含铌钢铸坯的冶炼与连铸
20MnSiNb_级螺纹钢开发
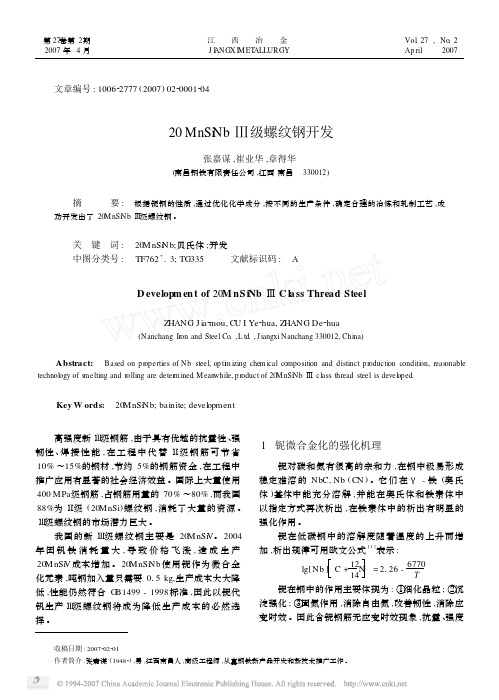
·3·
表明钢中出现脆化组织 。两炉 Φ20 mm 钢筋强度较 高而延伸勉强合格 ,也与钢中出现脆化组织有关 。 3. 3 组织及晶粒度分析
组织及晶粒度分析见表 4。 ( 1 )小型厂与棒材厂穿水生产的钢材都不同程
度存在粒状贝氏体 。当粒状贝氏体含量不多时 ,可 大幅提高强度 ,而塑性降低不明显 ;当粒状贝氏体含 量多时 ,强度虽大幅度提高 ,但脆性也大幅增加 ,屈 服表现 为连 续屈 服 (屈 服不明 显 ) 。组 织 情 况 如 图 1、图 2。
(1)转炉炼钢时采用高拉碳工艺 ,以避免终点 碳过低引起钢中氧含量高 、氧化物夹杂多的问题 ;
(2)为保证连铸坯质量 ,炼钢时尽量降低钢中 硫和氧含量 ,加强吹氩 ,减少气体与夹杂物 ;
(3)连铸过程中 ,二冷采用弱冷却制度 ,钢坯矫 直温度要求大于等于 950℃;
(4)连铸时中间包钢水尽量保持较小的过热 度。 2. 3 热轧工艺
偏低 ,甚至个别炉号延伸率不合格 。冷弯断裂的试
样断口平整 ,断口无明显的颈缩 ,呈现脆性断裂现 象。
(2) B5 - 02471为 Φ12 mm 钢筋 ,穿水冷却速度 快 ,强度比未穿水样提高 45 M Pa,而塑性严重下降 ,
第 27卷第 2期 张嘉谋 ,等 : 20M nSiNb Ⅲ级螺纹钢开发
应的穿水冷却强度 ,使钢筋得到良好边部及内部组 织 ,避免出现贝氏体和马氏体相变 。小型厂则严格 控制终轧温度 ,避免出现终轧后晶粒长大 ,充分发挥 细化晶粒强化带来的塑性提高 。
按调整后的冶炼和轧制工艺进行工业化生产 , 钢筋质量稳定 。到 2005年年底冶炼 20M nSiNb 3584 炉 ,轧制 Φ12 mm ~Φ28 mm 钢筋产量 250 8711199 t,内控达标率达 88% ,合格率为 99188%。 4. 2 力学性能
连铸过程中铸坯应变对碳氮化铌析出行为的影响

s ads a ntepeii t nbhvo fN ( N) w e tdigteN ( N) peiit n bhv ri e t n t i o rc ti e ai o b C, r rn h pao r hn s yn h b C, u rc t i eai nt pao o h
1 00 / 1 21 /1 3 0 m 5. 0 2. 7 0. 3
分应 变 及其应 变速 率对 铸坯 中碳 氮化 铌 的析 出可 能会 产生 一定 的影 响 。本文 通过 应变诱 导 析 出模
prce so o tnu u a tn . o s fc ni o s c i g s
Ke ywo ds S ri —i du e e i ia in, ta d, r ihtn n Sta n r t r tan n c d prc p tto S r n Stag e g, r ae i i
A sr c I w saaye y s a b t t t a n lzd b t i a r n—i u e r ii t n m d l h t b C N)pe ii t n W f ce y n c d pe pt o o e ta N ( , d c a i r p i a e etd b c t o s a
( 1中钢科技 发展 有限公司 ; 2钢铁研究总 院) 摘 要 采用应变诱 导析 出模 型分析 了连铸过程 中铸坯应 变对碳氮化铌 析 出行 为的影 响。结果 表明 : 拉
速变化对碳氮化铌 的最快析 出时间有 一定的影响 , 在同样 的应变及应变温度下 , 拉速越快碳氮化铌 最快 析出时 间越短 ; 在连 铸过程的矫直段及弯曲段 , 由于铸 坯应变及应 变速率较 小 , 在研 究连铸过 程碳氮 化铌析 出行为 时 铸 坯应变对碳氮化铌析 出行 为的影 响可以忽略 。
Nb-Ti-N微合金化生产HRB400E的实践

总第239期2021年4月 南 方 金 属SOUTHERNMETALSSum.239April 2021 收稿日期:2020-07-14;修订日期:2020-08-15 作者简介:严 明(1966-),男,1991年毕业于辽宁本溪冶金专科学校炼钢与铁合金专业,工程师。
文章编号:1009-9700(2021)02-0025-03Nb Ti N微合金化生产HRB400E的实践严 明(阳春新钢铁有限责任公司,广东阳春529629)摘 要:介绍了采用铌钛氮微合金化技术研制开发HRB400E钢筋的生产工艺和产品性能。
实践证明,采用铌钛氮复合合金替代钒氮合金生产HRB400E钢筋,不仅其力学性能良好,而且具有低成本优势。
关键词:铌钛氮复合合金;HRB400E钢筋;力学性能;低成本中图分类号:TG335.64 文献标志码:BPracticeofProducingSteelHRB400EbyNb Ti NMicroalloyingYANMing(YangchunNewSteelCo.,Ltd.,Yangchun,Guangdong,529629,P.R.China)Abstract:ThispaperintroducestheproductiontechnologyandproductperformanceofsteelbarHRB400EdevelopedwithTi Nmicroalloyingtechnology.IthasbeenprovedthatthebarsmadeofNbTi NalloyinsteadofV Nalloyhavenotonlygoodmechanicalpropertiesbutalsolowcostadvantages.Keywords:niobiumtitaniumnitrogencompositealloy;barHRB400E;mechanicalproperties;lowcost0 前言铌、钒、钛是重要的微合金化元素,在HRB400E螺纹钢生产过程中,绝大多数钢厂使用的是钒元素,个别钢厂使用铌元素,极少数钢厂使用钛元素。
连铸生产工艺

连铸生产工艺
连铸是指采用连续浇铸工艺将熔融金属连续浇铸成长条状的铸件,常用于生产铜、铝等金属材料。
连铸工艺相比传统离散铸造工艺具有高效、节能、高质量等优势,被广泛应用于现代金属材料的生产。
首先,连铸工艺的核心是焊接,由于金属的熔点通常很高,因此需要在高温环境下进行。
在连铸过程中,金属先经过一组预热炉,使其温度达到熔点以上,并保持恒定。
然后,熔融金属经过调漏口进入连铸机的浇注坑,通过直径大小不同的浇口,将金属流注到已经加热和涂有抗粘涂料的铸模中。
接下来,金属在连铸机中由于连铸速度以及冷却系统的作用,逐渐冷却凝固,在冷却过程中逐渐形成金属栅格状的微晶结构。
冷却速度的控制是连铸工艺中至关重要的一环,过快的冷却速度会导致过早的凝固,产生气孔和其他缺陷,而过慢的冷却速度则会影响生产效率。
因此,连铸工艺中通常通过调节冷却水的流量和温度以及调整浇注速度来控制冷却速度。
最后,凝固后的铸坯经过拉伸机进行拉拔,使其变为所需要的尺寸和形状。
拉拔是通过对铸坯施加轴向拉力来实现的,拉拔过程中金属的晶粒结构逐渐细化,从而提高了材料的强度和韧性。
拉拔机通常由一组连续的牵引辊和摩擦刹车组成,牵引辊以恒定的速度运转,将铸坯拉伸成所需尺寸。
在拉拔过程中,还可以通过在线热处理和表面处理,对材料进行进一步的改性和提高其耐腐蚀性。
总之,连铸生产工艺是一种高效、节能的金属材料生产工艺。
通过连续浇注和拉拔,可以大大提高生产效率,减少人工操作和能源消耗,同时还能提高材料质量和性能。
随着技术的不断进步,连铸工艺将继续发展,为金属材料的生产提供更好的解决方案。
连铸工艺与设备连铸的工艺流程与设备
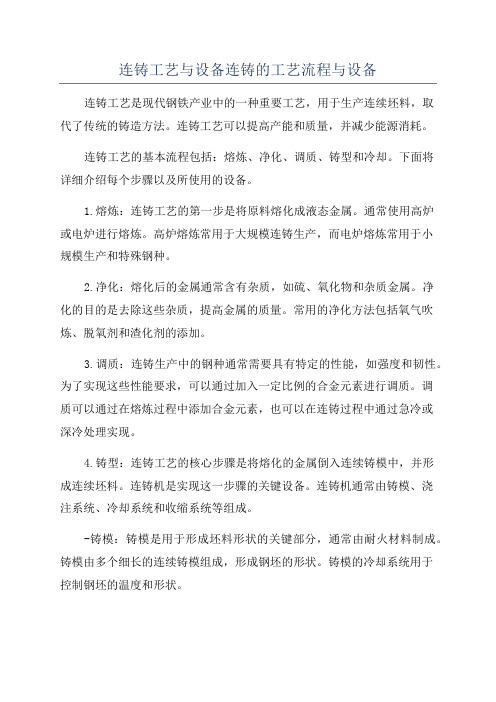
连铸工艺与设备连铸的工艺流程与设备连铸工艺是现代钢铁产业中的一种重要工艺,用于生产连续坯料,取代了传统的铸造方法。
连铸工艺可以提高产能和质量,并减少能源消耗。
连铸工艺的基本流程包括:熔炼、净化、调质、铸型和冷却。
下面将详细介绍每个步骤以及所使用的设备。
1.熔炼:连铸工艺的第一步是将原料熔化成液态金属。
通常使用高炉或电炉进行熔炼。
高炉熔炼常用于大规模连铸生产,而电炉熔炼常用于小规模生产和特殊钢种。
2.净化:熔化后的金属通常含有杂质,如硫、氧化物和杂质金属。
净化的目的是去除这些杂质,提高金属的质量。
常用的净化方法包括氧气吹炼、脱氧剂和渣化剂的添加。
3.调质:连铸生产中的钢种通常需要具有特定的性能,如强度和韧性。
为了实现这些性能要求,可以通过加入一定比例的合金元素进行调质。
调质可以通过在熔炼过程中添加合金元素,也可以在连铸过程中通过急冷或深冷处理实现。
4.铸型:连铸工艺的核心步骤是将熔化的金属倒入连续铸模中,并形成连续坯料。
连铸机是实现这一步骤的关键设备。
连铸机通常由铸模、浇注系统、冷却系统和收缩系统等组成。
-铸模:铸模是用于形成坯料形状的关键部分,通常由耐火材料制成。
铸模由多个细长的连续铸模组成,形成钢坯的形状。
铸模的冷却系统用于控制钢坯的温度和形状。
-浇注系统:浇注系统用于将熔化金属引入铸模,通常由浇注槽、分流器和导流板等组成。
浇注系统的设计和控制是影响连铸质量的重要因素。
-冷却系统:连铸过程中,冷却系统起到冷却钢坯并凝固的作用,以形成坯料。
连铸机的冷却系统通常由冷却水道和冷却喷嘴组成。
-收缩系统:收缩系统用于控制钢坯在冷却过程中的收缩,以避免出现内部缺陷。
收缩系统通常包括伸缩器、定位器和收缩量控制装置。
5.冷却:连铸过程中,钢坯会在铸模和冷却系统中逐渐凝固,并形成连续坯料。
冷却过程中,冷却水道和冷却喷嘴将水喷洒到钢坯上,以加快冷却速度和均匀性。
总结来说,连铸工艺是通过将熔融金属倒入连续铸模中,利用连铸机的浇注系统和冷却系统,控制金属的凝固和收缩过程,最终获得连续坯料。
HRB400热轧带肋钢筋研制

132
4.HRB400 热轧带肋钢筋力学性能和工艺性能
GB1499-1998 HRB400 钢筋混凝土用热轧带肋钢筋的力学性能工艺性能见表 7。
表7
牌号 HRB400
公 称 σs、σ0。2 直 径 MPa
6-25 400
28-50
σb
δ5
MPa (%)
570 14
弯曲试验 180o
无裂纹 d=4a 无裂纹 d=5a
变形速率越快,晶粒破碎作用越大,再结晶晶粒长大的倾向趋小。传搁时间
越短,晶粒长大的时间越短、晶粒越细。实际生产中,相同成分和 Ceq 的 HRB400,
分别经横列式轧机和连续式轧机生产同一规格产品,连续式轧机生产的产品力学
性能明显优于横列式的,从表 6 可以看出,9-69 和 9-70 两个号的 Nb 含量要比
性能明显优于棒材。说明现行工艺方案已能满足 HRB400 的生产要求。在提高强度的同时,
塑性指标有所下降,说明沉淀强化对塑性的损失作用超过了细化晶粒强化带来的塑性增量。
现行工艺条件下,终轧温度偏高,是限制晶粒进一步细化的主要原因。
表 9 是分别随机抽取 30-50 炉同期生产不同规格的 HRB335 和 4-5 炉相应规格的试制
514 0.23 1.47 0.025 0.026 0.56 0.036 0.48 全连续式 2-1255 0.21 1.47 0.023 0.020 0.61 0.037 0.46
1-1187 0.23 1.44 0.025 0.024 0.60 0.039 0.47
σs σb δ5 备注 430 625 22 φ25 430 625 21 φ25 440 625 25 φ25 460 635 24 φ25 425 620 27 φ12 430 635 29 φ12 485 690 29 φ10 495 705 26 φ10
特钢方坯连铸工艺路线的选择及若干问题的探讨

length by the torch cutting machine
and then send
the rolling
the bloom soaked,it went through the in—line reversing mill and rolled to different size billet and supplied to
结晶器、二冷导向喷淋设备及不同规格的引锭头和 过渡段等,使连铸机的备品管理繁杂;其次连铸机 的工艺管理复杂,由于日前的大方坯连铸机太多都 配备有凝固末端电磁搅拌或轻压下技术,甚至二种 都配备;在多规格生产肘,凝固末端(包括轻压下 的位置)对不同规格的铸坯,其位置是不相同的. 控制十分困难,容易出现质量问题;同时由于更换 生产规格时,需要对设备进行在线调整,占用铸机 的作业时间.影响连铸机的作业率。 本文在于探讨一种新的特钢连铸工艺路线: 4)特钢大方坯连铸机+在线轧制。 它的工艺特点在于;连铸机只生产最大规格的铸 坯,高温的红垤被切割成定尺后直接送入均热炉内均 热,然后,由可逆轧机将铸坯轧制成所需的各种规格
中国目前的特钢连铸生产的工艺流程主要有 以下种形式: 1)特钢小方坯连铸+小型连轧机(铸坯可以冷 装或热送)的工艺流程。 该工艺流程主要生产一些小规格的特殊钢材。 2)特钢大方坯连铸机生产多种规格铸坯+大、 中型轧机接小型连轧机的工艺流程。 该工艺流程生产特殊钢材的组距较宽,从十几 毫米的小规格钢材到七、八十毫米的中型钢材,个 别还能生产到0110mm--呻130mm的大型钢材。 除了上述二种工艺流程外,近期,采用圆坯连 铸机生产的圆坯,直接轧材的工艺流程正在以较快 的速度发展着。
2 2
2凝固末端电磁搅拌的形式 F_EMs通常采用旋转磁场的搅拌形式,搅拌器
铌在钢的控轧控冷工艺中微合金化的作用

铌在钢的控轧控冷工艺中微合金化的作用[摘要]本文主要介绍铌的强化原理、铌在钢中微合金化中应用,通过控轧控冷工艺改善铌在钢中的分布来提高铌的性能,以及当今世界铌钢的情况及生产铌钢应用的新工艺。
[关键词]控轧控冷;铌钢;强化;工艺;1.前言目前我国热轧钢筋的消费量已达5000余万吨,相对于发达国家钢筋以400N/mm2以上强度级别应用为主的局面,我国仍以335N /mm2级别的热轧钢筋为主。
近年来,随着建筑结构施工规范GB50010的修订执行HRB400热轧钢筋将逐步成为我国钢筋混凝土结构用主导钢铁材料,该级别钢筋使用比例是逐年上升的趋势。
建设部2022年4月正式新的《混凝土结构设计规范》后,建筑用钢的产品升级换代不断加快,HRB400热轧钢筋的主导钢种20MnSiV的必需原料V-Fe,VN合金价格大幅上涨,导致生产成本显著升高,急需开发新的生产工艺和替代钢种。
世界范围内的钢筋标准中,ISO标准、西欧等国钢筋标准是以轧后余热处理工艺为基础的,而在我国,轧后余热处理钢筋的生产使用受到各种限制,因此高强度级别钢筋生产基本以微合金化为主,在所有的微合金化方式中,以V微合金化最适合长型材生产工艺要求。
微合金化元素的应用较多地集中在Nb、V、Ti三大主要微合金元素,其中对Nb元素的研究应用较多地集中在扁平材上。
与V元素相比Nb析出物的溶入温度较高,因此要求相对高的工艺加热温度,同时Nb 微合金化技术的应用在于Nb的碳氮化物对再结晶的阻滞作用,以此来实现非再结晶轧制,而长型材生产本身具有的高温快轧的特点在现有生产线上较难实现非再结晶轧制。
虽然Nb的碳氮化物的析出强化作用较V的沉淀强化弱,但是利用Nh的沉淀强化和组织强化作用,也可作为HRB400热轧钢筋生产的微合金化方式。
上世纪末,国内开始超细晶碳素钢筋的研究工作。
通过在临界奥氏体区终轧诱发铁素体相变和铁素体动态再结晶,将晶粒细化至微米尺度,实现用普碳钢生产HRB400钢筋,材料成本低,具有经济效益显著和广阔的发展前景。
- 1、下载文档前请自行甄别文档内容的完整性,平台不提供额外的编辑、内容补充、找答案等附加服务。
- 2、"仅部分预览"的文档,不可在线预览部分如存在完整性等问题,可反馈申请退款(可完整预览的文档不适用该条件!)。
- 3、如文档侵犯您的权益,请联系客服反馈,我们会尽快为您处理(人工客服工作时间:9:00-18:30)。
2010年第2期世界钢铁含铌钢铸坯的冶炼与连铸Steven G Jansto(CB MM R M C公司,美国)摘要:为满足客户日益增加的需求和期望,高强度钢的产品质量也在不断地提高。
几乎所有的用户都逐步提高了对钢中残余元素的要求,同时还希望钢材的力学性能更加稳定、纯净度更高,以及表面和内部质量进一步改善。
为了高效、低成本生产高强度高品质的汽车用钢、管线钢和结构钢,钢厂必须严格规范好炼钢、钢包精炼和连铸等工艺操作,以在当今竞争激烈的全球钢铁市场中保持竞争力。
介绍了目前很多钢铁企业生产高质量含铌钢方坯、板坯及异形坯时在炼钢和连铸操作中所运用的一些要点和建议,这些做法也可以提高普通碳锰钢的产品质量。
关键词:连铸;纯净钢;热塑性;熔炼;铌Successfulm elting and casti ng of Nb-bearing carbon steelbillets,sl abs and bea m sSteven G Jansto(CB MM-R eference M etals Co m pany,USA)Abst ract:H igh strength stee l product quality con ti n ues to beco m e m ore stri n gent to m eet ever in-creasi n g custo m er de m ands and expectations.V irt u a lly all custo m ers have g raduall y tightened t h e ir specifications requ iri n g tighter control over the leve ls of acceptable resi d ua l ele m en ts.They a lso de-m and m ore consistentm echan ica lproperties,better stee l c l e an liness and i m proved surface and inter-nal qua lity.There is a need for steelm ills who expect to cost e ffecti v ely produce high strength,high qua lity auto m oti v e,pipeline and str uctural products to i n corporate mo re d i s c i p li n ed steel m ak i n g, clean steel-ladle m eta llurgy and consistent continuous casti n g practices to successfu ll y co m pete i n today.s g l o ba l co m petiti v e stee lm arke.t Th is paper descri b es the steel m ak i n g and casti n g consi d era-ti o ns and reco mm endations t h at are being i m ple m ented today by steel m akers to successfully cast high qua lity Nb-beari n g billets,slabs and bea m s.These practices have i n herently i m proved the qua lity of standar d carbon-m anganese g rades as w e l.lK ey w ords:conti n uous casting;clean stee;l ho t ductility;m e lti n g;n iob i u m0前言2008年全球含铌钢产量超过1亿,t世界各地有100多家钢铁厂生产含铌的板、带材及棒线材,其中一些钢厂严格控制了熔炼和连铸操作,可确保生产无裂纹缺陷的表面质量优良的方坯、板坯和异形坯等。
在已经发表的有关传统塑性低谷区的研究中,很多人认为塑性低谷区与高碳当量有关,而与是否含有微合金化元素(Nb、V和/或T i)无关。
然而,对于普通碳锰钢,如果某些炼钢和连铸参数不合理,塑性低谷区同样可以引起表面和内部质量问题。
比较了不同钢厂的炼钢和操作规程后发现,有些钢厂可以稳定地生产无缺陷含铌钢坯,而有些钢厂却总是遇到一些困难。
一般来说,能够稳定生产无缺陷坯的钢厂在其整个产品结构中总体质量评价也较好。
对于那些遇到困难的钢厂,他们通常将问题产生的原因归结于高温塑性低谷区。
许多研究表明塑性低谷区是普通碳锰钢和微合金化钢等各种成分钢的一种固有性质。
然而,相同成分的含铌钢可在其他钢厂成功地生产。
通常,在连铸过程中产生的裂纹是炼钢和连铸生产过程中的一些不合理的操作引起的,比如#17#2010年第2期残余元素的含量、过热度的波动、转包温度分层、结晶器保护渣不匹配、拉坯速度的波动、和/或过度二次冷却。
本文将探讨其中的一些根源,改进措施,减少或消除铸坯裂纹的产生办法,从而提高钢的表面和内部质量。
对于那些将自己定位于生产高品质含铌钢的钢厂,有机会享有生产附加值产品带来的更高的产品利润空间。
从熔炼到连铸,严格的过程控制是影响热轧产品最终性能的一个非常关键的因素,可使钢材获得:¹更好的低温韧性;º较高的屈服强度,以降低结构的横截面积;»改善扩孔成形性能;¼更好的可焊性,以减少施工时间;½改善热影响区(HAZ组织)韧性;¾改善高温性能;¿改善抗疲劳性能。
1炼钢过程中的冶金操作事项在生产高品质钢时,由于去除有害残留元素的动力学和热力学条件在炼钢和精炼过程不同,有时甚至是相互矛盾的,所以可以采取不同策略来控制残留元素的含量。
每个钢厂都需要彻底了解自身的过程冶金变量,形成自己的操作实践,才能生产所需成分的钢种。
钢中残余元素是一个非常重要的基础条件。
通常,钢厂在生产复杂的微合金钢初期,由于钢中残余元素高,可能导致产生裂纹、表面质量差和偏析问题。
造成热塑性降低的根本原因是残余元素含量高,但在某些情况下,缺陷或裂纹产生的根源被错误地归因于Nb对塑性低谷区的影响。
在生产高附加值的品质钢材时,残余元素的质量分数至少应符合以下标准:#w P:[0.015%;#w S:0.010%~0.015%,非关键钢种;0.005%~0.010%,钙处理钢;0.002%~0.005%,钙处理的重要钢种;#w O:[0.0015%;#w H:[0.0002%,关键钢种;#w N:尽可能低(转炉炼钢中w N通常低于0.0050%,而电炉炼钢中w N要低于0.0065%)。
在解决含铌钢表面质量问题时,建议优先采取的操作是:用钙处理,将S质量分数降至0.002%~0.010%水平。
钙处理并不能确保获得无缺陷铸坯,却能极大地增加改善表面质量和内部纯净度的可能性。
下一节将介绍残余元素对热塑性的影响,如N、H、S、P、Cu等。
1.1残余元素对铸造性和热塑性的影响在含A l的微合金化钢中,通常认为N不利于钢的热塑性。
为了避免横向裂缝,N含量应保持尽可能低的水平。
在某些情况下,T i的加入对热塑性也是有害的。
然而,在低冷却速度下,在低N(质量分数0.005%)的C-M n钢中添加T,i又有助于获得更好的热塑性。
当T i B N为4.5B1时,可以获得最佳的热塑性。
对于高N钢(电炉炼钢典型的质量分数0.010%),建议T i的加入量不要太高(质量分数0.010%),以减少含T i粒子的数量。
此外,钢中溶解的A l含量要低,以防止与过量N元素结合形成A l N。
对于C-M n-Nb-A l钢,T i的影响与C-M n钢类似。
这些钢中存在的Nb和A l元素会粗化含T i粒子,因而对热塑性低谷区的影响一般不大。
因为在较高的温度下高N含量会促进析出行为,T i与N结合后,剩余的N可能对热塑性有利。
钢中的S含量应保持在尽可能低的合理水平,以降低有害的细小硫化物在奥氏体晶界析出倾向。
钙夹杂物形貌控制处理将球化硫化锰夹杂并改善连铸机矫直段铸坯的塑性。
钢中残留的Cu通常来自废钢料,其残留的Cu 质量分数应小于0.15%。
残留Cu对铸坯的表面质量有害,促使发生横向开裂。
Sn的影响与Cu类似。
虽然Cu对热塑性有害,但是加入少量的N i可以抵消引起的热塑性损失(w N i B w Cu通常控制在1.5 ~2.0范围内)。
P是大量研究工作关注的一种元素。
过去的一些研究表明,在某些情况下,钢中P的质量分数低于0.25%可改善700~1200e区间铸坯的塑性[1]。
这种改善的结果是在偏析减少的前提下获得的。
如果有较多的P发生偏析,枝晶间液体将在低于固相线下的某一温度出现。
在奥氏体晶界上出现这种液膜将严重降低铸坯的热塑性[2]。
这种状况将使铸钢容易在连铸早期和结晶器后的铸造阶段产生开裂。
虽然已经证实少量P可改善C-Mn钢和C-M n-A l-Nb钢的热塑性,但不建议采用这种方法改善热塑性。
1.2控制氮含量降低裂纹率图1显示了铝镇静钢中随N含量的提高铸坯裂纹敏感性增加,在连铸汽车用钢和结构钢中这种现象更为明显。
通过使用低氮的原料及# 18 #世 界 钢 铁结合实际操作,可以尽量减少在炼钢过程中和随后工序中N 的吸入,从而达到降低钢中N 含量的目的。
图1 N 质量分数对裂纹指数的影响(铝镇静钢)[3]采用以下操作可使板坯连铸机中间包的N 质量分数低于0.006%:(1)对于联合炼钢,保持铁水中的T i 质量分数高于0.10%。
从高炉出来的铁水中的T i 含量越高,铁水中N 含量就越低;(2)避免转炉炼钢后吹操作。
在C 含量低的情况下,后吹操作的增加会使N 含量急剧上升。
如果后吹时间超过60s ,会吸入相当含量的N;(3)由于出钢温度的提高会引起N 含量的增加,所以降低出钢温度有利于降低N 含量[3]。
在较高温度下出钢,N 含量的波动要明显大一些;(4)在出钢过程中,进行部分脱氧和使用石灰石屑可减少N 质量分数的增加(高达0.001%);(5)钢水搅拌操作必须稳定一致,一定要尽可能避免钢包炉(LF 炉)底部强搅拌。
大部分N 的吸入是由于吹开钢液顶部的渣层,钢液表面直接暴露到大气中而产生的;(6)氩封长水口系统应取代氮封。
成本效益分析表明,改善表面质量和减少缺陷带来的好处超过使用氩气带来的较高成本。