基于加权应变能的某ATV车身拓扑优化设计
拓扑优化技术在某支架设计中的应用

拓扑优化技术在某支架设计中的应用作者:刘永超1 前言卡车驾驶室悬置支架是连接驾驶室和底盘的零件,它对驾驶室起到承托作用。
当汽车行进时,它同时也把底盘上的震动传递到驾驶室,这会降低驾驶员驾车的舒适度,长时间容易产生疲劳。
目前,世界各大重型车生产商都比较重视驾驶室的悬置技术,以期提高自身产品的乘坐舒适度。
由此产生了各项新技术,比如“全浮式驾驶室”悬置技术,就是在车身四角四个支点以浮式减振系统与车架底盘相连形成支撑,根据路面情况调节波动幅度。
这类系统给驾驶员带来舒适的同时,也提高了对支架的要求。
支架需要更高的强度和更小的变形,才能很好地适应新的技术。
本次设计的任务就是利用有限元分析软件HyperWorks对卡车驾驶室后悬置支架进行分析和拓扑优化,优化的约束是体积,目标是支架的柔度(Compliance)最小。
优化结构应同时满足强度和刚度要求。
本次分析和拓扑优化任务是基于优化结构,同时校核并降低应力。
其中拓扑优化是设计的核心任务。
拓扑优化技术是一项新兴的设计方法。
它可以在方案设计阶段给出零部件甚至车身原型合理的材料布局,减轻结构重量。
通过这项技术,企业能缩短设计周期,提高产品性能,减少昂贵的样件生产和整车测试的次数。
国外针对汽车底盘、发动机等零部件的拓扑优化分析和设计的研究及应用都已经比较成熟。
国内目前仍处于理论研究阶段,各汽车厂家也极少实际应用此项技术。
而且当前拓扑优化的软件还不成熟,需要更多的研究和实例应用。
目前汽车行业竞争激烈,国内国外各大厂家都在使用或者关注拓扑优化技术,期望通过它来提升产品的竞争力。
拓扑优化必将在未来几年得到快速的发展。
拓扑优化技术建立在有限元方法和CAE之上,它使计算力学的任务从被动的校核上升为主动的设计与优化,成为现代设计的重要手段。
拓扑优化的思想可追溯到20世纪60年代中期Dom等人的工作,但由于当时结构设计理论和方法的局限,在此后的20年间有关的研究进展缓慢。
到了20世纪80年代后期,随着结构优化设计理论和方法的逐步丰富与完善,以及计算机技术的飞速发展,拓扑优化设计重新引起众多学者的关注,并取得前所未有的发展,成为了国际上最前沿的优化设计方法之一。
车身骨架结构拓扑优化设计综述
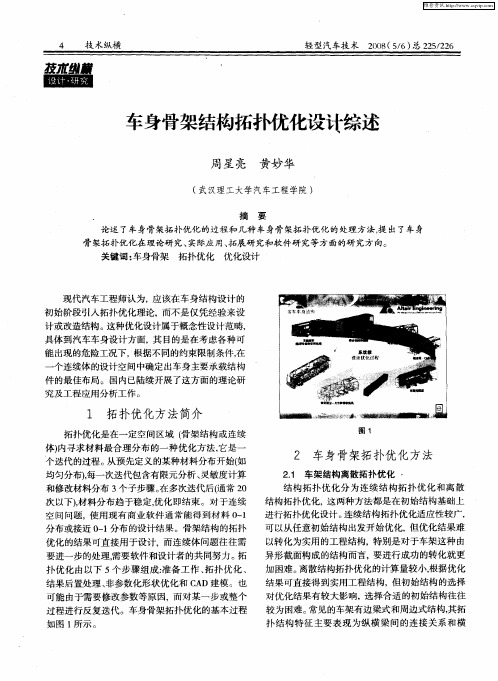
个连续体的设计空间中确定 出车身主要承载结构 件 的最 佳布 局 。国 内已陆续 开展 了这方 面 的理 论研
一
究 及工 程应 用分 析工作 。
1 拓扑优化方法简介
拓扑优化是在一定空间区域 ( 骨架结构或连续 体) 内寻求材料最合理分布 的一种优化方法, 它是一 个 迭代 的过程 。 预先 定义 的某种 材料 分布开 始 ( 从 如 均匀分 布) 一次迭 代包 含有 限元 分析 、 敏度 计算 , 每 灵 和修改材料分布 3 个子步骤。 在多次迭代后( 2 通常 O 次 以下 ) 料 分布 趋 于稳 定 , 化 即结 束 。对 于连续 , 材 优 空 间 问题 , 用现 有 商业 软 件通 常 能得 到 材料 0 1 使 — 分布或 接近 0 1 — 分布 的设 计结果 。骨 架结构 的拓 扑 优化的结果可直接用于设计, 而连续体问题往往需 要进一步的处理, 需要软件和设计者的共同努力 。 拓 扑优化 由以下 5 个步骤组成: 准备工作 、 拓扑优化 、 结果 后 置处理 、 非参数 化形 状优 化 和 C D建模 。也 A 可能由于需要修改参数等原因, 而对某一步或整个 过程 进行 反 复迭代 。车 身骨架 拓扑 优化 的基本 过程
如 图 1所示 。
图 1
ቤተ መጻሕፍቲ ባይዱ
2 车身骨架拓扑优 化方法
21 车 架结构 离散拓 扑优 化 ・ .
结 构 拓 扑 优 化 分 为连 续 结 构 拓 扑 优 化 和 离 散 结构 拓 扑优 化,这两 种方 法都 是 在初 始结 构基础 上 进行 拓扑 优化设 计 。 续结 构拓 扑优 化适应性 较广 , 连
基结构, 它是所有可选拓扑方案 的集合, 需要根据相 应的设计经验归纳得到。设在基结构 中有 n个构件 需 要 通过 优 化 来 确 定 存 在 状 态 , 用 变 量 x(= ,, 并 i l i 2 n )来 表示 ,当第 i 构 件在 最 优结 构 中存 在 时 x 个 ;
电动汽车变速箱壳体静动态分析及拓扑优化设计
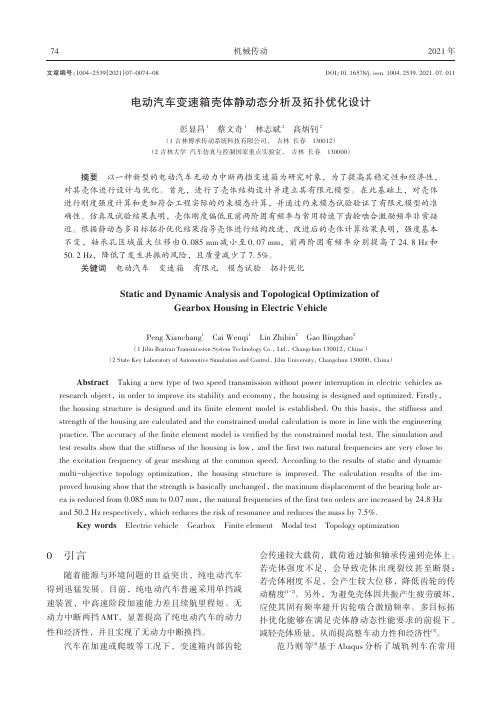
汽车在加速或爬坡等工况下,变速箱内部齿轮
会传递较大载荷,载荷通过轴和轴承传递到壳体上。 若壳体强度不足,会导致壳体出现裂纹甚至断裂; 若壳体刚度不足,会产生较大位移,降低齿轮的传 动精度[1-2]。另外,为避免壳体因共振产生疲劳破坏, 应使其固有频率避开齿轮啮合激励频率。多目标拓 扑优化能够在满足壳体静动态性能要求的前提下, 减轻壳体质量,从而提高整车动力性和经济性[3]。
表 2 1 挡及倒挡轴承支反力 Tab. 2 First gear and reverse bearing support reaction N
1挡
X轴
Y轴
Z轴
轴承 1
2 140
−2 237
−2 115
轴承 2
5 375
0
−3 726
轴承 3
−12 799
−6 503
−6 173
轴承 4
−5 478
2021 年
(a) 1 挡
图 4 壳体有限元模型 Fig. 4 Finite element model of housing
2. 2 变速箱壳体受力分析 变速箱在 1 挡和倒挡两种工况下传递较大转矩,
基于加权应变能的某atv车身拓扑优化设计

基于加权应变能的某atv车身拓扑优化设计
首先,基于加权应变能的某atv车身拓扑优化设计,需要从结构设计中考虑力学应变能(MEP)。
在此,首先考虑定义自由度、结构弹性系数矩阵和相对约束位置,确定车身应该具备的隔振性能。
其次,采用有限元方法,建立应变能有效系数与输入力之间的关系,从而建立车身拓扑优化设计模型。
之后,采用“力学应变能函数”作为优化目标函数,通过改变车身的结构参数,调整车身的体积分布以及各边界处的接触条件,有针对性地松弛某些边界条件以减少应变能,最终求解得到车身最优应变能函数值。
最后,采用精确的随机搜索算法,调整各结构参数,并计算相应的应变能,通过重复迭代,不断逼近应变能函数的最优值,得到最终的最优拓扑优化设计方案。
以上就是对加权应变能的某atv车身拓扑优化设计的整体思路。
基于拓扑优化的电动汽车白车身优化设计

基于拓扑优化的电动汽车白车身优化设计张伟;侯文彬;胡平【摘要】针对电动汽车的独特承载要求,提出一种结合拓扑优化和车身尺寸优化的优化设计方法。
以某型电动汽车为实例,通过建立白车身拓扑优化模型、有限元概念模型、尺寸优化模型和样车制造,进行了从整车拓扑结构到车身梁截面的优化设计过程,实现了电动汽车白车身的正向设计。
在优化过程中采用遗传算法,以弯曲刚度和扭转刚度同时作为优化目标,白车身质量最小作为优化约束,选取了灵敏度较高的梁作为变量进行多目标优化。
通过与样车参数的比较表明,该方法能够满足设计和工艺要求,实现轻量化设计,对提高白车身设计效率和精度有着重要的意义。
%According to the special requirements of the electric vehicle,a method on the basis of topolo-gy optimization and genetic algorithm was presented.In a sample of an electric vehicle,the optimization process includes structural topology optimization and section optimization through topology optimization model,finite element conceptual model,size optimization and manufacture of prototype,which indicates that the forward design can be achieved.In the process of optimization,the obj ectives are bending stiffness and torsional stiffness,and meanwhile,the minimum weight was set as a constraint.By choosing high sensitive beams,the multi-obj ective optimization was presented with genetic pared with the results of the real car,this method can meet the requirements of light weight design and manufacture, which provides theoretical significance in increasing the efficiency and accuracy of optimization.【期刊名称】《湖南大学学报(自然科学版)》【年(卷),期】2014(000)010【总页数】7页(P42-48)【关键词】拓扑优化;遗传算法;电动汽车;白车身【作者】张伟;侯文彬;胡平【作者单位】大连理工大学工业装备结构分析国家重点实验室,辽宁大连116024; 大连理工大学汽车工程学院,辽宁大连 116024;大连理工大学工业装备结构分析国家重点实验室,辽宁大连 116024; 大连理工大学汽车工程学院,辽宁大连 116024;大连理工大学工业装备结构分析国家重点实验室,辽宁大连116024; 大连理工大学汽车工程学院,辽宁大连 116024【正文语种】中文【中图分类】U463.811电动汽车(EV)在近几年得到了高速发展,其高效率、绿色环保等特点也吸引了越来越多学者的关注.而对于电动汽车白车身的研究也从改装传统动力汽车逐步发展到符合电动汽车特殊要求的专用白车身.高云凯等[1]在客车车身的优化中,采用了拓扑优化方法来获得车身的最优设计.谢伦杰等[2]在单目标拓扑优化的基础上引入了更全面的优化目标,实现了电动汽车白车身的多目标优化.上述文献虽然证明了拓扑优化在车身设计中的有效性,但单独应用拓扑优化得到的模型是车身质量的分布,因此并不能很好地描述车身截面的形状和尺寸,不能提供精确的车身模型.文献[3-4]提出了白车身梁截面的多目标优化方法,能够实现白车身的轻量化设计,并提供较为精确的白车身模型.但是这些多目标优化方法只能基于现有的车身模型进行优化设计,并不能在正向设计中实现车身拓扑结构的优化.本文结合上述两种优化方法,首先将拓扑优化引入到电动汽车白车身的正向设计中去,以拓扑优化结果为基础,建立白车身概念模型并根据遗传算法原理,以质量最小为约束,弯曲刚度、扭转刚度为目标,实现白车身梁截面多目标优化.使优化后的电动汽车白车身能够直接用于生产制造过程,从而达到轻量化设计的目的.通过某型电动汽车的设计和制造过程,充分验证了上述方法的有效性和高效性.1 白车身拓扑优化模型结构的拓扑优化过程实际是在给定的设计区域内寻求最优材料分布的问题[5].对于连续体问题,拓扑优化能够精确和高效地实现最佳结构,因此在汽车车身设计的早期阶段其扮演着越来越重要的角色.本文采用的是基于变密度法的SIMP(Solid Isotropic Microstructures with Penalization)优化方法.SIMP方法做了如下假设:引入一种假想的相对密度在0~1的可变材料;并假设该材料的宏观弹性模量与其密度具有非线性关系;采用惩罚因子约束抑制为0~1的单元.SIMP优化方法的原理是在假设的材料用量下,寻求在某种量度条件下的具备最大刚度结构的材料最佳分布形式[6].因此电动汽车白车身的拓扑优化公式表达为[7]:式中:ρe为第e个单元的相对密度;V为初始材料设计体积,被定义为长度为3 000mm,宽度为1 600mm,高度为1 500mm的长方体;V0为优化后要保留的体积,一般由相对密度与单元真实体积加权之和求得,即为体积约束,在拓扑优化过程中为了满足设计域的要求,体积约束取值小于1.在优化过程中,刚度最大化问题可转化为结构柔度最小化,函数c(ρe)为柔度目标函数,可写为:式中:ue为单元的位移向量;Ke为单元的刚度矩阵;P为惩罚因子.根据SIMP方法有:式中:Ke0为第e个单元的初始刚度矩阵.在工程应用中,惩罚因子的取值范围通常为3~5.在电动汽车白车身的拓扑优化过程中,将车身外形和尺寸作为几何约束,并考虑乘员舱、动力系统及行李舱等设计空间,同时综合考虑车身的弯曲工况、扭转工况进行拓扑优化设计.与传统动力汽车不同的是,本文中的电动汽车动力系统采用中置布局,将电动机和电池等布置在乘员舱与后轴之间,因此在拓扑优化过程中需要重新考虑车身的载荷分布并在传统动力汽车发动机舱部分得到更多的设计空间.车身外形如图1所示.图1 某型电动汽车车身外形Fig.1 A electric vehicle body style电动汽车的设计参数见表1.其中弯曲工况和扭转工况模拟了电动汽车车身在匀速行驶时车身的承载情况.在优化过程中弯曲工况按如下方式定义:约束4个悬架支座的6个自由度,施加动力系统模块和乘员舱及行李舱的负荷,计算多种负荷同时施加时的车身有效弯曲刚度;弯曲工况按如下方式定义:约束后轴2个悬架支座的6个自由度,在前轴2个悬架支座分别施加大小相等、方向相反的等效力[8].表1 某型电动汽车设计参数Tab.1 The design parameters of a electric vehiclemm 2 100前轮距/mm 1 244后轮距/mm 1 186弯曲刚度/(N·m-1)8 000扭转刚度/(N·m·deg-1) 7 000动力系统模块负荷/kg 150(距前轴800mm)乘员舱负荷/kg 200(距前轴1 000mm)参数数值轴距/在车身的拓扑优化过程中,取2种工况的权重相等,取惩罚因子等于2,经过反复验证得到的拓扑优化结果如图2所示.车身的拓扑优化结果实质是车身的质量单元的分布情况,通过质量单元分布的疏密程度形成了车身中每一根梁.如图2所示,车身前半段的质量单元确定了防火墙位置,从而基本确定了前设备舱的轮廓及其在车身中的比例.拓扑优化结果中的侧围位置的质量单元确定了B柱的位置,由于该型车是单排座椅,因此根据B柱的位置,乘员舱的尺寸及其在车身中的位置也确定了下来.跟上述分析过程类似的是,优化结果中质量单元最为集中的部分是两根贯穿整个车身的形状类似“彩虹”的梁,它们将成为车身中的主要承载部件.图2 白车身拓扑优化结果Fig.2 The results of body in white topology optimization白车身拓扑优化结果是一个比较抽象的车身模型,它定义了车身主要承载结构的位置和形状,为车身的设计提供了重要参考,但并没有详细描述出白车身中每根梁的参数细节.因此需要结合白车身设计制造的工程经验和资料,来得到车身概念模型.基于拓扑优化结果构建的车身梁结构如图3所示,根据拓扑优化的结果建立车身概念模型的过程主要分为3个部分:车厢地板、侧围、其他附属部件.在构建车厢地板的过程中,首先根据拓扑优化结果,按照最大化乘员舱的原则,确定乘员舱的位置及地板梁的分布情况;再以前轮罩的形状作为约束,确定前设备舱的梁的位置和尺寸;最后再根据车身的设计长度确定货厢的形状和尺寸.在车厢地板的设计过程中,A柱和B柱的位置也同时能够确定下来,因此再结合“彩虹梁”的尺寸,车身侧围的梁结构也较为容易地构建出来.图3中放大图所示为“彩虹”梁构建过程,在拓扑优化结果中,“彩虹”梁的截面形状接近圆形,并大致确定了梁的走向.为了保证梁的平滑,按照B样条线的生成原则,建立了“彩虹梁”的实体模型,并根据实体模型建立了车身的概念模型.图3 白车身梁的拓扑结构Fig.3 The topology structure of a beam in body in white图4所示是根据拓扑优化结果建立的白车身概念模型,其中主要承载梁的数量和位置是依据拓扑优化结果来确定的,并根据车身功能和生产工艺要求做了适当的修改.有别于传统的车身概念有限元模型,以图中的概念模型为基础建立的有限元模型在A柱、B柱等位置引入了柔性接头概念,能够有效地提高仿真的精度,缩短白车身的设计周期.车身概念有限元模型采用梁单元与壳单元相结合,在计算速度与计算精度上达到了较好的统一,模型中梁的个数为36根,单元数为396,采用铝合金作为主要材料,即密度为2.7g/cm3,弹性模量为72GPa,泊松比为0.31.施加载荷按如下定义:弯曲工况下,在距前轴886mm处施加竖直向下的等效载荷3 430N;扭转工况下,在前轴两减振器支座上分别施加竖直向上和向下的力463N.2 应用遗传算法的白车身优化模型2.1 多目标优化数学模型多目标优化的过程是对每一个子项单独应用优化算法,再对每一项加权从而叠加得到多目标优化的解.对于白车身的刚度优化问题的一般数学模型为:式中:x为优化变量,在本文中优化变量选取的是灵敏度较高梁的截面几何尺寸;f1(x)为弯曲刚度的目标函数,f2(x)为扭转刚度的目标函数,根据该型电动汽车设计参数的要求,弯曲刚度应不低于8 000 N/m,扭转刚度应不低于7000N·m/deg.g(x)为车身质量约束函数,在优化过程中该约束被定义为车身质量增加量最小,即满足整车刚度要求的最小车身质量.图4 白车身概念模型Fig.4 Body in white conceptual model2.2 优化目标式中:E1为白车身的弯曲刚度;F0为施加在车身上的等效载荷;u为门槛梁的垂直位移.白车身的扭转刚度按式(6)定义:式中:E2为白车身的扭转刚度;M0为施加在前轴的扭矩,在有限元模型中被定义为M0=2Fw,其中F为施加在前轴上两个方向相反的力,w为前轴距;θ为前后轴的扭转角度.因此目标函数可以写为:式中:E1,obj和E2,obj分别为设计弯曲刚度和设计扭转刚度;α和β分别为弯曲刚度和扭转刚度在目标函数中的权重.多目标优化问题的实质是对各个子目标进行协调和折中处理,使各个子目标函数尽可能达到最优,因此需要合理地选择子目标的权重.白车身刚度的优化目标为弯曲刚度和扭转刚度,并且它们对于车身性能的影响都比较大,因此采用线性加权法赋予它们相同的权重,归一化后,2个权重的取值均为0.5.2.3 优化变量在选择优化变量时,由于薄壁圆管的刚度质量比与圆管的直径成正比,而与圆管的厚度没有关系,因此将圆管的直径作为优化变量.在考虑对称性和几何连接的因素后,优化变量见表2,总计25个.在优化过程中,首先需要计算的是优化变量的灵敏度,即优化变量对目标函数的贡献值,剔除对车身刚度贡献较小的优化变量,从而提高计算效率.在优化过程中,灵敏度被定义为:式中:Fn为第n个变量对应的目标函数值;Xn为第n个变量值,本文中灵敏度的含义是目标函数值相对于梁截面直径的变化率.本次优化过程中的优化变量灵敏度计算结果见表2.由于目标函数值越小,车身刚度越大[9],因此灵敏度绝对值越大,对目标函数的贡献值越大.通过灵敏度计算结果的分析可知,“彩虹”梁对车身刚度的贡献最大,是车身中的主要承载部位,这同时也验证了拓扑优化的结果.表2 多目标优化变量Tab.2 The optimization variables编号变量名称灵敏度1前防撞梁-0.009 2发动机舱横梁-0.005 3防火墙上横梁-0.009 4 A柱横梁-0.016 5 B柱横梁-0.018 6地板前横梁-0.015 7地板中横梁-0.013 8地板后横梁-0.010 9行李舱前横梁-0.008 10 行李舱后横梁-0.007 11 后防撞梁-0.003 12 前纵梁-0.018 13 防火墙下横梁-0.005 14 门槛梁-0.017 15 地板纵梁-0.019 16 中央通道-0.023 17 行李舱中央纵梁-0.012 18 行李舱纵梁-0.009 19 后防撞梁连接梁-0.000 3 20 A柱-0.011 21 B柱-0.019 22 彩虹梁-0.031 23 B柱连接纵梁-0.013 24 行李舱连接梁-0.000 2 25 行李舱横梁-0.000 52.4 遗传算法的实现在众多求解多目标问题的算法中,遗传算法以其高效率、适应性强等特点被越来越多地应用在多目标优化问题中.遗传算法是一种具备自我调节能力的优化方法,它参考了进化论和遗传学的原理,实现了对连续变量或离散变量的优化.遗传算法在种群的繁殖过程中,以适应度作为种群中个体是否淘汰的标准,通过交叉和变异实现种群的最优化,从而得到问题的最优解.在白车身的多目标优化过程中,设优化参数的取值范围为40~100mm.通过采用浮点数进行编码来提高优化的效率,同时综合考虑遗传算法的效率和计算量取种群数为200.遗传算法在优化过程中不依赖任何外部的信息,仅以个体的适应度作为进化的依据.因此,选择合适的适应度函数对遗传算法的效率尤其重要.本文采用的适应度拉伸方法如式(9)[10]所示:式中:fm为第m个个体的适应度;g为遗传代数;θ为温度;θ0为初始温度;n 为种群规模.按上述公式定义的适应度使得在遗传算法的前期,个体的适应度相近,从而产生的后代概率相近.当温度不断下降后,拉伸作用加强,使个体的差异性被放大,从而使得优秀的个体优势更明显.在优化过程中,有时会碰到种群无法进化的现象.这是因为当个体具有同样的染色体、拥有相同的适应度时,种群无法选择出最佳的个体.这时需要引入适当的概率算法,能够增大交叉和变异的概率,从而推动种群的进化.采用自适应交叉概率和变异概率的计算公式为[11]:式中:fc为要交叉的2个个体中适应值较大的一个;fm为要变异的个体的适应值;fmax和favg分别为群体的最大适应值和平均适应值;Pc1,Pc2,Pm1,Pm2均为常数.3 白车身多目标优化结果在VCD(Vehicle Concept Design)系统中,按照上述有限元模型计算得到的应力云图如图5和图6所示.图中表示的是Mises等效应力云图,在弯曲工况下,白车身的最大应力出现在“彩虹”梁的中段;在扭转工况下,白车身的最大应力出现在“彩虹”梁的前段,因此作为车身的主要承载结构,“彩虹”梁的直径应是所有梁中最大的.图5 弯曲工况应力云图Fig.5 The stress nephogram of bending图6 扭转工况应力云图Fig.6 The stress nephogram of torsion在VCD系统的优化模块中调用Nastran求解器对初始车身模型进行优化.在优化模型的建立过程中,经过反复验证,综合考虑了车身质量和车身刚度,将圆管的初始直径设定为40mm,厚度为1 mm.为了提高优化效率,优化过程中选取了灵敏度较高的梁,总计14根.同时为了满足薄壁管件的工艺要求,优化后的取用值按四舍五入取整,梁截面优化的结果见表3.优化前后的车身质量、函数值、刚度等对比见表4,车身的初始设计刚度约达到了设计要求的50%,而优化后虽然质量有了35%的降低,但弯曲刚度和扭转刚度分别提高了87%和84%.结果表明,在刚度达到设计要求的同时,实现了白车身质量最小,达到了轻量化设计的目的.表3 圆管直径优化结果Tab.3 The optimization results of tubes40 45.61 46 B柱横梁 40 47.45 47地板前横梁 40 45.31 45地板中横梁 40 44.17 44地板后横梁 40 40.65 41前纵梁 40 48.77 49门槛梁 40 46.21 46地板纵梁 40 51.65 52中央通道 40 54.78 55行李舱中央纵梁 40 43.11 43 A柱 40 41.89 42 B柱 40 51.65 52彩虹梁 40 65.34 65 B柱连接纵梁变量名称初始数值优化数值取用值A柱横梁40 44.17 44表4 白车身多目标优化结果Tab.4 The optimization results of body in white? 车身的优化设计结果为样车的设计和制造提供了重要的依据,根据拓扑优化结果构建的车身结构模型确定了样车前设备舱、乘员舱、货舱3部分的轮廓及其在车身中的相对位置,从而确定了车身中主要梁的位置和形状.在拓扑优化的基础上,通过对主要梁截面的多目标优化,得到了满足车身性能要求的最佳梁截面,为薄壁管件的选择提供了依据.多目标优化的结果是小数,因此需要根据标准薄壁管件的许用值选用最接近的标准件.白车身中梁与梁的接头采用螺栓和焊接结合的办法来增强接头的刚度,外覆盖件通过采用工程塑料和碳纤维板来同时满足美观和轻量化的要求.根据优化结果制造的某型电动汽车样车如图7所示.经过刚度和称重实验,样车白车身的实际参数见表5.与样车结果相比,优化结果的平均误差大约为14.67%.误差主要来源于有限元模型计算误差以及实车的制造误差.有限元概念模型是基于梁单元的简化模型,因此计算结果会存在5%~10%的误差.同时在样车的制造过程中受限于制造工艺,“彩虹”梁的曲率与设计不完全相同,并且考虑标准件的采购,部分灵敏度较低的梁厚度大于设计值,因此最终的车身质量和性能均超过了设计值,但误差在合理的范围内,基本满足车身设计的要求.车身中的梁直径在40~65mm之间,除了“彩虹”梁以外,梁截面变化较为连续,满足制造工艺和美观的基本要求.图7 某型电动汽车样车Fig.7 The prototype of an electric vehicle表5 优化结果与实验结果比较Tab.5 The comparison between optimization and experiment优化结果实验结果误差122.14 135.45 11%弯曲刚度/(N·mm-1) 8 046.32 9 145.64 14%扭转刚度/(N·m·deg-1)质量/kg 7 139.28 8 530.67 19%4 结论本文提出了一种结合车身拓扑优化和车身梁截面多目标优化2种优点的优化方法,通过构建拓扑优化模型、概念模型、多目标优化模型,从车身的拓扑结构到车身的梁截面尺寸进行了全面的优化,实现了电动汽车白车身的正向设计过程.优化结果表明,在满足刚度要求的同时,能够实现白车身的轻量化设计.同时通过制造和测试样车,验证了该优化设计方法在车身性能和车身制造工艺上的有效性,为电动汽车车身的设计制造过程提供了重要参考.参考文献[1]高云凯,王婧人,汪翼.基于正交试验的大型客车车身结构多工况拓扑优化研究[J].汽车技术,2011(11):16-19.GAO Yun-kai,WANG Jing-ren,WANG Yi.Multi-case topology optimization of bus body structure based on orthogonaltest[J].Automobile Technology,2011(11):16-19.(In Chinese)[2]谢伦杰,张维刚,常伟波,等.基于SIMP理论的电动汽车车身多目标拓扑优化[J].汽车工程,2013,35(7):583-587.XIE Lun-jie,ZHANG Wei-gang,CHANG Wei-bo,et al.Multi-objective topology optimization for electric car body based on SIMP theory[J].Automotive Engineering,2013,35(7):583-587.(In Chinese)[3]BLASQUES J P,STOLPE M.Multi-material topology optimization of laminated composite beam cross sections[J].Composite Structures,2012,94(11):3278-3279.[4]YANG S,QI C,GUO D,et al.Topology optimization of a parallel hybrid electric vehicle body in white[J].Applied Mechanics and Materials,2012,148/149:668-671.[5]JIAN H R,XIAO H,LIU J,et al.An efficient structural topological optimization method for continuum structures with multiple displacement constraints[J].Finite Elements in Analysis and Design,2011,47(8):913-921.[6]姜欣,陈勇,史国宏,等.前期白车身架构优化设计[J].汽车工程,2010,32(8):682-685.JIANG Xin,CHEN Yong,SHI Guo-hong,et al.Body-inwhite structure optimization in early phase ofdevelopment[J].Automotive Engineering,2010,32(8):682-685.(In Chinese)[7]杨姝,王赢利,亓昌,等.纯电动汽车白车身拓扑优化设计及性能验证[J].实验室科学,2012,15(6):37-39.YANG Shu,WANG Ying-li,QI Chang,et al.Topology optimization designing and performance testing for Body-In-White of pure electric vehicle[J].Laboratory Science,2012,15(6):37-39.(In Chinese)[8]侯文彬,张红哲,徐金亭,等.基于概念设计的客车车身结构设计与优化系统[J].湖南大学学报:自然科学版,2013,40(10):58-63.HOU Wen-bin,ZHANG Hong-zhe,XU Jin-ting,et al.System of design andoptimization system for bus body structure based on conceptdesign[J].Journal of Hunan University:Natural Sciences,2013,40(10):58-63.(In Chinese)[9]刘宝越,侯文彬,张红哲.车身结构概念设计系统多目标优化模块设计[J].农业机械学报,2010,42(4):17-21.LIU Bao-yue,HOU Wen-bin,ZHANG Hong-zhe.Design of multi-objective optimization module in vehicle body structure concept design system[J].Transactions of the Chinese Society for Agricultural Machinery,2010,42(4):17-21.(In Chinese)[10]李楠,王明辉,马书根,等.基于多目标遗传算法的水陆两栖可变形机器人结构参数设计方法[J].机械工程学报,2012,48(17):10-20.LI Nan,WANG Ming-hui,MA Shu-geng,et al.Mechanismparameters design method of an amphibious transformable robot based on multi-objective genetic algorithm[J].Journal of Mechanical Engineering,2012,48(17):10-20.(In Chinese)[11]王平,郑松林,吴光强.基于协同优化和多目标遗传算法的车身结构多学科优化设计[J].机械工程学报,2011,47(2):102-108.WANG Ping,ZHENG Song-lin,WU Guang-qiang.Multidisciplinary design optimization of vehicle body structure based on collaborative optimization and multi-objective genetic algorithm[J].Journal of Mechanical Engineering,2011,47(2):102-108.(In Chinese)。
基于拓扑和尺寸组合优化的ATV车身轻量化研究

基于拓扑和尺寸组合优化的ATV车身轻量化研究卢建志;杨世文;李鹏;任子清【摘要】针对车身结构在概念设计阶段出现的拓扑优化结果不连续,结构优化设计周期时间长等问题,基于optistruct优化软件,提出一种拓扑和尺寸组合优化模型.该模型可以同时进行尺寸优化和拓扑优化设计,得到车身蒙皮优化尺寸和最优的车身骨架加载路径.同时缩短了结构的概念设计阶段的设计周期.以ATV车身的结构优化设计为研究对象,对比优化前后的分析结果,在不降低结构性能的前提下优化后的结构减重105.5 kg,验证了该方法的可行性.%In order to overcome the problems of discontinuous topological optimization results and the long cycle time of carbody structure optimization in the conceptual design stage, an optimization model that combines topology and size optimization was proposed. The method can not only obtain the best size and loading paths of body frame, but also shorten the cycle time. As an example, a body structure of ATV was optimized with 105. 5 kg being reduced of the structure.【期刊名称】《中北大学学报(自然科学版)》【年(卷),期】2012(033)002【总页数】4页(P141-144)【关键词】组合优化;拓扑优化;尺寸优化;ATV【作者】卢建志;杨世文;李鹏;任子清【作者单位】中北大学机电工程学院,山西太原030051;长安新能源汽车北京研发中心,北京100081;中北大学机电工程学院,山西太原030051;中北大学机电工程学院,山西太原030051;国营六一六厂铸造厂,山西大同037036【正文语种】中文【中图分类】U4830 引言车辆的车身质量占总质量的 40% 左右,车身的轻量化对整车的轻量化起着举足轻重的作用,车辆的轻量化正成为 21世纪车辆技术的前沿和热点[1].目前ComputerAidedEngineering(CAE)技术在车辆车身设计、分析与优化中的应用越来越广泛.文献 [2]中基于 Ansys软件对ATV车架进行了各个部件的尺寸优化,优化后车架的最大应力减少了 11.95%,车架的质量减少了 28.97%.文献 [3]以壳单元为基础,建立了ATV(全地形车)车架的有限元模型,选择满载状态下的典型工况,计算了车架的强度和刚度,进行了模态分析;并通过道路可靠性试验,验证了分析结果的正确性,提出了结构改进方案.文献[4]中提出了一种形状和尺寸组合优化方法,通过分离设计变量,分别采用渐进节点移动法和满应力法优化桁架结构的形状和尺寸;通过循环迭代,耦合形状和尺寸变量间的相互作用关系,得到了结构的最小重量.在文献 [5]中,P.S.Tang和 K.H.Chang提出了利用几何重构技术,集成拓扑和形状优化技术,从而得到光滑的几何边界和易于加工的几何模型的方法.首先将拓扑优化几何转换成光滑的参数化的 B样条曲线和曲面,然后曲线曲面导入到参数化的 CAD环境中建立结构的实体模型,再对结构进行形状优化.文中提出的组合优化方法,能够在概念设计阶段对车辆的车身结构同时进行车身蒙皮的尺寸优化和骨架的拓扑优化设计,并以 ATV车身的结构优化为算例,对比了原车和组合优化方法得到的有限元分析结果,验证了该方法的可行性.文中有限元建模采用 Hypermesh软件,结构优化使用的软件是 Optistruct.1 拓扑优化和尺寸优化方法1.1 基于密度法的材料插值拓扑优化方法从 20世纪末期以来,产生了许多拓扑材料插值理论和拓扑结构描述方法,其中均匀化方法和密度法材料插值模型最具有代表性.目前在工程拓扑优化问题的求解中很少采用均匀化方法,较多采用密度法材料插值模型.密度法以连续变量的密度函数形式表达单元相对密度与材料弹性模量间的对应关系,这种方法是基于各向同性材料,不需要引入微结构和附加的均匀化过程,它以每个单元的相对密度作为设计变量,人为假定相对密度和材料弹性模量间的某种对应关系,程序实现简单,计算效率高,是从均匀化方法发展而来的一种方法[6].1.2 尺寸优化对结构优化设计最简单和最直接的做法就是修改结构单元的尺寸.尺寸优化中的设计变量可能是杆的横截面积、惯性矩、板的厚度,或是复合材料的分层厚度和材料铺层角度.在用有限元计算结构位移和应力时,尺寸优化过程不需要网格重新划分,直接利用灵敏度分析和合适的数学规划方法就能完成尺寸优化.对于具有连续性结构的板或壳,也只是把各单元厚度作为设计变量,优化结果是阶梯形分布的板厚度或壳厚度.在这类优化过程中,设计变量与刚度矩阵一般为简单的线性关系.尺寸优化技术经历了 20多年的研究,重点主要集中在优化算法和灵敏度分析的研究[7].2 拓扑和尺寸组合优化模型ATV(全地形车)车身结构主要由车身蒙皮、车身骨架、座椅等组成.在车身的概念设计阶段,通常采用类似于文献 [5]中的设计方法:先确定载荷传递路径,再进行详细的尺寸设计的阶段优化方法对车身进行轻量化设计.这种常用的轻量化方法虽然可以得到结构的加载路径和详细的优化尺寸,但是得到的拓扑优化结果往往出现不连续、材料堆积等现象,而且整个概念设计至少需要二次的 CAD,有限元建模和优化计算过程;由于ATV车身结构尺寸比较大、形状复杂,这种阶段优化方法花费了大量的时间,加大了产品的时间成本,大大降低了所研发车身的市场竞争力.本文引入拓扑和尺寸组合优化方法,该方法分别以车身蒙皮的厚度和车身骨架的密度作为车身蒙皮尺寸优化设计变量和车身骨架的拓扑优化设计变量,以车身整体的刚度为约束条件,以尺寸和拓扑优化区域的总质量为目标函数;耦合拓扑变量和尺寸变量之间的关系,得到最优的载荷传递路径和蒙皮尺寸厚度.组合优化设计方法的流程如图 1所示.如图 1所示,整个组合优化设计可以分为拓扑优化和尺寸优化两个子模块,得到拓扑和尺寸设计变量的耦合变量,下面分别对这两个模块作简单介绍.2.1 拓扑优化模块拓扑优化模块采用当前拓扑优化中常用到的基于密度法的材料插值模型,其数值模型如下:式中:di是单元密度;f(d)是拓扑优化区域的目标函数;G(di)≤Gmax是约束条件.2.2 尺寸优化模块尺寸优化模块的数学模型如下:式中:ti为车身单元的厚度;f(t)是尺寸优化区域的目标函数;G(ti)≤Gmax是约束条件;tmin,tmax是许用的最小、最大厚度尺寸.2.3 拓扑和尺寸组合优化模型由以上组合优化的两个子模块的数学模型很容易得到拓扑和尺寸组合优化的数学模型:式中:密度 xi为拓扑优化设计变量;车壁厚度 ti为尺寸优化设计变量;Y(x,t)为组合优化的耦合变量;fmin(y)是组合优化的目标变数;f(x)和 f(t)分别为拓扑和尺寸优化区域的子目标函数;C(yi)≤Cmax为组合优化的约束条件;tmin,tmax分别为尺寸优化时的最小允许尺寸和最大允许尺寸.在 optistruct结构优化软件中,可以同时定义拓扑优化设计变量和尺寸优化设计变量,定义车身蒙皮和车身骨架的总质量最小为目标函数.3 ATV车身的拓扑和尺寸组合优化设计3.1 车体材料车体材料采用装甲钢板,材料的弹性模量为208 GPa,泊松比 0.3,抗拉强度 1000 MPa,屈服强度 800 MPa.轮边减速器壳体的材料为YL112,其抗拉强度 240 MPa,布氏硬度 85.3.2 ATV工况ATV的工况主要有:极限弯曲工况,极限扭转工况,制动工况,转弯工况,自由模态.本文以ATV车的极限扭转工况为例验证了拓扑和组合优化方法的可行性.扭转工况下车体的约束和载荷如下:载荷:扭转工况下,来自地面的冲击力作用在 1轴的两个轮上,作用力大小相等方向相反.考虑到安全因子 f=3,则载荷大小F=G×f=14000×3=42000 N.约束:在扭转工况下,车体 4轴的两轮全约束.3.3 ATV车身的拓扑和尺寸组合优化设计车身在左右不相等的载荷作用下将产生扭转变形,假设把前后轴(轴距为 l)具有相同刚度的圆棒,即将车身的扭转刚性看成是简单圆棒的扭转刚性,其单位长度的扭转角为h,故车身的扭转刚度为[8]式中:GJ为扭转刚度;L为轴距;T为扭矩;h为扭转角.车体 1轴与 4轴之间的距离 L为 2016 mm;1轴两轮间的距离 l为 553 mm;支撑点作用力大小为 F=42000 N,方向相反;扭矩T=42000×1.160=48720 N◦m.图2 山本图线Fig.2 Shanben graph具体的优化设置如表 1所示,得到的优化结果如图 3所示.表1 组合优化设置参数Tab.1 Combinatorial optimization parameters工况扭转设计变量 1 骨架单元密度设计变量 2 蒙皮厚度载荷作用点位移小于 10.8mm约束 2 最大应力 400 M Pa目标函数优化区域质量最低图3 车身拓扑和尺寸组合优化结构图Fig.3 Optimized structure of combinatorial optimization3.4 优化结果分析对比表 2中各项性能可知,组合优化方法得到的优化结构的最大应力比原车大了 4M Pa,最大位移大了 0.99 mm,均都在结构的允许范围之内.组合优化方法得到的结构在质量上减少了105.5 kg,结构优化计算的收敛时间仅为 63 min.而且由得到的组合优化结构(图 3)可知,优化结构清晰、连续,整体无明显的材料堆积现象.4 结论本文采用拓扑和尺寸组合优化方法对 ATV车身的结构进行了优化,在保证结构性能没有降低的情况下,结构的整体质量比原车减轻了105.5 kg.同时,得到的结构清晰、连续,整体无明显的材料堆积现象;该组合优化能够有效地减少车身在概念设计阶段的时间成本,提高了产品的市场竞争力.参考文献:[1]龙江启,兰凤崇,陈吉清.车身轻量化和钢铝一体化结构新技术的研究进展[J].机械工程学报,2008,44(6):28-35.Long Jiangqi, Lan Fengchong, ChenJiqing.Technology of lightweight and steel-aluminum hybrid structure car body[J].Chinese Journal of Mechanical Engineering,2008,44(6):28-35.(in Chinese)[2]许佩霞,蔡炳芳.基于 ANSYS的全地形车车架结构优化设计 [J].机械设计,2008,12(25):56-58.Xu Peixia, CaiBingfang. Structuraloptimization design on frame of all topography vehicle based on ANSYS[J].Journal Ofmach Ine Design,2008,12(25):56-58.(in Chinese)[3]朱茂桃,蔡炳芳,束荣军,等.全地形车车架结构有限元分析与轻量化设计 [J].拖拉机与农用运输车,2008,35(3):47-52.Zhu Maotao,Cai Bingfan,Shu Rongjun,et al.FEA and lightweight design for ATV frame structure[J].Tmctor& Farm Transporter,2008,35(3):47-52.(in Chinese)[4]王栋,张卫红,姜节胜.桁架结构形状与尺寸组合优化[J].应用力学学报,2007,19(3):72-76.Wang Dong, Zhang Weihong, Jiang bined shape and sizing optimization in truss design[J].Chinese Journal of Applied Mechanics,2007,19(3):72-76.(in Chinese)[5]Tang P S,Chang K H.Integration of topology and shape optimization for design of structural components[J].Struct.Multidisc.Optim.,2001,22:65-82.[6]傅晓锦.拓扑与形状集成优化算法的关键技术研究[D].杭州:浙江工业大学,2008.[7]Arora J S,Haug E J.Methods of design sensitivity analysis in structural optimization[J].AIAA Journal,1979,19(9):970-974.[8]乐玉汉.轿车车身设计[M].北京:高等教育出版社,2000:43-44.。
基于正交试验的大型客车车身结构多工况拓扑优化研究

基于正交试验的大型客车车身结构多工况拓扑优化研究随着社会的发展,大型客车在公共交通领域所占的重要性不断增加,面对着越来越严苛的环保和安全要求,其设计结构也不断升级。
而车身结构的优化设计是重要的研究方向之一,能够有效降低车身结构的重量、提高领域属性等。
本文基于正交试验的实验设计方法,对大型客车车身结构在多工况下进行拓扑优化研究。
正交试验法是一种系统的试验设计方法,通过少量试验次数就可确定多个因素对结果的影响,从而系统的分析优化问题和选择最佳方案。
将该方法应用在大型客车车身结构拓扑优化中,可以节省大量试验成本和时间,提高研究效率。
本文选取了大型客车车身结构优化过程中的重要参数进行分析,包括车身侧面2D模型、最大的主拱弓截面形状、前轮弹簧承载点位置、后轮悬挂单元参数等。
在进行正交试验的实验设计过程中,选取了四个因素进行研究,每个因素选择了三个不同的水平值。
通过正交试验设计表将这些水平值组合,得到12组实验,同时设置了多工况载荷,分析车身结构在不同工况下的受力变化情况,以实现全面分析和综合评价车身结构的工作性能。
通过对实验进行数据分析和处理,得出对大型客车车身结构优化的建议,包括:增加前轮弹簧承载点支撑的刚度增加车身的稳定性和承载能力;优化后悬挂单元参数,减小车身的横向摆动,提高舒适性;采用梯形横梁结构,减小车身重量,提高燃油经济性。
最终将这些优化方案进行综合,得到了一组最佳的车身结构设计方案。
在大型客车车身结构优化研究中,正交试验法是一种非常有效的设计方法,具有高效、全面、精确等优点。
通过减少试验次数,加快研究进程,同时可提供更加准确和全面的实验数据,为优化车身结构提供科学依据和理论支持。
此外,正交试验法还可以帮助研究人员寻找到主要影响车身结构性能的关键因素,进而优化方案的选择和设计。
在实验设计过程中,将多个参数进行组合测试,通过数据分析,发现每个因素的主要作用及其相互作用,可以帮助研究人员更准确地确定每个因素对车身结构的影响程度,并判定各个因素之间的相关性。
基于加权应变能的某ATV车身拓扑优化设计

第2期(总第165期)2011年4月机械工程与自动化M ECHA N ICAL EN GI NEER IN G & AU T O M A T IO N N o.2Apr.文章编号:1672-6413(2011)02-0052-03基于加权应变能的某AT V 车身拓扑优化设计卢建志,杨世文(中北大学机电工程学院,山西 太原 030051)摘要:以极限弯曲和扭转工况的加权应变能最小为目标函数,以设计区域的体积分数为约束,以设计区域的材料密度为设计变量,建立基于加权应变能的拓扑优化模型。
并对某A T V 车身进行拓扑优化设计,得到了结构的载荷传递路径,验证了该方法的可行性。
关键词:加权应变能;拓扑优化;A T V 车身骨架中图分类号:U 463.82 文献标识码:A收稿日期:2010-08-17;修回日期:2010-11-08作者简介:卢建志(1986-),男,福建莆田人,在读硕士研究生,研究方向:结构优化设计研究。
0 引言全地形车(All T err ain Vehicle,ATV )是一种全新概念的新车型,由于具有多种用途且不受道路和法规的限制,在西欧和北美广泛流行。
全地形车的使用工况复杂,能够适应各种地形,因此对性能提出较高的要求[1]。
文献[2]中基于AN SYS 软件对某AT V 车架进行各个部件的尺寸优化,优化后车架的最大应力减少了11.95%,车架的质量减少了28.97%。
文献[3]以壳单元为基础,建立A TV 车架的有限元模型,选择满载状态下的典型工况,计算车架的强度和刚度,并进行了模态分析,通过道路可靠性试验,验证了分析结果的正确性,提出了结构改进方案。
车体的拓扑优化,以优化车体内加强筋的布置、满足车体的刚度性能要求为目标。
由于车辆在行驶过程中存在不同的承载工况,因而车体的拓扑优化问题可以归结为以结构刚度最大化为目标的在多个工况下的刚度拓扑优化问题,亦可称作多刚度拓扑优化问题。
- 1、下载文档前请自行甄别文档内容的完整性,平台不提供额外的编辑、内容补充、找答案等附加服务。
- 2、"仅部分预览"的文档,不可在线预览部分如存在完整性等问题,可反馈申请退款(可完整预览的文档不适用该条件!)。
- 3、如文档侵犯您的权益,请联系客服反馈,我们会尽快为您处理(人工客服工作时间:9:00-18:30)。
第2期(总第165期)2011年4月机械工程与自动化M ECHA N ICAL EN GI NEER IN G & AU T O M A T IO N N o.2Apr.文章编号:1672-6413(2011)02-0052-03基于加权应变能的某AT V 车身拓扑优化设计卢建志,杨世文(中北大学机电工程学院,山西 太原 030051)摘要:以极限弯曲和扭转工况的加权应变能最小为目标函数,以设计区域的体积分数为约束,以设计区域的材料密度为设计变量,建立基于加权应变能的拓扑优化模型。
并对某A T V 车身进行拓扑优化设计,得到了结构的载荷传递路径,验证了该方法的可行性。
关键词:加权应变能;拓扑优化;A T V 车身骨架中图分类号:U 463.82 文献标识码:A收稿日期:2010-08-17;修回日期:2010-11-08作者简介:卢建志(1986-),男,福建莆田人,在读硕士研究生,研究方向:结构优化设计研究。
0 引言全地形车(All T err ain Vehicle,ATV )是一种全新概念的新车型,由于具有多种用途且不受道路和法规的限制,在西欧和北美广泛流行。
全地形车的使用工况复杂,能够适应各种地形,因此对性能提出较高的要求[1]。
文献[2]中基于AN SYS 软件对某AT V 车架进行各个部件的尺寸优化,优化后车架的最大应力减少了11.95%,车架的质量减少了28.97%。
文献[3]以壳单元为基础,建立A TV 车架的有限元模型,选择满载状态下的典型工况,计算车架的强度和刚度,并进行了模态分析,通过道路可靠性试验,验证了分析结果的正确性,提出了结构改进方案。
车体的拓扑优化,以优化车体内加强筋的布置、满足车体的刚度性能要求为目标。
由于车辆在行驶过程中存在不同的承载工况,因而车体的拓扑优化问题可以归结为以结构刚度最大化为目标的在多个工况下的刚度拓扑优化问题,亦可称作多刚度拓扑优化问题。
本文提出采用基于加权应变能的拓扑优化方法对AT V 车身进行拓扑优化,得到满足极限弯曲和扭转的加强筋布置方案,为AT V 车身的加强筋布置提供依据。
1 基于加权应变能的拓扑优化模型本文提出的基于加权应变能的拓扑优化模型,以极限弯曲和扭转工况的加权应变能最小为目标函数,以设计区域的体积分数为约束,以设计区域的材料密度为设计变量。
在拓扑优化过程中,把刚度最大问题等效为柔度最小问题来研究,柔度则用应变能来定义,因此,该问题的优化目标可以转化为全局柔度最小化。
采用optistruct 模型常用的多刚度线性叠加的模型将多个工况下的柔度目标值综合表述为全局柔度目标值,其柔度目标函数为:C w =∑w i C i =12∑w i u Ti f i 。
(1)……………其中:C w 为总的加权应变能;f i 为第i 个工况的载荷;C i 为第i 个工况的柔度目标函数;w i 为各工况的柔度函数的权重,其取值在0~1之间;u T i 为位移矩阵的转置矩阵。
由此得本拓扑优化数学模型为:M in:S ( )=∑ni =1w iC i( )s.t.∑n i =1(∑mj =1V j i j)-V ≤00<<1i =1,…,n j =1,…,m。
(2)……………其中:V j 为第j 个单元的体积;V 为优化区域体积分数; 为单元密度。
在Optistruct 软件中可以设置各个工况的权重系数w i 。
2 某ATV 车身骨架的拓扑优化设计2.1 车体材料选择车体材料采用装甲钢板,材料的弹性模量为208GPa ,泊松比为0.3,抗拉强度为1000M Pa ,屈服强度为800M Pa 。
轮边减速器壳体的材料为YL112,其抗拉强度为240M Pa ,伸长率为1%,硬度为85HB 。
另外一种选择是ZL101A,T 6处理的抗拉强度为295MPa,伸长率为3%,硬度为80HB,弹性模量为71000M Pa,泊松比为0.33。
2.2 拓扑优化设计域简述该车体结构为一承载式车身,如图1所示。
由于优化的是车体结构上的加强筋布置,因而以车体结构为基础,作为优化的设计域。
图1 A T V 车体结构图2.3 工况说明在拓扑优化过程中,共选取5种工况进行优化设计,其中包含2种极限工况以及3种辅助工况。
极限工况包括极限弯曲工况和极限扭转工况,辅助工况包括制动工况、拐弯工况和模态工况。
本文主要研究车体的极限工况。
2.3.1 极限扭转工况该工况模拟了满载车辆越过障碍时,车体由4轴两轮和1轴单轮共同支撑、而1轴另外一个轮悬空的车身承载情况。
根据受力分析,设置载荷与约束边界条件如下:载荷:仅由第一轴单独承受车体垂直方向上的力,经计算力的大小为4.2×104N;发动机重心位置的力为3.6×103N;前排和后排的座椅处的力分别为6.6×103N ;中排座椅处的力为1.1×103N ;车头货物的力为6×103N ;油箱加变速箱的力为3×103N ;车体施加3倍重力场。
约束:4轴的两轮全约束。
极限扭转工况载荷和约束设置如图2所示。
图2 极限扭转工况载荷和约束设置2.3.2 极限弯曲工况该工况模拟了该车在满载状态下,车体越过坡度最高点时,由第三轴单独支撑车身、其他各车轮悬空的极限承载情况。
在计算模型中,载荷和约束设置分别为:载荷:发动机重心位置的力为3.6×103N ;前排和后排的座椅处的力分别为6.6×103N;中排座椅处的力为1.1×103N ;车头货物的力为6×103N ;油箱加变速箱的力为3×103N ;车体施加3倍重力场。
约束:3轴两车轮全约束。
极限弯曲工况载荷和约束设置如图3所示。
图3 极限弯曲工况载荷和约束设置2.4 拓扑优化设置该车的拓扑优化目标是多工况下全局刚度的最大化。
首先,考虑到极限弯曲和极限扭转都是车体结构的重要工况,故优化中两种工况的加权系数均为0.5,以极限弯曲和扭转的加权应变能作为优化区域的响应;其次,以约束设计区域的体积分数0.3作为约束条件,以设计区域的加权应变能最小为目标函数;最后,通过optistr uct 的成员尺寸控制功能,控制最后的拓扑结构的成员尺寸大小,以简化最后的设计结构[4]。
2.5 优化结果分析拓扑优化结果见图4,根据优化结果对原车的加强筋进行重新设计(见图5),对改进的车体进行了极限弯曲和扭转工况的有限元分析计算,优化前后车体的性能对比见表1。
图4 拓扑优化结果密度云图从图5和表1中可以看出:经过优化后的结构在强度和刚度上都有所提高,车身加强筋质量从107kg・53・ 2011年第2期 卢建志,等:基于加权应变能的某AT V 车身拓扑优化设计降到85kg,车身骨架减轻了20.5%。
图5 改进后的车体设计表1 优化前后车体的性能对比工况极限弯曲工况极限扭转工况优化前优化后优化前优化后位移(mm )0.510.467.527.03应力(M Pa)2081962392293 结论本文采用基于加权应变能的拓扑优化方法,结合optistruct 结构优化软件,对某AT V 车身骨架进行重新优化设计,得到了清晰的车身加筋设计;优化后,车体加筋的质量降低了20.5%,车体的整体性能也得到一定的提高,该方法为AT V 车身骨架设计开发提供了一定的参考。
参考文献:[1] 许佩霞,蔡炳芳.全地形车车架早期失效原因分析与结构改进[J ].机械设计与制造,2008(11):53-55.[2] 许佩霞,蔡炳芳.基于A N SYS 的全地形车车架结构优化设计[J ].机械设计,25(12):56-58.[3] 朱茂桃,蔡炳芳,束荣军,等.全地形车车架结构有限元分析与轻量化设计[J ].拖拉机与农用运输车,2008,35(3):47-52.[4] 张胜兰,郑东黎,郝琪,等.基于Hy per wo rks 的结构优化设计技术[M ].北京:机械工业出版社,2007.ATV Body Topology Optimization Design Based on Weighted ComplianceLU Jian -zhi ,YANG Shi -wen(Sch ool of M echatron ic Engineering ,Nor th U nivers ity of Ch ina,T aiyuan 030051,China)Abstract :A mo del of to polog y optimizatio n based o n w eig hted co mpliance is pr oposed in t his paper.T he model is studied w ith theminimum co mpliance as objective and t he v olume fraction of the design ar ea as co nstr aints ;A s an ex ample ,a body fr ame of A T V is optimized ,the r esult show s that the pro posed met ho d is feasible .Key words :w eig hted co mpliance ;topo lo gy optimiza tio n ;A T V body fr ame(上接第49页)参考文献:[1] 谢志辉.Delphi 在工业测控系统中的应用[J].电工技术,2001(8):19-20.[2] 赵以蕙.矿井通风与空气调节[M ].徐州:中国矿业大学出版社,1989.[3] 杨瑞霞.矿井通风智能监控系统研究[D ].沈阳:东北大学,2007:14-16.[4] 郭国政,陆明心.煤矿安全技术与管理[M ].北京:冶金工业出版社,2006.[5] 赵兰涛,苏彦华.Delphi 串口通信技术与工程实践[M ].北京:人民邮电出版社,2003.[6] 张选正.变频器应用经验[M ].北京:中国电力出版社,2006.Air Volume Adjustment System Based on Delphi for MineWU Ji -chun ,ZHOU Jian -ping ,LIANG Chu -hua(School of M echanical Engin eering,Xinjian g U nivers ity,Urumqi 830046,China)Abstract :In t his paper ,o bject-o rient ed languag e Delphi w as applied to the design and implementatio n of a mine air volumeadjustment system ,and the paper put emphasis o n the use of thir d-par ty contr ol t o co mpile serial communication pr og ram to contr olthe inver ter ,at the same time ,the pa per int ro duced the pr og ramming to contr ol the stepping mo tor by calling the funct ion of motion contr oller.Key words :Delphi;ventilation;serial co mmunicat ion;mo tio n co nt ro ller(上接第51页)Optimization Design of Helical Gear ReducerDU Hai -xia(S chool of M echan ical Engineering ,S haanx i U nivers ity of T echnology ,Hanzh ong 723003,Ch ina)Abstract :A n o pt imal desig n metho d ba sed o n co mplex met ho d fo r helical gear r educer w as discussed in this paper .A ccor ding to the needs of o ptimization design ,taking minimum v olume as objective function ,the paper g ave the optimal model .A t last ,the method w as v er ified to be accurate by an ex ample .Key words :r educer ;o pt imal desig n ;co mplex metho d・54・ 机械工程与自动化 2011年第2期 。