出货计划表单
与表格大全

第一章研发管理制度与表格YFGL-01-01设计和开发控制程序设计和开发控制程序1目的对新产品设计和开发的全过程进行控制,确保新产品能满足顾客的需求和期望及有关法律、法规要求。
2于适用范围适用于对本厂新产品设计和开发全过程的控制,包括定型产品的技术改进等。
职责:技术部:负责设计和开发全过程的组织、协调、实施工作,进行设计和开发的策划、确定设计和开发的输入、输出、评审、验证、确认更改和负责新产品的检验和试验。
研发部经理:负责拟制及下达项目建议书、设计和开发任务书,设计开发方案、设计开发计划书、设计和开发评审、设计和开发验证报告和试产报告。
营销部:负责根据市场调查或分析,提供市场信息及新产品动向,负责所需物料的采购。
生产车间:负责新产品的试制和生产。
4.工作程序设计和开发策划4.1.1 设计和开发项目的来源(1)营销部与顾客签订的新产品合同或技术协议,根据主管副总批准的相应《合同评审表》,研发部经理提出《项目建议书》报主管副总审核,副总批准后,由研发部经理向产品开发责任人下达《设计开发任务书》,并实施。
(2)研发部根据市场调研或分析提出有关新产品《项目建议书》,经主管副总审核后,报总经理批准由开发经理向产品开发责任人下达《设计开发任务书》。
(3)研发部根据技术革新需要,提交《项目建议书》,经主管副总审核后,报总经理批准。
由研发部经理向产品开发责任人下达《设计开发任务书》,产品开发负责人实施技术革新项目。
4.1.2 研发部经理根据上述项目来源,确定项目负责人,将设计和开发策划的输出转化为《设计开发方案》和《设计开发计划书》。
计划书内容包括:(1)设计开发的输入、输出、评审、验证、确认等各阶段的划分和主要工作内容。
(2)各阶段人员职责和权限、进度要求和配合单位。
(3)资源配置需求,如:人员、信息、设施、资金保证等及其它相关内容。
4.1.3设计和开发策划的输出文件将随着设计和开发的进展,在适当时予以修订,应按《文件控制程序》的规定进行。
出货检验控制程序(含表格)

出货检验控制程序(ISO9001-2015)1.0目的:确保交付给客户的产品符合客户品质要求。
2.0范围:凡本公司所销售之产品均属之。
3.0定义:无。
4.0权责:4.1品保部:产品出货前的检验工作。
4.2制造/仓储:出货产品的包装和搬运,交货工作。
4.3生管:制订出货计划和出货交付运输安排。
5.0作业内容:5.1生管课依据客户订单交期或排程做出生产出货计划表以E-MAIL或PAPER 档的形式通知到品保、仓储、制造等各相关单位。
5.2制程产品在入库前需经过OQC检验,仓储根据出货需求,把待出货之产品移置到“OQC待检区”。
5.3OQC依据《SIP》、承认样本及限度样品的要求对出货前的产品进行抽样检验,并把检验结果记录在《制程巡检/抽检品质记录表》及《出货检验报告单》中。
5.4抽检时OQC按每个栈板为一个批次或小件以不超过1000PCS为一个批次,按照《ISO2859抽样计划》正常单次抽样,AQL:MA为0.4,Mi为0.65。
出现客诉问题需重点检查,无客诉问题产品则以出货前的查核为主。
如有客户要求,则按客户要求标准进行。
5.5OQC检验判定合格:5.5.1OQC依据《检试验管理程序》的要求在《产品标识单》上盖“OQCPASS”章。
5.5.2制造依据《产品标示单》OQC的标识进行入库。
5.6OQC检验判定不合格:5.6.1OQC把不合格现象或不合格样品呈报上级主管后,确认为异常,则发出《品质异常联络单》给相关责任单位处理与改善,并要求相关责任单位在《品质异常联络单》背面会签。
具体依照《品质异常处理流程》执行。
不合格批,每一栈板朝外的最上层的左上角贴《不良品标示单》,注明相关不良现象等内容。
具体依照《检试验管理程序》执行。
5.6.2经OQC判定的不合格品依据《不合格管理程序》进行处理;相关单位评审是否采取纠正措施或预防措施,如需采取纠正措施或预防措施则依据《纠正与预防措施管理程序》执行。
如果不采取纠正措施,因出货紧急,在不影响功能的情况下,由生管或业务提出特采申请,具体依照《特采作业流程》执行。
TMQP-002《生产管控流程》

5.11.品质部:负责公司生产全过程的品质监控。
5.11.1.负责车间产品的首样确认,未经过品质首样确认安排生产的,车间主管每批次罚50元,如造成报废损失的,另按《车间质量管理规定》处理,追究车间管责任。
1.目的
为规范生产运作程序,使产销得到合理的协调及安排,提高工作效率、降低库存和生产成本,以满足客户订单要求,特制定本程序。
2.范围
本公司生产运作体系。
3.定义
3.1.《客户订单》由销售部发出,至PMC部作生产安排依据。
3.2.《生产月计划》《周生产计划》由PMC部发出,至生产部作制造、领、退、补料依据,至仓库作发料依据。
5.7.3.五金车间/注塑车间,接《周生产计划》后,由车间主管按周计划顺序制定日生产计划,至少提前一天准备好图纸,模具、设备,人员,保障生产过程的顺畅,本周计划内的不同订单相同物件可同批次生产,严禁擅自安排未在本周计划内的生产任务,如车间主管提议更改生产计划的,必须经PMC确认后方可执行,否则追究车间主管责任。
5.8.3.各生产车间须在当日停产前,必须将已经品管部检验合格的产品全部入库。产品入仓依照《成品进仓作业流程》作业。
5.8.4.仓库日常管理参照《仓库管理制度》实行
5.9.生产异常处理
5.9.1.在生产过程中若出现超两小时仍无法解决的生产、品质异常或机器设备故障等情况时,生产车间以《生产异常处理报告》的方式通知PMC部。由PMC部在半小时内组织相关部门,召开“生产异常协调会”议定解决办法,若影响订单交期时,则须同销售部作交期协调。
PMC职能介绍

瑞洲科技制造中心
目录
一、PMC组织结构图; 二、PMC功能; 三、PMC岗位职责; 四、PMC考核指标; 五、PMC工作流程; 六、PMC表单、记录。
一、PMC组织结构图
二、PMC功能-PC
• PC: 1. 全局生产任务的筹划。 2. 弹性的计划,合理的调度。 3. 及时沟通,掌控第一时间信息。 4. 协调各部门合作,保证按时出货。
品所需的库存供给; 3、及时准确录入采购物品的入货信息、退货信息及库存信息,报送财务部和生
产部; 4、及时准确录入产品入库、出库及库存台账,送生产部和财务部; 5、组织对仓库人员培训,保证材料库及成品库的仓储环境,确保库存产品或材
料的材质不变,确保仓库数据正确无误; 6、制定并实施材料库及成品库的管理制度和管理方法; 7、审核、制定公司成品日出货报表递交财务进行对账; 8、负责仓库5S工作开展及执行情况分析; 9、负责原料库存的控制,物控成本的控制及管理,呆废料的控制处理。 10、完成上级交办的其他工作。
PMC表单、记录-仓库
仓库: 1. 进仓单; 2. 领料单; 3. 退货单;
谢谢大家!
统; 3. 负责原料库存的控制,物控成本的控制及
管理,呆废料的控制处理。
三、PMC岗位职责-PC
• PC岗位职责: 1. 负责接收业务部传递的客户订单及相关资料,接收部门联络单;
2. 负责对所接订单进行审核,如有需要组织相关部门进行相关评审。发现有误 ,及时与业务部进行沟通解决。
3. 核查成品仓库存,车间在制品数量,订单数量减去成品、在制品库存数量, 即为需安排生产数量。
讯; 10. 监控采购部的工作,使物料按期按时按量回来; 11. 监控物料在生产现场的使用情况; 12. 配合横向各部门做好相关配套工作; 13. 参于重大物料浪费事故处理;参与采购供应链的评估、及采购成本控制。 14. 根据生产用料情况发现异常必须及时上报经理。
生产型工厂各部门操作规范和表格模板单
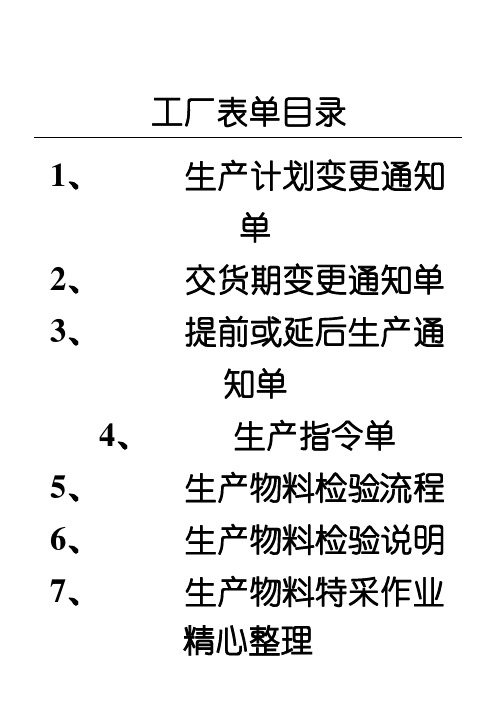
工厂表单目录
6、生产物料检验说明
7、生产物料特采作业
精心整理
流程
8、生产物料特采作业
15、特别领料单
精心整理
16、领料单(一)
17、领用单(二)
25、成品入库流程说明
精心整理
26、物料出库管理流程
27、原材料出库流程说明
35、仓库材料日报表
精心整理
36、库存控制表
37、计件工资控制表
精心整理
精心整理
交货期变更通知单
通知单位:年月日
生产指令单
精心整理
精心整理
精心整理
精心整理
生产物料特采作业流程
精心整理
生产物料领用流程说明
精心整理
精心整理
精心整理
精心整理
精心整理
.进料检验记录表
精心整理
特别领料单
编号:日期:
精心整理
领用部门:日期:
精心整理
精心整理
仓管员:品管员:补料员:
精心整理
精心整理
精心整理
精心整理
精心整理
2.物料出库管理流程
原材料出库流程说明
精心整理
精心整理
精心整理
物资仓储管理流程
物资仓储管理流程说明
精心整理
精心整理
精心整理
7.物料入库日报表
编号:入库日期:年月日
审核:
精心整理
精心整理
精心整理
精心整理
精心整理
精心整理
精心整理。
电子厂bom清单模板
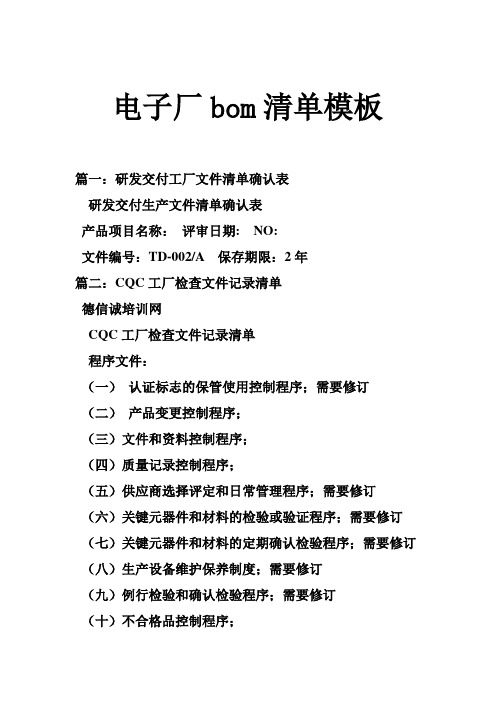
电子厂bom清单模板篇一:研发交付工厂文件清单确认表研发交付生产文件清单确认表产品项目名称:评审日期: NO:文件编号:TD-002/A 保存期限:2年篇二:CQC工厂检查文件记录清单德信诚培训网CQC工厂检查文件记录清单程序文件:(一)认证标志的保管使用控制程序;需要修订(二)产品变更控制程序;(三)文件和资料控制程序;(四)质量记录控制程序;(五)供应商选择评定和日常管理程序;需要修订(六)关键元器件和材料的检验或验证程序;需要修订(七)关键元器件和材料的定期确认检验程序;需要修订(八)生产设备维护保养制度;需要修订(九)例行检验和确认检验程序;需要修订(十)不合格品控制程序;(十一)内部质量审核程序;(十二)与质量活动有关的各类人员的职责和相互关系;三阶文件:1)BOM表、工艺作业指导书(列出主要生产过程,并识别出关键工序, 如焊接、装配等)、2)检验标准:原材料检验标准、成品检验标准3)仪器设备操作规程;保养计划、点检记录4)管理制度等:车间制度、及公司规章制度记录:(一)对供应商进行选择、评定和日常管理的记录;1)供应商选择与评定程序文件或者规范,以及评定审核计划;2)完整的合格供应商目录清单,需要经过审批;3)口头上对于采购工作的询问(二)关键元器件和材料的进货检验/验证记录及供货商提供的合格证明;1)供应商提供的出厂或者出货检验报告;或者供应商获得的第三方认证机构颁发的有效证书;(三)产品例行检验和确认检验记录;记录表单(四)检验和试验设备定期进行校准或检定的记录;1)设备、仪器点检表;2)外校证书或计划(五)例行检验和确认检验设备运行检查的记录;1)设备、仪器点检表;2)校验计划;设备保养规范或者计划(六)不合格品的处置记录;1)存放区域、标识、隔离、评审、处置、记录、返修、返工、报废品2)返工返修后产品是否可追溯(七)内部审核的记录;1)内审计划(包括计划、内审报告、不符合项报告、检查记录、一致性控制、纠正措施、顾客投诉)、2)内审总结报告(八)顾客投诉及采取纠正措施的记录;1)顾客投诉清单2)纠正措施(处理方式,分析记录、回复的报告等)(九)零部件定期确认检验记录;1)程序文件要包含:检验项目、技术要求、频次、放行准则等。
入库作业计划表
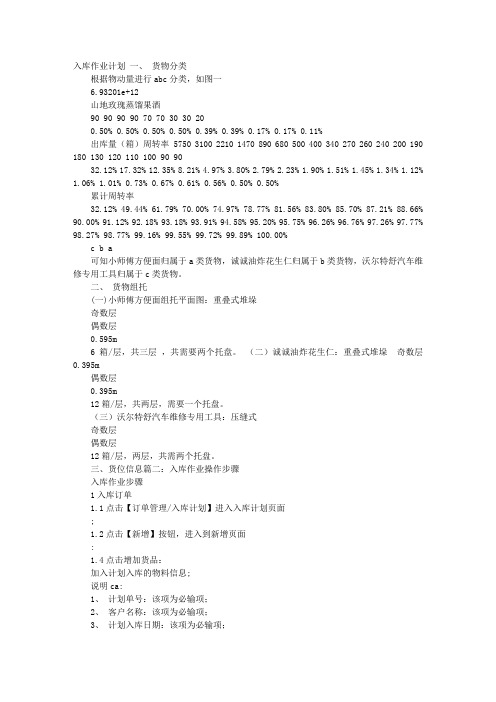
入库作业计划一、货物分类根据物动量进行abc分类,如图一6.93201e+12山地玫瑰蒸馏果酒90 90 90 90 70 70 30 30 20 0.50% 0.50% 0.50% 0.50% 0.39% 0.39% 0.17% 0.17% 0.11%出库量(箱)周转率 5750 3100 2210 1470 890 680 500 400 340 270 260 240 200 190180 130 120 110 100 90 9032.12% 17.32% 12.35% 8.21% 4.97% 3.80% 2.79% 2.23% 1.90% 1.51% 1.45% 1.34% 1.12%1.06% 1.01% 0.73% 0.67% 0.61% 0.56% 0.50% 0.50%累计周转率32.12% 49.44% 61.79% 70.00% 74.97% 78.77% 81.56% 83.80% 85.70% 87.21% 88.66%90.00% 91.12% 92.18% 93.18% 93.91% 94.58% 95.20% 95.75% 96.26% 96.76% 97.26% 97.77%98.27% 98.77% 99.16% 99.55% 99.72% 99.89% 100.00%c b a可知小师傅方便面归属于a类货物,诚诚油炸花生仁归属于b类货物,沃尔特舒汽车维修专用工具归属于c类货物。
二、货物组托(一)小师傅方便面组托平面图:重叠式堆垛奇数层偶数层0.595m 6箱/层,共三层,共需要两个托盘。
(二)诚诚油炸花生仁:重叠式堆垛奇数层0.395m偶数层0.395m12箱/层,共两层,需要一个托盘。
(三)沃尔特舒汽车维修专用工具:压缝式奇数层偶数层12箱/层,两层,共需两个托盘。
三、货位信息篇二:入库作业操作步骤入库作业步骤1入库订单1.1点击【订单管理/入库计划】进入入库计划页面;1.2点击【新增】按钮,进入到新增页面: 1.4点击增加货品:加入计划入库的物料信息;说明ca:1、计划单号:该项为必输项;2、客户名称:该项为必输项;3、计划入库日期:该项为必输项;4、备注:该项可以为空;1.5保存入库计划信息:(如上图)完成增加货品操作以后,点击【保存】按钮,保存入库计划。
出货检验作业指导书
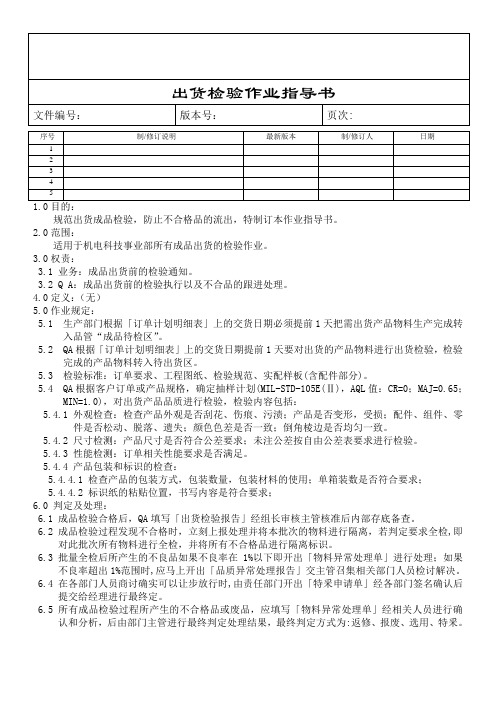
规范出货成品检验,防止不合格品的流出,特制订本作业指导书。
2.0范围:适用于机电科技事业部所有成品出货的检验作业。
3.0权责:3.1 业务:成品出货前的检验通知。
3.2 Q A:成品出货前的检验执行以及不合品的跟进处理。
4.0定义:(无)5.0作业规定:5.1 生产部门根据「订单计划明细表」上的交货日期必须提前1天把需出货产品物料生产完成转入品管“成品待检区”。
5.2 QA根据「订单计划明细表」上的交货日期提前1天要对出货的产品物料进行出货检验,检验完成的产品物料转入待出货区。
5.3 检验标准:订单要求、工程图纸、检验规范、实配样板(含配件部分)。
5.4 QA根据客户订单或产品规格,确定抽样计划(MIL-STD-105E(Ⅱ),AQL值:CR=0;MAJ=0.65;MIN=1.0),对出货产品品质进行检验,检验内容包括:5.4.1外观检查:检查产品外观是否刮花、伤痕、污渍;产品是否变形,受损;配件、组件、零件是否松动、脱落、遗失;颜色色差是否一致;倒角棱边是否均匀一致。
5.4.2 尺寸检测:产品尺寸是否符合公差要求;未注公差按自由公差表要求进行检验。
5.4.3 性能检测:订单相关性能要求是否满足。
5.4.4 产品包装和标识的检查:5.4.4.1 检查产品的包装方式,包装数量,包装材料的使用;单箱装数是否符合要求;5.4.4.2 标识纸的粘贴位置,书写内容是符合要求;6.0 判定及处理:6.1 成品检验合格后,QA填写「出货检验报告」经组长审核主管核准后内部存底备查。
6.2 成品检验过程发现不合格时,立刻上报处理并将本批次的物料进行隔离,若判定要求全检,即对此批次所有物料进行全检,并将所有不合格品进行隔离标识。
6.3 批量全检后所产生的不良品如果不良率在1%以下即开出「物料异常处理单」进行处理;如果不良率超出1%范围时,应马上开出「品质异常处理报告」交主管召集相关部门人员检讨解决。
6.4 在各部门人员商讨确实可以让步放行时,由责任部门开出「特釆申请单」经各部门签名确认后提交给经理进行最终定。
- 1、下载文档前请自行甄别文档内容的完整性,平台不提供额外的编辑、内容补充、找答案等附加服务。
- 2、"仅部分预览"的文档,不可在线预览部分如存在完整性等问题,可反馈申请退款(可完整预览的文档不适用该条件!)。
- 3、如文档侵犯您的权益,请联系客服反馈,我们会尽快为您处理(人工客服工作时间:9:00-18:30)。
日期
入库 数量
日期
入库 数量
与业务计 与生管计 划差异数 划差异数
注
业务跟 单: 业务课 长: 生管: 仓储组 长: 副厂 长: 业务部 经理: 制造部
生产(出货)计划表
模具编号
下单 日期
原定 交期材质业务货计划订单及入库情况计划出货
订单 数量
入库 已出货 待出货 待入库 数量 数量 数量
日期
出货 数量
承诺入库
日期
入库 确认完 数量 成日期
生管承诺与回复
不能完成的原因分析
原因分析
计
划 实际生产落实情况
实际入库
差异分析
备
日期
入库 数量
日期
入库 数量