钢管拱制造工艺
庞村西特大桥钢管拱加工技术方案

桁 架片连接 为一整体 ,组成一 条拱肋 ,拱肋钢 管桁 架为等截 面布置 ,拱 肋高 3 . 8 m ,拱肋宽 2 . 1 m 。标准段 拱肋上、下弦 杆 钢管均采用 e9 0 0X 1 6 a m 的直接 焊接 管 ,在拱脚至桥面 r
一
、
庞 村西特 大桥位于郑州 市南出 口暨郑州至新 郑快速通道 上, 在 K6 +0 3 5 . 7里程处与南水 北调总干渠相 交 , 路水交角
为 1 3 0 。 。
庞 村西特大桥 跨径布置为 :2 5 m +1 6 4 . 4 m +2 5 m ,桥 梁全长 为 2 2 0 . 4 m 。主桥采 用下承桁架 式钢管 混凝土无推力
摘
要 :郑州市 南出 口暨 郑州 至新 郑快速通道是郑州 市重 点工 程建 设项 目之一 ,采用一级公路技术标准 ,并兼有城
市快速路功能 。其中庞 村西特大桥是该项 目唯一 的一座特 大桥 ,是该项 目的控制性工程 。其主跨 1 6 4 . 4 m 钢管混凝 土下承式拱桥虽然技术成熟 ,但在 河南省仍属较大跨钢管混凝 土拱桥 。上部结构 系杆拱内部为高次超静定结构、外 部整 体为静定结构 。施 工工序 繁琐、复杂 ,其钢管拱加工 、焊接质量要求高、拼装难度 大、工艺技术复杂、难度大 。 文 中主 要描述了钢管拱的加工、拼装及其质量控制等 方面 ,相 信对 读者有一定的借鉴作用 。 关键 词:钢管拱 ;加工 ;拼装 ;方案
线距为 2 . 8 m。主拱拱 肋为 4肢钢管桁架式断面 ,每一拱 肋
为 两 片 由腹 杆 钢 管 与 上 、 下 弦 杆 钢 管 焊 接 形 成 的 桁 架 片 横 向 连 接 形 成 ,桁 架 横 向连 接 采 用 缀 板 与 横 隔板 结 合 方 式 将 两 片
钢管拱施工方法及工艺

钢管拱施工方法及工艺(共3页)--本页仅作为文档封面,使用时请直接删除即可----内页可以根据需求调整合适字体及大小--钢管拱施工方法及工艺1、工艺流程钢管拱施工流程详见下页“钢管拱施工工艺流程图”。
2、拱脚安装拱脚是拱肋线形控制的基础,拱脚节段定位施工应注意其几何尺寸位置及拱肋管的轴线尺寸、纵向仰角、横向垂直度,确保拱肋安装的精度。
另外,由于拱脚是与梁部混凝土一起施工,因此,在浇筑混凝土前,先将拱肋钢管定位好,安装型钢骨架将拱脚进行固定,以防在混凝土施工时移位。
拱脚定位骨架安装线性控制范围±10mm。
钢管拱施工工艺流程图3、拱肋安装支架钢管拱安装采用支架法进行安装,拟采用由钢管、型钢组拼成支架,支架底部与混凝土箱梁上预埋件焊接牢靠,支架顶面安装拱肋调整设施,支架顶部设置操作平台,以方便拱肋安装。
4、拱肋安装在工厂分段加工好的钢构件经检验、试拼装及线形调整合格后运至工地,在现场组拼焊接成吊装节段;焊接无破损探伤检测采用超声波和射线探伤方法进行。
焊缝中发现有缺陷超标现象,根据探伤人员的准确定位,进行返工处理后重新探伤复查,直至符合质量要求。
拱肋分段吊装按左右、两端由拱脚向拱顶依次进行,拼装过程中做好预拱度设置,安装横撑;各部尺寸、线形检查无误,并在设计要求的温度范围内进行焊接,随工检查焊缝质量。
钢管拱安装注意事项:①架设安装测量点标记在工厂制造时就应设置好,测量点放置在分段节点圆管非最高点(每个吊装节段两端均设置),作好标记。
②在拱肋架设过程中,每架设一节拱肋都会对前面架设的拱肋产生影响,因此每架设一节拱肋都应对前面架好的拱肋接口进行复测检查,如发现误差超限则应及时纠偏。
③为了减少温度对拱肋的影响,拱肋控制的放样与验收测量时间一般尽可能安排在早上7~9点和下午16~18点时间段内进行,其他施工验收和施工观测随进度进行。
④合拢段的施工是拱肋拼装的最后一个环节,是拱肋线形控制的重点。
对于钢管拱的合拢段拱肋节段在加工时应预留一定的加工余量,在安装时切割。
下承式钢管拱桥施工工艺

下承式钢管拱桥施工工艺一、概况轻纺大桥位于闻名全国的中国轻纺城中心,横跨杭甬运河。
该桥为轻纺城联运河两岸的主要交通干道。
在桥位处水面宽为150米,水深约4米,河床地质上层深约20米为淤泥质粘土。
20米至54米为粘土,54米至56米为卵石,56米以下为凝灰岩,主桥采用跨径为90米钢管拱,钢管拱为下承式系杆拱,系杆为柔性拉杆,引桥上部为20米跨径的预应力空心板,主桥下部为φ1.50米钻孔桩,桩长为54米和53米,桩尖进入风化层,桩尖标高为-55.00(-54.0)米。
引桥采用直径φ1.20米钻孔灌注桩。
跨径:3×20+92÷2×20米,桥梁全长197.04米。
桥面宽:3+22.4+3=28.4米。
设计荷载:汽-20,挂车-100,人群3.5KN/m2。
桥面纵坡:≤2.7%。
桥面横坡:1%。
竖曲线半径:R=1500米。
航道等级为八级。
编制依据:1.交通部《公路桥涵施工技术规范》JTJO41-89。
2.国家建材局《钢管混凝土结构与施工规程》JGJO1-89。
3.建设部《市政桥梁工程质量检验评定标准》GJJ2-90。
二、工艺流程:在4#与5#墩之间安装并张拉临时予拉束。
观察4#墩水平位移后拆除。
钢管拱工地组拼、整体半浮运、定位(合拢)。
灌注拱脚锚固端块混凝土。
安装水平系杆钢束。
张拉竖直粗钢管,水平系杆钢束(分批进行,详见表1)。
钢管拱肋混凝土灌住。
安装横梁。
现浇纵梁混凝土,安装预制纵梁(人行道板)。
安装预制纵梁(人行车道板)。
安装管线、栏杆、桥面铺装。
汽-20荷载动载试验。
锚固端块灌注封端混凝土。
三、钢管拱安装前的准备工作为保证钢管拱安装顺利,安装临时钢绞线束,检验4#墩的水平位移。
1.在4#墩附近古纤道上,桥轴线向西侧(向杭州方向)约60米处,塔建一座临时性的观测站,供上部结构安装期间,对4#墩进行水平位移观测。
2.观测方法:在4#墩侧面粘贴一条水平放置长约30厘米的钢卷尺,将经纬仪十字丝对准尺中部记下初读数,经纬仪固定不动,或在设计院同意的情况下,也可用其他仪器进行测量。
变截面锥形集束钢管拱制作技术

变截面锥形集束钢管拱制作技术摘要:肋拱桥中拱肋一般采用哑铃形断面、横向哑铃形桁拱断面和多肢桁式(格构式)断面的钢管混凝土肋拱形式,芜湖袁泽桥在我国首次采用了变截面锥形集束钢管混凝土肋拱的结构形式。
介绍芜湖袁泽桥钢管拱的制作工艺、大跨径空间变截面钢管拱的线形控制,以及在施工过程中焊接工艺、预拼装工艺的优化措施。
关键词:空间变截面;钢管拱;制造工艺;菱形截面;线形控制;变形控制1 概述芜湖袁泽桥采用带副拱的中承式钢管混凝土拱桥(图1),拱肋由主拱和副拱组成,主梁采用钢格构叠合梁模式。
图1 芜湖袁泽桥效果主拱轴线形采用悬链线,理论拱轴线拱脚水平距离L=135 m,矢高为30 m,矢跨比1∶4.5,拱轴系数m=1.5;两拱肋轴线横向距离为26.75 m。
主拱拱肋采用钢管混凝土结构,共由上、下、左、右4根钢管和腹板组成。
上、下钢管管径及拱肋外形尺寸沿X轴(顺桥向)按1.7次抛物线方程变化;管间采用正交异性加劲双腹板构造,其中内腹板设置于各肢钢管轴心连接线上,外设间距为340 mm、高度为150 mm的U形加劲肋,外侧再设置1道外腹板。
钢管及腹腔内填C50微膨胀混凝土。
拱肋桥面以上设置了7道人字形风撑。
为了使单幅桥内外侧主拱肋在桥面上、下结构一致,内、外侧主拱肋标高差由带2%横坡的24.45 m水平间距产生,即高差为0.489 m;风撑内侧高、外侧低,实际横向坡度为1.83%。
2 结构特点主桥构造布置如图2所示,主拱拱肋左、右侧钢管为等截面钢管,直径0.7 m,壁厚为20~16 mm。
上、下钢管采用变径截面,如图3所示,拱脚(理论IP点)处直径1.073 m、壁厚25 mm;拱顶截面直径0.7 m,壁厚16 mm;拱脚(理论IP点)处拱肋宽2.2 m、高3.1 m,拱顶处拱肋宽1.7 m、高2.0 m;主拱单拱拱肋划分为11个拱段,全桥共有44个拱段,其中F拱段为合龙段,最大拱段质量约13.5 t。
1—飞燕;2—主墩;3—主拱;4—副拱;5—风撑1;6—风撑2;7—风撑3;8—风撑4。
主拱肋制造工艺

主拱肋制造工艺大桥主桥(m跨)主拱肋为空间桁架结构。
拱肋钢管主桁架为全焊接结构,其焊接质量和结构空间几何尺寸及线型的要求都很高。
在施工设计图中,将156m跨拱肋分为6个拱肋节段,在现场安装过程中,按拱度坐标要求,逐一将拱肋节段起吊安装,待整体安装完毕,各检查点拱度坐标调整到位后再进行焊接固定,这就决定了各吊装节段制造过程中的高精度要求。
根据设计要求及制造、安装特点,主拱肋制造对其拱形线性精度、节段与节段之间联接的匹配精度、吊杆锚固及横撑安装位置精度和焊接质量等是关键质量要素。
影响这些质量的因素也很多,有下料切割、弦管煨变、相贯线加工、工装胎具制、组装合样和焊接变形控制等,涉及到每道工序。
为保证制造质量,我们将根据各工序的工艺特点,分别制定相应的工艺技术措施,设置关键质量控制点。
因此,针对该桁架的结构特点、质量及精度要求,我厂按精度控制技术、成组制造技术以及工艺相似性和结构相似性原理,将拱肋桁架吊装节段的制造实行多条流水线分道平行作业,其工艺流程如下:一、主拱肋制造工艺简介(1)材料采购及复验钢管拱桁架结构制造用料,如钢管、钢板、焊接材料及涂装材料等应符合设计文件的要求和现行标准的规定。
其中直缝焊接钢管和钢板按规定尺寸要求采购,尽量避免对接焊缝。
材料供应商须经评审合格。
所有材料除必须提供完整的材料质量证明书和产品合格证外,还应进行复验,复验合格者方可办理入库手续。
如果受供应商或运输条件限制,直缝焊接钢管和钢板不能按尺寸供应时,工厂将采用埋弧自动焊对接。
直缝焊接钢管对接在焊接转胎上进行,其内环缝采用CO2气体保护电弧焊封底焊接。
材质复验及直缝焊接管直径控制是该工序质量控制的关键。
(2)零件放样、下料及加工工厂根据设计院提供的设计图和有关文件绘制施工图,并编制制造工艺。
施工者根据施工图和制造工艺对零件进行放样,全部零件应做好标识。
①零件的放样:A、板类零件直接或用样板放样,放样前钢板应进行机械校平处理。
钢管混凝土系杆拱桥施工技术难点及对策
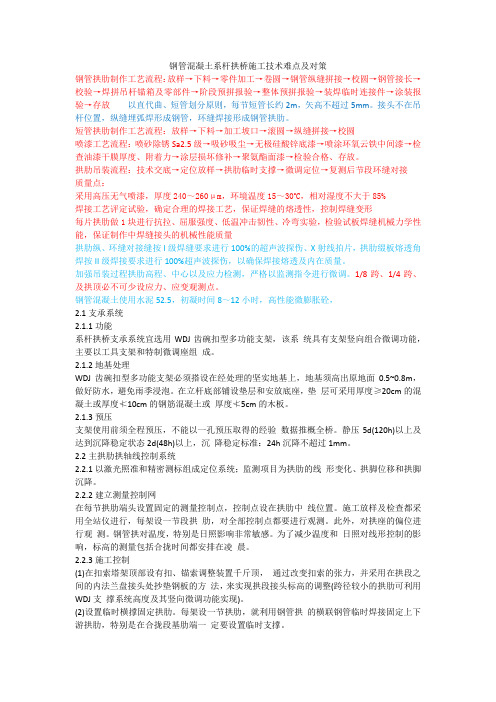
钢管混凝土系杆拱桥施工技术难点及对策钢管拱肋制作工艺流程:放样→下料→零件加工→卷圆→钢管纵缝拼接→校圆→钢管接长→校验→焊拼吊杆锚箱及零部件→阶段预拼报验→整体预拼报验→装焊临时连接件→涂装报验→存放以直代曲、短管划分原则,每节短管长约2m,矢高不超过5mm。
接头不在吊杆位置,纵缝埋弧焊形成钢管,环缝焊接形成钢管拱肋。
短管拱肋制作工艺流程:放样→下料→加工坡口→滚圆→纵缝拼接→校圆喷漆工艺流程:喷砂除锈Sa2.5级→吸砂吸尘→无极硅酸锌底漆→喷涂环氧云铁中间漆→检查油漆干膜厚度、附着力→涂层损坏修补→聚氨酯面漆→检验合格、存放。
拱肋吊装流程:技术交底→定位放样→拱肋临时支撑→微调定位→复测后节段环缝对接质量点:采用高压无气喷漆,厚度240~260μm,环境温度15~30o C,相对湿度不大于85%焊接工艺评定试验,确定合理的焊接工艺,保证焊缝的熔透性,控制焊缝变形每片拱肋做1块进行抗拉、屈服强度、低温冲击韧性、冷弯实验,检验试板焊缝机械力学性能,保证制作中焊缝接头的机械性能质量拱肋纵、环缝对接缝按I级焊缝要求进行100%的超声波探伤、X射线拍片,拱肋缀板熔透角焊按II级焊接要求进行100%超声波探伤,以确保焊接熔透及内在质量。
加强吊装过程拱肋高程、中心以及应力检测,严格以监测指令进行微调。
1/8跨、1/4跨、及拱顶必不可少设应力、应变观测点。
钢管混凝土使用水泥52.5,初凝时间8~12小时,高性能微膨胀砼,2.1支承系统2.1.1功能系杆拱桥支承系统宜选用WDJ齿碗扣型多功能支架,该系统具有支架竖向组合微调功能,主要以工具支架和特制微调座组成。
2.1.2地基处理WDJ齿碗扣型多功能支架必须搭设在经处理的坚实地基上,地基须高出原地面0.5~0.8m,做好防水,避免雨季浸泡。
在立杆底部铺设垫层和安放底座,垫层可采用厚度≥20cm的混凝土或厚度≮10cm的钢筋混凝土或厚度≮5cm的木板。
2.1.3预压支架使用前须全程预压,不能以一孔预压取得的经验数据推概全桥。
钢管混凝土拱桥钢管拱肋加工与控制
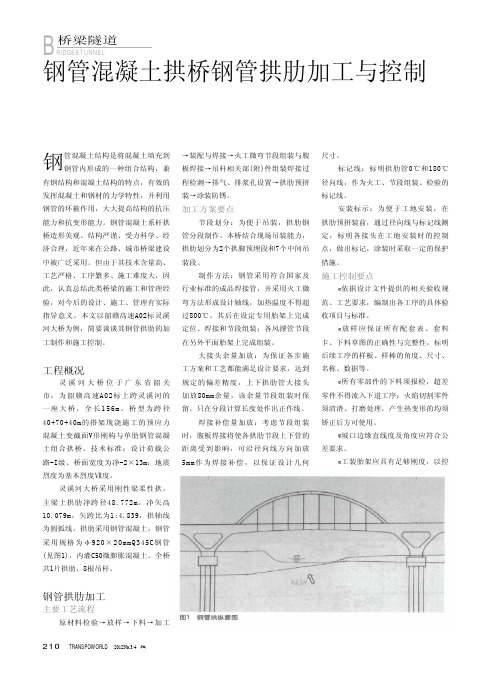
焊工要求:必须取得特种作业操 作证,经试焊合格后,方可独立上岗 操作。 焊接要求
工程概况
灵溪河大桥位于广东省韶关 市,为韶赣高速A02标上跨灵溪河的 一座大桥,全长156m。桥型为跨径 40+70+40m的搭架现浇施工的预应力 混凝土变截面V形刚构与单肋钢管混凝 土组合拱桥。技术标准:设计荷载公 路-I级、桥面宽度为净-2×13m;地震 烈度为基本烈度Ⅶ度。
灵溪河大桥采用刚性梁柔性拱, 主梁上拱肋净跨径48.772m,净矢高 10.079m,矢跨比为1:4.839,拱轴线 为圆弧线。拱肋采用钢管混凝土,钢管 采用规格为φ920×20mmQ345C钢管 (见图1),内灌C50微膨胀混凝土。全桥 共1片拱肋、8根吊杆。
工厂焊缝:灵溪河大桥拱肋钢管 制作、装配时,其纵缝、环缝均采用 V型坡口,单面焊接双面成形,反面 (管内)贴陶质衬垫。焊缝填充工艺分四 道,采用CO2气体保护焊打底填充两
道,埋弧自动焊填充一道、盖面一道。 纵缝焊接的起止端分别安装引弧板和熄 弧板,坡口型式与纵缝相同。环缝焊接 采用滚动胎架,以俯焊方式焊接。每道 工序焊缝焊接应一次完成,因故停焊又 续焊时,不得从母材上引弧,必须将引 弧处气刨或打磨成1∶4斜坡搭接,搭接 长度不少于50mm。
控制要点: 确保上胎架的待弯钢管定位正
确,即钢管径向线及其中心线应与胎架 纵向中心线及中线相吻合。
制订出周密的专业性测量工艺, 检测仪器须经计量部门检验合格,操作 时考虑环境的影响。
钢管混凝土拱桥的施工方法和结构设计

钢管混凝土拱桥的施工方法钢管砼结构,由于能通过互补使钢管和混凝土单独受力的弱点得以削弱甚至消除,管内混凝土可增强管壁的稳定性,钢管对混凝土的套箍作用,使砼处于三向受力状态,既提高了混凝土的承载力,又增大了其极限压缩应变,所以自钢管砼结构问世以来,是桥梁建筑业发展的一项新技术,具有自重轻、强度大、抗变形能力强的优点,因而得到突飞猛进的发展。
在桥梁方面,已以各种拱桥发展到桁架梁等结构形式,并发展到钢管混凝土作劲性骨架拱桥。
其施工方法发展很快,已经应用的有无支架吊装法,支架吊装法,转体施工法等。
1 拱肋钢管的加工制作拱肋加工前,应依理论设计拱轴座标和预留拱度值,经计算分析后放样,钢管拱肋骨架的弧线采用直缝焊接管时,通常焊成 1.2-2.0m的基本直线管节;当采用螺旋焊接管时,一般焊成12.0~20m弧形管节。
对于桁式拱肋的钢管骨架,再放样试拼,焊成10m左右的桁式拱肋单元,经厂内试拼合格后即可出厂.具体工艺流程为:选材料进场材料分类材质确认和检验划线与标记移植编号码下料坡口加工钢管卷制组圆、调圆焊接非坡口检验附件装配、焊接单节终检组成10m左右的大节桁式拱肋焊接无损检验大节桁式拱肋终检 1:1大样拼装检验防腐处理出厂。
当拱肋截面为组合型时,应在胎模支架上组焊骨架一次成型,经尺寸检验和校正合格后,先焊上、下两面,再焊两侧面(由两端向中间施焊).焊接采用坡口对焊,纵焊缝设在腔内,上、下管环缝相互错开。
在平台上按1:1放样时,应将焊缝的收缩变形考虑在内。
为保证各节钢管或其组合骨架拼组后符合设计线型,可在各节端部预留1cm左右的富余量,待拼装时根据实际情况将富余部分切除。
钢管焊接施工以“GBJD05-83、钢结构施工和施工及验收规范”的规定为标准.焊缝均按设计要求全部做超声波探伤检查和X射线抽样检查(抽样率大于5%)。
焊缝质量应达到二级质量标准的要求。
2 钢管混凝土拱桥的架设2.1无支架吊装法2。
1。
1缆索吊机斜拉扣挂悬拼法具体做法与其他拱肋的架设相似,只是钢管混凝土拱肋无支架架设方案用于较大跨度,它可根据吊机能力把钢管拱肋合成几大段进行分段对称吊装,并随时用扣索和缆风绳锚固,稳定在桥位上,最后合拢。
- 1、下载文档前请自行甄别文档内容的完整性,平台不提供额外的编辑、内容补充、找答案等附加服务。
- 2、"仅部分预览"的文档,不可在线预览部分如存在完整性等问题,可反馈申请退款(可完整预览的文档不适用该条件!)。
- 3、如文档侵犯您的权益,请联系客服反馈,我们会尽快为您处理(人工客服工作时间:9:00-18:30)。
钢管拱制造工艺
摘要:介绍钢管拱制造一般工艺。
关键词:钢管拱;主拱肋;工艺
Abstract:It introduces the pipeline arch manufacturing process.
Keywords: pipeline arch, main arch, process
钢管拱桥主拱肋一般为空间桁架结构。
拱肋钢管主桁架为全焊接结构,其焊接质量和结构空间几何尺寸及线型的要求都很高。
根据设计要求及制造、安装特点,主拱肋制造对其拱形线性精度、节段与节段之间联接的匹配精度、吊杆锚固及横撑安装位置精度和焊接质量等是关键质量要素。
影响这些质量的因素也很多,有下料切割、弦管煨变、相贯线加工、工装胎具制、组装合样和焊接变形控制等,涉及到每道工序。
为保证制造质量,将根据各工序的工艺特点,分别制定相应的工艺技术措施,设置关键质量控制点。
因此,针对钢管拱桁架的结构特点、质量及精度要求,按精度控制技术、成组制造技术以及工艺相似性和结构相似性原理,将拱肋桁架吊装节段的制造实行多条流水线分道平行作业,其工艺大致如下:
一、主拱肋制造工艺
1材料采购及复验
钢管拱桁架结构制造用料,如钢管、钢板、焊接材料及涂装材料等应符合设计文件的要求和现行标准的规定。
其中直缝焊接钢管和钢板按定尺要求采购,尽量避免对接焊缝。
材料供应商须经评审合格。
所有材料除必须提供完整的材料质量证明书和产品合格证外,还应进行复验,复验合格者方可办理入库手续。
如果受供应商或运输条件限制,直缝焊接钢管和钢板不能按定尺供应时,工厂将采用埋弧自动焊对接。
直缝焊接钢管对接在焊接转胎上进行,其内环缝采用CO2气体保护电弧焊封底焊接。
材质复验及直缝焊接管直径控制是该工序质量控制的关键。
2零件放样、下料及加工
根据设计院提供的设计图和相关文件绘制施工图,并编制制造工艺。
施工者根据施工图和制造工艺对零件进行放样,全部零件应做好标识。
(1).零件的放样:①板类零件直接或用样板放样,放样前钢板应进行机械校平处理。
②管类零件用微机制图做出样板放样。
(2).零件的下料及加工:①板类零件可以直接用精密数控等离子切割机或多头切割机精密切割下料,对板厚在12mm以下的板零件,也可用剪切方法下料,
但剪切后加工剪切边缘,消除因剪切可能产生的微裂纹。
②连接板钻孔直接用精密数控钻床完成。
③管类零件以钢管中线为基准,用样板划两端相贯线。
允许用氧乙炔焰精密切割完成,或初步切割后再用相贯线组合加工机床加工完成,然后再按焊接要求制作焊接坡口。
本工序对下料精度的控制,特别是对钢管相贯线精度及其坡口尺寸精度的控制是质量控制的关键。
3弦管煨弯
(1)根据设计要求合理分配弦管对接位置,确定对接弦管长度。
(2)用微机制图,计算出各弦管拱形曲线的控制点。
相邻控制点间距不超过1000mm,以保证获得连续的曲线。
(3)在工厂自制的特大型弯管设备,全液压--远红外自动弯管机上,按给定的控制点,调节煨弯工艺拱度曲线、安装弦管及辅件,煨弯弦管。
(4)热煨弯温度应设定在720-780度。
在此温度下,金属处于塑性状态,通过液压顶推装置缓慢地施加一定的外力,使钢管发生弯曲变形。
煨弯加热位置由钢管中间向两端移动,每处煨弯量根据预拱曲线确定,并通过调节钢管夹持装置进行控制。
(5)在工作平台上根据弦管预拱曲线按1:1比例放大样,待煨弯的钢管完全冷却至室温后将其放在平台上合样检查,并辅之以局部火焰矫正,使其精度达到要求,同时做上基准线及编号等标识,以利下步工作。
钢管煨弯工艺的关键在于:①严格控制各点加热温度,过高或过低都不适宜。
②煨弯是渐进的,过程控制必须严格,各点弯曲量及加载速度必须严格控制。
③煨弯后合样检查和调整,是保证弦管拱形曲线符合要求的不可缺少的控制措施。
4胎架制造
根据设计图样及组拼装工艺方法,设计制造主拱肋节段桁架组拼装胎架、“K”形及“米”形横撑组拼装胎架,胎架线型值由计算机提供,胎架必须牢固可靠,各种标记(中心线、检查线、轮廓线等)齐全,并作出明显样冲印记,施工时根据胎架设计图纸进行制造。
5主拱肋节段拱圈桁架组拼装
(1)、拱肋节段桁片的组拼及焊接(小拼)
在钢制平台上的钢制胎架内进行拱肋节段桁片(腹杆与上、下弦管所组成的
平面单元)的组拼及焊接。
①按桁片构造图制作地样,放上、下主弦管的位置线及直腹管的位置线,安装好定位板并确认。
②将上、下主弦管按地样位置分别定位,复查弦管间的尺寸,复查桁片上、下弦管的预拱曲线。
③直腹管按地样位置分别定位。
④再全面复查桁片各部位的拼装尺寸,确认后做好记录。
⑤焊接:桁片点固后按施焊顺序焊接。
⑥焊接检验。
⑦合样及校正:上拼装平台合样检验,检查弦管椭园度、弦管中心组合误差及对角线误差,矫正达图纸要求,并作好记录。
⑧划线:划上、下主弦管端口的十字中心线及安装吊索扣点的位置线,并打样冲,作好标识。
⑨检验。
⑩编号并作好标识。
该工序的关键控制点是:两弦管之中心距精度;组焊后拱肋节段桁片单元之扭曲和拱形曲线精度;腹杆与弦管之焊接质量。
(2)、拱肋节段组装及焊接(中拼)
拱肋节段的组装及焊接在专用拼装胎架上进行。
①将一片拱肋节段桁片吊入胎架,定位好后固定。
②将节段内上、下弦管单元的上横联盖板、缀板、平联板(或管)吊入并定位。
③将相应的另一片拱肋节段桁片吊入胎架并定位固定,使横联盖板、缀板、平联板(或管)与上、下弦管密贴。
④再全面复查拱肋节段各部位的拼装尺寸,确认后并作好记录。
⑤焊接:点固后在胎模中按施焊顺序对称施焊。
⑥拱肋节段内上、下弦管单元的上盖板、缀板、平联板(或管)拼装完成后,再将拱肋节段翻身并固定在专用拼装胎架上,然后再吊入上、下弦管单元的下盖板并定位,使下盖板与上、下弦管密贴。
焊接方法同上。
⑦校正及检验。
⑧节段端口联接部位的确认。
⑨用手工气割方法修割弦管端部,至符合要求。
⑩节段间联接部位的制备。
⑾交验。
⑿编号并作好标识
该工序控制要点:节段拱形曲线精度;缀板与弦管的焊缝焊接质量;节段端口的尺寸精度。
(3)单拱肋节段接头组装定位(预拼)
为了保证拱肋节段间的精密配合,确保节段的准确定位,达到拱肋总拼后拱轴线符合设计要求,必须进行拱肋节段与节段间的预拼装,预拼装方式为半孔平卧式。
在拱肋节段预拼装阶段,主要完成相邻拱肋阶段配合精度及弦管连接结合精度的调整工作,确保相邻拱肋阶段结合面的配合精度,使弦管弧线正确无误并光顺一致。
预拼在胎架上进行,按半孔拱肋节段为一组进行预拼。
预拼胎架制造→第一节段拱肋上胎架→调整水平拱度等尺寸→定位→检验→第二节段拱肋上胎架→调整水平拱度等尺寸→定位→检验→第三节段拱肋上胎架→调整水平拱度等尺寸→定位→检验→预栓接→相邻节段间的结合焊→检验→打上各种标识→ 双件拱肋预拼准.
该工序关键控制点:主拱圈的拱轴曲线精度;拱脚连接法兰座、横撑、吊杆锚座的位置精度;焊接质量。
(4)、双拱肋试装(大拼)
为了同段拱肋节段间横撑的拼装。
在拱肋节段与横撑总拼装阶段,主要完成拱肋节段弦管与横撑连接管(件)的定位及焊接工作,确保拱肋节段与横撑的结合精度。
预拼胎架制造→ 一件拱肋上胎架定位→“K”型横撑、“米”型横撑、单元上胎架定位→ 相对应的另一件拱肋上胎架定位→调整水平拱度等尺寸→ 横撑座管装焊→ 临时连接试装→检验→ 解体→发运前准备→ 发运.
以钢管十字线为基准,在工作平台上,调整好两拱肋相对距离(确定左右位置)并使相应节段中心线重合(确定前后高低位置),试装横撑,验证、调整横撑座位置并焊接。
二、横撑组件制造
根据设计要求在工作平台上放出1:1大样图,按与主拱肋相似的方法组装焊接。
横撑制造的关键是严格控制与拱肋连接的端口尺寸精度和焊接质量。
1“K”型横撑单元件制造
“K”型横撑组拼装(平面桁片和立体组拼)胎架制造→左横撑主管上胎架定位→桁片平联杆装配→右横撑主管上胎架定位组装成片体→焊接→修磨、校正→检验→ 将四个片体上“K”型横撑组拼装胎架定位斜杆装配定位→焊接→ 检验→吊点及临时支撑装焊→预拼前的准备。
2“米”型横撑单元件制造
“米”型横撑组拼装(平面桁片和立体组拼)胎架制造→ 左横撑主管上胎架定位→ 桁片平联杆装配→右横撑主管上胎架定位组装成片体→焊接→ 修磨、校正→ 检验→ 将一个片体上“米”型横撑组拼装胎架定位→斜杆装配定位→焊接→检验→吊点及临时支撑装焊→预拼前的准备。
三、结束语
终上所述,进一步收集该类型结构的制造工艺,对今后学习具有重要帮助。