钢管工艺
钢管生产工艺流程

钢管生产工艺流程钢管是指由钢坯经过加热、穿孔、成型、焊接、脱鳞、校直、切割、除锈等工艺加工而成的管材。
以下是钢管生产的工艺流程:第一步:材料准备钢管的制造过程以钢坯作为原材料。
钢坯可以是热轧钢板、冷轧钢板、热轧带钢或冷轧带钢等。
钢坯经过切割和检验后,进入下一步的加工准备阶段。
第二步:加热钢坯需要通过炉加热来提高其可塑性,以便后续的加工操作。
加热可采用火焰加热、电阻加热或电磁感应加热等方式。
第三步:穿孔加热后的钢坯被送入穿孔机,通过圆锥工具的旋转和下压,形成一个中空的管状形状。
穿孔可以分为冷轧穿孔和热轧穿孔两种方法。
第四步:成型穿孔后的钢坯进入成型机,通过连续滚轧或循环滚轧,使其成为长条状的管材。
这个过程将会通过一系列的传送辊和辊轧将钢坯变形成圆形。
第五步:焊接成型后的圆管经过焊接机焊接,形成钢管。
焊接可以采用多种方法,如电阻焊、气焊、电弧焊等。
第六步:脱鳞焊接后的钢管表面上会形成一层氧化皮和焊渣,需要经过脱鳞工艺进行清除。
脱鳞可以采用化学脱鳞、机械脱鳞或水压脱鳞等方法。
第七步:校直脱鳞后的钢管需要经过校直机进行校直,以保证钢管的外形尺寸及内外表面质量。
第八步:切割校直后的钢管被送入切割机,根据需求进行切割成不同的长度。
第九步:除锈切割后的钢管进行除锈处理,以去除表面的铁锈和污垢。
除锈可以采用酸洗、机械刷洗等方法进行。
以上就是钢管生产的主要工艺流程。
钢管生产过程中需要严格的控制各道工序的操作参数,确保钢管的质量和性能。
随着技术的进步,钢管生产工艺不断改进,以提高钢管的质量和效率。
冷轧钢管生产工艺
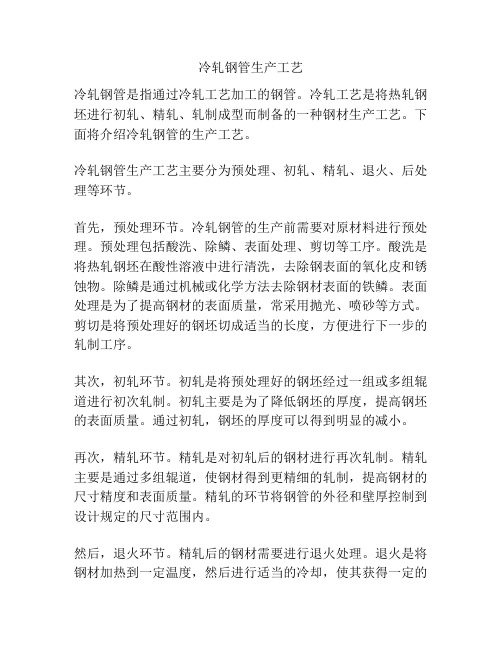
冷轧钢管生产工艺冷轧钢管是指通过冷轧工艺加工的钢管。
冷轧工艺是将热轧钢坯进行初轧、精轧、轧制成型而制备的一种钢材生产工艺。
下面将介绍冷轧钢管的生产工艺。
冷轧钢管生产工艺主要分为预处理、初轧、精轧、退火、后处理等环节。
首先,预处理环节。
冷轧钢管的生产前需要对原材料进行预处理。
预处理包括酸洗、除鳞、表面处理、剪切等工序。
酸洗是将热轧钢坯在酸性溶液中进行清洗,去除钢表面的氧化皮和锈蚀物。
除鳞是通过机械或化学方法去除钢材表面的铁鳞。
表面处理是为了提高钢材的表面质量,常采用抛光、喷砂等方式。
剪切是将预处理好的钢坯切成适当的长度,方便进行下一步的轧制工序。
其次,初轧环节。
初轧是将预处理好的钢坯经过一组或多组辊道进行初次轧制。
初轧主要是为了降低钢坯的厚度,提高钢坯的表面质量。
通过初轧,钢坯的厚度可以得到明显的减小。
再次,精轧环节。
精轧是对初轧后的钢材进行再次轧制。
精轧主要是通过多组辊道,使钢材得到更精细的轧制,提高钢材的尺寸精度和表面质量。
精轧的环节将钢管的外径和壁厚控制到设计规定的尺寸范围内。
然后,退火环节。
精轧后的钢材需要进行退火处理。
退火是将钢材加热到一定温度,然后进行适当的冷却,使其获得一定的力学性能和组织结构。
退火可以改善钢材的塑性和韧性,提高其加工性能。
退火后的钢材还需要进行后处理,如酸洗、抛光等工序,以提高表面质量。
最后,进行质检和包装。
经过上述工序后的冷轧钢管需进行质量检查,包括外观检查、尺寸检查、机械性能检验等。
合格的钢管进行包装,包括喷油、套塑料膜等,以保证产品质量。
以上就是冷轧钢管生产工艺的主要环节。
冷轧工艺通过多道轧制和退火处理,可以大幅提高钢管的尺寸精度和表面质量,使其更适用于需要高精度、高质量的领域。
钢管热处理工艺流程
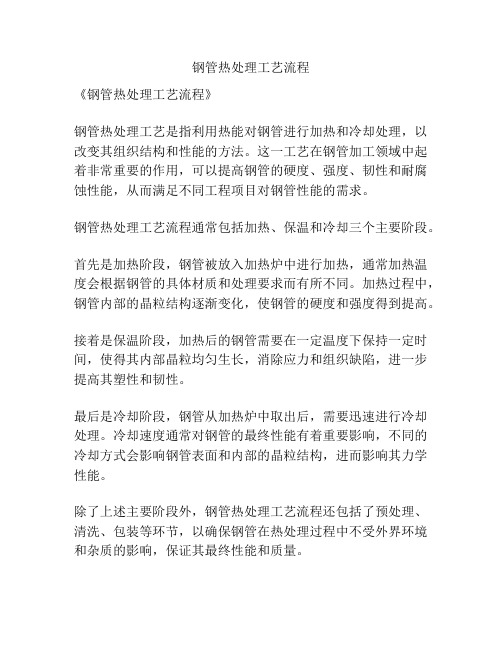
钢管热处理工艺流程
《钢管热处理工艺流程》
钢管热处理工艺是指利用热能对钢管进行加热和冷却处理,以改变其组织结构和性能的方法。
这一工艺在钢管加工领域中起着非常重要的作用,可以提高钢管的硬度、强度、韧性和耐腐蚀性能,从而满足不同工程项目对钢管性能的需求。
钢管热处理工艺流程通常包括加热、保温和冷却三个主要阶段。
首先是加热阶段,钢管被放入加热炉中进行加热,通常加热温度会根据钢管的具体材质和处理要求而有所不同。
加热过程中,钢管内部的晶粒结构逐渐变化,使钢管的硬度和强度得到提高。
接着是保温阶段,加热后的钢管需要在一定温度下保持一定时间,使得其内部晶粒均匀生长,消除应力和组织缺陷,进一步提高其塑性和韧性。
最后是冷却阶段,钢管从加热炉中取出后,需要迅速进行冷却处理。
冷却速度通常对钢管的最终性能有着重要影响,不同的冷却方式会影响钢管表面和内部的晶粒结构,进而影响其力学性能。
除了上述主要阶段外,钢管热处理工艺流程还包括了预处理、清洗、包装等环节,以确保钢管在热处理过程中不受外界环境和杂质的影响,保证其最终性能和质量。
总之,钢管热处理工艺流程是一个综合性的加工过程,需要严格控制各个环节的参数和操作,以确保钢管能够达到设计要求的性能,并满足使用需求。
只有专业的工艺流程和严密的操作才能保证钢管的质量和稳定性。
钢管生产工艺

3.3无缝钢管工艺流程图
四、焊管生产工艺
4.1焊接钢管
定义
• ◆焊接钢管即有缝钢管,其生产是将管坯(钢板和钢带)用各种
成型方法弯卷成要求的横断面形状和尺寸的管筒,再用不同的焊 接方法将焊缝焊合而得到钢管的过程
特点 • 产品精度高,尤其是壁厚精度 • 主题设备简单,占地小 • 生产上可以连续化作业 • 生产灵活、机组的产品范围宽
4.2.1直缝高频焊管(ERW)
将热轧卷板经过成型机成型后,利用 高频电流的集肤效应和邻近效应,使管坯 边缘加热熔化,在挤压辊的作用下进行 压力焊接来实现生产的
பைடு நூலகம்
4.2.2高频焊管工艺流程图
4.3.1螺旋钢管生产工艺
1、螺旋钢管原材料即带钢卷、焊丝、焊剂。 2、成型前带钢经过矫平、剪边、刨边,表面清 理输送和予弯边处理。 3、采用焊缝间隙控制装置来保证焊缝间隙满足 焊接要求,管径、错边量和焊缝间隙都得到严 格的控制。 4、切成单根钢管后,每批钢管头三根要进行严 格的首检制度,检查焊缝的力学性能,化学成 份,溶合状况,钢管表面质量以及经过无损探 伤检验,确保制管工艺合格后,才能正式投入 生产。
4.4.2.1UOE直缝埋弧焊管成型工艺
UOE直缝埋弧焊钢管成型工艺的三大主成形工序包括: 钢板预弯边、U 成型及O 成型。各工序分别采用专用的成 型压力机,依次完成钢板边部预弯、U成型及O成型三道工 序,将钢板变形成为圆形管筒。如图:
4.4.2.2JCOE直缝埋弧焊管成型工艺
成型:在JC0 成型机上经过多次步进冲压,首先将钢板的一半压 成“J,,形,再将钢板的另一半压成“J”开,形成 C”形, 最后从中部加压从而形成开口的“0”形管坯。如图:
4.4.3直缝埋弧焊钢管生产工艺流程图
钢管敷设工艺

钢管敷设工艺钢管是一种广泛应用于建筑、工业和市政工程中的重要材料,其敷设工艺对于项目的安全性和持久性至关重要。
本文将介绍钢管敷设的工艺流程以及相关注意事项。
一、材料准备在进行钢管敷设之前,需要准备以下材料:1. 钢管:根据工程要求选择适当的规格和材质的钢管。
2. 弯头和三通等管件:根据管道设计需要选择和准备相应的管件。
3. 焊接材料:包括焊接电极、焊接剂和涂层材料等。
4. 通气和排气设备:包括放气阀、压力表和检测设备等。
二、施工准备在进行钢管敷设之前,需要进行以下施工准备工作:1. 清理施工现场:清除施工区域内的杂物和障碍物,确保施工场地干净和安全。
2. 标志和测量:根据设计要求,在施工场地内标记出管道的位置和长度,并进行测量和记录。
3. 搭建支架和脚手架:根据需要,在施工区域内搭建支架和脚手架,以便于安装和固定钢管。
三、钢管敷设1. 钢管切割:根据设计要求,使用钢管切割机等工具将钢管切割成适当的长度。
2. 钢管配件安装:按照设计要求,在钢管的两端安装相应的配件,如弯头、三通等。
3. 钢管固定:使用焊接等方法,将钢管和配件固定在支架上,并保证其垂直度和水平度。
4. 焊接连接:根据设计要求,采用埋弧焊接、气体保护焊接等方法进行钢管的连接。
5. 检查和测试:在钢管敷设完成后,进行系统的检查和测试,确保管道的质量和安全性。
四、安全注意事项在进行钢管敷设工艺时,需要注意以下安全事项:1. 使用合适的个人防护装备:包括头盔、手套、防护眼镜等,确保施工人员的安全。
2. 注意防火防爆:钢管敷设过程中,应注意防止火花和明火接触,避免引发火灾或爆炸事故。
3. 检查气体泄漏:在敷设过程中,要定期检查气体泄漏情况,确保施工场地的安全。
4. 注意施工操作:施工人员应严格按照工艺要求进行操作,避免操作不当引发事故。
综上所述,钢管敷设工艺是一项复杂而重要的工程环节,其正确施工将保证管道的质量和使用寿命。
施工人员在进行钢管敷设时应严格按照工艺要求进行操作,并注意安全事项,确保施工过程的安全和高效。
钢管的铸造和锻造工艺
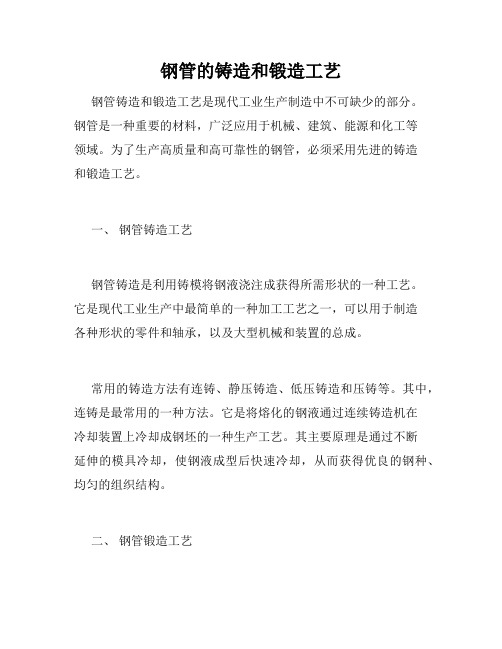
钢管的铸造和锻造工艺钢管铸造和锻造工艺是现代工业生产制造中不可缺少的部分。
钢管是一种重要的材料,广泛应用于机械、建筑、能源和化工等领域。
为了生产高质量和高可靠性的钢管,必须采用先进的铸造和锻造工艺。
一、钢管铸造工艺钢管铸造是利用铸模将钢液浇注成获得所需形状的一种工艺。
它是现代工业生产中最简单的一种加工工艺之一,可以用于制造各种形状的零件和轴承,以及大型机械和装置的总成。
常用的铸造方法有连铸、静压铸造、低压铸造和压铸等。
其中,连铸是最常用的一种方法。
它是将熔化的钢液通过连续铸造机在冷却装置上冷却成钢坯的一种生产工艺。
其主要原理是通过不断延伸的模具冷却,使钢液成型后快速冷却,从而获得优良的钢种、均匀的组织结构。
二、钢管锻造工艺钢管锻造是通过应用压力、力和温度等制造所需的形状的一种工艺。
这种工艺可以改变钢的物理和化学性质,从而提高其机械性能和耐磨性。
常用的锻造方法有自由锻、轧制锻造、环轧锻造、坯锻造和模锻等。
其中,自由锻造是最古老的锻造方法之一,也是最常用的一种方法。
它是将钢坯放在锻造装置上,并利用偏置、锤头等力量将钢坯加工成所需的形状。
三、钢管铸造与锻造工艺的比较钢管铸造和锻造工艺各自都有其优点和不足。
铸造工艺可以生产大量的产品,并能够制造复杂的零件和轴承。
而锻造工艺可以提高钢的机械性能,并能够生产更加精确的产品。
铸造工艺的缺点是其所生产的产品易受缺陷和杂质等因素的影响。
而锻造工艺的缺点则是其所生产的产品往往较小和比较难制造。
综上所述,钢管铸造和锻造工艺在现代工业生产中都扮演着重要的角色。
它们各自具有其独特的优点和不足,可以根据生产需要进行选择和应用。
无论是铸造还是锻造,都需要采用先进的工艺和设备,以确保生产出质量稳定,性能优良的钢管产品。
第二节 钢管施工工艺

第二节钢管施工工艺一、钢管安装工艺流程原水管线部分和设计点以后钢管单管部分施工采用单工作面流水推进作业,在设计点之间区段,两根管道前后错开一根钢管的长度同时施工。
测量放线→沟槽开挖→运输、铺筑轨道→钢管材料及内外防腐涂装→吊装设备就位→钢管管吊装入槽→待装管顶升对中→清口套胶圈涂润滑油→钢管焊接→内拉法安装→接头试压→进行下一节管道安装→测量复核→接头→沟槽回填→钢管砂浆内防腐层。
二、沟槽开挖及施工准备监理控制要点1、设计点位以后单管线钢管部分,采用机械开挖人工清底。
沟槽开挖按下图所示。
确定管沟上口宽,下底宽,焊接部位的工作坑(1.0m×1.2m)机械开挖,人工修整如图示。
钢管双管道施工征地范围内,管沟开挖下底设计宽度,上口设计宽度。
沟槽开挖前,由现场技术员进行测量放线,然后由工程部组织人员进行复核合格后方可进行土方开挖。
管沟开挖时采取分层开挖,开挖范围内的上层地表耕作土单独堆放在最外侧,管道施工完毕后再恢复到原地表位置。
下层土壤开挖时分层厚度一般不超过2米,在农田中开挖遇坑壁稳定性较差时,采取钢板桩等支撑等方式保持沟槽的稳定。
2、管道基础的处理在原水管道部分地层基础较好,原管沟表层平整后可直接作为管道基础。
钢管双管道部分设计段,原土层为粘土层,开挖时不扰动原状土情况下可不做垫层;在设计段点段,和D点以后段管道基本在农田中,主要是淤泥质粘土段,在原土上铺200mm厚粗砂垫层。
部分靠近溪流小河等地段管线,地下水比较丰富地层主要主要是含水率较高的淤泥质粘土,或其他土质条件较差地段,采用先铺一层竹排,再铺200mm厚粗砂垫层。
三、钢管材料及内外防腐涂装监理控制要点钢管材料为Q235B级热轧钢板,同一牌号、同一炉号、同一等级、同一品种、同一尺寸、同一交货状态,组成一个验收批次,每批重量不超过60T。
质保资料齐全、合格证,熔练分析表及力学性能试验表均达到GB 700-88《碳素结构钢》要求,锈蚀程度达到要求。
薄壁钢管生产工艺流程

薄壁钢管生产工艺流程如下:
1.上料、卷管。
根据用户订单需求和公司生产计划准备
不锈钢带进行下料操作,利用机组和磨具卷钢。
2.焊接。
将卷钢后的缝隙进行焊接。
3.内整平。
利用芯棒将管内壁整平。
4.打磨。
利用打磨机将管外壁打磨去除杂质。
5.光亮固溶退火。
将薄壁不锈钢焊管放入退火装置,并
加入保护气体(氢气),增加薄壁不锈钢焊管韧性,防止管件在卡压时回弹。
6.钢管微整。
再次利用机组和磨具使薄壁不锈钢焊管整
圆整直。
7.切割。
利用切割机将管材裁成客户需要的尺寸。
8.抛光打磨。
利用晶面抛光机将管材精细打磨。
9.管件实验。
进行压扁实验、扩口试验、液压试验、气
密实验、涡流探伤、晶间腐蚀试验、盐雾试验等。
10.喷码标识包装。
把生产及检查完成的薄壁不锈钢焊管
喷码、标识、包装。
- 1、下载文档前请自行甄别文档内容的完整性,平台不提供额外的编辑、内容补充、找答案等附加服务。
- 2、"仅部分预览"的文档,不可在线预览部分如存在完整性等问题,可反馈申请退款(可完整预览的文档不适用该条件!)。
- 3、如文档侵犯您的权益,请联系客服反馈,我们会尽快为您处理(人工客服工作时间:9:00-18:30)。
θ
n: 装料排数
G: 坯料的单重
思考题:计算1Cr18Ni9Ti,φ110╳1800的坯料在中径为17m炉宽4400mm 的环形炉中加热,问小时产量是多少?
二、管坯定心
(1)管坯定心:是指在管坯前端面钻孔或冲孔。
(2)定心目的:使顶头鼻部正确地对准管坯轴线,防止 穿孔时穿扁;减小毛管壁厚不均;改善 二次咬入条件。
(1)连铸圆坯:是目前国际上应用较多的坯料,也是衡量一 个国家钢管生产技术水平的标志之一。其具有成本低、 能耗少、组织性能稳定等特点,是管坯发展的主流,也 是钢管实现连轧的首要条件。
(2)轧坯:一般为圆坯,生产中也经常使用。 (3)铸(锭)坯:主要有方(锭)坯,用于P.P.M轧制方式(或压
力穿孔)。 (4)锻坯:用于穿孔性能较差的合金钢与高合金钢管的生产。
坯料加热一般遵循三个原则: ⑴ 温度准确,确保可穿性最好的温度; ⑵ 加热均匀,纵向、横向都均匀,内外温差不大 于30~50℃,最好小于15℃; ⑶ 烧损少,并且不产生有害的化学成分变化(C↑ 或C↓)。
加热温度的确定:
(1)加热温度在Fe-C相图中的单相奥氏体区 AC3线以上30~50℃,固相线以下100 ℃。即:在800~1300 ℃选 取,号钢一般1200 ℃左右。
(4)加热温度考虑工艺条件
a)GCr15 1%C(高碳钢),1.5%Cr(硬、耐磨),在 允许温度范围内取下限,防止脱碳;
b)硅钢希望脱碳,加热温度可提高;
c)超低碳不锈钢(00Cr18Ni9Ti),用于核潜艇,碳 含量越低越耐腐蚀,希望脱碳,加热温度应高些。
d)穿孔时要温升(50~80 ℃ ),塑性差的温升大, 塑性好的温升小。
④ 导盘比导板的寿命高4倍;
⑤ 高穿孔速度使顶头受热负荷的时间短,因而提高了顶头的使用寿命;
⑥ 可穿长的薄壁管;
⑦ 导盘的造价低,约为导板的1/8。
(3)双支撑的菌式穿孔机
双支撑菌式穿孔机示意图
特点:
1)轧辊轴线除与轧制线倾斜一个送进角α外, 还有一个辗轧角φ。
2)导向工具可用导板或导盘。 3)轧辊呈锥形,其直径沿穿孔变形区逐渐增大。
(2)狄舍尔穿孔机
特点:
① 主动导盘的圆周线速度(2.1~2.3m/s)大于毛管的出口速度(1.1~1.2m/s), 使其生产效率提高了(从0.7提高到0.8以上);
② 在送进角 (原始位置α=13°,可在8~13°内调节) α<15°的范围内, 金属的可穿性可提高20%以上;
③ 轧辊上下布置并采用双传动机构,较好的解决了大送进角穿孔机的主传动 布置问题,使万向接轴始终在小倾角条件下工作,既运动平稳又不易磨损;
热轧无缝管:实心管坯→穿孔→延伸 →定(减)径→冷却→精整。
焊管:板带坯料→成型(管筒状) →焊 接成管→精整。
1.3 钢管的技术要求与发展趋势
⑴ 对多种腐蚀介质的高抗蚀性、对高温强度 和低温韧性的要求越来越高,使得管材产品的 化学成分不断变化,冶炼、加工工艺不断改进;
⑵ 管材产品尺寸(壁厚精度)、形状精度的要 求促使在线检测、自动控制技术不断进步;
π
总
F p
F 0
π
D2
D2 4p π (D
2S
)2
4 4 p
0
0
式中: LP:管坯长度;
D2
D2
p
p
4D S 4S 2 4(D S )S
00
0
0
0
0
FP:管坯横断面; n:热轧管的倍齿数(根); D0,S0:成品管外径、壁厚;
L0:成品管长;
4(L L) (D S ) S
异型钢管示例
天津钢管Φ250限动芯棒连轧管机组
宝钢Φ140连轧管机组
1.2 钢管生产的基本方法
钢管生产的一般模式为:坯料→成型 →精整→一次成品→再加工→二次成品。
一般以产品的要求确定生产工艺、选 择生产设备,同时对工艺、设备不断改造 更新以适应产品 不断提高的要求。
按照成型的不同可以分成无缝管生产 和有缝管生产,而冷加工属于管材的二次 生产。
b)高合金钢等s=20~30mm, 以改善二次咬入条件;
c)对可穿性极低的钢材,可钻 通。
2.3 无缝钢管的穿孔工艺
坯料穿孔的目的:是将实心的管坯穿制成符合要求的 空心毛管。根据穿孔中金属流动变形特点,可将穿孔 方法分类如下。
三辊斜轧
管
圆轧坯 斜轧穿孔穿孔机
⑵ 火焰切割:适合大断面、合金钢等管坯,操作方便,费 用低,但金属损耗大(烧损、氧化),断面质量差。
⑶ 折断:适合Dp>φ140mm或σb>60Kg/mm2管坯。先在要 折断处切口,然后放入折断压力机中折断,支点间距一般 为(4~5) Dp。
⑷ 锯断:适合小断面管坯,合金钢及高合金钢等;是切断 质量最好的方法。
(1)环形炉的结构
(2)环型加热炉的优、缺点
优点:
1)适合加热圆形管坯,适应多种不同直径和长度的复 杂坯料;
2)管坯加热时间短、受热均匀、加热质量好; 3)炉底转动,坯料与炉底无相对滑动,氧化铁皮不易
脱落,且炉子装出料炉门在一侧,密封好,冷空气吸 入少、氧化铁皮少; 4)管坯放置位置灵活(可放料也可空出),便于更换 管坯规格,操作灵活。 5)机械化和自动化程度高。
L 0
0
0
0
P
k D2
P
△L:切头尾长(合金钢250~碳 钢450mm)
或
π(nL L) (D S ) S
L
0
0
0
0
P
kF
P
思考题:成品管φ146×15×5000mm,10#钢,用φ150坯轧制,
问坯长选多少?
三、坯料的截断方式一般有四种:
⑴ 剪断:适用于中小断面的管坯,生产效率高,费用低, 但管坯易被压扁(现场,一般压扁度不超过8~10%,切斜度 不超过6mm),对于易产生裂纹的管坯(如GCr15等),应预热 200℃~300℃。
四、剪切力计算
P K F K K F
max
1
1
2
b
K1:磨钝系数(鞍钢1.3) K2=τ/σb=0.6(碳钢)~0.8(合金)
思考题:在1000吨剪切机上冷剪20#管坯,最大直径 是多少?
(20#:σb=490.5MPa)
2.2 管坯的加热及定心
一、管坯加热
加热目的:提高塑性,降低变形抗力,为穿孔和轧管准 备良好的加工组织,改善金属的性能。
(2)加热温度考虑坯料的化学成分 a)加入Mn、Ni、Co能无限固溶于γ-Fe,奥氏体区扩大,固相线上 移,加热温度可提高; b)加入W、Mo、V、Nb等高熔点元素,加热温度可提高; c)加入Mg、Al、Cu等低熔点的元素,加热温度可降低。
(3)加热温度考虑坯料尺寸大小 大坯料在同样条件下温度应取上限,以提高加热速度。
曼乃斯曼穿孔机的环形孔型图 1-轧辊;2-导板;3-顶头;4-顶杆;5-
管坯;6-毛管
德国曼乃斯曼(Mannesmann)兄弟发 明的,瑞士工程师斯蒂弗尔(R.C Stiefeil)加以完善。
曼乃斯曼穿孔机的特点:
① 对心性好,毛管壁厚较均匀,延伸系数 μ=1.25~4.5;
② 穿孔时的变形及应力状态条件较差,毛管 内外表面易产生缺陷;
(2)做结构件:在同样重量下,钢管相 对于其他钢材具有更大的截面模数,也 就是说它具有更大的抗弯、抗扭能力, 属于经济断面钢材、高效钢材。
二、钢管的分类
1 按生产方式分类
(1)热加工管(无缝钢管):热轧穿孔、 挤压、P.P.M(压力穿孔)、冲压法;
(2)焊管(有缝钢管):包括直缝钢管 与螺旋焊管;
(3)冷加工管:冷轧、冷拔和冷旋压
2 按产品尺寸分类
(1)特厚管:D/S≤10; (2)厚壁管: D/S=10~20 (3)薄壁管: D/S=20~40 (4)极薄壁管: D/S≥40
3 其它分类
(1)用途:管道用管、结构管、石油管、 热工用管等; (2)材质: 普通碳素钢管、碳素结构钢 管、合金钢管、轴承钢管、不锈钢管等; (3)横断面形状: 圆管、异型钢管; (4)纵断面形状: 等断面、变断面
③ 轧制中旋转横锻效应大附加变形严重,能 耗大;
④ 受电机驱动条件限制,送进角较小(α< 13°,故轧制速度不快)。
送进角:轧辊轴线与轧制线在包含轧制线的垂直平面上投影之 间的夹角。
曼乃斯曼穿孔机的布置
图4-15 100穿孔机设备布置简图 1.受料槽;2.气动进料机;3.齿轮联轴节;4.主电机;5.减速齿轮座; 6.万向连接轴;7.扣瓦装置;8.穿孔机工作机座;9.翻料沟;10.顶杆小 车;11.至挡架;12.定心装置;13.升降辊;14.顶头;15穿孔机轧辊
坯料 加热 热定心 穿孔 空减 连轧 切头、尾 再加热 高压水除鳞 张力减径 冷却 切头、尾 矫直 无损探伤 表面 检查 入库
三辊轧管机组
坯料
加热 热定心 冷定心 加热
穿孔
三辊轧管 再加热
高压水除鳞
定(减)径 冷却 切断(或分锯)
矫直
热处理 表面检查 包装、入库
2.1 管坯的制备
一、根据穿孔方式、轧管方法及制管材质的不同, 一般采用以下四种坯料:
⑶ 对管材产品成本降低的要求使得其生产过 程向短流程、近终成型方向发展。
⑷ 对管材产品要求总的趋势是优质、廉价、 高效、低耗。
2 热轧无缝钢管生产
自动轧管机组生产工艺: (冷定心) 加热
管坯→加热→热定心→穿孔→轧管→均整 定径 再加热→减径→冷却→矫直→切管→
热处理→检查→入库
连轧管机组
坯
菌式穿孔机
穿
盘式穿孔机
孔 方轧坯