空气压缩机曲轴零件的机械加工工艺及夹具毕业设计论文英译汉
空气压缩机曲轴的加工工艺及夹具设计概述
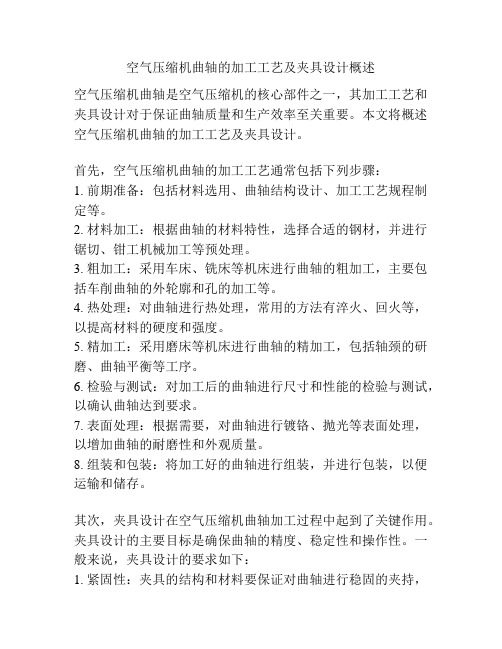
空气压缩机曲轴的加工工艺及夹具设计概述空气压缩机曲轴是空气压缩机的核心部件之一,其加工工艺和夹具设计对于保证曲轴质量和生产效率至关重要。
本文将概述空气压缩机曲轴的加工工艺及夹具设计。
首先,空气压缩机曲轴的加工工艺通常包括下列步骤:1. 前期准备:包括材料选用、曲轴结构设计、加工工艺规程制定等。
2. 材料加工:根据曲轴的材料特性,选择合适的钢材,并进行锯切、钳工机械加工等预处理。
3. 粗加工:采用车床、铣床等机床进行曲轴的粗加工,主要包括车削曲轴的外轮廓和孔的加工等。
4. 热处理:对曲轴进行热处理,常用的方法有淬火、回火等,以提高材料的硬度和强度。
5. 精加工:采用磨床等机床进行曲轴的精加工,包括轴颈的研磨、曲轴平衡等工序。
6. 检验与测试:对加工后的曲轴进行尺寸和性能的检验与测试,以确认曲轴达到要求。
7. 表面处理:根据需要,对曲轴进行镀铬、抛光等表面处理,以增加曲轴的耐磨性和外观质量。
8. 组装和包装:将加工好的曲轴进行组装,并进行包装,以便运输和储存。
其次,夹具设计在空气压缩机曲轴加工过程中起到了关键作用。
夹具设计的主要目标是确保曲轴的精度、稳定性和操作性。
一般来说,夹具设计的要求如下:1. 紧固性:夹具的结构和材料要保证对曲轴进行稳固的夹持,避免加工过程中的移动和变形。
2. 刚性和稳定性:夹具需要具备足够的刚性和稳定性,以确保在高速切削过程中不产生震动和振动,影响曲轴加工质量。
3. 操作性:夹具的设计应该考虑到操作人员的便捷性和安全性,方便加工过程中的夹紧和释放。
4. 运动控制:夹具应具备精确的夹紧力控制和夹持位置控制,以确保加工与装夹质量的一致性。
综上所述,空气压缩机曲轴的加工工艺和夹具设计对于曲轴的质量和生产效率至关重要。
通过合理的加工工艺和夹具设计,可以确保空气压缩机曲轴的精度和稳定性,提高生产效率和产品质量。
空气压缩机曲轴的加工工艺和夹具设计对于保证曲轴质量和生产效率至关重要。
在空气压缩机曲轴的加工工艺中,前期准备是非常关键的一步。
机械类英语论文及翻译翻译
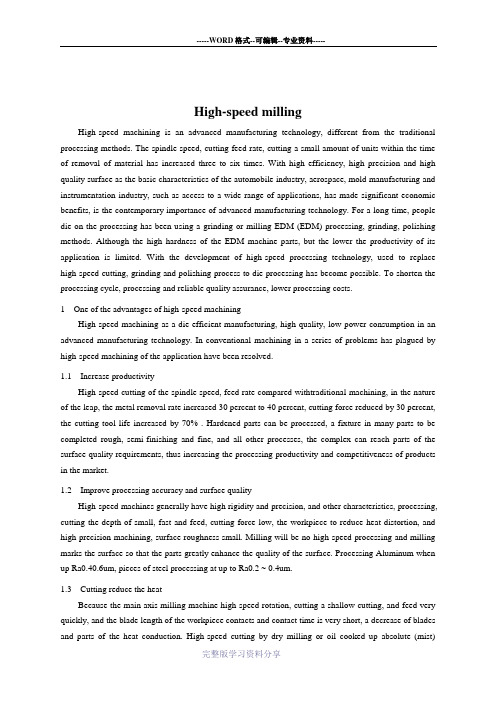
High-speed millingHigh-speed machining is an advanced manufacturing technology, different from the traditional processing methods. The spindle speed, cutting feed rate, cutting a small amount of units within the time of removal of material has increased three to six times. With high efficiency, high precision and high quality surface as the basic characteristics of the automobile industry, aerospace, mold manufacturing and instrumentation industry, such as access to a wide range of applications, has made significant economic benefits, is the contemporary importance of advanced manufacturing technology. For a long time, people die on the processing has been using a grinding or milling EDM (EDM) processing, grinding, polishing methods. Although the high hardness of the EDM machine parts, but the lower the productivity of its application is limited. With the development of high-speed processing technology, used to replace high-speed cutting, grinding and polishing process to die processing has become possible. To shorten the processing cycle, processing and reliable quality assurance, lower processing costs.1 One of the advantages of high-speed machiningHigh-speed machining as a die-efficient manufacturing, high-quality, low power consumption in an advanced manufacturing technology. In conventional machining in a series of problems has plagued by high-speed machining of the application have been resolved.1.1 Increase productivityHigh-speed cutting of the spindle speed, feed rate compared withtraditional machining, in the nature of the leap, the metal removal rate increased 30 percent to 40 percent, cutting force reduced by 30 percent, the cutting tool life increased by 70% . Hardened parts can be processed, a fixture in many parts to be completed rough, semi-finishing and fine, and all other processes, the complex can reach parts of the surface quality requirements, thus increasing the processing productivity and competitiveness of products in the market.1.2 Improve processing accuracy and surface qualityHigh-speed machines generally have high rigidity and precision, and other characteristics, processing, cutting the depth of small, fast and feed, cutting force low, the workpiece to reduce heat distortion, and high precision machining, surface roughness small. Milling will be no high-speed processing and milling marks the surface so that the parts greatly enhance the quality of the surface. Processing Aluminum when up Ra0.40.6um, pieces of steel processing at up to Ra0.2 ~ 0.4um.1.3 Cutting reduce the heatBecause the main axis milling machine high-speed rotation, cutting a shallow cutting, and feed very quickly, and the blade length of the workpiece contacts and contact time is very short, a decrease of blades and parts of the heat conduction. High-speed cutting by dry milling or oil cooked up absolute (mist)lubrication system, to avoid the traditional processing tool in contact with the workpiece and a lot of shortcomings to ensure that the tool is not high temperature under the conditions of work, extended tool life.1.4 This is conducive to processing thin-walled partsHigh-speed cutting of small cutting force, a higher degree of stability, Machinable with high-quality employees compared to the company may be very good, but other than the company's employees may Suanbu Le outstanding work performance. For our China practice, we use the models to determine the method of staff training needs are simple and effective. This study models can be an external object, it can also be a combination of internal and external. We must first clear strategy for the development of enterprises. Through the internal and external business environment and organizational resources, such as analysis, the future development of a clear business goals and operational priorities. According to the business development strategy can be compared to find the business models, through a comparative analysis of the finalization of business models. In determining business models, a, is the understanding of its development strategy, or its market share and market growth rate, or the staff of the situation, and so on, according to the companies to determine the actual situation. As enterprises in different period of development, its focus is different, which means that enterprises need to invest the manpower and financial resources the focus is different. So in a certain period of time, enterprises should accurately selected their business models compared with the departments and posts, so more practical significance, because the business models are not always good, but to compare some aspects did not have much practical significance, Furthermore This can more fully concentrate on the business use of limited resources. Identify business models, and then take the enterprise of the corresponding departments and staff with the business models for comparison, the two can be found in the performance gap, a comparative analysis to find reasons, in accordance with this business reality, the final identification of training needs. The cost of training is needed, if not through an effective way to determine whether companies need to train and the training of the way, but blind to training, such training is difficult to achieve the desired results. A comparison only difference between this model is simple and practical training.1.5 Can be part of some alternative technology, such as EDM, grinding high intensity and high hardness processingHigh-speed cutting a major feature of high-speed cutting machine has the hardness of HRC60 parts. With the use of coated carbide cutter mold processing, directly to the installation of a hardened tool steel processing forming, effectively avoid the installation of several parts of the fixture error and improve the parts of the geometric location accuracy. In the mold of traditional processing, heat treatment hardening of the workpiece required EDM, high-speed machining replace the traditional method of cutting the processing, manufacturing process possible to omit die in EDM, simplifying the processing technology and investment costs .High-speed milling in the precincts of CNC machine tools, or for processing centre, also in the installation of high-speed spindle on the general machine tools. The latter not only has the processingcapacity of general machine tools, but also for high-speed milling, a decrease of investment in equipment, machine tools increased flexibility. Cutting high-speed processing can improve the efficiency, quality improvement, streamline processes, investment and machine tool investment and maintenance costs rise, but comprehensive, can significantly increase economic efficiency.2 High-speed millingHigh-speed milling the main technical high-speed cutting technology is cutting the development direction of one of it with CNC technology, microelectronic technology, new materials and new technology, such as technology development to a higher level. High-speed machine tools and high-speed tool to achieve high-speed cutting is the prerequisite and basic conditions, in high-speed machining in the performance of high-speed machine tool material of choice and there are strict requirements.2.1 High-speed milling machine in order to achieve high-speed machiningGeneral use of highly flexible high-speed CNC machine tools, machining centers, and some use a dedicated high-speed milling, drilling. At the same time a high-speed machine tool spindle system and high-speed feeding system, high stiffness of the main characteristics of high-precision targeting and high-precision interpolation functions, especially high-precision arc interpolation function. High-speed machining systems of the machine a higher demand, mainly in the following areas:General use of highly flexible high-speed CNC machine tools, machining centers, and some use a dedicated high-speed milling, drilling. At the same time a high-speed machine tool spindle system and high-speed feeding system, high stiffness of the main characteristics of high-precision targeting and high-precision interpolation functions, especially high-precision arc interpolation function. High-speed machining systems of the machine a higher demand, mainly in the following areas:High-speed milling machine must have a high-speed spindle, the spindle speed is generally 10000 ~ 100000 m / min, power greater than 15 kW. But also with rapid speed or in designated spots fast-stopping performance. The main axial space not more than 0 .0 0 0 2 m m. Often using high-speed spindle-hydrostatic bearings, air pressure-bearing, mixed ceramic bearings, magnetic bearing structure of the form. Spindle cooling general use within the water or air cooled.High-speed processing machine-driven system should be able to provide 40 ~ 60 m / min of the feed rate, with good acceleration characteristics, can provide 0.4 m/s2 to 10 m/s2 acceleration and deceleration. In order to obtain good processing quality, high-speed cutting machines must have a high enough stiffness. Machine bed material used gray iron, can also add a high-damping base of concrete, to prevent cutting tool chatter affect the quality of processing. A high-speed data transfer rate, can automatically increase slowdown. Processing technology to improve the processing and cutting tool life. At present high-speed machine tool manufacturers, usually in the general machine tools on low speed, the feed of the rough and then proceed to heat treatment, the last in the high-speed machine on the half-finished and finished, in improving the accuracy and efficiency at the same time, as far as possible to reduce processing Cost.2.2 High-speed machining toolHigh-speed machining tool is the most active one of the important factors, it has a direct impact on the efficiency of processing, manufacturing costs and product processing and accuracy. Tool in high-speed processing to bear high temperature, high pressure, friction, shock and vibration, such as loading, its hardness and wear-resistance, strength and toughness, heat resistance, technology and economic performance of the basic high-speed processing performance is the key One of the factors. High-speed cutting tool technology development speed, the more applications such as diamond (PCD), cubic boron nitride (CBN), ceramic knives, carbide coating, (C) titanium nitride Carbide TIC (N) And so on. CBN has high hardness, abrasion resistance and the extremely good thermal conductivity, and iron group elements between the great inertia, in 1300 ℃ would not have happened significant role in the chemical, also has a good stability. The experiments show that with CBN cutting toolHRC35 ~ 67 hardness of hardened steel can achieve very high speed. Ceramics have good wear resistance and thermal chemical stability, its hardness, toughness below the CBN, can be used for processing hardness of HRC <5 0 parts. Carbide Tool good wear resistance, but the hardness than the low-CBN and ceramics. Coating technology used knives, cutting tools can improve hardness and cutting the rate, for cutting HRC40 ~ 50 in hardness between the workpiece. Can be used to heat-resistant alloys, titanium alloys, hightemperature alloy, cast iron, Chungang, aluminum and composite materials of high-speed cutting Cut, the most widely used. Precision machining non-ferrous metals or non-metallic materials, or the choice of polycrystalline diamond Gang-coated tool.2.3 High-speed processing technologyHigh-speed cutting technology for high-speed machining is the key. Cutting Methods misconduct, will increase wear tool to less than high-speed processing purposes. Only high-speed machine tool and not a good guide technology, high-speed machining equipment can not fully play its role. In high-speed machining, should be chosen with milling, when the milling cutter involvement with the workpiece chip thickness as the greatest, and then gradually decreased. High-speed machining suitable for shallow depth of cut, cutting depth of not more than 0.2 mm, to avoid the location of deviation tool to ensure that the geometric precision machining parts. Ensure that the workpiece on the cutting constant load, to get good processing quality. Cutting a single high-speed milling path-cutting mode, try not to interrupt the process and cutting tool path, reducing the involvement tool to cut the number to be relatively stable cutting process. Tool to reduce the rapid change to, in other words when the NC machine tools must cease immediately, or Jiangsu, and then implement the next step. As the machine tool acceleration restrictions, easy to cause a waste of time, and exigency stop or radical move would damage the surface accuracy. In the mold of high-speed finishing, in each Cut, cut to the workpiece, the feed should try to change the direction of a curve or arc adapter, avoid a straight line adapter to maintain the smooth process of cutting.3 Die in high-speed milling processing ofMilling as a highly efficient high-speed cutting of the new method,inMould Manufacturing has been widely used. Forging links in the regular production model, with EDM cavity to be 12 ~ 15 h, electrodes produced 2 h. Milling after the switch to high-speed, high-speed milling cutter on the hardness of HRC 6 0 hardened tool steel processing. The forging die processing only 3h20min, improve work efficiency four to five times the processing surface roughness of Ra0.5 ~ 0.6m, fully in line with quality requirements.High-speed cutting technology is cutting technology one of the major developments, mainly used in automobile industry and die industry, particularly in the processing complex surface, the workpiece itself or knives rigid requirements of the higher processing areas, is a range of advanced processing technology The integration, high efficiency and high quality for the people respected. It not only involves high-speed processing technology, but also including high-speed processing machine tools, numerical control system, high-speed cutting tools and CAD / CAM technology. Die-processing technology has been developed in the mold of the manufacturing sector in general, and in my application and the application of the standards have yet to be improved, because of its traditional processing with unparalleled advantages, the future will continue to be an inevitable development of processing technology Direction.4 Numerical control technology and equipping development trend and countermeasureEquip the engineering level, level of determining the whole national economy of the modernized degree and modernized degree of industry, numerical control technology is it develop new developing new high-tech industry and most advanced industry to equip (such as information technology and his industry, biotechnology and his industry, aviation, spaceflight, etc. national defense industry) last technology and getting more basic most equipment. Marx has ever said "the differences of different economic times, do not lie in what is produced, and lie in how to produce, produce with some means of labor ". Manufacturing technology and equipping the most basic means of production that are that the mankind produced the activity, and numerical control technology is nowadays advanced manufacturing technology and equips the most central technology. Nowadays the manufacturing industry all around the world adopts numerical control technology extensively, in order to improve manufacturing capacity and level, improve the adaptive capacity and competitive power to the changeable market of the trends. In addition every industrially developed country in the world also classifies the technology and numerical control equipment of numerical control as the strategic materials of the country, not merely take the great measure to develop one's own numerical control technology and industry, and implement blockading and restrictive policy to our country in view of " high-grade, precision and advanced key technology of numerical control " and equipping. In a word, develop the advanced manufacturing technology taking numerical control technology as the core and already become every world developed country and accelerate economic development in a more cost-effective manner, important way to improve the overall national strength and national position.Numerical control technology is the technology controlled to mechanical movement and working course with digital information, integrated products of electromechanics that the numerical control equipment is the new technology represented by numerical control technology forms to the manufacture industry of the tradition and infiltration of the new developing manufacturing industry, namely the so-called digitization is equipped, its technological range covers a lot of fields: (1)Mechanical manufacturing technology;(2)Information processing, processing, transmission technology; (3)Automatic control technology;(4)Servo drive technology; (5)Technology of the sensor; (6)Software engineering ,etc..Development trend of a numerical control technologyThe application of numerical control technology has not only brought the revolutionary change to manufacturing industry of the tradition, make the manufacturing industry become the industrialized symbol , and with the constant development of numerical control technology and enlargement of the application, the development of some important trades (IT , automobile , light industry , medical treatment ,etc. ) to the national economy and the people's livelihood of his plays a more and more important role, because the digitization that these trades needed to equip has already been the main trend of modern development. Numerical control technology in the world at present and equipping the development trend to see, there is the following several respect [1- ] in its main research focus.5 A high-speed, high finish machining technology and new trend equippedThe efficiency, quality are subjavanufacturing technology. High-speed, high finish machining technology can raise the efficiency greatly , improve the quality and grade of the products, shorten production cycle and improve the market competitive power. Japan carries the technological research association first to classify it as one of the 5 great modern manufacturing technologies for this, learn (CIRP) to confirm it as the centre in the 21st century and study one of the directions in international production engineering.In the field of car industry, produce one second when beat such as production of 300,000 / vehicle per year, and many variety process it is car that equip key problem that must be solved one of; In the fields of aviation and aerospace industry, spare parts of its processing are mostly the thin wall and thin muscle, rigidity is very bad, the material is aluminium or aluminium alloy, only in a situation that cut the speed and cut strength very small high, could process these muscles, walls. Adopt large-scale whole aluminium alloy method that blank " pay empty " make the wing recently, such large-scale parts as the fuselage ,etc. come to substitute a lot of parts to assemble through numerous rivet , screw and other connection way, make the intensity , rigidity and dependability of the component improved. All these, to processing and equipping the demand which has proposed high-speed, high precise and high flexibility.According to EMO2001 exhibition situation, high-speed machining center is it give speed can reach 80m/min is even high , air transport competent speed can up to 100m/min to be about to enter. A lot of automobile factories in the world at present, including Shanghai General Motors Corporation of our country, have already adopted and substituted and made the lathe up with the production line part that the high-speed machining center makes up. HyperMach lathe of U.S.A. CINCINNATI Company enters to nearly biggest 60m/min of speed, it is 100m/min to be fast, the acceleration reaches 2g, the rotational speed of the main shaft has already reached 60 000r/min. Processing a thin wall of plane parts, spend 30min only, and same part general at a high speed milling machine process and take 3h, the ordinary milling machine is being processed to need 8h; The speed and acceleration of main shaft of dual main shaft lathes of Germany DMG Company are up to 120000r/mm and 1g.In machining accuracy, the past 10 years, ordinary progression accuse of machining accuracy of lathe bring 5μm up to from 10μm already, accurate grades of machining center from 3~5μm, rise to 1~1.5μm, and ultraprecision machining accuracy is it e nter nanometer grade to begin already (0.01μm).In dependability, MTBF value of the foreign numerical control device has already reached above 6 000h,MTBF value of the servo system reaches above 30000h, demonstrate very high dependability .In order to realize high-speed, high finish machining, if the part of function related to it is electric main shaft, straight line electrical machinery get fast development, the application is expanded further .5.2 Link and process and compound to process the fast development of the lathe in 5 axesAdopt 5 axles to link the processing of the three-dimensional curved surface part, can cut with the best geometry form of the cutter , not only highly polished, but also efficiency improves by a large margin . It is generally acknowledged, the efficiency of an 5 axle gear beds can equal 2 3 axle gear beds, is it wait for to use the cubic nitrogen boron the milling cutter of ultra hard material is milled and pared at a high speed while quenching the hard steel part, 5 axles link and process 3 constant axles to link and process and give play to higher benefit. Because such reasons as complicated that 5 axles link the numerical control system , host computer structure that but go over, it is several times higher that its price links the numerical control lathe than 3 axles , in addition the technological degree of difficulty of programming is relatively great, have restricted the development of 5 axle gear beds.At present because of electric appearance of main shaft, is it realize 5 axle complex main shaft hair structure processed to link greatly simplify to make, it makes degree of difficulty and reducing by a large margin of the cost, the price disparity of the numerical control system shrinks. So promoted 5 axle gear beds of head of complex main shaft and compound to process the development of the lathe (process the lathe including 5).At EMO2001 exhibition, new Japanese 5 of worker machine process lathe adopt complex main shaft hair, can realize the processing of 4 vertical planes and processing of the wanton angle, make 5 times process and 5 axles are processed and can be realized on the same lathe, can also realize the inclined plane and pour the processing of the hole of awls. Germany DMG Company exhibits the DMUVoution series machining center, but put and insert and put processing and 5 axles 5 times to link and process in once, can be controlled by CNC system or CAD/CAM is controlled directly or indirectly.5.3 Become the main trend of systematic development of contemporary numerical control intelligently, openly, networkedly.The numerical control equipment in the 21st century will be sure the intelligent system, the intelligent content includes all respects in the numerical control system: It is intelligent in order to pursue the efficiency of processing and process quality, control such as the self-adaptation of the processing course, the craft parameter is produced automatically; Join the convenient one in order to improve the performance of urging and use intelligently, if feedforward control , adaptive operation , electrical machinery of parameter , discern load select models , since exactly makes etc. automatically; The ones that simplified programming , simplified operating aspect are intelligent, for instance intelligent automatic programming , intelligent man-machine interface ,etc.; There are content of intelligence diagnose , intelligent monitoring , diagnosis convenient to be systematic and maintaining ,etc..Produce the existing problem for the industrialization of solving the traditional numerical control system sealing and numerical control application software. A lot of countries carry on research to the open numerical control system at present, such as NGC of U.S.A. (The Next Generation Work-Station/MachineControl), OSACA of European Community (Open System Architecture for Control within Automation Systems), OSEC (Open System Environment for Controller) of Japan, ONC (Open Numerical Control System) of China, etc.. The numerical control system melts to become the future way of the numerical control system open. The so-called open numerical control system is the development of the numerical control system can be on unified operation platform, face the lathe producer and end user, through changing, increasing or cutting out the structure target(numerical control function), form the serration, and can use users specially conveniently and the technical know-how is integrated in the control system, realize the open numerical control system of different variety , different grade fast, form leading brand products with distinct distinction. System structure norm of the open numerical control system at present, communication norm , disposing norm , operation platform , numerical control systematic function storehouse and numerical control systematic function software development ,etc. are the core of present research.The networked numerical control equipment is a new light spot of the fair of the internationally famous lathe in the past two years. Meeting production line , manufacture system , demand for the information integration of manufacturing company networkedly greatly of numerical control equipment, realize new manufacture mode such as quick make , fictitious enterprise , basic Entrance that the whole world make too. Some domestic and international famous numerical control lathes and systematic manufacturing companies of numerical control have all introduced relevant new concepts and protons of a machine in the past two years, if in EMO2001 exhibition, " Cyber Production Center " that the company exhibits of mountain rugged campstool gram in Japan (Mazak) (intellectual central production control unit, abbreviated as CPC); The lathe company of Japanese big Wei (Okuma ) exhibits " IT plaza " (the information technology square , is abbreviated as IT square ); Open Manufacturing Environment that the company exhibits of German Siemens (Siemens ) (open the manufacturing environment, abbreviated as OME),etc., have reflected numerical control machine tooling to the development trend of networked direction.5.4 Pay attention to the new technical standard, normal setting-up5.4.1 Design the norm of developing about the numerical control systemAs noted previously, there are better common ability, flexibility, adaptability, expanding in the open numerical control system, such countries as U.S.A. ,European Community and Japan ,etc. implement the strategic development plan one after another , carry on the research and formulation of the systematic norm (OMAC , OSACA , OSEC ) of numerical control of the open system structure, 3 biggest economies in the world have carried on the formulation that nearly the same science planned and standardized in a short time, have indicated a new arrival of period of change of numerical control technology. Our country started the research and formulation of standardizing the frame of ONC numerical control system of China too in 2000.5.4.2 About the numerical control standardThe numerical control standard is a kind of trend of information-based development of manufacturing industry. Information exchange among 50 years after numerical control technology was born was all。
空气压缩机曲轴加工工艺及夹具设计
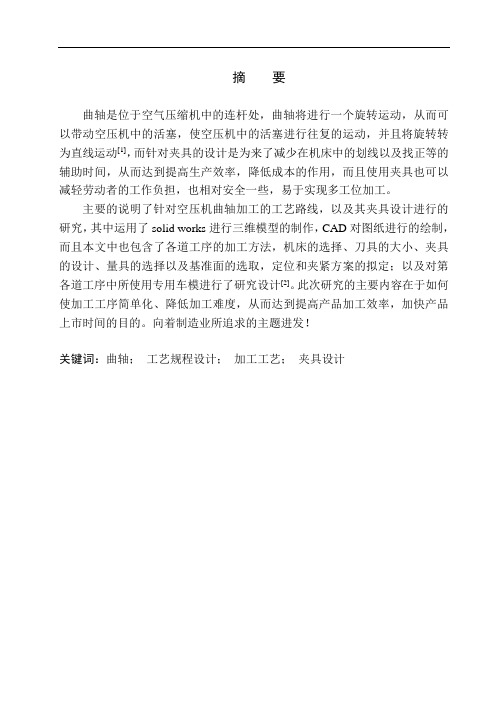
摘要曲轴是位于空气压缩机中的连杆处,曲轴将进行一个旋转运动,从而可以带动空压机中的活塞,使空压机中的活塞进行往复的运动,并且将旋转转为直线运动[1],而针对夹具的设计是为来了减少在机床中的划线以及找正等的辅助时间,从而达到提高生产效率,降低成本的作用,而且使用夹具也可以减轻劳动者的工作负担,也相对安全一些,易于实现多工位加工。
主要的说明了针对空压机曲轴加工的工艺路线,以及其夹具设计进行的研究,其中运用了solid works进行三维模型的制作,CAD对图纸进行的绘制,而且本文中也包含了各道工序的加工方法,机床的选择、刀具的大小、夹具的设计、量具的选择以及基准面的选取,定位和夹紧方案的拟定;以及对第各道工序中所使用专用车模进行了研究设计[2]。
此次研究的主要内容在于如何使加工工序简单化、降低加工难度,从而达到提高产品加工效率,加快产品上市时间的目的。
向着制造业所追求的主题进发!关键词:曲轴;工艺规程设计;加工工艺;夹具设计引言毕业设计是对我们大学四年的一个总结,运用了大学四年说学到的知识,此次毕业设计的主题是空气压缩曲轴加工工艺及夹具设计[3],运用了我们所学习的solid works,CAD,UG等软件,主要针对曲轴的加工以及夹具的设计,工艺不仅仅是制造技术的核心技术,它也是生产过程中最为活跃的因素[4]。
整个加工公的这个过程中通常都是采用金属的切削刀具,钻削或是磨具等加工方法来进行加工工件,并使工件达到图纸尺寸和金属的特有性能[5],从而生产出合格零件。
夹具的使用过程中可以有效的保证零件的加工精度,质量并且提高劳动效率,减轻劳动力。
考虑到机械零件的加工工艺的设计和零件夹具的设计过程中都可以直接的影响机油泵体的加工质量和经济的精度等等,所以在设计夹具和安排工序方面对零件的生产有着重要的意义。
毕业设计是先将进行了零件图分析,并绘制出零件图并对零件图的结构进行分析[6],最后确定生产的类型。
之后确定好毛坯的种类[7],因为在前一部分我们进行了工艺的分析,使用在这里我们采用了45号刚为材料进行加工处理,在毛坯轴两端先加工两个中心孔,再以两端中心孔定位,之后再进行粗加工以精加工,以中心孔为精基准再进行加工,之后确定加工工艺路线[8],并进行分析,根据参考文献来确定毛坯的加工余量,选择需要的刀具,量具以及夹具等等,最后再根据公式来确定切削用量。
机械加工毕业论文中英文资料外文翻译文献
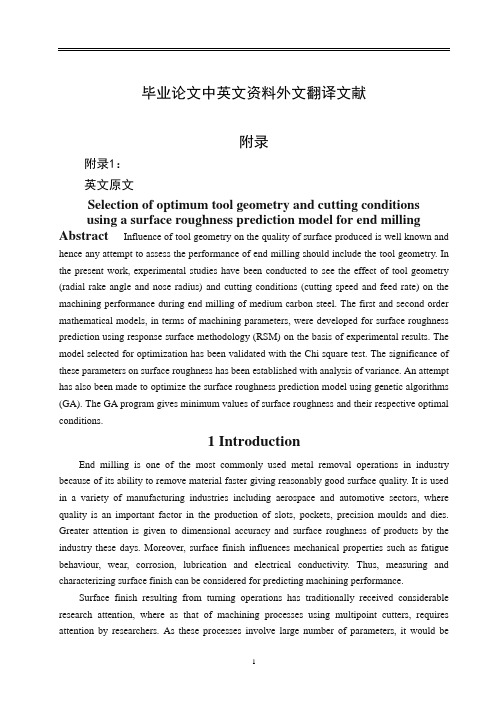
毕业论文中英文资料外文翻译文献附录附录1:英文原文Selection of optimum tool geometry and cutting conditionsusing a surface roughness prediction model for end milling Abstract Influence of tool geometry on the quality of surface produced is well known and hence any attempt to assess the performance of end milling should include the tool geometry. In the present work, experimental studies have been conducted to see the effect of tool geometry (radial rake angle and nose radius) and cutting conditions (cutting speed and feed rate) on the machining performance during end milling of medium carbon steel. The first and second order mathematical models, in terms of machining parameters, were developed for surface roughness prediction using response surface methodology (RSM) on the basis of experimental results. The model selected for optimization has been validated with the Chi square test. The significance of these parameters on surface roughness has been established with analysis of variance. An attempt has also been made to optimize the surface roughness prediction model using genetic algorithms (GA). The GA program gives minimum values of surface roughness and their respective optimal conditions.1 IntroductionEnd milling is one of the most commonly used metal removal operations in industry because of its ability to remove material faster giving reasonably good surface quality. It is used in a variety of manufacturing industries including aerospace and automotive sectors, where quality is an important factor in the production of slots, pockets, precision moulds and dies. Greater attention is given to dimensional accuracy and surface roughness of products by the industry these days. Moreover, surface finish influences mechanical properties such as fatigue behaviour, wear, corrosion, lubrication and electrical conductivity. Thus, measuring and characterizing surface finish can be considered for predicting machining performance.Surface finish resulting from turning operations has traditionally received considerable research attention, where as that of machining processes using multipoint cutters, requires attention by researchers. As these processes involve large number of parameters, it would bedifficult to correlate surface finish with other parameters just by conducting experiments. Modelling helps to understand this kind of process better. Though some amount of work has been carried out to develop surface finish prediction models in the past, the effect of tool geometry has received little attention. However, the radial rake angle has a major affect on the power consumption apart from tangential and radial forces. It also influences chip curling and modifies chip flow direction. In addition to this, researchers [1] have also observed that the nose radius plays a significant role in affecting the surface finish. Therefore the development of a good model should involve the radial rake angle and nose radius along with other relevant factors.Establishment of efficient machining parameters has been a problem that has confronted manufacturing industries for nearly a century, and is still the subject of many studies. Obtaining optimum machining parameters is of great concern in manufacturing industries, where the economy of machining operation plays a key role in the competitive market. In material removal processes, an improper selection of cutting conditions cause surfaces with high roughness and dimensional errors, and it is even possible that dynamic phenomena due to auto excited vibrations may set in [2]. In view of the significant role that the milling operation plays in today’s manufacturing world, there is a need to optimize the machining parameters for this operation. So, an effort has been made in this paper to see the influence of tool geometry(radial rake angle and nose radius) and cutting conditions(cutting speed and feed rate) on the surface finish produced during end milling of medium carbon steel. The experimental results of this work will be used to relate cutting speed, feed rate, radial rake angle and nose radius with the machining response i.e. surface roughness by modelling. The mathematical models thus developed are further utilized to find the optimum process parameters using genetic algorithms.2 ReviewProcess modelling and optimization are two important issues in manufacturing. The manufacturing processes are characterized by a multiplicity of dynamically interacting process variables. Surface finish has been an important factor of machining in predicting performance of any machining operation. In order to develop and optimize a surface roughness model, it is essential to understand the current status of work in this area.Davis et al. [3] have investigated the cutting performance of five end mills having various helix angles. Cutting tests were performed on aluminium alloy L 65 for three milling processes (face, slot and side), in which cutting force, surface roughness and concavity of a machined plane surface were measured. The central composite design was used to decide on the number of experiments to be conducted. The cutting performance of the end mills was assessed usingvariance analysis. The affects of spindle speed, depth of cut and feed rate on the cutting force and surface roughness were studied. The investigation showed that end mills with left hand helix angles are generally less cost effective than those with right hand helix angles. There is no significant difference between up milling and down milling with regard tothe cutting force, although the difference between them regarding the surface roughness was large. Bayoumi et al.[4] have studied the affect of the tool rotation angle, feed rate and cutting speed on the mechanistic process parameters (pressure, friction parameter) for end milling operation with three commercially available workpiece materials, 11 L 17 free machining steel, 62- 35-3 free machining brass and 2024 aluminium using a single fluted HSS milling cutter. It has been found that pressure and friction act on the chip – tool interface decrease with the increase of feed rate and with the decrease of the flow angle, while the cutting speed has a negligible effect on some of the material dependent parameters. Process parameters are summarized into empirical equations as functions of feed rate and tool rotation angle for each work material. However, researchers have not taken into account the effects of cutting conditions and tool geometry simultaneously; besides these studies have not considered the optimization of the cutting process.As end milling is a process which involves a large number f parameters, combined influence of the significant parameters an only be obtained by modelling. Mansour and Abdallaet al. [5] have developed a surface roughness model for the end milling of EN32M (a semi-free cutting carbon case hardening steel with improved merchantability). The mathematical model has been developed in terms of cutting speed, feed rate and axial depth of cut. The affect of these parameters on the surface roughness has been carried out using response surface methodology (RSM). A first order equation covering the speed range of 30–35 m/min and a second order equation covering the speed range of 24–38 m/min were developed under dry machining conditions. Alauddin et al. [6] developed a surface roughness model using RSM for the end milling of 190 BHN steel. First and second order models were constructed along with contour graphs for the selection of the proper combination of cutting speed and feed to increase the metal removal rate without sacrificing surface quality. Hasmi et al. [7] also used the RSM model for assessing the influence of the workpiece material on the surface roughness of the machined surfaces. The model was developed for milling operation by conducting experiments on steel specimens. The expression shows, the relationship between the surface roughness and the various parameters; namely, the cutting speed, feed and depth of cut. The above models have not considered the affect of tool geometry on surface roughness.Since the turn of the century quite a large number of attempts have been made to find optimum values of machining parameters. Uses of many methods have been reported in the literature to solve optimization problems for machining parameters. Jain and Jain [8] have usedneural networks for modeling and optimizing the machining conditions. The results have been validated by comparing the optimized machining conditions obtained using genetic algorithms. Suresh et al. [9] have developed a surface roughness prediction model for turning mild steel using a response surface methodology to produce the factor affects of the individual process parameters. They have also optimized the turning process using the surface roughness prediction model as the objective function. Considering the above, an attempt has been made in this work to develop a surface roughness model with tool geometry and cutting conditions on the basis of experimental results and then optimize it for the selection of these parameters within the given constraints in the end milling operation.3 MethodologyIn this work, mathematical models have been developed using experimental results with the help of response surface methodolog y. The purpose of developing mathematical models relating the machining responses and their factors is to facilitate the optimization of the machining process. This mathematical model has been used as an objective function and the optimization was carried out with the help of genetic algorithms.3.1 Mathematical formulationResponse surface methodology(RSM) is a combination of mathematical and statistical techniques useful for modelling and analyzing the problems in which several independent variables influence a dependent variable or response. The mathematical models commonly used are represented by:where Y is the machining response, ϕ is the response function and S, f , α, r are milling variables and ∈is the error which is normally distributed about the observed response Y with zero mean.The relationship between surface roughness and other independent variables can be represented as follows,where C is a constant and a, b, c and d are exponents.To facilitate the determination of constants and exponents, this mathematical model will have to be linearized by performing a logarithmic transformation as follows:The constants and exponents C, a, b, c and d can be determined by the method of least squares. The first order linear model, developed from the above functional relationship using least squares method, can be represented as follows:where Y1 is the estimated response based on the first-order equation, Y is the measured surface roughness on a logarithmic scale, x0 = 1 (dummy variable), x1, x2, x3 and x4 are logarithmic transformations of cutting speed, feed rate, radial rake angle and nose radiusrespectively, ∈is the experimental error and b values are the estimates of corresponding parameters.The general second order polynomial response is as given below:where Y2 is the estimated response based on the second order equation. The parameters, i.e. b0, b1, b2, b3, b4, b12, b23, b14, etc. are to be estimated by the method of least squares. Validity of the selected model used for optimizing the process parameters has been tested with the help of statistical tests, such as F-test, chi square test, etc. [10].3.2 Optimization using genetic algorithmsMost of the researchers have used traditional optimization techniques for solving machining problems. The traditional methods of optimization and search do not fare well over a broad spectrum of problem domains. Traditional techniques are not efficient when the practical search space is too large. These algorithms are not robust. They are inclined to obtain a local optimal solution. Numerous constraints and number of passes make the machining optimization problem more complicated. So, it was decided to employ genetic algorithms as an optimization technique. GA come under the class of non-traditional search and optimization techniques. GA are different from traditional optimization techniques in the following ways:1.GA work with a coding of the parameter set, not the parameter themselves.2.GA search from a population of points and not a single point.3.GA use information of fitness function, not derivatives or other auxiliary knowledge.4.GA use probabilistic transition rules not deterministic rules.5.It is very likely that the expected GA solution will be the global solution.Genetic algorithms (GA) form a class of adaptive heuristics based on principles derived from the dynamics of natural population genetics. The searching process simulates the natural evaluation of biological creatures and turns out to be an intelligent exploitation of a random search. The mechanics of a GA is simple, involving copying of binary strings. Simplicity of operation and computational efficiency are the two main attractions of the genetic algorithmic approach. The computations are carried out in three stages to get a result in one generation or iteration. The three stages are reproduction, crossover and mutation.In order to use GA to solve any problem, the variable is typically encoded into a string (binary coding) or chromosome structure which represents a possible solution to the given problem. GA begin with a population of strings (individuals) created at random. The fitness of each individual string is evaluated with respect to the given objective function. Then this initial population is operated on by three main operators – reproduction cross over and mutation– to create, hopefully, a better population. Highly fit individuals or solutions are given theopportunity to reproduce by exchanging pieces of their genetic information, in the crossover procedure, with other highly fit individuals. This produces new “offspring” solutions, which share some characteristics taken from both the parents. Mutation is often applied after crossover by altering some genes (i.e. bits) in the offspring. The offspring can either replace the whole population (generational approach) or replace less fit individuals (steady state approach). This new population is further evaluated and tested for some termination criteria. The reproduction-cross over mutation- evaluation cycle is repeated until the termination criteria are met.4 Experimental detailsFor developing models on the basis of experimental data, careful planning of experimentation is essential. The factors considered for experimentation and analysis were cutting speed, feed rate, radial rake angle and nose radius.4.1 Experimental designThe design of experimentation has a major affect on the number of experiments needed. Therefore it is essential to have a well designed set of experiments. The range of values of each factor was set at three different levels, namely low, medium and high as shown in Table 1. Based on this, a total number of 81 experiments (full factorial design), each having a combination of different levels of factors, as shown in Table 2, were carried out.The variables were coded by taking into account the capacity and limiting cutting conditions of the milling machine. The coded values of variables, to be used in Eqs. 3 and 4, were obtained from the following transforming equations:where x1 is the coded value of cutting speed (S), x2 is the coded value of the feed rate ( f ), x3 is the coded value of radial rake angle(α) and x4 is the coded value of nose radius (r).4.2 ExperimentationA high precision ‘Rambaudi Rammatic 500’ CNC milling machine, with a vertical milling head, was used for experimentation. The control system is a CNC FIDIA-12 compact. The cutting tools, used for the experimentation, were solid coated carbide end mill cutters of different radial rake angles and nose radii (WIDIA: DIA20 X FL38 X OAL 102 MM). The tools are coated with TiAlN coating. The hardness, density and transverse rupture strength are 1570 HV 30, 14.5 gm/cm3 and 3800 N/mm2 respectively.AISI 1045 steel specimens of 100×75 mm and 20 mm thickness were used in the present study. All the specimens were annealed, by holding them at 850 ◦C for one hour and then cooling them in a furnace. The chemical analysis of specimens is presented in Table 3. Thehardness of the workpiece material is 170 BHN. All the experiments were carried out at a constant axial depth of cut of 20 mm and a radial depth of cut of 1 mm. The surface roughness (response) was measured with Talysurf-6 at a 0.8 mm cut-off value. An average of four measurements was used as a response value.5 Results and discussionThe influences of cutting speed, feed rate, radial rake angle and nose radius have been assessed by conducting experiments. The variation of machining response with respect to the variables was shown graphically in Fig. 1. It is seen from these figures that of the four dependent parameters, radial rake angle has definite influence on the roughness of the surface machined using an end mill cutter. It is felt that the prominent influence of radial rake angle on the surface generation could be due to the fact that any change in the radial rake angle changes the sharpness of the cutting edge on the periphery, i.e changes the contact length between the chip and workpiece surface. Also it is evident from the plots that as the radial rake angle changes from 4◦to 16◦, the surface roughness decreases and then increases. Therefore, it may be concluded here that the radial rake angle in the range of 4◦to 10◦would give a better surface finish. Figure 1 also shows that the surface roughness decreases first and then increases with the increase in the nose radius. This shows that there is a scope for finding the optimum value of the radial rake angle and nose radius for obtaining the best possible quality of the surface. It was also found that the surface roughness decreases with an increase in cutting speed and increases as feed rate increases. It could also be observed that the surface roughness was a minimum at the 250 m/min speed, 200 mm/min feed rate, 10◦radial rake angle and 0.8 mm nose radius. In order to understand the process better, the experimental results can be used to develop mathematical models using RSM. In this work, a commercially available mathematical software package (MATLAB) was used for the computation of the regression of constants and exponents.5.1 The roughness modelUsing experimental results, empirical equations have been obtained to estimate surface roughness with the significant parameters considered for the experimentation i.e. cutting speed, feed rate, radial rake angle and nose radius. The first order model obtained from the above functional relationship using the RSM method is as follows:The transformed equation of surface roughness prediction is as follows:Equation 10 is derived from Eq. 9 by substituting the coded values of x1, x2, x3 and x4 in termsof ln s, ln f , lnαand ln r. The analysis of the variance (ANOV A) and the F-ratio test have been performed to justify the accuracy of the fit for the mathematical model. Since the calculated values of the F-ratio are less than the standard values of the F-ratio for surface roughness as shown in Table 4, the model is adequate at 99% confidence level to represent the relationship between the machining response and the considered machining parameters of the end milling process.The multiple regression coefficient of the first order model was found to be 0.5839. This shows that the first order model can explain the variation in surface roughness to the extent of 58.39%. As the first order model has low predictability, the second order model has been developed to see whether it can represent better or not.The second order surface roughness model thus developed is as given below:where Y2 is the estimated response of the surface roughness on a logarithmic scale, x1, x2, x3 and x4 are the logarithmic transformation of speed, feed, radial rake angle and nose radius. The data of analysis of variance for the second order surface roughness model is shown in Table 5.Since F cal is greater than F0.01, there is a definite relationship between the response variable and independent variable at 99% confidence level. The multiple regression coefficient of the second order model was found to be 0.9596. On the basis of the multiple regression coefficient (R2), it can be concluded that the second order model was adequate to represent this process. Hence the second order model was considered as an objective function for optimization using genetic algorithms. This second order model was also validated using the chi square test. The calculated chi square value of the model was 0.1493 and them tabulated value at χ2 0.005 is 52.34, as shown in Table 6, which indicates that 99.5% of the variability in surface roughness was explained by this model.Using the second order model, the surface roughness of the components produced by end milling can be estimated with reasonable accuracy. This model would be optimized using genetic algorithms (GA).5.2 The optimization of end millingOptimization of machining parameters not only increases the utility for machining economics, but also the product quality toa great extent. In this context an effort has been made to estimate the optimum tool geometry and machining conditions to produce the best possible surface quality within the constraints.The constrained optimization problem is stated as follows: Minimize Ra using the model given here:where xil and xiu are the upper and lower bounds of process variables xi and x1, x2, x3, x4 are logarithmic transformation of cutting speed, feed, radial rake angle and nose radius.The GA code was developed using MATLAB. This approach makes a binary coding system to represent the variables cutting speed (S), feed rate ( f ), radial rake angle (α) and nose radius (r), i.e. each of these variables is represented by a ten bit binary equivalent, limiting the total string length to 40. It is known as a chromosome. The variables are represented as genes (substrings) in the chromosome. The randomly generated 20 such chromosomes (population size is 20), fulfilling the constraints on the variables, are taken in each generation. The first generation is called the initial population. Once the coding of the variables has been done, then the actual decoded values for the variables are estimated using the following formula: where xi is the actual decoded value of the cutting speed, feed rate, radial rake angle and nose radius, x(L) i is the lower limit and x(U) i is the upper limit and li is the substring length, which is equal to ten in this case.Using the present generation of 20 chromosomes, fitness values are calculated by the following transformation:where f(x) is the fitness function and Ra is the objective function.Out of these 20 fitness values, four are chosen using the roulette-wheel selection scheme. The chromosomes corresponding to these four fitness values are taken as parents. Then the crossover and mutation reproduction methods are applied to generate 20 new chromosomes for the next generation. This processof generating the new population from the old population is called one generation. Many such generations are run till the maximum number of generations is met or the average of four selected fitness values in each generation becomes steady. This ensures that the optimization of all the variables (cutting speed, feed rate, radial rake angle and nose radius) is carried out simultaneously. The final statistics are displayed at the end of all iterations. In order to optimize the present problem using GA, the following parameters have been selected to obtain the best possible solution with the least computational effort: Table 7 shows some of the minimum values of the surface roughness predicted by the GA program with respect to input machining ranges, and Table 8 shows the optimum machining conditions for the corresponding minimum values of the surface roughness shown in Table 7. The MRR given in Table 8 was calculated bywhere f is the table feed (mm/min), aa is the axial depth of cut (20 mm) and ar is the radial depth of cut (1 mm).It can be concluded from the optimization results of the GA program that it is possible toselect a combination of cutting speed, feed rate, radial rake angle and nose radius for achieving the best possible surface finish giving a reasonably good material removal rate. This GA program provides optimum machining conditions for the corresponding given minimum values of the surface roughness. The application of the genetic algorithmic approach to obtain optimal machining conditions will be quite useful at the computer aided process planning (CAPP) stage in the production of high quality goods with tight tolerances by a variety of machining operations, and in the adaptive control of automated machine tools. With the known boundaries of surface roughness and machining conditions, machining could be performed with a relatively high rate of success with the selected machining conditions.6 ConclusionsThe investigations of this study indicate that the parameters cutting speed, feed, radial rake angle and nose radius are the primary actors influencing the surface roughness of medium carbon steel uring end milling. The approach presented in this paper provides n impetus to develop analytical models, based on experimental results for obtaining a surface roughness model using the response surface methodology. By incorporating the cutter geometry in the model, the validity of the model has been enhanced. The optimization of this model using genetic algorithms has resulted in a fairly useful method of obtaining machining parameters in order to obtain the best possible surface quality.中文翻译选择最佳工具,几何形状和切削条件利用表面粗糙度预测模型端铣摘要:刀具几何形状对工件表面质量产生的影响是人所共知的,因此,任何成型面端铣设计应包括刀具的几何形状。
机械设计与制造毕业设计论文中英文翻译外文翻译
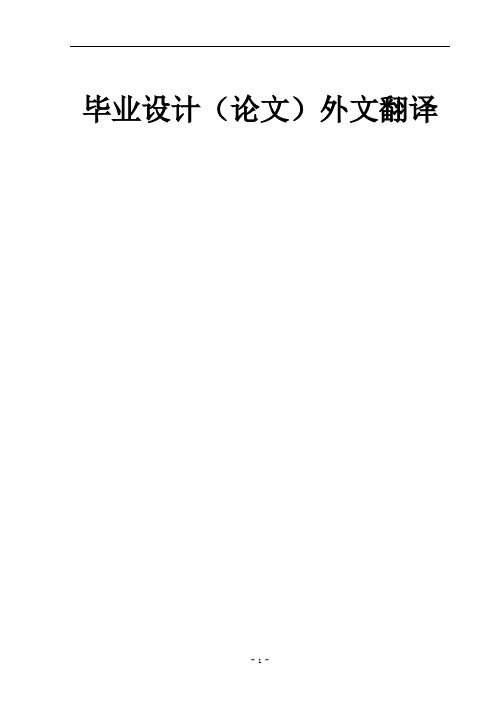
毕业设计(论文)外文翻译如何延长轴承寿命摘要:自然界苛刻的工作条件会导致轴承的失效,但是如果遵循一些简单的规则,轴承正常运转的机会是能够被提高的。
在轴承的使用过程当中,过分的忽视会导致轴承的过热现象,也可能使轴承不能够再被使用,甚至完全的破坏。
但是一个被损坏的轴承,会留下它为什么被损坏的线索。
通过一些细致的侦察工作,我们可以采取行动来避免轴承的再次失效。
关键词:轴承失效寿命轴承(“Bearing”,日本人称“轴受”)是在机械传动过程中起固定和减小载荷摩擦系数的部件。
也可以说,当其它机件在轴上彼此产生相对运动时,用来降低动力传递过程中的摩擦系数和保持轴中心位置固定的机件。
轴承是当代机械设备中一种举足轻重的零部件。
它的主要功能是支撑机械旋转体,用以降低设备在传动过程中的机械载荷摩擦系数。
按运动元件摩擦性质的不同,轴承可分为滚动轴承和滑动轴承两类。
1.轴承寿命的基本概念根据最新的轴承疲劳寿命理论,一只设计优秀、材质卓越、制造精良而且安装正确的轴承,只要其承受的负荷足够轻松(不大于该轴承相应的某个持久性极限负荷值),则这个轴承的材料将永远不会产生疲劳损坏。
因此,只要轴承的工作环境温度适宜而且变化幅度不大,绝对无固体尘埃、有害气体和水分侵入轴承,轴承的润滑充分而又恰到好处,润滑剂绝对纯正而无杂质,并且不会老化变质,则这个轴承将会无限期地运转下去。
这个理论的重大意义不仅在于它提供了一个比ISO寿命方程更为可靠的预测现代轴承寿命的工具,而且在于它展示了所有轴承的疲劳寿命都有着可观的开发潜力,并展示了开发这种潜力的途径,因而对轴承产品的开发、质量管理和应用技术有着深远的影响。
但是,轴承的无限只有在实验室的条件下才有可能“实现”,而这样的条件对于在一定工况下现场使用的轴承来说,既难办到也太昂贵。
现场使用轴承,其工作负荷往往大于其相应的疲劳持久性极限负荷,在工作到一定的期限后,或晚或早总会由于本身材料达致电疲劳极限,产生疲劳剥落而无法继续使用。
机械加工零件的工艺及夹具设计方案(中英文对照)
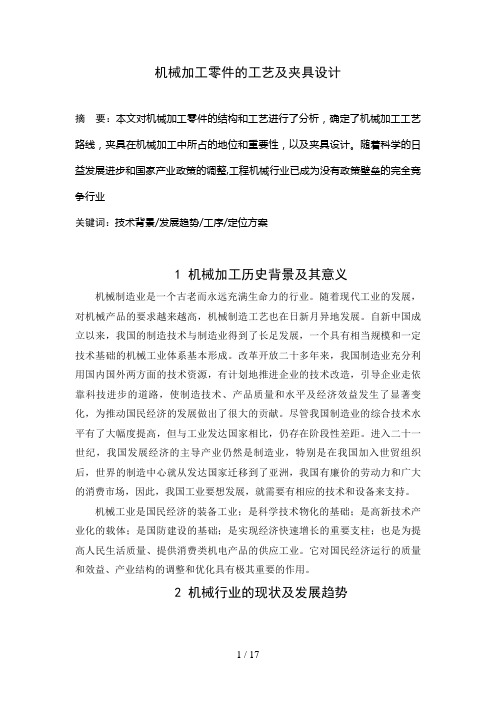
机械加工零件的工艺及夹具设计摘要:本文对机械加工零件的结构和工艺进行了分析,确定了机械加工工艺路线,夹具在机械加工中所占的地位和重要性,以及夹具设计。
随着科学的日益发展进步和国家产业政策的调整,工程机械行业已成为没有政策壁垒的完全竞争行业关键词:技术背景/发展趋势/工序/定位方案1 机械加工历史背景及其意义机械制造业是一个古老而永远充满生命力的行业。
随着现代工业的发展,对机械产品的要求越来越高,机械制造工艺也在日新月异地发展。
自新中国成立以来,我国的制造技术与制造业得到了长足发展,一个具有相当规模和一定技术基础的机械工业体系基本形成。
改革开放二十多年来,我国制造业充分利用国内国外两方面的技术资源,有计划地推进企业的技术改造,引导企业走依靠科技进步的道路,使制造技术、产品质量和水平及经济效益发生了显著变化,为推动国民经济的发展做出了很大的贡献。
尽管我国制造业的综合技术水平有了大幅度提高,但与工业发达国家相比,仍存在阶段性差距。
进入二十一世纪,我国发展经济的主导产业仍然是制造业,特别是在我国加入世贸组织后,世界的制造中心就从发达国家迁移到了亚洲,我国有廉价的劳动力和广大的消费市场,因此,我国工业要想发展,就需要有相应的技术和设备来支持。
机械工业是国民经济的装备工业;是科学技术物化的基础;是高新技术产业化的载体;是国防建设的基础;是实现经济快速增长的重要支柱;也是为提高人民生活质量、提供消费类机电产品的供应工业。
它对国民经济运行的质量和效益、产业结构的调整和优化具有极其重要的作用。
2 机械行业的现状及发展趋势随着社会的发展,各种机械逐渐运用到各个行业中,不管是在农用、军用、工用等方面,离开了机械的操作就谈不上效率,因此,从某中角度上来说,一个国家的经济实力、社会地位,和机械行业的发展是密不可分的。
各工业化国家经济发展的历程表明,没有强大的装备制造业,就不可能实现国民经济的工业化、现代化和信息化[3]。
发动机曲轴箱机加工工艺夹具设计毕业论文

发动机曲轴箱机加工工艺夹具设计毕业论
文
引言
本文描述了一种发动机曲轴箱夹具的设计方案,该夹具用于机加工过程中的定位和夹持操作,以保证加工精度和效率。
本文将介绍夹具的设计思路、结构、制造工艺以及使用效果的测试结果。
设计思路
夹具的设计根据曲轴箱的几何形状和加工要求,结合机加工操作的特点和工艺要求,采用了“定位-固定-夹紧”的基本夹持方式。
夹具由基座、定位导向部件、固定和夹紧部件组成。
夹具结构
整个夹具的设计与制造需要考虑以下几个因素:
- 曲轴箱的三维形状和尺寸
- 机加工工艺的需要
- 制造工艺和加工精度要求
为了减少加工难度和提高精度,夹具的制造部件应当采用数控
加工工艺,保证零件的精度。
夹具的结构应当具有可拆卸性,以方
便维修和更换配件。
制造工艺
夹具的制造工艺包括零件制造、零件装配和夹具整体调试。
首先,所有的夹具部件应当通过数控加工设备进行加工和组装。
然后,对所有的装配方式进行调试,并进行加工效果的检测。
使用效果测试
在夹具的制造和调试结束后,我们对夹具的使用效果进行了测试,测试结果显示,该夹具可以很好地满足机加工操作的需要,提
高了加工精度和效率,并具有较好的使用寿命。
总结
本文介绍了一种发动机曲轴箱机加工工艺夹具设计方案,该方案采用定位-固定-夹紧的基本夹持方式,夹具具有结构合理、制造精度高、使用寿命长等特点,并具有显著的使用效果。
3L-108空气压缩机曲轴零件的机械加工工艺及夹具设计
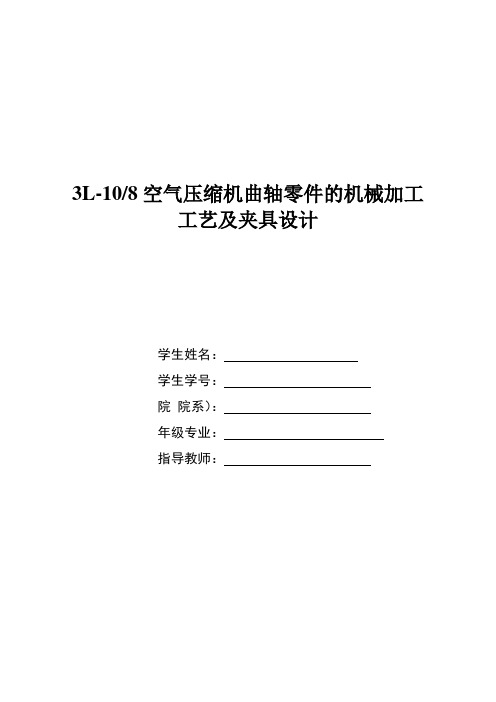
3L-10/8空气压缩机曲轴零件的机械加工工艺及夹具设计学生姓名:学生学号:院院系):年级专业:指导教师:目录目录摘要 (I)ABSTRACT (I)1 绪论 (1)2 零件分析 (2)2.1零件的作用 (2)2.2零件的工艺分析 (2)2.3零件加工的主要问题和工艺过程设计分析 (2)3 工艺规程设计 (5)3.1确定毛坯的制造形式 (5)3.2基面的选择 (5)3.2.1 粗基准选择 (5)3.2.2 精基准的选择 (5)3.3制定工艺路线 (5)3.4机械加工余量、工序尺寸及毛坯尺寸的确定 (7)3.5 确定切削用量及基本工时 (11)3.6 时间定额计算及生产安排 (31)4 专用夹具设计 (40)4.1加工曲拐上端面油孔夹具设计 (40)4.1.1定位基准的选择 (40)4.1.2切削力的计算与夹紧力分析 (40)4.1.3夹紧元件及动力装置确定 (41)4.1.4钻套、衬套及夹具体设计 (42)4.1.5夹具精度分析 (44)4.2加工曲拐上侧面油孔夹具设计 (45)4.2.1定位基准的选择 (45)4.2.2切削力的计算与夹紧力分析 (45)4.2.3夹紧元件及动力装置确定 (46)4.2.4钻套、衬套及夹具体设计 (47)4.2.5夹具精度分析 (48)4.3铣曲拐端面夹具设计 (49)4.3.1定位基准的选择 (49)4.3.2定位元件的设计 (49)4.3.3铣削力与夹紧力计算 (50)4.3.4对刀块和塞尺设计 (51)4 结论 (53)参考文献 (54)致谢······················································································错误!未定义书签。
- 1、下载文档前请自行甄别文档内容的完整性,平台不提供额外的编辑、内容补充、找答案等附加服务。
- 2、"仅部分预览"的文档,不可在线预览部分如存在完整性等问题,可反馈申请退款(可完整预览的文档不适用该条件!)。
- 3、如文档侵犯您的权益,请联系客服反馈,我们会尽快为您处理(人工客服工作时间:9:00-18:30)。
外文翻译题 目 离心泵学生姓名 冯涛专业名称 机械设计制造及其自动化指导教师 史革盟2012 年5月18日Centrifugal pumpThe concept of centrifugalCentrifugal inertia is the performance of an object, such as umbrellas on the water droplets, when the umbrella slowly rotating, the water droplets will follow the umbrella rotation, because the umbrella and the friction of water droplets to drop as the centripetal force of shiran. However, if the umbrella rotation speed, the friction enough to make water droplets in a circular motion, then drop the sport from the umbrella to the outer edge, like a rope pulling the stones to do with circular motion, if the speed is too fast, the rope will disconnect, stones will be flying out. This is the so-called centrifugal.Centrifugal pump is designed according to this theory, high-speed rotation of the impeller blades rotate driven water, throw water, so as to achieve the purpose of transportation.Good variety of centrifugal pumps, from the use can be divided into civil and industrial pumps; from the transmission medium can be divided into clear water pump, trash pump, corrosion pump and so on.Basic structure centrifugal pumpBasic structure of the centrifugal pump is composed of six parts, namely: impeller, shaft, bearings, seal rings, stuffing box.1 centrifugal impeller is a core component of its speed and high output force, the impeller blade has played a major role in the assembly before the impeller by static test. Impeller on the inside and outside surfaces required to be smooth to reduce flow friction loss.2, pump, also known as the pump casing, which is the main water pump. Play a role in supporting fixed, and with the installation of the bearing bracket connected.3, pump shaft and motor function is connected by coupling, the motor torque transmission impeller, it is the transfer of mechanical energy of the main components.4, the bearing is set on the support shaft in the shaft component, there are two kinds of rolling bearings and plain bearings. Rolling to use butter as lubricant oil to be appropriate is 2 / 3 3 / 4 size too much may have a fever, there are too few sound and heat! Pump bearing structure is transparent to the oil used for lubricants, fuel to the oil level line. Too much oil to be leaking along the shaft and drift *, too little overheated bearings and also burn the accident! Bearing in the pump during operation the maximum temperature of 85 ℃in the general run of 60 degrees, if we should find out the reasons high (whether impurities, oil is black, is water) and timely manner5, sealing ring, also known as leakage reduction ring. Impeller and pump casing of imports over the gap between high-pressure areas cause the pump's water flow through the gap area of low pressure affecting the pump out water, reducing efficiency! Gap is too small will cause the impeller and pump casing friction and wear. In order to increase the return to reduce the internal leakage resistance and delay of the impeller and pump casing life of the pump impeller shell edge and foreign aid junction with sealing ring, sealing the gap remained at 0.25 ~ 1.10mm hydrometer.6, stuffing mainly by the packing, seal ring, filler tube, packing gland, seal tubes. The main function of stuffing is to be closed between the pump casing and shaft gap, not to pump the water does not flow out to not let outside air into the pump. Always maintain the vacuum inside the pump! When the pump and fill the water seal friction depends on the heat pipe to live on the water to seal circle to fill the cooling! To maintain the normal operation of pumps. So check the pump to run during the tour of inspection of the stuffin g is the special attention! About running 600 hours on the packing should be replaced.The working principle of centrifugal pumpImpeller installed inside the pump casing 2 and fastened in the shaft 3, the shaft directly driven by the motor. Central has a liquid pump casing and suction pipe inhaling 4 5 connection. Liquid through the bottom valve 6 and the suction tube into the pump. Pump casing liquid discharge outlet on the discharge pipe 8 and 9 connections. Before starting the pump, the pump is transported shell filled with liquid; starts, starts, the impeller shaft driven by the high-speed rotation, the liquid between the blades must rotate with. Under the action of centrifugal force, the liquid was thrown from the center of the outeredge of the impeller and get energy from the impeller at high speed into the volute pump outer shell. In the spiral case, the fluid flow, gradually as the expansion slowed down in turn part of the kinetic energy into static pressure energy, the final discharge at higher pressure into the pipeline, sent to the need to place. The flow of liquid from the center of the outer edge of the impeller when the impeller center in the formation of a certain vacuum, due to the pressure tank above the liquid level is greater than the pressure at the entrance to the pump, the liquid will be pressed into the impeller in a row. Can be seen, as long as the constantly rotating impeller, the liquid will continue to be sucked and discharged.The phenomenon of gas tieWhen the pump casing to the existence of air, because air density is much smaller than the density of the liquid caused by a smaller centrifugal force. Thus, the tank liquid level above the entrance and the pressure difference between pump sufficient fluid pressure within the tank into the pump, that is not self-priming centrifugal pump, so pump can not transport liquid, such phenomenon is known as "gas tie phenomenon. " In order to pump full of liquid, usually installed in the suction pipe along the bottom of the bottom filter valve, the bottom valve until the valve, the filter is to prevent solid material into the pump impeller damage or impede the normal operation of the pump.The main components of centrifugal pump Main components are impeller, pump casing and shaft seal devices.1 impellerThe role of the impeller is the original motivation of the mechanical energy directly to the liquid, to increase the liquid static pressure energy and kinetic energy to the major increase in static pressure.Impeller are generally 6 to 12 after the curved blade.Impeller are open, semiclosed-type and closed three, as shown in Figure 2-2. Both sides of the blade open impeller without cover, create a simple, easy to clean, suitable for transmission over a large number of suspensions containing materials, inefficient delivery of the liquid pressure is not high; semi-enclosed impeller in the suction side of the non-cover board, while the other side of cover, precipitation, or easily applicable to transport materials containing particles, and lower efficiency; closed impeller, the impeller bladeson both sides of the front cover with high efficiency, suitable for delivery without impurities cleaning liquid. Multi-impeller centrifugal pumps in general for such.Impeller with a single suction and double suction two suction fluid ways.There is a single suction inlet, along with water from both sides for double suction.2 pump shellRole is to impeller enclosed in a certain space for the role by the impeller and the pressure of the fluid inhalation. Multi-spiral-shaped shell made of the pump, so called spiral. As the flow cross-sectional area gradually expanded to throw it around from the impeller speed liquid flow rate decreases, so that part of the kinetic energy is converted to static pressure can be effective. Together not only by the impeller pump casing throw the liquid, is also an energy conversion device.3 seal deviceRole is to prevent the pump shell along the axis of liquid leakage or air leakage into the pump outside the containment.Common seal device has two kinds of packing seal and mechanical seal.General packing coated with oil or graphite Baptist asbestos rope. Mainly by mechanical seal is mounted on the shaft of the ring and fixed on the pump casing static ring relative motion between the end face for the purpose to achieve the seal.Centrifugal flow passage componentsCentrifugal flow passage components are: inhalation chamber, impeller, achamber pressure of three parts. Is the core of the pump impeller chamber, is also part of the core flow. Pump liquid through the impeller on the Power, to increase the energy. Impeller according to the direction of liquid flow is divided into three categories:(1) run-of impeller (centrifugal impeller) and the liquid along the axis perpendicular to the direction of flow impeller.(2) oblique flow impeller (mixed flow impeller) of liquid along the axis tilt of the direction of flow impeller.(3) liquid axial flow impeller and the axis parallel to the direction.Impeller by way of inhalation is divided into two categories:(1) single-suction impeller (the impeller from the suction side of the liquid).(2) double suction impeller (the impeller from both sides of inhalation liquid).Divided into three categories according to the form of impeller cover:(1) closed impeller.(2) open impeller.(3) semi-open impeller.Closed impeller which is widely used, the aforementioned single-suction impeller double suction impeller belong to this form.Type of centrifugal pumpFrist. and, according to the number of categories impeller1, single-stage pump: that is, only one pump impeller.2, multi-stage pump.: In shaft with two or more of the impeller, when the total pump head for the n-of impeller and the resulting head.Second, according to classification of work stress1, low-pressure pump: pressure less than 100 m water column;2, medium pressure pumps: pressure is between 100 to 650 m water column;3, high-pressure pump: the water column pressure is higher than 650 meters.Third, by way of classification of the impeller inlet1, side water pump: also known as single-suction pump, which the impeller is only one intake;2, bilateral water pump: also known as double suction pump, which the impeller has an inlet on both sides. Its single suction pump flow ratio doubled in size, can be approximately regarded as two single-suction impeller placed together back to back.Fourth, according to the form of pump casing combined with joint classification1, horizontal split pumps: the line in the horizontal plane through the center of a combination of open seam.2, the vertically integrated surface pumps: the combination of surface and perpendicular to the axis line.Fifth, according to shaft position to Category1, horizontal pump: pump in the horizontal position.2, vertical pump: pump in the vertical position.Sixth, according to the impeller out of the water pressure out of room to lead the way classification1, volute pumps: water from the impeller out, directly into a spiral shape of the pump shell.2, guide vane pump: water came out from the impeller into the diffuser set it outside, and then proceed to the next level or into the outlet tube.Usually we say that a multi-stage pumps are pumps, impeller means in terms of how much. According to other structural features, which there may be horizontal pumps, vertical integration surface pumps, guide vane pumps, high pressure pump, water pump and so on one side. So according to different, it is called not the same. Also, according to use can also be classified as oil pump, water pump, condensate pump, ash pump, circulating water pumps, etc.Classification of the characteristics of centrifugal typeBy inhalation of a single suction pump means flow of liquid from the side of the impeller, there is the axial forceDouble suction pump liquid into the impeller from both sides, there is no axial force, the flow rate is almost double than single-suction pumps Series single-stage pump according to only one impeller shaftMulti-stage pump with a pump to upload two or more impellers, the liquid flow through each impeller in turn, more series, the higher lift Horizontal shaft by horizontal shaft orientationVertical shaft perpendicular to the horizontal planBy housing type pump housing by sub-vertical plane with the shaft portion between the segments and segment connections with long bolts Open-pump in the shell line in the plane through the center of SplitSpiral volute pump with pressurized water pump room, such as the common end-suction cantilever centrifugal pumpTurbine guide vane pump with pressurized water chamber of the pumpSpecial StructurePipeline pumps as part of pipeline, pipeline installation, no need to changeSubmersible pumps and motors made of one immersed in waterImmersed in liquid pump liquid pumpsShielding pump impeller and the motor rotor together as one and the same within a sealed shell without fully sealed, leak-free pumps areIn addition to magnetic pump inlet and outlet, the pump fully closed, the pump and motor coupling magnets can attract each other and driven by Special StructurePipeline pumps as part of pipeline, pipeline installation, no need to changeSubmersible pumps and motors made of one immersed in waterImmersed in liquid pump liquid pumpsShielding pump impeller and the motor rotor together as one and the same within a sealed shell without fully sealed, leak-free pumps areIn addition to magnetic pump inlet and outlet, the pump fully closed, the pump and motor coupling magnets can attract each other and driven by Self-priming pumps do not start filling liquidHigh-speed pump from the tank to pump speed to increase the growth rate, the general speed up 10000r/min above can also be called part of the tangential flow pump or booster pumpVertical Barrel Pump imports and exports over the same height in the upper part, there inside and outside the two-shell, internal shell from the rotor, stator, etc. component, shell body for the import diversion channel, the liquid from the lower part of inhalationMany different types of centrifugal pump, a common classification of the following ways1, by way of sub-suction impeller: single suction centrifugal double suction centrifugal pump;2, the number of points by the impeller: a single-stage centrifugalmulti-stage centrifugal pump;3 points by impeller structure: semi-open impeller centrifugal pumps with open impeller centrifugal pump closed impeller centrifugal pump;4 points by working pressure: low pressure centrifugal pump inhigh-pressure centrifugal pump;5 points by shaft position: horizontal centrifugal side of vertical centrifugal pumps.SG life to pumps, pump life, residential water pumps, life, water supply and drainage equipment, according to IS, IR-based performance parameters and vertical centrifugal pump's unique combination of design structure, and in strict accordance with ISO2858 requirements set wine production, with domestic water quality designed with the model, is the ideal next-generation horizontal pump. The product shall be used carbide mechanical seal. Applications:ISW-type pumps suitable for industrial and urban water supply and drainage, such as the pressurized water supply in high-rise buildings, garden irrigation, firebooster, long-distance transportation, HVAC refrigeration cycle, bathroom, and Equipment for Pressure, temperature does not exceed 85 ℃. ISWR pump widely used in: metallurgy, chemical, textile, paper, shops, restaurants and guest pressurized boiler heat the water, transport, and urban heating systems, SGWR type using the temperature does not exceed 120 ℃.Pipeline pump installation key technologies: the suction pump used to install a high degree ofFirst, the key to install the technology of centrifugal pumpInstallation of pipeline centrifugal pump installation key is to determine the height of the suction. The high water means the water pump impeller to the center line of the vertical distance, it allows a high degree of suction on the vacuum can not be mixed up, pump product specifications or nameplate allows a high degree of vacuum suction on the pump inlet section refers to the vacuum value, it is a standard atmospheric pressure, water temperature under 20 ℃, tested and determined to come by. It does not take into account the water flow after suction pipe supporting position. The pump mounting height should be allowed to smoke on a high vacuum suction pipe loss deduction after the head, the rest of that part of the value, it is highly absorbent to overcome the actual terrain. Pump installation height can not exceed the calculated value, otherwise, would be no water to pump. In addition, the effect size calculated is the resistance to water absorption pipe head loss, therefore, should use the shortest possible piping arrangements, and elbows and other fittings installed as little as possible, also be appropriately equipped with larger diameter water mains to reduce the internal velocity.It should be noted that the pipeline centrifugal pump installation site elevation and the water temperature is different from the experimental conditions, such as local elevation of 300 meters or pumping the water temperature exceeds 20 ℃, the calculated values to be amended. That is, different elevation Department of atmospheric pressure and temperature higher than 20 ℃when the saturated steam pressure. However, the water temperature is 20 ℃below the saturated vapor pressure is negligible.From the pipe installation technology, water absorbing pipes require strict sealing, can not leak, leakage, otherwise it will damage the intake pump vacuum to pump out the water less serious or even no water to. Therefore, to carefully work out the pipe interface, ensuring the construction quality of the connection pipe.Second, pump installation height calculation HgAllows a high degree of vacuum suction on the pump Hs is the pressure p1 at the entrance to the maximum allowable vacuum.The actual height to allow the vacuum suction on the Hs values are not calculated according to the value, but by the pump manufacturer experimental determination of the value that is attached to the pump samples for user reference. Bit should be noted that pump the sample values are given in Hs with water as the working medium, and the operating conditions of 20 ℃and pressure of 1.013 ×105Pa when the value, when the operating conditions and the working medium is not the same time, the need for conversion.1 transport water, but the operating conditions and experimental conditions, Ke Yi-type conversion underHs1 = Hs + Ha-10.33 - Hυ-0.242 transport other liquid when the liquid is transferred and the villain and the experimental conditions, conditions are not the same time, the need fortwo-step conversion: the first step according to the type will be detected sample pump Hs1; second step according to the following formula will be converted into H Hs1 s2 cavitation margin ΔhFor the pump, when the installation height calculation used to calculate the cavitation margin Δh, which pumps the liquid to allow the v acuum suction, which allows the installation of the pump height in meters. Used by the oil pump cavitation margin Δh che ck sample taken, its value is also measured with 20 ℃water for. If the delivery of other fluids, should also be calibrated, detailed investigation of the books.Suction = standard atmospheric pressure (10.33 m) - NPSH - safe level (0.5 m)Standard atmospheric pressure to high vacuum pressure pipe 10.33 meters.Pump worksKey Parts of centrifugal pump with suction chamber, the impeller and the pressurized water chamber. Suction chamber is located in front of the impeller inlet, impeller play the lead role of the liquid; pressurized water main spiral chamber pressurized water chamber (spiral type), guide vanes and guide vanes are three forms of space; pump impeller is the most important element of work is the heart of flow parts, impeller blades from the cover and intermediate composition.Pump before work, first pump filled with liquid, and then start the pump, impeller rotation speed, rotating impeller blades driven liquid, liquid to the impeller rotational inertia when rely on flow to the outer edge, while the impeller from the suction chamber inhalation liquid, this process, the liquid flow around the impeller blades, in the liquid flow around the role of sport in alift on the blade, and this in turn leaves a lift equal and opposite force on the liquid, the force acting on the fluid, so that the fluid flow of energy and impeller, then the kinetic energy and pressure energy of liquid will increase.Rotating impeller centrifugal pump relies on the role of fluid mechanical energy of the original motivation delivered to the liquid. As the role of centrifugal flow of liquid from the impeller import export process, its speed can be increased and pressure to have been discharged from the impeller through the pressure of the liquid rooms, most of the speed can be converted to pressure energy, and transportation along the discharge pipe out, this time, the impeller discharges the liquid inlet formed by vacuum or low pressure, suction pool of liquid in the surface pressure (atmospheric pressure) under the action of being pressed into the impeller of imports, thus, rotating with the impeller on the continuous to suction and discharge liquid.离心泵离心的概念离心其实是物体惯性的表现,比如雨伞上的水滴,当雨伞缓慢转动时,水滴会跟随雨伞转动,这是因为雨伞与水滴的摩擦力做为给水滴的向心力使然。