步进电机及单片机英文文献及翻译
步进电机PLC控制技术中英文对照外文翻译文献

步进电机PLC控制技术中英文对照外文翻译文献中英文对照外文翻译文献(文档含英文原文和中文翻译)The shallow treads into the PLC control technique and development trend of electrical engineering1. Say all:Along with the micro-electronics technique and the calculator technical hair Exhibition, the programmable preface controller has an advance by leaps and bounds of hair Exhibition, its function has already outrun a logic control far and far, in proper order The scope of control, it has an effect to combine with calculator, can enter Go to imitate to control most, have along range correspondence function etc.. Have-The person is called it the modern D industry controls of three pay pillar greatly(namely PLC, robot, CAD/CAM)it a, currently programmable controller BE applied in metallurgy extensively, Mineral industry, machine, light Class D realm, automate for the industry Provided to there is the tool of one dint The PLC controls of tread to open the wreath servo organization into the electrical engineering should Used for combining tool machine to produce an on-line number to control a slippery pedestal to control automatically Make, can the province go to the number of that unit to control system, making that unit The cost of controlling the system lowers.2、What is a stepper motor:Stepper motor is a kind of electrical pulses into angular displacement ofthe implementing agency. Popular little lesson: When the driver receives a step pulse signal, it will drive a stepper motor toset the direction of rotation at a fixed angle (and the step angle). You can control the number of pulses to control the angular displacement, so as to achieve accurate positioning purposes; the same time you can control the pulse frequency to control the motor rotation speed and acceleration, to achieve speed control purposes.What kinds of stepper motor sub-:In three stepper motors: permanent magnet (PM), reactive (VR) and hybrid (HB) permanent magnet stepper usually two-phase, torque, and smaller, step angle of 7.5 degrees or the general 15 degrees; reaction step is generallythree-phase, can achieve high torque output, step angle of 1.5 degrees is generally, but the noise and vibration are large. 80 countries in Europe and America have been eliminated; hybrid stepper is a mix of permanent magnet and reactive advantages. It consists of two phases and the five-phase: two-phase step angle of 1.8 degrees while the general five-phase step angle of 0.72 degrees generally. The most widely used Stepper Motor. What is to keep the torque (HOLDING TORQUE)3、Tread into the basic characteristics of electrical engineering:(1)、tread generally into the accuracy of the electrical engineering for tread into Cape of 3-5% and don't accumulate.(2)、tallest temperatures which enter electrical engineering outward appearance and allow tread and lead into the electrical engineering temperature high can make the magnetism material of electrical engineering back first, cause the dint descend thus is as for lose a step, so the electrical engineering outward appearance allow of the tallest temperature should be decided by small back with electrical engineeringmagnetism material and order; Speak generally, the magnetism material backs to order all above have in 130 C an of even be up to 200C above, so tread completely normal into the electrical engineering outward appearance temperature in 80-90C.(3)、dints which enter electrical engineering would with turn to go up but descend soon,While treading to turn to move into the electrical engineering,electrical engineering each electricity feeling which round a set mutually will become one anti- to electromotive force; The frequency is more high, anti- to electromotive force more big ,big in its function, the electrical engineering enlarges with the frequency(or speed) but mutually the electric current let up, causing the dint descend thus.(4)、can revolve normally when 4 enter electrical engineering low speed, but if high in certain the speed can't start, and the companion have a roar the interjection tread to have a technique parameter into the electrical engineering: empty carry start frequency, then tread into electrical engineering at empty carry under circumstance can start normally of pulse frequency, if the pulse frequency is high in should be worth., The electrical engineering can't start normally, the possible occurrence throws a step or blocks up to turn. Under the situation that there is one load, the start frequency should be much lower if want to make the electrical engineering attain high speed to turn to move, the pulse frequency should have an acceleration process, then start the frequency is lower, then press certain acceleration to rise the high hoped. Tread to show the characteristics of with it into the electric motor, turn ages of manufacturing to develop important use to accompany with in the numeral small together of numeral turn technical of development and tread into the electricalengineering technical exaltation,tread will get an application in more realms into the electrical engineering.4、enter an electrical engineering control system to constitute:Tread is a kind of performance organization that will give or get an electric shock a pulse conversion to move for the Cape into the electrical engineering. When tread to receive to a pulse signal into the actuator, it drives a step to press the direction of enactment to turn to move an angle for fixing to be called "tread to be apart from Cape" into the electrical engineering, it revolves one-step circulate with the fixed angle one step. Can pass control pulse piece to control a Cape to move to attain the purpose of assurance most and thus; Can pass control pulse frequency to control electrical engineering to become dynamic speed and acceleration in the meantime, the purpose attained to adjust thus soon treads into the electrical engineering. Can be the special kind electrical engineering that a kind of control uses, make use of it didn't accumulate error margin accuracy to 100 to divide 100 of characteristics, be suffused with to apply in various open a wreath control PLC which enter electrical engineering technique.5、Stepper motor of the PLC control technology:Make the importation tread to be subjected to a homologous control into total amount and pulse frequency of the importation pulse of electrical engineering. Establish the pulse signal occurrence that a pulse total amount and pulse frequency can control a machine therefore and in control,software; Can make use of PL in fixed time a machine composing for the frequency lower control pulse, the pulse frequency can pass in fixed time machine in fixed time constant control pulse period, the pulse amounts control then can establish a the pulsecounter C10 be when the pulse number attain initial value, count machine C1.The action cuts off pulse back track, making it stop, the servo organization tread into the electrical engineering have no the pulse input then stop operation,servo performance organization fixed position be servo performance organization of when move speed to have higher request, can use PLC high-speed pulse,Different PLC it the frequency of high-speed pulse can reach to 4000-6000Hzses. The PLC is used to produce control pulse, passing PLC plait distance exportation several pulses certainly the control treads to turn Cape into the electrical engineering, programmable controller output's control the pulse enters electrical engineering to switch on electricity sequence to assign by the step homologous of round a set. The PLC controls of tread can go an allotment machine by adoption software wreath into the electrical engineering, the hardware wreath goes allotment machine to adopt the PLC resources that the soft wreath takes up more, Tread especially to round a set to count mutually into the electrical engineering big should consider adoption hardware wreath to go allotment machine well for large production line at 4, although the hardware structure is a little bit a little more complicated, can save an exportation importation of taking up the PLC point, the market has a various appropriation chips to choose to use currently. Tread to enlarge to several ten highest hundred folds into the output's control of the actuator PLC of the electrical engineering power pulse, volt, several Anne arrive several ten several Anne s drive an ability, the exportation of general PLC connects to have to certainly drive an ability, but inside usual transistor flow exportation to connect an ability only for ten several arrive several ten volts, several ten arrive several 100 million Anne but tread to then have several request into theelectrical engineering to the power ten arrive up 100 volts, several Anne arrive several ten Anne s drive an ability so should adopt an actuator to output the pulse carry on enlarging.6、Application features of PLC(1)、High reliability, strong anti-interferenceHigh reliability is the key to performance of electrical control equipment. PLC as the use of modern large scale integrated circuit technology, using the strict production process, the internal circuits to the advanced anti-jamming technology, with high reliability. Constitute a control system using PLC, and the same size compared to relay contactor system, electrical wiring and switch contacts have been reduced to hundreds or even thousands of times, fault also greatly reduced. In addition, PLC hardware failures with self-detection, failure alarm timely information. In the application software, application are also incorporated into the peripheral device fault diagnosis procedure, the system is in addition to PLC circuits and devices other than the access protection fault diagnosis. In this way, the whole system extremely high reliability.(2)、Fully furnished, fully functional, applicabilityPLC to today, has formed a series products of various sizes, can be used for occasions of all sizes of industrial control. In addition to processing other than logic, PLC data, most of computing power has improved, can be used for a variety of digital control in the field. A wide variety of functional units in large numbers, so that penetration to the position of PLC control, temperature control, CNC and other industrial control. Enhanced communication capabilities with PLC and human-machine interface technology, using the PLC control system composed of a variety of very easily.(3)、Easy to learn, well engineering and technical personnel welcome PLC is facing the industrial and mining enterprises in the industrial equipment. It interfaces easily, programming language easily acceptable for engineering and technical personnel. Ladder language, graphic symbols and expressions and relay circuit very close to are not familiar with electronic circuits, computer principles and assembly language do not understand people who engage in industrial control to open the door.(4)、System design, the workload is small, easy maintenance, easy to transformPLC logic with memory logic instead of wiring, greatly reducing the control equipment external wiring, make the control system design and construction of the much shorter period, while routine maintenance is also easier up, even more important is to change the procedures of the same equipment has been changedproduction process possible. This is particularly suitable for many varieties, small batch production situations.7、The development trend of 5 domestic and international electrical engineering: (1)、continue along small scaled direction development turned along with electric motor application the realm open widely and each kind of whole machine is continuously small scaled to turn, the electric motor which requests with its kit have to also more and more small, at 57, the electric motor of 42 machine seat numbers applies many after years, now its machine seat number to 39,35,30,25 directions get down extension.(2 )、right nesses of electric motors carry on comprehensive design namely turn soon position to spread afeeling machine, decelerate the wheel gear etc. and electric motor essence to synthesize design together, so make it be able to constitute 1 to shut wreath system expediently, as a result have one more superior control function.(3)、to five mutually with three mutually the electric motor direction develop,Be suffused with currently applied of two mutually with four mutually the electric motor, its vibration and voice are bigger, but five mutually with three mutually the electric motor have advantage but in regard to these two kinds of electric motors, five mutually the electric motor drive electric circuit compare. 8、Conclusion:At present, the use of programmable process controller (that is, the PLC technology) can easily realize the control of motor speed and the position of the convenient, c onvenient for a variety of stepper motor operation, t o complete a variety of complex work. It represents the advanced industrial automation revolution; accelerate the realization of the electromechanical integration.浅析步进电机的PLC控制技术与发展趋势1、概述随着微电子技术和计算机技术的发展,可编程序控制器有一了突飞猛进的发展,其功能已远远超出了逻辑控制、顺序控制的范围,它与计算机有一效结合,可进行模拟最控制,具有一远程通信功能等。
单片机英文文献资料及翻译

单片机英文文献资料及翻译单片机(英文:Microcontroller)Microcontroller is a small computer on a single integrated circuit that contains a processor core, memory, and programmable input/output peripherals. Microcontrollers are designed for embedded applications, in contrast to the microprocessors used in personal computers or other general purpose applications.A microcontroller's processor core is typically a small, low-power computer dedicated to controlling the operation of the device in which it is embedded. It is often designed to provide efficient and reliable control of simple and repetitive tasks, such as switching on and off lights, or monitoring temperature or pressure sensors.MEMORYMicrocontrollers typically have a limited amount of memory, divided into program memory and data memory. The program memory is where the software that controls the device is stored, and is often a type of Read-Only Memory (ROM). The data memory, on the other hand, is used to store data that is used by the program, and is often volatile, meaning that it loses its contents when power is removed.INPUT/OUTPUTMicrocontrollers typically have a number of programmable input/output (I/O) pins that can be used to interface with external sensors, switches, actuators, and other devices. These pins can be programmed to perform specific functions,such as reading a sensor value, controlling a motor, or generating a signal. Many microcontrollers also support communication protocols like serial, parallel, and USB, allowing them to interface with other devices, including other microcontrollers, computers, and smartphones.APPLICATIONSMicrocontrollers are widely used in a variety of applications, including:- Home automation systems- Automotive electronics- Medical devices- Industrial control systems- Consumer electronics- RoboticsCONCLUSIONIn conclusion, microcontrollers are powerful and versatile devices that have become an essential component in many embedded systems. With their small size, low power consumption, and high level of integration, microcontrollers offer an effective and cost-efficient solution for controlling a wide range of devices and applications.。
基于单片机的步进电机电路控制设计英文文献及翻译

基于单片机的步进电机电路控制设计英文文献及翻译The Stepper motor control circuit be based on Singlechip microcomputerThe AT89C51 is a low-power, high-performance CMOS 8-bit microcomputer with 4K bytes of Flash programmable and erasable read only memory (PEROM). The device is manufactured using Atmel’s high-density nonvolatile memory technology and is compatible with the industry-standard MCS-51 instruction set and pinout. The on-chip Flash allows the program memory to be reprogrammed in-system or by a conventional nonvolatile memory programmer. By combining a versatile 8-bit CPU with Flash on a monolithic chip, the Atmel AT89C51 is a powerful microcomputer which provides a highly-flexible and cost-effective solution to many embedded control applications. Function characteristicThe AT89C51 provides the following standard features: 4K bytes of Flash, 128 bytes of RAM, 32 I/O lines, two 16-bit timer/counters, a five vector two-level interrupt architecture, a full duplex serial port, on-chip oscillator and clock circuitry. In addition, the AT89C51 is designed with static logic for operation down to zerofrequency and supports two software selectable power saving modes. The Idle Mode stops the CPU while allowing the RAM, timer/counters, serial port and interrupt system to continue functioning. The Power-down Mode saves the RAM contents but freezes the oscillator disabling all other chip functions until the next hardware reset.Pin DescriptionVCC:Supply voltage.GND:Ground.Port 0:Port 0 is an 8-bit open-drain bi-directional I/O port. As an output port, each pin can sink eight TTL inputs. When 1s are written to port 0 pins, the pins can be used as highimpedance inputs.Port 0 may also be configured to be the multiplexed loworder address/data bus during accesses to external program and data memory. In this mode P0 has internal pullups.Port 0 also receives the code bytes during Flash programming,and outputs the code bytes during programverification. External pullups are required during programverification.Port 1Port 1 is an 8-bit bi-directional I/O port withinternal pullups.The Port 1 output buffers can sink/source four TTL inputs.When 1s are written to Port 1 pins they are pulled high by the internal pullups and can be used as inputs. As inputs,Port 1 pins that are externally being pulled low will source current (IIL) because of the internal pullups.Port 1 also receives the low-order address bytes during Flash programming and verification.Port 2Port 2 is an 8-bit bi-directional I/O port with internal pullups.The Port 2 output buffers can sink/source four TTL inputs.When 1s are written to Port 2 pins they are pulled high by the internal pullups and can be used as inputs. As inputs,Port 2 pins that are externally being pulled low will source current, because of the internal pullups.Port 2 emits the high-order address byte during fetches from external program memory and during accesses to external data memory that use 16-bit addresses. In this application, it uses strong internal pullupswhen emitting 1s. During accesses to external data memory that use 8-bit addresses, Port 2 emits the contents of the P2 Special FunctionRegister.Port 2 also receives the high-order address bits and some control signals during Flash programming and verification.Port 3Port 3 is an 8-bit bi-directional I/O port with internal pullups.The Port 3 output buffers can sink/source four TTL inputs.When 1s are written to Port 3 pins they are pulled high by the internal pullups and can be used as inputs. As inputs,Port 3 pins that are externally being pulled low will source current (IIL) because of the pullups.Port 3 also serves the functions of various special features of the AT89C51 as listed below:Port 3 also receives some control signals for Flash programming and verification.RSTReset input. A high on this pin for two machine cycles while the oscillator is running resets the device. ALE/PROGAddress Latch Enable output pulse for latching the low byte of the address during accesses to external memory. This pin is also the program pulse input (PROG) during Flash programming.In normal operation ALE is emitted at a constant rate of 1/6 the oscillator frequency, and may be used for external timing or clocking purposes. Note, however, that one ALE pulse is skipped during each access to external Data Memory.If desired, ALE operation can be disabled by setting bit 0 of SFR location 8EH. With the bit set, ALE is active only during a MOVX or MOVC instruction. Otherwise, the pin is weakly pulled high. Setting the ALE-disable bit has no effect if the microcontroller is in external execution mode.PSENProgram Store Enable is the read strobe to external program memory.When the AT89C51 is executing code from。
步进电机概述论文翻译英文版
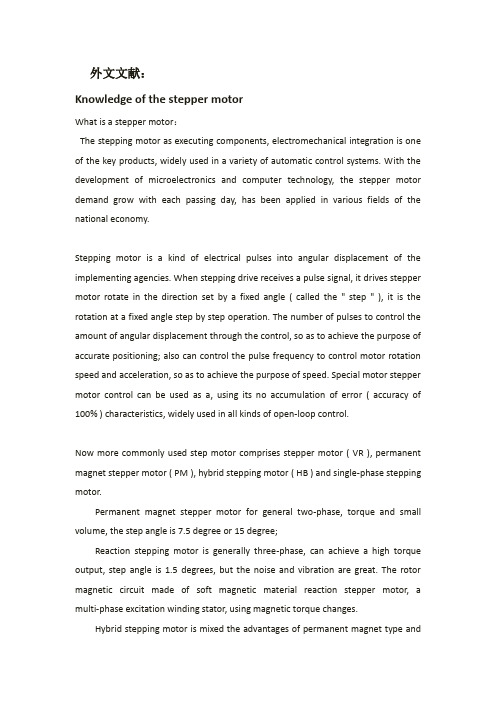
外文文献:Knowledge of the stepper motorWhat is a stepper motor:The stepping motor as executing components, electromechanical integration is one of the key products, widely used in a variety of automatic control systems. With the development of microelectronics and computer technology, the stepper motor demand grow with each passing day, has been applied in various fields of the national economy.Stepping motor is a kind of electrical pulses into angular displacement of the implementing agencies. When stepping drive receives a pulse signal, it drives stepper motor rotate in the direction set by a fixed angle ( called the " step " ), it is the rotation at a fixed angle step by step operation. The number of pulses to control the amount of angular displacement through the control, so as to achieve the purpose of accurate positioning; also can control the pulse frequency to control motor rotation speed and acceleration, so as to achieve the purpose of speed. Special motor stepper motor control can be used as a, using its no accumulation of error ( accuracy of 100% ) characteristics, widely used in all kinds of open-loop control.Now more commonly used step motor comprises stepper motor ( VR ), permanent magnet stepper motor ( PM ), hybrid stepping motor ( HB ) and single-phase stepping motor.Permanent magnet stepper motor for general two-phase, torque and small volume, the step angle is 7.5 degree or 15 degree;Reaction stepping motor is generally three-phase, can achieve a high torque output, step angle is 1.5 degrees, but the noise and vibration are great. The rotor magnetic circuit made of soft magnetic material reaction stepper motor, a multi-phase excitation winding stator, using magnetic torque changes.Hybrid stepping motor is mixed the advantages of permanent magnet type andreaction type. It is divided into two phase and five phase: two-phase stepper angle is 1.8 degree and five phase stepper angle is 0.72 degrees. Application of the stepping motor is the most widely, is also this subdivision driving of stepper motor selection scheme.Some of the basic parameters of step motor:The natural step motor:It says every hair a step pulse signal control system, motor rotation angle. Motor factory is a step angle values, such as type 86BYG250A motor is given a value of 0.9°/1.8 °( said a half step of work is 0.9 °, the whole step of work is 1.8 °), this step can be called ' motor fixed step ', it doesn't have to be the actual motor work when the real step angle, angle and drive the real steps.Stepper motor phase number:Is the number of coils inside the motor, commonly used in a two-phase, three-phase, four phase, five phase stepper motor. The number of motor phase is different, the step angle is also different, the general two-phase motor step angle is 0.9°/1.8 °, three-phase 0.75 °/1.5 °, five phase of 0.36 °/0.72 °. In the absence of subdivision drive, users mainly rely on different phases of the stepper motor to meet their own requirements of step angle. If you use a subdivision driver, is ' phase ' will become meaningless, users only need to change the fine fraction in the drive, you can change the step angle.Keep the torque ( HOLDINGTORQUE ):Is the stepper motor power but there is no rotation, the stator locked rotor torque. It is one of the most important parameters of step motor, usually stepper motor in the low-speed torque to keep the torque. Because of the larger output torque stepper motor with speed and continuous decay, increases the output power with the speed of change, so keep the torque becomes one of the most important parameters of step motor. For example, when people say 2N.m stepper motor, in the absence of exceptional circumstances described in that refers to keep the torquemotor for the 2N.m step.DETENTTORQUE:DETENTTORQUE:Refers to the stepper motor is not energized condition, the stator locked rotor torque. DETENTTORQUE does not have a unified way of translation in China, easy to make people misunderstand; as the rotor reaction stepper motor is not permanent magnetic material, so it has no DETENTTORQUE.Some of the characteristic of step motor:The 1 stepper motor step angle accuracy for 3-5%, and no accumulation.2 stepper motor appearance allows the maximum temperature.Stepper motor temperature is too high will first make the motor magnetic material demagnetization, resulting in lower torque and loss, so the highest temperature of motor appearance allows should depend on the different motor demagnetization magnetic materials; generally speaking, demagnetization point magnetic material in 130 degrees Celsius above, some even as high as 200 degrees Celsius stepping motor, so the surface temperature at 80-90 degrees Celsius completely normal.3 stepper motor torque will decrease with the increase of rotational speed.When the stepper motor rotates, the electrical inductance of the winding will form a reverse electromotive force; the higher the frequency, the greater the reverse emf. Under the influence of it, the motor with frequency ( or speed ) increase and the phase current is reduced, resulting in lower torque.4 stepper motor speed can be normal operation, but if it is more than a certain speed will not start, and accompanied by howling.Stepper motor is a technical parameter: no-load start frequency, namely the stepper motor under no-load condition can pulse frequency start, if the pulsefrequency is higher than the value, the motor can not start properly, may have lost step or stall. In under the condition of the load, start frequency should be less. If you want to enable the motor to rotate at high speed, pulse frequency should accelerate the process is started, the lower frequency, and then according to certain acceleration up to high frequency desired ( motor speed from low speed to high speed ).Characteristics of stepper motor with its significant, play an important purpose in the era of digital manufacturing. With the different development of digital technology and stepper motor itself technology improves, the stepper motor will be applied in more fields.How to determine the stepper motor driver DC power supply:A. Determination of the voltageHybrid stepping motor driver power supply voltage is generally a wide range (such as the IM483 supply voltage of 12 ~ 48VDC), the supply voltage is usually based on the work of the motor speed and response to the request to choose. If the motor operating speed higher or faster response to the request, then the voltage value is high, but note that the ripple voltage can not exceed the maximum input voltage of the drive, or it may damage the drive.B. Determination of CurrentPower supply current is generally based on the output phase current drive I to determine. If a linear power supply, power supply current is generally preferable 1.1 to 1.3 times the I; if we adopt the switching power supply, power supply current is generally preferable to I, 1.5 to 2.0 times.The main characteristics of stepping motor:A stepper motor drive can be added operate pulse drive signal must be no pulse when the stepper motor at rest, such asIf adding the appropriate pulse signal, it will to a certain angle (called the step angle) rotation. Rotation speed and pulse frequency is proportional to.2 Dragon step angle stepper motor version is 7.5 degrees, 360 degrees around,takes 48 pulses to complete.3 stepper motor has instant start and rapid cessation of superior characteristics. Change the pulse of the order of 4, you can easily change the direction of rotation. Therefore, the current printers, plotters, robotics, and so devices are the core of the stepper motor as the driving force.Stepper motor control exampleWe use four-phase unipolar stepper motor as an example. The structure shown in Figure 1:Four four-phase winding leads (as opposed to phase A1 A2 B1 phase phase B2) and two public lines (to the power of positive). The windings of one phase to the power of the ground. So that the windings will be inspired. We use four-phase eight-beat control, ie, 1 phase 2 phase alternating turn, would enhance resolution.0.9 °per step can be transferred to control the motor excitation is transferred in order as follows:If the requirements of motor reversal, the transmission excitation signal can be reversed. 2 control schemeControl system block diagram is as followsThe program uses AT89S51 as the main control device. It is compatible with the AT89C51, but also increased the SPI interface and the watchdog module, which not only makes the debugging process becomes easy and also more stable. The microcontroller in the program mainly for field signal acquisition and operation of the stepper motor to calculate the direction and speed information. Then sent to the CPLD.CPLD with EPM7128SLC84-15, EPM7128 programmable logic device of large-scale, for the ALTERA company's MAX7000 family. High impedance, electrically erasable and other characteristics, can be used for the 2500 unit, the working voltage of +5 V. CPLD receives information sent from the microcontroller after converted to the corresponding control signal output to the stepper motor drive. Put the control signal drives the motor windings after the input, to achieve effective control of the motor.2.1 The hardware structure of the motor driveMotor drive using the following circuit:R1-R8 in which the resistance value of 320Ω. R9-R12 resistance value 2.2KΩ. Q1-Q4 as Darlington D401A, Q5-Q8 for the S8550. J1, J2 and the stepper motor connected to the six-lead。
单片机的外文文献及中文翻译

SCM is an integrated circuit chip,is the use of large scale integrated circuit technology to a data processing capability of CPU CPU random access memory RAM,read—only memory ROM,a variety of I / O port and interrupt system, timers / timer functions (which may also include display driver circuitry,pulse width modulation circuit,analog multiplexer, A / D converter circuit) integrated into a silicon constitute a small and complete computer systems。
SCM is also known as micro—controller (Microcontroller),because it is the first to be used in industrial control. Only a single chip by the CPU chip developed from a dedicated processor。
The first design is by a large number of peripherals and CPU on a chip in the computer system,smaller, more easily integrated into a complex and demanding on the volume control device which. The Z80 INTEL is the first designed in accordance with this idea processor, then on the development of microcontroller and dedicated processors will be parting ways。
单片机控制步进电机外文文献翻译

单片机控制步进电机外文原文Stepping motor application and control stepper motor is an electrical pulse will be converted into angular displacement of the implementing agencies. Put it in simple language-speaking: When the stepper drive pulse signal to a receiver, it drives stepper motor rotation direction by setting a fixed point of view (and the step angle). You can control the number of pulses to control the amount of angular displacement, so as to achieve the purpose of accurate positioning; At the same time, you can by controlling the pulse frequency to control the motor rotation speed and acceleration,so as to achieve the purpose of speed.Stepper motor directly from the AC-DC power supply,and must use special equipment - stepper motor drive. Stepper motor drive system performance, in addition to their own performance with the motor on the outside, but also to a large extent depend on the drive is good or bad. A typical stepper motor drive system is operated by the stepper motor controller, stepper motor drives and stepper motor body is composed of three parts. Stepper motor controller stepper pulse and direction signal, each made of a pulse, stepper motor-driven stepper motor drives a rotor rotating step angle, that is, step-by-step further. High or low speed stepper motor, or speed, or deceleration, start or stop pulses are entirely dependent on whether the level or frequency.Decide the direction of the signal controller stepper motor clockwise or counterclockwise rotation. Typically, the stepper motor drive circuit from the logic control, power driver circuit, protection circuit and power components.Stepper motor drive controller, once received from the direction of the signal and step pulse, the control circuit on a pre-determined way of the electrical power-phase stepper motor excitation windings of the conduction or cut-off signal. Control circuit output signal power is low,can not provide the necessary stepping motor output power, the need for power amplifier, which is stepper motor driven power drive part. Power stepper motor drive circuit to control the input current winding to form a space for rotating magnetic field excitation, the rotor-driven movement.Protection circuit in the event of shortcircuit, overload, overheating, such as failure to stop the rapid drive and motor. Motor is usually for the permanent magnet rotor, when the current flows throughthe stator windings, the stator windings produce a magnetic field vector.The magnetic field will lead to a rotor angle of rotation, making a pair of rotor and stator magnetic field direction of the magnetic field direction. When the stator rotating magnetic field vector from a different angle. Also as the rotor magnetic field to a point of view. An electrical pulse for each input, the motor rotation angle step. Its output and input of the angular displacement is proportional to the pulses, with pulse frequency proportional to speed. Power to change the order of winding,the electrical will be reversed. We can, therefore, control the pulse number, frequency and electrical power windings of each phase to control the order of rotation of stepper motor.Stepper motor types:Permanent magnet (PM). Magnetic generally two-phase stepper, torque and are smaller and generally stepping angle of 7.5 degrees or 15 degrees; put more wind for air-conditioning.Reactive(VR), the domestic general called BF, have a common three-phase reaction, step angle of 1.5 degrees; also have five-phase reaction. Noise, no torque has been set at a large number of out.Hybrid (HB), common two-phase hybrid, five-phase hybrid, three-phase hybrid, four-phase hybrid, two-phase can be common with the four-phase drive, five-phase three-phase must be used with their drives;Two-phase, four-phase hybrid step angle is 1.8 degrees more than a small size, great distance,and low noise;Five-phase hybrid stepping motor is generally 0.72, the motor step angle small, high resolution, but the complexity of drive circuits, wiring problems, such as the 5- phase system of 10 lines.Three-phase hybrid stepping motor step angle of 1.2 degrees, but according to the use of 1.8 degrees, the three-phase hybrid stepping motor has a two-phase mixed than the five-phase hybrid more pole will help electric folder symmetric angle, it can be more than two-phase, five-phase high accuracy, the error even smaller, run moresmoothly.Stepper motor to maintain torque: stepper motor power means no rotation, the stator locked rotor torque. It is a stepper motor, one of the most important parameters, usually in the low-speed stepper motor torque at the time of close to maintain the torque. As the stepper motor output torque increases with the speed of constant attenuation, the output power also increases with the speed of change,so as to maintain torque on the stepper motor to measure the parameters of one of the most important. For example, when people say that the stepper motor 2N.m, in the absence of special circumstances that means for maintaining the torque of the stepper motor 2N.m.Precision stepper motors:stepper motor step angle accuracy of 3-5%, not cumulative.Stepper motor to allow the minimum amount of surface temperature:Stepper motor causes the motor temperature is too high the first magnetic demagnetization, resulting in loss of torque down even further, so the motor surface temperature should be the maximum allowed depending on the motor demagnetization of magnetic material points; Generally speaking,the magnetic demagnetization points are above 130 degrees Celsius, and some even as high as 200 degrees Celsius, so the stepper motor surface temperature of 80-90 degrees Celsius is normal.Start frequency of no-load: the stepper motor in case of no-load to the normal start of the pulse frequency, if the pulse frequency is higher than the value of motor does not start, possible to lose steps or blocking.In the case of the load, start frequency should be lower. If you want to achieve high-speed rotation motor, pulse frequency should be to accelerate the process, that is, the lower frequency to start, and then rose to a certain acceleration of the desired frequency (motor speed from low rise to high-speed).Step angle:that is to send a pulse,the electrical angle corresponding to rotation.Torque positioning: positioning torque stepper motor does not refer to the case of electricity,locked rotor torque stator.Operating frequency:step-by-step stepper motor can run without losing thehighest frequency.Subdivision Drive: stepper motor drives the main aim is to weaken or eliminate low-frequency vibration of the stepper motor to improve the accuracy of the motor running. Reduce noise. If the step angle is 1.8 °(full step) the two-phase hybrid stepping motor, if the breakdown of the breakdown of the number of drives for the 8, then the operation of the electrical pulse for each resolution of 0.072 °, the precision of motor can reach or close to 0.225 °, also depends on the breakdown of the breakdown of the drive current control accuracy and other factors, the breakdown of the number of the more difficult the greater the precision of control.How to determine the stepper motor driver DC power supply:A.Determination of the voltage: Hybrid stepping motor driver power supply voltage is generally a wide range (such as the IM483 supply voltage of 12 ~ 48VDC), the supply voltage is usually based on the work of the motor speed and response to the request to choose.If the motor operating speed higher or faster response to the request, then the voltage value is high, but note that the ripple voltage can not exceed the maximum input voltage of the drive,or it may damage the drive.B.Determination of CurrentPower supply current is generally based on the output phase current drive I to determine. If a linear power supply, power supply current is generally preferable 1.1 to 1.3 times the I; if we adopt the switching power supply, power supply current is generally preferable to I,1.5to 2.0 times.The main characteristics of stepping motor:1. A stepper motor drive can be added operate pulse drive signal must be no pulse when the stepper motor at rest, such as If adding the appropriate pulse signal, it will to a certain angle (called the step angle) rotation. Rotation speed and pulse frequency is proportional to.2.permanent magnet step angle stepper motor version is 7.5 degrees, 360 degrees around, takes48 pulses to complete.3.stepper motor has instant start and rapid cessation of superior characteristics. Change the order of the pulse4.you can easily change the direction of rotation.Therefore, the current printers, plotters, robotics, and so devices are the core of the stepper motor as the driving force.Stepper motors have the following benefits: (1)Low cost (2)Ruggedness (3)Simplicity in construction (4)High reliability(5)No maintenance(6)Wide acceptance(7)No tweaking to stabilize (8)No feedback components are neededThey work in just about any environment Inherently more failsafe than servo motors. There isvirtually no conceivable failure within the stepper drive module that could cause the motor to run away. Stepper motors are simple to drive and control in an open-loop configuration. They only require four leads. They provide excellent torque at low speeds, up to 5 times the continuous torque of a brush motor of the same frame size or double the torque of the equivalent brushless motor. This often eliminates the need for a gearbox. A stepper-driven-system is inherently stiff, with known limits to the dynamic position error.Stepper Motor Disadvantages:Stepper motors have the following disadvantages:1.Resonance effects and relatively long settling times.1.Rough performance at low speed unless a microstep drive is used.2.Liability to undetected position loss as a result of operating open-loop .4.They consume current regardless of load conditions and therefore tend to run hot5.Losses at speed are relatively high and can cause excessive heating, and they are frequently noisy (especially at high speeds).1.They can exhibit lag-lead oscillation, which is difficult to damp.There is a limit to their available size, and positioning accuracy relies on the mechanics(e.g., ballscrew accuracy).Many of these drawbacks can be overcome by the use of a closed-loop control scheme.外文资料翻译译文步进电机应用和控制步进电机是将电脉冲转换成角位移的执行机构。
基于单片机的步进电机电路控制设计英文文献与翻译

The Stepper motor control circuit be based on Single chipmicrocomputerThe AT89C51 is a low-power, high-performance CMOS 8-bit microcomputer with 4K bytes of Flash programmable and erasable read only memory (PEROM). The device is manufactured using Atmel’s high-density nonvolatile memory technology and is compatible with the industry-standard MCS-51 instruction set and pinout. The on-chip Flash allows the program memory to be reprogrammed in-system or by a conventional nonvolatile memory programmer. By combining a versatile 8-bit CPU with Flash on a monolithic chip, the Atmel AT89C51 is a powerful microcomputer which provides a highly-flexible and cost-effective solution to many embedded control applications.Function characteristicThe AT89C51 provides the following standard features: 4K bytes of Flash, 128 bytes of RAM, 32 I/O lines, two 16-bit timer/counters, a five vector two-level interrupt architecture, a full duplex serial port, on-chip oscillator and clock circuitry. In addition, the AT89C51 is designed with static logic for operation down to zero frequency and supports two software selectable power saving modes. The Idle Mode stops the CPU while allowing the RAM, timer/counters, serial port and interrupt system to continue functioning. The Power-down Mode saves the RAM contents but freezes the oscillator disabling all other chip functions until the next hardware reset.Pin DescriptionVCC:Supply voltage.GND:Ground.Port 0:Port 0 is an 8-bit open-drain bi-directional I/O port. As an output port, each pin can sink eight TTL inputs. When 1s are written to port 0 pins, the pins can be used as highimpedance inputs.Port 0 may also be configured to be the multiplexed loworder address/data bus during accesses to external program and data memory. In this mode P0 has internal pullups.Port 0 also receives the code bytes during Flashprogramming,and outputs the code bytes during programverification. External pullups are required during programverification.Port 1Port 1 is an 8-bit bi-directional I/O port with internal pullups.The Port 1 output buffers can sink/source four TTL inputs.When 1s are written to Port 1 pins they are pulled high by the internal pullups and can be used as inputs. As inputs,Port 1 pins that are externally being pulled low will source current (IIL) because of the internal pullups.Port 1 also receives the low-order address bytes during Flash programming and verification.Port 2Port 2 is an 8-bit bi-directional I/O port with internal pullups.The Port 2 output buffers can sink/source four TTL inputs.When 1s are written to Port 2 pins they are pulled high by the internal pullups and can be used as inputs. As inputs,Port 2 pins that are externally being pulled low will source current, because of the internal pullups.Port 2 emits the high-order address byte during fetches from external program memory and during accesses to external data memory that use 16-bit addresses. In this application, it uses strong internal pullupswhen emitting 1s. During accesses to external data memory that use 8-bit addresses, Port 2 emits the contents of the P2 Special Function Register.Port 2 also receives the high-order address bits and some control signals during Flash programming and verification.Port 3Port 3 is an 8-bit bi-directional I/O port with internal pullups.The Port 3 output buffers can sink/source four TTL inputs.When 1s are written to Port 3 pins they are pulled high by the internal pullups and can be used as inputs. As inputs,Port 3 pins that are externally being pulled low will source current (IIL) because of the pullups.Port 3 also serves the functions of various special features of the AT89C51 as listed below:Port 3 also receives some control signals for Flash programming and verification.RSTReset input. A high on this pin for two machine cycles while the oscillator is running resets the device.ALE/PROGAddress Latch Enable output pulse for latching the low byte of the address during accesses to external memory. This pin is also the program pulse input (PROG) during Flash programming.In normal operation ALE is emitted at a constant rate of 1/6 the oscillator frequency, and may be used for external timing or clocking purposes. Note, however, that one ALE pulse is skipped during each access to external Data Memory. If desired, ALE operation can be disabled by setting bit 0 of SFR location 8EH. With the bit set, ALE is active only during a MOVX or MOVC instruction. Otherwise, the pin is weakly pulled high. Setting the ALE-disable bit has no effect if the microcontroller is in external execution mode.PSENProgram Store Enable is the read strobe to external program memory.When the AT89C51 is executing code from external program memory, PSEN is activated twice each machine cycle, except that two PSEN activations are skipped during each access to external data memory.EA/VPPExternal Access Enable. EA must be strapped to GND in order to enable the device to fetch code from external program memory locations starting at 0000H up to FFFFH. Note, however, that if lock bit 1 is programmed, EA will be internally latched on reset.EA should be strapped to VCC for internal program executions.This pin also receives the 12-volt programming enable voltage(VPP) during Flash programming, for parts that require12-volt VPP.XTAL1Input to the inverting oscillator amplifier and input to the internal clock operating circuit.XTAL2Output from the inverting oscillator amplifier.Oscillator CharacteristicsXTAL1 and XTAL2 are the input and output, respectively,of an inverting amplifier which can be configured for use as an on-chip oscillator, as shown in Figure 1.Either a quartz crystal or ceramic resonator may be used. To drive the device from an external clock source, XTAL2 should be left unconnected while XTAL1 is driven as shown in Figure 2.There are no requirements on the duty cycle of the external clock signal, since the input to the internal clocking circuitry is through a divide-by-two flip-flop, but minimum and maximum voltage high and low time specifications must be observed.Figure 1. Oscillator Connections Figure 2. External Clock Drive ConfigurationIdle ModeIn idle mode, the CPU puts itself to sleep while all the onchip peripherals remain active. The mode is invoked by software. The content of the on-chip RAM and all the special functions registers remain unchanged during this mode. The idle mode can be terminated by any enabled interrupt or by a hardware reset.It should be noted that when idle is terminated by a hard ware reset, the device normally resumes program execution,from where it left off, up to two machine cycles before the internal reset algorithm takes control. On-chip hardware inhibits access to internal RAM in this event, but access to the port pins is not inhibited. To eliminate the possibility of an unexpected write to a port pin when Idle is terminated by reset, the instruction following the one that invokes Idle should not be one that writes to a port pin or to external memory.Power-down ModeIn the power-down mode, the oscillator is stopped, and the instruction that invokes power-down is the last instruction executed. The on-chip RAM and Special Function Registers retain their values until the power-down mode is terminated. The only exit from power-down is a hardware reset. Reset redefines the SFRs but does not change the on-chip RAM. The reset should not be activated before VCC is restored to its normal operating level and must be held active long enough to allow the oscillator to restart and stabilize.Program Memory Lock BitsOn the chip are three lock bits which can be left unprogrammed (U) or can be programmed (P) to obtain the additional features listed in the table below.When lock bit 1 is programmed, the logic level at the EA pin is sampled and latched during reset. If the device is powered up without a reset, the latch initializes to a random value, and holds that value until reset is activated. It is necessary that the latched value of EA be in agreement with the current logic level at that pin in order for the device to function properly.IntroductionStepper motors are electromagnetic incremental-motion devices which convertdigital pulse inputs to analog angle outputs. Their inherent stepping ability allows for accurate position control without feedback. That is, they can track any step position in open-loop mode, consequently no feedback is needed to implement position control. Stepper motors deliver higher peak torque per unit weight than DC motors; in addition, they are brushless machines and therefore require less maintenance. All of these properties have made stepper motors a very attractive selection in many position and speed control systems, such as in computer hard disk drivers and printers, XY-tables, robot manipulators, etc.Although stepper motors have many salient properties, they suffer from an oscillation or unstable phenomenon. This phenomenon severely restricts their open-loop dynamic performance and applicable area where high speed operation is needed. The oscillation usually occurs at stepping rates lower than 1000 pulse/s, and has been recognized as a mid-frequency instability or local instability [1], or a dynamic instability [2]. In addition, there is another kind of unstable phenomenon in stepper motors, that is, the motors usually lose synchronism at higher stepping rates, even though load torque is less than their pull-out torque. This phenomenon is identified as high-frequency instability in this paper, because it appears at much higher frequencies than the frequencies at which the mid-frequency oscillation occurs. The high-frequency instability has not been recognized as widely as mid-frequency instability, and there is not yet a method to evaluate it.Mid-frequency oscillation has been recognized widely for a very long time, however, a complete understanding of it has not been well established. This can be attributed to the nonlinearity that dominates the oscillation phenomenon and is quite difficult to deal with.384 L. Cao and H. M. SchwartzMost researchers have analyzed it based on a linearized model [1]. Although in many cases, this kind of treatments is valid or useful, a treatment based on nonlinear theory is needed in order to give a better description on this complex phenomenon. For example, based on a linearized model one can only see that the motors turn to be locally unstable at some supplyfrequencies, which does not give much insight into the observed oscillatory phenomenon. In fact, the oscillation cannot be assessed unless one uses nonlinear theory.Therefore, it is significant to use developed mathematical theory on nonlinear dynamics to handle the oscillation or instability. It is worth noting that Taft and Gauthier [3], and Taft and Harned [4] used mathematical concepts such as limit cycles and separatrices in the analysis of oscillatory and unstable phenomena, and obtained some very instructive insights into the socalled loss of synchronous phenomenon. Nevertheless, there is still a lack of a comprehensive mathematical analysis in this kind of studies. In this paper a novel mathematical analysis is developed to analyze the oscillations and instability in stepper motors.The first part of this paper discusses the stability analysis of stepper motors. It is shown that the mid-frequency oscillation can be characterized as a bifurcation phenomenon (Hopf bifurcation) of nonlinear systems. One of contributions of this paper is to relate the midfrequency oscillation to Hopf bifurcation, thereby, the existence of the oscillation is provedtheoretically by Hopf theory. High-frequency instability is also discussed in detail, and a novel quantity is introduced to evaluate high-frequency stability. This quantity is very easyto calculate, and can be used as a criteria to predict the onset of the high-frequency instability. Experimental results on a real motor show the efficiency of this analytical tool.The second part of this paper discusses stabilizing control of stepper motors through feedback. Several authors have shown that by modulating the supply frequency [5], the midfrequencyinstability can be improved. In particular, Pickup and Russell [6, 7] have presented a detailed analysis on the frequency modulation method. In their analysis, Jacobi series was used to solve a ordinary differential equation, and a set of nonlinear algebraic equations had to be solved numerically. In addition, their analysis is undertaken for a two-phase motor, and therefore, their conclusions cannot applied directly to oursituation, where a three-phase motor will be considered. Here, we give a more elegant analysis for stabilizing stepper motors, where no complex mathematical manipulation is needed. In this analysis, a d–q model of stepper motors is used. Because two-phase motors and three-phase motors have the same q–d model and therefore, the analysis is valid for both two-phase and three-phase motors. Up to date, it is only recognized that the modulation method is needed to suppress the midfrequency oscillation. In this paper, it is shown that this method is not only valid to improve mid-frequency stability, but also effective to improve high-frequency stability.2. Dynamic Model of Stepper MotorsThe stepper motor considered in this paper consists of a salient stator with two-phase or threephase windings, and a permanent-magnet rotor. A simplified schematic of a three-phase motor with one pole-pair is shown in Figure 1. The stepper motor is usually fed by a voltage-source inverter, which is controlled by a sequence of pulses and produces square-wave voltages. Thismotor operates essentially on the same principle as that of synchronous motors. One of major operating manner for stepper motors is that supplying voltage is kept constant and frequencyof pulses is changed at a very wide range. Under this operating condition, oscillation and instability problems usually arise.Figure 1. Schematic model of a three-phase stepper motorA mathematical model for a three-phase stepper motor is established using q–d framereference transformation. The voltage equations for three-phase windings are given byv a = Ri a + L*di a /dt − M*di b/dt − M*di c/dt + dλpma/dt ,v b = Ri b + L*di b/dt − M*di a/dt − M*di c/dt + dλpmb/dt ,v c = Ri c + L*di c/dt − M*di a/dt − M*di b/dt + dλpmc/dt ,where R and L are the resistance and inductance of the phase windings, and M is the mutual inductance between the phase windings. _pm a, _pm b and _pm c are the flux-linkages of thephases due to the permanent magnet, and can be assumed to be sinusoid functions of rotor position _ as followλpma = λ1 sin(Nθ),λpmb = λ1 sin(Nθ − 2 π/3),λpmc = λ1 sin(Nθ - 2 π/3),where N is number of rotor teeth. The nonlinearity emphasized in this paper is represented by the above equations, that is, the flux-linkages are nonlinear functions of the rotor position.By using the q; d transformation, the frame of reference is changed from the fixed phase axes to the axes moving with the rotor (refer to Figure 2). Transformation matrix from the a; b; c frame to the q; d frame is given by [8]For example, voltages in the q; d reference are given byIn the a; b; c reference, only two variables are independent (ia C ib C ic D 0); therefore, the above transformation from three variables to two variables is allowable. Applying the abovetransformation to the voltage equations (1), the transferred voltage equation in the q; d frame can be obtained asv q = Ri q + L1*di q/dt + NL1i dω + Nλ1ω,v d=Ri d + L1*di d/dt − NL1i qω, (5)Figure 2. a, b, c and d, q reference framewhere L1 D L C M, and ! is the speed of the rotor.It can be shown that the motor’s torque has the following form [2]T = 3/2Nλ1i qThe equation of motion of the rotor is written asJ*dω/dt = 3/2*Nλ1i q − B fω – Tl ,where Bf is the coefficient of viscous friction, and Tl represents load torque, which is assumed to be a constant in this paper.In order to constitute the complete state equation of the motor, we need another state variable that represents the position of the rotor. For this purpose the so called load angle _ [8] is usually used, which satisfies the following equationDδ/dt = ω−ω0 ,where !0 is steady-state speed of the motor. Equations (5), (7), and (8) constitute the statespace model of the motor, for which the input variables are the voltages vq and vd. As mentioned before, stepper motors are fed by an inverter, whose output voltages are not sinusoidal but instead are square waves. However, because the non-sinusoidal voltages do not change the oscillation feature and instability very much if compared to the sinusoidal case (as will be shown in Section 3, the oscillation is due to the nonlinearity of the motor), for the purposes of this paper we can assume the supply voltages are sinusoidal. Under this assumption, we can get vq and vd as followsv q = V m cos(Nδ) ,v d = V m sin(Nδ) ,where Vm is the maximum of the sine wave. With the above equation, we have changed the input voltages from a function of time to a function of state, and in this way we can represent the dynamics of the motor by a autonomous system, as shown below. This will simplify the mathematical analysis.From Equations (5), (7), and (8), the state-space model of the motor can be written in a matrix form as followsẊ = F(X,u) = AX + Fn(X) + Bu , (10) where X D T iq id ! _U T , u D T!1 Tl U T is defined as the input, and !1 D N!0 is the supply frequency. The input matrix B is defined byThe matrix A is the linear part of F._/, and is given byFn.X/ represents the nonlinear part of F._/, and is given byThe input term u is independent of time, and therefore Equation (10) is autonomous.There are three parameters in F.X;u/, they are the supply frequency !1, the supply voltage magnitude Vm and the load torque Tl . These parameters govern the behaviour of the stepper motor. In practice, stepper motors are usually driven in such a way that the supply frequency !1 is changed by the command pulse to control the motor’s speed, while the supply voltage is kept constant. Therefore, we shall investigate the effect of parameter !1.3. Bifurcation and Mid-Frequency OscillationBy setting ! D !0, the equilibria of Equation (10) are given asand ' is its phase angle defined byφ = arctan(ω1L1/R) . (16)Equations (12) and (13) indicate that multiple equilibria exist, which means that these equilibria can never be globally stable. One can see that there are two groups of equilibria as shown in Equations (12) and (13). The first group represented by Equation (12) corresponds to the real operatingconditions of the motor. The second group represented by Equation (13) is always unstable and does not relate to the real operating conditions. In the following, we will concentrate on the equilibria represented by Equation (12).基于单片机的步进电机电路控制设计89C51是一种带4K字节闪烁可编程可擦除只读存储器(FPEROM—Falsh Programmable and Erasable Read Only Memory)的低电压、高性能CMOS8位微处理器,俗称单片机。
单片机步进电机控制器设计文献翻译

毕业设计说明书The Use of Stepper Motor步进电机的应用学生姓名: 学号: 学 院: 系 名:专 业:指导教师:年 月(小二号居中)三号楷体 三号楷体 信息商务学院 三号楷体 只写名字,三号楷体 三号楷体The use of stepper motorStepper motor is the electric pulse signals into angular displacement or linear displacement of the open-loop stepper motor control element pieces. In the case of non-overloaded, the motor speed, stop position depends only on the pulse frequency and pulse number, regardless of load changes, when the driver receives a step pulse signal, it will drive a stepper motor to Set the direction of rotation of a fixed angle, called the "step angle", which the angle of rotation is fixed step by step operation. Number of pulses can be controlled by controlling the angular displacement, so as to achieve accurate positioning purposes; the same time by controlling the pulse frequency to control the motor rotation speed and acceleration, to achieve speed control purposes.Work:Induction motor is a stepper motor, does it work is the use of electronic circuits, the DC power supply into a time-sharing, multi-phase timing control current, this current stepper motor power supply, the stepper motor to work properly , The drive is sharing power supply for the stepper motor, the polyphase timing controllerAlthough the stepper motor has been widely used, but the stepper motor does not like a normal DC motor, AC motor in the conventional use. It must be double-ring pulse signal, power driver circuit composed of the control system can be used. Therefore, it is not easy with a good stepping motor, which involves mechanical, electrical, electronics and computers, and many other specialized knowledge.As the stepper motor actuators, electromechanical integration, one of the key products, widely used in a variety of automatic control systems. With the development of microelectronics and computer technology, increasing demand for stepper motor, has applications in all areas of the national economy.Categories:Now more commonly used include the reaction of step motor stepper motor (VR), permanent magnet stepper motor (PM), hybrid stepper motors (HB) and single-phase stepper motor.Permanent magnet stepper motorPermanent magnet stepper motor is generally two-phase, torque, and smaller, usually 7.5 degree step angle or 15 degrees;Permanent magnet stepper motor output torque, dynamic performance, but a large step angle:Reaction Stepper MotorReaction is generally three-phase stepping motor can achieve high torque output, step angle of 1.5 degrees is generally, but the noise and vibration are large. Reaction by the stepper motor rotor magnetic circuit made of soft magnetic materials, a number of the stator phase excitation winding, the use of permeability changes in torque. Step Motor simple structure, low production costs, step angle is small; but the dynamic performance is poor.Hybrid Stepping MotorHybrid Step Motor combines reactive, permanent magnet stepper motors of both, it's a small step angle, contribute a large, dynamic performance, is currently the highest performance stepper motor. It is also sometimes referred to as Permanent Magnet Induction Stepping Motor. It consists of two phases and the five-phase: the general two-phase step angle of 1.8 degrees and the general five-phase step angle 0.72 degrees. The most widely used Stepper Motor.Stepper motor drive for energy savingThree-phase stepper motor drive special features:■ 180% low torque output, low frequency characteristics of a good run■ Maximum output frequency 600Hz, high-speed motor control■ full range of detection of protection (over voltage, under voltage, overload) instantaneous power failure restart■ acceleration, deceleration, such as dynamic change in the stall protection function to prevent■ Electrical dynamic parameters of automatic recognition function to ensure stability and accuracy of the system■ quick response and high-speed shutdown■ abundant and flexible input and output interface and control, versatility■ use of SMT produc tion and three full-mount anti-paint treatment process, product stability and high■ full range of Siemens IGBT power devices using the latest, to ensure the quality of high-qualityBasic principlesUsually for the permanent magnet rotor motor, when current flows through the statorwindings, the stator windings produce a magnetic field vector. The magnetic field will lead to a rotor angle of the magnetic field makes the direction of a rotor and the stator's magnetic field direction. When the stator magnetic field vector rotating at an angle. As the rotor magnetic field is also transferred from another perspective. An electrical pulse for each input, the motor turning a point forward. It is the angular displacement of the output and input the number of pulses proportional to speed and pulse frequency is proportional to. Power to change the order of winding, the motor will reverse. Therefore, the number of available control pulse, frequency and power the motor windings of each phase in order to control the stepper motor rotation. Reaction Stepper MotorAs the response to stepping motor works is relatively simple. The following describes the first principle of three-phase stepping motor response.1, the structure: uniformly distributed rotor with many small teeth, the stator excitation windings of three teeth, the geometric axis of the rotor tooth axis in order were staggered. 0,1 / 3 て, 2 / 3 て, (adjacent to the two axes of the rotor tooth pitch distance between the てsaid), that is, with the teeth a relatively homogeneous A, B and staggered tooth 2 to the right 1 / 3 て, C and the right to stagger tooth 3 2 / 3 て, A 'and the tooth 5 is relatively homogeneous, (A' is A, is the gear teeth 5 1) The following is the rotor's expansion plan:2, rotation: If the A-phase power, B, C phase is not energized, the magnetic field, alignment of teeth 1 and A, (without any power of the rotor are the same the following). Such as the B-phase power, A, C phase is not energized, gear 2, and B should be aligned, when the rotor over to the right 1 / 3 て, this time offset teeth 3 and C 1 / 3 て, teeth 4 and A shift (て-1 / 3 te) = 2 / 3 て. Such as the C-phase power, A, B phase is not energized, gear 3, and C should be aligned, this time right off the rotor Youxiang 1 / 3 て, 4 and A gear shift time is 1 / 3 てalignment. Such as the A-phase power, B, C phase is not energized, 4 and A-aligned teeth, the rotor Youxiang right over 1 / 3 てso after A, B, C, A are energized, gear 4 (ie, the previous tooth 1 teeth) to the A-phase, rotor to the right around a pitch, if you continue to press the A, B, C, A ... ... power, the motor for each step (per pulse) 1 / 3 て, Rotate Right. Such as by A, C, B, A ... ... power, the motor to reverse. This shows that: the location and speed of motor conduction times by the (number of pulses) and frequency into one relationship. The direction determined by the conductivity of the order. However, out of torque, smooth, noise and reduce the angle considerations. Often withA-AB-B-BC-C-CA-A this conductive state, so that each step the original 1 / 3 てchanged to 1 / 6 て. Even through different combinations of two-phase current, so 1 / 3 てinto 1 / 12 て, 1 / 24, te, which is the basic theory of the motor-driven basis for subdivision. Easily introduced: m phase on the stator excitation windings, the axis of the rotor tooth axis were offset 1 / m, 2 / m ... ... (m-1) / m, 1. And conductivity at a certain phase sequence reversing motor can be controlled - this is the rotation of the physical conditions. As long as we meet this condition can theoretically create any phase stepper motor, because of cost, and many other considerations, the market generally two, three, four, five-phase is more.3, the torque: the motor once energized, will produce between the stator and rotor magnetic field (magnetic flux Ф) when the rotor and stator stagger angle to produce force F and (dФ / dθ) is proportional to S the magnetic flux Ф = Br * S Br for the flux density, F and S for the magnetic area of L * D * Br core is proportional to L, effective length, D is rot or diameter Br = N • I / RN • I was excited winding ampere turns (current x turns) R for the magnetic resistance. Torque = force * radius of the torque and the motor turns the effective volume * An * is proportional to the flux density (only consider the linear state), therefore, the greater the effective volume of the motor, the greater the excitation ampere turns, the smaller air gap between stator and rotor, the motor torque, and vice versa.Induction Stepping Motor1,features: Induction, compared with the traditional reactive, structural reinforced with a permanent magnet rotor, in order to provide the working point of soft magnetic materials, and the stator excitation magnetic field changes only need to provide to provide the operating point of the consumption of magnetic materials energy, so the motor efficiency, current, low heat. Due to the presence of permanent magnets, the motor has a strong EMF, the damping effect of its own good, it is relatively stable during operation, low noise, low frequency vibration. Induction can be seen as somewhat low-speed synchronous motor. A four-phase motor can be used for four-phase operation, but also can be used for two-phase operation. (Must be bipolar voltage drive), while the motor is not so reactive. For example: four phase, eight-phase operation (A-AB-B-BC-C-CD-D-DA-A) can use two-phase eight-shot run. Not difficult to find the conditions for C =, D =. a two-phase motor's internal winding consistent with the four-phase motors, small power motors are generally directly connected to the second phase, the power of larger motor, in order to facilitate the use and flexible to change the dynamic characteristics of the motor, its external connections often lead to eight (four-phase), so that when used either as afour-phase motors used, can be used for two-phase motor winding in series or parallel.2, classificationInduction motors can be divided in phases: two-phase motor, three phase motor, four-phase motor, five-phase motor. The frame size (motor diameter) can be divided into: 42BYG (BYG the Induction Stepping motor code), 57BYG, 86BYG, 110BYG, (international standard), and like 70BYG, 90BYG, 130BYG and so are the national standards.3, the stepper motor phase number of static indicators of terms: very differently on the N, S the number of magnetic field excitation coil. Common m said. Beat number: complete the necessary cyclical changes in a magnetic field pulses or conducting state with n said, or that turned a pitch angle of the motor pulses needed to four-phase motor, for example, a four-phase four-shot operation mode that AB -BC-CD-DA-AB, shot eight four-phase operation mode that A-AB-B-BC-C-CD-D-DA-A. Step angle: corresponds to a pulse signal, the angular displacement of the rotor turned with θ said. θ = 360 degrees (the rotor teeth number of J * run shot), the conventional two, four-phase, the rotor teeth 50 tooth motor as an example. Four step run-time step angle θ = 360 ° / (50 * 4) = 1.8 degrees (commonly called the whole step), eight-shot running s tep angle θ = 360 ° / (50 * 8) = 0.9 degrees (commonly known as half step.) Location torque: the motor is not energized in the state, its locked rotor torque (as well as by the magnetic field profile of harmonics caused by mechanical error) static torque: the motor under the rated static electricity, the motor without rotation, the motor shaft locking torque. The motor torque is a measure of volume (geometry) standards, and drive voltage and drive power, etc. has nothing to do. Although the static torque is proportional to the electromagnetic magnetizing ampere turns, and fixed air gap between the rotor teeth on, but over-use of reduced air gap, increase the excitation ampere-turns to increase the static torque is not desirable, this will cause the motor heating and mechanical noise.4, the dynamic indicators and terminology:1, step angle accuracy: turn a stepper motor step angle for each actual value with the theoretical value of the error. Expressed as a percentage: Error / Step Angle * 100%. Its value is the number of different running different beat, four beat running should be within 5%, eight runs should take less than 15%.2 step: the motor running operation steps, is not equal to the theoretical number of steps. Called the step.3, offset angle: the axis of the rotor tooth offset angle of the axis of the stator teeth, the motor is running there will be misalignment angle, the error caused by the misalignment angle, using division drive can not be solved.4, the maximum no-load starting frequency: a drive motor in the form of voltage and rated current, in the case without load, the maximum frequency can be started directly.5, the maximum operating frequency of load: a drive motor in the form of voltage and rated current, the motor maximum speed with no load frequency.6, running torque-frequency characteristics: the motor under test conditions in a measured frequency of operation between the output torque and running torque curve is called the frequency characteristic curve which is the motor number of the most important dynamic is the fundamental basis for motor selection. As shown below: There used to frequency characteristics of other features, starting frequency characteristics. Electrical Once selected, the motor torque to determine the static and dynamic torque is not the case, the motor torque depends on the dynamics of the average motor current (rather than static current), the average current increases, the greater the output torque of the motor, that motor frequency characteristics of the more hard. As shown below: where the maximum curve 3 current, or voltages; curve a minimum current, or voltage is the lowest curve and the load maximum speed of the intersection point of the load. For the average current, voltage increase as much as possible, so that the use of small inductor high current motor.7, the resonance point of the motor: stepping motor has a fixed resonance region, two, four-phase Induction in the resonance region is generally between 180-250pps (1.8 degree step angle) or about the 400pps (step angle 0.9 degrees), the higher the motor drive voltage, motor current increases, the lighter the load, the smaller the size the motor, the resonance shift upward, and vice versa, the motor output torque is large, yet further, and the whole system noise reduction, the general operating point should be offset more resonance.8, motor reversing control: timing is energized when the motor windings AB-BC-CD-DA or () is a positive turn, power the timing for the DA-CD-BC-AB or () when reversed.Some of the basic parameters of the stepper motorNatural step angle motorIt said each of the control system sends a pulse signal, the motor rotation angle.Motor factory, a step angle is given a value, such as 86BYG250A motors is given in 0.9 ° / 1.8 ° (half-step work that is 0.9 °, when the work of the whole step 1.8 °), the step angle can be called 'natural step angle motor', which is not necessarily true when the actual work the motor step angle, the real step angle and drive on.St epper motor step angle is usually the general computing β calculated as follows.β = 360 ° / (Z • m • K)Where β-stepper motor step angle;Z-rotor teeth;m-phase stepper motor number;K-control factor, the film is the ratio of the number of coefficients with the phase numberPhase stepper motorRefers to the number of the motor coil group, the commonly used two-phase, three phase, four-phase, five-phase stepper motor. Different number of motor phases, the step angle is different, the general two-phase motor step angle of 0.9 °/ 1.8 °, three-phase for the 0.75 ° / 1.5 °, five-phase for the 0.36 ° / 0.72 °. In the absence of sub-drive, the user select a different number of phases depends mainly on the stepper motor step angle to meet their own requirements. If you use the sub-drive, the 'phases' will become meaningless, the user simply changes in the subdivision number on the drive, you can change the step angle.Holding torque (HOLDING TORQUE)Stepper motor is energized but no rotation, the stator locked rotor torque. It is the stepper motor one of the most important parameters, usually when the stepper motor torque at low speed near the holding torque. As the stepper motor's output torque increases with the speed and continuous attenuation, output power increases with the speed change, so keep the torque stepper motor to become a measure of one of the most important parameters. For example, when people say 2N.m the stepper motor in case of no special note is the holding torque of the stepper motor for the 2N.m. DETENT TORQUE:Stepper motor is not energized, the stator locked rotor torque. DETENT TORQUE translation in the country there is no uniform way, easy to misunderstand us; the reaction is not a permanent magnet stepper motor rotor material, so it does not DETENT TORQUE.Characteristics of the stepper motor1. The general accuracy of the stepper motor step angle of 3-5%, and not cumulative.2. Appearance of the stepper motor to allow the maximum temperature.Stepper motor causes the motor temperature is too high the first magnetic demagnetization, resulting in loss of torque down even further, so the motor surface temperature should be the maximum allowed depending on the motor demagnetization of magnetic material points; Generally speaking, the magnetic demagnetization points are above 130 degrees Celsius, and some even as high as 200 degrees Celsius, so the stepper motor surface temperature of 80-90 degrees Celsius is normal.3. Stepper motor torque will decrease with the increase of speed.When the stepper motor rotates, the motor winding inductance of each phase will form a reverse electromotive force; the higher the frequency the greater the back emf. In its role, the motor with frequency (or speed) increases with the phase current decreases, resulting in decreased torque.4. Low-speed stepper motor can operate normally, but if not higher than a certain speed to start, accompanied by howling.Stepper motor has a technical parameters: no-load starting frequency, ie the stepper motor with no load to start the normal pulse frequency, pulse frequency is higher than the value if the motor does not start, you may lose steps or stall occurs. In the case of a load, start frequency should be lower. If you want the motor to achieve high-speed rotation, the pulse frequency should speed up the process, which started lower frequency, and then rise by a certain acceleration of the desired frequency (motor speed from low rise to high-speed).Stepper motor with its significant features, in the era of digital manufacturing play an important purpose. Along with the different development of digital technology and the stepper motor itself, improvements in technology, the stepper motor will be applied in more fields.步进电机的应用步进电机是将电脉冲信号转变为角位移或线位移的开环控制元步进电机件。
- 1、下载文档前请自行甄别文档内容的完整性,平台不提供额外的编辑、内容补充、找答案等附加服务。
- 2、"仅部分预览"的文档,不可在线预览部分如存在完整性等问题,可反馈申请退款(可完整预览的文档不适用该条件!)。
- 3、如文档侵犯您的权益,请联系客服反馈,我们会尽快为您处理(人工客服工作时间:9:00-18:30)。
外文文献:Knowledge of the stepper motorWhat is a stepper motor:Stepper motor is a kind of electrical pulses into angular displacement of the implementing agency. Popular little lesson: When the driver receives a step pulse signal, it will drive a stepper motor to set the direction of rotation at a fixed angle (and the step angle). You can control the number of pulses to control the angular displacement, so as to achieve accurate positioning purposes; the same time you can control the pulse frequency to control the motor rotation speed and acceleration, to achieve speed control purposes.What kinds of stepper motor sub-:In three stepper motors: permanent magnet (PM), reactive (VR) and hybrid (HB) permanent magnet stepper usually two-phase, torque, and smaller, step angle of 7.5 degrees or the general 15 degrees; reaction step is generally three-phase, can achieve high torque output, step angle of 1.5 degrees is generally, but the noise and vibration are large. 80 countries in Europe and America have been eliminated; hybrid stepper is a mix of permanent magnet and reactive advantages. It consists of two phases and the five-phase: two-phase step angle of 1.8 degrees while the general five-phase step angle of 0.72 degrees generally. The most widely used Stepper Motor.What is to keep the torque (HOLDING TORQUE)How much precision stepper motor? Whether the cumulative:The general accuracy of the stepper motor step angle of 3-5%, and not cumulative.Stepper motor to allow the minimum amount of surface temperatureStepper motor to allow the minimum amount of surface temperature:Stepper motor causes the motor temperature is too high the first magnetic demagnetization, resulting in loss of torque down even further, so the motor surface temperature should be the maximum allowed depending on the motor demagnetization of magnetic material points; Generally speaking, the magnetic demagnetization points are above 130 degrees Celsius, and some even as high as 200 degrees Celsius, so the stepper motor surface temperature of 80-90 degrees Celsius is normal.How to determine the stepper motor driver DC power supply:A. Determination of the voltageHybrid stepping motor driver power supply voltage is generally a wide range (such as the IM483 supply voltage of 12 ~ 48VDC), the supply voltage is usually based on the work of the motor speed and response to the request to choose. If the motor operating speed higher or faster response to the request, then the voltage value is high, but note that the ripple voltage can not exceed the maximum input voltage of the drive, or it may damage the drive.B. Determination of CurrentPower supply current is generally based on the output phase current drive I to determine. If a linear power supply, power supply current is generally preferable 1.1 to 1.3 times the I; if we adopt the switching power supply, power supply current is generally preferable to I, 1.5 to 2.0 times.The main characteristics of stepping motor:A stepper motor drive can be added operate pulse drive signal must be nopulse when the stepper motor at rest, such asIf adding the appropriate pulse signal, it will to a certain angle (called the step angle) rotation. Rotation speed and pulse frequency is proportional to.2 Dragon step angle stepper motor version is 7.5 degrees, 360 degrees around, takes 48 pulses to complete.3 stepper motor has instant start and rapid cessation of superior characteristics.Change the pulse of the order of 4, you can easily change the direction of rotation.Therefore, the current printers, plotters, robotics, and so devices are the core of the stepper motor as the driving force.Stepper motor control exampleWe use four-phase unipolar stepper motor as an example. The structure shown in Figure 1:Four four-phase winding leads (as opposed to phase A1 A2 B1 phase phase B2) and two public lines (to the power of positive). The windings of one phase to the power of the ground. So that the windings will be inspired. We use four-phase eight-beat control, ie, 1 phase 2 phase alternating turn, would enhance resolution. 0.9 °per step can be transferred to control the motor excitation is transferred in order as follows:If the requirements of motor reversal, the transmission excitation signal can be reversed. 2 control schemeControl system block diagram is as followsThe program uses AT89S51 as the main control device. It is compatible withthe AT89C51, but also increased the SPI interface and the watchdog module, which not only makes the debugging process becomes easy and also more stable. The microcontroller in the program mainly for field signal acquisition and operation of the stepper motor to calculate the direction and speed information. Then sent to the CPLD.CPLD with EPM7128SLC84-15, EPM7128 programmable logic device of large-scale, for the ALTERA company's MAX7000 family. High impedance, electrically erasable and other characteristics, can be used for the 2500 unit, the working voltage of +5 V. CPLD receives information sent from the microcontroller after converted to the corresponding control signal output to the stepper motor drive. Put the control signal drives the motor windings after the input, to achieve effective control of the motor. 2.1 The hardware structure of the motor driveMotor drive using the following circuit:R1-R8 in which the resistance value of 320Ω. R9-R12 resistance value 2.2KΩ. Q1-Q4 as Darlington D401A, Q5-Q8 for the S8550. J1, J2 and the stepper motor connected to the six-lead。