连铸坯凝固与铸坯质量
连铸坯质量缺陷

连铸坯的质量缺陷及控制摘要连铸坯质量决定着最终产品的质量。
从广义来说所谓连铸坯质量是得到合格产品所允许的连铸坯缺陷的严重程度,连铸坯存在的缺陷在允许范围以内,叫合格产品。
连铸坯质量是从以下几个方面进行评价的:(1)连铸坯的纯净度:指钢中夹杂物的含量,形态和分布。
(2)连铸坯的表面质量:主要是指连铸坯表面是否存在裂纹、夹渣及皮下气泡等缺陷。
连铸坯这些表面缺陷主要是钢液在结晶器内坯壳形成生长过程中产生的,与浇注温度、拉坯速度、保护渣性能、浸入式水口的设计,结晶式的内腔形状、水缝均匀情况,结晶器振动以及结晶器液面的稳定因素有关。
(3)连铸坯的内部质量:是指连铸坯是否具有正确的凝固结构,以及裂纹、偏析、疏松等缺陷程度。
二冷区冷却水的合理分配、支撑系统的严格对中是保证铸坯质量的关键。
(4)连铸坯的外观形状:是指连铸坯的几何尺寸是否符合规定的要求。
与结晶器内腔尺寸和表面状态及冷却的均匀程度有关。
下面从以上四个方面对实际生产中连铸坯的质量控制采取的措施进行说明。
关键词:连铸坯;质量;控制1 纯净度与质量的关系纯净度是指钢中非金属夹杂物的数量、形态和分布。
夹杂物的存在破坏了钢基体的连续性和致密性。
夹杂物的大小、形态和分布对钢质量的影响也不同,如果夹杂物细小,呈球形,弥散分布,对钢质量的影响比集中存在要小些;当夹杂物大,呈偶然性分布,数量虽少对钢质量的危害也较大。
此外,夹杂物的尺寸和数量对钢质量的影响还与铸坯的比表面积有关。
一般板坯和方坯单位长度的表面积(S)与体积(V)之比在0.2~0.8。
随着薄板与薄带技术的发展,S/V可达10~50,若在钢中的夹杂物含量相同情况下,对薄板薄带钢而言,就意味着夹杂物更接近铸坯表面,对生产薄板材质量的危害也越大。
所以降低钢中夹杂物就更为重要了。
提高钢的纯净度就应在钢液进入结晶器之前,从各工序着手尽量减少对钢液的污染,并最大限度促使夹杂物从钢液中排除。
为此应采取以下措施:⑴无渣出钢。
提高连铸坯内部质量的方法
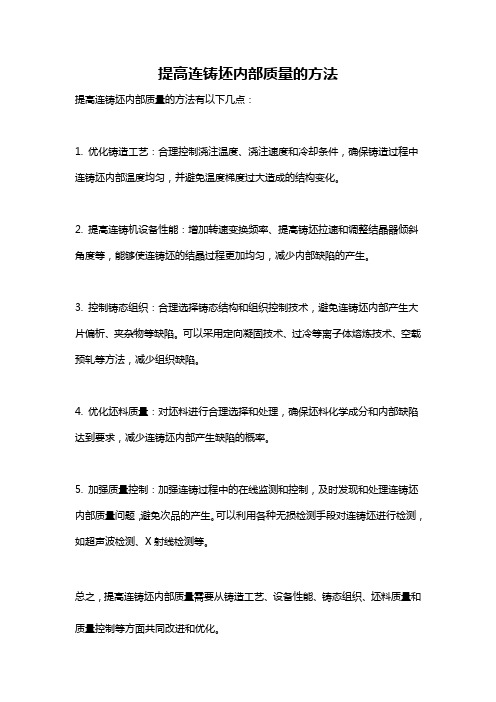
提高连铸坯内部质量的方法
提高连铸坯内部质量的方法有以下几点:
1. 优化铸造工艺:合理控制浇注温度、浇注速度和冷却条件,确保铸造过程中连铸坯内部温度均匀,并避免温度梯度过大造成的结构变化。
2. 提高连铸机设备性能:增加转速变换频率、提高铸坯拉速和调整结晶器倾斜角度等,能够使连铸坯的结晶过程更加均匀,减少内部缺陷的产生。
3. 控制铸态组织:合理选择铸态结构和组织控制技术,避免连铸坯内部产生大片偏析、夹杂物等缺陷。
可以采用定向凝固技术、过冷等离子体熔炼技术、空载预轧等方法,减少组织缺陷。
4. 优化坯料质量:对坯料进行合理选择和处理,确保坯料化学成分和内部缺陷达到要求,减少连铸坯内部产生缺陷的概率。
5. 加强质量控制:加强连铸过程中的在线监测和控制,及时发现和处理连铸坯内部质量问题,避免次品的产生。
可以利用各种无损检测手段对连铸坯进行检测,如超声波检测、X射线检测等。
总之,提高连铸坯内部质量需要从铸造工艺、设备性能、铸态组织、坯料质量和质量控制等方面共同改进和优化。
连铸圆坯凝固传热行为与铸坯质量的控制

。
随着 连铸技术 的发 展 , 提 高连 铸坯产 量 和质量成 为连铸 技 术研 究 的 主要 问题 之 一 。连续 铸 钢技 术 是将
液态钢水在浇注过程中连续不断地冷却凝 固成固态 , 在这一高温过程中伴 随着极其复杂 的传质 , 传热 , 相变 以及流动等物理化学现象。铸坯在冷却凝固传热过程 中, 由于受到复杂力 的作用( 机械应力 , 热应力, 相变 应 力等 ) , 从而对 连铸 坯 的质量有 着直 接 的影 响 , 连铸 坯在 这一过 程 中所形 成 的各 种 缺 陷 ( 包 括表 面裂 纹 , 内 部裂 纹 , 缩孔 , 偏析 , 变形 等 ) 基本 上 与温度 的分 布有关 系 。因此 , 在 很 大程 度 上 来 讲 , 通过 研 究 连铸 坯 在 二 次冷却过程中的凝固传热行为 , 来合理 的控制铸坯的冷却条件 , 从而提高铸坯的质量是非常有必要的。 连铸坯 裂纹 是影 响连铸 机产 量 和铸坯 质 量 的重要 缺 陷 之一 。据 生 产资 料 统计 铸 坯 各类 缺 陷 中约 5 0 % 为铸坯裂纹。铸坯出现裂纹, 严重 的情况时会导致铸坯出结晶器后拉漏 , 影响铸坯收得率; 轻微裂纹也不能 直接送轧钢厂进行轧制 , 必须进过精整处理者要进行精整处理 , 影响铸坯的热送率 。因此说 , 铸坯一旦 出现 裂纹, 就会影响铸机的生产率 , 产品的合格率 。 铸 坯产生裂 纹 与钢液 凝 固过 程传 热有极 大 的关 系 , 因此 , 通过 对铸 坯 在 二冷 区域传 热 的分 析研 究 , 来 探 索铸 坯裂 纹 的成 因相 当重 要 。
( 2 ) 潜热 , 是指 钢液从 液相 线温度 凝 固到 固相 线时所 释放 出来 的热量 。
( 3 ) 显热 , 是指 由固相线温度冷却至室温或指定温度时释放 的热量 。 在连铸机生产的过程中, 钢水热量的释放分别经历了结晶器冷却 ( 一次冷却 ) , 扇形段喷淋冷却( 二次冷 却) 和空冷。在一冷区, 钢水在水冷结晶器中形成厚度和强度足够且均匀的坯壳 , 以保证铸坯出结晶器不拉 漏; 在二冷区, 喷水 ( 雾) 以加速连铸坯 内部热量的传递; 空冷 区铸坯辐射传热 , 是铸坯内外温度均匀。传热 方式包括了对流、 热传导、 辐射传热 。影响铸坯热量传递过程的诸因素 中, 如果连铸机的设备和工艺操作确 定的情况下 , 通过控制二次冷却来解决热量的传递问题成为一种重要的处理手段。
连铸坯质量控制

连铸坯质量控制连铸坯质量控制1. 引言2. 连铸坯质量特点连铸坯的质量特点主要包括以下几个方面:2.1 凝固结构连铸坯是通过冷却凝固过程形成的,其凝固过程直接影响到坯体的凝固结构。
凝固结构的好坏会对后续的加工以及材料性能产生重要影响。
2.2 化学成分均匀性连铸坯的化学成分均匀性是其质量的重要指标之一。
成分不均匀容易导致后续钢材性能不稳定,从而影响到产品的质量。
2.3 表面缺陷由于连铸坯制造过程中的一些不可避免的因素,气体夹杂、氧化皮等,会在坯体表面形成一些缺陷。
这些表面缺陷会对后续产品的外观质量产生负面影响。
2.4 尺寸偏差连铸坯的尺寸偏差是指坯体的实际尺寸与标准尺寸之间的差异。
尺寸偏差会影响到钢材的加工工艺和成形质量。
3. 连铸坯质量控制因素及措施连铸坯质量的影响因素众多,包括原料质量、连铸工艺参数、设备状况等。
针对这些影响因素,可以采取以下控制措施来提高连铸坯的质量:3.1 原料质量控制通过严格控制原料的化学成分和物理性能,确保连铸坯的化学成分均匀性和机械性能达到要求。
3.2 连铸工艺参数控制连铸工艺参数的合理设置对坯体的凝固结构和表面质量具有决定性影响。
需要通过优化连铸工艺参数,如冷却水流量、浇注速度等,来控制连铸坯的质量。
3.3 设备维护与改进连铸设备的状态对连铸坯质量也有重要影响。
定期进行设备维护和检修,及时处理设备故障,可以保证设备处于良好状态,进而提高连铸坯的质量。
3.4 检测手段与技术利用先进的检测手段和技术,如超声波检测、磁力检测等,可以对连铸坯进行质量检测,及时发现问题并采取相应措施。
4.连铸坯质量控制是钢铁生产中至关重要的环节。
通过对连铸坯质量特点的分析和影响因素的控制,可以采取相应的措施来提高连铸坯的质量。
这不仅对于保证下游产品质量,还对于提高工业生产效益和降低资源消耗具有重要意义。
开展连铸坯质量控制工作是必不可少的。
连铸坯质量的控制

连铸坯质量的控制
一、引言
连铸是钢铁生产过程中的重要环节,其连铸坯的质量影响着钢质的稳定性、物
理性能和化学成分等方面。
因此,连铸坯质量控制一直是钢铁生产中的关键技术之一。
二、连铸坯质量的影响因素
1.原料质量:包括钢水、氧化渣等的质量;
2.坯型结构和尺寸:坯型结构和尺寸的设计直接影响坯料的冷却效果和
内部应力状态;
3.坯料表面状态:表面缺陷会在浇铸过程中暴露出来,影响坯料的质量;
4.坯料内部缺陷:坯料内部缺陷会影响钢材的使用寿命和物理性能;
5.连铸工艺参数:包括浇注速度、结晶器温度和冷却水流量等。
三、连铸坯质量控制的措施
为了控制连铸坯质量,需要在生产过程中采取以下措施:
1.加强原料质量控制:保证钢水、氧化渣等原料的质量,避免对坯料质
量的不利影响;
2.优化坯型设计:通过设计合理的坯型结构和尺寸,使坯料均匀冷却、
内部应力均匀分布;
3.改进坯料清理技术:减少表面缺陷的产生;
4.加强坯料表面处理:处理坯料表面缺陷,消除缺陷部位;
5.控制连铸工艺参数:调整浇注速度和结晶器温度等工艺参数控制坯料
成分,改善坯料品质。
四、
通过加强原料质量控制、优化坯型设计、改进坯料清理技术、加强坯料表面处
理和控制连铸工艺参数等措施,可以有效地控制连铸坯质量。
同时,连铸坯质量控制也是钢铁生产中不可或缺的环节,对于提高钢材质量和降低成本都具有非常重要的意义。
炼钢-精炼-连铸流程连铸坯质量控制

炼钢-精炼-连铸流程连铸坯质量“零缺陷”控制北京科技大学冶金与生态工程学院蔡开科孙彦辉2012.5目录1.连铸凝固过程的冶金特性2.连铸钢水质量纯净度(洁净度)控制3.连铸坯裂纹缺陷控制4.连铸坯内部中心缺陷控制5.结语21. 连铸坯凝固过程的冶金特性1. 1连铸坯凝固过程基本特征把钢水凝固成固体,根据冷却速度不同有两种凝固工艺如图:●钢锭模浇注工艺●连续铸钢工艺连铸与模铸流程比较连续铸钢是一项把钢水直接浇注成形的新工艺,它的出现从根本上改变了一个世纪以来占统治地位的钢锭→初轧工艺。
与模铸相比,连铸的优点:◆节省工序,缩短流程◆提高金属收得率10~14%◆降低能耗减少1/2~1/4◆机械化自动化程度高◆产品质量好2011年中国钢产量达到6.75亿吨,2011年我国连铸比达98%以上,已达到饱和状态。
近年来近终型(Near Net-Shape)连铸技术如薄板坯连铸连轧(CSP、FTSC…)和中等厚度板坯连铸得到了很大的发展。
与钢锭模浇铸工艺相比,如图所示,连续铸钢过程基本特点如下:(1)连铸坯凝固过程实质上是动态热量传递过程钢水从液态转变为固体放出热量:钢水→固体+Q放出热量包括:✓过热✓凝固潜热✓物理显热连铸凝固过程示意图以20钢为例,钢水凝固冷却到室温放出热量是:✓过热25.2 kJ/kg✓潜热328 kJ/kg✓显热958 kJ/kg总热量中大约1/3从液体→固体放出,其余2/3是完全凝固后放出的。
钢水在连铸机内凝固是一个热量释放和传递的过程,铸坯边运行,边放热,边凝固,形成了很长的液相穴(10~20几米),在液相穴长度上布置了三个冷却区:●一次冷却区:钢水在结晶器中形成足够厚的均匀坯壳,以保证铸坯出结晶器不拉漏。
●二次冷却区:喷水加速铸坯内部热量的传递,使其完全凝固。
●三次冷却区:铸坯向空气中辐射传热使铸坯温度均匀化。
以20钢为例,经过钢水凝固热平衡计算,得出以下概念:a)钢水从结晶器→二冷区→辐射区大约有40%热量放出来,铸坯钢水才能完全凝固。
连铸坯质量基础知识

•选分结晶与偏 析
3.钢水结晶基础理论
•中心偏析影响因素
• 主要影响因素: ①冷却速度。加大冷却速度,缩短凝固时间,使溶质元素 没有足够时间析出。 ②溶质元素的偏析倾向。用已凝固金属中的浓度与液相中 的浓度相比,比值越小,说明偏析的倾向越大。 ③溶质元素在固体金属中的扩散速度。
偏析的大小可用偏析量来表示: B=C÷〔(C1+C2+C3+C4)÷4 〕
3.钢水结晶基础理论
• 选分结晶又称选择结晶。合金元素在固、液相中的溶解度是 有差异的,一般而言在固相中的溶解度小于在液相中的溶解 度。因此合金元素在固相钢中分配的浓度要小,而在液相钢 (母液)中分配的浓度要大,所以在钢的结晶过程中,于结 晶前沿会有溶质大量析出并积聚,固相中溶质浓度就低于原 始浓度,这种现象即所谓选分结晶。随着母液溶质的不断富 集而使浓度不断上升,随温度的不断下降,钢液最终会全部 凝固,所以最后凝固部分的溶质含量会高于原始浓度。显然 在最终凝固结构中溶质浓度分布是不均匀的,这种成分不均 匀的现象称为偏析。 • 分析一根铸坯,通常会发现铸坯中心溶质浓度较高,即所谓 的中心偏析。
1.钢水中常见元素及基本概念
钒(V):钒是钢的优良脱氧剂。钢中加0.5%的钒可细 化组织晶粒,提高强度和韧性。钒与碳形成的碳化 物,在高温高压下可提高抗氢腐蚀能力。 钨(W):钨熔点高,比重大,是贵生的合金元素。钨 与碳形成碳化钨有很高的硬度和耐磨性。在工具钢 加钨,可显著提高红硬性和热强性,作切削工具及 锻模具用。
2.钢中残留元素及其控制
钢中微量元素分为两类:一类为有意加入的元 素,如为改善机械切削性能加入S、Pb、Se、Te,为 抗腐蚀加Cu等。另一类是由炼钢炉料和浇注过程带 入的元素,如来自炉料的元素有Cu、As、Sb、Zn、 Sn、S、P,来自结晶器的Cu,来自保护渣的S等。 在钢的成分中不是有意加入的元素,而是随原 料带入的元素,在冶炼过程中又没能去除而残留于 钢中称为残留元素。如Cu、Sn、Sb、As等,其中Cu、 Sn的危害最大,因此残留元素含量必须严格限制。 Cu、Sn含量限制在0.20%以下。
连铸坯产生质量问题的原因
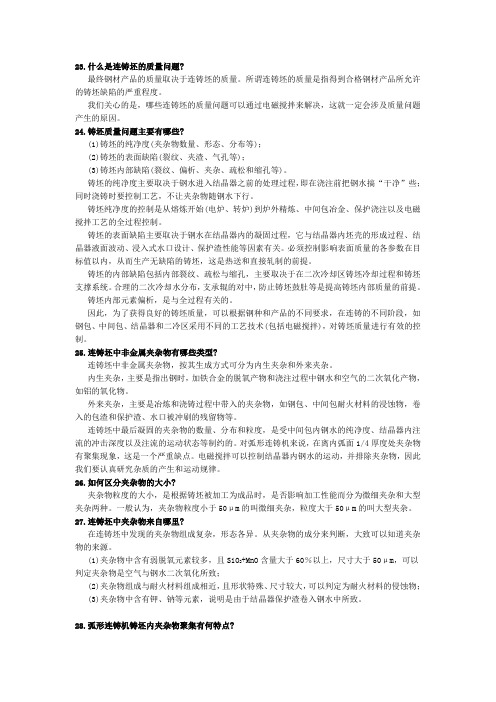
23.什么是连铸坯的质量问题?最终钢材产品的质量取决于连铸坯的质量。
所谓连铸坯的质量是指得到合格钢材产品所允许的铸坯缺陷的严重程度。
我们关心的是,哪些连铸坯的质量问题可以通过电磁搅拌来解决,这就一定会涉及质量问题产生的原因。
24.铸坯质量问题主要有哪些?(1)铸坯的纯净度(夹杂物数量、形态、分布等);(2)铸坯的表面缺陷(裂纹、夹渣、气孔等);(3)铸坯内部缺陷(裂纹、偏析、夹杂、疏松和缩孔等)。
铸坯的纯净度主要取决于钢水进入结晶器之前的处理过程,即在浇注前把钢水搞“干净”些;同时浇铸时要控制工艺,不让夹杂物随钢水下行。
铸坯纯净度的控制是从熔炼开始(电炉、转炉)到炉外精炼、中间包冶金、保护浇注以及电磁搅拌工艺的全过程控制。
铸坯的表面缺陷主要取决于钢水在结晶器内的凝固过程,它与结晶器内坯壳的形成过程、结晶器液面波动、浸入式水口设计、保护渣性能等因素有关。
必须控制影响表面质量的各参数在目标值以内,从而生产无缺陷的铸坯,这是热送和直接轧制的前提。
铸坯的内部缺陷包括内部裂纹、疏松与缩孔,主要取决于在二次冷却区铸坯冷却过程和铸坯支撑系统。
合理的二次冷却水分布,支承辊的对中,防止铸坯鼓肚等是提高铸坯内部质量的前提。
铸坯内部元素偏析,是与全过程有关的。
因此,为了获得良好的铸坯质量,可以根据钢种和产品的不同要求,在连铸的不同阶段,如钢包、中间包、结晶器和二冷区采用不同的工艺技术(包括电磁搅拌),对铸坯质量进行有效的控制。
25.连铸坯中非金属夹杂物有哪些类型?连铸坯中非金属夹杂物,按其生成方式可分为内生夹杂和外来夹杂。
内生夹杂,主要是指出钢时,加铁合金的脱氧产物和浇注过程中钢水和空气的二次氧化产物,如铝的氧化物。
外来夹杂,主要是冶炼和浇铸过程中带入的夹杂物,如钢包、中间包耐火材料的浸蚀物,卷入的包渣和保护渣、水口被冲刷的残留物等。
连铸坯中最后凝固的夹杂物的数量、分布和粒度,是受中间包内钢水的纯净度、结晶器内注流的冲击深度以及注流的运动状态等制约的。
- 1、下载文档前请自行甄别文档内容的完整性,平台不提供额外的编辑、内容补充、找答案等附加服务。
- 2、"仅部分预览"的文档,不可在线预览部分如存在完整性等问题,可反馈申请退款(可完整预览的文档不适用该条件!)。
- 3、如文档侵犯您的权益,请联系客服反馈,我们会尽快为您处理(人工客服工作时间:9:00-18:30)。
连铸坯凝固与铸坯质量50.钢中微量元素对连铸坯质量有何影响?所谓钢中微量元素分为两类:一类为有意加入的元素,如为改善机械切削性能加入S、Pb、Se、Te,为抗腐蚀加Cu等。
另一类不是有意加入而是由炼钢炉料和浇注过程带入的元素,如来自炉料的元素有Cu、As、Sb、Zn、Sn、S、P,来自结晶器的Cu,来自保护渣的S 等。
对于炉料带入的这些微量元素,对用高废钢的电炉冶炼是一个实际问题,在冶炼过程去除这些元素是很困难的,残留在钢中对质量的影响是:(1)结晶器裂纹:结晶器弯月面铜板由于热疲劳的原因常常出现网状裂纹。
如果保护渣中的硫和钢中的锌渗入铜板会形成深的裂纹而报废。
(2)铸坯表面裂纹:由于铸坯表面铁的氧化而使Cu、Sn、Sb等元素富集,形成细小表面晶间裂纹。
一般对钢筋钢无多大影响,而对特殊钢就会带来危害。
铸坯表面Ni的富集,可以抵销Cu的有害作用,因为Cu—Ni形成晶间化合物熔点较高。
(3)铸坯内部裂纹和偏析加重。
微量元素S、P偏析是输送酸性气体的高强度管线钢产生裂纹的根源。
因此要求把钢中硫降低到5ppm,磷降到25ppm,以满足所要求性能。
只有采用精选炉料或炉料搭配使用(如采用海绵铁),以减少炉料带入的微量元素。
提高钢质量。
51.脱氧方式对连铸坯质量有何影响?脱氧方式会影响钢中夹杂物类型、钢水流动性和钢的清洁度,因此选择脱氧方式是非常重要的。
一般的钢常用Si、Mn脱氧较好,这些脱氧剂一般形成可变形的球形硅酸盐夹杂物,这种夹杂物能上浮排除且不影响钢水可浇性。
用铝脱氧会形成高熔点(2050℃)成串簇状不变形的Al203夹杂,这种夹杂物会影响钢水的可浇性,还会沉积在中间包水口壁上造成水口堵塞,影响浇注正常进行。
采用Si-Ca脱氧,脱氧效果、夹杂物形态和钢水的可浇性都较好,但价格较贵,加入时产生烟雾,污染工作环境。
52.特殊钢凝固有哪些特点?特殊钢中加入了合金元素,其凝固特性与普碳钢有所不同,这是连铸时要注意之点。
(1)钢中含有较强的活泼元素:如不锈钢中含有Al、Ti等元素容易和0、N结合,生成Al2O3、TiO2、TiN、Ti(CN) (Cr—Al)2O3、(Mn—Ti)2O4等复杂的夹杂物,给浇注操作(如堵水口)和铸坯质量带来危害。
(2)凝固温度区间变化大:合金元素含量较高,意味着液相线和固相线温度区间较大。
如奥氏体不锈钢(18~20%Cr,8~10%Ni)的TL(液相线温度)=1449℃,Ts(固相线温度)=1393℃,△T=TL一TS=56℃;铁素体不锈钢(10~11%Cr)的TL=1507℃,Ts=1482℃,△T=25℃。
钢中C由0.2%增加到0.5%,△T由30℃增加到60℃。
凝固温度区间的变化,在选择钢水过热度、二次冷却水量和水量分配时必须予以考虑。
(3)凝固结构:铸坯凝固结构对产品质量有十分重要影响。
根据钢中合金元素含量不同,钢液凝固有3种类型:1)钢水凝固成δ相或γ相,如铁素体的Cr钢和奥氏体的Cr-Ni钢;2)钢水首先凝固成δ相,然后转变成γ相。
如含有δ相的Ni-Cr奥氏体钢;3)钢水首先凝固成δ相,然后发生δ→γ→α相的转变。
如C<O.53%的低合金钢的凝固。
初晶为δ相或γ相对显微偏析有很大的差别。
δ相中溶质元素扩散比γ相中快100倍。
因此γ相中显微偏析严重、提高裂纹敏感性。
二次枝晶间距是显微偏析的量度。
在冷却条件一定时,合金元素含量增加,二次枝晶间距减小,显微偏析减轻。
(4)热物理性能:合金钢热物理性能(如导热系数入、热膨胀系数α)变化较大。
如表6-1所示,不锈钢导热系数比碳钢要小,而凝固收缩量比碳钢要大。
表6-1钢热物理性能收缩量/%0~500℃膨胀系数10-6/℃导热系数800℃1000℃不锈钢(Cr-Ni)7.518.3622.825.4碳钢3-411.739.230.0纯铁--43.332.8二次冷却区传热速率主要受凝固壳厚度的限制。
而坯壳传热决定于钢的导热系数。
不锈钢导热系数小于碳钢,则凝固速度就有明显的差别。
如152mm厚碳钢坯完全凝固需6min,而同样厚的不锈钢坯则需18min,可见凝固速度是与钢的导热系数成比例的。
因此对合金钢坯二次冷却区的设计必须充分考虑这点。
钢的导热系数不同,凝固组织也不同。
如铁素体不锈钢导热系数比奥氏体不锈钢大20~50%,因而铁索体不锈钢典型凝固组织是柱状晶+等轴晶,而奥氏体不锈钢是贯穿的柱状晶,热加工时容易产生裂纹。
(5)钢高温性能:钢的裂纹敏感性取决于钢的高温力学性能(延伸率和强度)。
如奥氏体不锈钢,高温强度较高(1300℃的抗拉强度1.23kg/cm2),可用较高拉速。
铁素体(16~18%Cr)和马氏体不锈钢(Crl2~14%),高温强度较低(1300℃抗拉强度0.25kg/cm2),极易产生裂纹,连铸时必须相应降低拉速。
合金元素对钢的热延性曲线中的转变为脆性口袋区的温度有重要影响。
必须实测测定,以决定合理的二次冷却配水制度,保证进矫直机的铸坯表面温度达到规定值。
(6)裂纹敏感性:从本质上说,裂纹敏感性决定于钢种,但它又与钢水质量、冷却制度、凝固结构、铸坯应力等有关。
如Cr-Ni不锈钢,最终组织为奥氏体,显微偏析严重,故裂纹敏感性强。
Cr不锈钢凝固组织为铁素体,偏析轻,裂纹敏感性差。
上述特性,对不同钢种表现的程度是不一样的。
要使连铸特殊钢获得成功,主要是依靠对上述凝固的基本特性不断加深理解,就可使连铸产品质量超过相应的钢锭产品质量。
53.为什么连铸不能浇注沸腾钢?连铸浇沸腾钢时,由于钢水在结晶器内的沸腾,易使蜂窝气泡外露和钢水溢出,影响铸坯表面质量和生产安全性。
沸腾钢表面质量好,价格便宜。
广泛应用于生产薄板和其他产品。
而沸腾钢不能用Si脱氧,只能用少量Al脱氧。
因为Si高,SiO2一MnO系夹杂在热轧卷中以条状存在,影响伸展性,由于Si在表面富集,在退火时易使薄板表面产生回火缺陷。
为了适应连铸韵要求,开发了与沸腾钢具有同等质量的钢种:(1)吕班德(RIBAND)钢,其成分为C<0.10%,Mn0.2~0.6%,Si 0.03~0.08%,A1 0.004~0.015%:(2)准沸腾钢,其成分为C<0.10%,Si 0.01%,Mn 0.25%,A1 0.006%;(3)铝镇静钢,其成分为C 0.03~0.06%,Si<0.02%,Mn<0.3%,A1 0.02~0.05%。
54.硬线钢连铸有哪些特点?生产钢丝的高碳钢有两种,一是轮胎钢丝(C=0.80~0.85%)要求有高的深拉性冷拔到0.15~0.25mm。
二是弹簧钢丝(C=0.6~0.7%)要求高的疲劳寿命和良好的耐磨强度。
这类钢属Si—Mn镇静钢。
要求铸坯中Al2O3夹杂和不变形夹杂要少,以免冷拔时产生断裂,为此要控制好脱氧产物成分:Al2O3/(Si02+MnO+A1203)=0.15~0.30[Mn]/[Si]≥1.7此时夹杂物熔点低,热轧时容易伸长,拉伸性能大为改善。
铸坯中心偏析要小,以免冷拔加工出现杯状断裂。
连铸这类钢时应注意:(1)合适的炉外精炼或合成渣处理,以减少不变形夹杂物;(2)钢凝固是奥氏体结构,结晶器坯壳与铜壁接触良好,结晶器可强冷,增加坯壳厚度;(3)采用全程保护浇注,防止二次氧化;(4)中间包钢水过热度控制在15~20℃;(5)二次冷却要均匀,防止回温,采用弱冷,比水量小于l/kg钢为宜;(6)矫直点铸坯表面温度大于900℃;(7)采用电磁搅拌,以减轻中心偏析。
55.深冲薄板钢连铸有何特点?深冲冷轧薄板广泛应用于冲制搪瓷用品、汽车、食品包装等行业。
要求有良好的强度、表面质量、深冲性能、抗时效性能等。
冷轧薄板产品过去都是由沸腾钢锭轧制,由于连铸不能浇沸腾钢,开发出三种沸腾钢连铸的代用钢。
(1)吕班德钢:其化学成分是(%):C 0.03~0.06,Si 0.03~0.08,Mn 0.35~0.45,A1 0.004~0.015。
实质为低碳低硅镇静钢。
该钢冶炼的关键在于控制钢水的氧化性。
为此出钢前在炉内加MnFe予以脱氧,根据直接定氧,准确调整加Al量。
连铸时拉速尽可能高一些,以防止产生针孔和气泡。
(2)准沸腾钢:其化学成分是(%)C 0.04,Si 0.0l,Mn 0.25,P 0.015,S 0.014,A1 0.006,N 0.0022。
这种钢不用Si脱氧仅用少量Al脱氧。
生产中最大的问题是如何控制脱氧程度,使在结晶器内钢水不沸腾、不产生皮下气孔。
(3)铝镇静钢:是一种低碳低硅加铝完全脱氧钢。
连铸钢的要求是:1)保持铜中酸溶铝稳定在0.02~0.05%;2)防止钢水中A1203堵水口;3)尽可能减少铸坯中的夹杂物,提高钢清洁度,使钢中总氧含量达到20ppm。
用于食品包装(如罐头,易拉罐)的镀锡板,对连铸坯质量要求更为严格。
其特点:1)最终产品厚度可达0.1~0.18mm,要求钢具有均匀机械性能和深冲性;2)钢要有高清洁度,钢中>50μm大颗粒夹杂要达到每10公斤钢1毫克或更低的水平;3)非常好的表面质量,有利镀层的粘结;4)钢中硫、磷含量尽可能低,以增加抗腐蚀能力。
应根据深冲薄板的不同用途(如搪瓷、镀锌板、镀锡板),确定对连铸坯清洁度的要求。
总的来说,连铸这类钢应注意以下几点:1)控制好钢水氧含量,要把钢中[A1]控制在所规定的范围内;2)中间包钢水过热度以30℃为宜;3)全程保护浇注,防止二次氧化;4)结晶器保护渣应有充分吸收Al2O3的能力;5)发挥中间包冶金作用。
56.中厚板钢连铸有何特点?一般称厚度在4mm以上的叫中厚板。
主要用于机械结构、桥梁、船舶等。
对中厚板最重要性能的要求是:抗张强度、冲击韧性、焊接性、抗大气和海水腐蚀性能等。
对于海洋和石油管线用钢(海洋平台、管线、容器等)要求抗层状撕裂、抗氢脆裂纹和低温冲击韧性等。
这些性能要求连铸坯成分偏析小、无内裂纹、无中心疏松和缩孔、脆性夹杂和硫化物夹杂含量低。
根据生产中厚板的不同用途,适用钢种主要是两大类,一是硅一铝镇静钢如Q235、20g、3C等。
二是细晶粒低合金钢或含Nb、V等微合金元素的高强度钢,一般钢中Mn含量较高,可达1.6%以上。
连铸这类钢,应注意以下几点:1)中间包钢水过热度较低为宜(一般为15℃);2)采用全程保护浇注;3)采用浸入式水口+保护渣。
应研制专用保护渣;4)拉速应低一些,二次冷却要均匀;5)采用电磁搅拌和轻压下技术,减轻中心偏析。
57.不锈钢连铸有何特点?目前几乎所有的不锈钢均可用连铸生产。
对于奥氏体(Ni—Cr型)不锈钢高温强度和延性较好,可以采用较高拉速;热膨胀系数和导热系数较大,连铸二次冷却强度可大一些(比水量可达1.3L/kg钢)。
对于铁素体不锈钢(16~18%Cr)高温强度较低,铸坯易产生裂纹,拉速应低一些;导热系数较小,二次冷却强度可低一些(比水量<lL/kg钢)。