《SMT制程基本工艺流程》SMT(Surface Mount Technology)是一种在电子制造中广泛使用的工艺技术,它使用表面贴装元器件(Surface Mount Devices,SMD)在印刷电路板(Printed Circuit Board,PCB)上进行组装和焊接。
SMT制程流程是整个SMT生产过程中最核心的部分,它直接影响到产品质量和生产效率。
SMT制程基本工艺流程主要包括以下几个步骤:1. 设计与工程确认:在SMT制程开展之前,首先需要完成PCB的设计和工程确认。
这一步骤包括元器件布局设计、焊接方式确定、工艺参数确认等工作,确保SMT制程能够顺利进行。
2. 资料准备:在SMT制程进行之前,需要准备好焊接工艺规范、元器件数据表、焊接模板等资料,以便于操作人员进行生产操作。
3. 半成品制备:在SMT制程中,需要将PCB、元器件等半成品准备好,包括清洗、防潮处理、保护膜覆盖等工作。
4. SMT贴附:在此步骤中,将元器件贴附到PCB上,这是SMT制程中的重要步骤。
通常使用自动点胶机和贴片机来完成元器件的精确贴附工作。
5. 过爐焊接:完成贴附后的PCB将进行过爐焊接,以确保元器件与PCB的可靠连接。
这一步骤通常使用回流焊或波峰焊来完成。
6. 视觉检验:完成焊接后,需要进行视觉检验,以确保焊接质量符合标准要求。
7. 包装与出货:最后一步是将焊接合格的PCB进行包装,并出货给客户。
以上是SMT制程基本工艺流程的主要步骤,通过严格的工艺控制和精细的操作,可以确保产品质量和生产效率达到预期目标。
随着科技的不断发展,SMT制程也在不断优化和升级,为电子制造业的发展做出了重要贡献。
SMT制程工艺操作规程完整
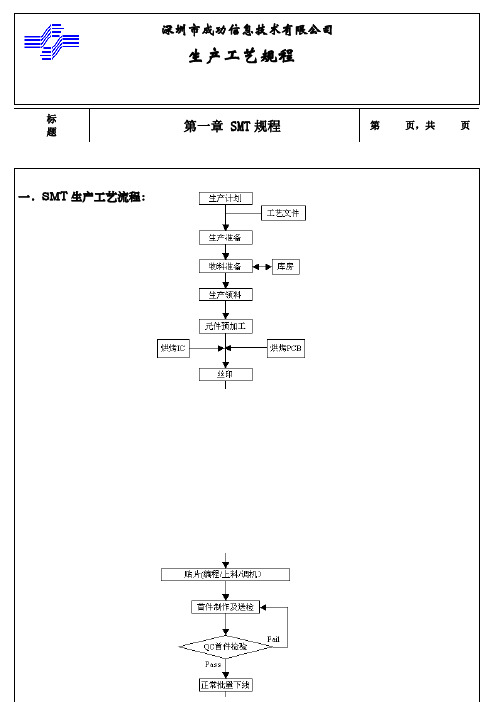
深圳市成功信息技术有限公司生产工艺规程标题第一章 SMT规程一.SMT生产工艺流程:第页,共页深圳市成功信息技术有限公司生产工艺规程标第一章 SMT规程第页,共页题标题第一章 SMT规程4.锡膏/红胶印刷: 1>作业依据:《锡膏印刷作业指导书》\《SMT红胶印刷操作规》2>作业注意事项:a.锡膏印刷必须在下线前做好锡膏解冻(4小时以上)及搅拌工作(搅拌时间必须在10分钟以上,搅拌时力度应适中、均匀),红胶解冻时间至少为4-8小时,并要检查钢网是否为所对应的机型、以及是否符合钢网标准(如是否完整无损坏、严重变形、堵孔等)。
b.印刷工位处不能有风扇或空调对着吹风,因为风会破坏锡膏的粘着特性。
c.丝印台及钢网在印刷前需清洁干净,不得有脏物。
d.在试印和钢过程中发现钢网或其它问题导致不能正常印刷时即时知会拉长处理。
e.印刷过程中要随时保持钢网底面及丝印台面的清洁,特别是对有金手指的板印刷时要特别做好清洁防护,印几块板后就要清洁一次,以防止金手指上锡。
f.在印刷过程中注意适当速度和角度,批量下线时每印刷好一块PCB 板后检查印刷的质量,合格的才能流入下一工位,印刷好的PCB板堆积数量不得超过5PCS以上.g.当印红胶过程中有个别印胶质量不佳的点时,需用棉签粘清洗剂清洗干净,并重新点胶以保证点胶品质h.在批量印刷过程中,当印刷质量变坏时,须用棉布沾酒精,对钢网各孔位及背面进行清洗,清洁后用压缩空气将印刷部分的空位吹通。
在清洗、第页,共页档,同时进行文件版本变更。
标题第一章 SMT规程e.对于操作员及生产拉长反馈之问题要即时进行确认和程序调整并做相应之程序文件更新。
f.编程员应做好相关产品贴片程序文件备份工作,防止数据丢失。
g.除被受权人员外,其他任何人不得私自进行贴片机主控计算机的操作,更不能进行贴片机程序的调用、更改。
3>作业质量要求:编程员要对所输出之贴片机程序文件及排料表的正确性进行检验确认,确保输出文件的正确性,并对操机员及拉长反馈的问题进行即时程序调整。
PCBA制程工艺控制要点

PCBA制程工艺控制要点PCBA(Printed Circuit Board Assembly)制程工艺控制是指在PCBA制造过程中,对各项工艺参数进行有效控制,以确保产品的质量和可靠性。
以下是PCBA制程工艺控制的要点:1.布板设计:布板设计是PCBA制程的基础,应根据电路图和产品需求进行布线,合理布置元件,避免信号冲突和干扰。
同时,还需要合理设置通孔位置和数量,以方便后续的组装和焊接。
2.元件采购与管理:在元件采购时,应优选可靠性高的供应商,并建立供应商的资质评估和管理体系。
同时,要对采购的元件进行严格的检验和测试,避免使用损坏、假冒或者不合格的元件。
3.焊接工艺控制:焊接是PCBA制程中最关键的一步,影响着产品的可靠性和性能。
在焊接过程中,应注意控制焊接温度、焊接时间和焊接压力等参数,保证焊点的质量和可靠性。
同时,还要合理选择焊接材料和工艺,确保能够满足产品的使用要求。
4.贴装工艺控制:贴装是将元件粘贴在PCB上的过程,需要控制贴装机的精度和稳定性。
在贴装过程中,要注意控制温度、湿度和气压等环境参数,以确保元件的精确位置和好的贴合性。
此外,还需要对贴装后的元件进行检查和测试,确保贴装质量达到要求。
5.测试和检验:在PCBA制程中,测试和检验是确保产品质量和可靠性的重要环节。
应建立全面的测试和检验方案,包括原件检测、电气测试、功能测试和环境测试等,确保产品符合设计要求和使用条件。
6.工艺参数监控和调整:在PCBA制程中,要建立良好的工艺参数监控和调整机制。
通过实时监测和记录各项工艺参数,及时发现和解决问题,并进行合理的调整,确保产品质量和稳定性。
8.员工培训和意识提升:PCBA制程工艺控制还需要加强对员工的培训和意识提升,提高其对质量控制和基本工艺的认识和理解。
培训内容包括质量要求、工艺规范、安全操作和质量问题的处理等,以提高员工的专业技能和责任意识。
综上所述,PCBA制程工艺控制要点包括布板设计、元件采购与管理、焊接工艺控制、贴装工艺控制、测试和检验、工艺参数监控和调整、质量管理体系建设以及员工培训和意识提升等。
晶圆制程工艺流程
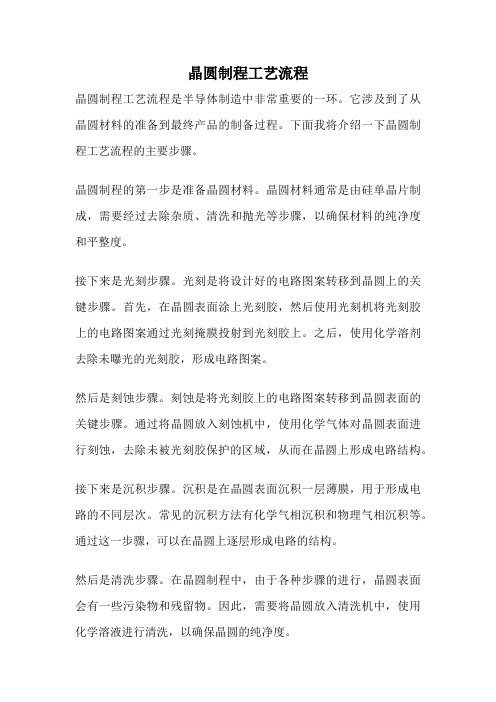
晶圆制程工艺流程晶圆制程工艺流程是半导体制造中非常重要的一环。
它涉及到了从晶圆材料的准备到最终产品的制备过程。
下面我将介绍一下晶圆制程工艺流程的主要步骤。
晶圆制程的第一步是准备晶圆材料。
晶圆材料通常是由硅单晶片制成,需要经过去除杂质、清洗和抛光等步骤,以确保材料的纯净度和平整度。
接下来是光刻步骤。
光刻是将设计好的电路图案转移到晶圆上的关键步骤。
首先,在晶圆表面涂上光刻胶,然后使用光刻机将光刻胶上的电路图案通过光刻掩膜投射到光刻胶上。
之后,使用化学溶剂去除未曝光的光刻胶,形成电路图案。
然后是刻蚀步骤。
刻蚀是将光刻胶上的电路图案转移到晶圆表面的关键步骤。
通过将晶圆放入刻蚀机中,使用化学气体对晶圆表面进行刻蚀,去除未被光刻胶保护的区域,从而在晶圆上形成电路结构。
接下来是沉积步骤。
沉积是在晶圆表面沉积一层薄膜,用于形成电路的不同层次。
常见的沉积方法有化学气相沉积和物理气相沉积等。
通过这一步骤,可以在晶圆上逐层形成电路的结构。
然后是清洗步骤。
在晶圆制程中,由于各种步骤的进行,晶圆表面会有一些污染物和残留物。
因此,需要将晶圆放入清洗机中,使用化学溶液进行清洗,以确保晶圆的纯净度。
最后是封装步骤。
封装是将制备好的芯片封装成最终产品的步骤。
在封装过程中,芯片会被封装在塑料封装体中,并进行焊接和封装密封等步骤,以保护芯片并提供电气连接。
晶圆制程工艺流程是一个复杂而关键的过程,它涉及到了多个步骤,包括晶圆材料的准备、光刻、刻蚀、沉积、清洗和封装等。
每个步骤都需要精确的控制和严格的质量检测,以确保最终产品的质量和性能。
晶圆制程工艺的不断改进和创新,对于半导体行业的发展起着重要的推动作用。
工艺技术和制程技术

工艺技术和制程技术工艺技术和制程技术是制造业中非常重要的概念。
工艺技术包括了产品的设计、生产过程中的材料选择、生产流程安排等一系列环节,而制程技术则涉及到了具体的生产技术和方法。
这两者紧密配合,共同决定了产品的质量、成本和效率。
工艺技术的重要性不言而喻。
一项产品的设计直接影响着其市场竞争力和销量。
一个好的设计除了要满足功能需求外,还要考虑到制造的可行性和成本。
例如,在设计汽车时,需要考虑到材料的选择、组件的安装和连接等一系列工艺技术问题。
精细的设计可以使得汽车结构更加坚固,驾驶更加稳定,同时又要保证成本的可控。
这就需要设计师具备扎实的工艺技术知识和经验。
制程技术是工艺技术的具体实施方式。
在软件开发行业中,有一个著名的项目管理方法叫做“敏捷开发”。
敏捷开发将软件开发过程分割成多个小的循环周期,每个周期都有相关的工作任务,开发人员按照固定的方法和流程进行工作,最后将结果集成在一起形成最终的产品。
这种方法可以提高开发效率,减少错误率,并且保证了软件质量。
在制造业中,制程技术也是决定产品质量和成本的重要因素。
以电子产品为例,现代电子产品通常都涉及到了多个组件的安装和连接,如果使用传统的手工操作,势必会导致效率低下和产品质量不稳定。
而采用自动化制程技术,可以大大提高生产效率和产品质量。
自动化制程技术还可以减少人力投入,降低产品生产成本。
制程技术还包括了物料管理和质量控制等方面。
在制造业中,物料的采购、储存和使用都需要制程技术的支持。
例如,在组装电子产品时,需要准确地组织各个物料的供应和使用,保证生产能够连续进行并且不出现缺料的情况。
另外,质量控制也是制程技术的重要组成部分。
通过制程技术的支持,可以对产品进行全面的检测和测试,及时发现和纠正质量问题,确保产品的合格率和用户满意度。
综上所述,工艺技术和制程技术在制造业中非常重要。
工艺技术负责产品设计和生产流程的规划,制程技术则负责具体的生产技术和方法的实施。
两者密切配合,共同决定了产品的质量、成本和效率。
紧固件制程工艺流程
紧固件制程工艺流程
《紧固件制程工艺流程》
紧固件制程工艺流程是指将原材料经过一系列加工和生产过程,最终形成成品紧固件的制造流程。
紧固件包括螺丝、螺栓、螺母、螺钉等产品,广泛应用于机械制造、航空航天、汽车等领域。
而制程工艺流程的精细化和标准化对于保证产品质量和提高生产效率至关重要。
首先,原材料准备是制程工艺流程的第一步。
通常原材料为金属材料,如碳钢、不锈钢、铜等。
原材料需要经过原材料筛选、清洗、熔炼等过程,保证其质量和性能符合生产要求。
其次,原材料加工是制程工艺流程的关键环节之一。
原材料需要经过切削、锻造、滚压等加工方法,将原材料加工成符合产品要求的形状和尺寸。
在此过程中,需要考虑材料的硬度、延展性等特性,确保产品的机械性能符合标准要求。
然后,热处理是制程工艺流程中不可或缺的环节。
热处理能够改善原材料的内在结构,提高其硬度和耐磨性,使产品具有更好的使用性能。
常见的热处理方法包括淬火、回火、渗碳等。
最后,表面处理和包装是制程工艺流程的最后步骤。
表面处理主要是通过镀层、酸洗、喷砂等方法,使产品的表面具备防腐蚀、美观等特性。
而包装则是保证产品在运输和储存过程中不受损坏,同时便于管理和销售。
综上所述,紧固件制程工艺流程是一个复杂而精细的制造过程,在现代工业生产中扮演着重要的角色。
通过严格的质量控制和标准化的流程管理,可以保证生产出高质量、高性能的紧固件产品。
连接器的制程和工艺
连接器的制程和工艺连接器制程和工艺是指在连接器的生产过程中所采用的工艺流程和制造工艺。
连接器是电子元器件中的一种,用于将各种电子设备的电路传输、输入和输出互连起来。
连接器的制程主要包括以下几个方面:原材料准备、材料加工、连接器成型、表面处理、检测和包装。
首先是原材料准备。
连接器的原材料通常是金属和塑料。
金属一般采用黄铜、磷青铜、不锈钢等。
塑料一般采用工程塑料,如PBT、PA、PC等。
在这个过程中,需要对原材料进行选型和采购,并按照制程要求进行质量检测。
第二是材料加工。
在连接器的制造过程中,需要对金属和塑料进行加工。
金属加工一般包括冷镦、铣削、折弯、锉削等工艺。
塑料加工一般包括注塑成型、挤出成型等工艺。
通过材料加工,可以将金属和塑料加工成所需的连接器零部件。
第三是连接器成型。
连接器成型是连接器制造的关键工艺。
连接器的成型一般采用模具成型工艺,将加工好的连接器零部件放入模具中,经过加热和压力作用,使金属和塑料材料充分熔融和流动,以达到成型连接器的目的。
第四是表面处理。
连接器的表面处理主要是为了改善连接器的电气性能、机械强度和防腐蚀能力。
常见的表面处理工艺有电镀、热处理、喷涂等。
电镀一般包括镀金、镀银、镀锡等。
热处理主要是通过加热和冷却过程改变连接器的结构和性能。
第五是检测。
连接器在制造过程中需要进行各种检测和测试。
常见的检测项目包括外观检查、尺寸测量、电气性能测试、力学性能测试等。
这些检测和测试可以保证连接器的质量和性能符合要求。
最后是包装。
连接器制造完成后,需要进行包装和标识。
包装一般采用塑料袋、纸箱等方式,并附上相应的产品标识和说明书。
包装的目的是保护连接器免受损坏,并方便运输和销售。
总的来说,连接器的制程和工艺是一个复杂的过程,涉及到多个环节和工艺流程。
通过合理的工艺和制程控制,可以生产出质量优良、性能稳定的连接器产品,满足不同应用场景的需求。
环氧工艺品生产流程
环氧工艺品生产流程如下:
1.将辅料各种适量按照一定的顺序加入到环氧树脂中(如
果操作温度较低,可以首先将环氧树脂加热到适当的粘
度范围,便于操作。
),搅拌均匀后静置5分钟,使
搅拌中产生的气泡消失后待用。
2.准备好改性胺类固化剂待用(注意未曾使用时密封保存,
避免接触空气,以免受潮使固化制品表面泛白。
)。
3.处理好模具,并且将所需饰品内设安装好(此操作可以
同1、2步操作同时进行)。
4.将预先准备好的两种材料按照厂家提供的比例混合均
匀(环氧树脂中添加的辅料可以忽略不计)后从准备好
的模具的内壁一侧缓慢倒入直至到自己所需要的量。
5.保持水平放入一定温度的烘箱内或者适宜固化的环境
中固化。
6.固化完成后,从模具中稳妥取出制品。
UV点胶设计及制程工艺分享
点胶槽整体截面尺寸需保证一致,不一致会导致一部分地方少 胶,一部分多胶,点胶不易控制。 点胶槽底部尽量保持在同一水平上,胶水粘稠度包容性大,倾 斜角度过大的话,流动性好的胶水容易向下流,导致胶水不均 匀,容易不密封。
01 UV 结构设计
零件材料
零件材料尽量选用ABS和PC,条件好的话尽量选用耐化材料,因为点胶的零件使用场景多涉及到各种温度,一般公司会要 求做水浴测试,或蒸烤测试,检验胶水耐温性能。
双Y点胶手柄
压力桶
PART Three
UV点胶检测
03 UV 点胶检测
气密性检测 一般UV工艺的产品有两种,一种是带孔的产品,如扫地机的水箱,一种是密封的产品。 1)带气孔产品 带气孔产品为常见产品,一般采用气密性检测方式, 检测设备包括:气密性检测仪和自动测试工装,这种组合的方式精度相对较高。 测量方式:一般分为进气和抽气两种,各有优劣。将气源冲入气孔用检测机构将孔周边堵塞, 常见测量参数:充气3~5S,气压4~20KPa不止,根据产品高度和承受压力决定。 保压一般5S即可测试不良品。 2)密封性产品 密封产品一般会采用水检+气检方式, 检测设备:气密性测试仪和密封压力容器,这种组合方式可有效将不良品检出。 测量方式:在密封压力容器内加入适量水,将产品没入水中,盖住压力容器,向里面充气。 常见测量参数:一般充气压力在10KPa以上,压力越大,越容易检出,保压时间要适当延长, 一般30S可有效检出不良,不良品内部会有明显水存在。
03 UV 点胶检测
零件颜色
零件尽量选用透明或浅色系,因为UV胶水固话需要紫外线照射,深色系零件,紫外线无法有效穿透,会降低紫外光强度, 导致产品胶水干的慢或无法快干。 此外,UV固话和光强功率和波长有关,功率越大越有利于穿透障碍,利于固化
- 1、下载文档前请自行甄别文档内容的完整性,平台不提供额外的编辑、内容补充、找答案等附加服务。
- 2、"仅部分预览"的文档,不可在线预览部分如存在完整性等问题,可反馈申请退款(可完整预览的文档不适用该条件!)。
- 3、如文档侵犯您的权益,请联系客服反馈,我们会尽快为您处理(人工客服工作时间:9:00-18:30)。
3D/立体产品制程工艺
一、产品来料检查(抽检);
根据客户信息,产品要求,规章产品生产制造管控等级规定。
产品核对:
①;确认产品材料型号、厚度。
②;确认产品材料制造批次。
③;确认产品要求。
④;确认产品数量。
⑤;确认产品变更序号、变更信息、变更位置。
外观要求:
①;刮花,产品来料全检/抽检(正反面),超过抽检标准为全检,依据产品面积、刮花
程度、深度,是否在蚀刻区域,或对下一工序是否有影响。
②;压伤,产品来料全检/抽检(正反面),超过抽检标准为全检,
轻微:模印、毛刺、(不影响功能,制程、使用性能等可接受,续生产)。
严重:正反面观、感如有明显凹凸不平或大于客户规定要求。
③;变形,产品来料全检/抽检(正反面),超过抽检标准为全检,依据客户产品要求,
变形趋势、变形量、变形程度。
以上问题处理:
发现严重刮花、压伤、变形,应进行产品全检,隔离,申报处理。
二、治具;
①;包装运输盒,包装盒必须要防震、防压、防摔、隔离等作用。
②;电泳挂具,
③;镭雕治具
④;蚀刻治具
三、电泳;
①;材料电泳挂位排布(上挂不能挂在蚀刻区域或妨碍蚀刻区域)。
②;电泳挂具是否导电,电流量是否符合电泳要求,挂具的手柄是否有安全胶体保护。
③;电泳前,材料表面除油、除锈。
④;酸洗,配比酸洗溶液(硫酸与水中和)。
⑤;清水或纯水过滤污垢水洗。
⑥;电解电泳槽;电泳漆的配比,电泳槽的导电性能设备是否符合挂具挂位的电流量,
⑦;电泳漆膜厚,(0.08-0.15)MM,根据产品的蚀刻要求及产品的性能变更。
⑧;烤箱,烘烤时间与温度的配合,根据产品的材料特性,材料的型号,油墨的厚度来
恒定电泳烘烤时间与温度。
一般产品烘烤时间为30-50分钟,烘烤温度在200-250℃为宜
注:电泳生产前必须做好首件的确认,巡检电泳漆与电泳槽是否符合生产的需求。
电泳后产品表面防止有灰尘的颗粒,赃物等电泳不良现象。
四、镭雕;
①;确认客户图档信息。
②;确认产品图档要求及公差尺寸。
③;确认电泳产品是否符合图档、图纸规格、型号。
④;确认产品图档尺寸的补强的蚀刻公差。
⑤;确认镭雕区域及镭雕要求。
⑥;确认镭雕治具及镭雕设备的检测。
调机工作;
①;调整激光的强度
②;调整参数设定
③;调整镭雕位置尺寸
注:镭雕成品的确认
确认镭雕首件的检测,确认镭雕位置是否符合产品要求的位置尺寸,镭雕人员应该佩戴手指套,预防镭雕好的产品与镭雕区域变色、脏污、生锈等现象。
五、检测
①;检测镭雕位置尺寸是否符合要求。
②;检测镭雕区域的数量,预防出现漏雕现象。
③;与镭雕面是否干净。
六、蚀刻一线
蚀刻一(补油)、
①;检查产品便面因运输或碰、刮伤的产品非蚀刻区域的表面油墨是否完好。
②;填补挂具的挂位空白处。
蚀刻一(蚀刻治具、摆盘)、
①;确认蚀刻区域,确认蚀刻的正反面。
②;确认蚀刻治具是否符合产品进机生产。
③;蚀刻产品的摆放位置,“符合蚀刻机的摆放位置”。
七、蚀刻二线
①;确认蚀刻图档、文件、要求、公差。
②;确认蚀刻区域(双面或单面)
③;确认蚀刻材质
④;确认蚀刻深度
⑤;蚀刻设备是否正常,蚀刻机生产前的检修与维护
⑥;蚀刻工检治具的准备
八、蚀刻三线
①;蚀刻成品首件的确认(无首件确认不可生产)
②;蚀刻成品巡检(蚀刻深度、蚀刻表面、蚀刻区域)
③;蚀刻成品抽检(蚀刻深度、蚀刻表面、蚀刻区域)
九、脱模线
①;脱漆的安全装置及流水线工具
②;脱漆剂的使用规范
③;产品表面脱漆标准及要求
④;水洗过滤
十、清洗线
①;清水过滤
②;超声波清洗
③;除油、除污清洗
目地要求:去除成品表面的赃污、残留产品表面药水。
十一、表面处理
十二、成品检测
①;确认蚀刻区域的位置,蚀刻表面效果蚀刻
②;确认蚀刻后处理及表面要求,外观的检测
③;确认蚀刻成品位置尺寸的测量是否符合客户要求
④;成品外观要求
⑤;成品蚀刻报表的填写记录
十三、产品包装
①;确认图纸及产品信息
②;确认图纸编号、品名
③;确认产品客户制作要求及检测要求
④;产品规格、型号、良(不良)品区分
⑤;包装素材盒选用(产品等级,及产品要求制定),防震、防压、易碎标致
⑥;包材符合ROHS及环保循环利用为好
⑦;箱体外应贴客户产品信息
规格要求:◆产品信息编号
◆产品名称
◆产品规格、型号
◆产品数量
◆产品批次
◆客户及供应商名称
◆产品制造生产日期
◆产品检测人员或QC标签
◆产品备注
十四、物控
①;产品制造信息出入登记
②;检查产品包装、数量、客户信息及要求标识卡。